明細書 発明の名称
薄膜形成用基板、 薄膜基板、 及び発光素子 技術分野
本発明は、 セラミック材料を主成分とする焼結体からなる窒化ガリウム、 窒化インジウム、 窒化アルミニウムを主成分とする薄膜を形成するための基板及び該薄膜が形成されている薄膜 基板、 該基板を用いて作製される発光素子に関する。 背景技術
近年、 発光ダイオード (L ED) あるいはレーザーダイオード (LD) などさまざまな発光 半導体素子がディスプレイ、 照明装置、 光通信、 記憶装置用などの光源に用いられるようにな つた。 このような発光半難素子の中で窒化ガリウム、 窒化インジウム、 窒化アルミニウムの うちから選ばれた少なくとも 1種以上を主成分とし、 該成分をドーピングにより P及び N型半 導体化した III— V族窒化物単結晶薄 及び量子井戸構造などの発光層の少なくとも 3層以 上からなる 11卜 V族窒化物薄膜を例えばサフアイァなどの基板上に主にェピタキシャル成長 させた緑青色〜青色〜青紫色〜紫外線を発光する素子が開発されて来ている。 上記の窒化ガリ ゥム、 窒化インジウム、 窒化アルミニウムのうちから選ばれた少なくとも 1種以上を主成分と する薄膜からなり少なくとも N型半導体層及び発光層及び P型半導体層を含む積層体により構 成される発光^? (以下本発明において特に断らない限り単に "発光素子"という)は信号機、 液晶用バックライト、 白熱電球や蛍光灯に代わる一般照明用などの光源や、 高容 ディスク 装置のレーザー光源などに使用されている。 用途によって発光素子からの光をそのまま使用す るか、 蛍光体を用いて相互作用により白色光に変換して用いられる。 該発光素子は通常上記各 窒化物あるいは各窒化物混晶の P型半導体及び N型半 本と発光層とから形成されたニ^素 子 (ダイオード) 構造で直流電力を印加することで駆動する。
このような発光素子を高出力レーザーの光源として用いたり、 一般照明の光源として用いる など発光素子の高出力化が始まっている。 発光素子をこのような用途に用いようとするとき発 光素子を形成する窒化ガリウム、 窒化インジウム、 窒化アルミニウムのうちから選ばれた少な くとも 1種以上を主成分とするェピタキシャル膜を主体とする薄膜を形成するための基板が問 題となってきている。 すなわち^から用いられているサファイア基板は単結晶ではあっても 発光素子を構成する窒化ガリウム、 窒化インジウム、 窒化アルミニウムとは結晶構造や熱膨張 率などが異なりそのためサファイア基板の上に形成される窒化ガリウム、 窒化インジウム、 窒 化アルミニウムから選ばれた少なくとも 1種以上を主成分とする薄膜が良好な結晶性を有する ものになりにくく、 ようやく近年の研究で高い結晶性の単結晶薄膜として形成できるようにな つた。 しかしながらたとえ高い結晶性の単結晶薄膜であつてもサフアイァ基板と該薄膜との間 の結晶格子不整合性や熱膨張率の違いによつて該薄膜中には結晶転位やひずみが生じ易いので このような薄膜を用いて製造される発光素子は製造歩留まりが低下に結びつき易く、 発光素子 の発光効率向上あるいはレーザー発振の高出力化や長 ^化などの特性向上の達成も困難であ る。 また、 サファイア基板は単結晶であるので製造コストも高くその上に形成される窒化ガリ ゥム、 窒化インジウム、 窒化アルミニウムのうちから選ばれた少なくとも 1種以上を主成分と する単結晶薄膜が広範な用途に使用できにくいという問題もある。
また一方では本発明による発光素子あるいは従来からのレーザーダイ才ード及び発光ダイォ
ードからの光を所望の強さ、 距離、 位置に導くための光導波路も ί ^からさまざまなものが提 案されてきている。通常 L i Nb 03、 シリコンなどの結晶基板、 あるいは石英ガラスなどのガ ラス基板に髙屈折率部を形成することで得られる。 ί ^からの光導波路は青色光、 紫外線など の波長の短い光に対する邏性が低かったり、 基板の電気騰性が小さいために光導波路が形 成されている基板上に電気回路を同時に形成しにくかったり、 あるいは基板の熱伝導率が低い ために光導波路が形成されている基板上に高出力の発光素子を同時に搭載できにくい、 などの 問題がある。
上記のように «からのサファイア基板を用いその上に形成される窒化ガリウム、 窒化イン ジゥム、 窒化アルミニウムのうちから選ばれた少なくとも 1種以上を主成分とする薄膜は近年 比較的高い結晶性の単結晶薄膜として形成できるようになってきた。 しかしながらサファイア 基板を用いその上に形成される薄膜により構成される発光素子の発光効率は低く通常 2 %〜 8 %程度であり を駆動させるために加えられる電力の 9 2 %〜 9 8 %が光に変換されず例 えば熱などとなって無駄に消費されており本来の III一 V族窒化物半導体の有する発光特性が 十分に発現されていない。 その原因は発光素子を構成する薄膜がサファイア基板上にたとえ高 い結晶性の単結晶薄膜として形成できたとしてもサフアイァ基板と該薄膜との間の結晶格子不 整合性や熱膨張率の違いによって該薄膜中には結晶転位やひずみが生じ易く、 さらにサフアイ ァ基板は薄膜状の窒化ガリウム、 窒化インジウム、 窒化アルミニウムと比べても屈折率が小さ く、 また透明で均質なバルク単結晶であるため発光素子から発した光の多くはサフアイァ基板 と上記薄膜との界面ゃサフアイァ基板の表面で反射されて発光素子内部に戻り閉じ込められ易 いためであろうと思われる。
そのため窒化ガリウム、 窒化インジウム、 窒化アルミニウムのうちから選ばれた少なくとも 1種以上を主成分とするェピタキシャル膜を含む薄膜を形成し発光素子を製造するための基板 材料に関して従来のサフアイァに代わつて炭化珪素、 シリコンなどを主成分とする単結晶基板 材料が提案されている。 炭化珪素単結晶を基板として用いる例として例えば特開平 1 0— 2 7 9 4 7あるいは特開平 1 1 - 4 0 8 8 4などの方法が提案されている。 シリコン基板としては 例えば特開平 1 0— 2 1 4 9 5 9などの方法が提案されている。 しかしながらこれらの基板を 用いてもやはり窒化ガリウム、 窒化インジウム、 窒化アルミニウムのうちから選ばれた少なく とも 1種以上を主成分とする単結晶薄膜と結晶構造や格子定数が異なるなどの理由で該基板上 に良好な単結晶薄膜が形成されにくい。 さらに特開平 9— 1 7 2 1 9 9には微からの単結晶 基板の持つ問題点を解決すべく単結晶基板に代わって石英ガラスなどのガラス基板、 多結晶シ リコンなど焼結法により作製した基板を用いる方法が提案されている。 しかしながらこの方法 板上に窒化ガリゥム系化合物半導体層を形成する前に酸化亜鉛や酸は銀などの II 素 の酸化物からなる Ιϋί料を形成しなければならないがその効果は必ずしも明確にされていない。 このような II 素の酸化物を形成した基板を用いた場合そこに形成される窒化ガリゥム系化 合物半導体を構成する薄膜の結晶性は必ずしも明確でなく作製される半導体素子の発光効率な どの特性に関しても明確でなく結局問題解決には至つていない。 上記のように«からのサフ アイァゃ炭化珪素などの単結晶基板に代わり窒化ガリウム、 窒化インジウム、 窒化アルミニゥ ムのうちから選ばれた少なくとも 1種以上を主成分とする良質な単結晶薄膜が形成できる基板 が求められているが実現できていない。 また、 上記窒化ガリウム、 窒化インジウム、 窒化アル ミニゥムのうちから選ばれた少なくとも 1種以上を主成分とする良質な単結晶薄膜を形成した 薄膜基板が求められているが実現できていない。
このように従来からのサフアイァ基板を用レ ^作製される発光素子は発光効率が低く本来の ΠΙ— V族窒化物半 本の有する発光特性を十分に発現できているとは云いがたぐ少なくとも サファイア基板を用いて作製される発光素子の発光効率と同等以上のものが求められているが
上記のようにサフアイァ基板に代わりその欠点を改善するために提案されてきた基板を用いて 作製される発光素子もサファイア基板を用いて作製される発光素子より発光効率が向上してい るとはいえず本来の II I一 V族窒化物半導体の有する発光特性が十分に実現できていないとい ぅ瞒があった。
また、 一方発光素子からの青色光、 紫外線などの波長の短レ洸を所望の強さ、 距離、 位置に 導くための光導波路として例えば特許第 3 1 1 9 9 6 5に記載される方法が提案されている。 この験はシリコン、 サファイアなどからなる単結晶基板に窒化アルミニウム薄膜による光導 波路を形成する方法が開示されているが、 青色光、 紫外線などの波長の短い光の伝送性を得る ために酸窒化アルミ二ゥムゃサイァ口ンなどからなるバッファ層を設ける必要がある。 このよ うな工夫はおそらく基板材料のシリコン、 サファイアと窒化アルミニゥムとの間に結晶格子不 齡性ゃ熱膨張率の違いがありその結果高い結晶性の窒化アルミニゥム薄膜の形成が困難であ り導波路の伝送損失が大きくなるためであろうと推測される。 また、 格子不整合性や熱膨張率 の違い以外にもシリコン基板を用いた場合直接形成された窒化アルミニウム薄膜の屈折率がシ リコンに比べて小さいため窒化アルミニウム薄膜中で光の全反射が生じないため導波路として 機能しないことも大きな原因であろうと搬則される。 さらに、 基板にシリコンを用いた場合電 気«性が小さくかつ誘電率が高いので直接基板上に電気回路が形成できにくく、 発光素子が 基板上に一体となって搭載できにくいという問題がある。 また、 基板にサファイアを使用する 場合熱伝導率が小さいので高出力発光素子を搭載した場合放熱性に問題が生じる。
したがって、 発光素子からの青色光、 紫外線などの波長の短い光を醒し、 素子睡用など の電気回路が形成され 高出力発光素子が搭載可能な光導波路は満足なものが得られていない という問題があった。 発明の開示
本発明は上記に示したような課題を解決するためになされたものである。 本発明者は窒化ガ リウム、 窒化インジウム、 窒化アルミニウムのうちから選ばれた少なくとも 1種以上を主成分 とする単結晶薄膜を形成するための基板として窒化アルミニウムを主成分とする焼結体を中心 に各種セラミック材料を主成分とする焼結体を検討し該セラミック材料を主成分とする焼結体 からなる基板を用いることで窒化ガリウム、 窒化インジウム、 窒化アルミニウムを主成分とす る結晶性に優れた単結晶薄膜がクラックや剥離などがなく強固に固着した状態で直接形成でき ることを見出し特願 2 0 0 2— 3 6 2 7 8 3、 特願 2 0 0 3— 1 8 6 1 7 5、 特願 2 0 0 3 - 2 9 4 2 5 9等にて提案してきた。 また今回上記のように窒化ガリウム、 窒化インジウム、 窒 化アルミニウムを主成分とする単結晶薄膜が直接形成し得る窒化アルミニウムなどのセラミツ ク材料を主成分とする焼結体には無定形薄膜、 多結晶薄膜、 配向性多結晶薄膜など必ずしもェ ピタキシャル成長した単結晶薄膜ではない窒化ガリウム、 窒化インジウム、 窒化アルミニウム のうちから選ばれた少なくとも 1種以上を主成分とする薄膜であってもクラックや剥離などが なく強固に固着した状態で直接形成できることを見出した。 さらにこのような各種結晶状態の 薄膜をあらかじめ形成したセラミック材料を主成分とする焼結体を基板として用いこの基板に 窒化ガリウム、 窒化インジウム、 窒化アルミニウムのうちから選ばれた少なくとも 1種以上を 主成分とする単結晶薄膜を成長させた時クラックゃ剥離などがなく強固に固着した状態で形成 でき、 得られる該単結晶薄膜は窒化アルミニウムなどのセラミック材料を主成分とする焼結体 に直接形成した単結晶薄膜より結晶性が優れていること、 などを見出した。
また本発明において光透過性を有するセラミック材料を主成分とする焼結体にはより結晶性 の優れた窒化ガリゥム、 窒化ィンジゥム、 窒化アルミニゥムのうちから選ばれた少なくとも 1 種以上を主成分とする単結晶薄膜が形成し得ることが見出された。 光透過性を有するセラミッ
ク材料を主成分とする焼結体には無定形薄膜、 多結晶薄膜、 配向性多結晶薄膜など必ずしもェ ピ夕キシャル成長した単結晶薄膜ではない窒化ガリウム、 窒化インジウム、 窒化アルミニウム のうちから選ばれた少なくとも 1種以上を主成分とする薄膜も形成し得る。 このような各種結 晶状態の薄膜をあらかじめ形成した光 ¾m性を有するセラミック材料を主成分とする焼結体を 用いればその上にはさらに結晶性の優れた窒化ガリウム、 窒化インジウム、 窒化アルミニウム のうちから選ばれた少なくとも 1種以上を主成分とする単結晶薄膜が形成し得ることが見出さ れた。
このように本発明においてセラミック材料を主成分とする焼結体及び光 ¾1性を有するセラ ミック材料を主成分とする焼結体には窒化ガリウム、 窒化インジウム、 窒化アルミニウムのう ちから選ばれた少なくとも 1種以上を主成分とする結晶性に優れた単結晶薄膜を形成できるこ とが見出され またセラミック材料を主成分とする焼結体及び光 性を有するセラミック材 料を主成分とする焼結体を用いることで上記窒化ガリウム、 窒化インジウム、 窒化アルミニゥ ムのうちから選ばれた少なくとも 1種以上を主成分とする結晶性に優れた単結晶薄膜を形成し た薄膜基板が得られることが見出された。
上記の薄膜を形成していないセラミック材料を主成分とする焼結体及び ¾¾ϋ性を有するセ ラミック材料を主成分とする焼結体、 あるいは上記セラミック材料を主成分とする焼結体及び 光透過性を有するセラミック材料を主成分とする焼結体に窒化ガリウム、 窒化インジウム、 窒 化アルミニウムのうちから選ばれた少なくとも 1種以上を主成分とする薄膜が形成された薄膜 基板を用いることで «からのサファイア基板を用いて作製される発光^?と比較して少なく とも同等以上、 最大 4〜 5倍以上の発光効率を有する発光素子が M できる。 さらに上記薄膜 基板を用いることで伝 員失が小さくかつ紫外光の伝送が低損失で可能な光導波路が^ Iでき ることが明らかとなつた。 また本発明において表面粗さの大きいセラミック材料を主成分とす る焼結体にはェピタキシャル成長した単結晶薄膜及び無定形薄膜、 多結晶薄膜、 配向性多結晶 薄膜など各種結晶状態の窒化ガリウム、 窒化インジウム、 窒化アルミニウムのうちから選ばれ た少なくとも 1種以上を主成分とする薄膜が形成し得ることが見出された。 このような表面粗 さの大きいセラミック材料を主成分とする焼結体を用いることで «からのサファイア基板を 用いて作製される発光素子と比較して少なくとも同等以上の発光効率を有する発光素子が作製 し得ることも見出された。
本発明において、 窒化ガリウム、 窒化インジウム、 窒化アルミニウムのうちから選ばれた少 なくとも 1種以上を主成分とする薄膜状の単結晶とセラミツク材料を主成分とする焼結体とは 強固に一体化し、 単結晶及びセラミック材料を主成分とする焼結体のそれぞれ単独ではなし得 ない相乗効果を有する薄膜基板が実現し得ることが見出された。 またこのようにセラミック材 料を主成分とする焼結体と一体化された薄膜状の単結晶であっても従来からのサファイアや炭 化珪素などの塊状やバルク状単結晶と同等かそれに近い高い結晶性を有するものが作製できる ことが見出された。
本発明において、 発光素子などの電子素子、 あるいは回路基板などの電子部品を作製する上 で«からのサファイアや炭化珪素などの塊状やバルク状などそれ自#¾虫立で単結晶として存 在し使用される材料では実現が困難であった特性を有する基板が窒化ガリゥム、 窒化ィンジゥ ム、 窒化アルミニウムのうちから選ばれた少なくとも 1種以上を主成分とする結晶性に優れた 薄膜状の単結晶とセラミック材料を主成分とする焼結体とを強固に一体化し、 単結晶及びセラ ミック材料を主成分とする焼結体のそれぞれ単独ではなし得ない相乗効果を引き出すことによ り実現し得ることが見出された。
本発明者はその他に、 炭化珪素、 窒化珪素、 窒化ガリウム、 酸化ベリリウム、 酸化亜鉛、 酸 化アルミ二ゥム、 窒化ガリゥムなど六方晶系又は三方晶系の結晶構造を有するセラミック材料
を主成分とする焼結体には酸化水銀などの II族元素の酸化物膽才料などを介在させなくとも窒 化ガリウム、 窒化インジウム、 窒化アルミニウムのうちから選ばれた少なくとも 1種以上を主 成分とする薄膜が形成し得ること、 特に特定の表面状態あるいは表面粗さのものを用いること で窒化ガリウム、 窒化インジウム、 窒化アルミニウムのうちから選ばれた少なくとも 1種以上 を主成分とする結晶性の高い単結晶薄膜を形成できることを見出した。 また、 上記六方晶系又 は Ξ方晶系の結晶構造を有するセラミック材料を主成分とする焼結体にあらかじめ窒化ガリゥ ム、 窒化インジウム、 窒化アルミニウムのうちから選ばれた少なくとも 1種以上を主成分とす る薄膜を形成したものはその上により結晶性のすぐれた単結晶薄膜が形成できることを見出し た。
また、 上記六方晶系又は三方晶系の結晶構造を有するセラミック材料を主成分とする焼結体 のなかで特定の組成を有する酸化ベリリウム、 酸化亜鉛、 酸化アルミニウム、 窒化ガリウムを 主成分とするものは単結晶薄膜を形成するために優れていることを見出した。 また 性に 優れたものが得られるので発光素子を作製するための基板として好ましいことを見出した。 上 記酸化亜鉛を主成分とする焼結体としてアルミニウム成分を含むもの、 及び窒化ガリゥムを主 成分とする焼結体は導電性でかつ 過性を有するのでこのような酸化亜鉛を主成分とする焼 結体及び窒化ガリゥムを主成分とする焼結体を用いれば発光効率の優れた発光素子が簡易な製 造工程で作製し得ることを見出した。
本発明は上記のような炭化珪素、 窒化珪素、 窒化ガリウム、 酸化ベリリウム、 酸化亜鉛、 酸 化アルミニゥムなど六方晶系又〖 方晶系の結晶構造を有するセラミック材料を主成分とする 焼結体からなることを特徴とする薄膜形成用基板を含み、 さらに六方晶系又 方晶系の結晶 構造を有するセラミック材料を主成分とする焼結体からなる基板に窒化ガリゥム、 窒化ィンジ ゥム、 窒化アルミニウムのうちから選ばれた少なくとも 1種以上を主成分とする薄膜が形成さ れていることを特徴とする薄膜基板も含む。
また、 本発明者はこのような炭化珪素、 窒化珪素、 窒化ガリウム、 酸化ベリリウム、 酸化亜 鉛、 酸化アルミニウムなど^晶系又 方晶系の結晶構造を有するセラミック材料を主成分 とする焼結体、 あるいは窒化ガリウム、 窒化インジウム、 窒化アルミニウムのうちから選ばれ た少なくとも 1種以上を主成分とする薄膜があらかじめ形成された炭化珪素、 窒化珪素、 窒化 ガリウム、 酸化ベリリウム、 酸化亜鉛、 酸化アルミニウムなど六方晶系又は三方晶系の結晶構 造を有するセラミック材料を主成分とする焼結体を用いて作製される発光素子を含み、 該発光 ^?の発光効率は少なくともサファイア基板を用いて作製される発光素子と比較して少なくと も同等以上、 最大 3〜 4倍以上のものが製造できることを見出した。
また本発明者はその他に、 例えぱ 匕ジルコニウム、 酸化マグネシウム、 アルミン酸マグネ シゥム、 酸化チタン、 チタン酸バリウム、 チタン酸ジルコン隱、 酸化イットリウムなどの希 土 ¾素酸ィ匕物、 酸化トリウム、 各種フェライト、 ムライト、 フォルステライト、 ステアタイ ト、 結晶化ガラス、 などの各種セラミック材料を主成分とする焼結体にあらかじめ窒化ガリウ ム、 窒化インジウム、 窒化アルミニウムのうちから選ばれた少なくとも 1種以上を主成分とす る薄膜を形成したものはその上により結晶性のすぐれた単結晶薄膜が形成できることを見出し た。 上記の酸化ジルコニウム、 酸化マグネシウム、 アルミン酸マグネシウム、 酸化チタン、 チ タン酸バリウム、 チタン酸ジルコン酸鉛、 酸化イットリウムなどの希土 I ^素酸化物、 酸化ト リウム、 各種フェライト、 ムライト、 フォルステライト、 ステアタイト、 結晶化ガラス、 など の各種セラミック材料を主成分とする焼結体にあらかじめ窒化ガリウム、 窒化インジウム、 窒 化アルミニウムのうちから選ばれた少なくとも 1種以上を主成分とする薄膜を形成したものは その上に結晶性のすぐれた単結晶薄膜が形成できることを見出した。 また、 これらの各種セラ ミック材料を主成分とする焼結体は比較的容易に 過性を有するものが作製できることも見
出した。
また、 本発明者は窒化アルミニウムを主成分とする焼結体及び炭化珪素、 窒化珪素、 窒化ガ リウム、 酸化ベリリウム、 酸化亜鉛、 酸化アルミニウムなど六方晶系又 方晶系の結晶構造 を有するセラミック材料を主成分とする焼結体だけでなく例えば ¾化ジルコニウム、 酸化マグ ネシゥム、 アルミン酸マグネシウム、酸化チタン、チタン酸バリウム、チタン酸ジルコン蘭、 酸化イットリウムなどの希土 «化物、 酸ィ匕トリウム、 各種フェライト、 ムライト、 フオリレス テライト、 ステア夕イト、 結晶化ガラス、 などのセラミック材料を主成分とする焼結体を用い て作製される発光素子の発光効率は少なくともサファイア基板を用いて作製される発光素子と 比較して少なくとも同等以上、 最大 2〜3倍以上のものが製造できることを見出した。
その他にも本発明者は比較的凹凸の多い表面状態のセラミック材料を主成分とする焼結体、 言い換えれば表面粗さの大きいセラミック材料を主成分とする焼結体を用いて作製される発光 素子は同じセラミックを主成分とする材料であつても表面粗さの小さいものを用レゝて作製され る発光素子に比べて発光効率が向上し易いことを見出した。
本発明は上記のようにセラミック材料を主成分とする;^結体からなることを特徴とする窒化 ガリウム、 窒化インジウム、 窒化アルミニウムのうちから選ばれた少なくとも 1種以上を主成 分とする単結晶薄膜を形成するための薄膜形成用基板を含み、 さらにセラミック材料を主成分 とする焼結体に窒化ガリゥム、 窒化ィンジゥム、 窒化アルミニゥムのうちから選ばれた少なく とも 1種以上を主成分とする単結晶薄膜が形成されていることを とする薄膜基板も含む。 また、 本発明は上記のように光 性を有するセラミック材料を主成分とする焼結体からな ることを特徴とする窒化ガリウム、 窒化インジウム、 窒化アルミニウムのうちから選ばれた少 なくとも 1種以上を主成分とする薄膜を形成するための薄膜形成用基板を含み、 さらに^ i 性を有するセラミック材料を主成分とする焼結体に窒化ガリウム、 窒化インジウム、 窒化アル ミニゥムのうちから選ばれた少なくとも 1種以上を主成分とする薄膜が形成されていることを 特徴とする薄膜基板も含む。
また、 本発明は上記のように窒化アルミニウム及び炭化珪素、 窒化珪素、 窒化ガリウム、 酸 化ベリリウム、 酸化 «、 酸化アルミニウムなど六方晶系又 方晶系の結晶構造を有するも のだけでなく例えば酸化ジルコニウム、 酸化マグネシウム、 アルミン酸マグネシウム、 酸化チ タン、 チタン酸バリウム、 チタン酸ジルコン酸鉛、 酸化イットリウムなどの希土纖化物、 酸 化トリウム、 各種フェライト、 ムライト、 フォルステライト、 ステア夕イト、 結晶化ガラス、 などのセラミック材料を主成分とする焼結体を用いて作製される発光素子も含む。
このように本発明は窒化アルミニウム及び炭化珪素、 窒化珪素、 窒化ガリウム、 酸化べリリ ゥム、 酸化亜鉗、 酸化アルミニウムなど六方晶系又は三方晶系の結晶構造を有するものだけで なく例えば 化ジルコニウム、 酸化マグネシウム、 アルミン酸マグネシウム、 酸化チタン、 チ 夕ン酸バリゥム、 チタン酸ジルコン酸鉛、 酸化ィットリゥムなどの希土靈化物、 酸化トリウ ム、 各種フェライト、 ムライト、 フォルステライト、 ステアタイト、 結晶化ガラス、 などのセ ラミック材料を主成分とする焼結体を用いて作製される発光素子も含む。
また、 本発明は上記のように窒化アルミニウム及び炭化珪素、 窒化珪素、 窒化ガリウム、 酸 化ベリリウム、 酸化亜鉛、 酸化アルミニウムなど六方晶系又 方晶系の結晶構造を有するも のだけでなく例えば酸化ジルコニウム、 酸化マグネシウム、 アルミン酸マグネシウム、 酸化チ タン、 チタン酸バリウム、 チタン酸ジルコン酸鉛、 酸化イットリウムなどの希土麵化物、 酸 化トリウム、 各種フェライト、 ムライト、 フォルステライト、 ステアタイト、 結晶化ガラス、 などの光 性を有するセラミック材料を主成分とする焼結体を用いて作製される発光素子も 含む。
また、 本発明は上記のように窒化アルミニウム及び炭化珪素、 窒化珪素、 窒化ガリウム、 酸
化ベリリウム、 酸化亜鉛、 酸化アルミニウムなど六方晶系又は三方晶系の結晶構造を有するも のだけでなく例えば ¾化ジルコニウム、 酸化マグネシウム、 アルミン酸マグネシウム、 酸化チ タン、 チタン酸バリウム、 チタン酸ジルコン酸鉛、 酸化イットリウムなどの希土難化物、 酸 化トリウム、 各種フェライト、 ムライト、 フォルステライト、 ステア夕イト、 結晶化ガラス、 など、 窒化ガリウム、 窒化インジウム、 窒化アルミニウムのうちから選ばれた少なくとも 1種 以上を主成分とする薄膜が形成されたセラミック材料を主成分とする焼結体を用いて作製され る発光素子ち含む。
また、 本発明は上記のように窒化アルミニウム及び炭化珪素、 窒化珪素、 窒化ガリウム、 酸 化ベリリウム、 酸化亜鉛、 酸化アルミニウムなど六方晶系又 方晶系の結晶構造を有するも のだけでなく例えば酸化ジルコニウム、 酸化マグネシウム、 アルミン酸マグネシウム、 酸化チ 夕ン、 チタン酸バリゥム、 チタン酸ジルコン酸鉛、 酸化ィットリゥムなどの希土難化物、 酸 匕トリウム、 各種フェライト、 ムライト、 フォルステライト、 ステア夕イト、 結晶化ガラス、 など、 窒化ガリウム、 窒化インジウム、 窒化アルミニウムのうちから選ばれた少なくとも 1種 以上を主成分とする単結晶薄膜が形成されたセラミツク材料を主成分とする焼結体を用いて作 製される発光軒も含む。
また、 本発明は上記のように窒化アルミニウム及び炭化珪素、 窒化珪素、 窒化ガリウム、 酸 化ベリリウム、 酸化碰、 酸化アルミニウムなど六方晶系又 方晶系の結晶構造を有するも のだけでなく例えば 化ジルコニウム、 酸化マグネシウム、 アルミン酸マグネシウム、 酸化チ タン、 チタン酸バリウム、 チタン酸ジルコン酸鉛、 酸化イットリウムなどの希土,化物、 酸 化トリウム、 各種フェライト、 ムライト、 フォルステライト、 ステアタイト、 結晶化ガラス、 など表面粗さの大きいセラミック材料を主成分とする焼結体を用いて作製される発光素子も含' む。
本発明は上記のように単結晶あるいは特定の結晶方位を有する配向性多結晶に比べて不均質 であるセラミック材料を主成分とする焼結体であっても窒化ガリウム、 窒化インジウム、 窒化 アルミニウムのうちから選ばれた少なくとも 1種以上を主成分とする単結晶薄膜が形成でき、 その結果該単結晶薄膜が形成された薄膜基板が比較的容易に製造できることを見出すことによ つてなされた。 なお、 各種セラミック材料を主成分とする焼結体にあらかじめ窒化ガリウム、 窒化インジウム、 窒化アルミニウムのうちから選ばれた少なくとも 1種以上を主成分とする薄 膜を形成したものを用いても窒化ガリウム、 窒化インジウム、 窒化アルミニウムのうちから選 ばれた少なくとも 1種以上を主成分とする同様に単結晶薄膜が形成でき、 その結果該単結晶薄 膜が形成された薄膜基板が比較的容易に製造できる。
さらに、 本発明者は上記のように単結晶あるいは特定の結晶方位を有する配向性多結晶に比 ベて不均質であるセラミック材料を主成分とする焼結体を用いて作製される発光素子であって もその発光効率は^からのサフアイァなどのバルク状単結晶基板を用いて作製される発光素 子と比較して少なくとも同等以上、 最大 4〜5倍以上のものが製造できることを見出した。 セ ラミック材料を主成分とする焼結体にあらかじめ窒化ガリウム、 窒化インジウム、 窒化アルミ ニゥムのうちから選ばれた少なくとも 1種以上を主成分とする薄膜が形成されたものを用いて 作製される発光素子であってもその発光効率はサファイア基板を用いて作製される発光素子と 比較して少なくとも同等以上、 最大 4〜5倍以上のものが製造できることを見出した。
本発明者は上記のように鋭意研究した結果本発明を完成させるに至つた。
すなわち本発明は、 窒化ガリウム、 窒化インジウム、 窒化アルミニウムのうちから選ばれた 少なくとも 1種以上を主成分とする単結晶薄膜を形成するための基板であって、 該基板がセラ ミック材料を主成分とする焼結体からなることを特徴とする薄膜形成用基板、 である。
また本発明は、 窒化ガリウム、 窒化インジウム、 窒化アルミニウムのうちから選ばれた少な
くとも 1種以上を主成分とする薄膜を形成するための基板であって、 該基板が)1 ffi 性を有す るセラミック材料を主成分とする焼結体からなることを特徴とする薄膜形成用基板、 である。 また本発明は、 上記薄膜形成用基板に用いられるセラミック材料を主成分とする焼結体が窒 化アルミニウムを主成分とする焼結体であることを特徴とする薄膜形成用基板、 である。 また本発明は、 上記薄膜形成用基板に用いられるセラミック材料を主成分とする焼結体が六 方晶系又は三方晶系のうちから選ばれた少なくともいずれかの結晶構造を有するセラミック材 料を主成分とする焼結体であることを特徴とする薄膜形成用基板、 である。
また本発明は、 上記薄膜形成用基板に用いられるセラミック材料を主成分とする焼結体力職 ィ匕亜鉛、 酸化ベリリウム、 酸化アルミニウム、 炭化珪素、 窒化珪素、 窒化ガリウムのうちから 選ばれた少なくとも 1種以上を主成分とする焼結体であることを特徴とする薄膜形成用基板、 である。
また本発明は、 上記薄膜形成用基板に用いられるセラミック材料を主成分とする焼結体力雙 化ジルコニウム、 酸化マグネシウム、 アルミン酸マグネシウム、 酸化チタン、 チタン酸パリウ ム、 チタン酸ジルコン酸鉛、 希土碰化物、 酸化トリウム、 各種フェライト、 ムライト、 フォ ルステライト、 ステア夕イト、 結晶化ガラスのうちから選ばれた少なくとも 1種以上を主成分 とする焼結体であることを特徴とする薄膜形成用基板、 である。
また本発明は、 窒化ガリウム、 窒化インジウム、 窒化アルミニウムのうちから選ばれた少な くとも 1種以上を主成分とする薄膜を形成するための基板の $¾i方法であって、 該基板が原料 として酸化アルミニウムの 法によるもの及び金属アルミニウムの直接窒化法によるものの なかから選ばれたいずれかをそれぞ Miで用いるかあるいは酸化アルミニウムの 法によ るもの及び金属アルミ二ゥムの直接窒化法によるものを混合して用いるか少なくともレゝずれか の原料を用いて難される窒化アルミニウムを主成分とする焼結体からなることを特徴とする 薄膜形成用基板の製造方法、 である。
また本発明は、 窒化ガリウム、 窒化インジウム、 窒化アルミニウムのうちから選ばれた少な くとも 1種以上を主成分とする薄膜を形成するための基板の $¾t方法であって、 該鎌が窒化 アルミニウムを主成分とする粉末成形体又は焼結体を非酸化性雰囲気中 1 5 0 以上の で 1 0分間以上 «することで得られる窒化アルミニウムを主成分とする焼結体からなること を特徴とする薄膜形成用基板の製造方法、 である。
また本発明は、 希土類 素及びアルカリ土類金属のうちから選ばれた少なくとも 1種以上の 成分の含有量が元素 で合計 0. 5重量%以下、酸 有量が元素 で 0. 9重量%以下、 結晶相として A 1 Nを 9 5 %以上、 窒化アルミニウム粒子の大きさが 5 m以上、 かつ光透過 性を有することを特徴とする窒化アルミニウムを主成分とする焼結体、 である。
また本発明は、 少なくともアルミニウム成分を含みかつ光 ¾i性を有する酸化亜鉛を主成分 とする焼結体、 である。
また本発明は、 光 ¾i性を有することを特徴とする窒化ガリウムを主成分とする焼結体、 で ある。
また本発明は、 導電性を有することを特徴とする窒化ガリウムを主成分とする焼結体、 であ る。
また本発明は、 光 性を有しカゝっ導電性を有することを とする窒化ガリゥムを主成分 とする焼結体、 である。
また本発明は、 アルカリ土類金属及び希土類 素のうちから選ばれた少なくとも 1種以上の 成分を含有することを特徴とする窒化ガリゥムを主成分とする焼結体、 である。
また本発明は、 »、 カドミウム、 ベリリウム、 マグネシウム、炭素、珪素、ゲルマニウム、 セレン、 及びテルルのうちから選ばれた少なくとも 1種以上の成分を含有することを特徴とす
る窒化ガリウムを主成分とする焼結体、 である。
また本発明は、 アルミニウム、 インジウム、 及び酸素のうちから選ばれた少なくとも 1種以 上の成分を含有することを特徴とする窒化ガリウムを主成分とする焼結体、 である。
また本発明は、 遷移金属のうちから選ばれた少なくとも 1種以上の成分を含有することを特 徴とする窒化ガリウムを主成分とする焼結体、 である。
また本発明は、 酸 有量 1 0重量%以下の窒化ガリウムを主成分とする粉末、 である。 また本発明は、 平均粒径 1 0 m以下の窒化ガリウムを主成分とする粉末、 である。
また本発明は、 金属ガリゥムと窒素含有物質とを窒化反応せしめることを特徴とする窒化ガ リウムを主成分とする粉末の製造方法、 である。
また本発明は、 酸化ガリウムを ϋ¾剤及び窒 有物質とを用いて室化反応せしめることを 特徴とする窒化ガリゥムを主成分とする粉末の製造方法、 である。
また本発明は、 気体状のガリゥム化合物を窒^^有物質と窒化反応せしめることを とす る窒化ガリウムを主成分とする粉末の製造方法、 である。
また本発明は、 セラミック材料を主成分とする焼結体に窒化ガリウム、 窒化インジウム、 窒 化アルミニウムのうちから選ばれた少なくとも 1種以上を主成分とする単結晶薄膜が形成され ていることを特徴とする薄膜基板、 である。
また本発明は、 ¾¾1性を有するセラミック材料を主成分とする焼結体に窒化ガリウム、 窒 化インジウム、 窒化アルミニウムのうちから選ばれた少なくとも 1種以上を主成分とする薄膜 が形成されていることを特徴とする薄膜基板、 である。
また本発明は、 上記薄膜基板に用いられるセラミック材料を主成分とする焼結体が窒化アル ミニゥムを主成分とする焼結体であることを特徴とする薄膜基板、 である。
また本発明は、 上記薄膜基板に用いられるセラミック材料を主成分とする焼結体が六方晶系 又は三方晶系のうちから選ばれた少なくともいずれかの結晶構造を有するセラミック材料を主 成分とする焼結体であることを特徴とする薄膜基板、 である。
また本発明は、上記薄 板に用いられるセラミック材料を主成分とする焼結体が ¾化亜鉛、 酸化ベリリウム、 酸化アルミニウム、 炭化珪素、 窒化珪素、 窒化ガリウムのうちから選ばれた 少なくとも 1種以上を主成分とする焼結体であることを特徴とする薄膜基板、 である。
また本発明は、 上記薄膜基板に用いられるセラミック材料を主成分とする焼結体が 化ジル コニゥム、 酸化マグネシウム、 アルミン酸マグネシウム、 酸化チタン、 チタン酸バリウム、 チ タン酸ジルコン赚、 希土謙化物、 酸化トリウム、 各種フェライト、 ムライト、 フオルステ ライト、 ステアタイト、 結晶化ガラスのうちから選ばれた少なくとも 1種以上を主成分とする 焼結体であることを特徴とする薄膜基板、 である。
また本発明は、 窒化アルミニウムを主成分とする焼結体に窒化ガリウム、 窒化インジウム、 窒化アルミニウムのうちから選ばれた少なくとも 1種以上を主成分とする薄膜により光導波路 が形成されていることを特徴とする薄膜基板、 である。
また本発明は、 セラミック材料を主成分とする焼結体に窒化ガリウム、 窒化インジウム、 窒 化アルミニウムのうちから選ばれた少なくとも 1種以上を主成分とする単結晶薄膜を形成した 薄膜基板の製造方法であって、 該薄膜がガリウム、 インジウム、 アルミニウムのうちから選ば れた少なくとも 1種以上のを含む有機化合物を主原料としアンモニア、 窒素、 水素のうちから 選ばれた少なくとも 1種以上を反応ガスとして形成されるものであることを特徴とする薄膜基 板の製造方法、 である。
また本発明は、 セラミック材料を主成分とする焼結体に窒化ガリウム、 窒化インジウム、 窒 化アルミニウムのうちから選ばれた少なくとも 1種以上を主成分とする単結晶薄膜を形成した 薄膜基板の製造方法であって、 該薄膜がガリウム、 インジウム、 アルミニウムのうちから選ば
れた少なくとも 1種以上の成分を含むハロゲン化物を主原料としアンモニア、 窒素、 τΚ素のう ちから選ばれた少なくとも 1種以上を反応ガスとして形成されるものであることを特徴とする 薄膜基板の製造方法、 である。
また本発明は、 性を有するセラミック材料を主成分とする焼結体に窒化ガリウム、 窒 化インジウム、 窒化アルミニウムのうちから選ばれた少なくとも 1種以上を主成分とする薄膜 を形成した薄膜基板の製造方法であって、 該薄膜がガリウム、 インジウム、 アルミニウムのう ちから選ばれた少なくとも 1種以上の成分を含む有機化合物を主原料としアンモニア、 窒素、 水素のうちから選ばれた少なくとも 1種以上を反応ガスとして形成されるものであることを特 徴とする薄膜基板の製造方法、 である。
また本発明は、 舰過性を有するセラミック材料を主成分とする焼結体に窒化ガリウム、 窒 化インジウム、 窒化アルミニウムのうちから選ばれた少なくとも 1種以上を主成分とする薄膜 を形成した薄膜基板の製造方法であって、 該薄膜がガリウム、 インジウム、 ァリレミニゥムのう ちから選ばれた少なくとも 1種以上の成分を含む八ロゲン化物を ¾ϋ料としアンモニア、窒素、 水素のうちから選ばれた少なくとも 1種以上を反応ガスとして形成されるものであることを特 徴とする薄膜基板の製造方法、 である。
また本発明は、 窒化ガリウム、 窒化インジウム、 窒化アルミニウムのうちから選ばれた少な くとも 1種以上を主成分としさらにニオブ及びタンタルのうちから選ばれた少なくとも 1種以 上の成分を含むことを特徴とする光導波路、 である。
また本発明は、 窒化ガリウム、 窒化インジウム、 窒化アルミニウムのうちから選ばれた少な くとも 1種以上を主成分とする薄膜からなる少なくとも Ν型半導体層及び発光層及び Ρ型半導 体層を含む積層体により構成される発光軒であって、 該 Ν型半 ¾{本層及び発光層及び Ρ型半 導体層の積層体がセラミック材料を主成分とする焼結体に形成されていることを特徴とする発 光素子、 である。
また本発明は、 窒化ガリウム、 窒化インジウム、 窒化アルミニウムのうちから選ばれた少な くとも 1種以上を主成分とする薄膜からなる少なくとも Ν型半 本層及び発光層及び Ρ型半導 体層を含む積層体により構成される発光素子であって、 該 Ν型半 本層及び発光層及び Ρ型半 導体層の積層体が ¾¾i性を有するセラミック材料を主成分とする焼結体に形成されているこ とを特徴とする発光素子、 である。
また本発明は、 窒化ガリウム、 窒化インジウム、 窒化アルミニウムのうちから選ばれた少な くとも 1種以上を主成分とする薄膜からなる少なくとも N型半 ¾#:層及び発光層及び P型半導 体層を含む積層体により構成される発光軒であって、 該 N型半導体層及び発光層及び P型半 導体層の積層体が表面粗さの大きいセラミック材料を主成分とする焼結体に形成されているこ とを特徴とする発光素子、 である。
また本発明は、 窒化ガリウム、 窒化インジウム、 窒化アルミニウムのうちから選ばれた少な くとも 1種以上を主成分とする薄膜からなる少なくとも N型半 本層及び発光層及び P型半導 体層を含む積層体により構成される発光素子であって、 該 N型半導体層及び発光層及び P型半 導体層の積層体が窒化ガリウム、 窒化インジウム、 窒化アルミニウムのうちから選ばれた少な くとも 1種以上を主成分とする薄膜が形成されたセラミック材料を主成分とする焼結体に形成 されていることを特徴とする発光素子、 である。
また本発明は、 窒化ガリウム、 窒化インジウム、 窒化アルミニウムのうちから選ばれた少な くとも 1種以上を主成分とする薄膜からなる少なくとも N型半導体層及び発光層及び P型半導 体層を含む積層体により構成される発光軒であって、 該 N型半導体層及び発光層及び P型半 導体層の積層体が窒化ガリウム、 窒化インジウム、 窒化アルミニウムのうちから選ばれた少な くとも 1種以上を主成分とする単結晶薄膜が形成されたセラミック材料を主成分とする焼結体
に形成されていることを特徴とする発光素子、 である。
また本発明は、 上記発光素子に用いられるセラミック材料を主成分とする焼結体が窒化アル ミニゥムを主成分とする焼結体であることを特徴とする発光素子、 である。
また本発明は、 上記発光素子に用いられるセラミック材料を主成分とする焼結体が六方晶系 又は三方晶系のうちから選ばれた少なくともいずれかの結晶構造を有する材料を主成分とする 焼結体であることを特徴とする発光素子、 である。
また本発明は、 上記発光素子に用いられる六方晶系又 方晶系のうちから選ばれた少なく ともいずれかの結晶構造を有する材料を主成分とする焼結体であり該六方晶系又は三方晶系の うちから選ばれた少なくともいずれかの結晶構造を有する材料を主成分とする焼結体力雙化亜 鉛、 酸化ベリリウム、 酸化アルミニウム、 炭化珪素、 窒化珪素、 窒化ガリウムのうちから選ば れた少なくとも 1種以上を主成分とする焼結体であることを特徴とする発光素子、 である。 また本発明は、 上記発光素子に用いられるセラミック材料を主成分とする焼結体が 化ジル コニゥム、 酸化マグネシウム、 アルミン酸マグネシウム、 酸化チタン、 チタン酸バリウム、 チ タン酸ジルコン酸鉛、 希土観素酸化物、 酸化トリウム、 各種フェライト、 ムライト、 フオル ステライト、 ステアタイト、 結晶ィ匕ガラスのうちから選ばれた少なくとも 1種以上を主成分と する焼結体であることを特徴とする発光素子、 である。
上記本発明について項 1〜項 1 7 2 7において詳細を説明した。 図面の簡単な説明
図 1は、 本発明による薄膜形成用基板及びその上に形成された単結晶薄膜の結晶方位を示す 図である。
図 2は、 本発明による薄膜形成用基板上に形成された単結晶薄膜による X線回折を示す図で める。
図 3は、 本発明による導通ビアを有する薄膜形成用基板の 1例を示す ^見図である。
図 4は、 本発明による薄膜形成用基概びその上に形成された単結晶薄膜の結晶方位を示す 図である。
図 5は、 本発明による薄膜形成用基板及び 膜基板の 1例を示す 図である。
図 6は、 本発明による薄膜基板の 1例を示す斜視図である。
図 7は、 本発明による導通ビア有する薄膜形成用基板及ぴ 膜基板の 1例を示す 見図であ る。
図 8は、 本発明による導通ビア有する薄膜基板の 1例を示す 図である。
図 9は、 本発明による窒化アルミニウム焼結体の;) 過率を示す図である。
図 1 0は、 本発明による薄廳電性材料が形成された薄膜形成用基板の 1例を示す 見図で ある。
図 1 1は、 本発明による薄膜導電性材料が形成された薄膜形成用基板の 1例を示す斜視図で める。
図 1 2は、 本発明による薄 電性材料が形成された導通ビアを有する薄膜形成用基板の 1 例を示す斜視図である。
図 1 3は、 本発明によるパターン形状の薄 電性材料が形成された薄膜形成用基板の 1例 を示す斜視図である。
図 1 4は、 本発明による薄膜導電性材料の上に窒化ガリウム、 窒化インジウム、 窒化アルミ ニゥムのうちから選ばれた少なくとも 1種以上を主成分とする薄膜が形成された薄膜基板の 1 例を示す斜視図である。
図 1 5は、 本発明による薄膜導電性材料及び窒化ガリウム、 窒化インジウム、 窒化アルミ二
ゥムのうちから選ばれた少なくとも 1種以上を主成分とする薄膜がそれぞれ異なる面に形成さ れた薄膜基板の 1例を示す斜視図である。
図 1 6は、 本発明による薄麟電性材料の上に窒化ガリウム、 窒化インジウム、 窒化アルミ ニゥムのうちから選ばれた少なくとも 1種以上を主成分とする薄膜が形成されさらに異なる面 に薄膜導電性材料が形成された薄膜基板の 1例を示す斜視図である。
図 1 7は、 本発明による窒化ガリウム、 窒化インジウム、 窒化アルミニウムのうちから選ば れた少なくとも 1種以上を主成分とする薄膜の上に薄]^電性材料が形成された薄膜基板の 1 例を示す斜視図である。
図 1 8は、 本発明によるあらかじめ薄麟電性材料が形成された窒化アルミニウムを主成分 とする焼結体に窒化ガリウム、 窒化インジウム、 窒化アルミニウムのうちから選ばれた少なく とも 1種以上を主成分とする薄膜が形成されその上にさらに薄 電性材料が形成された薄膜 基板の 1例を示す斜視図である。
図 1 9は、 本発明によるあらかじめ薄 J ^電性材料が形成された導通ビアを有する窒化アル ミニゥムを主成分とする焼結体に窒化ガリウム、 窒化インジウム、 窒化アルミニウムのうちか ら選ばれた少なくとも 1種以上を主成分とする薄膜が形成されさらに薄膜の表面に薄]^電性 材料が形成された薄膜基板の 1例を示す斜視図である。
図 2 0は、 本発明によるあらかじめ薄膜導電性材料が形成された窒化アルミニウムを主成分 とする焼結体にさらに窒化ガリゥム、 窒化ィンジゥム、 窒化アルミニゥムのうちから選ばれた 少なくとも 1種以上を主成分とする薄膜が形成されさらに薄膜の表面に薄膜導電性材料が形成 された薄膜基板の 1例を示す斜視図である。
図 2 1は、 本発明による窒化アルミニウムを主成分とする焼結体に窒化ガリウム、 窒化イン ジゥム、 窒化アルミニウムのうちから選ばれた少なくとも 1種以上を主成分とする薄膜により 二次元光導波路が形成されている薄膜基板の 1例を示す斜視図である。
図 2 2は、 本発明による二^ 5光導波路の上にクラッド層が形成され薄膜基板の 1例を示す 余ί見図である。
図 2 3は、 本発明による二次元光導波路が形成されている薄膜基板の 1例を示す斜視図であ る。
図 2 4は、 本発明による三次元光導波路が形成されている薄膜基板の 1例を示す斜視図であ る。
図 2 5は、 本発明による三次元光導波路が形成されている薄膜基板の 1例を示す斜視図であ る。
図 2 6は、 本発明によるリッジ型のミ^光導波路が形成されている薄膜基板の 1例を示す 斜視図である。
図 2 7は、 本発明による二次元光導波路に誘電体材料を形成することで二次元光導波路中に 三次元光導波路を形成した薄膜基板の 1例を示す斜視図である。
図 2 8は、 本発明による二次元光導波路に金属材料を直接形成することで二次元光導波路中 に Ξ次元光導波路を形成した薄膜基板の 1例を示す斜視図である。
図 2 9は、 本発明による二次元光導波路にバッファ層を介して電極を形成し該電極間に電位 を印加することで三次元光導波路を形成した薄膜基板の 1例を示す 見図である。
図 3 0は、 本発明による窒化ガリウム、 窒化インジウム、 窒化アルミニウムのうちから選ば れた少なくとも 1種以上を主成分とする薄膜に埋め込み型の三次元光導波路が形成されている 薄膜基板の 1例を示す斜視図である。
図 3 1は、 本発明による埋め込み型の三:^光導波路が形成されさらに電極が形成されてい る薄膜基板の 1例を示す斜視図である。
図 3 2は、 本発明による埋め込み型の三^光導波路が形成されさらに電極が形成されてい る薄膜基板の 1例を示す斜視図である。
図 3 3は、 本発明による埋め込み型の三次元光導波路が形成されさらに電極が形成されてい る薄膜基板の 1例を示す斜視図である。
図 3 4は、 本発明による三;^光導波路が形成されさらに電気回路が形成されている薄膜基 板の 1例を示す斜視図である。
図 3 5は、 本発明による埋め込み型の三次元光導波路が形成されさらに電気回路が形成され ている薄膜基板の 1例を示す斜視図である。
図 3 6は、 本発明による薄膜形成用基板の 1例を示す斜視図である。
図 3 7は、 本発明による薄膜導電性材料の上に窒化ガリウム、 窒化インジウム、 窒化アルミ ニゥムのうちから選ばれた少なくとも 1種以上を主成分とする薄膜が形成された薄膜基板の 1 例を示す斜視図である。
図 3 8は、 本発明による薄 電性材料の上に窒化ガリウム、 窒化インジウム、 窒化アルミ ニゥムのうちから選ばれた少なくとも 1種以上を主成分とする薄膜が形成された導通ビアを有 する薄膜基板の 1例を示す斜視図である。
図 3 9は、 発光素子の構成の 1例を示す断面図である。
図 4 0は、 からの基板を用いた発光素子の 1例を示す断面図である。
図 4 1は、 舰からの基板を用いた発光素子の 1例を示す断面図である。
図 4 2は、 本発明による発光素子の 1例を示す断面図である。
図 4 3は、 本発明による発光素子の 1例を示す断面図である。
図 4 4は、 本発明による発光素子の 1例を示す断面図である。
図 4 5は、 本発明による発光素子の 1例を示す斜視図である。
図 4 6は、 本発明による発光素子の 1例を示す斜視図である。
図 4 7は、 本発明による発光素子の 1例を示す断面図である。
図 4 8は、 本発明による発光素子の 1例を示す断面図である。
図 4 9は、 本発明による発光素子の 1例を示す断面図である。
図 5 0は、 本発明による発光素子の 1例を示す断面図である。
図 5 1は、 本発明による発光素子の 1例を示す断面図である。
図 5 2は、 本発明による発光素子の 1例を示す断面図である。
図 5 3は、 本発明による発光素子の 1例を示す断面図である。
図 5 4は、 本発明による発光素子の 1例を示す断面図である。
図 5 5は、 本発明による発光素子の 1例を示す断面図である。
図 5 6は、 本発明による発光素子の 1例を示す断面図である。
図 5 7は、 本発明による発光素子の 1例を示す断面図である。
図 5 8は、 本発明による発光素子の 1例を示す断面図である。
図 5 9は、 本発明による発光素子の発光の様子を推測した 1例を示す断面図である。
図 6 0は、 本発明による発光素子の発光の様子を推測した 1例を示す斜視図である。
図 6 1は、 本発明による発光素子の 1例を示す斜視図である。
図 6 2は、 A 1 N薄膜の結晶状態が無定形である場合の X線回折図形の 1例を示す図である。 図 6 3は、 A 1 N薄膜の結晶状態が多結晶である場合の X線回折図形の 1例を示す図である。 図 6 4は、 A 1 N薄膜の結晶状態が基板面に対して C軸が垂直な方向に形成された配向性多 結晶である場合の X線回折図形の 1例を示す図である。
図 6 5は、 A 1 N薄膜の結晶状態が基板面に対して C軸が垂直な方向に形成された単結晶で ある場合の X線回折図形の 1例を示す図である。
図 6 6は、 基板面に対して C軸が垂直な方向に形成された A 1 N単結晶薄膜の ωスキャンに よって計測されたミラー指数 (0 0 2 ) の格子面の X線回折線ロッキングカーブの 1例を示す 図形である。
図 6 7は、 G a Ν薄膜の結晶状態が基板面に対して C軸が垂直な方向に形成された単結晶で ある場合の X線回折図形の 1例を示す図である。
図 6 8は、 I nN薄膜の結晶状態が基板面に対して C軸が垂直な方向に形成された単結晶で ある場合の X線回折図形の 1例を示す図である。
図 6 9は、 本発明による薄膜導電性材料の 1例を示す正面図である。
図 7 0は、 本発明による薄膜導電性材料の 1例を示す正面図である。
図 7 1は、 比較的不規則な凹凸表面を有するセラミック材料を主成分とする焼結体の表面状 態の 1例を示す模式図である。
図 7 2は、 規則的な凹凸表面を有するセラミック材料を主成分とする焼結体の表面状態の 1 例を示す斜視図である。
図 7 3は、 規則的な凹凸表面を有するセラミック材料を主成分とする焼結体の表面状態の 1 例を示す斜視図である。 発明を実施するための最良の形態
本発明の意義と目的は、 窒化ガリウム、 窒化インジウム、 窒化アルミニウムのうちから選ば れた少なくとも 1種以上を主成分とする結晶性に優れた薄膜状の単結晶とセラミック材料を主 成分とする焼結体とを一体化することで単結晶及びセラミツク材料を主成分とする焼結体それ ぞ满虫ではなし得なレ、相乗効果を引き出し、 «からのサフアイァゃ炭化珪素などの塊状や パルク状などそれ自体独立で単結晶として存在し使用される材料では実現が困難であった優れ た機能を有する基板及び該基板を用いた発光素子などの電子素子、 あるいは回路基板などの電 子部品を提供することにある。 またこのような効果をもたらすセラミック材料を主成分とする 焼結体を提供することにある。
本発明は大きく見ればセラミツク材料を主成分とする焼結体を用いた薄膜基 び該基板を 用いた電子軒に関するものであるがより詳しく見れば、 1 .窒化ガリウム、窒化インジウム、 窒化アルミニウムを主成分とする単結晶薄膜を形成するための基板、 2. 上記単結晶薄膜形成 用基板の材料、 3. 窒化ガリウム、 窒化インジウム、 窒化アルミニウムを主成分とする単結晶 薄膜が形成された薄膜基板、 4. 窒化ガリウム、 窒化インジウム、 窒化アルミニウムを主成分 とする単結晶薄膜により構成される光導波路、 5. 窒化ガリウム、 窒化インジウム、 窒化アル ミ二ゥムを主成分とする単結晶薄膜により構成される発光素子、 に関するものであり基板の材 料として窒化アルミニウムを主成分とする焼結体など各種セラミック材料を主成分とする焼結 体を用いた点に特徴がある。
さらに本発明は、 6. 窒化ガリウム、 窒化インジウム、 窒化アルミニウムを主成分とする薄 膜を形成するための基板、 7. 上記薄麵成用基板の材料、 8. 窒化ガリウム、 窒化インジゥ ム、 窒化アルミニウムを主成分とする薄膜が形成された薄膜基板、 9. 窒化ガリウム、 窒化ィ ンジゥム、 窒化アルミニウムを主成分とする薄膜により構成される光導波路、 1 0. 窒化ガリ ゥム、 窒化インジウム、 窒化アルミニウムを主成分とする薄膜により構成される発光軒、 に 関するものであり基板の材料として窒化アルミニウムを主成分とする焼結体など光 ¾ 性を有 するセラミック材料を主成分とする焼結体を用いた点に特徴がある。
すなわち、 上記 1 . 〜1 0. に関する発明は窒化アルミニウムを主成分とする焼結体など各 種セラミック材料を主成分とする焼結体に窒化ガリウム、 窒化インジウム、 窒化アルミニウム を主成分とする結晶性に優れた単結晶薄膜が形成できるという現象を見出すことによって実現
され、 さらに窒化アルミニウムを主成分とする焼結体など各種セラミック材料を主成分とする 焼結体に窒化ガリウム、 窒化インジウム、 窒化アルミニウムを主成分とする結晶性に優れた単 結晶薄膜を形成していく検討の過程で新たに見出された現象に基づいて されたものである。 以下、 上記 1. 〜: L 0. に示された本発明について詳細に説明していく。
本発明に関する図面は上記のように図 1〜図 7 3で示されている。 図 1〜図 7 3において用 いられている符号 (参照番号) の内容は以下に示される通りである。
すなわち、
1 :窒化アルミニウムを主成分とする焼結体からなる基板
2 :窒化ガリウム、 窒化インジウム、 窒化アルミニウムのうちから選ばれた少なくとも 1種 以上を主成分とする単結晶薄膜
3 :導通ビア
4:窒化アルミニウムを主成分とする焼結体、 及び炭化珪素、 窒化珪素、 窒化ガリウム、 酸 化亜鉛、 酸化ベリリウムなどの六方晶結晶系及び酸化アルミニウムなどの三方晶結晶系あるい は六方晶系として分類できる結晶構造を有する各種セラミック材料を主成分とする焼結体、 及 びその他各種セラミツク材料を主成分とする焼結体からなる基板
5 :窒化ガリゥム、 窒化ィンジゥム、 窒化アルミニゥムのうちから選ばれた少なくとも 1種 以上を主成分とする薄膜
6 :薄膜基板
7 :導通ピアを有する薄膜基板
8 :窒化ガリウム、 窒化インジウム、 窒化アルミニウムのうちから選ばれた少なくとも 1種 以上を主成分とする薄膜
9 :導通ビアを有する窒化アルミニウムを主成分とする焼結体、 及び炭化珪素、 窒化珪素、 窒化ガリウム、 酸化菌、 謝匕ベリリウムなどの六方晶結晶系及び酸ィ匕アルミニウムなどの三 方晶結晶系あるいは六方晶系として分類できる結晶構造を有する各種セラミック材料を主成分 とする焼結体、 及びその他各種セラミック材料を主成分とする焼結体からなる基板
1 0:導通ビアを有する窒化アルミニウムを主成分とする焼結体からなる基板
1 2:回路パターン形状の薄膜導電性材料
1 3:窒化アルミニウムを主成分とする焼結体からなる基板
1 4:窒化アルミニウムを主成分とする焼結体からなる基板
1 5 :薄膜導電性材料が形成された薄膜基板
1 6:薄膜導電性材料が形成された導通ビアを有する薄膜基板
1 7 :薄膜導電性材料が形成された導通ビアを有する薄膜基板
1 8:薄膜導電性材料が形成された薄膜基板
1 9:薄膜導電性材料が形成された薄膜基板
2 0:薄膜導電性材料が形成された導通ビアを有する薄膜基板
2 1 :薄麟電性材料が形成された薄膜基板
2 4:薄膜導電性材料に形成された空間
3 0:発光素子作製用基板
3 1 :バッファ層
3 2:発光素子
3 2 - 1 :薄膜
3 2 - 2:窒化ガリウム、 窒化インジウム、 窒化アルミニウムのうちから選ばれた少なくと も 1種以上を主成分とする薄膜
33:魏からの発光素子作製用基板
34:窒化ガリウム、 窒化インジウム、 窒化アルミニウムのうちから選ばれた少なくとも 1 種以上を主成分とする N型半導体特性又は P型半導体特性を有する薄膜層
34-1 :窒化ガリウム、 窒化インジウム、 窒化アルミニウムのうちから選ばれた少なくと も 1種以上を主成分とする N型半導体特性又は P型半導体特性を有する薄膜層
34-1-1 :窒化ガリウム、 窒化インジウム、 窒化アルミニウムのうちから選ばれた少な くとも 1種以上を主成分とする N型半導体特性又は P型半導体特性を有する薄膜層
34-1-2 :窒化ガリゥム、 窒化ィンジゥム、 窒化アルミニウムのうちから選ばれた少な くとも 1種以上を主成分とする N型半導体特性又は P型半導体特性を有する薄膜層
34-2:窒化ガリウム、 窒化インジウム、 窒化アルミニウムのうちから選ばれた少なくと も 1種以上を主成分とする N型半導体特性又は P型半導体特性を有する薄膜層
34-2-1 :窒化ガリゥム、 窒化ィンジゥム、 窒化アルミニウムのうちから選ばれた少な くとも 1種以上を主成分とする N型半導体特性又は P型半導体特性を有する薄膜層
34- 2-2 :窒化ガリゥム、 窒化ィンジゥム、 窒化アルミニウムのうちから選ばれた少な くとも 1種以上を主成分とする N型半導体特性又は P型半導体特性を有する薄膜層
35:窒化ガリウム、 窒化インジウム、 窒化アルミニウムのうちから選ばれた少なくとも 1 種以上を主成分とする P型半導体特性又は N型半導体特性を有する薄膜層
35—1 :窒化ガリウム、 窒化インジウム、 窒化アルミニウムのうちから選ばれた少なくと も 1種以上を主成分とする N型半導体特性又は P型半導体特性を有する薄膜層
35— 1—1 :窒化ガリウム、 窒化インジウム、 窒化アルミニウムのうちから選ばれた少な くとも 1種以上を主成分とする N型半導体特性又は P型半導体特性を有する薄膜層
35-1-2 :窒化ガリウム、 窒化インジウム、 窒化アルミニウムのうちから選ばれた少な くとも 1種以上を主成分とする N型半導体特性又は P型半導体特性を有する薄膜層
35— 2:窒化ガリウム、 窒化インジウム、 窒化アルミニウムのうちから選ばれた少なくと も 1種以上を主成分とする N型半導体特性又は P型半導体特性を有する薄膜層
35-2-1 :窒化ガリウム、 窒化インジウム、 窒化アルミニウムのうちから選ばれた少な くとも 1種以上を主成分とする N型半導体特性又は P型半導体特性を有する薄膜層
35-2-2:窒化ガリウム、 窒化インジウム、 窒化アルミニウムのうちから選ばれた少な くとも 1種以上を主成分とする N型半導体特性又は P型半導体特性を有する薄膜層
36 :発光層
37 : «からの基板を用いた発光素子
38 :電極
38-1 :電力供給用
39:本発明による発光素子
40 :誘電体材料
50 :二次元光導波路
60 :三;^光導波路
61 :リッジ型三^ 5光導波路
62 :三次元光導波路
63 :三 ^光導波路
64:三 光導波路
65 :埋め込み型三次元光導波路
65' :光導波路の光導入部
66 :光導波路への導入光
6 6 ':光導波路からの放出光
7 0:クラッド層
7 1 :クラッド層
8 0:窒化ガリウム、 窒化インジウム、 窒化アルミニウムのうちから選ばれた少なくとも 1 種以上を主成分とする薄膜
9 0:電極
9 1 :電極
1 0 0 :金属材料
1 1 0:バッファ層
1 2 0 :電極
1 3 0:導電性を有するセラミック材料を主成分とする攝吉体からなる基板
1 4 0:発光層から発せられた光
1 4 1 :基板を ¾iiして発光 外部へ放出された光
1 4 2:薄 KBから 素子外部へ放出された光
1 4 3:発光層から発光素子外部へ放出された光
1 5 0:基板と薄 lとの界面
1 6 0:基板と外部空間との界面
1 7 0
1 7 1
である。 上記のように本発明において薄歸細基板は、 セラミック材料を主成分とする 体及び光 ¾i性を有するセラミック材料を主成分とする能結体からなるが、 さらに 1 ) 窒化ガリウム、 窒化インジウム、 窒化アルミニウムのうちから選ばれた少なくとも 1種以上を主成分とする薄 膜が形成されたセラミック材料を主成分とする ¾結体、 2) 窒化ガリウム、 窒化インジウム、 窒化アルミニウムのうちから選ばれた少なくとも 1種以上を主成分とする薄膜が形成された光 ¾ 生を^ Tるセラミック材料を主成分とする 結体、 が含まれる。 より具体的に言えば、 3) 窒化アルミニウムを主成分とする撫吉体をそのまま基板として用いたもの、 4) 晶系又は 三方晶系の結晶構造を有するセラミック材料を主成分とする焼結体をそのまま基板として用い たもの、 だけではなく 5) 窒化アルミニウムを主成分とする 結体からなる基板に窒化ガリウ ム、 窒化インジウム、 窒化アルミニウムのうちから選ばれた少なくとも 1種以上を主成分とす る薄膜が形成されたものをさらに薄藤删基板として用いたもの、 あるいは 6) 六方晶系又 方晶系の結晶猶を有するセラミック材料を主成分とする焼結体からなる基板に窒化ガリ ゥム、 窒化インジウム、 窒化アルミニウムのうちから選ばれた少なくとも 1種以上を主成分と する薄膜が形成されたものをさらに薄] 基板として用いたもの、 その他にも 7) 例えば 酸化ジルコニウム、 酸化マグネシウム、 アルミン酸マグネシウム、 酸化チタン、 チタン酸パリ ゥム、 チタン酸ジルコン麟、 酸化イットリウムなどの希土観素酸化物、 酸化トリウム、 各 種フェライト、 ムライト、 フオルステライト、 ステアタイト、 結晶化ガラス、 などの各種セラ ミック材料を主成分とする能結体をそのまま薄 ,成用基板として用いたもの、 また 8 ) 例え ば谢匕ジルコニウム、 酸化マグネシウム、 アルミン酸マグネシウム、 酸化チタン、 チタン酸バ リウム、 チタン酸ジルコン麟、 酸化イットリウムなどの希土 素酸化物、 酸化トリウム、 各種フェライト、 ムライト、 フォルステライト、 ステア夕イト、 結晶化ガラス、 などの各種セ ラミック材料を主成分とする焼結体に窒化ガリウム、 窒化インジウム、 窒化アルミニウムのう
ちから選ばれた少なくとも 1種以上を主成分とする薄膜が形成されたものをさらに薄膜形成用 基板として用いたもの、 なども含まれる。
本発明による薄膜形成用基板は上記のように、 窒化ガリウム、 窒化インジウム、 窒化アルミ ニゥムのうちから選ばれた少なくとも 1種以上を主成分とする単結晶薄膜を形成するための基 板であって、該基板がセラミック材料を主成分とする焼結体からなるもの、及び窒化ガリウム、 窒化インジウム、 窒化アルミニウムのうちから選ばれた少なくとも 1種以上を主成分とする簿 膜を形成するための基板であって、 該基板が 性を有するセラミック材料を主成分とする 焼結体からなるもの、 である。 そのうちセラミック材料を主成分とする焼結体からなる薄膜形 成用基板は窒化ガリウム、 窒化インジウム、 窒化アルミニウムのうちから選ばれた少なくとも
1種以上を主成分とする単結晶薄膜が形成されるものであるが、 該セラミツク材料を主成分と する焼結体からなる薄膜形成用基板には単結晶の他に無定形、 多結晶、 配向性多結晶のうちか ら選ばれた少なくともいずれかの結晶状態を有するものも形成し得る。
上記本発明による薄膜基板は、 セラミック材料を主成分とする焼結体に窒化ガリウム、 窒化 ィンジゥム、 窒化アルミニウムのうちから選ばれた少なくとも 1種以上を主成分とする単結晶 薄膜が形成されていることを特徴とするもの、 及び)1 ffi 性を有するセラミック材料を主成分 とする焼結体に窒化ガリウム、 窒化インジウム、 窒化アルミニウムのうちから選ばれた少なく とも 1種以上を主成分とする薄膜が形成されていることを特徴とするものであるがより具体的 に言えば、 1 ) 窒化アルミニウムを主成分とする焼結体に窒化ガリウム、 窒化インジウム、 窒 化アルミニウムのうちから選ばれた少なくとも 1種以上を主成分とする単結晶薄膜が形成され たもの、 あるいは 2) 六方晶系又は三方晶系の結晶構造を有するセラミック材料を主成分とす る焼結体に窒化ガリウム、 窒化インジウム、 窒化アルミニウムのうちから選ばれた少なくとも 1種以上を主成分とする単結晶薄膜が形成されたもの、その他に 3)例えば谢ヒジルコニウム、 酸化マグネシウム、 アルミン酸マグネシウム、 酸化チタン、 チタン酸バリウム、 チタン酸ジル コン «、 酸化イットリウムなどの希土 1 5素酸化物、 酸ィ匕トリウム、 各種フェライト、 ムラ イト、 フォルステライト、 ステア夕イト、 結晶化ガラス、 など各種セラミック材料を主成分と する焼結体に窒化ガリゥム、 窒化ィンジゥム、 窒化アルミニゥムのうちから選ばれた少なくと も 1種以上を主成分とする単結晶薄膜が形成されたもの、 4) 性を有する窒化アルミ二 ゥムを主成分とする焼結体に窒化ガリウム、 窒化インジウム、 窒化アルミニウムのうちから選 ばれた少なくとも 1種以上を主成分とする薄膜が形成されたもの、 あるいは 5) 光 ¾M性を有 する六方晶系又は三方晶系の結晶構造を有するセラミック材料を主成分とする焼結体に窒化ガ リウム、 窒化インジウム、 窒化アルミニウムのうちから選ばれた少なくとも 1種以上を主成分 とする薄膜が形成されたもの、 その他にも 6 ) 例えば 化ジルコニウム、 酸化マグネシウム、 アルミン酸マグネシウム、 酸化チタン、 チタン酸バリウム、 チタン酸ジルコン酸鉛、 酸化イツ トリウムなどの希土類 素酸化物、 酸ィ匕トリウム、 各種フェライト、 ムライト、 フォルステラ イト、 ステアタイト、 結晶化ガラス、 などを主成分とする光透過性を有する焼結体に窒化ガリ ゥム、 窒化インジウム、 窒化アルミニウムのうちから選ばれた少なくとも 1種以上を主成分と する薄膜が形成されていることを特徴とする薄膜基板を含む。
上記窒化アルミニウムを主成分とする焼結体、 あるいは六方晶系又は三方晶系の結晶構造を 有するセラミック材料を主成分とする焼結体、あるいは酸化ジルコニウム、酸化マグネシウム、 アルミン酸マグネシウム、 酸ィ匕チタン、 チタン酸バリウム、 チタン酸ジルコン酸鉛、 酸化イツ トリウムなどの希土類 素酸化物、 酸ィ匕トリウム、 各種フェライト、 ムライト、 フォルステラ イト、 ステアタイト、 結晶化ガラス、 などのセラミック材料を主成分とする焼結体に形成され ている窒化ガリウム、 窒化インジウム、 窒化アルミニウムのうちから選ばれた少なくとも 1種 以上を主成分とする薄膜は通常単結晶であるが、 その他にも無定形、 多結晶、 配向性多結晶の
うちから選ばれた少なくともいずれかの結晶状態のものも形成し得る。 また、 上記薄膜は単一 層だけでなく例えば単結晶、 無定形、 多結晶、 配向性多結晶のうちから選ばれた少なくともい ずれかの結晶状態のものもあらかじめセラミック材料を主成分とする焼結体に形成しさらにそ の上に単結晶薄膜を形成するといつた 2以上の層からなる薄膜も用いることができる。 通常単 結晶、 無定形、 多結晶、 配向性多結晶のうちから選ばれた少なくともいずれかの結晶状態のも のもあらかじめ形成しさらにその上に形成した単結晶薄膜の結晶性はセラミック材料を主成分 とする焼結体に直接形成したものより向上し易いので好ましい。
本発明において、 上記薄膜基板を窒化ガリウム、 窒化インジウム、 窒化アルミニウムのうち から選ばれた少なくとも 1種以上を主成分とする薄膜を形成するための薄膜形成用基板として 用いることができる。
なお、 上記セラミック材料を主成分とする焼結体として用いる結晶化ガラスとは例えば硼珪 酸ガラス (通常 S i 02及び B 2〇3を主成分とし、 その他に A 1 203、 C a O、 B a O、 P b O などの成分を含む) などのガラス母体 (ガラスマトリックス) 中にコ一ジエライト、 ァノール サイト (灰長石)、 コランダム (A 1 2〇3)、 ムライト ( 3 A 1 203 · 2 S i〇2)、 ウォラス卜 ナイト (C a O · S i〇2)、 マグネシウム (Mg O · S i 02) などの結晶成分が存在して いる構造を有しているものである。 結晶化ガラスは通常ガラス粉末に ¾ϋアルミナ粉末、 シリ 力粉末、 マグネシア粉末、 炭酸カルシウム粉末、 炭酸バリウム粉末、 酸化硼鎌末、 酸化鉛粉 末などを加え、 さらに要すれば T i 02、 Z r〇2、 S n〇2、 Z n O、 L i 20などの成分を加 えて混合し、 一軸プレス法やシート成形法などで粉末成形体となし、 その後 «して上記粉末 成形体を焼き固める方法により作製される。 $¾iの際上記 T i〇2、 Z r 02、 S n〇2、 Z nO、 L i 20などの成分を適 Πえたものを焼成すれば結晶化が促進される場合が多い。その他に結 晶化ガラスは溶融して成形したガラス成形体を熱処理し、 該ガラス成形体中に結晶を析出させ る方法などによっても作製し得る。
本発明による薄 成用基板及び薄膜基板に用いるセラミック材料を主成分とする焼結体あ るいは光 性を有するセラミック材料を主成分とする 体における 「セラミック材料」 と は焼結体を構成する材料が無機材料を主成分とするものであることを意味する。 該無機材料は 通常金属元素及び半金属元素のうちから選ばれた少なくとも 1種以上の元素と非金属元素のう ちから選ばれた少なくとも 1種以上の元素との組成物あるいは化合物、 あるいは金属元素のう ちから選ばれた少なくとも 1種以上の元素と半金属元素のうちから選ばれた少なくとも 1種以 上の元素との組成物あるいは化合物、 あるいは半金属元素のうちから選ばれた少なくともいず れか 2種以上の元素との組成物あるいは化合物を主成分とするものからなる。 上記非金属元素 としては通常窒素、 りん、 酸素、 硫黄、 ハロゲン元素 (フッ素、 纏、 臭素、 沃素、 ァス夕チ ン) などが好適に用いられる。 半金属元素として ¾®常ほう素、 炭素、 珪素、 ゲルマニウム、 ヒ素、 アンチモン、 ビスマス、 セレン、 テルル、 ポロニウムなどが好適に用いられる。 上記セ ラミック材料は通常無機化合物を主成分とするものであり、 これらのセラミック材料は結晶質 のものであってもよいしあるいは例えばガラスなどの非晶質状態のものであってもよいしある いは結晶質のものと非晶質のものとが混在したものであってもよい。 上記セラミック材料は通 常窒化物、 炭化物、 酸化物、 硼化物、 珪化物などの化合物あるいは組成物を主成分とするもの である。 これらの化合物あるいは組成物をより具体的に示せば例えば窒化アルミニウム、 六方 晶系又は三方晶系のうちから選ばれた少なくともいずれかの結晶構造を有する化合物 (例えば 炭化珪素、 窒化珪素、 窒化ガリウム、 酸化亜鉛、 酸化ベリリウム、 酸化アルミニウムなど)、 酸 化ジルコニウム、 酸化マグネシウム、 アルミン酸マグネシウム、 酸化チタン、 チタン酸バリウ ム、 チタン酸ジルコン酸鉛、 酸化イットリウムなどの希土讓匕物、 酸化トリウム、 各種フエ ライト、 ムライト、 フオルステライ卜、 ステアタイト、 結晶化ガラス、 などである。
なお、本発明において上記セラミック材料としては主成分である無機材料以外に金属、合金、 金属間化合物、 有機物質、 有機化合物、 有機樹脂、 その他に例えばハロゲン元素あるいはカル コゲン元素などの非金属などを含有するもの含まれる。
本発明において、 上記セラミック材料を主成分とする焼結体は光 ¾i性を有するものが好ま しく、 該セラミック材料を主成分とする焼結体に形成される窒化ガリウム、 窒化インジウム、 窒化アルミニウムのうちから選ばれた少なくとも 1種以上を主成分とする単結晶薄膜の結晶性 が向上し易くなるので好ましい。
上記で示した本発明による薄膜形成用基板及び 膜基板はその上に窒化ガリゥム、 窒化ィン ジゥム、 窒化アルミニウムのうちから選ばれた少なくとも 1種以上を主成分とするェピタキシ ャル成長した薄膜を形成して発光素子を作製するための基板として用いることができる。 また それ以外にも上記ェピタキシャル成長した薄膜をフィールドエミッション材料として作製する ための基板としても用いられる。 上記薄膜基板はその上にさらに薄膜や単結晶薄膜を形成せず もともと形成されている薄膜を iiStoェして光導波路や表面弾性波素子用などの圧電膜ゃ電気 回路基 の, «膜や誘電膜などにも用い得る。
本発明による窒化ガリウム、 窒化インジウム、 窒化アルミニウムのうちから選ばれた少なく とも 1種以上を主成分とする単結晶薄膜を形成するための基板は窒化アルミニウムなどセラミ ック材料を主成分とする焼結体であってバルク状単結晶や配向性多結晶体ではない。 なおバル ク状単結晶とは基板など他の材料に形成された状態でしか単結晶として存在し得ないものでは なく自己だけの状態で単結晶として存在し得るものを意味する。 したがって大きさには関係な く薄い膜状や小さな粒状であっても仮に基板に形成されるなど他の材料と共存している状態の ものであっても自己だけの状態で存在し得るものであればパルク状単結晶である。 また、 配向 性多結晶とは構成材料の結晶が特定の結晶軸方位に向きかつそれ以外の結晶軸方位に対しては でたらめな方向を向いている多結晶であり、 ノルク状単結晶とは異なる。 また、 例えば焼結体 など構成材料の結晶がでたらめな結晶方位を向いている通常の多結晶とも異なる。
本発明による窒化ガリウム、 窒化インジウム、 窒化アルミニウムのうちから選ばれた少なく とも 1種以上を主成分とする薄膜を形成するための基板は焼結体であるため主成分の窒化アル ミニゥム結晶の方位はでたらめでありあらゆる結晶軸方位の窒化アルミ二ゥム微結晶粒子から なっている。 また、 本発明による薄膜形成用基板は上記窒化アルミニウム以外に例えば炭化珪 素、 窒化珪素、 窒化ガリウム、 酸化亜鉛、 酸化アルミニウム、 酸化ベリリウムなどの 71 ^晶系 又 ¾H方晶系の結晶構造を有するセラミック材料、 あるいはその他に例えば ¾化ジルコニウム、 酸化マグネシウム、 アルミン酸マグネシウム、 酸化チタン、 チタン酸バリウム、 チタン酸ジル コン,、 酸化イットリウムなどの希土^ 5素酸化物、 酸匕トリウム、 各種フェライト、 ムラ イト、 フォルステライト、 ステアタイト、 結晶化ガラス、 など各種セラミック材料を主成分と する焼結体であるためその結晶方位はでたらめでありあらゆる結晶軸方位の微結晶粒子からな つている。 したがって上記本発明による基板に単一波長の特性 X線を照射し X線回折を行うと バルク状単結晶や配向性多結晶であれば特定の結晶格子面からの回折線だけしか出現しないが 本発明による基板は消滅則によってもともとは出現し得ない回折線を除いてあらゆる回折線が 出現するので明らかに区別できる。 本発明による窒化アルミニウムを主成分とする焼結体、 あ るいは例えば炭化珪素、 窒化珪素、 窒化ガリウム、 酸化亜鉛、 酸化アルミニウム、 酸化べリリ ゥムなどの六方晶系又は三方晶系の結晶構造を有するセラミック材料、 あるいはその他に例え ば谶化ジリレコニゥム、 酸化マグネシウム、 アルミン酸マグネシウム、 酸化チタン、 チタン酸パ リウム、 チタン酸ジルコン酸鉛、 酸化イットリウムなどの希土 素酸化物、 酸化トリウム、 各種フェライト、 ムライト、 フォルステライト、 ステアタイト、 結晶化ガラス、 など各種セラ ミック材料を主成分とする焼結体は X線回折を行うと上記のような特性を示す多結晶体である
が、 このような焼結体は窒化アルミニウム、 あるいは例えば炭化珪素、 窒化珪素、 窒化ガリウ 酸化亜鉛、 酸化アルミニウム、 酸化ベリリウムなどの六方晶系又 方晶系の結晶構造を 有するセラミック材料、 あるいはその他に例えば 化ジルコニウム、 酸化マグネシウム、 アル ミン酸マグネシウム、 酸化チタン、 チタン酸バリウム、 チタン酸ジルコン酸鉛、 酸化イツトリ ゥムなどの希土^ ¾素酸化物、酸化トリウム、各種フェライト、ムライト、 フオルステライト、 ステアタイト、 結晶化ガラス、 など各種セラミック材料を主成分とする原料粉末とその他必要 に応じて焼結助剤や有機バインダーあるいは溶媒などとを混合しその後金型プレス、 ラバープ レス、 艇み成形、 シート成形、 などの方法で目的に応じた形状に成形し必要に応じて脱バイ ンダ一などの予備焼成を行い最後に高温焼成することにより製造され、 その結果原料粉末同士 が焼き固められて緻密化し微細な窒化アルミニウム結晶粒子、 あるいは例えば炭化珪素、 窒化 珪素、 窒化ガリウム、 酸化亜鉛、 酸化アルミニウム、 酸化ベリリウムなどの六方晶系又 方 晶系の結晶構造を有するセラミック材料の微細な結晶粒子、 あるいはその他に例えば酸化ジル コニゥム、 酸ィ匕マグネシウム、 アルミン酸マグネシウム、 酸化チタン、 チタン酸バリウム、 チ タン酸ジルコン薩、 酸化イットリウムなどの希土 素酸化物、 酸化トリウム、 各種フェラ イト、 ムライト、 フォルステライト、 ステアタイト、 結晶化ガラス、 など各種セラミック材料 の微細な結晶 ί子、 を主成分に構成された多結晶体となしたものである。
本発明による単結晶薄膜はセラミック材料を主成分とする焼結体からなる基板に形成され基 板と膜の状態で固着一体化したものであって 2次元的な面状の広がりを有しそれ自体単独では なく基板と一体化した状態で存在し機能を発現し得る点に特徴があり、 3 的な寸法を有し それ自体で独立して存在し機能を発現し得るパルク状単結晶とは異なる。
«から塊状やパルク状といった比較的大型で 3 の寸法で表わされ得る単結晶を例えば 昇華法などによつて基板上に成長させる場合^S板の組成や材質あるレ 堪板の内部 «ある いは表面状態などの影響をあまり受けずに比較的容易に結晶性に優れたものが作製できる場合 が多い。 また基板に形成されていたとしても形成された 状やバルク状単結晶 板から切 り離し得るものであり、 それ自体で独立して存在しそして機能し得る。 それに対して本発明に よる面状の 2次元的な広がりを持つた膜状の単結晶はセラミック材料を主成分とする焼結体か らなる基板に固着した状態で存在しそして機能するものであるが、 このようなセラミック材料 を主成分とする焼結体と固着した薄膜状の単結晶を形成しようという試みは少なく、 仮に有つ たとしても通常薄膜の厚みは 3 0 0 m未満通常は 1 0 0 zm〜2 0 0 m以下程度と薄く多 結晶体であるセラミック材料を主成分とする焼結体の組成や材質あるいは不均質な内部組織あ るいは表面状態などの影響を受け易く結晶方位の不揃いなすなわち結晶性の低い例えば無定形 あるいは多結晶薄膜あるいは配向性多結晶薄膜となり易いので単結晶の薄膜が形成されにくい。 また膜状の単結晶の内部構造とセラミック材料を主成分とする焼結体の内部組織が異なるなど の理由で形成された単結晶薄膜にクラックゃ欠陥が生じたり、 該単結晶薄膜とセラミック材料 を主成分とする焼結体との界面で剥離などが生じ易かった。 また、 例えば上記昇華法などの方 法は塊状やパルク状など溝虫で大型の単結晶を得る方法としては適していると思われるが結晶 成長が高温で行われるため歪みが生じ易く基板に薄膜状の単結晶を成長させたとき該薄膜状の 単結晶及び基板にクラックや剥離などの不具合が生じ易いという欠点がある。 したがって基板 と一体化した状態の薄膜状の単結晶を作製することは困難であった。 そのような状況において 本発明によりセラミック材料を主成分とする焼結体に対して直接窒化ガリゥム、 窒化ィンジゥ ム、 窒化アルミニウムのうちから選ばれた少なくとも 1種以上を主成分とする単結晶薄膜が該 焼結体に強固に固着、 一体化され上記クラックゃ欠陥あるいは剥離など無い状態で形成し得る ことが可能となった。 このように本発明により薄い膜状の単結晶であってもセラミック材料を 主成分とする焼結体と強固に固着し一体化が行われ得ることが明らかとなった。 さらに窒化ガ
リウム、 窒化インジウム、 窒化アルミニウムのうちから選ばれた少なくとも 1種以上を主成分 とする例えば単結晶、 無定形、 多結晶、 配向性多結晶など各種結晶状態の薄膜をあらかじめ形 成したセラミック材料を主成分とする焼結体を用いることでその上にはさらに優れた結晶性を 有する窒化ガリウム、 窒化インジウム、 窒化アルミニウムのうちから選ばれた少なくとも 1種 以上を主成分とする単結晶薄膜が 固に一体化され上記クラックゃ欠陥あるいは剥離など無い 状態で形成し得ることが明らかとなつた。 またこのようにして形成される単結晶薄膜は比較的 厚みの厚い例えば 1 0 0 /im〜2 0 0 mより厚いものであっても結晶性に優れたものが形成 し得る。 このような単結晶薄膜の結晶性の向上が見られるのはおそらくあらかじめ上記各種結 晶状態の薄膜を形成しておくことで多結晶体であるセラミック材料を主成分とする焼結体の組 成や材質あるいは内部繊あるい 面状態などの影響を受けにくくなり従ってより結晶性に 優れた単結晶薄膜が成長し易くなるものと思われる。 本発明はこのようなセラミック材料を主 成分とする焼結体を用いた薄膜形成用基板を提供するものである。 また本発明は、 セラミック 材料を主成分とする焼結体と窒化ガリウム、 窒化インジウム、 窒化アルミニウムのうちから選 ばれた少なくとも 1種以上を主成分とするより結晶性の高い単結晶薄膜とが強固に一体化した 薄膜基板をも提供するものである。
本発明において、 光 ¾1性の窒化アルミニウムなど各種セラミック材料を主成分とする腿 体にはより結晶性の優れた窒化ガリウム、 窒化インジウム、 窒化アルミニウムのうちから選ば れた少なくとも 1種以上を主成分とする単結晶薄膜が形成し得る場合が多く、 また比較的厚み の厚い例えば 1 0 0 m〜2 0 0 mより厚い薄膜であっても比較的高い結晶性のものが形成 し得る場合が多い。 通常^ 11性の窒化アルミニウムなど各種セラミック材料を主成分とする 焼結体は光 ¾1性を有しないものに比べて比較的純度が高く焼結体内部組織は比較的均質であ る場合が多いことからも上記の が間接的に成り立つのではないかと思われる。 すなわち多 結晶体である窒化アルミニウムなど各種セラミック材料を主成分とする焼結体に強固に固着し 一体となった窒化ガリウム、 窒化インジウム、 窒化アルミニウムのうちから選ばれた少なくと も 1種以上を主成分とする薄膜状の単結晶は塊状やバルク状の単結晶を作製する場合と異なり 該焼結体の組成や材質あるいは内部組織あるいは表面状態などの影響を受け易いと思われる。 本発明においては光 性のセラミツク材料を主成分とする 結体を用いることで窒化ガリゥ ム、 窒化インジウム、 窒化アルミニウムのうちから選ばれた少なくとも 1種以上を主成分とす るより結晶性の高い面状の単結晶薄膜が該焼結体に強固に一体化した状態で提供できる。 さら に、 より結晶性の高い単結晶薄膜を得るために窒化ガリウム、 窒化インジウム、 窒化アルミ二 ゥムのうちから選ばれた少なくとも 1種以上を主成分とする単結晶、 無定形、 多結晶、 配向性 多結晶など各種結晶状態の薄膜をあらかじめ形成した光 ¾1性を有するセラミック材料を主成 分とする焼結体も好適に用いることができる。 本発明はこのような光 性を有するセラミッ ク材料を主成分とする焼結体を用いた薄膜形成用基板を提供するものである。 また本発明は、 光透過性を有するセラミック材料を主成分とする焼結体と窒化ガリウム、 窒化インジウム、 窒 化アルミニウムのうちから選ばれた少なくとも 1種以上を主成分とするより結晶性の高い単結 晶薄膜とが強固に一体化した薄膜基板をも提供するものである。
上記のように塊状やバルク状といった比較的大型で 3^¾の寸法で表わされ得る単結晶は、 例えば通常昇華法などのように雰囲気の圧力やガス組成などを制御しながら比較的高温で素材 の融点や飾灘に近い (例えば炭化珪素を主成分とするバルク状単結晶の場合は 2 0 0 0°C〜2 6 0 0°C程度、 窒化アルミニウムを主成分とするバルク状単結晶の場合 1 7 0 0T:〜 2 2 0 0°C程度) のおそらく ¥ί®に近い状態で単結晶素材そのものを含む原料 (例えば 7炭化 珪素を主成分とするバルク状単結晶の場合は炭化珪素粉末、 窒化アルミ二ゥムを主成分とする ノ^レク状単結晶を作製する場合は室化アルミニウム粉末) を加熱し素材そのものを昇華した後
単結晶として析出させるといつた方法で作製される場合が多ぐ 基板の材質や基板の内部組織 あるいは表面状態などの影響をあまり受けずに比較的容易に単独で結晶性に優れた大型の単結 晶が作製できる場合が多い。 これは恐らく上記塊状やバルク状の単結晶を昇華法で基板上に成 長させる場合平衡に近い状態で単結晶が行われるため昇華物質そのものが 結晶となり易いの で基板の影響をあまり受けずに結晶性の高い単結晶が成長するものと思われる。 また例えば引 き上げ法などでサファイアを作製する場合などは原料のアルミナを溶融して単結晶を育成する ため平衡に近い状態で該単結晶が作製される。 一方本発明による 2次元的な広がりを持った薄 膜状の単結晶をセラミック材料を主成分とする焼結体からなる基板に固着し一体化した状態で 形成する場合、 該薄膜状の単結晶の結晶性をより高め易くするために MO CVD (有機金属化 学纏分解成長) 法や MOVP E (有機金属気相ェピタキシャル成長) 法あるいはハライド V P E (ハロゲン化物気相ェピタキシャル成長) 法などで通常作製される。 このような方法にお いて通常基板温度は最高 1 5 0 0 程度であり該形成法や単結晶組成によって単結晶化し易い 基板温度範囲があり、 さらに単結晶薄膜形成用の原料も目的とする組成の中の金属成分を含む 化合物 (窒化ガリウムの場合はガリウム成分を含む化合物、 例えばトリメチルガリウムなど、 あるいは窒化ィンジゥムの場合はィンジゥム成分を含む化合物、 例え〖まトリメチルインジゥム など、 あるいは窒化アルミニウムの場合はアルミニウム成分を含む化合物、 例えばトリメチル アルミニウムなど) が用いられる場合が多くこのような化合物は一旦 军されてその後窒化反 応により目的とする組成となし単結晶薄膜を得るという過程を経るため非平衡状態で単結晶薄 膜の形成が行われ易いので条件により結晶性の低い例えば無定形あるいは多結晶薄膜あるいは 配向性多結晶薄膜となる場合がある。 また、 スパッタリング法やイオンプレーティング法ある いは蒸着法などが薄膜形成用の原料として分解 .反応などの過程を経ない薄膨組成そのものを 用いて薄膜形成を行う方法として使用し得るが通常基板温度は 6 0 0° (:〜 7 0 0°C以下程度の 低温で行われるなど、 薄膜形成が非平衡状態で行われるため形成される薄膜は単結晶とはなり にくく結晶性の低い例えば無定形あるいは多結晶薄膜あるいは配向性多結晶薄膜となり易い。 上記のように基板に形成される薄膜状の単結晶は 3次元的な大きさを有する塊状やバルク状の 単結晶と比較して結晶性が小さくなり易い。 またクラックや剥離など欠陥が生じ易い。 本発明 は上記で示したように結晶性が小さくなり易く、 欠陥などが生じ易い傾向を有する薄膜状の単 結晶であっても塊状やバルク状の単結晶と同等に近い比較的高い結晶性を有しさらにクラック や基板との間の剥離などの欠陥の少ないものを提供し得る方法を提示したものである。 本発明 により例えば窒化ガリウム、 窒化インジウム、 窒化アルミニウムのうちから選ばれた少なくと も;!種以上を主成分とする単結晶薄膜として厚み 3 0 0 m未満通常 2 0 0 m程度のものだ けでなく 0. 1 nm程度の薄いものであっても好適に形成し得るようになった。
上記のように本発明において、 セラミック材料を主成分とする焼結体に窒化ガリウム、 窒化 インジウム、 窒化アルミニウムのうちから選ばれた少なくとも 1種以上を主成分とする単結晶 薄膜を直接形成し得る。 さらにより結晶性の高い単結晶薄膜をセラミック材料を主成分とする 焼結体に形成しょうとする場合は、 例えば窒化ガリウム、 窒化インジウム、 窒化アルミニウム のうちから選ばれた少なくとも 1種以上を主成分とする薄膜を形成したセラミック材料を主成 分とする焼結体を用いる、 あるいは光 性を有するセラミック材料を主成分とする焼結体を 用いる、 あるいは窒化ガリウム、 窒化インジウム、 窒化アルミニウムのうちから選ばれた少な くとも 1種以上を主成分とする薄膜を形成した ¾¾ 性を有するセラミック材料を主成分とす る焼結体を用いる、 といった方法などを用いることが好ましい。
より詳しく言えば、 窒化ガリウム、 窒化インジウム、 窒化アルミニウムのうちから選ばれた 少なくとも 1種以上を主成分とする薄膜を形成したセラミック材料を主成分とする焼結体を用 いる方法の場合、 該窒化ガリウム、 窒化インジウム、 窒化アルミニウムのうちから選ばれた少
なくとも 1種以上を主成分とする薄膜として無定形、 多結晶、 配向性多結晶、 単結晶のうちか ら選ばれた少なくともいずれかの結晶状態を有するものを好適に用いることができる。 これら の結晶状態を有する薄膜のうち少なくとも一部が単結晶であるもの力好ましい。 また、 これら の薄膜として 1層だけからなるものを用いることができる。 また、 これらの薄膜として少なく とも 2以上の層からなるものも用いることができる。 また、 この 2以上の層からなる薄膜にお いて各層がそれぞれ無定形、 多結晶、 配向性多結晶、 単結晶のうちから選ばれる少なくともい ずれかの結晶状態を有するものを好適に用いることができる。 また、 この 2以上の層からなる 薄膜においてセラミック材料を主成分とする焼結体に直接形成された薄麵が無定形、多結晶、 配向性多結晶、 単結晶のうちから選ばれる少なくともいずれかの結晶状態を有するものを用い ることができる。 また、 この 2以上の層からなる薄膜においてセラミック材料を主成分とする 焼結体に直接形成された薄藤が無定形、 多結晶、 配向性多結晶のうちから選ばれる少なくと もいずれかの結晶状態を有するものを用いることができる。 また、 この 2以上の層からなる薄 膜においてセラミック材料を主成分とする焼結体に直接形成された薄 が 向性多結晶であ るものを用いることができる。 また、 この 2以上の層からなる薄膜において少なくとも 1層が 単結晶であるものを用いることができる。 また、 この 2以上の層からなる薄膜において最上層 の薄膜が単結晶であるものが好ましい。最上層の薄膜が単結晶であればその上に窒化ガリゥム、 窒化インジウム、 窒化アルミニウムのうちから選ばれた少なくとも 1種以上を主成分とする結 晶性の優れた薄膜が形成し得る。 また、 セラミック材料を主成分とする焼結体に形成された窒 化ガリウム、 窒化インジウム、 窒化アルミニウムのうちから選ばれた少なくとも 1種以上を主 成分とする薄膜が少なくとも単結晶薄 IISを有し該単結晶薄 の厚みが 3 0 0 m*満通常 は 2 0 0 m以下であるものを用いることが好ましい。 セラミック材料を主成分とする焼結体 に形成された該単結晶薄 のより好ましい厚みは 1 0 0 z/m以下である。 また、 セラミック 材料を主成分とする焼結体に形成された薄膜として少なくとも 0. 1 nm以上の厚みを有する ものを用いることが好ましい。 これは薄膜にピンホー =結晶の乱れなどに起因する欠陥を防 止する上で好ましい。 薄膜が 2以上の層の薄膜層からなる場合各薄 の厚みがそれぞれ 0 · 1 nmより薄い場合であってもすベての薄膜層を合計した厚みが 0. 1 nm以上であれば上記 の欠陥が生じにく。 より好ましい厚みは 0. 5 nm以上であり 0. 3 μπι以上の厚みのものが さらに好ましい。 また厚み 3. 5 /m以上、 あるいは 1 0 m以上、 あるいは 5 0 m以上の 薄膜を形成したセラミック材料を主成分とする焼結体も薄膜形成用基板として好適に用いるこ とができる。 また、 セラミック材料を主成分とする焼結体に形成された薄膜として少なくとも 窒化ガリウムを含むものを用いることができる。 より具体的には、 セラミック材料を主成分と する焼結体に形成された薄膜として少なくとも窒化ガリゥムを含むかあるいは窒化ガリゥムを 主成分とする薄膜を有するものを用いることができる。 さらに、 セラミック材料を主成分とす る焼結体に形成された薄膜として窒化ガリウムを主成分とするものを用いることができる。 例 えば上記の少なくとも窒化ガリゥムを含む薄膜を形成したセラミック材料を主成分とする焼結 体を用いた場合その上には結晶の優れた窒化ガリウム、 窒化インジウム、 窒化アルミニウムの うちから選ばれた少なくとも 1種以上を主成分とする単結晶薄膜が形成し易くなり、 上記の少 なくとも窒化ガリゥムを含む薄膜を形成したセラミック材料を主成分とする焼結体を用いて発 光素子を作製すればより発光効率の高いものが作製し得るようになる。 窒化ガリゥムを含むか あるいは窒化ガリゥムを主成分とする薄膜には窒化ガリゥム成分の他に例えば窒化ィンジゥム、 窒化アルミニウムのうちから選ばれた少なくとも 1種以上の成分や S iや Mgなどのドーピン グ成分が含まれている薄膜であってもよい。 なお、 上記の 「少なくとも窒化ガリウムを含む薄 についてより具体的に説明すれば、 本発明によるセラミック材料を主成分とする焼結体に 形成された薄膜は窒化ガリウム、 窒化インジウム、 窒化アルミニウムのうちから選ばれた少な
くとも 1種以上を主成分とするものであるがこれを例えば化学式 A l xG a y I x yNで表 わしたとき 「少なくとも窒化ガリウムを含む薄駒 とは 0く y≤lの組成を有するもの (すな わち 0≤xく 1、 0≤l - x - y< l ) を意味する。 通常窒化ガリウムを主成分とする薄膜と は窒化ガリウム成分を 5 0モル%以上含むものである。 また、 セラミック材料を主成分とする 焼結体に形成された薄膜として少なくとも単結晶を含むもの用いる場合該単結晶薄膜はミラー 指数 (0 0 2) の格子面の X線回折ロッキングカーブの半値幅が 3 6 0 0秒以下の結晶性であ ることが好ましく、 3 0 0秒以下であることがより好ましい。 また 2 4 0秒以下のもの、 ある いは 2 0 0秒以下、 あるいは 1 5 0秒以下、 あるいは 1 3 0秒以下のものがさらに好ましく、 1 0 0秒以下のものが最も好ましい。
また、 光透過性を有するセラミック材料を主成分とする焼結体を用いる方法の場合、 通常光
¾i率 1 %以上のセラミック材料を主成分とする焼結体を用いることができる。 また、 y m 率 1 0 %以上、 2 0 %以上、 3 0 %以上、 4 0 %以上、 5 0 %以上、 6 0 %以上、 さらに 過率 8 0 %以上及び 8 5 %以上のものも用いることができる。
また、 窒化ガリウム、 窒化インジウム、 窒化アルミニウムのうちから選ばれた少なくとも 1 種以上を主成分とする薄膜を形成した光 ¾1性を有するセラミック材料を主成分とする焼結体 を用いる方法の場合、 該窒化ガリウム、 窒化インジウム、 窒化アルミニウムのうちから選ばれ た少なくとも 1種以上を主成分とする薄膜として無定形、 多結晶、 配向性多結晶、 単結晶のう ちから選ばれた少なくともいずれかの結晶状態を有するものを好適に用いることができる。 こ れらの結晶状態を有する薄膜のうち少なくとも一部が単結晶であるものが好ましい。 また、 光 ¾M性を有するセラミック材料を主成分とする焼結体に形成された薄膜は少なくとも窒化ガリ ゥムを含むかあるいは窒化ガリウムを主成分とする薄膜を有するものを用いることができる。 また、 これらの薄膜として 1層だけからなるものを用いることができる。 また、 これらの薄膜 として少なくとも 2以上の層からなるものも用いることができる。 また、 この 2以上の層から なる薄膜において各層がそれぞれ無定形、 多結晶、 配向性多結晶、 単結晶のうちから選ばれる 少なくともいずれかの結晶状態を有するものを好適に用いることができる。 また、 この 2以上 の層からなる薄膜において 性を有するセラミック材料を主成分とする焼結体に直接形成 された薄 HIが無定形、 多結晶、 配向性多結晶、 単結晶のうちから選ばれる少なくともいずれ かの結晶状態を有するものを用いることができる。 また、 この 2以上の層からなる薄膜におい て 性を有するセラミック材料を主成分とする焼結体に直接形成された薄 MSが無定形、 多結晶、 配向性多結晶のうちから選ばれる少なくともいずれかの結晶状態を有するものを用い ることができる。 また、 この 2以上の層からなる薄膜において) ι6¾ϋ性を有するセラミック材 料を主成分とする焼結体に直接形成された薄膜層が己向性多結晶であるものを用いることがで きる。 また、 この 2以上の層からなる薄膜において少なくとも 1層が単結晶であるものを用い ることができる。 また、 この 2以上の層からなる薄膜において最上層の薄膜が単結晶であるも のが好ましい。 最上層の薄膜が単結晶であればその上に窒化ガリウム、 窒化インジウム、 窒化 アルミニウムのうちから選ばれた少なくとも 1種以上を主成分とする結晶性の優れた薄膜が形 成し得る。 また、 光 ¾1性を有するセラミック材料を主成分とする焼結体に形成された窒化ガ リウム、 窒化インジウム、 窒化アルミニウムのうちから選ばれた少なくとも 1種以上を主成分 とする薄膜が少なくとも単結晶薄 を有し該単結晶薄 の厚みが 3 0 0 m*満通常は 2 0 0 m以下であるものを用いることが好ましい。 光 ¾ί§性を有するセラミック材料を主成分 とする焼結体に形成された該単結晶薄翻のより好ましい厚みは 1 0 0 以下である。 また、 光 ¾i性を有するセラミック材料を主成分とする焼結体に形成された薄膜として少なくとも 0. 1 nm以上の厚みを有するものを用いることが好ましい。 これは薄膜にピンホールや結晶の乱 れなどに起因する欠陥を防止する上で好ましい。 薄膜が 2以上の層の薄 ΙΙβからなる場合各薄
膜層の厚みがそれぞれ 0. 1 nmより薄い場合であってもすベての薄膜層を合計した厚みが 0. l nm以上であれば上記の欠陥が生じにく。 より好ましい厚みは 0. 5 nm以上であり 0. 3 m以上の厚みのものがさらに好ましい。 また厚み 3. 5 /m以上、 あるいは 1 0 m以上、 あるいは 5 0 m以上の薄膜を形成した ¾¾¾性を有するセラミック材料を主成分とする焼結 体も薄膜形成用基板として好適に用いることができる。 光透過性を有するセラミック材料を主 成分とする焼結体に形成された薄膜として少なくとも窒化ガリウムを含むものを用いることが できる。 より具体的には、 光透過性を有するセラミック材料を主成分とする焼結体に形成され た薄膜は少なくとも窒化ガリウムを含むかあるいは窒化ガリウムを主成分とする薄膜を有する ものを用いることができる。 さらに、 ¾¾ 性を有するセラミック材料を主成分とする焼結体 に形成された薄膜として窒化ガリゥムを主成分とするものを用いることができる。 例えば上記 の少なくとも窒化ガリウムを含む薄膜を形成したセラミック材料を主成分とする焼結体を用い た場合その上には結晶の優れた窒化ガリウム、 窒化インジウム、 窒化アルミニウムのうちから 選ばれた少なくとも 1種以上を主成分とする単結晶薄膜が形成し易くなり、 上記の少なくとも 窒化ガリゥムを含む薄膜を形成したセラミック材料を主成分とする焼結体を用いて発光素子を 作製すればより発光効率の高いものが作製し得るようになる。 窒化ガリウムを含むかあるいは 窒化ガリゥムを主成分とする薄膜には窒化ガリゥム成分の他に例えば窒化ィンジゥム、 窒化ァ ルミニゥムのうちから選ばれた少なくとも 1種以上の成分や S iや M gなどのドーピング成分 が含まれている薄膜であってもよい。 なお、 上記の 「少なくとも窒化ガリウムを含む薄 に ついてより具体的に説明すれば、 本発明による ¾¾i性を有するセラミック材料を主成分とす る焼結体に形成された薄膜は窒化ガリウム、 窒化インジウム、 窒化アルミニウムのうちから選 ばれた少なくとも 1種以上を主成分とするものであるがこれを例えば化学式 A l xG ay I n x_ x_yNで表わしたとき「少なくとも窒化ガリウムを含む薄駒 とは 0く y≤lの糸滅を有するも の (すなわち 0≤xく 1、 0≤l - x - y< l ) を意味する。 通常窒化ガリウムを主成分とす る薄膜とは窒化ガリウム成分を 5 0モル%以上含むものである。 また、 光 生を有するセラ ミック材料を主成分とする焼結体に形成された薄膜として少なくとも単結晶を含むもの用いる 場合該単結晶薄膜はミラ一指数 (0 0 2) の格子面の X線回折ロッキングカーブの半値幅が 3 6 0 0秒以下の結晶性であることが好ましく、 3 0 0秒以下であることがより好ましい。 また 2 4 0秒以下のもの、 あるいは 2 0 0秒以下、 あるいは 1 5 0秒以下、 あるいは 1 3 0秒以下 のものがさらに好ましく、 1 0 0秒以下のものが最も好ましい。
なお本発明においては、 たとえ光透過性の小さいセラミック材料を主成分とする焼結体、 例 えば;)^過率が 1 %より小さいセラミック材料を主成分とする焼結体あるいは光 率 0 %の セラミック材料を主成分とする焼結体であっても窒化ガリウム、 窒化インジウム、 窒化アルミ ニゥムのうちから選ばれた少なくとも 1種以上を主成分とする単結晶薄膜を形成し得る。 例え ばこのような光 ¾i性の小さいセラミツク材料を主成分とする焼結体に窒化ガリゥム、 窒化ィ ンジゥム、 窒化アルミニウムのうちから選ばれた少なくとも 1種以上を主成分とする薄膜を形 成することによりより結晶性の高い単結晶薄膜を形成し得る。
上記のように本発明による薄膜形成用基板はセラミック材料を主成分とする焼結体及び髓 過性を有するセラミック材料を主成分とする焼結体からなるが、 さらに窒化ガリウム、 窒化ィ ンジゥム、 窒化アルミニウムのうちから選ばれた少なくとも 1種以上を主成分とする薄膜が形 成されたセラミック材料を主成分とする焼結体及び窒化ガリウム、 窒化インジウム、 窒化アル ミニゥムのうちから選ばれた少なくとも 1種以上を主成分とする薄膜が形成された光 ¾1性を 有するセラミック材料を主成分とする焼結体、 が含まれる。 また、 薄膜基板はセラミック材料 を主成分とする焼結体に窒化ガリウム、 窒化インジウム、 窒化アルミニウムのうちから選ばれ た少なくとも 1種以上を主成分とする薄膜を形成したもの、 及び光透過性を有するセラミック
材料を主成分とする能結体に窒化ガリウム、 窒化インジウム、 窒化アルミニウムのうちから選 ばれた少なくとも 1種以上を主成分とする薄膜を形成したものである。 上記セラミック材料を 主成分とする焼結体及び光透過性を有するセラミック材料を主成分とする焼結体は少なくとも 窒化アルミニウムを主成分とする焼結体、 あるいは六方晶系又 方晶系のうちから選ばれた 少なくともいずれかの結晶構造を有するセラミック材料を主成分とする焼結体、 あるいは酸化 ジリレコニゥム、酸ィ匕マグネシウム、 アルミン酸マグネシウム、酸ィ匕チタン、チタン酸バリウム、 チタン酸ジルコン酸鉛、 希土観素酸化物、 酸化トリウム、 各種フェライト、 ムライト、 フォ ルステライト、 ステアタイト、 結晶化ガラス、 のうちから選ばれた少なくとも 1種以上の材料 からなる; ¾結体、 などが少なくとも含まれる。 また、 上記六方晶系又 方晶系のうちから選 ばれた少なくともいずれかの結晶構造を有するセラミック材料を主成分とする焼結体には酸化 亜鉛を主成分とする焼結体、 酸化ベリリウムを主成分とする焼結体、 酸化アルミニウムを主成 分とする焼結体、 炭化珪素を主成分とする焼結体、 窒化珪素を主成分とする焼結体、 窒化ガリ ゥムを主成分とする焼結体、 などの各種セラミック材料を主成分とする焼結体を含む。
上記説明した窒化ガリウム、 窒化インジウム、 窒化アルミニウムのうちから選ばれた少なく とも 1種以上を主成分とする薄膜を形成したセラミック材料を主成分とする焼結体及び^ lii 性を有するセラミック材料を主成分とする焼結体からなる薄膜形成用基板において、 形成され た薄膜は単結晶、 無定形、 多結晶、 配向性多結晶のうちから選ばれる少なくともいずれかの結 晶状態を有するものが用い得るが、 これらの薄膜は単結晶、 無定形、 多結晶、 配向性多結晶の うちから選ばれる少なくともいずれかの結晶状態がそれぞす «虫で存在しているものだけでな く各結晶状態のものが少なくとも 2以上同時に存在しているものであってもよい。 すなわち例 えば各結晶状態の薄膜が明確な層を形成せず 2以上の結晶状態で混在しているものようなもの であってもよい。 より具体的に言えば例えば無定形と配向性多結晶、 あるいは配向性多結晶と 単結晶、 あるいは無定形と単結晶、 あるいは無定形と多結晶、 など明確な層を形成せずあたか も単一の層として存在しているようなものであってもよい。 又例えばセラミック材料を主成分 とする焼結体に形成された薄膜が単一層あるいは少なくとも 2以上の層からなる場合、 該薄膜 の少なくとも 1以上の層が単結晶、 無定形、 多結晶、 配向性多結晶のうちから選ばれた少なく ともいずれか 2以上の結晶状態が同時に混在しているものであつてもよい。
また、 上記薄膜基板においてセラミック材料を主成分とする焼結体及び;) 性を有するセ ラミック材料を主成分とする焼結体のうちから選ばれた少なくともいずれかの焼結体に形成す る窒化ガリウム、 窒化インジウム、 窒化アルミニウムのうちから選ばれた少なくとも 1種以上 を主成分とする薄膜は単結晶、 無定形、 多結晶、 配向性多結晶のうちから選ばれる少なくとも いずれかの結晶状態を有するものが用い得るが、 これらの薄膜は単結晶、 無定形、 多結晶、 配 向性多結晶のうちから選ばれる少なくともいずれかの結晶状態がそれぞれ単独で存在している ものだけでなく各結晶状態のものが少なくとも 2以上同時に存在しているものであってもよい。 すなわち例えば各結晶状態の薄膜が明確な層を形成せず 2以上の結晶状態で混在しているもの ようなものであってもよい。 より具体的に言えば例えば無定形と配向性多結晶、 あるいは配向 性多結晶と単結晶、 あるいは無定形と単結晶、 あるいは無定形と多結晶、 など明確な層を形成 せずあたかも単一の層として存在しているようなものであってもよい。
本発明において窒化ガリウム、 窒化インジウム、 窒化アルミニウムのうちから選ばれた少な くとも 1種以上を主成分とする単結晶薄膜の厚みとして例えば 2 0 0 mより厚いものであつ てもセラミック材料を主成分とする焼結体からなる基板に直接形成し得るが薄膜の厚みを厚く 形成すれば該単結晶薄膜の結晶性は小さくなり易い傾向があるためセラミツク材料を主成分と する焼結体からなる基板に直接形成する場合は厚みとして例えば 3 0 0 m未満通常は 2 0 0 m以下と薄い状態で形成することが結晶性に優れた単結晶薄膜を得る上では好ましい。 セラ
ミック材料を主成分とする焼結体に上記のような例えば 2 0 0 /mより厚みの厚い単結晶薄膜 を形成しょうとする場合は、 上記で示したように例えば窒化ガリウム、 窒化インジウム、 窒化 アルミニウムのうちから選ばれた少なくとも 1種以上を主成分とする薄膜を形成したセラミッ ク材料を主成分とする焼結体を用いるか、 あるいは光¾1性を有するセラミック材料を主成分 とする焼結体を用いるか、 あるいは窒化ガリウム、 窒化インジウム、 窒化アルミニウムのうち から選ばれた少なくとも 1種以上を主成分とする薄膜を形成した ¾¾1性を有するセラミック 材料を主成分とする焼結体を用いる、 といった方法などを用いることが好ましい。
本発明においてセラミック材料を主成分とする焼結体及び光透過性を有するセラミック材料 を主成分とする焼結体を用いその上に窒化ガリウム、 窒化インジウム、 窒化アルミニウムのう ちから選ばれた少なくとも 1種以上を主成分とする薄膜からなる少なくとも N型半導体層及び 発光層及び P型半導体層を含む積層体を形成して発光素子を作製すれば、 赚からのサフアイ ァなどのバルク状単結晶を用いて作製した発光素子に比べて少なくとも同等かより優れた発光 効率を有する発光素子が提供し得る。 さらに、 該セラミック材料を主成分とする焼結体及び光 ¾i性を有するセラミック材料を主成分とする焼結体として窒化ガリゥム、 窒化ィンジゥム、 窒化アルミニウムのうちから選ばれた少なくとも 1種以上を主成分とする薄膜を形成したもの を用いればより優れた発光効率を有する発光素子が作製し得る。 また、 上記薄膜の中で少なく とも窒化ガリウムを含むかあるいは窒化ガリウムを主成分とするものを形成した該セラミック 材料を主成分とする焼結体あるいは光 ¾i性を有するセラミック材料を主成分とする焼結体を 用いることによりさらに優れた発光効率を有する発光素子が作製し得る。
本発明において上記窒化ガリウム、 窒化インジウム、 窒化アルミニウムのうちから選ばれた 少なくとも 1種以上を主成分とする薄膜を形成したセラミック材料を主成分とする焼結体及び 光 ¾i 性を有するセラミック材料を主成分とする焼結体を用いて発光素子を作製する方法にお いて、 薄膜として単結晶、 無定形、 多結晶、 配向性多結晶のうちから選ばれる少なくともいず れかの結晶状態を有するものが用い得るが、 通常表面の (最上層の) 薄 なわち上記発光素 子を構成する窒化ガリウム、 窒化インジウム、 窒化アルミニウムのうちから選ばれた少なくと も 1種以上を主成分とする薄膜からなる少なくとも N型半導体層及び発光層及び P型半導体層 を含む積層体を直接形成する薄膜は単結晶であることが好ましぐ より優れた発光効率を有す る発光素子が作製し得る。
また、 セラミック材料を主成分とする焼結体として通常平均表面粗さ R a 2 0 0 0 nm以下 の表面状態を有するものを用いることで比較的結晶性に優れた単結晶薄膜を形成することがで きる。 このような表面状態は通常セラミック材料を主成分とする焼結体の焼成されたそのまま の表面〔焼き放し(a s— f i r e )表面、ラッフ 磨された表面、ブラスト研磨された表面、 鏡面研磨された表面、 化学腐食された表面及びプラズマガスにより腐食された表面、 あるいは 溝切りなど機械的な加工が施された表面などにおいて得ることができる。 本発明において上記 表面状態を有するセラミック材料を主成分とする焼結体及び mi性を有するセラミック材料 を主成分とする焼結体を用いその上に発光素子を構成する窒化ガリウム、 窒化インジウム、 窒 化アルミニウムのうちから選ばれた少なくとも 1種以上を主成分とする薄膜からなる少なくと も N型半導体層及び発光層及び P型半導体層を含む積層体を形成して発光素子を作製すること により、 «からのサファイアなどのバルク状単結晶を用いて作製した発光素子に比べて少な くとも同等かより優れた発光効率を有する発光素子が提供し得る。
また、 本発明においてはセラミック材料を主成分とする焼結体及び光 ¾1性を有するセラミ ック材料を主成分とする焼結体として表面粗さの大きいものであっても比較的結晶性に優れた 単結晶薄膜を形成することができる。 例えば表面粗さの大きいセラミック材料を主成分とする 焼結体及び光 M 生を有するセラミック材料を主成分とする焼結体としては平均表面粗さ R a
7 0 nm以上のものがであっても該焼結体には比較的結晶性に優れた単結晶薄膜を形成するこ とができる。 さらに R a 2 0 0 0 nmより大きい平均表面粗さを有するセラミック材料を主成 分とする焼結体及び光 性を有するセラミック材料を主成分とする焼結体であっても比較的 結晶性に優れた単結晶薄膜を形成することができる。 このような表面状態は通常セラミック材 料を主成分とする焼結体及び光透過性を有するセラミック材料を主成分とする焼結体の焼成さ れたそのままの表面 〔焼き放し (a s— f i r e)表面〕、 ラッフ ¾f磨された表面、 ブラスト研 磨された表面、 化学腐食された表面及びプラズマガスにより腐食された表面、 あるいは溝切り など機械的な加工が施された表面などにおいて得ることができる。 本発明においてセラミック 材料を主成分とする焼結体及び光 ¾ 性を有するセラミック材料を主成分とする焼結体を用い その上に発光素子を構成する窒化ガリウム、 窒化インジウム、 窒化アルミニウムのうちから選 ばれた少なくとも 1種以上を主成分とする薄膜からなる少なくとも N型半導体層及び発光層及 び P型半導体層を含む積層体を形成して発光素子を作製する場合、 該セラミック材料を主成分 とする焼結体あるいは光 性を有するセラミック材料を主成分とする焼結体としては上記で 例示した表面粗さの大きいものを用いることにより該発光素子の発光効率をより高め得る。 通 常表面粗さの大きいセラミック材料を主成分とする焼結体及び光透過性を有するセラミック材 料を主成分とする焼結体として平均表面粗さが R a 7 0 nm以上のものを用いることが好まし い。 また、 平均表面粗さが R a 1 0 0 O nmより大きいものさらに R a 1 0 0 O nmより大き いものも用い得、 発光効率のより高い発光素子が作製し得る。
本発明において上記平均表面粗さ R a 2 0 0 0 nm以下あるいは表面粗さの大きいセラミツ ク材料を主成分とする焼結体及び光 ¾ϋ性を有するセラミック材料を主成分とする焼結体に窒 化ガリウム、 窒化インジウム、 窒化アルミニウムのうちから選ばれた少なくとも 1種以上を主 成分とする比較的結晶性に優れた単結晶薄膜が直接形成し得るが、 窒化ガリウム、 窒化インジ ゥム、 窒化アルミニウムのうちから選ばれた少なくとも 1種以上を主成分とする薄膜を形成し たものを用いその上に窒化ガリウム、 窒化インジウム、 窒化アルミニウムのうちから選ばれた 少なくとも 1種以上を主成分とする単結晶薄膜を形成すればより結晶性に優れたものが作製し 得る。 本発明においては上記平均表面粗さ R a 2 0 0 0 nm以下あるいは表面粗さの大きいセ ラミック材料を主成分とする焼結体及び ¾¾i性を有するセラミック材料を主成分とする焼結 体を用いその上に窒化ガリウム、 窒化インジウム、 窒化アルミニウムのうちから選ばれた少な くとも 1種以上を主成分とする薄膜からなる少なくとも N型半 本層及び発光層及び P型半導 体層を含む積層体を直接形成して発光軒を作製することも可能であるが、 通常上記平均表面 粗さ R a 2 0 0 0 nm以下あるいは表面粗さの大きいセラミック材料を主成分とする焼結体及 び光透過性を有するセラミック材料を主成分とする焼結体に窒化ガリゥム、 窒化ィンジゥム、 窒化アルミニウムのうちから選ばれた少なくとも 1種以上を主成分とする薄膜を形成したもの を用いその上に上記積層体を形成することによって発光効率のより高い発光素子が作製し得る。 本発明は上記のようにセラミック材料を主成分とする焼結体を用いた発光素子を提供する。 また本発明は、 性を有するセラミック材料を主成分とする焼結体を用いた発光素子を提 供する。 また本発明は、 表面粗さの大きいセラミック材料を主成分とする焼結体を用いた発光 素子を提供する。 また本発明は、 窒化ガリウム、 窒化インジウム、 窒化アルミニウムのうちか ら選ばれた少なくとも 1種以上を主成分とする薄膜が形成されたセラミック材料を主成分とす る焼結体を用いた発光素子を提供する。 また本発明は、 窒化ガリウム、 窒化インジウム、 窒化 アルミニウムのうちから選ばれた少なくとも 1種以上を主成分とする単結晶薄膜が形成された セラミック材料を主成分とする焼結体を用いた発光素子を提供する。
なお、本発明における発光効率とは、発光素子を馬赚させるために軒に加えられた電力(電 気エネルギー) と実際発光素子によって光に変換され発光素子の外部へ放出された光出力 (光
エネルギー) との百分率比を意味する。 例えば発光効率が 1 0 %ということは、 電圧 3. 6ポ ルト、 電流 5 0 0mAを注入して発光素子を駆動させたとき光出力として 1 8 OmWが得られ るということである。 光出力は例えば発光 を積分球に装填して発光させ発せられたすべて の光を集め、 分光光度計などを用いて測定することができる。 なお、 照明分野で一般的に用い られている発光効率は単位時間当りの光エネルギー (W) に対する光の量 (光束: l m) であ るが(すなわち l mZWで表わされる)、 本発明の発光効率は照明分野で一般的に使用されてい る発光効率とは異なる。
通常結晶性など素材としての特性は塊状やバルク状単結晶の方がセラミック材料を主成分と する焼結体からなる基板に固着、一体化された薄膜状の単結晶より優れている場合が多かった。 しかしながら上記のように本発明により塊状やバルク状の単結晶と同等に近い結晶性を有する 窒化ガリウム、 窒化インジウム、 窒化アルミニウムのうちから選ばれた少なくとも 1種以上を 主成分とする単結晶薄膜がセラミック材料を主成分とする焼結体に形成できるようになった。 その結果、 該単結晶薄膜とセラミック材料を主成分とする焼結体とが一体化した状態のものは «の塊状やバルク状単結晶ではなし得なかった特性が発現し得ることが見出された。 例えば セラミツク材料を主成分とする焼結体を用いて作製した発光素子であっても従来からのサファ ィァなどのバルク状単結晶を用いて作製した発光^?に比べて少なくとも同等かより優れた発 光効率を有する発光素子が提供し得るようになった。 仮に上記セラミック材料を主成分とする 焼結体に形成される薄膜状の単結晶の結晶性が塊状やバルク状などの単結晶より劣っていると しても発光 や光導波路あるレ ^は回 板などの電子素子ゃ電 品を作製する場合、 セラ ミック材料を主成分とする焼結体と単結晶薄膜とが固着、 一体化された薄膜基板及び単結晶薄 膜が形成し得るセラミック材料を主成分とする焼結体からなる薄膜形成用基板を用いる方が塊 状やバルク状単結晶など単独で単結晶であるものを基板として用いたものより優れた特性を有 するものが得られ易い。 すなわち素材の特性がよいからといってそれを電子^?あるいは電子 部品を作製するための基板に用いたとしても作製される該電子素子あるいは電子部品の特性が 優れているとは限らない。 本発明で示すようにセラミック材料を主成分とする焼結体と薄膜状 の単結晶とがー体となったものを用いることで初めて からの塊状やバルク状単結晶だけ用 いたものではなし得なかった優れた特性の電子 あるいは電 品が作製し得る。 すなわち 例えば、 発光素子を作製する場合、 塊状やバルク状などの単結晶だけを基板として用いて作製 したものに比べ本発明によるセラミック材料を主成分とする焼結体に固着、 一体化された薄膜 状の単結晶を有する薄膜基板及びこのような薄膜が形成し得るセラミック材料を主成分とする 焼結体からなる薄膜形成用基板を用いて作製されたものは発光効率の面でより優れている。 す なわち低消費電力で大きな発光エネルギーが得られる。 これは塊状やバルク状塊状やパルク状 などの単結晶だけを基板として用いた場合、 発光 »を構成する窒化ガリウム、 窒化インジゥ ム、 窒化アルミニウムのうちから選ばれた少なくとも 1種以上を主成分とする薄膜からなる少 なくとも N型半導体層及び発光層及び P型半導体層を含む積層体は良好な結晶性のものが形成 できるが、 該塊状やバルク状の単結晶の有する均一性などの影響で該発光素子を構成する積層 体と基板との界面で光の反射が生じ易くなり発光層からの光が発光素子を構成する ¾層体の 内部に閉じ込められ易くなるためであると考えられる。 それに対して本発明による上記薄膜基 板あるいは薄膜形成用基板を用いた場合、 上記発光素子を構成する積層体は比較的高い結晶性 のものが形成できるということと、 さらにセラミツク材料を主成分とする焼結体が微粒子から なる多結晶体であるため積層体と基板との界面で光の反射が生じにくくなり発光層からの光が 発光素子を構成する謝責層体の内部に閉じ込められず^?外部に放出され易くなる、 という塊 状やバルク状などの単結晶だけを基板として用いたものでは実現し得ない 2つの機能の相乗効 果を有するためと考えられる。
また、 その他例えば光導波路や回路基板などの電子素子や電子部品を作製する場合も本発明 による上記薄膜基板あるいは薄膜形成用基板を用いれば、 セラミック材料を主成分とする焼結 体内部に電気回路が形成し得るので小型化や配線の引き回しが少ないため電気特性の向上など 塊状やバルク状などの単結晶だけを基板として用いたものでは実現し得ない優れた機能を有す るものが実現できる。
本発明の意義と目的は上記のように、 窒化ガリウム、 窒化インジウム、 窒化アルミニウムの うちから選ばれた少なくとも 1種以上を主成分とする結晶性に優れた単結晶を薄膜状となしセ ラミック材料を主成分とする焼結体と一体化することで単結晶及び、セラミック材料を主成分と する焼結体それぞ 独ではなし得ない相乗効果を引き出し、 «からのサフアイァゃ炭化珪 素などの塊状やバルク状などそれ自体独立で単結晶として存在し使用される材料では実現が困 難であった優れた機能を有する基板及び該基板を用いた発光素子などの電子素子、 あるいは回 路基板などの電子部品を提供することにある。 またこのような効果をもたらすセラミック材料 を主成分とする焼結体を提供することにある。
以下本発明に付いてさらに詳しく説明する。
本発明による窒化アルミニウムを主成分とする焼結体からなる基板は直接窒化ガリゥム、 窒 化インジウム、 窒化アルミニウムのうちから選ばれた少なくとも 1種以上を主成分とする薄膜 をその表面に形成でき、 薄膜として少なくともェピタキシャル成長した単結晶が直接形成でき る。 また、 窒化アルミニウムを主成分とする焼結体を基板として用いたときそこには窒化ガリ ゥム、 窒化インジウム、 窒化アルミニウムのうちから選ばれた少なくとも 1種以上を主成分と する薄膜としては上記のような単結晶状態のものだけに限らずその他無定形状態のもの、 多結 晶状態のもの、あるいは配向性多結晶状態のもの、など各種結晶状態の薄膜が 接形成できる。 本発明において上記の単結晶状態及び無定形状態、 多結晶状態、 配向性多結晶状態など各種結 晶状態の薄膜が形成された窒化アルミニウムを主成分とする焼結体を基板として用い、 この基 板に窒化ガリウム、 窒化インジウム、 窒化アルミニウムのうちから選ばれた少なくとも 1種以 上を主成分とする単結晶薄膜を成長させた時、 得られる該単結晶薄膜は窒化アルミニウムを主 成分とする焼結体からなる基板に直接形成した単結晶薄膜より結晶性が向上したものが形成さ れ易い。 本発明において 「直接」 という意味は文字通り窒化アルミニウムを主成分とする焼結 体からなる基板に他の材料や介在物などを介することなく直接窒化ガリゥム、窒化ィンジゥム、 窒化アルミニウムのうちから選ばれた少なくとも 1種以上を主成分とする薄膜を形成するとい うことである。 上記薄膜を形成するために窒化アルミニウムを主成分とする焼結体からなる基 板表面に特別な材料や介在物や介在材料などは必要としない。 このように本発明による窒 ί匕ァ ルミ二ゥムを主成分とする焼結体からなる基板を用いることで窒化ガリゥム、窒化ィンジゥム、 窒化アルミニウムのうちから選ばれた少なくとも 1種以上を主成分とする結晶性に優れた単結 晶薄膜を形成できる。 本発明による窒化アルミニウムを主成分とする焼結体からなる基板に直 接形成される薄膜は単結晶のものが形成できるがそれだけに限らず無定形状態のもの、 多結晶 状態のもの、 あるいは配向性多結晶状態のもの、 など各種結晶状態のものが形成できる。 さら に窒化ガリウム、 窒化インジウム、 窒化アルミニウムのうちから選ばれた少なくとも 1種以上 を主成分とする単結晶の薄膜を形成しょうとする場合、 本発明による窒化アルミニウムを主成 分とする焼結体からなる基板に窒化ガリウム、 窒化インジウム、 窒化アルミニウムのうちから 選ばれた少なくとも 1種以上を主成分とする単結晶、 無定形、 多結晶、 配向性多結晶など上記 各種結晶状態の薄膜があらかじめ形成された薄膜基板を用いその上に単結晶薄膜を形成するこ とでより高い結晶性の単結晶薄膜が得られる。 この窒化アルミニウムを主成分とする焼結体か らなる基板に窒化ガリウム、 窒化インジウム、 窒化アルミニウムのうちから選ばれた少なくと も 1種以上を主成分とする単結晶あるいは無定形を始めとする各種結晶状態の薄膜をあらかじ
め形成しさらにその上に単結晶薄膜を形成することで得られる薄膜基板の効果は、 この単結晶 薄膜が形成された薄膜基板を発光素子形成用基板として用いた場合さらに大きいものとなる。 発光素子は窒化ガリウム、 窒化インジウム、 窒化アルミニウムのうちから選ばれた少なくとも 1種以上を主成分として P型半導体層、 N型半導体層、 発光層など複数の薄膜層をェピタキシ ャル成長させ積層することで製造されるが、 このような発光素子の特性はェピタキシャル成長 させた薄膜、 すなわち単結晶薄膜の結晶性力稿いほど優れている。 このように発光素子を製造 する場合など、 窒化ガリウム、 窒化インジウム、 窒化アルミニウムのうちから選ばれた少なく とも 1種以上を主成分とする薄膜をより高い結晶性を有する単結晶薄膜として形成することが 求められる場合は、 上記のように本発明による単結晶薄膜が形成された薄膜基板を用いること がより効果的となる。 なお、 本発明による単結晶薄膜が形成された薄膜基板の中には上記窒化 アルミニウムを主成分とする焼結体からなる基板に窒化ガリウム、 窒化インジウム、 窒化アル ミニゥムのうちから選ばれた少なくとも 1種以上を主成分とする単結晶、 無定形、 多結晶、 配 向性多結晶など各種結晶状態の薄膜をあらかじめ形成しさらにその上〖こ単結晶薄膜を形成する ことで得られる薄膜基板だけでなぐ 窒化アルミニウムを主成分とする焼結体からなる基板に 窒化ガリウム、 窒化インジウム、 窒化アルミニウムのうちから選ばれた少なくとも 1種以上を 主成分とする単結晶薄膜を直接形成することにより得られる薄膜基板も含まれる。 このように 本発明による薄膜は自立したバルク材料とは異なり各種セラミック材料を主成分とする焼結体 からなる基板に固着され一体化された状態で存在し得るものである。
本発明による窒化アルミ二ゥムを主成分とする焼結体からなる基板には上記のように単結晶 だけに限らず無定形状態のもの、 多結晶状態のもの、 あるいは配向性多結晶状態のものなど各 種結晶状態の窒化ガリウム、 窒化インジウム、 窒化アルミニウムのうちから選ばれた少なくと も 1種以上を主成分とする薄膜を直接形成できる。本発明において重要なことは窒化ガリウム、 窒化インジウム、 窒化アルミニウムのうちから選ばれた少なくとも 1種以上を主成分とする単 結晶の薄膜を形成するということであり、 たとえ各種結晶状態の薄膜が形成できたとしても単 結晶状態のものが形成し得ない基板を用いることは好ましくない。 すなわち本発明は窒化ガリ ゥム、 窒化インジウム、 窒化アルミニウムのうちから選ばれた少なくとも 1種以上を主成分と する単結晶薄膜を形成し得る基板を提供すること、 及び窒化ガリウム、 窒化インジウム、 窒化 アルミニウムのうちから選ばれた少なくとも 1種以上を主成分とする少なくとも単結晶薄膜が 形成された薄膜基板を提供すること、 が大きな目的である。 上記のように本発明による窒化ァ ルミニゥムを主成分とする焼結体からなる基板には少なくとも単結晶状態の窒化ガリゥム、 窒 化ィンジゥム、 窒化アルミニウムのうちから選ばれた少なくとも 1種以上を主成分とする薄膜 が 1£接形成できる。このように本発明による薄藤成用基板は窒化ガリウム、窒化インジウム、 窒化アルミニウムのうちから選ばれた少なくとも 1種以上を主成分とする単結晶薄膜が直接形 成し得る優れたものである。 しかしながら本発明による薄膜形成用基板を用いた実際の使用形 態において、 必ずしも上記窒化ガリウム、 窒化インジウム、 窒化アルミニウムのうちから選ば れた少なくとも 1種以上を主成分とする単結晶薄膜を形成するための基板としてだけに限定さ れるものではない。 本発明による窒化アルミニウムを主成分とする焼結体からなる薄膜形成用 基板には単結晶以外に無定形、 多結晶、 配向性多結晶など各種結晶状態の窒化ガリウム、 窒化 ィンジゥム、 窒化アルミニウムのうちから選ばれた少なくとも 1種以上を主成分とする薄膜も 直接形成し得る。 本発明による窒化アルミニウムを主成分とする焼結体からなる薄膜形成用基 板は窒化ガリウム、 窒化インジウム、 窒化アルミニウムのうちから選ばれた少なくとも 1種以 上を主成分とする単結晶状態の薄膜を形成するためだけでなぐ 無定形、 多結晶、 配向性多結 晶など各種結晶状態の窒化ガリウム、 窒化インジウム、 窒化アルミニウムのうちから選ばれた 少なくとも 1種以上を主成分と薄膜を形成するための基板としても実際使用できる。
上記のように本発明による単結晶薄膜を形成し得る窒化アルミニウムを主成分とする焼結体 は単結晶薄膜が形成できるだけでなぐ 無定形、 多結晶、 配向性多結晶など各種結晶状態の窒 化ガリウム、 窒化インジウム、 窒化アルミニウムのうちから選ばれた少なくとも 1種以上を主 成分とする薄膜が形成できる。 具体的にいえば本発明は、 1 ) 窒化アルミニウムを主成分とす る焼結体からなる基板に窒化ガリウム、 窒化インジウム、 窒化アルミニウムのうちから選ばれ た少なくとも 1種以上を主成分とする単結晶薄膜が形成されたもの、 2) 窒化アルミニウムを 主成分とする焼結体からなる基板に窒化ガリウム、 窒化インジウム、 窒化アルミニウムのうち から選ばれた少なくとも 1種以上を主成分とする無定形薄膜が形成されたもの、 3 ) 窒化アル ミニゥムを主成分とする焼結体からなる基板に窒化ガリウム、 窒化インジウム、 窒化アルミ二 ゥムのうちから選ばれた少なくとも 1種以上を主成分とする多結晶薄膜が形成されたもの、 4) 窒化アルミニウムを主成分とする焼結体からなる基板に窒化ガリウム、 窒化インジウム、 窒化 アルミニウムのうちから選ばれた少なくとも 1種以上を主成分とする配向性多結晶薄膜が形成 されたもの、 など窒化アルミニウムを主成分とする焼結体からなる基板に単結晶薄膜が形成さ れた薄膜基板以外の無定形薄膜あるいは多結晶薄膜あるいは配向性多結晶薄膜など各種結晶状 態の薄膜が形成された薄膜基板を提供することができる。
すなわち本発明は、 窒化ガリウム、 窒化インジウム、 窒化アルミニウムのうちから選ばれた 少なくとも 1種以上を主成分と薄膜を形成するための基板であって、 該基板は窒化アルミニゥ ムを主成分とする焼結体からなる薄膜形成用基板、 を含む。 さらに本発明は、 窒化アルミニゥ ムを主成分とする焼結体からなる基板に窒化ガリウム、 窒化インジウム、 窒化アルミニウムの うちから選ばれた少なくとも 1種以上を主成分とする薄膜が形成されていることを特徴とする 薄膜基板、 も含む。
本発明による窒化アルミニウムを主成分とする焼結体は薄膜形成用基概ぴ菌形成用基板 のどちらの用途にも等しく用いることができる。
本発明において、 窒化ガリウム、 窒化インジウム、 窒化アルミニウムのうちから選ばれた少 なくとも 1種以上を主成分とする単結晶、 無定形、 多結晶、 配向性多結晶など各種結晶状態の 薄膜を形成するにあたって特別な成膜 、要とせず前記のように通常の M〇 CVD (有機 金属化学 目 成長) 法、 MOVP E (有機金属気相ェピタキシャル成長) 法、 ハイドライ ド V P E (水素化物細工ピタキシャル成長) 法、 クロライド VP E (塩化物細工ピ夕キシ ャル成長) 法などを含むハライド VP E (ハロゲン化物気相ェピタキシャル成長) 法、 プラズ マ CVD法、その他の CVD (化学 目 成長)法、 MB E ½m泉エピタキシー)法など、 あるいはあらかじめ形成した目的成分を含む固体材料を原料としエキシマレーザーなどを用い たレーザーアブレーション法、 P LD (パルスレーザーデポジシ aン:パルスレーザー分解) 法、 あるいはスパッタリング法、 イオンプレーティング法、 蒸着法など目的とする化学成分の 少なくとも一部を含有する化合物や単体を化学的物理的に^ しあるいは^ せずそのままの 状態で気体、 イオンあるいは 線とし難前記以外の化合物と反応させあるいは反応させず いったん目的とする化学成分を含む成分を気相とした後目的とする組成の薄膜を成長させる方 法であればどのようなものでも任意に適用できる。 単結晶状態、 無定形状態、 多結晶状態、 配 向性多結晶状態など各種結晶状態の薄膜作製用の原料としてはトリメチルガリゥム、 トリエチ ルガリウム、 トリイソブチルガリウム、 卜リメチリレインジゥム、 トリェチルインジウム、 トリ イソブチルインジウム、 トリメチルアルミニウム、 トリェチルアルミニウム、 トリイソブチル アルミニウムなどの有機金属化合物、 塩化ガリウム、 塩化インジウム、 塩化アルミニウムなど の塩化物や:^匕ガリウム、 : ¾ί匕インジウム、 匕アルミニウムなどの 匕物を含むガリウム、 インジウム、 アルミニウムのハロゲン化物、 ジェチルガリゥムクロライド、 ジ工チルインジゥ ムクロライド、 ジェチルアルミ二ゥムク口ライドなどのハロゲン元素を含むガリゥム、 インジ
ゥ厶、 アルミニウムの有衞匕合物、 窒化ガリウム、 窒化インジウム、 窒化アルミニウムなどの 窒化物、 ガリウム、 インジウム、 アルミニウムなどの純金属、 その他ドーピング元素用として S i、 あるいは S iH4、 S iHC 13、 S i (C2H5) 4などのシラン化合物、 S i C 14、 S i B r4などシリコンのハロゲン化物、 S i 3N4、 S i Cなどのシリコン化合物、マグネシウム、 ベリリウム、 カルシウム、 亜鉛、 カドミウム、 ゲルマニウムなどの金属及びジアルキルべリリ ゥム (例えばジメチルベリリウムなど)、 ジアルキルマグネシウム (例えばジメチルマグネシゥ ムなど) やビス—シクロペンタジェニルマグネシウム (MgCp2)、 ビス一シクロペンタジェ 二ルカルシゥム (CaCp2)、 ジェチル亜鉛、 ジメチルカドミウム、 テトラメチルゲルマン、 BeC l2、 BeBr2、 MgC l2、 MgBr2、 CaC l2、 CaBr2、 ZnC l2、 ZnB r 2、 CdC l2、 CdBr2、 GeC l4、 GeBr 4など該金属を含む有機金属化合物ゃノヽロゲン 化物などの化合物、 あるいは炭素、 シリコン、 セレン、 テルル、 酸素などの非金属及び該非金 属を含む化合物、 など各種化合物が使用できる。 MOCVD法、 MOVPE法では例えばトリ メチルガリゥム、 トリメチルインジゥム、 トリメチルアルミ二ゥムなどの有機化合物が主原料 として用いられる。 また、 クロライド VPE、 ハライド VP E法では例えば塩化ガリウム、 塩 化インジウム、 塩化アルミニウムなどのノ、ロゲン化物が主原料として用いられる。 上記 MOC VD法、 MOVPE法、 ハイドライド VPE法、 クロライド VPE法などを含むハライド VP E法、 プラズマ CVD法、 その他の CVD法、 MBE法など、 原料を気体状態として薄膜を形 成する方法において原料との反応ガスとしては通常アンモニアあるいは窒素が単独であるいは 混合された状態で使用される。 原料を気体状態とし反応部に搬送するキヤリァガスとしては水 素、 アルゴンあるいは窒素などが戦であるいは混合された状態で使用される。 結晶性の優れ た単結晶薄膜を形成するためには前記キャリアガスとしては少なくとも水素を含むものを用い ることがより好ましい。 薄膜形成チャンバ一内の雰囲気としては通常アンモニア、 水素、 アル ゴン、 窒素などが常圧下あるいは減圧下で用いられる。 また、 スパッタリング法により薄膜を 形^ Tる場合は上記各種原料をターゲットとして形成したものが用いられる。 このような方法 により窒化ガリゥム、 窒化ィンジゥム、 窒化アルミニゥムのうちから選ばれた少なくとも 1種 以上を主成分とする薄膜を単結晶、 無定形、 多結晶、 配向性多結晶など各種結晶状態で任意に 得ることができる。
なお、 窒化ガリウム、 窒化インジウム、 窒化アルミニウムのうちから選ばれた少なくとも 1 種以上を主成分とする単結晶薄膜を形成する場合は、 例え ^MOCVD法あるいは八ライド V PE法などのように原料としては目的とする組成の金属成分を含む化合物 (窒化ガリウムの場 合はガリウム成分を含む化合物、 例えばトリメチルガリウム、 三塩化ガリウムなど、 あるいは 窒化ィンジゥムの場合はィンジゥム成分を含む化合物、 例えばトリメチルインジゥム、 三塩化 インジウムなど、 あるいは窒化アルミニウムの場合はアルミニウム成分を含む化合物、 例えば トリメチルアルミニウム、 塩化アルミニウムなど) を用い、 該化合物は一旦分解されてその後 アンモニアなどの反応ガスと窒化反応して目的とする組成のものが形成されるという過程を経 て単結晶薄膜の形成を行うという方法を用いることが好ましい。 セラミツク材料を主成分とす る焼結体に薄膜状の単結晶を形成する場合は、 バルク状ゃ塊状の単結晶を作製するときのよう に昇華法などにより目的とする組成の原料をそのまま用い単に該原料を高温で昇華させ平衡に 近い状態で単結晶を作製するという方法よりも前記のように目的とする組成の金属成分を含む 化合物を用い該化合物を一旦分解しその後窒化反応させて目的とする組成を得るという方法の ほうがより結晶性の高い単結晶が作製し得る。 その理由は、 セラミック材料を主成分とする焼 結体はあらゆる方向を向いた微結晶粒子から構成されているので 2 ^¾的な広がりを有する薄 膜状の単結晶を形成しょうとしたとき、 原料となる材料や化合物の選定の範囲が広くさらにセ ラミック材料を主成分とする焼結体からなる基板に対する原料や反応ガスなどの供給方向や供
給量あるいは基板温度などの制御が容易なため、 セラミック材料を主成分とする焼結体中に存 在するあらゆる方向を向いた微結晶粒子の結晶方向にしたがつた自発的な結晶成長でなく目的 とする方向に単結晶が成長するよう制御することが可能であるためと思われる (すなわち、 例 えば基板面に対して C軸が垂直な方向にだけ成長するように制御できる)。一方、 昇華法などの ように目的とする組成の原料をそのまま用いて高温で昇華させて単結晶を作製する方法では大 量の原料が昇華できそのためバルク状ゃ塊状などのように大型の単結晶を短時間で得る場合に は適していると思われる。 しかしながらセラミック材料を主成分とする焼結体からなる基板に 薄膜状の単結晶を得るには原料の選定範囲が狭く原料の供給方向や供給量などの制御が困難と なり易いので本発明による単結晶薄膜を作製する方法としては必ずしも適した方法であるとは 言えない。
また上記窒化ガリウム、 窒化インジウム、 窒化アルミニウムのうちから選ばれた少なくとも
1種以上を主成分とする薄膜を形成する場合の基板温度として薄膜の組成や薄膜形成法の相違 などにより 択し得る。 薄膜として単結晶を形成する場合は無定形、 多結晶、 配向性多結 晶などの結晶状態を有するものよりも通常基板温度を高めることが好ましく、 基板温度が低い 場合は単結晶薄膜が形成しにくくなる場合がある。 例えば、 通常基板 ¾gとして窒化ガリウム を主成分とする薄膜を形成する場合 4 0 0°C〜1 2 0 0°C、 窒化インジウムを主成分とする薄 膜を形成する場合 4 0 0 °C〜1 0 0 0 ° (:、 窒化アルミニウムを主成分とする場合は 5 0 :〜 1 5 0 0でで行うこと力壁ましい。 上記各薄膜において窒化ガリウムを主成分とする無定形、 多結晶、 配向性多結晶など単結晶以外の結晶状態の薄膜を形成する場合基板温度として 4 0 0 ° (:〜 9 0 0 °C、 単結晶薄膜を形成する場合は 7 0 0°C〜1 2 0 0 Τ3と基板温度を高めて行う ことが ましい。 また、 窒化インジウムを主成分とする無定形、 多結晶、 配向性多結晶など単 結晶以外の結晶状態の薄膜を形成する場合基板温度として 4 0 0 ° (〜 7 0 0 °C、 単結晶薄膜を 形成する場合は 5 0 0°C〜 9 0 0°Cと基板温度を高めて行うことが ましい。 また、 窒化アル ミニゥムを主成分とする無定形、 多結晶、 配向性多結晶など単結晶以外の結晶状態の薄膜を形 成する場合基板温度として 5 0 0 °C〜1 2 0 0 °C、 単結晶薄膜を形成する場合は 6 0 0 °C〜1 5 0 0 °Cと基板髓を高めて行うことが望ましい。 より具体的には例え ^MO CVD法、 MO V P E法により単結晶薄膜を形成する場合の基板 ¾として窒化ガリウムを主成分とする薄膜 では 9 0 0 °C〜1 1 0 0 °C、 窒化インジウムを主成分とする薄膜では 6 0 0 t〜 9 0 0 、 窒 化アルミニウムを主成分とする薄膜では 9 0 0 °C〜1 2 0 0 °Cの範囲とすることが好ましい。 クロライド VP E法あるいはハラィド V P E法により単結晶薄膜を形成する場合の基板 と して窒化ガリウム (G a N) を主成分とする薄膜では 9 0 0 °C〜1 2 5 0° (:、 窒化インジウム ( I nN) を主成分とする薄膜では 7 0 0 °C〜1 0 0 0°C、 窒化アルミニウム (A 1 N) 薄膜 では 1 0 0 01:〜 1 5 0 0 °Cとすることが好ましく、 1 1 0 0 °C以上とすることが結晶性の高 い単結晶薄膜が形成し得るのでより好ましい。 基板温度が上記例示した驢ょり低い低い場合 は通常単結晶薄膜が形成しにくくなり易い。 このように窒化ガリウム、 窒化インジウム、 窒化 アルミニウムのうちから選ばれた少なくとも 1種以上を主成分とする単結晶薄膜を形成する場 合基板温度を高めることが好ましぐ 無定形、 多結晶、 配向性多結晶などの結晶状態のものを 形成する場合基板温度を低くすることが好ましい場合が多い。
基板の加熱は各種ヒーターを用いた抵抗加熱、 高周波電源を用いた高周波加熱、 赤外線ラン プによる加熱、 など、 どのような方法でも用いることができる。
本発明においてどのような薄膜形成法を用いたとしても基板温度としては上記の範囲にだけ 限定されず、 窒化ガリウムを主成分とする薄膜を基板 として室温〜 4 0 0 、 窒化インジ ゥムを主成分とする薄膜を基板温度として室温〜 4 0 0°C、 窒化アルミニウムを主成分とする 薄膜を基板 として室温〜 5 0 0 、 といった比較的低温で形成できる。 このような方法の
例として例えばスパッタリング法、 イオンプレーティング法、 蒸着法などの方法を用いること で上記の比較的 显で薄膜が形成できる。 また、例えば気体状態の原料と反応ガスとにより薄膜 を形成する方法においても、 例えばアンモニアあるいは窒素などの反応ガスとして高周波 (例 えば周波数 2. 4 5 GH zのマイクロ波、 あるいは周波数 1 3 · 5 6 MH zのラジオ波、 など) や磁力などによりプラズマ化された状態のものを用いれば基板 が上記のように低温であつ ても良好な薄膜を得ることができる。
本発明において、 窒化アルミニウムを主成分とする焼結体からなる基板上に成長する窒化ガ リウム、 窒化インジウム、 窒化アルミニウムのうちから選ばれた少なくとも 1種以上を主成分 とする単結晶薄膜はその結晶系が六方晶 (H e x a g o n a l ) で表わされる。 上記 CVD法 などを用いた場合形成される単結晶薄膜は通常基板面に対して該六方晶の C軸方位でェピ夕キ シャル成長しやすい傾向を有する。 言い換えれば上記単結晶薄膜は基板面と C面とが平行な方 位でェピタキシャル成長しやすい傾向を有する。 これ 板上に形成した上記単結晶薄膜の X 線回折を行うと六方晶のミラー指数 (0 0 2) の格子面からの強い回折線が観測されるので、 上記単結晶薄膜は基板面に対して C軸方向にェピタキシャル成長していることが観測されるこ とから説明できる。 言い換えれば上記単結晶薄膜は基板面と C面とが平行にェピタキシャル成 長していることが観測されることから説明できる。 図 1にこの様子を示す。 図 1において窒化 アルミニウムを主成分とする焼結体からなる基板 1の上に窒化ガリウム、 窒化インジウム、 窒 化アルミニウムのうちから選ばれた少なくとも 1種以上を主成分とする単結晶薄膜 2が形成さ れている。 また、 図 1のように単結晶薄膜 2が基板面に対して C軸が垂直な方向に形成された 基板において該単結晶薄膜 2の表面に X線を照射すれば六方晶ウルッ鉱型結晶構造を有する窒 化アルミニウム結晶のミラ一指数 ( 0 0 2) のネ各子面からの回折線だけが得られる。 図 2にこ の様子を示す。 もし基板 1の上に形成された薄膜が単結晶でなく多結晶ィ匕した状態であれば図 2に示すような 晶のミラ一指数 ( 0 0 2 ) の格子面以外の例えば (1 0 0 ) 格子面からの 回折など複数の回折線が鶴されるので明確に区別できる。 なお、 配向性多結晶は結晶粒子が 特定の結晶軸の方向に揃った特殊な状態の多結晶体である。 このような配向性多結晶であって も単結晶とは比較的容易に区別することができる。 より具体的に言えば、 窒化ガリウム、 窒化 インジウム、 窒化アルミニウムのうちから選ばれた少なくとも 1種以上を主成分とする薄膜は ウルッ鉱型の結晶構造を有し、 例えば基板面に対して C軸が垂直な方向に形成された単結晶薄 膜は通常の X線回折 2 0 / 0スキャンを行えばミラー指数 (0 0 2) の格子面からの回折線だ けしか出現しない。 一方薄膜が例えば基板面に対して C軸が垂直な方向に形成された配向性多 結晶の場合も X線回折の 2 スキャンではミラー指数 (0 0 2) の格子面からの回折線だ けしか出現しない。 しかし、 単結晶薄膜の場合 C軸に平行なミラー指数 ( 1 0 0) の格子面を 固定して 2 θ /ψスキャンを行えばミラー指数 (1 0 0) の格子面からの回折線しか出現しな いが配向性多結晶薄膜の場合は C軸に平行な他の格子面例えばミラ一指数 (1 1 0 ) 格子面か らの回折線も出現するので形成された薄膜が単結晶かあるいは配向性多結晶かの相違は容易に 判定できる。 すなわち単結晶には C面内回転が見られないのに対して配向性多結晶薄膜の場合 は C面内で結晶の回転が見られる。 これは単結晶の場合均質で一体化しており結晶粒子として の境界がないのに対して配向性多結晶は結晶粒子の集合体でありそれぞれの結晶粒子において 特定方向には結晶軸 (例えば C軸) が揃っているが他の結晶軸 (例えば A軸) はそれぞれの結 晶粒子間で異なる方位を取っているためと思われる。 このように配向性多結晶は結晶粒子が特 定の結晶軸の方向に揃つた特殊な状態の多結晶体とも云える。 通常の多結晶薄膜は前記のよう に X線回折 2 スキャンを行えばミラー指数 ( 0 0 2)の格子面からだけでなく例えば(1 0 0 ) の格子面からの回折線も出現するので通常の多結晶薄膜と配向性多結晶薄膜とは容易に 区別することができる。 またもし基板 1の上に形成された薄膜が単結晶あるいは多結晶でなく
無定形状態であれば明確なピークを持った回折線が得られず回折線はブロードなパターンとな るので単結晶あるいは多結晶あるいは配向性多結晶と明確に区別できる。 図 1において該単結 晶薄膜 2は C軸方向に成長し易くその成長方向は基板面に対して垂直な方向であり、 それはす なわち基板面と水平な方向が該単結晶薄膜 2の C面方向となる。 本発明において窒化アルミ二 ゥムを主成分とする焼結体からなる基板に形成される窒化ガリウム、 窒化インジウム、 窒化ァ ルミニゥムのうちから選ばれた少なくとも 1種以上を主成分とする単結晶薄膜の C軸は基板面 に対して垂直な方向に自発的に成長し易い。 しかしながら上記窒化アルミニウムを主成分とす る焼結体からなる基板を使用した場合でも薄膜の成長方法を纖工夫すれば窒化ガリウム、 窒 化インジウム、 窒化アルミニウムのうちから選ばれた少なくとも 1種以上を主成分とする単結 晶薄膜の C軸を基板面に対して水平な方向に形成し得る。 例えば上記基板温度を最初低めに設 定し徐々に を上げながら薄膜形成用の原料ガスを基板に対して水平な方向から供給するな どの工夫を行えば窒化ガリウム、 窒化インジウム、 窒化アルミニウムのうちから選ばれた少な くとも 1種以上を主成分とする単結晶薄膜の C軸を基板面に対して水平な方向に形成し得る。 この様子を図 4に示す。 図 4は窒化アルミニウムを主成分とする焼結体からなる基板 1に形成 された窒化ガリウム、 窒化インジウム、 窒化アルミニウムのうちから選ばれた少なくとも 1種 以上を主成分とする単結晶薄膜 2の C軸が基板面に対して水平な方向に形成されている (すな わち C面が基板面に対して垂直な方向に形成されている) ことを示す。 本発明において X線口 ッキングカーブによる窒化ガリウム、 窒化インジウム、 窒化アルミニウムのうちから選ばれた 少なくとも 1種以上を主成分とする単結晶薄膜の結晶性の評価は特に断らない限り図 1に示す ような基板面に対して C軸が垂直な方向に成長したものを用いて行った。 なお、 窒化アルミ二 ゥムを主成分とする焼結体からなる基板 1だけで表面の X線回折を行えば J C P D S ( J o i n t C omm i t t e e o n P owd e r D i f f r a c t i o n S t a n d a r d s ) ファイレ番号 2 5 - 1 1 3 4に記された粉末状 A 1 Nに相当する回折線が得られ焼結体 中の窒化アルミニウム粒子は特定の方向でなくあらゆる方向を向いた多結晶状態であることを 示している。 なお、 図 1、 図 2及び図 4において例示された基板の形状は円形であるが本発明 において使用できる基板の形状は円形だけでなく正方形、 長方形、 あるいはその他多角形など 任意の形状のものが使用できる。 また、 図 1、 図 2及び図 4に例示された本発明による窒化アル ミニゥムを主成分とする焼結体からなる薄膜形成用基板及び窒化アルミニウムを主成分とする 焼結体を用いることで作製される薄膜基板は焼結体およぴ 膜作製において通常用いられてい る方法を用いることで任意の大きさのものが、作製できる。すなわち焼結体の場合例えば外形 0. 0 l mm〜l 0 0 0 mm、 厚み 1 ΠΙ〜2 0 mm程度のものは容易に作製できる。
また本発明において窒化アルミニウムを主成分とする焼結体に形成された窒化ガリゥム、 窒 化インジウム、 窒化アルミニウムのうちから選ばれた少なくとも 1種以上を主成分とする単結 晶、 無定形、 多結晶、 配向性多結晶など各種結晶状態の薄膜と窒化アルミニウムを主成分とす る焼結体とは強固に接合し、 形成された薄膜内のクラックゃ該薄膜と窒化アルミニウムを主成 分とする焼結体との接合界面での剥離などは見られない。 接合性については例えば形成した上 記薄膜に粘着テープを接着し引き剥がしテストを行っても該薄膜と窒化アルミニウムを主成分 とする焼結体との接合界面での剥離や破壊は見られない。また窒化ガリウム、窒化インジウム、 窒化アルミニウムのうちから選ばれた少なくとも 1種以上を主成分とする単結晶、 無定形、 多 結晶、 配向性多結晶など各種結晶状態の薄膜と窒化アルミニウムを主成分とする焼結体との間 の接合性は通常垂直引張り強度で 2 K g Zmm2以上でありさらに垂直引張り強度 4 K g /m m2以上の接合のものも得られる。
窒化ガリウム、 窒化インジウム、 窒化アルミニウムのうちから選ばれた少なくとも 1種以上 を主成分とする単結晶薄膜のうち窒化ガリゥムおよび窒化ィンジゥムを主成分とする単結晶薄
膜〖こおいて含まれる単結晶状態の薄膜の結晶性を上記のように X線回折により判定する場合は 六方晶ウルッ鉱型結晶構造を有する該単結晶薄膜のミラー指数 (002) の格子面からの回折 線と下地の窒化アルミニウムを主成分とする焼結体からなる基板の六方晶のミラ一指数 (00 ) の格子面からの回折線とは明確に区別できるので形成した該単結晶薄膜のほとんどすべて の厚みのものに X線回折法が結晶性の判定に使用できる。 これは窒化ガリウム、 窒化インジゥ ム、 窒化アルミニウムは同じ六方晶に属するウルッ鉱型の結晶構造をもっていても格子定数が 少しずつ異なるため X線回折による六方晶のミラー指数 (002) の格子面からの回折線の位 置が容易に判別できる程度に異なるからである。 特性 X線として CuK«線 (波長 1. 542 A) を用いたとき下地窒化アルミニウム焼結体製基板のミラ一指数 (002) の格子面からの 回折線は回折角 0 =17. 65° 〜18. 45。 、 窒化ガリウム単結晶薄膜のミラー指数 (0 02) の格子面からの回折線は回折角 0=17. 20° 〜17. 53° 、 窒化インジウム単結 晶薄膜のミラー旨数 (002)の格子面からの回折線は回折角 0 =15. 55° 〜15. 88° 付近の範囲で現れるからであり、 これらの回折線どうし判定を不可能にするような重なり合い が生じることは実質的にない。 一方、 窒化アルミニウムを主成分とする単結晶薄膜のミラー指 数 (002) の格子面からの回折線は回折角 9 =17. 88° 〜18. 20。 の範囲にある。 したがって上記単結晶薄膜のうち窒化アルミニウムを主成分とする単結晶薄膜の結晶性を X線 回折により判定する場合形成されている該単結晶薄膜の厚みが薄くなれば X線が該単結晶薄膜 を透過し下にある窒化アルミニウムを主成分とする焼結体からの回折線と重なり合いその影響 が見られるようになる。 本発明においては使用した特性 X線は透過エネルギーを小さく抑える ために波長の比較的長い C rKa線 (波長 2. 29 lA)、 あるいは CuKaを用い、 X線発生 への加速電圧をできるだけ小さくすることで対応した。 X線回折により窒化アルミニゥム を主成分とする単結晶薄膜の結晶性を判定する場合、 上記のような工夫によって下地の窒化ァ ルミニゥムを主成分とする焼結体からの回折の影響が排除できる限界の単結晶薄 みは 50 0 nm程度である。 500 nm以下、 5 nm程度までの厚みの窒化アルミニウムを主成分とす る薄膜の単結晶性の判定には例えば; HEED (反射高速電子線回折) などの電子線回折を併 用し、 基板である窒化アルミ二ゥムを主成分とする焼結体からの影響が無いように考慮した。 したがって本発明において窒化アルミニウムを主成分とする焼結体からなる基板上へ形成する 窒化アルミニウムを主成分とする単結晶薄膜のミラ一指数 (002) の格子面の X線回折ロッ キングカーブの半値幅による結晶性の評価は通常該単結晶薄膜の厚み 500 nm以上好ましく は 1000 nm以上にて行った。
本発明により形成された窒化ガリウム、 窒化インジウム、 窒化アルミニウムのうちから選ば れた少なくとも 1種以上を主成分とする薄膜は 0. 5 nm程度の厚みのものが形成できるがこ のような少なくとも 0. 5 nm程度の厚みのものでも単結晶として形成されているものと考え られる。 本発明において上記の薄膜は単結晶だけでなく無定形、 多結晶、 配向性多結晶など各 種結晶状態のものも形成できる。 これら薄膜においてその厚みは 0. lnm〜0. 2nm程度 の厚みのものも形成し得る。 また、 窒化アルミニウムを主成分とする焼結体を薄膜形成用基板 として使用し上記の薄膜を直接該基板に形成した場合は薄膜の厚みは 0. 5 nm以上であるこ とが、好ましい。
本発明において、 窒化アルミニウムなど各種セラミック材料を主成分とする焼結体からなる 薄膜形成用基板を用いることにより窒化ガリウム、 窒化インジウム、 窒化アルミニウムのうち から選ばれた少なくとも 1種以上を主成分とする単結晶、 無定形、 多結晶、 配向性多結晶など 各種結晶状態の薄膜が形成し得る。また上記薄藤成用基板に窒化ガリウム、窒化インジウム、 窒化アルミニウムのうちから選ばれた少なくとも 1種以上を主成分とする単結晶薄膜が直接形 成された薄膜基板、 及び窒化ガリウム、 窒化インジウム、 窒化アルミニウムのうちから選ばれ
た少なくとも 1種以上を主成分とする単結晶、 無定形、 多結晶、 配向性多結晶など各種結晶状 態の薄膜があらかじめ形成された薄膜基板に窒化ガリウム、 窒化インジウム、 窒化アルミニゥ ムのうちから選ばれた少なくとも 1種以上を主成分とする単結晶薄膜をさらに形成した薄膜基 板を得ることができる。 さらに前記薄膜基板には窒化ガリウム、 窒化インジウム、 窒化アルミ ニゥムのうちから選ばれた少なくとも 1種以上を主成分とする単結晶、 無定形、 多結晶、 配向 性多結晶など各種結晶状態の薄膜が形成し得る。 本発明において上記薄膜のうち単結晶が形成 し得る基板には通常無定形、 多結晶、 配向性多結晶など各種結晶状態の薄膜も比較的容易に形 成できる。 本発明においては上記薄膜形成用基板及ぴ蒋膜基板が優れているかどうカゝの判定を 該基板に単結晶薄膜を形成しこの単結晶薄膜の結晶性を評価することにより行った。
本発明において窒化ガリウム、 窒化インジウム、 窒化アルミニウムのうちから選ばれた少な くとも 1種以上を主成分とする薄膜の結晶状態は前記のように X線回折により分析することで 容易に判定できる。 すなわち上記薄膜が単結晶であれば該単結晶薄膜の C軸が基板面に対して 垂直な方位に形成されている場合六方晶ウルッ鉱型結晶のミラー指数 ( 0 0 2) の格子面から の回折線しか検出されない。 また該単結晶薄膜の C軸が基板面に対して水平な方位に形成され ている場合六方晶ウルッ鉱型結晶のミラ一指数 (1 0 0 ) の格子面からの回折線しか検出され ない。 上記薄膜が多結晶であればミラ一指数 (0 0 2)、 あるいは (1 0 0) などの格子面から の複数の回折線が検出されるので容易に判別できる。 また上記薄膜が無定形であれば明確な回 折ピークは検出されずプロ一ドな回折パターンとなるので容易に判別できる。 なお本発明によ る窒化アルミニウムを主成分とする焼結体を薄膜形成用基板として用いた場合窒化ガリウム、 窒化インジウム、 窒化アルミニウムのうちから選ばれた少なくとも 1種以上を主成分とする単 結晶薄膜は C軸が基板面に対して垂直な方位に形成されやすいので通常は六方晶ゥルツ鉱型結 晶のミラー指数 ( 0 0 2 ) の格子面からの回折線しか検出されない。
本発明において該単結晶薄膜の結晶性 は通常特に断らない限り該単結晶薄膜のミラ一指 数 (0 0 2 ) の格子面の X線回折ロッキングカーブの半値幅を測定して行った。 使用した特性 X線は C u K a線 (波長 1. 5 4 2 A) である。 また、 本発明においては特に断らない限りミ ラー指数 (0 0 2) の格子面の X線回折ロッキングカーブの半値幅は通常の ωスキャンによつ て測定されたものであり、 単位として秒 (a r c s e c a n t ) で示す。 なおこのような結晶 性の 面を行うにあたり、 該単結晶薄膜形成用の基板として用いられる窒化アルミニウムなど 各種セラミック材料を主成分とする焼結体からなる基板表面は特に断らない限り平均表面粗さ
R a = 3 0 nm前後の鏡面状態としたものを使用した。
本発明による薄膜形成用基板は窒化アルミニウムを主成分とする焼結体であればよいのであ つて基板に直接窒化ガリゥム、 窒化ィンジゥム、 窒化アルミニゥムのうちから選ばれた少なく とも 1種以上を主成分とする単結晶を含む各種結晶状態の薄膜が形成できる。 また、 上記窒化 アルミニウムを主成分とする焼結体において光透過性を有するものを用いることが基板に形成 される窒化ガリウム、 窒化インジウム、 窒化アルミニウムのうちから選ばれた少なくとも 1種 以上を主成分とする単結晶薄膜の結晶性を高め易い。 このような焼結体の中でも少なくとも可 視光領域において 性カ犒いものほど形成される窒化ガリウム、 窒化インジウム、 窒化ァ ルミニゥムのうちから選ばれた少なくとも 1種以上を主成分とする単結晶薄膜の結晶性が高ま るので好ましい。可視光領域における 性は波長 3 8 0 nm〜8 0 0 nmの範囲において、 直径 2 5. 4mm厚み 0 · 5 mmの円盤状で表面を平均粗さ R a = 3 0 nm程度の鏡面に研磨 した焼結体で ½¾i率 1 %以上のものが好ましい。 光¾ 率 1 %以上の窒化アルミニウムを主 成分とする焼結体からなる基板を用いることで直接その上に形成された窒化ガリウム、 窒化ィ ンジゥム、 窒化アルミニウムのうちから選ばれた少なくとも 1種以上を主成分とする単結晶薄 膜の結晶性はミラー指数 (0 0 2 ) の格子面の X線回折ロッキングカーブの半値幅が 3 0 0秒
以下と良好なものが得られ易い。 過率が 5 %以上の窒化アルミニウムを主成分とする焼結 体からなる基板を用いることで上記 X線回折ロッキングカーブの半値幅が 2 4 0秒以下とより 良好なものが得られ易い。 さらに ¾¾ 率が 1 0 %以上の窒化アルミニウムを主成分とする焼 結体からなる基板を用いることで上記 X線回折ロッキングカーブの半値幅が 2 0 0秒以下とさ らに良好なものが得られ易くさらに好ましい。 本発明において可視光領域における 率と は上記波長 3 8 0 nm〜8 0 0 nmの範囲の光における光¾¾率のことであり、 本発明におい ては通常特に断らない限り波長 6 0 5 nmの光で測定された¾¾1率の値を用いた。 また本発 明による上記のような可視光領域における) 過率を有する窒化アルミニウムを主成分とする 焼結体は波長 2 0 0 nm〜3 8 0 nmの紫外領域の光においても同様な) ¾® 率を有し、 その 光 »率は 1 %以上のものが得られる。 すなわち本発明において、 窒化アルミニウムを主成分 とする焼結体.の中でも少なくとも波長 2 0 0 nm〜8 0 0 nmの範囲の光に対する光透過性が 高いものほど形成される窒化ガリウム、 窒化インジウム、 窒化アルミニウムのうちから選ばれ た少なくとも 1種以上を主成分とする単結晶薄膜の結晶性が高まるので好ましい。 また本発明 による可視) 率を有する窒化アルミニウムを主成分とする焼結体は波長 2 5 0〜3 8 0 n mの範囲の紫外光においては 5 %以上の 率を有するものが得られ、 波長 3 0 0〜 3 8 0 nmの範囲の紫外光においては 1 0 %以上の光 率を有するものが得られる。 本発明による 窒化アルミニウムを主成分とする焼結体は上記波長 2 0 0 nm〜3 8 0 nmの紫外領域におい て 4 0 %以上の ¾¾率を有するものが得られ、 さらに最大 6 0〜8 0 %あるいは 8 0 %以上 の¾¾率のものも得られる。 上記のように本発明による窒化アルミニウムを主成分とする焼 結体からなる基板は紫外光に対する透過性も有するので前記本発明による基板に例えば窒化ガ リウム、 窒化インジウム、 窒化アルミニウムのうちから選ばれた少なくとも 1種以上を主成分 とする単結晶薄膜を用いて紫外線発光の素子を形成すれば素子から発光された紫外線が基板部 分で吸収されることが少ないので発光素子の発光効率が高まるという効果が得られ好ましい。 このように本発明において窒化アルミニウムを主成分とする焼結体からなる基板は 2 0 O n m〜8 0 0 nmの範囲の光において少なくとも 1 %以上の光透過率を有しこのような光透過率 を有する基板を用いることでより優れた結晶性を有する窒化ガリウム、 窒化インジウム、 窒化 アルミニウムのうちから選ばれた少なくとも 1種以上を主成分とする単結晶薄膜が形成できる ことが明らかにされた。 また本発明において、 少なくとも 1 %以上の光 ¾i率を有する窒化ァ ルミ二ゥムを主成分とする焼結体を基板として用いることで窒化ガリウム、 窒化インジウム、 窒化アルミニウムのうちから選ばれた少なくとも 1種以上を主成分とする単結晶以外の無定形、 多結晶、 配向性多結晶など各種結晶状態の薄膜も形成できる。
以下本発明において特に断らない限り光透過率は波長 6 0 5 nmの光において測定されたも のである。 本発明による光腿性を有する窒化アルミニウムを主成分とする焼結体は通常少な くとも波長 3 8 0 nm〜8 0 0 nmの範囲の可視光領域においてはどのような波長の光に対し ても波長 6 0 5 nmの光で測定された¾¾率とほぼ同様の光透過率を示す。 本発明による窒 化アルミニウムを主成分とする焼結体は波長 2 0 0 nm〜8 0 0 nmのすベての波長範囲の光 において波長 6 0 5 nm以外で波長 6 0 5 nmと同様の)16¾過率を有するとは限らないが波長 6 0 5 nmの光において測定された光 ¾1率を用いるだけで本発明による窒化アルミニウムを 主成分とする焼結体の性能例えば窒化ガリウム、 窒化インジウム、 窒化アルミニウムのうちか ら選ばれた少なくとも 1種以上を主成分とする単結晶薄膜を形成したときの結晶性などを代表 して判別できる。 すなわち)1 έ¾過性を有する窒化アルミニウムを主成分とする焼結体の基板と しての特性を上記波長 6 0 5 nmの光において測定した光透過率で代表して判定し得る。
本発明において、 光 ¾ 性を有する窒化アルミニウムを主成分とする焼結体 tt®常波長 2 0 0 nm以上の光に対して光腿性を示す場合が多い。 すなわち、 波長 2 0 0 nm〜2 5 0 nm
の範囲の光に対して髓過性を示し始め、 波長 2 5 0 nm〜3 5 0 nmの範囲の光に対して急 激 (こ¾¾§性が上昇し紫外光から可視光領域入る境界領域にある波長 3 5 0 nm〜4 0 0 nm 以上の光に対してはほぼ一定の光 率を有する傾向がある。 本発明において窒化アルミニゥ ムを主成分とする焼結体の 過率とは特に断らない限り波長 6 0 5 nmの光に対して測定さ れた¾¾§率を意味する。 通常本発明において光翻性を有する窒化アルミニウムを主成分と する焼結体では波長 2 0 0 nm〜3 8 0 nmの紫外光で測定された光 率より波長 3 8 0 η m〜8 0 0 nmの範囲の可視光における光 ¾i 率の方が大きい。 具体的には通常本発明におい て¾¾生を有する窒化アルミニウムを主成分とする焼結体において波長 2 0 0 nm〜3 8 0 nmの紫外光で測定された光透過率が 1 %以上であれば波長 3 8 0 nm〜8 0 0 nmの範囲の 可視光における光透過率は 1 %より大きなものとなる。 したがって波長 2 0 0 nm〜3 8 0 η mの紫外光で測定された ¾¾ϋ率が 1 %以上の ¾¾ 性を有する窒化アルミニウムを主成分と する;^結体を基板として用いたときさらに優れた結晶性を有する窒化ガリゥム、 窒化ィンジゥ ム、 窒化アルミニウムのうちから選ばれた少なくとも 1種以上を主成分とする単結晶薄膜が直 接形成し得る。 このように耀過率として波長 6 0 5 nm以外の光に対する測定値を用いなく ても波長 6 0 5 nmの光に対する ¾¾i率を ffiJiしておけば本発明による窒化アルミニウムを 主成分とする焼結体の性能すなわち窒化ガリウム、 窒化インジウム、 窒化アルミニウムのうち から選ばれた少なくとも 1種以上を主成分とする単結晶薄膜を形成したときの結晶性を代表し て判別することが容易となり、 さらに例えば発光軒を構成する窒化ガリウム、 窒化インジゥ ム、 窒化アルミニウムのうちから選ばれた少なくとも 1種以上を主成分とする薄膜からなる少 なくとも N型半導体層及び発光層及び P型半導体層を含む積層体を形成するための基板(以下、 特に断らない限り単に 「発光素子作製用基 ¾J と言う) として用いたとき作製される発光素子 の発光効率を判定し得る。
本発明において、 波長 2 0 0 nm〜3 8 0 nmの範囲の紫外光における光 ¾ 率とは波長 2 0 0 nm〜3 8 0 nmの範囲におけるいずれか特定の波長に対する^ ¾ 率を意味する。 また、 本発明において特に断らない限り可視光とは波長 3 8 0 nm~ 8 0 0 nmの範囲の光であり、 紫外光とは波長 3 8 0 nm以下の光をいう。
本発明における光透過率の測定値は特に断らない限り直径 2 5. 4mm厚み 0. 5 mmの円 盤状で表面を鏡面に研磨した (通常は、 平均表面粗さ R a = 3 O nm程度) 窒化アルミニウム を主成分とする焼結体、 及びその他のセラミック材料を主成分とする焼結体 (例えば六方晶系 又は三方晶系のうちから選ばれた少なくともいずれかの結晶構造を有する材料を主成分とする 焼結体、 及ぴ 化ジルコニウム、 酸化マグネシウム、 アルミン酸マグネシウム、 酸化チタン、 チタン酸バリウム、 チタン酸ジルコン賺、 希土繊素酸化物、 酸化トリウム、 各種フェライ ト、 ムライト、 フォルステライト、 ステアタイト、 結晶化ガラスのうちから選ばれた少なくと も 1種以上を主成分とする焼結体、 など) を試料として用い、 通常分光光度計などを用いて所 定の波長の光を上記焼結体試料に当て、 入射した光の強度と透過した光の強度を測定しその比 を百分率で表わしたものである。 波長としては通常特に断らない限り 6 0 5 nmのものを用い て測定されたものである。 本発明における光透過率は上記測定用試料を積分球の内部にセット して全透過光を集めこの全 ¾1光と入射光との強度比を百分率で表した全 ¾ 率として求めた ものである。
ガラスなどの透明体の光透過率は通常直線透過率として求められるが、 一般に窒化アルミ二 ゥムを主成分とする焼結体などのセラミック材料の光透過率は入射光が焼結体内部で散乱され 直線的に ¾i されず、 散乱された状態であらゆる方向へ翻される。 したがって透過光の強度 はこのような方向性のない散乱光をすベて集めたものとなる。 本発明において窒化アルミニゥ ムを主成分とする焼結体及びその他のセラミック材料を主成分とする焼結体の光透過率はこの
ような全 ¾i率として測定されたものであり、 ガラスなどの透明体の直線透過率とは異なる。 光 率は試料の厚みによつて変化し本発明による上記窒化アルミ二ゥムを主成分とする焼 結体、 及びその他のセラミック材料を主成分とする焼結体 (例えば六方晶系又は三方晶系のう ちから選ばれた少なくともいずれかの結晶構造を有する材料を主成分とする焼結体、 及び豫化 ジルコニウム、酸化マグネシウム、アルミン酸マグネシウム、酸化チタン、チタン酸バリウム、 チタン酸ジルコン酸鉛、 希土類 素酸化物、 酸化トリウム、 各種フェライト、 ムライト、 フォ ルステライト、 ステア夕イト、 結晶化ガラスのうちから選ばれた少なくとも 1種以上を主成分 とする焼結体、 など) を薄膜形成用基板、 薄膜基板、 あるいは発光素子作製用碁板などに用い る場合該基板の厚みを薄くして光 ¾i率を高めることは例えば発光素子の発光効率を高める上 で有効である。 通常薄膜形成用基板、 薄膜基板、 あるいは発光素子作製用基板などとしては厚 み 0. 0 l mm以上のものを用いることが り扱い上の強度の点からは好ましい。 又厚みが厚 くなると ¾¾1率が低下し易いので通常薄膜形成用基板、 薄膜基板あるいは発光素子作製用基 板などとしては厚み 8. Omm以下のものを用いることが好ましい。 本発明において上記窒化 アルミニウムを主成分とする焼結体及びその他のセラミック材料を主成分とする焼結体はその 厚みが少なくとも 0. 0 1 mm〜 8. Ommの範囲において実際に使用される状態の薄膨成 用基板、 薄膜基板あるいは発光素子作製用基板などが光 性を有していれば有効である。 す なわち、 上記窒化アルミニウムを主成分とする焼結体及びその他のセラミック材料を主成分と する焼結体はその厚みが少なくとも 0. 0 1 mm〜8. Ommの範囲あるいはそれ以外であつ ても実際に使用される状態での光 ¾1率が少なくとも 1 %以上であればよいのであって、 例え ば発光素子作製用基板として実際に厚み 0. 1 mmあるいは 2. Ommなど厚みが必ずしも 0. 5 mmではないものであっても光 ¾i性を有し光 ¾1率が少なくとも 1 %以上であれば作製さ れる発光素子の発光効率は向上し易い。
本発明において、 窒化アルミニウムを主成分とする焼結体、 及びその他のセラミック材料を 主成分とする焼結体 (例えば六方蟲系又は三方晶系のうちから選ばれた少なくともいずれかの 結晶構造を有する材料を主成分とする焼結体、 及び 匕ジルコニウム、 酸化マグネシウム、 ァ ルミン酸マグネシウム、 酸化チタン、 チタン酸バリウム、 チタン酸ジルコン 、 希土 素 酸化物、 酸化トリウム、 各種フェライト、 ムライト、 フオルステライト、 ステアタイト、 結晶 化ガラスのうちから選ばれた少なくとも 1種以上を主成分とする焼結体、 など) の光 ¾ii性は 厚みには関係無い。 厚い状態では光 ¾i性を有しないものであっても薄くすることで光透過性 を有するものは本発明に含まれる。 すなわち、 例えば窒化アルミニウムを主成分とする焼結体 及びその他のセラミック材料を主成分とする焼結体の厚みが 0. 5 mmのとき光透過性を有し ないものであっても厚みを薄くすることで ¾¾i性が発現するものは本発明に含まれる。 また、 例えば窒化アルミニウムを主成分とする焼結体及びその他のセラミック材料を主成分とする焼 結体の厚みが 0. 5 mmより厚いとき光¾§性を有しないものであっても厚みを 0. 5mmと することで光透過性が発現するものは本発明に含まれる。 光 性を別の言葉で表現すれば、 本発明の光透過率として窒化アルミニウムを主成分とする焼結体及びその他のセラミック材料 を主成分とする焼結体の厚みには関係無ぐ 該焼結体の光透過率が 1 %以上であれば本発明に 含まれる。 すなわち、 例えば窒化アルミニウムを主成分とする焼結体及びその他のセラミック 材料を主成分とする焼結体の厚みが 0. 5mmのとき光透過率が 1 %より小さいものであって も厚みを薄くすることで)1 率が 1 %以上であるものは本発明に含まれる。 また、 例えば窒 化アルミニウムを主成分とする焼結体及びその他のセラミック材料を主成分とする焼結体の厚 みが 0. 5mmより厚いとき光透過率が 1 %より小さいものであっても厚みを 0. 5mmとす ることで光透過率が 1 %以上であるものは本発明に含まれる。
上記のように本発明による窒化アルミニウムを主成分とする焼結体及びその他のセラミック
材料を主成分とする焼結体の光 Mil性としては実際該焼結体が用いられている状態での 過 性が重要である。 したがって窒化アルミニウムを主成分とする焼結体及びその他のセラミック 材料を主成分とする焼結体として実際該焼結体が用いられている状態で) ^過性を有していれ ば本発明に含まれる。 別の表現をすれば、 本発明の光 ¾ 率としては窒化アルミニウムを主成 分とする焼結体及びその他のセラミック材料を主成分とする焼結体の厚みには関係無く、 該焼 結体の実使用状態での光顯率が 1 %以上であれば本発明に含まれる。 すなわち、 例えば窒化 アルミ二ゥムを主成分とする焼結体及びその他のセラミック材料を主成分とする焼結体の厚み が実使用状態で 0. 5mm以下あるいは 0. 5 mmより大きいとき光透過率が 1 %以上である ものは本発明に含まれる。
窒化アルミニウムを主成分とする焼結体及びその他のセラミック材料を主成分とする焼結体 の厚みが実使用状態で 0. 5 mmより薄い場合あるいは 0. 5 mmより厚い場合は基板厚み 0. 5 mmのとき測定した光透過率と異なり、 光¾1率は 0. 5 mmより薄い場合は 0. 5 mmの とき測定したより高くなり易く 0. 5 mmより厚い場合は 0. 5 mmのとき測定した光 ¾i率 より低くなり易い。 本発明においては上記のように実際に使用される状態で ¾¾i率が少なく とも 1 %以上の窒化アルミニウムを主成分とする焼結体及びその他のセラミック材料を主成分 とする焼結体を用いることが好ましい。
本発明において窒化アルミニウムを主成分とする焼結体からなる基板上に形成される窒化ガ リウム、 窒化インジウム、 窒化アルミニウムのうちから選ばれた少なくとも 1種以上を主成分 とする単結晶薄膜の結晶性はミラー指数 (0 0 2 ) の格子面の X線回折ロッキングカーブの半 値幅が 3 0 0秒以下である必要性は必ずしもない。 例えば上記 X線回折ロッキングカーブの半 値幅がブロードな結晶性のものでも表面弾性波素子用などの圧電膜ゃ回路基板用の «膜や誘 電膜、 あるいは光導波路用材料などの用途には問題なく使用できる。 このような用途には上記 X線回折ロッキングカーブの半値幅が 3 6 0 0秒以下程度であれば問題なく使用できる。 また 上記用途において窒化ガリゥム、 窒化ィンジゥム、 窒化アルミニゥムのうちから選ばれた少な くとも 1種以上を主成分とする薄膜の結晶性は場合によっては必ずしも単結晶でない無定形、 多結晶、 配向性多結晶などの結晶状態のものであっても使用し得る。 しかしながら窒化アルミ 二ゥムを主成分とする焼結体を基板として用いそこに形成される窒化ガリウム、 窒化インジゥ ム、 窒化アルミニウムのうちから選ばれた少なくとも 1種以上を主成分とする単結晶薄膜の上 に発光泰チを形成する場合、 あるいは該単結晶薄膜を直接発光素子構成層の一部として用いる 場合、 あるいは該単結晶薄膜をフィ一ルドエミッションディスプレイ (電界放出によるディス プレイ) の冷陰極材料として用いる場合などは該単結晶薄膜の結晶性は上記ミラ一指数 (0 0 2 ) の格子面の X線回折ロッキングカーブの半値幅が 3 0 0秒以下のシャープなものであるこ とが好ましい。
本発明において窒化アルミニウムを主成分とする焼結体からなる基板には直接窒化ガリウム、 窒化インジウム、 窒化アルミニウムのうちから選ばれた少なくとも 1種以上を主成分とする単 結晶を含む各種結晶状態の薄膜が形成できる。 さらに本発明において上記窒化アルミニウムを 主成分とする焼結体からなる基板に窒化ガリゥム、 窒化インジウム、 窒化アルミニウムのうち から選ばれた少なくとも 1種以上を主成分とする単結晶を含む各種結晶状態の薄膜を例えば発 光素子を製造する場合などのように 2以上の層構成として形成できる。 この 2以上の層で形成 された薄膜は各層において結晶状態、 組成、 あるいは厚みなどそれぞれ異なる状態で形成でき る。 本発明による 2層以上の薄膜層からなる薄膜基板は 2層以上の薄膜層のうち少なくとも 1 層以上は窒化ガリウム、 窒化インジウム、 窒化アルミニウムのうちから選ばれた少なくとも 1 種以上を主成分とする単結晶薄膜からなる。 本発明による薄膜基板を発光素子形成用基板など のように、 窒化ガリウム、 窒化インジウム、 窒化アルミニウムのうちから選ばれた少なくとも
1種以上を主成分とする単結晶薄膜を形成するために用いる場合など薄膜基板表面の薄膜は通 常単結晶であることが好ましい。本発明においては 2層以上から構成されている窒化ガリウム、 窒化インジウム、 窒化アルミニウムのうちから選ばれた少なくとも 1種以上を主成分とする単 結晶を含む各種結晶状態の薄膜においても形成されている単結晶薄膜においてそのミラ一指数 ( 0 0 2 ) の格子面の X線回折ロッキングカーブの半値幅が 3 0 0秒以下と、 シャープで結晶 性の高いものが得られ易い。
窒化アルミニウムを主成分とする焼結体からなる基板の可視光あるいは紫外光に対する舰 過率は 1 ) 焼結密度、 2 ) 焼結体内部の気孔の有無や大きさ、 3) 焼結助剤含有量、 4) 酸素 含有量、 5) 焼結助剤及び酸素以外の不純物含有量、 6) 焼結体中の窒化アルミニウム粒子の 大きさ、 あるいは 7 ) 焼結体中の窒化アルミニウム粒子の形状、 などといったセラミック特有 の複雑な要因で変化する。 通常は窒化アルミニウムを主成分とする焼結体からなる基板におい て 1 ) 焼結密度カ犒く、 2 ) 焼結体内部の気孔が少なくもしあつたとしてもサイズが小さく、 3 ) 焼結助剤量が必要最小量であるかもしくは焼結助剤を含まない、 4) 酸齢有量が少ない こと、 5 ) 焼結助剤以外の不純物含有量が少ないかもしくは含まない、 6) 焼結体中の窒化ァ ルミニゥム粒子が小さいか又は大きさが均一である、 あるいは 7 ) 焼結体中の窒化アルミニゥ ム立子の角が T又れた丸いものより多角形でお互いの粒子同士多角形の面や稜線、 あるいは多角 形の頂点での重なりが隙間なく緊密であるもの、 あるいは 8 ) 焼結体中の窒化アルミニウム粒 子が大きくても雄助剤などの A 1 N以外の成分が少なく A 1 Nとしての繊が高いもの、 9) 焼結体中の焼結助剤など A 1 N以外の成分が多くても窒化アルミニウム粒子が大きく成長した もの、 などの性状を有する窒化アルミニウム焼結体であれば ¾1視光に対する ¾¾ 率が 1 %以 上と高くなる傾向を有する。 したがつてこのような性状の窒化アルミ二ゥムを主成分とする焼 結体からなる基板を用いることで窒化ガリウム、 窒化インジウム、 窒化アルミニウムのうちか ら選ばれた少なくとも 1種以上を主成分とする単結晶薄膜の膜質、 結晶性は向上し易い。 元来窒化アルミニウムを主成分とする焼結体は焼結助剤や含有酸素量あるいはその他の不純 物量を制御することで謝云導率が室温において少なくとも 5 OWZmK以上であり、 通常は 1 0 OWZmK以上と高いものが得られる。 そのため窒化アルミニウムを主成分とする焼結体を 基材として用いて作製される発光素子はそこに加えられる電力を "がサフアイァの場合に比 ベて大きくできるので発光素子の発光出力が高まるという利点を有する。 上記の焼結助剤や酸 素あるいはその他の不純物を含む窒化アルミニウムを主成分とする焼結体の場合は室温におけ る熱伝導率が 1 5 OWZmK以上のものが容易に得られ、 窒化アルミニウムを主成分とする焼 結体を基材として製造される発光素子への投入電力をより高めることができるので好ましい。 また、 上記の焼結助剤や酸素あるいはその他の不純物を含む窒化アルミニウムを主成分とする 焼結体の場合は室温における熱伝導率が 1 7 OW/mK以上のものも容易に得られ、 窒化アル ミニゥムを主成分とする焼結体を として製造される発光素子への投入電力をさらに高める ことができるのでより好ましい。
本願発明者は窒化ガリウム、 窒化インジウム、 窒化アルミニウムのうちから選ばれた少なく とも 1種以上を主成分とする単結晶を含む各種結晶状態の薄膜を直接形成するための基板とし て窒化アルミニウム (A 1 N) 以外で炭化珪素 (S i C)、 窒化珪素 (S i 3N4)、 窒化ガリウ ム (G a N)、 酸化アルミニウム (A 1 203)、 酸化ジルコニウム (Z r 02)、 酸化亜鉛 (Z n 0)、 酸化マグネシウム (Mg O)、 酸化ベリリウム (B e O)、 アルミン酸マグネシウム (Mg A 1 204 :スピネル) などを主成分とする焼結体を検討してきた。 そのなかで炭化珪素、 窒化 珪素、 窒化ガリウム、 酸化亜鉛、 酸化ベリリウムなどの六方晶 (H e x a g o n a l ) 結晶構 造を有する力三方晶 (T r i g o n a l ) 結晶構造の酸化アルミニウムを主成分とする焼結体 が窒化ガリウム、 窒化インジウム、 窒化アルミニウムのうちから選ばれた少なくとも 1種以上
を主成分とする薄膜を単結晶化できる。 各炭化珪素、 窒化珪素、 窒化ガリウム、 酸化亜鉛、 酸 化ベリリウム基板、 酸化アルミニウムを主成分とする焼結体製基板においてその上に形成され る該単結晶薄膜の六方晶及び三方晶のミラ一指数 ( 0 0 2) 格子面のロッキングカーブの半値 幅は 3 6 0 0秒以下という結晶性を示し易い。 一方酸化ジルコニウム、 酸化マグネシウム、 ス ピネルを主成分とする焼結体からなる基板上に形成された窒化ガリウム、 窒化インジウム、 窒 化アルミニウムのうちから選ばれた少なくとも 1種以上を主成分とする薄膜は多結晶の状態で あり単結晶化しにくい。 これは酸化ジルコニウムの結晶系は正方晶 (T e t r a g o n a l ) もしくは立方晶 (C u b i c ) もしくは単斜晶 (Mo n o c 1 i n i c ) であり、 酸化マグネ シゥムとスピネルはそれぞれ立方晶 (C u b i c ) であるためと思われる。 酸化アルミニウム の結晶系は三方晶であるが六方晶としての分類も可能であるのでその上に直接形成される薄膜 が単結晶化できる焼結体は結局本質的には結晶系が六方晶及び六方晶として分類できる材料を 主成分とする基板だけであろうと本願発明者は考えている。 その理由は窒化ガリウム、 窒化ィ ンジゥム、 窒化アルミ二ゥム各薄膜の有する結晶構造はウルッ鉱型結晶であり該ゥルツ鉱型結 晶の属する結晶系は六方晶であり基板となる焼結体の主成分が六方晶系あるいは三方晶系ある いは六方晶系として分類できる結晶構造を有していれば上記窒化ガリゥム、 窒化ィンジゥム、 窒化アルミニウムのうちから選ばれた少なくとも 1種以上を主成分とする薄膜が自発的に単結 晶化し易いためと思われる。 本発明において窒化ガリウム、 窒化インジウム、 窒化アルミニゥ ムのうちから選ばれた少なくとも 1種以上を主成分とする単結晶薄膜を上記炭化珪素、 窒化珪 素、 窒化ガリウム、 酸化 « 酸化ベリリウムなどの六方晶結晶系及び 化アルミニウムなど の三方晶結晶系あるいは六方晶系として分類できる結晶系を有する材料を主成分とする焼結体 を用いた基板に直接形成する場合、 図 1、 図 2、 図 4に示したような基板 1の窒化アルミニゥ ムを主成分とする焼結体からなる基板に代わって上記炭化珪素、 窒化珪素、 窒化ガリウム、 酸 化亜鉛、 酸化ベリリウム及ぴ 化アルミニウムなどの焼結体からなる基板を用いることで実現 できる。 この場合該単結晶薄膜の成長方位は基板面に対して垂直な方向が該薄膜結晶の属する 六方晶の C軸として成長し易い。 又 X線を照射すれば図 2に示したのと同様該単結晶薄膜のミ ラ一指数 ( 0 0 2) の格子面からの回折線だけが検出される。なお、上記炭化珪素、窒化珪素、 窒化ガリウム、 酸化»、 酸化ベリリウム及び ¾化アルミニウムなどを主成分とする焼結体か らなる基板の形状は本発明において円形だけでなく正方形、 長方形、 あるいはその他多角形な ど任意の形状のものが細できる。 また、上記炭化珪素、窒化珪素、窒化ガリウム、酸化亜鉛、 酸化ベリリゥム及び 化アルミニウムなどを主成分とする焼結体からなる薄膜形成用基概び 炭化珪素、 窒化珪素、 窒化ガリウム、 酸化亜鉛、 酸化ベリリウム及び酸化アルミニウムなどを 主成分とする焼結体を用いることで作製される薄膜基板は焼結体および 膜作製において通常 用いられている方法を用いることで任意の大きさのものが作製できる。 すなわち焼結体の場合 例えば外形 0. 0 1讓〜1 0 0 0mm, 0mm程度のものは容易に作製できる。 本発明において検討してきた各種セラミック材料を主成分とする焼結体からなる基板の中で 窒化アルミニウムを主成分とする焼結体からなる基板は特に優れている。 上記窒化アルミニゥ ムを主成分とする焼結体からなる基板に形成された殆どすベての窒化ガリゥム、 窒化ィンジゥ ム、 窒化アルミニウムのうちから選ばれた少なくとも 1種以上を主成分とする単結晶薄膜にお いて該単結晶薄膜のミラ一指数 (0 0 2) の格子面の X線回折ロッキングカーブの半値幅とし て 3 0 0秒以下とシャープで特に結晶性に優れている。 したがって本発明が完成に至ったのも このような知見が得られたことが背景の大きな一つである。 おそらく窒化アルミニゥムを主成 分とする焼結体は結晶系だけでなく熱膨張率も窒化ガリウム、 窒化インジウム、 窒化アルミ二 ゥムのうちから選ばれた少なくとも 1種以上を主成分とする単結晶薄膜及び無定形、 多結晶、 配向性多結晶などの各種結晶状態の薄膜と極めて近いことも優れている原因の一つと本発明者
は衡則している。 すなわち窒化ガリウムが 5. 5 9 X 1 0— 6 (°C一1) であり、 窒化インジウム が 5. 7 0 X 1 0—6 CC-1) であり、 窒化アルミニウムが 5. 6 4 X 1 0—6 C"1) である。 例えば本発明による薄膜形成用基板として窒化アルミ二ゥムを主成分とする焼結体を基板とし て用いて窒化ガリウムの単結晶薄膜を 1 0 0 0 °C程度の MJtで形成し室温まで? ^した後窒化 ガリゥム単結晶薄膜に生じる応力はわずかで窒化ガリゥム単結晶薄膜に不具合が生じにくい。 またこの組み合わせの場合窒化ガリゥム単結晶薄膜に生じる応力は圧縮応力となり、 そのため さらに窒化ガリウム単結晶薄膜に不具合が生じにくくなるものと撤則される。 上記のように基 板の熱膨張率が窒化ガリゥム、 窒化ィンジゥム、 窒化アルミニゥムのうちから選ばれた少なく とも 1種以上を主成分とする単結晶薄膜及び無定形、 多結晶、 配向性多結晶などの各種結晶状 態の薄膜と近いことの利点としてはその他、基板に形成される窒化ガリウム、窒化インジウム、 窒化アルミニウムのうちから選ばれた少なくとも 1種以上を主成分とする単結晶薄膜及び無定 形、 多結晶、 配向性多結晶などの各種結晶状態の薄膜の を厚くする必要がある場合該単結 晶薄膜に生じる応力が小さくさらにその応力も JBI応力であることが多いので例えば 1 0 m 以上といった厚い藤の前記該単結晶薄膜及び無定形、 多結晶、 配向性多結晶などの各種結晶 状態の薄膜に転位や亀裂などの不具合が生じることが少ない、 ということが挙げられる。 この ように窒化アルミニウムを主成分とする焼結体からなる基板を薄膜形成用基板として用いたと き該基板に形成される窒化ガリウム、 窒化インジウム、 窒化アルミニウムのうちから選ばれた 少なくとも 1種以上を主成分とする単結晶薄膜及び無定形、 多結晶、 配向性多結晶などの各種 結晶状態の薄膜の厚みは任意の厚みのものが形成できるが少なくとも 5 nm以上のものが 形成できさらに 1 0 mm以上の厚いものも容易に形成できる。 このように窒ィ匕ァレミニゥム を主成分とする焼結体からなる基板を薄膜形成用基板として用いたとき該基板に形成される窒 化ガリウム、 窒化インジウム、 窒化アルミニウムのうちから選ばれた少なくとも 1種以上を主 成分とする薄膜は単結晶だけに限らず無定形、 多結晶、 配向性多結晶など各種結晶性のものも 任意の厚みで形成でき少なくとも 0. 5 n m以上のものが形成できさらに 1 0 mm以上の厚 いもの、 又必要に応じて 5 0 m以上のものも容易に形成できる。 本発明において上記窒化ァ ルミ二ゥムを主成分とする焼結体からなる基板に形成された殆どすベての窒化ガリゥム、 窒化 インジウム、 窒化アルミニウムのうちから選ばれた少なくとも 1種以上を主成分とする単結晶 薄膜の厚みが 0. 5 nm以上の場合 (1 O m以上、 あるいは 5 0 m以上の単結晶薄膜であ つても)、 該単結晶薄膜のミラー ί数 (0 0 2) の格子面の X線回折ロッキングカーブの半値幅 は 3 0 0秒以下とシャープで特に結晶性に優れている。 したがって本発明による基板を用いて 窒化ガリウム、 窒化インジウム、 窒化アルミニウムのうちから選ばれた少なくとも 1種以上を 主成分とする単結晶薄膜及び無定形、 多結晶、 配向性多結晶などの各種結晶状態の薄膜の積層 によって発光素子を形成したとき素子中の転位が少なぐ 発光素子を形成するにあたって必要 な単結晶薄膜及び無定形、 多結晶、 配向性多結晶などの各種結晶状態の薄膜の厚み及び発光素 子全体の厚みが任意に設定できるので発光素子の設計が容易となり発光効率の高い素子が製造 できる。
このように、 基板として窒化アルミニウムを主成分とする焼結体を用いれば炭化珪素、 窒化 珪素、 窒化ガリウム、 酸化亜鉛、 酸化ベリリウム及び ¾化アルミニウムなどを主成分とする焼 結体に比べて基板に形成される窒化ガリウム、 窒化インジウム、 窒化アルミニウムのうちから 選ばれた少なくとも 1種以上を主成分とする単結晶薄 E¾び無定形、 多結晶、 配向性多結晶な どの各種結晶状態の薄膜はより高品質のものが得られやすいという特徴を有する。 その他、 基 板として窒化アルミニウムを主成分とする焼結体を用いる場合の副次的な利点は波長 3 8 0 η m以下の紫外光に対する光透過率の高さである。 窒化アルミニウムを主成分とする焼結体以外 の炭化珪素、 窒化珪素、 窒化ガリウム、 酸化亜鉛、 酸化ベリリウム及び酸化アルミニウムなど
を主成分とする焼結体の場合波長 3 8 O nm以下の紫外光に対する光透過率は殆ど無く実質的 に 0 %である。 したがって基板として窒化アルミニウムを主成分とする焼結体を用いる場合炭 化珪素、 窒化珪素、 窒化ガリウム、 酸化菌、 酸化ベリリウム及び酸化アルミニウムなどを主 成分とする焼結体に比べて発光素子からの紫外光が基板で吸収される割合が減るので発光素子 の発光効率が高まるという利点がある。
基板にサファイアや炭化珪素単結晶あるいはシリコンといった単結晶材料を用い窒化ガリウ ム、 窒化インジウム、 窒化アルミニウムのうちから選ばれた少なくとも 1種以上を主成分とす る単結晶薄膜を形成したときこれらの基板材料は単結晶であるにもかかわらず得られる該単結 晶薄膜には反りや亀裂あるいは転位の増大が生じ易くさらに場合によっては該単結晶薄膜が厚 く形成できない場合があるが、 その原因の一つは該単結晶薄膜と熱膨張率が異なることも主因 の一つと推察される。 例えば上記単結晶基板の中で炭化珪素単結晶及びシリコンの熱膨張率は 窒化ガリウム、 窒化インジウム、 窒化アルミニウムのうちから選ばれた少なくとも 1種以上を 主成分とする単結晶薄膜及び無定形、 多結晶、 配向性多結晶などの各種結晶状態の薄膜より小 さくそのため該薄膜中には引張り応力が働き該薄膜を例えば 0. 5 mといった比較的薄い厚 みで形成しても該薄膜には亀裂や転位が生じやすい。
上記に述べたように窒化ガリウム、 窒化インジウム、 窒化アルミニウムのうちから選ばれた 少なくとも 1種以上を主成分とする単結晶薄膜を形成するための基板として必ずしも単結晶が 優れている訳ではなぐ 本発明者が示したように基板としてセラミック材料を用いても優れた 窒化ガリウム、 窒化インジウム、 窒化アルミニウムのうちから選ばれた少なくとも 1種以上を 主成分とする単結晶薄膜が 1形成できる。 セラミック材料の中でも窒化アルミニウムを主成分 とする焼結体が優れており«からの問題点を解決できる。
本発明による薄膜形成用基板及ぴ 膜基板は図 1、 図 2及び図 4で例示されたような窒化ァ ルミ二ゥムを主成分とずる焼結体からなる基板に窒化ガリウム、 窒化インジウム、 窒化アルミ ニゥムのうちから選ばれた少なくとも 1種以上を主成分とする単結晶薄膜を直接形成したもの だけではない。 本発明による薄膜形成用基板としては窒化アルミニウムを主成分とする焼結体 からなる基板だけでなく、.炭化珪素、 窒化珪素、 窒化ガリウム、 酸化ベリリウム、 酸化亜鉛、 酸化アルミニウムなど六方晶系又 方晶系の結晶構造を有する各種セラミック材料を主成分 とする焼結体からなる基板、 その他各種セラミック材料を主成分とする焼結体からなる基板も 使用でき、 該基板には単結晶を含め無定形、 多結晶、 配向性多結晶など各種結晶状態の窒化ガ リウム、 窒化インジウム、 窒化アルミニウムのうちから選ばれた少なくとも 1種以上を主成分 とする薄膜が直接形成し得る。
図 5は、 本発明による薄藤成用基板、 及び 膜基板の 1例を H見図である。 図 5において 符号 4で示したものが本発明による窒化アルミニウムを主成分とする焼結体、 及び炭化珪素、 窒化珪素、 窒化ガリウム、 酸化亜鉛、 酸化ベリリウムなどの六方晶結晶系及び 化アルミニゥ ムなどの三方晶結晶系あるいは六方晶系として分類できる結晶構造を有する各種セラミック材 料を主成分とする焼結体、 及びその他各種セラミック材料を主成分とする焼結体からなる基板 であり薄膜形成用基板として用いられる。 該基板 4には窒化ガリウム、 窒化インジウム、 窒化 アルミニウムのうちから選ばれた少なくとも 1種以上を主成分とする単結晶、無定形、多結晶、 配向性多結晶のうちから選ばれる少なくともいずれかの結晶状態を有する薄膜 5が形成され該 基板 4及ぴ丽 5により薄膜基板 6が構成されている。 該基板 4には窒化ガリウム、 窒化イン ジゥム、 窒化アルミニウムのうちから選ばれた少なくとも 1種以上を主成分とし単結晶あるい は無定形状態、 多結晶状態、 配向性多結晶状態のうちから選ばれた少なくともいずれかの結晶 状態を有する薄膜 5が形成されている。 薄膜 5は窒化ガリウム、 窒化インジウム、 窒化アルミ ニゥムのうちから選ばれた少なくとも 1種以上を主成分とする 2層以上から構成される薄膜と
しても形成できる。 本発明において 2層以上からなる薄膜のうち通常少なくとも 1層以上は窒 化ガリウム、 窒化インジウム、 窒化アルミニウムのうちから選ばれた少なくとも 1種以上を主 成分とする単結晶状態の薄膜が形成されたものが発光素子形成用基板、 あるいはフィールドエ ミッション用基板、 あるいは回路基板用誘電体材料、 あるいは光導波路材料、 など各種電子素 子及び電 品用途に使用していく上では好ましい。 上記の 2層以上で構成された薄膜のうち 基板表面の薄膜は単結晶であることがより好ましい。 2層以上に形成された薄膜 5は各層にお いて単結晶状態を含め無定形状態、多結晶状態、配向性多結晶状態などの各種結晶状態、組成、 あるいは厚みなどそれぞれ異なる状態で形成できる。 すなわち、 例えば窒化アルミニウムを主 成分とする焼結体、 及び炭化珪素、 窒化珪素、 窒化ガリウム、 酸化亜鉛、 酸化ベリリウムなど の六方晶結晶系及び酸化アルミニウムなどの三方晶結晶系あるいは六方晶系として分類できる 結晶構造を有する各種セラミック材料を主成分とする焼結体、 などを含めた各種セラミック材 料を主成分とする焼結体からなる基板に窒化ガリウム、 窒化インジウム、 窒化アルミニウムの うちから選ばれた少なくとも 1種以上を主成分とする無定形状態あるいは配向性多結晶状態の 薄膜があらかじめ形成されさらにその上に単結晶状態の薄膜が形成されている場合、 などであ る。 本発明において同じ結晶状態で組成がそれぞれ異なる 2層の薄膜としても形成できる。 す なわち、 例えば形成される薄膜がそれぞれ同じく単結晶で組成がそれぞ ¾なる 2層の薄膜と して形成できる。
なお、 図 3 6に窒化アルミニウムを主成分とする焼結体、 及び炭化珪素、 窒化珪素、 窒化ガ リウム、 酸化亜鉛、 酸化ベリリウムなどの六方晶結晶系及び ¾化アルミニウムなどの三方晶結 晶系あるいは六方晶系として分類できる結晶構造を有する各種セラミック材料を主成分とする 焼結体、 .及びその他各種セラミック材料を主成分とする焼結体からなる基板だけの図を例示し、 該基板を符号 4で示した。 図 3 6に例示した基板 4は薄膜形成用基板として用いられ 該基板 の上に窒化ガリゥム、 窒化ィンジゥム、 窒化アルミニゥムのうちから選ばれた少なくとも 1種 以上を主成分とする単結晶、 無定形、 多結晶、 配向性多結晶のうちから選ばれる少なくともい ずれかの結晶状態を有する薄膜が形成される。
本発明による上記の窒化アルミニウムを主成分とする焼結体、 及び炭化珪素、 窒化珪素、 窒 化ガリウム、 酸化亜鉛、 酸化ベリリウムなどの 7^晶結晶系及び 化アルミニウムなどの三方 晶結晶系あるいは六方晶系として分類できる結晶構造を有する各種セラミック材料を主成分と する焼結体、 などを含めた各種セラミック材料を主成分とする焼結体からなる基板 4には窒化 ガリウム、 窒化インジウム、 窒化アルミニウムのうちから選ばれた少なくとも 1種以上を主成 分とする少なくとも単結晶状態の薄膜が直接形成でき、 その他に無定形状態、 多結晶状態、 配 向性多結晶状態など各種結晶状態の薄膜も直接形成できる。 本発明における実施形態として上 記基板 4には必ずしも窒化ガリウム、 窒化インジウム、 窒化アルミニウムのうちから選ばれた 少なくとも 1種以上を主成分とする少なくとも単結晶状態の薄膜が直接形成されたものでなく てもよく、 無定形状態、 多結晶状態、 配向性多結晶状態のうちから選ばれた少なくともいずれ かの結晶状態の薄膜が直接形成されているものであってもよい。
本発明において図 5に示したような薄膜基板を用いその上にさらに窒化ガリゥム、 窒化ィン ジゥム、 窒化アルミニウムのうちから選ばれた少なくとも 1種以上を主成分とする単結晶、 無 定形、 多結晶、 配向性多結晶のうちから選ばれる少なくともいずれかの結晶状態を有する薄膜 を形成することができる。 その場合該薄膜基板は薄膜形成用基板としての機能を果たすことに なる。
図 5に例示した本発明による薄膜形成用基板、 及び薄膜基板を用いて発光素子、 あるいはフ ィールドエミッションディスプレイ、 あるいは回路基板、 あるいは光導波路など、 各種電子素 子及び電子部品を作製することができる。
図 6は、 図 5に示した薄膜が 2層で構成されている薄膜基板の 1例を示す斜視図である。 図 6において、 符号 4で示したものが本発明による窒化アルミニウムを主成分とする焼結体、 及 び炭化珪素、 窒化珪素、 窒化ガリウム、 酸化亜鉛、 酸化ベリリウムなどの六方晶結晶系及び 化アルミニウムなどの三方晶結晶系あるいは六方晶系として分類できる結晶構造を有する各種 セラミック材料を主成分とする焼結体、 などを含めた各種セラミック材料を主成分とする焼結 体からなる基板であり薄膜形成用基板として用いられる。該薄膜形成用基板には窒化ガリゥム、 窒化インジウム、 窒化アルミニウムのうちから選ばれた少なくとも 1種以上を主成分とする単 結晶、 無定形、 多結晶、 配向性多結晶のうちから選ばれる少なくともいずれかの結晶状態を有 する薄膜 5及び 膜 8がそれぞれ 1層合計 2層の薄膜が形成され薄膜基板 6が構成されている。 図 6に例示した薄膜 5及ぴ蒋膜 8は窒化ガリウム、 窒化インジウム、 窒化アルミニウムのう ちから選ばれた少なくとも 1種以上を主成分とし単結晶状態の薄膜、 あるいは必要に応じて、 無定形状態、 多結晶状態、 配向性多結晶状態のうちから選ばれた少なくともいずれかの結晶状 態を有するものである。 図 6に示した薄膜 5及び薄膜 8は各層において単結晶を含め無定形、 多結晶、 配向性多結晶などの結晶状態、 組成、 あるいは厚みなどそれぞれ異なる状態で形成で きる。 図 6に示した薄隞冓成において薄膜 5を単結晶、 無定形、 多結晶、 配向性多結晶のうち から選ばれた少なくともいずれかの結晶状態で形成し、 薄膜 8をェピタキシャル成長した単結 晶として形成すれば該薄膜 8の結晶性は基板 4に直接形成した単結晶薄膜の結晶性よりも向上 し易いので好ましい。 このような薄!^冓成の薄膜基板は例えば発光素子、 あるいはフィールド ェミッション、 あるいは回路基板、 あるいは光導波路など、 各種電子素子及び電子部品の作製 用に使用していく上で好ましい。 上記のように薄膜 8をェピタキシャル成長した単結晶として 形成していく場合、 薄膜 5は無定形、 多結晶、 配向性多結晶のうちから選ばれた少なくともい ずれかの結晶状態で形成されたものが該薄膜 8の結晶性などの特性面で優れたものが得られ易 いので好ましぐ 薄膜 5が配向性多結晶として形成されたものがより好ましい。
また、 本発明において、 図 6に示すような薄膜を 2層形成したものだけでなくさらに 3層以 上に形成された薄膜基板も容易に提供することができる。
上記のように図 5及び図 6に示した薄膜はすべてが単結晶であるとは限らない。 また単一の 層であるとは限らない。 図 5及び図 6に示した薄膜は窒化ガリウム、 窒化インジウム、 窒化ァ ルミニゥムのうちから選ばれた少なくとも 1種以上を主成分とする単結晶状態、 無定形状態、 多結晶状態、 配向性多結晶状態など各種結晶状態のものを用いることができる。 また、 図 5及 び図 6に示した薄膜は窒化ガリウム、 窒化インジウム、 窒化アルミニウムのうちから選ばれた 少なくとも 1種以上を主成分とする 2層以上から構成される薄膜としても形成できる。 2層以 上からなる薄膜は各層において単結晶状態を含め無定形状態、 多結晶状態、 配向性多結晶状態 などの結晶状態、 組成、 あるいは厚みなどそれぞれ異なる状態で形成できるが、 本発明におい て 2層以上で構成された薄膜のうち少なくとも 1層以上は窒化ガリウム、 窒化インジウム、 窒 化アルミニウムのうちから選ばれた少なくとも 1種以上を主成分とする単結晶であることが好 ましい。 本発明による薄膜基板を発光素子形成用基板、 あるいはフィールドェミッション用基 板、 あるいは回 ϊβ棚誘電体材料、あるいは光導波路用材料、などのように、窒化ガリウム、 窒化インジウム、 窒化アルミニウムのうちから選ばれた少なくとも 1種以上を主成分とする単 結晶薄膜をはじめとする各種結晶状態の薄膜を形成するために用いる場合など本発明による薄 膜基板の表面は通常単結晶状態であることが好ましい。
本発明による薄膜基板とは、 窒化アルミニウムを主成分とする焼結体、 及び炭化珪素、 窒化 珪素、 窒化ガリウム、 酸化亜鉛、 酸化ベリリウムなどの六方晶結晶系及び酸化アルミニウムな どの三方晶結晶系あるいは六方晶系として分類できる結晶構造を有する各種セラミック材料を 主成分とする焼結体、 その他各種セラミック材料を主成分とする焼結体つを基板として用い、
該基板に窒化ガリウム、 窒化インジウム、 窒化アルミニウムのうちから選ばれた少なくとも 1 種以上を主成分とする薄膜が形成された基板であって、 要すれば窒化ガリウム、 窒化インジゥ ム、 窒化アルミニウムのうちから選ばれた少なくとも 1種以上を主成分とする薄膜の少なくと も一部がェピタキシャル成長した単結晶状態である基板である。 本発明による薄膜基板におい て表面に窒化ガリウム、 窒化インジウム、 窒化アルミニウムのうちから選ばれた少なくとも 1 種以上を主成分とする単結晶薄膜を有するものの場合窒化アルミニウムを主成分とする焼結体、 及び炭化珪素、 窒化珪素、 窒化ガリウム、 酸化亜鉛、 酸化ベリリウムなどの六方晶結晶系及び 酸化アルミニウムなどの三方晶結晶系あるいは六方晶系として分類できる結晶構造を有する各 種セラミック材料を主成分とする焼結体、 などを含めた各種セラミック材料を主成分とする焼 結体に窒化ガリウム、 窒化インジウム、 窒化アルミニウムのうちから選ばれた少なくとも 1種 以上を主成分とする単結晶状態、 無定形状態、 多結晶状態、 配向性多結晶状態のうちから選ば れる少なくともいすれかの結晶状態の薄膜をあらかじめ形成し、 さらにその上に窒化ガリウム、 窒化インジウム、 窒化アルミニウムのうちから選ばれた少なくとも 1種以上を主成分とするェ ピタキシャル成長した薄膜を形成したものが ましい。 そうすることで窒化アルミニウムなど 各種セラミック材料を主成分とする焼結体に窒化ガリウム、 窒化インジウム、 窒化アルミニゥ ムのうちから選ばれた少なくとも 1種以上を主成分とする単結晶を直接形成したものより単結 晶薄膜の結晶性が向上するので好ましい。
本発明による上記図 5で示した薄膜基板 6及び図 6で示した薄膜基板 8には窒化ガリゥム、 窒化インジウム、 窒化アルミニウムのうちから選ばれた少なくとも 1種以上を主成分とする少 なくとも一部が単結晶状態である薄膜が形成でき、 その他無定形、 多結晶、 配向性多結晶など 各種結晶状態の薄膜も形成できる。
本発明による薄膜形成用基板としては図 5で示した窒化アルミニウムなど各種セラミック材 料を主成分とする焼結体からなる基板だけでなぐ 窒化アルミニウムを主成分とする焼結体に 窒化ガリウム、 窒化インジウム、 窒化アルミニウムのうちから選ばれた少なくとも 1種以上を 主成分とする薄膜が形成された基板も用いることができる。 このような窒化アルミニウムを主 成分とする焼結体に窒化ガリウム、 窒化インジウム、 窒化アルミニウムのうちから選ばれた少 なくとも 1種以上を主成分とする薄膜が形成された基板は図 6で示した薄膜基板と同質であり、 本発明による薄膜基板は発光素子作製用基板、 あるいはフィールドェミッション用基板、 ある いは回路基板用誘電体材料、 あるいは光導波路用材料、 などの電子素子及び電子部品だけでな く本発明による薄膜形成用基板としても用いることができる。
本発明による薄膜基板において窒化ガリウム、 窒化インジウム、 窒化アルミニウムのうちか ら選ばれた少なくとも 1種以上を主成分とする薄膜を形成するために用いる窒化アルミニウム を主成分とする焼結体は通常基板状で用いられる。 該基板状の窒化アルミニウムを主成分とす る焼結体は本発明による薄膜形成用基板として用いる窒化アルミニウムを主成分とする焼結体 からなる基板と同質である。 すなわち本発明による窒化アルミニウムを主成分とする焼結体か らなる薄膜形成用基板は本発明による薄膜基板を構成する基板としても用いることができる。 図 5及び図 6に記載されている薄膜形成用基板及び薄膜基板は円盤状であり、 薄膜は基板の 1面だけに形成されているように描かれているが、 本発明において上記薄臌堪板の 1面だけ でなくその他の面にも必要に応じて形成され得る。 また、 薄膜形成用基板及び 膜基板として 例えば四角い板状 (直方体) のものを用いた場合窒化ガリウム、 窒化インジウム、 窒化アルミ ニゥムのうちから選ばれた少なくとも 1種以上を主成分とする薄膜は必要に応じて上記薄膜形 成用基 ぴ育膜基板の 1面だけ、あるいは 2面だけ、あるいは 3面だけ、あるいは 4面だけ、 あるいは 5面だけ、 あるいは 6面すべて、 に形成できる。
図 1、 図 2、 図 4、 図 5、 図 6で示された窒化ガリウム、 窒化インジウム、 窒化アルミニゥ
ムのうちから選ばれた少なくとも 1種以上を主成分とする単結晶薄膜 5は少なくとも単結晶状 態を含み必要に応じて、 さらに無定形状態、 多結晶状態、 配向性多結晶状態など各種結晶状態 を含むものとして形成でき、 さらに該薄膜 5は単一の層だけでなく組成や結晶状態あるいは厚 みの異なる複数の層としても形成し得る。
本発明による窒化アルミニウムを主成分とする焼結体及び窒化アルミニウムを主成分とする 焼結体からなる基板の製造 « ^来からの方法を用いることができる。 すなわち窒化アルミニゥ ムを主成分とする粉末成形体をヘリウム、 ネオン、 アルゴン、 窒素などの少なくとも 1種以上 を主体とする中性雰囲気あるいは水素、 一酸化炭素、 炭素、 炭化水素などの少なくとも 1種以 上を含む 性雰囲気といった非酸化性雰囲気の常圧下で、 あるいは減圧下で、 あるいは加圧 下で通常 1 5 0 0〜2 4 0 0°C程度の温度範囲で加熱し製造される。 焼成時間は通常 1 0分〜 3時間程度の範囲が用いられる。 又真空中での «によっても $¾iされ得る。 さらにホットプ レス法あるいは H I P (熱間静水圧加圧焼結) によっても製造される。 ホットプレス法による 焼成条件としては上記非酸化性雰囲気中あるいは真空中通常 1 5 0 0〜2 4 0 0°C程度の焼成 温度範囲及び 1 0分〜 3時間程度の範囲の焼成時間及び 1 O K g/ c m2〜 1 0 0 O K g/ c m2程度の圧力範囲が用いられる。また H I P法による «条件としては上記非酸化性雰囲気を 5 0 O Kgノ c m2〜l 0 0 0 0 KgZc m2程度の範囲に加圧し通常 1 5 0 0〜2 4 0 0°C程 度の; 範囲及び 1 0分〜 1 0時間程度の範囲の «時間が用いられる。 上記の; Kに際 して窒化アルミニゥム成分が焼成雰囲気中に存在するような工夫を行うことでより ¾¾ 性に 優れた窒化アルミニウムを主成分とする焼結体が得やすい。 すなわち、 窒化アルミニウムを主 成分とする蒸気が «雰囲気中に存在することで光 ¾i性に優れた窒化アルミニゥムを主成分 とする焼結体がより得易くなる。 窒化アルミニウム成分を焼成雰囲気中に存在させる方法とし ては例えば被焼成物である窒化アルミニウムを主成分とする粉末成形体あるいは窒化アルミ二 ゥムを主成分とする焼結体の焼成中に謝皮 «物自体からの蒸発によつて雰囲気中に供給する 、 あるいは該被舰物以外から供給する方法がある。 具体的には例えば、 被誠物自体から 窒化アルミニウム成分を誠雰囲気中に供給する方法として、 難焼成物を窒化ほう素あるい はタングステン、 モリブデンなどできるだけカーボンを含まない材料で作製された 「さや」 や
「こう鉢」 などの賊容器あるいは 「セッ夕一」 などの焼成治具に収納し焼成するか、 あるい は力一ボンを含んだ焼成容器あるいは焼成治具を用いたとしてもその表面を窒化ほう素などで コ一ティングしたものを用いるなど効果がある。 焼成容器あるいは焼成治具などに収納後さら に密閉度を高めた状態で被焼成物を焼成することにより遞過性に優れた窒化アルミ二ゥムを 主成分とする焼結体を作製することもできる。 被誠物以外から窒化アルミニゥム成分を焼成 雰囲気中に供給する方法として、 被焼成物を窒化アルミニウムを主成分とする材料で作製され た 「さや」 や 「こう鉢」 などの焼成容器あるいは 「セッタ一」 などの焼成治具に収納し誠す ることで) 性に優れた窒化アルミ二ゥムを主成分とする焼結体を作製することができる。 また、 被誠物を窒化アルミ二ゥムを主成分とする粉末中に埋設して誠する方法は) 性 に優れた窒化アルミニウムを主成分とする焼結体が得やすい。 上記焼成容器あるいは誠治具 内に被焼成物以外の窒化アルミニウムを主成分とする粉末あるいは窒化アルミニウムを主成分 とする粉末成形体あるいは窒化アルミニウムを主成分とする焼結体のうちから選ばれた少なく ともいずれか 1以上のものを被焼成物とともに同時に存在させて! «しても 率に優れた 窒化アルミニウムを主成分とする焼結体を作製することができる。 この方法では被! «物をフ リ一な状態で焼成することができるので製品の大 理ゃ複雑な形状のものを«する場合に 好適である。 なお、 上記焼成容器あるいは舰治具のうち窒化アルミニウムを主成分とする材 料で作製された舰容器あるいは焼成治具を用い、 被舰物以外の窒化アルミニウムを主成分 とする粉末あるいは窒化アルミニウムを主成分とする粉末成形体あるいは窒化アルミニウムを
主成分とする焼結体のうちから選ばれた少なくともいずれか 1以上のものを被焼成物とともに 同時に存在させて舰しても光顯率に優れた窒化アルミニウムを主成分とする焼結体を作製 することができる。 上記窒化アルミニウム成分を舰雰囲気中に存在させ光扁性に優れた窒 化アルミニウムを主成分とする焼結体を作製する方法のなかで、 通常該窒化アルミニウム成分 を被 «物自体からの蒸発によつて雰囲気中に供給するよりも被; W物以外から供給する方が より光透過性に優れた窒化アルミニウムを主成分とする焼結体が作製し得る。 なお、 上記窒化 アルミニウム成分を誠雰囲気中に存在させ光删性に優れた窒化アルミニウムを主成分とす る焼結体を作製する方法は、 通常焼結助剤などの添加物や原料中に含まれる酸素あるいは不可 避不純物などの成分が焼成中に揮散しないので粉末成形体とほとんど同じ組成の窒化アルミ二 ゥムを主成分とする焼結体を作製することができる。
その他、 ホットプレス法や H I P法による焼成に際しては窒化アルミニウムを主成分とする 粉末成形体をそのまま加圧焼成するよりも 粉末成形体をいつたん焼成して窒化アルミニウム を主成分とする焼結体となし、 該焼結体をあらためてカロ圧焼成する方がより 1^性に優れた 窒化アルミニウムを主成分とする焼結体が得やすい。 また、 ホットプレス法や H I P法による 焼成においても、 上記焼成容器や焼成治具を用いるなど各種方法により焼成雰囲気中に窒化ァ ルミニゥ成分を存在させて誠することがより ¾i 生に優れた窒化アルミ二ゥムを主成分と する焼結体を作製する上で好ましい。
窒化アルミニウムを主成分とする焼結体の化学的献を向上させるときは必要に応じて上記 以外の条件も選択できる。 例えば 1 7 5 0°C以上の温度で 3時間以上の比較的長い時間をかけ 要すれば ^性雰囲気中で; «を行えば含まれる酸素や焼結助剤として用いられる希土 素 化合物やアル力リ土類金属化合物などの成分あるいは焼成温度低減化剤として用いられるアル カリ金属や珪素などの成分あるいは黒色化剤として用いられる Mo、 W、 V、 N b、 T a、 T iなどの金属成分やカーボンあるいは M o、 W、 V、 N b、 T a、 T i以外の不可避金属成分 などを飛散 ·除去し減少化できるので AL ONや上記アルミニウム以外の金属成分や珪素ある いは力一ボンを含む化合物の含有量が低減化されて A 1 N Jtが高まりその結果光 ¾i性が向 上した窒化アルミニウムを主成分とする焼結体を難することが可能となる。 上記のように 1 7 5 0°C以上の温度で 3時間以上の比較的長い時間をかけ要すれば還元性雰囲気中で焼成を行 うことで窒化アルミニウムを主成分とする焼結体の 性をより高めることができるが、 該 焼成により窒化アルミニウムを主成分とする焼結体中の窒化アルミニウム粒子が成長し易くそ の結果粒子境界が減少することも ½¾ϋ性が高まり易くなることの要因の 1つではないかと本 願発明者は推測している。
上記のように A 1 N献を高めた窒化アルミニウムを主成分とする焼結体を基板として用い て窒化ガリウム、 窒化インジウム、 窒化アルミニウムのうちから選ばれた少なくとも 1種以上 を主成分とする単結晶の薄膜を形成したとき該単結晶薄膜はより結晶性の高いものが形成でき 易くなるので好ましい。 また、 例えば 1 7 5 0 °C以上の温度で 3時間以上の比較的長い時間を かけて焼成を行うことで窒化アルミニウムを主成分とする焼結体の窒化アルミニゥム粒子を大 きく成長させることができる。 窒化アルミニウム粒子が成長した窒化アルミニウムを主成分と する焼結体を基板として用いて窒化ガリウム、 窒化インジウム、 窒化アルミニウムのうちから 選ばれた少なくとも 1種以上を主成分とする単結晶の薄膜を形成したとき該単結晶薄膜はより 結晶性の高いものが形成でき易くなるので好ましい。 本発明においてはこのように窒化ガリゥ ム、 窒化インジウム、 窒化アルミニウムのうちから選ばれた少なくとも 1種以上を主成分とす る薄膜を形成するための基板として A 1 N純度を高めた窒化アルミニウムを主成分とする焼結 体だけでなく、 窒化アルミニゥム粒子が成長した窒化アルミニゥムを主成分とする焼結体も有 効である。 上記のような A 1 の高い窒化アルミニウムを主成分とする焼結体あるいは窒
化アルミニウム粒子が成長した窒化アルミニウムを主成分とする焼結体を製造するときの焼成 として 寺間を短縮する上で 1 9 0 0°C以上がより好ましく、 2 0 5 0 °C以上がさらに 好ましく、 2 1 0 0 以上が最も好ましい。 2 0 5 O t以上はもちろんさらに 2 1 0 0 °C以上 の高温であっても A 1 N成分自体は殆ど昇華することなく焼成できる。 A 1 Nの を高める ためあるいは窒化アルミニウム粒子を成長させるために焼成温度 1 7 5 0 t〜 1 9 0 0°Cの範 囲では焼成時間は通常 1 0時間以上とすることが好ましくさらに 2 4時間以上でより大きな効 果が得られる。 j 'mf i 9 0 0 °C以上では焼成時間 6時間以上で十分 A 1 N J¾を高める、 あるいは窒化アルミニウム粒子を成長させる効果が得られさらに 1 0時間以上で A 1 Nの Jt を高める、 あるいは窒化アルミニウム粒子を成長させるためのより大きな効果が得られる。 焼 成温度 2 0 5 0 °C以上では焼成時間 4時間以上で十分 A 1 N純度を高める、 あるいは窒化アル ミニゥム粒子を成長させる効果が得られさらに 6時間以上で A 1 Nの!^を高める、 あるいは 窒化アルミニウム粒子を成長させるためのより大きな効果が得られる。 また焼成温度 2 1 0 0°C以上では焼成時間 3時間以上で十分 A 1 N¾¾¾を高める、 あるいは窒化アルミニウム粒子 を成長させる効果が得られさらに 4時間以上で A 1 Nの «を高める、 あるいは窒化アルミ二 ゥム粒子を成長させるためのより大きな効果が得られる。 上記のように窒化アルミニウムを主 成分とする焼結体の A 1 N純度を高める、 あるいは窒化アルミニウム粒子を成長させる上では 焼成温度を高めれば焼成時間を短くでき焼成温度を低くすれば焼成時間が長くなるという関係 にあり、 舰 と焼成時間は任意の条件のものを用いることができる。 上記のような A 1 N 績の高い窒化アルミニウムを主成分とする焼結体を難するときの舰雰囲気は不純物をよ り揮散させ易くするために例えば水素、 一酸化炭素、 炭素、 炭化水素などの少なくとも 1種以 上を含む 性雰囲気を用いることが好ましい。 ^1¾性雰囲気としては水素、 一酸化炭素、 炭 素、 炭化水素などのうち少なくとも 1種以上を主体とするものでも良いが窒素、 ヘリウム、 ネ オン、 アルゴンなどのうち少なくとも 1種以上を主成分とする雰囲気中に水素、 一酸化炭素、 炭素、 炭化水素などのうち少なくとも 1種以上を例えば 0. 1 p pm程度の微 む雰囲気で あっても良い。 還元性雰囲気が窒素、 ヘリウム、 ネオン、 アルゴンなどのうち少なくとも 1種 以上を主体とする雰囲気中に水素、 一酸化炭素、 炭素、 炭化水素などのうち少なくとも 1種以 上を微» む雰囲気である場合水素、 一酸化炭素、 炭素、 炭化水素などのうち少なくとも 1種 以上を 1 0 p pm以上含むものが窒化アルミニウムを主成分とする焼結体を高純度化する上で より好ましい。 また前記 S¾性雰囲気において水素、 一酸化炭素、 炭素、 炭化水素などのうち 少なくとも 1種以上を 1 0 0 p pm以上含むものが窒化アルミニウムを主成分とする焼結体を 高繊化する上でさらに好ましい。 窒化アルミニウム粒子が成長した窒化アルミニウムを主成 分とする焼結体を製造する時の雰囲気は特に還元雰囲気を用いる必要性はなく非酸化性の雰囲 気であれば十分である。 上記のような比較的長い時間焼成を行い A 1 N ¾の高い窒化アルミ 二ゥムを主成分とする焼結体あるいは窒化アルミニウム粒子が成長した窒化アルミニウムを主 成分とする焼結体を するとき、 窒化アルミニウム原料粉末を主成分とする粉末成形体を用 いて焼成してもよいし、 前記粉末成形体をいつたん焼成し焼結体としたものを用いても良い。 また、 主成分である窒化アルミニウム以外に希土 ¾素化合物あるいはアル力リ土類金属化合 物のうちから選ばれた少なくとも 1種以上を含む窒化アルミニウムを主成分とする粉末成形体 や焼結体を用いることも好ましい。
A 1 N純度の高い窒化アルミニウムを主成分とする焼結体を製造するときには特に焼結助剤 を使用せず原料粉末をそのまま使つた粉末成形体や焼結体を用い好ましくは前記のような還元 性雰囲気中 1 7 5 0 °C以上の温度で 3時間以上加熱して含まれる成分を揮散'除去してもよい が、 上記のように希土類 素化合物あるいはアルカリ土類金属化合物のうちから選ばれた少な くとも 1種以上を含む窒化アルミニウムを主成分とする粉末成形体や焼結体を用いることが A
1 N以外の成分を揮散 · 、 低減化し高 S化が達成され易いのでより好ましい。 また、 希 土 ®¾素化合物から選ばれた化合物を少なくとも 1種以上及びアル力リ土類金属化合物から選 ばれた化合物を少なくとも 1種以上同時に含んだ窒化アルミニウムを主成分とする粉末成形体 あるいは粉末成形体をいつたん焼成して焼結体としたものを用いることで、 希土類 素化合物 あるいはアル力リ土類金属化合物をそれぞれ単独で用いた場合に比べて焼成温度を 5 0 °C〜 3 0 0 程度低下することが可能となり効率的に窒化アルミニウム以外の成分を揮散 · P鉄、 低 減化し高¾ 化が達成され易くなるのでより好ましい。 このような方法により X線回折などの 方法を用いた分析で実質的に A 1 N単一相からなる窒化アルミニウム焼結体も製造できる。 本願発明において薄膜形成用基板として用いる窒化アルミニウムを主成分とする焼結体の A I N Jtを高めることはこの基板に形成する窒化ガリウム、 窒化インジウム、 窒化アルミニゥ ムのうちから選ばれた少なくとも 1種以上を主成分とする薄膜の質を向上させるためには有効 である。 その理由として焼結体中で粒界相の占める面積が減少し A 1 N粒子だけの影響しか受 けにくくなるためであろうと思われる。
しかしながら一方で窒化アルミニウム粒子が成長した窒化アルミニウムを主成分とする雕 体を基板として用いることも有効である。 すなわち例えば前記粉末成形体や焼結体を 1 7 5 0 °C以上の で 3時間以上の比較的長い時間をかけて «を行つて得られる窒化アルミニゥ ムを主成分とする焼結体は窒化アルミニウム粒子は大きく成長している一方で希土 素化合 物やアルカリ土類金属化合物などの焼結助剤、 あるいは酸素、 あるいは 低減化剤とし て用いられるアルカリ金属や珪素などの成分、 あるいは黒色化剤として用いられる Mo、 W、 V、 N b、 T a、 T iなどの金属成分や力一ポン、 あるいは M o、 W、 V、 N b、 T a、 T i 以外の不可避金属成分、 あるいは AL ONや上記アルミニウム以外の金属成分や珪素あるいは カーボンを含む化合物、 などの成分が比較的多く残存している場合がある。 このような焼結体 を基板として用いてもこの基板に形成される窒化ガリウム、 窒化インジウム、 窒化アルミニゥ ムのうちから選ばれた少なくとも 1種以上を主成分とする単結晶薄膜の結晶性が向上するなど 薄膜の質は向上する。 すなわち本発明において窒化ガリウム、 窒化インジウム、 窒化アルミ二 ゥムのうちから選ばれた少なくとも 1種以上を主成分とする薄膜を形成するための基板として 用いられる窒化アルミニウムを主成分とする焼結体は必ずしも A 1 の高いものでなくて も焼結体中の窒化アルミニゥム粒子を大きくすることが 効であることを示している。 その理 由として焼結体中の窒化アルミニウム結晶粒子の大きさが増大化すれば粒界が減少するので粒 界の影響が少なくなりこの大きく増大した A 1 N粒子が単結晶に近い性質を発現し易くなるた めであろうと推測される。 上記のように高い で長時間焼成すれば焼結体中の窒化アルミ二 ゥム結晶粒子の大きさが増大化するが通常それと同時に窒化アルミニウムを主成分とする焼結 体中の A 1 N難が高まり易い。 窒化アルミニウムを主成分とする焼結体中の窒化アルミニゥ ム結晶粒子の大きさを増大化させるだけで A 1 N純度の向上を抑制するためには焼成雰囲気を 水素、 一酸化炭素、 炭素、 炭化水素などの還元性成分の比較的少ない窒素やアルゴンなどの穽 酸化性雰囲気を用いることが好ましい。 又焼成炉もカーボン発熱体を用いる方式のものあるい は電磁誘導で力一ボンを発熱させる方式あるいはカーボン製の炉材を用いたものなど以外、 例 えばタングステン、 モリブデンなどの高融点金属を発熱体とする方式のものあるいは電磁誘導 でタングステン、 モリブデンなどの高融点金属を発熱させる方式あるいはタングステン、 モリ ブデンなどの高融点金属製の炉材を用いたものなどを用いることが有効である。 また水素、 一 酸化炭素、 炭素、 炭化水素などを含む還元性雰囲気中で焼成してもあるいはカーボン発熱体を 用いる方式のものや電磁誘導で力一ポンを発熱させる方式の焼成炉を用いても、 前記粉末成形 体や焼結体を窒化アルミ二ゥムゃ窒化ほう素あるいは夕ングステンなどできるだけ力一ボンを 含まないセッタ一や治具あるいはさや内に収納するか、 あるいは窒化アルミニウム粉末中に埋
設するか、 あるいはカーボンを含んだセッターや治具あるいはさやを用いたとしても窒化アル ミニゥム粉末中に埋設するか、 あるいは上記セッ夕一や治具あるいはさや内に収納しさらに窒 化アルミニウム粉末中に埋設するなど、 できるだけ還元性雰囲気と隔絶した状態で焼成するこ とも有効である。
上記のような焼結体の高! ¾S化を抑制するような焼成法でなくカーボン発熱体を用いる のものあるいは電磁誘導で力—ボンを発熱させる方式のものあるいはカーボン製の炉材を用い た焼成炉などを用いるか、 カーボン製のセッターや治具あるいはさやを用いて前記粉末成形体 あるいは焼結体を焼成すれば自発的に一酸化炭素や炭素を含 雰囲気が形成され易いので
A 1 N以外の成分が揮散 · 鉄され易くなり A 1 N献が高くかつ窒化アルミニウム粒子が成 長した窒化アルミニウムを主成分とする焼結体を容易に得ることができるので好ましい。 通常 カーボン発熱体を用いる のものあるいは電»導で力一ボンを発熱させる方式のものある いは力一ボン製の炉材を用いた焼成炉などを用い、 同時にカーボン製のセッターや治具あるい はさやを用いて前記粉末成形体あるいは焼結体を «することが A 1 N ¾Sが高くかつ窒化ァ ルミニゥム粒子が成長した窒化アルミニウムを主成分とする焼結体を! ¾tする上で好ましい。 また、 上記のような^ 5性が弱いかあるいは ¾性成分を含まない非酸化性雰囲気中で 3時 間以下と比較的短い時間、 又は ¾性が弱いかあるいは S¾性成分を含まない非酸化性雰囲気 中で例えば 1 9 0 0°C以下と比較的低温で «を行ない、 窒化アルミニウム結晶粒子の大きさ の増大が比較的少なぐ 不純物や焼結助剤などが比較的多く残存した状態の窒化アルミニウム を主成分とする焼結体も窒化ガリウム、 窒化インジウム、 窒化アルミニウムのうちから選ばれ た少なくとも 1種以上を主成分とする薄膜を形成するための基板として問題なく用いられる。 すなわち、 このようにして作製される窒化アルミニウムを主成分とする焼結体には原料粉末中 の不純物酸素や粉末成形体に添加した A 1 203に起因する酸素、 あるいは添加した希土 ¾素 化合物及びアル力リ土類金属化合物などの焼結助剤中の金属成分や酸素成分など、 あるいは添 加したアルカリ金属化合物及び ^有化合物中の金属成分、 珪素成分、 酸素成分など、 ある いは添力卩した M o、 W、 V、 N b、 T a、 T iの各遷移金属を含む化合物及びカーボンを含む 化合物中の金属成分やカーボン成分など、 あるいは添加した F e、 N i、 C r、 Mn、 Z r、 H f、 C o、 C u、 Z nなどの不可避不純物を含む化合物中の金属成分や酸素成分などは焼成 により殆ど揮散 · 鉄されないで粉末成形体中と殆ど同じ量存在する場合が多い。 一方、 本発 明においては特に断らない限り粉末成形体及び窒化アルミニウムを主成分とする焼結体中に含 まれる不純物あるいは加えられた各種添加物の量は実際含まれる不純物あるいは加えられる焼 結助剤などの化合物を酸化物換算あるいは元素騰した量で示しており、 前記窒化アルミニゥ ムを主成分とする焼結体の酸素成分や金属成分あるいは珪素成分の量 «®常特に断らない限り 酸化物換算あるいは元素換算によるものである。
上記のように A 1 N纖が高く力つ窒化アルミニウム粒子が成長した窒化アルミニウムを主 成分とする焼結体は薄膜形成用基板として好ましいが、必ずしも A 1 Nの繊が高くなくても、 すなわち希土 素化合物やアルカリ土類金属化合物などの焼結助剤、 あるいは酸素、 あるい は 低減化剤として用いられるアル力リ金属や珪素などの成分、 あるいは黒色化剤とし て用いられる M o、 W、 V、 N b、 T a、 T iなどの金属成分や力一ボン、 あるいは F e、 N i、 C r、 Mn、 Z r、 H f、 C o、 C u、 Z nなど M o、 W、 V、 N b、 T a、 T i以外の 不可避金属成分、 あるいは A L O Nや上記アルミニゥム以外の金属成分や珪素あるいは力一ポ ンを含む化合物、 などの成分が比較的多く残存している窒化アルミニウムを主成分とする焼結 体であっても窒化アルミニウム粒子が成長したものであれば結晶性の高い窒化ガリゥム、 窒化 インジウム、 窒化アルミニウムのうちから選ばれた少なくとも 1種以上を主成分とする単結晶 薄膜が形成し得る基板となり得る。 上記のような不純物が残存している一方で窒化アルミニゥ
ム粒子が成長している窒化アルミニウムを主成分とする焼結体は必ずしも光 ¾i性がなかった りあるいは小さいものではなく、 耀過率 6 0 %〜 8 0 %の高いものが得られる。 このような 窒化アルミニウムを主成分とする焼結体は結晶性の高い窒化ガリウム、 窒化インジウム、 窒化 アルミニウムのうちから選ばれた少なくとも 1種以上を主成分とする単結晶薄膜を形成し得る 優れた基板となり得る。
このような A 1 Ν の高い窒化アルミニウムを主成分とする焼結体あるいは窒化アルミ二 ゥム粒子が成長した窒化アルミニウムを主成分とする焼結体あるいは A 1 N繊が高くかつ窒 化アルミニゥム粒子が成長した窒化アルミ二ゥムを主成分とする焼結体は可視光あるいは紫外 光 ¾ 率カ搞まる。 さらに、 熱伝導率も例えば室温において 2 0 OWZmK以上あるいは 2 2 OW/mK以上に向上できるという副次的な効果をもたらす。 元来窒化アルミニウムを主成分 とする焼結体は熱伝導率が室温において少なくとも 5 OW/mK以上、 通常は 1 0 OW/mK 以上と高くそのため窒化アルミニウムを主成分とする焼結体を基材として用いて作製される発 光素子はそこに加えられる電力を基板がサファイアの場合に比べて大きくできるので発光素子 の発光出力が高まるという利点を有するが、 さらに例えば上記のような方法で熱伝導率を室温 において 2 0 OWZmK以上に高めることでさらに発光素子の発光出力を高めることができよ り好ましい。
さらに上記 A 1 N ^の高い窒化アルミニウムを主成分とする焼結体あるいは窒化アルミ二 ゥム粒子が成長した窒化アルミニウムを主成分とする焼結体は可視光及び/又は波長 2 0 0 n m〜3 8 0 nmの範囲の紫外光における光 ¾i率が高まり 2 0〜4 0 %以上と比較的高いもの が得られ易いので発光素子からの光が基板で吸収される割合が減り発光^?の発光効率が高ま るという別の利点もある。
上記の高渡化された窒化アルミニウムを主成分とする焼結体の)1 ά¾ϋ性を高めるためには 焼成に供する粉末成形体や焼結体の形状はどのようなものでも用いることができるが同じ体積 であれば立方体や直方体あるいは円柱状などのブロック状よりも例えば板状などより表面積の 大きなものを用いることが好ましい。また上記焼成に供する粉末成形体や焼結体の形状でその 1 辺大きさが 8mm以下のものを用いることが高 «化された窒化アルミニウムを主成分とする 焼結体の光 ¾1性を高める上で好ましい。 さらに上記の 1辺の大きさが 5 mm以下のものを用 いることがより好ましく、 上記の 1辺の大きさが 2. 5 mm以下のものを用いることがさらに 好ましく、 1辺の大きさが l mm以下のものを用いることが最も好ましい。 上記焼成に供する 粉末成形体や焼結体の形状が板状のときその厚みは 8 mm以下のものを用いることが高 Jt化 された窒化アルミニウムを主成分とする焼結体の 過性を高める上で好ましい。 さらに上記 板状の粉末成形体や焼結体の厚みは 5 mm以下のものを用いることがより好ましく、 厚み 2. 5 mm以下のものを用いることがさらに好ましく、 厚み l mm以下のものを用いることが最も 好ましい。 上記に示したことを具体的に述べれば例えば、 組成が実質的に同じで実質的に A 1 N単一相の焼結体であつても上記立方体や直方体あるいは円柱状などのプロック状のものある いは 1辺が 5mmを越える粉末成形体や焼結体を用いて S¾iした高繊化された窒化アルミ二 ゥムを主成分とする焼結体では板状あるいは 1辺が 8 mm以下の成形体や焼結体を用いて製造 したものに比べて光 ¾ 率が低減化し、 ±易合によっては黒色化して光 ¾1率がゼロに近いもの となる場合がある。 その理由は必ずしも明確ではないが、 焼成の過程で A 1 N以外の成分が揮 散 ·除去されるに際して該揮散成分の圧力が高まり焼結体から急激な抜け方をしたり、 例えば 焼結助剤の Y 2 O 3など揮散中に X線回折や化学分析では判別できにくい微量成分が窒化物や炭 ィ匕物などの還元生成物に変質するためではないかと推測される。
上記例示した方法などを ¾Μいることで窒化アルミニウムを主成分とする焼結体の、 1 ) 緻密度、 2)気?しの量や大きさ、 3)焼結助剤などの量や分布、 4)酸素の含有量や存在状態、
5) 焼結助剤以外の不純物の量や分布、 6) 窒化アルミニウム粒子の大きさや! ^分布、 7) 窒化アルミニウム粒子の形状、 などを制御できる。
また、 上記のように含まれるアルミニウム及び窒素以外の成分を飛散 ·鉄し減少化させる 焼成法により製造された焼結体は通常の焼成法 (上記した減圧下、 常圧下、 雰囲気加圧下、 ホ ットプレス、 H I Pなどの方法を含む) により製造されたものに比べて光透過性が高くなり、 A l N Jtも高くなり、 窒化アルミニウム粒子の大きさも大きくなる、 といった特徴がある。 このような焼結体は多結晶体ではあるが、粒界の影響が少なくなるので単結晶の性状に近づくた め該焼結体を基板として用いたものに形成される単結晶薄膜の結晶性が高まるなど窒化ガリウ ム、 窒化インジウム、 窒化アルミニウムのうちから選ばれた少なくとも 1種以上を主成分とす る薄膜の品質が向上し易い。 本発明はこのような高 化を目的とした焼成法により製造され る A 1 Ν«を高めた窒化アルミニウムを主成分とする焼結体あるいは窒化アルミニウム粒子 の大きさを成長させた窒化アルミニウムを主成分とする焼結体あるいは A 1 N«を高め窒化 アルミニウム粒子の大きさを成長させた窒化アルミニウムを主成分とする焼結体も提供する。 上記窒化アルミニウムを主成分とする焼結体の S8tに用いる原料粉末は酸化アルミニウムを カーボンで ϋ¾し、 窒化する酸化物 ¾法によるもの、 あるいは金属アルミニウムを直接窒化 する直接窒化法によるもの、 塩化アルミニウム、 トリメチルアルミニウム、 アルミニウムアル コキシドなどのアルミニウム化合物を分解し気相中でアンモニアなどを用いて窒化する CVD 法、 といった方法で作製されたものが使用される。 焼結体の 性を高めるためには均一な サブミクロンの一次粒子を有し化学的な «の高レ酸化物 S¾法により作製された原料を用い ることが好ましい。そのため上記方法による原料のうち酸ィ匕アレミニゥムをカーボンで^し、 窒化する酸化物斷法によるもの、 あるいは金属アルミニウムを直接窒化する直接窒化法によ るものを単独で用いるか混合して用いることが好ましい。
窒化アルミニウムを主成分とする焼結体の 過率は上記 S ^法を いることで 6 0〜 8 0 %程度あるいは 8 0〜9 0 %以上のものが得られる。 4 0 %以上の) 率を有する窒化 アルミニウムを主成分とする焼結体を基板として用いることで該基板に直接形成された窒化ガ リウム、 窒化インジウム、 窒化アルミニウムのうちから選ばれた少なくとも 1種以上を主成分 とする単結晶薄膜の結晶性はミラ一指数 (0 0 2) の格子面の X線回折ロッキングカーブの半 値幅が 1 5 0秒以下と良好なものが得られ易く好ましい。 また 6 0 %以上の高い光透過率を有 する窒化アルミニウムを主成分とする焼結体を基板として用いることで窒化ガリゥム、 窒化ィ ンジゥム、 窒化アルミニウムのうちから選ばれた少なくとも 1種以上を主成分とする単結晶薄 膜の結晶性はミラ一指数 (0 0 2) の格子面の X線回折ロッキング力一ブの半値幅が 1 3 0秒 以下と良好なものが得られ易く特に好ましい。 また 8 0 %以上の高い 率を有する窒化ァ ルミ二ゥムを主成分とする焼結体を基板として用いることで窒化ガリゥム、 窒化ィンジゥム、 窒化アルミニウムのうちから選ばれた少なくとも 1種以上を主成分とする単結晶薄膜の結晶性 はミラー指数 ( 0 0 2) の格子面の X線回折ロッキングカーブの半値幅が 1 0 0秒以下と良好 なものが得られ易く最も好ましい。 上記 ¾¾ 率は通常波長 6 0 5 nmの単色光で測定された ものであるが前記方法により測定された¾¾ 率を有する窒化アルミニウムを主成分とする焼 結体は波長 3 8 0 nm〜8 0 0 nmの範囲の全可視光領域でも同様な光 ¾1率を有する。 また このような可視光に対する ^過率を有する窒化アルミ二ゥムを主成分とする焼結体は波長 2 0 0 nm〜3 8 0 nmの範囲の紫外領域の光においても高い 率を有し、 この紫外領域の 光の中で波長 2 5 0 nm〜3 8 0 nmの範囲の光においてはより高い光透過率を有する。 本発明において基板は窒化アルミニウムを主成分とする焼結体であるため焼結体中の窒化ァ ルミニゥム粒子の結晶方位はランダムな方向を向いている。 したがって該上記窒化アルミニゥ ムを主成分とする焼結体中の窒化アルミニゥム粒子は窒化ガリゥムゃ窒化ィンジゥムと同じゥ
ルツ鉱型の結晶構造であり格子定数も殆ど同じであるが窒化ガリウム、 窒化インジウム、 窒化 アルミニウムのうちから選ばれた少なくとも 1種以上を主成分とする単結晶薄膜と基板とは従 来から言われている理論的な考え方において格子整合するとは言い得ない。 このように理論的 には基板と格子整合し得ないと思われるにもかかわらず基板上に形成される薄膜は単結晶であ る。実際本願発明者 化アルミニウムを主成分とする焼結体からなる基板上に窒化ガリゥム、 窒化インジウム、 窒化アルミニウムのうちから選ばれた少なくとも 1種以上を主成分とする薄 膜を 0. 5〜5 nm程度の比較的薄い厚みで形成してみたが少なくとも窒化ガリウム、 窒化ィ ンジゥムを主成分とする薄膜はミラ一指数 (0 0 2) の格子面の X線回折ロッキングカーブの 半値幅が 3 0 0秒以下の良好な結晶性を有する単結晶薄膜である。 また窒化アルミニウムを主 成分とする上記厚み 0. 5〜 5 nmの薄膜も電子線回折で単結晶であると判定される。 上記窒 化ガリウム、 窒化インジウム、 窒化アルミニウムのうちから選ばれた少なくとも 1種以上を主 成分とする薄膜の厚みを 3〜6 m及び 1 0 m以上と厚く形成したものでもミラー指数 ( 0 0 2) の格子面の X線回折ロッキングカーブの半値幅が 3 0 0秒以下と良好な結晶性のものが 得られる。 さらに可視光に対する) ·6¾過率以外に下記に示すような窒化アルミニウムを主成分 とする焼結体の特性により基板上に形成される窒化ガリウム、 窒化インジウム、 窒化アルミ二 ゥムのうちから選ばれた少なくとも 1種以上を主成分とする単結晶薄膜の結晶性をミラー指数 ( 0 0 2) の格子面の X線回折ロッキングカーブの半値幅が 3 0 0秒〜 1 5 0秒以下のより良 好なものとすることもできる。 本発明による窒化アルミニウムを主成分とする焼結体という多 結晶体からなる基板を用いることで窒化ガリウム、 窒化インジウム、 窒化アルミニウムのうち から選ばれた少なくとも 1種以上を主成分とする単結晶薄膜がなぜ形成できるのかその原因に ついては現時点では必ずしも明確ではない。 おそらく窒化アルミニゥムという化学成分とそれ が有する結晶構造のために焼結体内で窒化アルミニゥム微粒子がまつたくランダムな方向性で あっても、 その上に窒化ガリウム、 窒化インジウム、 窒化アルミニウムのうちから選ばれた少 なくとも 1種以上を主成分とする気体成分が気体から固体に変化し核成長が始まるとき に 例えば C軸方向に整列し単結晶化し易い性状をもともと有しているのではないかと推測される。 すなわち窒化アルミニウムという焼結体中の主成分そのものが、 窒化ガリウム、 窒化インジゥ ム、 窒化アルミニゥムのうちから選ばれた少なくとも 1種以上を主成分とする成分が気体から 固体へ変化し窒化アルミニウムを主成分とする焼結体からなる基板上へ薄膜が形成される過程 において薄膜の単結晶化を手助けするような性質をもともと強く持っているためではないかと 衝則される。基板が窒化アルミニウムと同じ六方晶あるい 方晶の結晶系に属する炭化珪素、 窒化珪素、 窒化ガリウム、 酸化アルミニウム、 酸化亜鉛、 酸化ベリリウム、 などを主成分とす る焼結体でも該薄膜の単結晶似鍵成できるが形成された薄膜の結晶性において窒化アルミ二 ゥムを主成分とする焼結体をもちいた基板上に直接形成されたものが優れていることからも上 記推察の妥当性が間接的ながらも説明できる。 また薄膜がいったん窒化ガリウム、 窒化インジ ゥム、窒化アルミニウムのうちから選ばれた少なくとも 1種以上を形成しうる成分を含む気体、 イオン、 単肝あるいは 線などを経てその後窒化ガリウム、 窒化インジウム、 窒化アルミ ニゥムのうちから選ばれた少なくとも 1種以上を主成分とする固体膜へと変換される過程を経 た薄膜は単結晶化したものが得られ易い。
本発明において基板としては窒化アルミニウムを 5 (Η«%以上含む焼結体を用いることで 窒化ガリウム、 窒化インジウム、 窒化アルミニウムのうちから選ばれた少なくとも 1種以上を 主成分とする単結晶薄膜が直接基板上に形成され易くなるので好ましい。 なお窒化アルミニゥ ムを主成分とする焼結体からなる基板中の窒化アルミニウムの含有量は焼結体に含まれる希土 素化合物、 アルカリ土類金属化合物、 酸素、 アルカリ金属、 珪素、 M o、 W、 V、 N b、 T a、 T iなどの金属成分、 カーボン、 Mo、 W、 V、 N b、 T a、 T i以外の不可避金属成
分、 AL〇N、 上記アルミニウム以外の金属成分、 などアルミニウム以外の成分の含有量をそ れぞれ元素霧として求めることにより容易に算定できる。 なお酸素は酸化アルミニウムとし て換算したものである。
上記推測は実際窒化アルミニウムを主成分とする焼結体の) e®i性と基板上に形成される窒 化ガリウム、 窒化インジウム、 窒化アルミニウムのうちから選ばれた少なくとも 1種以上を主 成分とする単結晶薄膜の結晶性とに相関が見られることからもある程度は説明されうる。 すな わち、 窒化アルミニウムを主成分とする焼結体の ½¾ 性は、 1 ) 焼結体の密度、 2) '焼結体 内部の気孔の有無や大きさ、 3 ) 焼結体の焼結助剤や黒色化剤の含有量、 4) 焼結体の酸素含 有量、 5 ) 焼結体の焼結助剤及び酸素以外の不純物含有量、 6 ) 焼結体中の窒化アルミニウム 粒子の大きさ、 7) 焼結体中の窒化アルミニウム粒子の形状、 といった要因で変化するが、 こ れら焼結体の光翻性に影響を与える要因は窒化ガリウム、 窒化インジウム、 窒化アルミニゥ ムのうちから選ばれた少なくとも 1種以上を主成分とする単結晶薄膜の生成に対しても何らか の影響を与えている可能性が高いと思えるからである。
本発明において、 窒化アルミニウムを主成分とする焼結体の ¾¾i性と該焼結体からなる基 板上の窒化ガリウム、 窒化インジウム、 窒化アルミニウムのうちから選ばれた少なくとも 1種 以上を主成分とする単結晶薄膜の生成との間には上記のように相関が認められるが、 窒化アル ミニゥムを主成分とする焼結体の可視光に対する光 率あるいは紫外光に対する光 ¾率が それぞれ 1 %より低いかあるいは実質的に光を ¾ しないものであっても窒化アルミニウムを 主成分とする焼結体からなる基板上に窒化ガリウム、 窒化インジウム、 窒化アルミニウムのう ちから選ばれた少なくとも 1種以上を主成分とする単結晶薄膜の生成は可能である。 例えばモ リブデン、 タングステン、 力一ボンなどの黒色化元素を含むものや鉄、 ニッケル、 クロム、 マ ンガンなどの不可避金属不純物を含むものあるいはリチウムなどのアル力リ金属や珪素化合物 などの焼成 低減化剤を含む窒化アルミニウムを主成分とする焼結体の光醒率は 1 %より 低いかあるいは実質的に;)1 ά¾ 率はゼロの場合が多い。 このような焼結体からなる基板であつ てもその上には窒化ガリウム、 窒化インジウム、 窒化アルミニウムのうちから選ばれた少なく とも 1種以上を主成分とする単結晶薄膜が ¾:接形成でき、 さらにその結晶性は上記ミラー指数
( 0 0 2 ) の格子面の X線回折ロッキングカーブの半値幅が 3 0 0秒以下と良好なものも得ら れる。 このことはやはり前記のように、 窒化アルミニウムという焼結体中の主成分そのものが 窒化ガリウム、 窒化インジウム、 窒化アルミニウムのうちから選ばれた少なくとも 1種以上を 主成分とする成分力 misや肝線を経て窒化アルミニウムを主成分とする焼結体からなる基板 上へ薄膜として形成される過程で容易に単結晶化されるのを手助けするような性質をもともと 持っているためと推測される。
窒化アルミニウムを主成分とする焼結体の密度であるが、 窒化アルミニウムや焼結助剤など が密に詰まった状態でないと単結晶薄膜は形成できないであろうことは容易に撤則できる。 実 際本発明において窒化アルミニウムを主成分とする焼結体の相対密度 9 5 %以上であることが 好ましくこのような基板には直接窒化ガリウム、 窒化インジウム、 窒化アルミニウムのうちか ら選ばれた少なくとも 1種以上を主成分とする単結晶薄膜が形成できる。 実際本発明において 窒化アルミニウムを主成分とする焼結体の相対密度 9 8 %以上で該窒化アルミニウムを主成分 とする焼結体からなる基板に直接形成された窒化ガリウム、 窒化インジウム、 窒化アルミニゥ ムのうちから選ばれた少なくとも 1種以上を主成分とする単結晶薄膜のミラー指数 ( 0 0 2 ) の格子面の X線ロッキングカーブの半値幅が 3 0 0秒以下のものが形成され易い。 焼結体の相 対密度 9 9 %以上で該単結晶薄膜のミラ一指数 (0 0 2 ) の格子面の X線ロッキングカーブの 半値幅として 2 4 0秒以下のものが形成され易くより好ましい。また、焼結体の相対密度 9 9. 5 %以上で該単結晶薄膜のミラー指数 (0 0 2 ) の格子面の X線ロッキングカーブの半値幅と
して 200秒以下のものが形成され易くさらに好ましい。 なお、 本発明において相対密度は焼 結助剤や黒色化剤などの添加物を加えないで作製した窒化アルミニウムを主成分とする焼結体 は窒化アルミニウムの理論密度(3. 26 lg/cm3) に対するものであるが、 焼結助剤や黒 色化剤などの添加物を加えて作製した窒化アルミ二ゥムを主成分とする焼結体は窒化アルミ二 ゥムの理論密度に対するものではなく窒化アルミニウムと焼結助剤などの成分が単に混合して いていると見なしたとき計算上の密度に対する値で示した。 したがって窒化アルミニウムを主 成分とする焼結体の相対密度は焼結体組成に依存する。 具体的に言えば例えば窒化アルミニゥ ム (A1N) を 95重量%、 酸化イットリウム (Y2〇3) を 5重量%含む窒化アルミニウムを 主成分とする焼結体において、 A 1 Nの密度は 3.261 g/cm3であり、 Y2〇3の密度は 5. 03 g/cm3であるからこの組成の焼結体が完全に緻密化したときの密度は 3. 319 g/c m3であると算定されるので、実際得られた焼結体の密度と前記計算上の密度との百分率が本発 明で言う相対密度となる。 さらに具体例を示せば窒化アルミニウム (A1N) を 90重量%、 酸化エルビウム (Er203) を 10重量%含む窒化アルミニウムを主成分とする焼結体におい て、 Er2〇3の密度は 8. 64 gZcm3であるからこの組成の搬吉体が完全に緻密化したとき の密度は 3. 477gZcm3であると算定されるので、実際得られた^;結体の密度と前記計算 上の密度との百分率が本発明で言う相対密度となる。また窒化アルミニウム(A 1 N)を 99. 5重量%、 酸化カルシウム (CaO) を 0. 5重量%含む窒化アルミニウムを主成分とする焼 結体において、 C a〇の密度は 3. 25 g/c m3であるからこの糸!^の焼結体が完全に緻密化 したときの密度は 3. 261 gZ cm3であると算定されるので、実際得られた焼結体の密度と この計算上の密度との百分率が本発明で言う相対密度となる。
また窒化アルミニウムを主成分とする焼結体内部の気孔の大きさも小さいほうが良質な単結 晶薄膜が形成できるであろうことも容易に推測できる。 実際本発明において焼結体中の気孔の 大きさが平均 1 m以下で該窒化アルミニウムを主成分とする焼結体からなる基板に直接形成 された窒化ガリウム、 窒化インジウム、 窒化アルミニウムのうちから選ばれた少なくとも 1種 以上を主成分とする単結晶薄膜のミラー指数 (002) の格子面の X線ロッキングカーブの半 値幅が 300秒以下のものが形成され易い。 また、 気孔の大きさが平均 0. 7 以下で該単 結晶薄膜のミラ一指数 (002) の格子面の X線ロッキングカーブの半値幅として 240秒以 下のものが形成され易くより好ましい。 また、 気孔の大きさが平均 0. 5 m以下で該単結晶 薄膜のミラー指数 (002) の格子面の X線ロッキングカーブの半値幅として 200秒以下の ものが形成され易い。
上記焼結体密度の向上、 及び焼結体内部気孔の減少あるいは内部気孔の大きさを小さくする ためには例えば以下の方法が有効である。 すなわち、 1. 焼結体 用原料として一次粒子が サブミクロンで粒子サイズの分布が均一なものを使用する、 2. を低減化し粒子成長 を抑制する、 3. 雰囲気加圧焼成ゃホットプレスあるいは H I Pなど焼成を 1気圧より高い状 態で行う、 4. 焼成において保持温度を多段階に行う、 5. 減圧焼成あるいは常圧焼成と雰囲 気加圧焼成ゃホットプレスあるいは H I Pなどの 1気圧より高い雰囲気下での焼成とを組み合 わせて行う、 などである。 また、 上記方法を 2以上組み合わせて行うことも有効である。 また本発明による基板は主成分である窒化アルミニウム以外に焼結助剤として例えば S c 2 03、 Y203、 La203、 Ce02、 Pr60l Nd2〇3、 Pm203、 Sm2Os、 Eu2〇3、 Gd203、 Tb4〇7、 Dy203、 Ho2〇3、 Er2〇3、 Tm2〇3、 Yb203、 Lu2〇3、 など の希土類 素酸化物あるいはその他 S c、 Y、 La、 Ce、 Pr、 Nd、 Pm、 Sm、 Eu、 Gd、 Tb、 Dy、 Ho、 Er、 Tm、 Yb、 L uなどの希土類£素成分、 あるいはその他 S c、 Y、 La、 Ce、 Pr、 Nd、 Pm、 Sm、 Eu、 Gd、 Tb、 Dy、 Ho、 Er、 Tm、 Yb Luなどを含む炭酸塩、 硝酸塩、 硫酸塩、 塩化物などの無機希土類化合物、 酢酸塩、 蓚
酸塩、 クェン酸塩などの有機希土類化合物などの各種希土 素化合物、 Be〇、 MgO、 C aO、 S rO、 B a〇などのアルカリ土類金属酸化物や Be、 Mg、 Ca、 S r、 Baなどの アルカリ土類金属元素成分、 あるいはその他 Be、 Mg、 Ca、 Sr、 B aなどを含む炭酸塩、 硝酸塩、 麵塩、 塩化物などの無機アルカリ土類金属化合物、 酢酸塩、 謙塩、 クェン酸塩な どの有機ァリレ力リ土類金属化合物などの各種アル力リ土類金属化合物、 ! « J 低減化のため に希土観素化合物とアルカリ土類金属化合物を同時併用で用いることや L i 2〇、 L i 2C03、 L iF、 L iOH、 Na2〇、 Na2C〇3、 NaF、 NaOH、 K20、 K2C03、 KF、 KO Hなどのアルカリ金属化合物や S i〇2、 S i 3N4、 S i Cなどの珪素化合物、黒色化をはかる ために Mo、 W、 V、 Nb、 Ta、 Tiなどを含む金属、 合金及び金属化合物やカーボンなど の成分を含んだものも用いることができる。 本発明による窒化アルミニウムを主成分とする焼 結体には上記のように希土観素成分及びアルカリ土類金属成分、 アルカリ金属成分、 珪素成 分、 Mo、 W、 V、 Nb、 Ta、 Ti、 カーボンなどの成分を含むものを用いることができる。 これら焼結助剤や 低減化剤、 黒色化剤も焼結体の光 ¾1性に影響を与えることは容易 に衡則できる。 実際本発明において窒化アルミニウムを主成分とする焼結体からなる基板にお いて、 上記主成分である窒化アルミニウム以外の成分の含有量は希土 素及びアル力リ土類 金属の場合は酸化物購で合計 25體%以下、 アルカリ金属及ぴ 素の場合は酸化物騰で 合計 10 %、 上記黒色化をはかるための成分は元素 で合計 25#¾%以下の焼結体を 用いることで、 基板上には直接窒化ガリウム、 窒化インジウム、 窒化アルミニウムのうちから 選ばれた少なくとも 1種以上を主成分とする単結晶薄膜が形成され易い。 このとき基板上に直 接形成された該単結晶薄膜の結晶性はミラー指数 (002) の格子面の X線回折ロッキング力 ーブの半値幅において 300秒以下と良好なものが得られ易い。 また、 アルカリ金属成分及び 珪素成分を酸化物匪で合計 5體%以下含む 化アルミニウムを主成分とする焼結体を基板 として用いることで、 基板上には直接窒化ガリウム、 窒化インジウム、 窒化アルミニウムのう ちから選ばれた少なくとも 1種以上を主成分とする単結晶薄膜が形成され易い。 このとき基板 上に直接形成された該単結晶薄膜の結晶性はミラ一指数 (002) の格子面の X線回折ロッキ ング力一ブの半値幅において 240秒以下と良好なものが得られ易い。 アルカリ金属成分及び 珪素成分はそれぞ 独で含有されたものであってもよいしアルカリ金属成分及ぴ 素成分を 同時に含有された状態であってもよい。 上記焼結助剤や «¾Jt低減化剤、 黒色化剤は窒化ァ ルミ二ゥムと異なる化合物や結晶相を焼結体内部に生じ易い。 上記焼結助剤や焼成 £g低減化 剤、 黒色化剤により生成した化合物や結晶相の結晶構造は窒化ガリウム、 窒化インジウム、 窒 化アルミニウムなどのウルッ鉱型と異なるので上記焼結助剤ゃ舰 J 低減化剤、 黒色化剤に より生成した化合物や結晶相が多量に存在している基板上では結晶核成長の方向カ坏規則とな り易く良好な結晶性を有する窒化ガリウム、 窒化インジウム、 窒化アルミニウムのうちから選 ばれた少なくとも 1種以上を主成分とする単結晶薄膜は得られにくいものとも推測される。 本発明で言う上記基板を構成する窒化アルミニゥムを主成分とする焼結体に含まれる希土類 元素及びアル力リ土類金属の含有量とは含まれる希土類及びアル力リ土類金属を希土類 素及 びアルカリ土類金属元素として重量百分率 (重量%) で求めその後希土 11¾素酸化物及びアル カリ土類金属酸化物に換算し、 さらにこれら酸化物の密度から龍百分率 (#¾%) に算定し 直して求めたものである。 換算に用いる希土類 素酸化物は Sc2〇3、 Y203、 La203、 C e〇2、 P r Nd2〇3、 Pm203、 Sm203、 Eu203、 Gd203、 Tb407、 Dy2 03、 Ho203、 Er 203、 Tm203、 Yb203、 Lu203であり、 アルカリ土類金属酸化物 は BeO、 MgO、 Ca〇、 S r 0、 BaOである。 また、 基板を構成する窒化アルミニウム を主成分とする焼結体に含まれるアル力リ金属及び珪素の含有量とは含まれるアル力リ金属及 ぴ 素の含有量をアルカリ金属元素及び 素として重量百分率 (重量%) で求めその後アル力
リ金属酸化物及ぴ 素酸化物に換算し、 さらにこれら酸化物の密度から確百分率 (體%) に算定し直して求めたものである。觀に用いるアルカリ金属酸化物は L i 20、 N a 2〇、 K2 〇、 R b 2〇、 C s 20であり、 珪素酸化物は S i〇2 (密度: 2. 6 5 g/ c m3)、 である。 ま た、 基板を構成する窒化アルミニウムを主成分とする焼結体に含まれる Mo、 W、 V、 N b、 T a、 T iなどを含む金属、 合金及び金属化合物やカーボンなどを含む化合物の含有量とは、 含まれる Mo、 W、 V、 N b、 T a、 T i、 力一ボン各成分の含有量を元素として重量百分率 (重量%) で求め、 さらにこれら元素の密度から髓百分率 (碰%) に算定し直して求めた ものである。
本発明において特に断らない限りアルカリ土類金属にはカルシウム(C a)、ストロンチウム (S r )、 バリウム (B a)、 ラジウム (R a) だけでなくベリリウム (B e ) 及びマグネシゥ ム (Mg) を含む。
なお上記髓% (髓百分率) と 板に含まれる窒化アルミニウム以外の各元素成分を酸 化物に換算しこの酸化物の密度と重量百分率とから算定したものである。 例えば前記基板に含 まれる窒化アルミニウム以外の各元素成分がお互いにあるいは酸素や遷移金属などの不可避混 入成分と反応して実際生じる反応物の体積百分率を意味するものではないが焼結体の緻密さを 測る尺度になり得る。
具体的に言えば例えば窒化アルミニウム (A 1 N) を 9 5重量%、謝匕イットリウム (Y2〇 3) を 5重量%含む窒化アルミニウムを主成分とする焼結体において、 A 1 Nの密度は 3. 2 6 l gZc m3であり、 Y203の密度は 5. 0 3 g/cm3であるから希土類 素化合物の含有量 は 3. 3 0#¾%であると算定される。 また窒化アルミニウム (A 1 N) を 9 0重量%、 酸化 エルビウム (E r 203) を 1 0重量%含む窒化アルミニウムを主成分とする焼結体において、 E r 203の密度は 8. 6 4 gZ c m3であるから希土 ¾素化合物の含有量は 4. 0 2#¾%で あると算定される。 また窒化アルミニウム (A 1 N) を 9 9. 5重量%、 炭酸カルシウム (C a C03) を酸化カルシウム (C a O) »で 0. 5重量%含む窒化アルミニウムを主成分とす る焼結体において、 C a Oの密度は 3. 2 5 gZc m3であるからアルカリ土類金属化合物の含 有量は 0. 5 0体積%であると算定される。
また、本発明による基板は主成分である窒化アルミニウム以外に上記能結助剤としての成分、 黒色化をはかるための成分、 焼成 の低減化を図るための成分だけでなく焼結体 用原料 に含まれさらに S¾t工程から混入し易い遷移金属の不可避不純物成分を含有する。 このような 不可避不純物は希土 素及び Mo、 W、 V、 N b、 T a、 T i以外の遷移金属例えば鉄、 二 ッケル、 クロム、 マンガン、 ジルコニウム、 ハフニウム、 コバル卜、 銅、 亜鉛などの成分を含 むものである。 本発明において上記 「遷移金属の不可避不純物成分を含有する」 とは上記鉄、 ニッケル、 クロム、 マンガン、 ジルコニウム、 ハフニウム、 コバルト、 銅、 亜鉛などの成分の うちの少なくとも 1種以上を含むことを意味する。 窒化アルミニウムを主成分とする焼結体か らなる基板に含まれる上記遷移金属などの不可避不純物成分の混入量 «®常 1重量%以下であ る場合が多く 0. 5重量%以下、 あるいは 0. 2重量%以下、 好ましくは 0. 0 5重量%以下 である。 勿論このような不可避不純物の混入はできるだけ少ない方が好ましいが本発明におい ては上記鉄、 ニッケル、 クロム、 マンガン、 ジルコニウム、 ハフニウム、 コバルト、 銅、 亜鉛 などの遷移金属成分を比較的多く含む窒化アルミニゥムを主成分とする焼結体であつても基板 には直接窒化ガリウム、 窒化インジウム、 窒化アルミニウムのうちから選ばれた少なくとも 1 種以上を主成分とする単結晶薄膜が形成できる。 すなわち、 窒化アルミニウムを主成分とする 焼結体中の上記鉄、 ニッケル、 クロム、 マンガン、 ジルコニウム、 八フニゥム、 コバルト、 銅、 亜鉛などの遷移金属成分の含有量は元素換算で 3 0重量%以下であることが好ましく基板上に は直接窒化ガリゥム、 窒化ィンジゥム、 窒化アルミニゥムのうちから選ばれた少なくとも 1種
以上を主成分とする単結晶薄膜が形成でき、 このとき窒化アルミニウムを主成分とする焼結体 からなる基板上に形成された該単結晶薄膜の結晶性はミラー指数 ( 0 0 2) の格子面の X線回 折ロッキングカーブの半値幅において 3 0 0秒以下と良好なものが得られ易い。 又不可避不純 物を含む成分の含有量が元素換算で 2 0重量%以下の基板を用いることで基板上に直接形成さ れた該単結晶薄膜の結晶性はミラー指数 ( 0 0 2 ) の格子面の X線回折ロッキングカーブの半 値幅において 2 4 0秒以下と良好なものが得られ易いので、 基板としてはより好ましく、 1 0 重量%以下であることが基板上に直接形成された該単結晶薄膜の結晶性はミラー指数 (0 0 2) の格子面の X線回折ロッキングカーブの半値幅において 2 0 0秒以下と良好なものが得られ易 いのでより好ましい。 窒化アルミニウムを主成分とする焼結体の製造に際して高純度原料を使 用しダリ一ンシ一卜や粉末プレス用顆粒製造あるいは焼成などの製造工程でセラミックが接触 する部分に使用する部材の高純度化をはかるなどの工夫で不可避不純物の混入を減少すること ができる。
また、本発明による基板は主成分である窒化アルミニウム以外に上記^;結助剤としての成分、 黒色化をはかるための成分、 焼成温度の低減化を図るための成分、 不可避金属不純物成分だけ でなく焼結体製造用原料に含まれさらに $ ^工程から混入する酸素を含有する。 焼結体 S ^用 原料には通常酸素が 0. 0 1〜5. 0重量%程度含まれ、 焼成中に一部揮散するが殆どこのま ま焼結体中に取り込まれることが多く焼結助剤などを用いないで された焼結体中にはスピ ネル型結晶構造の AL ON (酸窒化アルミニウム: A I Nと A l 2〇3との化合物) が生成され ることが多い。 この AL ONは通常 J C P D Sファイル番号 3 6 - 5 0に示される回折線を示 す。 酸素は又焼結体中に AL ONを生成するよう積極的に A 1 203を添加することにより含有 される。 さらに、 焼結助剤や黒色化剤が ¾化物や複合酸化物など酸素を含む化合物である場合 はこれらの分も含有される。 焼結体中の酸素量が 1 0重量%より多いと焼結体内部で A L ON あるいは焼結助剤と酸素、 黒色化剤と酸素、 焼成 ¾低減化剤と酸素、 などの化合物の生成が 多くなり単結晶薄膜の結晶性の低下をもたらし易い。 焼結体中での AL ONの生成量は酸素量 と希土類 素化合物やアル力リ土類金属化合物などの焼結助剤量で制御できるが、 焼結助剤を 用いない場合は焼結体中の酸素量だけに依存する。 上記 AL ONの結晶構造は窒化ガリゥム、 窒化ィンジゥム、 窒化アルミニウムなどのウルッ鉱型と異なるが AL ON量が窒化アルミニゥ ムを主成分とする焼結体中で 1 2 %以下であれば該窒化アルミニウムを主成分とする焼結体か らなる基板に直接形成された窒化ガリウム、 窒化インジウム、 窒化アルミニウムのうちから選 ばれた少なくとも 1種以上を主成分とする単結晶薄膜の結晶性として該単結晶薄膜のミラ一指 数 (0 0 2) の格子面の X線回折ロッキングカーブの半値幅 2 4 0秒以下のものが形成され易 く結晶性の向上が見られるので好ましい。 また、 AL ONの量が 7 %以下の焼結体を基板とし て用いることで上記 X線回折ロッキングカーブの半値幅において 2 0 0秒以下のものが形成さ れ易くより結晶性の向上が見られるので好ましい。 なお AL ONの含有量は基板表面の X線回 折により AL ONのミラ一指数 (3 1 1 ) 格子面からの回折線強度と A 1 Nのミラ一指数 ( 1 0 0) 格子面からの回折線強度との比を百分率で求めたものである。 焼結体中において 1 2 % 以下の A L〇 Nの量は焼結助剤などの添加剤を用 ^ずに窒化アルミニゥム原料粉末だけあるレ は該原料粉末と A 1 203との混合粉末とだけで焼成された焼結体において酸素量 5. 0重量% 以下のもので形成され易い。 7 %以下の AL ONの量は焼結助剤などの添加剤を用いずに窒化 アルミニウム原料粉末だけあるいは該原料粉末と A 1 203との混合粉末とだけで焼成された焼 結体において酸素量 3. 0重量%以下のもので形成され易い。 また焼結体中の AL ONの量が 2 0 %以下の基板を用いることで基板上に窒化ガリウム、 窒化インジウム、 窒化アルミニウム のうちから選ばれた少なくとも 1種以上を主成分とする単結晶薄膜のミラー指数 ( 0 0 2) の 格子面の X線回折口ッキングカーブの半値幅において 3 0 0秒以下のものが形成され易い。 2
0 %以下の AL ONの含有量は焼結助剤などの添加剤を用いずに窒化アルミニウム原料粉末だ けあるいは該原料粉末と A 1 2〇3との混合粉末とだけで焼成された焼結体において酸素量 1 0. 0重量%以下のもので形成され易い。 焼結体中に AL ONが 2 0 %より多く生成している基板 上ではミラー指数 (0 0 2) の格子面の X線回折ロッキングカーブの半値幅において 3 0 0秒 以下の良好な結晶性を有する窒化ガリウム、 窒化インジウム、 窒化アルミニウムのうちから選 ばれた少なくとも 1種以上を主成分とする単結晶薄膜は形成しにくくなる。 それはウルッ鉱型 と異なる AL ON結晶が多くなることで該単結晶薄膜の結晶成長がもともと有しているできる だけ C軸方向に向かおうとする力が阻害され不規則な方向となり易くなるためであろうと推測 される。
なお、 窒化アルミニウムを主成分とする焼結体中の AL ON含有量は上記のように X線回折 によって AL ONのミラ一指数 (3 1 1 ) 格子面からの回折線強度と A 1 Nのミラ一指数 ( 1 0 0 ) 格子面からの回折線強度との比の百分率で求めたものであるが、 該焼結体に含まれる酸 ¾ ^有量と上記 J C P D Sファイル番号 3 6— 5 0に記載されている AL ONの密度 3. 8 3 7 g / c m3とを比較してみて近似的に ί機分率と見なし得る。
また、 窒化アルミニウムを主成分とする焼結体中に A 1 N及び AL ON以外の化合物が生成 している場合 AL ONの含有量は X線回折による該化合物の最強線と A 1 N及び AL ONの最 強線を合計し AL ONの最強線との比を百分率で含めたものである。
また、本発明において酸素の含有量、及び鉄、ニッケル、 クロム、マンガン、 ジルコニウム、 ハフニウム、 コノ^レト、 銅、 亜鉛などの Mo、 W、 V、 Nb、 T a、 T i以外の遷移金属の含 有量はそれぞれの元素換算による重量百分率 (重量%) で示したが、 これら成分を體百分率 で表示し直すことは上記方法により容易に行うことができる。 鉄、 ニッケル、 クロム、 マンガ ン、 ジルコニウム、 ハフニウム、 コバルト、 銅、 亜鉛などの含有量を機百分率に算定しなお す場合はこれら鉄、 ニッケル、 クロム、 マンガン、 ジルコニウム、 ノ、フニゥム、 コバルト、銅、 亜鉛などの各成分の含有量を元素として重量百分率 (重量%) で求め、 さらにこれら元素の密 度から体積百分率 a %) に算定し直して求めることができる。 また、 酸素の含有量を体積 百分率で算定し直す場合、 有量を市販の酸素 ·窒素分析装置などを用いて元素として 重量百分率で求めた後 A 1 2〇3に騰し直して、 すなわち A 1 203の ί稀百分率として求める ことができる。 A 1 203に鍵し直す理由は霞素は窒化アルミニウムを主成分とする能結体 中でアルミニウム成分あるいは窒化アルミニウム成分あるいは希土類 素やアルカリ土類金属 などの焼結助剤と反応して A 1 203として、 あるいは AL ONとして、 あるいは希土 ¾素や アルカリ土類金属との複合酸化物として被している場合が多ぐ該 AL ONは A 1 Nと A 1 2 〇3との化合物であり該希土類 素ゃアル力リ土類金属との複合酸化物は希土類元素の酸化物 やアルカリ土類金属の酸化物と A 1 203との化合物であるため結局含まれる酸素成分は A 1 2 〇3として見なし得る場合が多いためである。 A 1 2〇3の密度は 3. 9 8 7 gZc m3でありこ れに基き容易に算定し直すことができる。
例えば 素を 5重量%含む窒化アルミニウムを主成分とする焼結体において A 1 Nの密度が 3. 2 6 1 g/ c m3であるので麵素の含有量は 8. 8 6髓%であると算定される。 また鉄 を元素換算で 1重量%含む窒化アルミニウムを主成分とする焼結体において鉄の密度が 7. 8 6 gZ c m3であるので鉄の含有量は元素換算で 0. 4 1 7体積%であると算定される。
また、 本発明において ALONの含有量を体積百分率に算定し直す場合は X線回折により A L ONの含有量を求めた後、 AL ONの密度 3. 8 3 7 g/ c m3及び A 1 Nの密度さらに AL ON及び A 1 N以外に含まれる場合はその成分の含有量と密度を求めることにより行うことが できる。 なお、 検量線の作成結果 X線回折による窒化アルミニウムを主成分とする焼結体中に 含まれる AL ONの含有量は近似的には重量分率であると見なし得る。 例えば AL ONを 1
0 %含む窒化アルミニウムを主成分とする焼結体において AL ONの含有量は 8. 6 3体積% であると算定できる。
本発明において窒化アルミニウムを主成分とする焼結体からなる基板において焼結体中の窒 化アルミニウム粒子を例えば平均 0. 5 / m程度と成長させずに、 すなわち原料粉末の粒子の 大きさと同じ状態で焼結したものも使用できる。 一方、 本発明による窒化アルミニウムを主成 分とする焼結体からなる基板において焼結体内部に含まれる窒化アルミニウム粒子の大きさが 増大化すれば該基板に形成される窒化ガリウム、 窒化インジウム、 窒化アルミニウムのうちか ら選ばれた少なくとも 1種以上を主成分とする薄膜の結晶性が向上し易い。 窒化ガリウム、 窒 化インジウム、 窒化アルミニウムのうちから選ばれた少なくとも 1種以上を主成分とする薄膜 を単結晶で形成し該単結晶薄膜の結晶性により薄膜の品質を謝面したとき窒化アルミニウムを 主成分とする焼結体内部に含まれる窒化アルミニウム粒子の大きさが平均 1 以上であれば 該焼結体からなる基板上に直接形成される単結晶薄膜のミラー指数 ( 0 0 2 ) の格子面の X線 回折ロッキングカーブの半値幅が 3 0 0秒以下のものが形成され易い。 窒化アルミニウム粒子 の大きさが平均 5 m以上の焼結体で〖滅板上に形成される窒化ガリゥム、 窒化ィンジゥム、 窒化アルミニゥムのうちから選ばれた少なくとも 1種以上を主成分とする単結晶薄膜のミラ一 指数 ( 0 0 2 ) の格子面の X線回折ロッキングカーブの半値幅が 2 4 0秒以下と良好な結晶性 のものが得られ易い。 窒化アルミニウム粒子の大きさが平均 8 m以上の焼結体では上記単結 晶薄膜のミラー指数 ( 0 0 2) の格子面の X線回折ロッキング力一ブの半値幅が 2 0 0秒以下 とより良好な結晶性のものが得られ易い。 窒化アルミニウム粒子の大きさが平均 1 5 ^m以上 の焼結体では上記単結晶薄膜のミラ一指数 (0 0 2 ) の格子面の X線回折ロッキングカーブの 半値幅が 1 5 0秒以下とさらに良好な結晶性のものが得られ易い。 窒化アルミニウム粒子の大 きさが平均 2 5 以上の焼結体では上記単結晶薄膜のミラー指数 ( 0 0 2 ) の格子面の X線 回折ロッキングカーブの半値幅が 1 3 0秒以下とさらに良好な結晶性のものが得られ易い。 こ れは焼結体内部の窒化アルミニゥム粒子の大きさが大きくなれば窒化アルミニゥム結晶粒子の 粒界の面積が減少し粒界の影響が減じるので窒化アルミニウム結晶粒子自体の性質が反映され 易くなり窒化ガリウム、 窒化インジウム、 窒化アルミニウムのうちから選ばれた少なくとも 1 種以上を主成分とする単結晶薄膜の核成長の方向をより規則的なものにし易いためであろうと 推測される。
上記のような窒化アルミニゥム粒子を大きくすることの効果は通常どのような組成の窒化ァ ルミ二ゥムを主成分とする焼結体からなる基板であっても見られる。 このような窒化アルミ二 ゥムを主成分とする焼結体の例としては前記した酸素、 あるいは焼結助剤として用いられる希 土頻 素化合物やアル力リ土類金属化合物などの成分、 あるいは焼成温度低減化剤として用い られるアルカリ金属や珪素などの成分、 あるいは黒色化剤として用いられる M o、 W、 V、 N b、 T a、 T iなどの金属成分、 あるいはカーボンあるいは M o、 W、 V、 N b、 T a、 T i 以外の不可避金属成分など、 さらに結晶相として AL ONなどを含むものである。 また、 この ような窒化アルミニウムを主成分とする焼結体の例としては原料粉末に焼結助剤を加えないで 製造され実質的に希土類 素化合物あるいはアルカリ土類金属化合物などの焼結助剤を含まな い焼結体も含まれる。 上記で例示した窒化アルミニウムを主成分とする焼結体からなる基板に おいて、 窒化アルミニウム粒子の大きさを増大することで該基板に形成される窒化ガリウム、 窒化インジウム、 窒化アルミニウムのうちから選ばれた少なくとも 1種以上を主成分とする単 結晶薄膜の品質が向上し易くなる。 窒化アルミニウムを主成分とする焼結体中の窒化アルミ二 ゥム粒子の大きさを増大化させる効果はあとでも述べるが、 窒化アルミニウム粒子の大きさを 増大ィ匕させさらに A 1 N を高めた窒化アルミニウムを主成分とする焼結体を薄膜形成用基 板として用いれば、 これら基板に形成される窒化ガリウム、 窒化インジウム、 窒化アルミニゥ
ムのうちから選ばれた少なくとも 1種以上を主成分とする単結晶薄膜の品質が向上し易くなる。 上記のような窒化アルミニゥム粒子を大きくすることの効果は通常どのような組成の窒化アル ミニゥムを主成分とする焼結体からなる基板であっても見られが、 焼結体中の A 1 Nの含有量 が少なくなるにつれて効果の程度は少なくなる傾向はある。 本発明による窒化アルミ二ゥムを 主成分とする焼結体からなる基板における A 1 Nの含有量は 5 0髓%以上であれば該基板を 用いて窒化ガリゥム、 窒化ィンジゥム、 窒化アルミニゥムのうちから選ばれた少なくとも 1種 以上を主成分とする単結晶薄膜が形成できる。 A 1 Nの含有量が 5 (H機%以上の窒化アルミ 二ゥムを主成分とする焼結体において該焼結体に形成される窒化ガリゥム、 窒化ィンジゥム、 窒化アルミニウムのうちから選ばれた少なくとも 1種以上を主成分とする単結晶薄膜のミラー 指数 ( 0 0 2 ) の格子面の X線回折ロッキングカーブの半値幅が 3 6 0 0秒以下のもの力 S得ら れ易い。 上記のような窒化アルミニウム粒子を大きくすることの効果を発現し易くするために は窒化アルミニウムを主成分とする焼結体からなる基板における A 1 Nの含有量は 8 Oi % 以上であること力 ましい。 窒化アルミニウムを主成分とする焼結体の A 1 Nの含有量が 8 0 体積%以上のものでは該焼結体に形成される窒化ガリウム、 窒化インジウム、 窒化アルミニゥ ムのうちから選ばれた少なくとも 1種以上を主成分とする単結晶薄膜のミラ一指数 ( 0 0 2 ) の格子面の X線回折ロッキングカーブの半値幅が 3 0 0秒以下のものが得られ易い。
なお、 窒化アルミニウムを主成分とする焼結体内部に含まれる結晶粒子の大きさは平均の大 きさであって含まれる結晶粒子が均等に近い大きさに揃っている状態のものだけでなく結晶粒 子の大きさカ坏揃いのものや結晶粒子の形状がいびつで針状あるいは板状など一辺が小さく他 の一辺が大きい形状の結晶粒子、 例えばポリタイプ A 1 N粒子など一辺が数 mで他の一辺が 1 0数 m以上に大きく成長した針状あるいは板状などの結晶粒子を含むものであっても本発 明においては問題なく用いることができる。
窒化アルミニウムを主成分とする焼結体中の窒化アルミニウム粒子の大きさを増大化させる ために通常誠 を高めるか焼成時間を長くすることが 果的である。 窒化アルミニウム粒 子の大きさを制御するためには窒化アルミニウムの原料粉末の由来ゃ髓、 あるいは成形体や 焼結体の組成にも依存しやすいが本発明によれば 1 7 5 0 以上の温度で 3時間以上比較的長 い時間焼成することで平均 5 m以上の窒化アルミニウム粒子を有する窒化アルミニウムを主 成分とする焼結体が得られ易い。 平均 8 m以上を有する窒化アルミニウム粒子の焼結体を得 るために 1 7 5 0 以上の温度で 1 0時間以上、 1 9 0 0 °C以上の温度では 3時間以上の焼成 を行うことが好ましい。 平均 1 5 m以上を有する窒化アルミニウム粒子の焼結体を得るため には 1 9 0 0 °C以上の温度で 6時間以上、 2 0 5 0 °C以上の温度で 3時間以上の焼成を行うこ とが好ましい。 平均 2 5 m以上を有する窒化アルミニウム粒子の焼結体を得るためには 2 0 5 0 X:以上の温度で 4時間以、 2 1 0 0 °C以上の温度で 3時間以上の焼成を行うことが好まし い。 このような焼成において窒化アルミニウム粒子の大きさが増大しているだけで酸素、 ある いは焼結助剤として用いられる希土麵素化合物やアル力リ土類金属化合物などの成分、 ある いは誠? 氐減化剤として用いられるアルカリ金属や珪素などの成分、 あるいは黒色化剤と して用いられる M o、 W、 V、 N b、 T a、 T iなどの金属成分、 あるいは力一ポンあるいは M o、 W、 V、 N b、 T a、 T i以外の不可避金属成分など、 の成分の揮散 · I ^を抑制しさ らに含まれる結晶相として AL ONなどを含有した状態の窒化アルミニウムを主成分とする焼 結体を得るためには前記したように還元性成分の比較的少ない窒素やアルゴンなどの非酸化性 雰囲気を用いることが好ましい。 一方窒化アルミニウム粒子の大きさが増大しかつ A 1 N$m が向上した窒化アルミニウムを主成分とする焼結体を得るためには水素、 一酸化炭素、 炭素、 炭化水素などの 性成分を含む非酸化性雰囲気中で焼成することが好ましい。
また、 本発明による窒化アルミニウムを主成分とする焼結体からなる基板において焼結体内
部に含まれる窒化アルミニウム粒子の形状 立子の角が れた丸いものより多角形でお互いの 面や稜線、 多角形の頂点での重なり緊密なものであることが焼結体の光 ¾i率を 1 %以上に高 め、 基板上に形成される窒化ガリウム、 窒化インジウム、 窒化アルミニウムのうちから選ばれ た少なくとも 1種以上を主成分とする単結晶薄膜の結晶性が形成されたミラー指数 (0 0 2 ) の格子面の X線回折ロッキングカーブの半値幅において 3 0 0秒以下と良好なものが得られ易 いので、 基板としては好ましい。 これは窒化アルミニウム粒子の形状が角が取れた丸いもので あれば焼結体内部において焼結体粒子同士が隙間なく合体できず窒化アルミニゥム以外の成分 からなる粒界相が介在し易く、 これら粒界相によって焼結体の^ i性は低下しさらに成長し 始めている窒化ガリウム、 窒化インジウム、 窒化アルミニウムのうちから選ばれた少なくとも 1種以上を主成分とする単結晶薄膜の核成長の方向を不規則なものとするためであろうと推測 される。 焼結体粒子が丸みを帯びたものは通常前記焼結助剤や誠温度低減化剤が過剰に含ま れる場合に見られる。 すなわち舰中過剰な焼結助剤によって過剰な液相が生成されその液相 の中で焼結体粒子が成長するので丸みを帯び易い。 本発明において焼結体粒子が丸みを帯び易 くなるのは前記の希土 素化合物やアル力リ土類金属元素化合物などの焼結助剤、 アル力リ 金属元素化合物、 珪素化合物などの焼成温度低減化剤などが前記に示した範囲より多く含まれ る場合に生じやすいということを意味する。
なお上記薄膜形成用基板として用いられる窒化アルミニウムを主成分とする焼結体を難す るための原料粉末中には通常 A 1 N成分以外に酸素を 0. 0 1重量%〜5. 0重量%程 む。 本発明において窒化アルミニウムを主成分とする焼結体中に含まれる希土観素の含有量は前 記のように酸化物換算で 5 0 %以下のものを用いることが好ましい。 窒化アルミニウムを 主成分とする焼結体中に含まれる希土 ¾素の含有量は酸化物騰で 2 5体積%以下であるこ とが、さらに好ましい。 上記希土類 素の好ましい含有量は酸化物購で 1 2. 0ίΦ¾%以下で ある。 より好ましい含有量は酸化物換算で 7. 0髓%以下である。 上記希土観素は窒化ァ ルミニゥム粉末成形体の緻密化を {©1しながら原料中に含まれる酸素をトラップし粒界相とし て析出させ焼結体中の窒化アルミニウム結晶粒子を高 it化させる作用をするので、 全体とし て得られた基板の熱伝導率を向上させる。 そのため焼成後得られた窒化アルミニウムを主成分 とする焼結体における希土観素の存在形態はアルミニウムとの複合酸化物あるいは希土 素単独の酸化物である場合が多い。 複合酸化物としての存在は X線回折により容易に同定出来 る。 薩合酸化物は希土 素を L nで表した時、 ガーネット型結晶構造の 3 L n 2〇3 · 5 A 1 203、 ぺロブスカイト型結晶構造の: L n 203 · A 1 203、 単斜晶結晶構造 2 L n 203 · A 1 2〇3、 など 3種類の結晶形のものである。 これら複合酸化物のうちの一又は二以上を同時に含 む。 上記複合酸化物は焼結体内部において主に窒化アルミニウム粒子間の粒界相として存在し ている。 本発明の基板はこれら複合酸化物が形成されたものを含む。 これら複合酸化物は窒化 アルミニウム粒子のウルッ鉱型と異なる結晶構造を有している。 本発明による薄膜形成用基板 及び ¾膜基板において希土 素の含有量が 化物換算で 5 o #¾%以下の窒化アルミニウム を主成分とする焼結体に直接形成される窒化ガリウム、 窒化インジウム、 窒化アルミニウムの うちから選ばれた少なくとも 1種以上を主成分とする単結晶薄膜は該単結晶薄膜のミラー指数 ( 0 0 2 ) の格子面の X線回折ロッキング力一ブの半値幅として 3 6 0 0秒以下のものが得ら れ易い。 また、 ±湯合によっては希土 素の含有量が衡匕物換算で 5 0鍾%以下の窒化アル ミニゥムを主成分とする焼結体に直接形成される窒化ガリウム、 窒化インジウム、 窒化アルミ ニゥムのうちから選ばれた少なくとも 1種以上を主成分とする単結晶薄膜は該単結晶薄膜のミ ラー指数 (0 0 2 ) の格子面の X線回折ロッキング力一ブの半値幅として 3 0 0秒以下のもの が得られることがある。 本発明による薄膜形成用基板及確膜基板において希土^ ΰ素の含有 量が 化物纏で 2 5 ί機%以下の窒化アルミニゥムを主成分とする焼結体に直接形成される
窒化ガリウム、 窒化インジウム、 窒化アルミニウムのうちから選ばれた少なくとも 1種以上を 主成分とする単結晶薄膜は該単結晶薄膜のミラー指数 (002) の格子面の X線回折ロッキン グカーブの半値幅が 300秒以下と結晶性に優れたものが得られ易い。 窒化アルミニウムを主 成分とする焼結体の希土類 素含有量が前記に示したように酸化物換算で 25#¾%より多い と形成された窒化ガリウム、 窒化インジウム、 窒化アルミニウムのうちから選ばれた少なくと も 1種以上を主成分とする単結晶薄膜のミラ一指数 (002) の格子面の X線回折ロッキング カーブの半値幅が 300秒以下のものが場合によっては得られなくなるのは、 おそらくこのよ うな結晶構造の異なる複合酸化物が多く生成したため単結晶薄膜の核成長の方向を一定にする 制御力が限界を超えその結果核成長カ坏規則なものとなるのではないかと推測される。 本発明 において希土 素を含む基板においてもともと焼結体中の窒化アルミニゥム粒子の形状は角 カ 又れた丸レものではなく多角形でぉ互 ¾の粒子同士面や稜線、 あるいは多角形の頂点での重 なりが隙間なく緊密なものとなり易い。 また、 希土類 素の含有量が 化物 で 12. 0体 積%以下の窒化アルミニウムを主成分とする焼結体を用いることで該窒化アルミニウムを主成 分とする焼結体に直接形成される窒化ガリウム、 窒化インジウム、 窒化アルミニウムのうちか ら選ばれた少なくとも 1種以上を主成分とする単結晶薄膜は該単結晶薄膜のミラー指数 (00 2) の格子面の X線回折ロッキングカーブの半値幅が 240秒以下とより結晶性に優れたもの が得られ易い。 また希土類 素の含有量が 化物換算で 7.0體%以下の窒化アルミニウム を主成分とする焼結体では S化アルミニウムを主成分とする焼結体に形成される窒化ガリウ ム、 窒化インジウム、 窒化アルミニウムのうちから選ばれた少なくとも 1種以上を主成分とす る単結晶薄膜は該単結晶薄膜のミラ一指数 (002) の格子面の X線回折ロッキングカーブの 半値幅が 200秒以下とさらに結晶性に優れたものが得られ易い。 この窒化ガリウム、 窒化ィ ンジゥム、 窒化アルミニウムのうちから選ばれた少なくとも 1種以上を主成分とする単結晶薄 膜の結晶性の向上はおそらく主として粒界相として存在する上記ガーネット型結晶構造の 3 L n2〇3 · 5 A 1203 (例えば 3Υ2〇3 · 5A 1203、 3Dy 2〇3 · 5 A 1203、 3Ηο203 · 5Α12〇3、 3Ε r 2〇3 · 5Α 12〇3、 3 Yb 203 · 5 A 12〇3、 など)、 ぺロブスカイト型 結晶構造の Ln2〇3. Al 203 (例えば YA103、 LaA103、 PrA103、 NdA103、 SmAl〇3、 EuA103、 GdA103、 DyA103、 HoA103、 ErAl〇3、 YbA 103、 など)、 単斜晶結晶構造 2Ln203 · A 1203 (例えば 2 Y2〇3 · A 1203、 2 Sm2 03 ·Α 1203、 2Eu203 · A 1203、 2 Gd 203 · A 12〇3、 2Dy 203 · A 1203、 2 Ηο203 ·Α12〇3、 2Er2〇3 · Al 2〇3、 2 Yb 203 · A 1203、 など) の生成量の減少 に伴うものであろうと推測される。
本発明の基板において上記窒化アルミニウムを主成分とする焼結体中に含まれるアルカリ土 類金属の含有量も前記の通り酸化物換算で 25髓%以下であることが好ましい。 好ましい含 有量は酸化物換算で 5. 0碰%以下である。より好ましい含有量は酸化物騰で 3. 0籠% 以下である。 アル力リ土類金属は窒化アルミニウム粉末成形体の緻密化を鍵しながら原料中 に含まれる酸素をトラップし粒界相として析出させ窒化アルミニウムセラミック中の A 1 N結 晶粒子を高! ^化させる作用をするので、 全体として得られた基板の熱伝導率を向上させる。 そのため «後得られた窒化アルミニウム基板におけるアルカリ土類 素の存在形態はアルミ ニゥムとの複合酸化物あるいはアル力リ土類金属単独の酸化物である場合が多い。 複合酸化物 としての存在は X線回折により容易に同定出来る。 合酸化物はアル力リ土類金属元素を A eで表した時、 3Ae〇'Al 203、 Ae ·Α 1203、 Ae · 2A 1203、 Ae · 6A 1203、 などの結晶形のものである。 これら複合酸化物のうちの一又は二以上を同時に含む。 上記アル カリ土類金属元素を含む複合酸化物は焼結体内部において主に窒化アルミニウム粒子間の粒界 相として存在している。 本発明の基板はこれら複合酸化物が形成されたものを含む。 これら複
合酸化物は窒化アルミニウム粒子のウルッ鉱型と異なる結晶構造を有している。 本発明の基板 において焼結体中のアルカリ土類金属の含有量が ¾化物換算で 2 5体積%以下のもので窒化ガ リウム、 窒化インジウム、 窒化アルミニウムのうちから選ばれた少なくとも 1種以上を主成分 とする単結晶薄膜のミラ一指数 (0 0 2) の格子面の X線回折ロッキングカーブの半値幅が 3 0 0秒以下と結晶性に優れたものが得られ易い。 本発明の基板においてアルカリ土類金属が前 記に示したように酸化物購で 2 5髓%より多いと形成された窒化ガリウム、 窒化インジゥ ム、 窒化アルミニウムのうちから選ばれた少なくとも 1種以上を主成分とする単結晶薄膜のミ ラー指数 (0 0 2) の格子面の X線回折ロッキングカーブの半値幅が 3 0 0秒以下と結晶性に 優れたものが得られにくくなる傾向を有するのは、 おそらくこのような結晶構造の異なる複合 酸化物が多く生成したため単結晶薄膜の核成長の方向を一定にする制御力が限界を超えその結 果核成長カ坏規則なものとなるのではないかと推測される。 本発明における窒化アルミニウム を主成分とする焼結体からなる基板においてアル力リ土類金属の含有量カ戰化物購で 5. 0 体積%以下のものは焼結体中の窒化アルミニゥム粒子の形状は多角形のもものが多く粒子同士 お互いの面や稜線、 あるいは多角形粒子の頂点での重なりが緊密なものとなり易い。 この組成 範囲のアルカリ土類金属を含む基板を用いることで窒化ガリウム、 窒化インジウム、 窒化アル ミニゥムのうちから選ばれた少なくとも 1種以上を主成分とする単結晶薄膜のミラー指数 ( 0 0 2) の格子面の X線回折ロッキングカーブの半値幅が 2 4 0秒以下とより結晶性に優れたも のが得られ易い。 またアルカリ土類金属の含有量が 化物換算で 3. 0體%以下の基板では 窒化ガリウム、 窒化インジウム、 窒化アルミニウムのうちから選ばれた少なくとも 1種以上を 主成分とする単結晶薄膜のミラー指数 (0 0 2 ) の格子面の X線回折ロッキングカーブの半値 幅が 2 0 0秒以下とさらに結晶性に優れたものが得られ易い。 この窒化ガリウム、 窒化インジ ゥム、 窒化アルミニウムのうちから選ばれた少なくとも 1種以上を主成分とする単結晶薄膜の 結晶性の向上はおそらく主として粒界相として する上記 3 A e O - A l 203 A e · Α 1 2 〇3、 A e · 2 A 1 203、 A e · 6 A 1 2〇3、 などウルッ鉱型と異なる結晶構造を有する複合酸 化物の生成量の減少に伴うものであろうと推測される。
本発明において窒化アルミニウムを主成分とする焼結体中に含まれる Mo、 W、 V、 N b、 T a、 T i、 カーボンのうちから選ばれた少なくとも 1種以上の成分の含有量は前記のように 元素換算で 2 5碰%以下であることが好ましい。 このような組成の窒化アルミニウムを主成 分とする焼結体からなる基板上には窒化ガリウム、 窒化インジウム、 窒化アルミニウムのうち から選ばれた少なくとも 1種以上を主成分とする単結晶薄膜が直接形成され易く該単結晶薄膜 の結晶性はミラー指数 ( 0 0 2 ) の格子面の X線回折ロッキングカーブの半値幅において 3 0 0秒以下と良好なものが得られ易い。 また、 窒化アルミニウムを主成分とする焼結体の M o、 W、 V、 N b、 T a、 T i、 カーボンのうちから選ばれた少なくとも 1種以上の成分の含有量 が元素換算で 1 0髓%以下の基板においては形成される窒化ガリウム、 窒化インジウム、 窒 化アルミニウムのうちから選ばれた少なくとも 1種以上を主成分とする単結晶薄膜の結晶性が ミラ一指数 (0 0 2 ) の格子面の X線回折ロッキング力一ブの半値幅において 2 4 0秒以下と より良好なものが得られ易い。また、窒化アルミニウムを主成分とする焼結体の Mo、 W、 V、 N b T a、 T i、 力一ボンのうちから選ばれた少なくとも 1種以上の成分の含有量が元素換 算で 5体積%以下の基板においては形成される上記単結晶薄膜の結晶性がミラ一指数(0 0 2) の格子面の X線回折ロッキングカーブの半値幅において 2 0 0秒以下とさらに良好なものが得 られ易い。
本発明において窒化アルミニウムを主成分とする焼結体中に含まれる酸素は主成分の A 1 N と反応して AL ONとして存在するかあるいは焼結助剤の希土類 J£素化合物やアルカリ土類金 属化合物と反応して粒界相として存在するかあるいは焼結体中の A 1 N結晶粒子の結晶格子に
固溶するかいずれかで存在していると思われる。 本発明において窒化アルミニウムを主成分と する焼結体中に含まれる全酸素量は 1 0重量%以下が好ましい。 全酸素量が 1 0重量%以下の 窒化アルミニウムを主成分とする焼結体からなる基板においてその上に直接形成される窒化ガ リウム、 窒化ィンジゥム、 窒化アルミ二ゥムのうちから選ばれた少なくとも 1種以上を主成分 とする単結晶薄膜のミラ一指数 ( 0 0 2) の格子面の X線回折ロッキングカーブの半値幅が 3 0 0秒以下と結晶性に優れたものが得られ易い。 全酸素量が 5. 0重量%以下の焼結体で窒化 ガリウム、 窒化インジウム、 窒化アルミニウムのうちから選ばれた少なくとも 1種以上を主成 分とする単結晶薄膜のミラー指数 ( 0 0 2) の格子面の X線回折ロッキングカーブの半値幅が 2 4 0秒以下のより優れた結晶性を有する単結晶薄膜が形成し易い。 また全酸素量が 3. 0重 量%以下の焼結体で窒化ガリゥム、 窒化ィンジゥム、 窒化アルミニゥムのうちから選ばれた少 なくとも 1種以上を主成分とする単結晶薄膜のミラ一指数 ( 0 0 2 ) の格子面の X線回折ロッ キングカーブの半値幅が 2 0 0秒以下のさらに優れた結晶性を有する単結晶薄膜が形成し易い。 本願発明者は前記 1 7 5 0°C以上の温度で 3時間以上要すれば ¾性雰囲気中で焼成を行い 含まれる酸素、 希土類 素化合物及びアル力リ土類金属化合物など焼結助剤として用いられる 成分、 あるいは舰 氐減化剤として用いられるアルカリ金属や珪素などの成分あるいは黒 色化剤として用いられる M o、 W、 V、 N b、 T a、 T iなどの金属成分やカーボンあるいは M o、 W、 V、 N b、 T a、 T i以外の不可避金属成分などを飛散 · し、 減少させ、 結晶 相としての AL ONや上記アルミニウム以外の金属成分や珪素あるいは力一ボンを含む化合物 の含有量が低減化された A 1 N ¾tの高い窒化アルミニウムを主成分とする焼結体を窒化ガリ ゥム、 窒化インジウム、 窒化アルミニウムのうちから選ばれた少なくとも 1種以上を主成分と する薄膜を直接形成するための基板として使用ときの基板特性についてさらに検討した。 また、 上記窒化アルミニウムを主成分とする焼結体としての特性及び該焼結体に直接窒化ガリゥム、 窒化インジウム、 窒化アルミニウムのうちから選ばれた少なくとも 1種以上を主成分とする薄 膜を形成した薄膜基板の特性を調べた。
上記窒化アルミニウムを主成分とする焼結体において A 1 N鍵は焼成 が高くなるほど 又焼成時間を長くするほど高くなる傾向がある。 焼成温度としては 1 9 0 0 °C以上がより好ま しく、 2 0 5 0 °C以上がさらに好ましく、 2 1 0 0 °C以上が最も好ましい。 窒化アルミニウム を主成分とする焼結体の A 1 N純度を高める上では焼成温度を高めれば焼成時間を短くでき焼 成 ¾Sを低くすれば; «時間が長くなるという関係にあり、 どちらでも効果は殆ど同じである。 A 1 Nの純度を高めるために焼成温度 1 7 5 0 °C〜1 9 0 0 °Cの範囲では焼成時間は通常 1 0 時間以上とすることが好ましい。 焼成温度 1 9 0 0°C以上では焼成時間 6時間以上、 焼成温度 2 0 5 0 °C以上では焼成時間 4時間以上、 焼成温度 2 1 0 0 °C以上では焼成時間 3時間以上と することが好ましい。 このような方法により本発明による A 1 N Jtを高めた窒化アルミニゥ ムを主成分とする焼結体として希土類 素及びアルカリ土類金属のうちから選ばれた少なくと も 1種以上の含有量が元素換算で合計 0. 5重量% ( 5 0 0 O p pm) 以下かつ酸餘有量が 0. 9重量%以下の組成のものを得ることができる。 このような組成の A 1 N純度を高めた窒 化アルミニウムを主成分とする焼結体を基板として用いこの基板に直接形成した窒化ガリウム、 窒化インジウム、 窒化アルミニウムのうちから選ばれた少なくとも 1種以上を主成分とする単 結晶薄膜は結晶性の優れたものが得られる。 本発明においてこの A 1 を高めた窒化アル ミ二ゥムを主成分とする焼結体として希土 11¾素及びアル力リ土類金属のうちから選ばれた少 なくとも 1種以上の含有量が元素騰で合計 0. 2重量% ( 2 0 0 O p pm) 以下かつ酸素含 有蘆が 0. 5重量%以下の組成を有するものを得ることができ好ましい。 また本発明において A 1 N纖を高めた窒化アルミニウムを主成分とする焼結体として希土紙素及びアルカリ土 類金属のうちから選ばれた少なくとも 1種以上の含有量が元素換算で合計 0. 0 5重量% ( 5
0 O p pm) 以下かつ酸 ^^有量が 0. 2重量%以下の組成を有するものを得ることができょ り好ましい。 また、 この A I N i を高めた窒化アルミニウムを主成分とする焼結体として希 土类! ¾素及びアルカリ土類金属のうちから選ばれた少なくとも 1種以上の含有量が元素 で 合計 0. 0 2重量% ( 2 0 O p pm) 以下かつ酸餘有量が 0. 1重量%以下の組成を有する ものを得ることができさらに好ましい。 また、 この A 1 N½gを高めた窒化アルミニウムを主 成分とする焼結体として希土 素及びアル力リ土類金属のうちから選ばれた少なくとも 1種 以上の含有量が元素換算で合計 0. 0 0 5重量% ( 5 0 p pm) 以下かつ酸素量が 0 · 0 5重 量%以下の組成を有するものを得ることができ最も好ましい。 本発明者はこの A 1 N«を高 めた窒化アルミニウムを主成分とする焼結体を基板に用いこの基板に直接窒化ガリゥム、 窒化 インジウム、 窒化アルミニウムのうちから選ばれた少なくとも 1種以上を主成分とする薄膜を 成長させて製造される薄膜の品質を調べた。 なお形成された薄膜は単結晶であり薄膜の品質と してはこの単結晶薄膜の結晶性で龍した。 その結果 A 1 N纖を高めた窒化アルミニウムを 主成分とする焼結体として希土類 素及びアルカリ土類金属のうちから選ばれた少なくとも 1 種以上の含有量が元素換算で合計 0. 5重量%以下かつ酸 有量が 0. 9重量%以下の組成 を有するものを基板として用いたときそこに直接形成される窒化ガリウム、 窒化インジウム、 窒化アルミニウムのうちから選ばれた少なくとも 1種以上を主成分とする単結晶薄膜はミラ一 指数 (0 0 2) の格子面の X線回折ロッキングカーブの半値幅が 2 4 0秒以下と良好な結晶性 を有するものが得られ易い。 また、 A 1 N«を高めた窒化アルミニウムを主成分とする焼結 体として希土^素及びアルカリ土類金属のうちから選ばれた少なくとも 1種以上の含有量が 元素騰で合計 0. 2重量%以下かつ酸素含有量が 0. 5重量%以下の組成を有するものを基 板として用いたときそこに直接形成される上記単結晶薄膜はミラ一指数 ( 0 0 2) の格子面の X線回折ロッキングカーブの半値幅が 2 0 0秒以下とより良好な結晶性を有するものが得られ 易く好ましい。 また、 A 1 N鍵を高めた窒化アルミニウムを主成分とする焼結体として希土 類 素及びアル力リ土類金属のうちから選ばれた少なくとも 1種以上の含有量が元素 で合 計 0. 0 5重量%以下かつ酸素含有量が 0. 2重量%以下の組成を有するものを基板として用 いたときそこに直接形成される上記単結晶薄膜はミラ一指数 ( 0 0 2 ) の格子面の X線回折口 ッキングカーブの半値幅が 1 5 0秒以下とより良好な結晶性を有するものが得られ易くより好 ましい。 また、 A l N ¾itを高めた窒化アルミニウムを主成分とする焼結体として希土類 素 及びアル力リ土類金属のうちから選ばれた少なくとも 1種以上の含有量が元素 で合計 0. 0 2重量%以下かつ酸素含有量が 0. 1重量%以下の組成を有するものを基板として用いたと きそこに直接形成される上記単結晶薄膜はミラ一指数 ( 0 0 2 ) の格子面の X線回折ロッキン グカーブの半値幅が 1 3 0秒以下とより良好な結晶性を有するものが得られ易くさらに好まし レ^ A 1 N ¾Jtを高めた窒化アルミニウムを主成分とする焼結体として希土 ¾素及びアル力 リ土類金属のうちから選ばれた少なくとも 1種以上の含有量が元素換算で合計 0. 0 0 5重 量%以下かつ酸素含有量が 0. 0 5重量%以下の組成を有するものを基板として用いたときそ こに直接形成される上記単結晶薄膜はミラー指数 ( 0 0 2 ) の格子面の X線回折ロッキング力 ーブの半値幅が 1 0 0秒以下とより良好な結晶性を有するものが得られ易く最も好ましい。 上記 A 1 N純度を高めた組成を有する窒化アルミニウムを主成分とする焼結体に含まれる結 晶相は A 1 N力 S 9 5〜 9 8 %以上であり、 A L 0 Nや希土^ ¾素化合物あるいはアル力リ土類 金属化合物などの結晶相は 2〜 5 %以下であり、 実質的に A I N単一相のものも得られる。 ま た、 ¾¾ 性を有するものが得られ易く例えば光醒率 1 %以上のものが得られ易く、 さらに 5 %以上、 1 0 %以上、 2 0 %以上、 3 0 %以上、 4 0 %以上、 6 0 %以上、 8 0 %以上のも のも得られ最大 8 5 %以上の光 ¾1率を有するものも得られる。 なお、 窒化アルミニウムを主 成分とする焼結体中の結晶相は X線回折による得られた各結晶相の示す回折ピークの最強線を
相対比 ¾Tることで容易に計測できる。
また、 上記の方法により酸素あるいは希土類沅素ゃアル力リ土類金属以外にも誠 低減 化剤として用いられるアル力リ金属や珪素などの成分あるいは黒色化剤として用いられる M O、
I V ひナジゥム)、 Nb、 Ta、 T i、 カーボンなどの成分あるいは Mo、 W、 V、 Nb、 T a、 T i の窒ィ匕アルミニゥム粉末原料や焼結体 $¾i工程から混入する F e、 N i、 C 0、 Mn、 Cr、 Z r、 Hf、 Cu、 Z nなどの遷移金属不純物が揮散 · 、 低減化できるので A 1 Ν Φ^の高い窒化アルミニウム焼結体を製造できる。 A 1 N J を高めた窒化アルミニゥ ムを主成分とする焼結体として含まれるアル力リ金属や珪素成分が元素換算で合計 0. 2重 量%以下かつ酸素量が 0. 9重量%以下の組成を有するものを基板に用いたときそこに直接形 成される窒化ガリウム、 窒化インジウム、 窒化アルミニウムのうちから選ばれた少なくとも 1 種以上を主成分とする単結晶薄膜はミラー指数 (002) の格子面の X線回折ロッキング力一 ブの半値幅が 240秒以下と良好な結晶性を有するものが得られ易い。 A 1 N«を高めた窒 化アルミニウムを主成分とする; ¾結体中として Mo、 W、 V (バナジウム)、 Nb、 Ta、 T i、 カーボンが元素換算で合計 0. 2重量%以下かつ酸素量が 0. 9重量%以下の組成を有するも のを基板に用いたときそこに直接形成される窒化ガリウム、 窒化インジウム、 窒化アルミニゥ ムのうちから選ばれた少なくとも 1種以上を主成分とする単結晶薄膜はミラ一指数 (002) の格子面の X線回折ロッキングカーブの半値幅が 240秒以下と良好な結晶性を有するものが 得られ易い。 また、 A 1N«を高めた窒化アルミニウムを主成分とする焼結体として Fe、 Ni、 Co、 Mn、 Cr、 Zr、 Hf、 Cu、 Znが元素換算で合計 0. 2重量%以下かつ酸 素量が 0. 9重量%以下の組成を有するものを基板に用いたときそこに直接形成される窒化ガ リウム、 窒化インジウム、 窒化アルミニウムのうもから選ばれた少なくとも 1種以上を主成分 とする単結晶薄膜はミラー指数 (002) の格子面の X線回折ロッキングカーブの半値幅が 2 40秒以下と良好な結晶性を有するものが得られ易い。
なお上記窒化アルミ二ゥムを主成分とする焼結体中に含まれる希土摩 素化合物とは S c、 Y、 La、 Ce、 Pr、 Nd、 Pm、 Sm、 Eu、 Gd、 Tb、 Dy、 Ho、 Er、 Tm、 Y b、 Luなどの希土類 素、 及び Sc
20
3、 Y
20
3、 La
20
3、 Ce0
2、
い Nd
2 0
3、 Pm
20
3、 Sm
2〇
3、 Eu
2〇
3、 Gd
20
3、 Tb
40
7、 Dy
20
3、 Ho
20
3、 Er
20
3、 Tm
20
3、 Yb
2〇
3、 Lu
2〇
3、 などの希土 素酸化物あるいはその他 S c、 Y、 La、 C e、 Pr、 Nd、 Pm、 Sm、 Eu、 Gd、 Tb、 Dy、 Ho、 Er、 Tm、 Yb、 Lu、 な どを含む炭酸塩、 硝酸塩、 硫酸塩、 塩化物などの無機希土類化合物、 酢酸塩、 塩、 クェン 酸塩などの有機希土類化合物などの各種希土類 素化合物であり、 さらに L nを希土 ¾素と して表したときガーネット型結晶構造の 3 Ln
2〇
3 · 5A1
20
3 (例えば 3Υ
2〇
3 · 5A1
2 〇
3、 3Dy
2〇
3 · 5 A 1
20
3、 3 Ho
20
3 · 5 A 1
20
3、 3 E r
2〇
3 · 5 A 1
2〇
3、 3 Yb
2 〇
3 · 5A 1
20
3、 など)、 ベロブスカイト型結晶構造の Ln
20
3 · A 1
2〇
3 (例えば YA 1 O
3、 LaAl〇
3、 P r A 10
3> NdA10
3、 SmAl〇
3、 EuAl〇
3、 GdA10
3、 Dy A10
3、 HoAl〇
3、 ErA10
3、 YbA10
3、 など)、単斜晶結晶構造 2 Ln
2〇
3 · A 1
2〇
3 (例えば 2Y
2〇
3 · A 1
20
3、 2 Sm
20
3 · A 1
20
3、 2 Eu
20
3 · A 1
2〇
3、 2Gd
2 0
3 ·Α 1
20
3、 2Dy
20
3 · A 1
2〇
3、 2Ho
20
3 · A 1
20
3、 2 E r
20
3 · A 1
20
3、 2 Υ13
20
3 ·Α 1
20
3、 など) などの各種希土類 素を含む複合酸化物、 などである。 また上記 窒化アルミニウム焼結体中に含まれるアルカリ土類金属化合物とは Be、 Mg、 Ca、 S r、 B aなどのアルカリ土類金属、 及び BeO、 MgO、 CaO、 S r 0、 B a Oなどのアルカリ 土類金属酸化物やその他 B e、 Mg、 Ca、 S r、 B aなどを含む炭酸塩、 硝酸塩、 硫酸塩、 塩化物などの無機アルカリ土類金属化合物、 酢酸塩、 謙塩、 クェン酸塩などの有機アルカリ 土類金属化合物などの各種アルカリ土類金属化合物であり、 さらに A eをアルカリ土類金属と
して表したとき 3 A e O · A 1
20
3、 A e · A 1
20
3、 A e · 2 A 1
20
3、 A e · 6 A 1
2〇
3 などのアルカリ土類金属を含む複合酸化物、 などである。
上記 M¾性雰囲気中 1 7 5 0 °C以上の で 3時間以上といった比較的長い時間加熱する方 法により得られる窒化アルミニウムを主成分とする焼結体の特徴は室温における熱伝導率が室 温において 2 0 OW/mK以上と高いものが得られ易い。 又窒化アルミニウムを主成分とする 焼結体において不純物含有量が少ないものや A 1 N単一相からなるものの場合にはさらに室温 における熱伝導率が 2 2 OWZmK以上のものが得られ易い。 このような特徴に加えて上記 A I N J を高めた窒化アルミニウムを主成分とする焼結体は 性の高いものが得られ易い。 これは希土類 素ゃアル力リ土類金属以外にも誠温度低減化剤として用いられるアル力リ金 属ゃ珪素などの成分あるいは黒色化剤として用いられる Mo、 W、 V ひナジゥム)、 Nb、 T a、 T i、 カーボンなどの成分あるいは Mo、 W、 V、 N b、 T a、 T i以外の窒化アルミ二 ゥム粉末原料や焼結体製造工程から混入する F e、 N i、 C o, Mnなどの遷移金属不純物が 揮散 ·除去、 低減化されるためであろうと推測される。 また、 上記遷移金属などの不純物や焼 結助剤が残留している焼結体であっても室温における熱伝導率が 2 0 OW/mK以上さらに 2 2 OWZmK以上の高熱伝導率を有するもの、 あるいは ½¾過性に優れた窒化アルミニウムを 主成分とする焼結体が得られる。 これはおそらく長時間加熱することで焼結体中の窒化アルミ ニゥム粒子が大きく成長し粒界の影響が少なくなるために A 1 N本来の単結晶としての性質が より発現し易くなるためであろうと本願発明者は推測している。
本発明によれば上記高謹化を行う舰過程で窒化アルミニウムを主成分とする焼結体中の 窒化アルミニウム粒子の大きさが通常増大化する。 上記高續化され A 1 N纖を高めた窒化 アルミ二ゥムを主成分とする焼結体中の窒化アルミニゥム粒子の大きさが増大化することが窒 化アルミ二ゥムを主成分とする焼結体からなる基板に直接形成される窒化ガリゥム、 窒化ィン ジゥム、 窒化アルミニウムのうちから選ばれた少なくとも 1種以上を主成分とする単結晶薄膜 の結晶性を増大化させ、 さらに高い光 ¾1率を与える大きな要因であると思われる。
を高めるか航時間を長くすることで窒化アルミニウムを主成分とする焼結体の焼結助剤など A 1 N以外の成分が揮散 ·随減少し焼結体中の窒化アルミニウム粒子内部ゃ窒化アルミニゥ ム; 子の ϋ界に A 1 N以外の成分が少なくなるかあるいは実質的にゼロに近くなるということ に加えて焼結体中の窒化アルミニゥム結晶粒子の大きさが増大化する。 これは窒化アルミニゥ ムを主成分とする焼結体において窒化アルミニウム粒子内部ゃ窒化アルミニウム粒子の粒界に A 1 N以外の成分が少なくなるかあるいは実質的にゼロに近くなるということに加えて焼結体 中の窒化アルミニウム粒子の大きさが増大化すれば窒化アルミニウム粒子境界 (粒界) が減少 するので粒界の影響が少なくなりこの大きく増大した窒化アルミニウム粒子自体も高,舊化さ れさらに結晶性も高まり i の高い単結晶の窒化アルミニウムに近い性質を発現し易くなるた めであろうと推測される。 すなわち純度の高い単結晶に近い状態の大きな結晶粒子からなる焼 結体であるため 性も窒化アルミニウム単結晶の吸収端の波長 2 0 O nm付近から長波長 側で単結晶に匹敵する高い光透過率を有するようになる。 またこの焼結体を基板に使用すれば 窒化ガリウム、 窒化インジウム、 窒化アルミニウムのうちから選ばれた少なくとも 1種以上を 主成分とする単結晶薄膜が窒化アルミニウムの単結晶を基板として用いたのと同程度の高い結 晶性で形成され易くなる。 本発明において焼成温度を高めあるいは焼成時間を長くすることで A 1 N Jtを高めた窒化アルミニウムを主成分とする焼結体が! ¾tされるがこの焼結体の窒化 アルミニウム粒子の大きさは通常平均 5 m以上である。 通常焼成温度を高めていくかあるい は焼成時間を長くすれば焼結体中の窒化アルミニウム粒子の大きさも平均 2 5 以上に増大 する。 また実験上では窒化アルミニウム粒子の大きさ平均 1 0 0 m程度のものが得られてい る。 このように増大化した窒化アルミニウム粒子は A 1 N|¾Sも高まることから単結晶に近い
状態であろうと思われる。 上記方法により高^ JS化され A 1 N Jtを高めた窒化アルミニウム を主成分とする焼結体を基板として用いたとき焼結体中の窒化アルミニウム粒子の大きさが平 均 5 m以上では該基板に直接形成される窒化ガリウム、 窒化インジウム、 窒化アルミニウム のうちから選ばれた少なくとも 1種以上を主成分とする単結晶薄膜のミラー指数 ( 0 0 2) の 格子面の X線回折ロッキングカーブの半値幅が 2 0 0秒以下と良好なものが得られる。 窒化ァ ルミニゥム粒子の大きさが平均 8 /m以上の基板を用いたとき該基板に直接形成される窒化ガ リウム、 窒化インジウム、 窒化アルミニウムのうちから選ばれた少なくとも 1種以上を主成分 とする単結晶薄膜のミラー指数 (0 0 2 ) の格子面の X線回折ロッキングカーブの半値幅が 1 5 0秒以下と良好なものが得られる。 また、 窒化アルミニウム粒子の大きさが平均 1 5 以 上の基板を用いたとき該基板に直接形成される窒化ガリウム、 窒化インジウム、 窒化アルミ二 ゥムのうちから選ばれた少なくとも 1種以上を主成分とする単結晶薄膜のミラー指数 (0 0 2) の格子面の X線回折ロッキングカーブの半値幅が 1 3 0秒以下と良好なものが得られる。 また、 窒化アルミニウム粒子の大きさが平均 2 5 m以上の基板を用いたとき該基板に直接形成され る窒化ガリウム、 窒化インジウム、 窒化アルミニウムのうちから選ばれた少なくとも 1種以上 を主成分とする単結晶薄膜のミラ一指数 ( 0 0 2) の格子面の X線回折ロッキングカーブの半 値幅が 1 0 0秒以下と良好なものが得られる。 このように焼結助剤など A 1 N以外の成分を揮 散 · 鉄、 減少することで難される高繊化された窒化アルミニウムを主成分とする焼結体 の窒化アルミニウム粒子の大きさは重要である。 本発明においては上記のように焼結体中の窒 化アルミニウム粒子の大きさが平均 5 mi以上の窒化アルミニウムを主成分とする焼結体を提 供でき、 該焼結体中の窒化アルミニウム粒子の大きさ平均 1 0 0 m程度のものは比較的容易 に製造できる。
例えば平均粒径 1 urn, 酸素を 1重量%含む高績窒化アルミニウム粉末を原料とし焼結助 剤として Y203を 3. 3体積% (Υとして 3. 9重量%、 酸素として 1 . 1重量%を含む) 混 合した大きさ外形 6 0 X 6 Omm、厚み 0. 8 mmの板状正方形とした粉末成形体を 1 8 0 0°C 1時間焼成して得られる窒化アルミニウムを主成分とする焼結体は室温における熱伝導率 1 5 OW/mK:〜 1 8 OWZmKの範囲であり、 焼結助剤として用いられた Y203中のイットリウ ム成分は殆どそのままの量焼結体中に残り 5〜2 0 %程度の量の Υ203 · 5 A 1 203、 YA 1 03、 2 Y203 · A 1 2〇3、 Y203などの希土^ ΰ素化合物を主体とする粒 が X線回折によ り存在することが認められる。 また原料の酸素及び焼結助剤として用いられた Υ 2 Ο 3中の酸素 も殆どそのままの量焼結体中に残り、 該焼結体の光 ¾1率は 1 0 %程度あるいはそれ以下の場 合もある。 上記焼結体において窒化アルミニウム粒子の大きさは平均 2〜4 iim程度である。 この焼結体をさらに例えば一酸化炭素を 1 p pm〜 1 0 0 0 p pmの範囲で含む窒素雰囲気中 で 2 0 5 O t〜 2 2 0 0 °C 3時間〜 2 4時間焼成すれば用いた原料及び焼結助剤に含まれてい た酸素は 0 · 5量%以下に減少し最も少ないもので 0. 0 1 4重量%のものが得られた。 Y20 3は殆ど揮散 '除去され含有量は 0. 2重量%以下となり最も少ないもので 0. 0 0 0 0 5重量% ( 0. 5 p m) 以下の窒化アルミニウムを主成分とする焼結体が得られた。 波長 2 0 0 nm 〜 8 0 0 nmの範囲の光において光透過率は最低でも 1 0 %以上多くのものが 2 0 %〜 6 0 % 以上であり最大 8 8 %のものが得られた。 焼結体の相構成は A 1 N 9 8 %以上であり実質的に A 1 N単一相のものも容易に得られた。 室温における熱伝導率は 2 0 OWZmK;〜 2 2 0W/ mK以上となり ¾^:2 3 7W/mKのものが得られた。 この焼結体中の窒化アルミニウム粒子 の大きさは最低平均 5〜 8 m以上多くのものは平均 1 5 m〜 2 5 m以上に大きく成長し ており最大で平均 7 4 mのものが得られた。 上記例示した A 1 N ¾Sを高めた窒化アルミ二 ゥムを主成分とする焼結体を基板として用いこの基板に直接形成された窒化ガリウム、 窒化ィ ンジゥム、 窒化アルミニウムのうちから選ばれた少なくとも 1種以上を主成分とする単結晶薄
膜はミラー指数 (0 0 2 ) の格子面の X線回折ロッキングカーブの半値幅が 1 5 0秒以下の良 好な結晶性を示すものが得られ、 最も結晶性のよいもので 1 0 0秒以下のものが得られる。 上 記例示した焼成条件で焼結助剤を揮散 ·除去し減少化する方法により作製し高 S化され A 1 N ¾¾が高められた窒化アルミニウムを主成分とする焼結体を厚み 0 · 5 mmに研削及び鏡面 研磨して光透過率を測定したところ波長 6 0 5 nmにおいて 8 8 %の高いものであった。 その 結果を図 9に示す。 なおこの光 率測定に用いた窒化アルミニウムを主成分とする焼結体の Y (イットリウム) 含有量は 0. 0 0 0 5重量%以下、 酸 ^^有量 0. 0 3 4重量%、 構成相 は実質的に A 1 N単一相であり、 窒化アルミニウム粒子の大きさは平均 2 9 m である。 この窒化アルミニウムを主成分とする焼結体の)1 ά¾1率は図 9から明らかなように波長 2 1 0〜 2 2 0 nmの光に対して 1 %以上の 1 β®Μ率を示し、 波長 2 2 0 n m〜 2 3 0 nmの光に おいて 5 %以上の)16¾1率であり、波長 2 5 O nmの光において 率は 3 0 %以上であり、 波長 3 0 0 nmの光において光透過率は 6 0 %以上であり、 波長 3 3 0 nmの光で 8 0 %以上 の光 ¾ϋ率を示すようになり、 波長 3 3 0 nm以上のすべての波長の光において 8 0 %以上の 率を示す。 又½¾§率の最大値は波長 4 8 0 nm〜6 5 0 nmの範囲の光において 8 5 〜8 8 %と 8 5 %以上の高いものである。 この窒化アルミニウムを主成分とする焼結体を基板 として用いこの基板に直接形成された窒化ガリウム、 窒化インジウム、 窒化アルミニウムのう ちから選ばれた少なくとも 1種以上を主成分とする単結晶薄膜の結晶性はミラー指数 (0 0 2) の格子面の X線回折ロッキングカーブの半値幅が 1 0 0秒以下と良好なものが得られた。 上記の A 1 N純度を高めた窒化アルミニウムを主成分とする焼結体を基板として用いた時の 主な有効性をまとめると、 1 ) 基板に形成される窒化ガリウム、 窒化インジウム、 窒化アルミ ニゥムのうちから選ばれた少なくとも 1種以上を主成分とする単結晶薄膜は高い結晶性のもの が得られやすいのでこの単結晶薄膜を用いて製造される発光^?内部からの発光効率は高いも のとなる、 2) 基板の熱伝導率が室温において 2 0 OWZmK以上と高いものが得られ易くこ のような基板に形成される発光素子には大きな電力の印加が可能となり発光出力を高めること ができる、 3 ) 基板の波長 2 0 0 nm〜8 0 0 nmの範囲の光において光 ¾ϋ率が高いので基 板からの光吸収が少なく発光軒から出た光は大部分素子外部へ放出される、などの点である。 すなわち高効率、 高出力、 かつ低コストの発光素子の ®tが可能となり産業に与える影響は大 である。
本発明において、 光翻性を有する窒化アルミニウムを主成分とする焼結体は通常波長 2 0 0 nm以上の光において光 ¾1性を示す。 図 9に例示したように波長 2 0 0 nm〜2 5 0 nm の範囲の光において舰過性を示し始め、 波長 2 5 0 nm〜3 5 0 nmの範囲の光において急 激に光 Mi 性が上昇し波長 3 5 0 nm〜4 0 0 nm以上の光においてはほぼ一定の光透過率を 有する傾向があることが確認された。 本発明において窒化アルミニウムを主成分とする焼結体 の^ 1率は特に断らない限り波長 6 0 5 nmの光において測定された光透過率を意味してい るが、 波長 6 0 5 nmの光における光透過率を用いても本発明による窒化アルミニウムを主成 分とする焼結体の性能すなわち窒化ガリウム、 窒化インジウム、 窒化アルミニウムのうちから 選ばれた少なくとも 1種以上を主成分とする単結晶薄膜を直接形成したときの結晶性を代表し て判別できる。 より具体的にいえば本発明において特に断らない限り 1 %以上の光醒率とは 波長 6 0 5 nmの光に対する光 ¾i率である。 このような 1 %以上の ¾¾1率を有する窒化ァ ルミ二ゥムを主成分とする焼結体は波長 2 0 0 nm〜8 0 0 nmの範囲の光において波長 6 0 5 nm以外でも 1 %以上の 過率を有するとは限らないがこの窒化アルミニウムを主成分と する焼結体を基板として用いることでより優れた結晶性を有する窒化ガリゥム、 窒化ィンジゥ ム、 窒化アルミニウムのうちから選ばれた少なくとも 1種以上を主成分とする単結晶薄膜が形 成できる。 本発明において、 窒化ガリウム、 窒化インジウム、 窒化アルミニウムのうちから選
ばれた少なくとも 1種以上を主成分とする単結晶薄膜を形成するための基板として用いる窒化 アルミニウムを主成分とする焼結体は波長 2 0 0 nm〜8 0 0 nmの範囲の光においてどの波 長の光に対しても 1 %以上の光透過率を有するもの力壁ましいが、 仮にすベての波長に対して 1 %以上の光 ¾ 率を有さないとしても少なくとも波長 6 0 5 nmの光に対して 1 %以上の光 率を有するもの力壁ましい。 また本発明において、 1 %以上の ½¾i率を有する窒化アル ミニゥムを主成分とする焼結体を基板として用いることで窒化ガリウム、 窒化インジウム、 窒 化アルミニウムのうちから選ばれた少なくとも 1種以上を主成分とする単結晶以外の無定形、 多結晶、 配向性多結晶など各種結晶状態の薄膜も形成できる。
本発明において A 1 N ¾J¾が高くかつ窒化アルミニウム粒子が成長した窒化アルミニウムを 主成分とする焼結体は単結晶薄膜を形成するための基板として好ましいが、 必ずしも A 1 Nの 譲が高くなくても、 すなわち希土麵素化合物やアルカリ土類金属化合物などの焼結助剤、 あるいは酸素、 あるいは焼成驢低減化剤として用いられるアルカリ金属や珪素などの成分、 あるいは黒色化剤として用いられる M o、 W、 V、 N b、 T a、 T iなどの金属成分やカーボ ン、 あるいは M o、 W、 V、 N b、 T a、 T i以外の不可避金属成分、 あるいは ALONや上 記アルミニウム以外の金属成分や珪素あるいはカーボンを含む化合物、 などの成分が比較的多 く残存している窒化アルミニウムを主成分とする焼結体であっても窒化アルミニウム粒子が成 長したものであれば結晶性の高い窒化ガリウム、 窒化インジウム、 窒化アルミニウムのうちか ら選ばれた少なくとも 1種以上を主成分とする単結晶薄膜が形成し得る基板となり得る。 この ような窒化アルミニゥム以外の成分を比較的多く含み窒化アルミニゥム粒子が成長した窒化ァ ルミ二ゥムを主成分とした焼結体は前述のようにできるだけ ¾¾性成分を含まない非酸化性雰 囲気中で 1 7 5 0 °C以上で 3時間以上の比較的高温、 力つ長時間 «することにより作製でき る。なわち、上記のような希土 素、 アルカリ土類金属、酸素、 アルカリ金属、珪素、 Mo、 W、 V、 N b、 T a、 T iなどの金属成分、 力一ボン、 Mo、 W、 V、 N b、 T a、 T i以外 の不可避金属成分、 AL ON、 上記アルミニウム以外の金属成分、 などの成分を比較的多く含 む窒化アルミニウムを主成分とする焼結体内部に含まれる窒化アルミニウム粒子の大きさが平 均 1 m以上であれば該焼結体からなる基板上に直接形成される単結晶薄膜のミラ一指数 (0 0 2 ) の格子面の X線回折ロッキングカーブの半値幅が 3 0 0秒以下のものが形成され易い。 窒ィ匕ァリレミニゥム^子の大きさが、平均 5 m以上に成長した焼結体では該基板上に直接形成さ れる窒化ガリウム、 窒化インジウム、 窒化アルミニウムのうちから選ばれた少なくとも 1種以 上を主成分とする単結晶薄膜のミラ一指数 (0 0 2 ) の格子面の X線回折ロッキングカーブの 半値幅が 2 4 0秒以下と良好な結晶性のものが得られ易い。 窒化アルミニウム粒子の大きさが 平均 8 m以上に成長した焼結体では該基板上に直接形成される窒化ガリゥム、 窒化ィンジゥ ム、 窒化アルミニウムのうちから選ばれた少なくとも 1種以上を主成分とする単結晶薄膜のミ ラー指数 ( 0 0 2) の格子面の X線回折ロッキングカーブの半値幅が 2 0 0秒以下とより良好 な結晶性のものが得られ易い。 窒化アルミニウム粒子の大きさが平均 1 5 /im以上に成長した 焼結体では該基板上に直接形成される窒化ガリウム、 窒化インジウム、 窒化アルミニウムのう ちから選ばれた少なくとも 1種以上を主成分とする単結晶薄膜のミラー指数 ( 0 0 2) の格子 面の X線回折ロッキングカーブの半値幅が 1 5 0秒以下とさらに良好な結晶性のものが得られ 易い。 窒化アルミニウム粒子の大きさが平均 2 5 xm以上に成長した焼結体では該基板上に直 接形成される窒化ガリウム、 窒化インジウム、 窒化アルミニウムのうちから選ばれた少なくと も 1種以上を主成分とする単結晶薄膜のミラー指数 ( 0 0 2) の格子面の X線回折ロッキング カーブの半値幅が 1 3 0秒以下とさらに良好な結晶性のものが得られ易い。 これは焼結体内部 の窒化アルミニゥム粒子の大きさが大きくなれば窒化アルミニゥム結晶粒子の粒界の面積が減 少し粒界の影響が減じるので窒化アルミニウム結晶粒子自体の性質が反映され易くなり窒化ガ
リウム、 窒化インジウム、 窒化アルミニウムのうちから選ばれた少なくとも 1種以上を主成分 とする単結晶薄膜の核成長の方向をより規則的なものにし易いためであろうと推測される。 本 発明において上記のようにできるだけ還元性成分を含まない非酸化性雰囲気中焼成温度を高め あるいは舰時間を長くすることで希土類 素、 アルカリ土類金属、 酸素、 アルカリ金属、 珪 素、 Mo、 W、 V、 N b、 T a、 T iなどの金属成分、 カーボン、 Mo、 W、 V、 Nb、 T a、 T i以外の不可避金属成分、 AL ON、 上記アルミニウム以外の金属成分、 などの成分を比較 的多く含む窒化アルミニウムを主成分とする焼結体においても窒化アルミニウム粒子が成長し たものが難されるが、 この焼結体の成長した窒化アルミニウム粒子の大きさ〖雄常平均 5 m以上である。 通常 を高めていくかあるいは «時間を長くすれば焼結体中の窒化ァ ルミニゥム粒子の大きさも平均 8 m以上、 さらに平均 1 5 2 m以上、 さらに平均 2 5 m以 上に増大し、実験上では窒化アルミニウム粒子の大きさ平均 1 0 0 /m程度のものも得られる。 本発明において上記のようにできるだけ還元性成分を含まない非酸化性雰囲気中焼成温度を 高めあるいは焼成時間を長くすることで窒化アルミニウム粒子が成長し、 希土類 素、 アル力 リ土類金属、 酸素、 アルカリ金属、 珪素、 Mo、 W、 V、 N b、 T a、 T iなどの金属成分、 カーボン、 Mo、 W、 V、 N b、 T a、 T i以外の不可避金属成分、 AL〇N、 上記アルミ二 ゥム以外の金属成分、 などの成分を比較的多く含む窒化アルミニゥムを主成分とする焼結体と しては窒化アルミニウムを主成分とする (例えば A 1 Nとして 5 0 %#¾以上含む) ものであ ればどのような組成のものでも使用できるが、 その中で希土 ¾素あるいはアル力リ土類金属 のうちから選ばれた少なくとも 1種以上の含有量カ戰化物換算で 2 5髓%以下、 酸餘有量 1 0重量%以下、 アル力リ金属あるいは珪素のうちから選ばれた少なくとも 1種以上の成分の 含有量が ¾化物 で1 (ΗΦ«%以下、 Mo、 W、 V、 N b、 T a、 T i、 力一ボンのうちか ら選ばれた少なくとも 1種以上を含む成分の含有量が元素換算で 2 5繊%以下、 鉄、 ニッケ ル、 クロム、 マンガン、 ジルコニウム、 ハフニウム、 コバルト、 銅、 亜鉛など希土 素及び M o、 W、 V、 N b、 T a、 T i以外の遷移金属を含む成分の含有量が元素購で合計 3 0重 量%以下、 AL ON含有量 2 0 %以下、 の組成のものを用いることが好ましい。 上記のような 組成であれば必ずしも A 1 Nの! 6¾が高くない窒化アルミニウムを主成分とする焼結体であつ ても窒化アルミニウムの粒子が成長したものは優れた窒化ガリウム、 窒化インジウム、 窒化ァ ルミニゥムのうちから選ばれた少なくとも 1種以上を主成分とする単結晶薄膜形成用の基板と して使用し得る。 このような組成を有し窒化アルミニウムの粒子が成長した基板には上記窒化 ガリウム、 窒化インジウム、 窒化アルミニウムのうちから選ばれた少なくとも 1種以上を主成 分とする単結晶状態の薄膜が直接形成でき、 さらに単結晶以外の無定形、 多結晶、 配向性多結 晶など各種結晶状態の薄膜も形成できる。 また、 上記のような組成であれば必ずしも A 1 Nの 繊が高くない窒化アルミニウムを主成分とする焼結体であっても窒化アルミニウムの粒子が 成長したものを基板として用い該基板に窒化ガリウム、 窒化インジウム、 窒化アルミニウムの うちから選ばれた少なくとも 1種以上を主成分とする単結晶薄膜が形成された優れた薄膜基板 が し得る。 このような単結晶薄膜が形成された薄膜基板にはさらに窒化ガリウム、 窒化ィ ンジゥム、 窒化アルミニウムのうちから選ばれた少なくとも 1種以上を主成分とする単結晶状 態の薄膜が形成でき、 さらに単結晶以外の無定形、 多結晶、 配向性多結晶など各種結晶状態の 薄膜も形成できる。
上記のように誠 を高めあるいは誠時間を長くすることで窒化アルミニゥム粒子が成 長し、 希土^ ¾素、 アルカリ土類金属、 酸素、 アルカリ金属、 珪素、 Mo、 W、 V、 N b、 T a、 T iなどの金属成分、 カーボン、 M o、 W、 V、 N b、 T a、 T i の不可避金属成分、 AL ON, 上記アルミニウム以外の金属成分、 などの成分を比較的多く含む窒化アルミニウム を主成分とする焼結体はできるだけ水素や一酸化炭素、 炭素、 炭化水素などの^ ί性成分を含
まない焼成雰囲気で焼成することにより得られ易い。
本発明において上記のように薄膜形成用基板として用いられる窒化アルミニウムを主成分と する焼結体は希土類 J£素あるいはアルカリ土類金属のうちから選ばれた少なくとも 1種以上の 含有量が 化物換算で 2 5髓%以下、 酸餘有量 1 0重量%以下、 アルカリ金属あるいは珪 素のうちから選ばれた少なくとも 1種以上の成分の含有量が 化物換算で 1 0 %以下、 M o、 W、 V、 N b、 T a、 T i、 力一ボンのうちから選ばれた少なくとも 1種以上を含む成分 の含有量が元素^:で 2 5 以下、 希土 M¾素及び 1VI o、 W、 V、 N b、 T a、 T i以外 の遷移金属を含む成分の含有量が元素^^で 3 0重量%以下、 AL ON含有量 2 0 %以下、 の 組成のものを用いることが好ましい。 このような組成の窒化アルミニウムを主成分とする焼結 体を薄膜形成用基板として用いることで窒化ガリウム、 窒化インジウム、 窒化アルミニウムの うちから選ばれた少なくとも 1種以上を主成分とする単結晶薄膜のミラ一指数 (0 0 2) の格 子面の X線回折ロッキングカーブの半値幅が 3 0 0秒以下の結晶性のものが得られ易い。 本発明においては窒化アルミニウムを主成分とする焼結体の窒化アルミニウム成分の含有量 は 5 0體%以上であることが好ましいが、 該焼結体の希土 素あるいはアルカリ土類金属 のうちから選ばれた少なくとも 1種以上の含有量が ¾化物換算で 5 0#¾%以下、 酸餘有量 2 5重量%以下、 アル力リ金属あるいは珪素のうちから選ばれた少なくとも 1種以上の成分の 含有量が 化物 で 2 0#¾%以下、 Mo、 W、 V、 N b、 T a、 T i、 カーボンのうちか ら選ばれた少なくとも 1種以上を含む成分の含有量が元素換算で 5 0浦%以下、 鉄、 ニッケ ル、 クロム、 マンガン、 ジルコニウム、 ハフニウム、 コバルト、 銅、 亜鉛など希土類 素及び Mo、 W、 V、 N b、 T a、 T i以外の遷移金属を含む成分の含有量が元素麟で 5 0重量% 以下、 AL ON含有量 5 0 %以下、 の窒化アルミニウム以外の成分を比較的多く含むものを薄 膜形成用基板として用いた齢でも、 該基板に形成される窒化ガリウム、 窒化インジウム、 窒 化アルミニウムのうちから選ばれた少なくとも 1種以上を主成分とする単結晶薄膜としてミラ —指数 (0 0 2) の格子面の X線回折ロッキングカーブの半値幅が少なくとも 3 6 0 0秒以下 の結晶性のものが得られ易く、 該半値幅が 3 0 0秒以下の結晶性のものも得られる。
さらに上記窒化アルミニゥム以外の成分を比較的多く含む窒化アルミ二ゥムを主成分とする 焼結体において、 該焼結体中に含有される希土 素のうちから選ばれた少なくとも 1種以上 とアルカリ土類金属のうちから選ばれた少なくとも 1種の成分を同時に酸化物換算で 5 0体 積%以下含むもの、 該焼結体の酸素含有量が 2 5重量%以下で同時に希土! ^素あるいはアル カリ土類金属のうちから選ばれた少なくとも 1種以上の成分を含むもの、 該; ¾結体のアルカリ 金属あるいは珪素のうちから選ばれた少なくとも 1種以上の成分の含有量カ戰化物 で 2 0 ί機%以下で同時に希土 素あるいはアルカリ土類金属のうちから選ばれた少なくとも 1種 以上の成分を含むもの、 該焼結体の M o、 W、 V、 N b、 T a、 T i、 力一ボンのうちから選 ばれた少なくとも 1種以上を含む成分の含有量が元素換算で 5 0体積%以下で同時に希土類 素あるいはアルカリ土類金属のうちから選ばれた少なくとも 1種以上の成分を含むもの、 該焼 結体の鉄、 ニッケル、 クロム、 マンガン、 ジルコニウム、 ハフニウム、 コノルト、 銅、 亜鉛な ど希土類 素及ぴ^ f o、 W、 V、 N b、 T a、 T i以外の遷移金属を含む成分の含有量が元素 換算で 5 0重量%以下で同時に希土 素あるいはアルカリ土類金属のうちから選ばれた少な くとも 1種以上の成分を含むもの、 該焼結体の AL ON含有量が 5 0 %以下で同時に希土航 素あるいはアルカリ土類金属のうちから選ばれた少なくとも 1種以上の成分を含むもの、 を薄 膜形成用基板として用いたとき、 該基板に形成される窒化ガリウム、 窒化インジウム、 窒化ァ ルミニゥムのうちから選ばれた少なくとも 1種以上を主成分とする単結晶薄膜のミラ一指数 ( 0 0 2 ) の格子面の X線回折ロッキングカーブの半値幅が少なくとも 3 0 0秒以下の結晶性 のものがより一層得られ易くなる。 すなわち、 希土!^素とアルカリ土類金属成分を同時に含
む、 あるいは酸素、 アルカリ金属、 珪素、 M o、 W、 V、 N b、 T a、 T i、 力一ボン、 鉄、 ニッケル、 クロム、 マンガン、 ジルコニウム、 ハフニウム、 コノルト、 銅、 亜鉛、 AL ONな どの成分と同時に希土^ δ素あるいはアルカリ土類金属のうちから選ばれた少なくとも 1種以 上の成分を含む窒化アルミニウムを主成分とする焼結体を薄膜形成用基板として用いたとき、 希土類元素、 アルカリ土類金属、 酸素、 アルカリ金属、 珪素、 Mo、 W、 V、 N b、 T a、 T i、 力一ポン、鉄、 ニッケル、 クロム、 マンガン、 ジルコニウム、 ハフニウム、 コバルト、 銅、 亜鉛、 A L〇 Nなどの成分をそれぞれ単独に含む窒化アルミ二ゥムを主成分とする焼結体を薄 膜形成用基板として用いた場合に比べて該基¾±に形成される窒化ガリウム、窒化インジウム、 窒化アルミニウムのうちから選ばれた少なくとも 1種以上を主成分とする単結晶薄膜の結晶性 力 S向上し易い。
なお上記のように希土類 素とアルカリ土類金属成分を同時に含む、 あるいは酸素、 アル力 リ金属、 珪素、 M o、 W、 V、 N b、 T a、 T i、 カーボン、 鉄、 ニッケル、 クロム、 マンガ ン、 ジルコニウム、 ハフニウム、 コバルト、 銅、 亜鉛、 A L ONなどの成分と同時に希土類 J£ 素あるいはアルカリ土類金属のうちから選ばれた少なくとも 1種以上の成分を含む窒化アルミ 二ゥムを主成分とする焼結体においても窒化アルミニウム成分の含有量は 5 0#¾%であるこ とが好ましい。 窒化アルミニウム成分の含有量が 5 0髓%より少なければ窒化ガリウム、 窒 化ィンジゥム、 窒化アルミニウムのうちから選ばれた少なくとも 1種以上を主成分とする単結 晶薄膜の形成が困難になり易いので好ましくない。 すなわち、 窒化アルミニウムを主成分とす る焼結体が希土 素とアルカリ土類金属のうちから選ばれた少なくとも 1種以上の成分を同 時に合計 5 0体積%以下含むもの、 該焼結体のアルカリ金属あるいは珪素のうちから選ばれた 少なくとも 1種以上の成分の含有量カ戰化物換算で 2 0髓%以下で同時に希土類 素あるい はアルカリ土類金属のうちから選ばれた少なくとも 1種以上の成分を合計 5 0髓%以下含む もの、 該焼結体の Mo、 W、 V、 N b、 T a、 T i、 力一ボンのうちから選ばれた少なくとも 1種以上を含む成分の含有量が元素換算で 5 0髓%以下で同時に希土類沅素あるいはアル力 リ土類金属のうちから選ばれた少なくとも 1種以上の成分を合計 5 0髓%以下含むもの、 該 焼結体の鉄、 ニッケル、 クロム、 マンガン、 ジルコニウム、 ハフニウム、 コノルト、 銅、 亜鉛 など希土!^素及ぴ o、 W、 V、 N b、 T a、 T i以外の遷移金属を含む成分の含有量が元 素騰で 5 0重量%以下で同時に希土^ ¾素あるいはアル力リ土類金属のうちから選ばれた少 なくとも 1種以上の成分を合計 5 0髓%含むもの、 該焼結体の AL ON含有量が 5 0 %以下 で同時に希土誕素あるいはアルカリ土類金属のうちから選ばれた少なくとも 1種以上の成分 を合計 5 (H機%以下含むもの、 該焼結体の酸餘有量が 2 5重量%以下で同時に希土類 素 あるいはアルカリ土類金属のうちから選ばれた少なくとも 1種以上の成分を合計 5 0髓%以 下含むもの、 といった組成を有する窒化アルミニウムを主成分とする焼結体を用いることが好 ましい。
このように希土紙素とアルカリ土類金属成分を同時に含む、あるいは酸素、アルカリ金属、 珪素、 M o、 W、 V、 N b、 T a、 T i、 カーボン、 鉄、 ニッケル、 クロム、 マンガン、 ジル コニゥム、 ハフニウム、 コノルト、 銅、 亜鉛、 AL ONなどの成分と同時に希土 ϋ¾素あるい はアルカリ土類金属のうちから選ばれた少なくとも 1種以上の成分を含む窒化アルミニウムを 主成分とする焼結体を単結晶薄膜を形成するための基板として用いたとき、 希土類 素、 アル カリ土類金属、酸素、 アルカリ金属、 珪素、 M o、 W、 V、 Nb、 T a、 T i、 力一ボン、 鉄、 ニッケル、 クロム、 マンガン、 ジルコニウム、 ハフニウム、 コゾルト、 銅、 、 AL ONな どの成分をそれぞ姆独に含む窒化アルミニウムを主成分とする焼結体を単結晶薄膜を形成す るための基板として用いた場合に比べて該基板上に形成される窒化ガリゥム、窒化ィンジゥム、 窒化アルミニウムのうちから選ばれた少なくとも 1種以上を主成分とする単結晶薄膜の結晶性
は向上し易いが、 その理由については必ずしも明確ではない。 本願発明者は、 希土類元素とァ ルカリ土類金属を同時に含む場合あるいは酸素、 アルカリ金 、 珪素、 Mo、 W、 V、 N b、 T a、 T i、 カーボン、 鉄、 ニッケル、 クロム、 マンガン、 ジルコニウム、 ハフニウム、 コパ ルト、 銅、 亜鉛、 AL ONなどの成分と同時に希土 素あるいはアルカリ土類金属のうちか ら選ばれた少なくとも 1種以上を含む場合は各成分をそれぞ^ 虫で含む場合に比べて 5 0 °C 〜3 0 0 °C程度低い « J で緻密化が可能となることから液相が比較的多量に生成し易く、 そのため上記窒化アルミニウムを主成分とする焼結体を構成する窒化アルミニウム粒子の結晶 子が鎌相中で自発的に発達して結晶性が向上し、 その結果上記単結晶薄膜が窒化アルミニゥ ムを主成分とする焼結体上に形成される過程で該単結晶薄膜の結晶整列が促進されるのではな いかと推測している。
上記希土 素とアルカリ土類金属を同時に含む、 あるいは酸素、 アルカリ金属、 珪素、 M o、 W、 V、 N b、 T a、 T i、 カーボン、 鉄、 ニッケル、 クロム、 マンガン、 ジルコニウム、 ハフニウム、 コバルト、 銅、 亜鉛、 ALONなどの成分と同時に希土觀素あるいはアルカリ 土類金属のうちから選ばれた少なくとも 1種以上を含む窒化アルミニウムを主成分とする焼結 体を単結晶薄膜を形成するための基板として用いたとき、 希土^ ¾素、 アルカリ土類金属、 酸 素、 アルカリ金属、 珪素、 Mo、 W、 V、 N b、 T a、 T i、 カーボン、 鉄、 ニッケル、 クロ ム、 マンガン、 ジルコニウム、 ハフニウム、 コバルト、 銅、 赚、 AL ONなどの成分をそれ ぞ湖虫に含む窒化アルミニウムを主成分とする焼結体を単結晶薄膜を形成するための基板と して用いた場合に比べて該基板上に形成される窒化ガリウム、 窒化インジウム、 窒化アルミ二 ゥムのうちから選ばれた少なくとも 1種以上を主成分とする単結晶薄膜の結晶性が向上し易い のは、 上記各成分を比較的多量に含む場合だけに限らない。
本発明においては、 窒化アルミニウムを主成分とする焼結体中に含有される希土類 素のう ちから選ばれた少なくとも 1種以上とアルカリ土類金属のうちから選ばれた少なくとも 1種以 上とを同時に酸化物騰で 2 5碰%以下含むもの、 該焼結体の酸餘有量が 1 0重量%以下 で同時に希土類 素あるいはアルカリ土類金属のうちから選ばれた少なくとも 1種以上を含む もの、 該焼結体のアル力リ金属あるいは珪素のうちから選ばれた少なくとも 1種以上の成分の 含有量が ¾化物換算で 1 0体積%以下で同時に希土類元素あるいはアル力リ土類金属のうちか ら選ばれた少なくとも 1種以上を含むもの、 該焼結体の Mo、 W、 V、 N b、 T a、 T i、 力 —ボンのうちから選ばれた少なくとも 1種以上を含む成分の含有量が元素^^で 2 5 ί«%以 下で同時に希土類 素あるいはアルカリ土類金属のうちから選ばれた少なくとも 1種以上を含 むもの、該赚体の鉄、 ニッケル、 クロム、 マンガン、 ジルコニウム、ハフニウム、 コバルト、 銅、 菌など希土 IS¾素及び^ M o、 W、 V、 N b、 T a、 T i以外の遷移金属を含む成分の含 有量が元素換算で 3 0重量%以下で同時に希土 ¾素あるいはアル力リ土類金属のうちから選 ばれた少なくとも 1種以上を含むもの、 該焼結体の AL ON含有量が 2 0 %以下で同時に希土 類 素あるいはアルカリ土類金属のうちから選ばれた少なくとも 1種以上を含むもの、 を単結 晶薄膜を形成するための基板として用いたとき該基板に形成される窒化ガリゥム、 窒化ィンジ ゥム、 窒化アルミニウムのうちから選ばれた少なくとも 1種以上を主成分とする単結晶薄膜の 結晶性は向上し易く該単結晶薄膜のミラー指数 ( 0 0 2 ) の格子面の X線回折ロッキング力一 ブの半値幅として少なくとも 2 4 0秒以下のものが得られ易い。
また、 本発明においては、 窒化アルミニウムを主成分とする焼結体中に含有される希土観 素のうちから選ばれた少なくとも 1種以上とアルカリ土類金属のうちから選ばれた少なくとも 1種以上とを同時に酸化物換算で 2 5体積%以上含むもの、 該焼結体の酸素含有量が 1 0重 量%以上で同時に希土類 素あるいはアルカリ土類金属のうちから選ばれた少なくとも 1種以 上を含むもの、 該焼結体のアルカリ金属あるいは珪素のうちから選ばれた少なくとも 1種以上
の成分の含有量が 化物騰で 1 o #¾%以上で同時に希土 素あるいはアル力リ土類金属 のうちから選ばれた少なくとも 1種以上を含むもの、 該焼結体の Mo、 W、 V、 N b、 T a、 T i、 カーボンのうちから選ばれた少なくとも 1種以上を含む成分の含有量が元素 で 2 5 #¾%以上で同時に希土類 素あるいはアルカリ土類金属のうちから選ばれた少なくとも 1種 以上を含むもの、 該焼結体の鉄、 ニッケル、 クロム、 マンガン、 ジルコニウム、 ハフニウム、 コバルト、 銅、 亜鉛など希土類 素及び o、 W、 V、 N b、 T a、 T i以外の遷移金属を含 む成分の含有量が元素換算で 3 0重量%以上で同時に希土類元素あるいはアル力リ土類金属の うちから選ばれた少なくとも 1種以上を含むもの、 該能結体の AL ON含有量が 2 0 %以上で 同時に希土類 素あるいはアルカリ土類金属のうちから選ばれた少なくとも 1種以上を含むも の、 を単結晶薄膜を形成するための基板として用いたとき該基板に形成される窒化ガリウム、 窒化インジウム、 窒化アルミニウムのうちから選ばれた少なくとも 1種以上を主成分とする単 結晶薄膜の結晶性は向上し易く該単結晶薄膜のミラー指数 ( 0 0 2) の格子面の X線回折ロッ キングカーブの半値幅として少なくとも 3 0 0秒以下のものが得られ易い。
本発明において窒化ガリゥム、 窒化ィンジゥム、 窒化アルミ二ゥムのうちから選ばれた少な くとも 1種以上を主成分とする単結晶薄膜を形成するための基板を製造するとき上記の高純度 化された窒化アルミニウムを主成分とする焼結体の光翻性を高めるためには舰に供する粉 末成形体や焼結体の形状は例えば立方体や直方体あるいは円柱状などどのようなものでも用い ることができるが基板状に加工し易いあらかじめ板状のものを用いることが好ましい。 同じ体 積であれば立方体や直方体あるいは円柱状などのプロック状よりも表面積の大きなものを用い ることが好ましい。 また上記焼成に供する粉末成形体や能結体の形状でその 1辺大きさが 8m m以下のものを用いることが |f ^化された窒化アルミニウムを主成分とする焼結体の) 性を高める上で好ましい。 さらに上記の 1辺の大きさが 5 mm以下のものを用いることがより 好ましく、 1辺の大きさが 2. 5 mm以下のものを用いることがさらに好ましく、 1辺の大き さが 1 mm以下のものを用いることが最も好ましい。 上記焼成に供する粉末成形体や焼結体の 形状が板状のときその厚みは 8mm以下のものを用いることが高繊化された窒化アルミニゥ ムを主成分とする焼結体の光 ¾ 生を高める上で好ましい。 さらに上記板状の粉末成形体や焼 結体の厚みは 5 mm以下のものを用いることがより好ましく、 厚み 2. 5mm以下のものを用 いることがさらに好ましく、 厚み l mm以下のものを用いることが最も好ましい。 上記に示し たことを具体的に述べれば例えば、 組成が実質的に同じで実質的に A 1 N単一相の焼結体であ つても上記立方体や直方体あるいは円柱状などのプロック状のものあるいは 1辺が 8 mmを越 える粉末成形体や焼結体を用いて製造した高繊化された窒化アルミニウムを主成分とする焼 結体では板状あるいは 1辺が 8 mm以下の成形体や焼結体を用いて製造したものに比べて光透 過率が低減化し、 場合によっては黒色化が高まって光透過率がさらに低下する場合がある。 窒化ガリウム、 窒化インジウム、 窒化アルミニウムのうちから選ばれた少なくとも 1種以上 を主成分とする単結晶薄膜を形成するために本発明による窒化アルミニウムを主成分とする焼 結体からなる基板 (すなわち薄膜形成用基 表面あるいは該単結晶薄膜が形成された薄膜基 板表面の平滑度は平均表面粗さ R aが 2 0 0 0 nm以下であることが好ましい。 このような基 板の表面平滑性を有することが上記単結晶薄膜を形成するためには望ましい。 したがって本発 明においては上記薄膜形成用基板及び薄膜基板の少なくとも 1つ以上の面が上記のような平滑 度を有することが望ましい。 本発明においては R a 2 0 0 0 nm以下の平均表面粗さを有する 基板は窒化アルミニウムを主成分とする焼結体の焼き放し (a s— ί i r e ) 表面やラッフ Iff 削された表面、 あるいはサンドブラストなどにより研磨された表面、 あるいは鏡面研磨された 表面、 あるいは化学的にエッチング (腐食) された表面、 あるいは機械的に翻り加工などが 施された表面などにおいて得ることができる。 化学的なエッチングは例えば薬液などを用いた
ゥエツト; ^やフッ素などの成分を含有するプラズマガスなどによるドライ方式などが好適に 使用し得る。 R a 2 0 0 O nm以下の平均表面粗さを有する基板には直接窒化ガリウム、 窒化 インジウム、 窒化アルミニウムのうちから選ばれた少なくとも 1種以上を主成分とする単結晶 化した薄膜が形成でき該単結晶薄膜のミラ一指数 (0 0 2 ) の格子面の X線回折ロッキング力 ーブの半値幅として 3 6 0 0秒以下のものが得られ易い。 より好ましくい基板の平均表面粗さ R aは 1 0 0 0 nm以下である。 R a 1 0 0 0 nm以下の平均表面粗さを有する基板は窒化ァ ルミ二ゥムを主成分とする能結体の焼き放し(a s— f i r e )表面やラップ研削された表面、 あるいはブラスト研磨された表面、 あるいは鏡蘭磨された表面、 あるいは化学的にエツチン グ (腐食) された表面、 あるいは機械的に溝切り加工などが施された表面などにおいて得るこ とができる。 R a 1 0 0 0 nm以下の平均表面粗さを有する基板には直接窒化ガリウム、 窒化 インジウム、 窒化アルミニウムのうちから選ばれた少なくとも 1種以上を主成分とする単結晶 化した薄膜が形成でき該単結晶薄膜のミラー指数 (0 0 2) の格子面の X線回折ロッキング力 —ブの半値幅として 1 0 0 0秒以下のものが得られ易い。 また基板の平均表面粗さ R aは 1 0 0 nm以下であることがさらに好ましい。 R a 1 0 0 nm以下の平均表面粗さ R aを有する基 扳は窒化アルミニウムを主成分とする焼結体の焼き放し (a s— f i r e ) 表面ゃ鏡丽磨さ れた表面などにおいて得ることができる。 R a 1 0 0 nm以下の平均表面粗さを有する基板に は直接窒化ガリウム、 窒化インジウム、 窒化アルミニウムのうちから選ばれた少なくとも 1種 以上を主成分とする単結晶化した薄膜が形成でき該単結晶薄膜のミラー指数 ( 0 0 2) の格子 面の X線回折ロッキングカーブの半値幅として 3 0 0秒以下のものが得られ易い。 1 0 0 nm 以下の平均表面粗さ R aを有する基板において通常は R a 6 0 nm以下より好ましくは R a 3 0 nm以下さらに好ましくは R a 2 0 nm以下の鏡面状態としたものが好ましい。 鏡面状態と することで形成される単結晶薄膜の結晶性が向上し易くなる。 窒化アルミ二ゥムを主成分とす る焼結体からなる基板において平均表面粗さ R a 6 0 nm以下のものには窒化ガリウム、 窒化 インジウム、 窒化アルミニウムのうちから選ばれた少なくとも 1種以上を主成分とする単結晶 化した薄膜が形成でき該単結晶薄膜のミラ一指数 ( 0 0 2) の格子面の X線回折ロッキング力 ーブの半値幅として 2 4 0秒以下のものが得られ易い。 窒化アルミニウムを主成分とする焼結 体を用いた基板の中で平均表面粗さ R a 3 0 nm以下のものには窒化ガリゥム、 窒化ィンジゥ ム、 窒化アルミニウムのうちから選ばれた少なくとも 1種以上を主成分とする単結晶ィ匕した薄 膜が形成でき該単結晶薄膜のミラー指数 (0 0 2 ) の格子面の X線回折ロッキングカーブの半 値幅として 2 0 0秒以下のものが得られ易い。 また窒化アルミニウムを主成分とする焼結体を 用いた基板の中で平均表面粗さ R a 2 O nm以下のものには窒化ガリウム、 窒化インジウム、 窒化アルミニウムのうちから選ばれた少なくとも 1種以上を主成分とする単結晶化した薄膜が 形成でき該単結晶薄膜のミラ一指数 ( 0 0 2 ) の格子面の X線回折ロッキングカーブの半値幅 として 1 5 0秒以下のものが得られ易い。
上記窒化アルミニウムを主成分とする焼結体からなる基板の焼き放し (a s— f i r e ) 面 を用いるときは、 ブラシ掛けあるいはアルミナ粉末などを用いたホーニングにより基板表面の 付着物、 異物、 突起などを取り除いた状態のものを用いることが好ましい。 ラッフ ff磨は通常 用いられているラッフ ¾ff削機によりアルミナ砥粒、 炭化珪素砥粒、 ダイヤモンド砥粒などを用 いた方法が問題なく使用できる。 ブラスト研磨はアルミナ砥粒、 炭化珪素砥粒などを用いて通 常のサンドブラスト機などにより問題なく行うことができる。 また、 鏡面研磨は通常の布製パ ッドゃポリウレタンパッドなどの工具 (ポリシャ一) を有する研磨機により微粒のアルミナ、 酸化セリウム、 ダイヤモンド、 酸化珪素あるいは酸化クロムなどを主成分とする研鶴 ijを 用いた方法が問題なく使用できる。
本発明において窒化アルミニウムを主成分とする焼結体からなる薄膜形成用基板、 窒化アル
ミ二ゥムを主成分とする焼結体を基板として用いることで作製される薄膜基板においては窒化 ガリウム、 窒化インジウム、 窒化アルミニウムのうちから選ばれた少なくとも 1種以上を主成 分とする単結晶薄膜を形成する場合その基板の表面状態、 表面平滑性が特に重要である。 この 表面状態、 表面平滑性は例えば 1 7 5 0°C以上の温度で 3時間以上の比較的長い時間焼成する ことなどで得られる A 1 N が高められた窒化アルミニウムを主成分とする焼結体あるいは 窒化アルミニウム粒子が大きく成長した窒化アルミニウムを主成分とする焼結体あるいは光透 過率が高められた窒化アルミニウムを主成分とする焼結体、 などを基板とした場合も同様に重 要である。 また、 窒化ガリウム、 窒化インジウム、 窒化アルミニウムのうちから選ばれた少な くとも 1種以上を主成分とする薄膜が基板の 1面しか形成されない場合、 該薄膜が形成されて いない窒化アルミニウムを主成分とする焼結体からなる薄膜形成用基板の面、 窒化アルミニゥ ムを主成分とする焼結体を基板として用いることで作製される薄膜基板の面の表面状態、 表面 平滑性は必要に応じて任意の状態が選択でき該薄膜が形成される表面状態と異なっていても良 い。 本発明による上記窒化アルミ二ゥムを主成分とする焼結体からなる基板の表面状態として は鏡面に研磨した状態のものが基板に直接形成される窒化ガリウム、 窒化インジウム、 窒化ァ ルミニゥムのうちから選ばれた少なくとも 1種以上を主成分とする単結晶薄膜の結晶性が高い 傾向がある。 焼き放し (a s— f i r e ) 状態のものとラッフ Iff磨した状態のものを比較する と焼き放し状態の基板表面の方が基板に直接形成される上記単結晶薄膜の結晶性が高い傾向が ある。 このような現象はおそらく基板表面の平滑度すなわち基板表面の粗さの程度により窒化 ガリウム、 窒化インジウム、 窒化アルミニウムのうちから選ばれた少なくとも 1種以上を主成 分とする単結晶薄膜の成長時における核成長の方向を一定にする度合いが異なるためであろう と f|現 ijされる。
上記焼き放し状態、 あるいはラッフ ¾ff磨、 ブラスト研磨、 鏡面研磨、 機械的な溝切り加工な どの表面加工を施した窒化アルミニウムを主成分とする焼結体からなる基板をさらに例えばフ ッ化水素酸 (HF)、 フッ麵 (HF +HN03の混合酸)、 纖 (HN03)、 疆 (HC 1 )、 硫酸(H2 S〇4)などの酸に浸漬したり、 アセトン、イソプロピルアルコール、塩化メチレン、 フルォロカーボンなどの有機溶剤に浸漬したり、 H2、 N2、 A rなどを含む非酸化性雰囲気中 あるいは減圧中で加熱ァニールする、 あるいはこれらを複数組み合わせて行う、 などの処理を 施すことにより基板に形成される単結晶薄膜の結晶性の改善をはかることが可能であり有効と なり得る。 このような処理を施すことで形成される単結晶薄膜の結晶性力 善され易くなる理 由は基板表面の異物、 突起、 傷、 くぼみなどの欠陥あるいは研削'研磨などにより生じるひず みが除去されたり軽減されるためであろうと本願発明者は推測している。 窒化アルミニウムを 主成分とする焼結体からなる基板は窒化アルミニウム微粒子の集合した多結晶体であるので基 板表面に微粒子脱落や微粒子の欠けなどによる欠陥や研削 ·研磨ひずみが生じ易いと思われる のでこのような処理を施すことで平均表面粗さを例えば R a 1 O nm以下とより小さくできる 効果があると思われる。
本発明において窒化アルミニウムを主成分とする焼結体を基板として用い窒化ガリウム、 窒 化インジウム、 窒化アルミニウムのうちから選ばれた少なくとも 1種以上を主成分とする薄膜 が形成されている薄膜基板の表面平滑性は通常基板として使用する窒化アルミニウムを主成分 とする焼結体の表面状態と同等かあるいは向上する。 すなわち窒化アルミニウムを主成分とす る焼結体からなる基板表面の平滑度が例えば平均表面粗さ R a = 3 0 nmであれば本発明によ る薄膜基板の表面平滑度は R a 3 0 nmあるいはそれ以下となる。 したがって本発明による窒 化ガリウム、 窒化インジウム、 窒化アルミニウムのうちから選ばれた少なくとも 1種以上を主 成分とする薄膜が形成された薄膜基板表面の平滑性は、 平均表面粗さ R a = 2 0 0 0 nm以下 の窒化アルミニウムを主成分とする焼結体からなる基板を用いた場合は 2 0 0 0 nm以下、 平
均表面粗さ R a = 1 0 0 0 nm以下の窒化アルミニウムを主成分とする焼結体からなる基板を 用いた場合は R a 1 0 0 0 nm以下、 平均表面粗さ R a = 1 0 0 nm以下の窒化アルミニウム を主成分とする焼結体からなる基板を用いた場合は R a 1 0 0 nm以下、 平均表面粗さ R a = 2 0 nm以下の窒化アルミニウムを主成分とする焼結体からなる基板を用いた場合は R a 2 0 nm以下である。 本発明による窒化アルミニウムを主成分とする焼結体を基板として用い窒化 ガリウム、 窒化インジウム、 窒化アルミニウムのうちから選ばれた少なくとも 1種以上を主成 分とする薄膜が形成された薄膜基板表面の平滑性は平均表面粗さ R a 1 O nm以下あるいは R a 3 nm〜5 nm以下さらに R a 1 nm〜3 nm以下のもの得られる。 本発明による薄膜基板 において、 窒化アルミニウムを主成分とする焼結体からなる基板の表面平滑性と同等あるいは そ^¾上に向上した表面平滑性を与える薄膜は窒化ガリウム、 窒化インジウム、 窒化アルミ二 ゥムのうちから選ばれた少なくとも 1種以上を主成分とし単結晶薄膜だけに限らない。 窒化ァ ルミ二ゥムを主成分とする焼結体からなる基板を用い窒化ガリウム、 窒化インジウム、 窒化ァ ルミニゥムのうちから選ばれた少なくとも 1種以上を主成分とする無定形、 多結晶、 配向性多 結晶のうちから選ばれた少なくともいずれかの結晶状態を有する薄膜が形成された本発明によ る薄膜基板の場合も上記単結晶薄膜と同様に、 窒化アルミニウムを主成分とする焼結体からな る基板の表面平滑性と同等かそれ以上に向上し、 平滑性の程度も平均表面粗さ R a 2 0 nm以 下、 あるいは R a 1 O nm以下、 あるいは R a 3 nm〜 5 nm以下、 さらに1 & 1 11111〜3 1 m以下のもの得られる。
このような表面平滑性を有する薄膜基板にはさらに優れた窒化ガリゥム、 窒化ィンジゥム、 窒化アルミニウムのうちから選ばれた少なくとも 1種以上を主成分とする薄膜が形成できる。 すなわち、 窒化アルミニウムを主成分とする焼結体を基板として窒化ガリウム、 窒化インジゥ ム、 窒化アルミニウムのうちから選ばれた少なくとも 1種以上を主成分とする単結晶薄膜が形 成されている薄膜基板に対して、 あるいは窒化アルミニウムを主成分とする焼結体を基板とし て用い窒化ガリウム、 窒化インジウム、 窒化アルミニウムのうちから選ばれた少なくとも 1種 以上を主成分とし単結晶、 無定形、 多結晶、 配向性多結晶のうちから選ばれた少なくともいず れかの結晶状態を有する薄膜が形成されている薄膜基板に対して、 さらに窒化ガリウム、 窒化 インジウム、 窒化アルミニウムのうちから選ばれた少なくとも 1種以上を主成分とする単結晶 薄膜を形成した場合、 上記薄膜基板の表面平滑性が R a 5 0 nm以下では該薄膜基板に形成さ れる上記窒化ガリウム、 窒化インジウム、 窒化アルミニウムのうちから選ばれた少なくとも 1 種以上を主成分とする単結晶薄膜のミラー指数 ( 0 0 2) の格子面の X線回折ロッキング力一 ブの半値幅が 2 4 0秒以下の単結晶薄膜が得られ易い。 また、 上記薄膜基板の表面平滑性が R a 2 O nm以下では該薄膜基板に形成される上記窒化ガリウム、 窒化インジウム、 窒化アルミ ニゥムのうちから選ばれた少なくとも 1種以上を主成分とする単結晶薄膜のミラ一指数 ( 0 0 2) の格子面の X線回折ロッキング力一ブの半値幅が 2 0 0秒以下の単結晶薄膜が得られ易い。 上記薄膜基板の表面平滑性が R a 1 0 nm以下では該薄膜基板に形成される上記窒化ガリウム、 窒化ィンジゥム、 窒化アルミニウムのうちから選ばれた少なくとも 1種以上を主成分とする単 結晶薄膜のミラー指数 ( 0 0 2 ) の格子面の X線回折ロッキングカーブの半値幅が 1 5 0秒以 下の単結晶薄膜が得られ易い。 上記本薄膜基板の表面平滑性が R a 5 nm以下では該薄膜基板 に形成される上記窒化ガリゥム、 窒化ィンジゥム、 窒化アルミニウムのうちから選ばれた少な くとも 1種以上を主成分とする単結晶薄膜のミラー指数 ( 0 0 2) の格子面の X線回折ロッキ ングカーブの半値幅が 1 3 0秒以下の単結晶薄膜が得られ易い。 さらに上記薄膜基板の表面平 滑性が R a 3 nm以下では該薄膜基板に形成される上記窒化ガリウム、 窒化インジウム、 窒化 アルミニウムのうちから選ばれた少なくとも 1種以上を主成分とする単結晶薄膜のミラー指数 ( 0 0 2 ) の格子面の X線回折ロッキングカーブの半値幅が 1 0 0秒以下の単結晶薄膜が得ら
れ易い。 本発明によるこのような平滑性を有する薄膜基板には上記例示したような窒化ガリゥ ム、 窒化インジウム、 窒化アルミニウムのうちから選ばれた少なくとも 1種以上を主成分とす る単結晶薄膜だけでなぐ 無定形、 多結晶、 配向性多結晶のうちから選ばれた少なくともいず れかの結晶状態を有する窒化ガリウム、 窒化インジウム、 窒化アルミニウムのうちから選ばれ た少なくとも 1種以上を主成分とする薄膜も形成できる。
また、 本発明による上記薄膜基板において、 窒化アルミニウムを主成分とする焼結体からな る基板に形成され該窒化アルミニウムを主成分とする焼結体からなる基板の表面平滑性と同等 あるいはそれ以上に向上した表面平滑性を与える薄膜は窒化ガリウム、 窒化インジウム、 窒化 アルミニウムのうちから選ばれた少なくとも 1種以上を主成分とし単結晶、 無定形、 多結晶、 配向性多結晶のうちから選ばれた少なくともいずれかの結晶状態を有するものであるが、 この 薄膜の厚みは 0. 5 nm以上であれば窒化アルミニウムを主成分とする焼結体からなる基板の 表面平滑性と同等あるいはそれ以上に向上した表面平滑性の薄膜基板が得られる。
上記のように、 窒化アルミニウムを主成分とする焼結体からなる基板に窒化ガリウム、 窒化 インジウム、窒化アルミニウムのうちから選ばれた少なくとも 1種以上を主成分とする単結晶、 無定形、 多結晶、 配向性多結晶など各種結晶状態の薄膜が形成された基板の表面平滑性は、 薄 膜が形成されていない窒化アルミニウムを主成分とする焼結体からなる基板よりも向上し易い。 また、上記の窒化アルミニウムを主成分とする 体からなる基板に単結晶、無定形、多結晶、 配向性多結晶など各種結晶状態の薄膜があらかじめ形成された基板の上にさらに単結晶、 無定 形、 多結晶、 配向性多結晶など各種結晶状態の薄膜を形成することにより (薄膜を多層に形成 することにより) 基板の表面粗さが小さくなり表面平滑性がさらに改善され得る。 該基板の平 均表面粗さ R a «®常 1 O nm以下のものが比較的容易に得られる。 このような多層の薄膜を 形成することで基板の表面平滑性を改善する場合、 窒化アルミニウムを主成分とする焼結体か らなる基板にあらかじめ最初に形成される単結晶薄膜、 無定形薄膜、 多結晶薄膜、 配向性多結 晶薄膜の中では無定形薄膜、 多結晶薄膜、 配向性多結晶薄膜のなかから選ばれる少なくともい ずれかの結晶状態を有する薄膜を形成した基板を用いることが好ましぐ 平均表面粗さ R aが 3 nm以下の薄膜基板が作製し得る。 また、 上記多層の薄膜を形成することで基板の表面平滑 性を改善する場合、 窒化アルミニウムを主成分とする焼結体からなる基板にあらかじめ最初に 形成される単結晶薄膜、 無定形薄膜、 多結晶薄膜、 配向性多結晶薄膜の中では配向性多結晶薄 膜を形成した基板を用いることが好ましい。 まず窒化アルミニウムを主成分とする焼結体から なる基板に直接配向性多結晶薄膜を形成し、 その後さらに単結晶薄膜、 無定形薄膜、 多結晶薄 膜、 配向性多結晶薄膜を形成した基板の平均表面粗さは少なくとも R a 2 nm以下さらには R a 1 nm以下のものが得られ易い。 上記のような配向性多結晶薄膜形成による効果がなぜ生じ るのかその理由は必ずしも明確でないが、 窒化アルミニウムを主成分とする焼結体からなる基 板に薄膜を直接形成する時に生じる表面平滑性の違いがそのままその上に形成される薄膜にも 影響を与えることが大きな要因ではないかと本願発明者は推測している。 すなわち、 窒化アル ミニゥムを主成分とする焼結体からなる基板に形成される配向性多結晶薄膜の表面粗さは通常 単結晶薄膜、 無定形薄膜及び多結晶薄膜より小さい場合が多い。 このような元々の表面粗さの 違いがそのままその上に形成される薄膜の表面粗さの違いとして反映されるのではないかと思 われる。 元々の表面粗さの違いは、 例えば単結晶薄膜を形成する時は比較的高温を要すること が多いので薄膜中で局部的な結晶成長の相違により、 あるいは無定形薄膜及 結晶薄膜では 薄膜の緻密さが低くミク口な欠陥が多く存在することにより、 窒化アルミニウムを主成分とす る焼結体からなる基板に存在するミクロな空孔、 突起、 窒化アルミニウム粒子の欠けなど焼結 体に起因する欠陥を補う程度が配向性多結晶薄膜より小さい結果生じるのではないかと本願発 明者は推測している。
窒化アルミニウムを主成分とする焼結体からなる基板に形成された薄膜によるこのような表 面平滑性は自発的に生じ得るが、 前記で例示したような研削及び研磨装置、 研^ ijを用いてメ カノケミカルな (機械的ィ匕学的な操作による) 研削あるいは鏡面研磨を行うことによつても達 成される。 メカノケミカルな研削あるいは鏡面研磨により薄膜基板の平均表面粗さ R aは少な くとも 1 O nm以下のものが作製し得る。 また、 平均表面粗さ R aが 3 nm以下、 あるいは 2 nm以下、 さらには l nm以下の薄膜基板が作製し得る。 上記メカノケミカルな研削あるいは 研磨により窒化アルミ二ゥムを主成分とする焼結体と同等かそれ以上の優れた平滑性が得られ る理由は窒化アルミニウムを主成分とする焼結体に形成された薄膜は窒化アルミニウムを主成 分とする焼結体に比べてより微細な粒子からなるかあるいは微粒子などからでなく均質で連続 し一体化した構造 (モノリシック構造) であるため nmレベルの欠陥が少ないためであろうと 推彻 jされる。
また、上記のような薄膜が形成された基板をさらに例えばフッ化水素酸(HF)、フッ碰 (H F +HN〇3の混合酸)、 » (HN03)、 « (HC 1 )、 硫酸 (H2 S 04) などの酸に浸漬し たり、 H2、 N2、 A rなどを含む非酸化性雰囲気中あるいは減圧中で加熱ァニールする、 ある いはこれらを複数組み合わせて行う、 などの処理を施すことにより基板表面に形成される単結 晶薄膜の結晶性の改善をはかることが可能であり有効となり得る。
このような表面平滑性を有する薄膜基板を用いて、 発光素子、 光導波路、 回驢板、 表面弾 性波素子などの電子素子あるいは電子部品を作製すればより優れた特性のものが得られ易い。 特に発光効率の優れた発光素子が作製し得る。
窒化ガリウム、 窒化インジウム、 窒化アルミニウムのうちから選ばれた少なくとも 1種以上 を主成分とする単結晶をはじめ各種結晶状態の薄膜を形成するために本発明において炭化珪素、 窒化珪素、 窒化ガリウム、 酸化亜鉛、 酸化ベリリウムなどの六方晶系及び ¾化アルミニウムな どの三方晶系あるいは六方晶系として分類できる結晶構造を有する材料からなる焼結体を用い た基板 (すなわち薄膜 成用基 ¾) 表面あるいは前記薄膜形成用基板に窒化ガリウム、 窒化ィ ンジゥム、 窒化アルミニウムのうちから選ばれた少なくとも 1種以上を主成分とする薄膜が形 成された薄膜基板表面の平滑度は平均表面粗さ R aが 1 0 0 0 nm以下であることが好ましい。 このような基板の表面平滑性を有することが前記単結晶薄膜を形成するためには望ましい。 し たがって本発明においては前記薄膜形成用基板を用いて作製される薄膜基板の少なくとも 1つ の面が上記のような平滑度を有することが ましい。 R a 1 0 0 0 nm以下の平均表面粗さを 有する基板は炭化珪素、 窒化珪素、 窒化ガリウム、 酸化亜鉛、 酸化ベリリウムなどの六方晶系 及び酸化アルミニウムなどの三方晶系あるいは六方晶系として分類できる結晶構造を有する材 料を主成分とする焼結体の焼き放し (a s— f i r e ) 表面やラップ研削された表面、 あるい はブラスト研磨された表面、 あるいは鏡面研磨された表面、 あるいは化学的にエッチング (腐 食) された表面、 あるいは機械的に溝切り加工などが施された表面、 あるいは前記薄膜形成用 基板を用いて作製される薄膜基板の表面などにおいて得ることができる。 化学的なエッチング は例えば薬液などを用いたウエット方式やフッ素などの成分を含有するプラズマガスなどによ るドライ ^などが好適に使用し得る。 R a 1 0 0 0 nm以下の平均表面粗さを有するこれら 基板には直接窒化ガリウム、 窒化インジウム、 窒化アルミニウムのうちから選ばれた少なくと も 1種以上を主成分とする単結晶化した薄膜が形成でき該単結晶薄膜のミラ一指数 (0 0 2 ) の格子面の X線回折ロッキングカーブの半値幅として 3 6 0 0秒以下のものが得られ易い。 前 記薄膜形成用基板を用いて作製される薄膜基板の表面平滑性は通常は R a 1 0 0 nm以下、 よ り好ましくは R a 3 0 nm以下の鏡面状態のものが好ましい。 鏡面状態とすることで形成され る単結晶薄膜の結晶性が向上し易くなる。 炭化珪素、 窒化珪素、 窒化ガリウム、 酸化亜鉛、 酸 化べリリゥムなどの六方晶系及び 化アルミ二ゥムなどの三方晶系あるいは六方晶系として分
類できる結晶構造を有する材料を主成分とする焼結体を用いた基板の中で平均表面粗さ R aが 1 0 O nm以下のものには窒化ガリウム、 窒化インジウム、 窒化アルミニウムのうちから選ば れた少なくとも 1種以上を主成分とする単結晶化した薄膜が形成でき該単結晶薄膜のミラー指 数 (0 0 2) の格子面の X線回折ロッキングカーブの半値幅として 1 0 0 0秒以下のものが得 られ易い。 またこれら基板の平均表面粗さ R aは 1 O nm以下であることがより好ましい。 R a 1 O nm以下の平均表面粗さを有するこれらの基板は炭化珪素、 窒化珪素、 窒化ガリウム、 酸化疆、 酸化ベリリウムなどの六方晶系及び 化アルミニウムなどの三方晶系あるいは六方 晶系として分類できる結晶構造を有する材料を主成分とする焼結体の鏡面研磨された前記薄膜 形成用基板を用いて作製される薄膜基板の表面などにおいて得ることができる。 R a 1 O nm 以下の平均表面粗さを有する基板には直接窒化ガリゥム、 窒化ィンジゥム、 窒化アルミニゥム のうちから選ばれた少なくとも 1種以上を主成分とする単結晶化した薄膜が形成でき該単結晶 薄膜のミラ一指数 (0 0 2) の格子面の X線回折ロッキングカーブの半値幅として 3 0 0秒以 下のものが得られ易い。 またこれら基板の平均表面粗さ R aは 5 nm以下であることがさらに 好ましい。 R a 5 nm以下の平均表面粗さを有する基板は炭化珪素、窒化珪素、窒化ガリウム、 酸化亜鉛、 酸化ベリリウムなどの六方晶系及び酸化アルミニウムなどの三方晶系あるいは六方 晶系として分類できる結晶構造を有する材料を主成分とする焼結体の鏡 ®研磨された前記薄膜 形成用基板を用いて作製される薄膜基板の表面などにおいて得ることができる。 R a 5 nm以 下の平均表面粗さを有する基板には直接窒化ガリウム、 窒化インジウム、 窒化アルミニウムの うちから選ばれた少なくとも 1種以上を主成分とする単結晶化した薄膜が形成でき該単結晶薄 膜のミラー指数 (0 0 2 ) の格子面の X線回折ロッキングカーブの半値幅として 2 4 0秒以下 のものが得られ易い。
上記炭化珪素、 窒化珪素、 窒化ガリウム、 酸化碰、 酸化ベリリウムなどの A¾晶系及び酸 化アルミニウムなどの三方晶系あるいは六方晶系として分類できる結晶構造を有する材料を主 成分とする焼結体からなる基板の焼き放し (a s— f i r e ) 面を用いるときは、 ブラシゃァ ルミナ粉末などを用いたホーニングにより基板表面の付着物、 異物、 突起などを取り除いた状 態のものを用いることが好ましい。 ラッフ Iff磨は通常行われているようなラップ研削機により アルミナ砥粒、 炭化珪素嫩、 ダイヤモンド砥粒を用いた方法が問題なく使用できる。 また、 鏡面研磨は通常の布製パッドゃポリウレタンパッドなどの工具を有する研磨機により微粒のァ ルミナ、 酸化セリウム、 ダイヤモンド、 酸化珪素あるいは酸化クロムなどを主成分とする研磨 剤を適宜用いた方法が問題なく使用できる。
本発明において炭化珪素、 窒化珪素、 窒化ガリウム、 酸化亜鉛、 酸化ベリリウムなどの六方 晶系及び ¾化アルミニウムなどの三方晶系あるいは六方晶系として分類できる結晶構造を有す る材料を主成分とする焼結体からなる薄膜形成用基板を用いて作製される薄膜基板においてそ の表面状態は薄膜が形成される面が特に重要である。 窒化ガリウム、 窒化インジウム、 窒化ァ ルミニゥムのうちから選ばれた少なくとも 1種以上を主成分とする薄膜が基板の 1面しか形成 されない場合、 該薄膜が形成されない炭化珪素、 窒ィ匕珪素、 窒ィ匕ガリウム、 酸化亜鉛、 酸化べ リリゥムなどの六方晶系及び酸化アルミニウムなどの三方晶系あるいは六方晶系として分類で きる結晶構造を有する材料を主成分とする焼結体からなる薄膜形成用基板を用いて作製される 薄膜基板の表面状態は必要に応じて任意の状態が選択でき窒化ガリウム、 窒化インジウム、 窒 化アルミニウムのうちから選ばれた少なくとも 1種以上を主成分とする薄膜が形成される表面 状態と異なっていても良い。本発明による上記炭化珪素、窒化珪素、窒化ガリウム、酸化 »、 酸化ベリリゥムなどの六方晶系及び酸化アルミニウムなどの三方晶系あるいは六方晶系として 分類できる結晶構造を有する材料を主成分とする焼結体からなる基板の表面状態としては鏡面 に研磨した状態のものが基板に直接形成される窒化ガリウム、 窒化インジウム、 窒化アルミ二
ゥムのうちから選ばれた少なくとも 1種以上を主成分とする単結晶薄膜の結晶性が高い傾向が ある。 焼き放し (a s— f i r e) 状態のものとラップ研磨した状態のものを比較すると焼き 放し状態の基板表面の方が基板に直接形成される上記単結晶薄膜の結晶性が高い傾向がある。 このような現象はおそらく基板表面の平滑度すなわち基板表面の粗さの程度により窒化ガリゥ ム、 窒化インジウム、 窒化アルミニウムのうちから選ばれた少なくとも 1種以上を主成分とす る単結晶薄膜の成長時における核成長の方向を一定にする度合いが異なるためであろうと推測 される。 また、 このような現象は窒化アルミニウムを主成分とする焼結体を用いた基板の場合 に比べより基板表面の平滑度が高いものが求められるという違いはあるが、 おそらく基板表面 の平滑度すなわち基板表面の粗さの程度により窒化ガリゥム、 窒化ィンジゥム、 窒化アルミ二 ゥムのうちから選ばれた少なくとも 1種以上を主成分とする単結晶薄膜の成長時における核成 長の方向を一定にする度合いが異なるためであろうと推測される。
本発明において炭化珪素、 窒化珪素、 窒化ガリウム、 酸化亜鉛、 酸化ベリリウムなどの六方 晶系及び酸化アルミ二ゥムなどの三方晶系あるいは六方晶系として分類できる結晶構造を有す る材料を主成分とする焼結体を基板として用い窒化ガリウム、 窒化インジウム、 窒化アルミ二 ゥムのうちから選ばれた少なくとも 1種以上を主成分とする薄膜が形成される薄膜基板の表面 平滑性は通常基板として使用する炭化珪素、 窒化珪素、 窒化ガリウム、 酸化亜鉛、 酸化べリリ ゥムなどの六方晶系及び酸化アルミニウムなどの三方晶系あるいは六方晶系として分類できる 結晶構造を有する材料を主成分とする焼結体の表面状態と同等かあるいは向上する。 すなわち 炭化珪素、 窒化珪素、 窒化ガリウム、 酸化亜鉛、 酸化ベリリウムなどの六方晶系及び酸化アル ミニゥムなどの三方晶系あるいは六方晶系として分類できる結晶構造を有する材料を主成分と する焼結体からなる基板表面の平滑度が例えば平均表面粗さ R a = 3 0 nmであれば本発明に よる薄膜基板の表面平滑度は R a 3 0 nmあるいはそれ以下となる。 したがって本発明による 窒化ガリウム、 窒化インジウム、 窒化アルミニウムのうちから選ばれた少なくとも 1種以上を 主成分とする単結晶薄膜が形成された薄膜基板表面の平滑性は、 平均表面粗さ R a = l 0 0 0 nm以下の炭化珪素、 窒化珪素、 窒化ガリウム、 酸化亜鉛、 酸化ベリリウムなどの六方晶系及 ぴ谶化アルミニウムなどの三方晶系あるいは六方晶系として分類できる結晶髓を有する材料 を主成分とする焼結体からなる基板を用いた場合は R a 1 0 0 0 nm以下、 平均表面粗さ R a = 1 0 0 nm以下の炭化珪素、 窒化珪素、 窒ィヒガリウム、 酸化亜鉛、 酸化ベリリウムなどの六 方晶系及び酸化アルミ二ゥムなどの三方晶系あるいは六方晶系として分類できる結晶構造を有 する材料を主成分とする焼結体からなる基板を用いた場合は R a 1 0 0 nm以下、 平均表面粗 さ R a = 3 0 nm以下の炭化珪素、 窒化珪素、 窒ィ匕ガリウム、 酸化亜鉛、 酸化ベリリウムなど の六方晶系及び 化アルミニウムなどの三方晶系あるいは六方晶系として分類できる結晶構造 を有する材料を主成分とする焼結体からなる基板を用いた場合は R a 3 0 nm以下、 平均表面 粗さ R a = l O nm以下の炭化珪素、 窒化珪素、 窒化ガリウム、 酸化亜鉛、 酸化ベリリウムな どの六方晶系及び mi匕アルミ二ゥムなどの三方晶系ある は六方晶系として分類できる結晶構 造を有する材料を主成分とする焼結体からなる基板を用いた場合は R a 1 0 nm以下、 平均表 面粗さ R a = 5 nm以下の炭化珪素、 窒化珪素、 窒ィ匕ガリウム、 酸化亜鉛、 酸ィ匕ベリリウムな どの六方晶系及び酸化アルミニウムなどの三方晶系あるいは六方晶系として分類できる結晶構 造を有する材料を主成分とする焼結体からなる基板を用いた場合は R a 5 nm以下である。 本発明による炭化珪素、 窒化珪素、 窒化ガリウム、 酸化亜鉛、 酸化ベリリウムなどの六方晶 系及ぴ 化アルミ二ゥムなどの三方晶系あるいは六方晶系として分類できる結晶構造を有する 材料を主成分とする焼結体を基板として用い窒化ガリウム、 窒化インジウム、 窒化アルミニゥ ムのうちから選ばれた少なくとも 1種以上を主成分とする薄膜が形成された薄膜基板表面の平 滑性は R a 1 0 nm以下あるいは R a 3 nm〜5 nm以下さらに R a l nm〜3 nm以下のも
の得られる。本発明による薄膜基板において、炭化珪素、窒化珪素、窒化ガリウム、酸化亜鉛、 酸化ベリリゥムなどの六方晶系及び酸化アルミニウムなどの三方晶系あるいは六方晶系として 分類できる結晶構造を有する材料を主成分とする焼結体からなる基板の表面平滑性と同等ある いはそれ以上に向上した表面平滑性を与える薄膜は窒化ガリウム、 窒化インジウム、 窒化アル ミニゥムのうちから選ばれた少なくとも 1種以上を主成分とし単結晶薄膜だけに限らない。 炭 化珪素、 窒化珪素、 窒化ガリウム、 酸化 »、 酸化ベリリウムなどの六方晶系及び 化アルミ ニゥムなどの三方晶系あるいは六方晶系として分類できる結晶構造を有する材料を主成分とす る焼結体からなる基板を用い窒化ガリウム、 窒化インジウム、 窒化アルミニウムのうちから選 ばれた少なくとも 1種以上を主成分とする無定形、 多結晶、 配向性多結晶のうちから選ばれた 少なくともいずれかの結晶状態を有する薄膜が形成された本発明による薄膜基板の場合も上記 単結晶薄膜と同様に、 炭化珪素、 窒化珪素、 窒化ガリウム、 酸化碰、 酸化ベリリウムなどの 六方晶系及び 化アルミニウムなどの三方晶系あるいは六方晶系として分類できる結晶構造を 有する材料を主成分とする焼結体からなる基板の表面平滑性と同等かそれ以上に向上し、 平滑 性の程度も R a 2 0 nm以下、あるいは R a 1 0 nm以下、あるいは R a 3 nm〜 5 nm以下、 さらに R a 1 nm〜3 nm以下のもの得られる。
また、本発明による上記薄膜基板において、炭化珪素、窒化珪素、窒化ガリウム、酸化 «、 酸化ベリリゥムなどの六方晶系及び酸化アルミニウムなどの三方晶系あるいは六方晶系として 分類できる結晶構造を有する材料を主成分とする焼結体からなる基板の表面平滑性と同等ある いはそれ以上に向上した表面平滑性を与える薄膜は窒化ガリウム、 窒化インジウム、 窒化アル ミニゥムのうちから選ばれた少なくとも 1種以上を主成分とし単結晶、 無定形、 多結晶、 配向 性多結晶のうちから選ばれた少なくともいずれかの結晶状態を有するものであるが、 この薄膜 の厚みは 0. 5 nm以上であれば炭化珪素、 窒化珪素、 窒化ガリウム、 酸化亜鉛、 酸化べリリ ゥムなどの六方晶系及び酸化アルミニウムなどの三方晶系あるいは六方晶系として分類できる 結晶構造を有する材料を主成分とする焼結体からなる基板の表面平滑性と同等あるいはそれ以 上に向上した表面平滑性の薄膜基板が得られる。
上記のように、 炭化珪素、 窒化珪素、 窒化ガリウム、 酸化亜鉛、 酸化ベリリウムなどの 7^ 晶系及び 化アルミ二ゥムなどの三方晶系あるいは六方晶系として分類できる結晶構造を有す る材料を主成分とする焼結体からなる基板に窒化ガリウム、 窒化インジウム、 窒化アルミニゥ ムのうちから選ばれた少なくとも 1種以上を主成分とする単結晶、 無定形、 多結晶、 配向性多 結晶など各種結晶状態の薄膜が形成された基板の表面平滑性は、 薄膜が形成されていない炭化 珪素、 窒化珪素、 窒化ガリウム、 酸化亜鉛、 酸化ベリリウムなどの六方晶系及び 化アルミ二 ゥムなどの三方晶系あるいは六方晶系として分類できる結晶構造を有する材料を主成分とする 焼結体からなる基板よりも向上し易い。 また、 上記の炭化珪素、 窒化珪素、 窒化ガリウム、 酸 化亜鉛、 酸化ベリリウムなどの六方晶系及び酸化アルミニウムなどの三方晶系あるいは六方晶 系として分類できる結晶構造を有する材料を主成分とする焼結体からなる基板に単結晶、 無定 形、 多結晶、 配向性多結晶など各種結晶状態の薄膜があらかじめ形成された基板の上にさらに 単結晶、 無定形、 多結晶、 配向性多結晶など各種結晶状態の薄膜を形成することにより (薄膜 を多層に形成することにより)基板の表面粗さが小さくなり表面平滑性がさらに改善され得る。 このような多層の薄膜を形成することで基板の表面平滑性を改善する場合、 炭化珪素、 窒化珪 素、 窒化ガリウム、 酸化亜鉛、 酸化ベリリウムなどの六方晶系及び 化アルミニウムなどの三 方晶系あるいは六方晶系として分類できる結晶構造を有する材料を主成分とする焼結体からな る基板に最初に直接形成される単結晶薄膜、 無定形薄膜、 多結晶薄膜、 配向性多結晶薄膜の中 では酉'己向性多結晶薄膜を形成した基板を用いることが好ましい。 まず炭化珪素、 窒化珪素、 窒 化ガリウム、 酸化亜鉛、 酸化ベリリウムなどの六方晶系及び 化アルミニウムなどの三方晶系
あるいは六方晶系として分類できる結晶構造を有する材料を主成分とする焼結体からなる基板 に直接配向性多結晶薄膜を形成し、 その後さらに単結晶薄膜、 無定形薄膜、 多結晶薄膜、 配向 性多結晶薄膜を形成した基板の表面粗さは少なくとも 2 nm以下さらには 1 nm以下のものが 得られ易い。 上記のような配向性多結晶薄膜形成による効果がなぜ生じるのカ の理由は必ず しも明確でないが、 炭化珪素、 窒化珪素、 窒化ガリウム、 酸化亜鉛、 酸化ベリリウムなどの六 方晶系及ぴ谶化アルミニウムなどの三方晶系あるいは六方晶系として分類できる結晶構造を有 する材料を主成分とする焼結体からなる基板に薄膜を直接形成する時に生じる表面平滑性の違 いがそのままその上に形成される薄膜にも影響を与えることが大きな要因ではないかと本願発 明者は推測している。 すなわち、 炭化珪素、 窒化珪素、 窒化ガリウム、 酸化亜鉛、 酸化べリリ ゥムなどの六方晶系及び 化アルミ二ゥムなどの三方晶系あるいは六方晶系として分類できる 結晶構造を有する材料を主成分とする焼結体からなる基板に形成される配向性多結晶薄膜の表 面粗さは通常単結晶薄膜、 無定形薄膜及 結晶薄膜より小さい場合が多い。 このような元々 の表面粗さの違いがそのままその上に形成される薄膜の表面粗さの違いとして反映されるので はないかと思われる。 元々の表面粗さの違いは、 例えば単結晶薄膜を形成する時は比較的高温 を要することが多いので薄膜中で局部的な結晶成長の相違により、 あるいは無定形薄膜及び多 結晶薄膜では薄膜の緻密さが低くミクロな欠陥が多く存在することにより、 炭化珪素、 窒化珪 素、 窒化ガリウム、 酸化亜鉛、 酸化ベリリウムなどの六方晶系及ぴ 化アルミニウムなどの三 方晶系あるいは六方晶系として分類できる結晶構造を有する材料を主成分とする焼結体からな る基板に存在するミクロな空孔、 突起、 焼結体粒子の欠けなど焼結体に起因する欠陥を補う程 度が 向性多結晶薄膜より小さい結果生じるのではないかと本願発明者は推測している。 炭化珪素、 窒化珪素、 窒化ガリウム、 酸化亜鉛、 酸化ベリリウムなどの六方晶系及び ¾化ァ ルミニゥムなどの三方晶系あるいは六方晶系として分類できる結晶構造を有する材料を主成分 とする焼結体からなる基板に形成された薄膜によるこのような平滑性は自発的に生じ得るが、 メカノケミカルな (機械的化学的な操作による) 研削あるいは研磨を行うことによつても達成 される。 上記メカノケミカルな研削あるいは研磨により炭化珪素、 窒化珪素、 窒化ガリウム、 酸化 » 酸化ベリリウムなどの六方晶系及ぴ衡匕アルミニウムなどの三方晶系あるいは六方 晶系として分類できる結晶構造を有する材料を主成分とする焼結体と同等かそれ以上の優れた 平滑性が得られる理由は各焼結体に形成された薄膜は炭化珪素、 窒化珪素、 窒化ガリウム、 酸 化 酸化ベリリウムなどの六方晶系及び镀化アルミニウムなどの三方晶系あるいは六方晶 系として分類できる結晶構造を有する材料を主成分とする焼結体に比べてより微細な粒子から なるかあるいは微粒子などからでなく均質で連続し一体化した構造 (モノリシック構造) であ るため nmレベルの欠陥が少ないためであろうと推測される。 上記のように薄膜が形成された 基板をさらに例えばフッ化水素酸(HF)、 フッ硝酸 (HF +HN〇3の混合酸)、 碰 (HNO 3)、 « (HC 1 )、 硫酸 (H2 S 04) などの酸に浸漬したり、 H2、 N2、 A rなどを含む非酸 化性雰囲気中あるいは減圧中で加熱ァニ一ルする、 あるいはこれらを複数組み合わせて行う、 などの処理を施すことにより基板表面に形成される単結晶薄膜の結晶性の改善をはかることが 可能であり有効となり得る。
なお、 上記の窒化アルミニウムを主成分とする焼結体の表面状態及び炭化珪素、 窒化珪素、 窒化ガリウム、 酸化亜鉛、 酸化ベリリウムなどの六方晶系及び酸化アルミニウムなどの三方晶 系あるいは六方晶系として分類できる結晶構造を有する材料を主成分とする焼結体の表面状態 とその上に形成される窒化ガリウム、 窒化インジウム、 窒化アルミニウムのうちから選ばれた 少なくとも 1種以上を主成分とする単結晶薄膜の結晶性及び単結晶、 無定形、 多結晶、 配向性 多結晶など各種結晶状態の薄膜の表面状態との関係は、 これら焼結体以外の例えぱ谢匕ジルコ 二ゥム、 酸化マグネシウム、 アルミン酸マグネシウム、 酸化チタン、 チタン酸バリウム、 チタ
ン酸ジルコン酸鉛、 酸化イットリウムなどの希土 素酸化物、 酸化トリウム、 各種フェライ ト、 ムライト、 フォルステライト、 ステアタイト、 結晶化ガラス、 など各種セラミック材料を 主成分とする焼結体を用いた場合であってもその表面状態とその上に形成される窒化ガリウム、 窒化インジウム、 窒化アルミニウムのうちから選ばれた少なくとも 1種以上を主成分とする単 結晶薄膜の結晶性及び単結晶、 無定形、 多結晶、 配向性多結晶など各種結晶状態の薄膜の表面 状態との関係においても同様の傾向を有する。
本願発明者は、 基板として窒化アルミニウムを主成分とする焼結体を用いる場合可視光及び
/又は波長 2 0 0 nm〜3 8 0 nmの範囲の紫外光における光透過率と基板に形成される窒化 ガリウム、 窒化インジウム、 窒化アルミニウムのうちから選ばれた少なくとも 1種以上を主成 分とする単結晶薄膜の結晶性とは相関があることを示した。 さらに光 ¾ii率が ぃ場合の利点 として窒化アルミニウムを主成分とする焼結体からなる基板に形成される発光 、 あるいは 窒化アルミニウムを主成分とする焼結体からなる基板を用いて窒化ガリゥム、窒化ィンジゥム、 窒化アルミニウムのうちから選ばれた少なくとも 1種以上を主成分とする単結晶薄膜を形成し た基板に形成される発光素子からの光を基板で吸収する割合が小さくでき素子の外部に放出さ れる光の割合を高めることができるので発光素子の発光効率を高めることができる。 上記のよ うな特徴や利点を有する窒化アルミニウムを主成分とする焼結体からなる基板の光翻率を高 めるためには焼結体の化学組成ゃ微構造などの焼結体そのものの特性を改善する以外に基板の 厚みを薄くすることも有効である。 基板の厚みが 8. Omm以下であれば波長 2 0 0 nm〜8 0 0 nmの範囲の光に対して ¾¾i性を謙し得る。 ¾1性を纖できるということは窒化ァ ルミ二ゥムを主成分とする焼結体からなる基板の厚みが 8. 0 mmであつても 過率が 1 % 以上であるということを意味する。 窒化アルミニウムを主成分とする焼結体からなる基板の厚 みが 0. 5 mmのものを用いて測定した時の光透過率が例えば波長 2 0 0 nm〜 8 0 0 nmの 範囲の光において 6 0〜8 0 %の範囲の髙ぃ光 ¾li率を有するものでも基板の厚みが厚くなれ ば光 ¾ 率は減少していく。 基板の厚みが 0. 5mmのものを用いて測定した時の波長 2 0 0 nm〜 8 0 0 nmの範囲の光における光 ¾ 率が例えば 8 0 %の基板の場合その厚みが 8. 0 mmであっても波長 2 0 0 nm〜8 0 0 nmの範囲の光において光 ¾ii率は 1 %以上である。 基板の厚みが 5. 0 mm以下であれば ¾¾ 率は 5 %以上のものが得られる。基板の厚みが 2. 5 mm以下であれば 率は 1 0 %以上のものが得られる。 さらに基板の厚みが 1 . Omm 以下であれば光 ¾ί§率は 6 0 %以上のものが得られる。 基板の厚みが 0. 2 mm以下と薄くな れば光 ¾i率は 9 0 %以上のものが得られる。 基板の厚みが 0. 0 5 mm以下の場合 率 は 9 5 %以上のものが得られる。 また基板の厚みが 0. 5 mmのものを用いて測定した時の波 長 2 0 0 nm〜 8 0 0 nmの範囲の光に対する光透過率が例えば 1 . 0 %の基板の場合その厚 みが 0. 2mmと薄くなれば光 ¾ 率 1 0 %以上のものが得られる。 基板の厚みが 0. l mm 以下の場合光透過率は 2 0 %以上のものが得られる。 また基板の厚みが 0. 0 5 mm以下の場 合光 ¾1率は 4 0 %以上のものが得られる。 このように波長 2 0 0 nm〜8 0 0 nmの範囲の 光において 6 0 %以上の高い光 ¾i率を有する窒化アルミニウムを主成分とする焼結体からな る基板において厚み 1 . O mm以下で《S板の厚みにあまり影響されず高い ¾¾1性を有し、 0. 2mm以下の厚みでは 9 0 %以上殆ど透明に近い光¾1率となる。 実質的に 1 0 0 %に近 い光 ¾1率を有するものも得られる。 通常基板の厚みは薄いほど避過率は高まる傾向を有す るが機械的強度が小さくなるので基板に窒化ガリウム、 窒化インジウム、 窒化アルミニウムの うちから選ばれた少なくとも 1種以上を主成分とする単結晶薄膜を形成する場合の作業時にク ラックや欠けが生じ始めるという欠点があるので基板の厚みは 0. 0 l mm以上であることが 好ましく、 0. 0 2 mm以上であることがより好ましく、 0. 0 5 mm以上であることがさら に好ましい。 上記のように本発明による窒化アルミニウムを主成分とする焼結体からなる基板
を窒化ガリウム、 窒化インジウム、 窒化アルミニウムのうちから選ばれた少なくとも 1種以上 を主成分とする薄膜を形成するための基板として用いる場合 性の観点からみて (すなわ ち本発明による窒化アルミニウムを主成分とする焼結体からなる基板に発光軒を形成した時 の優位性) 基板の厚みは 8mm以下であることが好ましく、 5. 0mm以下であることがより 好ましい。 また基板の厚みは 2. 5 mm以下であることがさらに好ましぐ 基板の厚みは 1. 0 mm以下であることが最も好ましい。 このような厚みの基板において機械的強度の観点から は 0. 0 l mm以上であることが好ましく、 0. 0 2mm以上であることがより好ましく、 0. 0 5 mm以上であることがさらに好ましい。
本発明による窒化アルミニウムを主成分とする焼結体からなる薄膜形成用基板には導通ビア を設けることができる。 導通ピアが設けられた窒化アルミニウムを主成分とする焼結体からな る基板は単結晶薄膜を形成するためだけでなく各種結晶状態の薄膜形成用基板としても同等に 用いることができる。 導通ビアは通常窒化アルミニウムを主成分とする焼結体からなる薄膜形 成用基板の内部に設けられる。 該導通ビアは通常基板の上下表面 (すなわち単結晶薄膜、 ある いは無定形薄膜、 あるいは多結晶薄膜、 あるいは配向性多結晶薄膜などの各種結晶状態の薄膜 が形成される側の基板面と、 その反対側の基板面) を電気的に接続するために形成される。 該 導通ビアは例えば窒化アルミニウムを主成分とするグリーンシートなどのセラミック粉末成形 体にスルーホール (貫通孔) を形成してそこにあらかじめ金属などを主成分とする導電性粉末 を入れ同時誠する、 スルーホールが形成された窒化アルミ二ゥムを主成分とする焼結体から なる基板を溶融金属に含浸し該スル一ホール部分に溶融金属導入する、 基板のスルーホールに 導電性ペーストを導入し加熱あるいは舰する、 などの方法で容易に形成できる。 上記導通ビ ァは窒化アルミニウムを主成分とする焼結体の内部だけでなぐ 炭化珪素、 窒化珪素、 窒化ガ リウム、 酸化亜鉛、 酸化ベリリウムなどの六方晶結晶系及び ¾化アルミニウムなどの三方晶結 晶系あるいは六方晶系として分類できる結晶構造を有する各種セラミック材料を主成分とする 焼結体、 及びその他各種セラミツク材料からなる焼結体にも形成することができる。
図 3には内部に導通ビア 3 (斜線で示された部分) を有する窒化アルミニウムを主成分とす る焼結体、 及び炭化珪素、 窒化珪素、 窒化ガリウム、 酸化亜鉛、 酸化ベリリウムなどの六方晶 結晶系及び 匕アルミニウムなどの三方晶結晶系あるいは六方晶系として分類できる結晶構造 を有する各種セラミック材料を主成分とする焼結体、 及びその他各種セラミック材料を主成分 とする焼結体からなる基板 9の様子が例示されている。 該導通ビア 3を有する基板 9は薄膜形 成用基板として用いることができる。
また、 該薄膜形成用基板の上には窒化ガリウム、 窒化インジウム、 窒化アルミニウムのうち から選ばれた少なくとも 1種以上を主成分とする単結晶、 無定形、 多結晶、 配向性多結晶のう ちから選ばれる少なくともいずれかの結晶状態を有する薄膜が形成できる。
図 7には導通ビア 3が形成された窒化アルミニウムを主成分とする焼結体、 及び炭化珪素、 窒化珪素、 窒化ガリウム、 酸化亜鉛、 酸化ベリリウムなどの六方晶結晶系及び 匕アルミニゥ ムなどの三方晶結晶系あるいは六方晶系として分類できる結晶構造を有する各種セラミック材 料を主成分とする焼結体、 及びその他各種セラミック材料を主成分とする焼結体からなる基板 9の上に窒化ガリゥム、 窒化ィンジゥム、 窒化アルミニウムのうちから選ばれた少なくとも 1 種以上を主成分とする単結晶、 無定形、 多結晶、 配向性多結晶のうちから選ばれる少なくとも いずれかの結晶状態を有する薄膜が形成された薄膜基板の 1例が示されている。
図 7において、 導通ビア 3が形成された窒化アルミニウムを主成分とする焼結体、 及び炭化 珪素、 窒化珪素、 窒化ガリウム、 酸化亜鉛、 酸化ベリリウムなどの六方晶結晶系及ぴ谢匕アル ミニゥムなどの三方晶結晶系あるいは六方晶系として分類できる結晶構造を有する各種セラミ ック材料を主成分とする焼結体、 及びその他各種セラミック材料を主成分とする焼結体からな
る基板 9が薄膜形成用基板として用いられ、 該薄膜形成用基板には窒化ガリウム、 窒化インジ ゥム、 窒化アルミニウムのうちから選ばれた少なくとも 1種以上を主成分とする単結晶、 無定 形、 多結晶、 配向性多結晶のうちから選ばれる少なくともいずれかの結晶状態を有する薄膜 5 が形成され該基板 9 mmrn 5により薄膜基板 iが構成されている。
このような導通ビアが形成された窒化アルミニゥムを主成分とする焼結体、 及び炭化珪素、 窒化珪素、 窒化ガリウム、 酸化亜鉛、 酸化ベリリウムあるいは酸化アルミニウムなどの各種セ ラミック材料を主成分とする焼結体、 及びその他各種セラミック材料を主成分とする能結体に は窒化ガリウム、 窒化インジウム、 窒化アルミニウムのうちから選ばれた少なくとも 1種以上 を主成分とする単結晶、 無定形、 多結晶、 配向性多結晶など各種結晶状態の薄膜が形成できる が、 導通ビアにも直接上記窒化ガリウム、 窒化インジウム、 窒化アルミニウムのうちから選ば れた少なくとも 1種以上を主成分とする単結晶、 無定形、 多結晶、 配向性多結晶など各種結晶 状態の薄膜が形成できる。
図 7で例示された導通ビアを有する薄膜基板に形成されている薄膜 5はェピタキシャル成長 した単結晶薄膜として形成できるが該薄膜 5はすべてが単結晶でなくその他に無定形、多結晶、 配向性多結晶のうちから選ばれる少なくともいずれかの結晶状態を有する薄膜も形成できる。 また単一層としてだけでなく 2層以上の多層化された薄 成のものも形成できる。すなわち、 窒化ガリウム、 窒化インジウム、 窒化アルミニウムのうちから選ばれた少なくとも 1種以上を 主成分とする単結晶、 無定形、 多結晶、 配向性多結晶のうちから選ばれる少なくともいずれか の結晶状態を有する薄膜を形成しその上にさらに窒化ガリウム、 窒化インジウム、 窒化アルミ ニゥムのうちから選ばれた少なくとも 1種以上を主成分とするェピタキシャル成長した単結晶 薄膜が形成された 2層構成の薄膜が形成できる。 このような構成で形成された単結晶薄膜の結 晶性 板に直接形成された単結晶薄膜よりも優れたものが得られ易いので好ましい。 また例 えば、 窒化ガリウム、 窒化インジウム、 窒化アルミニウムのうちから選ばれた少なくとも 1種 以上を主成分とする単結晶、 無定形、 多結晶、 配向性多結晶のうちから選ばれる少なくともい ずれかの結晶状態を有する薄膜を形成でき、 単結晶を含まない構成の薄膜も形成し得る。 また 上記の構成に限らず薄膜 5は窒化ガリウム、 窒化インジウム、 窒化アルミニウムのうちから選 ばれた少なくとも 1種以上を主成分とする 2層以上から構成される薄膜として形成できる。 2 層以上に形成された薄膜 5は各層〖こおいて単結晶を含め無定形、 多結晶、 配向性多結晶などの 結晶状態、 組成、 あるいは厚みなどそれぞれ異なる状態で形成でき、 本発明において 2層以上 の薄膜層のすべてが単結晶でない薄膜構成であっても形成出来る。 2層以上の薄膜層で構成さ れている薄 USすべてが窒化ガリウム、 窒化インジウム、 窒化アルミニウムのうちから選ばれ た少なくとも 1種以上を主成分とする単結晶薄膜からなるものも形成出来る。 本発明による薄 膜基板を発光素子、 あるいはフィールドェミッションディスプレイ、 あるいは回路基板、 ある いは光導波路など、 各種電子素子及び電 品の作製用として用いる場合など、 薄膜基板表面 に形成される薄膜は通常ェピタキシャル成長した単結晶であることが好ましい。
図 7で例示された薄膜基板 7にはさらに窒化ガリウム、 窒化インジウム、 窒化アルミニウム のうちから選ばれた少なくとも 1種以上を主成分とする単結晶、 無定形、 多結晶、 配向性多結 晶のうちから選ばれる少なくともいずれかの結晶状態を有する薄膜が形成できる。 その場合該 薄膜基板は薄膜形成用基板としての機能を果たすことになる。
図 8には薄膜を 2層形成した導通ビアを有する薄膜基板の 1例を示す。 図 8において、 薄膜 形成用基板として導通ピア 3が形成された窒化アルミニウムを主成分とする焼結体、 及び炭化 珪素、 窒化珪素、 窒化ガリウム、 酸化亜鉛、 酸化ベリリウムなどの六方晶結晶系及び谶化アル ミニゥムなどの三方晶結晶系あるいは六方晶系として分類できる結晶構造を有する各種セラミ ック材料を主成分とする焼結体、 及びその他各種セラミック材料を主成分とする焼結体からな
る基板 9が用いられ 該基板には窒化ガリウム、 窒化インジウム、 窒化アルミニウムのうちか ら選ばれた少なくとも 1種以上を主成分とする単結晶、 無定形、 多結晶、 配向性多結晶のうち から選ばれる少なくともレゝずれかの結晶状態を有する薄膜 5及び 膜 8が形成され導通ビアを 有する薄膜基板 7が形成されている。
図 8で例示された薄膜基板に形成されている薄膜 5及び 膜 8はェピタキシャル成長した単 結晶薄膜として形成できるが該薄膜すベてが単結晶でなくその他に無定形、 多結晶、 配向性多 結晶のうちから選ばれる少なくともいずれかの結晶状態を有する薄膜も形成できる。 例えば、 窒化ガリウム、 窒化インジウム、 窒化アルミニウムのうちから選ばれた少なくとも 1種以上を 主成分とする単結晶、 無定形、 多結晶、 配向性多結晶など各種結晶状態を有する薄膜を形成で き、 単結晶を含まない構成の薄膜も形成し得る。 また例えば、 薄膜 5として窒化ガリウム、 窒 化ィンジゥム、 窒化アルミニウムのうちから選ばれた少なくとも 1種以上を主成分とする単結 晶、 無定形、 多結晶、 配向性多結晶のうちから選ばれる少なくともいずれかの結晶状態を有す るものを形成し、 その上に薄膜 8として窒化ガリウム、 窒化インジウム、 窒化アルミニウムの うちから選ばれた少なくとも 1種以上を主成分とするェピタキシャル成長した単結晶薄膜を形 成すれば該薄膜 8の結晶性は基板 9に直接形成した単結晶薄膜の結晶性よりも向上し易いので 好ましい。 このような薄膨冓成の薄膜基板は例えば発光軒、 あるいはフィールドエミッショ ン、 あるいは回路基板、 あるいは光導波路など、 各種電子素子及び電 品の作製用に使用し ていく上で好ましい。 また上記の構成に限らす^膜 5及び 膜 8をそれぞれ 2層以上に多層化 し窒化ガリウム、 窒化インジウム、 窒化アルミニウムのうちから選ばれた少なくとも 1種以上 を主成分とする合計 3層以上の薄膜で構成することもできる。 それぞれ 2層以上に形成された 薄膜 5及び薄膜 8は各層において単結晶を含め無定形、多結晶、配向性多結晶などの結晶状態、 組成、 あるいは厚みなどそれぞれ異なる状態で形成でき、 本発明において薄編のすべてが単 結晶でない窒化ガリウム、 窒化インジウム、 窒化アルミニウムのうちから選ばれた少なくとも 1種以上を主成分とする薄膜の構成であっても形成出来る。
図 8に例示された薄膜層 2層で構成された薄膜基板だけでなく薄膜層が 3層以上形成された 薄膜基板であっても該薄麵すべてが窒化ガリウム、 窒化インジウム、 窒化アルミニウムのう ちから選ばれた少なくとも 1種以上を主成分とする単結晶薄膜からなるものも形成出来る。 図 8で例示された薄膜基板 7にはさらに窒化ガリウム、 窒化インジウム、 窒化アルミニウム のうちから選ばれた少なくとも 1種以上を主成分とする単結晶、 無定形、 多結晶、 配向性多結 晶のうちから選ばれる少なくともいずれかの結晶状態を有する薄膜が形成できる。 その場合該 薄膜基板は薄膜形成用基板としての機能を果たすことになる。
また、 図 8に例示された薄膜基板において導通ビア 3には上記窒化ガリゥム、 窒化ィンジゥ ム、窒化アルミニウムのうちから選ばれた少なくとも 1種以上を主成分とする単結晶、無定形、 多結晶、 配向性多結晶など各種結晶状態を有する薄膜 5が直接形成し得る。
図 8に例示された薄膜 2層あるいは 3層以上が形成された薄膜基板を発光素子、 あるいはフ ィールドエミッションディスプレイ、 あるいは回 板、 あるいは光導波路など、 各種電子素 子及び電^¾品の作翻として用いる場合など、 薄膜基板表面に形成される薄膜 常ェピタ キシャル成長した単結晶であることが好ましい。
本発明による導通ビアを有する薄膜基板とは、 導通ビアを有する窒化アルミニウムを主成分 とする焼結体、 及び炭化珪素、 窒化珪素、 窒化ガリウム、 酸化亜鉛、 酸化ベリリウムなどの六 方晶結晶系及び酸化アルミニウムなどの三方晶結晶系あるいは六方晶系として分類できる結晶 構造を有する各種セラミック材料を主成分とする焼結体、 及びその他各種セラミック材料を主 成分とする焼結体からなる基板に窒化ガリウム、 窒化インジウム、 窒化アルミニウムのうちか ら選ばれた少なくとも 1種以上を主成分とする薄膜が形成された基板である。
本発明による導通ビアを有する薄膜基板に形成される薄膜として、 窒化ガリウム、 窒化イン ジゥム、 窒化アルミニウムのうちから選ばれた少なくとも 1種以上を主成分とする単結晶、 無 定形、 多結晶、 配向性多結晶のうちから選ばれる少なくともいずれかの結晶状態を有する薄膜 をあらかじめ形成し、 要すればさらにその上に窒化ガリウム、 窒化インジウム、 窒化アルミ二 ゥムのうちから選ばれた少なくとも 1種以上を主成分とする単結晶薄膜を形成した構成とする ことで該単結晶薄膜の結晶はよりすぐれたものが得られ易いので好ましい。
図 3、 図 7及び図 8において示された導通ビアを有する基板の形状は円盤状であるが本発明 において使用できる導通ビアを内部に形成した基板の形状は円盤状だけでなく正方形、長方形、 あるいはその他多角形状など任意の形状のものが使用できる。 又、 図 3、 図 7、 図 8において 導通ビアは 1個しか示されていないが基板中には適宜複数個の導通ピケを設けることができる。 例えば窒化ガリウム、 窒化インジウム、 窒化アルミニウムのうちから選ばれた少なくとも 1種 以上を主成分とする単結晶薄膜を構成成分とする発光素子 1個の大きさは 0. 0 5 - 1 0. 0 mm程度であるので直径 2 5. 4 mmの円盤状基板では切断しろを考慮して 2〜: L 0 0 0 0個 程度の導通ビアを設けることができる。 この導通ビアを有する基板上に発光素子を形成 光 素子を 1個ずつ基板から切り離すことで^?の上下面に P N電極配置を有する発光^?が形成 できる。 このような上下面配置の電極が形成され発光素子はサファイア基板を用いた場合のよ うに素子の片面にだけ P N電極が形成されたものと違い電極を形成するために素子の一部をェ ツチングする必要がなぐ 基板から切り離すだけでそのまま素子が形成できるのでエッチング 中に生じやすい素子のダメージの恐れがなくまた素子の製造コス卜の低減化がはかれるので好 ましい。 また、 本発明による導通ビアを形成した基板を用いることで P Nの電極を素子の片面 だけでなく素子の上下面に電極を配置した素子が設計できるので設計に自由度も向上するとい う特徴ちある。
導通ビアに用いられる導電性材料は窒化アルミニウムを主成分とする焼結体、及び炭化珪素、 窒化珪素、 窒化ガリウム、 酸化 \ 酸化ベリリウムなどの六方晶結晶系及び 化アルミニゥ ムなどの三方晶結晶系あるいは六方晶系として分類できる結晶構造を有する各種セラミック材 料を主成分とする焼結体、 及びその他各種セラミック材料を主成分とする焼結体と一体化し易 くさらに窒化ガリゥム、 窒化ィンジゥム、 窒化アルミニウムのうちから選ばれた少なくとも 1 種以上を主成分とする薄膜との接合性が高く該薄膜を導通ビアに対して形成したときにクラッ クや導通ビアとの界面における剥離などの不具合が生じることがなくさらに要すれば電気的に も薄膜との接続性が高いものであればどのような材料でも用いることができる。 このような材 料は例えば金、 銀、 銅、 アルミニウム、 鉄、 コノルト、 ニッケル、 ルテニウム、 ロジウム、 パ ラジウム、 オスミウム、 イリジウム、 白金、 タングステン、 モリブデン、 クロム、 チタン、 窒 化チタン及び窒化ジルコニウムなどのうちから選ばれた少なくとも 1種以上を主成分とするも のである。 このような材料からなる導通ビアは上記窒化アルミ二ゥムを主成分とする焼結体、 及び炭化珪素、 窒化珪素、 窒化ガリウム、 酸化亜鉛、 酸化ベリリウムなどの六方晶結晶系及び 酸化アルミニウムなどの三方晶結晶系あるいは六方晶系として分類できる結晶構造を有する各 種セラミック材料を主成分とする焼結体、 及びその他各種セラミック材料を主成分とする焼結 体からなる基板材料と一体化し易いだけでなぐ 基板に形成される薄膜との接合性が高く導通 ビアには直接窒化ガリゥム、 窒化ィンジゥム、 窒化アルミニウムのうちから選ばれた少なくと も 1種以上を主成分とする薄膜が形成できる。 また、 上記材料からなる導通ピアは電気的にも 窒化ガリウム、 窒化インジウム、 窒化アルミニウムのうちから選ばれた少なくとも 1種以上を 主成分とする薄膜との接続性が高い。 通常上記材料からなる導通ビアに直接形成される単結晶 薄膜は該単結晶薄膜のミラー指数 (0 0 2 ) の格子面の X線回折ロッキングカープの半値幅 3 6 0 0秒以下の結晶性のものが得られ易い。 またビアの材料として上記の主成分に窒化アルミ
二ゥム、炭化珪素、窒化珪素、窒化ガリウム、酸化 »、酸化ベリリウム、酸化アルミニウム、 希土類沅素化合物、 アルカリ土類金属化合物などのうちから選ばれた少なくとも 1種以上の成 分を加えたものは窒化アルミニウム焼結体を始めとする基板材料とより一体化し易いだけでな く、 基板に形成される薄膜との接合性がさらに高く導通ビアには直接窒化ガリウム、 窒化イン ジゥム、 窒化アルミニウムのうちから選ばれた少なくとも 1種以上を主成分とする単結晶薄膜 が形成できその結晶性はミラ一指数 ( 0 0 2) の格子面の X線回折ロッキングカーブの半値幅 1 0 0 0秒以下のものが得られ易い。 また、 上記材料からなる導通ビアは電気的にも窒化ガリ ゥム、 窒化インジウム、 窒化アルミニウムのうちから選ばれた少なくとも 1種以上を主成分と する薄膜との接続性も高い。 上記の導通ビアの材料の中でモリブデン、 タングステン、 銅、 窒 化チタン、 窒化ジルコニウムの中から選ばれた少なくとも 1種以上を主成分とするもの «S板 の窒化アルミニウム焼結体を始めとする材料とより一体化し易いだけでなぐ 基板に形成され る薄膜を介してあるいは導通ビアに直接窒化ガリウム、 窒化インジウム、 窒化アルミニウムの うちから選ばれた少なくとも 1種以上を主成分とする単結晶薄膜が形成できその結晶性はミラ —指数 (0 0 2) の格子面の X線回折ロッキングカーブの半値幅 3 0 0秒以下のものが得られ 易いのでより好ましい。 また、 モリブデン、 タングステン、 銅、 窒化チタン、 窒化ジルコニゥ ムの中から選ばれた少なくとも 1種以上の成分を主成分としさらに窒化アルミニウム、 酸化ァ ルミ二ゥム、 希土 素化合物、 アルカリ土類金属化合物のうちから選ばれた少なくとも 1種 以上の成分を含むもの 板の窒化アルミニウム焼結体を始めとする材料とより一体化し易い だけでなぐ 基板に形成される薄膜を介してあるいは導通ビアに直接窒化ガリウム、 窒化イン ジゥム、 窒化アルミニウムのうちから選ばれた少なくとも 1種以上を主成分とする単結晶薄膜 が形成できその結晶性はミラ一指数 (0 0 2 ) の格子面の X線回折ロッキングカーブの半値幅
2 4 0秒以下のものが得られ易いのでさらに好ましい。 この導通ビアを形成する材料に含まれ る窒化アルミニウム、 酸化アルミニウム、 希土 素化合物、 アルカリ土類金属化合物のうち 力 選ばれた少なくとも 1種以上の成分の含有量は合計で 3 0重量%以下であることが好まし く上記材料により構成される導通ビアの室温における抵抗率が 1 X 1 0— 3 Ω · c m以下となる。
3 0重量%より多いと上記材料により構成される導通ビアの室温における抵抗率が 1 X 1 0一3 Ω · c mより高いものとなり易いので好ましくない。 より好ましレ含有量は 1 0重量%以下で あり、 上記材料により構成される導通ビアの室温における抵抗率は 1 X 1 0— 4Ω · c m以下と なり易いのでより好ましい。 さらに好ましい含有量は 5重量%以下であり、 上記材料により構 成される導通ビアの室温における抵抗率は 1 X 1 0— 5 Ω · c m以下となり易いのでより好まし レ^ なお、 上記導通ビアの主成分として用いられるモリブデン及びタングステンは金属だけで なく炭化物や窒化物としても用いることができる。 このように導通ビアの材料の中でモリブデ ン、 タングステン、 銅、 窒化チタン、 窒化ジルコニウムの中から選ばれた少なくとも 1種以上 を主成分とするものや、 モリブデン、 タングステン、 銅、 窒化チタン、 窒化ジルコニウムの中 から選ばれた少なくとも 1種以上の成分を主成分としさらに窒化アルミニウム、 酸化アルミ二 ゥム、 希土 素化合物、 アル力リ土類金属化合物のうちから選ばれた少なくとも 1種以上の 成分を含むものが基板に形成される薄膜を介してあるいは導通ビアに直接形成される窒化ガリ ゥム、 窒化インジウム、 窒化アルミニウムのうちから選ばれた少なくとも 1種以上を主成分と する単結晶薄膜が い結晶性を有する理由は必ずしも明確でない。 本願発明者はおそらく上記 モリブデン、 タングステン、 銅、 窒化チタン、 窒化ジルコニウムの中から選ばれた少なくとも 1種以上を主成分とする材料の熱膨張率は比較的小さく窒化アルミニウムを主成分とする焼結 体に近くまた窒化ガリウム、 窒化インジウム、 窒化アルミニウムのうちから選ばれた少なくと も 1種以上を主成分とする単結晶薄膜の熱膨張率に近いため、 あるいは銅の場合比較的軟質で あるためェピタキシャル成長した該単結晶薄膜に大きなひずみや応力が生じにくいと推測して
おり、 また導通ビアに窒化ガリウム、 窒化インジウム、 窒化アルミニウムのうちから選ばれた 少なくとも 1種以上を主成分とする薄膜形成されるとき窒化アルミニウムを主成分とする焼結 体が導通ビア付近で該薄膜の単結晶化が阻害されないように働くのではないかと推測している。 なお、上記導通ビアに用いられる希土類 J£素化合物とは Sc、 Y、 La、 Ce、 Pr、 Nd、 Sm、 Eu、 Gd、 Dy、 Ho、 Er、 Yb、 Luなどの希土類 、 及び Sc 203、 Y203、 La203、 Ce02、 P r 6011¾ Nd203、 Sm2〇3、 Eu2〇3、 Gd203、 Dy2〇3、 Ho 2〇3、 Er203、 Yb203、 Lu2〇3、 などの希土類 素酸化物あるいはその他 S c、 Y、 L a、 Ce、 Pr、 Nd、 Sm、 Eu、 Gd、 Dy、 Ho、 Er、 Yb、 Lu、 などを含む炭酸 塩、 «塩、 硫酸塩、 塩化物などの無機希土類化合物、 酢酸塩、 «塩、 クェン酸塩などの有 機希土類化合物などの各種希土^ ΰ素化合物などであり、 さらに L ηを希土類 素として表し たときガーネット型結晶構造の 3Ln2〇3 · 5A12〇3 (例えば 3Υ2〇3· 5Α 1203、 3D y203 - 5 A 1203, 3Ho203 · 5 A 1203、 3 E r 203 · 5 A 1203、 3 Yb203 - 5A 1203、 など)、 ぺロブスカイト型結晶構造の Ln2〇3 · A 1203 (例えば YA 1〇3、 LaA 103、 PrAl〇3、 NdA103、 SmA 103、 EuA103、 GdA103、 DyA 103 HoA103、 ErA103、 YbA103、 など)、 単斜晶結晶構造 2 L n203 · A 1203 (例 えば 2Y203 · Al 203、 2 Sm203 · A 12〇3、 2Eu203 · A 12〇3、 2Gd2〇3 · A 1 203、 2Dy203 · A 12〇3、 2Ho2〇3 · A 1203、 2 E r 203 · A 12〇3、 2Yb2〇3 · A 1203、 など) などの希土類 素を含む複合酸化物、 などである。 また上記導通ビアに用い られるアルカリ土類金属化合物とは Mg、 Ca、 Sr、 B aなどのアルカリ土類金属、 及び M g〇、 C a 0、 S r 0、 B a Oなどのアル力リ土類金属酸化物やその他 M g、 C a、 S r、 B aなどを含む炭酸塩、 硝酸塩、 硫酸塩、 塩化物などの無機アルカリ土類金属化合物、 酢酸塩、 據酸塩、 クェン酸塩などの有機アル力リ土類金属化合物などの各種アル力リ土類金属化合物で あり、さらに八6をァルカリ土類金属として表したとき3八6〇'八1203、 Ae ·Α 1203、 Ae · 2A 1203、 Ae · 6 A 12〇3などのアルカリ土類金属を含む複合酸化物、 である。 本発明において、 導通ビアに用いられる前記モリブデン、 タングステン、 銅、 窒化チタン、 窒化ジルコニウムの中から選ばれた少なくとも 1種以上の成分を主成分としさらに窒化アルミ 二ゥム、 酸化アルミニウム、 希土類 素化合物、 アルカリ土類金属化合物のうちから選ばれた 少なくとも 1種以上の成分を含むもの以外の各材料においてもその室温における抵抗率は 1 X 10— 3Ω · cm以下程度の導電性があれば好ましく室温における抵抗率が 1 X 10_4Ω · cm 以下であることがより好ましくまた室温における抵抗率が 1 X 10— 5Ω · cm以下であること が'さらに好-ましい。
本発明において上記導通ビアが形成される基板が窒化アルミニウムを主成分とする焼結体で ある場合焼結助剤、 焼成 低減化剤、 黒色化剤、 不可避不純物、 ALONなどのうち少なく とも 1種以上を含むものであっても良いし、 高純度化され結晶相として A 1Nを 95%以上含 むものあるいは A 1 Nを 98 %以上含むものあるいは実質的に A 1 N単一相からなるものであ つてもよく、 いずれの窒化アルミニウムを主成分とする焼結体も用いることができる。 窒化ァ ルミ二ゥムを主成分とする焼結体に形成される導通ビアの材料がモリブデン、 タングステン、 銅、 窒化チタン、 窒化ジルコニウムの中から選ばれた少なくとも 1種以上の成分を主成分とす るもの、 あるいはモリブデン、 タングステン、 銅、 窒化チタン、 窒化ジルコニウムの中から選 ばれた少なくとも 1種以上の成分を主成分としさらに窒化アルミニウム、 酸化アルミニウム、 希土 素化合物、 アル力リ土類金属化合物のうちから選ばれた少なくとも 1種以上の成分を 含むものを用いれば窒化アルミニウムを主成分とする焼結体を高 «化し光 ¾ 性を高めるた めに行われる高温で長時間の熱処理中にも揮散されることが殆どないので導通ビアを有する基 板が容易に製造可能となり、 高熱伝導率で光透過性を有し熱膨張率が窒化ガリウム、 窒化イン
ジゥム、 窒化アルミニウムのうちから選ばれた少なくとも 1種以上を主成分とする単結晶薄膜 に近くさらに基板の上下面を電気的に接続できる優れた基板が低コストで提供でき産業界に与 える影響はさらに大きい。
本発明において導通ビアの大きさ及び形状は ¾ s定でき、 どのような大きさのものであつ ても窒化ガリウム、 窒化インジウム、 窒化アルミニウムを主成分とする薄膜が直接形成し得要 すれば単結晶薄膜が形成し得るものであればよい。 又形状もどのようなものでも選択でき窒化 ガリウム、 窒化インジウム、 窒化アルミニウムを主成分とする薄膜が直接形成し得要すれば単 結晶薄膜が形成し得るものであればよい。 通常導通ビアの大きさは 2 5 0 mより大きいもの であっても該導通ビアに窒化ガリウム、 窒化インジウム、 窒化アルミニウムのうちから選ばれ た少なくとも 1種以上を主成分とする単結晶薄膜が直接形成し得る。 すなわち導通ビアの大き さが 2 5 O ^mより大きい場合でも導通ビアに直接形成される窒化ガリウム、窒化インジウム、 窒化アルミニウムのうちから選ばれた少なくとも 1種以上を主成分とする単結晶薄膜として該 単結晶博膜のミラ一指数 ( 0 0 2 ) の格子面の X線回折ロッキングカーブの半値幅 3 6 0 0秒 以下の結晶性のものが得られ易い。 例えば導通ビアの大きさが' 5 0 0 mといった比較的大き いものであっても該導通ビアに形成される窒化ガリウム、 窒化インジウム、 窒化アルミニウム のうちから選ばれた少なくとも 1種以上を主成分とする単結晶薄膜として該単結晶博膜のミラ 一指数 (0 0 2 ) の格子面の X線回折ロッキングカーブの半値幅 3 6 0 0秒以下の結晶性のも のが得られる。 通常導通ピアの大きさは 2 5 0 m以下であることが好ましい。 導通ビアの大 きさが 2 5 0 m以下であれば導通ビアに直接形成された窒化ガリウム、 窒化インジウム、 窒 化アルミニウムのうちから選ばれた少なくとも 1種以上を主成分とする単結晶薄膜のミラ一指 数 (0 0 2 ) の格子面の X線回折ロッキングカーブの半値幅が 3 0 0秒以下と結晶性に優れた ものが得られ易い。 好ましくい導通ビアの大きさは 1 0 0 m以下である。 導通ビアの大きさ が 1 0 0〃m以下であれば導通ビアに直接形成された窒化ガリウム、 窒化インジウム、 窒化ァ ルミニゥムのうちから選ばれた少なくとも 1種以上を主成分とする単結晶薄膜のミラ一指数 ( 0 0 2 ) の格子面の X線回折ロッキングカーブの半値幅が 2 4 0秒以下とより結晶性に優れ たものが得られ易い。 さらに好ましくは 5 0 m以下である。 導通ビアの大きさが、 5 0 /xm以 下であれば導通ビアに直接形成された窒化ガリウム、 窒化インジウム、 窒化アルミニウムのう ちから選ばれた少なくとも 1種以上を主成分とする単結晶薄膜のミラー指数 ( 0 0 2 ) の格子 面の X線回折ロッキングカーブの半値幅が 2 0 0秒以下とさらに結晶性に優れたものが得られ 易い。 さらに好ましくは 2 5 m以下である。 導通ビアの大きさが 2 5 m以下であれば導通 ビアに直接形成された窒化ガリウム、 窒化インジウム、 窒化アルミニウムのうちから選ばれた 少なくとも 1種以上を主成分とする単結晶薄膜のミラー指数 ( 0 0 2 ) の格子面の X線回折口 ッキングカーブの半値幅が 1 5 0秒以下とさらに結晶性に優れたものが得られ易い。 導通ビア の大きさにより基板上に形成される窒化ガリウム、 窒化インジウム、 窒化アルミニウムのうち から選ばれた少なくとも 1種以上を主成分とする単結晶薄膜の結晶性に相違が生じる易いのは、 導通ビア〖堪板の主成分である窒化アルミニウムとは異なる材料であるためその大きさにより 基板上に形成される窒化ガリウム、 窒化インジウム、 窒化アルミニウムのうちから選ばれた少 なくとも 1種以上を主成分とする単結晶薄膜の成長時における核成長の方向を一定にする度合 いに違いが生じるためであろうと推測される。 なお、 本発明において導通ビアの大きさとは断 面の最大寸法で示す。 すなわち断面が直径 2 0 0 mの円形の場合導通ビアの大きさはそのま ま 2 0 0 mであり、 一辺 1 5 0 mの正方形の場合導通ビアの大きさは 2 1 2 mである。 また導通ビアの断面形状は任意のものが使用できるが加工性の点から断面が円形のものを用 いることが好ましくこのような形状であれば窒化ガリウム、 窒化インジウム、 窒化アルミニゥ ムのうちから選ばれた少なくとも 1種以上を主成分とする単結晶薄膜が形成し得る。
導通ビアを形成するために上記のように窒化アルミニゥムを主成分とするグリーンシートな どのセラミック粉末成形体にスルーホールを形成する方法として通常行われている二一ドルを 用いたパンチング法以外に例えば炭酸ガスレーザ一や YAGレーザーあるいはエキシマレーザ —などによるレーザ一加工法が微細な穴あけ加工法としては好ましい。 上記レーザー加工法は 焼成後の焼結体への穿孔にも適する。 レーザー加工法を用いることで 5 0 m以下、 l m程 度までの導通ビアが形成できる。 ダリ一ンシートを焼成することにより得られる窒化アルミ二 ゥムを主成分とする焼結体に形成された導通ビアの大きさが 5 0 zmからさらに小さくなり 1 mに近づくにつれ導通ビアに直接形成された窒化ガリウム、 窒化インジウム、 窒化アルミ二 ゥムのうちから選ばれた少なくとも 1種以上を主成分とする単結晶薄膜のミラー指数 (0 0 2) の格子面の X線回折ロッキングカーブの半値幅が窒化アルミニウムを主成分とする焼結体が本 来有していると思われる 1 5 0秒以下と結晶性に優れたものが得られ易くなり特に好ましい。 また、 本発明において導通ビアの形態として導電性材料がスルーホール内に密に充填された ものやスルーホールの側壁に導電性材料を形成したものなど各種形態のものが使用できる。 そ の中でスル一ホール内に導電性材料が緻密な状態で形成されたいわゆる充填ビアの形態のもの が好ましく、 窒化ガリウム、 窒化インジウム、 窒化アルミニウムのうちから選ばれた少なくと も 1種以上を主成分とする単結晶薄膜が容易に形成できる利点がある。
導通ビアを設けることで 電気的には «体である窒化アルミニウムを主成分とする « 体からなる薄膜形成用基板の表裏面を電気的に接続できるので、 軒の電極を上下面からとす ることができる。 導通ビアを設けない場合発光素子の電極 板上に形成された発光素子側だ けの面にしか設けられないが、 基板に導通ビアを形成することで発光素子の実装を行う場合の 自由度が高まり有利となる。
本発明者は各種金属、 合金、 金属窒化物、 金属炭化物、 金属珪化物などの材料を主成分とす る導電性を有する薄膜が形成された窒化アルミニウムを主成分とする焼結体について窒化ガリ ゥム、 窒化インジウム、 窒化アルミニウムのうちから選ばれた少なくとも 1種以上を主成分と する薄膜形成について検討を行なった。 その結果上記各種金属、 合金、 金属窒化物、 金属炭化 物、 金属珪化物などを主成分とする薄騰電性材料が形成された窒化アルミニウムを主成分と する焼結体は該薄騰電性材料が形成されていない窒化アルミニウムを主成分とする焼結体と 同等に薄膜形成用基板として用いることができることが明らかになつた。 このような薄 電 性材料は窒化アルミニウムを主成分とする焼結体との接合性が高く窒化ガリゥム、 窒化ィンジ ゥム、 窒化アルミニウムのうちから選ばれた少なくとも 1種以上を主成分とする薄膜との接合 性が高くさらに要すれば電気的な接続性が高いものあるいは光反射率の高いものであればどの ようなものでも用いることができる。 すなわち、 例えば金、 銀、 銅、 アルミニウム、 鉄、 コバ ル 1ヽ、 ニッケル、 ルテニウム、 ロジウム、 パラジウム、 オスミウム、 イリジウム、 白金、 タン タル、 モリブデン、 タングステン、 クロム、 チタン、 ニッケル一クロム合金、 窒化チタン、 窒 化ジルコニウム、 窒化タンタル、 などのうちから選ばれた少なくとも 1種以上を主成分とする 導電性材料を用いスパッタリング、 イオンプレーティング、 蒸着、 MO CVD (有機金属化学 気相 成長) 法、 MOVP E (有機金属気相ェピタキシャル成長) 法、 ハイドライド VP E (水素化物気相ェピタキシャル成長) 法、 クロライド VP E (塩化物餅目ェピタキシャル成長) 法などのハライド VP E (ハロゲン化物気相ェピタキシャル成長) 法、、 プラズマ CVD法、 そ の他の CVD (化学気相分解成長) 法、 MB E ( 線エピタキシー) 法、 あるいはエキシマ レーザーなどを用いたレーザーアブレーシ aン法、 P LD (パルスレーザ一デポジシヨン:パ ルスレーザー分解) 法などの方法により目的成分を含む有機化合物、 無機化合物、 窒化物など の各種化合物、 金属、 合金などからなる材料を原料とし本発明による窒化アルミニウムを主成 分とする焼結体に該導電性材料を主成分とする薄膜を形成して薄膜導電性材料を得、 該薄膜導
電性材料の上に窒化ガリウム、 窒化インジウム、 窒化アルミニウムのうちから選ばれた少なく とも 1種以上を主成分とする薄膜が形成できる。 通常上記薄鹏電性材料は窒化アルミニウム を主成分とする焼結体の表面に形成される。 前記薄膜導電性材料が形成された窒化アルミニゥ ムを主成分とする焼結体には 藤件を選択することにより単結晶、 無定形、 多結晶、 配 向性多結晶など各種結晶状態の窒化ガリウム、 窒化インジウム、 窒化アルミニウムのうちから 選ばれた少なくとも 1種以上を主成分とする薄膜を形成することができる。 なおスパッタリン グ法の条件として上記金、 銀、 銅、 アルミニウム、 鉄、 コバルト、 ニッケル、 ルテニウム、 口 ジゥム、ノ ラジウム、 オスミウム、 イリジウム、 白金、 タンタル、 モリブデン、 タングステン、 ク ΠΙム、 チタン、 ニッケル—クロム合金、 窒化チタン、 窒化ジルコニウム、 窒化タンタル、 な どのうちから選ばれた少なくとも 1種以上を主成分とする導電性材料をタ一ゲットとして用い 基板 ¾Jtを it! [室温〜 3 0 0°Cとしさらに基板? ^を 3 0 0°C以上とし減圧下例えば A r ガスを圧力 0. 2〜2. O P aで 1 0〜2 0 0 c c Zm i n. の流量で流し 0. 3〜3 KWの 直流電力あるいは高周波電力をかけて «を行う。 高周波 (R F) 電力の周波数は通常 2. 4 5 GH zのマイクロ波あるいは 1 3. 5 6 MH zのラジオ波などが用いられる。 また薄麟電 性材料が窒化チタン、 窒化ジルコニウム、 窒化タンタルなどの金属化合物である場合など雰囲 気ガスとして適宜例えば N2ガスや NH3ガスなどの反応性ガスを単独であるいは A rガス、 H2 ガスなどのキヤリァガスに加えて用い反応性スパッタリングにより該薄膜導電性材料を形成す ることも有効である。 イオンプレーティング法の条件として上記金、 銀、 銅、 アルミニウム、 鉄、 コバルト、 ニッケル、 ルテニウム、 ロジウム、 パラジウム、 オスミウム、 イリジウム、 白 金、 タンタル、 モリブデン、 タングステン、 クロム、 チタン、 ニッケル一クロム合金、 などの うちから選ばれた少なくとも 1種以上を主成分とする導電性材料を溶融原料として用い基板温 度を適宜室温〜 3 0 Ot:としあるいは基板温度を適宜 3 0 0 °C以上とし成膜チャンバ一内の真 空度を 2 X 1 0— 3 P a以下の真空度としてイオン化電圧 1 0〜2 0 0 V、 基板への印加電圧 3 0 0〜5 0 0 0 Vにて謹を行う。 あるいは印加電力として高周波を用いて行うこともできる。 高周波 (R F) 電力の周波数は通常 2. 4 5 GH zのマイクロ波あるいは 1 3. 5 6 MH zな どが用いられる。 また薄鹏電性材料が窒化チタン、 窒化ジルコニウム、 窒化タンタルなどの 金属化合物である場合など溶融材料にチタン、 ジルコニウム、 タンタルなどの金属を用いてチ ヤンバー内に適宜例えば N2ガスや NH3ガスなどの反応性ガスを単独であるいは A rガス、 H2 ガス、 N2ガスなどのキヤリァガスに加えて導入して反応性イオンプレーティング法により該薄 麟電性材料を形成することも有効に実施できる。 真空蒸着法の条件として上記金、 銀、 銅、 ァリレミ二ゥム、 鉄、 コパリレト、 ニッケル、 ルテニウム、 ロジウム、 パラジウム、 オスミウム、 イリジウム、 白金、 タンタル、 モリブデン、 タングステン、 クロム、 チタン、 ニッケル一クロ ム合金、 などのうちから選ばれた少なくとも 1種以上を主成分とする導電性材料を溶融原料と して用い基板温度を 室温〜 3 0 O t:としさらに基板^ ¾を¾|[3 0 0 °C以上とし成膜チヤ ンバー内の真空度を 2 X 1 0—3 P a以下の真空度として成膜を行う。 上記スパッタリング法、 イオンプレーティング法あるいは蒸着法は薄膜導電性材料の形成だけでなく MO CVD法、 ク 口ライド VP E法、 ハライド V P E法、 ハイドライド VP E法あるいは MB E法などともに本 発明による窒化ガリウム、 窒化インジウム、 窒化アルミニウムのうちから選ばれた少なくとも 1種以上を主成分とする単結晶、 無定形、 多結晶、 配向性多結晶など各種結晶状態の薄膜、 及 び S i、 G e、 S e、 T e、 〇、 Mg、 B e、 C a、 Z n、 C d、 Cなどのドーピング成分を 含む窒化ガリゥム、 窒化ィンジゥム、 窒化アルミニゥムのうちから選ばれた少なくとも 1種以 上を主成分とする単結晶、 無定形、 多結晶、 配向性多結晶など各種結晶状態の薄膜を形成する 方法としても用いることができる。 これらの薄膜形成に際してスパッタリング法では窒化ガリ ゥム、 窒化インジウム、 窒化アルミニウムを主成分とするターゲットを用いて目的とする組成
の窒化ガリウム、 窒化インジウム、 窒化アルミニウムを主成分とする薄膜を得る、 あるいは金 属ガリウム、 金属インジウム、 金属アルミニウムをターゲットとして用い上記 N2ガスや NH3 ガスなどと反応させることで目的とする組成の窒化ガリウム、 窒化インジウム、 窒化アルミ二 ゥムを主成分とする薄膜を得ることができる。 また、 イオンプレーティング法及び蒸着法では 金属ガリウム、 金属インジウム、 金属アルミニウムをターゲットとして用い上記 N2ガスや NH 3ガスなどと反応させることで目的とする組成の窒化ガリウム、 窒化インジウム、 窒化アルミ二 ゥムを主成分とする薄膜を得ることができる。 薄 電性材料を有する窒化アルミニウムを主 成分とする焼結体に形成された窒化ガリウム、 窒化インジウム、 窒化アルミニウムのうちから 選ばれた少なくとも 1種以上を主成分とする薄膜にはクラックは見られず、 該薄膜導電性材料 と窒化ガリウム、 窒化インジウム、 窒化アルミニウムのうちから選ばれた少なくとも 1種以上 を主成分とする薄膜との間に剥離などの不具合は見られにくい。 窒化アルミニウムを主成分と する焼結体に上記導電性材料を主成分とする薄膜を形成しさらにその上に窒化ガリゥム、 窒化 インジウム、 窒化アルミニウムのうちから選ばれた少なくとも 1種以上を主成分とする単結晶 薄膜を形成したとき該単結晶薄膜のミラ一指数 (0 0 2) の格子面の X線回折ロッキングカー ブの半値幅 3 6 0 0秒以下の結晶性のものが得られ易い。 また、 窒化ガリウム、 窒化インジゥ ム、 窒化アルミニウムのうちから選ばれた少なくとも 1種以上を主成分とする薄膜との接合性 も高く垂直引っ張り弓艘 2 KgZmm2以上のものが得られ易いので好ましい。 また、 上記薄膜 導電性材料を有する窒化アルミニウムを主成分とする焼結体に形成した窒化ガリゥム、 窒化ィ ンジゥム、 窒化アルミニウムのうちから選ばれた少なくとも 1種以上を主成分とする薄膜に粘 着テープを接着し引き剥がしテストを行っても、 該薄膜導電性材料と窒化ガリウム、 窒化イン ジゥム、 窒化アルミニウムのうちから選ばれた少なくとも 1種以上を主成分とする薄膜との間 に剥離は見られない。 上記の接合性は窒化ガリウム、 窒化インジウム、 窒化アルミニウムのう ちから選ばれた少なくとも 1種以上を主成分とする薄膜が単結晶、 無定形、 多結晶、 配向性多 結晶などどのような結晶状態であっても同様に得ることができる。 このように本発明による薄 電性材料は窒化ガリウム、 窒化インジウム、 窒化アルミニウムのうちから選ばれた少なく とも 1種以上を主成分とする薄膜との間に高い接合性を有しているが、 上記の接合性諮耐去の 結果から見て本発明による薄膜導電性材料は窒化アルミニウムを主成分とする焼結体に対して も垂直引張り強度 2 K gZmm2以上と薄膜と少なくとも同等の接合性を有しているものと思 われる。 通常上記薄膜導電性材料はその厚みが 2 0 m以下のものを使用することがその上に 形成される窒化ガリウム、 窒化インジウム、 窒化アルミニウムのうちから選ばれた少なくとも 1種以上を主成分とする薄膜の品質を高め該薄膜との接合性を高める上で好ましい。 すなわち 上記薄膜導電性材料の厚みが 2 0 m以下であれば該薄 電性材料の上に形成した窒化ガリ ゥム、 窒化インジウム、 窒化アルミニウムのうちから選ばれた少なくとも 1種以上を主成分と する単結晶薄膜は該単結晶薄膜のミラ一指数 (0 0 2) の格子面の X線回折ロッキングカーブ の半値幅 3 0 0秒以下の結晶性のものが得られ易く、 また該薄膜が無定形や多結晶など必ずし も単結晶でない結晶状態であっても該薄膜との接合性も垂直引っ張り強度 2 K g/mm2以上 のものが得られ易いのでより好ましい。 また上記薄膜導電性材料の厚みが 5 m以下であれば 該薄膜導電性材料の上に形成した窒化ガリウム、 窒化インジウム、 窒化アルミニウムのうちか ら選ばれた少なくとも 1種以上を主成分とする単結晶薄膜は該単結晶薄膜のミラー指数 (0 0 2)の格子面の X線回折ロッキングカーブの半値幅 2 4 0秒以下の結晶性のものが得られ易ぐ また該薄膜が無定形や多結晶など必ずしも単結晶でない結晶状態であっても該薄膜との接合性 も垂直引っ張り強度 2 Kg/mm2以上のものが得られ易いのでより好ましい。上記薄騰電性 材料の厚みが 1 以下であれば該薄麟電性材料の上に形成した窒化ガリウム、 窒化インジ ゥム、 窒化アルミニウムのうちから選ばれた少なくとも 1種以上を主成分とする単結晶薄膜は
該単結晶薄膜のミラー指数 (0 0 2 ) の格子面の X線回折ロッキングカーブの半値幅 2 0 0秒 以下の比較的結晶性の高いものが得られ易ぐ また該薄膜が無定形や多結晶など必ずしも単結 晶でない結晶状態であっても該薄膜との接合性も垂直引っ張り強度 2 K g/mm2以上のもの が得られ易いのでより好ましい。
上記の結果、 薄騰電性材料が形成された窒化アルミニウムを主成分とする焼結体に窒化ガ リウム、 窒化インジウム、 窒化アルミニウムのうちから選ばれた少なくとも 1種以上を主成分 とする薄膜が形成された薄膜基板を製造することができることが確認された。
また、 上記薄膜導電性材料が形成された炭化珪素、 窒化珪素、 窒化ガリウム、 酸化亜鉛、 酸 化ベリリゥムなどの六方晶結晶系及び酸化アルミニウムなどの三方晶結晶系あるいは六方晶系 として分類できる結晶構造を有する各種セラミック材料を主成分とする焼結体、 及びその他各 種セラミック材料を主成分とする焼結体からなる基板の上にはさらに窒化ガリゥム、 窒化ィン ジゥム、 窒化アルミニウムのうちから選ばれた少なくとも 1種以上を主成分とする単結晶、 無 定形、 多結晶、 配向性多結晶のうちから選ばれる少なくともいずれかの結晶状態を有する薄膜 が形成できる。 該薄膜は単一層としてだけでなく結晶状態、 組成などが異なる 2層以上の薄膜 層として形成できる。
薄麟電性材料が形成されている窒化アルミニウムを主成分とする焼結体からなる基板には 窒化ガリウム、 窒化インジウム、 窒化アルミニウムのうちから選ばれた少なくとも 1種以上を 主成分とするェピタキシャル成長した単結晶薄膜が形成できるがすべてが単結晶でなくその他 に無定形、 多結晶、 配向性多結晶のうちから選ばれる少なくともいずれかの結晶状態を有する 薄膜も形成できる。 また単一層としてだけでなく 2層以上の多層化された薄膜構成のものも形 成できる。 すなわち、 あらかじめ窒化ガリウム、 窒化インジウム、 窒化アルミニウムのうちか ら選ばれた少なくとも 1種以上を主成分とする単結晶、 無定形、 多結晶、 配向性多結晶のうち から選ばれる少なくともいずれかの結晶状態からなる薄膜を形成しその上に窒化ガリウム、 窒 化インジウム、 窒化アルミニウムのうちから選ばれた少なくとも 1種以上を主成分とするェピ タキシャル成長した単結晶薄膜が形成された 2層構成の薄膜が形成できる。 このような構成で 形成された単結晶薄膜の結晶性は薄膜導電性材料が形成されている窒化アルミニウムを主成分 とする焼結体からなる基板に直接形成された単結晶薄膜よりも優れたものが得られ易いので好 ましい。 また例えば、 窒化ガリウム、 窒化インジウム、 窒化アルミニウムのうちから選ばれた 少なくとも 1種以上を主成分とする単結晶、 無定形、 多結晶、 配向性多結晶のうちから選ばれ る少なくともいずれかの結晶状態を有する薄膜を形成し、 その上に単結晶を含まない無定形、 多結晶、 配向性多結晶のうちから選ばれる少なくともいずれかの結晶状態からなる薄膜が形成 された 2層構成の薄膜も形成できる。 2層以上で形成された薄膜は各層において単結晶を含め 無定形、 多結晶、 配向性多結晶などの結晶状態、 組成、 あるいは厚みなどそれぞれ異なる状態 で形成でき、 本発明においては 2層以上の薄膜層のすべてが単結晶でない薄膨冓成であっても 形成出来る。 2層以上の薄翻で構成されている薄膜層すべてが窒化ガリウム、 窒化インジゥ ム、 窒化アルミ二ゥムのうちから選ばれた少なくとも 1種以上を主成分とする単結晶薄膜から なるものも形成出来る。 2層以上で構成されている薄膜層のうち少なくとも 1層以上要すれば 表面の薄 l は単結晶であることが好ましい。 特に、 本発明によるあらかじめ薄膜導電性材料 が形成された基板に窒化ガリウム、 窒化インジウム、 窒化アルミニウムのうちから選ばれた少 なくとも 1種以上を主成分とする薄膜が形成された薄膜基板を発光素子、 あるいはフィールド ェミッションディスプレイ、 あるいは回路基板、 あるいは光導波路など、 各種電子素子及び電 子部品の作製に用いる場合など、 基板表面に形成される薄膜は通常ェピタキシャル成長した単 結晶であることが好ましい。
本発明において上記薄膜導電性材料は窒化アルミニウムを主成分とする焼結体に窒化ガリウ
ム、 窒化インジウム、 窒化アルミニウムのうちから選ばれた少なくとも 1種以上を主成分とす る薄膜が形成された薄膜基板にも形成することができる。 すなわち、 上記薄 電性材料は窒 化アルミニウムを主成分とする焼結体にあらかじめ形成されている窒化ガリウム、 窒化インジ ゥム、 窒化アルミニウムのうちから選ばれた少なくとも 1種以上を主成分とする薄膜に形成で き十分な接合性を有している。 上記薄膜導電性材料が形成された窒化ガリウム、 窒化インジゥ ム、 窒化アルミニウムのうちから選ばれた少なくとも 1種以上を主成分とする薄膜にはクラッ クは見られず、 化ガリウム、 窒化インジウム、 窒化アルミニウムのうちから選ばれた少な くとも 1種以上を主成分とする薄膜と上記薄膜導電性材料と間に剥離などの不具合は見られに くい。 また、 接合弓艘も垂直引っ張り法で 2 KgZmm2以上のものが得られ易い。 このような 良好な接合性が得られる理由として窒化ガリウム、 窒化インジウム、 窒化アルミニウムのうち から選ばれた少なくとも 1種以上を主成分とする薄膜は窒化アルミニウムを主成分とする焼結 体に形成されているため格子不整合や熱膨張率の相違などによる内部応力が少なく、 さらに薄 膜導電性材料を形成したときに生じる歪や引っ張り応力は脆性材料である該薄膜にではなく比 較的柔らかくあるいは熱膨張率のより大きい薄^電性材料により多くあるいは薄!^電性材 料にだけ生じやすいことが大きな要因ではないかと本願発明者は推測している。
なお、 上記の接合性は窒化ガリウム、 窒化インジウム、 窒化アルミニウムのうちから選ばれ た少なくとも 1種以上を主成分とする薄膜が単結晶、 無定形、 多結晶、 配向性多結晶などどの ような結晶状態であっても同様に得ることができる。
上記薄膜導電性材料のうち金あるいは銅のようにはんだ付け力河能な材料を形成しはんだを 用いて接合弓娘を測 れば 4KgZmm2以上の垂直引張り強度のものが得られやすい。 これ は本発明による薄騰電性材料と窒化ガリウム、 窒化インジウム、 窒化アルミニウムのうちか ら選ばれた少なくとも 1種以上を主成分とする薄膜との接合が高いということだけでなく、 窒 化アルミニウムを主成分とする焼結体と薄騰電性材料との接合性及び窒化アルミニウムを主 成分とする焼結体と窒化ガリウム、 窒化インジウム、 窒化アルミニウムのうちから選ばれた少 なくとも 1種以上を主成分とする薄膜との接合性も本来高いものであることを示している。 本発明による上記薄騰電性材料は窒化ガリウム、 窒化インジウム、 窒化アルミニウムのう ちから選ばれた少なくとも 1種以上を主成分とする薄膜の表面だけでなく該薄膜の内部にも形 成することができる。 すなわち、 窒化アルミニウムを主成分とする焼結体にあらかじめ形成さ れている窒化ガリウム、 窒化インジウム、 窒化アルミニウムのうちから選ばれた少なくとも 1 種以上を主成分とする薄膜に対して薄膜導電性材料を形成しさらに窒化ガリゥム、 窒化ィンジ ゥム、 窒化アルミニウムのうちから選ばれた少なくとも 1種以上を主成分とする薄膜を被覆し て窒化ガリウム、 窒化インジウム、 窒化アルミニウムのうちから選ばれた少なくとも 1種以上 を主成分とする薄膜の内部に薄膜導電性材料を形成したとき、 該薄膜導電性材料と窒化ガリゥ ム、 窒化インジウム、 窒化アルミニウムのうちから選ばれた少なくとも 1種以上を主成分とす る薄膜との接合界面の剥離ゃ窒化ガリウム、 窒化インジウム、 窒化アルミニウムのうちから選 ばれた少なくとも 1種以上を主成分とする薄膜内部にクラックやなどの不具合が生じにくい。 また本発明は、 窒化ガリウム、 窒化インジウム、 窒化アルミニウムのうちから選ばれた少な くとも 1種以上を主成分とする薄膜を形成するための基板であって、 該基板は薄膜導電性材料 が形成された窒化アルミニウムを主成分とする焼結体からなることを特徴とする薄膜形成用基 板を含む。 また、 窒化アルミニウムを主成分とする焼結体に窒化ガリウム、 窒化インジウム、 窒化アルミニウムのうちから選ばれた少なくとも 1種以上を主成分とする薄膜が形成された薄 膜基板であって、 さらに薄膜導電性材料が形成されていることを特徴とする薄膜基板を含む。 このように本発明においては、 1 ) 窒化アルミニウムを主成分とする焼結体に薄廳電性材 料が形成された薄膜形成用基板、 2) あらかじめ薄膜導電性材料が形成された窒化アルミニゥ
ムを主成分とする焼結体に窒化ガリウム、 窒化インジウム、 窒化アルミニウムのうちから選ば れた少なくとも 1種以上を主成分とする薄膜が形成された薄膜基板、 3) 窒化アルミニウムを 主成分とする焼結体に形成された窒化ガリウム、 窒化インジウム、 窒化アルミニウムのうちか ら選ばれた少なくとも 1種以上を主成分とする薄膜の上にさらに薄膜導電性材料を形成した薄 膜基板、 4) あらかじめ薄廳電性材料が形成された窒化アルミニウムを主成分とする焼結体 に窒化ガリウム、 窒化インジウム、 窒化アルミニウムのうちから選ばれた少なくとも 1種以上 を主成分とする薄膜を形成しその上にさらに薄膜導電性材料を形成した薄膜基板、 など各種薄 膜形成用基板及び蒋膜基板を提供することができる。 また、 上記 2)、 3)、 4) のそれぞれの 薄膜基板において、 形成されている窒化ガリウム、 窒化インジウム、 窒化アルミニウムのうち から選ばれた少なくとも 1種以上を主成分とする薄膜の内部に薄膜導電性材料が形成された薄 膜基板ち提供することができる。
本発明による窒化アルミニウムを主成分とする焼結体に上記薄膜導電性材料が形成された薄 膜形成用基板及び育膜基板を用いる効果は、 該薄膜形成用基板及び該薄膜基板を単に窒化ガリ ゥム、 窒化インジウム、 窒化アルミニウムのうちから選ばれた少なくとも 1種以上を主成分と する薄膜を形成するための基板としてだけでなぐ 例えば上記薄鹏電性材料を回路パターン 状に加工するなどして該薄 ^#電性材料が形成された薄膜形成用基板及び薄膜基板上に形成さ れる発光素子を電気的に駆動させるための電気回路機能が付加された基板として用いることが できることである。 さらに導通ビアを有する窒化アルミニウムを主成分とする焼結体に上記薄 膜導電性材料が形成された薄膜形成用基板及び 膜基板を用いれば該薄^電性材料が形成さ れていない導通ビアを有する窒化アルミニウムを主成分とする焼結体を用いる場合に比べて基 板の上下表面の電気的接続性が向上するという効果が得られる。 すなわち、 窒化ガリウム、 窒 化インジウム、 窒化アルミニウムのうちから選ばれた少なくとも 1種以上を主成分とする薄膜 が導電性を有するものであれば導通ビアを介して該導電性を有する薄膜と該薄膜が形成されて いる反対側の基板面とを電気的に接続することができる。 また、 本発明による上記薄 電性 材料を形成した薄膜形成用基板あるいは薄膜基板を用いて発光素子をその上に形成する場合上 記薄 電性材料を該発光素子から発せられる光の反射部材として用いることができるので発 光素子から発せられる光を効率よく集光したり特定の方向へ放出することが可能になるという 効果がある。 すなわち、 発光素子の発光層から発せられる光を^?外部へ窒化アルミニウムを 主成分とする焼結体からなる基板側でなくその反対側のほうから放出したい場合や反対側の特 定の方向に集光したい場合など、 反射部材として上記薄 電性材料を基板に形成しておくこ とにより比較的容易に実現することができる。 特定の方向に発光素子からの光を制御すること 力壁まれるのは例えば面発光レ一ザ一ダイオード (L D) や平板状表示装置などに使用される 発光ダイオード (L ED) などである。 上記薄騰電性材料を形成していない窒化アルミニゥ ムを主成分とする焼結体からなる基板を用いた場合、 該窒化アルミニウムを主成分とする焼結 体の少なくとも波長 2 0 0 nmあるいは 2 0 0 nmより長い波長の光に対する反射率は通常 1 5 %以下と低いので仮に基板側からの ¾¾ を防止する目的で) ¾¾ 性の小さい窒化アルミ二 ゥムを主成分とする焼結体を基板として用いたとしても効率よく目的とする発光素子からの光 の方向制御や集光制御することが困難となることが多い。
上記薄膜導電性材料を反射部材としても形成した基板を用いて作製した発光素子であっても その発光効率が従来からのサフアイァなどの基板を用いた場合と比べて大きく低下することは 少なぐ 少なくとも同等以上の発光効率を有する発光軒が提供し得る。 上記薄膜導電性材料 を反射部材としても形成した基板を用いて作製した発光素子は通常少なくとも 8 %以上の発光 効率を有するものが作製し得る。
このような薄 電性材料のうち例えば室温における抵抗率が 1 X 1 0— 3 Ω · c m以下の低
抵抗のものは電気回路の導体として用いることが好ましい。 また、 1 X 10— 3Ω · cm以上の 抵抗率の高いものは電気回路の抵抗体として用いることが好ましい。
また、 上記薄騰電性材料を発光素子作製用の窒化アルミニウムを主成分とする焼結体から なる基板に形成し反射部材として用いる場合通常基板の表面に形成される。 また、 該薄騰電 性材料を反射部材として用!/ゝる場合は発光素子からの発光に対する反射率は 15 %以上のもの を用いることが好ましい。 また発光素子からの発光に対する反射率が 50%以上の材料を用い ることがより好ましい。 また発光素子からの発光に対する反射率が 70%以上の材料を用いる ことがさらに好ましい。 また発光素子からの発光に対する反射率が 80%以上の材料を用いる ことが最も好ましい。 なお、 上記発光素子からの発光に対する反射率とは少なくとも波長 20 0 nm〜800 nmの範囲の光に対する反射率である。 また、 波長 200 ηπ!〜 800 nmの 範囲の光に対する反射率とは波長 200 nm〜800 nmの範囲のいずれか特定の波長の光で 測定された反射率を意味する。 本発明においては特に断らない限り通常波長 605 nmの光に 対する反射率を用いた。
上記薄膜導電性材料は窒化アルミニウムを主成分とする焼結体に対して例えば金、 銀、 銅、 ァレミ二ゥム、 鉄、 コバルト、 ニッケル、 ルテニウム、 ロジウム、 ノ、°ラジウム、 オスミウム、 イリジウム、 白金、 タンタル、 モリブデン、 タングステン、 クロム、 チタン、 ニッケル一クロ ム合金、 窒化チタン、 窒化ジルコニウム、 窒化タンタルなどのうちから選ばれた単一の材料だ けを用いた 1層構造のメタライズとして形成されたもの、 などを用いることができる。 またそ の他にクロム、 チタン、 ジルコニウム、 窒化チタン、 窒化ジルコニウムなどを窒化アルミニゥ ムを主成分とする焼結体との密着材料として用い、 その上に鉄、 コバルト、 ニッケル、 ロジゥ ム、 パラジウム、 オスミウム、 イリジウム、 白金、 モリブデン、 タングステン、 窒化チタン、 窒化ジリレコニゥムなどを纖バリア材料として形成し、 さらに金、 銀、 銅、 アルミニウムなど の低抵抗材料を適宜形成した例えばクロム Z銅、 チタン/モリブデン Z金、 チタン/タンダス テン/ニッケル、 チタン/タングステン/金、 チタン/白金 z金、 チタン/ニッケル/金、 ジ ルコニゥム Zタングステン/金、 ジルコニウム z白金 Z金、 など薄 層構造のものも用いる ことができる。 上記薄膜導電性材料のうち金、 銀、 銅、 アルミニウムなどの低抵抗材料を主成 分として用いた 1層構造あるいは多層構造のものは電気回路の導体として用いることが好まし レ^また窒化タン夕リ^ニッケル一クロム合金など抵抗率の高い材料は電気回路の抵抗体とし て用いることが好ましい。 なお上記窒化タンタルとしては T a及び T aと Nとの化合物 (例え ば T a N、 T a 2N等)及びアモルファス状の T a—N組成系の薄膜などを することができ る。
また、 該薄騰電性材料を反射部材として用いる場合、 例えば難ベリリウム (Be)、 マグ ネシゥム (Mg)、 スカンジウム (Sc)、 イットリウム (Y)、 希土類金属、 チタン (T i)、 ジルコニウム (Zr)、 ハフニウム (Hf)、 バナジウム (V)、 ニオブ (Nb)、 タンタル (T a)、 クロム(Cr)、モリブデン (Mo), タングステン (W)、 マンガン(Mn)、 レニウム (R e),鉄(Fe)、 コバルト (Co)、 ニッケル(Ni)、 ルテニウム (Ru)、 ロジウム (Rh)、 パラジウム(Pd)、 オスミウム(〇s)、 イリジウム (I r)、 白金(P t)、銅(Cu)、銀(A g)、 金 (Au)、 亜鉛 (Zn)、 硼素 (B)、 アルミニウム (Al)、 ガリウム (Ga)、 インジ ゥム(I n)、珪素 (S i)、ゲルマニウム(Ge)、錫(Sn)、鉛 (Pb)、 アンチモン(Sb)、 ビスマス (B i)、 などのうちから 1種以上を主成分とする金属あるいは合金を使用できる。合 金としてはこれらの金属あるいは合金の波長 605 nmの光に対する反射率は通常 15%以上 であり、 基板の表面に形成されることで十分反射部材として使用し得る。 また、 上記例示され た材料の中で Cu、 Ag、 Au、 Al、 Mg、 Zn、 Mo、 W、 Mn、 Fe、 Co、 Ni、 R h、 Pd、 Os、 I r、 P tのうちから選ばれた 1種以上を主成分とする金属あるいは合金は
波長 6 0 5 nmの光に対する反射率が 5 0 %以上と高いものが得やすく損失が小さいので好ま しい。 また、 上記金属材料あるいは合金材料のうち C u、 A g、 Au、 A l、 Mg、 Z n、 F e、 C o、 N i、 R h、 P d、 O s、 I r、 P tのうちから選ばれた 1種以上を主成分とする 金属あるいは合金が波長 6 0 5 nmの光に対する反射率が 7 0 %以上とより高いものが得やす く損失がより小さいので好ましい。 これら金属あるいは合金のなかで銅/タングステン、 銅/ モリブデン、 銀 Zタングステン、 銀/モリブデン、 金 Zタングステン、 金/モリブデンなど C u、 A g、 Auと W、 M oとの合金なども波長 6 0 5 n mの光に対する反射率が 5 0 %以上と 高いものが得易くさらに組成によっては反射率が 7 0 %以上とより高いものも得られるので反 射部材として好適に用いることができる。 上記例示した反射率 7 0 %以上の 1 4種類の金属あ るいは合金のうち R h、 P d、 〇s、 I r、 P tなどの白金族のうちから選ばれた少なくとも 1種以上を主成分とする金属又は合金は作製条件により反射率 8 0 %以上のものが得られるの で好ましい。 また、 これら反射率 7 0 %以上の金属あるいは合金材料のうち C u、 A g、 Au、 A 1を主成分とする金属あるいは合金は波長 6 0 5 nmの光に対する反射率 8 0 %以上の高い ものが得やすく損失が最も小さいので好ましい。
このように上記で例示した各種金属あるいは合金からなる薄膜導電性材料を本発明による発 光素子作製用基板に形成して用いた場合、 該薄 電性材料は発光素子からの発光に対する良 好な反射部材としての機能を有する。
なお、 薄膜導電'性材料の反射率は分光光度計 (S p e c t r o p h o t ome t e r ) など の光学機器を用いて容易に行うことができる。
本発明において、上記薄騰電性材料は窒化アルミニウムを主成分とする焼結体だけでなぐ 炭化珪素、 窒化珪素、 窒化ガリウム、 酸化亜鉛、 酸化ベリリウムなどの 1 ^晶結晶系及び 化 アルミ二ゥムなどの三方晶結晶系あるいは六方晶系として分類できる結晶構造を有する各種セ ラミック材料を主成分とする焼結体、 及びその他各種セラミック材料を主成分とする焼結体か らなる基板にも形成することができる。 また、 該炭化珪素、 窒化珪素、 窒化ガリウム、 酸化亜 鉛、 酸化ベリリウムなどの六方晶結晶系及び酸化アルミニウムなどの三方晶結晶系あるいは六 方晶系として分類できる結晶構造を有する各種セラミック材料を主成分とする焼結体、 及びそ の他各種セラミック材料を主成分とする焼結体として導通ビアを有するものも用いることがで さる。
上記薄麟電性材料が形成された炭化珪素、 窒化珪素、 窒化ガリウム、 酸化 ¾、 酸化ベリ リウムなどの六方晶結晶系及び酸化アルミニウムなどの三方晶結晶系あるいは六方晶系として 分類できる結晶構造を有する各種セラミック材料を主成分とする焼結体、 及びその他各種セラ ミック材料を主成分とする焼結体からなる基板の上にはさらに窒化ガリゥム、窒化ィンジゥム、 窒化アルミニウムのうちから選ばれた少なくとも 1種以上を主成分とする単結晶、 無定形、 多 結晶、 配向性多結晶のうちから選ばれる少なくともいずれかの結晶状態を有する薄膜が形成で きる。 該薄膜は単一層としてだけでなく結晶状態、 組成などが異なる 2層以上の薄膜層として 形成できる。
薄騰電性材料が形成されている炭化珪素、 窒化珪素、 窒化ガリウム、 酸化亜鉛、 酸化ベリ リウムなどの六方晶結晶系及び ¾化アルミニウムなどの三方晶結晶系あるいは^晶系として 分類できる結晶構造を有する各種セラミック材料を主成分とする焼結体、 及びその他各種セラ ミック材料を主成分とする焼結体からなる基板には窒化ガリウム、 窒化インジウム、 窒化アル ミニゥムのうちから選ばれた少なくとも 1種以上を主成分とするェピタキシャル成長した単結 晶薄膜が形成できるがすべてが単結晶でなくその他に無定形、 多結晶、 配向性多結晶のうちか ら選ばれる少なくともいずれかの結晶状態を有する薄膜も形成できる。 また単一層としてだけ でなく 2層以上の多層ィ匕された薄廳冓成のものも形成できる。 すなわち、 あらかじめ窒化ガリ
ゥム、 窒化インジウム、 窒化アルミニウムのうちから選ばれた少なくとも 1種以上を主成分と する単結晶、 無定形、 多結晶、 配向性多結晶のうちから選ばれる少なくともいずれかの結晶状 態からなる薄膜を形成しその上に窒化ガリウム、 窒化インジウム、 窒化アルミニウムのうちか ら選ばれた少なくとも 1種以上を主成分とするェピタキシャル成長した単結晶薄膜が形成され た 2層構成の薄膜が形成できる。 このような構成で形成された単結晶薄膜の結晶性は薄膜導電 性材料が形成されている窒化アルミニウムを主成分とする焼結体からなる基板に直接形成され た単結晶薄膜よりも優れたものが得られ易いので好ましい。 また例えば、 窒化ガリウム、 窒化 インジウム、窒化アルミニウムのうちから選ばれた少なくとも 1種以上を主成分とする単結晶、 無定形、 多結晶、 配向性多結晶のうちから選ばれる少なくともいずれかの結晶状態を有する薄 膜を形成し、 その上に単結晶を含まない無定形、 多結晶、 配向性多結晶のうちから選ばれる少 なくともいずれかの結晶状態からなる薄膜が形成された 2層構成の薄膜も形成できる。 2層以 上で形成された薄膜は各層において単結晶を含め無定形、 多結晶、 配向性多結晶などの結晶状 態、 組成、 あるいは厚みなどそれぞれ異なる状態で形成でき、 本発明においては 2層以上の薄 膜層のすべてが単結晶でない薄膨冓成であっても形成出来る。 2層以上の薄膜層で構成されて いる薄麵すべてが窒化ガリゥム、 窒化ィンジゥム、 窒化アルミニゥムのうちから選ばれた少 なくとも 1種以上を主成分とする単結晶薄膜からなるものも形成出来る。 2層以上で構成され ている薄膜層のうち少なくとも 1層以上要すれば表面の薄膜層は単結晶であることが好ましい。 特に、 本発明によるあらかじめ薄麟電性材料が形成された基板に窒化ガリウム、 窒化インジ ゥム、 窒化アルミニウムのうちから選ばれた少なくとも 1種以上を主成分とする薄膜が形成さ れた薄膜基板を発光素子、あるいはフィールドェミッションディスプレイ、あるいは回路基板、 あるいは光導波路など、 各種電子素子及び電子部品の作製に用いる場合など、 基板表面に形成 される薄膜は通常ェピタキシャル成長した単結晶であることが好ましい。
また、 窒化ガリウム、 窒化インジウム、 窒化アルミニウムのうちから選ばれた少なくとも 1 種以上を主成分とする単結晶、 無定形、 多結晶、 配向性多結晶のうちから選ばれる少なくとも いずれかの結晶状態を有する薄膜が形成された窒化アルミニウムを主成分とする焼結体からな る基板の上には薄麟電性材料が形成できるが、 本発明においては上記窒化アルミニウムを主 成分とする焼結体からなる基板だけでなく窒化ガリウム、 窒化インジウム、 窒化アルミニウム のうちから選ばれた少なくとも 1種以上を主成分とする単結晶、 無定形、 多結晶、 配向性多結 晶のうちから選ばれる少なくともいずれかの結晶状態を有する薄膜が形成された炭化珪素、 窒 化珪素、 窒化ガリウム、 酸化亜鉛、 酸化ベリリウムなどの六方晶結晶系及び 化アルミニウム などの三方晶結晶系あるいは六方晶系として分類できる結晶構造を有する各種セラミック材料 を主成分とする焼結体、 及びその他各種セラミック材料を主成分とする焼結体からなる基板の 上にも薄膜導電性材料が形成できる。
上記のように本発明において薄騰電性材料が形成された炭化珪素、 窒化珪素、 窒化ガリウ ム、 酸化 «、 酸化ベリリウムなどの六方晶結晶系及び 化アルミニウムなどの三方晶結晶系 あるいは六方晶系として分類できる結晶構造を有する各種セラミック材料を主成分とする焼結 体、 及びその他各種セラミック材料を主成分とする焼結体からなる基板を用いて発光舒、 あ るいはフィ一ルドエミッションディスプレイ、 あるいは回路基板、 あるいは光導波路、 など各 種電子素子及び電子部品を作製していくことができる。 以下、 図 1 0〜図 2 0、 及び図 3 7〜図 3 8で本発明による薄]^電性材料が形成された薄膜 形成用基板、 及び薄膜基板の例を示す。 図 6 9〜図 7 0は薄膜導電性材料の 1例を示す。 図 1 0〜図 2 0、 及び図 3 7〜図 3 8は斜視図で記載し、 図 6 9〜図 7 0は正面図で記載した。 図 1 0は窒化アルミニウムを主成分とする焼結体からなる基板 1 3に薄膜導電性材料 1 1が
形成された薄膜形成用基板の 1例を示す図である。
図 1 1は窒化アルミニウムを主成分とする焼結体からなる基板 1 3の両面に薄膜導電性材料 1 1が形成された薄膜形成用基板の 1例を示す図である。
図 1 2は導通ビアを有する窒化アルミニウムを主成分とする焼結体からなる基板 1 0の両面 に薄膜導電性材料 1 1が形成された薄膜形成用基板の 1例を示す図である。 導通ビアにより基 板両面に形成された薄膜導電性材料 1 1どうしが電気的に接続される。
図 1 3は窒化アルミニウムを主成分とする焼結体からなる基板 1 3に回路パターン状の薄膜 導電性材料 1 2が形成された薄膜形成用基板の 1例を示す図である。 本発明においてはこれら 回路パターンに直接窒化ガリウム、 窒化インジウム、 窒化アルミニウムのうちから選ばれた少 なくとも 1種以上を主成分とする薄膜を形成することができる。 あるいはこれら回路パターン を避け回路パターンが形成されていない窒化アルミニウムを主成分とする焼結体の部分に窒化 ガリウム、 窒化インジウム、 窒化アルミニウムのうちから選ばれた少なくとも 1種以上を主成 分とする薄膜を形成することもできる。 また本発明による薄!^電性材料を電気回路パターン として形成した薄膜形成用基板いて例えば該薄 J»成用基板上に発光素子などの機能素子を形 成すれば、 発光素子を搭載するための回腿板あるいはパッケージ一体型の基板としても機能 する。 したがって通常であれば発光素子などの機能素子を搭載するための回路基板あるいはパ ッケージが必要であるが本発明による機能一体型の基板を用いることで回路基板あるい «Λ°ッ ケージを別に用意する必要がなくなるという効果が得られる。
図 1 4はあらかじめ薄膜導電性材料が形成された窒化アルミニウムを主成分とする焼結体か らなる基板に窒化ガリウム、 窒化インジウム、 窒化アルミニウムのうちから選ばれた少なくと も 1種以上を主成分とする薄膜 5が形成されている薄膜基板の 1例を示す図である。 図 1 4に おいて薄鹏電性材料 1 1が形成された窒化アルミ二ゥムを主成分とする焼結体からなる基板 1 3に窒化ガリウム、 窒化インジウム、 窒化アルミニウムのうちから選ばれた少なくとも 1種 以上を主成分とする薄膜 5が形成されることで薄膜基板 1 5が構成されている。
図 1 5はあらかじめ薄膜導電性材料が形成された導通ビアを有する窒化アルミニウムを主成 分とする焼結体からなる基板に窒化ガリウム、 窒化インジウム、 窒化アルミニウムのうちから 選ばれた少なくとも 1種以上を主成分とする薄膜が形成されている薄膜基板の 1例を示す図で ある。 図 1 5においてあらかじめ薄騰電性材料 1 1が基板の片面に形成された導通ビア 3を 有する窒化アルミニウムを主成分とする焼結体からなる基板 1 0の該薄膜導電性材料 1 1が形 成されていない方の面に窒化ガリウム、 窒化インジウム、 窒化アルミニウムのうちから選ばれ た少なくとも 1種以上を主成分とする薄膜 5が形成されることで薄膜基板 1 6が構成されてい る。 図 1 5において窒化ガリウム、 窒化インジウム、 窒化アルミニウムのうちから選ばれた少 なくとも 1種以上を主成分とする薄膜 5が導電性を有するものであれば該導電性を有する薄膜 5と導通ビア 3を介して該薄膜 5が形成されている反対側の基板面とを電気的に接続すること ができる。
図 1 6はあらかじめ薄膜導電性材料が!^面に形成された導通ビアを有する窒化アルミニウム を主成分とする焼結体からなる基板に窒化ガリウム、 窒化インジウム、 窒化アルミニウムのう ちから選ばれた少なくとも 1種以上を主成分とする薄膜 5が形成されている薄膜基板の 1例を 示す図である。 図 1 6においてあらかじめ薄膜導電性材料 1 1力 面に形成された導通ビア 3 を有する窒化アルミニウムを主成分とする焼結体からなる基板 1 0に窒化ガリウム、 窒化イン ジゥム、 窒化アルミニウムのうちから選ばれた少なくとも 1種以上を主成分とする薄膜 5が形 成されることで薄膜基板 1 7が構成されている。 図 1 6において窒化ガリウム、 窒化インジゥ ム、 窒化アルミニウムのうちから選ばれた少なくとも 1種以上を主成分とする薄膜 5が導電性 を有するものであれば該導電性を有する薄膜 5と導通ビア 3を介して該薄膜 5が形成されてい
る反対側の基板面とより高い信頼性で電気的に接続することができる。
図 1 7は窒化アルミニウムを主成分とする焼結体からなる基板に形成された窒化ガリゥム、 窒化インジウム、 窒化アルミニウムのうちから選ばれた少なくとも 1種以上を主成分とする薄 膜の上にさらに薄 電性材料を形成した薄膜基板の 1例を示す。 図 1 7において窒化アルミ 二ゥムを主成分とする焼結体からなる基板 1 3に窒化ガリウム、 窒化インジウム、 窒化アルミ ニゥムのうちから選ばれた少なくとも 1種以上を主成分とする薄膜 5が形成されその上に薄膜 導電性材料 1 1が形成された薄膜基板 1 8の様子が示されている。
図 1 8はあらかじめ薄鹏電性材料が形成された窒化アルミニウムを主成分とする焼結体か らなる基板に窒化ガリウム、 窒化インジウム、 窒化アルミニウムのうちから選ばれた少なくと も 1種以上を主成分とする薄膜が形成されその上にさらに薄 電性材料が形成された薄膜基 板の 1例を示す。 図 1 8においてあらかじめ薄膜導電性材料 1 1が形成された窒化ァフレミエゥ ムを主成分とする焼結体からなる基板 1 3に窒化ガリウム、 窒化インジウム、 窒化アルミニゥ ムのうちから選ばれた少なくとも 1種以上を主成分とする薄膜 5が形成されさらに薄膜 5の表 面上に薄 電性材料 1 1が形成された薄膜基板 1 9の様子が示されている。
図 1 9はあらかじめ薄)^電性材料が形成された導通ビアを有する窒化アルミニウムを主成 分とする焼結体からなる基板に窒化ガリウム、 窒化インジウム、 窒化アルミニウムのうちから 選ばれた少なくとも 1種以上を主成分とする薄膜が形成されその上にさらに薄 電性材料が 形成された薄膜基板の 1例を示す。 図 1 9においてあらかじめ薄膜導電性材料 1 1が形成され た導通ビア 3を有する窒化アルミニウムを主成分とする焼結体からなる基板 1 0に窒化ガリゥ ム、 窒化インジウム、 窒化アルミニウムのうちから選ばれた少なくとも 1種以上を主成分とす る薄膜 5が形成されさらに薄膜 5の表面上に薄鹏電性材料 1 1が形成された薄膜基板 2 0の 様子が示されている。
図 2 0は窒化アルミニウムを主成分とする焼結体からなる基板にあらかじめ薄騰電性材料 力形成されその上に窒化ガリウム、 窒化インジウム、 窒化アルミニウムのうちから選ばれた少 なくとも 1種以上を主成分とする薄膜が形成され該薄膜表面にさらに薄 電性材料による電 気回路パターンが形成された薄膜基板の 1例を示す。 図 2 0においてあらかじめ薄]^電性材 料 1 1が形成された窒化アルミニウムを主成分とする焼結体からなる基板 1 3に窒化ガリウム、 窒化インジウム、 窒化アルミニウムのうちから選ばれた少なくとも 1種以上を主成分とする薄 膜 5が形成されさらに薄膜 5の表面上に回路パターン形状の薄騰電性材料 1 2が形成された 薄膜基板 2 1の様子が示されている。
図 3 7はあらかじめ薄膜導電性材料が形成された窒化アルミニウムを主成分とする焼結体か らなる基板の上に窒化ガリウム、 窒化インジウム、 窒化アルミニウムのうちから選ばれた少な くとも 1種以上を主成分とする薄膜が 2層形成された薄膜基板の 1例を示す。 図 3 7において あらかじめ薄膜導電性材料 1 1が形成された窒化アルミニウムを主成分とする焼結体からなる 基板 1 3に窒化ガリウム、 窒化インジウム、 窒化アルミニウムのうちから選ばれた少なくとも 1種以上を主成分とする薄膜 5が形成され、 さらにその上に窒化ガリウム、 窒化インジウム、 窒化アルミニウムのうちから選ばれた少なくとも 1種以上を主成分とする薄膜 8力 S形成された 構成の薄膜基板が符号 2 2で示されている。 例えば、 薄膜 5として窒化ガリウム、 窒化インジ ゥム、 窒化アルミニウムのうちから選ばれた少なくとも 1種以上を主成分とする単結晶、 無定 形、 多結晶、 配向性多結晶のうちから選ばれる少なくともいずれかの結晶状態を有するものを 形成し、 その上に薄膜 8として窒化ガリウム、 窒化インジウム、 窒化アルミニウムのうちから 選ばれた少なくとも 1種以上を主成分とするェピタキシャル成長した単結晶薄膜を形成すれば 該薄膜 8の結晶性は基板 1 3に直接形成した単結晶薄膜の結晶性よりも向上し易いので好まし い。 このような薄臌冓成の薄膜基板は例えば発光素子、 あるいはフィ一ルドエミッション、 あ
るいは回路基板、 あるいは光導波路など、 各種電子素子及び電子部品の作製用に使用していく 上で好ましい。
図 3 8はあらかじめ薄膜導電性材料が形成された導通ビアを有する窒化アルミニウムを主成 分とする焼結体からなる基板の上に窒化ガリウム、 窒化インジウム、 窒化アルミニウムのうち から選ばれた少なくとも 1種以上を主成分とする薄膜が 2層形成された薄膜基板の 1例を示す。 図 3 8においてあらかじめ薄 電性材料 1 1が形成された導通ビア 3を有する窒化アルミ二 ゥムを主成分とする焼結体からなる基板 1 0に窒化ガリウム、 窒化インジウム、 窒化アルミ二 ゥムのうちから選ばれた少なくとも 1種以上を主成分とする薄膜 5が形成され、 さらにその上 に窒化ガリウム、 窒化インジウム、 窒化アルミニウムのうちから選ばれた少なくとも 1種以上 を主成分とする薄膜 8が形成された構成の薄膜基板が符号 2 3で示されている。 例えば、 薄膜 5として窒化ガリゥム、 窒化ィンジゥム、 窒化アルミニゥムのうちから選ばれた少なくとも 1 種以上を主成分とする単結晶、 無定形、 多結晶、 配向性多結晶のうちから選ばれる少なくとも いずれかの結晶状態を有するものを形成し、 その上に薄膜 8として窒化ガリウム、 窒化インジ ゥム、 窒化アルミニウムのうちから選ばれた少なくとも 1種以上を主成分とするェピタキシャ ル成長した単結晶薄膜を形成すれば該薄膜 8の結晶性は基板 1 0に直接形成した単結晶薄膜の 結晶性よりも向上し易いので好ましい。 このような薄藤成の薄膜基板は例えば発光素子、 あ るいはフィー Jレドエミッション、 あるいは回路基板、 あるいは光導波路など、 各種電子^?及 び電子部品の作製用に使用していく上で好ましい。
図 6 9及び図 7 0は窒化アルミニウムを主成分とする焼結体からなる基板に形成する薄騰 電性材料の例を示す正面図である。 図 6 9及び図 Ί 0において薄 fl^電性材料 1 1の内部に空 間 2 4が形成されている。 該空間は本発明による薄膜導電性材料が形成された基板を例えば発 光^?作製用基板として用いる場合など、 発光素子から発せられた光が薄膜導電性材料に遮断 さ s¾ ^部に放出されにくくなることを防止するために設けられる。 薄膜導電性材料に空間 を設けることで発光 から発せられた光は薄 電性材料に遮断されることなく該空間を通 過して基 »部に放出され易くなり、 発光^?の発光効率が高められるので好ましい。 図 6 9 は空間が円形であるものを示す。 空間は円形に限らず例えば図 7 0に示すような四角形などど のような形状のものであってもよく、 このような空間を設けることにより発光素子の発光効率 の向上が可能となり易いので好ましい。
図 1 0〜図 2 0、 及び図 3 7〜図 3 8で示された薄!^電性材料が形成された基板には窒化 アルミニウムを主成分とする焼結体を用いた例が示されているが、 本発明においては上記窒化 アルミニウムを主成分とする焼結体からなる基板 (すなわちそれぞれ、 図 1 0の符号 1 3で示 される基板、 図 1 1の符号 1 3で示される基板、 図 1 2の符号 1 0で示される基板、 図 1 3の 符号 1 3で示される基板、 図 1 4の符号 1 3で示される基板、 図 1 5の符号 1 0で示される基 板、 図 1 6の符号 1 0で示される基板、 図 1 7の符号 1 3で示される基板、 図 1 8の符号 1 3 で示される基板、 図 1 9の符号 1 0で示される基板、 図 2 0の符号 1 3で示される基 に代 えて、 炭化珪素、 窒化珪素、 窒化ガリウム、 酸化亜鉛、 酸化ベリリウムなどの六方晶結晶系及 ぴ酸化アルミニウムなどの三方晶結晶系あるいは六方晶系として分類できる結晶構造を有する 各種セラミック材料を主成分とする焼結体、 及びその他各種セラミック材料を主成分とする焼 結体からなる基板を用いて上記薄膜導電性材料が形成された図 1 0〜図 2 0で例示されたもの と同じ態様の薄膜形成用基板及ぴ 膜基板を作製することができる。
本発明による窒化アルミニウムを主成分とする焼結体からなる基板、 あるいは炭化珪素、 窒 化珪素、 章化ガリウム、 酸化亜鉛、 酸化ベリリウムなどの六方晶結晶系及び 化アルミニウム などの三方晶結晶系あるいは六方晶系として分類できる結晶系を有する各種セラミック材料を 主成分とする焼結体からなる基板には上記のように窒化ガリゥム、 窒化ィンジゥム、 窒化アル
ミニゥムのうちから選ばれた少なくとも 1種以上を主成分とする単結晶薄膜を直接形成できる。 本願発明者は窒化アルミニウムを主成分とする焼結体からなる基板、 あるいは炭化珪素、 窒化 珪素、 窒化ガリウム、 酸化 ¾、 酸化ベリリウムなどの^晶結晶系及び 化アルミニウムな どの三方晶結晶系あるいは六方晶系として分類できる結晶系を有する各種セラミック材料を主 成分とする焼結体からなる基板に窒化ガリウム、 窒化インジウム、 窒化アルミニウムのうちか ら選ばれた少なくとも 1種以上を主成分とする単結晶薄膜を形成するための実験を行ってきた が、 その過程で新たに窒化ガリウム、 窒化インジウム、 窒化アルミニウムのうちから選ばれた 少なくとも 1種以上を主成分とする必ずしも単結晶ではない薄膜が形成できることを見出した。 すなわちこの薄膜は単結晶状態だけではなく無定形状態や多結晶状態あるいは配向性多結晶状 態など各種結晶状態のものであり、 これら各種結晶状態の薄膜も窒化アルミニゥムを主成分と する焼結体からなる基板及び炭化珪素、 窒化珪素、 窒化ガリウム、 酸化碰、 酸化ベリリウム などの六方晶結晶系及び 化アルミニウムなどの三方晶結晶系あるいは 晶系として分類で きる結晶系を有する各種セラミック材料を主成分とする焼結体からなる基板に直接形成できる。 なお、 配向性多結晶とは特定の一方向に結晶が成長した多結晶を意味する。 例えば基板表面に 対し垂直の方向に C軸が成長した多結晶で、 基板面に対して水平の方向にある結晶軸は単結晶 と異なりあらゆる方向を向いている。 窒化ガリウム、 窒化インジウム、 窒化アルミニウムのう ちから選ばれた少なくとも 1種以上を主成分とする単結晶薄膜であれば基板面に対し垂直な方 向に C軸が成長した場合 A軸は基板面に水平の方向に成長しかつその方向は一定であるが、 配 向性多結晶では基板面に対し垂直な方向に C軸が成長していても基板と水平な方向 A軸は一定 の方向性がない。 なお、 上記窒化アルミニウムを主成分とする焼結体からなる基板及び各種セ ラミック材料を主成分とする焼結体からなる基板には導通ビアを有する基板も含まれる。
本発明は窒化ガリウム、 窒化インジウム、 窒化アルミニウムのうちから選ばれた少なくとも 1種以上を主成分とする単結晶薄膜が形成し得る窒化アルミ二ゥムを主成分とする焼結体から なる基板及び炭化珪素、 窒化珪素、 窒化ガリウム、 酸化亜鉛、 酸化ベリリウムなどの六方晶結 晶系及び 化アルミニウムなどの三方晶結晶系あるいは六方晶系として分類できる結晶系を有 する各種セラミック材料を主成分とする焼結体からなる基板には、 窒化ガリウム、 窒化インジ ゥム、 窒化アルミニウムのうちから選ばれた少なくとも 1種以上を主成分とする無定形状態な ど必ずしも単結晶だけではない薄膜も直接形成し得るという知見に基づいてなされたものであ る。 上記窒化ガリウム、 窒化インジウム、 窒化アルミニウムのうちから選ばれた少なくとも 1 種以上を主成分とする無定形薄膜や多結晶薄膜あるいは配向性多結晶薄膜は単結晶薄膜と同様 比較的容易に形成できる。 すなわち上記単結晶以外の薄膜は MO CVD (有機金属化学気相分 解成長) 法、 MOVP E (有機金属細工ピタキシャル成長) 法、 ハイドライド VP E (水素 化物 目ェピタキシャル成長) 法、 クロライド VP E (塩化物気相ェピタキシャル成長) 法な どのハライド V P E (ハロゲン化物気相ェピタキシャル成長) 法、 プラズマ C VD法、 その他 の CVD (化学気相 成長) 法、 MB E ( 線エピタキシー) 法など、 あるいはあらかじ め形成した目的成分を含む固体材料を原料としエキシマレーザーなどを用いたレーザーアブレ ーシヨン法、 P L D (パルスレ一ザーデポジション:パルスレーザー^) 法など通常はェピ タキシャル成長に用い得る方法、 あるいはスパッタリング法、 イオンプレーティング法、 蒸着 法、 などの方法で形成できる。 単結晶あるいは単結晶以外の薄膜を形成する場合は前記«法 を用いたとき、 例えば基板の温度を低く設定するか、 薄膜原料ガスの濃度を高めにするなど成 麟件の変更などで容易に行うこと力 きる。例えば上記 MOC VD、ハイドライド VP E法、 クロライド V P E法、 ハライド VP E法などの各種 CVD、 あるいはスパッタリング法ゃィォ ンプレ一ティング法を用いて窒化ガリウム、 窒化インジウム、 窒化アルミニウムのうちから選 ばれた少なくとも 1種以上を主成分とする薄膜を窒化アルミニウムを主成分とする焼結体から
なる基板及び炭化珪素、 窒化珪素、 窒化ガリウム、 酸化亜鉛、 酸化ベリリウムなどの六方晶結 晶系及び酸化アルミ二ゥムなどの三方晶結晶系あるいは六方晶系として分類できる結晶系を有 する各種セラミック材料を主成分とする焼結体からなる基板に直接形成する場合、 単結晶薄膜 の場合は該基板の温度を例えば 6 0 0 °C〜7 0 0 °C以上と比較的高めとし、 単結晶以外の薄膜 を形成する場合は該基板の を 6 0 0 °C〜7 0 0 °C以下例えば 5 0 0 °C以下さらに 4 0 0 °C 以下に低く設定することで比較的容易に単結晶薄膜と単結晶以外の薄膜とを作り分けることが 可能である。 例えば窒化ガリゥムの薄膜をトリメチルガリゥムを原料として MO C VD法で形 成する場合単結晶薄膜は 7 0 0 〜 8 0 0°C以上、 好ましくは 9 0 0 T〜 1 1 0 0 °Cで形成で きる。 無定形状態や多結晶状態あるいは配向性多結晶状態の薄膜は 8 0 0 °C以下の例えば 6 0 01:以下の温度で形成できる。
また、 上記窒化ガリウム、 窒化インジウム、 窒化アルミニウムのうちから選ばれた少なくと も 1種以上を主成分とする薄膜形成を行うに際して単一の方法を用いるだけでなぐ 例えば M O CVD法とスパッタリング法を組み合わせて行う、 あるいはクロライド VP E法とスパッ夕 リング法を組み合わせて行う、 あるいは MO CVD法とクロライド VP E法及びスパッタリン グ法の 3つの方法を組み合わせて行う、 など複数の方法を組み合わせて上記薄膜を形成するこ とができる。 このような組み合わせにより、 例えば窒化アルミニゥムを主成分とする焼結体か らなる基板及び炭化珪素、 窒化珪素、 窒化ガリウム、 酸化亜铅、 酸化ベリリウムなどの六方晶 結晶系及び酸化アルミニウムなどの三方晶結晶系あるいは六方晶系として分類できる結晶系を 有する各種セラミック材料を主成分とする焼結体からなる基板にまずあらかじめスパッタリン グ法で窒化ガリウム、 窒化インジウム、 窒化アルミニウムのうちから選ばれた少なくとも 1種 以上を主成分とする基板面に対して垂直方向に結晶 C軸が成長した配向性多結晶状態の薄膜あ るいは無定形状態の薄膜を形成し、 その上に MOCVD法あるいはクロライド VP E法などに より窒化ガリウム、 窒化インジウム、 窒化アルミニウムのうちから窒化ガリウム、 窒化インジ ゥム、 窒化アルミニウムのうちから選ばれた少なくとも 1種以上を主成分とする単結晶状態の 薄膜を形成するといつたことなどを任意に実施できる。 さらに単結晶以外の薄膜はイオンプレ 一ティング法あるいは蒸着法など通常は単結晶薄膜が形成できにくい薄膜形成法を用いても窒 化アルミニウムを主成分とする焼結体からなる基板に比較的容易に直接形成できるという特徴 がある。 このような単結晶以外の薄膜をイオンプレーティング法、 あるいは蒸着法を用いて形 成する齢窒化アルミニウムを主成分とする焼結体からなる基板あるいは炭化珪素、窒化珪素、 窒化ガリウム、 酸化 «、 酸化ベリリウムなどの六方晶結晶系及び 化アルミニウムなどの三 方晶結晶系あるいは六方晶系として分類できる結晶系を有する各種セラミック材料を主成分と する焼結体からなる基板 figは 6 0 0°C以下、 通常 4 0 0°C以下で行われる。
上記薄膜がどのような結晶状態であるかは X線回折により容易に判別できることは前に述べ た。 すなわち、 無定形であればブロードな回折パターンとなり特定の回折角度の位置に回折線 が出現しない。 多結晶であれば回折パターンはブロードな図形となり易く 1本の特定の回折線 (例えばミラー指数 (0 0 2 ) の回折線だけあるいは (1 0 0 ) の回折線) だけでなく複数の 回折線が出現するので容易に単結晶であるかどうかの判別ができる。 配向性多結晶の場合 X線 回折により結晶配向方向に従つて特定の回折線が出現する。 前記のように例え〖ί¾板面に対し て C軸が垂直な方向に配向した多結晶薄膜では出現する回折線は 2 Θ / Θスキヤンではミラ一 指数 ( 0 0 2) 面の回折線だけである。 また、 基板面に対して C軸が垂直な方向に形成された 単結晶薄膜においても 2 スキャンの X線回折を行えば出現する回折線はミラ一指数 ( 0 0 2) 面の回折線だけである。 本発明において単結晶薄膜の場合ミラー指数 (0 0 2 ) の格子 面の回折線はシャープであり、 該ミラ一指数 (0 0 2 ) の格子面の X線回折ロッキングカーブ の半値幅は 3 6 0 0秒以下のものが容易に得られる。一方配向性多結晶薄膜ではミラ一指数(0
0 2 ) の格子面の回折線は単結晶と比較してブロードなものとなり易ぐ 該ミラー指数 (0 0 2 ) の格子面の X線回折ロッキングカーブの半値幅は 3 6 0 0秒以上となり易い。 配向性多結 晶薄膜が上記のようなミラ一指数 (0 0 2) の格子面の X線回折ロッキングカーブがブロード になる理由は必ずしも明確でないが、 単結晶薄膜が均質で連続し一体化した構造であるのに対 して配向性多結晶薄膜は C軸方向だけが垂直な方向に揃つた窒化ガリゥム、 窒化ィンジゥム、 窒化アルミニウムのうちから選ばれた少なくとも 1種以上を主成分とする微粒子からなるため を組み合わせて結晶の C面内回転の有無を確認する方法だけでなく上記 2 0 Z 0スキャン X線 回折だけ行いロッキングカーブの半値幅を測定することによつても配向性多結晶薄膜と単結晶 薄膜との区別を容易に行うことができる。 また S EM (走査型電子顕纖)、 S PM (走査型プ ローブ顕 などによる薄膜の微構造観察、 あるいは RHE ED (反射高速電子線回折) を 併用することでも比較的容易に多結晶薄膜と単結晶薄膜との区別をつけることができる。
窒化ガリウム、 窒化インジウム、 窒化アルミニウムのうちから選ばれた少なくとも 1種以上 を主成分とする C軸が垂直な方向に配向した配向性多結晶薄膜を上記各方法により窒化アルミ 二ゥムを主成分とする焼結体からなる基板あるいは炭化珪素、 窒化珪素、 窒化ガリウム、 酸化 亜鉛、 酸化ベリリウムなどの六方晶結晶系及び酸化アルミニウムなどの三方晶結晶系あるいは 六方晶系として分類できる結晶系を有する各種セラミック材料を主成分とする焼結体からなる 基板に直接形成する場合、 通常形成される配向性多結晶のミラ一指数 ( 0 0 2) の格子面の X 線回折ロッキング力一ブの半値幅として 3 6 0 0 0秒以下の結晶性を有するものが形成し得る。 また上記各種方法のうち MOCVD法、 MOV P E法、 ハイドライド VP E法、 クロライド V P E法、 ハライド V P E法、 プラズマ CVD法、 その他の CVD法、 MB E法、 エキシマレー ザ一などを用いたレーザーアブレーシヨン法、 P L D法、 スパッタリング法、 イオンプレーテ イング法、 蒸着法を用いて形成した配向性多結晶薄膜は該薄膜のミラー指数 (0 0 2) の格子 面の X線回折ロッキングカーブの半値幅として 2 1 0 0 0秒以下の結晶性を有するものが形成 し得る。
上記窒化ガリウム、 窒化インジウム、 窒化アルミニウムのうちから選ばれた少なくとも 1種 以上を主成分とする薄膜のうち配向性多結晶薄膜を窒化アルミニウムを主成分とする焼結体か らなる基板あるいは炭化珪素、 窒化珪素、 窒化ガリウム、 酸化亜鉛、 酸化ベリリウムなどの六 方晶結晶系及び酸化アルミニウムなどの三方晶結晶系あるいは六方晶系として分類できる結晶 系を有する各種セラミック材料を主成分とする焼結体からなる基板に直接形成する場合通常 M OCVD法、 MOVP E法、ノ \ィドライド VP E法、 クロライド VP E法、ハライド VP E法、 プラズマ CVD法、その他の CVD法、 MB E法などの方法を用いる方が、スパッタリング法、 イオンプレーティング法、 あるいは蒸着法を用いるよりも結晶性の優れた配向性多結晶薄膜が 得られ易い。例えば窒化アルミニウムを主成分とする焼結体からなる基板に直接窒化ガリゥム、 窒化インジウム、 窒化アルミニウムのうちから選ばれた少なくとも 1種以上を主成分とする配 向性多結晶薄膜を形成する場合、 MO CVD法、 MOVP E法、 ハイドライド VP E法、 クロ ライド V P E法、 ハライド VP E法、 プラズマ CVD法、 その他の CVD法、 MB E法などの 方法を用いて形成したものはミラ一指数 (0 0 2 ) の格子面の X線回折ロッキングカーブの半 値幅として 5 0 0 0秒以下のものが形成し得る。
上記窒化ガリウム、 窒化インジウム、 窒化アルミニウムのうちから選ばれた少なくとも 1種 以上を主成分とする薄膜のうち配向性多結晶薄膜を MO C VD法、 MOVP E法、 ハイドライ ド VP E法、 クロライド V P E法、ハライド VP E法、 プラズマ CVD法、その他の CVD法、 MB E法などの方法を用いて形成する場合、 窒化アルミニウムを主成分とする焼結体からなる 基板を用いる方がより結晶性に優れた配向性多結晶薄膜が形成し得る。 炭化珪素、 窒化珪素、
窒化ガリゥム、 酸化亜鉛、 酸化ベリリゥムなどの六方晶結晶系及び ¾化アルミニウムなどの三 方晶結晶系あるいは六方晶系として分類できる結晶系を有する各種セラミック材料を主成分と する焼結体からなる基板に上記 MOCVD法、 MOVP E法、 ハイドライド VP E法、 クロラ イド VP E法、 ハライド VP E法、 プラズマ CVD法、 その他の CVD法、 Μβ Ε法などの方 法を用いて直接形成する場合得られる配向性多結晶薄膜のミラー指数 ( 0 0 2) の格子面の X 線回折ロッキングカーブの半値幅として 5 0 0 0秒より大きいものになり易い。
なお、 本発明によるミラー指数 (0 0 2) の格子面の X線回折ロッキングカーブの半値幅に よる薄膜の結晶性評価法において、 形成される薄膜の結晶性は、 該薄膜内部の結晶がどの程度 乱れているかという指標で議が行われると言い換えることもできる。 一般的に «έ¾から実在 の結晶は単結晶と見なされるものであっても不完全であり、 微細な完全結晶 (結晶子) の集合 体であるモザィク構造から成ると云われている。 モザィク構造は方位が少しずつ異なる微細な 完全結晶 (結晶子) が集合した構造であり、 実在の単結晶はこのように乱れたモザイク構造か ら成ると云われている。 本発明において例えば形成される薄膜が単結晶であれば該薄膜のミラ
—指数 (0 0 2)の格子面の X線回折ロッキングカーブの半値幅 tt®常 3 6 0 0秒以下である。 従って本発明において単結晶薄膜はその内部においておよそ土 3 6 0 0秒以内すなわちおよそ 土 1度以内の角度でお互いの C軸方位が異なる結晶子から成るものであるとも推測される。 さ らに具体的に言えば、 例えば形成される薄膜がミラー指数 ( 0 0 2) の格子面の X線回折ロッ キングカーブの半値幅として 3 0 0秒の単結晶であれば該薄膜はその内部においておよそ土 3 0 0秒以内すなわち土 5分以内の角度でお互いの C軸方位が異なる結晶子から成るものである とも撥則される。 本発明による薄膜は自立したバルク材料とは異なり各種セラミック材料を主 成分とする焼結体からなる基板上に形成された状態のものである。 従って別の表現をすれば、 薄膜中の結晶子が基板面に対してどの程度の傾きを有しているかということで、 形成される薄 膜の結晶性が¥価され得るものと見なすことも可能であると思われる。 例えば薄膜の C軸を基 板面に対して垂直になるよう形成する場合、 形成される薄膜がミラ一指数 ( 0 0 2 ) の格子面 の X線回折ロッキングカーブの半値幅が 3 6 0 0秒の単結晶であれば該薄膜はその C軸が基板 面に対しておよそ 8 9度〜 9 0度の角度範囲 (すなわち基板面の H泉に対しておよそ 1度以内 の角度範囲) にある結晶子から成っているとも見なし得る。 また、 例えば形成される単結晶薄 膜のミラ一指数 (0 0 2) の格子面の X線回折ロッキング力一ブの半値幅が 3 0 0秒であれば 該薄膜はその C軸が基板面に対しておよそ 8 9度 5 5分〜 9 0度の角度範囲 (すなわち基板面 の垂線に対しておよそ 5分以内の角度範囲) にある微結晶から成っているとも見なし得る。 一方、 例えば形成される薄膜が配向性多結晶の場合該薄膜のミラー指数 (0 0 2 ) の格子面 の X線回折ロッキングカーブの半値幅は 3 6 0 0秒以上となり易いので配向性多結晶から成る 薄膜は単結晶薄膜に比べてさらに結晶方位が乱れた結晶子あるいは微粒子から成るものと推測 される。 すなわち本発明において配向性多結晶薄膜はその内部において土 3 6 0 0秒以上すな わち土 1度以上の角度でお互いの C軸方位が異なる結晶子あるいは微粒子が相当数存在するも のであると搬則される。 さらに具体的に言えば、 例えば 成される薄膜がミラ一指数 ( 0 0 2) の格子面の X線回折ロッキングカーブの半値幅として 2 1 0 0 0秒の配向性多結晶であれば該 薄膜はその内部においておよそ ± 2 1 0 0 0秒以内すなわち士 7度以内の角度でお互いの C軸 方位が異なる結晶子あるいは微粒子から成るものであるとも推測される。 別の表現をすれば ¾ 膜の C軸を基板面に対して垂直になるよう形成するとき形成される該薄膜がミラー指数 ( 0 0 2 ) の格子面の X線回折ロッキング力一ブの半値幅が 2 1 0 0 0秒の配向性多結晶であれば該 薄膜はその C軸が基板面に対しておよそ 8 3度以下の角度範囲 (すなわち基板面の垂線に対し ておよそ 7度以内の角度範囲) にある結晶子から成っているとも見なし得る。
このような単結晶、無定形、多結晶、配向性多結晶など各種結晶状態を有する窒化ガリウム、
窒化ィンジゥム、 窒化アルミニゥムのうちから選ばれた少なくとも 1種以上からなる薄膜を窒 化アルミニウムを主成分とする焼結体及び炭化珪素、 窒化珪素、 窒化ガリウム、 酸化亜鉛、 酸 ィ匕ベリリゥムなどの六方晶結晶系及び酸化アルミニウムなどの Ξ方晶結晶系あるいは六方晶系 として分類できる結晶系を有する各種セラミック材料を主成分とする焼結体からなる基板に直 接形成することの意味は大きい。 すなわち窒化アルミニウムを主成分とする焼結体及び炭化珪 素、 窒化珪素、 窒化ガリウム、 酸化亜鉛、 酸化ベリリウムなどの六方晶結晶系及び mi匕アルミ ニゥムなどの三方晶結晶系あるいは六方晶系として分類できる結晶系を有する各種セラミック 材料を主成分とする焼結体からなる基板にあらかじめ窒化ガリウム、 窒化インジウム、 窒化ァ ルミニゥムのうちから選ばれた少なくとも 1種以上からなる上記単結晶、 無定形、 多結晶、 配 向性多結晶など各種結晶状態の薄膜を形成しても、 該各種結晶状態の薄膜の上には窒化ガリゥ ム、 窒化インジウム、 窒化アルミニウムのうちから選ばれた少なくとも 1種以上を主成分とす る単結晶薄膜が比較的容易に形成でき、 このようにして形成された該単結晶薄膜の結晶性は向 上し易くなり、 さらに該単結晶薄膜の結晶方位の制御ができ易くなるという利点が生じるため である。
本発明においては窒化アルミニウムを主成分とする焼結体からなる基板、 及び炭化珪素、 窒 化珪素、 窒化ガリウム、 酸化亜鉛、 酸化ベリリウムなどの六方晶結晶系及び酸化アルミニウム などの三方晶結晶系あるいは六方晶系として分類できる結晶系を有する各種セラミック材料を 主成分とする焼結体からなる基板には高い結晶性を有する窒化ガリウム、 窒化インジウム、 窒 化アルミニウムのうちから選ばれた少なくとも 1種以上を主成分とする単結晶薄膜がもともと 直接形成できる。
すなわち、 本発明においては窒化アルミニウムを主成分とする焼結体からなる基板、 及び炭 化珪素、 窒化珪素、 窒化ガリウム、 酸化 »、 酸化ベリリウムなどの 1 ^晶結晶系及び 化ァ ルミニゥムなどの三方晶結晶系あるいは六方晶系として分類できる結晶系を有する各種セラミ ック材料を主成分とする焼結体からなる基板に窒化ガリウム、 窒化インジウム、 窒化アルミ二 ゥムのうちから選ばれた少なくとも 1種以上からなる単結晶薄膜を直接形成することができ該 単結晶薄膜の結晶性は高いものが形成し得る。 しかしながら、 上記窒化アルミニウムを主成分 とする焼結体からなる基板、 及び炭化珪素、 窒化珪素、 窒化ガリウム、 酸化亜鉛、 酸化べリリ ゥムなどの六方晶結晶系及び酸化アルミニウムなどの三方晶結晶系あるいは六方晶系として分 類できる結晶系を有する各種セラミック材料を主成分とする焼結体からなる基板に直接形成さ れた窒化ガリウム、 窒化インジウム、 窒化アルミニウムのうちから選ばれた少なくとも 1種以 上を主成分とする単結晶薄膜の結晶性よりも、 上記のようにあらかじめ窒化ガリウム、 窒化ィ ンジゥム、窒化アルミニウムのうちから選ばれた少なくとも 1種以上からなる単結晶、無定形、 多結晶、 配向性多結晶など各種結晶状態の薄膜を形成した窒化アルミ二ゥムを主成分とする焼 結体からなる基板、 及び炭化珪素、 窒化珪素、 窒化ガリウム、 酸化亜鉛、 酸化ベリリウムなど の六方晶結晶系及び酸化アルミニウムなどの三方晶結晶系あるいは六方晶系として分類できる 結晶系を有する各種セラミック材料を主成分とする焼結体からなる基板を用いることで、 上記 各種結晶状態の薄膜の上に形成される窒化ガリウム、 窒化インジウム、 窒化アルミニウムのう ちから選ばれた少なくとも 1種以上からなる単結晶薄膜の結晶性はさらに向上し易くなる。 本 発明において窒化アルミニウムを主成分とする焼結体及び炭化珪素、窒化珪素、窒化ガリウム、 酸化亜鉛、 酸化ベリリウムなどの六方晶結晶系及び ¾化アルミニウムなどの三方晶結晶系ある いは六方晶系として分類できる結晶系を有する各種セラミツク材料を主成分とする焼結体から なる基板にあらかじめ窒化ガリウム、 窒化インジウム、 窒化アルミニウムのうちから選ばれた 少なくとも 1種以上からなる単結晶、 無定形、 多結晶、 配向性多結晶のうちから選ばれる少な くともいずれかの結晶状態を有する薄膜を形成し、 さらに該薄膜の上から窒化ガリウム、 窒ィ匕
ィンジゥム、 窒化アルミニウムのうちから選ばれた少なくとも 1種以上を主成分とする単結晶 薄膜を形成すれば該単結晶薄膜の結晶性をさらに高めることが可能となる。 このような薄腿冓 成は、 窒化アルミニウムを主成分とする焼結体、 及び炭化珪素、 窒化珪素、 窒化ガリウム、 酸 化亜鉛、 酸化ベリリウムなどの六方晶結晶系及び 化アルミニウムなどの三方晶結晶系あるい は六方晶系として分類できる結晶系を有する各種セラミック材料を主成分とする焼結体からな る基板に窒化ガリウム、 窒化インジウム、 窒化アルミニウムのうちから選ばれた少なくとも 1 種以上を主成分とする単結晶、 無定形、 多結晶、 配向性多結晶のうちから選ばれる少なくとも いずれかの結晶状態を有する薄膜をあらかじめ形成し、 該薄膜の上に窒化ガリウム、 窒化イン ジゥム、 窒化アルミニウムのうちから選ばれた少なくとも 1種以上を主成分とする単結晶、 無 定形、 多結晶、 配向性多結晶のうちから選ばれる少なくともいずれかの結晶状態を有する薄膜 を形成し、 さらにその上に窒化ガリウム、 窒化インジウム、 窒化アルミニウムのうちから選ば れた少なくとも 1種以上を主成分とする単結晶薄膜を形成するという、 少なくとも 3層構成の 薄膜において 2層目あるいは 3層目以上に形成されるそれぞれの単結晶薄膜の結晶性を高める ことができる。
また、 本発明において単結晶、 無定形、 多結晶、 配向性多結晶などの各種結晶状態の薄膜を 形成した窒化アルミニウムを主成分とする焼結体からなる基板及び炭化珪素、 窒化珪素、 窒化 ガリウム、 酸化亜鉗、 酸化ベリリウムなどの六方晶結晶系及び 化アルミニウムなどの三方晶 結晶系あるいは六方晶系として分類できる結晶系を有する各種セラミック材料を主成分とする 焼結体からなる基板を用いれば窒化ガリウム、 窒化インジウム、 窒化アルミニウムのうちから 選ばれた少なくとも 1種以上からなる単結晶薄膜の結晶方位が制御でき易くなる。
本発明において上記のように、 窒化アルミニウムを主成分とする焼結体からなる基板、 及び 炭化珪素、 窒化珪素、 窒化ガリウム、 酸化亜鉛、 酸化ベリリウムなどの六方晶系及ぴ 化アル ミニゥムなどの三方晶系あるいは六方晶系として分類できる結晶構造を有する各種セラミック 材料を主成分とする焼結体からなる基板に窒化ガリウム、 窒化インジウム、 窒化アルミニウム のうちから選ばれた少なくとも 1種以上を主成分とする単結晶、 無定形、 多結晶、 配向性多結 晶のうちから選ばれる少なくともいずれかの結晶状態を有する薄膜を形成し、 さらに該薄膜の 上に窒化ガリゥム、 窒化ィンジゥム、 窒化アルミニゥムのうちから選ばれた少なくとも 1種以 上を主成分とする単結晶薄膜を形成することで、 上記各種セラミック材料からなる基板に直接 形成するよりも優れた結晶性を有する単結晶薄膜が形成された薄膜基板を作製し得る。 このよ うな薄膨冓成からなる薄膜基板を用いて作製される発光素子、 光導波路、 回路基板、 音響光学 素子などの電子素子あるいは電子部品などの特性が向上し易い。 例えば上記薄膜基板の上に新 たに発光素子、 光導波路、 回路基板、 音響光学素子などの電子素子あるいは電子部品を形成し ていく場合、 あるいは上記薄膜基板を構成している各種薄膜の一部を発光素子、 光導波路、 回 路基板、 音響光学素子などの電子素子あるいは電子部品を構成する部材の少なくとも 1部とし て用いる場合、 など該発光素子、 光導波路、 回路基板、 音響光学素子などの電子素子あるいは 電子部品特性の向上がはかり易くなるので好ましい。
本発明において、 窒化アルミニウムを主成分とする焼結体からなる基板、 及び炭化珪素、 窒 化珪素、 窒化ガリウム、 酸化亜鉛、 酸化ベリリウムなどの六方晶系及び殿化アルミニウムなど の Ξ方晶系あるいは六方晶系として分類できる結晶構造を有する各種セラミック材料を主成分 とする焼結体からなる基板にあらかじめ形成される窒化ガリウム、 窒化インジウム、 窒化アル ミニゥムのうちから選ばれた少なくとも 1種以上を主成分とする単結晶、 無定形、 多結晶、 配 向性多結晶のうちから選ばれる少なくともいずれかの結晶状態を有する薄膜は、 該薄膜を単一 層として形成したものだけでなくそれぞれ異なる 2以上の結晶状態のものからなる 2層以上の 多層薄膜層として形成したもの、 あるいは同じ結晶状態であってもそれぞれ異なる 2以上の組
成からなる 2層以上の多層薄膜層として形成したもの、 など組成及び Z又は結晶状態が異なる 2層以上の多層構成のものも用いることができる。 また、 さらに上記各種結晶状態の薄膜の上 から形成される窒化ガリウム、 窒化インジウム、 窒化アルミニウムのうちから選ばれた少なく とも 1種以上を主成分とする単結晶薄膜も同じ組成ではあっても異なる結晶性を有するもの、 あるいは異なる組成を有するもの、 など 2以上の薄膜層を積層して多層構成としたものも用い ることができる。 また上記 2以上の薄 を積層して多層構成としたもののなかで少なくとも 1以上の薄顧は単結晶状態であり残りの薄 は無定形、 多結晶、 配向性多結晶など単結晶 状態でない構成としたものも用いることができる。 また、 同じ組成でかつ同じ結晶状態のもの を 2回以上に分けて 2以上の薄膜層として形成することもできる。
また、 窒化アルミニウムを主成分とする焼結体からなる基板、 及び炭化珪素、 窒化珪素、 窒 化ガリウム、 酸化亜鉛、 酸化ベリリウムなどの六方晶系及び 化アルミニウムなどの三方晶系 あるいは六方晶系として分類できる結晶構造を有する各種セラミック材料を主成分とする焼結 体からなる基板にあらかじめ形成される窒化ガリウム、 窒化インジウム、 窒化アルミニウムの うちから選ばれた少なくとも 1種以上を主成分とする単結晶、 無定形、 多結晶、 配向性多結晶 のうちから選ばれる少なくともいずれかの結晶状態を有する薄膜の厚みは任意のものが形成で きる。 また、 さらにその上に形成する窒化ガリウム、 窒化インジウム、 窒化アルミニウムのう ちから選ばれた少なくとも 1種以上を主成分とする単結晶薄膜の厚みも任意のものが形成でき る。 上記あらかじめ形成される単結晶、 無定形、 多結晶、 配向性多結晶のうちから選ばれる少 なくともいずれかの結晶状態を有する薄膜及びさらにその上に形成される単結晶薄膜はそれぞ れ任意の厚みの単一層あるいは 2以上の薄 l sで構成される多層構造のものが作製し得る。 上 記あらかじめ形成される薄膜及びさらにその上に形成される単結晶薄膜の各薄 SISの は通 常それぞれ 0. 5 nm〜l 0 0 0 mの範囲もの、 好ましくは 0. 5 nm〜2 0 0 zmの範囲 のものを ¾g組み合わせて用いることが好ましい。
より具体的に述べれば、 窒化アルミニウムを主成分とする焼結体に窒化ガリウム、 窒化イン ジゥム、 窒化アルミニウムのうちから選ばれた少なくとも 1種以上を主成分とする単結晶、 無 定形、 多結晶、 配向性多結晶のうちから選ばれる少なくともいずれかの結晶状態を有する薄膜 をあらかじめ形成し、 さらにその上に窒化ガリウム、 窒化インジウム、 窒化アルミニウムのう ちから選ばれた少なくとも 1種以上を主成分とする単結晶薄膜を形成したとき、 該単結晶薄膜 はミラー指数 ( 0 0 2) の格子面の X線回折ロッキングカーブの半値幅が少なくとも 3 0 0秒 以下のものが形成できるだけでなくさらに 1 0 0秒以下と高い結晶性のものが形成し得る。 ま た、 このような薄殿冓成は、 窒化アルミニウムを主成分とする焼結体に窒化ガリウム、 窒化ィ ンジゥム、 窒化アルミニウムのうちから選ばれた少なくとも 1種以上を主成分とする単結晶、 無定形、 多結晶、 配向性多結晶のうちから選ばれる少なくともいずれかの結晶状態を有する薄 膜をあらかじめ形成し、 さらにその上に窒化ガリウム、 窒化インジウム、 窒化アルミニウムの うちから選ばれた少なくとも 1種以上からなる単結晶、 無定形、 多結晶、 配向性多結晶のうち から選ばれる少なくともいずれかの結晶状態を有する薄膜を形成し、 合計 2層の薄膜が形成さ れた基板にさらに窒化ガリウム、 窒化インジウム、 窒化アルミニウムのうちから選ばれた少な くとも 1種以上からなる単結晶薄膜を形成した場合でも、 2層目あるいは 3層目に形成される 単結晶薄膜はミラー指数 (0 0 2 ) の格子面の X線回折ロッキング力一ブの半値幅が少なくと も 3 0 0秒以下のものが形成できるだけでなくさらに 1 0 0秒以下と高い結晶性のものが形成 し得る。 このような効果は窒化ガリウム、 窒化インジウム、 窒化アルミニウムのうちから選ば れた少なくとも 1種以上を主成分とする単結晶、 無定形、 多結晶、 配向性多結晶のうちから選 ばれる少なくともいずれかの結晶状態を有する薄膜をあらかじめ 1層あるいは 2層形成した窒 化アルミ二ゥムを主成分とする焼結体からなる基板だけでなくあらかじめ 3層以上形成したも
のを基板として用いた場合でも同様に得られる。 すなわち窒化ガリウム、 窒化インジウム、 窒 化アルミニウムのうちから選ばれた少なくとも 1種以上を主成分とする単結晶、 無定形、 多結 晶、 配向性多結晶のうちから選ばれる少なくともいずれかの結晶状態を有する薄膜をあらかじ め合計 3層以上形成した窒化アルミニウムを主成分とする焼結体の上にさらに窒化ガリウム、 窒化インジウム、 窒化アルミニウムのうちから選ばれた少なくとも 1種以上を主成分とする単 結晶薄膜を形成したとき、 該単結晶薄膜はミラ一指数 ( 0 0 2) の格子面の X線回折ロッキン グカーブの半値幅が少なくとも 3 0 0秒以下のものが形成できるだけでなくさらに 1 0 0秒以 下と高い結晶性のものが形成し得る。
前記のように窒化アルミニウムを主成分とする焼結体からなる基板に例えば窒化ガリウム、 窒化インジウム、 窒化アルミニウムのうちから選ばれた少なくとも 1種以上を主成分とするミ ラー指数 (0 0 2) の格子面の X線回折ロッキングカーブの半値幅が 1 0 0秒以下の高い結晶 性の単結晶薄膜を直接形成しょうとすれば、 焼結体の光醒性を向上させたり、 焼結体纖時 の誠を高温で長時間行い焼結体中の窒化アルミニウム粒子を増大化させたり、 焼結助剤を揮 散させ焼結体の繊を高めるなど、 焼結体材質の改善が必要な場合が多い。 また、 基板の厚み や表面平滑性などによっても形成される単結晶薄膜の結晶性は影響を受け易い。
しかしながら本発明においては、 上記のように窒化ガリウム、 窒化インジウム、 窒化アルミ ニゥムのうちから選ばれた少なくとも 1種以上を主成分とする単結晶、 無定形、 多結晶、 配向 性多結晶のうちから選ばれる少なくともいずれかの結晶状態を有する薄膜を窒化アルミニゥム を主成分とする焼結体からなる基板にあらかじめ形成し、 さらに該単結晶、 無定形、 多結晶、 配向性多結晶のうちから選ばれる少なくともいずれかの結晶状態からなる薄膜の上から窒化ガ リウム、 窒化インジウム、 窒化アルミニウムのうちから選ばれた少なくとも 1種以上からなる 単結晶薄膜を形成することで、 該単結晶薄膜〖雄板として用いる窒化アルミニウムを主成分と する焼結体の光透過性、 焼結体粒子の大きさ、 該焼結体の組成や純度、 など該焼結体の材質、 あるい〖堪板の厚み、 基板の表面平滑性、 基板中の導通ビアの有無、 などに余り影響を受けず にあるいは影響を受けたとしてもより高い結晶性のものが得られ易い。 すなわち本発明におい ては窒化アルミニウムを主成分とする焼結体としてはその材質や難条件などにあまり影響を 受けることなくあるいは影響を受けたとしてもより高レ ^結晶性の単結晶薄膜を形成するための 基板として用いることが可能である。 また言い換えれば、 窒化アルミニウムを主成分とする焼 結体からなる基板にあらかじめ窒化ガリウム、 窒化インジウム、 窒化アルミニウムのうちから 選ばれた少なくとも 1種以上を主成分とする無定形、 多結晶、 配向性多結晶、 単結晶のうちか ら選ばれる少なくともいずれかの結晶状態を有する薄膜を形成することは、該無定形、多結晶、 配向性多結晶、 単結晶のうちから選ばれる少なくともいずれかの結晶状態からなる薄膜の上か らさらに形成される窒化ガリウム、 窒化インジウム、 窒化アルミニウムのうちから選ばれた少 なくとも 1種以上を主成分とする単結晶薄膜の結晶性を向上させる効果があると云える。 この ような効果〖堪板として用いる窒化アルミ二ゥムを主成分とする焼結体の光醒性、 該焼結体 立子の大きさ、 該焼結体の組成や純度、 など焼結体の材質、 あるいは基板の厚み、 基板の表面 平滑性、 基板中の導通ビアの有無、 などに余り影響されずに発現され得る。
もちろん上記のように例えば窒化アルミニウムを主成分とする焼結体が高い ¾¾i率を有す るもの、 該焼結体製造時の誠を高温で長時間行い焼結体中の窒化アルミニウム粒子の大きさ が増大化したもの、 焼結助剤を揮散させ難結体の! ^を高めたもの、 などを基板として用い た場合などもともと該基板には窒化ガリウム、 窒化インジウム、 窒化アルミニウムのうちから 選ばれた少なくとも 1種以上を主成分とするミラー指数 (0 0 2 ) の格子面の X線回折ロッキ ングカーブの半値幅が 1 0 0秒以下を有する単結晶薄膜が ¾:接形成できるが、 このような窒化 アルミニウムを主成分とする焼結体からなる基板を用いた場合でも該基板にあらかじめ窒化ガ
リウム、 窒化インジウム、 窒化アルミニウムのうちから選ばれた少なくとも 1種以上を主成分 とする単結晶、 無定形、 多結晶、 配向性多結晶のうちから選ばれる少なくともいずれかの結晶 状態を有する薄膜を形成し、 さらにその上に窒化ガリウム、 窒化インジウム、 窒化アルミニゥ ムのうちから選ばれた少なくとも 1種以上を主成分とする単結晶薄膜を形成したとき、 該単結 晶薄膜はミラ一指数 (0 0 2) の格子面の X線回折ロッキングカーブの半値幅は少なくとも 1 0 0秒以下のものが形成し得る。
別の見方をすれば、 もともと窒化ガリウム、 窒化インジウム、 窒化アルミニウムのうちから 選ばれた少なくとも 1種以上を主成分とする単結晶薄膜のミラー指数 ( 0 0 2) の格子面の X 線回折ロッキングカーブの半値幅が少なくとも 1 0 0秒以下の結晶性で直接形成し得る窒化ァ ルミ二ゥムを主成分とする焼結体は、 あらかじめ窒化ガリウム、 窒化インジウム、 窒化アルミ ニゥムのうちから選ばれた少なくとも 1種以上を主成分とする単結晶、 無定形、 多結晶、 配向 性多結晶のうちから選ばれる少なくともいずれかの結晶状態を有する薄膜を形成しなくても、 どのような方法であっても窒化ガリウム、 窒化インジウム、 窒化アルミニウムのうちから選ば れた少なくとも 1種以上を主成分とする上記のような結晶性に優れた単結晶薄膜を形成し得る ので単結晶薄膜を形成するための基板として優れた特性を有していると云える。
上記のように、 本発明においては窒化アルミニウムを主成分とする焼結体からなる基板には 窒化ガリウム、 窒化インジウム、 窒化アルミニウムのうちから選ばれた少なくとも 1種以上を 主成分とする単結晶薄膜を直接形成することができ形成された該単結晶薄膜の結晶性は高いが、 上記のように該窒化アルミニウムを主成分とする焼結体からなる基板にあらかじめ単結晶、 無 定形、 多結晶、 配向性多結晶のうちから選ばれる少なくともいずれかの結晶状態を有する薄膜 を形成し該単結晶、 無定形、 多結晶、 配向性多結晶のうちから選ばれる少なくともいずれかの 結晶状態を有する薄膜の上からさらに単結晶薄膜を形成すれば該単結晶薄膜の結晶性はさらに 向上し易くなる。
窒化アルミニウムを主成分とする焼結体からなる基板にあらかじめ形成する上記窒化ガリウ ム、 窒化インジウム、 窒化アルミニウムのうちから選ばれた少なくとも 1種以上を主成分とす る薄膜の中で単結晶よりも無定形、 多結晶、 配向性多結晶のうちから選ばれる少なくともいず れかの結晶状態を有する薄膜を用いる方がその上に形成される単結晶薄膜の結晶性をより向上 させる効果が大きい。 すなわち、 窒化アルミニウムを主成分とする焼結体からなる基板にあら かじめ窒化ガリウム、 窒化インジウム、 窒化アルミニウムのうちから選ばれた少なくとも 1種 以上を主成分とする無定形、 多結晶、 配向性多結晶のうちから選ばれる少なくともいずれかの 結晶状態を有する薄膜を形成し、 さらに^結晶状態を有する薄膜の上に窒化ガリウム、 窒化ィ ンジゥム、 窒化アルミニウムのうちから選ばれた少なくとも 1種以上を主成分とする単結晶薄 膜を形成したとき該単結晶薄膜のミラ一指数 ( 0 0 2 ) の格子面の X線回折ロッキングカーブ の半値幅は容易に 1 0 0秒以下の高い結晶性のものが得られ易い。 一方、 窒化アルミニウムを 主成分とする焼結体からなる基板にあらかじめ窒化ガリウム、 窒化インジウム、 窒化アルミ二 ゥムのうちから選ばれた少なくとも 1種以上を主成分とする単結晶状態の薄膜を形成し、 さら に該単結晶状態の薄膜の上に窒化ガリウム、 窒化インジウム、 窒化アルミニウムのうちから選 ばれた少なくとも 1種以上を主成分とする単結晶薄膜を形成したとき該単結晶薄膜のミラー指 数 (0 0 2) の格子面の X線回折ロッキングカーブの半値幅は 1 0 0秒以下のものが得られる 場合もあるが必ずしも 1 0 0秒以下の高い結晶性のものが得られるとは限らず、 条件によって は 1 0 0秒以上ものが形成される場合がある。 その理由は必ずしも明確でないが、 通常窒化ァ ルミ二ゥムを主成分とする焼結体からなる基板に直接形成した状態の単結晶薄膜の表面平滑性 板に直接形成した状態の無定形、 多結晶、 配向性多結晶の結晶状態を有する薄膜より小さ い (表面粗さが大きい) ±易合が多いので、 おそらくこのような基板表面に存在する微細な凹凸
が生じ易くそのため形成条件によつてはその上に成長する単結晶薄膜の結晶方位に歪みが生じ 易くなるためではないかと本願発明者は推測している。
本発明において、 窒化アルミニウムを主成分とする焼結体からなる基板にあらかじめ形 る単結晶、 無定形、 多結晶、 配向性多結晶のうちから選ばれる少なくともいずれかの結晶状態 を有する薄膜のうち無定形、 多結晶、 配向性多結晶のうちから選ばれる少なくともいずれかの 結晶状態を有する薄膜を形成し、 該薄膜の上からさらに単結晶薄膜を形成すれば表面平滑性に より優れた単結晶薄膜が得られ易いので好ましい。 すなわち、 窒化アルミニウムを主成分とす る焼結体からなる基板にあらかじめ形成する薄膜が単結晶の場合、 該単結晶薄膜の上からさら に形成される単結晶薄膜の平均表面粗さ R aは通常 3 nmより大きくなり易いのに対して、 窒 化アルミニウムを主成分とする焼結体からなる基板にあらかじめ形成する薄膜が無定形、 多結 晶、配向性多結晶のうちから選ばれる少なくともいずれかの結晶状態を有するものである場合、 該無定形、 多結晶、 配向性多結晶のうちから選ばれる少なくともいずれかの結晶状態を有する 薄膜の上からさらに形成される単結晶薄膜の平均表面粗さ R a«®常少なくとも 3 nm以下に なり易い。 また、 窒化アルミニウムを主成分とする焼結体からなる基板にあらかじめ直接形成 する単結晶、 無定形、 多結晶、 配向性多結晶のうちから選ばれる少なくともいずれかの結晶状 態を有する薄膜のうち配向性多結晶薄膜を形成し、 該配向性多結晶薄膜の上からさらに単結晶 薄膜を形成すれば該単結晶薄膜の表面平滑性としてはさらに優れたものが得られ易いので好ま しい。 すなわち、 窒化アルミニウムを主成分とする焼結体からなる基板にあらかじめ形成する 各種結晶状態の薄膜のうち無定形薄膜及 ϋ 結晶薄膜の場合、 該無定形薄膜及 結晶薄膜の 上からさらに形成される単結晶薄膜の平均表面粗さ R a \m 2 nmより大きくなり易いのに 対して、 窒化アルミニウムを主成分とする焼結体からなる基板にあらかじめ形成する薄膜が配 向性多結晶の場合、 該配向性多結晶薄膜の上からさらに形成される単結晶薄膜の平均表面粗さ R aは少なくとも 2 nm以下になり易く、 通常は 1. 5 nm以下になり易く、 さらに 1. O n m以下のものも比較的容易に得られ易い。 このように R a 2 nm以下の単結晶薄膜をそのまま 発光素子などを構成する薄麵の一部として用いる、 あるいは R a 2 nm以下の単結晶薄膜が 形成された薄膜基板を用いてその上に発光素子などを形成すれば発光効率などの特性がより優 れたものが製造できるという効果がある。
上記のように窒化アルミニウムを主成分とする焼結体からなる基板にあらかじめ形成する窒 化ガリウム、 窒化インジウム、 窒化アルミニウムのうちから選ばれた少なくとも 1種以上を主 成分とする薄膜の中で単結晶よりも無定形、 多結晶、 配向性多結晶のうちから選ばれる少なく ともいずれかの結晶状態を有する薄膜を用いる方が好ましいことを説明した。 さらに本発明に おいては、 窒化アルミニウムを主成分とする焼結体からなる基板にあらかじめ形成する窒化ガ リウム、 窒化インジウム、 窒化アルミニウムのうちから選ばれた少なくとも 1種以上を主成分 とする無定形、 多結晶、 配向性多結晶のうちから選ばれる少なくともいずれかの結晶状態を有 する薄膜の中で配向性多結晶薄膜を用いるほうがより好ましい。 その理由は上記のように、 窒 化アルミニウムを主成分とする焼結体からなる基板にあらかじめ形成する窒化ガリウム、 窒化 インジウム、 窒化アルミニウムのうちから選ばれた少なくとも 1種以上を主成分とする薄膜が 配向性多結晶である場合、 さらにその上に形成される単結晶薄膜の表面平滑性が無定形、 多結 晶状態の薄膜よりも優れたものが得易く、 また該単結晶薄膜の結晶性もより優れたものが得易 いためである。 通常少なくとも同じ窒化アルミニウムを主成分とする焼結体からなる基板を用 ぃ該基板にあらかじめ窒化ガリゥム、 窒化ィンジゥム、 窒化アルミニウムのうちから選ばれた 少なくとも 1種以上を主成分とする配向性多結晶の薄膜を形成した場合、 該配向性多結晶薄膜 の上からさらに形成される単結晶薄膜の結晶性はあらかじめ形成される薄膜が無定形、 多結晶 のものよりも優れたものが得易い。
例えば、 窒化アルミニウムを主成分とする焼結体からなる基板にあらかじめ窒化ガリゥム、 窒化インジウム、 窒化アルミニウムのうちから選ばれた少なくとも 1種以上を主成分とする単 結晶、 無定形、 多結晶、 配向性多結晶のうちから選ばれる少なくともいずれかの結晶状態を有 する薄膜を形成した薄膜基板の上にェピタキシャル成長した窒化ガリゥム、 窒化ィンジゥム、 窒化アルミニウムのうちから選ばれた少なくとも 1種以上を主成分とする薄膜により発光素子 を作製していく場合、 あるいは窒化アルミニウムを主成分とする焼結体からなる基板にあらか じめ窒化ガリウム、 窒化インジウム、 窒化アルミニウムのうちから選ばれた少なくとも 1種以 上を主成分とする単結晶、 無定形、 多結晶、 配向性多結晶のうちから選ばれる少なくともいず れかの結晶状態を有する薄膜を形成し、該薄膜の上からさらに窒化ガリゥム、窒化ィンジゥム、 窒化アルミニウムのうちから選ばれた少なくとも 1種以上を主成分とする単結晶薄膜を形成し た薄膜基板の上にェピタキシャル成長した窒化ガリウム、 窒化インジウム、 窒化アルミニウム のうちから選ばれた少なくとも 1種以上を主成分とする薄膜により発光素子を作製していく場 合、 などあらかじめ形成する薄膜が単結晶のものより無定形、 多結晶、 配向性多結晶のうちか ら選ばれる少なくともいずれかの結晶状態を有する方がより発光効率などの優れたものが得易 く、 あらかじめ形成する薄膜が無定形、 多結晶のうちから選ばれる少なくともいずれかの結晶 状態を有するものより配向性多結晶である方がさらに発光効率などの優れたものが得易い。 また、 このような効果は窒化アルミニゥムを主成分とする焼結体を基板として用いた場合だ けでなく、 炭化珪素、 窒化珪素、 窒化ガリウム、 酸化亜鉛、 酸化ベリリウムなどの六方晶結晶 系及び酸化アルミ二ゥムなどの三方晶結晶系あるいは六方晶系として分類できる結晶系を有す る各種セラミック材料を主成分とする焼結体を基板として用いた場合でも同様である。 すなわ ち、 炭化珪素、 窒化珪素、 窒化ガリウム、 酸化亜鉛、 酸化ベリリウムなどの六方晶結晶系及び 酸化アルミニウムなどの三方晶結晶系あるいは六方晶系として分類できる結晶系を有する各種 セラミツク材料を主成分とする焼結体からなる基板に窒化ガリゥム、 窒化インジウム、 窒化ァ ルミニゥムのうちから選ばれた少なくとも 1種以上を主成分とする単結晶、 無定形、 多結晶、 配向性多結晶のうちから選ばれる少なくともいずれかの結晶状態を有する薄膜をあらかじめ形 成し、 さらにその上に窒化ガリウム、 窒化インジウム、 窒化アルミニウムのうちから選ばれた 少なくとも 1種以上を主成分とする単結晶薄膜を形成したとき、該単結晶薄膜はミラー指数 (0 0 2) の格子面の X線回折ロッキングカーブの半値幅が少なくとも 3 0 0秒以下のものが形成 できるだけでなくさらに 2 0 0秒以下と高い結晶性のものが形成し得る。 また、 このような薄 騰成は、 炭化珪素、 窒化珪素、 窒化ガリウム、 酸化亜鉛、 酸化ベリリウムなどの六方晶結晶 系及び酸化アルミニウムなどの三方晶結晶系あるいは六方晶系として分類できる結晶系を有す る各種セラミック材料を主成分とする焼結体からなる基板に窒化ガリゥム、 窒化ィンジゥム、 窒化アルミニウムのうちから選ばれた少なくとも 1種以上を主成分とする単結晶、 無定形、 多 結晶、 配向性多結晶のうちから選ばれる少なくともいずれかの結晶状態を有する薄膜をあらか じめ形成し、 その上に窒化ガリウム、 窒化インジウム、 窒化アルミニウムのうちから選ばれた 少なくとも 1種以上からなる単結晶、 無定形、 多結晶、 配向性多結晶のうちから選ばれる少な くともいずれかの結晶状態を有する薄膜を合計 2層あらかじめ形成した基板を用い、 この基板 にさらに窒化ガリゥム、 窒化ィンジゥム、 窒化アルミニゥムのうちから選ばれた少なくとも 1 種以上を主成分とする単結晶薄膜を形成した場合でも、 2層目あるいは 3層目に形成される単 結晶薄膜はミラ一指数 ( 0 0 2 ) の格子面の X線回折ロッキングカーブの半値幅が少なくとも 3 0 0秒以下のものが形成できるだけでなくさらに 2 0 0秒以下と高い結晶性のものが形成し 得る。 このような効果は炭化珪素、 窒化珪素、 窒化ガリウム、 酸化亜鉛、 酸化ベリリウムなど の六方晶結晶系及び酸化アルミ二ゥムなどの三方晶結晶系あるいは六方晶系として分類できる 結晶系を有する各種セラミック材料を主成分とする焼結体からなる基板に窒ィ匕ガリゥム、 窒化
インジウム、窒化アルミニウムのうちから選ばれた少なくとも 1種以上を主成分とする単結晶、 無定形、 多結晶、 配向性多結晶のうちから選ばれる少なくともいずれかの結晶状態を有する薄 膜をあらかじめ 1層あるいは 2層だけ形成した場合だけでなく、 さらにあらかじめ合計 3層以 上形成したものを基板として用いた場合でも同様に得られる。 すなわち窒化ガリウム、 窒化ィ ンジゥム、 窒化アルミニウムのうちから選ばれた少なくとも 1種以上を主成分とする単結晶、 無定形、 多結晶、 配向性多結晶のうちから選ばれる少なくともいずれかの結晶状態を有する薄 膜をあらかじめ 3層以上形成した炭化珪素、 窒化珪素、 窒化ガリウム、 酸化碰、 酸化べリリ ゥムなどの六方晶結晶系及び 化アルミ二ゥムなどの三方晶結晶系あるいは^晶系として分 類できる結晶系を有する各種セラミック材料を主成分とする焼結体からなる基板の上にさらに 窒化ガリウム、 窒化インジウム、 窒化アルミニウムのうちから選ばれた少なくとも 1種以上を 主成分とする単結晶薄膜を形成したとき、 該単結晶薄膜はミラ一指数 (0 0 2) の格子面の X 線回折ロッキングカーブの半値幅が少なくとも 3 0 0秒以下のものが形成できるだけでなくさ らに 2 0 0秒以下と高い結晶性のものが形成し得る。
前記のように炭化珪素、 窒化珪素、 窒化ガリウム、 酸化亜鈴、 酸化ベリリウムなどの六方晶 結晶系及び酸化アルミ二ゥムなどの三方晶結晶系あるいは六方晶系として分類できる結晶系を 有する各種セラミック材料を主成分とする焼結体からなる基板に例えば窒化ガリウム、 窒化ィ ンジゥム、 窒化アルミニウムのうちから選ばれた少なくとも 1種以上を主成分とするミラ一指 数 (0 0 2) の格子面の X線回折ロッキングカーブの半値幅が 2 0 0秒以下の高い結晶性の単 結晶薄膜を直接形成しょうとすれば、 例えば焼結体中の結晶粒子の大きさを大きくする、 光透 過性の焼結体を用いる、 基板の表面平滑性を向上させる、 形成する単結晶薄膜の厚みを増大さ せる、 などの工夫によっても通常困難な塲合が多い。
しかしながら本発明においては、 上記のように窒化ガリウム、 窒化インジウム、 窒化アルミ ニゥムのうちから選ばれた少なくとも 1種以上を主成分とする単結晶、 無定形、 多結晶、 配向 性多結晶のうちから選ばれる少なくともいずれかの結晶状態を有する薄膜を炭化珪素、 窒化珪 素、 窒化ガリウム、 酸化亜鉛、 酸化ベリリウムなどの 晶結晶系及び 化アルミニウムなど の三方晶結晶系あるいは六方晶系として分類できる結晶系を有する各種セラミック材料を主成 分とする焼結体からなる基板にあらかじめ形成し、 さらにその上に窒化ガリウム、 窒化インジ ゥム、 窒化アルミニウムのうちから選ばれた少なくとも 1種以上からなる単結晶薄膜を形成す ることで、 該単結晶薄膜《S板として用いる焼結体の結晶粒子の大きさ、 基板の表面平滑性、 薄膜の厚みなどに余り影響を受けずにあるいは影響を受けたとしてもより高い結晶性のものが 得られ易い。すなわち本発明において》¾扳として用いる炭化珪素、窒化珪素、窒化ガリウム、 酸化碰、 酸化ベリリウムなどの六方晶結晶系及び ¾化アルミニウムなどの三方晶結晶系ある いは六方晶系として分類できる結晶系を有する各種セラミック材料を主成分とする焼結体の材 質や、 該焼結体を基板として用いたとき表面平滑性など基板の性状などにあまり影響を受ける ことなくあるいは影響を受けたとしてもより高い結晶性の単結晶薄膜を形成すること力河能で ある。
上記のように、 本発明においては炭化珪素、 窒化珪素、 窒ィ匕ガリウム、 酸化亜鉛、 酸化ベリ リゥムなどの六方晶結晶系及び 化アルミニウムなどの三方晶結晶系あるいは六方晶系として 分類できる結晶系を有する各種セラミック材料を主成分とする焼結体に窒化ガリウム、 窒化ィ ンジゥム、 窒化アルミニウムのうちから選ばれた少なくとも 1種以上を主成分とする単結晶薄 膜を直接形成することができまた該単結晶薄膜の結晶性は高いものが形成し得るが、 上記のよ うに炭化珪素、 窒化珪素、 窒化ガリウム、 酸化亜鉛、 酸化ベリリウムなどの六方晶結晶系及び 酸化アルミニウムなどの三方晶結晶系あるいは六方晶系として分類できる結晶系を有する各種 セラミック材料を主成分とする焼結体からなる基板にあらかじめ単結晶、 無定形、 多結晶、 配
向性多結晶のうちから選ばれる少なくともいずれかの結晶状態を有する薄膜を形成したものを 用い、 この基板に単結晶薄膜を形成すればこの単結晶薄膜の結晶性はさらに向上し易くなる。 炭化珪素、 窒化珪素、 窒化ガリウム、 酸化碰、 酸化ベリリウムなどの六方晶結晶系及び酸 化アルミニウムなどの三方晶結晶系あるいは六方晶系として分類できる結晶系を有する各種セ ラミツク材料を主成分とする焼結体にあらかじめ形成する上記窒化ガリゥム、窒化ィンジゥム、 窒化アルミニウムのうちから選ばれた少なくとも 1種以上を主成分とする薄膜の中で単結晶よ りも無定形、 多結晶、 配向性多結晶のうちから選ばれる少なくともいずれかの結晶状態を有す る薄膜を用いる方が該薄膜の上に形成される単結晶薄膜の結晶性をより向上させる効果が大き いのでより好ましい。 すなわち、 炭化珪素、 窒化珪素、 窒化ガリウム、 酸化亜鉛、 酸化べリリ ゥムなどの六方晶結晶系及び 化アルミニウムなどの三方晶結晶系あるいは六方晶系として分 類できる結晶系を有する各種セラミック材料を主成分とする焼結体からなる基板に窒化ガリゥ ム、 窒化インジウム、 窒化アルミニウムのうちから選ばれた少なくとも 1種以上を主成分とす る無定形、 多結晶、 配向性多結晶のうちから選ばれる少なくともいずれかの結晶状態を有する 薄膜をあらかじめ形成し、 その上に窒化ガリウム、 窒化インジウム、 窒化アルミニウムのうち から選ばれた少なくとも 1種以上を主成分とする単結晶薄膜を形成したとき該単結晶薄膜のミ ラー指数 (0 0 2) の格子面の X線回折ロッキングカーブの半値幅は容易に 2 0 0秒以下の高 い結晶性のものが得られ易い。 一方、 炭化珪素、 窒化珪素、 窒化ガリウム、 酸化亜鉛、 酸化べ リリウムなどの六方晶結晶系及び酸化アルミニウムなどの三方晶結晶系あるいは六方晶系とし て分類できる結晶系を有する各種セラミック材料を主成分とする焼結体からなる基板に窒化ガ リウム、 窒化インジウム、 窒化アルミニウムのうちから選ばれた少なくとも 1種以上を主成分 とする単結晶薄膜をあらかじめ形成し、 その上に窒化ガリウム、 窒化インジウム、 窒化アルミ ニゥムのうちから選ばれた少なくとも 1種以上を主成分とする単結晶薄膜を形成したとき該単 結晶薄膜のミラ一指数 ( 0 0 2 ) の格子面の X線回折ロッキングカーブの半値幅は必ずしも 2 0 0秒以下の高い結晶性のものが得られるとは限らず、 条件によっては 2 0 0秒以上のものが 形成される場合がある。 その理由は必ずしも明確でないが、 通常炭化珪素、 窒化珪素、 窒化ガ リウム、 酸化亜鉛、 酸化ベリリウムなどの六方晶結晶系及び 化アルミニウムなどの三方晶結 晶系あるいは六方晶系として分類できる結晶系を有する各種セラミック材料を主成分とする焼 結体からなる基板に直接形成した状態の単結晶薄膜の表面平滑性は、 あらかじめ基板に形成し た無定形、 多結晶、 配向性多結晶のうちから選ばれる少なくともいずれかの結晶状態を有する 薄膜より小さい (表面粗さが大きい) 場合が多いので、 おそらくこのような基板表面に存在す る微細な凹凸が生じ易くそのため形成条件によつてはその上に成長する単結晶薄膜の結晶方位 に歪みが生じ易くなるためではないかと本願発明者は推測している。
また、 炭化珪素、 窒化珪素、 窒化ガリウム、 酸化赚、 酸化ベリリウムなどの六方晶結晶系 及び酸化アルミニウムなどの三方晶結晶系あるいは六方晶系として分類できる結晶系を有する 各種セラミツク材料を主成分とする焼結体にあらかじめ形成する上記窒化ガリゥム、 窒化ィン ジゥム、 窒化アルミニウムのうちから選ばれた少なくとも 1種以上を主成分とする薄膜の中で 無定形及 結晶よりも配向性多結晶の結晶状態を有する薄膜を用いる方がその上に形成され る単結晶薄膜の結晶性をより向上させる効果が大きいのでさらに好ましい。 すなわち、 窒化ガ リウム、 窒化インジウム、 窒化アルミニウムのうちから選ばれた少なくとも 1種以上を主成分 とする配向性多結晶の結晶状態を有する薄膜があらかじめ形成された炭化珪素、 窒化珪素、 窒 化ガリウム、 酸化亜鉛、 酸化ベリリウムなどの六方晶結晶系及び 化アルミニウムなどの三方 晶結晶系あるいは六方晶系として分類できる結晶系を有する各種セラミック材料を主成分とす る焼結体からなる基板を用いたとき、 その上に形成される単結晶薄膜のミラ一指数 ( 0 0 2) の格子面の X線回折ロッキングカーブの半値幅は容易に 1 5 0秒以下の高い結晶性のものが得
られ易い。 一方、 窒化ガリウム、 窒化インジウム、 窒化アルミニウムのうちから選ばれた少な くとも 1種以上を主成分とする無定形状態及び多結晶状態の薄膜があらかじめ形成された炭化 珪素、 窒化珪素、 窒化ガリウム、 酸化亜鉛、 酸化ベリリウムなどの六方晶結晶系及び 匕アル ミニゥムなどの三方晶結晶系あるいは六方晶系として分類できる結晶系を有する各種セラミツ ク材料を主成分とする焼結体からなる基板を用いたときは、 その上に形成される単結晶薄膜の ミラ一指数 (0 0 2) の格子面の X線回折ロッキングカーブの半値幅は必ずしも 1 5 0秒以下 の高い結晶性のものが得られるとは限らない。 その理由は必ずしも明確でないが、 通常炭化珪 素、 窒化珪素、 窒化ガリウム、 酸化亜鉛、 謝匕ベリリウムなどの六方晶結晶系及び 化アルミ 二ゥムなどの三方晶結晶系あるいは六方晶系として分類できる結晶系を有する各種セラミック 材料を主成分とする焼結体からなる基板に直接形成した無定形薄廠 結晶薄膜の表面平滑 性 W¾板に直接形成した配向性多結晶薄膜より小さい (表面粗さが大きい) 場合が多いので、 おそらくこのような基板表面に存在する微細な凹凸が生じ易くそのため形成条件によってはそ の上に成長する単結晶薄膜の結晶方位に歪みが生じ易くなるためではないかと本願発明者は推 測している。
例えば、 炭化珪素、 窒化珪素、 窒化ガリウム、 酸化亜鉛、 酸化ベリリウムなどの六方晶結晶 系及び 化アルミ二ゥムなどの三方晶結晶系あるレは六方晶系として分類できる結晶系を有す る各種セラミック材料を主成分とする焼結体からなる基板にあらかじめ窒化ガリゥム、 窒化ィ ンジゥム、 窒化アルミニウムのうちから選ばれた少なくとも 1種以上を主成分とする単結晶、 無定形、 多結晶、 配向性多結晶のうちから選ばれる少なくともいずれかの結晶状態を有する薄 膜を形成した薄膜基板の上に窒化ガリウム、 窒化インジウム、 窒化アルミニウムのうちから選 ばれた少なくとも 1種以上を主成分とするェピタキシャル成長した薄膜により発光素子を作製 していく場合、 あるいは炭化珪素、 窒化珪素、 窒化ガリウム、 酸化亜鉛、 酸化ベリリウムなど の 晶結晶系及び酸化アルミニウムなどの三方晶結晶系あるいは六方晶系として分類できる 結晶系を有する各種セラミック材料を主成分とする焼結体からなる基板にあらかじめ窒化ガリ ゥム、 窒化インジウム、 窒化アルミニウムのうちから選ばれた少なくとも 1種以上を主成分と する単結晶、 無定形、 多結晶、 配向性多結晶のうちから選ばれる少なくともいずれかの結晶状 態を有する薄膜を形成し、 該薄膜の上からさらに窒化ガリウム、 窒化インジウム、 窒化アルミ ニゥムのうちから選ばれた少なくとも 1種以上を主成分とする単結晶薄膜を形成して得られる 薄膜基板を用いて、 その上に窒化ガリウム、 窒化イン'ジゥム、 窒化アルミニウムのうちから選 ばれた少なくとも 1種以上を主成分とするェピタキシャル成長した薄膜により発光素子を作製 していく場合、 などあらかじめ形成する薄膜が単結晶のものより無定形、 多結晶、 配向性多結 晶のうちから選ばれる少なくともいずれかの結晶状態を有するものの方がより発光効率などの 特性に優れたものが得易く、 あらかじめ形成する薄膜が無定形及 結晶のものより配向性多 結晶の結晶状態である方がさらに発光効率などの特性に優れたものが得易い。
上記のように窒化アルミニウムを主成分とする焼結体、 あるいは炭化珪素、 窒化珪素、 窒化 ガリウム、 酸化亜鉛、 酸化べリリウムなどの六方晶結晶系及び 化アルミ二ゥムなどの三方晶 結晶系あるいは六方晶系として分類できる結晶系を有する各種セラミック材料を主成分とする 焼結体からなる基板にあらかじめ窒化ガリウム、 窒化インジウム、 窒化アルミニウムのうちか ら選ばれた少なくとも 1種以上を主成分とする単結晶、 無定形、 多結晶、 配向性多結晶のうち から選ばれる少なくともいずれかの結晶状態を有する薄膜を形成し、 さらにその上に窒化ガリ ゥム、 窒化インジウム、 窒化アルミニウムのうちから選ばれた少なくとも 1種以上を主成分と する単結晶薄膜を形成すれば結晶性に優れた単結晶薄膜が容易に形成できる。
本発明においては通常前記のように窒化アルミニゥムを主成分とする焼結体及び炭化珪素、 窒化珪素、 窒化ガリウム、 酸化亜鉛、 酸化ベリリウムなどの六方晶結晶系及び 化アルミニゥ
ムなどの三方晶結晶系あるいは六方晶系として分類できる結晶系を有する各種セラミック材料 を主成分とする焼結体からなる基板には窒化ガリウム、 窒化インジウム、 窒化アルミニウムの うちから選ばれた少なくとも 1種以上を主成分とする単結晶薄膜を直接形成できるが、 該基板 に直接形成した単結晶薄膜の結晶性は前記のように基板として用いる焼結体の組成、 焼結体の 光透過性、 焼結体中の結晶粒子の大きさ、 基板の表面平滑性などにより影響を受ける。
しかしながら一方において上記のように、 窒化アルミニウムを主成分とする焼結体及び炭化 珪素、 窒化珪素、 窒化ガリウム、 酸化 、 酸化ベリリウムなどの六方晶結晶系及び 化アル ミニゥムなどの三方晶結晶系あるいは六方晶系として分類できる結晶系を有する各種セラミツ ク材料を主成分とする焼結体からなる基板にあらかじめ窒化ガリウム、 窒化インジウム、 窒化 アルミニウムのうちから選ばれた少なくとも 1種以上を主成分とする無定形、 多結晶、 配向性 多結晶、 単結晶のうちから選ばれる少なくともいずれかの結晶状態を有する薄膜を形成し、 さ らにその上に窒化ガリウム、 窒化インジウム、 窒化アルミニウムのうちから選ばれた少なくと も 1種以上を主成分とする単結晶薄膜を形成することにより窒化アルミニウムを主成分とする 焼結体及び炭化珪素、 窒化珪素、 窒化ガリウム、 酸化亜鉛、 酸化ベリリウムなどの六方晶結晶 系及び酸化アルミニウムなどの三方晶結晶系あるいは六方晶系として分類できる結晶系を有す る各種セラミック材料を主成分とする焼結体からなる基板の表面平滑性や焼結体中の結晶粒子 の大きさなどにあまり影響されることなくあるいは影響を受けたとしてもより高い結晶性の単 結晶薄膜を比較的容易に形成することが可能となる。
また、 本発明においては窒化アルミニウムを主成分とする焼結体及び炭化珪素、 窒化珪素、 窒化ガリウム、 酸化亜鉛、 酸化ベリリウムなどの六方晶結晶系及び ¾化アルミニウムなどの三 方晶結晶系あるいは六方晶系として分類できる結晶系を有する各種セラミック材料を主成分と する焼結体からなる基板表面の平滑性が例えば焼き放し (a s— f i r e) 状態、 ラッフ Iff磨 状態、 鏡面研磨状態、 ブラスト研磨状態など、 どのようなものであっても、 あるいは基板の表 面状態がその他例えば研削加工、 研磨加工、 溝切り加工などによってどのようなものであった としても、 上記のようにあらかじめ窒化ガリウム、 窒化インジウム、 窒化アルミニウムのうち から選ばれた少なくとも 1種以上を主成分とする無定形、 多結晶、 配向性多結晶、 単結晶のう ちから選ばれる少なくともいずれかの結晶状態を有する薄膜を形成すれば、 該基板には結晶性 の高い単結晶薄膜が比較的容易に形成できる。 すなわち、 基板表面の平滑性が小さい、 すなわ ち平均表面粗さ R aが大きい基板であっても上記のようにあらかじめ窒化ガリゥム、 窒化ィン ジゥム、 窒化アルミニウムのうちから選ばれた少なくとも 1種以上を主成分とする無定形、 多 結晶、 配向性多結晶、 単結晶のうちから選ばれる少なくともいずれかの結晶状態を有する薄膜 を形成することにより該基板には結晶性の高い単結晶薄膜が比較的容易に形成できる。
通常窒化アルミニウムを主成分とする焼結体からなる基板の場合例えば焼き放し (a s— ί i r e) の表面、 あるいはラッフ ¾ff磨、 ブラスト研磨などの加工を施した表面など平均表面粗 さ R aが 2 0 0 O nmより大きい基板には窒化ガリウム、 窒化インジウム、 窒化アルミニウム のうちから選ばれた少なくとも 1種以上を主成分とする単結晶薄膜が直接形成できないことが 多いが、 該基板に上記のようにあらかじめ窒化ガリウム、 窒化インジウム、 窒化アルミニウム のうちから選ばれた少なくとも 1種以上を主成分とする無定形、 多結晶、 配向性多結晶、 単結 晶のうちから選ばれる少なくともいずれかの結晶状態を有する薄膜を形成することにより、 平 均表面粗さ R aが 2 0 0 O nmより大きい基板であっても窒化ガリウム、 窒化インジウム、 窒 化アルミニウムのうちから選ばれた少なくとも 1種以上を主成分とする単結晶薄膜のミラ一指 数 (0 0 2) の格子面の X線回折ロッキングカーブの半値幅 3 0 0秒以下の結晶性に優れた単 結晶薄膜が比較的容易に形成し得る。 また、 炭化珪素、 窒化珪素、 窒化ガリウム、 酸化亜鉛、 酸化ベリリゥムなどの六方晶結晶系及び ¾化アルミニウムなどの三方晶結晶系あるいは 71 ^晶
系として分類できる結晶系を有する各種セラミック材料を主成分とする焼結体からなる基板の 場合では例えば焼き放し (a s— f i r e) の表面、 あるいはラップ研磨、 ブラスト研磨など の加工を施した表面など平均表面粗さ R aが 1 0 0 0 nmより大きい基板には窒化ガリウム、 窒化インジウム、 窒化アルミニウムのうちから選ばれた少なくとも 1種以上を主成分とする単 結晶薄膜が直接形成できないことが多いが、 該基板に上記のようにあらかじめ窒化ガリゥム、 窒化インジウム、 窒化アルミニウムのうちから選ばれた少なくとも 1種以上を主成分とする無 定形、 多結晶、 配向性多結晶、 単結晶のうちから選ばれる少なくともいずれかの結晶状態を有 する薄膜を形成することにより、 平均表面粗さ R aが 1 0 0 O nmより大きい基板であっても 窒化ガリウム、 窒化インジウム、 窒化アルミニウムのうちから選ばれた少なくとも 1種以上を 主成分とする単結晶薄膜のミラー指数 ( 0 0 2 ) の格子面の X線回折ロッキングカーブの半値 幅 3 0 0秒以下の結晶性に優れた単結晶薄膜が比較的容易に形成し得る。
本発明において、 基板として用いる炭化珪素、 窒化珪素、 窒化ガリウム、 酸化亜鉛、 酸化べ リリゥムなどの六方晶結晶系及ぴ谢匕アルミニウムなどの三方晶結晶系あるいは六方晶系とし て分類できる結晶系を有する各種セラミック材料を主成分とする焼結体中の結晶粒子は例えば 0. 5 m程度と成長させずに、 すなわち原料粉末の粒子の大きさと同じ状態で焼結したもの も^ i¾でき、 このような基板の上にはミラ一指数 (0 0 2) の格子面の X線回折ロッキング力 ーブの半値幅 3 6 0 0秒以下の結晶性を有する窒化ガリウム、 窒化インジウム、 窒化アルミ二 ゥムのうちから選ばれた少なくとも 1種以上を主成分とする単結晶薄膜が 接形成し得る。 通 常は平均 1 m以上の結晶粒子からなる能結体が基板として用いられる。すなわち、炭化珪素、 窒化珪素、 窒化ガリウム、 酸化 »、 酸化ベリリウムなどの六方晶結晶系及び酸化アルミニゥ ムなどの三方晶結晶系あるいは六方晶系として分類できる結晶系を有する各種セラミック材料 を主成分とする平均 1 m以上の結晶粒子からなる焼結体を基板として用いたとき該基板には ミラー指数 ( 0 0 2 ) の格子面の X線回折ロッキングカーブの半値幅 3 6 0 0秒以下の結晶性 を有する窒化ガリウム、 窒化インジウム、 窒化アルミニウムのうちから選ばれた少なくとも 1 種以上を主成分とする単結晶薄膜が 接形成し得る。 また、 上記各種セラミック材料を主成分 とする焼結体内部の結晶粒子の大きさが増大化すれば該基板に形成される窒化ガリゥム、 窒化 ィンジゥム、 窒化アルミニウムのうちから選ばれた少なくとも 1種以上を主成分とする薄膜の 結晶性が向上し易い。 すなわち、 上記各種セラミック材料を主成分とする焼結体内部に含まれ る結晶粒子の大きさが平均 5 m以上の焼結体で《S板上に形成される窒化ガリウム、 窒化ィ ンジゥム、 窒化アルミニウムのうちから選ばれた少なくとも 1種以上を主成分とする単結晶薄 膜のミラー指数 ( 0 0 2 ) の格子面の X線回折ロッキングカーブの半値幅が 2 0 0 0秒以下の 結晶性を有するものが ¾:接形成し得る。 また、 上記各種セラミック材料を主成分とする焼結体 内部に含まれる結晶粒子の大きさが平均 8 m以上の焼結体では基板上に形成される窒化ガリ ゥム、 窒化インジウム、 窒化アルミニウムのうちから選ばれた少なくとも 1種以上を主成分と する単結晶薄膜のミラ一指数 (0 0 2 ) の格子面の X線回折ロッキングカーブの半値幅が 1 0 0 0秒以下と良好な結晶性のものが直接形成し得る。 また、 上記各種セラミック材料を主成分 とする焼結体内部に含まれる結晶粒子の大きさが平均 1 5 m以上の焼結体では基板上に形成 される窒化ガリウム、 窒化インジウム、 窒化アルミニウムのうちから選ばれた少なくとも 1種 以上を主成分とする単結晶薄膜のミラ一指数 ( 0 0 2 ) の格子面の X線回折ロッキングカーブ の半値幅が 3 0 0秒以下とより良好な結晶性のものが直接形成し得る。 また、 上記各種セラミ ック材料を主成分とする焼結体内部に含まれる結晶粒子の大きさが平均 2 5 /im以上の焼結体 で 板上に形成される窒化ガリウム、 窒化インジウム、 窒化アルミニウムのうちから選ばれ た少なくとも 1種以上を主成分とする単結晶薄膜のミラ一指数 ( 0 0 2) の格子面の X線回折 ロッキングカーブの半値幅が 2 4 0秒以下とさらに良好な結晶性のものが直接形成し得る。
なお、 上記各種セラミック材料を主成分とする焼結体内部に含まれる結晶粒子の大きさは平 均の大きさであって含まれる結晶粒子が均等に近い大きさに揃っている状態のものだけでなく 結晶粒子の大きさが 揃いのものや結晶粒子の形状がレゝびつで針状あるいは板状など一辺が小 さく他の一辺が大きい形状の結晶粒子、 例えば窒化珪素を主成分とする焼結体において 一 S i 3N4粒子など一辺が数/ で他の一辺が 1 0数/ 以上に大きく成長した針状あるいは板状 などの結晶粒子を含むものであっても本発明においては問題なく用いることができる。 また、 上記各種セラミック材料を主成分とする焼結体内部に含まれる結晶粒子の大きさは、 焼成温度 を高くする、 あるいは焼成時間を長くする、 などの焼成条件を単独で用いるか併用することで 制御することができる。
しかしながら、 本発明においては前記のように、 炭化珪素、 窒化珪素、 窒化ガリウム、 酸化 亜鉛、 酸化ベリリウムなどの六方晶結晶系及び酸化アルミニウムなどの三方晶結晶系あるいは 六方晶系として分類できる結晶系を有する各種セラミック材料を主成分とする焼結体からなる 基板にあらかじめ窒化ガリウム、 窒化インジウム、 窒化アルミニウムのうちから選ばれた少な くとも 1種以上を主成分とする無定形、 多結晶、 配向性多結晶、 単結晶のうちから選ばれる少 なくともいずれかの結晶状態を有する薄膜を形成し、 さらにその上に窒化ガリウム、 窒化イン ジゥム、 窒化アルミニウムのうちから選ばれた少なくとも 1種以上を主成分とする単結晶薄膜 を形成すれば該単結晶薄膜の結晶性は上記各種セラミック材料を主成分とする焼結体中の結晶 立子の大きさや、 該焼結体からなる基板の表面平滑性などに比較的影響を受けずに良好なもの を作製することができる。
上記のように窒化ガリウム、 窒化インジウム、 窒化アルミニウムのうちから選ばれた少なく とも 1種以上を主成分とする無定形、 多結晶、 配向性多結晶、 単結晶など各種結晶状態の薄膜 を形成した基板を用いることでその上には良好な結晶性を有する単結晶薄膜が形成されるが、 本発明において該単結晶薄膜の結晶性をさらに改善することが可能である。 すなわち、 炭化珪 素、 窒化珪素、 窒化ガリウム、 酸化亜鉛、 酸化ベリリウムなどの六方晶結晶系及ぴ衡匕アルミ ニゥムなどの三方晶結晶系あるいは六方晶系として分類できる結晶系を有する各種セラミック 材料を主成分とする焼結体からなる基板の表面平滑性の向上によりさらに改善し得る。 より具 体的に言えば、 上記各種セラミック材料からなる焼結体を用いた基板の平均表面粗さ R aが 1 O nmより大きい場合、 該基板にあらかじめ形成される窒化ガリウム、 窒化インジウム、 窒化 アルミニゥムのうちから選ばれた少なくとも 1種以上を主成分とする配向性多結晶薄膜はミラ 一指数 (0 0 2 ) の格子面の X線回折ロッキングカーブの半値幅が 1 0 0 0 0秒より大きくな り易く、 このような結晶性を有する配向性多結晶薄膜の上に形成される単結晶薄膜はミラー指 数 (0 0 2 ) の格子面の X線回折ロッキングカーブの半値幅は 1 5 0秒より大きくなり易い傾 向を有する。 しかしながら、 上記各種セラミック材料を主成分とする焼結体からなる基板の平 均表面粗さ R aが 1 O nm以下の場合、 該基板にあらかじめ形成される上記配向性多結晶薄膜 のミラ一指数 ( 0 0 2 ) の格子面の X線回折ロッキングカーブの半値幅が 1 0 0 0 0秒以下と なり易く、このような結晶性の配向性多結晶薄膜の上に形成される単結晶薄膜のミラ一指数 (0 0 2) の格子面の X線回折ロッキングカーブの半値幅は 1 5 0秒以下となり易い傾向を有する。 さらに、 炭化珪素、 窒化珪素、 窒化ガリウム、 酸化亜鉛、 酸化ベリリウムなどの六方晶結晶系 及び酸化アルミニウムなどの三方晶結晶系あるいは六方晶系として分類できる結晶系を有する 各種セラミック材料を主成分とする焼結体からなる基板の平均表面粗さ R aが 5 nm以下の場 合、 該基板にあらかじめ形成される上記配向性多結晶薄膜のミラー指数 ( 0 0 2 ) の格子面の X線回折ロッキングカーブの半値幅として 8 0 0 0秒以下となり易く、 このような結晶性の配 向性多結晶薄膜の上に形成される単結晶薄膜のミラー指数 (0 0 2) の格子面の X線回折ロッ キングカーブの半値幅は 1 3 0秒以下となり易い傾向を有し、 通常は 1 2 0秒以下となり易い
傾向がある。 上記炭化珪素、 窒化珪素、 窒化ガリウム、 酸化亜鉛、 酸化ベリリウムなどの六方 晶結晶系及び酸化アルミニウムなどの三方晶結晶系あるいは六方晶系として分類できる結晶系 を有する各種セラミック材料を主成分とする焼結体からなる基板の平均表面粗さ R aが 5 nm 以下の場合、 該基板にあらかじめ形成される窒化ガリウム、 窒化インジウム、 窒化アルミニゥ ムのうちから選ばれた少なくとも 1種以上を主成分とする薄膜のうち無定形、 多結晶、 単結晶 のうちから選ばれる少なくともいずれかの結晶状態を有するものもその上に形成される単結晶 薄膜のミラ一指数 (0 0 2) の格子面の X線回折ロッキングカーブの半値幅は 1 3 0秒以下と なり易い傾向を有するが、 上記のようにあらかじめ基板に形成する薄膜が 向性多結晶の結晶 状態であるほうが、 さらにその上に形成した単結晶薄膜の結晶性はより優れたものとなり易い。 本発明において、 炭化珪素、 窒化珪素、 窒ィ匕ガリウム、 酸化亜鉛、 酸ィ匕ベリリウムなどの六 方晶結晶系及び ¾化アルミニウムなどの三方晶結晶系あるいは^晶系として分類できる結晶 系を有する各種セラミック材料を主成分とする焼結体からなる基板にあらかじめ形成する単結 晶、 無定形、 多結晶、 配向性多結晶のうちから選ばれる少なくともいずれかの結晶状態を有す る薄膜のうち無定形、 多結晶、 配向性多結晶のうちから選ばれる少なくともいずれかの結晶状 態を有するものを形成した基板のほうが、 その上に形成する単結晶薄膜の表面平滑性としては より優れたものが通常得られ易いので好ましい。 基板にあらかじめ形成する薄膜が単結晶であ る場合、 さらにその上に形成される単結晶薄膜の平均表面粗さ R aは通常 3 nmより大きいの に対して、 基板にあらかじめ形成する薄膜が無定形、 多結晶、 配向性多結晶のうちから選ばれ る少なくともいずれかの結晶状態を有するものである場合、 その上に形成される単結晶薄膜の 平均表面粗さ R aは通常少なくとも 3 nm以下である。 また、 炭化珪素、 窒化珪素、 窒化ガリ ゥム、 酸化亜鉛、 謝匕ベリリウムなどの六方晶結晶系及び酸化アルミニウムなどの三方晶結晶 系あるいは六方晶系として分類できる結晶系を有する各種セラミック材料を主成分とする焼結 体からなる基板にあらかじめ形成する薄膜が己向性多結晶である場合、 その上に形成する単結 晶薄膜の表面平滑性としては通常最も優れたものが得られ易いのでさらに好ましい。 該基板に あらかじめ形成する薄膜が無定形及び多結晶である場合その上に形成される単結晶薄膜の平均 表面粗さ R aは通常 2 nmより大きくなり易いが、 該基板にあらかじめ形成する薄膜が配向性 多結晶の場合、 その上に形成される単結晶薄膜の平均表面粗さ R aは少なくとも 2 nm以下で あり、 通常は 1. 5 nm以下で、 さらに 1. 0 nm以下のものも比較的容易に得られる。 この ように R a 2 nm以下の単結晶薄膜をそのまま発光素子などの電子素子を構成する薄膜層の一 部に用いる、 あるいは R a 2 nm以下の単結晶薄膜が形成された基板を用いてその上に発光素 子などの電子素子を形成すれば発光効率などの特性がより優れたものが製造できるという効果 がある。
このような高い結晶性の単結晶薄膜が形成された基板に発光素子を形成していく場合、 ある いは直接この高い結晶性の単結晶薄膜を発光素子を構成する薄膜の一部として用いる場合など 形成される発光素子の発光効率が高まり易いので好ましい。
また、 窒化アルミニウムを主成分とする焼結体からなる基板あるいは炭化珪素、 窒化珪素、 窒化ガリウム、 酸化亜鉛、 酸化ベリリウムなどの六方晶結晶系及び 化アルミニウムなどの三 方晶結晶系あるいは六方晶系として分類できる結晶系を有する各種セラミック材料を主成分と する焼結体からなる基板にあらかじめ窒化ガリウム、 窒化インジウム、 窒化アルミニウムのう ちから選ばれた少なくとも 1種以上からなる単結晶、 無定形、 多結晶、 配向性多結晶のうちか ら選ばれる少なくともいずれかの結晶状態を有する薄膜を形成後さらに窒化ガリゥム、 窒化ィ ンジゥム、 窒化アルミニウムのうちから選ばれた少なくとも 1種以上からなる単結晶薄膜を形 成すれば該単結晶薄膜の C軸結晶方位が基板面に垂直な方向あるいは基板面に水平な方向に制 御し易くなる。 該単結晶薄膜の C軸結晶方位が基板面に垂直な方向に形成されたものは該単結
晶薄膜の示す X線回折パターンはミラ一指数 (0 0 2) の回折面からの回折線が出現しミラ一 指数 ( 1 0 0) の回折面からの回折線は出現しない。 また、 該単結晶薄膜の C軸結晶方位が基 板面に水平な方向に形成されたものは該単結晶薄膜の示す X線回折パターンはミラ一指数 ( 1 0 0) の回折面からの回折線が出現しミラ一指数 ( 0 0 2) の回折面からの回折線は出現しな いので該単結晶薄膜の方位は容易に判別できる。
上記のように本発明においては窒化アルミニウムを主成分とする焼結体、 及び炭化珪素、 窒 化珪素、 窒化ガリウム、 酸化亜鉛、 酸化ベリリウムなどの六方晶結晶系及ぴ谢匕アルミニウム などの三方晶結晶系あるいは六方晶系として分類できる結晶系を有する各種セラミック材料を 主成分とする焼結体からなる基板にあらかじめ窒化ガリウム、 窒化インジウム、 窒化アルミ二 ゥムのうちから選ばれた少なくとも 1種以上からなる単結晶、.無定形、 多結晶、 配向性多結晶 のうちから選ばれる少なくともいずれかの結晶状態を有する薄膜を少なくとも 1層以上形成し た基板を用い、 該薄膜が形成された基板に単結晶薄膜を形成すれば該単結晶薄膜の結晶性はさ らに向上し得る。
以下この現象が生じる理由を窒化アルミニゥムを主成分とする焼結体を例にして具体的に説 明する。すなわち、窒化アルミニウムを主成分とする焼結体に窒化ガリウム、窒化インジウム、 窒化アルミニウムのうちから選ばれた少なくとも 1種以上からなる単結晶薄膜を直接形成する 場合、 窒化アルミニウムを主成分とする焼結体の 性、 化学組成、 結晶粒子の大きさなど 該窒化アルミニウムを主成分とする焼結体の材質によって形成される単結晶薄膜の結晶性は影 響を受けやすい。 例えば通常窒化アルミニウムを主成分とする焼結体として窒化アルミニウム 成分を 5 0髓%以上含む.ことが良質の単結晶薄膜を直接形成する場合には重要である。 窒化 アルミニゥム成分の含有量が 5 0体積%より少ないと良質の単結晶薄膜が 接形成できにくい かあるいは多結晶状態の薄膜が形成され易いので好ましくない場合がある。
それに対して単結晶、 無定形、 多結晶、 配向性多結晶のうちから選ばれる少なくともいずれ かの結晶状態を有する薄膜をあらかじめ形成した窒化アルミニウムを主成分とする焼結体から なる基板を用いこの薄膜があらかじめ形成された基板に単結晶薄膜を形成すれば窒化アルミ二 ゥムを主成分とする焼結体の光 ¾1性、 化学組成、 結晶粒子の大きさなど該窒化アルミニウム を主成分とする焼結体の材質によって形成される単結晶薄膜の結晶性は影響を受けにくくなる という特徴がある。 すなわち例えば、 窒化アルミニウムを主成分とする焼結体の窒化アルミ二 ゥム成分の含有量が 5 0ィ 責%より少ないものであってもその上にあらかじめ単結晶、無定形、 多結晶、 配向性多結晶のうちから選ばれる少なくともいずれかの結晶状態を有する薄膜を形成 したものを基板として用いれば、 その上に形成される窒化ガリウム、 窒化インジウム、 窒化ァ ルミニゥムのうちから選ばれた少なくとも 1種以上からなる薄膜は多結晶化しにくく比較的結 晶性に優れた単結晶薄膜が形成し得る。 このような現象は単結晶、 無定形、 多結晶、 配向性多 結晶など各種結晶状態の薄膜中に N型半導体特性を付与する S i、 G e、 S e、 T e、 O及び p型半導体特性を付与する Mg、 B e、 C a、 Z n、 C d、 Cなどのドーピング成分が 1ある いは 2以上含まれていてもその効果は同様である。 実験的には少なくとも 2 0体積%以上の窒 化アルミニウム成分を含有する窒化アルミニウムを主成分とする焼結体の上にあらかじめ単結 晶、 無定形、 多結晶、 配向性多結晶のうちから選ばれる少なくともいずれかの結晶状態を有す る薄膜が形成可能であり、 該薄膜を形成したものを基板として用いれば、 その上にはミラー指 数 (0 0 2) の格子面の X線回折ロッキングカーブの半値幅が 3 0 0秒以下の結晶性を有する 窒化ガリウム、 窒化インジウム、 窒化アルミニウムのうちから選ばれた少なくとも 1種以上か らなる単結晶薄膜が形成できることが確かめられた。 また、 5 0髓%以上の窒化アルミニゥ ム成分を含有する窒化アルミニウムを主成分とする焼結体の上にあらかじめ単結晶、 無定形、 多結晶、 配向性多結晶のうちから選ばれる少なくともいずれかの結晶状態を有する薄膜を形成
したものを基板として用いれば、 その上にはミラ一指数 (0 0 2) の格子面の X線回折ロッキ ングカーブの半値幅が 2 4 0秒以下の結晶性を有する窒化ガリウム、 窒化インジウム、 窒化ァ ルミニゥムのうちから選ばれた少なくとも 1種以上からなる単結晶薄膜が形成し得ることが H かめられた。
上記 2 0體%以上の窒化アルミニゥム成分を含有する窒化アルミニゥムを主成分とする焼 結体において、 窒ィ匕ァリレミニゥム以外の成分として例えば希土 ¾素及びアル力リ土類金属の うちから選ばれた少なくともいずれかの成分を酸化物換算で 8 0體%以下、 あるいは M o、 W、 V、 N b、 T a、 T i、 力一ボンのうちから選ばれた少なくともいずれかの成分を元素換 算で 8 0体積%以下、 あるいは AL ONを 8 0 %以下含むものを好適に用いることができる。 また、 2 (H機%以上の窒化アルミニウム成分を含有する窒化アルミニウムを主成分とする焼 結体において酸 有量としては元素換算で 3 0重量%以下のものを好適に用いることができ る。 酸素含有量が 3 0重量%以下であれば A L ON含有量 8 0 %以下の窒化アルミニウムを主 成分とする焼結体が得られ易い。 上記の成分は 1種だけ単独で含まれていてもよいし 2種以上 が同時に含まれていてもよい。 2種以上が同時に含まれる場合、 上記希土編素及びアルカリ 土類金属の中から 1種以上、 及ぴ lV[o、 W、 V、 N b、 T a、 T i、 力一ボンのうちから選ば れた少なくともいずれかの成分の中から 1種以上、 及び AL ON、 及ぴ襤素、 の中から選ばれ る成分が 2種以上含まれたものでもよいし、 あるいは例えば希土贩素の中から¾1[ 2種 以上、 あるいはアルカリ土類金属の中から適宜 2種以上、 あるいは Mo、 W、 V、 N b、 T a、 T i、 カーボンのうちから選ばれた少なくともいずれかの成分の中から ¾1:2種以上、 含まれ たものであってもよい。
また、 5 0体積%以上の窒化アルミニウム成分を含有する窒化アルミニウムを主成分とする 焼結体においては、 上記窒化アルミニウム以外の各成分を 5 0髓%以下含むものと、 その他 にアルカリ金属及ぴ 素のうちから選ばれた少なくともいずれかの成分を酸化物換算で 5 0体 積%以下含むものも好適に用いることができる。 そのうちアルカリ金属としては酸化物騰で 3 0 %以下含む窒化アルミニウムを主成分とする焼結体を用いることが好ましい。 また、 希土類 素及び ~Mo、 W、 V、 Nb、 T a、 T i以外の遷移金属例えば鉄、 ニッケル、 クロム、 マンガン、 ジルコニウム、 ハフニウム、 コノ 1>レト、 銅、 亜鉛のうちから選ばれた少なくともい ずれかの成分を元素換算で 8 0重量%以下含む窒化アルミニゥムを主成分とする焼結体も基板 として好適に用いることができる。 本発明において上記希土 ¾素及 ϋ¾ίο、 W、 V、 N b、 T a、 T i以外の遷移金属例えば鉄、 ニッケル、 クロム、 マンガン、 ジルコニウム、 ハフニゥ ム、 コバルト、 銅、 亜鉛各成分の含有量は元素騰の重量百分率 (重量%) で示してきたがこ れら成分の密度から容易に # ^貴百分率 に算定し直すことができる。 上記の成分は 1 種だけ単独で含まれていてもよいし 2種以上が同時に含まれていてもよい。 2種以上が同時に 含まれる場合、 上記アルカリ金属及ぴ 素のうちから選ばれた少なくともいずれかの成分の中 から建 1種以上、 及び希土類 素及び M o、 W、 V、 N b、 T a、 T i以外の遷移金属例え ば鉄、 ニッケル、 クロム、 マンガン、 ジルコニウム、 ハフニウム、 コノルト、 銅、 亜鉛のうち から選ばれた少なくともいずれかの成分の中から l種以上、 の中から選ばれる成分が ¾a 2種以上含まれたものでもよいし、 あるいはアル力リ金属及び 素のうちから選ばれた少なく ともいずれかの成分の中から難 2種以上、 あるいは希土 素及び Mo、 W、 V、 N b、 T a、 Τ i の遷移金属例えば鉄、ニッケル、 クロム、マンガン、 ジルコニウム、ハフニウム、 コバルト、 銅、 亜鉛のうちから選ばれた少なくともいずれかの成分の中から ¾2種以上、 含 まれたものであってもよい。
前記のように酸化ジルコニウム (Z r 02)、 酸ィ匕マグネシウム (Mg O)、 アルミン酸マグネ シゥム (MgA l 204) などを主成分とする焼結体からなる基板には窒化ガリウム、 窒化イン
ジゥム、 窒化アルミニウムのうちから選ばれた少なくとも 1種以上を主成分とする単結晶薄膜 を直接形成することは困難な場合が多い。 しかしながら、 上記基板には窒化ガリウム、 窒化ィ ンジゥム、 窒化アルミニウムのうちから選ばれた少なくとも 1種以上を主成分とする無定形、 多結晶、 配向性多結晶のうちから選ばれる少なくともいずれかの結晶状態を有する薄膜であれ ばS接形成し得ることが見出された。 さらに、 本発明において上記酸化ジルコニウム、 酸化マ グネシゥム、 アルミン酸マグネシウムなどを主成分とする焼結体を基板とし、 該基板にあらか じめ窒化ガリウム、 窒化インジウム、 窒化アルミニウムのうちから選ばれた少なくとも 1種以 上を主成分とする無定形、 多結晶、 配向性多結晶のうちから選ばれる少なくともいずれかの結 晶状態を有する薄膜を形成すれば、 その上にはミラー指数 ( 0 0 2) の格子面の X線回折ロッ キング力一ブの半値幅が少なくとも 3 6 0 0秒以下の結晶性を有する窒化ガリゥム、 窒化ィン ジゥム、 窒化アルミニウムのうちから選ばれた少なくとも 1種以上を主成分とする単結晶薄膜 が形成し得ることも見出された。 また、 例えば酸化チタン (T i 02)、 チタン酸バリウム (B a T i〇3)、 チタン酸ジルコン酸鉛 (P Z T:チタンとジルコニウムをモル数 1 : 1の割合で 含む複合酸化物)、酸化ィットリウム(Y 203)などの希土匿ィ匕物、酸化トリウム(T h O 2)、 各種フェライト (F e 304あるいは Mn F e 204など一 j¾AF e 2〇4であらわされる複合酸 化物:ただし、 Aは 2価の金属元素)、 ムライト (3 A 1 2〇3 · 2 S i 02)、 フオルステライト ( 2 Mg O · S i 02)、 ステアタイト (Mg O · S i 02)、 結晶化ガラス、 などの各種セラミ ック材料を主成分とする焼結体も基板として用いることができ、 該基板にも窒化ガリウム、 窒 化インジウム、 窒化アルミニウムのうちから選ばれた少なくとも 1種以上を主成分とする無定 形、 多結晶、 配向性多結晶のうちから選ばれる少なくともいずれかの結晶状態を有する薄膜で あれば 接形成し得ることが見出された。 さらにあらかじめ窒化ガリウム、 窒化インジウム、 窒化アルミニウムのうちから選ばれた少なくとも 1種以上を主成分とする無定形、 多結晶、 配 向性多結晶のうちから選ばれる少なくともいずれかの結晶状態を有する薄膜を形成したものを 基板として用いれば、 その上にはミラ一指数 ( 0 0 2 ) の格子面の X線回折ロッキングカーブ の半値幅が少なくとも 3 6 0 0秒以下の結晶性を有する窒化ガリゥム、 窒化ィンジゥム、 窒化 アルミニウムのうちから選ばれた少なくとも 1種以上を主成分とする単結晶薄膜が形成し得る ことも見出された。 上記酸化ジルコニウム、 酸化マグネシウム、 アルミン酸マグネシウム、 酸 化チタン、チタン酸バリウム、チタン酸ジルコン酸鉛、酸化イットリウムなどの希土鍵化物、 酸化トリウム、各種フェライト、ムライト、 フオルステライ卜、ステアタイト、結晶化ガラス、 などの各種セラミック材料を主成分とする焼結体からなる基板の表面を鏡面研磨あるいはその 他の方法で研削し平均表面粗さ 5 0 nm以下とした基板を用い、 あらかじめ窒化ガリウム、 窒 化インジウム、 窒化アルミニウムのうちから選ばれた少なくとも 1種以上を主成分とする無定 形、 多結晶、 配向性多結晶のうちから選ばれる少なくともいずれかの結晶状態を有する薄膜を 形成することで、 その上にはミラー指数 (0 0 2 ) の格子面の X線回折ロッキングカーブの半 値幅が少なくとも 3 0 0秒以下の結晶性を有する窒化ガリウム、 窒化インジウム、 窒化アルミ ニゥムのうちから選ばれた少なくとも 1種以上を主成分とする単結晶薄膜が形成し得る。 また、 平均表面粗さ 1 0 nm以下とした基板には該ロッキングカーブの半値幅が 2 0 0秒以下の結晶 性を有する単結晶薄膜が形成し得る。 また、 平均表面粗さ 5 nm以下とした基板には該ロッキ ングカーブの半値幅が 1 5 0秒以下の結晶性を有する単結晶薄膜が形成し得る。 また、 平均表 面粗さ 1 0 nm以下とした基板にはミラ一指数 (0 0 2 ) の格子面の X線回折ロッキングカー ブの半値幅が 1 0 0 0 0秒以下の窒化ガリウム、 窒化インジウム、 窒化アルミニウムのうちか ら選ばれた少なくとも 1種以上を主成分とする配向性多結晶薄膜があらかじめ形成し得る。 ま た、 平均表面粗さ 5 nm以下とした基板にはミラー指数 (0 0 2 ) の格子面の X線回折ロッキ ングカーブの半値幅が 8 0 0 0秒以下の窒化ガリウム、 窒化インジウム、 窒化アルミニウムの
うちから選ばれた少なくとも 1種以上を主成分とする配向性多結晶薄膜があらかじめ形成し得 る。
窒化アルミニウムを主成分とする焼結体からなる基板、 及び炭化珪素、 窒化珪素、 窒化ガリ ゥム、 酸化亜鉛、 酸化ベリリウムなどの六方晶結晶系及ぴ谧化アルミニウムなどの三方晶結晶 系あるいは六方晶系として分類できる結晶系を有する各種セラミック材料を主成分とする焼結 体からなる基板、 及ぴ 化ジルコニウム、 酸化マグネシウム、 アルミン酸マグネシウム、 酸化 チタン、 チタン酸バリウム、 チタン酸ジルコン »、 酸化イットリウムなどの希土 化物、 酸化トリウム、各種フェライト、ムライト、 フォルステライト、ステアタイト、結晶化ガラス、 などの各種セラミック材料を主成分とする焼結体にあらかじめ窒化ガリゥム、窒化ィンジゥム、 窒化アルミニウムのうちから選ばれた少なくとも 1種以上からなる上記単結晶、 無定形、 多結 晶、 配向性多結晶のうちから選ばれる少なくともいずれかの結晶状態を有する薄膜を形成後さ らに窒化ガリウム、 窒化インジウム、 窒化アルミニウムのうちから選ばれた少なくとも 1種以 上からなる単結晶薄膜を形成する方法として例えば以下のものが例示できる。 すなわち、 単結 晶、 無定形、 多結晶、 配向性多結晶のうちから選ばれる少なくともいずれかの結晶状態を有す る薄膜が形成された基板を成膜装置から取り出しあらためて単結晶薄膜を形成していくという 方法、 あるい《S板の を最初低く設定しておき、 まず無定形の薄膜を基板に形成し基板は そのままの状態で基板の を段階的もしくは連続的に上昇して段階的もしくは連続的に単結 晶薄膜を形成していく、 などの方法がある。
窒化アルミニウムを主成分とする焼結体からなる基板、 あるいは炭化珪素、 窒化珪素、 窒化 ガリウム、 酸化亜鉛、 酸化ベリリウムなどの六方晶結晶系及び 化アルミニウムなどの三方晶 結晶系あるいは六方晶系として分類できる結晶系を有する各種セラミック材料を主成分とする 焼結体からなる基板、 あるいは酸化ジルコニウム、 酸化マグネシウム、 アルミン酸マグネシゥ ム、 酸化チタン、 チタン酸バリウム、 チタン酸ジルコン 、 酸化イットリウムなどの希土類 酸化物、 酸化トリウム、 各種フェライト、 ムライト、 フオルステライト、 ステア夕イト、 結晶 化ガラス、 などの各種セラミック材料を主成分とする焼結体からなる基板に形成される薄膜は 単一層としてだけではなく上記のように少なくとも 2層以上からなる薄膜として形成できる。 なお、 上記窒化アルミニウムを主成分とする焼結体からなる基板及び各種セラミック材料を主 成分とする焼結体からなる基板には導通ビアを有する基板も含まれる。 この 2層以上の薄膜と して形成される薄膜は同一組成としてあるいはそれぞれ異なる成分からなるものとしても形成 でき、 さらに 3層以上の薄膜においてすベて同一組成として形成できまた 2層以上が同一組成 で他の 1層以上が異なる組成の薄 USとして形成することができさらに全て異なる組成の薄膜 層としても形成できる。窒化アルミニウムを主成分とする焼結体からなる基板、及び炭化珪素、 窒化珪素、 窒化ガリウム、 酸化亜鉛、 酸化ベリリウムなどの六方晶結晶系及び 化アルミニゥ ムなどの三方晶結晶系あるいは六方晶系として分類できる結晶系を有する各種セラミック材料 を主成分とする焼結体からなる基板、 及び酸化ジルコニウム、 酸化マグネシウム、 アルミン酸 マグネシウム、 酸化チタン、 チタン酸バリウム、 チタン酸ジルコン酸鉛、 酸化イットリウムな どの希土 «化物、 酸ィ匕トリウム、 各種フェライト、 ムライト、 フォルステライト、 ステア夕 イト、 結晶化ガラス、 などの各種セラミック材料を主成分とする焼結体からなる基板に 2層以 上に分けて形成された薄膜の構成は各薄膜層の組成が異なるだけではなく前述のように各薄膜 層の結晶状態が同一の状態のものや各薄翻の結晶状態が例えば単結晶、 無定形、 多結晶、 配 向性多結晶など異なるものであつても窒化アルミ二ゥムを主成分とする焼結体からなる基板、 及び炭化珪素、 窒化珪素、 窒化ガリウム、 酸化亜鉛、 酸化ベリリウムなどの六方晶結晶系及び 酸化アルミニウムなどの三方晶結晶系あるいは六方晶系として分類できる結晶系を有する各種 セラミック材料を主成分とする焼結体からなる基板、 及び ¾化ジルコニウム、 酸化マグネシゥ
ム、 アルミン酸マグネシウム、 酸化チタン、 チタン酸バリウム、 チタン酸ジルコン^^、 酸化 イットリウムなどの希土鐘化物、 酸化トリウム、 各種フェライト、 ムライト、 フォルステラ イト、 ステアタイ卜、 結晶化ガラス、 などの各種セラミック材料を主成分とする焼結体からな る基板に形成できる。 すなわち窒化アルミニウムを主成分とする焼結体からなる基板、 及び炭 化珪素、 窒化珪素、 窒化ガリウム、 酸化 ¾、 酸化ベリリウムなどの六方晶結晶系及び 化ァ ルミニゥムなどの三方晶結晶系あるいは六方晶系として分類できる結晶系を有する各種セラミ ック材料を主成分とする焼結体からなる基板、 さらに酸化ジルコニウム、 酸化マグネシウム、 アルミン酸マグネシウム、 酸化チタン、 チタン酸パリゥム、 チタン酸ジルコン醒、 酸化イツ トリウムなどの希土 ィ匕物、酸匕トリウム、各種フェライト、ムライト、 フオルステライト、 ステアタイト、 結晶化ガラス、 などの各種セラミック材料を主成分とする焼結体からなる基板 には窒化ガリウム、 窒化インジウム、 窒化アルミニウムのうちから選ばれた少なくとも 1種以 上からなる薄膜が 2層以上形成できるが、 この 2層以上で構成されている薄膜において各薄膜 層として単結晶、 無定形、 多結晶、 配向性多結晶のうちから選ばれた少なくともいずれの状態 のものが何ら制限されることなく形成できる。 例えば Εβが 2層の場合、 2層とも同じ結晶 状態であるものと各層の結晶状態が異なるものがあり、 2層とも同じ結晶状態であるものを例 示すれば 1 ) 各薄 全ての層が単結晶状態であるもの、 2 ) 各層全てが無定形であるもの、 などであり、 各層の結晶状態が異なるものを例示すれば 3) 基板側の薄膜が無定形でその上に 形成されている薄膜が単結晶であるもの、 あるいは 4) 基板側の薄膜が多結晶でその上に形成 されている薄膜が単結晶であるもの、 あるいは 5) 基板側の薄膜が 向性多結晶でその上に形 成されている薄膜が単結晶であるもの、 などである。 上記薄膜層が 2層の場合薄膜層の結晶状 態は、 基板側の薄翻として単結晶、 無定形、 多結晶、 配向性多結晶の少なくとも 4種類の結 晶状態のものが形成でき、 この上に形成される薄顧はそれぞ 結晶、 無定形、 多結晶、 配 向性多結晶の少なくとも 4種類の結晶状態のものが形成できるので計 1 6種類の組み合わせの 2層薄膜形成が可能である。 また、 例えば薄膜層が 3層の場合、 3層とも同じ結晶状態である もの、 各層の結晶状態が 3層とも異なるもの、 3層のうち 2層が同じ結晶状態で 1層が異なる ものがあり、 3層とも同じ結晶状態であるものを例示すれば 1 ) 各薄膜層全ての層が単結晶状 態であるもの、 2 ) 各層全てが無定形であるもの、 などであり、 各層の結晶状態が 3層とも異 なるものを例示すれば 3 ) 基板側の薄膜が無定形でその上に形成されている薄膜が多結晶でそ の上に形成されている薄膜が単結晶であるもの、 3層のうち 2層が同じ結晶状態で 1層が異な るものを例示すれば 4 ) 基板側の薄膜が無定形でその上に形成されている薄膜が 2層とも単結 晶であるもの、 などである。 上記薄膜層が 3層の場合薄膜層の結晶状態は、 基板側の薄膜層が 単結晶、 無定形、 多結晶、 配向性多結晶の少なくとも 4種類の結晶状態のものが形成でき、 こ の上に形成される薄翻はそれぞ^1 結晶、 無定形、 多結晶、 配向性多結晶の少なくとも 4種 類の結晶状態のものが形成でき、さらにその上に形成される薄編はそれぞ 結晶、無定形、 多結晶、 配向性多結晶の少なくとも 4種類の結晶状態のものが形成できるので結晶状態が異な る少なくとも計 6 4種類の組み合わせの 3層薄膜形成が可能である。 また、 4層以上の薄膜も 上記のように 4層薄膜であれば少なくとも 2 5 6種類、 5層薄膜であれば少なくとも 1 0 2 4 種類、 あるいは 6層薄膜であれば少なくとも 4 0 9 6種類、 また 7層薄膜であれば少なくとも 1 6 3 8 4種類、 さらに 8層薄膜であれば少なくとも 6 5 5 3 6種類の組み合わせの、 という ように各層の結晶状態を任意に組み合わせることで結晶状態が異なるあらゆる多層薄膜の形成 が可能である。
本発明において、 窒化アルミニウムを主成分とする焼結体からなる基板、 及び炭化珪素、 窒 化珪素、 窒化ガリウム、 酸化亜鉛、 酸化ベリリウムなどの六方晶系及び酸化アルミニウムなど の Ξ方晶系あるいは六方晶系として分類できる結晶構造を有する各種セラミック材料を主成分
とする焼結体からなる基板、 及び ¾化ジルコニウム、 酸化マグネシウム、 アルミン酸マグネシ ゥム、 酸化チタン、 チタン酸パリゥム、 チタン酸ジルコン酸鉛、 酸化ィットリゥムなどの希土 »化物、 酸化トリウム、 各種フェライト、 ムライト、 フォルステライト、 ステア夕イト、 結 晶化ガラス、 などの各種セラミック材料を主成分とする焼結体からなる基板に少なくとも 2層 以上で形成される窒化ガリウム、 窒化インジウム、 窒化アルミニウムのうちから選ばれた少な くとも 1種以上を主成分とする薄膜の各層における膜厚も任意の組み合わせが可能である。 通 常各薄膜層の膜厚はそれぞれ 0. 5 nm〜 1 0 0 0 M mの範囲もの、 好ましくは 0. 5 n m〜 2 0 0 mの範囲のものを M組み合わせて用いられる。
このように本発明による窒化アルミニウムを主成分とする焼結体、及び炭化珪素、窒化珪素、 窒化ガリウム、 酸化亜鉛、 酸化ベリリウムなどの六方晶系及ぴ襥化アルミニウムなどの三方晶 系あるいは六方晶系として分類できる結晶構造を有する各種セラミック材料を主成分とする焼 結体、 及び 化ジルコニウム、 酸化マグネシウム、 アルミン酸マグネシウム、 酸化チタン、 チ タン酸バリウム、 チタン酸ジルコン酸鉛、 酸ィ匕イットリウムなどの希土 «化物、 酸ィ匕トリウ ム、 各種フェライト、 ムライト、 フオレステライト、 ステアタイト、 結晶化ガラス、 などの各 種セラミック材料を主成分とする焼結体に窒化ガリウム、 窒化インジウム、 窒化アルミニウム のうちから選ばれた少なくとも 1種以上を主成分とする薄膜が形成された薄膜基板に形成され ている窒化ガリウム、 窒化インジウム、 窒化アルミニウムのうちから選ばれた少なくとも 1種 以上を主成分とする薄膜は単一の結晶状態のものだけでなく単結晶、 無定形、 多結晶、 配向性 多結晶のうちから選ばれた少なくともいずれかの結晶状態の異なる 2以上を適 袓み合わせた 構成からなるものを用いることができる。 このような薄膜の結晶状態の組み合わせとして例え ば 膜が 2つの異なる結晶状態からなる場合、 窒化アルミ二ゥムを主成分とする焼結体からな る基板側にある薄膜は単結晶、 無定形、 多結晶、 配向性多結晶の少なくとも 4種類の結晶状態 のものが形成でき、 この上に形成される薄膜はそれぞれ単結晶、 無定形、 多結晶、 配向性多結 晶の少なくとも 4種類の結晶状態のものが形成できるので、 2つの異なる結晶状態で構成され ている薄膜の場合は計 1 2種類の異なる結晶状態の組み合わせのものが形成可能である。 また、 例えば薄膜が 3つのそれぞれ異なる結晶状態からなる場合、 窒化アルミ二ゥムを主成分とする 焼結体からなる基板側の薄膜が単結晶、 無定形、 多結晶、 配向性多結晶の各 4種類の結晶状態 のものが形成でき、 この上に形成される薄膜は単結晶、 無定形、 多結晶、 配向性多結晶の各 4 種類の結晶状態のものが形成でき、 さらにその上に形成される薄^ 8はそれぞれ単結晶、 無定 形、 多結晶、 配向性多結晶の各 4種類の結晶状態のものが形成できるので計 3 6種類の組み合 わせが 3つの異なる結晶状態からなる薄膜において形成可能である。 また、 4つ以上の異なる 結晶状態からなる薄膜も上記のように 1 0 8種類の組み合わせが 4つの異なる結晶状態からな る薄膜において、 3 2 4種類の組み合わせが 5つの異なる結晶状態からなる薄膜において、 9 7 2種類の組み合わせが 6つの異なる結晶状態からなる薄膜において、 また 2 9 1 6種類の組 み合わせが 7つの異なる結晶状態からなる薄膜において、 さらに 8 7 4 8種類の組み合わせが 8つの異なる結晶状態からなる薄膜において、 というように異なる結晶状態の組み合わせが無 限に形成可能である。
なお、 本発明による薄膜基板は形成されている薄膜が多層化され各層が単結晶、 無定形、 多 結晶、 配向性多結晶など各種結晶状態で、 組成も各薄 で異なりさらに厚みも各層で異なつ ていたとしても少なくとも単結晶薄膜が形成されているものである。 また上記薄膜基板に形成 されている単結晶薄膜は、 基板に直接形成されているものより、 単結晶、 無定形、 多結晶、 配 向性多結晶など各種結晶状態の薄膜をあらかじめ形成した基板を用いてその上に形成したもの のほうが通常は結晶性に優れる。 本発明による薄膜基板に形成される薄膜は多層化され各層が 単結晶、 無定形、 多結晶、 配向性多結晶など各種結晶状態で、 組成も各薄膜層で異なりさらに
厚みも各層で異なっていたとしても少なくとも単結晶薄膜を含む。 . 少なくとも 2層以上からなる薄膜において成分が異なるという意味は薄膜の実質的な組成が 異なるということであり、 薄膜の組成として該薄膜の主成分である窒化ガリウム、 窒化インジ ゥム、 窒化アルミニウムのうちから選ばれた少なくとも 1種以上からなる成分の割合が異なる ものだけでなぐ 例えば ¾膜が主成分として窒化ガリウム、 窒化インジウム、 窒化アルミニゥ ムのうちから選ばれる 1種類だけでその他の成分として例えばドーピング剤だけの場合なども 含まれる。 より具体的に言えば、 薄膜の主成分が例えば窒化ガリウムだけでその他実質的にド —ピング剤としてマグネシウム (Mg) だけを含むものの場合、 窒化ガリウムとマグネシウム の組成比が異なるものも含まれる。 あるいは同様に、 薄膜の主成分が例えば窒化アルミニウム だけでその他実質的にドーピンク として珪素 (S i ) だけを含むものの場合、 窒化アルミ二 ゥムと珪素の組成比が異なるものも含まれる。 本発明においては上記のように窒化アルミニゥ ムを主成分とする焼結体からなる基板に直接窒化ガリウム、 窒化インジウム、 窒化アルミニゥ ムのうちから選ばれた少なくとも 1種以上を主成分とする同一成分の薄膜を単一層としてある いは少なくとも 2層以上に分けて形成できるだけでなく異なる成分からなる少なくとも 2層以 上の薄膜として形成することができる。 同一成分を 2層以上に分けて形成したものや異なる成 分のものを 2層以上に形成したものであっても形成されたそれぞれの薄膜が単結晶である場合 該単結晶薄膜のミラー指数 ( 0 0 2) の格子面の X線回折ロッキングカーブの半値幅が 2 4 0 秒以下と優れた結晶性のものが得られる。 また上記のような 2層以上の薄膜を炭化珪素、 窒化 珪素、 窒化ガリウム、 酸化碰、 酸化ベリリウムなどの六方晶系及び 化アルミニウムなどの 三方晶系あるいは六方晶系として分類できる結晶構造を有する材料を主成分とする焼結体を基 板として用いて形成したとき窒化ガリウム、 窒化インジウム、 窒化アルミニウムのうちから選 ばれた少なくとも 1種以上を主成分とする単結晶薄膜のミラー指数 ( 0 0 2 ) の格子面の X線 回折ロッキングカーブの半値幅が 3 0 0秒以下の優れた結晶性のものが得られるので好ましい。 本発明においては上記のように、 窒化アルミニウムを主成分とする焼結体からなる基板、 あ るいは炭化珪素、 窒化珪素、 窒化ガリウム、 酸化亜鉛、 酸化ベリリウムなどの六方晶結晶系及 化アルミニウムなどの三方晶結晶系あるいは六方晶系として分類できる結晶構造を有する セラミック材料を主成分とする焼結体からなる基板、 あるいは酸ィ匕ジルコニウム、 酸化マグネ シゥム、 アルミン酸マグネシウム、 酸化チタン、 チタン酸バリウム、 チタン酸ジルコン酸鉛、 酸化イットリウムなどの希土 «化物、 酸化トリウム、 各種フェライト、 ムライト、 フォルス テライト、 ステアタイト、 結晶化ガラス、 などの各種セラミック材料を主成分とする焼結体か らなる基板に形成された薄膜は単一層としてだけではなく上記のように少なくとも単結晶を含 む 2層以上からなる薄膜として形成できる。 本発明において単結晶薄膜を含む上記 2層以上に 形成できる薄膜として窒化アルミニウムを主成分とする焼結体、あるいは炭化珪素、窒化珪素、 窒化ガリウム、 酸化亜鉛、 酸化ベリリウムなどの六方晶結晶系及び 化アルミニウムなどの三 方晶結晶系あるいは六方晶系として分類できる結晶系を有する各種セラミック材料を主成分と する焼結体、 あるいは酸化ジルコニウム、 酸化マグネシウム、 アルミン酸マグネシウム、 酸ィ匕 チタン、 チタン酸バリウム、 チタン酸ジルコン酸鉛、 酸化イットリウムなどの希土鍾化物、 酸化トリウム、各種フェライト、ムライト、 フォルステライト、ステア夕イト、結晶化ガラス、 などの各種セラミツク材料を主成分とする焼結体からなる薄膜形成用基板に形成され得る薄膜 だけではなく、 本発明による薄膜基板に形成されている薄膜も含まれる。 すなわち、 本発明に おいて上記 2層以上に形成できる薄膜には薄膜形成用基板に形成され得る薄膜、 及 D簿膜基板 に形成された薄膜の 2つの薄膜が含まれる。 これらの薄膜は単一の層としてだけではなく少な くとも 2層以上の単結晶薄膜を含む薄膜としても形成できることを明らかにした。
本発明は上記のように、 窒化ガリウム、 窒化インジウム、 窒化アルミニウムのうちから選ば
れた少なくとも 1種以上からなる無定形、 多結晶、 配向性多結晶、 単結晶のうちから選ばれた 少なくともいずれかの結晶状態を有する薄膜を形成し得る窒化アルミニウムを主成分とする焼 結体からなる薄麵成用基板を提供する。 さらに、 窒化アルミニウムを主成分とする焼結体か らなる基板に窒化ガリウム、 窒化インジウム、 窒化アルミニウムのうちから選ばれた少なくと も 1種以上からなる無定形、 多結晶、 配向性多結晶、 単結晶のうちから選ばれた少なくともい ずれかの結晶状態を有する薄膜が形成されている薄膜基板も提供する。 また本発明は、 窒化ガ リウム、 窒化インジウム、 窒化アルミニウムのうちから選ばれた少なくとも 1種以上からなる 無定形、 多結晶、 配向性多結晶、 単結晶のうちから選ばれた少なくともいずれかの結晶状態を 有する薄膜を形成し得る炭化珪素、 窒化珪素、 窒化ガリウム、 酸化亜鉛、 酸化ベリリウムなど の六方晶結晶系及び酸化アルミニウムなどの三方晶結晶系あるいは六方晶系として分類できる 結晶構造を有するセラミック材料を主成分とする焼結体からなる薄膜形成用基板を提供する。 さらに、 炭化珪素、 窒化珪素、 窒化ガリウム、 酸化亜鉛、 酸化ベリリウムなどの六方晶結晶系 及び衞匕アルミ二ゥムなどの三方晶結晶系あるいは六方晶系として分類できる結晶構造を有す るセラミック材料を主成分とする焼結体からなる基板に窒化ガリウム、 窒化インジウム、 窒化 アルミニウムのうちから選ばれた少なくとも 1種以上からなる無定形、多結晶、配向性多結晶、 単結晶のうちから選ばれた少なくともいずれかの結晶状態を有する薄膜が形成されている薄膜 基板も提供する。
また本発明は、 窒化ガリウム、 窒化インジウム、 窒化アルミニウムのうちから選ばれた少な くとも 1種以上からなる無定形、 多結晶、 配向性多結晶、 単結晶のうちから選ばれた少なくと もいずれかの結晶状態を有する薄膜を形成し得る酸化ジルコニウム、 酸化マグネシウム、 アル ミン酸マグネシウム、 酸化チタン、 チタン酸バリウム、 チタン酸ジルコン酸鉛、 酸化イツトリ ゥムなどの希土 «化物、 酸匕トリウム、 各種フェライト、 ムライト、 フォルステライト、 ス テアタイト、 結晶化ガラス、 などの各種セラミック材料を主成分とする焼結体からなる薄膜形 成用基板を提供する。 さらに、 酸化ジルコニウム、 酸化マグネシウム、 アルミン酸マグネシゥ ム、 酸化チタン、 チタン酸バリウム、 チタン酸ジルコン麟、 酸化イットリウムなどの希土類 酸化物、 酸化トリウム、 各種フェライト、 ムライト、 フォルステラィ卜、 ステア夕イト、 結晶 化ガラス、 などの各種セラミック材料を主成分とする焼結体からなる基板に窒化ガリウム、 窒 化インジウム、 窒化アルミニウムのうちから選ばれた少なくとも 1種以上からなる無定形、 多 結晶、 配向性多結晶、 単結晶のうちから選ばれた少なくともいずれかの結晶状態を有する薄膜 が形成されている薄膜基板も提供する。
また本発明においては前記のように、 窒化アルミニウムを主成分とする焼結体、 及び炭化珪 素、 窒化珪素、 窒化ガリウム、 酸化亜鉛、 酸化ベリリウムなどの六方晶結晶系及び ¾化アルミ ニゥムなどの三方晶結晶系あるいは六方晶系として分類できる結晶系を有する各種セラミック 材料を主成分とする焼結体、 及び 化ジルコニウム、 酸化マグネシウム、 アルミン酸マグネシ ゥム、 酸化チタン、 チタン酸バリウム、 チタン酸ジルコン酸鉛、 酸化イットリウムなどの希土 ¾化物、 酸化トリウム、 各種フェライト、 ムライト、 フォルステライト、 ステアタイト、 結 晶化ガラス、 などの各種セラミック材料を主成分とする焼結体には窒化ガリウム、 窒化インジ ゥム、 窒化アルミニウムのうちから選ばれた少なくとも 1種以上からなる単結晶薄膜が形成し 得る。 該単結晶薄膜は各焼結体におけるセラミック材料の違いによって該焼結体に直接形成し 得るものもあるし、 あるいは該焼結体にあらかじめ窒化ガリウム、 窒化インジウム、 窒化アル ミニゥムのうちから選ばれた少なくとも 1種以上からなる単結晶、 無定形、 多結晶、 配向性多 結晶のうちから選ばれる少なくともいずれかの結晶状態を有する薄膜を形成後その上に形成し 得るものもある。 例えば窒化アルミニウムを主成分とする焼結体、 及び炭化珪素、 窒化珪素、 窒化ガリウム、 酸化亜鉛、 酸化ベリリウムなどの六方晶結晶系及び酸化アルミニウムなどの三
方晶結晶系あるいは六方晶系として分類できる結晶系を有する各種セラミック材料を主成分と する焼結体には窒化ガリウム、 窒化インジウム、 窒化アルミニウムのうちから選ばれた少なく とも 1種以上からなる単結晶薄膜が直接形成し得る。 一方、 酸化ジルコニウム、 酸化マグネシ ゥム、 アルミン酸マグネシウム、 酸化チタン、 チタン酸バリウム、 チタン酸ジルコン 、 酸 化イットリウムなどの希土鐘化物、 酸化トリウム、 各種フェライト、 ムライト、 フオルステ ライト、 ステアタイト、 結晶化ガラス、 などの各種セラミック材料を主成分とする焼結体には あらかじめ窒化ガリウム、 窒化インジウム、 窒化アルミニウムのうちから選ばれた少なくとも
1種以上からなる無定形、 多結晶、 配向性多結晶のうちから選ばれる少なくともいずれかの結 晶状態を有する薄膜を形成後その上に窒化ガリウム、 窒化インジウム、 窒化アルミニウムのう ちから選ばれた少なくとも 1種以上からなる単結晶薄膜を形成し得る。
かくして本発明により、 窒化ガリウム、 窒化インジウム、 窒化アルミニウムのうちから選ば れた少なくとも 1種以上を主成分とする単結晶薄膜を形成するための基板であって、 該基板が セラミック材料を主成分とする焼結体からなることを特徴とする薄膜形成用基板、 が提供し得 る。 また本発明により、 セラミック材料を主成分とする焼結体に窒化ガリウム、 窒化インジゥ ム、 窒化アルミニウムのうちから選ばれた少なくとも 1種以上を主成分とする単結晶薄膜が形 成されていることを Mとする薄膜基板、 が提供し得る。 又本発明により、 窒化ガリウム、 窒 化インジウム、 窒化アルミニウムのうちから選ばれた少なくとも 1種以上を主成分とする薄膜 を形成するための基板であって、 該基板が 性を有するセラミック材料を主成分とする焼 結体からなることを とする薄膜形成用基板、 が提供し得る。 さらに本発明により、 過 性を有するセラミック材料を主成分とする焼結体に窒化ガリウム、 窒化インジウム、 窒化アル ミニゥムのうちから選ばれた少なくとも 1種以上を主成分とする薄膜が形成されていることを 特徴とする薄膜基板、 が提供し得る。 なお、 上記セラミック材料とは焼結体を構成する例えば 窒化アルミニウム、 六方晶系又は三方晶系のうちから選ばれた少なくともいずれかの結晶構造 を有する化合物 (例えば炭化珪素、 窒化珪素、 窒化ガリウム、 謝匕亜鉛、 酸化ベリリウム、 酸 化アルミニウムなど)、 酸化ジルコニウム、 酸化マグネシウム、 アルミン酸マグネシウム、 酸化 チタン、 チタン酸バリウム、 チタン酸ジルコン麵、 酸化イットリウムなどの希土讓化物、 酸化トリウム、各種フェライト、ムライト、 フォルステライト、ステアタイト、結晶化ガラス、 などの金属元素及び半金属元素のうちから選ばれた少なくとも 1種以上の元素と非金属元素の うちから選ばれた少なくとも 1種以上の元素との組成物あるいは化合物、 あるいは金属元素の うちから選ばれた少なくとも 1種以上の元素と半金属元素のうちから選ばれた少なくとも 1種 以上の元素との組成物あるいは化合物、 あるいは半金属元素のうちから選ばれた少なくともい ずれか 2種以上の元素との組成物あるいは化合物を主成分とするものからなる。 上記非金属元 素としては通常窒素、 りん、 酸素、 硫黄、 ハロゲン元素 (フッ素、 塩素、 臭素、 沃素、 ァスタ チン)などが謹に用いられる。半金属元素として〖雄常ほう素、炭素、珪素、ゲルマニウム、 ヒ素、 アンチモン、 ビスマス、 セレン、 テルル、 ポロニウムなどが好適に用いられる。 上記セ ラミック材料は通常無機化合物を主成分とするものであり、 これらのセラミック材料は結晶質 のものであってもよいしあるいは例えばガラスなどの非晶質状態のものであってもよいしある いは結晶質のものと非晶質のものとが混在したものであってもよい。 上記セラミック材料は通 常窒化物、 炭化物、 酸化物、 硼化物、 珪化物などの化合物あるいは組成物を主成分とするもの であ
なお、本発明において上記セラミック材料としては主成分である無機材料以外に金属、合金、 金属間化合物、 有機物質、 有機化合物、 有機樹脂、 その他に例えばハロゲン元素あるいはカル コゲン元素などの非金属などを含有するもの含まれる。
本発明において、 上記セラミック材料を主成分とする焼結体は光 ¾ 性を有するもの力好ま
しく、 該セラミック材料を主成分とする焼結体に形成される窒化ガリウム、 窒化インジウム、 窒化アルミニウムのうちから選ばれた少なくとも 1種以上を主成分とする単結晶薄膜の結晶性 が向上し易くなるので好ましい。
上記薄膜形成用基板は窒化ガリウム、 窒化インジウム、 窒化アルミニウムのうちから選ばれ た少なくとも 1種以上からなる単結晶をはじめ無定形、 多結晶、 配向性多結晶など各種結晶状 態の薄膜を形成するために用いることができる。 又上記薄膜基板も窒化ガリウム、 窒化インジ ゥム、 窒化アルミニウムのうちから選ばれた少なくとも 1種以上からなる単結晶をはじめ無定 形、 多結晶、 配向性多結晶など各種結晶状態の薄膜を形成するために用いることができる。 そ の他に上記薄膜形成用基板及び薄膜基板は発光素子、 あるいは光導波路、 あるいは表面弾性波 素子用などの圧纖、 あるいは電気回縫棚の ゃ誘纖などにも用いることができる。 上記のように本発明は、 ( 1 )窒化ガリウム、 窒化インジウム、 窒化アルミニウムのうちから 選ばれた少なくとも 1種以上を主成分とする単結晶をはじめ無定形、 多結晶、 配向性多結晶な ど各種結晶状態の薄膜を形成するための薄膜形成用基板、 ( 2 )窒化ガリゥム、窒化ィンジゥム、 窒化アルミニウムのうちから選ばれた少なくとも 1種以上を主成分とする少なくとも単結晶を はじめ無定形、 多結晶、 配向性多結晶など各種結晶状態の薄膜が形成された薄膜基板、 という 大きく分けて二種類の基板を提供する。上記二種類の基板には窒化ガリウム、窒化インジウム、 窒化アルミニウムのうちから選ばれた少なくとも 1種以上を主成分とする単結晶薄膜を形成し 得る。 これら 2種類の基板にはそれぞ 通ビアを有するものも含まれる。 上記二種類の基板 をより具体的にいえば、 ( 1 ) 薄膜形成用基板:窒化アルミニウムをはじめとする各種セラミツ ク材料を主成分とする難体をそのまま基板としたもの、 ( 2)薄膜基板:窒化アルミニウムを はじめとする各種セラミック材料を主成分とする焼結体に窒化ガリウム、 窒化インジウム、 窒 化アルミニウムのうちから選ばれた少なくとも 1種以上を主成分とする単結晶をはじめ無定形、 多結晶、 配向性多結晶のうちから選ばれた少なくともいずれかの結晶状態を有する薄膜を形成 したもの、 の二種類である。 本発明はこれらを提供する。 また、 上記二種類の基板にはそれぞ れ窒化ガリウム、 窒化インジウム、 窒化アルミニウムのうちから選ばれた少なくとも 1種以上 を主成分とする単結晶薄膜を形成し得る。 また、 これら二種類の基板にはそれぞれ導通ビアを 有するものも含まれる。 なお、 上記薄膜基板は薄膜形成用基板としても用いることができる。 上記のように本発明は薄膜形成用基板、 及び薄膜基板の 2種類の基板を提供するものである ことを説明した。 また、 この 2種類の基板の中で薄膜形成用基板は窒化アルミニウムをはじめ とする各種セラミック材料を主成分とする焼結体をそのまま基板としたものであることを説明 したが、 該薄膜形成用基板としては窒化アルミニウムを主成分とする焼結体、 及び炭化珪素、 窒化珪素、 窒化ガリウム、 酸化亜鉛、 酸化ベリリウム、 酸化アルミニウムなどの三方晶結晶系 あるいは六方晶系として分類できる結晶系を有する各種セラミック材料を主成分とする焼結体、 及びその他酸化ジルコニウム、 酸化マグネシウム、 アルミン酸マグネシウム、 酸化チタン、 チ タン酸バリウム、 チタン酸ジルコン酸鉛、 酸化イットリウムなどの希土 «化物、 酸ィ匕トリウ ム、 各種フェライト、 ムライト、 フォルステライト、 ステアタイト、 結晶化ガラス、 などの各 種セラミック材料を主成分とする焼結体をそのまま基板としたものだけでなぐ 該窒化アルミ 二ゥムを主成分とする焼結体、 及び炭化珪素、 窒化珪素、 窒化ガリウム、 酸化亜鉛、 酸化ベリ リウム、酸ィ匕アルミニウム、酸化ジルコニウム、酸化マグネシウム、 アルミン酸マグネシウム、 酸化チタン、 チタン酸バリウム、 チタン酸ジルコン酸鉛、 酸化イットリウムなどの希土鍾化 物、 酸ィ匕トリウム、 各種フェライト、 ムライト、 フォルステライト、 ステアタイト、 結晶化ガ ラスなどの各種セラミック材料を主成分とする焼結体に窒化ガリウム、 窒化インジウム、 窒化 アルミニウムのうちから選ばれた少なくとも 1種以上を主成分とする薄膜が形成されたものを 基板としたものも用いることができる。 すなわち本発明による薄膜形成用基板としては窒化ァ
ルミ二ゥムを主成分とする焼結体、 及び炭化珪素、 窒化珪素、 窒化ガリウム、 酸化亜鉛、 酸化 ベリリウム、 酸化アルミニウムなどの三方晶結晶系あるいは六方晶系として分類できる結晶系 を有する各種セラミック材料を主成分とする焼結体をそのまま基板としたもの、 窒化アルミ二 ゥムを主成分とする焼結体、 及び炭化珪素、 窒化珪素、 窒化ガリウム、 酸化亜鉛、 酸化べリリ ゥム、 酸化アルミニウムなどの三方晶結晶系あるいは六方晶系として分類できる結晶系を有す る各種セラミック材料を主成分とする焼結体、 及びその他酸化ジルコニウム、 酸化マグネシゥ ム、 アルミン酸マグネシウム、 酸化チタン、 チタン酸バリウム、 チタン酸ジルコン«、 酸化 イットリウムなどの希土 «ィ匕物、 酸化トリウム、 各種フェライト、 ムライト、 フォルステラ イト、 ステアタイト、 結晶化ガラス、 などの各種セラミック材料を主成分とする焼結体に窒化 ガリウム、 窒化インジウム、 窒化アルミニウムのうちから選ばれた少なくとも 1種以上を主成 分とする薄膜が形成されたものを基板としたもの (すなわち薄膜基板と同質)、 という 2種類の ものを用いることができる。 前記のように窒化アルミニウムをはじめとする各種セラミック材 料を主成分とする焼結体には窒化ガリウム、 窒化インジウム、 窒化アルミニウムのうちから選 ばれた少なくとも 1種以上を主成分とする薄膜を形成することができる。 窒化アルミニウムを 主成分とする焼結体、 及び炭化珪素、 窒化珪素、 窒化ガリウム、 酸化亜鉛、 酸化ベリリウム、 酸化アルミニウムなどの三方晶結晶系あるいは六方晶系として分類できる結晶系を有する各種 セラミック材料を主成分とする焼結体、 及びその他酸化ジルコニウム、 酸化マグネシウム、 ァ ルミン酸マグネシウム、 酸化チタン、 チタン酸バリウム、 チタン酸ジルコン酸鉛、 酸化イット リウムなどの希土 化物、 酸ィ匕トリウム、 各種フェライト、 ムライト、 フォルステラィ卜、 ステアタイト、 結晶化ガラス、 などの各種セラミック材料を主成分とする焼結体に形成される 窒化ガリウム、 窒化インジウム、 窒化アルミニウムのうちから選ばれた少なくとも 1種以上を 主成分とする薄膜として前記のように単結晶及び無定形、 多結晶、 配向性多結晶などの結晶状 態のものを用いることができる。 また、 該薄膜は前記のように単結晶、 無定形、 多結晶、 配向 性多結晶のうちから選ばれた単一の結晶状態のものだけでなくこれら結晶状態のうちから選ば れた少なくとも 2以上の結晶状態からなるものも同時に用いることができる。 また、 該薄膜は 前記のように単一層のものだけでなく少なくとも 2以上の層で構成されたものも好適に用いる ことができる。 また、 該薄膜は前記のように単一組成のものだけでなく異なる 2以上の組成か らなるものであっても好適に用いることができる。 また、 該薄膜は前記のように少なくとも 2 以上の層で構成され各薄膜層のうち少なくとも 2以上は異なる組成からなるものであっても好 適に用いることができる。 また、 該薄膜は前記のように導電性を有するものであっても好適に 用いることができる。 前記のように窒化アルミニウムを主成分とする焼結体、 及び炭化珪素、 窒化珪素、 窒化ガリウム、 酸化亜鉛、 酸化ベリリウム、 酸化アルミニウムなどの三方晶結晶系 あるいは六方晶系として分類できる結晶系を有する各種セラミック材料を主成分とする焼結体、 及びその他酸化ジルコニウム、 酸化マグネシウム、 アルミン酸マグネシウム、 酸化チタン、 チ タン酸パ Jゥム、 チタン酸ジルコン酸鉛、 酸化イットリウムなどの希土 «化物、 酸ィ匕トリウ ム、 各種フェライト、 ムライト、 フオルステライト、 ステアタイト、 結晶化ガラス、 などの各 種セラミック材料を主成分とする 結体に上記窒化ガリウム、 窒化インジウム、 窒化アルミ二 ゥムのうちから選ばれた少なくとも 1種以上を主成分とする薄膜があらかじめ形成されたもの を基板として用いることによりその上に形成される窒化ガリウム、 窒化インジウム、 窒化アル ミニゥムのうちから選ばれた少なくとも 1種以上を主成分とする単結晶薄膜の結晶性は該薄膜 を形成していない窒化アルミニウムを主成分とする焼結体をそのまま基板として用いる場合に 比べてより向上し易くなる。 窒化アルミニウムをはじめとする各種セラミック材料を主成分と する焼結体に窒化ガリウム、 窒化インジウム、 窒化アルミニウムのうちから選ばれた少なくと も 1種以上を主成分とする薄膜が形成された基板には導通ビアを有するものも含まれる。
本発明において上記のように薄膜形成用基板としては窒化アルミニウムをはじめとする各種 セラミック材料を主成分とする焼結体などをそのまま基板としたもの、 窒化アルミニウムをは じめとする各種セラミツク材料を主成分とする焼結体などに窒化ガリゥム、 窒化ィンジゥム、 窒化アルミニウムのうちから選ばれた少なくとも 1種以上を主成分とする薄膜が形成されたも のを基板としたもの、 という 2種類のものを用いることができる。
すなわち本発明による薄膜形成用基板として、 窒化アルミニウムを主成分とする焼結体、 及 び炭化珪素、 窒化珪素、 窒化ガリウム、 酸化亜鉛、 酸化ベリリウム、 酸化アルミニウムなどの 三方晶結晶系あるいは六方晶系として分類できる結晶構造を有する各種セラミック材料を主成 分とする焼結体、及びその他酸化ジルコニウム、酸化マグネシウム、アルミン酸マグネシウム、 酸化チタン、 チタン酸バリウム、 チタン酸ジルコン酸鉛、 酸化イットリウムなどの希土賺化 物、 酸化トリウム、 各種フェライト、 ムライト、 フォルステライト、 ステアタイト、 結晶化ガ ラス、 などの各種セラミック材料を主成分とする焼結体をそのまま基板としたものと、 窒化ガ リウム、 窒化インジウム、 窒化アルミニウムのうちから選ばれた少なくとも 1種以上を主成分 とする薄膜が形成されている窒化アルミニウムを主成分とする焼結体からなる基板、 及び窒化 ガリウム、 窒化インジウム、 窒化アルミニウムのうちから選ばれた少なくとも 1種以上を主成 分とする薄膜が形成されている炭化珪素、 窒化珪素、 窒化ガリウム、 酸化亜鉛、 酸化ベリリウ ム、 酸化アルミニウムなどの三方晶結晶系あるいは六方晶系として分類できる結晶系を有する 各種セラミック材料を主成分とする焼結体からなる基板、 及びその他酸化ジルコニウム、 酸化 マグネシウム、 アルミン酸マグネシウム、 酸化チタン、 チタン酸パリゥム、 チタン酸ジルコン 酸鉛、 酸ィ匕イットリウムなどの希土 ィ匕物、 酸 ί匕トリウム、 各種フェライト、 ムライト、 フ オルステライト、 ステアタイト、 結晶化ガラス、 などの各種セラミック材料を主成分とする焼 結体からなる基板、 も含まれる。
本発明 ¾^化アルミニウムを主成分とする焼結体、及び炭化珪素、窒化珪素、窒化ガリウム、 酸化 »、 酸化ベリリウム、 酸化アルミニウムなどの三方晶結晶系あるいは六方晶系として分 類できる結晶系を有する各種セラミック材料を主成分とする焼結体、 及びその他酸化ジルコ二 ゥム、 酸化マグネシウム、 アルミン酸マグネシウム、 酸化チタン、 チタン酸バリウム、 チタン 酸ジルコン■、 酸化イットリウムなどの希土難化物、 酸化トリウム、 各種フェライト、 ム ライト、 フォルステライト、 ステアタイト、 結晶化ガラス、 などの各種セラミック材料を主成 分とする焼結体に窒化ガリウム、 窒化インジウム、 窒化アルミニウムのうちから選ばれた少な くとも 1種以上を主成分とする薄膜が形成された薄膜基板も含む。 本発明による薄膜基板に形 成されている薄膜の結晶状態としては単結晶のものだけではなく無定形、 多結晶、 配向性多結 晶などのように必ずしも単結晶でない状態のものであってもよい。 より詳しく言えば、 本発明 による前記薄膜基板に形成されている薄膜の結晶状態としては単結晶、 無定形、 多結晶、 配向 性多結晶のうちから選ばれた少なくとも 1種以上の結晶状態のものであってもよぐ 例えば必 ずしも単結晶を含まない窒化ガリウム、 窒化インジウム、 窒化アルミニウムのうちから選ばれ た少なくとも 1種以上を主成分とする無定形状態だけの薄膜であってもよい。 本発明によるこ のような薄膜基板をより具体的に例示すれば、 例えば 1 ) 窒化アルミニウムを主成分とする焼 結体、 及び炭化珪素、 窒化珪素、 窒化ガリウム、 酸化亜鉛、 酸化ベリリウム、 酸化アルミニゥ ムなどの三方晶結晶系あるいは六方晶系として分類できる結晶系を有する各種セラミック材料 を主成分とする焼結体、 及びその他酸化ジルコニウム、 酸化マグネシウム、 アルミン酸マグネ シゥム、 酸化チタン、 チタン酸バリウム、 チタン酸ジルコン酸鉛、 酸化イットリウムなどの希 土 «化物、 酸ィ匕トリウム、 各種フェライト、 ムライト、 フォルステライト、 ステアタイト、 結晶化ガラス、 などの各種セラミック材料を主成分とする焼結体に窒化ガリウム、 窒化インジ ゥム、 窒化アルミニウムのうちから選ばれた少なくとも 1種以上を主成分とする単結晶薄膜が
形成された薄膜基板、また例えば 2)窒化アルミニウムを主成分とする脑体、及び炭化珪素、 窒化珪素、 窒化ガリウム、 酸化亜鉛、 酸化ベリリウム、 酸化アルミニウムなどの三方晶結晶系 あるいは六方晶系として分類できる結晶系を有する各種セラミック材料を主成分とする焼結体、 及びその他酸化ジルコニウム、 酸化マグネシウム、 アルミン酸マグネシウム、 酸化チタン、 チ タン酸バリウム、 チタン酸ジルコン酸鉛、 酸化イットリウムなどの希土鍵化物、 酸化トリゥ ム、 各種フェライト、 ムライト、 フォルステライト、 ステアタイト、 結晶化ガラス、 などの各 種セラミック材料を主成分とする焼結体に窒化ガリウム、 窒化インジウム、 窒化アルミニウム のうちから選ばれた少なくとも 1種以上を主成分とする無定形薄膜が形成された薄膜基板、 ま た例えば 3 ) 窒化アルミニウムを主成分とする焼結体、 及び炭化珪素、 窒化珪素、 窒化ガリウ ム、 酸化赚、 酸化ベリリウム、 酸化アルミニウムなどの三方晶結晶系あるいは六方晶系とし て分類できる結晶系を有する各種セラミック材料を主成分とする焼結体、 及びその他酸化ジル コニゥム、 酸ィ匕マグネシウム、 ァレミン酸マグネシウム、 酸化チタン、 チタン酸バリウム、 チ タン酸ジルコン^^、酸化イットリウムなどの希土 匕物、酸ィ匕トリウム、各種フェライ卜、 ムライト、 フォルステライト、 ステアタイト、 結晶化ガラス、 などの各種セラミック材料を主 成分とする焼結体に窒化ガリウム、 窒化インジウム、 窒化アルミニウムのうちから選ばれた少 なくとも 1種以上を主成分とする多結晶薄膜が形成された薄膜基板、 また例えば 4) 窒化アル ミニゥムを主成分とする焼結体、 及び炭化珪素、 窒化珪素、 窒化ガリウム、 酸化亜鉛、 酸化べ リリウム、 酸化アルミニウムなどの三方晶結晶系あるいは六方晶系として分類できる結晶系を 有する各種セラミック材料を主成分とする焼結体、 及びその他酸化ジルコニウム、 酸化マグネ シゥム、 アルミン酸マグネシウム、 酸化チタン、 チタン酸バリウム、 チタン酸ジルコン 、、 酸化イットリウムなどの希土 «化物、 酸 ί匕トリウム、 各種フェライト、 ムライト、 フォルス テライト、 ステア夕イト、 結晶化ガラス、 などの各種セラミック材料を主成分とする焼結体に 窒化ガリウム、 窒化インジウム、 窒化アルミニウムのうちから選ばれた少なくとも 1種以上を 主成分とする配向性多結晶薄膜が形成された薄膜基板、 また例えば 5 ) 窒化アルミニウムを主 成分とする焼結体、 及び炭化珪素、 窒化珪素、 窒化ガリウム、 酸化亜鉛、 酸化ベリリウム、 酸 化アルミニウムなどの三方晶結晶系あるいは六方晶系として分類できる結晶系を有する各種セ ラミック材料を主成分とする焼結体、 及びその他酸化ジ Jレコニゥム、 酸化マグネシウム、 アル ミン酸マグネシウム、 酸化チタン、 チタン酸バリウム、 チタン酸ジルコン酸鉛、 酸化イツトリ ゥムなどの希土 ィ匕物、 酸ィ匕トリウム、 各種フェライト、 ムライト、 フォルステライト、 ス テアタイト、結晶化ガラス、などの各種セラミック材料を主成分とする;^結体に窒化ガリウム、 窒化ィンジゥム、 窒化アルミニウムのうちから選ばれた少なくとも 1種以上を主成分とする無 定形薄膜が形成されさらにその上に窒化ガリウム、 窒化インジウム、 窒化アルミニウムのうち から選ばれた少なくとも 1種以上を主成分とする単結晶薄膜が形成された薄膜基板、 また例え ば 6 ) 窒化アルミニウムを主成分とする焼結体、 及び炭化珪素、 窒化珪素、 窒化ガリウム、 酸 化 «、 酸化ベリリウム、 酸化アルミニウムなどの三方晶結晶系あるいは六方晶系として分類 できる結晶系を有する各種セラミック材料を主成分とする焼結体、 及びその他酸化ジルコニゥ ム、 酸化マグネシウム、 ァリレミン酸マグネシウム、 酸化チタン、 チタン酸バリウム、 チタン酸 ジルコン酸鉛、 酸ィ匕イットリウムなどの希土 «ィ匕物、 酸ィ匕トリウム、 各種フェライト、 ムラ イト、 フォルステライト、 ステアタイト、 結晶化ガラス、 などの各種セラミック材料を主成分 とする焼結体に窒化ガリウム、 窒化インジウム、 窒化アルミニウムのうちから選ばれた少なく とも 1種以上を主成分とする多結晶薄膜が形成されさらにその上に窒化ガリゥム、 窒化ィンジ ゥム、 窒化アルミニウムのうちから選ばれた少なくとも 1種以上を主成分とする単結晶薄膜が 形成された薄膜基板、また例えば 7 )窒化アルミニウムを主成分とする離体、及び炭化珪素、 窒化珪素、 窒化ガリウム、 酸化亜鉛、 酸化ベリリウム、 酸化アルミニウムなどの三方晶結晶系
あるいは六方晶系として分類できる結晶系を有する各種セラミック材料を主成分とする焼結体、 及びその他酸化ジルコニウム、 酸化マグネシウム、 アルミン酸マグネシウム、 酸化チタン、 チ タン酸バリウム、 チタン酸ジルコン酸鉛、 酸化イットリウムなどの希土鍵化物、 酸化トリゥ ム、 各種フェライト、 ムライト、 フオルステライト、 ステアタイト、 結晶化ガラス、 などの各 種セラミック材料を主成分とする焼結体に窒化ガリウム、 窒化インジウム、 窒化アルミニウム のうちから選ばれた少なくとも 1種以上を主成分とする配向性多結晶薄膜が形成されさらにそ の上に窒化ガリゥム、 窒化ィンジゥム、 窒化アルミニウムのうちから選ばれた少なくとも 1種 以上を主成分とする単結晶薄膜が形成された薄膜基板、 また例えば 8 ) 窒化アルミニウムを主 成分とする焼結体、 及び炭化珪素、 窒化珪素、 窒化ガリウム、 酸化亜鉛、 酸化ベリリウム、 酸 化アルミニウムなどの三方晶結晶系あるいは六方晶系として分類できる結晶系を有する各種セ ラミック材料を主成分とする焼結体、 及びその他酸化ジルコニウム、 酸化マグネシウム、 アル ミン酸マグネシウム、 酸化チタン、 チタン酸バリウム、 チタン酸ジルコン酸鉛、 酸化イツトリ ゥムなどの希土難化物、 酸化トリウム、 各種フェライト、 ムライト、 フォルステライト、 ス テアタイト、結晶化ガラス、などの各種セラミック材料を主成分とする! ¾結体に窒化ガリウム、 窒化インジウム、 窒化アルミニウムのうちから選ばれた少なくとも 1種以上を主成分とする単 結晶薄膜が形成されさらにその上に窒化ガリウム、 窒化インジウム、 窒化アルミニウムのうち から選ばれた少なくとも 1種以上を主成分とする単結晶薄膜が形成された薄膜基板、 また例え ば 9 ) 窒化アルミニウムを主成分とする焼結体、 及び炭化珪素、 窒化珪素、 窒化ガリウム、 酸 化亜鉛、 酸化ベリリウム、 酸化アルミニウムなどの三方晶結晶系あるいは六方晶系として分類 できる結晶系を有する各種セラミック材料を主成分とする焼結体、 及びその他酸化ジルコニゥ ム、 酸化マグネシウム、 アルミン酸マグネシウム、 酸化チタン、 チタン酸バリウム、 チタン酸 ジルコン醒、 酸化イットリウムなどの希土難化物、 酸化トリウム、 各種フェライト、 ムラ イト、 フォルステライト、 ステアタイト、 結晶化ガラス、 などの各種セラミック材料を主成分 とする焼結体に窒化ガリウム、 窒化インジウム、 窒化アルミニウムのうちから選ばれた少なく とも 1種以上を主成分とする無定形薄膜が形成されさらにその上に窒化ガリゥム、 窒化ィンジ ゥム、 窒化アルミニウムのうちから選ばれた少なくとも 1種以上を主成分とする配向性多結晶 薄膜が形成されさらにその上に窒化ガリウム、 窒化インジウム、 窒化アルミニウムのうちから 選ばれた少なくとも 1種以上を主成分とする単結晶薄膜が形成された薄膜基板、 などである。 なお、 本発明による窒化アルミニウムを主成分とする焼結体からなる基板、 及び炭化珪素、 窒化珪素、 窒化ガリウム、 酸化碰、 酸化ベリリウム、 酸化アルミニウムなどの三方晶結晶系 あるいは六方晶系として分類できる結晶系を有する各種セラミック材料を主成分とする焼結体 からなる基板、 及びその他酸化ジルコニウム、 酸化マグネシウム、 アルミン酸マグネシウム、 酸化チタン、 チタン酸バリゥム、 チタン酸ジルコン酸鉛、 酸化ィットリゥムなどの希土 «化 物、 酸化トリウム、 各種フェライト、 ムライト、 フ才ルステライト、 ステア夕イト、 結晶化ガ ラス、 などの各種セラミック材料を主成分とする焼結体からなる基板に窒化ガリウム、 窒化ィ ンジゥム、 窒化アルミニウムのうちから選ばれた少なくとも 1種以上を主成分とする薄膜が形 成された薄膜基板は形成されている薄膜が多層化され各層が単結晶、 無定形、 多結晶、 配向性 多結晶のうちから選ばれた少なくとも 1種以上の結晶状態で、 組成も各薄膜層で異なりさらに 厚みも各層で異なっていたとしてもその上には単結晶薄膜が形成し得る。 また本発明による薄 膜基板に形成される単結晶薄膜は、 窒化アルミニウムを主成分とする焼結体からなる基板、 及 び炭化珪素、 窒化珪素、 窒化ガリウム、 酸化亜鉛、 酸化ベリリウム、 酸化アルミニウムなどの 三方晶結晶系あるいは六方晶系として分類できる結晶系を有する各種セラミック材料を主成分 とする焼結体からなる基板、 及びその他酸化ジルコニウム、 酸化マグネシウム、 アルミン酸マ グネシゥム、 酸化チタン、 チタン酸バリウム、 チタン酸ジルコン 、 酸化イットリウムなど
の希土 化物、 酸化トリウム、 各種フェライト、 ムライト、 フォルステライト、 ステアタイ ト、 結晶化ガラス、 などの各種セラミック材料を主成分とする焼結体からなる基板に直接形成 されるものより窒化アルミニウムを主成分とする焼結体からなる基板、 及び炭化珪素、 窒化珪 素、 窒化ガリウム、 酸化亜鉛、 酸化ベリリウム、 酸化アルミニウムなどの三方晶結晶系あるい は六方晶系として分類できる結晶系を有する各種セラミック材料を主成分とする焼結体からな る基板、 及びその他酸化ジルコニウム、 酸化マグネシウム、 アルミン酸マグネシウム、 酸化チ タン、 チタン酸バリウム、 チタン酸ジルコン酸鉛、 酸化イットリウムなどの希土鍵化物、 酸 ィ匕トリウム、 各種フェライト、 ムライト、 フォルステライト、 ステアタイト、 結晶化ガラス、 などの各種セラミック材料を主成分とする焼結体からなる基板にあらかじめ単結晶、 無定形、 多結晶、 配向性多結晶のうちから選ばれた少なくとも 1種以上の結晶状態の薄膜が形成された 基板を用い、 その上に形成されたもののほうが結晶性に優れる。
上記本発明による窒化アルミニウムを主成分とする焼結体、 及び炭化珪素、 窒化珪素、 窒化 ガリウム、 酸化碰、 酸化ベリリウム、 酸化アルミニウムなどの三方晶結晶系あるいは六方晶 系として分類できる結晶系を有する各種セラミック材料を主成分とする焼結体からなる基板、 及びその他酸化ジルコニウム、 酸化マグネシウム、 アルミン酸マグネシウム、 酸化チタン、 チ タン酸パリゥム、 チタン酸ジルコン酸鉛、 酸化イットリウムなどの希土難化物、 酸化トリゥ ム、 各種フェライト、 ムライト、 フオルステライト、 ステアタイト、 結晶化ガラス、 などの各 種セラミック材料を主成分とする焼結体からなる基板に窒化ガリウム、 窒化インジウム、 窒化 アルミニウムのうちから選ばれた少なくとも 1種以上を主成分とする薄膜が形成された薄膜基 板において、 少なくとも 2層以上で形成されている薄膜の成分が異なるという意味は薄膜の実 質的な糸賊が異なるということであり、薄膜の組成として該薄膜の主成分である窒化ガリウム、 窒化ィンジゥム、 窒化アルミ二ゥムのうちから選ばれた少なくとも 1種以上からなる成分の割 合が異なるものだけでなぐ 例えば育膜が主成分として窒化ガリウム、 窒化インジウム、 窒化 アルミニゥムのうちから選ばれる 1種類だけでその他の成分として例えばドーピング剤だけの 場合なども含まれる。 より具体的に言えば、 薄膜の主成分が例えば窒化ガリウムだけでその他 実質的にドーピング剤としてマグネシウム (Mg) だけを含むものの場合、 窒化ガリウムとマ グネシゥムの組成比が異なるものも含まれる。 あるいは同様に、 薄膜の主成分が例えば窒化ァ ルミニゥムだけでその他実質的にドーピング剤として珪素 (S i ) だけを含むものの場合、 窒 化アルミニゥムと珪素の組成比が異なるものも含まれる。 本発明においては上記のように窒化 アルミニウムを主成分とする焼結体からなる基板、 及び炭化珪素、 窒化珪素、 窒化ガリウム、 酸化亜鉛、 酸化ベリリウム、 酸化アルミニウムなどの三方晶結晶系あるいは六方晶系として分 類できる結晶系を有する各種セラミック材料を主成分とする焼結体からなる基板、 及びその他 酸化ジルコニウム、 酸化マグネシウム、 アルミン酸マグネシウム、 酸化チタン、 チタン酸バリ ゥム、 チタン酸ジルコン難、 酸化イットリウムなどの希土謙化物、 酸化トリウム、 各種フ エライト、 ムライト、 フォルステライト、 ステアタイト、 結晶化ガラス、 などの各種セラミツ ク材料を主成分とする焼結体からなる基板に窒化ガリウム、 窒化インジウム、 窒化アルミニゥ ムのうちから選ばれた少なくとも 1種以上を主成分とする同一成分の薄膜を単一層としてある いは少なくとも 2層以上に分けて形成できるだけでなく異なる成分からなる少なくとも 2層以 上の薄膜として形成することができる。 同一成分を 2層以上に分けて形成したものや異なる成 分のものを 2層以上に形成したものであっても形成された薄膜が単結晶である場合該単結晶薄 膜のミラー指数 (0 0 2 ) の格子面の X線回折ロッキングカーブの半値幅が 2 4 0秒以下と優 れた結晶性のものが得られる。 また、 本発明においては窒化アルミニウムを主成分とする焼結 体からなる基板、 及び炭化珪素、 窒化珪素、 窒化ガリウム、 酸化亜鉛、 酸化ベリリウム、 酸化 アルミニウムなどの三方晶結晶系あるいは六方晶系として分類できる結晶系を有する各種セラ
ミック材料を主成分とする焼結体からなる基板、 及びその他酸化ジルコニウム、 酸化マグネシ ゥム、 アルミン酸マグネシウム、 酸化チタン、 チタン酸バリウム、 チタン酸ジルコン隱、 酸 化イットリウムなどの希土謹化物、 酸ィ匕トリウム、 各種フェライト、 ムライト、 フオルステ ライト、 ステアタイト、 結晶化ガラス、 などの各種セラミック材料を主成分とする焼結体から なる基板には前記のように少なくとも 2以上の層で構成される薄膜が形成できるが、 各薄膜層 のうち少なくとも 2以上は異なる組成からなるものであっても好適に用いることができる。 こ のことをより具体的に説明すれば、 例えば薄膜が 3層から構成される場合 3層のうち 2層は同 じ組成で残り 1層の組成が異なるもの、 及び 3層ともはそれぞれ組成が異なるもの、 の 2種類 の状態の薄膜が含まれる。 また、 例えば薄膜が 4層から構成される場合 4層のうち 2層は同じ 組成で残り 2層の組成がそれぞれ異なるもの、 4層のうち 3層は同じ組成で残り 1層の組成が 異なるもの、 4層ともそれぞれ組成が異なるもの、 の 3種類の状態の薄膜が含まれる。
本発明は上記のように、 窒化ガリウム、 窒化インジウム、 窒化アルミニウムのうちから選ば れた少なくとも 1種以上からなる無定形、 多結晶、 配向性多結晶、 単結晶のうちから選ばれた 少なくとも 1種以上の結晶状態の薄膜を形成し得る窒化アルミニウムを主成分とする焼結体か らなる薄膜形成用基板を提供する。 さらに、 窒化アルミニウムを主成分とする焼結体からなる 基板に窒化ガリウム、 窒化インジウム、 窒化アルミニウムのうちから選ばれた少なくとも 1種 以上からなる無定形、 多結晶、 配向性多結晶、 単結晶のうちから選ばれた少なくとも 1種以上 の結晶状態の薄膜が形成されている薄膜基板も提供する。
また、 本発明は上記のように、 窒化ガリウム、 窒化インジウム、 窒化アルミニウムのうちか ら選ばれた少なくとも 1種以上からなる無定形、 多結晶、 配向性多結晶、 単結晶のうちから選 ばれた少なくとも 1種以上の結晶状態の薄膜を形成し得る炭化珪素、窒化珪素、窒化ガリウム、 酸化亜鉛、 酸化ベリリウム、 酸化アルミニウムなどの三方晶結晶系あるいは六方晶系として分 類できる結晶系を有する各種セラミック材料を主成分とする焼結体からなる薄膜形成用基板を 提供する。 さらに、 炭化珪素、 窒化珪素、 窒化ガリウム、 酸化菌、 酸化ベリリウム、 酸化ァ ルミニゥムなどの三方晶結晶系あるいは六方晶系として分類できる結晶系を有する各種セラミ ック材料を主成分とする焼結体からなる基板に窒化ガリウム、 窒化インジウム、 窒化アルミ二 ゥムのうちから選ばれた少なくとも 1種以上からなる無定形、 多結晶、 配向性多結晶、 単結晶 のうちから選ばれた少なくとも 1種以上の結晶状態の薄膜が形成されている薄膜基板も提供す る。
上記薄膜形成用基板は窒化ガリウム、 窒化インジウム、 窒化アルミニウムのうちから選ばれ た少なくとも 1種以上からなる薄膜のうち単結晶薄膜を形成するために用いることができる。 又上記薄膜基板も窒化ガリウム、 窒化インジウム、 窒化アルミニウムのうちから選ばれた少な くとも 1種以上からなる単結晶薄膜を形成するために用いることができる。
上記で説明したように本発明による薄膜基板は、 窒化アルミニゥムを主成分とする焼結体か らなる基板に窒化ガリウム、 窒化インジウム、 窒化アルミニウムのうちから選ばれた少なくと も 1種以上を主成分とする薄膜が形成されていることを特徴とする薄膜基板、 である。 また本 発明による薄膜基板は、 炭化珪素、 窒化賴、 窒化ガリウム、 酸化亜鉛、 酸化ベリリウム、 酸 化アルミ二ゥムなどの三方晶結晶系あるいは六方晶系として分類できる結晶系を有する各種セ ラミツク材料を主成分とする焼結体からなる基板に窒化ガリゥム、 窒化ィンジゥム、 窒化アル ミニゥムのうちから選ばれた少なくとも 1種以上を主成分とする薄膜が形成されていることを 特徴とする薄膜基板、 である。 また本発明による薄膜基板は、 光 ¾i 性を有するセラミック材 料を主成分とする焼結体に窒化ガリウム、 窒化インジウム、 窒化アルミニウムのうちから選ば れた少なくとも 1種以上を主成分とする薄膜が形成されていることを特徴とする薄膜基板、 で ある。 また本発明による薄膜基板は、 セラミック材料を主成分とする焼結体に窒化ガリウム、
窒化インジウム、 窒化アルミニウムのうちから選ばれた少なくとも 1種以上を主成分とする単 結晶薄膜が形成されていることを特徴とする薄膜基板、 である。 本発明による薄膜基板はより 具体的に、 窒化アルミニウムを主成分とする焼結体からなる基板、 及び炭化珪素、 窒化珪素、 窒化ガリウム、 酸化亜鉛、 酸化ベリリウム、 酸化アルミニウムなどの三方晶結晶系あるいは六 方晶系として分類できる結晶系を有する各種セラミック材料を主成分とする焼結体からなる基 板、 及びその他例えば 化ジルコニウム、 酸化マグネシウム、 アルミン酸マグネシウム、 酸化 チタン、 チタン酸バリウム、 チタン酸ジルコン酸鉛、 酸化イットリウムなどの希土猶化物、 酸化トリウム、各種フェライト、 ムライト、 フォルステライト、 ステアタイト、結晶化ガラス、 などの各種セラミック材料を主成分とする焼結体からなる基板に窒化ガリゥム、 窒化ィンジゥ ム、 窒化アルミニウムのうちから選ばれた少なくとも 1種以上を主成分とし単結晶、 無定形、 多結晶、 配向性多結晶のうちから選ばれた少なくともいずれかの結晶状態の薄膜が形成されて いることを特徴とする薄膜基板、 である。
本発明による窒化アルミニウムを主成分とする焼結体からなる基板、 及び炭化珪素、 窒化珪 素、 窒化ガリウム、 酸化亜鉛、 酸化ベリリウム、 酸化アルミニウムなどの三方晶結晶系あるい は六方晶系として分類できる結晶系を有する各種セラミック材料を主成分とする焼結体からな る基板、 及びその他例えば魔化ジルコニウム、 酸化マグネシウム、 アルミン酸マグネシウム、 酸化チタン、 チタン酸バリウム、 チタン酸ジルコン酸鉛、 酸化ィットリウムなどの希土謙化 物、 酸化トリウム、 各種フェライト、 ムライト、 フォルステライト、 ステアタイト、 結晶化ガ ラス、 などの各種セラミック材料を主成分とする焼結体からなる基板上へ形成される窒化ガリ ゥム、 窒化インジウム、 窒化アルミニウムのうちから選ばれた少なくとも 1種以上を主成分と する薄膜として導電性を有するものが形成し得ることが見出された。 また、 窒化アルミニウム を主成分とする維体、及び炭化珪素、窒化珪素、窒化ガリウム、酸化葡、酸化ベリリウム、 酸化アルミニウムなどの三方晶結晶系あるいは六方晶系として分類できる結晶系を有する各種 セラミック材料を主成分とする焼結体、 及びその他酸化ジルコニウム、 酸化マグネシウム、 ァ ルミン酸マグネシウム、 酸化チタン、 チタン酸パリゥム、 チタン酸ジルコン隱、 酸化イット リウムなどの希土 «ィ匕物、 酸ィ匕トリウム、 各種フェライ卜、 ムライト、 フォルステライト、 ステアタイト、 結晶化ガラス、 などの各種セラミック材料を主成分とする焼結体を基板として この基板に窒化ガリウム、 窒化インジウム、 窒化アルミニウムのうちから選ばれた少なくとも
1種以上を主成分とする無定形、 多結晶、 配向性多結晶、 単結晶など各種結晶状態の薄膜をあ らかじめ形成した薄膜基板を用いた場合にも、 この基板に形成される窒化ガリウム、 窒化イン ジゥム、 窒化アルミニウムのうちから選ばれた少なくとも 1種以上を主成分とする薄膜は導電 性を有するものが形成し得ることが見出された。 このような導電性の窒化ガリウム、 窒化イン ジゥム、 窒化アルミニウムのうちから選ばれた少なくとも 1種以上を主成分とする薄膜を導通 ビアが形成されている窒化アルミニウムを主成分とする焼結体、 及び炭化珪素、 窒化珪素、 窒 化ガリウム、 酸化亜鉛、 酸化ベリリウム、 酸化アルミニウムなどの三方晶結晶系あるいは六方 晶系として分類できる結晶系を有する各種セラミック材料を主成分とする焼結体、 及びその他 例えば酸化ジルコニウム、 酸化マグネシウム、 アルミン酸マグネシウム、 酸化チタン、 チタン 酸バリウム、 チタン酸ジルコン酸鉛、 酸化イットリウムなどの希土讓化物、 酸化トリウム、 各種フェライト、 ムライト、 フオルステライト、 ステアタイト、 結晶化ガラス、 などの各種セ ラミツク材料を主成分とする焼結体に形成した薄膜基板は該導通ビアを介して該薄膜基板の上 下表面を電気的に接続できる。 したがってこのような導電性薄膜が形成されている薄膜基板あ るいは薄膜形成用基板を用いて発光素子などの半導体デバィスを作製すれば素子の片面でなく 上下面に電極を配置できるので電極を取り出すための薄膜エッチングカ坏要になりさらに該素 子のパッケージへの実装性を高めることができるので好ましい。 導電性を発現するために通常
は該薄膜にドーピンク を加えることで P型あるいは N型に半導体化できるようになる。 P型 あるいは N型に半導体化することで該薄膜を多層構造の発光素子を構成するひとつの半導体層 としても用いることができる。 本発明においては窒化アルミニゥム及び各種セラミック材料を 主成分とする焼結体からなる基板に窒化ガリウム、 窒化インジウム、 窒化アルミニウムのうち から選ばれた少なくとも 1種以上を主成分とする各種結晶状態の薄膜を形成した薄膜基板に形 成される無定形、 多結晶、 配向性多結晶、 単結晶など各種結晶状態の薄膜も導電性を有するも のが形成できる。 上記薄膜基板に形成された各種結晶状態の薄膜においても導電性はド一ピン グ剤を加え P型あるいは N型に半導体化することで発現するようになる場合が多いが、 窒化ガ リウム、 窒化インジウム、 窒化アルミニウムのうちから選ばれた少なくとも 1種以上を主成分 とする薄膜のなかで窒化ガリウム、 窒化インジウムを主成分とする薄膜 (窒化ガリウム +窒化 ィンジゥムの混合組成からなる薄膜を含む) はドーピング剤なしで自発的に N型に半 ¾#:化し 導電性が発現する場合がある。 P型あるいは N型に半導体化することで本発明による薄膜基板 に形成された各種結晶状態の薄膜を多層構造の発光素子を構成するひとつの半導体層として用 いることができる。 又、 上記各種結晶状態の薄膜を半導体化することで導通ビアを有する窒化 アルミニウムを主成分とする焼結体からなる基板に発光^?などの半導体デバイスを作製すれ ば素子の片面でなく上下面に電極を配置できるので電極を取り出すための薄膜エッチングカ坏 要になりさらに該素子のパッケージへの実装性を高めることができるので好ましい。 本発明に よる各種結晶状態の薄膜を P型半導体化するためのドーピング剤としてはマグネシウム、 ベリ リウム、 亜鉛、 炭素など 1種あるいは 2種以上同時に使用できる。 本発明による各種結晶状態 の薄膜を N型半導体化するためのドーピング剤としては珪素、 酸素など 1種あるいは 2種以上 同時に使用できる。 また上記 P型半導体及び N型半導体形成用ド一ビング剤の両方を用いるい わゆるコド一プによる半導体化も可能である。 半導体化された上記無定形、 多結晶、 配向性多 結晶、単結晶などの各種結晶状態の薄膜の室温における抵抗率は 1 X 1 04Ω . c m以下である ことが好ましい。 より好ましくは室温における抵抗率 1 X 1 0 2 Ω · c m以下である。 さらに好 ましく 温における抵抗率 1 X 1 0 · c m以下である。最も好ましくは室温における抵抗 率 1 X 1 0。Ω · c m以下である。 ,このような抵抗率を有する窒化ガリウム、 窒化インジウム、 窒化アルミニウムのうちから選ばれた少なくとも 1種以上を主成分とする薄膜を窒化アルミ二 ゥムを主成分とする焼結体からなる基板、及び炭化珪素、窒化珪素、窒化ガリウム、酸化 »、 酸化ベリリウム、 酸化アルミニウムなどの三方晶結晶系あるいは^晶系として分類できる結 晶系を有する各種セラミック材料を主成分とする焼結体からなる基板、 及びその他例えば 化 ジルコニウム、酸化マグネシウム、アルミン酸マグネシウム、酸化チタン、チタン酸バリウム、 チタン酸ジルコン^ 酸化イットリウムなどの希土 ¾化物、 酸化トリウム、 各種フェライ ト、 ムライト、 フォルステライト、 ステアタイト、 結晶化ガラス、 などの各種セラミック材料 を主成分とする焼結体からなる基板、 及びこれらの基板にあらかじめ窒化ガリウム、 窒化イン ジゥム、 窒化アルミニウムのうちから選ばれた少なくとも 1種以上を主成分とする薄膜が形成 されている薄膜基板に形成できることが明らかとなつた。
また本発明による上記窒化アルミニウムを主成分とする焼結体からなる基板、及び炭化珪素、 窒化珪素、 窒化ガリウム、 酸化亜鉛、 酸化ベリリウム、 酸化アルミニウムなどの三方晶結晶系 あるいは六方晶系として分類できる結晶系を有する各種セラミツク材料を主成分とする焼結体 からなる基板、 及びその他例えぱ襯化ジルコニウム、 酸化マグネシウム、 アルミン酸マグネシ ゥム、 酸化チタン、 チタン酸バリウム、 チタン酸ジルコン酸鉛、 酸化イットリウムなどの希土 難化物、 酸化トリウム、 各種フェライト、 ムライト、 フォルステラィト、 ステア夕イト、 結 晶化ガラス、 などの各種セラミック材料を主成分とする焼結体からなる基板、 及びこれらの基 板にあらかじめ窒化ガリウム、 窒化インジウム、 窒化アルミニウムのうちから選ばれた少なく
とも 1種以上を主成分とする薄膜が形成されている薄膜基板には単結晶を始めとして無定形、 多結晶、 配向性多結晶、 など各種結晶状態の導電性を有する窒化ガリウム、 窒化インジウム、 窒化アルミニウムのうちから選ばれた少なくとも 1種以上を主成分とする薄膜が形成できる。 本発明による上記窒化アルミニウムを主成分とする焼結体からなる基板、 及び炭化珪素、 窒化 珪素、 窒化ガリウム、 酸化亜鉛、 酸化ベリリウム、 酸化アルミニウムなどの三方晶結晶系ある いは六方晶系として分類できる結晶系を有する各種セラミック材料を主成分とする焼結体から なる基板、及びその他例えば ¾化ジルコニウム、酸化マグネシウム、アルミン酸マグネシウム、 酸化チタン、 チタン酸バリウム、 チタン酸ジルコン酸鉛、 酸化イットリウムなどの希土鍵化 物、 酸化トリウム、 各種フェライト、 ムライト、 フォルステライト、 ステアタイト、 結晶化ガ ラス、 などの各種セラミック材料を主成分とする焼結体からなる基板、 及びこれらの基板にあ らかじめ窒化ガリウム、 窒化インジウム、 窒化アルミニウムのうちから選ばれた少なくとも 1 種以上を主成分とする薄膜が形成されている薄膜基板に形成する窒化ガリゥム、 窒化ィンジゥ ム、 窒化アルミニウムのうちから選ばれた少なくとも 1種以上を主成分とする各種結晶状態の 薄膜を P型半 ί本化するためのド一ピンク^ ijとしてはマグネシウム(Mg)、ベリリウム(B e )、 カルシウム (C a)、 亜鉛 (Z n)、 カドミウム (C d)、 炭素 (C) など 1種あるいは 2種以上 同時に使用できる。 また霞化ガリウム、 窒化インジウム、 窒化アルミニウムのうちから選ば れた少なくとも 1種以上を主成分とする各種結晶状態の薄膜を N型半導体化するためのド一ピ ング剤としては珪素 (S i )、 ゲルマニウム (G e )、 酸素 (0)、 セレン (S e )、 テルル (T e ) など 1種あるいは 2種以上同時に使用できる。 また上記 P型半導体及び N型半導体形成用 ドーピンク の両方を用いるいわゆるコド一プによる半 ¾{本化も可能である。 上記薄膜形成用 基板、及び 膜基板には室温における抵抗率は 1 X 1 04Ω · c m以下の半 (本化された窒化ガ リウム、 窒化インジウム、 窒化アルミニウムのうちから選ばれた少なくとも 1種以上を主成分 とする無定形、 多結晶、 配向性多結晶、 単結晶など各種結晶状態の薄膜が形成できる。 また上 記薄膜形成用基板、 及び育膜基板には室温における 率 1 X 1 0 2Ω . c m以下の無定形、多 結晶、 配向性多結晶、 単結晶など各種結晶状態の薄膜が形成できるので好ましい。 さらに上記 薄 ^成用基板、 及び育膜基板には室温における抵抗率 1 X 1 0 Χ Ω · c m以下の無定形、 多結 晶、 配向性多結晶、 単結晶など各種結晶状態の薄膜が形成できるのでより好ましい。 また上記 薄 «成用基板、 及び 膜基板には室温における抵抗率 1 X 1 0 °Ω - c m以下の無定形、 多結 晶、 配向性多結晶、 単結晶など各種結晶状態の薄膜が形成できるのでさらに好ましい。 本発明 による無定形、 多結晶、 配向性多結晶、 単結晶など各種結晶状態の薄膜を上記のような抵抗率 を有する半導体となすことにより該各種結晶状態の薄膜を直接発光素子の一部として使用する ことができるし、 発光素子の電極を形成するために通常行われる発光素子を形成する薄膜層の 一部をエッチングする工程が省略でき、 さらに該発光素子をパッケージへ実装する場合などに 有利である。 Mg、 B e、 C a、 Z n、 C d、 C、 S i、 G e、 0、 S e、 T eなどのド一ピ ング剤を含む薄膜は通常該薄膜形成後、純 N2中や真空中などの雰囲気中で再熱処理を行ったり 電^泉などを照射することで導電性が向上する場合があるので i g実行することが好ましい。
M g, B e、 C a、 Z n、 C d、 Cなど窒化ガリウム、 窒化インジウム、 窒化アルミニウム のうちから選ばれた少なくとも 1種以上を主成分とする薄膜を P型半導体化するために用いら れるドーピング成分、 及び S i、 G e、 〇、 S e、 T eなど窒化ガリウム、 窒化インジウム、 窒化アルミニウムのうちから選ばれた少なくとも 1種以上を主成分とする薄膜を N型半導体化 するために用いられるドーピング成分は通常該窒化ガリウム、 窒化インジウム、 窒化アルミ二 ゥムのうちから選ばれた少なくとも 1種以上を主成分とする薄膜中に元素換算で 0. 0 0 0 0 1〜1 0モル%の範囲含まれることが好ましく、 該窒化ガリウム、 窒化インジウム、 窒化アル ミニゥムのうちから選ばれた少なくとも 1種以上を主成分とする薄膜の室温における抵抗率を
z少なくとも 1 X 104Ω · cm以下とすることができる。 上記ドーピング成分を元素騰で 0. 00001〜10モル%の範囲で含む窒化ガリウム、 窒化インジウム、 窒化アルミニウムのう ちから選ばれた少なくとも 1種以上を主成分とする薄膜が、 該主成分として窒化アルミニウム を 95モル%以下含み残りが窒化ガリゥム、 窒化ィンジゥムのうちから選ばれた少なくとも 1 種以上からなる組成を有するものである場合、通常室温における抵抗率が少なくとも 1 X 102 Ω · cm以下のものを作製し得る。 また、 上記ドーピング成分を元素醇で 0. 00001〜 10モル%の範囲で含む窒化ガリゥム、 窒化ィンジゥム、 窒化アルミニゥムのうちから選ばれ た少なくとも 1種以上を主成分とする薄膜が、 該主成分として窒化アルミニウム成分を 55モ ル%以下含み残りが窒化ガリウム、 窒化インジウムのうちから選ばれた少なくとも 1種以上か らなる組成を有するものである場合、通常室温における抵抗率が少なくとも 1 X 10丄0 · cm 以下のものを作製し得る。
上記のように本発明において窒化アルミニウムを主成分とする焼結体、 及び炭化珪素、 窒化 珪素、 窒化ガリウム、 酸化亜鉛、 酸化ベリリウム、 酸化アルミニウムなどの三方晶結晶系ある いは六方晶系として分類できる結晶系を有する各種セラミック材料を主成分とする焼結体、 及 びその他例えは衡匕ジルコニウム、酸化マグネシウム、アルミン酸マグネシウム、酸化チタン、 チタン酸バリウム、 チタン酸ジルコン酸鉛、 酸化イットリウムなどの希土謙化物、 酸化トリ ゥム、 各種フェライト、 ムライト、 フォルステライト、 ステア夕イト、 結晶化ガラス、 などの 各種セラミック材料を主成分とする焼結体を基板として用いた薄膜形成用基板、 及ぴ 膜基板 には窒化ガリウム、 窒化インジウム、 窒化アルミニウムのうちから選ばれた少なくとも 1種以 上を主成分とする無定形、 多結晶、 配向性多結晶、 単結晶など各種結晶状態の導電性を有する 薄膜が形成できる。本発明においてこのような薄膜の中で、
(0≤χ≤1. 0) の化学組成式であらわされる窒化ガリウムと窒化アルミニウムの二成分を主成分とする無定形、 多結晶、 配向性多結晶、 単結晶など各種結晶状態の導電性薄膜も得ることができる。 上記二成 分系の薄膜は波長 380 nm以下の紫外光の吸収が少ないのでこの材料を形成した薄膜基板を
Ξ兀素子作製用基板として用いれ〖堪板による光吸収が少ない、 したがって発光効率に優れた 発光素子が製造し得る。 該ニ成分系薄膜の導電性はドーピング剤を用い P型及び N型に半導体 ィ匕することで得られる。 P型半 本化用のド一ピンク^!にはマグネシウム (Mg)、 ベリリウム (Be), カリレシゥム (Ca)、 亜鉛 (Zn)、 カドミウム (Cd)、 炭素 (C) などを好適に用 いることができ、 その中ではマグネシウム (Mg) を用いることがより好ましい。 また、 N型 半 本化用のド一ピンク には珪素 (S i)、ゲルマニウム(Ge)、酸素(0)、セレン(S e)、 テルル (Te) などを好適に用いることができ、 その中では珪素 (S i) を用いることがより 好ましい。 上記二成分系の薄膜は主成分 AlxGa i一 ΧΝ (0≤χ≤1· 0) の化学式であらわ される組成物に対し上記 M gなどの Ρ型半導体化用のドーピング剤を元素換算で 0. 0000 1~10モル%の範囲で含むことができ室温における抵抗率 1 X 104Ω · cm以下の無定形、 多結晶、 配向性多結晶、 単結晶など各種結晶状態の導電性薄膜が形成できる。 その中で主成分 A 1 xGax_xN (0≤x≤0. 6) の化学式であらわされる組成物に対して上記 Mgなどの P 型半導体化用のドーピング剤を元素換算で 0. 00001〜 10モル%の範囲で含む薄膜は室 温における纖率 1 X 1 - cm~lX 102Ω - cm程度の無定形、多結晶、 配向性多結 晶、 単結晶など各種結晶状態の導電性薄膜が形成できる。 また、 上記二成分系の薄膜において 主成分 (0. 6≤x≤l. 0) の化学式であらわされる組成物に対して上記 M gなどの P型半導体化用のドーピング剤を元素換算で 0. 00001〜0. 5モレ%の範囲で 含む薄膜は室温における抵抗率 1 X 104Ω · cm以下の無定形、 多結晶、 配向性多結晶、 単結 晶など各種結晶状態の導電性薄膜が形成できる。 また、上記二成分系の薄膜は主成分 A 1 XG a !_ΧΝ (0≤χ≤1. 0) の化学式であらわされる組成物に対し上記 S iなどの N型半導体化用
のドーピング剤を元素換算で 0. 00001〜 10モル%の範囲で含むことができ室温におけ る ί氐抗率 1 X 102Ω - cm~lX 104Ω - cm以下の無定形、 多結晶、 配向性多結晶、 単結 晶など各種結晶状態の導電性薄膜が形成できる。 その中で主成分 AlxGai— XN (0. 6≤x ≤1. 0) の化学式であらわされる組成物に対し上記 S iなどの N型半導体化用のドーピング 剤を元素換算で 0. 00001-0. 5モル%の範囲で含む薄膜は室温における抵抗率 1 X 1 02Ω · cm〜: LX103Ω · cm以下の無定形、 多結晶、 配向性多結晶、 単結晶など各種結晶 状態の導電性薄膜が形成できる。 この組成の薄膜には x=l. 0すなわち主成分が窒化アルミ ニゥムだけからなり上記 S iなどの Ν型半導体化用のド一ピンク を元素 で 0. 0000 1モル%〜0. 5モル%の範囲で含有する薄膜も含まれる。 また、 主成分 AlxGa — XN (0 ≤x≤0. 6) の化学式であらわされる組成物に対して上記 S iなどの N型半導体化用のドー ビング剤を元素換算で 0. 00001〜 10モル%の範囲で含む薄膜は室温における抵抗率 1 X 10— 3Ω · cm~lX 10ΧΩ · c m程度の比較的低抵抗の無定形、 多結晶、 配向性多結晶、 単結晶など各種結晶状態の導電性薄膜が形成できる。 また、 上記二成分系薄膜において主成分 A 1 xGa!_xN (0≤χ≤1. 0) の化学式であらわされる組成物に対し上記 Mgなどの P型 半^ ί本化用のドーピング剤及び S iなどの N型半 本化用のドーピンク とを同時に合計で元 素購で 0. 00001〜 10モル%の範囲で含むことができその室温における抵抗率は 1 X 104Ω · cm以下の無定形、 多結晶、 配向性多結晶、 単結晶など各種結晶状態の導電性薄膜が 形成できる。 なお、 例え «Mg、 S iなどのド一ピンク^ ijの含有量が主成分に対して元素換算 で 0. 00001〜10モル%であるということは上記二成分系薄膜が主成分である A 1 xGa を 90〜99. 99999モル%の範囲含み、 ド一ピンク である Mg、 S iなどを元素 換算で 0. 00001〜10モル%範囲で含む組成からなるものであることを意味する。 本発明において窒化アルミニウムを主成分とする焼結体あるいは炭化珪素、 窒化珪素、 窒化 ガリウム、 酸化亜鉛、 酸化ベリリウムなどの六方晶系及び 化アルミニウムなどの三方晶系ぁ るいは六方晶系として分類できる結晶構造を有する各種セラミック材料を主成分とする焼結体 あるいはその他例えば 化ジルコニウム、 酸化マグネシウム、 アルミン酸マグネシウム、 酸化 チタン、 チタン酸バリウム、 チタン酸ジルコン薩、 酸化イットリウムなどの希土画匕物、 酸化トリウム、各種フェライト、ムライト、 フォルステライト、ステアタイト、結晶化ガラス、 などの各種セラミック材料を主成分とする焼結体を窒化ガリウム、 窒化インジウム、 窒化アル ミニゥムのうちから選ばれた少なくとも 1種以上を主成分とする単結晶、 無定形、 多結晶、 配 向性多結晶など各種結晶状態の薄膜を形成するための基板として用いることができる。 また、 本発明においては窒化アルミニウムを主成分とする焼結体、 あるいは炭化珪素、 窒化珪素、 窒 ィ匕ガリウム、 酸化亜鉛、 酸化ベリリウムなどの六方晶系及び 化アルミニウムなどの三方晶系 あるいは六方晶系として分類できる結晶構造を有する各種セラミック材料を主成分とする焼結 体、 あるいはその他例えば酸化ジルコニウム、 酸化マグネシウム、 アルミン酸マグネシウム、 酸化チタン、 チタン酸バリウム、 チタン酸ジルコン酸鉛、 酸化イットリウムなどの希土鍵化 物、 酸化トリウム、 各種フェライト、 ムライト、 フォルステライト、 ステア夕イト、 結晶化ガ ラス、 などの各種セラミック材料を主成分とする焼結体からなる基板に窒化ガリウム、 窒化ィ ンジゥム、 窒化アルミニウムのうちから選ばれた少なくとも 1種以上を主成分とする単結晶、 無定形、 多結晶、 配向性多結晶など各種結晶状態の薄膜を形成した薄膜基板が提供できる。 該 薄膜の厚みは任意のものが形成し得るが、 該薄膜を上記の各種セラミック材料を主成分とする 焼結体からなる薄膜形成用基板に形成する場合その厚みは薄膜中のピンホールや欠陥などを低 減化し易くするために少なくとも 0. 5 nm以上であることが望ましい。 上記窒化アルミニゥ ムを主成分とする焼結体からなる薄膜形成用基板に直接形成された薄膜は 0. 5 nm以上の厚 み、 あるいはさらに 10 m以上のものも形成できる。 またさらに 50 m以上といったもの
も形成し得る。 前記のように本発明においては MO CVD (有機金属化学気相分解成長) 法、 MOVP E (有機金属気相ェピタキシャル成長) 法、 ハイドライド VP E (水素ィ匕物気相ェピ タキシャル成長) 法、 クロライド VP E (塩化物気相ェピタキシャル成長) 法などのハライド VP E (八ロゲン化物気相ェピタキシャル成長) 法、 プラズマ CVD法、 その他の CVD (化 学細適成長) 法、 あるいは MB E 泉エピタキシー) 法、 あるいはエキシマレ一ザ一 などを用いたレーザ一アブレーション法、 P LD ひ \°ルスレーザーデポジション:ノ\°ルスレ一 ザー^^) 法など、 あるいはスパッタリング法などの方法を適宜用いて 5 0 0 m〜 1 0 0 0 m程度の比較的厚みの厚いものも形成し得るが、 通常薄膜の厚みとしては 2 0 0 m以下の ものを用いることが結晶性の高い単結晶薄膜を得る上では好ましい。 通常 MO CVD法、 ある いは M〇 V P E法では薄膜の成長速度が 1時間当り最大で 5 m〜 1 0 であり、 また通常 はそれ以下で比較的小さい場合が多いのに対して、 原料として塩化ガリゥムなどのようなハロ ゲン化物を用いるクロライド VP E法、 ハライド VP E法などを用いれば薄膜の成長速度が 1 時間当り 5 zm~ 2 0 0 mと大きくより短時間で厚みの厚い薄膜を形成することができるの で特に、 厚みの厚い薄膜を形成する場合は好ましい。 また、 窒化ガリウム、 窒化インジウム、 窒化アルミニウムのうちから選ばれた少なくとも 1種以上を主成分とする単結晶、 無定形、 多 結晶、 配向性多結晶など各種結晶状態の薄膜は上記窒化アルミニウムを主成分とする焼結体か らなる薄膜形成用基板、 あるいは炭化珪素、 窒化珪素、 窒化ガリウム、 酸化亜鉛、 酸化べリリ ゥムなどの六方晶系及び酸化アルミニウムなどの三方晶系あるいは六方晶系として分類できる 結晶構造を有する各種セラミック材料を主成分とする焼結体からなる薄膜形成用基板、 あるい はその他例えば酸化ジルコニウム、酸ィ匕マグネシウム、アルミン酸マグネシウム、酸化チタン、 チタン酸バリウム、 チタン酸ジルコン醒、 酸化イットリウムなどの希土靈化物、 酸化トリ ゥム、 各種フェライト、 ムライト、 フォルステライト、 ステア夕イト、 結晶化ガラス、 などの 各種セラミック材料を主成分とする焼結体からなる薄膜形成用基板に直接形成されたものだけ でなぐ 窒化アルミニウムを主成分とする焼結体、 あるいは炭化珪素、 窒化珪素、 窒化ガリウ ム、 酸化亜鉛、 酸化ベリリウムなどの六方晶系及び 化アルミニウムなどの三方晶系あるいは 六方晶系として分類できる結晶構造を有する各種セラミック材料を主成分とする焼結体、 ある いはその他例えば 化ジルコニウム、 酸化マグネシウム、 アルミン酸マグネシウム、 酸化チタ ン、 チタン酸パリゥム、 チタン酸ジルコン 、、 酸化イットリウムなどの希土鍵化物、 酸化 トリウム、 各種フェライト、 ムライト、 フォルステライト、 ステアタイト、 結晶化ガラス、 な どの各種セラミック材料を主成分とする焼結体を用いて作製される窒化ガリゥム、 窒化ィンジ ゥム、 窒化アルミニウムのうちから選ばれた少なくとも 1種以上を主成分とする単結晶、 無定 形、 多結晶、 配向性多結晶など各種結晶状態の薄膜が形成された薄膜基板の上に形成される薄 膜においても上記と同様な,を有するものが比較的容易に得られる。
本発明において窒化アルミニウムを主成分とする焼結体からなる基板、 あるいは炭化珪素、 窒化珪素、 窒化ガリウム、 酸化亜鉗、 酸化ベリリウムなどの六方晶系及び 化アルミニウムな どの三方晶系あるいは六方晶系として分類できる結晶構造を有する各種セラミック材料を主成 分とする焼結体からなる基板、 あるいはその他例えば 化ジルコニウム、 酸化マグネシウム、 アルミン酸マグネシウム、 酸化チタン、 チタン酸バリウム、 チタン酸ジルコン mi&、 酸化イツ トリウムなどの希土鍵化物、酸化トリウム、各種フェライト、ムライト、 フォルステライト、 ステアタイト、 結晶化ガラス、 などの各種セラミック材料を主成分とする焼結体からなる基板 に形成される窒化ガリウム、 窒化インジウム、 窒化アルミニウムのうちから選ばれた少なくと も 1種以上を主成分とする単結晶薄膜、 配向性多結晶薄膜の結晶性は前記のように焼結体の組 成や光透過性あるいは焼結体粒子の大きさ、 基板の表面状態、 形成される薄膜の構成、 あるい は薄膜形成条件などにも影響されるが、 一方では形成される該薄膜の厚みにも影響される。
本発明において窒化アルミニウムを主成分とする焼結体からなる基板には窒化ガリウム、 窒 化ィンジゥム、 窒化アルミニウムのうちから選ばれた少なくとも 1種以上を主成分とする厚み 0. 5 nm以上の単結晶薄膜が形成できる。 この厚みの単結晶薄膜の結晶性としてはミラ一指 数 (0 0 2) の格子面の X線回折ロッキングカーブの半値幅として 3 0 0秒以下のものが形成 し得る。 また、 本発明による窒化アルミニウムを主成分とする焼結体からなる薄膜形成用基板 あるいは薄膜基板を用いることで 0. 3 m以上の厚みの上記単結晶薄膜も形成できる。 窒化 ガリウム、 窒化インジウム、 窒化アルミニウムのうちから選ばれた少なくとも 1種以上を主成 分とする単結晶薄膜の厚みが 0. 3 m以上のものであれば該単結晶薄膜のミラ一指数 (0 0 2 ) の格子面の X線回折ロッキングカーブの半値幅として 2 4 0秒以下の結晶性のものが得ら れ易い。本発明による窒化アルミニウムを主成分とする焼結体からなる基板を用いることで 3. 5 以上の厚みの上記単結晶薄膜も形成できる。 窒化ガリウム、 窒化インジウム、 窒化アル ミニゥムのうちから選ばれた少なくとも 1種以上を主成分とする単結晶薄膜の厚みが 3. 5 11 m以上のものであれば該単結晶薄膜のミラ一指数 ( 0 0 2) の格子面の X線回折ロッキング力 ーブの半値幅として 2 0 0秒以下の結晶性のものが得られ易い。 また、 本発明による窒 ί匕アル ミニゥムを主成分とする焼結体からなる基板を用いることで 1 0 以上の比較的厚い単結晶 薄膜も形成できる。 窒化ガリウム、 窒化インジウム、 窒化アルミニウムのうちから選ばれた少 なくとも 1種以上を主成分とする単結晶薄膜の厚みが 1 0 zm以上のものであつても該単結晶 薄膜のミラ一指数 (0 0 2) の格子面の X線回折ロッキングカーブの半値幅として 1 5 0秒以 下の結晶性に優れたものが得られ易い。 本発明による窒化アルミニウムを主成分とする焼結体 からなる基板に形成される窒化ガリウム、 窒化インジウム、 窒化アルミニウムのうちから選ば れた少なくとも 1種以上を主成分とする単結晶薄膜の厚みとして 5 0 xm以上は十分可能であ る。 窒化ガリウム、 窒化インジウム、 窒化アルミニウムのうちから選ばれた少なくとも 1種以 上を主成分とする単結晶薄膜の厚みが 5 0 xm以上のものであれば該単結晶薄膜のミラー指数
( 0 0 2 ) の格子面の X線回折ロッキングカーブの半値幅として 1 3 0秒以下の結晶性のもの が得られ易く好ましい。 本発明による窒化アルミニウムを主成分とする焼結体からなる基板に は窒化ガリウム、 窒化インジウム、 窒化アルミニウムのうちから選ばれた少なくとも 1種以上 を主成分とする単結晶薄膜として厚み 2 0 0 m程度のものは十分形成が可能である。 なお、 例えば窒化ガリウム、 窒化インジウム、 窒化アルミニウムのうちから選ばれた少なくとも 1種 以上を主成分とする無定形、 多結晶、 配向性多結晶、 単結晶など各種結晶状態の薄膜をあらか じめ形成した基板を用いたり、 あるいは) 性の窒化アルミニウムを主成分とする焼結体か らなる基板を用いれば実際上 1 0 0 0 m程度の厚みの単結晶薄膜も形成し得るが、 通常窒化 ガリウム、 窒化インジウム、 窒ィ匕アルミニウムのうちから選ばれた少なくとも 1種以上を主成 分とする単結晶薄膜の厚みとしては 2 0 0 m程度以下のものが好ましい。 本発明において薄 膜は通常 MO CVD法や MOV P E法あるいはハライド VP E法などの非平衡状態で形成され るため該薄膜の厚みが 2 0 0 mより厚くなれば上記のように結晶性の低下が生じ易くなる場 合があるからである。
本発明において、 上記で示した窒化ガリウム、 窒化インジウム、 窒化アルミニウムのうちか ら選ばれた少なくとも 1種以上を主成分とする単結晶薄膜の ,と結晶性との関係は窒化アル ミニゥムを主成分とする焼結体に直接形成されたものだけではなく、 窒化アルミニウムを主成 分とする焼結体を用いて作製される窒化ガリウム、 窒化インジウム、 窒化アルミニウムのうち から選ばれた少なくとも 1種以上を主成分とする単結晶、 無定形、 多結晶、 配向性多結晶など 各種結晶状態の薄膜があらかじめ形成された薄膜基板の上に形成された単結晶薄膜においても 同様な薄膜の膜厚と結晶性との関係を有する。
また、 基板としては上記窒化アルミニウムを主成分とする焼結体からなるものだけでなく、
炭化珪素、 窒化珪素、 窒化ガリウム、 酸化亜鉛、 酸化ベリリウムなどの六方晶系及び 化アル ミニゥムなどの三方晶系あるいは六方晶系として分類できる結晶構造を有する各種セラミック 材料を主成分とする焼結体からなる基板にも窒化ガリウム、 窒化インジウム、 窒化アルミニゥ ムのうちから選ばれた少なくとも 1種以上を主成分とする単結晶、 無定形、 多結晶、 配向性多 結晶など各種結晶状態の薄膜が形成できる。 本発明において炭化珪素、 窒化珪素、 窒化ガリウ ム、 酸化 »、 酸化ベリリウムなどの六方晶系及び 化アルミニウムなどの三方晶系あるいは 六方晶系として分類できる結晶構造を有する各種セラミック材料を主成分とする焼結体からな る基板に形成される窒化ガリウム、 窒化インジウム、 窒化アルミニウムのうちから選ばれた少 なくとも 1種以上を主成分とする単結晶薄膜、 配向性多結晶薄膜の結晶性は前記のように基板 の表面状態、 形成される薄膜の構成、 あるいは薄膜形成条件などにも影響されるが、 一方では 形成される該薄膜の厚みにも影響される。本発明において炭化珪素、窒化珪素、窒化ガリウム、 酸化亜鉛、 酸化ベリリウムなどの六方晶系及び酸化アルミニウムなどの三方晶系あるいは六方 晶系として分類できる結晶構造を有する各種セラミック材料を主成分とする焼結体からなる基 板には窒化ガリウム、 窒化インジウム、 窒化アルミニウムのうちから選ばれた少なくとも 1種 以上を主成分とする厚み 0. 5 nm以上の単結晶薄膜が形成できる。 その結晶性は該単結晶薄 膜のミラー指数 (0 0 2 ) の格子面の X線回折ロッキングカーブの半値幅として 3 0 0秒以下 のものが形成し得る。 また、 本発明による炭化珪素、 窒化珪素、 窒化ガリウム、 酸化亜鉛、 酸 ィ匕ベリリゥムなどの六方晶系及び酸化アルミニウムなどの三方晶系あるいは六方晶系として分 類できる結晶構造を有する各種セラミック材料を主成分とする焼結体からなる基板を用いるこ とで 0. 3 m以上の厚みの上記単結晶薄膜も形成できる。 窒化ガリウム、 窒化インジウム、 窒化アルミニウムのうちから選ばれた少なくとも 1種以上を主成分とする単結晶薄膜の厚みが 0. 3 m以上のものにおいても該単結晶薄膜のミラ一指数 (0 0 2 ) の格子面の X線回折口 ッキングカーブの半値幅として 3 0 0秒以下の結晶性のものが得られ易い。 本発明による炭化 珪素、 窒化珪素、 窒化ガリウム、 酸化亜鉛、 酸化ベリリウムなどの六方晶系及び 化アルミ二 ゥムなどの三方晶系あるいは六方晶系として分類できる結晶構造を有する各種セラミック材料 を主成分とする焼結体からなる基板を用いることで 3. 5 zxm以上の厚みの上記単結晶薄膜も 形成できる。 窒化ガリウム、 窒化インジウム、 窒化アルミニウムのうちから選ばれた少なくと も 1種以上を主成分とする単結晶薄膜の厚みが 3. 5 m以上のものであれば該単結晶薄膜の ミラー指数 (0 0 2) の格子面の X線回折ロッキングカーブの半値幅として 2 4 0秒以下の結 晶性のものが得られ易い。 また、本発明による炭化珪素、窒化珪素、窒化ガリウム、酸化 、 酸化べリリウムなどの六方晶系及ぴ襯化アルミ二ゥムなどの三方晶系あるレゝは六方晶系として 分類できる結晶構造を有する各種セラミック材料を主成分とする焼結体からなる基板を用いる ことで 1 0 m以上の比較的厚い単結晶薄膜も形成できる。 窒化ガリウム、 窒化インジウム、 窒化アルミニウムのうちから選ばれた少なくとも 1種以上を主成分とする単結晶薄膜の厚みが 1 0 m以上のものであっても該単結晶薄膜のミラ一指数 (0 0 2 ) の格子面の X線回折ロッ キングカーブの半値幅として 2 4 0秒以下の結晶性に優れた単結晶薄膜が得られ易い。 また、 本発明による炭化珪素、 窒化珪素、 窒化ガリウム、 酸化亜鉛、 酸化ベリリウムなどの六方晶系 及び酸化アルミニウムなどの三方晶系あるいは六方晶系として分類できる結晶構造を有する各 種セラミック材料を主成分とする焼結体からなる基板に形成される窒化ガリウム、 窒化インジ ゥム、 窒化アルミニウムのうちから選ばれた少なくとも 1種以上を主成分とする単結晶薄膜の 厚みとして 5 0 m以上は十分可能である。本発明による炭化珪素、窒化珪素、窒化ガリウム、 酸化亜鉛、 酸化ベリリウムなどの六方晶系及ぴ谢匕アルミニウムなどの三方晶系あるいは六方 晶系として分類できる結晶構造を有する各種セラミック材料を主成分とする焼結体からなる基 板に形成される窒化ガリウム、 窒化インジウム、 窒化アルミニウムのうちから選ばれた少なく
とも 1種以上を主成分とする単結晶薄膜の厚みが 5 0 m以上のものであれば該単結晶薄膜の ミラー指数 (0 0 2 ) の格子面の X線回折ロッキングカーブの半値幅として 2 0 0秒以下の結 晶性のものが得られ易く好ましい。 また、 本発明による炭化珪素、 窒化珪素、 窒化ガリウム、 酸化赚、 酸化ベリリウムなどの六方晶系及び 化アルミニウムなどの三方晶系あるいは六方 晶系として分類できる結晶構造を有する各種セラミック材料を主成分とする焼結体からなる基 板に形成される窒化ガリウム、 窒化インジウム、 窒化アルミニウムのうちから選ばれた少なく とも 1種以上を主成分とする単結晶薄膜の厚みとして 1 0 0 !〜 2 0 0 m程度のものは十 分可能である。 なお、 例えば窒化ガリウム、 窒化インジウム、 窒化アルミニウムのうちから選 ばれた少なくとも 1種以上を主成分とする無定形、 多結晶、 配向性多結晶、 単結晶など各種結 晶状態の薄膜をあらかじめ形成した基板を用いたり、あるいは) 性の炭化珪素、窒化珪素、 窒化ガリウム、 酸化亜鉛、 酸化ベリリウムなどの六方晶系及び酸化アルミニウムなどの三方晶 系あるいは六方晶系として分類できる結晶構造を有する各種セラミック材料を主成分とする焼 結体からなる基板には窒化ガリウム、 窒化インジウム、 窒化アルミニウムのうちから選ばれた 少なくとも 1種以上を主成分とする単結晶薄膜の厚みが 5 0 0 m〜 1 0 0 0 m程度のもの であっても形成し得るが、 通常窒化ガリウム、 窒化インジウム、 窒化アルミニウムのうちから 選ばれた少なくとも 1種以上を主成分とする単結晶薄膜の厚みとしては 2 0 0 m程度以下の ものが好ましい。 本発明において薄膜は通常 MOCVD法や MOVP E法あるいはハライド V P E法などの非平衡状態で形成されるため該薄膜の厚みが 2 0 0 / mより厚くなれば上記のよ うに結晶性の低下が生じ易くなる場合があるからである。
本発明において、 上記で示した窒化ガリウム、 窒化インジウム、 窒化アルミニウムのうちか ら選ばれた少なくとも 1種以上を主成分とする単結晶薄膜の IU¥と結晶性との関係は炭化珪素、 窒化珪素、 窒化ガリウム、 酸化亜鉛、 酸化ベリリウムなどの六方晶系及び酸化アルミニウムな どの三方晶系あるいは六方晶系として分類できる結晶構造を有する各種セラミック材料を主成 分とする焼結体に単一層として形成されたものだけではなぐ 炭化珪素、 窒化珪素、 窒化ガリ ゥム、 酸化亜鉛、 酸化ベリリウムなどの六方晶系及び ¾化アルミニウムなどの三方晶系あるい は六方晶系として分類できる結晶構造を有する各種セラミック材料を主成分とする焼結体を用 いて作製される窒化ガリウム、 窒化インジウム、 窒化アルミニウムのうちから選ばれた少なく とも 1種以上を主成分とする単結晶、 無定形、 多結晶、 配向性多結晶など各種結晶状態の薄膜 があらかじめ形成された薄膜基板の上に形成された単結晶薄膜においても同様な薄膜の膜厚と 結晶性との関係を有する。
上記のように、 本発明において窒化アルミ二ゥムを主成分とする焼結体からなる基板に形成 される窒化ガリウム、 窒化インジウム、 窒化アルミニウムのうちから選ばれた少なくとも 1種 以上を主成分とする単結晶薄膜は、 炭化珪素、 窒化珪素、 窒化ガリウム、 酸化亜鉛、 酸化ベリ リウムなどの六方晶系及び酸化アルミニウムなどの三方晶系あるいは六方晶系として分類でき る結晶構造を有する各種セラミック材料を主成分とする焼結体からなる基板に形成される該単 結晶薄膜の に比べてより薄いものであっても結晶性に優れたものが得られ易い。
本発明において上記のように、 窒化アルミニウムを主成分とする焼結体からなる基板あるい は炭化珪素、 窒化珪素、 窒化ガリウム、 酸化亜鉛、 酸化ベリリウムなどの六方晶結晶系及び 化アルミニウムなどの三方晶結晶系あるいは六方晶系として分類できる結晶構造を有する各種 セラミツク材料を主成分とする焼結体からなる基板あるいはその他例えば酸化ジルコニウム、 酸化マグネシウム、 アルミン酸マグネシウム、 酸化チタン、 チタン酸バリウム、 チタン酸ジル コン酸鉛、酸化イットリウムなどの希土 «化物、酸ィ匕トリウム、各種フェライ卜、ムライト、 フォルステライト、 ステアタイト、 結晶化ガラス、 などの各種セラミック材料を主成分とする 焼結体からなる基板に形成される窒化ガリウム、 窒化インジウム、 窒化アルミニウムのうちか
ら選ばれた少なくとも 1種以上を主成分とする薄膜は単一層としてだけではなく上記のように 少なくとも 2層以上からなる薄膜として形成できる。 又上記 2層以上の薄膜には組成がそれぞ れ異なるもの結晶状態がそれぞれ異なるものなどが含まれる。 今まで説明してきたように本発 明において窒化ガリウム、 窒化インジウム、 窒化アルミニウムのうちから選ばれた少なくとも 1種以上を主成分とする薄膜は単一の層としてだけではなく少なくとも 2層以上の薄膜として も形成できることを明らかにしてきたが、 本発明においては上記少なくとも 2層以上からなる 窒化ガリウム、 窒化インジウム、 窒化アルミニウムのうちから選ばれた少なくとも 1種以上を 主成分とする薄膜においても各薄膜層において任意の厚みのものが形成し得る。 また、 上記少 なくとも 2層以上からなる窒化ガリウム、 窒化インジウム、 窒化アルミニウムのうちから選ば れた少なくとも 1種以上を主成分とする薄膜において窒化アルミニウムを主成分とする焼結体 からなる基板あるいは炭化珪素、 窒化珪素、 窒化ガリウム、 酸化 ffii 酸化ベリリウムなどの 六方晶結晶系及び酸化アルミニウムなどの三方晶結晶系あるいは六方晶系として分類できる結 晶系を有する各種セラミック材料を主成分とする焼結体からなる基板あるいはその他例えば麼 化ジルコニウム、 酸化マグネシウム、 アルミン酸マグネシウム、 酸化チタン、 チタン酸バリウ ム、 チタン酸ジルコン雌、 酸化イットリウムなどの希土謙化物、 酸化トリウム、 各種フエ ライト、 ムライト、 フォルステライト、 ステア夕イト、 結晶化ガラス、 などの各種セラミック 材料を主成分とする焼結体からなる基板に直接形成されている薄 MB (基板側に形成されてい る薄膜層) はその厚みが 0. 5 nm以上であることがより結晶性に優れた単結晶薄膜を得る上 で好ましい。 上記窒化アルミニウムを主成分とする焼結体からなる基板あるいは炭化珪素、 窒 化珪素、 窒化ガリウム、 酸化亜鉛、 酸化ベリリウムなどの六方晶結晶系及び 化アルミニウム などの三方晶結晶系あるいは六方晶系として分類できる結晶系を有する各種セラミック材料を 主成分とする焼結体からなる基板あるいはその他例えば谢匕ジソレコ二ゥム、酸化マグネシウム、 アルミン酸マグネシウム、 酸化チタン、 チタン酸バリウム、 チタン酸ジルコン酸鉛、 酸化イツ トリウムなどの希土 «化物、酸ィ匕トリウム、各種フェライト、ムライト、 フォルステライト、 ステアタイト、 結晶化ガラス、 などの各種セラミック材料を主成分とする焼結体からなる基板 に形成される少なくとも 2層以上からなる窒化ガリウム、 窒化インジウム、 窒化アルミニウム のうちから選ばれた少なくとも 1種以上を主成分とする薄膜のうち少なくとも 1層が単結晶薄 膜でありその厚みが 0. 5 nm以上の場合該単結晶薄膜のミラー指数 ( 0 0 2) の格子面の X 線回折ロッキングカーブの半値幅として 3 0 0秒以下の結晶性のものが形成し得る。 また、 上 記少なくとも 2層以上からなる窒化ガリウム、 窒化インジウム、 窒化アルミニウムのうちから 選ばれた少なくとも 1種以上を主成分とする薄膜層のうち少なくとも 1層が単結晶薄膜であり その厚みが 0. 3 /xm以上の場合該単結晶薄膜のミラー指数 ( 0 0 2) の格子面の X線回折口 ッキングカーブの半値幅として 3 0 0秒以下の結晶性のものが形成し得る。 該単結晶薄膜が形 成される基板が窒化アルミニウムを主成分とする焼結体であれば窒化ガリゥム、 窒化ィンジゥ ム、 窒化アルミニウムのうちから選ばれた少なくとも 1種以上を主成分とする単結晶薄膜のミ ラー指数 (0 0 2 ) の格子面の X線回折ロッキング力一ブの半値幅が 2 4 0秒以下の結晶性の 良い単結晶薄膜が得られる。 また、 上記少なくとも 2層以上からなる窒化ガリウム、 窒化イン ジゥム、 窒化アルミニウムのうちから選ばれた少なくとも 1種以上を主成分とする薄 ΙΙβのう ち少なくとも 1層が単結晶薄膜でありその厚みが 3. 5 m以上の場合でも該単結晶薄膜のミ ラー指数 (0 0 2) の格子面の X線回折ロッキングカーブの半値幅として 3 0 0秒以下の結晶 性のものが形成し得る。 該単結晶薄膜層が形成される基板が窒化アルミニウムを主成分とする 焼結体であれば窒化ガリウム、 窒化インジウム、 窒化アルミニウムのうちから選ばれた少なく とも 1種以上を主成分とする単結晶薄膜のミラー指数 ( 0 0 2) の格子面の X線回折ロッキン ダカ一ブの半値幅が 2 0 0秒以下の結晶性に優れた単結晶薄膜が得られる。 また本発明による
窒化アルミニウムを主成分とする焼結体からなる基板あるいは炭化珪素、 窒化珪素、 窒化ガリ ゥム、 酸化亜鉛、 酸化ベリリウムなどの六方晶結晶系及び ¾ィ匕アルミニウムなどの三方晶結晶 系あるいは六方晶系として分類できる結晶系を有する各種セラミック材料を主成分とする焼結 体からなる基板あるいはその他例えば 化ジルコニウム、 酸化マグネシウム、 アルミン酸マグ ネシゥム、 酸化チタン、 チタン酸バリウム、 チタン酸ジルコン酸鉛、 酸化イットリウムなどの 希土 化物、酸ィ匕トリウム、各種フェライト、ムライト、 フオルステライト、ステアタイト、 結晶化ガラス、 などの各種セラミック材料を主成分とする焼結体からなる基板を用いることで 少なくとも 2層以上からなる 1 0 m以上の比較的厚い薄膜も形成できる。 上記少なくとも 2 層以上からなる窒化ガリゥム、 窒化ィンジゥム、 窒化アルミニゥムのうちから選ばれた少なく とも 1種以上を主成分とする薄膜層のうち少なくとも 1層が単結晶薄膜でありその厚みが 1 0 m以上の場合でも該単結晶薄膜のミラー指数 ( 0 0 2) の格子面の X線回折ロッキング力一 ブの半値幅として3 0 0秒以下の結晶性のものが形成し得る。 該単結晶薄膜が形成される基板 が窒化アルミニウムを主成分とする焼結体であれば窒化ガリウム、 窒化インジウム、 窒化アル ミニゥムのうちから選ばれた少なくとも 1種以上を主成分とする単結晶薄膜のミラー指数 ( 0 0 2) の格子面の X線回折ロッキングカーブの半値幅が 1 5 0秒以下の結晶性に優れた単結晶 薄膜が得られる。 本発明による窒化アルミニウムを主成分とする 体からなる基板あるいは 炭化珪素、 窒化珪素、 窒化ガリウム、 酸化亜鉛、 酸化ベリリウムなどの六方晶結晶系及び 化 アルミニウムなどの三方晶結晶系あるいは六方晶系として分類できる結晶系を有する各種セラ ミック材料を主成分とする焼結体からなる基板あるいはその他例えば 化ジルコニウム、 酸ィ匕 マグネシウム、 アルミン酸マグネシウム、 酸化チタン、 チタン酸バリウム、 チタン酸ジルコン 酸鉛、 酸ィ匕イットリウムなどの希土 ¾ィ匕物、 酸ィ匕トリウム、 各種フェライト、 ムライト、 フ オルステライト、 ステアタイト、 結晶化ガラス、 などの各種セラミック材料を主成分とする焼 結体からなる基板に形成される窒化ガリウム、 窒化インジウム、 窒化アルミニウムのうちから 選ばれた少なくとも 1種以上を主成分とする 2層以上からなる薄膜として厚み 5 0 m以上の ものは十分形成可能である。上記少なくとも 2層以上からなる窒化ガリウム、窒化インジウム、 窒化アルミニウムのうちから選ばれた少なくとも 1種以上を主成分とする薄 のうち少なく とも 1層が単結晶薄膜でありその厚みが 5 0 zm以上の場合でも該単結晶薄膜のミラ一指数 ( 0 0 2 ) の格子面の X線回折ロッキングカーブの半値幅として 3 0 0秒以下の結晶性のもの が形成し得る。 該単結晶薄膜が形成される基板が窒化アルミニウムを主成分とする焼結体であ れば窒化ガリウム、 窒化インジウム、 窒化アルミニウムのうちから選ばれた少なくとも 1種以 上を主成分とする単結晶薄膜のミラー指数 ( 0 0 2 ) の格子面の X線回折ロッキングカーブの 半値幅が 1 3 0秒以下の優れた結晶性のものが得られるので好ましい。 本発明による薄膜形成 用基板として例えば窒化ガリウム、 窒化インジウム、 窒化アルミニウムのうちから選ばれた少 なくとも 1種以上を主成分とする無定形、 多結晶、 配向性多結晶、 単結晶など各種結晶状態の 薄膜をあらかじめ形成した基板を用いたり、 あるいは光 ¾1性の基板を用いれば窒化ガリウム、 窒化インジウム、 窒化アルミニウムのうちから選ばれた少なくとも 1種以上を主成分とする少 なくとも 2層以上からなる厚み 5 0 0 xm程度の薄膜を形成することが十分可能であり、 実際 ± 1 0 0 0 mの厚みの単結晶薄膜も形成し得る場合がある。 上記少なくとも 2層以上からな る窒化ガリウム、 窒化インジウム、 窒化アルミニウムのうちから選ばれた少なくとも 1種以上 を主成分とする薄膜層のうち少なくとも 1層が単結晶薄膜でありその厚みが 5 0 0 m〜: 1 0 0 の範囲のものであっても該単結晶薄膜のミラ一指数 (0 0 2) の格子面の X線回折口 ッキングカーブの半値幅として 3 0 0秒以下の結晶性のものも形成し得る。 通常上記少なくと も 2層以上からなる窒化ガリウム、 窒化インジウム、 窒化アルミニウムのうちから選ばれた少 なくとも 1種以上を主成分とする単結晶薄膜の厚みとしては 2 0 0 zm程度までのものが好ま
しい。 本発明において薄膜は通常 MO CVD法や MOVP E法あるい ライド V P E法など の非平衡状態で形成されるため該薄膜の厚みが 2 0 0 mより厚くなれば上記のように結晶性 の低下が生じ易くなる場合があるからである。
本発明において、 上記少なくとも 2層以上からなる窒化ガリウム、 窒化インジウム、 窒化ァ ルミニゥムのうちから選ばれた少なくとも 1種以上を主成分とする薄膜を形成するにあたり M O CVD (有機金属化学^ =目 成長) 法、 MOVP E (有機金属気相ェピタキシャル成長) 法、 ハイドライド VP E (水素化物気相ェピタキシャル成長) 法、 クロライド VP E (塩化物 気相ェピタキシャル成長) 法などの八ライド V P E (ハロゲン化物気相ェピタキシャル成長) 法、 プラズマ CVD法、 その他の CVD (化学^ f目 军成長) 法、 あるいは MB E (^線ェ ピ夕キシ一) 法、 あるいはエキシマレーザーなどを用いたレーザーアブレ一シヨン法、 P L D (パルスレーザ一デポジション:パルスレーザ一^?) 法など、 あるいはスパッタリング法な どを MMいて目的とする構成の薄膜を得ることができる。 また、 上記 1 0 以上の比較的 厚い単結晶薄膜は塩化ガリウム、 塩化インジウム、 塩化アルミニウムなどの金属塩化物とアン モニァ、 窒素、 7素などの反応ガスを原料としたクロライド VP E (塩化物気相ェピタキシャ ル成長) 法などを用いれば薄膜の成長速度が 1時間あたり 1 0 m〜5 0 0 m程度と大きい ので生産性の面で有利である。
本発明において、 上記 2層以上からなる窒化ガリウム、 窒化インジウム、 窒化アルミニウム のうちから選ばれた少なくとも 1種以上を主成分とする薄膜のうち単結晶薄膜の厚みとその結 晶性との関係は窒化アルミニウムを主成分とする焼結体あるいは炭化珪素、 窒化珪素、 窒化ガ リウム、 酸化亜鉛、 酸化ベリリウムなどの 71 ^晶結晶系及び ¾化アルミニウムなどの三方晶結 晶系あるいは六方晶系として分類できる結晶系を有する各種セラミック材料を主成分とする焼 結体に直接形成されたものだけではなぐ 窒化アルミニウムを主成分とする焼結体あるいは炭 化珪素、 窒化珪素、 窒化ガリウム、 酸化亜鉛、 酸化ベリリウムなどの六方晶結晶系及び麼化ァ ルミニゥムなどの三方晶結晶系あるいは六方晶系として分類できる結晶系を有する各種セラミ ック材料を主成分とする焼結体あるいはその他例えば 化ジルコニウム、 酸化マグネシウム、 アルミン酸マグネシウム、 酸化チタン、 チタン酸バリウム、 チタン酸ジルコン蘭、 酸化イツ トリウムなどの希土 化物、酸丫匕トリウム、各種フェライト、ムライト、 フオルステライ卜、 ステアタイト、 結晶化ガラス、 などの各種セラミック材料を主成分とする焼結体に窒化ガリウ ム、 窒化インジウム、 窒化アルミニウムのうちから選ばれた少なくとも 1種以上を主成分とす る単結晶、 無定形、 多結晶、 配向性多結晶など各種結晶状態の薄膜があらかじめ形成された薄 膜基板の上に形成された単結晶薄膜においても上記と同様な膜厚と結晶性との関係を得ること ができる。
本発明において、 窒化アルミニウムを主成分とする焼結体、 あるいは炭化珪素、 窒化珪素、 窒化ガリウム、 酸化亜鉛、 酸化ベリリウムなどの六方晶系及び 化アルミニウムなどの三方晶 系あるいは六方晶系として分類できる結晶構造を有する材料の焼結体からなる基板に形成され る窒化ガリウム、 窒化インジウム、 窒化アルミニウムのうちから選ばれた少なくとも 1種以上 を主成分とする単結晶薄膜は同一成分のものを単一層としてあるいは少なくとも 2層以上に分 けて形成できるだけでなく異なる成分からなる少なくとも 2層以上の単結晶薄膜として形成す ることができる。 本発明において窒化アルミニウムを主成分とする焼結体あるいは炭化珪素、 窒化珪素、 窒化ガリウム、 酸化亜鉛、 酸化ベリリウムなどの六方晶結晶系及び 化アルミニゥ ムなどの三方晶結晶系あるいは六方晶系として分類できる結晶構造を有する各種セラミック材 料を主成分とする焼結体あるいはその他例えぱ 化ジルコニウム、 酸化マグネシウム、 アルミ ン酸マグネシウム、 酸化チタン、 チタン酸バリウム、 チタン酸ジルコン赚、 酸化イットリウ ムなどの希土類酸化物、 酸ィ匕トリウム、 各種フェライト、 ムライト、 フォルステライト、 ステ
ァタイト、 結晶化ガラス、 などの各種セラミック材料を主成分とする焼結体には上記のように 少なくとも 2以上の層で構成される単結晶薄膜が形成できるが、 各単結晶薄膜層のうち少なく とも 2以上は異なる組成からなるものであっても好適に用いることができる。 このことをより 具体的に説明すれば、 例えば単結晶薄膜が 3層から構成される場合 3層のうち 2層は同じ組成 で残り 1層の組成が異なるもの、 及び 3層ともはそれぞれ組成が異なるもの、 の 2種類の状態 の単結晶薄膜が含まれる。 また、 例えば単結晶薄膜が 4層から構成される場合 4層のうち 2層 は同じ組成で残り 2層の組成がそれぞれ異なるもの、 4層のうち 3層は同じ組成で残り 1層の 組成が異なるもの、 4層ともはそれぞれ組成が異なるもの、 の 3種類の状態の単結晶薄膜が含 まれる。
ここで異なる組成という意味は単結晶薄膜の実質的な組成が異なるということであり、 単結 晶薄膜の組成が該単結晶薄膜の主成分である窒化ガリウム、 窒化インジウム、 窒化アルミニゥ ムのうちから選ばれた少なくとも 1種以上からなる成分の割合が異なるものだけでなぐ 例え ば単結晶薄膜の主成分が窒化ガリウム、 窒化インジウム、 窒化アルミニウムのうち 1種類だけ でその他の成分が実質的に例えばドーピンク^だけの場合なども含まれる。 より具体的に言え ば、 単結晶薄膜の主成分が例えば窒化ガリゥムだけでその他実質的にドーピング剤としてマグ ネシゥム (Mg) だけを含むものの場合、 窒化ガリウムとマグネシウムの組成比が異なるもの も含まれる。 あるいは同様に、 単結晶薄膜の主成分が例えば窒化アルミニウムだけでその他実 質的にド一ピンク として珪素 (S i ) だけを含むものの場合、 窒化アルミニウムと珪素の組 成比が異なるものも含まれる。 本発明においては上記のように窒化アルミニウムを主成分とす る焼結体、 あるいは炭化珪素、 窒化珪素、 窒化ガリウム、 酸化亜鉛、 酸化ベリリウムなどの六 方晶系及び 化アルミ二ゥムなどの三方晶系あるいは六方晶系として分類できる結晶構造を有 する材料の焼結体からなる基板に形成される窒化ガリウム、 窒化インジウム、 窒化アルミニゥ ムのうちから選ばれた少なくとも 1種以上を主成分とする単結晶薄膜は同一成分のものを単一 層としてあるいは少なくとも 2層以上に分けて形成できるだけでなく異なる成分からなる少な くとも 2層以上の単結晶薄膜として形成することができるが、 同一成分を 2層以上に分けて形 成したものや異なる成分のものを 2層以上に形成したものであっても各層の単結晶薄膜のミラ —指数 (0 0 2) の格子面の X線回折ロッキングカーブの半値幅が 3 0 0秒以下の結晶性のも のが得られる。 また、 該単結晶薄膜が直接形成される基板が窒化アルミニウムを主成分とする 焼結体であれば窒化ガリゥム、 窒化ィンジゥム、 窒化アルミニゥムのうちから選ばれた少なく とも 1種以上を主成分とする単結晶薄膜のミラー指数 (0 0 2) の格子面の X線回折ロッキン グカーブの半値幅が 1 5 0秒以下の優れた結晶性のものが得られるので好ましい。
本発明において窒化アルミニウムを主成分とする焼結体、 あるいは炭化珪素、 窒化珪素、 窒 化ガリウム、 酸化亜鉛、 酸化ベリリウムなどの六方晶系及び 化アルミニウムなどの三方晶系 あるいは六方晶系として分類できる結晶構造を有する各種セラミック材料を主成分とする焼結 体、 あるいはその他例えば酸化ジルコニウム、 酸化マグネシウム、 アルミン酸マグネシウム、 酸化チタン、 チタン酸バリウム、 チタン酸ジルコン酸鉛、 酸化イットリウムなどの希土鍵化 物、 酸化トリウム、 各種フェライト、 ムライト、 フォルステライト、 ステアタイト、 結晶化ガ ラス、 などの各種セラミック材料を主成分とする焼結体からなる基板に形成される窒化ガリゥ ム、 窒化インジウム、 窒化アルミニウムのうちから選ばれた少なくとも 1種以上を主成分とす る単結晶、 無定形、 多結晶、 配向性多結晶など各種結晶状態の薄膜の結晶性に与える因子とし ては、今まで説明してきたことをまとめると次のように分類される。使用する基板においては、 1 ) セラミックの材質 (窒化アルミニウムを主成分とする焼結体か、 あるいは炭化珪素、 窒化 珪素、 窒化ガリウム、 酸化亜鉛、 酸化ベリリウムなどの六方晶系及び 化アルミニウムなどの 三方晶系あるいは六方晶系として分類できる結晶構造を有する各種セラミック材料を主成分と
する焼結体か、 などの相違)、 2) セラミックの組成 (主成分の tm及び含有量、 添加物あるい は不純物の含有量、 など)、 3) セラミックの 率、 4) セラミック粒子の大きさ、 5 ) セ ラミックの密度、 6 )セラミックの厚み、 7 )セラミックの; «条件、 8)基板の表面平滑性、 また薄膜においては、 9)薄膜の構成(単一層、 あるいは 2層以上の多層構成か、 など)、 1 0 ) 薄膜の厚み、 1 1 ) 薄膜の形成条件 (MO CVD、 クロライド VP Eあるいはスパッタリング などの薄膜形成方法、 基板温度、 など)、 などである。
また、 上記セラミック基板に形成される薄膜の結晶性にあまり影響を与えない因子としては 以下の点が挙げられる。 1 ) セラミック基板中に導通ビアを有しているかどうか (導通ビアの 有無にカゝかわらず、基板に形成される薄膜の結晶性にはあまり影響がない)、 2)薄膜の糸滅(窒 化ガリウム、 窒化インジウム、 窒化アルミニウムのうちから選ばれた少なくとも 1種以上を主 成分とする組成であればあらゆる組み合わせが形成される薄膜の結晶性を左右されることなく 可能、 また各種ドーピング成分を含有する薄膜も結晶性を左右されることなく形成可能)、 など である。
本発明において、 窒化ガリウム、 窒化インジウム、 窒化アルミニウムのうちから選ばれた少 なくとも 1種以上を主成分とする無定形、 多結晶、 配向性多結晶、 単結晶など各種結晶状態の 薄膜を形成するための薄膜形成用基板、及び該薄膜が形成された薄膜基板を i¾iするにあたり、 上記のように基板として用いる窒化アルミニウムを主成分とする焼結体、 及び炭化珪素、 窒化 珪素、 窒化ガリウム、 酸化亜鉛、 酸化ベリリウムなどの六方晶系及び 化アルミニウムなどの 三方晶系あるいは六方晶系として分類できる結晶構造を有する各種セラミック材料を主成分と する焼結体、 及びその他例えば 化ジルコニウム、 酸化マグネシウム、 アルミン酸マグネシゥ ム、 酸化チタン、 チタン酸バリウム、 チタン酸ジルコン酸鉛、 酸化イットリウムなどの希土類 酸化物、 酸化トリウム、 各種フェライト、 ムライト、 フォルステライト、 ステアタイト、 結晶 化ガラス、などの各種セラミック材料を主成分とする焼結体からなる基板の材質が重要である。 そのうち炭化珪素、 窒化珪素、 窒化ガリウム、 酸化亜鉛、 酸化ベリリウムなどの六方晶系及び 酸化アルミニウムなどの三方晶系あるいは 晶系として分類できる結晶構造を有する各種セ ラミック材料を主成分とする焼結体、及びその他例えは 化ジルコニウム、酸化マグネシウム、 アルミン酸マグネシウム、 酸化チタン、 チタン酸バリウム、 チタン酸ジルコン蘭、 酸化イツ トリウムなどの希土 匕物、謝匕トリウム、各種フェライト、ムライト、 フォルステラィト、 ステアタイト、 結晶化ガラス、 などの各種セラミック材料を主成分とする焼結体についても従 来から行われている方法を用いて製造されたものを問題なく使用できる。すなわち、炭化珪素、 窒化珪素、窒化ガリウム、酸化亜鉛、酸化ベリリウム、酸化アルミニウム、酸化ジルコニウム、 酸化マグネシウム、 アルミン酸マグネシウム、 酸化チタン、 チタン酸バリウム、 チタン酸ジル コン ,、酸化イットリウムなどの希土 «化物、酸ィ匕トリウム、各種フェライト、ムライト、 フオルステライト、 ステアタイト、 結晶化ガラスなどを主成分とする微粉末に適宜焼結助剤、 ノィンダ一、分散剤などを混合した粉末成形体を高温で焼成し焼結体としたものである。 焼成条件はそれぞれ各種セラミック材料の原料粉末の や組成に依存するが、 焼成? と して例えば炭化珪素で 1 5 0 0 °C〜2 5 0 0°C、 窒化珪素で 1 6 0 0 :〜 2 1 0 0 ° (:、 窒化ガ リウムで 1 0 0 0 °C〜1 7 0 0 °C、 酸ィ匕亜鉛で 1 1 0 0 ° (:〜 1 7 0 0 °C、 酸化ベリリウムで 1 1 0 0 °C〜2 0 0 0 :、 酸ィ匕アルミニウムで 1 1 0 0 °C〜2 0 0 0 :、 などの温度が用いられ る。 焼成時の雰囲気として炭化珪素、 窒化珪素、 窒化ガリウムなどの非酸化物の場合はァルゴ ン、 ヘリウム、 窒素、 水素、 一酸化炭素、 カーボンなどを主成分とする非酸化性雰囲気や 7 6 O T o r r未満の減圧状態あるいは 1 X 1 0一3 T o r r以下の高真空状態などが用いられ、 酸 化亜鉛、 酸化ベリリウム、 酸化アルミニウムなどの酸化物の場合は上記非酸化性雰囲気や減圧 状態あるいは高真空状態以外にも大気、 酸素、 二酸化炭素などを主成分とする酸化性雰囲気な
どが用いられる。 誠時の庄力は上記減圧状態あるいは高真空状態以外にも常圧焼成で用いら れる lKg/cm2 (76 OTo r r) 前後の圧力、 及び加圧 «、 ホットプレス、 H I Pなど で用いられる 5000 Kg/cm2程度以下の圧力が問題なく使用できる。
上記炭化珪素、 窒化珪素、 窒化ガリウム、 酸化亜鉛、 酸化ベリリウムなどの六方晶系及び酸 化アルミニウムなどの三方晶系あるいは六方晶系として分類できる結晶構造を有する各種セラ ミック材料を主成分とする焼結体の組成としては焼結助剤などの添加物を含まずそれぞれの材 料の主成分だけ含むもの、 あるいは主成分の他に ¾!:焼結助剤、 黒色化剤、 あるいは原料中の 不純物、 などの成分を単独であるいは複合で含むものであっても問題なく使用できる。 すなわ ち、 例えば炭化珪素を主成分とする焼結体の組成としては実質的に S i Cだけからなるもの、 あるいは力一ボン成分、あるいは B、 B4C、 BNなどの硼素成分、あるいは Y2〇3、 Er 203、 Yb203などの希土類 素成分、 Be〇、 MgO、 Ca〇、 S r 0、 BaOなどのアルカリ土 類金属成分、 あるいは A 1203などのアルミニウム成分、 あるいは S i〇2などの珪素成分、 こ れらの成分を単独あるいは複合で含むものなどである。 窒化珪素を主成分とする焼結体の組成 としては実質的に S i 3N4だけからなるもの、 あるいは Y203、 Er203、 Yb203などの希 土類^;素成分、 Be〇、 Mg〇、 CaO、 S r〇、 B a〇などのアルカリ土類金属成分、 ある いは A 1203などのアルミニウム成分、 あるいは S i 02などの珪素成分、 あるいは力一ポン、 モリブデン、 タングステンなどの黒色化促進成分、 あるいは Ti〇2、 Cr 203、 MnO、 Co 〇、 NiO、 Fe203などの遷移金属成分、 これらの成分を単独あるいは複合で含むものなど である。窒化ガリゥムを主成分とする焼結体の賊としては実質的に G a Nだけからなるもの、 あるいは Y203、 E r2〇3、 丫13203などの希土^¾素成分、 BeO、 MgO、 Ca〇、 S r 〇、 BaOなどのアルカリ土類金属成分、 あるいは A 12〇3などのアルミニウム成分、 あるい は S i〇2などの珪素成分、 あるいは力一ボン、 モリブデン、 タングステンなどの黒色化促進成 分、 あるいは Ti02、 Cr203、 MnO、 CoO、 N i〇、 F e 203などの遷移金属成分、 こ れらの成分を単独あるいは複合で含むものなどである。 酸化亜鉛を主成分とする焼結体の組成 としては実質的に ZnOだけからなるもの、 あるいは Y203、 Er 203、 Yb203などの希土 類沅素成分、 あるいは Be 0、 MgO、 CaO、 S rO、 B a Oなどのアルカリ土類金属成分、 あるいは A 1203などのアルミニウム成分、 あるいは S i 02などの珪素成分、 あるいは T i 0 2、 Cr2〇3、 MnO、 Co〇、 N i 0、 F e 203などの遷移金属成分、 これらの成分を職あ るいは複合で含むものなどである。 酸化ベリリウムを主成分とする焼結体の組成としては実質 的に Be Oだけからなるもの、 あるいは Y203、 Er 203、 Yb 203などの希土^ ¾素成分、 あるいは Mg〇、 Ca〇、 S r〇、 B a〇などのアルカリ土類金属成分、 あるいは A 1203な どのアルミニウム成分、 あるいは S i 02などの珪素成分、 あるいは Ti〇2、 Cr2〇3、 Mn 0、 CoO、 Ni〇、 Fe203などの遷移金属成分、 これらの成分を単独あるいは複合で含む ものなどである。 酸化アルミニウムを主成分とする焼結体の組成としては実質的に A 12〇3だ けからなるもの、 あるいは Y203、 Er2〇3、 Yb203などの希土^ ¾素成分、 あるいは Be 〇、 Mg〇、 CaO、 S rO、 B a Oなどのアルカリ土類金属成分、 あるいは S i 02などの珪 素成分、あるいは T i 02、 C r 203、 Mn〇、 C oO、 N i〇、 F e 2〇3などの遷移金属成分、 これらの成分を単独あるいは複合で含むものなどである。
今まで説明してきたように炭化珪素、 窒化珪素、 窒化ガリウム、 酸化亜鉛、 酸化ベリリウム などの六方晶系及び酸化アルミニウムなどの三方晶系あるいは六方晶系として分類できる結晶 構造を有する各種セラミック材料を主成分とする焼結体を基板として用いたときこの基板上の 表面平滑性を高めることで該基板上に直接形成される窒化ガリウム、 窒化インジウム、 窒化ァ ルミニゥムのうちから選ばれた少なくとも 1種以上を主成分とする単結晶薄膜の結晶性を高め ることができる。 しかしながら該基板の平滑性として平均表面粗さ R aが 2 nm程度のもので
あっても該単結晶薄膜のミラー指数 (0 0 2) の格子面の X線回折ロッキングカーブの半値幅 が 2 0 0秒より大きいものとなり易い。
一方、 炭化珪素、 窒化珪素、 窒化ガリウム、 酸化亜鉛、 酸化ベリリウムなどの六方晶系及び 酸化アルミニウムなどの三方晶系あるいは六方晶系として分類できる結晶構造を有する各種セ ラミック材料を主成分とする焼結体を基板として用い、 該基板にあらかじめ窒化ガリウム、 窒 化インジウム、 窒化アルミニウムのうちから選ばれた少なくとも 1種以上を主成分とする無定 形、 多結晶、 配向性多結晶、 単結晶のうちから選ばれた少なくとも 1種以上の結晶状態を有す る薄膜を形成し、 その上にさらに窒化ガリウム、 窒化インジウム、 窒化アルミニウムのうちか ら選ばれた少なくとも 1種以上を主成分とする単結晶薄膜を形成することで該単結晶薄膜の結 晶性を高めることができる。 このような薄膨冓成とすることで上記基板の表面平滑性などにあ まり影響されずに形成される単結晶薄膜の結晶性を高めることが可能となる。また、炭化珪素、 窒化珪素、 窒化ガリウム、 酸化亜鉛、 酸化ベリリウムなどの六方晶系及び 化アルミニウムな どの三方晶系あるいは六方晶系として分類できる結晶構造を有する各種セラミック材料を主成 分とする焼結体の組成を最適化することでさらに高い結晶性を有する単結晶薄膜が作製し得る。 前記のように、 酸化亜鉛を主成分とする焼結体を基板として用いたとき該基板に直接形成さ れる窒化ガリウム、 窒化インジウム、 窒化アルミニウムのうちから選ばれた少なくとも 1種以 上を主成分とする単結晶薄膜は該基板の表面平滑性などの影響を受け易く必ずしも結晶性に優 れたものとなり得ない場合があるのに対して、 該酸化亜鉛を主成分とする焼結体からなる基板 の上にあらかじめ窒化ガリウム、 窒化インジウム、 窒化アルミニウムのうちから選ばれた少な くとも 1種以上を主成分とする無定形、 多結晶、 配向性多結晶、 単結晶のうちから選ばれた少 なくとも 1種以上の結晶状態を有する薄膜を形成しさらにその上に窒化ガリゥム、 窒化ィンジ ゥム、 窒化アルミニウムのうちから選ばれた少なくとも 1種以上を主成分とする単結晶薄膜を 形成すれば該単結晶薄膜は該基板の表面平滑性などの影響をより受けにくくなり結晶性はさら に優れたものとなり得る。 すなわち、 酸ィ 鉛を主成分とする焼結体を基板として用い、 窒化 ガリウム、 窒化インジウム、 窒化アルミニウムのうちから選ばれた少なくとも 1種以上を主成 分とする単結晶薄膜を直接形成すれば該単結晶薄膜のミラー指数 ( 0 0 2) の格子面の X線回 折口ッキングカーブの半値幅が 2 0 0秒以下の比較的結晶性に優れたものになるとは必ずしも 限らない。 それに対して、 酸化亜鉛を主成分とする焼結体を基板として用い、 該基板にあらか じめ窒化ガリウム、 窒化インジウム、 窒化アルミニウムのうちから選ばれた少なくとも 1種以 上を主成分とする無定形、 多結晶、 配向性多結晶、 単結晶のうちから選ばれた少なくとも 1種 以上の結晶状態を有する薄膜を形成しさらにその上に窒化ガリウム、 窒化インジウム、 窒化ァ ルミニゥムのうちから選ばれた少なくとも 1種以上を主成分とする単結晶薄膜を形成すれば該 単結晶薄膜のミラー指数 ( 0 0 2) の格子面の X線回折ロッキングカーブの半値幅は 2 0 0秒 以下の比較的結晶性に優れたものが形成し得る。
上記酸化稀を主成分とする焼結体において、 以外に B e O、 Mg〇、 C a O、 S r〇、 B a〇などのアルカリ土類金属成分、 あるいは S c 203、 Y203、 L a 203、 C e〇2、 P r 6 Ou、 N d 2〇3、 Pm203、 Sm203、 E u 203、 G d 203、 T b 4〇7、 D y 2〇3、 H o 20 3、 E r 203、 Tm203、 Y b 203、 L u 2〇3などの希土 ^素成分、 あるいは S i 02などの 珪素成分、 あるいは Mn〇、 C o O、 N i O、 F e 2〇3、 C r 203、 T i 02などの遷移金属成 分、 あるいはアルミニウム成分などを含有するものを基板として用いたとき該基板には比較的 良好な結晶性の薄膜が形成し得る場合が多い。 そのなカゝでもアルミニウム成分を含む酸化亜鉛 を主成分とする焼結体を用いることが好ましい。通常アルミニウム成分を A 1 203 で 4 5. 0モル%以下の範囲で含む酸化亜鉛を主成分とする焼結体を基板として用いたときその上には ミラー指数 (0 0 2 ) の格子面の X線回折ロッキングカーブの半値幅が 3 0 0秒以下の結晶性
に優れた窒化ガリウム、 窒化インジウム、 窒化アルミニウムのうちから選ばれた少なくとも 1 種以上を主成分とする単結晶薄膜が 接形成し得る。 上記酸化亜鉛を主成分とする焼結体のう ちアルミニウム成分を A 1 2〇3騰で 0. 0 0 1モル%〜4 5. 0モル%の範囲で含むものを 基板として用いたときその上にはミラ一指数 (0 0 2 ) の格子面の X線回折ロッキングカーブ の半値幅が 2 0 0秒以下の結晶性に優れた窒化ガリウム、 窒化インジウム、 窒化アルミニウム のうちから選ばれた少なくとも 1種以上を主成分とする単結晶薄膜が 接形成できる。 さらに、 アルミニウム成分を A 1 203騰で 0. 0 2モル%〜4 5. 0モル%の範囲で含む酸化 ¾を 主成分とする焼結体を基板として用いたとき該基板にはミラ一指数 ( 0 0 2 ) の格子面の X線 回折口ッキングカーブの半値幅が 1.5 0秒以下の結晶性に優れた単結晶薄膜が 接形成できる。 また、 アルミニウム成分を A 1 203換算で0. 0 8モル%〜3 5. 0モル%の範囲で含む酸化 »を主成分とする焼結体を基板として用いたとき該基板にはミラー指数 ( 0 0 2) の格子面 の X線回折ロッキングカーブの半値幅が 1 3 0秒以下の結晶性に優れた単結晶薄膜が直接形成 できる。
また、 酸化亜鉛を主成分とする; ¾結体において、 亜鉛以外に S c 2〇3、 Y2〇3、 L a 203、 C e〇2、 P r 6Oi N d 2〇3、 Pm2〇3、 Sm203、 E u 2〇3、 G d 2〇3、 T b 4〇7、 D y 203、 H o 2〇3、 E r 203、 Tm203、 Yb 2〇3、 L u 203などの希土 ¾素成分、 あるいは Mn〇、 C o〇、 N i〇、 F e 2〇3、 C r 2〇3、 T i〇2などの遷移金属成分のうちから選ばれ た少なくとも 1種以上の成分を酸化物 で 1 0. 0モル%以下含有するものを基板として用 いた場合でも該基板の上にはミラー指数 (0 0 2 ) の格子面の X線回折ロッキングカーブの半 値幅が 3 0 0秒以下の結晶性に優れた窒化ガリウム、 窒化インジウム、 窒化アルミニウムのう ちから選ばれた少なくとも 1種以上を主成分とする単結晶薄膜が直接形成し得る。 通常上記遷 移金属成分として F e及び C rのうちから選ばれた少なくとも 1種以上の成分を酸化物換算 (それぞれ F e 2 O 3及び C r 203で示される) で 1 0. 0モル%以下含有する酸化 を主成 分とする焼結体が好ましく、 このような組成の焼結体を基板として用いることでその上には窒 化ガリウム、 窒化インジウム、 窒化アルミニウムのうちから選ばれた少なくとも 1種以上を主 成分とする結晶性に優れた単結晶薄膜が形成し得る。
さらに、 上記アルミニゥム成分を含有する酸化亜鉛を主成分とする焼結体からなる基板を用 いたとき該基板に直接形成される窒化ガリウム、 窒化インジウム、 窒化アルミニウムのうちか ら選ばれた少なくとも 1種以上を主成分とする単結晶薄膜の結晶性よりも、 同じ組成のアルミ ニゥム成分を含有する酸化 «を主成分とする焼結体からなる基板の上にあらかじめ窒化ガリ ゥム、 窒化インジウム、 窒化アルミニウムのうちから選ばれた少なくとも 1種以上を主成分と する無定形、 多結晶、 配向性多結晶、 単結晶のうちから選ばれた少なくともいずれかの結晶状 態を有する薄膜を形成しさらにその上に窒化ガリウム、 窒化インジウム、 窒化アルミニウムの うちから選ばれた少なくとも 1種以上を主成分とする単結晶薄膜を形成すれば該単結晶薄膜の 結晶性はさらに優れたものとなり得る。 具体的に言えば、 アルミニウム成分を A 1 203換算で 4 5. 0モル%以下の範囲で含む酸化亜鉛を主成分とする焼結体を基板として用いたとき、 そ の上にあらかじめ窒化ガリウム、 窒化インジウム、 窒化アルミニウムのうちから選ばれた少な くとも 1種以上を主成分とする無定形、 多結晶、 配向性多結晶、 単結晶のうちから選ばれた少 なくともいずれかの結晶状態を有する薄膜を形成しさらにその上に窒化ガリゥム、 窒化ィンジ ゥム、 窒化アルミニウムのうちから選ばれた少なくとも 1種以上を主成分とする単結晶薄膜を 形成すればミラ一指数 (0 0 2 ) の格子面の X線回折ロッキングカーブの半値幅として 2 0 0 秒以下、 通常 1 5 0秒以下の結晶性に優れた単結晶薄膜が比較的容易に形成できる。 また、 ァ ルミニゥム成分を A 1 203換算で 0. 0 0 1モル%〜 4 5. 0モル%の範囲で含む酸化亜紛を 主成分とする焼結体を基板として用いれば、 その上にあらかじめ窒化ガリウム、 窒化インジゥ
ム、窒化アルミニウムのうちから選ばれた少なくとも 1種以上を主成分とする無定形、多結晶、 配向性多結晶、 単結晶のうちから選ばれた少なくともいずれかの結晶状態を有する薄膜を形成 しさらにその上に窒化ガリウム、 窒化インジウム、 窒化アルミニウムのうちから選ばれた少な くとも 1種以上を主成分とする単結晶薄膜を形成することによりミラ一指数 ( 0 0 2) の格子 面の X線回折ロッキングカーブの半値幅として 1 3 0秒以下の結晶性に優れた単結晶薄膜が比 較的容易に形成できる。 また、 アルミニウム成分を A 1 203換算で 0. 0 0 5モル%〜4 5. 0モル%の範囲で含む酸化亜鉛を主成分とする焼結体を基板として用いたとき、 その上にあら かじめ窒化ガリゥム、 窒化ィンジゥム、 窒化アルミニゥムのうちから選ばれた少なくとも 1種 以上を主成分とする無定形、 多結晶、 配向性多結晶、 単結晶のうちから選ばれた少なくともい ずれかの結晶状態を有する薄膜を形成しさらにその上に窒化ガリウム、 窒化インジウム、 窒化 アルミニウムのうちから選ばれた少なくとも 1種以上を主成分とする単結晶薄膜を形成すれば ミラ一指数 (0 0 2 ) の格子面の X線回折ロッキングカーブの半値幅として 1 0 0秒以下の結 晶性に優れた単結晶薄膜が比較的容易に形成し得る。
その際、 上記アルミニウム成分を A 1 2〇 3換算で 0. 0 0 1モル%〜4 5. 0モル%の範固 で含む酸化»を主成分とする焼結体からなる基板にあらかじめ形成する窒化ガリゥム、 窒化 インジウム、 窒化アルミニウムのうちから選ばれた少なくとも 1種以上を主成分とする配向性 多結晶薄膜の結晶性も上記範囲のアルミニウム成分を含まない酸化亜鉛を主成分とする焼結体 からなる基板を用いたものに比べて向上し易ぐ 該配向性多結晶薄膜のミラー指数 (0 0 2 ) の格子面の X線回折ロッキングカーブの半値幅は 9 0 0 0秒以下のものが比較的容易に形成し 得る。 また、 アルミニウム成分を A 1 203観で 0. 0 0 5モル%〜4 5. 0モル%の範囲で 含む酸化亜鉛を主成分とする焼結体からなる基板では、 該基板にあらかじめ形成する窒化ガリ ゥム、 窒化インジウム、 窒化アルミニウムのうちから選ばれた少なくとも 1種以上を主成分と する配向性多結晶薄膜のミラ一指数 ( 0 0 2) の格子面の X線回折ロッキングカーブの半値幅 として 8 0 0 0秒以下のものが比較的容易に形成し得る。
また、 酸化亜鉛を主成分とする 結体において、 ffifj、以外に S c 203、 Y203、 L a 203、 C e 02、 P r gO n, N d 203、 Pm203、 Sm2〇3、 E u 203、 G d 203、 T b 407、 D y 203、 H o 203、 E r 2〇3、 Tm203、 Y b 2〇3、 L u 203などの希土 素成分、 あるいは Mn〇、 C o O、 N i O、 F e 203、 C r 203、 T i 02などの遷移金属成分のうちから選ばれ た少なくとも 1種以上の成分を酸化物^:で 1 0. 0モル%以下含有するものを基板として用 いた場合、 その上にあらかじめ窒化ガリウム、 窒化インジウム、 窒化アルミニウムのうちから 選ばれた少なくとも 1種以上を主成分とする無定形、 多結晶、 配向性多結晶、 単結晶のうちか ら選ばれた少なくともいずれかの結晶状態を有する薄膜を形成しさらにその上に窒化ガリゥム、 窒化インジウム、 窒化アルミニウムのうちから選ばれた少なくとも 1種以上を主成分とする単 結晶薄膜を形成すれば該単結晶薄膜のミラー指数 ( 0 0 2) の格子面の X線回折ロッキング力 ーブの半値幅として 1 3 0秒以下の結晶性に優れたものが比較的容易に形成し得る。 通常上記 遷移金属成分として F e及び C rのうちから選ばれた少なくとも 1種以上の成分を酸化物換算 (それぞれ F e 203及び C r 203で示される) で 1 0モル%以下含有する酸化 »、を主成分と する焼結体が好ましく、 このような組成の焼結体を基板として用いることでその上には窒化ガ リウム、 窒化インジウム、 窒化アルミニウムのうちから選ばれた少なくとも 1種以上を主成分 とする結晶性に優れた単結晶薄膜が形成し得る。
このように酸化亜鉛を主成分とする焼結体からなる基板にあらかじめ窒化ガリゥム、 窒化ィ ンジゥム、 窒化アルミニウムのうちから選ばれた少なくとも 1種以上を主成分とする無定形、 多結晶、 配向性多結晶、 単結晶のうちから選ばれた少なくともいずれかの結晶状態を有する薄 膜を形成すれば、 さらにその上に形成される窒化ガリウム、 窒化インジウム、 窒化アルミニゥ
ムのうちから選ばれた少なくとも 1種以上を主成分とする単結晶薄膜の結晶性を向上させる効 果がある。 その効果は酸化亜鉛を主成分とする焼結体からなる基板の組成以外の要素、 例えば 表面平滑性などにも大きく影響されず、 例えば平均表面粗さ R aを 5 n m以下にしたものでな くても (すなわち、 焼き放しの表面状態の基板、 ラッフ Iff磨した表面状態の基板、 ブラスト研 磨した表面状態の基板、 機械的な溝切り加工が施された基板、 あるいは鏡面研磨してある基板 など、 平均表面粗さ R aが 5 nm以上のものであっても) 発揮され得る。
このような単結晶薄膜の結晶性に及ぼす酸化亜鉛を主成分とする焼結体中の亜鉛以外の成分 そのなかでも特にアルミニウム成分の効果は、 例えば該酸化亜鉛を主成分とする焼結体中に B eO、 MgO、 Ca〇、 SrO、 B a Oなどのアルカリ土類金属成分、 あるいは Sc2〇3、 Y2 03、 L a2Os Ce〇2、 P r 601Χ^ Nd203、 Pm203、 Sm203、 Eu2〇3、 Gd203、 Tb4〇7、 Dy203、 Ho2〇3、 Er 203、 Tm2〇3、 Yb2〇3、 L u 2〇3などの希土類 素 成分、 あるいは S i〇2などの珪素成分、 あるいは Mn〇、 Co〇、 Ni〇、 Fe203、 Cr2 〇3、 Ti〇2などの遷移金属成分、 などアルミニウム成分以外の金属成分が少なくとも 1種以 上含まれていたとしても減じることは少ない。
アルミニウム成分を A 1203騰で 45. 0モル%以下の範囲で含む酸化亜鉛を主成分とす る焼結体を基板として用いたとき基板の上に形成される単結晶薄膜がこのような高い結晶性を 有するものとなる原因は必ずしも明確ではないが、 本願発明者は以下のように考えている。 ァ ルミニゥム成分を含まなレ酸化亜鉛を主成分とする焼結体は通常白色あるいは黄白色を呈して いるのに対してアルミニウム成分を含む酸化亜鉛を主成分とする焼結体は通常青色に呈色しァ ルミニゥム成分の含有量の増加に伴つて呈色性が増大する傾向を有する。 上記青色への呈色は 酸化亜鉛中に存在する A 1イオンが 化碰の結晶格子へ入り込み Z nイオンと置換されてド ナ一 立を形成するためであり、 上記 A 1イオンによる酸化亜鉛結晶中の Z nイオンとの置換 により該酸化亜鉛結晶の大きさが小さくなる方向へ変化し (すなわち格子定数が小さくなる)、 窒化ガリウム、 窒化インジウム、 窒化アルミニウムのうちから選ばれた少なくとも 1種以上を 主成分とする薄膜の成長開始時における薄膜結晶の成長方向がより揃い易くなり (ェピタキシ ャル成長性が自発的に高まり)、その結果このようなアルミニウム成分を含む酸化亜鉛を主成分 とする焼結体を基板として用いたときその上には結晶性に優れた窒化ガリウム、 窒化インジゥ ム、 窒化アルミニウムのうちから選ばれた少なくとも 1種以上を主成分とする単結晶薄膜が形 成され易くなるものと本願発明者は推測している。
アルミニウム成分を含まない酸化亜鉛を主成分とする焼結体の導電性は通常小さいが、 上記 アルミニウム成分を A 12〇3鶴で 45. 0モル%以下の範囲で含む酸 «を主成分とする 焼結体の導電性は向上する。 具体的にいえば、 アルミニウム成分を Al 203換算で 0. 001 モル%〜 45. 0モル%の範囲で含む酸化亜鉛を主成分とする焼結体の導電性は向上し例えば 室温における抵抗率が少なくとも 1 X 102Ω · cm以下のものが得られ易い。アルミニウム成 分を A 1203換算で 0. 005モル%〜45. 0モル%の範囲含む酸化亜鉛を主成分とする焼 結体では室温における抵抗率が少なくとも 1 X 10丄0 · cm以下のものが得られ易く該焼結体 を導通ビアのない基板として用いることカ坷能となるので好ましい。 また、 アルミニウム成分 を A 12〇3換算で0. 02モル%〜45. 0モル%の範囲で含む酸化亜鉛を主成分とする焼結 体では室温における抵抗率が少なくとも 1 X 10。Ω · cm以下のものが得られ易く該焼結体を 導通ビアのない基板として用いることが可能となるのでより好ましい。 アルミニウム成分を A 12 O 3購で 0. 08モル%〜 35. 0モル%の範囲で む酸化 »を主成分とする焼結体で は室温における抵抗率が少なくとも 1 X 1 Ο^Ω · cm以下のものが得られ易く該焼結体を導 通ビアのない基板として用いることが可能となるのでさらに好ましい。 アルミニウム成分を A 12 O 3 で 0. 2モル%〜 25. 0モル%の範囲で含む酸化亜鉛を主成分とする焼結体では
室温における抵抗率が少なくとも 1X 10— 2Ω· ο m以下のものが得られ易く、 1〜 2 X 10一 3Ω · cm程度のより低い抵抗率を有するものも得られる。 このような導電性を有する酸化亜鉛 を主成分とする焼結体は特に基板の上下表面を電気的に接続するための導通ビアを設ける必要 がないので好ましい。 また、 上記酸化亜鉛を主成分とする焼結体は B e 0、 Mg〇、 Ca〇、 S rO、 B a Oなどのアルカリ土類金属成分、 あるいは MnO、 CoO、 N i〇、 Fe203、 C r 203、 T i〇2などの遷移金属成分、あるいは S i 02などの珪素成分、あるいは S c 2〇3、 Y2〇3、 La2〇3、 Ce〇2、 Pr6Oxl, Nd2Os、 Pm203、 Sm203、 Eu203、 Gd2 〇3、 Tb407、 Dy2〇3、 Ho203、 Er203、 Tm2〇3、 Yb2〇3、 Lu203などの希土 l¾素成分、 などのうちから選ばれた少なくとも 1種以上の成分がアルミニウム成分以外に含 まれていたとしても導電性が損なわれる程度は少ない。 上記酸化亜鉛を主成分とする焼結体中 に含まれるアルミニウム以外の成分の含有量としては導電性が損なわれる程度が小さければど のようなものであってもよい。 通常該ァルミニゥム以外の成分の含有量として酸化物換算で 1 0. 0モル%以下であることが導電性が損なわれる程度が小さいので好ましい。
また、 導電性を有する酸化亜鉛を主成分とする焼結体は亜鉛以外の成分としてアルミニゥム 成分だけでなく、 Sc203、 Y203、 La2〇3、 Ce02、 P r 6Oi Nd203、 Pm2〇3、 Sm2〇3、 Eu2〇3、 Gd203、 Tb4〇7、 Dy2〇3、 Ho2〇3、 Er2〇3、 Tm2〇3、 Yb 203、 Lu203などの希土^ ¾素成分、 あるいは Mn〇、 CoO、 N i 0、 Fe2〇3、 C r 2 03、 T i 02などの遷移金属成分のうちから選ばれた少なくとも 1種以上の成分を酸化物換算 で 10モル%以下含有するものでも得ることが可能である。 通常上記遷移金属成分として F e 及び C rのうちから選ばれた少なくとも 1種以上の成分を酸化物購で 10モル%以下含有す る酸化亜鉛を主成分とする焼結体が好ましく、 このような組成の焼結体を基板として用いるこ とでその上には窒化ガリゥム、 窒化ィンジゥム、 窒化アルミニゥムのうちから選ばれた少なく とも 1種以上を主成分とする結晶性に優れた単結晶薄膜が形成し得る。
上記酸化亜鉛を主成分とする焼結体は COや H2などを含む S¾性雰囲気、 あるいは Ar、 H e、 N2などを含む非酸化性雰囲気、 あるいは減圧状態、 あるいはホットプレスなどによる高圧 状態などの雰囲気中で焼成することで比較的高い光 ¾i性を有するものが作製できるが、 特に このような雰囲気を用いず常圧の大気中で焼成を行ったものであっても比較的高い光 ¾1性を 有するものを作製可能である。 すなわち、 酸化亜鉛を主成分とする焼結体はどのような組成の ものであっても少なくとも波長 380 nm以上の可視光及び可視光より波長の長い光に対して 光透過性を有するものが作製し得る。 例えば、 酸化亜鉛を主成分とする焼結体はどのような組 成のものであっても光透過率 1%以上のものが作製し得る。 通常酸化亜鉛成分を ZnO で 55. 0モル%以上含有する酸化亜鉛を主成分とする焼結体において光 ¾i率 1 %以上のもの が作製し得る。 また、 例えば添加物を用いず焼成し実質的に ZnOだけからなる酸化亜鉛を主 成分とする焼結体では光 ¾1率 10%以上のものが作製し得る。 なお、 本発明において酸化亜 鉛を主成分とする焼結体の光 «率は少なくとも波長 200 nm〜800 nmの範囲の光に対 してのものである。 上記光 率は波長 605 nmの光に対して測定されたものである。 本発 明においては今後特に断らない限り酸化亜鉛を主成分とする焼結体の 率には上記測定値 を用いた。
また、 上記のようにアルミニウム成分を A 1203換算で 45. 0モル%以下の範囲で含む酸 化亜鉛を主成分とする焼結体は上記のように導電性を有するだけでなく光透過性を有するもの が作製し得る。 上記アルミニゥム成分を含む酸化亜鉛を主成分とする焼結体の 過率として は 1%以上のものが作製でき、 通常光透過率 10%以上のものが作製し得る。 さらに、 上記の ようにアルミニウム成分を A 1203換算で0. 001モル%〜45. 0モル%の範囲で含む酸 化亜鉛を主成分とする焼結体は上記のように導電性を有するだけでなく光 ¾1率 20%以上に
向上したものが得られ易く、 光 ¾1率 30 %以上、 40 %以上、 50 %以上、 60 %以上さら に 80%以上のものも作製し得る。 なお上記光透過率とはガラスなどの透明体の直線透過率で はなく窒化アルミニウムを主成分とする焼結体の光¾§率と同様に全 ¾i率を意味する。 詳しく説明すれば、 このような^ I過性を有する酸化 »を主成分とする焼結体は他に B e 〇、 MgO、 CaO、 Sr〇、 B a Oなどのアルカリ土類金属成分、 あるいは MnO、 Co〇、 N i〇、 F e 2〇3、 C r 203、 T i〇2などの遷移金属成分、あるいは S i〇2などの珪素成分、 あるいは S c 203、 Y203、 La203、 Ce02、 P r 6Oxl. Nd203、 Pm203、 Sm2〇3、 Eu203、 Gd2〇3、 Tb407、 Dy203、 Ho203、 Er 203、 Tm203、 Yb203、 Lu 2〇3などの希土類 素成分、 などの金属成分がアルミニウム成分以外に含まれていたとしても 性あるいは導電性が減じることは少ない。 その中で例えば A 1203などのアルミニウム 成分と同時に Sc、 Y、 La、 Ce、 Pr、 Nd、 Pm、 Sm、 Eu、 Gd、 Tb、 Dy、 H o、 Er、 Tm、 Yb、 L uなどの希土^ ¾素成分のうちから選ばれた少なくとも 1種以上の 成分を酸化物換算で 10. 0モル%以下含む酸化亜鉛を主成分とする焼結体であっても光 ¾ί§ 率 20%以上のものを得ることができる。 また、 上記希土麵 素成分を酸化物騰で 0. 00 02モル%〜 10. 0モル%の範囲で含む酸化亜鉛を主成分とする焼結体はさらに 率が 向上し易くなり 率 30%以上のものが得られ易くなり、 本発明においては最大 84%の ものも得られた。 すなわちアルミニウム成分を Α 12〇3換算で 45. 0モル%以下含み同時に 希土^ δ素成分のうちから選ばれた少なくとも 1種以上の成分を酸化物 で合計 0. 000 2モル%〜: L 0. 0モル%の範囲で含む酸化亜鉛を主成分とする焼結体は)1 ά¾ϋ率 30 %以上 のものが得られ易い。 また、 ァルミニゥム成分を八1203鍵で45. 0モル%以下含みさら に希土類 素成分のうちから選ばれた少なくとも 1種以上の成分を酸化物換算で合計 0. 00 06モル%〜 6. 0モル%の範囲で含む酸化亜鉛を主成分とする焼結体は光透過率 40 %以上 のものが得られ易い。 また、 アルミニウム成分を Α 12〇3換算で 45. 0モル%以下含みさら に希土類 素成分のうちから選ばれた少なくとも 1種以上の成分を酸化物 で合計 0. 00 1モル%〜 6. 0モル%の範囲で含む酸化亜鉛を主成分とする焼結体は光 率 50 %以上の ものが得られ易い。 また、 アルミニウム成分を A 1203鍵で 45. 0モル%以下含みさらに 希土 素成分のうちから選ばれた少なくとも: L種以上の成分を酸化物^ で合計 0. 002 モル%〜 3. 0モル%の範囲で含む酸化亜鉛を主成分とする焼結体は光 ¾ ^率 60 %以上のも のが得られ易い。
なお、 上記酸化亜鉛を主成分とする焼結体に含まれる希土類 素成分の含有量の換算に用い る酸ィ匕物とま S c2〇3、 Y203、 La203、 Ce〇2、 P r 6Oi Nd2〇3、 Pm203、 Sm 2〇3、 Eu2〇3、 Gd2〇3、 Tb407、 Dy2〇3、 Ho203、 Er203、 Tm2〇3、 Yb20 3、 Lu203を意味する。 また、上記アルミニウム成分と希土類沅素成分とを同時に含む酸化亜 鉛を主成分とする焼結体におけるアルミニウム成分の含有量は A 12〇3換算で 0. 001モ ル%〜45. 0モル%の範囲であること力 ¾¾ 性を高める上では好ましい。 このようにアル ミニゥム成分と希土観素成分とを同時に含む酸化亜鉛を主成分とする焼結体はより)16¾ 性 の優れたものが得られ易いが、 アルミニウム成分と希土! ^素成分とを同 むことによって 導電性が損じられることは少ない。
また、 上記アルミニウム成分の他に希土類元素成分とを同時に含む比較的高い光 ¾ϋ性を有 する酸化亜鉛を主成分とする焼結体を基板として用いた場合でも、 該基板に形成される窒化ガ リウム、 窒化インジウム、 窒化アルミニウムのうちから選ばれた少なくとも 1種以上を主成分 とする単結晶薄膜、 あるいは窒化ガリウム、 窒化インジウム、 窒化アルミニウムのうちから選 ばれた少なくとも 1種以上を主成分とする配向性多結晶薄膜の結晶性は、 アルミニゥム成分を 含むが実質的に希土 素成分を含まない酸化亜鉛を主成分とする焼結体を基板として用いた
ものに比べて通常は同じ程度であり、 結晶性カ汰きく低下するなどの変化は少ない。
上記のように、 アルミニウム成分を含む酸化亜鉛を主成分とする焼結体は導電性とともに比 較的高い光透過性とを有するものが比較的容易に作製し得る。
また上記のように、 アルミニゥム成分と希土類 素成分とを同時に含む酸化 を主成分と する焼結体は導電性とともにより高い光透過性とを有するものが比較的容易に作製し得る。 また、 上記のような酸化 などの導電性を有するセラミック材料を主成分とする焼結体を 基板として用いて発光素子を作製すれば、 基板に導通ビアを形成せずに上下に電極を配して電 極と素子との電気的接続をはかるという形状の発光素子が作製し得るという體を有する。 導 電性を有するセラミック材料を主成分とする焼結体を基板として用いる場合該焼結体の室温に おける抵抗率としては 1 X 1 0 2Ω · c m以下であれば上下に電極を配した形状の発光素子であ つても少ない損失で十分な電力を供給し得る。 導電性を有する焼結体の室温における抵抗率と しては室温において 1 X 1 0 ^ · c m以下のものが好ましく、 1 X 1 0 α Ω · c m以下のもの がより好ましく、 1 X 1 0 -' Ω · c m以下のものがさらに好ましい。
また、 本発明において前記のように、 酸化ベリリウムを主成分とする焼結体を基板として用 いたとき狭基板に直接形成される窒化ガリウム、 窒化インジウム、 窒化アルミニウムのうちか ら選ばれた少なくとも 1種以上を主成分とする単結晶薄膜は該基板の表面平滑性などの影響を 受け易く必ずしも結晶性に優れたものとなり得ない場合があるのに対して、 麵匕ベリリウム を主成分とする焼結体からなる基板の上にあらかじめ窒化ガリウム、 窒化インジウム、 窒化ァ ルミニゥムのうちから選ばれた少なくとも 1種以上を主成分とする無定形、 多結晶、 配向性多 結晶、単結晶など各種結晶状態の薄膜を形成しさらにその上に窒化ガリウム、室化インジウム、 窒化アルミニウムのうちから選ばれた少なくとも 1種以上を主成分とする単結晶薄膜を形成す れば該単結晶薄膜は該基板の表面平滑性などの影響をより受けにくくなり結晶性はさらに優れ たものとなり得る。 すなわち、 酸化ベリリウムを主成分とする焼結体を基板として用い、 窒化 ガリウム、 窒化インジウム、 窒化アルミニウムのうちから選ばれた少なくとも 1種以上を主成 分とする単結晶薄膜を直接形成すれば該単結晶薄膜のミラー指数 (0 0 2) の格子面の X線回 折口ッキングカーブの半値幅が 2 0 0秒以下の比較的結晶性に優れたものになるとは必ずしも 限らない。 それに対して、 酸化ベリリウムを主成分とする焼結体を基板として用い、 あらかじ め窒化ガリウム、 窒化インジウム、 窒化アルミニウムのうちから選ばれた少なくとも 1種以上 を主成分とする無定形、 多結晶、 配向性多結晶、 単結晶など各種結晶状態の薄膜を形成しさら にその上に窒化ガリウム、 窒化インジウム、 窒化アルミニウムのうちから選ばれた少なくとも 1種以上を主成分とする単結晶薄膜を形成すれば該単結晶薄膜のミラ一指数 ( 0 0 2 ) の格子 面の X線回折ロッキングカーブの半値幅は 2 0 0秒以下の比較的結晶性に優れたものが形成し 得る。
上記酸化ベリリゥムを主成分とする焼結体において、 ベリリゥム以外にマグネシウム成分、 カルシウム成分、 珪素成分のうちから選ばれた少なくとも 1種以上の成分を含有するものを基 板として用いたとき該基板には比較的良好な結晶性の薄膜が形成し得る。 通常マグネシウム成 分、 カルシウム成分、 珪素成分のうちから選ばれた少なくとも 1種以上の成分を酸化物 で 合計 3 5. 0モル%以下の範囲で含む酸化ベリリウムを主成分とする焼結体を基板として用い たときその基板上にはミラ一指数 ( 0 0 2) の格子面の X線回折ロッキングカーブの半値幅が 3 0 0秒以下の結晶性に優れた窒化ガリウム、 窒化インジウム、 窒化アルミニウムのうちから 選ばれた少なくとも 1種以上を主成分とする単結晶薄膜が 接形成し得る。 上記酸化ベリリウ ムを主成分とする焼結体のうちマグネシウム成分、 カルシウム成分、 珪素成分のうちから選ば れた少なくとも 1種以上の成分を酸化物 で合計 0. 0 0 0 2モル%〜 3 5. 0モル%の範 囲で含むものを基板として用いたときその基板上にはミラー指数 ( 0 0 2) の格子面の X線回
折ロッキングカーブの半値幅が 2 0 0秒以下の結晶性に優れた窒化ガリウム、窒化インジウム、 窒化アルミニウムのうちから選ばれた少なくとも 1種以上を主成分とする単結晶薄膜力埴接形 成できる。 また、 マグネシウム成分、 カルシウム成分、 珪素成分のうちから選ばれた少なくと も 1種以上の成分を酸化物霧で合計 0. 0 0 4モル%〜 3 5. 0モル%の範囲で含む酸化べ リリウムを主成分とする焼結体を基板として用いたとき該基板にはミラー指数 ( 0 0 2) の格 子面の X線回折ロッキングカーブの半値幅が 1 5 0秒以下の結晶性に優れた単結晶薄膜が 接 形成できる。 また、 マグネシウム成分、 カルシウム成分、 珪素成分のうちから選ばれた少なく とも 1種以上の成分を酸化物換算で合計 0. 0 1 5モル%〜 2 5. 0モル%の範囲で含む酸化 ベリリウムを主成分とする焼結体を基板として用いたとき該基板にはミラー指数 ( 0 0 2 ) の 格子面の X線回折ロッキングカーブの半値幅が 1 3 0秒以下の結晶性に優れた単結晶薄膜が直 接形成できる。
なお、 上記酸化ベリリウムを主成分とする焼結体において、 マグネシウム成分、 カルシウム 成分、 珪素成分、 各成分の含有量として酸化物 した値が用いられているが に用いた酸 化物とはマグネシウム成分の場合 Mg O、 カルシウム成分の: t は C a O、 珪素成分の場合は S i〇2である。以下本発明において酸化ベリリウムを主成分とする焼結体に含まれるマグネシ ゥム成分、 カルシウム成分、 珪素成分、 各成分の酸化物 に用いる化合物としては特に断ら ない限りそれぞれ Mg〇、 C a O、 S i〇2である。
さらに、 上記マグネシウム成分、 カルシウム成分、 珪素成分を含有する酸化ベリリウムを主 成分とする焼結体からなる基板を用いたとき該基板に直接形成される窒化ガリゥム、 窒化ィン ジゥム、 窒化アルミニウムのうちから選ばれた少なくとも 1種以上を主成分とする単結晶薄膜 の結晶 '性よりも、 同じ組成のマグネシウム成分、 カリレシゥム成分、 珪素成分を含有する酸化べ リリウムを主成分とする焼結体からなる基板の上にあらかじめ窒化ガリウム、窒化インジウム、 窒化アルミニウムのうちから選ばれた少なくとも 1種以上を主成分とする無定形、 多結晶、 配 向性多結晶、 単結晶など各種結晶状態の薄膜を形成しさらにその上に窒化ガリウム、 窒化イン ジゥム、 窒化アルミニウムのうちから選ばれた少なくとも 1種以上を主成分とする単結晶薄膜 を形成すれば該単結晶薄膜の結晶性はさらに優れたものとなり得る。 具体的に言えば、 マグネ シゥム成分、 カルシウム成分、 珪素成分のうちから選ばれた少なくとも 1種以上の成分を酸化 物 »で合計 3 5. 0モル%以下の範囲で含む酸化ベリリウムを主成分とする焼結体を基板と して用い、 その上にあらかじめ窒化ガリウム、 窒化インジウム、 窒化アルミニウムのうちから 選ばれた少なくとも 1種以上を主成分とする無定形、 多結晶、 配向性多結晶、 単結晶など各種 結晶状態の薄膜を形成しさらにその上に窒化ガリウム、 窒化インジウム、 窒化アルミニウムの うちから選ばれた少なくとも 1種以上を主成分とする単結晶薄膜を形成すれば該単結晶薄膜の ミラー指数 ( 0 0 2) の格子面の X線回折ロッキングカーブの半値幅としては 2 0 0秒以下、 通常 1 5 0秒以下の結晶性に優れたものが比較的容易に形成し得る。また、マグネシウム成分、 カルシウム成分、 珪素成分のうちから選ばれた少なくとも 1種以上の成分を酸化物 で合計 0. 0 0 0 2モル%〜 3 5. 0モル%の範囲で含む酸化ベリリゥムを主成分とする焼結体を基 板として用い、 その上にあらかじめ窒化ガリウム、 窒化インジウム、 窒化アルミニウムのうち から選ばれた少なくとも 1種以上を主成分とする無定形、 多結晶、 配向性多結晶、 単結晶など 各種結晶状態の薄膜を形成しさらにその上に窒化ガリウム、 窒化インジウム、 窒化アルミニゥ ムのうちから選ばれた少なくとも 1種以上を主成分とする単結晶薄膜を形成すれば該単結晶薄 膜のミラー指数 (0 0 2) の格子面の X線回折ロッキングカーブの半値幅として 1 3 0秒以下 の結晶性に優れたものが比較的容易に形成し得る。また、マグネシウム成分、カルシウム成分、 珪素成分のうちから選ばれた少なくとも 1種以上の成分を酸化物換算で合計 0. 0 0 1モル% 〜3 5. 0モル%の範囲で含む酸化ベリリウムを主成分とする焼結体を基板として用い、 その
上にあらかじめ窒化ガリウム、 窒化インジウム、 窒化アルミニウムのうちから選ばれた少なく とも 1種以上を主成分とする無定形、 多結晶、 配向性多結晶、 単結晶など各種結晶状態の薄膜 を形成しさらにその上に窒化ガリウム、 窒化インジウム、 窒化アルミニウムのうちから選ばれ た少なくとも 1種以上を主成分とする単結晶薄膜を形成すれば該単結晶薄膜のミラ一指数 ( 0 0 2 ) の格子面の X線回折ロッキングカーブの半値幅として 1 0 0秒以下の結晶性に優れたも のが比較的容易に形成し得る。
その際、 上記マグネシウム成分、 カルシウム成分、 珪素成分のうちから選ばれた少なくとも 1種以上の成分を酸化物換算で合計 0. 0 0 0 2モル%〜 3 5. 0モル%の範囲で含む酸化べ リリウムを主成分とする焼結体からなる基板にあらかじめ形成する窒化ガリウム、 窒化インジ ゥム、 窒化アルミニウムのうちから選ばれた少なくとも 1種以上を主成分とする配向性多結晶 薄膜の結晶性も上記範囲のマグネシウム成分、 カルシウム成分、 珪素成分を含まない酸化ベリ リウムを主成分とする焼結体からなる基板を用いたものに比べて向上し易ぐ 該配向性多結晶 薄膜のミラ一指数 (0 0 2) の格子面の X線回折ロッキング力一ブの半値幅は 9 0 0 0秒以下 のものが比較的容易に形成し得る。 また、 マグネシウム成分、 カルシウム成分、 珪素成分のう ちから選ばれた少なくとも 1種以上の成分を酸化物換算で合計 0. 0 0 1モル%〜 3 5. 0モ ル%の範囲で含む酸化ベリリウムを主成分とする焼結体からなる基板では、 該基板にあらかじ め形成する窒化ガリウム、 窒化インジウム、 窒化アルミニウムのうちから選ばれた少なくとも 1種以上を主成分とする配向性多結晶薄膜では該配向性多結晶薄膜のミラ一指数 ( 0 0 2) の 格子面の X線回折ロッキングカーブの半値幅として 8 0 0 0秒以下のものが比較的容易に形成 し得る。
このように酸ィ匕ベリリゥムを主成分とする焼結体からなる基板にあらかじめ窒化ガリゥム、 窒化インジウム、 窒化アルミニウムのうちから選ばれた少なくとも 1種以上を主成分とする無 定形、 多結晶、 配向性多結晶、 単結晶など各種結晶状態の薄膜を形成すれば、 さらにその上に 形成される窒化ガリウム、 窒化インジウム、 窒化アルミニウムのうちから選ばれた少なくとも
1種以上を主成分とする単結晶薄膜の結晶性を向上させる効果がある。 その効果は酸化ベリリ ゥムを主成分とする焼結体からなる基板の組成以外の要素、 例えば表面平滑性などにも大きく 影響されず、 例えば平均表面粗さ R aを 5 nm以下にしたものでなくても (すなわち、 焼き放 しの表面状態の基板、 ラッフ 磨した表面状態の基板、 ブラスト研磨した表面状態の基板、 機 械的な溝切り加工が施された基板、 あるいは鏡面研磨してある基板など、 平均表面粗さ R aが 5 nm以上のものであっても) 発揮され得る。
このような単結晶薄膜の結晶性に及ぼす酸化ベリリゥムを主成分とする焼結体中のマグネシ ゥム成分、 カルシウム成分、 珪素成分のうちから選ばれた少なくとも 1種以上の成分を含むこ との効果は、 例えば該酸化ベリリウムを主成分とする焼結体中に S r〇、 B a Oなどのアル力 リ土類金属成分、 あるいは S c 203、 Y2〇3、 L a 203、 C e 02、 P i^C^い Nd 203、 P m203、 Sm203、 E u 2〇3、 G d 2〇3、 T b 407、 D y 2〇3、 H o 2〇3、 E r 2〇3、 Tm2 03、 Y b 203、 11 203などの希土艇素成分、 その他 Mn O、 C o〇、 N i 0、 F e 203、 C r 203、 T i〇2など、 マグネシウム成分、 カルシウム成分、 珪素成分以外の金属成分が含ま れていたとしても減じることは少ない。 マグネシウム成分、 カルシウム成分、 珪素成分のうち から選ばれた少なくとも 1種以上の成分を酸化物換算で合計 3 5. 0モル%以下の範囲で含む 酸化ベリリウムを主成分とする焼結体を基板として用いたときその上に形成される単結晶薄膜 がこのような高い結晶性を有するものとなる原因については必ずしも明確ではないが、 おそら く上記の成分は粒界相となって酸化ベリリウム粒子間に存在し一部の酸化ベリリウム粒子の異 常粒子成長を抑制するので粒子間の空隙が少なく酸化ベリリゥム結晶粒子の大きさが比較的揃 つた微構造の焼結体となりその結果形成される単結晶薄膜の結晶性の向上をもたらすものと本
願発明者は考えている。
また、 上記酸化ベリリウムを主成分とする焼結体は通常 COや H2などを含 ϋ¾¾性雰囲気、 あるいは Ar、 He、 N2などを含む非酸化性雰囲気、 あるいは赃状態、 あるいはホットプレ スなどによる高圧状態などの雰囲気中で焼成することで高い光 ¾i性を有するものが作製でき るが、 このような雰囲気を用いず常圧の大気中で焼成を行ったものであっても比較的高い光透 過性を有するものが得られる。 すなわち、 酸化ベリリウムを主成分とする焼結体はどのような 組成のものであつても少なくとも波長 200n m以上の紫外光、 可視光及ぴ^ ^視光より波長の 長い光に対して 性を有するものが作製し得る。 例えば、 酸化ベリリウムを主成分とする 焼結体はどのような組成のものであっても光 ¾M率 1 %以上のものが作製し得る。 通常酸化べ リリウム成分を Be O換算で 65. 0モル%以上含有する酸化ベリリウムを主成分とする焼結 体において光透過率 1%以上のものが作製し得る。 また、 例えば添加物を用いず焼成し実質的 に B e 0だけからなる酸化ベリリゥムを主成分とする焼結体では光 率 10 %以上のものが 作製し得る。 なお、 本発明において酸化ベリリウムを主成分とする焼結体の)1 ά«率は少なく とも波長 200 nm〜800 nmの範囲の光に対してのものである。 上記光透過率は波長 60 5 nmの光に対して測定されたものである。 本発明においては今後特に断らない限り酸化ベリ リウムを主成分とする焼結体の光醒率には上記測定値を用いた。
また、 上記のようにマグネシウム成分、 カルシウム成分、 珪素成分のうちから選ばれた少な くとも 1種以上の成分を酸化物換算で合計 35. 0モル%以下の範囲で含む酸化べリリウムを 主成分とする焼結体でも¾¾¾率が 10%以上のものが作製し得る。 さらに、 上記のようにマ グネシゥム成分、 カルシウム成分、 珪素成分のうちから選ばれた少なくとも 1種以上の成分を 酸化物換算で合計 0. 0002モル%〜 35. 0モル%の範囲で含む酸化ベリリゥムを主成分 とする焼結体は 率が 20%以上に向上したものが得られ易く、 ¾¾i率 30%以上、 4 0%以上、 50%以上、 60%以上、 さらに 80%以上のものも作製し得る。 なお上記)1 ά¾§ 率とはガラスなどの透明体の直線透過率ではなく窒化アルミニウムを主成分とする焼結体の光 ¾ 率と同様に全透過率を意味する。
詳しく説明すれば、 上記に示すような酸化ベリリウムを主成分とする焼結体は S rO、 Ba 0、 Mn〇、 Co〇、 NiO、 Fe
2〇
3、 Cr
20
3、 Ti〇
2、 Sc
20
3、 Y
20
3、 L a
2O
a> Ce0
2、 PreOiい Nd
2〇
3、 Pm
2〇
3、 Sm
2〇
3、 Eu
20
3、 Gd
20
3、 Tb
40
7、 Dy
2〇
3、 Ho
20
3、 E r
2〇
3、 Tm
2〇
3、 Yb
2〇
3、 Lu
2〇
3など、 マグネシウム成分、 カルシ ゥム成分、 珪素成分以外の他の金属成分が含まれていたとしても
1 ^過性が減じることは少な い。 その中で例えば M g〇などのマグネシウム成分、 C a Oなどのカルシウム成分、 S i〇
2な どの珪素成分のうちから選ばれた少なくとも 1種以上の成分と同時に Sc、 Y、 La、 Ce、 Pr、 Nd、 Pm、 Sm、 Eu、 Gd、 Tb、 Dy、 Ho、 Er、 Tm、 Yb、 Luなどの希 土! ^素成分のうちから選ばれた少なくとも 1種以上の成分を酸化物 1^で合計 5. 0モル% 以下含む酸化ベリリゥムを主成分とする焼結体であっても光 ¾1率 20 %以上のものを得るこ とができる。 また、 上記希土類 素成分を酸化物露で 0. 00005モレ%〜5. 0モル% の範囲で含む酸化ベリリゥムを主成分とする焼結体はさらに光透過性が向上し易くなり光 ¾Μ 率 30%以上のものが得られ易くなり、 本発明においては最大 81%のものも得られた。 すな わちマグネシウム成分、 カルシウム成分、 珪素成分のうちから選ばれた少なくとも 1種以上の 成分を酸化物換算で合計 35. 0モル%以下の範囲で含み、 さらに希土^ ¾素成分のうちから 選ばれた少なくとも 1種以上の成分を酸化物換算で合計 0. 00005モル%〜5. 0モル% の範囲で含む酸化ベリリゥムを主成分とする焼結体は ¾¾1率 30 %以上のものが得られ易い。 また、 マグネシウム成分、 カルシウム成分、 珪素成分のうちから選ばれた少なくとも 1種以上 の成分を酸化物換算で合計 35. 0モル%以下の範囲で含み、 さらに希土類¾素成分のうちか
ら選ばれた少なくとも 1種以上の成分を酸化物 で合計 0. 0 0 0 5モル%〜 3. 0モル% の範囲で含む酸化ベリリウムを主成分とする焼結体はう 率 4 0 %以上のものが得られ易い。 また、 マグネシウム成分、 カルシウム成分、 珪素成分のうちから選ばれた少なくとも 1種以上 の成分を酸化物^:で合計 3 5. 0モル%以下の範囲で含み、 さらに希土 ¾素成分のうちか ら選ばれた少なくとも 1種以上の成分を酸化物 で合計 0. 0 0 2モル%〜 3. 0モル%の 範囲で含む酸化ベリリウムを主成分とする焼結体は光 ¾i率 5 0 %以上のものが得られ易い。 また、 マグネシウム成分、 カルシウム成分、 珪素成分のうちから選ばれた少なくとも 1種以上 の成分を酸化物 で合計 3 5. 0モル%以下の範囲で含み、 さらに希土類 素成分のうちか ら選ばれた少なくとも 1種以上の成分を酸化物 で合計 0. 0 0 5モル%〜 3. 0モル%の 範囲で含む酸化ベリリゥムを主成分とする焼結体は) 率 6 0 %以上のものが得られ易い。 なお、 上記酸化ベリリウムを主成分とする焼結体に含まれる希土類元素成分の含有量の » に用いる酸化物とは S c
20
3、 Y
20
3、 L a
2〇
3、 C e〇
2、 P r
N d
20
3, Pm
20
3、 Sm
20
3、 E u
20
3、 G d
2〇
3、 T b
4〇
7、 D y
2〇
3、 H o
20
3、 E r
20
3、 Tm
2〇
3、 Y b
2〇
3、 L u
2〇
3である。 また、 上記マグネシウム成分、 カルシウム成分、 珪素成分のうち少な くとも 1種以上を含み、 さらに希土 素成分を含む酸化ベリリウムを主成分とする焼結体に おいて、 マグネシウム成分、 カルシウム成分、 珪素成分のうちから選ばれた少なくとも 1種以 上の成分の含有量としては酸化物 で合計 0. 0 0 0 2モル%〜 3 5. 0モル%の範囲であ ることが、 光透過性を高める上では好ましい。
また、 上記マグネシウム成分、 カルシウム成分、 珪素成分のうち少なくとも 1種以上の成分 を含みさらに希土^素成分を同時に含む比較的高い)1 ά¾ϋ性を有する酸化ベリリゥムを主成 分とする焼結体を基板として用いた場合でも、 該基板に形成される窒化ガリウム、 窒化インジ ゥム、 窒化アルミニウムのうちから選ばれた少なくとも 1種以上を主成分とする単結晶薄膜、 あるいは窒化ガリウム、 窒化インジウム、 窒化アルミニウムのうちから選ばれた少なくとも 1 種以上を主成分とする配向性多結晶薄膜の結晶性は、 マグネシウム成分、 カルシウム成分、 珪 素成分のうち少なくとも 1種以上の成分を含むが実質的に希土類 素成分を含まなレ ^酸化ベリ リゥムを主成分とする焼結体を基板として用いたものに比べて通常は同じ程度であり、 結晶性 が大きく低下するなどの変化は少ない。
本発明において前記のように、 酸化アルミニウムを主成分とする焼結体を基板として用いた とき該基板に直接形成される窒化ガリウム、 窒化インジウム、 窒化アルミニウムのうちから選 ばれた少なくとも 1種以上を主成分とする単結晶薄膜は該基板の表面平滑性などの影響を受け 易く必ずしも結晶性に優れたものとなり得ない場合があるのに対して、 讀化アルミ二ゥムを 主成分とする焼結体からなる基板の上にあらかじめ窒化ガリウム、 窒化インジウム、 窒化アル ミニゥムのうちから選ばれた少なくとも 1種以上を主成分とする無定形、 多結晶、 配向性多結 晶、 単結晶など各種結晶状態の薄膜を形成しさらにその上に窒化ガリウム、 窒化インジウム、 窒化アルミニウムのうちから選ばれた少なくとも 1種以上を主成分とする単結晶薄膜を形成す れば該単結晶薄膜は該基板の表面平滑性などの影響をより受けにくくなり結晶性はさらに優れ たものとなり得る。 すなわち、 酸化アルミニウムを主成分とする焼結体を基板として用い、 窒 化ガリウム、 窒化インジウム、 窒化アルミニウムのうちから選ばれた少なくとも 1種以上を主 成分とする単結晶薄膜を直接形成すれば該単結晶薄膜のミラ一指数 ( 0 0 2 ) の格子面の X線 回折口ッキングカーブの半値幅は 2 0 0秒以下の比較的結晶性に優れたものになるとは必ずし も限らない。 それに対して、 酸化アルミニウムを主成分とする焼結体を基板として用い、 あら かじめ窒化ガリウム、 窒化インジウム、 窒化アルミニウムのうちから選ばれた少なくとも 1種 以上を主成分とする無定形、 多結晶、 配向性多結晶、 単結晶など各種結晶状態の薄膜を形成し さらにその上に窒化ガリゥム、 窒化ィンジゥム、 窒化アルミニゥムのうちから選ばれた少なく
とも 1種以上を主成分とする単結晶薄膜を形成すれば該単結晶薄膜のミラ一指数 ( 0 0 2) の 格子面の X線回折ロッキング力一ブの半値幅は 2 0 0秒以下の比較的結晶性に優れたものが形 成し得る。
上記酸化アルミニウムを主成分とする焼結体において、 アルミニウム以外にマグネシウム成 分、 カルシウム成分、 珪素成分のうちから選ばれた少なくとも 1種以上の成分を含有するもの を基板として用いたとき該基板には比較的良好な結晶性の薄膜が形成し得る。 通常マグネシゥ ム成分、 カルシウム成分、 珪素成分のうちから選ばれた少なくとも 1種以上の成分を酸化物換 算で合計 4 5. 0モル%以下の範囲で含む酸化アルミニウムを主成分とする ¾結体を基板とし て用いたときその基板上にはミラ一指数 (0 0 2 ) の格子面の X線回折ロッキングカーブの半 値幅が 3 0 0秒以下の結晶性に優れた窒化ガリウム、 窒化インジウム、 窒化アルミニウムのう ちから選ばれた少なくとも 1種以上を主成分とする単結晶薄膜が直接形成し得る。 上記酸化ァ ルミ二ゥムを主成分とする焼結体のうちマグネシウム、 カルシウム、 珪素成分のうちから選ば れた少なくとも 1種以上の成分を酸化物換算で合計 0. 0 0 1モル%〜4 5. 0モル%の範囲 で含むものを基板として用いたときその基板上にはミラ一指数 (0 0 2) の格子面の X線回折 ロッキングカーブの半値幅が 2 0 0秒以下の結晶性に優れた窒化ガリウム、 窒化インジウム、 窒化アルミニウムのうちから選ばれた少なくとも 1種以上を主成分とする単結晶薄膜が直接形 成できる。 また、 マグネシウム、 カルシウム、 珪素成分のうちから選ばれた少なくとも 1種以 上の成分を酸化物 で合計 0. 0 2モル%〜4 5. 0モル%の範囲で含む酸化アルミニウム を主成分とする 結体を基板として用いたとき該基板にはミラー指数 ( 0 0 2) の格子面の X 線回折ロッキングカーブの半値幅が 1 5 0秒以下の結晶性に優れた単結晶薄膜が直接形成でき る。 また、 マグネシウム、 カルシウム、 珪素成分のうちから選ばれた少なくとも 1種以上の成 分を酸化物 で合計 0. 0 8モル%〜 3 5. 0モル%の範囲で含む酸化アルミニゥムを主成 分とする焼結体を基板として用いたとき該基板にはミラー指数 ( 0 0 2 ) の格子面の X線回折 ロッキングカーブの半値幅が 1 3 0秒以下の結晶性に優れた単結晶薄膜が直接形成できる。 なお、 上記酸化アルミニウムを主成分とする焼結体において、 マグネシウム成分、 カルシゥ ム成分、 珪素成分、 各成分の含有量として酸化物 »した値が用いられているが換算に用いた 酸化物とはマグネシウム成分の場合 Mg O、 カルシウム成分の場合は C a 0、 珪素成分の場合 は S i 02である。以下本発明において酸化アルミニウムを主成分とする焼結体に含まれるマグ ネシゥム成分、 カレシゥム成分、 珪素成分、 各成分の酸化物^^に用いる化合物としては特に 断らない限りそれぞれ Mg O、 C a O、 S i 02である。
さらに、 上記マグネシウム成分、 カルシウム成分、 珪素成分を含有する酸化アルミニウムを 主成分とする焼結体からなる基板を用いたとき該基板に直接形成される窒化ガリウム、 窒化ィ ンジゥム、 窒化アルミニウムのうちから選ばれた少なくとも 1種以上を主成分とする単結晶薄 膜の結晶性よりも、 同じ組成のマグネシウム成分、 カルシウム成分、 珪素成分を含有する酸化 アルミニウムを主成分とする焼結体からなる基板の上にあらかじめ窒化ガリゥム、 窒化ィンジ ゥム、 窒化アルミニウムのうちから選ばれた少なくとも 1種以上を主成分とする無定形、 多結 晶、 配向性多結晶、 単結晶など各種結晶状態の薄膜を形成しさらにその上に窒化ガリウム、 窒 化インジウム、 窒化アルミニウムのうちから選ばれた少なくとも 1種以上を主成分とする単結 晶薄膜を形成すれば該単結晶薄膜の結晶性はさらに優れたものとなり得る。 具体的に言えば、 マグネシウム、 カルシウム、 珪素成分のうちから選ばれた少なくとも 1種以上の成分を酸化物 換算で合計 4 5. 0モル%以下の範囲で含む酸化アルミニウムを主成分とする焼結体を基板と して用い、 その上にあらかじめ窒化ガリウム、 窒化インジウム、 窒化アルミニウムのうちから 選ばれた少なくとも 1種以上を主成分とする無定形、 多結晶、 配向性多結晶、 単結晶など各種 結晶状態の薄膜を形成しさらにその上に窒化ガリウム、 窒化インジウム、 窒化アルミニウムの
うちから選ばれた少なくとも 1種以上を主成分とする単結晶薄膜を形成すれば該単結晶薄膜の ミラー指数 (0 0 2) の格子面の X線回折ロッキングカーブの半値幅としては 2 0 0秒以下、 通常 1 5 0秒以下の結晶性に優れたものが比較的容易に形成できる。 また、 マグネシウム、 力 ルシゥム、 珪素成分のうちから選ばれた少なくとも 1種以上の成分を酸化物換算で合計 0. 0 0 1モル%〜4 5. 0モル%の範囲で含む酸化アルミニウムを主成分とする焼結体を基板とし て用い、 その上にあらかじめ窒化ガリウム、 窒化インジウム、 窒化アルミニウムのうちから選 ばれた少なくとも 1種以上を主成分とする無定形、 多結晶、 配向性多結晶、 単結晶など各種結 晶状態の薄膜を形成しさらにその上に窒化ガリウム、 窒化インジウム、 窒化アルミニウムのう ちから選ばれた少なくとも 1種以上を主成分とする単結晶薄膜を形成すれば該単結晶薄膜のミ ラー指数 (0 0 2) の格子面の X線回折ロッキングカーブの半値幅として 1 3 0秒以下の結晶 性に優れたものが比較的容易に形成できる。 また、 マグネシウム、 カルシウム、 珪素成分のう ちから選ばれた少なくとも 1種以上の成分を酸化物換算で合計 0. 0 0 5モル%〜 4 5. 0モ ル%の範囲で含む酸化アルミニウムを主成分とする焼結体を基板として用い、 その上にあらか じめ窒化ガリウム、 窒化インジウム、 窒化アルミニウムのうちから選ばれた少なくとも 1種以 上を主成分とする無定形、 多結晶、 配向性多結晶、 単結晶など各種結晶状態の薄膜を形成しさ らにその上に窒化ガリウム、 窒化インジウム、 窒化アルミニウムのうちから選ばれた少なくと も 1種以上を主成分とする単結晶薄膜を形成すれば該単結晶薄膜のミラ一指数 (0 0 2) の格 子面の X線回折ロッキングカーブの半値幅として 1 0 0秒以下の結晶性に優れたものが比較的 容易に形成し得る。
その際、 上記マグネシウム成分、 カルシウム成分、 珪素成分のうちから選ばれた少なくとも 1種以上の成分を酸化物購で合計 0. 0 0 1モル%〜4 5. 0モル%の範囲で含む酸化アル ミニゥムを主成分とする焼結体からなる基板にあらかじめ形成する窒化ガリウム、 窒化インジ ゥム、 窒化アルミニウムのうちから選ばれた少なくとも 1種以上を主成分とする配向性多結晶 薄膜の結晶性も上記範囲のマグネシウム成分、 カルシウム成分、 珪素成分を含まない酸化アル ミニゥムを主成分とする焼結体からなる基板を用いたものに比べて向上し易ぐ 該配向性多結 晶薄膜のミラ一指数 (0 0 2) の格子面の X線回折ロッキングカーブの半値幅は 9 0 0 0秒以 下のものが比較的容易に形成し得る。 また、 マグネシウム成分、 カルシウム成分、 珪素成分の うちから選ばれた少なくとも 1種以上の成分を酸化物 で合計 0. 0 0 5モル%〜 4 5. 0 モル%の範囲で含む酸化アルミニウムを主成分とする焼結体からなる基板では、 該基板にあら かじめ形成する窒化ガリウム、 窒化インジウム、 窒化アルミニウムのうちから選ばれた少なく とも 1種以上を主成分とする配向性多結晶薄膜のミラ一指数 (0 0 2 ) の格子面の X線回折口 ッキングカーブの半値幅として 8 0 0 0秒以下のものが比較的容易に形成し得る。
このように酸化アルミニウムを主成分とする焼結体からなる基板にあらかじめ窒化ガリウム、 窒化インジウム、 窒化アルミニウムのうちから選ばれた少なくとも 1種以上を主成分とする無 定形、 多結晶、 配向性多結晶、 単結晶など各種結晶状態の薄膜を形成すれば、 さらにその上に 形成される窒化ガリウム、 窒化インジウム、 窒化アルミニウムのうちから選ばれた少なくとも 1種以上を主成分とする単結晶の結晶性を向上させる効果がある。 その効果は酸化アルミニゥ ムを主成分とする焼結体からなる基板の組成以外の要素、 例えば表面平滑性などにも大きく影 響されず、 例えば平均表面粗さ R aを 5 nm以下にしたものでなくても (すなわち、 焼き放し の表面状態の基板、 ラップ研磨した表面状態の基板、 ブラス卜研磨した表面状態の基板、 機械 的な溝切り加工が施された基板、 あるいは鏡面研磨してある基板など、 平均表面粗さ R aが 5 nm以上のものであっても) 発揮され得る。
このような単結晶薄膜の結晶性に及ぼす酸化アルミ二ゥムを主成分とする焼結体中のマグネ シゥム、 カルシウム、 珪素成分のうちから選ばれた少なくとも 1種以上を含むことの効果は、
例えば該酸化アルミニウムを主成分とする焼結体中に Be 0、 S rO、 B a Oなどのアルカリ 土類金属成分、 あるいは Sc 203、 Y2〇3、 La2〇3、 Ce〇2、 Pr^O い Nd203、 Pm 2〇3、 Sm2〇3、 Eu2〇3、 Gd203、 Tb407、 Dy203、 Ho2〇3、 Er2〇3、 Tm20 3、 Yb2〇3、 Lu2〇3などの希土贩素成分、 その他 MnO、 CoO、 N i 0、 Fe2〇3、 C r203、 Ti〇2など、 マグネシウム成分、 カルシウム成分、珪素成分以外の金属成分が含まれ ていたとしても減じることは少ない。 マグネシウム、 カルシウム、 珪素成分のうちから選ばれ た少なくとも 1種以上の成分を酸化物換算で合計 45. 0モル%以下の範囲で含む酸化アルミ 二ゥムを主成分とする焼結体を基板として用いたときその上に形成される単結晶薄膜がこのよ うな高い結晶性を有するものとなる原因については必ずしも明確ではないが、 おそらく上記の 成分は粒界相となって酸化アルミニゥム粒子間に存在し一部の酸化アルミニゥム粒子の異常粒 子成長を抑制するので立子間の空隙が少なく酸化アルミニウム結晶粒子の大きさが比較的揃つ た微構造の焼結体となりその結果形成される単結晶薄膜の結晶性の向上をもたらすものと本願 発明者は考えている。
また、上記酸化アルミニウムを主成分とする焼結体〖雄常 COや H2などを含 ¾ ¾性雰囲気、 あるいは Ar、 He、 N2などを含む非酸化性雰囲気、 あるいは減圧状態、 あるいはホットプレ スなどによる高圧状態などの雰囲気中で «することで高い光 ¾i性を有するものが作製でき るが、 このような雰囲気を用いず常圧の大気中で «を行ったものであっても比較的高い光透 過性を有するものが得られる。 すなわち、 酸化アルミニウムを主成分とする焼結体はどのよう な組成のものであつても少なくとも波長 160n m以上の紫外光、 可視光及び可視光より波長 の長い光に対して光 ¾1性を有するものが作製し得る。 例えば、 酸化アルミニウムを主成分と する焼結体はどのような組成のものであっても光 ¾i率 1 %以上のものが作製し得る。 通常酸 化アルミニウム成分を A 1203購で 55. 0モル%以上含有する酸化アルミニウムを主成分 とする焼結体において光透過率 1%以上のものが作製し得る。 また、 例えば添加物を用いず焼 成し実質的に A 1203だけからなる酸化アルミニウムを主成分とする焼結体では 過率 1 0%以上のものが作製し得る。 なお、 本発明において酸化アルミニウムを主成分とする焼結体 の光 ¾ii率は少なくとも波長 160 nm〜800 nmの範囲の光に対してのものである。 上記 の光顯率は波長 605 nmの光に対して測定されたものである。 本発明においては今後特に 断らない限り酸化アルミニウムを主成分とする焼結体の光透過率には上記測定値を用いた。 また、 上記のようにマグネシウム成分、 カルシウム成分、 珪素成分を含む酸化アルミニゥム を主成分とする焼結体のうち、 少なくとも Mg〇などのマグネシウム成分及び C a Oなどの力 ルシゥム成分及び S i 02などの珪素成分のうちから選ばれた少なくとも 1種以上の成分を酸 化物騰で合計 45. 0モル%以下の範囲で含む酸化アルミニウムを主成分とする焼結体は通 常光透過率が 10%以上のものが作製し得る。 さらに、 マグネシウム成分、 カルシウム成分、 珪素成分を含む酸化アルミニウムを主成分とする焼結体のうち、 少なくとも MgOなどのマグ ネシゥム成分及び C a〇などのカルシウム成分及び S i〇 2などの珪素成分のうちから選ばれ た少なくとも 1種以上の成分を酸化物換算で合計 0. 001モル%〜 45. 0モル%の範囲で 含む酸化アルミニウムを主成分とする焼結体は通常光透過率が 20 %以上に向上したものが得 られ易く、 光透過率 30%以上、 40 %以上、 50%以上、 60%以上、 さらに 80%以上の ものも作製し得る。 なお、 上記光 ¾1率とはガラスなどの透明体の直線透過率ではなく窒化ァ ルミ二ゥムを主成分とする焼結体の光透過率と同様に全 ¾1率を意味する。
詳しく説明すれば、 このような酸化アルミニウムを主成分とする焼結体は Be 0、 Sr〇、 BaO、 MnO、 CoO、 N i 0、 Fe2〇3、 Cr 203、 T i 02、 Sc203、 Y203、 La2 03、 Ce02、 P r 6Οι Nd2〇3、 Pm203、 Sm203、 Eu203、 Gd203、 Tb407、 Dy203、 Ho2〇3、 E r 203、 Tm203、 Yb2〇3、 Lu2〇3など、 マグネシウム成分、 力
ルシゥム成分、 珪素成分以外の他の金属成分が含まれていたとしても光 ¾i性が減じることは 少ない。 その中で例えば M g Oなどのマグネシウム成分及び C a Oなどのカルシウム成分及び S i〇2などの珪素成分のうちから選ばれた少なくとも 1種以上の成分を含み、 さらに同時に S c、 Y、 La、 Ce、 Pr、 Nd、 Pm、 Sm、 Eu、 Gd、 Tb、 Dy、 Ho、 Er、 Tm、 Yb、 L uなどの希土^ ΰ素成分のうちから選ばれた少なくとも 1種以上の成分を酸化物換算 で 10. 0モル%以下含む酸化アルミニウムを主成分とする焼結体であっても ½¾ 率 20 % 以上のものを得ること力 きる。また、上記希土顔 素成分を酸化物騰で 0. 0002モル%
〜 10. 0モル%の範囲で含む酸化アルミニウムを主成分とする焼結体はさらに光扁性が向 上し易くなり½¾1率 30%以上のものが得られ易くなり、 本発明においては最大 82%のも のも得られた。 すなわち、 マグネシウム成分及びカルシウム成分及び 素成分のうちから選ば れた少なくとも 1種以上の成分を酸化物換算で合計 45. 0モル%以下含み、 さらに同時に希 土 素成分のうちから選ばれた少なくとも 1種以上の成分を酸化物 で合計 0. 0002 モル%〜 10. 0モル%の範囲で含む酸化アルミニウムを主成分とする焼結体は光透過率 3 0%以上のものが得られ易い。 また、 マグネシウム成分及びカルシウム成分及ぴ 素成分のう ちから選ばれた少なくとも 1種以上の成分を酸化物換算で合計 45. 0モル%以下含み、 さら に同時に希土類 素成分のうちから選ばれた少なくとも 1種以上の成分を酸化物 »で合計 0. 001モル%〜 6. 0モル%の範囲で含む酸化アルミ二ゥムを主成分とする焼結体は ½¾ 率 40%以上のものが得られ易い。 また、 マグネシウム成分及びカルシウム成分及び 素成分の うちから選ばれた少なくとも 1種以上の成分を酸化物換算で合計 45. 0モル%以下含み、 さ らに同時に希土類 素成分のうちから選ばれた少なくとも 1種以上の成分を酸化物 で合計 0. 005モル%〜6. 0モル%の範囲で含む酸化アルミニウムを主成分とする焼結体は 過率 50 %以上のものが得られ易い。 また、 マグネシウム成分及びカルシウム成分及ぴ 素成 分のうちから選ばれた少なくとも 1種以上の成分を酸化物購で合計 45. 0モル%以下含み、 さらに同時に希土 M¾素成分のうちから選ばれた少なくとも 1種以上の成分を酸化物換算で合 計 0. 01モル%〜 3. 0モル%の範囲で含む酸化アルミニゥムを主成分とする焼結体は光透 過率 60%以上のものが得られ易い。
また、 上記マグネシウム成分及びカルシウム成分及び珪素成分のうちから選ばれた少なくと も 1種以上の成分を含みさらに同時に希土類 J£素成分を含む酸化アルミニウムを主成分とする 焼結体において、 含まれるマグネシウム成分及びカルシウム成分及び珪素成分のうちから選ば れた少なくとも 1種以上の成分は酸化物換算で合計 0. 001モル%〜 45. 0モル%の範囲 であることが、 性を高める上では好ましい。
なお、 上記酸化アルミニウムを主成分とする焼結体に希土類元素成分と同時に含まれるマグ ネシゥム成分及びカルシウム成分及ぴ 素成分としては通常これらのうちの少なくとも 2種以 上を用いることが光透過性をより向上させる上で好ましい。 M g〇などのマグネシウム成分及 び C a Oなどのカルシウム成分及び S i〇2などの珪素成分のうちから選ばれた少なくとも 2 種以上の成分を含むということは具体的にはマグネシウム成分と珪素成分とを同時に含む、 あ るいはカルシウム成分と珪素成分とを同時に含む、 あるいはマグネシウム成分とカルシウム成 分とを同時に含む、 あるいはマグネシウム成分とカルシウム成分及び 成分の 3成分を同時 に含むということを意味する。 上記酸化アルミニウムを主成分とする焼結体に含まれるマグネ シゥム成分、 カルシウム成分、 珪素成分の含有量の換算に用いる酸化物とはそれぞれマグネシ ゥム成分で MgO、 カルシウム成分で C a〇、 珪素成分で S i02である。 また、 上記酸化アル ミニゥムを主成分とする焼結体に含まれる希土類 J£素成分の含有量の換算に用いる酸化物とは Sc2〇3、 Y203、 La2〇3、 Ce02、 P r 60!^ Nd2〇3、 Pm2〇3、 Sm203、 Eu2 03、 Gd203、 Tb407、 Dy203、 Ho203、 Er 203、 Tm203、 Yb203、 Lu203
である。
また、 上記マグネシウム成分、 カルシウム成分、 珪素成分のうちから選ばれた少なくとも 1 種以上の成分を含みさらに希土 素成分を同時に含む比較的高い光 性を有する酸化アル ミニゥムを主成分とする焼結体、 あるいはマグネシウム成分、 カルシウム成分、 珪素成分のう ちから選ばれた少なくとも 1種以上あるいは 2種以上の成分を含みさらに希土類 素成分を同 時に含む比較的高い ¾¾1性を有する酸化アルミニウムを主成分とする焼結体を基板として用 いた場合でも、 該基板に形成される窒化ガリウム、 窒化インジウム、 窒化アルミニウムのうち から選ばれた少なくとも 1種以上を主成分とする単結晶薄膜、 あるいは窒化ガリウム、 窒化ィ ンジゥム、 窒化アルミニウムのうちから選ばれた少なくとも 1種以上を主成分とする配向性多 結晶薄膜の結晶性は、 マグネシウム成分、 カルシウム成分、 珪素成分のうち少なくとも 1種以 上の成分を含むが実質的に希土類 素成分を含まない酸化アルミニウムを主成分とする焼結体 を基板として用いたものに比べて通常は同じ程度であり、 大きく結晶性が低下するなどの変化 は少ない。
前記のように、 窒化ガリウムを主成分とする焼結体を基板として用いたとき該基板に直接形 成される窒化ガリウム、 窒化インジウム、 窒化アルミニウムのうちから選ばれた少なくとも 1 種以上を主成分とする単結晶薄膜は該基板の表面平滑性などの影響を受け易く必ずしも結晶性 に優れたものとなり得ない場合があるのに対して、 該窒化ガリウムを主成分とする焼結体から なる基板の上にあらかじめ窒化ガリウム、 窒化インジウム、 窒化アルミニウムのうちから選ば れた少なくとも 1種以上を主成分とする無定形、 多結晶、 配向性多結晶、 単結晶のうちから選 ばれた少なくとも 1種以上の結晶状態を有する薄膜を形成しさらにその上に窒化ガリゥム、 窒 化インジウム、 窒化アルミニウムのうちから選ばれた少なくとも 1種以上を主成分とする単結 晶薄膜を形成すれば該単結晶薄膜は該基板の表面平滑性などの影響をより受けにくくなり結晶 性はさらに優れたものとなり得る。 すなわち、 窒化ガリウムを主成分とする焼結体を基板とし て用い、 窒化ガリウム、 窒化インジウム、 窒化アルミニウムのうちから選ばれた少なくとも 1 種以上を主成分とする単結晶薄膜を直接形成すれば該単結晶薄膜のミラー指数 (002) の格 子面の X線回折ロッキングカーブの半値幅が 200秒以下の比較的結晶性に優れたものになる とは必ずしも限らない。それに対して、窒化ガリウムを主成分とする焼結体を基板として用い、 該基板にあらかじめ窒化ガリウム、 窒化インジウム、 窒化アルミニウムのうちから選ばれた少 なくとも 1種以上を主成分とする無定形、 多結晶、 配向性多結晶、 単結晶のうちから選ばれた 少なくとも 1種以上の結晶状態を有する薄膜を形成しさらにその上に窒化ガリウム、 窒化イン ジゥム、 窒化アルミニウムのうちから選ばれた少なくとも 1種以上を主成分とする単結晶薄膜 を形成すれば該単結晶薄膜のミラー指数 (002) の格子面の X線回折ロッキングカーブの半 値幅は 200秒以下の比較的結晶性に優れたものが形成し得る。
上記窒化ガリウムを主成分とする焼結体において、ガリウム以外に BeO、 MgO、 CaO、 S r〇、 B a Oなどのアルカリ土類金属成分、 及び Sc2〇3、 Y203、 La203、 Ce〇2、 P r 6Oi Nd203、 Pm203、 Sm203、 Eu203、 Gd203、 Tb407、 Dy2〇3、 Ho 203、 Er2〇3、 Tm203、 Yb2〇3、 L u 2〇3; iどの希土 II¾素成分、及び nO、 CoO、 Ni〇、 Fe2〇3、 Cr2〇3、 T i 02、 Mo〇3、 W03、 Nb205、 Ta205、 V205など の遷移金属元素成分、 及びアルミニウム成分、 及びインジウム成分、 及び ¾素、 ms^ (Z n)、 カドミウム (Cd)、 炭素 (C)、 珪素 (S i)、 ゲルマニウム (Ge)、 セレン (Se;)、 テルル (Te) などの成分を少なくとも 1種以上含有するものを用いたとき該焼結体には比較 的良好な結晶性の薄膜が形成し得る場合が多い。 なお、 ベリリウム (Be)、 マグネシウム (M g)、 Zn、 Cd、 C, S i、 Ge、 Se、 Te、 酸素などの成分を少なくとも 1種以上含む窒 化ガリウムを主成分とする焼結体は比較的高い導電性を有するものが作製し得る。
通常ガリウム成分を G a N で 55. 0モル%以上含む窒化ガリウムを主成分とする焼結 体を用いたときその上にはミラー指数 (002) の格子面の X線回折ロッキングカープの半値 Ψ畐が 300秒以下の結晶性に優れた窒化ガリウム、 窒化インジウム、 窒化アルミニウムのうち から選ばれた少なくとも 1種以上を主成分とする単結晶薄膜がず接形成し得る。 上記窒化ガリ ゥムを主成分とする焼結体のうち Be 0、 MgO、 Ca〇、 S rO、 Ba〇などのアルカリ土 類金属成分、 及び Sc203、 Y203、 La203、 Ce〇2、 P Γ6Οι Nd2〇3、 Pm2〇3、 Sm203、 Eu203、 Gd203、 Tb407、 Dy203、 Ho2〇3、 Er203、 Tm203、 Yb 203、 Lu2〇3などの希土類 素成分を含むものは該焼結体に形成される単結晶薄膜の結晶性 向上に有効な作用を及ぼす。 アル力リ土類金属成分及«土類 素成分は窒化ガリゥムを主成 分とする焼結体中にそれぞれ単独で含まれていてもよいしあるいは同時に含まれていてもよい。 該ァルカリ土類金属成分及び希土類 素成分のうちから選ばれた少なくとも 1種以上の成分を 酸化物換算で 30. 0モル%以下含むものを用いたときその上にはミラー指数 (002) の格 子面の X線回折ロッキングカーブの半値幅が 200秒以下の結晶性に優れた窒化ガリウム、 窒 化ィンジゥム、 窒化アルミニウムのうちから選ばれた少なくとも 1種以上を主成分とする単結 晶薄膜が直接形成できる。 さらに、 Be〇、 MgO、 CaO、 Sr〇、 B a Oなどのアルカリ 土類金属成分、及び S c203、' Y203、 La2〇3、 Ce〇2、 P r 6011¾ Nd203, Pm2〇3、 Sm2〇3、 Eu203、 Gd2〇3、 Tb4〇7、 Dy2〇3、 Ho2〇3、 Er2〇3、 Tm2〇3、 Yb 2〇3、 L u203などの希土類 素成分のうちから選ばれた少なくとも 1種以上の成分を酸化物 換算で 20. 0モル%以下含窒化ガリウムを主成分とする焼結体を用いたときその上にはミラ —指数 (002) の格子面の X線回折ロッキングカーブの半値幅が 150秒以下の結晶性に優 れた単結晶薄膜が直接形成できる。 また、 Be〇、 Mg〇、 CaO、 S r〇、 Ba〇などのァ ルカリ土類金属成分、 及び Sc203、 Y2〇3、 La2〇3、 Ce〇2、 P r6Oxl, Nd203、 P m2〇3、 Sm203、 Eu203、 Gd2〇3、 Tb407、 Dy203、 Ho2〇3、 Er2Os、 Tm2 03、 Yb203、 Lu203などの希土 素成分のうちから選ばれた少なくとも 1種以上の成分 を酸化物 »で 10. 0モル%以下含窒化ガリゥムを主成分とする焼結体を用いたときその上 にはミラ一指数 (002) の格子面の X線回折ロッキングカーブの半値幅が 130秒以下の結 晶性に優れた単結晶薄膜が直接形成できる。
また、 上記窒化ガリウムを主成分とする焼結体として、 その他ガリウム以外に Mn〇、 Co 0、 NiO、 Fe2〇3、 Cr2〇3、 T i 02、 Mo03、 W03、 Nb2〇5、 Ta205、 V2Os などの遷移金属元素成分のうちから選ばれた少なくとも 1種以上の成分を元素 で 10. 0 モル%以下含有するものを用いた場合でも該焼結体の上にはミラー指数 (002) の格子面の X線回折ロッキングカーブの半値幅が 300秒以下の結晶性に優れた窒化ガリウム、 窒化イン ジゥム、 窒化アルミニウムのうちから選ばれた少なくとも 1種以上を主成分とする単結晶薄膜 が直接形成し得る。 通常上記遷移金属元素成分として Mo、 W、 Nb、 Ta、 V、 及び T iの うちから選ばれた少なくとも 1種以上の成分を元素換算で 10. 0モル%以下含有する窒化ガ リゥムを主成分とする焼結体が好ましく、 このような組成の焼結体を用いることでその上には 窒化ガリウム、 窒化インジウム、 窒化アルミニウムのうちから選ばれた少なくとも 1種以上を 主成分とする結晶性に優れた単結晶薄膜が形成し得る。
また、 上記窒化ガリウムを主成分とする焼結体として、 ガリウム以外に Zn、 Cd、 Be、 Mg、 C、 S i、 Ge、 Se、 T eなどのうちから選ばれた少なくとも 1種以上の成分を含有 するものは比較的高い導電性を有するが得られ易いが、該 Zn、 Cd、 Be、 Mg、 (:、 S i、 Ge、 Se、 Teなどのうちから選ばれた少なくとも 1種以上の成分を元素 で10. 0モ ル%以下含有する窒化ガリゥムを主成分とする焼結体を用いた場合でも該焼結体の上にはミラ 一指数 (002) の格子面の X線回折ロッキングカーブの半値幅が 300秒以下の結晶性に優
れた窒化ガリウム、 窒化インジウム、 窒化アルミニウムのうちから選ばれた少なくとも 1種以 上を主成分とする単結晶薄膜が直接形成し得る。
また、上記窒化ガリウムを主成分とする焼結体として、その他ガリウム以外にアルミニウム、 及びインジウム、 及び酸素のうちから選ばれた少なくとも 1種以上の成分を元素換算で 40. 0モル%以下含有するものを用いた場合でも該焼結体の上にはミラー指数 (002) の格子面 の X線回折ロッキングカーブの半値幅が 300秒以下の結晶性に優れた窒化ガリウム、 窒化ィ ンジゥム、 窒化アルミニウムのうちから選ばれた少なくとも 1種以上を主成分とする単結晶薄 膜が直接形成し得る。
さらに、 上記アルミニウム成分を含有する窒化ガリウムを主成分とする焼結体を用いたとき 該基板に直接形成される窒化ガリウム、 窒化インジウム、 窒化アルミニウムのうちから選ばれ た少なくとも 1種以上を主成分とする単結晶薄膜の結晶性よりも、 同じ組成の窒化ガリゥムを 主成分とする焼結体の上にあらかじめ窒化ガリウム、 窒化インジウム、 窒化アルミニウムのう ちから選ばれた少なくとも 1種以上を主成分とする無定形、 多結晶、 配向性多結晶、 単結晶の うちから選ばれた少なくともいずれかの結晶状態を有する薄膜を形成しさらにその上に窒化ガ リゥム、 窒化ィンジゥム、 窒化アルミニゥムのうちから選ばれた少なくとも 1種以上を主成分 とする単結晶薄膜を形成すれば該単結晶薄膜の結晶性はさらに優れたものとなり得る。 具体的 に言えば、 ガリウム成分を GaN»で 55. 0モル%以上含む窒化ガリウムを主成分とする 焼結体を用いたとき、 その上にあらかじめ窒化ガリウム、 窒化インジウム、 窒化アルミニウム のうちから選ばれた少なくとも 1種以上を主成分とする無定形、 多結晶、 配向性多結晶、 単結 晶のうちから選ばれた少なくともいずれかの結晶状態を有する薄膜を形成しさらにその上に窒 化ガリウム、 窒化インジウム、 窒化アルミニウムのうちから選ばれた少なくとも 1種以上を主 成分とする単結晶薄膜を形成すればミラ一指数 (002) の格子面の X線回折ロッキングカー ブの半値幅として 200秒以下、 通常 150秒以下の結晶性に優れた単結晶薄膜が比較的容易 に形成できる。 また、 Be〇、 MgO、 Ca〇、 S r〇、 B a〇などのアルカリ土類金属成分、 及び Sc
2〇
3、 Y
2〇
3、 La
2〇
3、 Ce0
2、 P r
60
X1^ Nd
2〇
3、 Pm
20
3、 Sm
2〇
3、 E u
20
3、 Gd
20
3、 Tb
40
7、 Dy
2〇
3、 Ho
20
3、 Er
2〇
3、 Tm
2〇
3、 Yb
2〇
3、 Lu
2 〇
3などの希土^素成分のうちから選ばれた少なくとも 1種以上の成分を酸化物換算で 30. 0モル%以下含む窒化ガリゥムを主成分とする焼結体を用いれば、 その上にあらかじめ窒化ガ リゥム、 窒化ィンジゥム、 窒化アルミニゥムのうちから選ばれた少なくとも 1種以上を主成分 とする無定形、 多結晶、 配向性多結晶、 単結晶のうちから選ばれた少なくともいずれかの結晶 状態を有する薄膜を形成しさらにその上に窒化ガリウム、 窒化インジウム、 窒化アルミニウム のうちから選ばれた少なくとも 1種以上を主成分とする単結晶薄膜を形成することによりミラ 一指数 (002) の格子面の X線回折ロッキングカーブの半値幅として 130秒以下の結晶性 に優れた単結晶薄膜が比較的容易に形成できる。 また、 Be〇、 Mg〇、 Ca〇、 S r〇、 B a〇などのアルカリ土類金属成分、 及び Sc
20
3、 Y
20
3、 La
2〇
3、 Ce0
2、 P
Nd2〇3、 Pm203、 Sm203、 Eu203、 Gd2〇3、 Tb407、 Dy2〇3、 Ho203、 E r 203、 Tm203、 Yb2〇3、 Lu203などの希土類 素成分のうちから選ばれた少なくとも 1 種以上の成分を酸化物換算で 20. 0モル%以下含む窒化ガリウムを主成分とする焼結体を用 いたとき、 その上にあらかじめ窒化ガリウム、 窒化インジウム、 窒化アルミニウムのうちから 選ばれた少なくとも 1種以上を主成分とする無定形、 多結晶、 配向性多結晶、 単結晶のうちか ら選ばれた少なくともいずれかの結晶状態を有する薄膜を形成しさらにその上に窒化ガリゥム、 窒化インジウム、 窒化アルミニウムのうちから選ばれた少なくとも 1種以上を主成分とする単 結晶薄膜を形成すればミラー指数 (002) の格子面の X線回折ロッキングカーブの半値幅と して 100秒以下の結晶性に優れた単結晶薄膜が比較的容易に形成し得る。
その際、 上記 Be〇、 MgO、 CaO、 S r 0、 B a Oなどのアルカリ土類金属成分、 及び Sc2〇3、 Y203、 La203、 Ce〇2、 P r ^O^, Nd203、 Pm2〇3、 Sm2〇3、 Eu2 〇3、 Gd2〇3、 Tb407、 Dy203、 Ho203、 Er2〇3、 Tm203、 Yb2〇3、 Lu2Os などの希土類 素成分のうちから選ばれた少なくとも 1種以上の成分を酸化物,で 30. 0 モル%以下含む窒化ガリゥムを主成分とする焼結体にあらかじめ形成する窒化ガリゥム、 窒化 インジウム、 窒化アルミニウムのうちから選ばれた少なくとも 1種以上を主成分とする配向性 多結晶薄膜の結晶性も上記範囲のアルミニウム成分を含まない窒化ガリウムを主成分とする焼 結体を用いたものに比べて向上し易く、 該配向性多結晶薄膜のミラー指数 (002) の格子面 の X線回折ロッキングカーブの半値幅は 9000秒以下のものが比較的容易に形成し得る。 ま た、 BeO、 MgO、 Ca〇、 S r 0、 B a Oなどのアルカリ土類金属成分、 及び Sc 203、 Y203、 La2Os、 Ce〇2、 Pr6Oxl, Nd203、 Pm203、 Sm203、 Eu203、 Gd2 03、 Tb407、 Dy203、 Ho203、 Er203、 Tm2Os、 Yb203、 Lu203などの希土 類 素成分のうちから選ばれた少なくとも 1種以上の成分を酸化物換算で 20. 0モル%以下 含む窒化ガリウムを主成分とする焼結体では、 該焼結体にあらかじめ形成する窒化ガリウム、 窒化インジウム、 窒化アルミニウムのうちから選ばれた少なくとも 1種以上を主成分とする配 向性多結晶薄膜のミラー指数 (002) の格子面の X線回折ロッキングカーブの半値幅として 8000秒以下のものが比較的容易に形成し得る。
また、窒化ガリウムを主成分とする 結体として、ガリウム以外に Mn〇、 CoO、 Ni〇、 Fe203、 Cr2〇3、 T i 02、 Mo03、 W03、 Nb2〇5、 Ta205、 V2〇5などの遷移金 属元素成分のうちから選ばれた少なくとも 1種以上の成分を元素^^で 10. 0モル%以下含 有するものを用いた場合、 その上にあらかじめ窒化ガリウム、 窒化インジウム、 窒化アルミ二 ゥムのうちから選ばれた少なくとも 1種以上を主成分とする無定形、 多結晶、 配向性多結晶、 単結晶のうちから選ばれた少なくともいずれかの結晶状態を有する薄膜を形成しさらにその上 に窒化ガリウム、 窒化インジウム、 窒化アルミニウムのうちから選ばれた少なくとも 1種以上 を主成分とする単結晶薄膜を形成すれば該単結晶薄膜のミラ一指数 (002) の格子面の X線 回折ロッキング力—ブの半値幅として 130秒以下の結晶性に優れたものが比較的容易に形成 し得る。 また、 上記遷移金属元素成分のうちから選ばれた少なくとも 1種以上の成分を元素換 算で 5. 0モル%以下含有するものを用いた場合、 その上にあらかじめ窒化ガリウム、 窒化ィ ンジゥム、 窒化アルミニウムのうちから選ばれた少なくとも 1種以上を主成分とする無定形、 多結晶、 配向性多結晶、 単結晶のうちから選ばれた少なくともいずれかの結晶状態を有する薄 膜を形成しさらにその上に窒化ガリウム、 窒化インジウム、 窒化アルミニウムのうちから選ば れた少なくとも 1種以上を主成分とする単結晶薄膜を形成すれば該単結晶薄膜のミラ一指数 (002) の格子面の X線回折ロッキングカーブの半値幅として 100秒以下の結晶性に優れ たものが比較的容易に形成し得るので好ましい。 通常上記遷移金属元素成分として Mo、 W、 Nb、 Ta、 V、 及び T iのうちから選ばれた少なくとも 1種以上の成分を元素騰で 10. 0モル%以下含有する窒化ガリゥムを主成分とする焼結体が好ましく、 このような組成の焼結 体を用いることでその上には窒化ガリウム、 窒化インジウム、 窒化アルミニウムのうちから選 ばれた少なくとも 1種以上を主成分とする結晶性に優れた単結晶薄膜が形成し得る。
また、 窒化ガリウムを主成分とする焼結体として、 その他ガリウム以外に Zn、 Cd、 C, S i、 Ge、 Se、 Teなどのうちから選ばれた少なくとも 1種以上の成分を元素換算で 10. 0モル%以下含有するものを用いた場合、その上にあらかじめ窒化ガリウム、窒化インジウム、 窒化アルミニウムのうちから選ばれた少なくとも 1種以上を主成分とする無定形、 多結晶、 配 向性多結晶、 単結晶のうちから選ばれた少なくともいずれかの結晶状態を有する薄膜を形成し さらにその上に窒化ガリウム、 窒化インジウム、 窒化アルミニウムのうちから選ばれた少なく
とも 1種以上を主成分とする単結晶薄膜を形成すれば該単結晶薄膜のミラー指数 (002) の 格子面の X線回折ロッキングカーブの半値幅として 130秒以下の結晶性に優れたものが比較 的容易に形成し得る。 また、 上記 Zn、 Cd、 C、 S i、 Ge、 Se、 Teなどのうちから選 ばれた少なくとも 1種以上の成分を元素換算で 5. 0モル%以下含有するものを用いた場合、 その上にあらかじめ窒化ガリウム、 窒化インジウム、 窒化アルミニウムのうちから選ばれた少 なくとも 1種以上を主成分とする無定形、 多結晶、 配向性多結晶、 単結晶のうちから選ばれた 少なくともいずれかの結晶状態を有する薄膜を形成しさらにその上に窒化ガリゥム、 窒化ィン ジゥム、 窒化アルミニウムのうちから選ばれた少なくとも 1種以上を主成分とする単結晶薄膜 を形成すれば該単結晶薄膜のミラー指数 (002) の格子面の X線回折ロッキングカーブの半 値幅として 100秒以下の結晶性に優れたものが比較的容易に形成し得るので好ましい。 また、 窒化ガリゥムを主成分とする焼結体として、 その他ガリゥム以外にアルミニウム、 及 びインジウム、 及ぴ ¾素のうちから選ばれた少なくとも 1種以上の成分を元素 »で 40. 0 モル%以下含有するものを用いた場合、 その上にあらかじめ窒化ガリウム、 窒化インジウム、 窒化アルミニウムのうちから選ばれた少なくとも 1種以上を主成分とする無定形、 多結晶、 配 向性多結晶、 単結晶のうちから選ばれた少なくともいずれかの結晶状態を有する薄膜を形成し さらにその上に窒化ガリウム、 窒化インジウム、 窒化アルミニウムのうちから選ばれた少なく とも 1種以上を主成分とする単結晶薄膜を形成すれば該単結晶薄膜のミラー指数 (002) の 格子面の X線回折ロッキングカーブの半値幅として 130秒以下の結晶性に優れたものが比較 的容易に形成し得る。 また、 上記アルミニウム、 及びインジウム、 及び 素のうちから選ばれ た少なくとも 1種以上の成分を元素換算で 30. 0モル%以下含有するものを用いた場合、 そ の上にあらかじめ窒化ガリウム、 窒化インジウム、 窒化アルミニウムのうちから選ばれた少な くとも 1種以上を主成分とする無定形、 多結晶、 配向性多結晶、 単結晶のうちから選ばれた少 なくともいずれかの結晶状態を有する薄膜を形成しさらにその上に窒化ガリゥム、 窒化ィンジ ゥム、 窒化アルミニウムのうちから選ばれた少なくとも 1種以上を主成分とする単結晶薄膜を 形成すれば該単結晶薄膜のミラー指数 (002) の格子面の X線回折ロッキング力一ブの半値 幅として 100秒以下の結晶性に優れたものが比較的容易に形成し得るので好ましい。
このように窒化ガリゥムを主成分とする魁吉体にあらかじめ窒化ガリゥム、窒化ィンジゥム、 窒化アルミニウムのうちから選ばれた少なくとも 1種以上を主成分とする無定形、 多結晶、 配 向性多結晶、 単結晶のうちから選ばれた少なくともいずれかの結晶状態を有する薄膜を形成す れば、 さらにその上に形成される窒化ガリウム、 窒化インジウム、 窒化アルミニウムのうちか ら選ばれた少なくとも 1種以上を主成分とする単結晶薄膜の結晶性を向上させる効果がある。 その効果は窒化ガリゥムを主成分とする焼結体の組成以外の要素、 例えば表面平滑性などにも 大きく影響されず、 例えば平均表面粗さ Raを 5nm以下にしたものでなくても (すなわち、 焼き放しの表面状態の焼結体、 ラップ研磨した表面状態の焼結体、 ブラスト研磨した表面状態 の焼結体、 表面に機械的な溝切り加工力堀された焼結体、 あるいは鏡面研磨してある焼結体、 など平均表面粗さ R aが 5 nm以上のものであっても) 発揮され得る。
このような単結晶薄膜の結晶性に及ぼす窒化ガリゥムを主成分とする焼結体中のガリゥム以 外の成分のなかでも特に Be〇、 MgO、 CaO、 S rO、 B a Oなどのアルカリ土類金属成 分、及び Sc2〇3、 Y203、 La2Os> Ce〇2、 P r 60X1 Nd203、 Pm2〇3、 Sm203、 Eu203、 Gd203、 Tb407、 Dy2.〇3、 Ho203、 Er2〇3、 Tm203、 Yb203、 Lu 2〇3などの希土 素成分の効果は、例えば聽化ガリウムを主成分とする焼結体中に MnO、 Co〇、 NiO、 Fe203、 Cr203、 T i 02、 Mo03、 W03、 Nb2〇5、 Ta2〇5、 V2 〇5などの遷移金属元素成分、ァリレミニゥム成分、インジウム成分、酸素、及び Zn、 Cd、 C、 S i、 Ge、 Se、 Te、 などアルカリ土類金属成分及び希土 M¾素成分以外の成分が少なく
とも 1種以上含まれていたとしても減じることは少ない。
ガリウム成分を GaN換算で 55. 0モル%以上含む窒化ガリウムを主成分とする焼結体を 用いたとき該焼結体の上に形成される単結晶薄膜がこのような高い結晶性を有するものとなる 原因は必ずしも明確ではないが、 本願発明者は窒化ガリゥムを主成分とする焼結体は窒化ガリ ゥム、 窒化インジウム、 窒化アルミニウム各薄膜と同じウルッ鉱型結晶の結晶構造であるため 窒化ガリウム、 窒化インジウム、 窒化アルミニウムのうちから選ばれた少なくとも 1種以上を 主成分とする薄膜が自発的に単結晶化し易いためと推測している。
窒化ガリゥムを主成分とする焼結体は窒化ガリゥム粒子からなり従って粒界が 在しており、 単結晶や薄膜などのように比較的均質に近い状態ではないにもカゝかわらず通常導電性を有する ものが得られる場合が多い。 I ^化ガリウムを主成分とする 結体が Be、 Mg、 Zn、 Cd、 C、 S i、 Ge、 Se、 Te、 酸素などの成分を実質的に含まないものであっても室温におけ る職率 1 X 108Ω · cm以下の導電性を有するものが得られる場合が多い。 また、 Be、 M g、 Zn、 Cd、 C、 S i、 Ge、 Se、 Te、 酸素のうちから選ばれた少なくとも 1種以上 を含む窒化ガリウムを主成分とする焼結体の導電性は向上し易いので好ましい。 すなわち、 B e、 Mg、 Zn、 Cd、 C、 S i、 Ge、 Se、 Te、 酸素などの成分を実質的に含まない窒 化ガリウムを主成分とする焼結体は室温における抵抗率が必ずしも 1 X 104Ω · cm以下の導 電性を有するとは限らないが Be、 Mg、 Zn、 Cd、 C、 S i、 Ge、 Se、 Te、 酸素の うちから選ばれた少なくとも 1種以上を含む窒化ガリゥムを主成分とする焼結体の導電性は室 温における抵抗率が IX 104Ω■ cm以下に向上し易いので好ましい。 より具体的に言えば、 Be、 Mg、 Zn、 Cd、 C、 S i、 Ge、 Se、 Te、 酸素のうちから選ばれた少なくとも 1種以上を元素購で 10. 0モル%以下含む窒化ガリゥムを主成分とする焼結体の導電性は 向上し例えば室温における 率が少なくとも IX 104Ω · cm以下のものが得られ易い。 ま た、 Be、 Mg、 Zn、 Cd、 C, S i、 Ge、 Se、 Te、 酸素のうちから選ばれた少なく とも 1種以上の成分を元素購で 0. 00001モル%〜 10. 0モル%の範囲含む窒化ガリ ゥムを主成分とする焼結体の導電性は向上し例えば室温における抵抗率が少なくとも 1 X 10 3Ω · cm以下のものが得られ易い。 また、 Be、 Mg、 Zn、 Cd、 C, S i、 Ge、 Se、 T e、 酸素のうちから選ばれた少なくとも 1種以上の成分を元素 で 0. 00001モル% 〜 7. 0モル%の範囲含む窒化ガリゥムを主成分とする焼結体では室温における抵抗率が少な くとも 1 X 10 · cm以下のものが得られ易く該焼結体を導通ビアのない基板として用いる ことが可能となるので好ましい。 また、 Be、 Mg、 Zn、 Cd、 C、 S i、 Ge、 Se、 T e、 酸素のうちから選ばれた少なくとも 1種以上の成分を元素 で 0· 00001モル%〜 5. 0モル%の範囲で含む窒化ガリゥムを主成分とする焼結体では室温における抵抗率が少な くとも 1 X 100Ω · cm以下のものが得られ易く該焼結体を導通ビアのなレ基板として用いる ことカ坷能となるのでより好ましい。 また、 Be、 Mg、 Zn、 Cd、 C, S i、 Ge、 Se、 T e、 酸素のうちから選ばれた少なくとも 1種以上の成分を元素換算で 0. 00001モル% 〜 3 · 0モル%の範囲で含む窒化ガリゥムを主成分とする焼結体では室温における抵抗率が少 なくとも 1 X 10一1 Ω · cm以下のものが得られ易く該焼結体を導通ビアのない基板として用 いることが可能となるのでさらに好ましい。 このような組成の窒化ガリゥムを主成分とする焼 結体において室温における抵抗率が 1 X 10— 2Ω · cm以下あるいはさらに:!〜 2 X 10一3 Ω · cm程度のより低い抵抗率を有するものも得られる。 このような導電性を有する窒化ガリ ゥムを主成分とする焼結体は特に基板の上下表面を電気的に接続するための導通ビアを設ける 必要がないので好ましい。
また、 上記窒化ガリゥムを主成分とする焼結体は C a 0、 S r〇、 B a Oなどのアル力リ土 類金属成分、 及ぴ Sc
20
3、 Y
2〇
3、 La
20
3、 Ce0
2、 P τ
Nd
2O
s、 Pm
20
3、
Sm
20
3、 Eu
2〇
3、 Gd
20
3、 Tb
40
7、 Dy
2〇
3、 Ho
20
3、 Er
20
3、 Tm
2〇
3、 Yb
2〇
3、 Lu
20
3などの希土類 素成分、 MM O, CoO、 N i〇、 Fe
2〇
3、 Cr
2〇
3、 Ti〇
2、 Mo0
3、 WO
3, Nb
20
5、 Ta
2〇
5、 V
2〇
5などの遷移金属元素成分、 及びアル ミニゥム成分、 インジウム成分などのうちから選ばれた少なくとも 1種以上の成分が Be、 M g、 Zn、 Cd、 C、 S i、 Ge、 Se、 Te、 酸素のうちから選ばれた少なくとも 1種以上 の成分以外に含まれていたとしても導電性が損なわれる程度は少ない。 上記窒化ガリゥムを主 成分とする焼結体中に含まれる Be、 Mg、 Zn、 Cd、 C, S i、 Ge、 Se、 Te、 酸素 のうちから選ばれた少なくとも 1種以上の成分以外の成分の含有量は導電性が損なわれる程度 が小さければどのようなものであってもよい。 通常該 Be、 Mg、 Zn、 Cd、 C、 S i、 G e、 S e、 T e、 酸素のうちから選ばれた少なくとも 1種以上の成分以外の成分の含有量とし てアル力リ土類金属成分及び希土類 J£素成分は酸化物換算で 10. 0モル%以下、 遷移金属元 素成分は元素換算で 10. 0モル%以下、 アルミニウム成分及びインジウム成分は元素換算で 40. 0モル%以下であることが導電性が損なわれる程度が小さいので好ましい。
また、導電性を有する窒化ガリウムを主成分とする能結体はガリウム以外の成分として B e、 Mg、 Zn、 Cd、 C、 S i、 Ge、 Se、 Te、 酸素のうちから選ばれた少なくとも 1種以 上の成分だけでなく、 CaO、 SrO、 B a〇などのアルカリ土類金属成分及び S c 203、 Y2 03、 La203、 Ce〇2、 Ρ r 6011¾ Nd203、 Pm2〇3、 Sm2〇3、 Eu2〇3、 Gd2〇3、 Tb4〇7、 Dy2〇3、 Ho203、 Er2〇3、 Tm203、 Yb203、 L u2〇3などの希土^ ¾素 成分のうちから選ばれた少なくとも 1種以上の成分を酸化物換算で 10. 0モル%以下、 ある いは MnO、 Co〇、 Ni〇、 Fe2〇3、 Cr2〇3、 Ti〇2、 Mo03、 W〇3、 Nb2〇5、 T a 2〇 5、 V 2 O 5などの遷移金属元素成分のうちから選ばれた少なくとも 1種以上の成分を元 素換算で 10. 0モル%以下、 あるいは成分アルミニウム成分及びインジウムのうちから選ば れた少なくとも 1種以上の成分を元素騰で 40. 0モル%以下含有するものでも得ることが 可能である。
上記窒化ガリゥムを主成分とする焼結体は C〇や H2などを含む 性雰囲気及び A r、 H e、 N2などを含む非酸化性雰囲気の常圧中、 あるいは減圧中、 あるいはホットプレスや HI Pなど による高圧下で; Wすることにより比較的高い ½¾性を有するものが、作製し得る。すなわち、 窒化ガリゥムを主成分とする焼結体はどのような組成のものであっても通常少なくとも波長 3 60 nm以上の可視光及び^ ί視光より波長の長い光に対して·6¾Ι性を有するものが作製し得 る。 例えば、 窒化ガリウムを主成分とする焼結体はどのような組成のものであっても光 ¾ϋ率 1 %以上のものが作製し得る。 通常ガリゥム成分を G a N換算で 55. 0モル%以上含有する 窒化ガリウムを主成分とする焼結体において光 ¾i§率 1%以上のもの力 S作製し得る。 また、 例 えば添加物を用いず! «し実質的に GaNだけからなる窒化ガリウムを主成分とする焼結体で は光透過率 10%以上のものが作製し得る。 なお、 本発明において窒化ガリウムを主成分とす る焼結体の光 ¾ϋ率は少なくとも波長 200 nm〜800 nmの範囲の光に対してのものであ る。 上記光 率は波長 605 nmの光に対して測定されたものである。 本発明においては今 後特に断らない限り窒化ガリウムを主成分とする焼結体の)1 έ¾ϋ率には上記測定値を用いた。 その中で例えば B e 0、 Mg 0、 C a 0、 S r 0、 B a Oなどのアル力リ土類金属成分及び Sc2〇3、 Y2〇3、 La203、 Ce02、 P r 6Οι Nd2〇3、 Pm2〇3、 Sm203、 Eu2 03、 Gd2〇3、 Tb407、 Dy203、 Ho203、 Er 203、 Tm203、 Yb203、 Lu203 などの希土类 素成分は窒化ガリウムを主成分とする焼結体の)16¾性に有効な作用を及ぼす。 アル力リ土類金属成分及び希土類 素成分は窒化ガリゥムを主成分とする焼結体中にそれぞれ 単独で含まれていてもよいしあるいは同時に含まれていてもよい。 該ァルカリ土類金属成分及 び希土類元素成分のうちから選ばれた少なくとも 1種以上の成分を酸化物換算で 30. 0モ
ル%以下含む窒化ガリゥムを主成分とする焼結体は光透過率 10 %以上のものが作製し得る。 また、 上記アルカリ土類金属成分及び希土 素成分のうちから選ばれた少なくとも 1種以上 の成分を酸化物換算で 20. 0モル%以下含む窒化ガリウムを主成分とする焼結体はさらに光 性が向上し易くなり ¾¾1率 20%以上のものが得られ易い。 また、 アルカリ土類金属成 分及び希土^素成分のうちから選ばれた少なくとも 1種以上の成分を酸化物換算で 10. 0 モル%以下含む窒化ガリゥムを主成分とする焼結体は ½¾1率 30 %以上のものが得られ易い。 また、 アルカリ土類金属成分及び希土類 素成分のうちから選ばれた少なくとも 1種以上の成 分を酸化物^^で 6. 0モル%以下含む窒化ガリウムを主成分とする焼結体は ¾¾率 40% 以上のものが得られ易い。 また、 アルカリ土類金属成分及び希土類 素成分のうちから選ばれ た少なくとも 1種以上の成分を酸化物 で 3. 0モル%以下含む窒化ガリゥムを主成分とす る焼結体は通過率 50%以上のものが得られ易い。 また、 アルカリ土類金属成分及 0¾土類 元素成分のうちから選ばれた少なくとも 1種以上の成分を酸化物 で 0. 0001モル%〜
3. 0モル%以下含む窒化ガリゥムを主成分とする焼結体は^ 率 60 %以上のものが得ら れ易い。 さらに 率 80%以上のものも作製し得る。 本発明においては)16¾¾率が最大 8
6%のものが得られた。
その他、 MnO、 CoO、 NiO、 Fe2〇3、 Cr2〇3、 Ti〇2、 Mo〇3、 W03、 Nb2 〇5、 Ta205、 V2〇5などの遷移金属元素成分のうちから選ばれた少なくとも 1種以上の成分 を元素換算で 10. 0モル%以下含む窒化ガリゥムを主成分とする焼結体では光 ¾ϋ率 10 % 以上のものが作製し得る。 また、 Zn、 Cd、 C、 S i、 Ge、 Se、 Teのうちから選ばれ た少なくとも 1種以上の成分を元素換算で 10. 0モル%以下の範囲 む窒化ガリウムを主 成分とする焼結体では光 ¾率 10%以上のものが作製し得る。 さらに、 アルミニウム及びィ ンジゥム及ぴ 素のうちから選ばれた少なくとも 1種以上の成分を元素騰で 40. 0モル% 以下含む窒化ガリウムを主成分とする焼結体では) ¾¾ 率 10%以上のものが作製し得る。 ま た、 アルミニウム及びインジウム及ぴ 素のうちから選ばれた少なくとも 1種以上の成分を元 素^^で 30. 0モル%以下含む窒化ガリウムを主成分とする焼結体では 率 20%以上 のものが作製し得るので好ましい。
また、 上記アルカリ土類金属成分及び希土観素成分のうちから選ばれた少なくとも 1種以 上の成分、あるいは Mn〇、 CoO、 Ni〇、 Fe2〇3、 Cr 203、 T i〇2、 Mo03、 W〇3、
Nb205、 Ta205、 V205などの遷移金属元素成分のうちから選ばれた少なくとも 1種以上 の成分、 あるいは Zn、 Cd、 C, S i、 Ge> Se、 T eのうちから選ばれた少なくとも 1 種以上の成分、 あるいはアルミニゥム及びィンジゥム及び酸素のうちから選ばれた少なくとも
1種以上の成分、 といつた成分を少なくとも 2種以上同時に含む窒化ガリゥムを主成分とする 焼結体であっても½¾1性のものが作製し得る。 例えば、 BeO、 Mg〇、 Ca〇、 S r 0、
BaOなどのアルカリ土類金属成分及び S c203、 Y2〇3、 La203、 Ce〇2、 P r 6Oxl,
Nd2〇3、 Pm2〇3、 Sm203、 Eu203、 Gd2〇3、 Tb407、 Dy203、 Ho2〇3、 E r
203、 Tm203、 Yb2〇3、 Lu203などの希土 ®¾素成分のうちから選ばれた少なくとも 1 種以上の成分を酸化物 で 30. 0モル%以下含み同時に Mn〇、 CoO、 N i〇、 Fe2〇
3、 Cr2〇3、 Ti〇2、 Mo03、 W〇3、 Nb205、 Ta2〇5、 V205などの遷移金属元素成 分のうちから選ばれた少なくとも 1種以上の成分を元素 で 10. 0モル%以下含む窒化ガ リゥムを主成分とする焼結体、 あるいは上記範囲のアル力リ土類金属成分及 土観素成分 のうちから選ばれた少なくとも 1種以上の成分を含み同時に Zn、 Cd、 C、 S i、 Ge、 S e、 T eのうちから選ばれた少なくとも 1種以上の成分を元素換算で 10. 0モル%以下の範 囲で含む望化ガリウムを主成分とする焼結体、 あるいは上記範囲のアルカリ土類金属成分及び 希土類 素成分のうちから選ばれた少なくとも 1種以上の成分を含み同時にアルミニウム及び
ィンジゥム及び酸素のうちから選ばれた少なくとも 1種以上の成分を元素換算で 40. 0モ ル%以下含む窒化ガリウムを主成分とする焼結体、 であってもそれぞれ 過率 10%以上の ものが作製し得る。
なお、 上記アルカリ土類金属成分及び希土類 素成分のうちから選ばれた少なくとも 1種以 上の成分、あるいは MnO、 CoO、 Ni〇、 Fe2〇3、 Cr2〇3、 Ti〇2、 Mo〇3、 W03、 Nb2〇5、 Ta205、 V205などの遷移金属元素成分のうちから選ばれた少なくとも 1種以上 の成分、 あるいは Zn、 Cd、 C, S i、 Ge、 Se、 T eのうちから選ばれた少なくとも 1 種以上の成分、 あるいはアルミニウム及びインジウム及び酸素のうちから選ばれた少なくとも 1種以上の成分、 といつた成分を少なくとも 2種以上同時に含む窒化ガリゥムを主成分とする 焼結体であっても、 該焼結体に形成される窒化ガリウム、 窒化インジウム、 窒化アルミニウム のうちから選ばれた少なくとも 1種以上を主成分とする単結晶薄膜、 あるいは窒化ガリウム、 窒化インジウム、 窒化アルミニウムのうちから選ばれた少なくとも 1種以上を主成分とする配 向性多結晶薄膜の結晶性は、 上記アル力リ土類金属成分及び希土 素成分のうちから選ばれ た少なくとも 1種以上の成分、 あるいは Mn〇、 CoO、 NiO、 Fe203、 Cr2〇3、 T i
02、 Mo03、 WO 3, Nb205、 Ta205、 V2〇5などの遷移金属元素成分のうちから選ば れた少なくとも 1種以上の成分、 あるいは Zn、 Cd、 C、 S i、 Ge、 Se、 Teのうちか ら選ばれた少なくとも 1種以上の成分、 あるいはアルミニウム及びインジウム及び 素のうち から選ばれた少なくとも 1種以上の成分、 といった成分をそれぞ 独で含む窒化ガリウムを 主成分とする焼結体を用いたものに比べて通常は同じ程度であり、 結晶性が大きく低下するな どの変化は少ない。
また、 Be、 Mg、 Zn、 Cd、 C、 S i、 Ge、 Se、 Te、 酸素のうちから選ばれた少 なくとも 1種以上の成分を含む窒化ガリウムを主成分とする焼結体は導電性を有するだけでな く 1 β®Μ性を有するもの力 s作製し得る。上記 Be、 Mg、 Zn、 Cd、 C, S i、 Ge、 Se、 Te、 酸素のうちから選ばれた少なくとも 1種以上の成分を含む窒化ガリウムを主成分とする 焼結体の光 ¾ϋ率としては 1%以上のものが作製し得る。 上記のように Be、 Mg、 Zn、 C d、 C> S i、 Ge、 Se、 Te、 酸素のうちから選ばれた少なくとも 1種以上の成分を元素 で 10. 0モル%以下含む窒化ガリゥムを主成分とする焼結体は上記のように導電性を有 するだけでなく光 ¾i率 10%以上に向上したものが作製し得る。 また、 Be、 Mg、 Zn、 Cd、 C、 S i、 Ge、 Se、 Te、 酸素のうちから選ばれた少なくとも 1種以上の成分を元 素換算で 0. 00001モル%〜 10. 0モル%の範囲で含む窒化ガリゥムを主成分とする焼 結体は導電性を有するだけでなく耀過率 20%以上のものが作製し得、 さらに光超過率が 3 0 %以上、 40 %以上、 50 %以上、 60 %以上さらに 80 %以上のものも作製し得る。 また、 このような導電性を有しさらに光 性を有する窒化ガリゥムを主成分とする焼結体 において、 Be、 Mg、 Zn、 Cd、 C、 S i、 Ge、 Se、 Te、 酸素のうちから選ばれた 少なくとも 1種以上の成分が含まれているものだけでなく同時に C a 0、 S r 0、 Ba Oなど のアルカリ土類金属成分及び Sc 203、 Y203、 La203、 Ce〇2、 P r60lx, Nd2〇3、 Pm2〇3、 Sm2〇3、 Eu203、 Gd203、 Tb407、 Dy2〇3、 Ho203、 Er 203、 Tm 2〇3、 Yb203、 Lu203などの希土 素成分のうちから選ばれた少なくとも 1種以上の成 分を含むもの、 あるいは Be、 Mg、 Zn、 Cd、 C、 S i、 Ge、 Se、 Te、 酸素のうち から選ばれた少なくとも 1種以上の成分と同時に MnO、 CoO、 NiO、 Fe2〇3、 Cr2〇
3、 Ti02、 Mo03、 WO 3, Nb205、 Ta205、 V2〇5などの遷移金属元素成分のうちか ら選ばれた少なくとも 1種以上の成分を含むもの、 あるいは Be、 Mg、 Zn、 Cd、 C、 S i、 Ge、 Se、 Te、 酸素のうちから選ばれた少なくとも 1種以上の成分と同時にアルミ二 ゥム及びインジウムのうちから選ばれた少なくとも 1種以上の成分を含むものであったとして
も上記導電性あるいは光醒性が減じることは少ない。 導電性を有しさらに ½¾i性を有する 窒化ガリウムを主成分とする焼結体において、 上記の例示した成分をそれぞれ 1種ずつ計 2種 含むものだけでなく、 どちらかの成分を少なくとも 2種以上計 3種以上の成分を含むものであ つても上記導電性あるいは光透過性が減じることは少ない。 本発明において、 例えば上記アル 力リ土類金属成分及び希土類 素成分のうちから選ばれた少なくとも 1種以上の成分及び Z n、 C d、 C、 S i、 G e、 S e、 T eのうちから選ばれた少なくとも 1種以上の成分を同時に含 む窒化ガリウムを主成分とする 結体は室温における抵抗率 1 X 1 0 4 Ω · c m以下の導電性を 有しかつ光 ¾i性を有するものが作製し得るが、 このような組成の窒化ガリゥムを主成分とす る焼結体において室温における抵抗率 1. 7 X 1 0 2 Ω · c mを有し光 ¾i率 8 2 %と高い導 電性と同時に高い光透過率を有するものもが得られた。
なお上記 率とはガラスなどの透明体の直線 ¾i率ではなく窒化アルミ二ゥムを主成分 とする焼結体の光透過率と同様に全 率を意味する。
窒化ガリゥムを主成分とする焼結体が上記のような高い光 ¾i性を有する理由については必 ずしも明確ではないが、 比較的均質で緻密な繊を有するものが容易に作製し得ることが大き な要因であろうと推測される。 さらに上記組成の窒化ガリウムを主成分とする焼結体において より均質で緻密な組織を有するものが作製し得るため光 ¾i性の高いものが得られるものと思 われる。
窒化ガリゥムを主成分とする焼結体は通常窒化ガリゥムを主成分とする粉末を主体とする成 形体を非酸化性雰囲気中 1 0 0 0 〜 1 7 0 0 程度の で«することにより比較的容易 に作製できる。 性を高めるために 常 1 2 0 0°C以上で誠することが好ましい。 上 記の窒化ガリゥムを主成分とする焼結体を作製するために使用する窒化ガリゥムの原料粉末は どのようなものでも使用できるが、 焼結性に優れたものを用いることが光 ¾ 性の窒化ガリウ ムを主成分とする焼結体を作製する上で好ましい。 通常平均粒径 1 0 /zm以下の微粉末であれ ば好適に用いることができ)1 έ¾ 性の窒化ガリウムを主成分とする焼結体が作製し得る。 また、 平均粒径 5. 0 xm以下のものがより好ましく、 平均粒径 2. 0 m以下のものがさらに好ま しい。 また、 平均粒径 1. C m以下のものも用いることができる。 なお、 平均;^径 1 0 m より大きいものであってもポールミルゃジエツトミルなどで粉碎することにより 1 0輝以下 の微粉末とすることにより好適に用いることができる。 このような窒化ガリウムを主成分とす る原料粉末としては、 1 ) 金属ガリウムを窒素やアンモニアなどの窒素含有物質などを用いて 直接窒化反応せしめて作製したもの、 2) 酸化ガリウムをカーボンなどの還元剤と窒素やアン モニァなどの窒餘有物質とを用いて 窒化して作製したもの、 3 ) ガリウム化合物 (例え ばトリメチルガリゥムなどの有機ガリゥム化合物や塩化ガリゥムなどの無機ガリゥム化合物) を気体となして窒素ゃァンモニァなどの窒素含有物質と反応させて (要すれば水素などの還元 ガスを共存させ) 作製した化学輸送法によるもの、 などが好適に用いられる。 また、 その他巿 販のものも用いることができる。 金属ガリゥムを直接窒化して窒化ガリゥム粉末を作製する方 法として、 例えば金属ガリウムは融点が低いので通常アルゴン、 ヘリウムなどの不活性雰囲気 中、 あるいは水素などの ίΜ¾雰囲気中で 3 0 0 °C〜1 7 0 0 °C程度の温度で加熱し金属ガリゥ ムを気化させた後、 該気体となった金属ガリゥムを窒素やアンモニアなどの窒素成分を含むガ スと 3 0 0°C〜1 7 0 程度の で反応させて窒化ガリウム粉末を作製するといつた方法 がある。 酸化ガリウムを^ 5窒化して窒化ガリウム粉末を作製する方法として、 例えば酸化ガ リゥム粉末をカーボン粉末とともに混合し窒素やアンモニアなどの窒素成分を含むガスと 4 0 0 °C〜1 6 0 0 °C程度の? itで加熱して酸化ガリウムの と窒化反応を行ない窒化ガリウム 粉末を作製するといった方法がある。 なお反応物中に残留力一ボンがあれば大気などの酸化雰 囲気中で加熱するなどして! ^する。 ガリゥム化合物を気化させて窒化ガリゥム粉末を作製す
る方法として、 例えば塩化ガリウム、 匕ガリウムあるいはトリメチルガリウムなどのガリゥ ム化合物をアルゴン、 ヘリウム、 窒素などの非酸化性雰囲気中、 あるい «ΤΚ素などの 雰囲 気中で 50 〜 1800°C程度の で加熱し該塩化ガリウム、 匕ガリウムあるいはトリメ チルガリウムなどのガリウム化合物を気化させた後、 気体となった該塩化ガリウム、 匕ガリ ゥムあるいはトリメチルガリゥムなどのガリゥム化合物を窒素やアンモニアなどの窒素成分を 含むガスさらに要すれば水素などの還元ガスを加えた窒素やアンモニアなどの窒素成分を含む ガスと 300°C〜1800 程度の温度で反応させて窒化ガリウム粉末を作製するといつた方 法がある。 このような焼結体作製用の原料として用い得る窒化ガリゥムを主成分とする粉末に は不純物として酸素が含まれる場合があるがこのような不純物酸素を含む原料粉末を用いて作 製される窒化ガリゥムを主成分とする焼結体であっても緻密で光透過性を有するもの、 導電性 を有するものが作製し得る。 通常窒化ガリウム粉末の酸^"有量が 10重量%以下であれば該 粉末を用いて作製される窒化ガリウムを主成分とする焼結体の光透過性あるいは導電性は発現 し得る。 さらに酸齢有量 10重量%以下の窒化ガリウム粉末を用いて作製される窒化ガリウ ムを主成分とする焼結体を用いた場合、 その上には窒化ガリウム、 窒化インジウム、 窒化アル ミニゥムのうちから選ばれた少なくとも 1種以上を主成分とするミラー指数 (002) の格子 面の X線回折ロッキング力一ブの半値幅として 300秒以下の単結晶薄膜が比較的容易に直接 形成し得る。 また該窒化ガリウムを主成分とする焼結体あらかじめ窒化ガリウム、 窒化インジ ゥム、 窒化アルミニウムのうちから選ばれた少なくとも 1種以上を主成分とする無定形、 多結 晶、 配向性多結晶、 単結晶のうちから選ばれた少なくともいずれかの結晶状態を有する薄膜を 形成しさらにその上に窒化ガリウム、 窒化インジウム、 窒化アルミニウムのうちから選ばれた 少なくとも 1種以上を主成分とする単結晶薄膜を形成すれば該単結晶薄膜のミラー指数 ( 00 2) の格子面の X線回折ロッキング力一ブの半値幅として 130秒以下の結晶性に優れたもの が比較的容易に形成し得る。 ·窒化ガリゥム粉末の酸餘有量が 5. 0重量%以下であれば少な くとも 16¾i率 5%以上あるいは室温における抵抗率 1 X 104Ω· cm以下の窒化ガリウムを 主成分とする焼結体を得るので好ましい。
なお、 上記本発明による窒化ガリゥムを主成分とする粉末とは通常ガリゥム成分を G で 55. 0モル%以上含む粉末を意味する。
なお、 上記窒化ガリゥムを主成分とする焼結体に含まれるアル力リ土類金属成分の含有量の :用いる酸化物とは Be 0、 Mg〇、 Ca〇、 S r〇、 BaOを意味し、 希土類 J£素成分 の含有量の騰に用いる酸化物とは S c20 Y203、 La203、 Ce〇2、 P r6Oxl> Nd 203、 Pm203、 Sm203、 Eu2〇3、 Gd203、 Tb4〇7、 Dy2〇3、 Ho203、 E r 20 3、 Tm203、 Yb2〇3、 Lu203を意味する。
本発明において、 上記のような窒化ガリウムなどの導電性を有するセラミック材料を主成分 とする焼結体を用いて発光素子を作製すれば、 基板に導通ビアを形成せずに上下に電極を配し て電極と素子との電気的接続をはかるという形状の発光^?が作製し得るという特徵を有する。 導電性を有するセラミック材料を主成分とする焼結体を用いる場合該焼結体の室温における抵 抗率としては 1 X 104Ω · cm以下であれば上下に電極を配した形状の発光軒が作製し得る。 導電性を有する焼結体の室温における抵抗率としては室温において通常 1 X 102Ω · cm以下 のものであれば少ない損失で十分な電力を供給し得る。 導電性を有する焼結体の室温における 抵抗率としては室温において 1 X 10^ · cm以下のものが好ましく、 1 X 100Ω · cm以 下のものがより好ましく、 1X10-χΩ · cm以下のものがさらに好ましい。
本発明において、 上記のように酸化亜鉛、 酸化ベリリウム、 酸化アルミニウムそれぞれを主 成分とする焼結体を基板とすることで高い結晶性の窒化ガリウム、 窒化インジウム、 窒化アル ミニゥムのうちから選ばれた少なくとも 1種以上を主成分とする単結晶薄膜が作製できる。 し
たがって、 このような単結晶薄膜が形成された基板を用いてその上にあらためて薄膜を形成す ることで発光素子を作製することもできるし、 あるいはこのような高い結晶性を有する薄膜を そのまま発光素子を構成する薄 milの少なくとも一部として使用することにより発光^?を作 製することもできる。 このような酸化亜鉛、 酸化ベリリウム、 酸化アルミニウムそれぞれを主 成分とする焼結体を基板として用いて作製される発光^?は^からのサフアイァ基板を用い て作製される発光素子に比べて発光効率が少なくとも同等かそれ以上のものが提供できるよう になった。
一方、 上記のように酸化碰、 酸化ベリリウム、 酸化アルミニウムそれぞれを主成分とする 焼結体は比較的高い光透過性のものが得られ、 したがってこのような ¾¾i性の酸化菌、 酸 化ベリリウム、 酸化アルミニウムそれぞれを主成分とする焼結体を基板として用いた発光素子 も作製できる。 このような光透過性の酸化 酸化ベリリウム、 酸化アルミニウムそれぞれ を主成分とする焼結体を基板として用いて作製された発光素子はさらに発光効率の優れたもの が得られ易いので^からのサフアイァ基板を用いて作製される発光素子に比べてより発光効 率の優れたものが提供できる。 その理由は必ずしも明確でないが、 基板が «からのサフアイ ァなどの単結晶と異なり微粒子から構成される多結晶質の焼結体であり微粒子の結晶方向があ らゆる方向を向いているため発光素子からの発光は基板と発光素子を構成する薄膜との界面で 反射が減少しそのまま基板内へ透過され易くなり、 基板が光 M 生であるため基板に進入した 光が基板外部へ放出され易くなり発光素子の発光効率が向上し易くなるものと思われる。 また 発光^?を構成する薄膜層と周囲の雰囲気との界面での反射が生じにくくなり発光^?からの 発光が該薄膜層を通して素子外部へ放出され易くなるものと思われる。
なお、 本発明において特に断らない限り上記の炭化珪素、 窒化珪素、 窒化ガリウム、 酸ィ 鉛、 酸化ベリリウムなどの六方晶系及び酸化アルミニウムなどの三方晶系あるいは六方晶系と して分類できる結晶構造を有する各種セラミック材料を主成分とする焼結体の光 ¾ 率の測定 値は窒化アルミニウムを主成分とする焼結体と同様直径 2 5. 4mm厚み 0. 5mmの円盤状 で表面を鏡面に研磨した状態の試料を用い所定の波長の光を上記焼結体試料に当て、 入射した 光の強度と透過した光の強度を分光光度計などで測定しその比を百分率で表わしたものである。 波長としては通常特に断らない限り 6 0 5 nmのものを用いて測定されたものである。 本発明 における)1 έ¾ 率は上記測定用試料を積分球の内部にセットして^ ¾1¾を集めこの ^SIii光 と入射光との強度比を百分率で表した全 ¾i 率として求めたものである。 なお、 光 ¾1率とし て波長 6 0 5 nm以外の光に対するものを測定していなくても波長 6 0 5 nmの光に対しての 光醒率を^ iしていれば本発明による炭化珪素、 窒化珪素、 窒化ガリウム、 酸化亜鉛、 酸化 ベリリゥムなどの六方晶系及び酸化アルミ二ゥムなどの三方晶系あるいは六方晶系として分類 できる結晶構造を有する各種セラミック材料を主成分とする焼結体の性能、 すなわち例えば発 光素子作製用基板として用いたとき作製される発光素子の発光効率を判定し得る。
率は試料の厚みによって変化し本発明による上記炭化珪素、窒化珪素、窒化ガリウム、 酸化亜鉛、 酸化ベリリウムなどの六方晶系及び酸化アルミニウムなどの三方晶系あるいは六方 晶系として分類できる結晶構造を有する各種セラミック材料を主成分とする焼結体を薄膜形成 用基板、 薄膜基板あるいは発光素子作製用基板などとして実際に用いる場合該基板の厚みを薄 くして光腿率を高めることは例えば発光軒の発光効率を高める上で有効である。 通常薄膜 形成用基板、 薄膜基板あるいは発光素子作製用基板などとしては厚み 0. 0 1 mm以上のもの を用いることが り扱い上の強度の点からは好ましい。 又厚みが厚くなると光透過率が低下し 易いので通常薄膜形成用基板、 薄膜基板あるいは発光素子作製用基板などとしては厚み 8. 0 mm以下のものを用いることが好ましい。 本発明において上記炭化珪素、 窒化珪素、 窒化ガリ ゥム、 酸化亜鉛、 酸化ベリリウムなどの六方晶系及び酸化アルミニウムなどの三方晶系あるい
は六方晶系として分類できる結晶構造を有する各種セラミック材料を主成分とする焼結体とし てはその厚みが少なくとも 0. 0 1 mm〜8. 0 mmの範囲において薄膜形成用基板、 薄膜基 板あるいは発光素子作製用などの基板として該焼結体を実際に使用する状態で光透過性を有し ていれば有効である。 すなわち、 上記炭化珪素、 窒化珪素、 窒化ガリウム、 酸化亜鉛、 酸化べ リリウムなどの六方晶系及び酸化アルミニウムなどの三方晶系あるいは六方晶系として分類で きる結晶構造を有する各種セラミック材料を主成分とする焼結体はその厚みが少なくとも 0.
0 l mm〜8. O mmの範囲あるいはそれ以外であっても実際に使用される状態での光透過率 が少なくとも 1 %以上であればよいのであって、 例えば発光素子作製用基板として実際に厚み 0. 1 mmあるいは 2. 0 mmなど厚みが必ずしも 0. 5 mmではないものであっても光透過 性を有し例えば光 ¾1率が少なくとも 1 %以上であれば作製される発光素子の発光効率は向上 し易い。
本発明において、 炭化珪素、 窒化珪素、 窒化ガリウム、 酸化亜鉛、 酸化ベリリウムなどの六 方晶系及び 化アルミ二ゥムなどの三方晶系あるいは六方晶系として分類できる結晶構造を有 する各種セラミック材料を主成分とする焼結体の光 ¾i性は厚みには関係無い。 厚い状態では 光透過性を有しないものであっても薄くすることで光透過性を有するものは本発明に含まれる。 すなわち、 例えば炭化珪素、 窒化珪素、 窒化ガリウム、 酸化亜鉛、 酸化ベリリウムなどの六方 晶系及び 化アルミニウムなどの三方晶系あるいは六方晶系として分類できる結晶構造を有す る各種セラミック材料を主成分とする焼結体の厚みが 0. 5 mmのとき)16¾ϋ性を有しないも のであっても厚みを薄くすることで光透過性が発現するものは本発明に含まれる。 また、 例え ば炭化珪素、 窒化珪素、 窒化ガリウム、 酸化亜鉛、 酸化ベリリウムなどの六方晶系及び 化ァ ルミ二ゥムなどの三方晶系あるいは六方晶系として分類できる結晶構造を有する各種セラミツ ク材料を主成分とする焼結体の厚みが 0. 5 mmより厚いとき) ffii性を有しないものであつ ても厚みを 0. 5 mmとすることで光透過性が発現するものは本発明に含まれる。 光 性を 別の言葉で表現すれば、 本発明の光 ¾i率として炭化珪素、 窒化珪素、 窒化ガリウム、 酸化亜 鉛、 酸化ベリリウムなどの六方晶系及び 化アルミニウムなどの三方晶系あるいは"^晶系と して分類できる結晶構造を有する各種セラミック材料を主成分とする焼結体の厚みには関係無 く、 該焼結体の ¾¾i率が 1 %以上であれば本発明に含まれる。 すなわち、 例えば炭化珪素、 窒化珪素、 窒化ガリウム、 酸化亜鉛、 酸化ベリリウムなどの六方晶系及び ¾化アルミニウムな どの三方晶系あるいは六方晶系として分類できる結晶構造を有する各種セラミック材料を主成 分とする焼結体の厚みが 0. 5 mmのとき光透過率が 1 %より小さいものであっても厚みを薄 くすることで光 ¾1率が 1 %以上であるものは本発明に含まれる。 また、 例えば炭化珪素、 窒 化珪素、 窒化ガリウム、 酸化亜鉛、 酸化ベリリウムなどの六方晶系及び 化アルミニウムなど の三方晶系あるいは六方晶系として分類できる結晶構造を有する各種セラミック材料を主成分 とする焼結体の厚みが 0. 5 mmより厚いとき光 ¾i率が 1 %より小さいものであっても厚み を 0. 5 mmとすることで光透過率が 1 %以上であるものは本発明に含まれる。
上記のように本発明による炭化珪素、 窒化珪素、 窒化ガリウム、 酸化亜鉛、 酸化ベリリウム などの六方晶系及び謝匕アルミニウムなどの三方晶系あるいは六方晶系として分類できる結晶 構造を有する各種セラミツク材料を主成分とする焼結体の光 ¾性としては実際該焼結体が用 いられている状態での ¾¾1性が重要である。したがって炭化珪素、窒化珪素、窒化ガリウム、 酸化碰、 酸化ベリリウムなどの六方晶系及び 化アルミニウムなどの三方晶系あるいは六方 晶系として分類できる結晶構造を有する各種セラミツク材料を主成分とする焼結体として実際 該焼結体が用いられている状態で耀過性を有していれば本発明に含まれる。 別の表現をすれ ば、 本発明の光翻率としては炭化珪素、 窒化珪素、 窒化ガリウム、 酸化亜鉛、 酸化ベリリウ ムなどの六方晶系及び酸化アルミニウムなどの三方晶系あるいは六方晶系として分類できる結
晶構造を有する各種セラミック材料を主成分とする焼結体の厚みには関係無ぐ 該焼結体の実 使用状態での) 率が 1 %以上であれば本発明に含まれる。 すなわち、 例えば炭化珪素、 窒 化珪素、 窒化ガリウム、 酸化亜鉛、 酸化ベリリウムなどの六方晶系及ぴ谢匕アルミニウムなど の三方晶系あるいは六方晶系として分類できる結晶構造を有する各種セラミック材料を主成分 とする焼結体の厚みが実使用状態で 0. 5mm以下あるいは 0. 5mmより大きいとき光 M 率が 1 %以上であるものは本発明に含まれる。
炭化珪素、 窒化珪素、 窒化ガリウム、 酸化 »、 酸化ベリリウムなどの六方晶系及び酸化ァ ルミニゥムなどの三方晶系あるいは六方晶系として分類できる結晶構造を有する各種セラミツ ク材料を主成分とする焼結体の厚みが実使用状態で 0. 5mmより薄い場合あるいは 0. 5 m mより厚い場合は基板厚み 0. 5 mmのとき測定した光 率と異なり、 光透過率は 0. 5 m mより薄い場合は 0. 5 mmのとき測定したより高くなり易く 0. 5 mmより厚い場合は 0. 5 mmのとき測定した光羅率より低くなり易い。 本発明においては上記のように実際に使用 される状態で光透過率が 1 %以上の炭化珪素、 窒化珪素、 窒化ガリウム、 酸化亜鉛、 酸化ベリ リウムなどの六方晶系及び 化アルミニウムなどの三方晶系あるいは六方晶系として分類でき る結晶構造を有する各種セラミック材料を主成分とする焼結体を用いることが好ましい。
なお、 今まで炭化珪素、 窒化珪素、 窒化ガリウム、 酸化亜鉛、 酸化ベリリウム、 酸化アルミ ニゥムなどを主成分とする焼結体は通常主成分である該炭化珪素、 窒化珪素、 窒化ガリウム、 酸化亜鉛、 酸化ベリリウム、 酸化アルミニウムなどとして六方晶あるいは三方晶の結晶構造を 有するものが薄膜形成用基板及び薄膜基板として用いられることを主に例示してきたが上記主 成分が例えば立方晶、 正方晶、 斜方晶、 単斜晶、 三斜晶、 アモルファスなど六方晶あるいは三 方晶以外の結晶構造を有するものであっても炭化珪素、 窒化珪素、 窒化ガリウム、 酸化亜鉛、 酸化ベリリウム、 酸化アルミニウムなどを主成分とするものであれば 膜形成用基板及び 膜 基板として好適に用いることができる。 例えば炭化珪素を主成分とする焼結体などは結晶構造 として例えば立方晶を有するものであっても好適に用いることができる。 また例えば酸化アル ミニゥムを主成分とする焼結体などは結晶構造として例えば立方晶、 スピネル構造の酸化アル ミニゥムを主成分とする焼結体であっても基板として好適に用いることができる。
本発明において、上記酸化アルミニウム、酸化 ¾、酸化ベリリウム、炭化珪素、窒化珪素、 窒化ガリウムを主成分とする焼結体だけでなく、 酸化ジルコニウム、 酸化マグネシウム、 アル ミン酸マグネシウム、 酸化チタン、 チタン酸バリウム、 チタン酸ジルコン酸鉛、 酸化イツトリ ゥムなどの希土類 素酸化物、酸化トリウム、各種フェライト、ムライト、 フオルステライト、 ステアタイト、 結晶化ガラス、 などのセラミック材料を主成分とする焼結体を基板とし、 該基 板にあらかじめ窒化ガリウム、 窒化インジウム、 窒化アルミニウムのうちから選ばれた少なく とも 1種以上を主成分とする単結晶、 無定形、 多結晶、 配向性多結晶など各種結晶状態の薄膜 を形成したものを基板として用いれば、 その上には窒化ガリウム、 窒化インジウム、 窒化アル ミニゥムのうちから選ばれた少なくとも 1種以上を主成分とする単結晶薄膜が形成し得るので、 このような単結晶薄膜が形成された基板を用レゝてその上にあらためて薄膜を形成することで発 光^?を作製することもできるし、 あるいはこのようにして形成された単結晶薄膜をそのまま 発光素子を構成する薄膜層の少なくとも一部として使用することにより発光素子を作製するこ ともできる。
本発明において、 上記のようにあらかじめ窒化ガリウム、 窒化インジウム、 窒化アルミニゥ ムのうちから選ばれた少なくとも 1種以上を主成分とする単結晶、 無定形、 多結晶、 配向性多 結晶など各種結晶状態の薄膜を炭化珪素、 窒化珪素、 窒化ガリウム、 酸化ジルコニウム、 酸化 マグネシウム、 アルミン酸マグネシウム、 酸化チタン、 チタン酸バリウム、 チタン酸ジルコン 酸鉛、酸化イットリウムなどの希土類 素酸化物、謝匕トリウム、各種フェライ卜、ムライト、
フォルステライト、 ステアタイト、 結晶化ガラス、 など各種セラミック材料を主成分とする焼 結体からなる基板に形成し、 その上にさらに窒化ガリウム、 窒化インジウム、 窒化アルミニゥ ムのうちから選ばれた少なくとも 1種以上を主成分とする単結晶薄膜を形成した基板を用いて 作製される発光^?も からのサフアイァ基板を用いて作製される発光素子に比べて発光効 率が少なくとも同等かそれ以上のものが提供できるようになつた。
詳しく説明すれば、 本発明において上記酸化アルミニウム、 酸化亜鉛、 酸化ベリリウム、 炭 化珪素、 窒化珪素、 窒化ガリウムを主成分とする焼結体だけでなぐ 酸化ジルコニウム、 酸化 マグネシウム、 アルミン酸マグネシウム、 酸化チタン、 チタン酸バリウム、 チタン酸ジルコン ,、酸化イットリウムなどの希土 ¾素酸化物、酸ィ匕トリウム、各種フェライ卜、ムライト、 フォルステライト、 ステアタイト、 結晶化ガラス、 など各種セラミック材料を主成分とする焼 結体においても光 性を有するものを得ることが可能である。 具体的には光 ¾i率として少 なくとも 1%以上通常 10%以上を有するものが作製し得る。 また上記酸化ジルコニウム、 酸 化マグネシウム、 アルミン酸マグネシウム、 酸化チタン、 チタン酸バリウム、 チタン酸ジルコ ン醒(特に希土類 素成分を含むもの)、酸化イットリウムなどの希土 素酸化物、酸化ト リウム、 各種フェライト、 ムライト、 フォルステライト、 ステア夕イト、 結晶化ガラス、 など を主成分とする焼結体は ½S 率が 50%以上のものが作製でき、 駄 80%以上のものも作 製し得る。 このような光 ¾性の各種セラミック材料を主成分とする焼結体を発光^?作製用 基板に用いれば、 作製される発光素子の発光効率は^からのサファイアなどを基板として用 いて作製される発光軒と比べて向上し易い。 その理由は必ずしも明確でないが、 基板が ¾έ¾ からのサファイアなどと異なり焼結体であるため発光素子からの発光は基板と発光素子を構成 する薄膜との界面で反射が減少しそのまま基板内へ ¾され易くなり、 基板が 性である ため基板に進入した光が基¾ ^部へ放出され易くなるため発光素子の発光効率が向上し易くな るものと思われる。 また発光素子を構成する薄膜層からも周囲の雰囲気との界面での反射が生 じにくくなり発光^?からの発光ヵ簿 JMを通して^?外部へ放出され易くなるものと思われ る。 上記各種セラミック材料を主成分とする焼結体のうちで酸化ジルコニウム、 酸化マグネシ ゥム、 アルミン酸マグネシウム、 酸化イットリウムなどの希土 素酸化物、 酸化トリウム、 ムライト、 結晶化ガラスを主成分とする焼結体は特に 性に優れ、 纖焼結助剤を添加し て常圧焼成 (例えば大気中、 あるいは H
2などの還元性ガス中、 あるいは N
2などの非酸化性ガ ス中、 あるいは C〇
2などの弱酸化性ガス中)、 減圧焼成、 ホットプレスなどの定法により比較 的容易に光透過性のものを作製することができる。 大気中での常圧焼成であっても光 率 1 0 %以上、 通常光透過率 20 %以上あるいは光透過率 30 %以上のものを作製することができ る。 また水素中での焼成あるいはホットプレスあるいは減圧焼成などによって光透過率 40 % 以上、 通常は光透過率 50 %以上あるいは光透過率 60 %以上のものを作製することができ、 光透過率 80%以上のものも作製できる。 光透過性を向上させるために焼結助剤としては例え ば谶化ジルコニウムの場合は S c
2〇
3、 Y
20
3、 La
2〇
3、 Ce〇
2、 Pr
6〇
1]L、 Nd
2〇
3、 Pm
20
3、 Sm
2〇
3、 Eu
2〇
3、 Gd
20
3、 Tb
40
7、 Dy
2〇
3、 Ho
2〇
3、 Er
2〇
3、 Tm
20
3、 Yb
20
3、 L u
20
3など希土類 素成分を含む酸化物などの化合物あるいは Be〇、 M g〇、 CaO、 S rO、 B a Oなどアルカリ土類金属成分を含む酸化物などの化合物、 などを 好適に用いることができる。 また、 酸化マグネシウムの場合は Sc
20
3、 Y
20
3、 La
2O
s、 Ce0
2、 P r
60
11¾ Nd
20
3、 Pm
20
3、 Sm
20
3、 Eu
20
3、 Gd
2〇
3、 Tb
4〇
7、 Dy
2〇
3、 Ho
20
3、 Er
20
3、 Tm
20
3、 Yb
2O
s> Lu
20
3など希土阮素成分を含む酸化物 などの化合物あるいは B e 0、 C a 0、 S r 0、 B a Oなどァレ力リ土類金属成分を含む酸ィ匕 物などの化合物あるいは L i F、 N a Fなどアルカリ金属成分を含む弗化物などの化合物ある いは S i 0
2などの珪素化合物、 などを赚に用いることができる。 また、 アルミン酸マグネシ
ゥムの場合は Sc
2〇
3、 Y
20
3、 La
20
3、 Ce〇
2、 P r
60
1X Nd
2〇
3、 Pm
2〇
3、 Sm
2〇
3、 Eu
2〇
3、 Gd
20
3、 Tb
40
7、 Dy
20
3、 Ho
2〇
3、 Er
2〇
3、 Tm
20
3、 Yb
20
3、 Lu
2〇
3など希土类阮素成分を含む酸化物などの化合物あるいは Be 0、 MgO、 CaO、 S rO、 B a〇などアルカリ土類金属成分を含む酸化物などの化合物あるいは S i 0
2などの珪 素ィ匕合物、 などを好適に用いることができる。 また、 酸化イットリウムなどの希土類 J£素酸化 物の場合は A 1
20
3などアルミニウム成分を含む酸化物などの化合物あるいは S c
2〇
3、 Y
2 〇ゥ、 La
20
3、 Ce〇
2、 Pr
60
1±, Nd
20
3、 Pm
20
3、 Sm
2〇
3、 Eu
2〇
3、 Gd
20
3、 Tb
40
7、 Dy
20
3、 Ho
20
3、 Er
20
3、 Tm
2〇
3、 Yb
2〇
3、 L u
2〇
3などの中から選ば れた少なくとも 1種以上の主成分と異なる希土 素成分を含む酸化物などの化合物あるいは B e〇、 Mg〇、 C a〇、 S r〇、 B a Oなどァリレ力リ土類金属成分を含む酸化物などの化合 物、 などを好適に用いることができる。 また、酸化トリウムの場合は Sc
20
3、 Y
20
3、 La
2 0
3、 Ce〇
2、 Pr
6On、 Nd
20
3、 Pm
20
3、 Sm
2〇
3、 Eu
2〇
3、 Gd
20
3、 Tb
4〇
7、 Dy
2〇
3、 Ho
2〇
3、 Er
2〇
3、 Tm
2〇
3、 Yb
2〇
3、 L u
20
3など希土類 素成分を含む酸 化物などの化合物あるいは B e〇、 MgO、 CaO、 S r〇、 B a Oなどアルカリ土類金属成 分を含む酸化物などの化合物、 などを好適に用いることができる。 また、 ムライトの:^は S c
2〇
3、 Y
20
3、 La
2〇
3、 Ce〇
2、 P r
Nd
2〇
3、 Pm
2〇
3、 Sm
20
3、 Eu
20
3、 Gd
20
3、 Tb
4〇
7、 Dy
2〇
3、 Ho
20
3、 Er
2〇
3、 Tm
2〇
3、 Yb
2〇
3、 Lu
2〇
3な ど希土 ¾素成分を含む酸化物などの化合物あるいは Be 0、 Mg〇、 CaO、 S rO、 Ba Oなどアルカリ土類金属成分を含む酸化物などの化合物あるいは S 1〇
2などの珪素化合物、な どを好適に用いることが きる。 また、 結晶化ガラスの場合は S c
20
3、 Y
2〇
3、 La
20
3、 Ce〇
2、 Pr
60
1]L、 Nd
2〇
3、 Pm
2〇
3、 Sm
2〇
3、 Eu
2〇
3、 Gd
2〇
3、 Tb
4〇
7、 Dy
20
3、 Ho
20
3、 Er
20
3、 Tm
2〇
3、 Yb
20
3、 L u
20
3など希土類 素成分を含む酸化物 などの化合物あるいは Be〇、 MgO、 Ca〇、 S r〇、 B a〇などアルカリ土類金属成分を 含む酸化物などの化合物あるいは S iO ょどの珪素化合物、などを好適に用いることができる。 また、 これら酸化ジルコニウム、 酸化マグネシウム、 ァレミン酸マグネシウム、 酸化イット リウムなどの希土^素酸化物、 酸化トリウム、 ムライト、 結晶化ガラスを主成分とする焼結 体にはそれぞれ上記例示した成分以外に例えばモリブデン、 タングステン、 バナジウム、 ニォ ブ、 タンタル、 チタン、 鉄、 ニッケル、 クロム、 マンガン、 ジルコニウム、 ハフニウム、 コバ ルト、 銅、 などの遷移金属成分、 あるいはカーボンなどの成分を含むものも好適に用いる ことができ、 これらの成分を含むものは黒色、 灰黒色、 灰色、 褐色、 黄色、 緑色、 青色、 あず き色、 赤色などに呈色したものが得られ易ぐ 呈色したものであっても^ ffi 性を有するもの が、得られる。
なお、 本発明において上記各種セラミック材料を主成分とする焼結体の耀過率は少なくと も波長 200 nm〜800 nmの範囲の光に対してのものである。 上記光 ¾i 率は波長 605 n mの光に対して測定されたものである。 本発明においては今後特に断らない限り各種セラミ ック材料を主成分とする焼結体の光 率には上記測定値を用いた。
このような光 ¾i性を有する各種セラミック材料を主成分とする焼結体を基板とし、 該基板 にあらかじめ窒化ガリウム、 窒化インジウム、 窒化アルミニウムのうちから選ばれた少なくと も 1種以上を主成分とする単結晶、 無定形、 多結晶、 配向性多結晶など各種結晶状態の薄膜を 形成したものを基板として用いれば、 その上には窒化ガリウム、 窒化インジウム、 窒化アルミ ニゥムのうちから選ばれた少なくとも 1種以上を主成分とする単結晶薄膜が形成し得るので、 このような単結晶薄膜が形成された基板を用いてその上にあらためて薄膜を形成することで発 光素子を作製することもできるし、 あるいはこのようにして形成された単結晶薄膜の少なくと も一部を発光素子を構成する薄11の少なくとも一部として使用することにより発光素子を作
製することもできる。
本発明において、 上記酸化ジルコニウム、 酸化マグネシウム、 アルミン酸マグネシウム、 酸 化チタン、 チタン酸バリウム、 チタン酸ジルコン酸鉛、 酸化イットリウムなどの希土 素酸 化物、 酸化トリウム、 各種フェライト、 ムライト、 フォルステライト、 ステアタイト、 結晶化 ガラス、 などそれぞれを主成分とする焼結体のうち光透過性を有するものを基板として用いて 作製される発光素子は発光効率の優れたものが得られ易いので^からのサフアイァ基板を用 いて作製される発光素子に比べて発光効率が少なくとも同等か、 最大 2〜3倍以上に向上した ものが作製できるようになった。
なお、 本発明において特に断らない限り上記の酸化ジルコニウム、 酸化マグネシウム、 アル ミン酸マグネシウム、 酸化チタン、 チタン酸バリウム、 チタン酸ジルコン酸鉛、 酸化イツトリ ゥムなどの希土類 素酸化物、酸化トリウム、各種フェライト、ムライト、 フォルステライト、 ステア夕イト、 結晶化ガラス、 など各種セラミック材料を主成分とする焼結体の光透過率の測 定値は窒化アルミニウムを主成分とする焼結体と同様直径 2 5. 4mm厚み 0. 5 mmの円盤 状で表面を鏡面に研磨した状態の試料を用い所定の波長の光を上記焼結体試料に当て、 λ し た光の強度と透過した光の強度を分光光度計などで測定しその比を百分率で表わしたものであ る。 波長としては通常特に断らない限り 6 0 5 nmのものを用いて測定されたものである。 本 発明における光 ¾i 率は上記測定用試料を積分球の内部にセットして^ ¾ ¾を集めこの^! 過光と入射光との強度比を百分率で表した全 ¾i率として求めたものである。 なお、 y として波長 6 0 5 nm以外の光に対するものを測定していなくても波長 6 0 5 nmの光に対し ての) ¾¾ 率を iffl していれば本発明による酸化ジルコニウム、 酸化マグネシウム、 アルミン 酸マグネシウム、 酸化チタン、 チタン酸バリウム、 チタン酸ジルコン麵、 酸化イットリウム などの希土類 J5素酸化物、 酸化トリウム、 各種フェライト、 ムライト、 フオルステライト、 ス テア夕イト、 結晶化ガラス、 など各種セラミック材料を主成分とする焼結体の性能、 すなわち 例えば発光素子作製用基板として用いたとき作製される発光素子の発光効率を判定し得る。 光翻率は試料の厚みによって変化し本発明による上記酸化ジルコニウム、 酸化マグネシゥ ム、 アルミン酸マグネシウム、 酸化チタン、 チタン酸バリウム、 チタン酸ジルコン 、 酸化 イットリウムなどの希土^ ¾素酸化物、 酸化トリウム、 各種フェライト、 ムライト、 フォルス テライト、 ステアタイト、 結晶化ガラス、 など各種セラミック材料を主成分とする焼結体を薄 膜形成用基板、 薄膜基板あるいは発光^?作製用基板などとして実際に用いる場合該基板の厚 みを薄くして光 ¾ 率を高めることは例えば発光素子の発光効率を高める上で有効である。 通 常薄膜形成用基板、 薄膜基板あるいは発光素子作製用などの基板としては厚み 0. 0 1 mm以 上のものを用いることが取り扱い上の強度の点からは好ましい。 又厚みが厚くなると½¾1率 が低下し易いので通常薄膜形成用基板、 薄膜基板あるいは発光素子作製用などの基板としては 厚み 8. 0mm以下のものを用いることが好ましい。 本発明において上記酸ィ匕ジルコニウム、 酸化マグネシウム、 アルミン酸マグネシウム、 酸化チタン、 チタン酸バリウム、 チタン酸ジル コン ,、 酸ィ匕イットリウムなどの希土 ¾素酸ィ匕物、 酸ィ匕トリウム、 各種フェライト、 ムラ イト、 フォルステライト、 ステアタイト、 結晶化ガラス、 など各種セラミック材料を主成分と する焼結体としてはその厚みが少なくとも 0. 0 1 mm〜 8. 0 mmの範囲において薄膜形成 用基板、 薄膜基板あるいは発光素子作製用などの基板として該焼結体を実際に使用する状態で 光進性を有していれば有効である。 すなわち、 上記酸化ジルコニウム、 酸化マグネシウム、 ァレミン酸マグネシウム、 酸化チタン、 チタン酸バリウム、 チタン酸ジルコン,、 酸化イツ トリウムなどの希土类 5素酸化物、 酸ィ匕トリウム、 各種フェライト、 ムライト、 フォルステラ イト、 ステアタイト、 結晶化ガラス、 など各種セラミック材料を主成分とする焼結体はその厚 みが少なくとも 0. 0 1 mm〜8. 0 mmの範囲あるいはそれ以外であっても実際に使用され
る状態での光透過率が少なくとも 1 %以上であればよいのであって、 例えば発光素子作製用基 板として実際に厚み 0. 1 mmあるいは 2. 0 mmなど厚みが必ずしも 0. 5mmではないも のであっても光 ¾ 性を有し例えば光透過率が少なくとも 1 %以上であれば作製される発光素 子の発光効率は向上し易い。
本発明において、 酸化ジルコニウム、 酸化マグネシウム、 アルミン酸マグネシウム、 酸化チ タン、チタン酸バリウム、チタン酸ジルコン難、酸化イツトリウムなどの希土誕素酸化物、 酸化トリウム、各種フェライ卜、ムライ卜、 フオルステライ Kステアタイ卜、結晶化ガラス、 など各種セラミック材料を主成分とする焼結体の光透過性は該焼結体の厚みには関係無い。 厚 い状態では光 性を有しないものであっても薄くすることで)1 ά¾ϋ性を有するものは本発明 に含まれる。 すなわち、 例えば 化ジルコニウム、 酸化マグネシウム、 アルミン酸マグネシゥ ム、 酸化チタン、 チタン酸バリゥム、 チタン酸ジルコン酸鉛、 酸化ィットリゥムなどの希土類 元素酸化物、 酸ィ匕トリウム、 各種フェライト、 ムライト、 フォルステライト、 ステアタイト、 結晶化ガラス、 など各種セラミック材料を主成分とする焼結体の厚みが 0. 5mmのとき)^ 過性を有しないものであっても厚みを薄くすることで光 性が発現するものは本発明に含ま れる。 また、 例えば" m化ジルコニウム、 酸化マグネシウム、 アルミン酸マグネシウム、 酸化チ タン、チタン酸バリウム、チタン酸ジルコン膽、酸化イットリウムなどの希土麵素酸化物、 酸化トリウム、各種フェライト、ムライト、 フォルステライト、ステア夕イト、結晶化ガラス、 など各種セラミック材料を主成分とする焼結体の厚みが 0. 5mmより厚いとき光透過性を有 しないものであつても厚みを 0. 5 mmとすることで光 性が発現するものは本発明に含ま れる。 光醒性を別の言葉で表現すれば、 本発明の光 率として酸化ジルコニウム、 酸化マ グネシゥム、 アルミン酸マグネシウム、 酸化チタン、 チタン酸バリウム、 チタン酸ジルコン酸 鉛、 酸化イットリウムなどの希土 素酸化物、 酸化トリウム、 各種フェライト、 ムライト、 フォルステライト、 ステアタイト、 結晶化ガラス、 など各種セラミック材料を主成分とする焼 結体の厚みには関係無ぐ 該焼結体の) 率が 1 %以上であれば本発明に含まれる。 すなわ ち、 例えば 化ジルコニウム、 酸化マグネシウム、 アルミン酸マグネシウム、 酸化チタン、 チ タン酸バリウム、 チタン酸ジルコン酸鉛、 酸化イットリウムなどの希土 素酸化物、 酸化ト リウム、 各種フェライト、 ムライト、 フォ Jレステライト、 ステアタイト、 結晶化ガラス、 など 各種セラミック材料を主成分とする焼結体の厚みが 0. 5 mmのとき光¾¾率が 1 %より小さ いものであっても厚みを薄くすることで光 ¾ 率が 1 %以上であるものは本発明に含まれる。 また、 例えば 化ジルコニウム、 酸化マグネシウム、 アルミン酸マグネシウム、 酸化チタン、 チタン酸バリウム、 チタン酸ジルコン赚、 酸化イットリウムなどの希土類 素酸化物、 酸化 トリウム、 各種フェライト、 ムライト、 フォ Jレステライト、 ステア夕イト、 結晶化ガラス、 な ど各種セラミツク材料を主成分とする焼結体の厚みが 0. 5 mmより厚いとき光 率が 1 % より小さいものであっても厚みを 0. 5 mmとすることで光透過率が 1 %以上であるものは本 発明に含まれる。
上記のように本発明による酸化ジルコニウム、酸化マグネシウム、アルミン酸マグネシウム、 酸化チタン、 チタン酸バリウム、 チタン酸ジルコン酸鉛、 酸化イットリウムなどの希土類元素 酸化物、 酸化トリウム、 各種フェライト、 ムライト、 フォルステライト、 ステアタイト、 結晶 化ガラス、 など各種セラミック材料を主成分とする焼結体としては実際該焼結体が用いられて いる状態での光 ¾ϋ性が重要である。 したがって酸化ジルコニウム、 酸化マグネシウム、 アル ミン酸マグネシウム、 酸化チタン、 チタン酸バリウム、 チタン酸ジルコン酸鉛、 酸化イツトリ ゥムなどの希土! ^素酸化物、酸化トリウム、各種フェライト、ムライト、 フォルステラィト、 ステアタイト、 結晶化ガラス、 など各種セラミック材料を主成分とする焼結体として実際該焼 結体が用いられている状態で光 ¾1性を有していれば本発明に含まれる。 別の表現をすれば、
本発明の) 率としては酸化ジルコニウム、 酸化マグネシウム、 アルミン酸マグネシウム、 酸化チタン、 チタン酸バリゥム、 チタン酸ジルコン酸鉛、 酸化ィットリゥムなどの希土類 素 酸化物、 酸化トリウム、 各種フェライト、 ムライト、 フォルステライト、 ステアタイト、 結晶 化ガラス、 など各種セラミック材料を主成分とする焼結体の厚みには関係無ぐ 該焼結体の実 使用状態での光 ¾i率が 1 %以上であれば本発明に含まれる。 すなわち、 例えば 化ジルコ二 ゥム、 酸化マグネシウム、 アルミン酸マグネシウム、 酸化チタン、 チタン酸バリウム、 チタン 酸ジルコン職、酸化イットリウムなどの希土類元素酸化物、酸化トリウム、各種フェライト、 ムライト、 フォルステライト、 ステア夕イト、 結晶化ガラス、 など各種セラミック材料を主成 分とする焼結体の厚みが実使用状態で 0. 5mm以下あるいは 0. 5 mmより大きいとき光透 過率が 1 %以上であるものは本発明に含まれる。
酸化ジルコニウム、 酸化マグネシウム、 アルミン酸マグネシウム、 酸化チタン、 チタン酸バ リウム、 チタン酸ジルコン難、 酸化イットリウムなどの希土類 素酸化物、 酸化トリウム、 各種フェライト、 ムライト、 フォルステラィト、 ステアタイト、 結晶化ガラス、 など各種セラ ミック材料を主成分とする焼結体の厚みが実使用状態で 0. 5 mmより薄い場合あるいは 0. 5 mmより厚い場合は基板厚み 0. 5mmのとき測定した光透過率と異なり、 光 率は 0. 5 mmより薄い場合は 0 · 5 mmのとき測定したより高くなり易く 0. 5 mmより厚い場合は 0. 5mmのとき測定した光 ¾i率より低くなり易い。 本発明においては上記実際に使用され る状態で 率が少なくとも 1 %以上の酸化ジルコニウム、 酸化マグネシウム、 アルミン酸 マグネシウム、 酸化チタン、 チタン酸バリゥム、 チタン酸ジルコン酸鉛、 酸化ィットリゥムな どの希土類 素酸化物、 酸匕トリウム、 各種フェライト、 ムライト、 フォルステライト、 ステ ァタイト、 結晶化ガラス、 など各種セラミック材料を主成分とする焼結体を用いることが好ま しい。
また、 本発明において窒化アルミニウムを主成分とする焼結体に窒化ガリウム、 窒化インジ ゥム、 窒化アルミニウムのうちから選ばれた少なくとも 1種以上を主成分とする薄膜による光 導波路が形成された薄膜基板を提供することができる。 本発明による光導波路が形成された薄 膜基板を用いることで例えば波長 2 0 0 nm〜7 0 0 0 nmの範囲といった紫外線領域から赤 外線領域の幅広い波長領域の光伝送に対応できる薄膜基板が提供できる。 特に 2 0 0 ηπ!〜 3 8 O nmの範囲の紫外光を大きな損失を伴うことなく伝送することが可能となった。 光導波路 として用いる窒化ガリウム、 窒化インジウム、 窒化アルミニウムのうちから選ばれたいずれか 少なくとも 1種以上を主成分とする薄膜が単結晶であれば光の伝 員失をより低減化すること ができる。 この光伝送性は窒化ガリウム、 窒化インジウム、 窒化アルミニウムのうちから選ば れた少なくとも 1種以上を主成分とする薄膜が高い光透過性を有することにより実現できる。 波長の短い特に 2 0 0 nm~ 3 8 0 nmの範囲の紫外光の伝送は窒化アルミニウムの含有量の 多い薄膜を用いることで実現できる。 このような光伝送性は窒化アルミニウムを主成分とする 焼結体に光導波路となる窒化ガリウム、 窒化インジウム、 窒化アルミニウムのうちから選ばれ た少なくとも 1種以上を主成分とする薄膜が単結晶として形成し得るということにも起因する。 さらにこのような光伝送性は光導波路となる窒化ガリウム、 窒化インジウム、 窒化アルミニゥ ムのうちから選ばれた少なくとも 1種以上を主成分とする薄膜と窒化アルミニウムを主成分と する焼結体との良好な接合性にも起因する。 前記のように窒化ガリウム、 窒化インジウム、 窒 化アルミニウムのうちから選ばれた少なくとも 1種以上を主成分とする薄膜と窒化アルミニゥ ムを主成分とする焼結体との間の接合性について接合後の薄膜にはクラックは見られず、 接合 界面には剥離が見られず、 粘着テープによる引き剥がしテストなどを行っても接合界面での剥 離が生じない。 さらに、 本発明において窒化アルミニウムを主成分とする焼結体には窒ィ匕ガリ ゥム、 窒化インジウム、 窒化アルミニウムのうちから選ばれた少なくとも 1種以上を主成分と
する単結晶薄膜が形成できるということによる。 本発明は窒化ガリウム、 窒化インジウム、 窒 化アルミニウムのうちから選ばれた少なくとも 1種以上を主成分とする薄膜により光導波路が 形成された薄膜基板を含むが、 基板を構成する材料に窒化アルミニウムを主成分とする焼結体 を用いており放熱性に優れるので半導体レーザーなど高出力の発光素子を搭載する上で好まし い。
また、 該窒化アルミニウムを主成分とする焼結体には上記光導波路だけでなくその内部及び
Z又は表面に電気回路を形成することができるので、 上記光導波路及び電気回路とを有する光 配 us板として用いることができるという特徴がある。 すなわち、 本発明により今 m きく応 用が広がると予測される窒化ガリウム、 窒化インジウム、 窒化アルミニウムのうちから選ばれ た少なくとも 1種以上を主成分とする半導体レーザーダイオードあるいは発光ダイオードなど の青色及び紫外光発光素子からの光を伝送可能な薄膜基板が提供できる。 また、 本発明は上記 青色及び紫外光発光素チを直接搭載し光配^ S板として機能する薄膜基板を提供できるという 特徴がある。
窒化アルミニウムを主成分とする焼結体に形成された窒化ガリウム、 窒化インジウム、 窒化 アルミニウムのうちから選ばれた少なくとも 1種以上を主成分とする薄膜による光導波路とし て単結晶、 無定形、 多結晶、 配向性多結晶のうちから選ばれた少なくともいずれかの結晶状態 を有するものを用いることができる。 このような結晶状態の薄膜を用いることで例えば波長 6 5 0 nmの光を伝送したとき伝送損失が通常少なくとも 1 0 d B/ c m以下の光導波路が形成 できる。 その中でも単結晶薄膜を用いることで伝送損失の低減化をはかること力河能となり通 常少なくとも 5 d BZc m以下の光導麵を形成することが可能となる。 窒化ガリウム、 窒化 ィンジゥム、 窒化アルミニウムのうちから選ばれた少なくとも 1種以上を主成分とする単結晶 薄膜のミラー指数 (0 0 2) の格子面からの X線回折ロッキングカーブの半値幅が 1 0 0秒以 下のものでは少なくとも 3 d Bズ c m以下の光導波路を形成することが可能となる。
本発明による光導波路を用いて伝送可能な光の波長は窒化ガリウム、 窒化インジウム、 窒化 アルミニウムのうちから選ばれた少なくとも 1種以上を主成分とする薄膜の組成に依存する。 波長 2 0 0 nm〜3 8 0 nmの範囲の紫外光及び波長 3 8 0 nm以上の光に対しては窒化ガリ ゥム及び窒化アルミニウムのうちから選ばれた少なくとも 1種以上を主成分とする薄膜を光導 波路として用いることが好ましい。 より波長の短い紫外光を ¾ する場合窒化アルミ二ゥム単 独か窒化アルミニウムの含有量の多い組成の薄膜を用いることが好ましい。 このような組成の 薄膜を用いることで波長の短い紫外光をより低損失で伝送することができるようになる。 波長 3 8 0 n m〜 6 5 0 nmの可視光に対しては上記組成の薄膜の他に窒化ガリウム、 窒化インジ ゥム、 窒化アルミニウムのうちから選ばれた少なくとも 1種以上を主成分とする薄膜を光導波 路として用いることができる。 より波長の短い可視光を ¾iする場合窒化アルミニウム単独か 窒化アルミニウムの含有量の多い組成の薄膜あるいは窒化ガリゥム単独力、窒化ガリゥムの含有 量の多い組成の薄膜を用いることが好ましい。 このような組成の薄膜を用いることで波長の短 い可視光をより低損失で伝送することができるようになる。 また、 少なくとも波長 6 5 0 nm 以上の光に対しては窒化ガリウム、 窒化インジウム、 窒化アルミニウムのあらゆる組み合わせ の組成の薄膜を光導波路として用いることができる。
本発明において紫外光を伝送するための光導波路としては上記のように窒化ガリウム及び窒 化アルミニウムのう.ちから選ばれた少なくとも 1種以上を主成分とする薄膜を用いることが好 ましい。 より具体的にいえば紫外光を伝送するための光導波路として A 1 XG a ( 0. 0 ≤x≤l . 0) の化学式であらわされる組成物を主成分とする薄膜を用いることが好ましい。 これらの材料を光導波路として用いることで波長 2 0 0 nmの紫外線まで伝送することが^ [能 となる。 上記窒化ガリウム及び窒化アルミニウムのうちから選ばれた少なくとも 1種以上を主
成分とする薄膜により形成された光導波路は紫外光だけでなく波長 38 Onm以上の可視光及 び波長 80 Onm以上の赤外光も低損失で伝送することができる。 より波長の短い紫外光の伝 纖失を少なくする上では窒化アルミニウム成分を多く含む薄膜を光導波路として用いること がより好ましい。すなわち上記の化学式において波長 380 nm以下の光を伝送する上では 0· 0≤χ≤1. 0の範囲の組成を有する薄膜を用いることが好ましく波長 38 Onmの光を用い たとき伝送損失 1 OdB/cm以下の光導波路が形成できる。 上記組成範囲の薄膜として単結 晶を用いることにより伝送損失 5 dB, cm以下の光導波路が形成できる。 該単結晶薄膜のミ ラー指数 (002) の格子面の X線回折ロッキングカーブの半値幅が 100秒以下のものでは 少なくとも 3 dB/cm以下の光導波路を形成することが可能となる。
また、 波長 300 nm以下の光を伝送する上では 0. 5≤ x≤ 1. 0の範囲の組成を有する 薄膜を用いることが好ましく波長 30 Onmの光を用いたとき伝送損失 1 OdBZ cm以下の 光導波路が形成できる。 上記組成範囲の薄膜として単結晶を用いることにより伝送損失 5 d B , cm以下の光導波路が形成できる。 該単結晶薄膜のミラー指数 (002) の格子面の X線回 折ロッキングカーブの半値幅が 100秒以下のものでは少なくとも 3 dBZ cm以下の光導波 路を形成することが可能となる。
波長 270 nm以下の光を伝送する上では 0. 8≤ x≤ 1. 0の範囲の組成を有する薄膜を 用いることが好ましく波長 27 Onmの光を用いたとき伝送損失 10 dB/cm以下の光導波 路が形成できる。 上記組成範囲の薄膜として単結晶を用いることにより伝送損失 5 dB/cm 以下の光導波路が形成できる。 該単結晶薄膜のミラー指数 (002) の格子面の X線回折ロッ キングカーブの半値幅が 100秒以下のものでは少なくとも 3dBZcm以下の光導波路を形 成することが可能となる。
波長 25 Onm以下の光を伝送する上では 0. 9≤x≤l. 0の範囲の組成を有する薄膜を 用いることが好ましく波長 250 nmの光を用いたとき伝 ¾Ji失 10 dB/cm以下の光導波 路が形成できる。 上記組成範囲の薄膜として単結晶を用いることにより伝送損失 5dB/cm 以下の光導波路が形成できる。 該単結晶薄膜のミラ一指数 (002) の格子面の X線回折ロッ キングカーブの半値幅が 100秒以下のものでは少なくとも 3dBZcm以下の光導波路を形 成することが可能となる。
また上記 0. 8≤x≤l. 0の範囲の組成を有する単結晶薄膜を用いれば波長 30 Onm以 上の光の伝還員失 ldB/c m以下の埋め込み型の三^ ¾光導波路が得ることが可能となる。 光導波路として ¾έ¾から使用されている L iNb〇3、 L iTa〇3、 PLZT、 GaAs、 P bMo04などの材料は紫外光を透過しないので紫外光の伝送ができない。紫外光を透過し伝 送可能な材料としてシリカガラス、 アルミナ (サファイア)、 弗化カルシウムなど多くのものが 知られている。 しかしながらこれらの材料を薄膜として例えば 0. 5 m以上の厚みで窒化ァ ルミ二ゥムを主成分とする焼結体に形成したとき、 これらの薄膜には格子不 あるいは熱膨 張率差に起因すると考えられる歪が生じたり極端な場合はクラックが発生したりあるいは窒化 アルミニウムを主成分とする焼結体とシリカガラス、 アルミナ (サファイア)、 弗化カルシウム などの薄 J»料との接合界面で剥離が生じる場合があるので実質上紫外光の伝送には不適当で ある。 本発明においては窒化アルミニウムを主成分とする焼結体に窒化ガリゥム及び窒化アル ミニゥムのうちから選ばれた少なくとも 1種以上を主成分とする薄膜を用いるためこのような 不具合は生じにくい。上記のように本発明により従来の L iNb03系など従来材料を用いた光 導波路では困難であった紫外光が伝送可能な光導波路を有する薄膜基板が提供できる。
その他、 紫外光を透過し伝送可能な材料として窒化ガリゥム及び窒化アルミニゥムのうちか ら選ばれた少なくとも 1種以上を主成分とする薄膜をサフアイァ基板ゃシリコン基板に光導波 路として形成したものがある。 しかしこれらの薄膜はたとえ高い結晶性の単結晶薄膜として形
成できても基板と該薄膜との間の結晶格子不 生や熱膨張率の違いによって光導波路中に結 晶転位やひずみが生じ易くその結果伝送損失が 1 O d B/c mより大きくなり易い。 また、 シ リコン基板に形成した窒化アルミニウム薄膜にはクラックゃ基板との剥離が生じ易く光導波路 として機能することが困難であり、 さらに、 シリコン基板を用いた場合電気纖性が小さくか つ誘電率が高いので直接基板上に電気回路が形成しにくい。
また、 本発明による上記紫外光が伝送可能な光導波路を有する薄膜基板を構成する窒化アル ミ二ゥムを主成分とする焼結体には上記光導波路だけでなくその内部及び/又は表面に電気回 路を形成することができるので、 本発明による薄膜基板は光導波路と電気回路とを有する紫外 光の伝送が可能な光配線基板として用いることができるという特徴がある。
本発明において光導波路としては窒化アルミニウムを主成分とする焼結体に直接形成された 窒化ガリウム、 窒化インジウム、 窒化アルミニウムのうちから選ばれた少なくとも 1種以上を 主成分とする薄膜を光導波路として用いることができる。 また、 あらかじめ窒化ガリウム、 窒 化インジウム、 窒化アルミニウムのうちから選ばれた少なくとも 1種以上を主成分とする薄膜 を形成した窒化アルミニウムを主成分とする焼結体を用いその上にあらためて形成される窒化 ガリウム、 窒化インジウム、 窒化アルミニウムのうちから選ばれた少なくとも 1種以上を主成 分とする薄膜を光導難として用いることもでき、 窒化アルミニウムを主成分とする焼結体に 直接薄膜を形成したものより伝 ¾ί員失を低減化し得る場合がある。
上記あらかじめ窒化ガリウム、 窒化インジウム、 窒化アルミニウムのうちから選ばれた少な くとも 1種以上を主成分とする薄膜を形成した窒化アルミニウムを主成分とする焼結体の上に あらためて形成される薄膜の屈折率は窒化アルミニウムを主成分とする焼結体にあらかじめ形 成されている薄膜の屈折率よりも大きいものであることが伝送損失を低減化する上で望ましい。 それは前記のように窒化アルミ二ゥムを主成分とする焼結体に直接形成するよりも良質の薄膜 が形成できるという理由以外に、 屈折率の小さい材料に屈折率の大きい材料が形成された塲合 屈折率の大きい材料中を透過する光は屈折率の大きい材料中に閉じ込められその結果光が伝送 されるという原理によるものと考えられる。
また上記あらかじめ形成する薄膜の厚みはどのようなものでも用いることができ、例えば 0. 5 nm〜 1 0 0 0 /imの範囲のもの、 通常は結晶性の高い単結晶薄膜を得られるので薄膜の厚 みとして 2 0 0 m以下のものを用いることがは好ましい。 また、 厚み 5 O nm以上とするこ とでより伝 ¾ί員失の少ない光導波路を作製することができる。 また、 あらかじめ形成する薄膜 の上からあらためて形成する光導波路として機能する屈折率の大きい薄膜の厚みは 0. 1 um 〜1 0 0 0 / mの範囲のもの、 通常は結晶性の高い単結晶薄膜を得られるので薄膜の厚みとし て 2 0 0 m以下のものを用いることがは好ましい。 屈折率の小さい薄膜と屈折率の大きい薄 膜とを組み合わせて屈折率の大きい薄膜を光導波路として機能させる場合該光導波路の厚みは 0. l m以上あれば十分機能し得る。
本発明においては屈折率の小さい薄膜と光導波路となる屈折率の大きい薄膜のあらゆる組み 合わせが可能である。 すなわち、 窒化ガリウム、 窒化インジウム、 窒化アルミニウムのうちか ら選ばれた少なくとも 1種以上を主成分とする薄膜のすべての組成において、 あるいは単結晶、 無定形、 多結晶、 配向性多結晶などすベての結晶状態において上記組み合わせが可能である。 該屈折率の小さい薄膜は通 来から用いられている光導波路におけるクラッド層としての役 割を担い得る。
本発明において上記のように屈折率の小さい薄膜は窒化アルミニウムを主成分とする焼結体 と光導波路として用いる屈折率の大きい薄膜との間に形成されるものだけではなぐ 窒化アル ミニゥムを主成分とする焼結体に形成された光導波路として用いられる屈折率の大きい薄膜の 上に形成された状態のものも用いることができ、 屈折率の小さい薄膜が上記のような形成状態
であっても通^«から用いられている光導波路におけるクラッド層としての役割を担い得る。 屈折率の小さい薄膜に光導波路となる屈折率の大きい薄膜とを組み合わせて形成した薄膜基 板について具体的な例を示せば、 1 ) 窒化ガリウム、 窒化インジウム、 窒化アルミニウムのう ちから選ばれた少なくとも 1種以上を主成分とする薄膜と窒化ガリウム、 窒化インジウム、 窒 化アルミニウムのうちから選ばれた少なくとも 1種以上を主成分としガリウム、 インジウムの うちから選ばれた少なくとも 1種以上の成分をより多く含む薄膜とを組み合わせたものがある。 また、 2 ) 窒化ガリウム、 窒化インジウム、 窒化アルミニウムのうちから選ばれた少なくとも 1種以上を主成分とする薄膜と窒化ガリウム、 窒化インジウム、 窒化アルミニウムのうちから 選ばれた少なくとも 1種以上を主成分としさらにニオブ、 タンタルのうちから選ばれた少なく とも 1種以上の成分を含む薄膜とを組み合わせたもの、 などの例がある。
上記具体例が示されたことの背景は以下 2点の知見が得られたことに基づく。すなわち、 1 ) 窒化アルミニウムを主成分とする焼結体に形成された窒化ガリウム、 窒化インジウム、 窒化ァ ルミニゥムのうちから選ばれた少なくとも 1種以上を主成分とする薄膜においてガリウム、 ィ ンジゥムのうちから選ばれた少なくとも 1種以上の成分を多く含むにしたがって薄膜の屈折率 は上昇することカ鳩認されことによる。 具体的にいえば、 元々の窒化ガリウム、 窒化インジゥ ム、 窒化アルミニウムのうちから選ばれた少なくとも 1種以上を主成分とする薄膜に対して窒 化ガリゥム及び窒化ィンジゥムのうちから選ばれた少なくともいずれか一種以上の成分の増加 量が主成分に対して 2 0モル%以下の場合屈折率の上昇は 2 X 1 0—1以下である。 また、 元々 の窒化ガリウム、 窒化インジウム、 窒化アルミニウムのうちから選ばれた少なくとも 1種以上 を主成分とする薄膜に対して窒化ガリウム及び窒化ィンジゥムのうちから選ばれた少なくとも いずれか一種以上の成分の増加量が主成分に対して 0. 0 1モル%程度であっても屈折率の上 昇が少なくとも 1 X 1 0 _5以上認められる。 2 ) 窒化ガリウム、 窒化インジウム、 窒化アルミ ニゥムのうちから選ばれた少なくとも 1種以上を主成分としさらにニオブ、 タンタルのうちか ら選ばれた少なくとも 1種以上の成分を含む薄膜はニオブあるいはタンタルを含まない窒化ガ リウム、 窒化インジウム、 窒化アルミニウムのうちから選ばれた少なくとも 1種以上を主成分 とする薄膜に比べて屈折率が上昇することが見出されたことによる。 具体的にいえば、 窒化ガ リウム、 窒化インジウム、 窒化アルミニウムのうちから選ばれた少なくとも 1種以上を主成分 とする薄膜においてニオブ及びタンタルのうちから選ばれた少なくとも 1種以上の成分の含有 量が主成分に対して窒化物換算で 2 0モル%以下のものでは屈折率の上昇は 2 X 1 0—1以下で ある。 また、 窒化ガリウム、 窒化インジウム、 窒化アルミニウムのうちから選ばれた少なくと も 1種以上を主成分とする薄膜においてニオブ及びタンタルのうちから選ばれた少なくとも 1 種以上の成分の含有量が主成分に対して窒化物換算で 0. 0 1モル%程度であっても屈折率の 上昇が 1 X 1 0 _5以上認められる。
ニオブあるいはタンタルを含むことの効果はおそらくニオブあるいはタンタルが窒化ガリウ ムあるいは窒化インジウムあるいは窒化アルミニウムあるいはこれら成分を複数有する化合物 へ固溶し易い性質を持つことが主原因であろうと本願発明者は推測している。 すなわちニオブ あるいは夕ン夕ルは窒化ニオブあるいは窒化タンタルとして窒化ガリゥムあるいは窒化ィンジ ゥムあるいは窒化アルミニウムあるいはこれら成分を複数有する化合物の結晶へ固溶するもの と推測される。 窒化ニオブあるいは窒化タンタルは窒化ガリウムあるいは窒化インジウムある いは窒化アルミニゥムあるいはこれら成分を複数有する化合物と同じ六方晶系の結晶構造を有 するため固溶が実現され易いと思われる。 異なる材料として単に物理的に混合されているので はなく異なる成分であっても同じ結晶構造のもの同士が結晶内部で原子レベルで溶け合つてい るため屈折率の上昇が達成されるものと推測される。
本発明において上記窒化ガリウム、 窒化インジウム、 窒化アルミニウムのうちから選ばれた
少なくとも 1種以上を主成分としさらにニオブあるいはタンタルのうちから選ばれた少なくと も 1種以上の成分を含む薄膜は可視光及び赤外光を伝送できるだけでなく波長 200 nm〜3 80 nmの範囲の紫外領域の光を伝送できるので少なくとも波長 200nm〜 7000η の 範囲の光を伝送する光導波路としても使用することができる。
なお、 窒化ガリウム、 窒化インジウム、 窒化アルミニウムのうちから選ばれた少なくとも 1 種以上を主成分とする薄膜はニオブ単独あるいはタンタル単独あるいはニオブ及びタンタルの 両方の成分を同時に含むものを得ることができる。 また、 窒化ガリウム、 窒化インジウム、 窒 化アルミニウムのうちから選ばれた少なくとも 1種以上を主成分とする薄膜のニオブ及びタン タルのうちから選ばれる少なくとも 1種以上の成分の含有量は主成分に対して窒化物 で 2 0モル%以下であることが好ましい。 すなわち、 ニオブ成分及びタンタル成分は薄膜中でそれ ぞれ窒化ニオブ(NbN;)、 窒化タンタル(TaN) として雜しているものとみなして、 主成 分の含有量を m (AlxGay I η yN: 0. 0≤χ≤1. 0、 0. 0≤y≤l. 0力、つ 0. 0≤x + y≤l. 0) の組成式で表わしたとき含有されるニオブ成分あるいはタンタル成分の 含有量は(1— m) (NbuTax_uN) の組 で示され、 薄膜中のニオブ及びタンタルの含有 量は 0. 8≤m≤l. 0かつ 0. 0≤u≤l. 0の範囲であることが好ましい。 薄膜中のニォ ブ及び夕ンタルのうちから選ばれる少なくとも 1種以上の成分の含有量が窒化物換算で 20モ ル%より多ければ該薄膜を光導波路として使用したとき伝送損失が増大化し易くなるためであ る。 また窒化ガリウム、 窒化インジウム、 窒化アルミニウムのうちから選ばれた少なくとも 1 種以上を主成分とする薄膜へのニオブ及び夕ンタルが含有されることの効果は主成分に対して 窒化物換算で 0. 01モル%程度の量であっても主成分の屈折率を少なくとも 1 X 10_5以上 上昇させ該薄膜を光導波路として機能せしめ得る。
なお、 薄膜の屈折率の測定は通常のエリプソメーターなどを用いた偏光解斤法、 繰り返し干 渉顕微鐘法、 プリズムカップラ一^:、 あるいはその他分光光度計 (Spe c t r opho t ome t e r) などの光学機器を用いて容易に行うことができる。 このような屈折率の測定精 度は 1 X 10— 5の桁まで可能で少なくとも 2 X 10_5の精度で測定できる。
上記のように本発明において窒化ガリウム、 窒化インジウム、 窒化アルミニウムのうちから 選ばれた少なくとも 1種以上を主成分とする薄膜だけでなぐ窒化ガリウム、窒化インジウム、 窒化アルミニウムのうちから選ばれた少なくとも 1種以上を主成分とする薄膜にニオブ及び夕 ンタルのうちから選ばれた少なくとも 1種以上の成分を含む薄膜も光導波路として用いること ができる。
上記窒化ガリウム、 窒化インジウム、 窒化アルミニウムのうちから選ばれた少なくとも 1種 以上を主成分とする薄膜にニオブ及び夕ンタルのうちから選ばれた少なくとも 1種以上の成分 を含む薄膜は該薄膜より屈折率の小さい薄膜と組み合わせた光導波路としてだけでなぐ 例え ば窒化アルミニウムを主成分とする焼結体に直接形成するなど該薄麵虫でも光導波路として 用いることができる。
本発明において上記屈折率の小さい薄膜に光導波路となる屈折率の大きい薄膜を形成した薄 膜基板、 あるいは光導波路となる屈折率の大きい薄膜に屈折率の小さい薄膜を形成した薄膜基 板は、 前記 CVD、 MOCVD、 MBE、 スパッ夕などの定法により屈折率の小さい薄膜に屈 折率の大きい薄膜、 あるいは屈折率の大きい薄膜に屈折率の小さい薄膜を順次積層されたもの を用いることができる。 このような方法により例えば図 21、 図 22、 図 23、 図 24、 図 2 5、 図 26、 図 34に例示される光導波路を作製することができる。 また、 屈折率の小さい薄 膜中に溝や窪みを形成しておき屈折率の大きい薄膜を順次埋め込んでいくという方法も用いる ことができ、 このような方法によって図 27、 図 28、 図 29、 図 30、 図 31、 図 32、 図 33、 図 35に例示される光導波路を作製することができる。
また、 上記屈折率の小さい薄膜に光導波路となる屈折率の大きい薄膜を形成した薄膜基板と して上記のように積層法により薄膜を順次形成していくという以外にも、 例えぱ滅散法ある いはイオン注入法などを用いて窒化ガリウム、 窒化インジウム、 窒化アルミニウムのうちから 選ばれた少なくとも 1種以上を主成分とする薄膜の特に深さ方向に例えばガリゥム、 ィンジゥ ム、 ニオブ、 タンタルのうちから選ばれた少なくとも 1種以上の成分を含有せしめることで該 ガリウム、 インジウム、 ニオブ、 タンタルのうちから選ばれた少なくとも 1種以上の成分が含 有された薄膜部分の屈折率を上昇させる方法によっても形成することができる。
«散法としては、例えば窒化アルミニウムを主成分とする焼結体に形成した窒化ガリゥム、 窒化インジウム、 窒化アルミニウムのうちから選ばれた少なくとも 1種以上を主成分とする薄 膜に窒化ガリウム、 金属ガリウム、 酸化ガリウムなどのガリウム成分、 あるいは窒化インジゥ ム、 金属インジウム、 酸化インジウムなどのインジウム成分、 あるいは窒化ニオブ、 金属ニォ ブ、 酸化ニオブなどのニオブ成分、 あるいは窒化タンタル、 金属タンタル、 酸化タンタルなど のタンタル成分を含有する材料をあらたに形成し例えば窒素などの非酸化性雰囲気中要すれば
8 0 0 °C以上の高温で加熱処理することにより該ガリウム、 インジウム、 ニオブ、 タン夕レ成 分を窒化ガリウム、 窒化インジウム、 窒化アルミニウムのうちから選ばれた少なくとも 1種以 上を主成分とする薄膜中に拡散させる、 などの方法がある。 その結果元々の窒化ガリウム、 窒 化インジウム、 窒化アルミニウムのうちから選ばれた少なくとも 1種以上を主成分とする薄膜 よりもガリゥムあるいはィンジゥムの含有量の多い部分が薄膜の深さ方向及び幅方向に形成さ れ屈折率が上昇し光導波路として機能するようになる。 また、 ニオブあるいはタンタル成分を あらたに含む窒化ガリウム、 窒化インジウム、 窒化アルミニウムのうちから選ばれた少なくと も 1種以上を主成分とする薄膜が形成され屈折率が上昇し光導波路として機能するようになる。 上記熱拡散法によれば屈折率の上昇は加熱温度あるいは加熱時間にもよるが 2 X 1 0—1以下で あり通常 1 X 1 0 _5〜2 X 1 0—1の範囲にあるので元々の窒化ガリウム、 窒化インジウム、 窒 化アルミニウムのうちから選ばれた少なくとも 1種以上を主成分とする薄膜に対して窒化ガリ ゥム及び窒化ィンジゥムのうちから選ばれた少なくともいずれか一種以上の成分の増加量は主 成分に対して 2 0モル%以下であると思われる。 また上記窒化ガリウムあるいは窒化インジゥ ム成分の増加量は主成分に対して 1モル%以下のものであっても屈折率の上昇は通常 1 X 1 0 一5〜 I X 1 0一2の範囲にあり十分光導波路として機能する。 さらに、 上記 »散法によれば二 ォブ及び夕ンタルのうちから選ばれた少なくとも 1種以上を含む窒化ガリゥム、 窒化ィンジゥ ム、 窒化アルミニゥムのうちから選ばれた少なくとも 1種以上を主成分とする薄膜の屈折率は 加熱温度あるいは加熱時間にもよるが 2 X 1 0—1以下であり通常 1 X 1 0— 5〜2 X 1 0— 1の 範囲にあるのでニオブ及びタンタルのうちから選ばれた少なくとも 1種以上の成分の含有量は 主成分に対して 2 0モル%以下であると思われる。 ニオブあるいはタンタルの含有量は伝送損 失を低減化する上で 成分に対して 1 0モル%以下であることが好ましい。 また上記ニオブ あるいはタン夕レ含有量は主成分に対して 1モル%以下のものであっても屈折率の上昇は通常 1 X 1 0—5〜: L X 1 0— 2の範囲にあり十分光導波路として機能する。
イオン 法としては、 例えばイオン源に塩化ガリウム、 匕ガリウム、 水素化ガリウムな どのガリウム成分、 あるいは塩化インジウム、 臭化インジウム、 水素化インジウムなどのイン ジゥム成分、 あるいは塩ィ匕ニオブ、 臭化ニオブ、 7_Κ素化ニオブなどのニオブ成分、 あるいは塩 化タンタル、 : ¾{ヒタンタル、 水素化タンタルなどのタンタル成分を用い放電などを用いて上記 成分をイオンィ匕し質量分析器などで不要イオンを取り除いた後加速器でガリゥム、ィンジゥム、 ニオブ、 タンタルイオンを加速して窒化ガリウム、 窒化インジウム、 窒化アルミニウムのうち から選ばれた少なくとも 1種以上を主成分とする薄膜に打ち込みその後打ち込んだイオンが均 一になるよう例えば窒素などの非酸化性雰囲気中要すれば 5 0 0 °C以上の温度で加熱処理し該
薄膜にガリウムあるいはインジウムが多く含まれる部分やニオブあるいはタンタルを新たに含 有する部分を形成する、 といった方法などがある。 その結果元々の窒化ガリウム、 窒化インジ ゥム、 窒化アルミニゥムのうちから選ばれた少なくとも 1種以上を主成分とする薄膜よりもガ リゥムあるいはィンジゥムの含有量の多い部分が薄膜の深さ方向及び幅方向に形成され屈折率 が上昇し光導波路として機能するようになる。 また、 ニオブあるいはタンタル成分をあらたに 含む窒化ガリウム、 窒化インジウム、 窒化アルミニウムのうちから選ばれた少なくとも 1種以 上を主成分とする薄膜が形成され屈折率が上昇し光導波路として機能するようになる。
上記難散法あるいはイオン注入法により光導波路を形成する場合窒化アルミニウムを主成 分とする焼結体に形成された元々の窒化ガリウム、 窒化インジウム、 窒化アルミニウムのうち から選ばれた少なくとも 1種以上を主成分とする薄膜は光導波路より屈折率が小さくなるので 該薄膜は必然的に光導波路で伝送される光を閉じ込めるためのクラッド層として機能する。 熱拡散法あるいはィオン注入法は光リソダラフィ一など加工法を用いて微細な光導波路が形 成できるので従来から広く用いられている埋め込み型の光導波路を形成する場合など有効であ る。 なお、 埋め込み型の光導波路の例として本発明においては後述する図 3 0、 図 3 1、 図 3 2、 図 3 3、 図 3 5を例示してある。
上記本発明において 散法あるいはイオン注入法により光導波路を形成する場合屈折率を 向上させる成分が導入される部分の大きさは任意のものが作製できるが、 通常上記埋め込み型 の光導波路の場合幅として 0. 5 m以上あれば十分光導波路として機能する。 通常光導波路 の幅は 1 m以上で形成される。 通常光導波路の幅は 1 m〜5 0 0 mの範囲のものが用い られる。 また拡散深さあるいは注入深さは任意のものが作製できるが、 0. 1 m以上あれば 十分伝纖失の小さい光導波路として機能し得る。 また拡散深さあるいは注入深さは 0. 3 " m以上あれば伝週失のより小さい光導波路として機能し得る。 通常拡散深さあるいは注入深 さは 0. 5 m以上のものが用いられる。
また、 上記 »散法あるいはイオン注入法により光導波路を形成する場合特に蒙 散法にお いてあらかじめ薄膜上に屈折率を向上させる成分が形成された部分は熱拡散後に該屈折率向上 成分が導入された部分の幅が 散前と比べて広がり易いがこのような状態であっても問題な く光導波路として機能し得る。
なお、 上記光導波路のような幅の細い薄膜の屈折率測定において通常の光学的方法を用いる 場合被測定部分へ照射する光ビームを光学レンズなどで絞り込むため屈折率の精度が 1 X 1 0 一1〜 I X 1 0 _2程度の桁まで低下し易いのでこのような幅の細い部分では直接測定せず、 同じ 方法で同じ組成になるよう薄膜を広い面状に別の部分に形成し該薄膜の屈折率を測定すること で幅の細い薄膜の屈折率と見なす場合が多い。 被測定部分へ照射する光ビームの径は通常 5 0 0 m以上のものが用いられるがこのような光ビームを光学レンズなどを用いて最小で光の波 長例えば 6 5 0 nm程度に絞り込み、 例えば幅 6 5 0 nmあるいはそれ以上の幅を有する薄膜 部分に照射して屈折率を測定することは可能であるが、 その結果屈折率の測定精度が本来の 1 X 1 0一5の桁から 1 X 1 0―1〜 1 X 1 0—2程度の桁まで大きく低下し易い。 より具体的に言え ば、 例えば上記順次積層法、 拡散法あるいはイオン注入法などを用いて幅 1 C mの細い薄膜 を光導波路として形成する場合、 この光導波路を形成する部分の薄膜の屈折率は直接測定せず、 同じ組成になるように別の部分に広い面積 (例えば 0. 5 mmx 2 mmあるいはそれ以上) で 形成した薄膜の屈折率を測定し、 該薄膜の屈折率をもって幅 1 0 mの光導波路の屈折率と見 なす、 ということである。 本発明においても幅の細い薄膜で構成された光導波路の屈折率はこ のような方法で測定された。
本発明においてニオブ及びタンタルを含有する窒化ガリウム、 窒化インジウム、 窒化アルミ ニゥムのうちから選ばれた少なくとも 1種以上を主成分とする材料の屈折率の増加及び光導波
路としての光伝送性は上記薄膜以外でも確かめられた。 すなわち、 薄膜ではない窒化ガリウム 及び窒化アルミ二ゥムの各バルク状単結晶を用いて維散法によりニオブ及び夕ンタルを含有 せしめたところ屈折率の上昇及び光伝送性が認められる。 上記 散法により窒化ガリゥムの ノルク状単結晶にィンジゥム、 ニ才ブ及び夕ンタレを含有せしめることで形成した光導波路に おいて屈折率が T視光領域において少なくとも 1 X 1 0一5以上上昇し、 該窒化ガリウムを主成 分とするバルク単結晶には少なくとも波長 3 8 0 nm以上の光が伝 失 3 d BZc m以下で 伝送可能な光導波路が形成し得る。 また上記 散法により窒化アルミニウムのバルク状単結 晶にガリウム、 インジウム、 ニオブ及びタンタルを含有せしめることで形成した光導波路にお いて屈折率が可視光領域において少なくとも 1 X 1 0—5以上上昇し、 該窒化ガリウムを主成分 とするバルク単結晶には少なくとも波長 2 5 0 nm以上の光が伝 員失 3 d B/ c m以下で伝 送可能な光導波路が形成し得る。 さらに該窒化ガリゥムを主成分とするバルク単結晶には少な くとも波長 2 2 0 nm以上の光が伝纖失 1 0 d BZ c m以下で伝送可能な光導波路が形成し 得る。
本発明において窒化アルミニウムを主成分とする焼結体に形成した窒化ガリゥム、 窒化ィン ジゥム、 窒化アルミニウムのうちから選ばれた少なくとも 1種以上を主成分とする薄膜を光導 波路として用いたとき、 上記バルク単結晶を用いて作製した光導波路と比べて少なくとも同等 あるいはそれ以下の低い伝送損失のものが作製し得る。
本発明において窒化アルミニウムを主成分とする焼結体に直接形成した窒化ガリゥム、 窒化 ィンジゥム、 窒化アルミニウムのうちから選ばれた少なくとも 1種以上を主成分とする薄膜を 光導波路として用いることができる。 このことは薄膜の屈折率が窒化アルミニウムを主成分と する焼結体より高いものであることを示唆している。 元々窒化ガリウム、 窒化インジウム、 窒 化アルミ二ゥムの各成分の中で窒化アルミ二ゥムが最も屈折率が小さいことが大きな要因であ ると思われるが、 その他にも十分緻密化された窒化アルミニウムを主成分とする焼結体におい て該焼結体を構成する窒化アルミニウム粒子は十分結晶化が進行し単結晶に近い状態になって いるものと考えられるが窒化アルミニウム粒子中への不純物固溶や焼結体としての粒界や粒界 相の影響で単結晶の屈折率よりも小さくなるためであろうと推測される。 そのため窒化アルミ 二ゥムを主成分とする焼結体に直接形成された薄膜であってもその中で全反射が生じ易くなる ものと思われる。 窒化アルミニウム結晶は光軸すなわち結晶 C軸に垂直な方向が常光の方向と なり C軸に平行な方向が異常光の方向となる光学的異方体で常光と異常光とで屈折率が異なり 異常光の屈折率のほうが可視光領域においては 0. 0 5程度大きい。 一方窒化アルミニウムを 主成分とする焼結体は多結晶体であるので該焼結体を構成する窒化アルミニゥム結晶粒子はあ らゆる方向を向いているのでこのような結晶の方向性は実質的になく結晶としての光学的な性 質は平均化されたものになっていると思われる。 また、 窒化アルミニウムを主成分とする焼結 体は誠により作製されるので焼結体を構成する窒化アルミニウム粒子中への微量な陽イオン 不純物あるいは炭素や酸素など不純物固溶があると思われる。 さらに、 窒化アルミニウムを主 成分とする焼結体は上記のように多結晶体であるので粒界や粒界相が存在するためその部分へ の不純物 析出が考えられる。 以上のような焼結体としての の結果屈折率は単結晶よ り低下ししたがつて窒化アルミ二ゥムを主成分とする焼結体に直接形成した窒化ガリウム、 窒 化インジウム、 窒化アルミニウムのうちから選ばれた少なくとも 1種以上を主成分とする薄膜 が光導波路として十分機能できるものと本願発明者は考えている。
通常窒化アルミニウムを主成分とする焼結体に直接形成された窒化ガリゥム、 窒化ィンジゥ ム、 窒化アルミニウムのうちから選ばれた少なくとも 1種以上を主成分とする薄膜であっても 単結晶として形成されたものの屈折率は 2. 0以上であり十分光導波路として機能する。 光導 波路として用いる窒化ガリウム、 窒化インジウム、 窒化アルミニウムのうちから選ばれた少な
くとも 1種以上を主成分とする単結晶薄膜、 その中でも窒化アルミニウムを主成分とする単結 晶薄膜の結晶性を向上させるために窒化アルミニウムを主成分とする焼結体との間に中間層と して同質の窒化ガリゥム、 窒化ィンジゥム、 窒化アルミニゥムのうちから選ばれた少なくとも
1種以上を主成分とする薄膜を用いる場合該中間層薄膜の屈折率は 2. 0より小さいものを用 いることが好ましい。 この場合該中間層薄膜は光導波路を機能させるためのクラッド層として の役割を果たすものと思われる。
本発明において窒化アルミニウムを主成分とする焼結体に窒化ガリゥム、 窒化ィンジゥム、 窒化アルミニウムのうちから選ばれた少なくとも 1種以上を主成分とする薄膜からなる光導波 路が形成された薄膜基板に電極を設けることで該薄膜基板を光変調器、 光位相変^^、 波長フ ィル夕一、 光スィツチなどの光伝送用基板あるいは音響光学デバイスとして使用することがで きる。 それが可能となるのは窒化ガリウム、 窒化インジウム、 窒化アルミニウムのうちから選 ばれた少なくとも 1種以上を主成分とする薄膜に対して電位を印加することで該薄膜の屈折率 を変化させることができるためであろうと思われる。 また、 形成されている窒化ガリウム、 窒 化インジウム、 窒化アルミニウムのうちから選ばれた少なくとも 1種以上を主成分とする薄膜 は単結晶を用いることが好ましい。 その理由は伝送損失が低減化でき易いというほかに、 該薄 膜が単結晶であれば光軸 (すなわち結晶の c軸)に対する電位の方向を制御できその結果屈折率 の変化量を制御し易くなるためである。 窒化アルミニウム結晶、 窒化ガリウム結晶、 窒化イン ジゥム結晶、 あるいはこれら窒化物同士の混晶は光軸すなわち結晶 C軸に垂直な方向が常光の 方向となり C軸に ¥1亍な方向が異常光の方向となる光学的異方体で常光と異常光とで屈折率が 異なり異常光のほうが大きい。 薄膜が単結晶であれば電位の印加方向を C軸に平行にしたりあ るいは C軸に垂直にすることで屈折率の変化を制御でき易くなる。 さらに本発明において室化 アルミニウムを主成分とする焼結体に窒化ガリウム、 窒化インジウム、 窒化アルミニウムのう ちから選ばれた少なくとも' 1種以上を主成分とする単結晶薄膜を形成した薄膜基板を提供でき るが、 該単結晶薄膜の結晶軸形成方向〖堪板面に対して C軸が垂直な方向あるいは水平の方向 のいずれも作製可能であり、 多様な屈折率制御がさらに可能でとなる。
光導波路を形成する薄膜に上記のような単結晶を用いる効果は例えば後述 (例えば図 3 0、 図 3 1、 図 3 2、 図 3 3、 図 3 5 ) の埋め込み型光導波路を有する薄膜基板において大きい。 本発明において上記のように電極を設け電位を印加することで該薄膜の屈折率カ雙化し易いと いう性質を禾 IJ用して光変調器、 光位相変腿、 波長フィルター、 光スィッチ、 などを作製する ことができる。
上記のように本発明の i [は «からのサファィァ基板などでなく、 窒化アルミニゥムを主 成分とする焼結体に窒化ガリウム、 窒化インジウム、 窒化アルミニウムのうちから選ばれた少 なくとも 1種以上を主成分とする薄膜による光導波路が形成できるという点にある。 例えば紫 外光を低伝週員失で伝送できるといった上記のような光導波路としての特性が得られるのは窒 化アルミニウムを主成分とする焼結体と窒化ガリウム、 窒化インジウム、 窒化アルミニウムの うちから選ばれた少なくとも 1種以上を主成分とする薄膜との高い接合性が得られることが主 因の一つと思われる。 その結果ひずみや欠陥が少ない薄膜が容易に形成し易くなる。 また、 上 記のような光導波路としての特性が得られるのは窒化アルミニゥムを主成分とする焼結体に窒 化ガリウム、 窒化インジウム、 窒化アルミニウムのうちから選ばれた少なくとも 1種以上を主 成分とする単結晶薄膜が形成できるということも主因の 1つであると思われる。
上記のように本発明によって窒化アルミニウムを主成分とする焼結体に窒化ガリゥム、 窒化 ィンジゥム、 窒化アルミニウムのうちから選ばれた少なくとも 1種以上を主成分とする薄膜に よる光導波路が形成された薄膜基板を提供できる。 本発明による光導波路は«から知れられ ているどのような構造の二次元導波路及び三次元光導波路のものであっても作製することがで
さる。
また、 本発明による薄膜基板にさらに電気回路を形成することで該薄膜基板を少なくとも光 導波路及び電気回路を有する光配驢板として用いることができる。 上記電気回路を形成する ための材料として窒化アルミニウムを主成分とする焼結体及び窒化ガリゥム、窒化ィンジゥム、 窒化アルミニウムのうちから選ばれた少なくとも 1種以上を主成分とする薄膜との接合性の優 れるため本発明による薄,電性材料を用いることが好ましい。 その他上記電気回路を形成す るための材料として窒化アルミニウムを主成分とする焼結体との同時舰により形成される夕 ングステン、 モリブデン、 銅を主成分とするもの、 あるいは窒化アルミニウムを主成分とする 焼結体に対して厚扁寸け法により形成される金、銀、銅、 白金、ノ°ラジウム、 タングステン、 モリブデン、 マンガン、 ニッケルなどを主成分材料、 あるいは窒化アルミニウムを主成分とす る焼結体に対して導電性べ一ストとして樹脂成分を用いた接着法による金、 銀、 銅、 白金、 パ ラジウム、 ニッケルなどを主成分材料、 などを用いることができる。
以下本発明による窒化アルミニウムを主成分とする焼結体に窒化ガリゥム、窒化ィンジゥム、 窒化アルミニウムのうちから選ばれた少なくとも 1種以上を主成分とする薄膜による光導波路 が形成された薄膜基板について以下図を例示して説明する。
図 2 1〜図 2 3は二次元光導波路が形成された薄膜基板を示す例である。
図 2 1は窒化アルミニウムを主成分とする焼結体からなる基板 1 4に窒化ガリウム、 窒化ィ ンジゥム、 窒化アルミニウムのうちから選ばれた少なくとも 1種以上を主成分とする薄膜によ り二次元光導波路 5 0が形成されている薄膜基板の 1例を示す斜視図である。
図 2 2は窒化アルミニウムを主成分とする焼結体からなる基板 1 4に窒化ガリウム、 窒化ィ ンジゥム、 窒化アルミニウムのうちから選ばれた少なくとも 1種以上を主成分とする薄膜によ り二次元光導波路 5 0が形成され該二次元光導波路の上にクラッド層 7 0が形成され薄膜基板 の 1例を示す斜視図である。 図 2 2において、 クラッド層は光導波路を形成している窒化ガリ ゥム、 窒化インジウム、 窒化アルミニウムのうちから選ばれた少なくとも 1種以上を主成分と する薄膜より屈折率の小さい材料であれば、 例えば S i 02、 A l 2〇3、 各種ガラスなど、 どの ようなものでも用いることができるが同質の窒化ガリウム、 窒化インジウム、 窒化アルミニゥ ムのうちから選ばれた少なくとも 1種以上を主成分とする材料を用いることが接合性などの点 から好ましい。 また、 図 2 2において、 クラッド層は空気を用いることができその場合図 2 2 に示される薄膜基板は図 2 1に示された薄膜基板と同等のものとなる。
図 2 3は窒化アルミニウムを主成分とする焼結体からなる基板 1 4にクラッド層 7 0が形成 されその上に窒化ガリゥム、 窒化ィンジゥム、 窒化アルミニゥムのうちから選ばれた少なくと も 1種以上を主成分とする薄膜により二次元光導波路 5 0が形成されている薄膜基板の 1例を 示す斜視図である。 図 2 3において、 クラッド層は光導波路を形成している窒化ガリウム、 窒 化インジウム、 窒化アルミニウムのうちから選ばれた少なくとも 1種以上を主成分とする薄膜 より屈折率の小さい材料であれば、 例えば S i〇2、 A l 2〇3、 各種ガラスなど、 どのようなも のでも用いることができるが同質の窒化ガリウム、 窒化インジウム、 窒化アルミニウムのうち から選ばれた少なくとも 1種以上を主成分とする材料を用いることが接合性などの点から好ま しい。
図 2 1〜図 2 3において、 平板状に形成された窒化ガリウム、 窒化インジウム、 窒化アルミ ニゥムのうちから選ばれた少なくとも 1種以上を主成分とする薄膜に光が導入されたとき導入 光は基板の垂直方向に閉じ込められ、 該薄膜は二 ^¾光導波路として機能する。
図 2 4〜図 3 0は三次元光導波路が形成された薄膜基板を示す例である。
図 2 4は窒化アルミニウムを主成分とする焼結体からなる基板 1 ,4に窒化ガリウム、 窒化ィ ンジゥム、 窒化アルミニウムのうちから選ばれた少なくとも 1種以上を主成分とする薄膜によ
り三次元光導波路 6 0が形成されている薄膜基板の 1例を示す斜視図である。 図 2 4において 三^光導波路 6 0の周囲は空気である。
図 2 5は窒化アルミニウムを主成分とする焼結体からなる基板 1 4にクラッド層 7 0が形成 されその上に窒化ガリウム、 窒化インジウム、 窒化アルミニウムのうちから選ばれた少なくと も 1種以上を主成分とする薄膜により三次元光導波路 6 0が形成されている薄膜基板の 1例を 示す斜視図である。 図 2 5において、 クラッド層は光導波路を形成している窒化ガリウム、 窒 化インジウム、 窒化アルミニウムのうちから選ばれた少なくとも 1種以上を主成分とする薄膜 より屈折率の小さい材料であれば、 例えば S i 02、 A l 2〇3、 各種ガラスなど、 どのようなも のでも用いることができるが同質の窒化ガリウム、 窒化インジウム、 窒化アルミニウムのうち から選ばれた少なくとも 1種以上を主成分とする材料を用いることが接合性などの点から好ま しい。
図 2 6は窒化アルミニウムを主成分とする焼結体からなる基板 1 4に窒化ガリウム、 窒化ィ ンジゥム、窒化アルミニウムのうちから選ばれた少なくとも 1種以上を主成分とするリッジ(山 の背) 状に形成された薄膜により三^光導波路 6 1が形成されている薄膜基板の 1例を示す ^見図である。 図 2 6には図示されていないが窒化アルミニウムを主成分とする焼結体からな る基板 1 4とリッジ状の三次元光導波路 6 1との間に 導波路より屈折率の小さい材料、 例 えば同質の窒化ガリウム、 窒化インジウム、 窒化アルミニウムのうちから選ばれた少なくとも 1種以上を主成分とするものを用いることが光伝送損失を低減化する上で好ましい。
図 2 7は窒化アルミ二ゥムを主成分とする焼結体からなる基板 1 に窒化ガリゥム、 窒化ィ ンジゥム、 窒化アルミニウムのうちから選ばれた少なくとも 1種以上を主成分とする平板状の 薄膜を形成することでニ¾¾¾¾導波路 5 0を作製し該ニ^光導«に S i〇2、 A 1 2〇3、各 種ガラスなどの誘電体材料 4 0を形成し 電体材料が形成された部分の二次元光導波路の屈 折率を上昇させることで三次元光導波路 6 2とせしめた薄膜基板の 1例を示す斜視図である。 図 2 7には図示されていないが窒化アルミニウムを主成分とする焼結体からなる基板 1 4と二 ^光導波路 5 0及び三次元光導波路 6 2との間に該光導波路より屈折率の小さい材料、 例え ば同質の窒化ガリウム、 窒化インジウム、 窒化アルミニウムのうちから選ばれた少なくとも 1 種以上を主成分とするものを用いることが光伝送損失を低減化する上で好ましい。
図 2 8は窒化アルミニウムを主成分とする焼結体からなる基板 1 4に窒化ガリウム、 窒化ィ ンジゥム、 窒化アルミニウムのうちから選ばれた少なくとも 1種以上を主成分とする平板状の 薄膜を形成することで二: ^光導波路 5 0を作製し該二 光導波路に金属材料 1 0 0を直接 形成し該金属材料が形成された部分の二 光導波路の屈折率を低化させることで相対的に該 金属の形成されていない部分の屈折率を高め三次元光導波路 6 3とせしめた薄膜基板の 1例を 示す S図である。 図 2 8には図示されていないが窒化アルミニウムを主成分とする焼結体か らなる基板 1 4と二^;光導波路 5 0及び三次元光導波路 6 3との間に 導波路より屈折率 の小さい材料、 例えば同質の窒化ガリウム、 窒化インジウム、 窒化アルミニウムのうちから選 ばれた少なくとも 1種以上を主成分とするものを用いることが光伝送損失を低減化する上で好 ましい。
図 2 9は窒化アルミニウムを主成分とする焼結体からなる基板 1 4に窒化ガリウム、 窒化ィ ンジゥム、 窒化アルミニウムのうちから選ばれた少なくとも 1種以上を主成分とする平板状の 薄膜を形成することで二次^ "6導' » 5 0を作製しさらに例えば S i 02、 A 1 203、各種ガラ スなど窒化ガリウム、 窒化インジウム、 窒化アルミニウムのうちから選ばれた少なくとも 1種 以上を主成分とする薄膜より屈折率の小さい材料によりバッファ層 1 1 0を形成しその上に電 極 9 0及び 9 1を形成し該電極間に電位を印カロして高い電位が印加されている電極 9 1の部分 の二次元光導波路の屈折率を上昇させることで三次元光導波路 6 4を形成せしめた薄膜基板の
1例を示す 図である。 図 2 9には図示されていないが窒化アルミニウムを主成分とする焼 結体からなる基板 1 4とニ^ ¾光導波路 5 0及び 次元光導波路 6 4との間に 導波路より 屈折率の小さい材料、 例えば同質の窒化ガリウム、 窒化インジウム、 窒化アルミニウムのうち から選ばれた少なくとも 1種以上を主成分とするものを用いることが光伝送損失を低減化する 上で好ましい。
図 3 0は窒化アルミニウムを主成分とする焼結体からなる基板 1 4に窒化ガリウム、 窒化ィ ンジゥム、 窒化アルミニウムのうちから選ばれた少なくとも 1種以上を主成分とする薄膜 8 0 に埋め込み型のミ^光導波路 6 5が形成されている薄膜基板の 1例を示す耕見図である。 図 3 0において三^ ¾光導波路 6 5は該導波路より屈折率の小さい薄膜 8 0の内部に埋め込まれ 基板表面においてその一部が空気に接することで埋め込み型の三次元光導波路として機能する。 図 3 0において光導波路 6 5は窒化ガリウム、 窒化インジウム、 窒化アルミニウムのうちから 選ばれた少なくとも 1種以上を主成分とする薄膜 8 0に溝加工しこの溝に薄膜 8 0より屈折率 の大きい窒化ガリウム、 窒化インジウム、 窒化アルミニウムのうちから選ばれた少なくとも 1 種以上を主成分とする薄膜を積層することにより得られる。 また、 図 3 0において埋め込み型 の光導波路 6 5は窒化ガリウム、 窒化インジウム、 窒化アルミニウムのうちから選ばれた少な くとも 1種以上を主成分とする薄膜 8 0にガリウム、 インジウム、 ニオブ及びタンタルのうち から選ばれた少なくとも 1種以上の成分を含有せしめることのより薄膜 8 0より屈折率の大き い部分を薄膜 8 0の内部に形成することでも作製することができる。 この屈折率が大きくなつ た部分を光導波路 6 5として用いる。 窒化ガリウム、 窒化インジウム、 窒化アルミニウムのう ちから選ばれた少なくとも 1種以上を主成分とする薄膜 8 0にガリウム、 インジウム、 ニオブ 及びタンタルのうちから選ばれた少なくとも 1種以上の成分を含有せしめる方法として前記熱 拡散及びイオン注入などの方法を用いることができる。 すなわち窒化アルミニウムを主成分と する焼結体からなる基板 1 4に形成した窒化ガリウム、 窒化インジウム、 窒化アルミニウムの うちから選ばれた少なくとも 1種以上を主成分とする薄膜 8 0にレジストを塗布し光リソダラ フィ一により光導波路 6 5の幅の大きさだけレジストを取り除いて該薄膜表面に達する空間を 形成する。 熱拡散法では例えば上記リフトオフ法を用いて光導波路を形成できる。 すなわち、 光リソグラフィ一により光導波路 6 5の幅の大きさだけレジストを取り除いて該薄膜表面に達 する空間を形成し該空間からガリウムあるいはインジウムあるいはニオブあるいはタンタル成 分を含む薄膜をスパッ夕や真空蒸着あるいは CVDなどの方法で形成し、 その後レジストを取 り除けば窒化ガリウム、 窒化インジウム、 窒化アルミニウムのうちから選ばれた少なくとも 1 種以上を主成分とする薄膜 8 0表面には光導波路 6 5の幅だけガリウムあるいはインジウムあ るいはニオブあるいはタンタル成分を含む薄膜が残りその状態で高温加熱処理すればガリウム あるいはィンジゥムあるいはニオブあるいはタンタル成分が窒化ガリゥム、 窒化ィンジゥム、 窒化アルミニウムのうちから選ばれた少なくとも 1種以上を主成分とする薄膜 8 0中に拡散し 光導波路 6 5が該薄膜 8 0に埋め込まれた形態で形成される。 イオン注入法では例えば上記の 方法により形成されたレジス卜に形成された空間からガリゥムあるいはィンジゥムあるいは二 ォブあるいは夕ンタル成分を含むィオンを打ち込み纖熱処理を行つて光導波路 6 5が該薄膜 8 0に埋め込まれた形態で形成される。
なお、 図 3 0には図示されていないが窒化アルミニウムを主成分とする焼結体からなる基板 1 4と薄膜 8 0との間に同質の窒化ガリウム、 窒化インジウム、 窒化アルミニウムのうちから 選ばれた少なくとも 1種以上を主成分とする薄膜をさらに形成することで光伝對員失が低減化 され易くなり好ましい。
図 3 1〜図 3 3は光導波路を有する薄膜基板に電極が形成された例を示している。 なお、 図 3 1〜図 3 3において光導波路としては図 3 0で例示した埋め込み型のものを用いて記載され
ている。 本発明において上記のように電極を設け電位を印加することで該薄膜の屈折率が 化 し易いという性質を利用して光変調器、 光スィッチなどを作製することができる。 図 3 1〜図 3 3に例示された電極が形成された光導波路を有する薄膜基板はこのような機能を有する薄膜 基板の例として示されている。 埋め込み型光導波路を有する薄膜基板において、 ガリウムある いはィンジゥムの含有量の多い光導波路の領域もしくはニオブあるいはタンタル成分を含む光 導波路の領域では上記電位の印加によりさらに大きな屈折率変化得られ易い。
図 3 1は窒化アルミニウムを主成分とする焼結体からなる基板 1 4に窒化ガリウム、 窒化ィ ンジゥム、 窒化アルミニウムのうちから選ばれた少なくとも 1種以上を主成分とする薄膜 8 0 に埋め込み型の三^ ¾導波路 6 5が形成されさらに電極 1 2 0が光導 6 5を挟むように 薄膜 8 0の表面に形成されている薄膜基板の 1例を示す斜視図である。 図 3 1に示された薄膜 基板は電極に電位を印加することで屈折率を変化させて光位相の変調、 光波長の変調、 光振幅 の変調などができ光位相変調器などに使用し得る。
図 3 2は窒化アルミニウムを主成分とする焼結体からなる基板 1 4に窒化ガリウム、 窒化ィ ンジゥム、 窒化アルミニウムのうちから選ばれた少なくとも 1種以上を主成分とする薄膜 8 0 に埋め込み型の三^光導波路 6 5が形成されさらに電極 1 2 0が薄膜 8 0及び光導波路 6 5 に形成されている薄膜基板の例を示す斜視図である。 図 3 2に示された薄膜基板は電極に電位 を印加することで屈折率を変化させて光位相の変調、 光波長の変調、 光振幅の変調などができ 光位相変調器などに使用し得る。
図 3 3は窒化アルミニウムを主成分とする焼結体からなる基板 1 4に窒化ガリウム、 窒化ィ ンジゥム、 窒化アルミニウムのうちから選ばれた少なくとも 1種以上を主成分とする薄膜 8 0 に埋め込み型の三 ^光導波路 6 5が形成されさらに電極 1 2 0が光導 «6 5に形成されて いる薄膜基板の例を示す斜視図である。 図 3 3に示された薄膜基板は電極に電位を印加するこ とで屈折率を変化させて光位相の変調、光波長の変調、光振幅の変調などができ光位相変調器、 伝送路切換などの光スィッチなどに使用し得る。 '
なお、 図 3 1〜図 3 3において電極 1 2 0としてはどのような材料でも用い得るが窒化ガリ ゥム、 窒化インジウム、 窒化アルミニウムのうちから選ばれた少なくとも 1種以上を主成分と する薄膜との接合信頼性が«いなど本発明による前記の薄膜導電性材料を用いることが好まし い。 また図 3 1〜図 3 3に W¾されていないが薄膜 8 0と電極 1 2 0との間、 及び光導波路 6 5と電極 1 2 0との間に例えば S i〇2、 A 1 2〇3、各種ガラスなど薄膜 8 0及び光導波路 6 5 より屈折率の小さい材料によりバッファ層を形成することが伝送損失を低減化する上では好ま しい。
また、 図 3 1〜図 3 3には図示されていないが窒化アルミニウムを主成分とする焼結体から なる基板 1 4と薄膜 8 0との間に同質の窒化ガリウム、 窒化インジウム、 窒化アルミニウムの うちから選ばれた少なくとも 1種以上を主成分とする薄膜をさらに形成することで光伝還員失 が低減化され易くなり好ましい。
図 3 4及び図 3 5は本発明による光導波路を有する薄膜基板にさらに電気回路が同時に形成 された薄膜基板の例を示したものである。 図 3 4及び図 3 5に例示した薄膜基板は電気及び光 の両方が伝送可能な光配線基板として用いることができる。
図 3 4は窒化アルミニウムを主成分とする焼結体からなる基板 1 4に窒化ガリウム、 窒化ィ ンジゥム、 窒化アルミニウムのうちから選ばれた少なくとも 1種以上を主成分とする薄膜など からなるクラッド層 7 1が形成されその上に三^ 5導波路 6 0が形成されている薄膜基板の 1 例を示す观図である。 さらに窒化アルミニウムを主成分とする焼結体 1 4部分には電気回路 1 2が同時に形成されている。 なお、 クラッド層の屈折率は光導波路の屈折率より小さいもの であることが光の伝送損失を低減化する上で好ましい。
図 3 5は窒化アルミニウムを主成分とする焼結体からなる基板 1 4に窒化ガリウム、 窒化ィ ンジゥム、 窒化アルミニウムのうちから選ばれた少なくとも 1種以上を主成分とする薄膜 8 0 に埋め込み型の三次元光導波路 6 5が形成されている薄膜基板の 1例を示す斜視図である。 さ らに該薄膜 8 0の一部には電気回路 1 2が同時に形成されている。 図 3 5には図示されていな いが窒化アルミニウムを主成分とする焼結体からなる基板 1 4と薄膜 8 0との間に同質の窒化 ガリウム、 窒化インジウム、 窒化アルミニウムのうちから選ばれた少なくとも 1種以上を主成 分とする薄膜をさらに形成することで光伝邀員失が低減化され易くなり好ましい。
なお、 光導波路には通常 導波路の外部側面から光が導入され他の外部側面から放出され る。 図 3 0には推測される光導波路内への導入光の進行状況が点線及び矢印で示されている。 すなわち、 図 3 0に示す光導波路 6 5の側面 6 5 ' の部分から¾½導波路と薄 8 0との界 面に対して水平方向に光 6 6が導入され 光導波路内では点線で示すように魏導波路に沿つ て進行し反対側の側面から光 6 6 ' として放出されるものと思われる。
図 3 0に示した光導波路のように窒化アルミニウムを主成分とする焼結体からなる基板に形 成した窒化ガリウム、 窒化インジウム、 窒化アルミニウムのうちから選ばれた少なくとも 1種 以上を主成分とする薄膜内に作製した光導波路だけでなく、 該窒化アルミニウムを主成分とす る焼結体からなる基板に窒化ガリウム、 窒化インジウム、 窒化アルミニウムのうちから選ばれ た少なくとも 1種以上を主成分とする薄膜を直接形成することにより作製した光導波路であつ ても伝送損失は少ない。 その原因は導入される光の方向が光導波路と基板との間の界面に対し て水平方向な方向であるため、 窒化アルミニウムを主成分とする焼結体を用いても該焼結体と 上記窒化ガリウム、 窒化インジウム、 窒化アルミニウムのうちから選ばれた少なくとも 1種以 上を主成分とする薄膜との界面において該窒化アルミニウムを主成分とする焼結体による導入 光の ¾ 、 及び該焼結体中の結晶粒子や粒界あるレ ^は添加物などによる粒界相による光の吸収 や散乱が生じにくいことも伝 員失が小さい原因であろうと思われる。
このような光導波路内に導入された光の挙動は図 3 0に例示する本発明による三 光導波 路だけでなく二次元光導波路においても同様であると思われる。
本発明による光導波路の大きさはどのようなものでも用いることができ、 幅として 0 . 5 m以上、 深さ (あるいは厚み) は 0 . 1 m以上であれば十分機能する。 図 2 4〜図 3 5に例 示した本発明による三^ £導波路において通常幅 1 m以上、 深さ (あるいは厚み) は 0 . 3 m以上であれば十分機能する。
本発明により窒化アルミニウムを主成分とする焼結体からなる基板、 あるいは該窒化アルミ 二ゥムを主成分とする焼結体からなる基板に窒化ガリウム、 窒化インジウム、 窒化アルミニゥ ムのうちから選ばれた少なくとも 1種以上を主成分とする無定形、 多結晶、 配向性多結晶、 単 結晶など各種結晶状態の薄膜を形成した薄膜基板、 を用いることで発光効率に優れた発光素子 が作製し得る。 このような基板上へ形成される発光素子は通常トリメチルガリウム、 トリメチ ルインジウム、 トリメチルアルミニウムなどの有機金属化合物や塩化ガリウム、 塩化インジゥ ム、 塩化アルミニウムなどのハロゲン化物とアンモニアなどの窒素含有化合物とを主な原料と して、 その他に S i H、 S i Hなどのシラン化合物ゃジメチルマグネシウムやビス一シクロべ ンタジェニルマグネシウムなどの有機金属化合物をドーピング元素用の原料として前記 MO C VD法、 MOV P E法、ハイドライド V P E法、クロライド V P E法を含むハライド V P E法、 プラズマ C VD法、 その他の C VD (化学細 成長) 法、 MB E ( 泉エピタキシー) 法、 あるいはあらかじめ形成した目的成分を含む固体材料を原料としエキシマレーザーなどを 用いたレ一ザ一アブレーション法、 P L D ひ レスレーザーデポジション:ノ\°ルスレーザー分 解) 法、 あるいはスパッタリング法、 イオンプレーティング法、 蒸着法などによって目的とす る化学成分の少なくとも一部を含有する化合物や単体を化学的物理的に しあるいは せ
ずそのままの状態で気体、 イオンあるいは奸線とし建前記以外の化合物と反応させあるい は反応させずいったん目的とする化学成分を含む成分を気相とした後目的とする組成の薄膜を ェピタキシャル成長させることで製造される。 発光素子の構成は通常基板上に上記に例示した 原料から窒化ガリウム、 窒化インジウム、 窒化アルミニウムのうちから選ばれた少なくとも 1 種以上を主成分とするェピタキシャル成長した各種組成の薄膜を用い、 それぞれ 5 nm〜 数 m程度の厚みで少なくとも N型半導体層及び量子井戸構造などからなる発光層及び P型半 導体層を積層して発光機能を発現させたものである。 上記 N型半導体層及び発光層及び P型半 導体層は発光層の発光を発現させるための 的構成要素である。 本発明は窒化アルミニウム を主成分とする焼結体あるいは該焼結体を基板状としその上に少なくとも上記の N型半導体層 及び発光層及び P型半導体層を積層して積層体となし発光素子を構成したことに特徴がある。 上記 N型半導体層は通常主成分以外に S i、 G e、 S e、 T e、 Oなどのドナー形成ド一ピン グ剤を含む。 また、 P型半導体層は通常主成分以外に Mg、 B e、 C a、 Z n、 C d、 Cなど のァクセプタ一形成ドーピンク を含む。発光素子の 的構成要素である上記 N型半導体層、 発光層、 及び P型半導体層は通常ェピタキシャル成長した単結晶薄膜が用いられるが、 該単結 晶以外に纖無定形、 多結晶、 配向性多結晶など各種結晶状態のものも用い得る。 その他、 発 光素子の構成要素として上記 N型半導体層、 発光層、 及び P型半導体層以外に基板と該 N型半 »本層、あるいは P型半難層との間の緩衝層ひ ソファ層)も 、要に応じて用いられる。 該バッファ層は通常窒化ガリウム、 窒化インジウム、 窒化アルミニウムのうちから選ばれた少 なくとも 1種以上を主成分とする薄膜により形成される。 該バッファ層を構成する薄膜は無定 形、 多結晶、 配向性多結晶、 単結晶など各種結晶状態のものが用い得るが、 通常は無定形、 多 結晶、 配向性多結晶のうちから選ばれる少なくともいずれかの結晶状態のものが用いられる。 また、 ェピタキシャル成長した単結晶のものも用いることができる。 このようような発光素子 に数 mW〜数 度の直流電力を注入することで緑青色、 あるいは青色、 あるいは青紫色、 あ るいは紫外線、 あるいは例えば YAG (ィッ卜リゥムアルミニウムガ一ネット) を主成分とす る蛍光体などを併用して白色などの発光 (L i g h t Em i s s i o n) や、 あるいはレ一 ザ一発振による光が得られる。 上記発光素子を作製するに際して無定形、 多結晶、 配向性多結 晶、 単結晶など各種結晶状態の薄膜形成〖雄常 4 0 0 °C〜1 3 0 0 °C程度の基板 で行われ る。 あるいは纖室温〜 4 0 0 °Cの比較的低温の基板髓で行われる。 基板? を低温で行う ことは基板に形成する薄膜の結晶成長を抑制し結晶方位を制御するときなどに有効な場合があ る。 なお、 Mgなどの P型半導体を形成するためのドーピング元素は単結晶薄膜形成後に水素 をできるだけ含まない窒素などの非酸化性雰囲気中 4 0 0 以上でァニーリングを行うことが より低抵抗の P型単結晶薄膜を形成する上で好ましい。 本発明は窒化アルミニウムを主成分と する焼結体からなる基板上に直接形成される窒化ガリウム、 窒化インジウム、 窒化アルミニゥ ムのうちから選ばれた少なくとも 1種以上を主成分とする無定形、 多結晶、 配向性多結晶、 単 結晶など各種結晶状態の薄膜が P型半導体層、 あるいは N型半導体層、 あるいは量子井戸構造 を有する発光層、 として発光素子を構成する層の一部として形成されているものも含まれる。 また、 本発明は窒化アルミニウムを主成分とする焼結体からなる基板上に直接形成される上記 窒化ガリウム、 窒化インジウム、 窒化アルミニウムのうちから選ばれた少なくとも 1種以上を 主成分とする無定形、 多結晶、 配向性多結晶、 単結晶など各種結晶状態の薄膜を用いた発光素 子も含まれる。
なお、 通常発光効率を高めるために発光素子を構成する少なくとも N型半導体層、 発光層、 P型半導体層、 の各薄膜層はェピタキシャル成長した窒化ガリウム、 窒化インジウム、 窒化ァ ルミニゥムのうちから選ばれた少なくとも 1種以上を主成分とする結晶性の高い単結晶薄膜で あることが好ましい。 本発明においてこの発光素子を構成する単結晶薄膜の結晶性をより高め
るために該単結晶薄膜を形成する前にあらかじめ窒化アルミニウムを主成分とする焼結体から なる基板に形成される窒化ガリウム、 窒化インジウム、 窒化アルミニウムのうちから選ばれた 少なくとも 1種以上を主成分とする薄膜を形成することが好ましいが、 この窒化アルミニウム を主成分とする焼結体からなる基板にあらかじめ形成する薄膜は単結晶に限らず無定形、 多結 晶、 配向性多結晶など、 どのような結晶状態のものであっても用いることができる。
また、 上記 N型半導体層は単一層だけでなく電極と接 するためのコンタク卜層及び発光層 と接続するクラッド層など少なくとも 2層以上の薄膜層から構成されるものも好適に使用され る。 また上記 N型半導体層を構成するコンタク卜層及びクラッド層は単一層だけでなくそれぞ れ少なくとも 2層以上の薄膜層から構成されるものも好適に使用される。 発光層はへテロ構造 やダブルへテロ構造、 あるいは単一量子井戸構造などのように単一層だけでなく、 例えば多重 *ΐ井戸構造のように少なくとも 2層以上の薄膜層から構成されるのものも好適に使用される。 また Ρ型半導体層は単一層だけでなく電極と接続するためのコンタクト層及び発光層と接続す るクラッド層など少なくとも 2層以上の薄膜層から構成されるものも好適に使用される。 上記 Ρ型半導体層を構成するコンタク卜層及びクラッド層は単一層だけでなくそれぞれ少なくとも 2層以上の薄 から構成されるものも好適に使用される。
また、 基板上に発光素子を形成していく場合、 基板に直ちにコンタクト層を形成せず基板と コンタクト層との間に通常窒化ガリウム、 窒化インジウム、 窒化アルミニウムのうちから選ば れた少なくとも 1種以上を主成分とする薄膜からなる緩衝層 ひ ッファ層) を形成しその後 Ν 半 本特性あるいは Ρ型半導体特性を有するコンタクト層を形成することが好ましい。 該バッ ファ層を形成する薄膜は上記のように窒化ガリウム、 窒化インジウム、 窒化アルミニウムのう ちから選ばれた少なくとも 1種以上を主成分とする無定形、 多結晶、 配向性多結晶、 単結晶な どのうちから選ばれた少なくともいずれかの結晶状態のものが用レゝ得るが通常無定形、多結晶、 配向性多結晶などの結晶状態のものが用いられる。 また、 ェピタキシャル成長した結晶性の高 い単結晶薄膜であっても用いることができる。 また、 該バッファ層はドーピング元素を含まな い状態でも用い得るしドーピング元素を含有せしめて Ν半導体特性あるいは Ρ型半導体特性を 有する状態でも好適に用い得る。
本発明による発光軒の特徴はその基板に窒化アルミニウムを主成分とする焼結体を用いた 点にある。 さらに詳しく言えば、 本発明による発光素子を作製するための基板として、 窒化ァ ルミ二ゥムを主成分とする焼結体をそのまま基板として用いたものと、 窒化アルミニウムを主 成分とする焼結体を基板としてその上に窒化ガリウム、 窒化インジウム、 窒化アルミニウムの うちから選ばれた少なくとも 1種以上を主成分とする無定形、 多結晶、 配向性多結晶、 単結晶 などのうちから選ばれた少なくともいずれかの結晶状態の薄膜を少なくとも 1層以上形成して 薄膜基板としたもの、 という少なくとも 2種類の基板がある。 さらに該薄膜基板には、 窒化ァ ルミ二ゥムを主成分とする焼結体からなる基板にあらかじめ窒化ガリウム、 窒化インジウム、 窒化アルミニウムのうちから選ばれた少なくとも 1種以上を主成分とする無定形、 多結晶、 配 向性多結晶、 単結晶などのうちから選ばれた少なくともいずれかの結晶状態の薄膜を少なくと も 1層以上形成し、 さらにその上に窒化ガリウム、 窒化インジウム、 窒化アルミニウムのうち から選ばれた少なくとも 1種以上を主成分とする単結晶薄膜を少なくとも 1層以上形成して薄 膜基板としたものも含まれる。
本発明による窒化アルミニウムを主成分とする焼結体を基板として使用して作製した発光素 子は «からのサフアイァなどの単結晶基板を使用して作製された発光 の発光効率が通常
2 %〜 8 %程度であるのに対して少なくとも同等あるいは最大 4〜 5倍以上の発光効率のもの が得られる。 すなわち本発明による発光素子は入力された電力の最大 3 0〜4 0 %以上が発光 素子外部へ光エネルギーとして放出し得る。なお、本発明における発光効率とは前記のように、
発光 ¾ΐを駆動させるために該素子に加えられた電力 (電気工ネルギー) と実際発光^?によ つて光に変換され発光素子の外部へ放出された光出力 (光エネルギー) との百分率比である。 例えば発光効率が 4 0 %ということは、 例えば発光層が G a N/ I n N系の量子井戸構造など で構成される発光素子を用い、 該素子に電圧 3. 6ポルト、 電流 5 0 0 mAを注入して睡さ せたとき光出力として 7 2 O mWが得られるということである。
本発明による窒化アルミニウムを主成分とする焼結体からなる基板を用いて作製される発光 素子が高い発光効率を有する原因について 、ずしも明確ではないが、 ^?を構成する窒化ガ リウム、 窒化インジウム、 窒化アルミニウムのうちから選ばれた少なくとも 1種以上を主成分 とする高い結晶性の単結晶薄膜が窒化アルミニウムを主成分とする焼結体からなる基板に形成 できるようになりこのような結晶性に優れた単結晶薄膜を発光素子の少なくとも N型半導体層、 発光層、 P型半 本層、 として使用できるようになったことが第一番目に重要なことであるこ とは間違いない。 しかし、 本発明による発光素子がサファイアなどの単結晶基板を用いたもの より高い発光効率を有する原因としてはそれだけではなぐ 基板として用いる窒化アルミニゥ ムを主成分とする焼結体としての微構造に起因することが大きく寄与していると思われる。 本願発明者が検討したところサファイア基板上にも窒化アルミニウムを主成分とする焼結体 からなる基板と同様にミラ一指数 ( 0 0 2) の格子面の X線回折ロッキングカーブの半値幅が 少なくとも 3 0 0秒以下の結晶性を有する窒化ガリウム、 窒化インジウム、 窒化アルミニウム のうちから選ばれた少なくとも 1種以上を主成分とする単結晶薄膜が形成できる。 «サファ ィァなどの基板上に要すればバッファ層をまず形成した後このような結晶性に優れた単結晶薄 膜を少なくとも N型半導体層、 発光層、 P型半導体層、 の各層が構成されるよう形成すること で発光素子が製造されてきた。 また、 一方本発明において今まで説明してきたように、 窒化ァ ルミニゥムを主成分とする焼結体からなる基板にも«からのサフアイァなどの単結晶基板と 少なくとも同等あるいはそれ以上に結晶性の優れた窒化ガリウム、 窒化インジウム、 窒化アル ミニゥムのうちから選ばれた少なくとも 1種以上を主成分とする単結晶薄膜が形成でき、 該単 結晶薄膜は発光素子として機能するよう少なくともそれぞれ N型半導体層、 発光層、 P型半導 体層、 あるいはバッファ層として形成することができる。 本発明において、 窒化ガリウム、 窒 化インジウム、 窒化アルミニウムのうちから選ばれた少なくとも 1種以上を主成分とする薄膜 を用いて同じ騰成で発光素子を作製したとき、 基板として縣からのサファイアなどを用い た場合と窒化アルミニウムを主成分とする焼結体を用いた場合とで比較したとき、 窒化アルミ ニゥムを主成分とする焼結体からなる基板を用いた場合は^ |ξからのサファイアなどを基板と して用いた場合と少なくとも同等かあるいは最大 4倍〜 5倍以上高い。 具体的にいえば、 基板 として ¾έ¾からのサフアイァ及び窒化アルミ二ゥムを主成分とする焼結体を用い、 これらの基 板に窒化ガリウム、 窒化インジウム、 窒化アルミニウムのうちから選ばれた少なくとも 1種以 上を主成分とする薄膜で同じ構成の Ν型半導体層、 発光層、 Ρ型半導体層、 あるいは必要に応 じてバッファ層を有する発光素子を作製したとき、 発光 を構成するこれらの薄 のうち 少なくとも該 N型半導体層、 発光層、 P型半導体層を構成する薄膜がミラ一指数 ( 0 0 2 ) の 格子面の X線回折ロッキングカーブの半値幅として例えば同じ 1 5 0秒の結晶性を有する単結 晶であったとしても、 窒化アルミニウムを主成分とする焼結体からなる基板を用いて作製した 発光素子の発光効率が従来からのサファイアを基板として用レゝた場合と比較して少なくとも同 等か最大 4倍〜 5倍以上高い。
したがって、 上記のように発光効率の高い発光素子を作製する場合、 窒化アルミニウムを主 成分とする焼結体からなる基板に結晶性の優れた単結晶薄膜が形成できるということはまず第 一番目に重要な条件ではあっても、 それだけでは窒化アルミニウムを主成分とする焼結体から なる基板を用いて作製した発光素子の発光効率が従来からのサファイアなどの基板と少なくと
も同等かそれよりもさらに高いということにはならないと思われる。 やはり、 光吸収端が波長
2 0 0 nm付近にある、 あるいは屈折率が窒化ガリウムに近いなど窒化アルミニウムという物 質が元来有する特性とともに、 窒化アルミ二ゥムを主成分とする焼結体は窒化アルミ二ゥムを 主成分とする結晶粒子あるいは粒界相が焼き固まって構成されているという微構造を有するた めサフアイァのような透明体と異なり焼結体と薄膜との界面あるいは焼結体と外部空間との界 面で光の反射が生じにくいためと推測される。 すなわち、 このような光反射が生じにくいので 発光軒から発せられた光のうち直接上記焼結体と薄膜との界面に照射されたもの、 あるいは 発光素子を構成している薄膜のうち基板側でなく外部空間と直接接している薄膜面から反射さ れて上記界面に照射された光も、 ほとんど反射されることなく窒化アルミニウムを主成分とす る焼結体内部へ侵入しさらに該窒化アルミニウムを主成分とする焼結体と外部空間との界面に 達した光は素子外部へと放出されるものと思われる。
サフアイァ基板と窒化アルミニゥムを主成分とする焼結体からなる基板との) 過性を比較 したとき窒化アルミ二ゥムを主成分とする焼結体からなる基板の場合は最も優れているもので も波長 2 1 0〜2 2 0 nmまでの光に対して聖性を示し、 波長 3 3 0 nmの光で 8 0 %以上 の ¾¾1率を示すのに対してサファイア基板の場合通常波長 1 5 O nm付近の紫外領域まで透 明で) ¾¾1率も、波長 2 0 0 nm〜4 5 0 0 nmの範囲で 8 0 %〜 9 0 %でありさらに透明体で あるので光は直線的に ¾i し易く、 したがって^ 性の面ではサフアイァ基板の方が窒化ァ ルミ二ゥムを主成分とする焼結体からなる基板よりも優れていると思える。 したがって光透過 性の面から見ると発光素子の発光層から発せられた光はサファイア基板を用いた方が窒化アル ミニゥムを主成分とする焼結体からなる基板よりも^?の外部へより多く放出されると思われ るが実際はその逆になつている。
また、 窒化アルミニウムを主成分とする焼結体のうち mi性のないものを基板として用い たときでも該基板上に形成される発光素子の発光効率はサファイア基板と同等以上であつたの で、 おそらく発光軒の発光層から発せられた光はサファイア基板と薄膜との界面あるいはサ フアイァ基板と外部空間との界面で反射されサフアイァ基板を殆ど ¾iしないものと思われる。 言い換えれば、 サフアイァ基板を用いた場合おそらく上記各界面で発光素子の発光層から発せ られた光は反射されて素子内部へ戻されサファイア基板を ¾iしては素子外部へ放出されにく いものと撤則される。 また、 発光^?から発せられた光のうち発光素子を構成している薄膜の うちサフアイァ基板側でなく外部空間と直接接している薄膜面から反射されて上記各界面に照 射された光もほとんどのものは反射され再び外部空間と直接接している薄膜面に達し、 該薄膜 面でまた反射されるという繰り返えしが生じ、 その結果として該薄膜面から外部へ放出される 光も 性を有しない窒化アルミニウムを主成分とする焼結体を基板として用いた場合より もかえって減少し易いのではないかと推測される。
発光素子の外形の大きさは 0. 0 5 mm角〜 1 0 mm角程度で通常は 0. 1 mm角〜 3 mm 角程度であり、 発光素子を構成する薄膽の厚みは合計すると 0 · 5 m〜 5 0 m程度で通 常は l m〜2 O m程度である。 また、 発光^?の発光層は面形状であり該発光層から発せ られた光は 0. 5 m〜 5 0 m程度の ί離をおいて垂直に対峙する基板面に照射されると思 われるのでもともとは基板と発光素子を構成する薄膜との界面で全反射などの現象は生じにく いと思われるが、 サフアイァ基板の場合波長 6 5 0 nmにおいて屈折率が 1 . 7 6〜 1. 7 8 と薄膜を構成する窒化ガリウム、 室化インジウム、 窒化アルミニウムと比べて低く、 さらに単 結晶であるため粒界や粒界相などはなく均質であり基板表面の平滑性も高いことなどが原因と なって上記の界面における反射が生じ易くなるものと思われる。 また、 上記のように窒化アル ミニゥムを主成分とする焼結体のうち光透過性のないものを基板として用いたものでも該基板 上に形成される発光素子の発光効率はサファイア基板を用いたものと同等かあるいはさらに優
れていたので従来から云われているように格子不齡ゃ熱膨張率の違いなどによる薄膜中の転 位あるいはひずみがサフアイァ基板の場合は多いことも発光効率が低い原因であろうと推測さ れた。
それに対して基板として窒化アルミニウムを主成分とする焼結体を用いた場合、 窒化アルミ 二ゥムの屈折率は波長 6 5 0 nmにおいて 2. 0 0〜 2. 2 5であり発光素子を構成する窒化 アルミニウム以外の窒化ガリウム、 窒化インジウムと比較的近く、 発光素子を構成する薄膜と の界面には窒化アルミニウムを主成分とする焼結体中の窒化アルミニウムを主成分とする結晶 粒子や粒界あるいは添加物などによる粒界相が存在し均質でなく基板表面の平滑性もサフアイ ァに比べて通常は小さいので発光層から発せられた光の反射がより一層生じにくく窒化アルミ 二ゥムを主成分とする焼結体中に発光層から発せられた光の多くが進入可能であることが発光 効率向上の大きな原因であろうと搬則される。 また、 窒化アルミニウムを主成分とする焼結体 は透明体と異なり直線的な光透過性は低くても光 ¾ϋ率としては 8 0 %以上と比較的高いもの が ®tできるのでこのような窒化アルミニウムを主成分とする焼結体中に進入した発光^?の 発光層から発せられた多くの光が該窒化アルミニウムを主成分とする焼結体を邏して発光素 子外部へと放出されることもサフアイァ基板に比べて発光効率が飛躍的に高まった大きな原因 であろうと推測される。
また、上記のように発光素子の外形の大きさは 0 · 0 5 mm角〜 1 0 mm角程度で通常は 0 · 1 mm角〜 3 mm角程度であり、 発光 ¾Tを構成する薄 の厚みは合計すると 0. 5 m〜 5 0 m程度で通常は 1 m〜2 0 m程度である。 通常発光軒に形成されている発光層は 面形状であり該発光層から発せられた光は 0. 5 m〜 5 0 xm程度の ί瞧をおいて垂直に対 峙する基板面に照射されると思われるのでもともとは基板と発光素子を構成する薄膜との界面 で全反射などの現象は生じにくい構造であることも基板として窒化アルミニウムを主成分とす る焼結体がより有効に機能する大きな要因であると思われる。
さらに窒化アルミニウムを主成分とする焼結体を用いた基板の熱伝導率はサファイア基板に 比べて 5倍〜 1 0倍と大きいのでたとえ一部の光が素子内部に閉じ込めら熱エネルギーに変わ つたとしても速やかに発光素子の外部へ放出されるため素子の温度上昇が抑制されるので素子 の温度上昇による発光効率の低下がないことも要因の一つであろうと思われる。
本発明において、 上記発光素子を作製するための基板として用いられる窒化アルミニウムを 主成分とする焼結体は、 該発光素子の構成要素である少なくとも Ν型半導体層、 発光層、 Ρ型 半 本層を形成する窒化ガリウム、 窒化インジウム、 窒化アルミニウムのうちから選ばれた少 なくとも 1種以上を主成分とする薄膜がェピタキシャル成長した単結晶として形成しうるもの であればどのようなものでも用いることができる。 言い換えれば、 以下に述べる方法により窒 化ガリウム、 窒化インジウム、 窒化アルミニウムのうちから選ばれた少なくとも 1種以上を主 成分とするェピタキシャル成長した単結晶薄膜が形成できるものであればどのような窒化アル ミニゥムを主成分とする焼結体であっても発光素子を作製するための基板として用いることが できる。
すなわち、 1 ) 窒化アルミニウムを主成分とする焼結体をそのまま基板として用い、 その上 に直接発光素子を構成する窒化ガリウム、 窒化インジウム、 窒化アルミニウムのうちから選ば れた少なくとも 1種以上を主成分とするェピタキシャル成長した単結晶薄膜を Ν型半導体層、 発光層、 Ρ型半導体層、 として積層し発光素子を作製していく方法である。 この方法において 要すれば窒化ガリゥム、 窒化ィンジゥム、 窒化アルミニゥムのうちから選ばれた少なくとも 1 種以上を主成分とする薄膜からなるバッファ層をまず基 に形成し、その上に Ν型半導体層、 発光層、 Ρ型半導体層を積層して発光素子を作製していくことが望ましい。
また、 2 ) 窒化アルミニウムを主成分とする焼結体を基板として作製し、 該基板の上にあら
かじめ窒化ガリウム、 窒化インジウム、 窒化アルミニウムのうちから選ばれた少なくとも 1種 以上を主成分とする無定形、 多結晶、 配向性多結晶、 単結晶のうちから選ばれた少なくともい ずれかの結晶状態を有する薄膜を少なくとも 1層以上形成して薄膜基板とし、 その上に発光素 子を構成する窒化ガリウム、 窒化インジウム、 窒化アルミニウムのうちから選ばれた少なくと も 1種以上を主成分とするェピタキシャル成長した単結晶薄膜を N型半導体層、 発光層、 P型 半導体層、 として積層し発光素子を作製していく方法である。 上記薄膜基板を用いて発光素子 を作製していく場合、 該薄膜基板に形成されている薄膜層の少なくとも一部を発光素子が機能 するための構成要素として用いることも可能である。 この方法において薄膜基板の上に要すれ ぱ窒化ガリウム、 窒化インジウム、 窒化アルミニウムのうちから選ばれた少なくとも 1種以上 を主成分とする薄膜からなるバッファ層をまず形成し、 その上に N型半導体層、 発光層、 P型 半導体層を積層して発光素子を作製していくことが ましい。 ,
また、 3 ) 窒化アルミニウムを主成分とする焼結体を基板として作製し、 該基板の上にあら かじめ窒化ガリウム、 窒化インジウム、 窒化アルミニウムのうちから選ばれた少なくとも 1種 以上を主成分とする無定形、 多結晶、 配向性多結晶、 単結晶のうちから選ばれた少なくともい ずれかの結晶状態を有する薄膜をあらかじめ少なくとも 1層以上形成し、 その上にさらに窒化 ガリウム、 窒化インジウム、 窒化アルミニウムのうちから選ばれた少なくとも 1種以上を主成 分とする単結晶薄膜を少なくとも 1層以上形成して薄膜基板とし、 その上に発光素子を構成す る窒化ガリウム、 窒化インジウム、 窒化アルミニウムのうちから選ばれた少なくとも 1種以上 を主成分とするェピタキシャル成長した単結晶薄膜を N型半導体層、 発光層、 P型半導体層、 として積層し発光素子を作製していく方法である。 上記薄膜基板を用いて発光素子を作製して いく場合、 該薄膜基板に形成されている薄膜層の少なくとも一部を発光素子が機能するための 構成要素として用いることも可能である。 この方法において薄膜基板の上に要すれば窒化ガリ ゥム、 窒化インジウム、 窒化アルミニウムのうちから選ばれた少なくとも 1種以上を主成分と する薄膜からなるバッファ層をまず形成し、 その上に N型半導体層、 発光層、 P型半導体層を 積層して発光素子を作製していくことが ましい。
上記 1 ) 〜3 ) で示した方法のなかで、 2) 〜3 ) に示した窒化アルミニウムを主成分とす る焼結体を基板とし該基板にあらかじめ窒化ガリウム、 窒化インジウム、 窒化アルミニウムの うちから選ばれた少なくとも 1種以上を主成分とする無定形、 多結晶、 配向性多結晶、 単結晶 のうちから選ばれた少なくともいずれかの結晶状態を有する薄膜を形成したものを薄膜作製用 基板として用いることが発光効率の優れた発光素子を作製する上で好ましい。 通常このような 薄膜基板を用いることで発光効率 1 0 %以上の発光素子が作製し得る。 さらに、 基板に形成す る窒化ガリウム、 窒化インジウム、 窒化アルミニウムのうちから選ばれた少なくとも 1種以上 を主成分とする薄膜を少なくとも 2層以上とし、 該 2層以上の薄膜のうち表面のものを単結晶 とした基板を用いれば、 基板にあらかじめ形成する薄膜の結晶状態に関係なくその上には発光 効率に優れた発光軒を容易に作製し得るので好ましい。 すなわち、 窒化アルミニウムを主成 分とする焼結体を基板として用いる &、その上にあらかじめ窒化ガリウム、窒化インジウム、 窒化アルミニウムのうちから選ばれた少なくとも 1種以上を主成分とする無定形、 多結晶、 配 向性多結晶、 単結晶のうちから選ばれた少なくともいずれかの結晶状態を有する薄膜を少なく とも 1層以上形成し、 その上にさらに窒化ガリウム、 窒化インジウム、 窒化アルミニウムのう ちから選ばれた少なくとも 1種以上を主成分とする単結晶薄膜を少なくとも 1層以上形成した 基板を用いれば、 その上には発光効率 1 2 %以上の発光素子を容易に作製し得る。 特に発光素 子として発光効率が 1 5 %以上のものを作製していく場合、 あるいは発光素子としてレーザー ダイオードを作製する場合にはこのような表面に単結晶薄膜を形成した薄膜基板を用いること が有効である。
上記薄膜基板を用いて発光素子を作製していく場合、 該薄膜基板に形成されている薄膜層の 少なくとも一部を発光素子が機能するための構成要素として用いることも可能である。 この方 法において薄膜基板の上に要すれば窒化ガリウム、 窒化インジウム、 窒化アルミニウムのうち から選ばれた少なくとも 1種以上を主成分とする薄膜からなるバッファ層をまず形成し、 その 上に N型半 #ί本層、発光層、 Ρ型半導体層を積層して発光素子を作製していくことが ましい。 また本発明による薄膜基板を用いて発光素子を作製していく場合、 上記バッファ層を特に設け ずに発光素子を作製することも可能である。
本発明において、 このような特性を有する窒化アルミニウムを主成分とする焼結体を用いた 基板に形成される薄膜の結晶性などの性状について、 鍵化アルミニウムを主成分とする焼結 体の組成、 績、 窒化アルミニウム成分の含有量、 光 ¾i性、 焼結体結晶粒子の大きさ、 導通 ビアの有無などとの関係、 あるいは 化アルミニウムを主成分とする焼結体を基板としたと きの表面平滑性、 基板の厚みなどとの関係、 あるいは 化アルミニウムを主成分とする焼結 体からなる基板に形成される薄膨冓成、 薄 J»みなどとの関係について今まで説明してきた。 本発明において、窒化アルミニウムを主成分とする鶴吉体は窒化ガリウム、窒化インジウム、 窒化アルミニウムのうちから選ばれた少なくとも 1種以上を主成分とする単結晶薄膜が形成で きるものであればどのような組成のものであっても該窒化アルミニウムを主成分とする焼結体 を基板として用いることにより優れた発光効率を有する発光素子が作製し得る。 通 から のサファイアなどの基板を用いて作製される発光素子の発光効率と比べて少なくとも同等か、 最大 4〜 5倍以上に改善された発光効率を有する発光素子を提供し得る。 通常窒化アルミニゥ ム成分を少なくとも 2 (H權%以上含む窒化アルミニウムを主成分とする焼結体を基板として 用いることが好ましく «からのサフアイァなどの基板を用いて作製される発光素子の発光効 率と比べて少なくとも同等か、 最大 4〜 5倍以上に改善された発光素子を作製し得る。
より詳しく言えば、 1 )窒化アルミニウムを主成分とする焼結体をそのまま基板として用い、 その上に直接要すれば窒化ガリゥム、 窒化ィンジゥム、 窒化アルミニゥムのうちから選ばれた 少なくとも 1種以上を主成分とする薄勵ゝらなるバッファ層をまず形成し、 その上に窒化ガリ ゥム、 窒化インジウム、 窒化アルミニウムのうちから選ばれた少なくとも 1種以上を主成分と するェピタキシャル成長した単結晶薄膜を N型半導体層、 発光層、 P型半導体層、 として積層 していくことで発光素子を作製していく方法の ±給、 通常窒化アルミニウム成分を 5 0髓% 以上含む窒化アルミニゥムを主成分とする焼結体を用いることが好ましく発光効率が少なくと も 1 0 %以上の発光素子を作製し得る。
また、 2) 窒化アルミニウムを主成分とする焼結体を基板として作製し、 その上にあらかじ め窒化ガリウム、 窒化インジウム、 窒化アルミニウムのうちから選ばれた少なくとも 1種以上 を主成分とする無定形、 多結晶、 配向性多結晶、 単結晶のうちから選ばれた少なくともいずれ 力 結晶状態を有する薄膜を少なくとも 1層以上形成して薄膜基板とし、 該薄膜基板の上に要 すれば窒化ガリゥム、 窒化ィンジゥム、 窒化アルミ二ゥムのうちから選ばれた少なくとも 1種 以上を主成分とする薄膜からなるバッファ層をまず形成し、 窒化ガリウム、 窒化インジウム、 窒化アルミニウムのうちから選ばれた少なくとも 1種以上を主成分とするェピタキシャル成長 した単結晶薄膜を Ν型半導体層、 発光層、 Ρ型半導体層、 として積層して発光素子を作製して いく方法、 及び 3) 窒化アルミニウムを主成分とする焼結体を基板として作製し、 その上にあ らかじめ窒化ガリウム、 窒化インジウム、 窒化アルミニウムのうちから選ばれた少なくとも 1 種以上を主成分とする無定形、 多結晶、 配向性多結晶、 単結晶のうちから選ばれた少なくとも いずれかの結晶状態を有する薄膜を少なくとも 1層以上形成し、その上にさらに窒化ガリゥム、 窒化インジウム、 窒化アルミニウムのうちから選ばれた少なくとも 1種以上を主成分とする単 結晶薄膜を少なくとも 1層以上形成して薄膜基板とし、 該薄膜基板の上に要すれば窒化ガリゥ
ム、 窒化インジウム、 窒化アルミニウムのうちから選ばれた少なくとも 1種以上を主成分とす る薄膜からなるバッファ層をまず形成し、 その上に窒化ガリウム、 窒化インジウム、 窒化アル ミニゥムのうちから選ばれた少なくとも 1種以上を主成分とするェピタキシャル成長した単結 晶薄膜を N型半導体層、発光層、 P型半 本層、として積層して発光素子を作製していく方法、 という上記 2) 〜3) で説明した方法により発光素子を作製する場合でも、 発光効率が少なく とも 1 0 %以上の発光素子を作製し得る。
上記 1 ) 〜3) に示した方法において通常窒化アルミニウム成分を 2 0碰%以上含む窒化 アルミ二ゥムを主成分とする焼結体を基板として用いることが好ましく発光効率が少なくとも 1 0 %以上の発光素子を作製し得る。 窒化アルミニウム成分を 2 0体積%以上含む窒化アルミ 二ゥムを主成分とする能結体を基板として用いる場合、通常該基板にあらかじめ窒化ガリウム、 窒化ィンジゥム、 窒化アルミニウムのうちから選ばれた少なくとも 1種以上を主成分とする無 定形、 多結晶、 配向性多結晶のうちから選ばれた少なくともいずれかの結晶状態を有する薄膜 を形成した基板を用いることが好ましい。 窒化アルミニウム成分を 2 0髓%以上含む窒化ァ ルミ二ゥムを主成分とする焼結体を基板として用いる場合、 該基板にあらかじめ形成する窒化 ガリウム、 窒化インジウム、 窒化アルミニウムのうちから選ばれた少なくとも 1種以上を主成 分とする薄膜力 向性多結晶の結晶状態を有するものであれば、 その上には発光効率が少なく とも 1 2 %以上の発光素子を作製し得る。 また、 窒化アルミニウム成分を 2 0髓%以上含む 窒化アルミニウムを主成分とする焼結体を基板として用いる場合、 窒化ガリウム、 窒化インジ ゥム、 窒化アルミニウムのうちから選ばれた少なくとも 1種以上を主成分とする薄膜を少なく とも 2層以上形成し、 該 2層以上の薄膜のうち表面のものが単結晶であれば、 基板にあらかじ め形成する薄膜の結晶状態に関係なくその上には発光効率が少なくとも 1 2 %以上の発光素子 を作製し得る。 すなわち、 窒化アルミニウム成分を 2 0髓%以上含む窒化アルミニウムを主 成分とする焼結体を基板として用いる場合、 その上にあらかじめ窒化ガリウム、 窒化インジゥ ム、窒化アルミニウムのうちから選ばれた少なくとも 1種以上を主成分とする無定形、多結晶、 配向性多結晶のうちから選ばれた少なくともいずれかの結晶状態を有する薄膜を少なくとも 1 層以上形成し、 その上にさらに窒化ガリウム、 窒化インジウム、 窒化アルミニウムのうちから 選ばれた少なくとも 1種以上を主成分とする単結晶薄膜を少なくとも 1層以上形成した基板を 用いれば、 その上には発光効率が少なくとも 1 2 %以上の発光素子を作製し得る。 また、 窒化 アルミニウム成分を 5 C機%以上含む窒化アルミニウムを主成分とする焼結体を基板として 用いる場合、 そのまま発光^?作製用基板として用いることができるが、 通常該基板にあらか じめ窒化ガリウム、 窒化インジウム、 窒化アルミニウムのうちから選ばれた少なくとも 1種以 上を主成分とする単結晶、 無定形、 多結晶、 配向性多結晶のうちから選ばれた少なくともいず れかの結晶状態を有する薄膜を形成したものを用いることが好ましい。 窒化アルミニウム成分 を 5 0体積%以上含む窒化アルミニウムを主成分とする焼結体を基板として用いる場合、 該基 板にあらかじめ形成する窒化ガリウム、 窒化インジウム、 窒化アルミニウムのうちから選ばれ た少なくとも 1種以上を主成分とする薄膜が無定形、 多結晶、 配向性多結晶のうちから選ばれ た少なくともいずれかの結晶状態を有するものであれば、 その上には発光効率が少なくとも 1 2 %以上の発光素子を作製し得る。 また、 窒化アルミニウム成分を 5 (H«%以上含む窒化ァ ルミ二ゥムを主成分とする焼結体を基板として用いる場合、 該基板にあらかじめ形成する窒化 ガリウム、 窒化インジウム、 窒化アルミニウムのうちから選ばれた少なくとも 1種以上を主成 分とする薄膜が配向性多結晶の結晶状態を有するものであれば、 その上には発光効率が少なく とも 1 5 %以上の発光素子を作製し得る。 また、 窒化アルミニウム成分を 5 0# ^貴%以上含む 窒化アルミニウムを主成分とする焼結体を基板として用いる場合、 窒化ガリウム、 窒化インジ ゥム、 窒化アルミニウムのうちから選ばれた少なくとも 1種以上を主成分とする薄膜を少なく
とも 2層以上形成し、 該 2層以上の薄膜のうち表面のものが単結晶であれば、 基板にあらかじ め形成する薄膜の結晶状態に関係なくその上には発光効率が少なくとも 1 5 %以上の発光素子 を作製し得る。 すなわち、 窒化アルミニウム成分を 5 ()■%以上含む窒化アルミニウムを主 成分とする焼結体を基板として用いる場合、 その上にあらかじめ窒化ガリウム、 窒化インジゥ ム、窒化アルミニウムのうちから選ばれた少なくとも 1種以上を主成分とする無定形、多結晶、 配向性多結晶、 単結晶のうちから選ばれた少なくともいずれかの結晶状態を有する薄膜を少な くとも 1層以上形成し、 その上にさらに窒化ガリウム、 窒化インジウム、 窒化アルミニウムの うちから選ばれた少なくとも 1種以上を主成分とする単結晶薄膜を少なくとも 1層以上形成し た基板を用いれば、 その上には発光効率が少なくとも 1 5 %以上の発光^?を作製し得る。 特 に発光素子として発光効率が 2 0 %以上のものを作製していく場合、 あるいは発光素子として レーザ—ダイオードを作製する場合にはこのような表面に単結晶薄膜を形成した基板を用いる ことが有効である。
本発明において、 光 ¾1率が 1 %より小さいかあるいは実質的に ½¾M生を有しない窒化ァ ルミ二ゥムを主成分とする焼結体を基板として用いても優れた発光効率を有する発光素子を作 製し得る。 また、 ¾¾ 率が 1 %以上の) ffii性を有する窒化アルミニウムを主成分とする焼 結体を基板として用いても優れた発光効率を有する発光軒を作製し得る。 通常上記窒化アル ミ二ゥムを主成分とする焼結体を基板として用いることにより発光効率が従来からのサフアイ ァなどの基板を用いて作製される発光素子の発光効率と比べて少なくとも同等か、 最大 4〜5 倍以上に改善された発光素子を提供し得る。
より詳しく言えば、 窒化アルミニウムを主成分とする焼結体の光腿率が 1 %より小さいか 実質的に ½¾i性を有しないもの、 あるいは窒化アルミニウムを主成分とする焼結体の ¾¾1 率が 1 %以上のものを基板として用いれば発光効率 1 0 %以上の発光素子を作製し得る。通常、 窒化アルミニウムを主成分とする焼結体はより高い光顯性を有するものを基板として用いる ほうがより発光効率の高い発光素子を作製し得るので好ましい。 すなわち、 窒化アルミニウム を主成分とする焼結体の光 ¾ 率 1 0 %以上のものを基板として用いたときその上に形成され る発光素子の発光効率は 1 2 %以上のものが得られ易いので好ましい。 また、 窒化アルミニゥ ムを主成分とする焼結体の光 ¾1率 2 0 %以上のものを基板として用いたときその上に形成さ れる発光 の発光効率は 1 5 %以上のものが得られ易い。 また、 窒化アルミニウムを主成分 とする焼結体の光 率 3 0 %以上のものを基板として用いたときその上に形成される発光素 子の発光効率は 2 0 %以上のものが得られ易い。 また、 窒化アルミニウムを主成分とする焼結 体の光透過率 4 0 %以上のものを基板として用いたときその上に形成される発光素子の発光効 率は 2 5 %以上のものが得られ易い。 また、 窒化アルミニウムを主成分とする焼結体の光 ¾1 率 5 0 %以上のものを基板として用いたときその上に形成される発光素子の発光効率は 3 0 % 以上のものが得られ易い。 前記のように本発明において耀過率が 6 0 %以上、 さらに駄 8 0 %以上のものも得られるがこのような高い光 ¾1率を有する窒化アルミニウムを主成分とす る焼結体ものを基板として用いたときその上に形成される発光素子の発光効率は 4 0 %以上、 最大 6 2 %のものが得られた。
このように窒化アルミニウムを主成分とする焼結体を基板として用いて作製される発光^? の発光効率は少なくとも 1 0 %以上のものが得られ易いので、 «からのサファイアなどの基 板を用いて作製される発光素子の発光効率と比べて少なくとも同等か、 最大 4〜5倍以上に改 善された発光素子を提供し得る。
本発明において、窒化アルミニウムを主成分とする能結体は窒化ガリウム、窒化インジウム、 窒化アルミニウムのうちから選ばれた少なくとも 1種以上を主成分とする単結晶薄膜が形成で きるものであれば該焼結体中の窒化アルミニゥム結晶) &子がどのような大きさのものであつて
も 化アルミニウムを主成分とする焼結体を基板として用いることにより優れた発光効率を 有する発光素子が作製し得る。 通常該発光素子の発光効率は^からのサフアイァなどの基板 を用いて作製される発光素子の発光効率と比べて少なくとも同等か、 最大 4〜 5倍以上に改善 された発光軒を提供できる。 通常窒化アルミニウム結晶粒子の大きさが平均 0. 5 ^m以上 の窒化アルミニウムを主成分とする焼結体を基板として用いることが好ましく縣からのサフ アイァなどの基板を用いて作製される発光素子の発光効率と比べて少なくとも同等か、 最大 4 〜 5倍以上に改善された発光素子を作製し得る。
より詳しく言えば、 窒化アルミニウム結晶粒子の大きさが平均 1 . 0 m以上の窒化アルミ 二ゥムを主成分とする焼結体を基板として用いることで発光効率が少なくとも 1 0 %以上の発 光素子を作製し得る。
また、 含まれる結晶粒子が均等に近い大きさに揃っている状態のものだけでなく結晶粒子の 大きさカ坏揃いのものや結晶粒子の形状がいびつで針状あるいは板状など一辺が小さく他の一 辺が大きい形状の結晶粒子、 例えばポリタイプ A 1 N粒子など一辺が数 mで他の一辺が 1 0 数 m以上に大きく成長した針状あるいは板状などの形状の結晶粒子を有する窒化アルミニゥ ムを主成分とする焼結体を基板として用いても何ら問題なく発光効率の優れた発光素子を作製 することができる。
その他、 窒化アルミニウムを主成分とする焼結体中に導通ビアを形成したものを基板として 用いても窒化ガリウム、 窒化インジウム、 窒化アルミニウムのうちから選ばれた少なくとも 1 種以上を主成分とする単結晶薄膜が形成可能であり優れた発光効率を有する発光素子が作製し 得る。 導通ビアとしては導電性を有する材料であればどのようなものでも用いること力河能で ある。 通常は導通ビアの材料としてタングステン、 モリブデン、 金、 銀、 銅、 窒化チタンなど の金属、 あるいは合金、 あるいは金属化合物を主成分とする材料が用いられる。 このような材 料からなる導通ビアを形成した窒化アルミニウムを主成分とする焼結体を基板として用いるこ とにより、 通常 ¾έ¾からのサフアイァなどの基板を用いて作製される発光素子の発光効率と比 ベて少なくとも同等か、 最大 4〜5倍以上に改善された発光効率を有する発光素子を提供し得 る。
より詳しく言えば、 窒化アルミニウムを主成分とする焼結体中に導通ビアを形成したものを 基板として用いることで発光効率が少なくとも 1 0 %以上の発光素子を作製し得る。
上記のように、 発光素子を作製するための基板として窒化アルミニウムを主成分とする雄 体を用いることは有効であり、 特に 性を有するものであればより発光効率に優れた発光 素子が作製し得ることを説明した。
また本発明において、 窒化アルミニウムを主成分とする焼結体からなる基板の表面平滑性と してどのような状態のものであっても窒化ガリウム、 窒化インジウム、 窒化アルミニウムのう ちから選ばれた少なくとも 1種以上を主成分とする単結晶薄膜が形成できるものであれば、 該 窒化アルミニウムを主成分とする焼結体からなる基板の上に形成される発光素子は優れた発光 効率を有するものが作製し得る。 通常上記表面平滑性を有する窒化アルミニウムを主成分とす る焼結体からなる基板を用いることにより作製される発光素子の発光効率は^からのサファ ィァなどの基板を用いて作製される発光素子の発光効率と比べて少なくとも同等か、 最大 4〜 5倍以上に改善されたものを提供し得る。
より詳しく言えば、 1 )窒化アルミニウムを主成分とする焼結体をそのまま基板として用い、 その上に直接要すれば窒化ガリゥム、 窒化ィンジゥム、 窒化アルミニゥムのうちから選ばれた 少なくとも 1種以上を主成分とする薄膜からなるバッファ層をまず形成し、 その上に窒化ガリ ゥム、 窒化インジウム、 窒化アルミニウムのうちから選ばれた少なくとも 1種以上を主成分と するェピタキシャル成長した単結晶薄膜を Ν型半導体層、 発光層、 Ρ型半導体層、 として積層
することで発光素子を作製していく方法の場合、 通常窒化アルミニウムを主成分とする焼結体 からなる基板の平均表面粗さ R aが 2 0 0 0 nm以下のものを用いることで発光効率が少なく とも 1 0 %以上の発光素子を作製し得る。
また、 2 ) 窒化アルミニウムを主成分とする焼結体を基板として作製し、 その上にあらかじ め窒化ガリウム、 窒化インジウム、 窒化アルミニウムのうちから選ばれた少なくとも 1種以上 を主成分とする無定形、 多結晶、 配向性多結晶、 単結晶のうちから選ばれた少なくともいずれ かの結晶状態を有する薄膜を少なくとも 1層以上形成して薄膜基板とし、 該薄膜基板の上に要 すれば窒化ガリゥム、 窒化ィンジゥム、 窒化アルミニゥムのうちから選ばれた少なくとも 1種 以上を主成分とする薄膜からなるバッファ層をまず形成し、 窒化ガリウム、 窒化インジウム、 窒化アルミニウムのうちから選ばれた少なくとも 1種以上を主成分とするェピタキシャル成長 した単結晶薄膜を N型半導体層、 発光層、 P型半導体層、 として積層して発光素子を作製して いく方法、 及び 3 ) 窒化アルミニウムを主成分とする焼結体を基板として作製し、 その上にあ らかじめ窒化ガリウム、 窒化インジウム、 窒化アルミニウムのうちから選ばれた少なくとも 1 種以上を主成分とする無定形、 多結晶、 配向性多結晶、 単結晶のうちから選ばれた少なくとも いずれかの結晶状態を有する薄膜を少なくとも 1層以上形成し、その上にさらに窒化ガリゥム、 窒化インジウム、 窒化アルミニウムのうちから選ばれた少なくとも 1種以上を主成分とする単 結晶薄膜を少なくとも 1層以上形成して薄膜基板とし、 該薄膜基板の上に要すれば窒化ガリウ ム、 窒化インジウム、 窒化アルミニウムのうちから選ばれた少なくとも 1種以上を主成分とす る薄膜からなるバッファ層をまず形成し、 その上に窒化ガリウム、 窒化インジウム、 窒化アル ミニゥムのうちから選ばれた少なくとも 1種以上を主成分とするェピタキシャル成長した単結 晶薄膜を N型半導体層、発光層、 P型半謝本層、 として積層して発光素子を作製していく方法、 という上記 2) 〜3) で示した方法により発光素子を作製する場合、 通常窒化アルミニウムを 主成分とする焼結体からなる基板の平均表面粗さ R aが 2 0 0 0 nmより大きいものを用いて も発光効率が少なくとも 1 0 %以上の発光素子を作製し得る。
本発明において、 窒化アルミニウムを主成分とする焼結体からなる基板の厚みはどのような ものであっても窒化ガリウム、 窒化インジウム、 窒化アルミニウムのうちから選ばれた少なく とも 1種以上を主成分とする単結晶薄膜が形成できるものであれば、 該窒化アルミニウムを主 成分とする焼結体からなる基板の上に形成される発光 は優れた発光効率を有するものが作 製し得る。 通常上記基 ¾J?みを有する窒化アルミニウムを主成分とする焼結体からなる基板を 用いることにより作製される発光素子の発光効率は^からのサファイアなどの基板を用いて 作製される発光素子の発光効率と比べて少なくとも同等か、 最大 4〜 5倍以上に改善されたも のを提供し得る。 通常窒化アルミニウムを主成分とする焼結体からなる基板の厚みが 8. 0 m m以下のものを用いることで発光効率が少なくとも 1 0 %以上の発光素子を作製し得る。
以上、 発光素子を作製するための基板として窒化アルミニウムを主成分とする焼結体を用い ることは有効であり、 化アルミニウムを主成分とする焼結体について繊 (組成)、 ¾¾ 率、 焼結体結晶粒子、 導通ビアの有無、 基板としての表面平滑性、 基板としての厚み、 などに ついてその効果を説明してきた。
上記で説明してきたように、 a) 窒化アルミニウムを主成分とする焼結体を基板として作製 し、 その上にあらかじめ窒化ガリウム、 窒化インジウム、 窒化アルミニウムのうちから選ばれ た少なくとも 1種以上を主成分とする無定形、 多結晶、 配向性多結晶、 単結晶のうちから選ば れた少なくともいずれかの結晶状態を有する薄膜を少なくとも 1層以上形成して薄膜基板とし、 該薄膜基板の上に N型半導体層、 発光層、 P型半導体層、 を積層して発光素子を作製していく 方法、 さらに b) 窒化アルミニウムを主成分とする焼結体を基板として作製し、 その上にあら かじめ窒化ガリウム、 窒化インジウム、 窒化アルミニウムのうちから選ばれた少なくとも 1種
以上を主成分とする無定形、 多結晶、 配向性多結晶、 単結晶のうちから選ばれた少なくともい ずれかの結晶状態を有する薄膜を少なくとも 1層以上形成し、 さらにその上に窒化ガリゥム、 窒化インジウム、 窒化アルミニウムのうちから選ばれた少なくとも 1種以上を主成分とする単 結晶薄膜を少なくとも 1層以上形成して薄膜基板とし、 該薄膜基板の上に N型半導体層、 発光 層、 P型半導体層、 を積層して発光素子を作製していく方法、 という上記 a)、 b) で示した方 法により発光素子を作製する場合、 窒化アルミニウムを主成分とする搬吉体からなる基板にあ らかじめ形成する窒化ガリウム、 窒化インジウム、 窒化アルミニウムのうちから選ばれた少な くとも 1種以上を主成分とする薄膜が単結晶、 無定形、 多結晶、 配向性多結晶のうちから選ば れた少なくともいずれかの結晶状態を有するものでは、 特に断らない限りその上には通常発光 効率 1 0 %以上の発光素子が作製し得る。 上記の基板にあらかじめ形成する窒化ガリウム、 窒 化インジウム、 窒化アルミニウムのうちから選ばれた少なくとも 1種以上を主成分とする薄膜 のうち無定形、 多結晶、 配向性多結晶のうちから選ばれた少なくともいずれかの結晶状態を有 するものがより好ましい。 また、 基板にあらかじめ形成する窒化ガリウム、 窒化インジウム、 窒化アルミニウムのうちから選ばれた少なくとも 1種以上を主成分とする薄膜が 13向性多結晶 の結晶状態を有するものでは、 特に断らない限りその上には通常発光効率 1 2 %以上の発光素 子が作製し得る。 また、 窒化ガリウム、 窒化インジウム、 窒化アルミニウムのうちから選ばれ た少なくとも 1種以上を主成分とする薄膜を少なくとも 2層以上とし、 該 2層以上の薄膜のう ち表面のものを単結晶とした基板を用いれば、 基板にあらかじめ形成する薄膜の結晶状態に関 係なくその上には通常発光効率 1 2 %以上の発光素子が作製し得る。
本発明において、 上記窒化アルミニウムを主成分とする焼結体からなる基板だけでなぐ 炭 化珪素、 窒化珪素、 窒化ガリウム、 酸化亜鉛、 酸化ベリリウムなどの六方晶系及び 化アルミ 二ゥムなどの三方晶系ぁるいは六方晶系として分類できる結晶構造を有する各種セラミック材 料を主成分とする焼結体を基板として用い、該基板に要すれば窒化ガリウム、窒化インジウム、 窒化アルミニウムのうちから選ばれた少なくとも 1種以上を主成分とする薄勵ゝらなるバッフ ァ層をまず形成し、 その上に窒化ガリウム、 窒化インジウム、 窒化アルミニウムのうちから選 ばれた少なくとも 1種以上を主成分とするェピタキシャル成長した単結晶薄膜を N型半導体層、 発光層、 P型半 ¾ί本層、 として積層し発光素子を作製することができる。 本発明は炭化珪素、 窒ィ匕珪素、 窒化ガリウム、 酸化亜鉛、 酸化ベリリウムなどの六方晶系及び谶化アルミニウムな どの三方晶系あるいは六方晶系として分類できる結晶構造を有する各種セラミツク材料を主成 分とする焼結体あるいは該焼結体を基板状としその上に少なくとも上記の N型半導体層及び発 光層及び P型半導体層を積層して積層体となし発光素子を構成したことに特徴がある。 上記炭 化珪素、 窒化珪素、 窒化ガリウム、 酸化亜鉛、 酸化ベリリウムなどの六方晶系及び酸化アルミ 二ゥムなどの三方晶系あるいは六方晶系として分類できる結晶構造を有する各種セラミック材 料を主成分とする焼結体を基板として用いて作製される発光素子も発光効率の優れたものを作 製し得る。 すなわち、 炭化珪素、 窒化珪素、 窒化ガリウム、 酸化亜鉛、 酸化ベリリウムなどの 六方晶系及び酸化アルミニウムなどの三方晶系あるいは六方晶系として分類できる結晶構造を 有する各種セラミック材料を主成分とする焼結体からなる基板を用いることにより、 «から のサファイアなどの単結晶基板を用いて作製される発光素子の発光効率と比べて少なくとも同 等か、 最大 3〜 4倍以上に改善された発光効率を有する発光素子が提供し得る。 すなわち本発 明による炭化珪素、 窒化珪素、 窒化ガリウム、 酸化亜鉛、 酸化ベリリウムなどの六方晶系及び 酸化アルミニウムなどの三方晶系あるいは六方晶系として分類できる結晶構造を有する各種セ ラミック材料を主成分とする焼結体からなる基板を用いて作製される発光素子は入力された電 力の最大 2 0〜3 0 %以上が発光素子外部へ光エネルギーとして放出し得る。
炭化珪素、 窒化珪素、 窒ィ匕ガリウム、 酸化亜鉛、 酸化ベリリウムなどの六方晶系及び 化ァ
ルミニゥムなどの三方晶系あるいは六方晶系として分類できる結晶構造を有する各種セラミッ ク材料を主成分とする焼結体からなる基板を用いて作製される発光素子がなぜこのような優れ た発光効率を有するかその原因については必ずしも明確ではないが、 上記基板には窒化ガリゥ ム、 窒化インジウム、 窒化アルミニウムのうちから選ばれた少なくとも 1種以上を主成分とす る結晶性に優れた単結晶薄膜が形成し得るということがまず第一に重要であると思われる。 し かしそれだけではなく上記炭化珪素、 窒化珪素、 窒化ガリウム、 酸化亜鉛、 酸化ベリリウムな どの六方晶系及び ¾化アルミニウムなどの三方晶系あるいは六方晶系として分類できる結晶構 造を有する各種セラミック材料を主成分とする焼結体からなる基板が窒化アルミ二ゥムを主成 分とする焼結体からなる基板と同様、 サファイアのようなバルク単結晶でなく焼き固められ結 晶粒子や粒界相などから構成される焼結体としての微構造を有するということが ^からのサ ファイアなどの単結晶基板と同等あるいはそれ以上の発光効率を有する原因としてさらに重要 であると思われる。
上記のように、 サファイア基板上にもミラー指数 (0 0 2) の格子面の X線回折ロッキング カーブの半値幅が少なくとも 3 0 0秒以下の結晶性を有する窒化ガリゥム、 窒化ィンジゥム、 窒化アルミニウムのうちから選ばれた少なくとも 1種以上を主成分とする単結晶薄膜が形成で き、 このような結晶性に優れた単結晶薄膜を少なくとも N型半導体層、 発光層、 P型半導体層 の各層が構成されるようサフアイァ基板上に形成することで発光素子が Mitされてきた。 本発 明による炭化珪素、 窒化珪素、 窒化ガリウム、 酸化亜鉛、 酸化ベリリウムなどの六方晶系及び 酸化アルミニウムなどの三方晶系あるいは六方晶系として分類できる結晶構造を有する各種セ ラミック材料を主成分とする焼結体からなる基板を用いて作製される発光素子は、 上記サファ ィァなどの単結晶基板を用いて作製される発光素子の発光効率と比べて少なくとも同等か、 最 大 3〜4倍以上に改善された発光効率を有する発光素子が提供し得る。 すなわち、 本発明によ る炭化珪素、 窒化珪素、 窒化ガリウム、 酸化亜鉛、 酸化ベリリウムなどの六方晶系及び酸化ァ ルミニゥムなどの三方晶系あるいは六方晶系として分類できる結晶構造を有する各種セラミッ ク材料を主成分とする焼結体からなる基板を用いて作製される発光素子は、 少なくとも発光効 率 8 %以上のものが作製し得る。
本発明において、上記発光素子を作製するための基板として用いられる炭化珪素、窒化珪素、 窒化ガリゥム、 酸化亜鉛、 酸化べリリウムなどの六方晶系及び 化アルミ二ゥムなどの三方晶 系あるいは六方晶系として分類できる結晶構造を有する各種セラミック材料を主成分とする焼 結体は、 該発光素子の構成要素である少なくとも N型半導体層、 発光層、 P型半導体層、 を形 成する窒化ガリウム、 窒化インジウム、 窒化アルミニウムのうちから選ばれた少なくとも 1種 以上を主成分とする薄膜がェピタキシャル成長した単結晶として形成しうるものであればどの ようなものでも用いることができる。 言い換えれば、 以下に述べる方法により窒化ガリウム、 窒化インジウム、 窒化アルミニウムのうちから選ばれた少なくとも 1種以上を主成分とするェ ピタキシャル成長した単結晶薄膜が形成できるものであればどのような炭化珪素、 窒化珪素、 窒化ガリウム、 酸化亜鉛、 酸化ベリリウムなどの六方晶系及び 化アルミニウムなどの三方晶 系あるいは 晶系として分類できる結晶構造を有する各種セラミック材料を主成分とする焼 結体であっても発光素子を作製するための基板として用いることができる。
すなわち、 1 ) 炭化珪素、 窒化珪素、 窒化ガリウム、 酸化 、 酸化ベリリウムなどの ^ 晶系及び酸化アルミ二ゥムなどの三方晶系あるいは六方晶系として分類できる結晶構造を有す る各種セラミック材料を主成分とする焼結体をそのまま基板として用い、 その上に直接発光素 子を構成する窒化ガリウム、 窒化インジウム、 窒化アルミニウムのうちから選ばれた少なくと も 1種以上を主成分とするェピタキシャル成長した単結晶薄膜を N型半導体層、 発光層、 P型 半導体層、 として積層し発光素子を作製していく方法である。 この方法において要すれば窒化
ガリウム、 窒化インジウム、 窒化アルミニウムのうちから選ばれた少なくとも 1種以上を主成 分とする薄膜からなるバッファ層をまず基板上に形成し、 その上に N型半導体層、 発光層、 P 型半導体層を積層して発光素子を作製していくことが望ましい。
また、 2 ) 炭化珪素、 窒化珪素、 窒化ガリウム、 酸化亜鉛、 酸化ベリリウムなどの六方晶系 及び酸化アルミニウムなどの三方晶系あるいは六方晶系として分類できる結晶構造を有する各 種セラミック材料を主成分とする焼結体を基板として作製し、 該基板の上にあらかじめ窒化ガ リウム、 窒化インジウム、 窒化アルミニウムのうちから選ばれた少なくとも 1種以上を主成分 とする無定形、 多結晶、 配向性多結晶、 単結晶のうちから選ばれた少なくともいずれかの結晶 状態を有する薄膜を少なくとも 1層以上形成して薄膜基板とし、 その上に発光素子を構成する 窒化ガリウム、 窒化インジウム、 窒化アルミニウムのうちから選ばれた少なくとも 1種以上を 主成分とするェピタキシャル成長した単結晶薄膜を N型半導体層、 発光層、 P型半導体層、 と して積層し発光素子を作製していく方法である。 上記薄膜基板を用いて発光軒を作製してい く場合、 該薄膜基板に形成されている薄膜層の少なくとも一部を発光素子が機能するための構 成要素として用いることも可能である。 なお、 この方法において上記薄膜基板の上に要すれば 窒化ガリウム、 窒化インジウム、 窒化アルミニウムのうちから選ばれた少なくとも 1種以上を 主成分とする薄膜からなるバッファ層をまず形成し、 その上に N型半導体層、 発光層、 P型半 導体層を積層して発光素子を作製していくこと力 ましい。
また、 3 ) 炭化珪素、 窒化珪素、 窒化ガリウム、 酸化亜鉛、 酸化ベリリウムなどの六方晶系 及び 化アルミニウムなどの三方晶系あるいは六方晶系として分類できる結晶構造を有する各 種セラミック材料を主成分とする焼結体を基板として作製し、 該基板の上にあらかじめ窒化ガ リゥム、 窒化ィンジゥム、 窒化アルミニゥムのうちから選ばれた少なくとも 1種以上を主成分 とする無定形、 多結晶、 配向性多結晶、 単結晶のうちから選ばれた少なくともいずれかの結晶 状態を有する薄膜をあらかじめ少なくとも 1層以上形成し、 その上にさらに窒化ガリウム、 窒 化インジウム、 窒化アルミニウムのうちから選ばれた少なくとも 1種以上を主成分とする単結 晶薄膜を少なくとも 1層以上形成して薄膜基板とし、 その上に発光素子を構成する窒化ガリウ ム、 窒化インジウム、 窒化アルミニウムのうちから選ばれた少なくとも 1種以上を主成分とす るェピタキシャル成長した単結晶薄膜を N型半導体層、 発光層、 P型半導体層、 として積層し 発光^?を作製していく方法である。 上記薄膜基板を用いて発光素子を作製していく場合、 該 薄膜基板に形成されている薄膜層の少なくとも一部を発光素子が機能するための構成要素とし て用いることも可能である。 なお、 この方法において上記薄膜基板の上に要すれば窒化ガリウ ム、 窒化インジウム、 窒化アルミニウムのうちから選ばれた少なくとも 1種以上を主成分とす る薄膜からなるバッファ層をまず形成し、 その上に N型半導体層、 発光層、 P型半導体層を積 層して発光素子を作製していくことが ましい。
上記 1 ) 〜3 ) で示した方法により、 本発明による炭化珪素、 窒化珪素、 窒化ガリウム、 酸 化亜鉛、 酸化ベリリウムなどの六方晶系及び酸化アルミニウムなどの三方晶系あるいは六方晶 系として分類できる結晶構造を有する各種セラミック材料を主成分とする焼結体を発光素子作 製用基板として用いることで発光効率 8 %以上の発光素子を容易に作製し得る。
上記 1 ) 〜3 ) で示した方法のなかで、 基板に形成する窒化ガリウム、 窒化インジウム、 窒 化アルミニウムのうちから選ばれた少なくとも 1種以上を主成分とする薄膜を少なくとも 2層 以上とし、 該 2層以上の薄膜のうち表面の薄膜を単結晶とした基板を用いれば、 基板にあらか じめ形成する薄膜の結晶状態に関係なくその上には発光効率に優れた発光素子を容易に作製し 得るので好ましい。 すなわち、 炭化珪素、 窒化珪素、 窒化ガリウム、 酸化亜鉛、 酸化ベリリウ ムなどの六方晶系及び酸ィ匕アルミニウムなどの三方晶系あるいは六方晶系として分類できる結 晶構造を有する各種セラミック材料を主成分とする焼結体を基板として用いる場合、 その上に
あらかじめ窒化ガリウム、 窒化インジウム、 窒化アルミニウムのうちから選ばれた少なくとも 1種以上を主成分とする無定形、 多結晶、 配向性多結晶、 単結晶のうちから選ばれた少なくと もいずれかの結晶状態を有する薄膜を少なくとも 1層以上形成し、 その上にさらに窒化ガリウ ム、 窒化インジウム、 窒化アルミニウムのうちから選ばれた少なくとも 1種以上を主成分とす る単結晶薄膜を少なくとも 1層以上形成した基板を用いれば、 その上には発光効率 1 0 %以上 の発光素子を容易に作製し得る。 特に発光軒として発光効率が 1 2 %以上のものを作製して いく場合、 あるいは発光素子としてレーザーダイォ一ドを作製する場合にはこのような表面に 単結晶薄膜を形成した基板を用いることが有効である。
上記薄膜基板を用いて発光素子を作製していく場合、 該薄膜基板に形成されている薄膜層の 少なくとも一部を発光素子が機能するための構成要素として用いることも可能である。 この方 法において薄膜基板の上に要すれば窒化ガリウム、 窒化インジウム、 窒化アルミニウムのうち から選ばれた少なくとも 1種以上を主成分とする薄膜からなるバッファ層をまず形成し、 その 上に N型半導体層、発光層、 P型半導体層を積層して発光素子を作製していくことが ましい。 また本発明による薄膜基板を用いて発光素子を作製していく場合、 上記バッファ層を特に設け ずに発光素子を作製することも可能である。
本発明において、 このような特性を有する炭化珪素、 窒化珪素、 窒化ガリウム、 酸化亜鉛、 酸化ベリリウムなどの六方晶系及ぴ 化アルミニウムなどの三方晶系あるいは六方晶系として 分類できる結晶構造を有する各種セラミック材料を主成分とする焼結体を用いた基板に形成さ れる薄膜の結晶性などの性状について、 該炭化珪素、 窒化珪素、 窒化ガリウム、 酸化亜鉛、 酸 化ベリリゥムなどの六方晶系及び 化アルミニウムなどの三方晶系あるいは六方晶系として分 類できる結晶構造を有する各種セラミック材料を主成分とする焼結体の組成、 、 窒化アル ミニゥム成分の含有量、 ¾¾ 性、 焼結体糸吉晶立子の大きさ、 導通ビアの有無などとの関係、 あるいは該炭化珪素、 窒化珪素、 窒化ガリウム、 酸化亜鉛、 酸化ベリリウムなどの六方晶系及 ぴ 化アルミニウムなどの三方晶系あるいは六方晶系として分類できる結晶構造を有する各種 セラミック材料を主成分とする焼結体を基板としたときの表面平滑性などとの関係、 あるいは 該炭化珪素、 窒化珪素、 窒化ガリウム、 酸化亜鉛、 酸化ベリリウムなどの六方晶系及び 化ァ ルミニゥムなどの三方晶系あるいは六方晶系として分類できる結晶構造を有する各種セラミツ ク材料を主成分とする焼結体からなる基板に形成される薄膨冓成、 薄 みなどとの関係につ いて今まで説明してきた。
本発明において、 炭化珪素、 窒化珪素、 窒化ガリウム、 酸化亜鉛、 酸化ベリリウムなどの六 方晶系及び酸化アルミニウムなどの三方晶系あるいは六方晶系として分類できる結晶構造を有 する各種セラミック材料を主成分とする焼結体は窒化ガリウム、 窒化インジウム、 窒化アルミ ニゥムのうちから選ばれた少なくとも 1種以上を主成分とする単結晶薄膜が形成できるもので あればどのような組成のものであっても、 該炭化珪素、 窒化鶴、 窒化ガリウム、 酸化亜鉛、 酸化ベリリゥムなどの六方晶系及び 化アルミニウムなどの三方晶系あるいは六方晶系として 分類できる結晶構造を有する各種セラミック材料を主成分とする焼結体を基板として用いるこ とにより優れた発光効率を有する発光素子が作製し得る。 通常^からのサファイアなどの基 板を用いて作製される発光素子の発光効率と比べて少なくとも同等か、 最大 3〜4倍以上に改 善された発光効率を有する発光素子を提供し得る。
具体的には、 例えば炭化珪素を主成分とする焼結体の組成としては実質的に S i Cだけから なるもの、あるいは力一ボン成分、あるいは B、 B 4C、 B Nなどの硼素成分、あるいは Y203、 E r 2〇3、 Y b 203などの希土類 素成分、 B e〇、 Mg O、 C a〇、 S r O、 B a Oなどの アルカリ土類金属成分、 あるいは A 1 203などのアルミニウム成分、 あるいは S i O ょどの珪 素成分、 これらの成分を勒虫あるいは複合で含むものなどである。 窒化珪素を主成分とする焼
結体の組成としては実質的に S i 3N4だけからなるもの、 あるいは Y2〇3、 Er 203、 Yb2 〇3などの希土^ ¾素成分、 Be〇、 Mg〇、 CaO、 S r 0、 B a Oなどのアルカリ土類金属 成分、 あるいは A 12〇3などのアルミニウム成分、 あるいは S i 02などの珪素成分、 あるいは カーボン、 モリブデン、 タングステンなどの黒色化促進成分、 あるいは Ti02、 Cr2〇3、 M nO、 Co〇、 Ni〇、 Fe2〇3などの遷移金属成分、 これらの成分を戦虫あるいは複合で含 むものなどである。 酸化亜鉛を主成分とする焼結体の組成としては実質的に Z ηθだけからな るもの、 あるいは Y203、 Er2〇3、 Yb203などの希土類 素成分、 あるいは Be〇、 Mg 0、 Ca〇、 S rO、 B a〇などのアルカリ土類金属成分、 あるいは A 12〇3などのアルミ二 ゥム成分、 あるいは S iO ょどの珪素成分、 あるいは Ti〇2、 Cr2〇3、 MnO、 Co〇、 N i〇、 Fe 203などの遷移金属成分、 これらの成分を単独あるいは複合で含むものなどであ る。 酸化ベリリゥムを主成分とする焼結体の組成としては実質的に B e Oだけからなるもの、 あるいは Y203、 Er203、 Yb2〇3などの希土 ¾素成分、 あるいは Mg〇、 CaO、 S r 〇、 B a Oなどのアルカリ土類金属成分、 あるいは A 12〇3などのアルミニウム成分、 あるい は S i〇2などの珪素成分、 あるいは Ti〇2、 Cr2〇3、 Mn〇、 CoO、 N i〇、 Fe2Os などの遷移金属成分、 これらの成分を稱虫あるいは複合で含むものなどである。 酸化アルミ二 ゥムを主成分とする!^結体の組成としては実質的に A 1203だけからなるもの、あるいは Y2〇 3、 Er 203、 丫132〇3などの希土^¾素成分、 あるいは Be〇、 MgO、 CaO、 SrO、 B a Oなどのアルカリ土類金属成分、 あるいは S i〇2などの珪素成分、 あるいは Ti〇2、 Cr2 〇3、 MnO、 CoO、 Ni〇、 F e 2〇3などの遷移金属成分、 これらの成分を職あるいは複 合で含むものなどである。
より詳しく言えば、 通常酸化亜鉛成分を Z n O鍵で 55. 0モル%以上含む酸化亜鉛を主 成分とする焼結体を用いることが好ましく、 該酸化亜鉛を主成分とする焼結体を基板として用 いることで発光効率が少なくとも 8 %以上の発光^?を作製し得る。 上記酸化菌以外の成分 として、 例えばアルミニウム成分を A 1203騰で 45. 0モル%以下含む酸化«を主成分 とする焼結体、 あるいはアルミニウム成分を A 12〇3購で 45. 0モル%以下含み同時に S c、 Y、 La、 Ce、 Pr、 Nd、 Pm、 Sm、 Eu、 Gd、 Tb、 Dy、 Ho、 Er、 Tm、 Yb、 L uなどの希土類 素成分のうちから選ばれた少なくとも 1種以上の成分を酸化物換算 で 10. 0モル%以下含む酸化 »を主成分とする焼結体、 これらの焼結体からなる基板を用 いることで発光効率が少なくとも 8 %以上の発光素子を作製し得る。
また、 通常酸化べリリゥム成分を B e〇換算で 65. 0モル%以上含む酸化べリリウムを主 成分とする焼結体を用いることが好ましぐ 該酸化ベリリウムを主成分とする焼結体を基板と して用いることで発光効率が少なくとも 8 %以上の発光素子を作製し得る。 上記酸化ベリリゥ ム以外の成分として、 例えばマグネシウム成分、 カルシウム成分、 珪素成分のうちから選ばれ た少なくとも 1種以上の成分を M g〇、 C a 0、 S i〇 で合計 35. 0モリレ%以下含む酸 化ベリリゥムを主成分とする焼結体、 あるいはマグネシウム成分、 カルシウム成分、 珪素成分 のうちから選ばれた少なくとも 1種以上の成分を M g〇、 C a 0、 S i O 2腿で合計 35. 0 モル%以下含み同時に S c、 Y、 La、 Ce、 Pr、 Nd、 Pm、 Sm、 Eu、 Gd、 Tb、 Dy、 Ho、 Er、 Tm、 Yb、 L uなどの希土類 素成分のうちから選ばれた少なくとも 1 種以上の成分を酸化物換算で 5. 0モル%以下含む酸化ベリリウムを主成分とする焼結体、 こ れらの焼結体からなる基板を用いることで発光効率が少なくとも 8 %以上の発光素子を作製し 得る。
また、 通常酸化アルミニウム成分を A 1203観で 55. 0モル%以上含む酸化アルミニゥ ムを主成分とする焼結体を用いることが好ましぐ 該酸化アルミニウムを主成分とする焼結体 を基板として用いることで発光効率が少なくとも 8%以上の発光軒を作製し得る。 上記酸化
アルミニゥム以外の成分として、 例えばマグネシウム成分、 カルシウム成分、 珪素成分のうち から選ばれた少なくとも 1種以上の成分を M g 0、 C a 0、 S i〇 2騰で合計 4 5. 0モル% 以下含む酸化アルミニウムを主成分とする焼結体、 あるいはマグネシウム成分、 カルシウム成 分、 珪素成分のうちから選ばれた少なくとも 1種以上の成分を Mg〇、 C a〇、 S i 02^で 合計 4 5. 0モル%以下含み同時に S c、 Y、 L a、 C e、 P r、 N d、 Pm、 Sm、 E u、 G d、 T b、 D y、 H o、 E r、 Tm、 Y b、 L uなどの希土 素成分のうちから選ばれた 少なくとも 1種以上の成分を酸化物換算で 1 0. 0モル%以下含む酸化アルミニウムを主成分 とする焼結体、 あるいはマグネシウム成分、 カルシウム成分、 珪素成分のうちから選ばれた少 なくとも 1種以上の成分を Mg 0、 C a 0、 S i 02 で合計 4 5. 0モル%以下含み同時に S c、 Y、 L a、 C e、 P r、 N d、 Pm、 Sm、 E u、 G d、 T b、 D y、 H o、 E r、 T m、 Y b、 L uなどの希土^ ¾素成分のうちから選ばれた少なくともいずれか 2種以上の成分 を酸化物騰で 1 0. 0モル%以下含む酸化アルミニウムを主成分とする焼結体、 これらの焼 結体からなる基板を用いることで発光効率が少なくとも 8 %以上の発光素子を作製し得る。 本発明において、 光 率が 1 %より小さいかあるいは実質的に^ lii性を有しない炭化珪 素、 窒化珪素、 窒化ガリウム、 酸化亜鉛、 酸化ベリリウムなどの六方晶系及び 化アルミニゥ ムなどの三方晶系あるいは六方晶系として分類できる結晶構造を有する各種セラミック材料を 主成分とする焼結体を基板として用いても優れた発光効率を有する発光軒が作製し得る。 ま た、 光 ¾ 率が 1 %以上の光 ¾i性を有する炭化珪素、 窒化珪素、 窒化ガリウム、 酸化亜鉛、 酸化ベリリゥムなどの六方晶系及び酸化アルミニウムなどの三方晶系あるいは六方晶系として 分類できる結晶構造を有する各種セラミック材料を主成分とする焼結体を基板として用いても 優れた発光効率を有する発光素子が作製し得る。通常上記炭化珪素、窒化珪素、窒化ガリウム、 酸化碰、 酸化ベリリウムなどの六方晶系及ぴ谢匕アルミニウムなどの三方晶系あるいは六方 晶系として分類できる結晶構造を有する各種セラミック材料を主成分とする焼結体を基板とし て用いることにより発光効率が «からのサフアイァなどの基板を用いて作製される発光素子 の発光効率と比べて少なくとも同等か、默3〜4倍以上に改善された発光軒を提供し得る。 より詳しく言えば、 酸化亜鉛を主成分とする焼結体の 過率が 1 %より小さいカ续質的に 光 ¾ 生を有しないもの、 あるいは酸化亜鉛を主成分とする焼結体の ½¾i率が 1 %以上のも のを基板として用いれば発光効率 8 %以上の発光素子を作製し得る。 通常、 酸化亜鉛を主成分 とする焼結体はより高い光 ¾i性を有するものを基板として用いるほうがより発光効率の高い 発光素子を作製し得るので好ましい。 すなわち、 酸化亜鉛を主成分とする焼結体の ¾¾¾率 1 0 %以上のものを基板として用いたときその上に形成される発光素子の発光効率は 1 0 %以上 のものが得られ易い。 また、 酸化亜鉛を主成分とする焼結体の光 ¾i率 2 0 %以上のものを基 板として用いたときその上に形成される発光素子の発光効率は 1 2 %以上のものが得られ易い ので好ましい。 また、 酸化亜鉛を主成分とする焼結体の光透過率 3 0 %以上のものを基板とし て用いたときその上に形成される発光素子の発光効率は 1 5 %以上のものが得られ易い。 また、 酸化亜鉛を主成分とする焼結体の光 ¾ii率 4 0 %以上のものを基板として用いたときその上に 形成される発光^?の発光効率は 2 0 %以上のものが得られ易い。 また、 酸化亜鉛を主成分と する焼結体の光透過率 5 0 %以上のものを基板として用いたときその上に形成される発光素子 の発光効率は 2 5 %以上のものが得られ易い。 前記のように本発明において 率が 6 0 % 以上、 さらに最大 8 0 %以上のものも得られるがこのような高レゝ光 ¾1率を有する酸化亜鉛を 主成分とする焼結体ものを基板として用いたときその上に形成される発光素子の発光効率は 3 0 %以上、 最大 5 5 %のものが得られた。
また、 酸化ベリリウムを主成分とする焼結体の光 率が 1 %より小さいか実質的に光邏 性を有しないもの、 あるいは酸化ベリリウムを主成分とする焼結体の光 ¾1率が 1 %以上のも
のを基板として用いれば発光効率 8 %以上の発光素子を作製し得る。 通常、 酸化ベリリウムを 主成分とする焼結体はより高い光透過性を有するものを基板として用いるほうがより発光効率 の高い発光素子を作製し得るので好ましい。 すなわち、 酸化ベリリウムを主成分とする焼結体 の光 ¾i率 1 0 %以上のものを基板として用いたときその上に形成される発光素子の発光効率 は 1 0 %以上のものが得られ易い。 また、 酸化ベリリウムを主成分とする焼結体の) 率 2 0 %以上のものを基板として用いたときその上に形成される発光素子の発光効率は 1 2 %以上 のものが得られ易いので好ましい。 また、 酸化ベリリウムを主成分とする焼結体の 率 3 0 %以上のものを基板として用いたときその上に形成される発光素子の発光効率は 1 5 %以上 のものが得られ易い。 また、 酸化ベリリウムを主成分とする焼結体の) 率 4 0 %以上のも のを基板として用いたときその上に形成される発光素子の発光効率は 2 0 %以上のものが得ら れ易い。 また、 酸化ベリリウムを主成分とする焼結体の光 ¾ϋ率 5 0 %以上のものを基板とし て用いたときその上に形成される発光素子の発光効率は 2 5 %以上のものが得られ易い。 前記 のように本発明において) ¾®i率が 6 0 %以上、 さらに ¾λ: 8 0 %以上のものも得られるがこ のような高い光 ¾ 率を有する酸化ベリリウムを主成分とする焼結体ものを基板として用いた ときその上に形成される発光素子の発光効率は 3 0 %以上、 最大 5 2 %のものが得られた。 また、 酸化アルミニウムを主成分とする焼結体の舰過率が 1 %より小さいか実質的に舰 過性を有しないもの、 あるいは酸化アルミニウムを主成分とする焼結体の光 ¾ 率が 1 %以上 のものを基板として用いれば発光効率 8 %以上の発光素子を作製し得る。 通常、 酸化アルミ二 ゥムを主成分とする焼結体はより高い光 ¾i性を有するものを基板として用いるほうがより発 光効率の高い発光素子を作製し得るので好ましい。 すなわち、 酸化アルミニウムを主成分とす る焼結体の光 率 1 0 %以上のものを基板として用いたときその上に形成される発光素子の 発光効率は 1 0 %以上のものが得られ易い。 また、 酸化アルミニウムを主成分とする焼結体の 光透過率 2 0 %以上のものを基板として用いたときその上に形成される発光素子の発光効率は 1 2 %以上のものが得られ易いので好ましい。 また、 酸化アルミニウムを主成分とする焼結体 の ¾¾¾率 3 0 %以上のものを基板として用いたときその上に形成される発光素子の発光効率 は 1 5 %以上のものが得られ易い。 また、 酸化アルミニウムを主成分とする焼結体の ¾¾i率 4 0 %以上のものを基板として用いたときその上に形成される発光素子の発光効率は 2 0 %以 上のものが得られ易い。 また、 酸化アルミニウムを主成分とする焼結体の光 ¾1率 5 0 %以上 のものを基板として用いたときその上に形成される発光素子の発光効率は 2 5 %以上のものが 得られ易い。 前記のように本発明において16¾過率が 6 0 %以上、 さらに最大 8 0 %以上のも のも得られるがこのような高い 率を有する酸化アルミニウムを主成分とする焼結体もの を基板として用いたときその上に形成される発光素子の発光効率は 3 0 %以上、 最大 5 1 %の ものが得られた。
また、 窒化ガリウムを主成分とする焼結体の光 ¾i率が 1 %より小さいか実質的に光透過性 を有しないもの、 あるいは窒化ガリゥムを主成分とする能結体の光透過率が 1 %以上のものを 基板として用いれば発光効率 8 %以上の発光素子を作製し得る。 通常、 窒化ガリウムを主成分 とする焼結体はより高い光透過性を有するものを基板として用いるほうがより発光効率の高い 発光素子を作製し得るので好ましい。 すなわち、 窒化ガリウムを主成分とする焼結体の光透過 率 1 0 %以上のものを基板として用いたときその上に形成される発光素子の発光効率は 1 0 % 以上のものが得られ易い。 また、 窒化ガリウムを主成分とする焼結体の ¾¾i率 2 0 %以上の ものを基板として用いたときその上に形成される発光素子の発光効率は 1 2 %以上のものが得 られ易いので好ましい。 また、 窒化ガリウムを主成分とする焼結体の光 ¾i率 3 0 %以上のも のを基板として用いたときその上に形成される発光素子の発光効率は 1 5 %以上のものが得ら れ易い。 また、 窒化ガリウムを主成分とする焼結体の光 ¾1率 4 0 %以上のものを基板として
用いたときその上に形成される発光素子の発光効率は 2 0 %以上のものが得られ易い。 また、 窒化ガリゥムを主成分とする焼結体の光透過率 5 0 %以上のものを基板として用いたときその 上に形成される発光素子の発光効率は 2 5 %以上のものが得られ易い。 前記のように本発明に おいて光 ¾ϋ率が 6 0 %以上、 さらに最大 8 0 %以上のものも得られるがこのような高い光透 過率を有する窒化ガリウムを主成分とする焼結体ものを基板として用いたときその上に形成さ れる発光素子の発光効率は 3 0 %以上、 最大 6 3 %と高いものが得られた。
このように炭化珪素、 窒化珪素、 窒化ガリウム、 酸化 、 酸化ベリリウムなどの六方晶系 及び 匕アルミニウムなどの三方晶系あるいは六方晶系として分類できる結晶構造を有する各 種セラミック材料を主成分とする焼結体を基板として用いて作製される発光素子の発光効率は 少なくとも 8 %以上のものが得られ易いので、 従来からのサファイアなどの基板を用いて作製 される発光素子の発光効率と比べて少なくとも同等か、 最大 3〜 4倍以上に改善された発光素 子を提供し得る。
本発明において、 炭化珪素、 窒化珪素、 窒化ガリウム、 酸化亜鉛、 酸化ベリリウムなどの六 方晶系及び 化アルミニウムなどの三方晶系あるいは六方晶系として分類できる結晶構造を有 する各種セラミック材料を主成分とする焼結体は窒化ガリウム、 窒化インジウム、 窒化アルミ ニゥムのうちから選ばれた少なくとも 1種以上を主成分とする単結晶薄膜が形成できるもので あれば該焼結体中の炭化珪素、 窒化珪素、 窒化ガリウム、 酸化碰、 酸化ベリリウム、 酸化ァ ルミニゥムなどの結晶粒子がどのような大きさのものであっても該炭化珪素、 窒化珪素、 窒化 ガリウム、 酸化亜鉛、 酸化ベリリウムなどの六方晶系及び 化アルミニウムなどの三方晶系ぁ るいは六方晶系として分類できる結晶構造を有する各種セラミック材料を主成分とする焼結体 を基板として用いることにより優れた発光効率を有する発光^?が作製し得る。 通常該発光素 子の発光効率は からのサファイアなどの基板を用いて作製される発光素子の発光効率と比 ベて少なくとも同等か、 最大 3〜 4倍以上に改善された発光素子を提供できる。
通常炭化珪素、 窒化珪素、 窒化ガリウム、 酸化亜鉛、 酸化ベリリウム、 酸化アルミニウムな どの結晶粒子の大きさが平均 0 . 5 m以上の炭化珪素、窒化珪素、窒化ガリウム、酸化赚、 酸化ベリリウムなどの六方晶系及び酸化アルミニウムなどの三方晶系あるいは六方晶系として 分類できる結晶構造を有する各種セラミック材料を主成分とする焼結体を基板として用いるこ とが好ましく «からのサファイアなどの基板を用いて作製される発光素子の発光効率と比べ て少なくとも同等か、 最大 3〜4倍以上に改善された発光素子を作製し得る。
より詳しく言えば、 炭化珪素、 窒化珪素、 窒化ガリウム、 酸化亜鉛、 酸化ベリリウム、 酸化 アルミニウムなどの結晶粒子の大きさが平均 1 . 0 m以上の炭化珪素、 窒化珪素、 窒化ガリ ゥム、 酸化亜鉛、 酸化ベリリウムなどの六方晶系及び酸化アルミニウムなどの三方晶系あるい は六方晶系として分類できる結晶構造を有する各種セラミック材料を主成分とする焼結体を基 板として用いることで発光効率が少なくとも 8 %以上の発光素子を作製し得る。
また、 含まれる結晶粒子が均等に近い大きさに揃っている状態のものだけでなく結晶粒子の 大きさが不揃いのものや結晶粒子の形状がいびつで針状あるいは板状など一辺が小さく他の一 辺が大きい形状の結晶粒子、 例えば) 3— S i 3N4粒子など一辺が数 mで他の一辺が 1 0数 m以上に大きく成長した針状あるいは板状などの形状の結晶粒子を有する炭化珪素、窒化珪素、 窒化ガリウム、 酸化亜鉛、 酸化ベリリウムなどの六方晶系及び 化アルミニウムなどの三方晶 系あるいは六方晶系として分類できる結晶構造を有する各種セラミック材料を主成分とする焼 結体を基板として用いても何ら問題なく発光効率の優れた発光素子を作製することができる。 その他、 炭化珪素、 窒化珪素、 窒化ガリウム、 酸化亜鉛、 酸化ベリリウムなどの六方晶系及 び 化アルミニウムなどの三方晶系あるいは六方晶系として分類できる結晶構造を有する各種 セラミック材料を主成分とする焼結体中に導通ビアを形成したものを基板として用いても窒化
ガリウム、 窒化インジウム、 窒化アルミニウムのうちから選ばれた少なくとも 1種以上を主成 分とする単結晶薄膜が形成可能であり優れた発光効率を有する発光素子が作製し得る。 導通ビ ァとしては導電性を有する材料であればどのようなものでも用いることが 能である。 通常は 導通ビアの材料としてタングステン、 モリブデン、 金、 銀、 銅、 窒化チタンなどを主成分とす る材料が用いられる。 このような材料からなる導通ビアを形成した炭化珪素、 窒化珪素、 窒化 ガリウム、 酸化亜鉛、 酸化ベリリウムなどの六方晶系及び麼化アルミニウムなどの三方晶系ぁ るいは六方晶系として分類できる結晶構造を有する各種セラミツク材料を主成分とする焼結体 を基板として用いることにより、 通常 からのサフアイァなどの基板を用いて作製される発 光素子の発光効率と比べて少なくとも同等か、 最大 3〜4倍以上に改善された発光効率を有す る発光素子を提供し得る。
より詳しく言えば、 炭化珪素、 窒化珪素、 窒化ガリウム、 酸化亜鉛、 酸化ベリリウムなどの 六方晶系及び酸化アルミニウムなどの三方晶系あるいは六方晶系として分類できる結晶構造を 有する各種セラミック材料を主成分とする焼結体中に導通ビアを形成したものを基板として用 いることで発光効率が少なくとも 8 %以上の発光素子を作製し得る。
上記のように、 発光素子を作製するための基板として炭化珪素、 窒化珪素、 窒化ガリウム、 酸化亜鉛、 酸化ベリリウムなどの六方晶系及び 化アルミニウムなどの三方晶系あるいは六方 晶系として分類できる結晶構造を有する各種セラミック材料を主成分とする焼結体を用いるこ とは有効であり、 特に光翻性を有するものであればより発光効率に優れた発光素子が作製し 得ることを説明した。
また本発明において、 炭ィ匕珪素、 窒化珪素、 窒化ガリウム、 酸化亜鉛、 酸化ベリリウムなど の六方晶系及び酸化アルミ二ゥムなどの三方晶系あるいは六方晶系として分類できる結晶構造 を有する各種セラミック材料を主成分とする焼結体からなる基板の表面平滑性としてどのよう な状態のものであっても窒化ガリウム、 窒化インジウム、 窒化アルミニウムのうちから選ばれ た少なくとも 1種以上を主成分とする単結晶薄膜が形成できるものであれば、 該炭化珪素、 窒 化珪素、 窒化ガリウム、 酸化亜鉛、 酸化ベリリウムなどの六方晶系及び 化アルミニウムなど の三方晶系あるいは六方晶系として分類できる結晶構造を有する各種セラミック材料を主成分 とする焼結体からなる基板の上に形成される発光素子は優れた発光効率を有するものが作製し 得る。 通常上記表面平滑性を有する炭化珪素、 窒化珪素、 窒化ガリウム、 酸化亜鉛、 酸化ベリ リウムなどの六方晶系及び酸化アルミニウムなどの三方晶系あるいは六方晶系として分類でき る結晶構造を有する各種セラミック材料を主成分とする焼結体からなる基板を用いることによ り作製される発光素子の発光効率は従来からのサファイアなどの基板を用いて作製される発光 軒の 効率と比べて少なくとも同等か、駄 3〜4倍以上に改善されたものを提供し得る。 より詳しく言えば、 1 ) 炭化珪素、 窒化珪素、 窒化ガリウム、 酸化亜鉛、 酸化ベリリウムな どの六方晶系及び酸化アルミニウムなどの三方晶系あるいは六方晶系として分類できる結晶構 造を有する各種セラミック材料を主成分とする焼結体をそのまま基板として用い、 その上に要 すれば窒化ガリウム、 窒化インジウム、 窒化アルミニウムのうちから選ばれた少なくとも 1種 以上を主成分とする薄膜からなるバッファ層をまず形成し、 その上に窒化ガリウム、 窒化イン ジゥム、 窒化アルミニウムのうちから選ばれた少なくとも 1種以上を主成分とするェピタキシ ャル成長した単結晶薄膜を N型半導体層、 発光層、 P型半導体層、 として積層し発光素子を作 製していく方法の場合、 通常炭化珪素、 窒化珪素、 窒化ガリウム、 酸化亜鉛、 酸化ベリリウム などの六方晶系及び酸化アルミ二ゥムなどの三方晶系あるいは六方晶系として分類できる結晶 構造を有する各種セラミック材料を主成分とする焼結体からなる基板の平均表面粗さ R aが 1 0 0 0 nm以下のものを用いることで発光効率が少なくとも 8 %以上の発光素子を作製し得る。 また、 2 ) 炭化珪素、 窒化珪素、 窒化ガリウム、 酸化亜鉛、 酸化ベリリウムなどの六方晶系
及び mi匕アルミニウムなどの三方晶系あるいは六方晶系として分類できる結晶構造を有する各 種セラミック材料を主成分とする焼結体を基板として作製し、 その上にあらかじめ窒化ガリゥ ム、 窒化インジウム、 窒化アルミニウムのうちから選ばれた少なくとも 1種以上を主成分とす る無定形、 多結晶、 配向性多結晶、 単結晶のうちから選ばれた少なくともいずれかの結晶状態 を有する薄膜を少なくとも 1層以上形成して薄膜基板とし、 該薄膜基板の上に要すれば窒化ガ リゥム、 窒化ィンジゥム、 窒化アルミニゥムのうちから選ばれた少なくとも 1種以上を主成分 とする薄膜からなるバッファ層をまず形成し、 窒化ガリウム、 窒化インジウム、 窒化アルミ二 ゥムのうちから選ばれた少なくとも 1種以上を主成分とするェピタキシャル成長した単結晶薄 膜を N型半導体層、 発光層、 P型半導体層、 として積層して発光素子を作製していく方法、 及 び 3) 炭化珪素、 窒化珪素、 窒化ガリウム、 酸化亜鉛、 酸化ベリリウムなどの六方晶系及び褫 化アルミニウムなどの三方晶系あるいは六方晶系として分類できる結晶構造を有する各種セラ ミック材料を主成分とする焼結体を基板として作製し、 その上にあらかじめ窒化ガリウム、 窒 化インジウム、 窒化アルミニウムのうちから選ばれた少なくとも 1種以上を主成分とする無定 形、 多結晶、 配向性多結晶、 単結晶のうちから選ばれた少なくともいずれかの結晶状態を有す る薄膜を少なくとも 1層以上形成し、 その上にさらに窒化ガリウム、 窒化インジウム、 窒化ァ ルミニゥムのうちから選ばれた少なくとも 1種以上を主成分とする単結晶薄膜を少なくとも 1 層以上形成して薄膜基板とし、 該薄膜基板の上に要すれば窒化ガリウム、 窒化インジウム、 窒 化アルミニウムのうちから選ばれた少なくとも 1種以上を主成分とする薄膜からなるバッファ 層をまず形成し、 その上に窒化ガリウム、 窒化インジウム、 窒化アルミニウムのうちから選ば れた少なくとも 1種以上を主成分とするェピタキシャル成長した単結晶薄膜を N型半導体層、 発光層、 P型半 本層、 として積層して発光素子を作製していく方法、 という上記 2) 〜3) で示した方法により発光軒を作製する:!^、 通常炭化珪素、 窒化珪素、 窒化ガリウム、 酸化 亜铅、 酸化ベリリウムなどの六方晶系及び酸化アルミニウムなどの三方晶系あるいは六方晶系 として分類できる結晶構造を有する各種セラミック材料を主成分とする焼結体からなる基板の 平均表面粗さ R aが 1 0 0 0 nmより大きいものを用いても発光効率が少なくとも 8 %以上の 発光素子を作製し得る。
本発明において、 炭化珪素、 窒化珪素、 窒化ガリウム、 酸化 K 酸化ベリリウムなどの六 方晶系及ぴ褫化アルミニウムなどの三方晶系あるいは^晶系として分類できる結晶構造を有 する各種セラミック材料を主成分とする焼結体からなる基板の厚みはどのようなものであって も窒化ガリウム、 窒化インジウム、 窒化アルミニウムのうちから選ばれた少なくとも 1種以上 を主成分とする単結晶薄膜が形成できるものであれば、該炭化珪素、窒化珪素、窒化ガリウム、 酸化 ffii 酸化ベリリウムなどの六方晶系及び 化アルミニウムなどの三方晶系あるいは六方 晶系として分類できる結晶構造を有する各種セラミック材料を主成分とする焼結体からなる基 板の上に形成される発光素子は優れた発光効率を有するものが作製し得る。 通常上記基板厚み を有する炭化珪素、 窒化珪素、 窒化ガリウム、 酸化亜鉛、 酸化ベリリウムなどの六方晶系及び 酸化アルミニウムなどの三方晶系あるいは六方晶系として分類できる結晶構造を有する各種セ ラミック材料を主成分とする焼結体からなる基板を用いることにより作製される発光素子の発 光効率は従来からのサファイアなどの基板を用いて作製される発光素子の発光効率と比べて少 なくとも同等か、最大 3〜4倍以上に改善されたものを提供し得る。通常炭化珪素、窒化珪素、 窒化ガリウム、 酸化亜鉛、 酸化ベリリウムなどの六方晶系及び酸化アルミニウムなどの三方晶 系あるいは六方晶系として分類できる結晶構造を有する各種セラミック材料を主成分とする焼 結体からなる基板の厚みが 8. Omm以下のものを用いることで発光効率が少なくとも 8 %以 上の発光素子を作製し得る。
以上、舰素子を作製するための基板として炭化珪素、窒化珪素、窒化ガリウム、酸化 «、
酸化ベリリゥムなどの六方晶系及び 化アルミニウムなどの三方晶系あるいは六方晶系として 分類できる結晶構造を有する各種セラミツク材料を主成分とする焼結体を用いることは有効で あり、 該炭化珪素、 窒化珪素、 窒化ガリウム、 酸化亜鉛、 酸化ベリリウムなどの六方晶系及び 酸化アルミニウムなどの三方晶系あるいは六方晶系として分類できる結晶構造を有する各種セ ラミック材料を主成分とする焼結体について純度 (組成)、 y , 鹿結体結晶粒子、 導通ビ ァの有無、 基板としての表面平滑性、 基板としての厚み、 などについてその効果を説明してき た。
上記で説明してきた、 a) 炭化珪素、 窒化珪素、 窒化ガリウム、 酸化亜鉛、 酸化ベリリウム などの六方晶系及び 化アルミニウムなどの三方晶系あるいは六方晶系として分類できる結晶 構造を有する各種セラミック材料を主成分とする焼結体を基板として作製し、 その上にあらか じめ窒化ガリウム、 窒化インジウム、 窒化アルミニウムのうちから選ばれた少なくとも 1種以 上を主成分とする無定形、 多結晶、 配向性多結晶、 単結晶のうちから選ばれた少なくともいず れかの結晶状態を有する薄膜を少なくとも 1層以上形成して薄膜基板とし、 該薄膜基板の上に 発光軒を作製していく方法、 及び b) 炭化珪素、 窒ィ匕珪素、 窒ィ匕ガリウム、 酸化亜鉛、 酸化 ベリリゥムなどの六方晶系及び酸化アルミニウムなどの三方晶系あるいは六方晶系として分類 できる結晶構造を有する各種セラミック材料を主成分とする焼結体を基板として作製し、 その 上にあらかじめ窒化ガリウム、 窒化インジウム、 窒化アルミニウムのうちから選ばれた少なく とも 1種以上を主成分とする無定形、 多結晶、 配向性多結晶、 単結晶のうちから選ばれた少な くともいずれかの結晶状態を有する薄膜を少なくとも 1層以上形成し、 さらにその上に窒化ガ リウム、 窒化インジウム、 窒化アルミニウムのうちから選ばれた少なくとも 1種以上を主成分 とする単結晶薄膜を少なくとも 1層以上形成して薄膜基板とし、 該薄膜基板の上に発光素子を 作製していく方法、 という上記 a)、 b) で示した方法により発光^?を作製する塲合、 炭化珪 素、 窒化珪素、 窒化ガリウム、 酸化亜鉛、 酸化ベリリウムなどの六方晶系及び ¾化アルミニゥ ムなどの三方晶系あるいは六方晶系として分類できる結晶構造を有する各種セラミック材料を 主成分とする焼結体からなる基板にあらかじめ形成する窒化ガリウム、 窒化インジウム、 窒化 アルミニゥムのうちから選ばれた少なくとも 1種以上を主成分とする薄膜が単結晶、 無定形、 多結晶、 配向性多結晶のうちから選ばれた少なくともいずれかの結晶状態を有するものでは、 特に断らない限りその上には通常発光効率 8 %以上の発光素子が作製し得る。 上記の基板にあ らかじめ形成する窒化ガリウム、 窒化インジウム、 窒化アルミニウムのうちから選ばれた少な くとも 1種以上を主成分とする薄膜のうち無定形、 多結晶、 配向性多結晶のうちから選ばれた 少なくともいずれかの結晶状態を有するものがより好ましい。 また、 基板にあらかじめ形成す る窒化ガリウム、 窒化インジウム、 窒化アルミニウムのうちから選ばれた少なくとも 1種以上 を主成分とする薄膜が配向性多結晶の結晶状態を有するものでは、 特に断らない限りその上に は通常発光効率 1 0 %以上の発光素子が作製し得る。 また、 窒化ガリウム、 窒化インジウム、 窒化アルミニウムのうちから選ばれた少なくとも 1種以上を主成分とする薄膜を少なくとも 2 層以上とし、 該 2層以上の薄膜のうち表面のものを単結晶とした基板を用いれば、 基板にあら かじめ形成する薄膜の結晶状態に関係なくその上には通常発光効率 1 0 %以上の発光素子が作 製し得る。
なお、 上記例示した炭化珪素、 窒化珪素、 窒化ガリウム、 酸化亜鉛、 酸化ベリリウム、 酸化 アルミニウムなどを主成分とする焼結体は通常主成分である該炭化珪素、 窒化珪素、 窒化ガリ ゥム、 酸化菌、 酸化ベリリウム、 酸化アルミニウムなどとして六方晶あるい 方晶の結晶 構造を有する主成分とするものが発光素子作製用基板として用いられることを主に例示してき たが上記主成分が例えば立方晶、 正方晶、 斜方晶、 単斜晶、 三斜晶、 アモルファスなど六方晶 あるいは三方晶以外の結晶構造を有するものであっても炭化珪素、 窒化珪素、 窒化ガリウム、
酸化 酸化ベリリウム、 酸化アルミニウムなどを主成分とするものであれば発光素子作製 用基板として好適に用いることができる。 例えば炭化珪素を主成分とする焼結体などは結晶構 造として例えば立方晶を有する炭化珪素を主成分とする焼結体であっても基板として好適に用 いることができる。 また例えぱ衡匕アルミニウムを主成分とする焼結体などは結晶構造として 例えば立方晶、 スピネル構造の酸化アルミニウムを主成分とする焼結体であっても基板として 好適に用いることができる。
本発明において、 上記炭化珪素、 窒化珪素、 窒化ガリウム、 酸化亜鉛、 酸化ベリリウムなど の六方晶系及び酸化アルミニウムなどの三方晶系あるいは六方晶系として分類できる結晶構造 を有する各種セラミック材料を主成分とする焼結体だけでなぐ 例えば ¾化ジルコニウム (ζ r〇2)、 酸化マグネシウム (Mg O)、 アルミン酸マグネシウム (MgA l 204)、 酸化チタン (T i〇2)、 チタン酸バリウム (B a T i〇3)、 チタン酸ジルコン酸鉛 (P Z T :チタンとジ ルコニゥムをモル数 1: 1の割合で含む複合酸化物)、 酸化イットリウム (Y2〇3) などの希土 «化物、 酸 f匕トリウム (T h〇2)、 各種フェライト (F e 304あるいは Mn F e 204など一 «AF e 2〇4であらわされる複合酸化物:ただし、 Aは 2価の金属元素)、 ムライト (3 A 1 203 - 2 S i 02)、フオルステライ卜 (2 Mg O - S i 02)、ステアタイト (Mg O - S i 02)、 結晶化ガラス、 などの各種セラミツク材料を主成分とする焼結体を基板として用いることで発 光効率の優れた概軒が作製し得る。また上記例えぱ谢匕ジルコニウム、酸化マグネシウム、 アルミン酸マグネシウム、 酸化チタン、 チタン酸バリウム、 チタン酸ジルコン酸鉛、 酸化イツ トリウムなどの希土^ ¾素酸化物、 酸ィ匕トリウム、 各種フェライト、 ムライト、 フォルステラ イト、 ステア夕イト、 結晶化ガラス、 などの各種セラミック材料を主成分とする焼結体は光透 過性を有するものが比較的容易に作製できるので、 このような光透過性を有するセラミック材 料を主成分とする焼結体を基板として用いることでも発光効率のより優れた発光素子が作製し 得る。
通常上記炭化珪素、 窒化珪素、 窒化ガリウム、 酸化亜鉛、 酸化ベリリウムなどの六方晶系及 ぴ 化アルミニウムなどの三方晶系あるいは六方晶系として分類できる結晶構造を有する各種 セラミック材料を主成分とする焼結体だけでなぐ 例えば 化ジルコニウム、 酸化マグネシゥ ム、 アルミン酸マグネシウム、 酸化チタン、 チタン酸バリウム、 チタン酸ジルコン蘭、 酸化 イットリウムなどの希土^ ¾素酸ィ匕物、 酸ィ匕トリウム、 各種フェライト、 ムライト、 フォルス テライト、 ステアタイト、 結晶化ガラス、 などの各種セラミック材料を主成分とする焼結体を そのまま基板として用い、 その上に直接窒化ガリウム、 窒化インジウム、 窒化アルミニウムの うちから選ばれた少なくとも 1種以上を主成分とするェピタキシャル成長した単結晶薄膜を形 成することが困難な場合が多いので、 上記各焼結体をそのまま用いてェピタキシャル成長した 単結晶薄膜を N型半導体層、 発光層、 P型半導体層、 として積層し発光素子を作製していく方 法では良好な発光効率を有する発光素子を作製することが通常は困難である。
しかしながら、上記例えば 化ジルコニウム、酸化マグネシウム、アルミン酸マグネシウム、 酸化チタン、 チタン酸バリウム、 チタン酸ジルコン酸鉛、 酸化イットリウムなどの希土類 素 酸化物、 酸化トリウム、 各種フェライト、 ムライト、 フォルステライト、 ステア夕イト、 結晶 化ガラス、 などの各種セラミック材料を主成分とする焼結体からなる基板の上にあらかじめ窒 化ガリウム、 窒化インジウム、 窒化アルミニウムのうちから選ばれた少なくとも 1種以上を主 成分とする無定形、 多結晶、 配向性多結晶のうちから選ばれた少なくともいずれかの結晶状態 を有する薄膜を少なくとも 1層以上形成して薄膜基板とし、 該薄膜基板の上には発光素子を構 成する窒化ガリウム、 窒化インジウム、 窒化アルミニウムのうちから選ばれた少なくとも 1種 以上を主成分とするェピタキシャル成長した単結晶薄膜を N型半導体層、 発光層、 P型半導体 層、 あるいはバッファ層として積層していくことが可能となり、 たとえ光透過率が 1 %より小
さいかあるいは実質的に光 ¾ii性を有しないものであっても少なくとも 8 %以上の発光効率を 有する発光^?を作製し得る。 なおこの際、 あらかじめ形成する窒化ガリウム、 窒化インジゥ ム、 窒化アルミニウムのうちから選ばれた少なくとも 1種以上を主成分とする薄膜の少なくと も一部を発光素子の構成要素として用いることも可能である。
本発明において、 上記のように酸化ジルコニウム、 酸化マグネシウム、 アルミン酸マグネシ ゥム、 酸化チタン、 チタン酸バリウム、 チタン酸ジルコン酸鉛、 酸化イットリウムなどの希土 ^¾素酸化物、酸匕トリウム、各種フェライト、ムライ卜、 フオルステライト、ステアタイト、 結晶化ガラス、 などの各種セラミック材料を主成分とする焼結体からなる基板にあらかじめ窒 化ガリウム、 窒化インジウム、 窒化アルミニウムのうちから選ばれた少なくとも 1種以上を主 成分とする無定形、 多結晶、 配向性多結晶のうちから選ばれた少なくともいずれかの結晶状態 を る薄膜を少なくとも 1層以上形成し、 その上にさらに窒化ガリウム、 窒化インジウム、 窒化アルミニウムのうちから選ばれた少なくとも 1種以上を主成分とする単結晶薄膜を少なく とも 1層以上形成して薄膜基板とし、 該薄膜基板を用いることによりたとえ ¾¾i率が 1 %よ り小さいかあるいは実質的に光透過性を有しないものであっても少なくとも 1 0 %以上の発光 効率を有する発光素子が作製し得るようになるので好ましい。
このように本発明において、 酸化ジルコニウム、 酸化マグネシウム、 アルミン酸マグネシゥ ム、 酸化チタン、 チタン酸バリウム、 チタン酸ジルコン酸铅、 酸化イットリウムなどの希土類 元素酸化物、 酸ィ匕トリウム、 各種フェライト、 ムライト、 フォルステライト、 ステアタイト、 結晶化ガラス、 などの各種セラミック材料を主成分とする焼結体からなる基板を用いても « からのサフアイァなどの単結晶基板を用いて作製される発光素子に比べて発光効率が少なくと も同等か、 最大 2〜3倍以上に改善されたものを提供し得る。
本発明において、 上記の酸化ジルコニウム、 酸化マグネシウム、 アルミン酸マグネシウム、 酸化チタン、 チタン酸バリウム、 チタン酸ジルコン酸鉛、 酸化イットリウムなどの希土誕素 酸化物、 酸化トリウム、 各種フェライト、 ムライト、 フォルステライト、 ステアタイト、 結晶 化ガラス、 など ¾¾i性を有する各種セラミック材料を主成分とする焼結体は光 率として 少なくとも 1 %以上、 通常 1 0 %以上を有するものが作製し得る。 上記酸化ジルコニウム、 酸 化マグネシウム、 アルミン酸マグネシウム、 酸化チタン、 チタン酸バリウム、 チタン酸ジルコ ン蘭(特に希土類 素成分を含むもの)、酸化イットリウム、酸化トリウム、各種フェライ卜、 ムライト、 フオルステライト、 ステアタイト、 結晶化ガラス、 のうちから選ばれた少なくとも 1種以上を主成分とする焼結体は光透過率が 5 0 %以上のものが作製でき、 最大 8 0 %以上の ものも作製し得る。その中で酸化ジルコニウム、酸化マグネシウム、アルミン酸マグネシウム、 酸化イットリウムなどの希土 «化物、 酸化トリウム、 ムライト、 結晶化ガラスのうちから選 ばれた少なくとも 1種以上を主成分とする焼結体を用いることが好ましい。 また特に、 Y2〇3 などの希土 素化合物あるいは C a Oなどのアル力リ土類金属化合物含む酸化ジルコニウム を主成分とする焼結体、 L i Fや N a Fなどのアル力リ金属あるいは C a〇などのアル力リ土 類金属あるいは Y2〇3などの希土^ £素化合物を含む酸化マグネシウムを主成分とする焼結体、 原料中ゃ纖工程中に混入する不純物以外の成分を含まない実質的に酸化マグネシウムだけか らなる焼結体、 C a Oなどのァリレ力リ土類金属あるいは Y2〇 3などの希土^ 5素化合物を含む アルミン酸マグネシウムを主成分とする焼結体、 原料中や製造工程中に混入する不純物以外の 成分を含まない実質的にアルミン酸マグネシウムだけからなる焼結体、 異なる希土 素成分 を含む Υ 2 Ο 3などの希土類 素酸化物を主成分とする焼結体、 原料中や製造工程中に混入する 不純物以外の成分を含まない実質的に Υ203などの希土類 素酸化物だけからなる焼結体、 な どは優れた光 ¾1性のものが作製できるのでより好ましい。 このような光透過性を有する各種 セラミック材料を主成分とする焼結体を基板とし、 該基板にあらかじめ窒化ガリウム、 窒化ィ
ンジゥム、 窒化アルミニウムのうちから選ばれた少なくとも 1種以上を主成分とする単結晶、 無定形、多結晶、配向性多結晶など各種結晶状態の薄膜を形成したものを基板として用いれば、 その上には窒化ガリウム、 窒化インジウム、 窒化アルミニウムのうちから選ばれた少なくとも
1種以上を主成分とする単結晶薄膜が形成し得るので、 このような単結晶薄膜が形成された基 板を用いてその上にあらためて薄膜を形成することで発光素子を作製することもできるし、 あ るいはこのようにして形成された単結晶薄膜をそのまま発光素子を構成する薄膜層の少なくと も一部として使用することにより発光素子を作製することもできる。
本発明において、 上記酸化ジルコニウム、 酸化マグネシウム、 アルミン酸マグネシウム、 酸 化チタン、 チタン酸バリウム、 チタン酸ジルコン,、 酸化イットリウムなどの希土類 素酸 化物、 酸化トリウム、 各種フェライト、 ムライト、 フォルステライト、 ステアタイト、 結晶化 ガラス、 などそれぞれの材料を主成分とする焼結体のうち光透過性を有するものを基板として 用いて作製される発光素子はよりすぐれた発光効率のものが作製可能で従来からのサファイア などの単結晶基板を用いて作製される発光素子に比べて発光効率が少なくとも同等か、 最大 3 〜4倍以上に改善されたものを提供し得る。
より具体的に言えば、上記酸化ジルコニウム、酸化マグネシウム、アルミン酸マグネシウム、 酸化チタン、 チタン酸バリウム、 チタン酸ジルコン酸鉛、 酸化イットリウムなどの希土^ 5素 酸化物、 酸化トリウム、 各種フェライト、 ムライト、 フォルステライト、 ステアタイト、 結晶 化ガラス、 などそれぞれの材料を主成分とする焼結体のうち 1 0 %以上の光透過性を有するも のを基板として用いて作製される発光素子は発光効率 1 0 %以上を有するものを作製し得る。 また、 光 ¾1率が 2 0 %以上のものを基板として用いて作製される発光素子は発光効率 1 2 % 以上を有するものを作製し得る。 また、 率が 3 0 %以上のものを基板として用いて作製 される発光素子は発光効率 1 5 %以上を有するものを作製し得る。 また、 光透過率が 4 0 %以 上のものを基板として用いて作製される発光素子は発光効率 2 0 %以上を有するものを作製し 得る。 また、 光薩率が 5 0 %以上のものを基板として用いて作製される発光素子は発光効率 2 5 %以上を有するものを作製し得る。 また、 光 率が 6 0 %以上のものを基板として用い て作製される発光素子は発光効率 3 0 %以上を有するものを作製し得る。 また、 本発明におい て酸化マグネシウム、 及びアルミン酸マグネシウムを主成分とする焼結体からなる基板でそれ ぞれ 8 3 %及び 8 1 %の¾¾1性を有するものが作製されたが、 これらの基板を用いて作製さ れた発光素子は発光効率がそれぞれ最大 5 1 %及び 5 0 %と優れたものであった。
上記で説明してきたように、 本発明においては酸化ジルコニウム、 酸化マグネシウム、 アル ミン酸マグネシウム、 酸化チタン、 チタン酸バリウム、 チタン酸ジルコン酸鉛、 酸化イツトリ ゥムなどの希土類 J¾素酸ィ匕物、酸ィ匕トリウム、各種フェライ卜、ムライト、 フォルステラィト、 ステアタイト、 結晶化ガラス、 などの各種セラミック材料を主成分とする焼結体を基板として 作製し、 その上にあらかじめ窒化ガリウム、 窒化インジウム、 窒化アルミニウムのうちから選 ばれた少なくとも 1種以上を主成分とする無定形、 多結晶、 配向性多結晶のうちから選ばれた 少なくともいずれかの結晶状態を有する薄膜を少なくとも 1層以上形成して薄膜基板とし、 該 薄膜基板の上に発光素子を作製していく方法により発光素子を作製する場合、 作製される発光
^?は特に断らない限り通常発光効率 8 %以上のものが作製し得る。また、酸化ジルコニウム、 酸化マグネシウム、 アルミン酸マグネシウム、 酸化チタン、 チタン酸バリウム、 チタン酸ジル コン酸鉛、 酸化イットリウムなどの希土 ¾素酸化物、 酸ィ匕トリウム、 各種フェライト、 ムラ イト、 フォルステライト、 ステア夕イト、 結晶化ガラス、 などの各種セラミック材料を主成分 とする焼結体からなる基板にあらかじめ窒化ガリウム、 窒化インジウム、 窒化アルミニウムの うちから選ばれた少なくとも 1種以上を主成分とする無定形、 多結晶、 配向性多結晶のうちか ら選ばれた少なくともいずれかの結晶状態を有する薄膜を少なくとも 1層以上形成し、 その上
にさらに窒化ガリウム、 窒化インジウム、 窒化アルミニウムのうちから選ばれた少なくとも 1 種以上を主成分とする単結晶薄膜を少なくとも 1層以上形成して薄膜基板とし、 該薄膜基板を 用いることにより特に断らない限り通常少なくとも 1 0 %の発光効率を有する発光素子が作製 し得る。
本発明による発光 の特徴はその基板に窒化アルミニウムを主成分とする焼結体、 及び炭 化珪素、 窒化珪素、 窒化ガリウム、 酸化亜鉛、 酸化ベリリウムなどの六方晶系及ぴ 匕アルミ ニゥムなどの三方晶系あるいは六方晶系として分類できる結晶構造を有する各種セラミック材 料を主成分とする焼結体、 及びその他に例えば 化ジルコニウム、 酸化マグネシウム、 アルミ ン酸マグネシウム、 酸化チタン、 チタン酸バリゥム、 チタン酸ジルコン酸鉛、 酸化ィットリウ ムなどの希土 素酸ィ匕物、 酸ィ匕トリウム、 各種フェライト、 ムライト、 フォルステライト、 ステアタイト、 結晶化ガラス、 など各種セラミック材料を主成分とする焼結体を用いた点にあ る。
本発明による発光素子を作製するための基板として、 窒化アルミニウムを主成分とする焼結 体、 及び炭化珪素、 窒化珪素、 窒化ガリウム、 酸化亜鉛、 酸化ベリリウムなどの六方晶系及び 酸化アルミニウムなどの三方晶系あるいは六方晶系として分類できる結晶構造を有する各種セ ラミック材料を主成分とする焼結体、 及びその他に例えば酸ィ匕ジレコ二ゥム、 酸化マグネシゥ ム、 アルミン酸マグネシウム、 酸化チタン、 チタン酸バリウム、 チタン酸ジルコン歸、 酸化 イットリウムなどの希土^ t素酸化物、 酸ィ匕トリウム、 各種フェライト、 ムライト、 フォルス テライト、 ステアタイト、 結晶化ガラス、 など各種セラミック材料を主成分とする焼結体のう ち ¾¾1性を有するものを用いることが発光素子の発光効率を高める上ではより好ましい。 本 発明による発光素子の特徴はさらにこのような ½¾ 性を有する各種セラミック材料を主成分 とする焼結体を発光素子を作製するための基板として用いた点に特徴がある。
本発明による発光素子を作製するための基板として、 窒化アルミニウムを主成分とする焼結 体、 及び炭化珪素、 窒化珪素、 窒化ガリウム、 酸化亜鉛、 酸化ベリリウムなどの六方晶系及び 酸化アルミニウムなどの三方晶系あるいは六方晶系として分類できる結晶構造を有する各種セ ラミック材料を主成分とする焼結体をそのまま基板として用いたものと、 窒化アルミニウムを 主成分とする焼結体、 及び炭化珪素、 窒化珪素、 窒化ガリウム、 酸化疆、 酸化ベリリウムな どの六方晶系及び酸化アルミニウムなどの三方晶系あるいは六方晶系として分類できる結晶構 造を有する各種セラミック材料を主成分とする嫌吉体、及びその他に例えば谢匕ジルコニウム、 酸化マグネシウム、 アルミン酸マグネシウム、 酸化チタン、 チタン酸バリウム、 チタン酸ジル コン^ 酸化イットリウムなどの希土類 素酸化物、 謝匕トリウム、 各種フェライト、 ムラ イト、 フォルステラィト、 ステアタイト、 結晶化ガラス、 など各種セラミック材料を主成分と する焼結体を基板としその上に窒化ガリウム、 窒化インジウム、 窒化アルミニウムのうちから 選ばれた少なくとも 1種以上を主成分とする無定形、 多結晶、 配向性多結晶、 単結晶のうちか ら選ばれた少なくともいずれかの結晶状態の薄膜を少なくとも 1層以上形成して薄膜基板とし たもの、 という少なくとも 2種類の基板がある。 また、 該薄膜基板には窒化アルミニウムを主 成分とする焼結体、 及び炭化珪素、 窒化珪素、 窒化ガリウム、 酸化亜鉛、 酸化ベリリウムなど の六方晶系及び酸化アルミニウムなどの三方晶系あるいは六方晶系として分類できる結晶構造 を有する各種セラミック材料を主成分とする焼結体、 及びその他に例えぱ 化ジルコニウム、 酸化マグネシウム、 アルミン酸マグネシウム、 酸化チタン、 チタン酸バリウム、 チタン酸ジル コン酸鉛、 酸化イットリウムなどの希土!^素酸化物、 酸ィ匕トリウム、 各種フェライト、 ムラ イト、 フォルステライト、 ステアタイト、 結晶化ガラス、 など各種セラミック材料を主成分と する焼結体を基板としその上にあらかじめ窒化ガリウム、 窒化インジウム、 窒化アルミニウム のうちから選ばれた少なくとも 1種以上を主成分とする無定形、 多結晶、 配向性多結晶、 単結
晶などのうちから選ばれた少なくともいずれかの結晶状態の薄膜を少なくとも 1層以上形成し、 さらにその上に窒化ガリウム、 窒化インジウム、 窒化アルミニウムのうちから選ばれた少なく とも 1種以上を主成分とする単結晶薄膜を少なくとも 1層以上形成して薄膜基板としたものも ある。 通常このような発光素子を作製するための薄膜基板のなかで窒化ガリウム、 窒化インジ ゥム、 窒化アルミニウムのうちから選ばれた少なくとも 1種以上を主成分とする単結晶薄膜を 形成したものを用いることが発光素子の発光効率を高める上では好ましい。
本発明において、 上記各種セラミック材料を主成分とする焼結体からなる基板のなかで、 窒 化アルミニゥムを主成分とする焼結体を用いたものがより発光効率の優れた発光素子が得られ 易いので好ましい。 すなわち、 具体的には窒化アルミニウムを主成分とする焼結体をそのまま 基板として用いたもの、 及び窒化アルミニウムを主成分とする能結体を基板としその上に窒化 ガリウム、 窒化インジウム、 窒化アルミニウムのうちから選ばれた少なくとも 1種以上を主成 分とする無定形、 多結晶、 配向性多結晶、 単結晶のうちから選ばれた少なくともいずれかの結 晶状態の薄膜を少なくとも 1層以上形成して薄膜基板としたもの、 及び該薄膜基板のなかで窒 化アルミニウムを主成分とする焼結体を基板としその上にあらかじめ窒化ガリゥム、 窒化ィン ジゥム、 窒化アルミニウムのうちから選ばれた少なくとも 1種以上を主成分とする無定形、 多 結晶、 配向性多結晶、 単結晶のうちから選ばれた少なくともいずれかの結晶状態の薄膜を少な くとも 1層以上形成し、 さらにその上に窒化ガリウム、 窒化インジウム、 窒化アルミニウムの うちから選ばれた少なくとも 1種以上を主成分とする単結晶薄膜を少なくとも 1層以上形成し て薄膜基板としたもの、 などである。
また、 上記各種セラミック材料を主成分とする焼結体からなる基板のなかで、 酸化亜鉛を主 成分とする焼結体を用いたものが発光効率の比較的優れた発光軒を作製でき、 さらに纖化 亜鉛を主成分とする焼結体は光 ¾ 率が 1 0 %以下あるいはさらに^ 率が 0 %と 性 が小さいかあるいは ¾¾1性を有しないものであっても室温における抵抗率 1 X 1 0 2 Ω - c m 以下の導電性のものも作製でき上下導通タイプの電極配置の発光素子を作製し得るので好まし い。
また、 上記各種セラミック材料を主成分とする焼結体からなる基板のなかで、 光翻性を有 する焼結体を用いたものがより発光効率の優れた発光素子が得られ易いので好ましい。 上記酸 ィ匕亜鉛を主成分とする焼結体は光 ¾i性と同時に導電性を有するものが得られるので発光効率 に優れた上下導通タイプの電極配置の発光素子を作製し得るので好ましい。
上記窒化アルミニウムを主成分とする焼結体、 及び炭化珪素、 窒化珪素、 窒化ガリウム、 酸 化亜紛、 酸化ベリリウムなどの六方晶系及び酸化アルミニウムなどの三方晶系あるいは六方晶 系として分類できる結晶構造を有する各種セラミック材料を主成分とする焼結体、 及びその他 に例えば谢匕ジルコニウム、 酸化マグネシウム、 アルミン酸マグネシウム、 酸化チタン、 チタ ン酸バリウム、 チタン酸ジルコン酸鉛、 酸化イットリウムなどの希土 素酸化物、 酸化トリ ゥム、 各種フェライト、 ムライト、 フォルステライト、 ステア夕イト、 結晶化ガラス、 など各 種セラミック材料を主成分とする焼結体に、 窒化ガリウム、 窒化インジウム、 窒化アルミニゥ ムのうちから選ばれた少なくとも 1種以上を主成分とする無定形、 多結晶、 配向性多結晶、 単 結晶のうちから選ばれた少なくともいずれかの結晶状態の薄膜を少なくとも 1層以上形成した 薄膜基板は、 該薄膜基板に形成された鍵化ガリウム、 窒化インジウム、 窒化アルミニウムの うちから選ばれた少なくとも 1種以上を主成分とする無定形、 多結晶、 配向性多結晶、 単結晶 のうちから選ばれた少なくともいずれかの結晶状態の薄膜が形成されたままの状態で する こともできるし、 あるいは該薄膜を鏡面など研磨にした状態で用いることもできる。
また、 窒化アルミニウムを主成分とする焼結体、 及び炭化珪素、 窒化珪素、 窒化ガリウム、 酸化亜鉛、 酸化ベリリウムなどの六方晶系及び 化アルミニウムなどの三方晶系あるいは六方
晶系として分類できる結晶構造を有する各種セラミック材料を主成分とする焼結体、 及びその 他に例えば酸化ジルコニウム、 酸化マグネシウム、 アルミン酸マグネシウム、 酸化チタン、 チ タン酸バリウム、 チタン酸ジルコン酸鉛、 酸化イットリウムなどの希土類 素酸化物、 酸化ト リウム、 各種フェライト、 ムライト、 フォルステライト、 ステア夕イト、 結晶化ガラス、 など 各種セラミック材料を主成分とする焼結体に、 あらかじめ窒化ガリウム、 窒化インジウム、 窒 化アルミニウムのうちから選ばれた少なくとも 1種以上を主成分とする無定形、 多結晶、 配向 性多結晶、 単結晶のうちから選ばれた少なくともいずれかの結晶状態の薄膜を少なくとも 1層 以上形成し、 さらにその上に窒化ガリウム、 窒化インジウム、 窒化アルミニウムのうちから選 ばれた少なくとも 1種以上を主成分とする単結晶薄膜を少なくとも 1層以上形成した薄膜基板 は、 該薄膜基板に形成された該窒化ガリウム、 窒化インジウム、 窒化アルミニウムのうちから 選ばれた少なくとも 1種以上を主成分とする単結晶薄膜が形成されたままの状態で使用するこ ともできるし、 あるいは該単結晶薄膜を鏡面など研磨した状態で用いることもできる。
上記薄膜基板の表面平滑性は薄膜が形成されたままの状態でもすなわち自発的に平均表面粗 さ R aが少なくとも 1 0 nm以下のものが得られ、 さらに自発的に平均表面粗さ R aが 3 nm 以下、あるいは 2 nm以下、あるいは l nm以下の薄膜基板も比較的容易に作製し得る。また、 該薄膜基板をメカノケミカルな方法などを用いた鏡面研磨などによっても少なくとも平均表面 粗さ R aが少なくとも 1 0 nm以下のものが得られ、 さらに平均表面粗さ R aが 3 nm以下、 あるいは 2 nm以下、 あるいは l nm以下の薄膜基板も比較的容易に作製し得る。 したがって 仮に基板に形成した薄膜の自発的な表面平滑性が低かつたとしても、 上記の研磨あるいは研削 などをの方法を用いて目的とする表面平滑性の薄膜基板を作製することができる。
このような表面平滑性を有する薄膜基板を用いることにより発光効率の優れた発光素子が作 製し得る。
本発明による発光素子〖堪扳として上記のように窒化アルミニウムを主成分とする焼結体、 及び炭化珪素、 窒化珪素、 窒化ガリウム、 酸化亜鉛、 酸化ベリリウムなどの六方晶結晶系及び 酸化アルミニウムなどの三方晶結晶系あるいは^晶系として分類できる結晶構造を有する各 種セラミック材料を主成分とする焼結体、 及びその他に例えぱ 化ジルコニウム、 酸化マグネ シゥム、 アルミン酸マグネシウム、 酸化チタン、 チタン酸バリウム、 チタン酸ジルコン^ 酸化イットリウムなどの希土 素酸化物、 酸ィ匕トリウム、 各種フェライト、 ムライト、 フォ ルステライト、 ステアタイト、 結晶化ガラスなど各種セラミック材料を主成分とする焼結体、 を用いた点が大きな特徴である。 さらに光»性を有する各種セラミック材料を主成分とする 焼結体を用いた点が大きな特徴である。 本発明において、 発光素子はこれらのセラミック材料 を主成分とする焼結体からなる基板をそのまま用いてその上に作製する、 あるいはこれらのセ ラミック材料を主成分とする焼結体からなる基板に窒化ガリウム、 窒化インジウム、 窒化アル ミニゥムのうちから選ばれた少なくとも 1種以上を主成分とする薄膜を形成後その上に作製し ていく、 あるいはこれらのセラミック材料を主成分とする焼結体からなる基板に窒化ガリウム、 窒化インジウム、 窒化アルミニウムのうちから選ばれた少なくとも 1種以上を主成分とする薄 膜を形成して薄膜基板とし該薄膜基板の上に作製していく、 といった方法で提供することがで きる。 上記のセラミック材料を主成分とする焼結体からなる基板として、 図 3、 図 5〜図 8、 図 1 0〜図 2 0、 図 3 6〜図 3 8に例示するものなどが好適に用いられる。
上記発光素子を作製していく前にセラミツク材料を主成分とする基板に形成される窒化ガリ ゥム、 窒化インジウム、 窒化アルミニウムのうちから選ばれた少なくとも 1種以上を主成分と する薄膜、 及び薄膜基板を作製するためにセラミック材料を主成分とする基板に形成される窒 化ガリウム、 窒化インジウム、 窒化アルミニウムのうちから選ばれた少なくとも 1種以上を主 成分とする薄膜は通常スパッタリング法、あるいはイオンプレーティング法、あるいは蒸着法、
あるいは MOCVD法、 あるいは MOVP E法、 あるいはその他の CVD法、 あるいはクロラ イド V P E法などのハライド V P E法、 あるいはその他のハライド VP E法、 あるいは MB E 法などの方法により形成される。 該薄膜としては単結晶、 無定形、 多結晶、 配向性多結晶など 各種結晶状態のものが用い得る。 該薄膜は単一層あるいは少なくとも 2層以上の多層構成のも のも問題なく用いることができる。 該薄膜を単一層として形成する場合、 無定形、 多結晶、 配 向性多結晶のうちから選ばれた少なくともいずれかの結晶状態で形成することがその上に結晶 性及び表面平滑性などの特性がより優れた単結晶薄膜が形成でき発光素子の発光効率を高める 上で好ましい。 また、 該薄膜を単一層として形成する場合、 配向性多結晶の結晶状態で形成す ることがその上に結晶性及び表面平滑性などの特性がさらに優れた単結晶薄膜が形成できるの でさらに好ましい。 該薄膜のうち配向性多結晶状態あるいは単結晶状態で形成する場合〖¾1常 結晶の C軸が基板面に対して垂直方向に形成されたものが用いられる。 上記のように該薄膜は 単一の層構成でなく複数の層 (例えば組成が異なる、 あるいは結晶状態が異なる、 など) から 構成されたものであってもよい。 該薄膜が複数層で形成される場合表面層の薄膜が結晶性の優 れた単結晶として形成し得るのでその上には発光効率の優れた発光素子が作製し得る。 このよ うな結晶性のより優れた単結晶薄膜を形成するためには上記セラミック材料を主成分とする焼 結体からなる基板にあらかじめ無定形、 多結晶、 配向' 14 結晶のうちから選ばれた少なくとも いずれかの結晶状態の薄膜を形成しておくことが好ましい。 また、 あらかじめ配向性多結晶状 態の薄膜を形成しておくことがさらに好ましい。 該薄膜は導電性を有するものであってもよい が必ずしも導電性を有するものでなくともよい。該薄膜には主成分に対して S i (珪素)、 G e
(ゲルマニウム)、 S e (セレン)、 T e (テフレレ)、 〇 (酸素)、 Mg (マグネシウム)、 B e (ベ リリウム)、 C a (カリレシゥム)、 Z n (亜鉛)、 C d (カドミウム)、 C (炭素) などのドーピ ング成分を加えることで該薄膜を N型半導体化あるいは P型半導体化することで比較的容易に 導電性を付与することができる。
上記のように本発明によりセラミツク材料を主成分とする焼結体及び;) 性を有するセラ ミック材料を主成分とする焼結体のうちから選ばれた少なくともいずれかの焼結体を発光素子 作製用基板として用いることで高い発光効率を有する発光素子が難できるようになった。 本 発明においては発光素子の発光効率をさらに高めることが^能である。 具体的には以下に述べ る少なくとも 2つの方法がある。 すなわち、 1 ) 表面粗さの比較的大きなセラミック材料を主 成分とする焼結体及び光 性を有するセラミック材料を主成分とする焼結体のうちから選ば れた少なくともいずれかの焼結体を基板として用いる、 2) 基板として用いるセラミック材料 を主成分とする焼結体及び 性を有するセラミック材料を主成分とする焼結体のうちから 選ばれた少なくともいずれかの焼結体に形成する薄膜として少なくとも窒化ガリゥムを含むか あるいは窒化ガリウムを主成分とするものを用いる、 ことである。 これらの方法をさらに詳し く説明を行う。
まず上記 1 ) の方法であるが、 発光素子を構成する窒化ガリウム、 窒化インジウム、 窒化ァ ルミニゥムのうちから選ばれた少なくとも 1種以上を主成分とする薄膜からなる少なくとも Ν 型半導体層及び発光層及び Ρ型半導体層を含む積層体を形成するセラミック材料を主成分とす る焼結体の表面を比較的凹凸の多い状態とすることで発光素子の発光効率が向上する。 すなわ ち、 例えば鏡面研磨された面のように比較的凹凸の少ない表面状態のセラミック材料を主成分 とする焼結体を発光素子作製用基板として用いて作製される発光素子の発光効率に比べて、 同 じセラミック材料を主成分とする焼結体で表面の凹凸が比較的多いものを用いて作製される発 光素子の発光効率は少なくとも同等かそれ以上の、 通常は 2 %〜 5 0 %程度高い発光素子をも たらす場合が多い。 すなわち例えば鏡面研磨された面のように凹凸の少ない表面状態のセラミ ック材料を主成分とする焼結体を発光素子作製用基板として用いて作製される発光素子の発光
効率が 1 0 %であれば、 上記のように比較的凹凸の多い表面状態のセラミック材料を主成分と する焼結体を発光素子作製用基板として用いた場合は発光効率が少なくとも 1 0 %以上、 通常 は発光効率が 1 2 %〜 6 0 %の発光素子を作製し得る。 このような表面状態のセラミック材料 を主成分とする焼結体を用いることで、 微粒子の集合体である該セラミック材料を主成分とす る焼結体が本来有する発光素子の発光効率を向上させ易いという効果をさらに高めることが可 能となる。
上記比較的凹凸の多い表面状態のセラミック材料を主成分とする焼結体を用いて発光素子を 作製する場合に見られる発光効率の向上は、 該セラミック材料を主成分とする焼結体力 性を有するか否かに拘わらず見られる。 セラミック材料を主成分とする焼結体が光¾¾ '生を有 する場合、 該セラミック材料を主成分とする焼結体を用いて作製される発光素子は比較的高い 発光効率を有するものが得られ易いが、 セラミック材料を主成分とする焼結体が ¾¾¾性を有 しその表面が比較的凹凸の多い表面状態言い換えれば表面粗さの大きいものであれば、 該セラ ミック材料を主成分とする焼結体を用いて作製される発光素子はさらに高い発光効率を有する ものが得られ易い。 本発明においては例えば光 ¾1率 8 0 %以上を有する例えば窒化ガリウム を主成分とする焼結体、 窒化アルミニウムを主成分とする焼結体、 酸化亜鉛を主成分とする焼 結体などを用いて作製した発光素子では発光効率 7 0 %以上のものが作製し得る。 また、 セラ ミック材料を主成分とする焼結体が光 ¾1性を有しないものであってもその表面が比較的凹凸 の多い表面状態であれば、 該セラミック材料を主成分とする焼結体を用いて作製される発光素 子は同じ光 ¾i性を有しないセラミック材料を主成分とする焼結体で比較的凹凸の少ない表面 状態のものを用いて作製される発光素子に比べて高い発光効率を有するものが得られ易い。 セラミック材料を主成分とする能結体の表面が比較的凹凸の多い状態とは通常表面平滑性の 小さい、 言い換えれば表面粗さの大きい状態を意味する。 また、 セラミック材料を主成分とす る焼結体の表面が比較的凹凸の多い状態のものには、 例えば焼き放し s— f i r e ) 表面 やラップ研削された表面、あるいはブラスト研磨された表面、あるいは化学的にエッチング(腐 食) された表面、 などのように比較的不規則な凹凸状態からなるものだけでなぐ 例えば溝切 りなど機械的な加工を施し規則的な桝目状、 円形状、 直線状などの凹凸が形成されたものなど も含まれる。 溝切りなどの機械加工は例えばダイヤモンドブレ一ドゃダイヤモンドドリルなど のダイヤモンド工具を用いる方法、 超音波を用いる方法、 レーザーを用いる方法、 などが好適 に用いられる。 上記繊啲な桝目状、 円形状、 直線状などの凹凸の形成は機械的な加工法だけ に限らず例えばセラミック材料を主成分とする焼結体に規則的な空隙が形成されているレジス トなどのマスクを施し、 空隙部分のセラミック材料を主成分とする焼結体部分だけをィ匕学的に 薬液あるいは不活性ガス、 フッ素、 酸素などの成分を含有するイオンビームやプラズマガスな どによる R I E (反応性イオンエッツチング)、 E C R (電子サイクロトロン共鳴)、 イオンミ リングなどのドライ方式でエッチングしたり、 サンドブラストなどによる物理的な加工法によ つても達成できる。
上記のように本発明において、 セラミック材料を主成分とする焼結体を機械的方法、 物理的 方法あるいは化学的方法などを用いて加工することにより表面粗さの大きいセラミツク材料を 主成分とする焼結体を得ることができる。
また一方、 本発明においては機械的方法あるいは物理的方法あるいは化学的方法などを用い て焼成後のセラミック材料を主成分とする焼結体の表面を特に加工しなくても粉末成形体を焼 成することで焼き放し (a s— f i r e ) のものであっても表面粗さの大きいセラミック材料 を主成分とする焼結体を得ることができる。 焼き放し (a s— f i r e) の状態で表面粗さの 大きいセラミック材料を主成分とする焼結体を得る場合、 焼成前の粉末成形体として特に表面 粗さを大きくしたものでなくても粉末成形体の焼成過程で自発的にセラミック材料を主成分と
する焼結体が表面粗さの大きい状態を有するものとなり得る。 また、 焼き放し (a s— ί i r e ) 状態で表面粗さの大きいセラミック材料を主成分とする焼結体を得る場合、 焼成前の粉末 成形体として表面粗さの大きいものを用いることも有効である。 より具体的に言えば、 目的と するセラミック材料を主成分とする粉末を例えばシート成形や一軸プレス成形あるいは静水圧 ( I s o s t a t i c P r e s s ) 成形あるいは铸込み成形あるいは押し出し成形などの成 形法によって作製した粉末成形体を表面粗さの大きい状態に加工し該粉末成形体を«するこ とで焼き放し (a s— f i r e) の状態で表面粗さの大きいセラミック材料を主成分とする焼 結体が作製できる。 上記粉末成形体の表面粗さを大きくする方法としては一旦作製した粉末成 形体の表面を溝切りやサンドプラストあるいはブラシ研磨などの機械的方法あるいはその他に 物理的方法あるいは化学的方法などにより後から加工する方法がある。 上記粉末成形体を後か ら加工し粉末成形体の表面粗さを大きくする方法の場合、 凹凸など¾|:の形状を有する型や針 状や棒状といった形状を有する治工具を粉末成形体に押しつけて前記型や治工具に形成された 形状のものを粉末成形体の表面に形成し目的とする表面粗さの大きい粉末成形体を得る、 とい つた方法なども用いることができる。 例えばドクターブレード法によるシート成形などにより シ一ト状の粉末成形体を作製し該1粉末成形体の表面粗さを大きくする場合、 上記シート成形体 は溶媒の乾燥過程で自発的に形成された表面状態を有し易く表面粗さの制御範囲が狭い場合が 多いので上記のような後から粉末成形体の表面粗さを大きくする方法が有効に ¾δでき、 任意 の表面粗さのシート成形体を作製することが 能である。 粉末成形体の表面に後から上記例示 した型や治工具などを押し付けて表面粗さの大きなものを形成する場合室温で行うこともでき るが、 含まれるバインダーや可翻などの種類や量などにより該粉末成形体を建例えば室温 〜2 0 0 程度の? 範囲に加熱し該粉末成形体を柔らかい状態にしたものを用いることで型 や治工具に形成された形状のものがそのまま粉末成形体の表面により一層形成され易くなりそ の結果目的とする表面粗さを有する粉末成形体をより好適に作製することができる。 加熱して 柔らかい状態にした粉末成形体を用い型や治工具などを押し付けて表面粗さの大きレ粉末成形 体を作製する方法は、 例えばドク夕一ブレード法によるシート状の粉末成形体の表面粗さを大 きくする場合などに対して好適に用いることができる。 上記例示した型あるいは治工具を粉末 成形体に押しつけて目的とする表面粗さの大きレ粉末成形体を得る方法において、 型や治工具 を押し付けるときの圧力¾1常 2 0 0 Kg/ cm2以下で十分効果が発揮し得る。加熱して柔ら かい状態の粉末成形体を用いる場合は通常 1 0 O KgZc m2以下の圧力で十分効果が発揮し 得る。
また、 上記粉末成形体の表面粗さを大きくする方法として成形するとき同時に該粉末成形体 の表面粗さを大きくする方法があり好適に用いることができる。 例えば一軸プレス成形ゃ静水 圧成形あるいは^ Eみ成形などにより粉末成形体を作製する場合、 成形用の金型やゴム型ある いは石膏型などの型に凹凸や溝など適宜の形状を施し成形と同時に凹凸や溝などの形状が形成 された粉末成形体が作製できその結果目的とする表面状態を有する粉末成形体が得られる。 ま た例えば押し出し成形により粉末成形体を作製する場合、 成形用の口金に凹凸などの形状を施 したものを用いれば成形と同時に成形方向に溝あるいは凹凸などの形状が形成された成形体が 作製できその結果表面粗さの大きレゝ粉末成形体が得られる。 もちろん上記例示した一軸プレス 成形や静水圧成形あるいは »み成形あるいは押し出し成形などを用いて作製した粉末成形体 においては成形と同時に表面粗さを大きく方法だけでなく、 成形後に前記機械的あるいは物理 的あるいは化学的な方法などで表面粗さを大きくすることもできる。 このような成形後あるい は成形と同時に表面粗さを大きくした粉末成形体を用いて表面粗さの大きいセラミック材料を 主成分とする焼結体を得ることができる。
なおその他、 焼き放し (a s— f i r e) の状態で表面粗さの大きいセラミック材料を主成
分とする焼結体を得る場合、ホットプレスや H I P法などの高圧焼成法も用いることができる。 例えば凹凸や溝など適宜の形状を施した力一ボン製などの型を用いてホットプレスを行ないセ ラミック材料を主成分とする成形用粉末を焼結すると同時に凹凸や溝などの形状が形成された セラミック材料を主成分とする焼結体が作製でき、 その結果焼き放し (a s _ f i r e ) の状 態で目的とする表面粗さの大きいセラミック材料を主成分とする焼結体が得られる。
上記のように、 本発明においてはセラミック材料を主成分とする焼結体を機械的方法、 物理 的方法あるいは化学的方法などを用いて加工することにより表面粗さの大きいセラミック材料 を主成分とする焼結体を得ることができる。 また焼き放し (a s _ f i r e ) 状態で自発的に 表面粗さの大きいセラミック材料を主成分とする焼結体を得ることができる。 さらに、 表面粗 さの大きな粉末成形体を用いて焼成することで表面粗さの大きいセラミック材料を主成分とす る焼吉体を得ること力 sできる。
本発明において、 上記で例示した表面粗さの大きいセラミック材料を主成分とする焼結体に は窒化ガリウム、 窒化インジウム、 窒化アルミニウムのうちから選ばれた少なくとも 1種以上 を主成分とする単結晶薄膜が形成し得る。 該単結晶薄膜はあらかじめ窒化ガリウム、 窒化イン ジゥム、 窒化アルミニウムのうちから選ばれた少なくとも 1種以上を主成分とする無定形、 多 結晶、 配向性多結晶、 単結晶などの結晶状態を有する薄膜が形成された表面粗さの大きいセラ ミック材料を主成分とする焼結体に対してだけでなく、 該表面粗さの大きいセラミック材料を 主成分とする焼結体に対して直接形成し得る。 該単結晶薄膜は形 法を工夫することで表面 粗さの大きいセラミック材料を主成分とする焼結体に対してであっても比較的容易に直接形成 し得る。 例えば、 薄膜の原料となるガリウム成分、 インジウム成分及びアルミニウム成分を該 表面粗さの大きいセラミック材料を主成分とする焼結体に対して特定の方向から供給するなど の工夫で直接形成し得る。 より具体的にいえば、 薄膜の原料となるガリウム成分、 インジウム 成分及びアルミニゥム成分の供給をセラミック材料を主成分とする焼結体からなる基板面に対 して垂直及び水平及び斜めのうちから選ばれた少なくとも 1以上の方向から行うことで、 表面 粗さの大きいセラミック材料を主成分とする焼結体に対して窒化ガリゥム、 窒化ィンジゥム、 窒化アルミニウムのうちから選ばれた少なくとも 1種以上を主成分とする単結晶薄膜が直接形 成し得る。 通常薄膜の原料となるガリウム成分、 インジウム成分及びアルミニウム成分をセラ ミック材料を主成分とする焼結体からなる基板面に対して垂直及び水平及び斜めのうちから選 ばれた少なくとも 2以上の方向から供給することで、 表面粗さの大きいセラミツク材料を主成 分とする焼結体に対して窒化ガリウム、 窒化インジウム、 窒化アルミニウムのうちから選ばれ た少なくとも 1種以上を主成分とする結晶性に優れた単結晶薄膜がt接形成し得る。すなわち、 1 ) 上記薄膜の原料となるガリウム成分、 インジウム成分及びアルミニウム成分の供給をセラ ミック材料を主成分とする焼結体からなる基板面に対して垂直方向から行う、 2 ) 上記薄膜の 原料となるガリゥム成分、 ィンジゥム成分及びアルミニゥム成分の供給をセラミツク材料を主 成分とする焼結体からなる基板面に対して水平方向から行う、 3 ) 上記薄膜の原料となるガリ ゥム成分、 ィンジゥム成分及びアルミニゥム成分の供給をセラミック材料を主成分とする焼結 体からなる基板面に対して斜め方向から行う、 4) 上記薄膜の原料となるガリウム成分、 イン ジゥム成分及びアルミニウム成分の供給をセラミック材料を主成分とする焼結体からなる基板 面に対して垂直方向及び水平方向の 2方向から行う、 5 )上記薄膜の原料となるガリウム成分、 ィンジゥム成分及びアルミニゥム成分の供給をセラミック材料を主成分とする焼結体からなる 基板面に対して垂直方向及び斜め方向の 2方向から行う、 6 ) 上記薄膜の原料となるガリウム 成分、 ィンジゥム成分及びアルミニウム成分の供給をセラミック材料を主成分とする焼結体か らなる基板面に対して水平方向及び斜め方向の 2方向から行う、 7 ) 上記薄膜の原料となるガ リゥム成分、 ィンジゥム成分及びアルミニゥム成分の供給をセラミック材料を主成分とする焼
結体からなる基板面に対して垂直方向及び水平方向及び斜め方向の 3方向から行う、 という少 なくとも 7つの方法で薄膜の原料を供給することで表面粗さの大きいセラミック材料を主成分 とする焼結体に対して窒化ガリウム、 窒化インジウム、 窒化アルミニウムのうちから選ばれた 少なくとも 1種以上を主成分とする単結晶薄膜が 接形成し得る。 なお、 薄膜の原料となるガ リウム成分、 インジウム成分及びアルミニウム成分の供給方向が斜めであるということは、 該 供給方向が基板面に対して垂直及び水平以外のすべての方向であるということを意味する。 本発明において、 窒化ガリウム、 窒化インジウム、 窒化アルミニウムのうちから選ばれた少 なくとも 1種以上を主成分とする単結晶薄膜は例えば MO CVD法あるいは八ライド VP E法 などガリウム成分、 インジウム成分、 及びアルミニウム成分を含む化合物を一旦分解しその後 アンモニアなどの反応ガスとの窒化反応により目的とする組成のものを作製する方法により良 好な結晶性のものが形成される場合が多いので、 薄膜の原料を特定の方向から供給することは 容易であり効果的に単結晶薄膜を形成することが可能となり得る。 より具体的にいえば、 例え ば MO CVD法ゃハライド VP E法を用いて単結晶薄膜を形成する場合、 主原料である例えば 有機ガリウム化合物、 有機インジウム化合物、 有機アルミニウム化合物、 ガリウムのハロゲン 化物、 インジウムのハロゲン化物、 アルミニウムのハロゲン化物をセラミック材料を主成分と する焼結体からなる基板面に対して垂直及び水平及び斜めのうちから選ばれた少なくとも 1以 上の方向から供給することで、 比較的表面粗さの大きいセラミック材料を主成分とする 体 であってもその表面には窒化ガリウム、 窒化インジウム、 窒化アルミニウムのうちから選ばれ た少なくとも 1種以上を主成分とする単結晶薄膜が直接形成し得る。 通常上記主原料である例 えば有機ガリウム化合物、 有機インジウム化合物、 有機アルミニウム化合物、 ガリウムのハロ ゲン化物、 インジウムのハロゲン化物、 アルミニウムのハロゲン化物をセラミック材料を主成 分とする焼結体からなる基板面に対して垂直及び水平及び斜めのうちから選ばれた少なくとも 2以上の方向から供給することが形成される単結晶薄膜の結晶性を高める上で好ましい。 該単 結晶薄膜としてミラー指数 ( 0 0 2) の格子面の X線回折ロッキングカーブの半値幅として少 なくとも 3 0 0秒以下の比較的結晶性に優れたものが形成し得る。 通常 MO CVD法あるいは 八ライド V P E法などの方法を用いる場合ガリゥム成分、 ィンジゥム成分、 及びアルミニウム 成分を含む主原料は水素あるいは窒素 +水素あるいはアルゴンなどのキヤリァガスとともに供 給される。 また、 反応ガスであるアンモニアや窒素あるいは水素などもセラミック材料を主成 分とする焼結体からなる基板面に対して垂直及び水平及び斜めのうちから選ばれた少なくとも 1以上好ましくは 2以上の方向から供給することが該セラミツク材料を主成分とする焼結体に 窒化ガリウム、 窒化インジウム、 窒化アルミニウムのうちから選ばれた少なくとも 1種以上を 主成分とする単結晶薄膜を直接形成する上で好ましい。 このように本発明において、 表面粗さ の大きいセラミック材料を主成分とする焼結体であっても窒化ガリウム、 窒化インジウム、 窒 化アルミニウムのうちから選ばれた少なくとも 1種以上を主成分とする単結晶薄膜が形成でき る。 その結果本発明において、 表面粗さの大きいセラミック材料を主成分とする焼結体を用い ることで高い発光効率を有する発光素子を作製することができる。
なお、 表面粗さの大きい窒化アルミニウムを主成分とする焼結体、 あるいは酸化亜鉛を主成 分とする焼結体、 酸化ベリリウムを主成分とする焼結体、 酸化アルミニウムを主成分とする焼 結体、 炭化珪素を主成分とする焼結体、 窒化珪素を主成分とする焼結体、 窒化ガリウムを主成 分とする焼結体など六方晶系又 方晶系のうちから選ばれた少なくともいずれかの結晶構造 を有する表面粗さの大きいセラミック材料を主成分とする焼結体に対しては薄膜の原料となる ガリゥム成分、 ィンジゥム成分及びアルミニゥム成分の供給を上記のようにセラミック材料を 主成分とする焼結体からなる基板面に対して垂直及び水平及び斜めのうちから選ばれた少なく とも 1以上あるいは少なくとも 2以上といった特定の方向から行わなくても、 すなわち薄膜の
原料供給の方向を特に限定しなくても窒化ガリウム、 窒化インジウム、 窒化アルミニウムのう ちから選ばれた少なくとも 1種以上を主成分とする単結晶薄膜が直接形成し得るが、 結晶性の 優れた単結晶薄膜を形成する上では薄膜の原料となるガリゥム成分、 ィンジゥム成分及びアル ミニゥム成分を上記のように少なくとも 1以上好ましくは 2以上の方向から供給することが好 ましい。
また、 本発明において上記のように薄膜の形成方法を工夫することで、 例え〖講膜の原料と なるガリゥム成分、 ィンジゥム成分及びアルミニウム成分をセラミック材料を主成分とする焼 結体に対して特定の方向から供給するなどの工夫で窒化アルミ二ゥムを主成分とする焼結体、 あるいは酸化亜鉛を主成分とする焼結体、 酸化ベリリウムを主成分とする焼結体、 酸化アルミ 二ゥムを主成分とする焼結体、 炭化珪素を主成分とする焼結体、 窒化珪素を主成分とする焼結 体、 窒化ガリゥムを主成分とする焼結体など六方晶系又 方晶系のうちから選ばれた少なく ともいずれかの結晶構造を有するセラミック材料を主成分とする焼結体ではなくても窒化ガリ ゥム、 窒化インジウム、 窒化アルミニウムのうちから選ばれた少なくとも 1種以上を主成分と する単結晶薄膜が直接形成し得ることが見出された。 より具体的に言えば、 薄膜の原料となる ガリゥム成分、 ィンジゥム成分及びアルミニゥム成分をセラミック材料を主成分とする焼結体 からなる基板面に対して垂直及び水平及び斜めのうちから選ばれた少なくとも 1以上好ましく は 2以上の方向から供給することで、 窒化アルミニウムを主成分とする焼結体、 あるいは酸化 亜鉛を主成分とする焼結体、 酸化ベリリウムを主成分とする焼結体、 酸化アルミニウムを主成 分とする焼結体、 炭化珪素を主成分とする焼結体、 窒化珪素を主成分とする焼結体、 窒化ガリ ゥムを主成分とする焼結体など六方晶系又は三方晶系のうちから選ばれた少なくともいずれか の結晶構造を有するセラミック材料を主成分とする焼結体ではなくても窒化ガリゥム、 窒化ィ ンジゥム、 窒化アルミニウムのうちから選ばれた少なくとも 1種以上を主成分とする単結晶薄 膜が直接形成し得ることが見出された。
すなわち、 例えば酸化ジルコニウム、 酸化マグネシウム、 アルミン酸マグネシウム、 酸化チ タン、 チタン酸バリウム、 チタン酸ジルコン酸鉛、 酸化イットリウムなどの希土謹化物、 酸 化トリウム、 各種フェライト、 ムライト、 フォルステライト、 ステアタイト、 結晶化ガラスの うちから選ばれた少なくとも 1種以上を主成分とする焼結体に窒化ガリゥム、窒化ィンジゥム、 窒化アルミニウムのうちから選ばれた少なくとも 1種以上を主成分とする単結晶薄膜を直接形 成しようとしたとき、 薄膜の原料供給の方向を限定せずに行えば通常単結晶薄膜の形成が困難 である場合が多い。 一方、 薄膜の原料となるガリウム成分、 インジウム成分及びアルミニウム 成分の供給を特定の方向から行えば、 例えば原料の供給を上記セラミック材料を主成分とする 焼結体からなる基板面に対して垂直及び水平及び斜めのうちから選ばれた少なくとも 1以上の 方向から行えば、 あるいは原料の供給を少なくとも異なる 2以上の方向を組み合わせることに より薄膜の形成を行えば、 例えば 化ジルコニウム、 酸化マグネシウム、 アルミン酸マグネシ ゥム、 酸化チタン、 チタン酸バリウム、 チタン酸ジルコン酸鉛、 酸化イットリウムなどの希土 化物、 酸化トリウム、 各種フェライト、 ムライト、 フォルステライト、 ステア夕イト、 結 晶化ガラスのうちから選ばれた少なくとも 1種以上を主成分とする焼結体には窒化ガリウム、 窒化インジウム、 窒化アルミニウムのうちから選ばれた少なくとも 1種以上を主成分とする単 結晶薄膜が直接形成し得る。 これらのセラミック材料を主成分とする焼結体はその表面状態に よらず、 例えば平均表面粗さ R a 7 0 nm以上と比較的大きいものでなくても、 すなわち例え ば平均表面粗さ R a 7 0 nm以下のものであっても上記のように薄膜の原料となるガリウム成 分、 ィンジゥム成分及びアルミニウム成分を上記セラミック材料を主成分とする焼結体からな る基板面に対して垂直及び水平及び斜めのうちから選ばれた少なくとも 1以上、 好ましくは少 なくとも 2以上の方向から供給することにより窒化ガリウム、 窒化インジウム、 窒化アルミ二
ゥムのうちから選ばれた少なくとも 1種以上を主成分とする単結晶薄膜が該セラミック材料を 主成分とする焼結体に直接形成し得る。
このように薄膜の原料となるガリゥム成分、 ィンジゥム成分及びアルミニウム成分をセラミ ック材料を主成分とする焼結体からなる基板面に対して垂直及び水平及び斜めのうちから選ば れた少なくとも 1以上、 好ましくは少なくとも 2以上の方向から供給することにより窒化アル ミニゥムを主成分とする焼結体、 あるいは六方晶系又は三方晶系のうちから選ばれた少なくと もいずれかの結晶構造を有するセラミック材料を主成分とする焼結体ではないセラミック材料 を主成分とする焼結体、 及び表面粗さの大きいセラミック材料を主成分とする焼結体に対して 窒化ガリウム、 窒化インジウム、 窒化アルミニウムのうちから選ばれた少なくとも 1種以上を 主成分とする単結晶薄膜が直接形成し得る理由については必ずしも明確でない。 しかしながら 本発明者はその理由を以下のように搬則している。すなわち、窒化ガリウム、窒化インジウム、 窒化アルミニウムのうちから選ばれた少なくとも 1種以上を主成分とする薄膜、 特に MO CV D法あるい ライド VP E法などのようにガリウム成分、 ィンジゥム成分、 及びアルミニゥ ム成分を含む化合物を一旦分解しその後アンモニアなどの反応ガスとの窒化反応により作製さ れる薄膜は元来基板面に対して垂直な方向に C軸が成長し易い性質を有しているものと思われ るが、 セラミック材料を主成分とする焼結体は結晶方向があらゆる方向を向いた微粒子からな る多結晶体であるので原料が一つの方向からだけ供給されればセラミック材料の種類によって は薄総晶の成長がセラミツク粒子の結晶方向に従つて行われるので多結晶化され易くなり、 原料が少なくとも 1以上の方向からあるいはさらに 2以上の方向から供給されればセラミック 粒子の結晶方向に薄膨結晶が成長しょうとする力を打ち消しあるいは抑制し窒化ガリゥム、 窒 化インジウム、 窒化アルミニウムのうちから選ばれた少なくとも 1種以上を主成分とする薄膜 が元来有している方向への結晶成長が行われ易くなり従って結晶性に優れた単結晶薄膜が 11接 形成し得るようになるものと思われる。
上記のように比較的表面粗さの大きいセラミック材料を主成分とする焼結体に形成された窒 化ガリウム、 窒化インジウム、 窒化アルミニウムのうちから選ばれた少なくとも 1種以上を主 成分とする薄膜は自発的に表面平滑性に優れたものとなり得るが、 メカノケミカルな (機械的 化学的な操作による)研削あるいは鏡面研磨を行うことによつても表面平滑性あるいは平坦性 を高めたりすることができる。 メカノケミカルな研削あるいは鏡面研磨により比較的表面粗さ の大きいセラミック材料を主成分とする焼結体に形成された窒化ガリウム、 窒化インジウム、 窒化アルミニウムのうちから選ばれた少なくとも 1種以上を主成分とする薄膜であってもその 平均表面粗さ R aは少なくとも 1 O nm以下のものが作製し得る。 また、 平均表面粗さ R aが 3 nm以下、 あるいは 2 nm以下、 さらには 1 nm以下のものが作製し得る。 上記のように窒 化ガリウム、 窒化インジウム、 窒化アルミニウムのうちから選ばれた少なくとも 1種以上を主 成分とする薄膜の平滑性あるいは平坦性を高めることでその上には高い発光効率を有する発光 素子が作製し得る。 また、 上記窒化ガリウム、 窒化インジウム、 窒化アルミニウムのうちから 選ばれた少なくとも 1種以上を主成分とする薄膜が形成された比較的表面耝さの大きいセラミ ック材料を主成分とする焼結体からなる基板をさらに例えばフッ化水素酸(HF)、フッ碰 (H F +HN03の混合酸)、硝酸(HN03)、 « (HC 1 )、 硫酸(H2 S〇4) などの酸に浸漬し たり、 H2、 N2、 A rなどを含む非酸化性雰囲気中あるいは減圧中で加熱ァニールする、 ある いはこれらを複数組み合わせて行う、 などの処理を施すことにより基板表面に形成される単結 晶薄膜の結晶性の改善をはかることが可能であり有効となり得る。
図 7 1は比較的不規則な凹凸表面を有する (言い換えれば表面粗さの大きい) セラミック材 料を主成分とする焼結体の表面状態の 1例を示す模式図である。 図 7 2は規則的な凹凸表面を 有するセラミック材料を主成分とする焼結体の表面状態の 1例を示す斜視図である。 図 7 2に
おいて、 例えば機械的な溝切り加工やプラズマガスなどによるエッチングなどによりセラミッ ク材料を主成分とする焼結体表面に直線状の溝部 1 7 0を設けることで規則的な凹凸表面が形 成されている様子が示されている。 図 7 3は規則的な凹凸表面を有するセラミック材料を主成 分とする焼結体の表面状態の 1例を示す斜視図である。 図 7 3において、 例えば機械的な溝切 り加工などによりセラミック材料を主成分とする焼結体表面に直線状の溝部 1 7 0及び 1 7 1 をお互い直角方向に設けることで規則的な桝目状の凹凸表面が形成されている様子が示されて いる。
セラミック材料を主成分とする焼結体表面の凹凸状態 (凹凸の程度) は通常上記のように表 面平滑性、 すなわち表面粗さにより表わされ得る。 特に図 7 1に例示した比較的不規則な凹凸 状態の表面に対してはその凹凸の程度を明確に表わし得る。 表面粗さは十点平均表面粗さ (R ζ )、 ¾λ表面粗さ (Rm a x)、 平均表面粗さ (R a:算術平均粗さ)、 などによって表わされ るが本発明においては平均表面粗さ (R a) を用いた。 また機械加工などにより規則的な凹凸 を施したセラミック材料を主成分とする焼結体表面の凹凸状態 (凹凸の程度) も上記表面粗さ により表わし得るが、 加工形状とその大きさによっても表わし得る。
本発明において、 比較的凹凸の多い表面状態のセラミック材料を主成分とする焼結体として 通常平均表面粗さ R aが 7 0 nm以上、 通用 R a 1 0 0 nm以上のものを用いることが好まし い。 同じセラミック材料を主成分とする焼結体を用いた場合、 平均表面粗さ R a 7 O nmより 小さいセラミック材料を主成分とする焼結体を用いて作製した発光素子に比べて発光効率が少 なくとも同等かそれ以上の、 通常は 2 %〜 3 0 %程度高い発光素子をもたらす場合が多い。 す なわち例えば鏡面研磨された面のように凹凸の少ない表面状態のセラミック材料を主成分とす る焼結体を用いて作製される発光軒の発光効率が 4 0 %であれば、 上記のように比較的凹凸 の多い表面状態のセラミック材料を主成分とする焼結体を発光素子作製用基板として用いた場 合は発光効率が少なくとも 4 0 %以上、 通常発光効率が 4 2 %~ 7 0 %の発光素子を作製し得 る。 セラミック材料を主成分とする焼結体の平均表面粗さとして R a 7 0 nm以上であれば該 焼結体を用いて作製される発光素子の発光効率向上の効果が認められる場合が多い。 例えば R a 2 0 0 0 nmあるいはそれ以上の比較的凹凸の多い表面状態を有するセラミック材料を主成 分とする焼結体を用いて発光素子を作製した場合、 平均表面粗さ R a 7 O nmより小さい状態 の同じセラミツク材料を主成分とする焼結体を用いて作製した発光素子に比べて発光効率向上 の効果が認められる場合が多い。 したがって窒化ガリウム、 窒化インジウム、 窒化アルミニゥ ムのうちから選ばれた少なくとも 1種以上を主成分とする薄膜がクラックや剥離などの不具合 が生じない状態で形成し得るものであればセラミック材料を主成分とする焼結体の表面状態と してどのようなものであっても好適に用いることができる。 例えば MOCVD法、 ハライド V P E法などの各種 CVD法、 MB E法、スパッタリング法、イオンプレーティング法、蒸着法、 あるいは P LD法などを用いることができる。発光素子の発光効率を高める上で窒化ガリゥム、 窒ィ匕インジウム、 窒化アルミニウムのうちから選ばれた少なくとも 1種以上を主成分とする結 晶性の高い単結晶薄膜を形成したセラミック材料を主成分とする焼結体を用いることが好まし い場合が多い。 上記単結晶薄膜 面粗さの大きいセラミック材料を主成分とする焼結体に直 接形成したものであってもよいし、 まず窒化ガリウム、 窒化インジウム、 窒化アルミニウムの うちから選ばれた少なくとも 1種以上を主成分とする無定形、 多結晶、 配向性多結晶、 単結晶 などの結晶状態を有する薄膜を該セラミック材料を主成分とする焼結体に形成しその上にあら ためて形成したものであってもよい。 すなわち、 単結晶薄膜を形成した表面粗さの大きいセラ ミック材料を主成分とする焼結体に発光素子を構成する窒化ガリウム、 窒化インジウム、 窒化 アルミニウムのうちから選ばれた少なくとも 1種以上を主成分とする薄膜からなる少なくとも N型半導体層及び発光層及び P型半導体層を含む積層体を形成していくことが好ましい場合が
多い。 このような方法であれば例えばセラミック材料を主成分とする焼結体の平均表面粗さと して R a 5 0 0 0 nm程度の凹凸の多いものであっても薄膜中や薄膜とセラミック材料を主成 分とする焼結体との界面での剥離などの不具合が生じにくくなり、 発光効率の高い発光素子が 安定に作製し得る。
なお、 本発明においてはセラミック材料を主成分とする焼結体の組成や材質あるいは内音 Hi 造が異なれば平均表面粗さ R a 7 0 nmより小さい表面状態を有するものを用いて作製した発 光素子であっても R a 7 0 nm以上のセラミック材料を主成分とする焼結体を用いて作製した 発光素子の発光効率と同等かさらに優れたものが作製し得る場合もある。
本発明において、 比較的凹凸の多い表面状態の、 言い換えれば表面粗さの大きいセラミック 材料を主成分とする焼結体を用いて発光軒を作製する場合、 該発光素子を構成する窒化ガリ ゥム、 窒化インジウム、 窒化アルミニウムのうちから選ばれた少なくとも 1種以上を主成分と する薄膜からなる少なくとも N型半導体層及び発光層及び P型半導体層を含む積層体を直接上 記の比較的凹凸の多い表面状態のセラミツク材料を主成分とする焼結体に形成することも可能 であるが、 窒化ガリウム、 窒化インジウム、 窒化アルミニウムのうちから選ばれた少なくとも 1種以上を主成分とする薄膜を形成したセラミック材料を主成分とする焼結体に上記積層体を 形成すればより発光効率の高い発光素子が作製し得る。 上記窒化ガリウム、 窒化インジウム、 窒化アルミニウムのうちから選ばれた少なくとも 1種以上を主成分とする薄膜は通常無定形、 多結晶、 配向性多結晶、 単結晶のうちから選ばれた少なくとも 1種以上の結晶状態で使用され る。 上記比較的凹凸の多い表面状態を有するセラミック材料を主成分とする焼結体に形成する 窒化ガリウム、 窒化インジウム、 窒化アルミニウムのうちから選ばれた少なくとも 1種以上を 主成分とする薄膜は、 例えば無定形、 多結晶、 配向性多結晶、 単結晶のうちから選ばれた少な くとも 1種以上の結晶状態を有するもの 1層だけの構成のものだけでなく、 2層以上の構成の ものも好適に用いることができる。 2層以上の構成の薄膜は、 例えばまず無定形、 多結晶、 配 向性多結晶、 単結晶のうちから選ばれた少なくとも 1種以上の結晶状態を有するものを形成し その上にさらに窒化ガリウム、 窒化インジウム、 窒化アルミニウムのうちから選ばれた少なく とも 1種以上を主成分とする単結晶状態のものを形成したもの、 などがあり好適に用いること ができる。 表面粗さの大きいセラミック材料を主成分とする焼結体に形成する薄膜としては通 常単結晶薄膜を用いることが発光素子の発光効率を高める上で好ましい。 セラミツク材料を主 成分とする焼結体が例えば窒化アルミニウムを主成分とする焼結体あるいは炭化珪素、 窒化珪 素、 窒化ガリウム、 酸化ベリリウム、 酸化亜鉛、 酸化アルミニウム、 窒化ガリウムなど六方晶 系又は三方晶系の結晶構造を有するセラミック材料を主成分とする焼結体であれば、 比較的凹 凸の多い表面状態を有したものであっても該セラミック材料を主成分とする焼結体には窒化ガ リウム、 窒化インジウム、 窒化アルミニウムのうちから選ばれた少なくとも 1種以上を主成分 とする単結晶薄膜が直接形成し得る。 また一方で、 薄膜の原料となるガリウム成分、 インジゥ ム成分及びアルミニゥム成分の供給をセラミツク材料を主成分とする焼結体に対して特定の方 向から行うことで、上記窒化アルミニウムを主成分とする焼結体あるいは炭化珪素、窒化珪素、 窒化ガリウム、 酸化ベリリウム、 酸化亜鉛、 酸化アルミニウム、 窒化ガリウムなど六方晶系又 方晶系の結晶構造を有するセラミック材料を主成分とする焼結体以外のものであっても窒 化ガリウム、 窒化インジウム、 窒化アルミニウムのうちから選ばれた少なくとも 1種以上を主 成分とする単結晶薄膜が直接形成し得る。 該単結晶薄膜としてミラー指数 ( 0 0 2 ) の格子面 の X線回折ロッキングカーブの半値幅が少なくとも 3 6 0 0秒以下、 通常 3 0 0秒以下の結晶 性を有するものが作製し得る。 また上記のように、 比較的凹凸の多い表面状態を有するセラミ ック材料を主成分とする焼結体であっても該觸吉体には例えば無定形、多結晶、配向性多結晶、 単結晶のうちから選ばれた少なくとも 1種以上の結晶状態を有する 2層以上で構成される薄膜
が形成し得る。 本発明において今まで、 セラミック材料を主成分とする焼結体にあらかじめ窒 化ガリウム、 窒化インジウム、 窒化アルミニウムのうちから選ばれた少なくとも 1種以上を主 成分とする無定形、 多結晶、 配向性多結晶、 単結晶のうちから選ばれた少なくとも 1種以上の 結晶状態を有する薄膜を形成し、 さらにその上に窒化ガリウム、 窒化インジウム、 窒化アルミ ニゥムのうちから選ばれた少なくとも 1種以上を主成分とする単結晶薄膜を形成すれば該単結 晶薄膜は該焼結体の表面平滑性などの影響を受けにくくなり高い結晶性の薄膜が作製し得るこ とを説明してきた。 セラミック材料を主成分とする焼結体が窒化アルミニウムを主成分とする 焼結体あるいは炭化珪素、 窒ィ匕珪素、 窒化ガリウム、 酸ィ匕ベリリウム、 酸化亜鉛、 酸化アルミ 二ゥム、 窒化ガリウムなど六方晶系又》H方晶系の結晶構造を有するセラミック材料を主成分 とする焼結体だけでなく、 その他例えば 化ジルコニウム、 酸化マグネシウム、 アルミン酸マ グネシゥム、 酸化チタン、 チタン酸バリウム、 チタン酸ジルコン酸鉛、 希土類 素酸化物、 酸 化トリウム、 各種フェライト、 ムライト、 フォルステライト、 ステアタイト、 結晶化ガラスな どを主成分とする焼結体など、 通常どのようなセラミック材料を主成分とするものであっても その上には単結晶、 無定形、 多結晶、 配向性多結晶のうちから選ばれた少なくとも 1種以上の 結晶状態を有する薄膜が直接形成し得る。 該単結晶、 無定形、 多結晶、 配向性多結晶のうちか ら選ばれた少なくとも 1種以上の結晶状態を有する窒化ガリウム、 窒化インジウム、 窒化アル ミニゥムのうちから選ばれた少なくとも 1種以上を主成分とする薄膜の上にはさらに窒化ガリ ゥム、 窒化インジウム、 窒化アルミニウムのうちから選ばれた少なくとも 1種以上を主成分と する単結晶薄膜及び、 無定形、 多結晶、 配向性多結晶のうちから選ばれた少なくとも 1種以上 の結晶状態を有する薄膜が形成し得る。 このように比較的凹凸の多い表面状態を有するセラミ ック材料を主成分とする焼結体がどのような材料を主成分とするものであってもその上には薄 膜の構成を少なくとも 2層以上とすることによつても窒化ガリウム、 窒化インジウム、 窒化ァ ルミニゥムのうちから選ばれた少なくとも 1種以上を主成分とする単結晶薄膜が形成し得る。 すなわち、 セラミック材料を主成分とする焼結体が例えば窒化アルミニウムを主成分とする焼 結体、 あるいは炭化珪素、 窒化珪素、 窒化ガリウム、 酸化ベリリウム、 酸化亜鉛、 酸化アルミ 二ゥム、 窒化ガリゥムなど六方晶系又 方晶系の結晶構造を有するセラミック材料を主成分 とする焼結体、 あるいは酸化ジルコニウム、 酸化マグネシウム、 アルミン酸マグネシウム、 酸 化チタン、 チタン酸バリウム、 チタン酸ジルコン歸、 希土類 素酸化物、 酸化トリウム、 各 種フェライト、 ムライト、 フォルステライト、 ステア夕イト、 結晶化ガラスなどを主成分とす る焼結体など、 通常どのようなセラミック材料を主成分とする焼結体であってもその上にまず 窒化ガリウム、 窒化インジウム、 窒化アルミニウムのうちから選ばれた少なくとも 1種以上を 主成分とする無定形、 多結晶、 配向性多結晶、 単結晶のうちから選ばれた少なくとも 1種以上 の結晶状態を有する薄膜を形成しその上に窒化ガリウム、 窒化インジウム、 窒化アルミニウム のうちから選ばれた少なくとも 1種以上を主成分とする単結晶薄膜を形成する、 といった方法 などにより単結晶薄膜を含む 2層以上で構成される薄膜が形成し得る。 上記 2層以上で構成さ れている薄膜のうち少なくとも単結晶薄膜はミラー指数 ( 0 0 2) の格子面の X線回折ロッキ ングカーブの半値幅が 3 0 0秒以下の結晶性を有するものが作製し得る。
上記のように比較的凹凸の多い表面状態のセラミック材料を主成分とする焼結体を用いて発 光素子を作製する場合、 なぜ該発光素子の発光効率が向上し易いのかその原因については必ず しも明確でない。 セラミック材料を主成分とする焼結体は単結晶やガラスなどと異なり微粒子 からなつているのでその表面状態に依らず、 発光素子を構成する N型半導体層及び発光層及び P型半導体層の積層体、 あるいはあらかじめ形成した窒化ガリウム、 窒化インジウム、 窒化ァ ルミニゥムのうちから選ばれた少なくとも 1種以上を主成分とする薄膜と該セラミック材料を 主成分とする焼結体との界面で反射あるいは全反射がもともと生じにくいと衝則される。 比較
的凹凸の多い表面状態のセラミック材料を主成分とする焼結体を用いて発光素子を作製する場 合、 発光素子を構成する N型半 本層及び発光層及び P型半導体層の積層体と該セラミック材 料を主成分とする焼結体との界面、 あるいはあらかじめ形成した窒化ガリウム、 窒化インジゥ ム、 窒化アルミニウムのうちから選ばれた少なくとも 1種以上を主成分とする薄膜と該セラミ ック材料を主成分とする焼結体との界面で、 発光層からの光がより一層反射あるいは全反射さ れにくくなるため発光素子を構成する窒化ガリウム、 窒化インジウム、 窒化アルミニウムのう ちから選ばれた少なくとも 1種以上を主成分とする薄膜からなる少なくとも N型半導体層及び 発光層及び P型半導体層を含む積層体内部に光が閉じ込められにくくなりその結果 層体外 部へ (すなわち発光素子外部へ) 放出され易くなるためであろうと思われる。
次に、 発光素子の発光効率をさらに高めるために、 上記 2) 少なくとも窒化ガリウムを含む かあるいは窒化ガリゥムを主成分とする薄膜を形成したセラミック材料を主成分とする焼結体 及び光 ¾1性を有するセラミック材料を主成分とする焼結体のうちから選ばれた少なくともい ずれかの焼結体用いて発光素子を作製する方法に付いて説明する。
本発明による発光素子は上記のように、 セラミック材料を主成分とする焼結体及び ¾¾1性 を有するセラミック材料を主成分とする焼結体のうちから選ばれた少なくともいずれかの焼結 体に窒化ガリウム、 窒化インジウム、 窒化アルミニウムのうちから選ばれた少なくとも 1種以 上を主成分とする薄膜からなる少なくとも N型半導体層及び発光層及び P型半導体層を含む積 層体を形成したものである。 発光素子を作製するにあたりセラミック材料を主成分とする焼結 体及び光 ¾ 生を有するセラミック材料を主成分とする焼結体には直接上記積層体を形成する ことも可能であるが、 通常窒化ガリウム、 窒化インジウム、 窒化アルミニウムのうちから選ば れた少なくとも 1種以上を主成分とする薄膜を形成したセラミック材料を主成分とする焼結体 及び «ii性を有するセラミック材料を主成分とする焼結体に上記積層体を形成することによ つて発光効率のより高い発光素子が作製し得る。 なお上記セラミック材料を主成分とする焼結 体及び光透過性を有するセラミック材料を主成分とする焼結体に形成される窒化ガリウム、 窒 化インジウム、 窒化アルミニウムのうちから選ばれた少なくとも 1種以上を主成分とする薄膜 は通常無定形、 多結晶、 配向性多結晶、 単結晶のうちから選ばれた少なくとも 1種以上の結晶 状態で用いられる。 セラミック材料を主成分とする焼結体及び光 ¾1性を有するセラミック材 料を主成分とする焼結体に形成する窒化ガリウム、 窒化インジウム、 窒化アルミニウムのうち から選ばれた少なくとも 1種以上を主成分とする薄膜としては、 例えば無定形、 多結晶、 配向 性多結晶、 単結晶のうちから選ばれた少なくとも 1種以上の結晶状態を有するもの 1層だけの 構成のものだけでなく、 2層以上の構成のものも好適に用いることができる。 2層以上の構成 の薄膜としては、 例えばまず無定形、 多結晶、 配向性多結晶、 単結晶のうちから選ばれた少な くとも 1種以上の結晶状態を有するものを形成しその上にさらに窒化ガリゥム、 窒化ィンジゥ ム、 窒化アルミニウムのうちから選ばれた少なくとも 1種以上を主成分とする単結晶状態のも のを形成したもの、 などがあり好適に用いることができる。
本発明において、 上記のように窒化ガリウム、 窒化インジウム、 窒化アルミニウムのうちか ら選ばれた少なくとも 1種以上を主成分とする薄膜を形成したセラミック材料を主成分とする 焼結体あるいは窒化ガリウム、 窒化インジウム、 窒化アルミニウムのうちから選ばれた少なく とも 1種以上を主成分とする薄膜を形成した ¾¾i性を有するセラミック材料を主成分とする 焼結体を用いて発光素子を作製すれば比較的高い発光効率を有する発光素子が作製し得るが、 該セラミック材料を主成分とする焼結体及び光 ¾ii性を有するセラミック材料を主成分とする 焼結体に形成する薄膜として少なくとも窒化ガリウムを含むかあるいは窒化ガリウムを主成分 とするものを用いることでより高い発光効率を有する発光素子が作製し得るので好ましい。 本 発明において上記少なくとも窒化ガリゥムを含むかあるいは窒化ガリゥムを主成分とする薄膜
を形成したセラミック材料を主成分とする焼結体あるいは少なくとも窒化ガリウムを含むかあ るいは窒化ガリウムを主成分とする薄膜を形成した ¾¾1性を有するセラミック材料を主成分 とする焼結体を用いてその上に発光素子を作製すれば、 窒化ガリゥムを含まない窒化ィンジゥ ム、 窒化アルミニウムのうちから選ばれた少なくとも 1種以上だけを主成分とする薄膜を形成 した同じセラミック材料を主成分とする焼結体及び ¾¾i性を有するセラミック材料を主成分 とする焼結体を用いて作製される発光素子よりも少なくとも同等かそ ¾上の、 通常は 2 %〜
1 0 %程度高い発光素子をもたらす場合が多い。 すなわち例えば窒化インジウム、 窒化アルミ ニゥムのうちから選ばれた少なくとも 1種以上を主成分とする薄膜を形成したセラミック材料 を主成分とする焼結体あるいは窒化ィンジゥム、 窒化アルミニウムのうちから選ばれた少なく とも 1種以上を主成分とする薄膜を形成した^ 性を有するセラミック材料を主成分とする 焼結体を用いて作製される発光素子の発光効率が 5 0 %であれば、 上記のように少なくとも窒 化ガリゥムを含むかあるいは窒化ガリゥムを主成分とする薄膜を形成した同じセラミック材料 を主成分とする ¾結体及び少なくとも窒化ガリゥムを含? ίίかあるいは窒化ガリゥムを主成分と する薄膜を形成した同じ光 ¾ 性を有するセラミック材料を主成分とする焼結体を用いた場合、 発光効率が少なくとも 5 0 %以上、通常は発光効率が 5 2 %〜6 0 %の発光軒を作製し得る。 本発明において上記のように少なくとも窒化ガリウムを含むかあるいは窒化ガリウムを主成 分とする薄膜を形成したセラミック材料を主成分とする焼結体あるいは少なくとも窒化ガリゥ ムを含むかあるいは窒化ガリウムを主成分とする薄膜を形成した) 性を有するセラミック 材料を主成分とする焼結体を用いてその上に発光素子を作製すれば該発光素子の発光効率はよ り向上し易い。 本発明においてセラミック材料を主成分とする焼結体及び光透過性を有するセ ラミック材料を主成分とする焼結体に形成した窒化ガリゥムを含むかあるいは窒化ガリゥムを 主成分とする薄膜とは少なくとも窒化ガリウム成分を含むかあるいは窒化ガリウム成分が主成 分として含まれる薄膜を意味する。 窒化ガリゥムを含むかあるいは窒化ガリゥムを主成分とす る薄膜には窒化ガリゥム成分の他に例えば窒化ィンジゥム、 窒化アルミニウムのうちから選ば れた少なくとも 1種以上の成分や S iや Mgなどのドーピング成分が含まれている薄膜であつ てもよい。 通常窒化ガリウムを主成分とする薄膜とは窒化ガリウム成分を 5 0モル%以上含む ものである。 本発明においてはこのような窒化ガリウムを主成分とする薄膜だけでなく窒化ガ リウム成分を 5 0モル%より少ない量しか含まない薄膜であっても少なくとも窒化ガリウム成 分を含むものであれば発光素子の発光効率向上に寄与し得る。 本発明においては窒化ガリゥム を含むかあるいは窒化ガリゥムを主成分とする薄膜を形成したセラミック材料を主成分とする 焼結体及び;)^過性を有するセラミック材料を主成分とする焼結体を用いて発光素子を作製し た:!^觀光素子の発光効率はより向上し得る。上記の ゆなくとも窒化ガリウムを含む薄駒 について別の表現で説明すれば、 本発明によるセラミック材料を主成分とする焼結体及び光透 過性を有するセラミック材料を主成分とする焼結体に形成された薄膜は窒化ガリウム、 窒化ィ ンジゥム、 窒化アルミニウムのうちから選ばれた少なくとも 1種以上を主成分とするものであ るがこれを例えば化学式 A l xG a y I ― x_yNで表わしたとき「少なくとも窒化ガリウムを含 む薄 S j とは 0 <y≤lの組成を有するもの (すなわち 0≤xく 1、 0≤l - x - y< l ) を 意味する。 セラミック材料を主成分とする焼結体及び光透過性を有するセラミック材料を主成 分とする焼結体に形成した薄膜がすべてこのような少なくとも窒化ガリゥムを含むかあるいは 窒化ガリゥムを主成分とする薄膜のものだけでなく少なくとも窒化ガリゥムを含むかあるいは 窒化ガリゥムを主成分とする薄膜が少なくとも一部含まれる構成のものであっても発光素子の 発光効率め向上 寄与する場合が多い。 すなわち窒化インジウム、 窒ィ匕アルミニウムのうちか ら選ば^ なくとも 1種以上を主成分とする薄膜と少なくとも窒化ガリウムを含むかあるい は窒化ガ ムを主成分とする薄膜とを組み合わせて形成したセラミック材料を主成分とする
焼結体及び 性を有するセラミック材料を主成分とする焼結体を用いて発光素子を作製し た塲合でも、 該発光素子の発光効率は向上する。 具体的に言えばセラミック材料を主成分とす る焼結体及び光 ¾ϋ性を有するセラミック材料を主成分とする焼結体に形成した薄膜として一 部が少なくとも窒化ガリゥムを含むかあるいは窒化ガリゥムを主成分とする薄膜であり一部が 窒化インジウム、 窒化アルミニウムのうちから選ばれた少なくとも 1種以上を主成分とするも のであっても発光軒の発光効率は向上する。 より具体的に言えば例えばセラミック材料を主 成分とする焼結体及び光 ¾1性を有するセラミック材料を主成分とする焼結体に形成した薄膜 が 2層からなる場合 2層すべてが少なくとも窒化ガリゥムを含むかあるいは窒化ガリゥムを主 成分とするものであってもよいし、 あるいは 1層が窒化インジウム、 窒化アルミニウムのうち から選ばれた少なくとも 1種以上を主成分とするもので 1層が窒化ガリウムを含むかあるいは 窒化ガリウムを主成分とするものであってもよい。 また、 表面 (最上層) の薄膜が少なくとも 窒化ガリゥムを含むかあるいは窒化ガリゥムを主成分とする薄膜であれば発光素子の発光効率 はより向上し得る。 このように少なくとも窒化ガリゥムを含むかあるいは窒化ガリゥムを主成 分とする薄膜を含む構成の薄膜を形成したセラミック材料を主成分とする焼結体及び光 ¾1性 を有するセラミック材料を主成分とする焼結体を用いて発光素子を作製した場合該発光素子の 発光効率はより向上し得る。
上記のように少なくとも窒化ガリゥムを含むかあるいは窒化ガリゥムを主成分とする薄膜を 形成したセラミック材料を主成分とする焼結体あるいは少なくとも窒化ガリゥムを含むかある いは窒化ガリゥムを主成分とする薄膜を形成した «ί§性を有するセラミック材料を主成分と する焼結体を用いることで、 微粒子の集合体である該セラミック材料を主成分とする焼結体及 び光 ¾ί§性を有するセラミック材料を主成分とする焼結体が本来有する発光素子の発光効率を 向上させ易いという効果をさらに高めることが可能となる。
上記少なくとも窒化ガリゥムを含むかあるいは窒化ガリゥムを主成分とする薄膜を形成した セラミック材料を主成分とする焼結体を用いて発光素子を作製する場合に見られる発光効率の 向上は、 該セラミック材料を主成分とする焼結体が光 ¾ 性を有するカゝ否かに拘わらず見られ る。 セラミック材料を主成分とする焼結体が光透過性を有する場合、 ¾透過性を有するセラ ミック材料を主成分とする焼結体を用いて作製される発光素子は比較的高い発光効率を有する ものが得られ易いが、 セラミック材料を主成分とする焼結体が 性を有しさらに少なくと も窒化ガリゥムを含むかあるいは窒化ガリゥムを主成分とする薄膜を形成したものであれば、 該セラミツク材料を主成分とする焼結体を用いて作製される発光素子はさらに高い発光効率を 有するものが得られ易い。 なお、 セラミック材料を主成分とする焼結体が光¾¾生を有しない ものであっても少なくとも窒化ガリウムを含むかあるいは窒化ガリウムを主成分とする薄膜を 形成したものであれば、 該セラミック材料を主成分とする焼結体を用いて作製される発光素子 は同じ光 ¾性を有しないセラミック材料を主成分とする焼結体を用いて作製される発光素子 に比べて高い発光効率を有するものが得られ易い。
また、 上記少なくとも窒化ガリウムを含むかあるいは窒化ガリウムを主成分とする薄膜を形 成したセラミック材料を主成分とする焼結体及び光透過性を有するセラミック材料を主成分と する焼結体を用いて発光^?を作製する に見られる発光効率の向上は、 該セラミック材料 を主成分とする焼結体及び;) ¾¾ 性を有するセラミック材料を主成分とする焼結体が前記比較 的凹凸の多い表面状態を有するセラミック材料を主成分とする焼結体及び光透過性を有するセ ラミック材料を主成分とする焼結体に少なくとも窒化ガリゥムを含むかあるいは窒化ガリゥム を主成分とする薄膜を形成したものであっても同様に見ることができる。 比較的凹凸の多い表 面状態を有するセラミック材料を主成分とする焼結体及び光 ¾i性を有するセラミック材料を 主成分とする焼結体を用いて作製される発光素子は比較的高い発光効率を有するものが得られ
易いが、 該比較的凹凸の多い表面状態を有するセラミック材料を主成分とする焼結体及び光透 過性を有するセラミック材料を主成分とする焼結体にさらに少なくとも室化ガリゥムを含むか あるいは窒化ガリゥムを主成分とする薄膜を形成したものを用いて作製される発光 »はさら に高い発光効率を有するものが得られ易い。 本発明においては平均表面粗さ 7 O nm以上の比 較的凹凸の多い表面状態を有する例えば窒化ガリゥムを主成分とする焼結体、 窒化アルミニゥ ムを主成分とする焼結体、 及び 化亜鉛を主成分とする焼結体などに少なくとも窒化ガリウム を含むかあるいは窒化ガリウムを主成分とする薄膜を形成したものを用いて作製した発光素子 では発光効率 7 0 %以上のものが作製し得る。
窒化ガリゥムを含むかあるいは窒化ガリゥムを主成分とする薄膜は例えば無定形、 多結晶、 配向性多結晶、 単結晶のうちから選ばれた少なくとも 1種以上の結晶状態を有するものなどが 使用し得る。 また、 薄 «成として 1層だけのものだけでなく、 2層以上の構成のものも好適 に用いることができる。 2層以上の構成の薄膜としては、 例えばまず無定形、 多結晶、 配向性 多結晶、 単結晶のうちから選ばれた少なくとも 1種以上の結晶状態を有するものを形成しその 上にさらに無定形、 多結晶、 配向性多結晶、 単結晶のうちから選ばれた少なくとも 1種以上の 結晶状態を有するものを形成したもの、 などがあり好適に用いることができる。 通常セラミツ ク材料を主成分とする焼結体及び光 ¾i性を有するセラミック材料を主成分とする焼結体に形 成する窒化ガリゥムを含むかあるいは窒化ガリゥムを主成分とする薄膜が 2層以上で構成され る場合表面の薄膜 (すなわち発光軒を構成する窒化ガリウム、 窒化インジウム、 窒化アルミ ニゥムのうちから選ばれた少なくとも 1種以上を主成分とする薄膜からなる少なくとも N型半 導体層及び発光層及び P型半導体層を含む積層体が直接形成される薄膨 は単結晶であること が発光効率に優れた発光素子を作製する上で好ましい。 また、 セラミック材料を主成分とする 焼結体及び 性を有するセラミック材料を主成分とする焼結体が窒化アルミニウムを主成 分とする焼結体あるいはその他に炭化珪素、 窒化珪素、 窒化ガリウム、 酸化ベリリウム、 酸化 亜鉛、 酸化アルミニウム、 窒化ガリウムなど六方晶系又 方晶系の結晶構造を有するセラミ ック材料を主成分とする焼結体であれば、 該セラミック材料を主成分とする焼結体及び;)1^ 性を有するセラミック材料を主成分とする焼結体には窒化ガリウム、 窒化インジウム、 窒化ァ ルミニゥムのうちから選ばれた少なくとも 1種以上を主成分とする単結晶薄膜が形成し得るが 該単結晶薄膜が窒化ガリウムを含むかあるいは窒化ガリウムを主成分とするものであっても直 接形成し得る。 該窒化ガリゥムを含むかあるいは窒化ガリゥムを主成分とする単結晶薄膜とし てミラ一指数 (0 0 2) の格子面の X線回折ロッキングカーブの半値幅が 3 6 0 0秒以下の結 晶性を有するものが作製し得る。 セラミック材料を主成分とする焼結体及び光 ¾ii性を有する セラミック材料を主成分とする焼結体として窒化アルミニウムを主成分とする焼結体あるいは 炭化珪素、 窒化珪素、 窒化ガリウム、 酸化ベリリウム、 酸化亜鉛、 酸化アルミニウム、 窒化ガ リウムなど六方晶系又は三方晶系の結晶構造を有するセラミック材料を主成分とする焼結体だ けでなく、 その他酸化ジルコニウム、 酸化マグネシウム、 アルミン酸マグネシウム、 酸化チタ ン、 チタン酸バリウム、 チタン酸ジルコン隱、 希土 IR¾素酸化物、 酸化トリウム、 各種フエ ライト、 ムライト、 フオルステライト、 ステアタイト、 結晶化ガラスなどを主成分とする焼結 体など、 通常どのようなセラミック材料を主成分とするものであってもその上には少なくとも 無定形、 多結晶、 配向性多結晶のうちから選ばれた少なくとも 1種以上の結晶状態を有する窒 化ガリウム、 窒化インジウム、 窒化アルミニウムのうちから選ばれた少なくとも 1種以上を主 成分とする薄膜が直接形成し得るが該薄膜が窒化ガリゥムを含むかあるいは窒化ガリゥムを主 成分とするものであっても直接形成し得る。 該無定形、 多結晶、 配向性多結晶のうちから選ば れた少なくとも 1種以上の結晶状態を有する薄膜の上にはさらに窒化ガリウム、 窒化ィンジゥ ム、 窒化アルミニウムのうちから選ばれた少なくとも 1種以上を主成分とする単結晶薄膜、 及
び無定形、 多結晶、 配向性多結晶のうちから選ばれた少なくとも 1種以上の結晶状態を有する 薄膜が形成し得るが該薄膜が窒化ガリウムを含むかあるいは窒化ガリウムを主成分とするもの であっても形成し得る。 このようにセラミック材料を主成分とする焼結体及び 過性を有す るセラミック材料を主成分とする焼結体がどのような材料を主成分とするものであってもその 上には薄膜の構成を少なくとも 2層以上とすることで窒化ガリウムを含むかあるいは窒化ガリ ゥムを主成分とする薄膜が単結晶の状態で形成し得る。 上記 2層以上で構成されている薄膜の うち少なくとも単結晶薄膜はミラー指数 ( 0 0 2) の格子面の X線回折ロッキングカーブの半 値幅が 3 0 0秒以下の結晶性を有するものが作製し得る。
上記のように少なくとも窒化ガリウムを含むかあるいは窒化ガリウムを主成分とする薄膜を 形成したセラミック材料を主成分とする焼結体及び光 ¾ 性を有するセラミック材料を主成分 とする焼結体を用いて発光素子を作製する場合、 該発光素子の発光効率が窒化ィンジゥム及び 窒化アルミニウムのうちから選ばれた少なくとも 1種以上を主成分とする薄膜だけを形成した セラミック材料を主成分とする焼結体及び) ¾¾i性を有するセラミック材料を主成分とする焼 結体を用いて作製した発光素子に比べてなぜ向上し易いのかその原因については必ずしも明確 でない。 窒化ガリゥムと窒化アルミニウムとを比較したとき窒化ガリゥムの屈折率は窒化アル ミニゥムの屈折率よりも大きい。 そのため形成された窒化ガリウムを含むかあるいは窒化ガリ ゥムを主成分とする薄膜とセラミック材料を主成分とする焼結体あるいは ¾¾1性を有するセ ラミック材料を主成分とする焼結体との界面における発光層からの光の反射あるいは全反射が 窒化アルミニウムあるいは窒化アルミニウムを主成分とする薄膜とセラミック材料を主成分と する焼結体あるいは ¾¾1性を有するセラミツク材料を主成分とする焼結体との界面における ものよりも生じにくいと搬則される。 従って少なくとも窒化ガリウムを含むかあるいは窒化ガ リゥムを主成分とする薄膜を形成したセラミック材料を主成分とする焼結体及び光 ¾i性を有 するセラミック材料を主成分とする焼結体を用いて発光素子を作製すれば、 窒化アルミニウム あるいは窒化アルミニウムを主成分とする薄膜だけを形成したセラミック材料を主成分とする 焼結体あるいは)1 ά¾ϋ性を有するセラミック材料を主成分とする焼結体を用いて作製した発光 軒に比べて発光素子を構成する窒化ガリウム、 窒化インジウム、 窒化アルミニウムのうちか ら選ばれた少なくとも 1種以上を主成分とする薄膜からなる少なくとも Ν型半 本層及び発光 層及び Ρ型半導体層を含む積層体内部に光が閉じ込められにくくなり、 その結果該積層体外部 へ (すなわち発光素子外部へ) 放出され易くなるためであろうと思われる。 また、 窒化インジ ゥムあるいは窒化ィンジゥムを主成分とする薄膜だけを形成したセラミック材料を主成分とす る焼結体あるいは ¾¾i性を有するセラミック材料を主成分とする焼結体を用いて発光素子を 作製した場合、 窒化ィンジゥムあるいは窒化ィンジゥムを主成分とする薄膜のバンドギヤップ エネルギーが窒化ガリゥムに比べて小さいため窒化ガリゥムに比べて波長の短い光の吸収が生 じ易く、 従って発光効率が低下し易くなるものと推測される。
このように本発明においては発光素子の発光効率を高めるために、 1 ) 光 ¾ 性のセラミツ ク材料を主成分とする焼結体を使用して発光素子を作製する、 2) 比較的凹凸の多い表面状態 を有するセラミック材料を主成分とする焼結体、 言い換えれば表面粗さの大きいセラミック材 料を主成分とする焼結体を翻して発光軒を作製する、 3 )窒化ガリウム、窒化インジウム、 窒化アルミニウムのうちから選ばれた少なくとも 1種以上を主成分とする薄膜を形成したセラ ミック材料を主成分とする焼結体を用いて発光軒を作製する、 4) 窒化ガリウム、 窒化イン ジゥム、 窒化アルミニウムのうちから選ばれた少なくとも 1種以上を主成分とする薄膜を形成 したセラミック材料を主成分とする焼結体のうちで少なくとも窒化ガリウムを含むかあるいは 窒化ガリゥムを主成分とする薄膜を形成したセラミック材料を主成分とする焼結体を用いて発 光素子を作製する、 といった方法などが有効である。 さらにこれらの方法を組み合わせて発光
素子を作製することが発光効率を高める上で効果的である。 例えば、 5 ) 光 性でかつ表面 粗さの大きいセラミック材料を主成分とする焼結体を使用して発光素子を作製する、 6) 光透 過性のセラミック材料を主成分とする焼結体に窒化ガリウム、 窒化インジウム、 窒化アルミ二 ゥムのうちから選ばれた少なくとも 1種以上を主成分とする薄膜を形成したものを使用して発 光素子を作製する、 7 ) ¾¾i性のセラミック材料を主成分とする焼結体に少なくとも窒化ガ リウムを含むかあるいは窒化ガリウムを主成分とする薄膜を形成したものを使用して発光素子 を作製する、 8 ) 表面粗さの大きいセラミック材料を主成分とする焼結体に窒化ガリウム、 窒 化インジウム、 窒化アルミニウムのうちから選ばれた少なくとも 1種以上を主成分とする薄膜 を形成したものを使用して発光素子を作製する、 9) 表面粗さの大きいセラミック材料を主成 分とする焼結体に少なくとも窒化ガリゥムを含むかあるいは窒化ガリゥムを主成分とする薄膜 を形成したものを使用して発光素子を作製する、 1 0 ) ¾¾ 生でかつ表面粗さの大きいセラ ミック材料を主成分とする焼結体に窒化ガリウム、 窒化インジウム、 窒化アルミニウムのうち から選ばれた少なくとも 1種以上を主成分とする薄膜を形成したものを使用して発光素子を作 製する、 1 1 ) 光 ¾ϋ性でかつ表面粗さの大きいセラミック材料を主成分とする焼結体に少な くとも窒化ガリウムを含むかあるいは窒化ガリウムを主成分とする薄膜を形成したものを使用 して発光素子を作製する、 といった方法などが有効である。 また上記の発光 の発光効率を 高めるために使用されるセラミック材料を主成分とする焼結体及び光透過性を有するセラミッ ク材料を主成分とする焼結体としては窒化ガリウムを主成分とする焼結体、 窒化アルミニウム を主成分とする焼結体、 及び襟化亜鉛を主成分とする焼結体などを用いることが好ましい。 このように本発明により、 窒化ガリウム、 窒化インジウム、 窒ィ匕アルミニウムのうちから選 ばれた少なくとも 1種以上を主成分とする薄膜からなる少なくとも N型半導体層及び発光層及 び P型半導体層を含む積層体により構成される発光素子であって、 該 N型半導体層及び発光層 及び P型半 ¾本層の積層体がセラミック材料を主成分とする焼結体に形成されていることを特 徴とする発光素子、 が提供される。 本発明による発光素子は少なくとも N型半導体層及び発光 層及び P型半導体層を含む積層体がセラミック材料を主成分とする焼結体に形成されているこ とを特徴とし、 «からのサフアイァなどの単結晶基板を用いて作製される発光素子に比べて 発光効率が少なくとも同等か、 »:4〜 5倍以上のものが提供できる。 本発明による発光素子 は少なくとも N型半導体層及び発光層及び P型半導体層を含む積層体が単結晶や配向性多結晶 などに比べて不均質なセラミック材料を主成分とする焼結体に形成されているにもかかわらず 従来からのサフアイァなどの単結晶基板を用いて作製される発光素子に比べて発光効率が少な くとも同等か、 最大 4〜 5倍以上のものが提供できる。 従来セラミック材料を主成分とする材 料は不均質であり単結晶基板や配向性多結晶基板でなければ窒化ガリゥム、 窒化ィンジゥム、 窒化アルミニウムのうちから選ばれた少なくとも 1種以上を主成分とする薄膜をェピ夕キシャ ル成長させることが困難であると通常考えられており、 もしェピタキシャル成長できたとして もその結晶性は低くそのため少なくとも N型半導体層及び発光層及び P型半導体層を含む積層 体から構成される発光素子の発光効率は徹からのサファイアなどの単結晶基板を用いて作製 される発光 »に比べて必ずしも優れたものが提供できる状態ではなかった。 本発明により従 来からのこのような常識及び状況が打破されたといえる。 上記セラミック材料を主成分とする 焼結体としては光透過性を有しないものだけでなく光透過性を有するものを用いることも可能 である。 セラミック材料を主成分とする焼結体として光透過性を有するものを用いれば発光素 子の発光効率が向上し易いので好ましい。 また、 上記発光素子を構成する少なくとも N型半導 体層及び発光層及び P型半導体層を含む積層体はセラミック材料を主成分とする焼結体に直接 形成することができるだけでなくあらかじめ窒化ガリウム、 窒化インジウム、 窒化アルミニゥ ムのうちから選ばれた少なくとも 1種以上を主成分とする薄膜が形成されたセラミック材料を
主成分とする焼結体にも形成することができる。 あらかじめ窒化ガリウム、 窒化インジウム、 窒化アルミニウムのうちから選ばれた少なくとも 1種以上を主成分とする薄膜を形成したセラ ミック材料を主成分とする焼結体を用いその上に少なくとも N型半導体層及び発光層及び P型 半導体層を含む積層体を形成すれば発光素子の発光効率が向上し易いので好ましい。
なお、 上記セラミック材料とは焼結体を構成する例えば窒化アルミニウム、 六方晶系又 ¾Ξ 方晶系のうちから選ばれた少なくともいずれかの結晶構造を有する材料 (例えば炭化珪素、 窒 化珪素、 窒化ガリウム、 酸イ^ ffi鉛、 酸化ベリリウム、 酸化アルミニウムなど)、 酸化ジルコニゥ ム、 酸化マグネシウム、 アルミン酸マグネシウム、 酸化チタン、 チタン酸バリウム、 チタン酸 ジルコン酸鉛、 酸化イットリウムなどの希土 «化物、 酸ィ匕トリウム、 各種フェライト、 ムラ イト、 フォルステライト、 ステアタイト、 結晶ィ匕ガラス、 などの金属元素及び半金属元素のう ちから選ばれた少なくとも 1種以上の元素と非金属元素のうちから選ばれた少なくとも 1種以 上の元素との組成物あるいは化合物、 あるいは金属元素のうちから選ばれた少なくとも 1種以 上の元素と半金属元素のうちから選ばれた少なくとも 1種以上の元素との組成物あるいは化合 物、 あるいは半金属元素のうちから選ばれた少なくともいずれか 2種以上の元素との組成物あ るいは化合物を主成分とするものからなる。 上記非金属元素としては通常窒素、 りん、 酸素、 硫黄、 ハロゲン元素 (フッ素、 髓、 臭素、 沃素、 アスタチン) などが好適に用いられる。 半 金属元素として〖雄常ほう素、 炭素、 珪素、 ゲルマニウム、 ヒ素、 アンチモン、 ビスマス、 セ レン、 テルル、 ポロニウムなどが好適に用いられる。 上記セラミック材料は通常無衞匕合物を 主成分とするものであり、 これらのセラミック材料は結晶質のものであってもよいしあるいは 例えばガラスなどの非晶質状態のものであってもよいしあるいは結晶質のものと非晶質のもの とが混在したものであってもよい。 上記セラミック材料 常窒化物、 炭化物、 酸化物、 硼ィ匕 物、 珪化物などの化合物あるいは組成物を主成分とするものである。
なお、本発明において上記セラミック材料としては主成分である無機材料以外に金属、合金、 金属間化合物、 有機物質、 有機化合物、 有機樹脂、 その他に例えばハロゲン元素あるいはカル コゲン元素などの非金属などを含有するもの含まれる。
本発明において、 上記セラミック材料を主成分とする焼結体は ¾¾性を有するものが好ま しく、 該光 ¾1性を有するセラミ Vク材料を主成分とする焼結体に形成される窒化ガリゥム、 窒化インジウム、 窒化アルミニウムのうちから選ばれた少なくとも 1種以上を主成分とする薄 膜の結晶性が向上し易くなるとともに、 該 ¾¾¾性を有するセラミック材料を主成分とする焼 結体に形成した少なくとも N型半 本層及び発光層及び P型半導体層を含む積層体から構成さ れる発光軒の発光効率がより優れたものとなる得るので好ましい。 また本発明において、 上 記セラミック材料を主成分とする焼結体としては窒化ガリウム、 窒化インジウム、 窒化アルミ ニゥムのうちから選ばれた少なくとも 1種以上を主成分とする薄膜をあらかじめ形成したもの が好ましく、 該薄膜があらかじめ形成されたセラミック材料を主成分とする焼結体には結晶性 の優れた窒化ガリウム、 窒化インジウム、 窒化アルミニウムのうちから選ばれた少なくとも 1 種以上を主成分とする単結晶薄膜が形成し易くなるとともに、 該薄膜があらかじめ形成された セラミック材料を主成分とする焼結体に少なくとも N型半導体層及び発光層及び P型半 本層 を含む積層体を形成することにより得られる発光素子の発光効率がより優れたものとなり得る ので好ましい。
本発明による発光素子は、 1 ) 窒化ガリウム、 窒化インジウム、 窒化アルミニウムのうちか ら選ばれた少なくとも 1種以上を主成分とする薄膜からなる少なくとも N型半導体層及び発光 層及び P型半導体層を含む積層体により構成される発光素子であって、 該 N型半導体層及び発 光層及び P型半導体層の積層体がセラミック材料を主成分とする焼結体に形成されていること を特徴とする発光素子、 であるがさらに詳細に言えば、 2) 窒化ガリウム、 窒化インジウム、
窒化アルミニウムのうちから選ばれた少なくとも 1種以上を主成分とする薄膜からなる少なく とも N型半導体層及び発光層及び P型半導体層を含む積層体により構成される発光素子であつ て、 該 N型半導体層及び発光層及び P型半導体層の積層体が)1 ά¾ 生を有するセラミック材料 を主成分とする焼結体に形成されていることを特徴とする発光素子、 を含む。 また、 3) 窒化 ガリウム、 窒化インジウム、 窒化アルミニウムのうちから選ばれた少なくとも 1種以上を主成 分とする薄膜からなる少なくとも Ν型半導体層及び発光層及び Ρ型半導体層を含む積層体によ り構成される発光^?であって、 該 Ν型半導体層及び発光層及び Ρ型半導体層の積層体が窒化 ガリウム、 窒化インジウム、 窒化アルミニウムのうちから選ばれた少なくとも 1種以上を主成 分とする薄膜が形成されたセラミック材料を主成分とする焼結体に形成されていることを特徴 とする発光素子、 を含む。 また、 4) 窒化ガリウム、 窒化インジウム、 窒化アルミニウムのう ちから選ばれた少なくとも 1種以上を主成分とする薄膜からなる少なくとも Ν型半導体層及び 発光層及び Ρ型半導体層を含む積層体により構成される発光素子であって、 該 Ν型半導体層及 び発光層及び Ρ型半導体層の積層体が窒化ガリウム、 窒化インジウム、 窒化アルミニウムのう ちから選ばれた少なくとも 1種以上を主成分とする単結晶薄膜が形成されたセラミック材料を 主成分とする焼結体に形成されていることを特徴とする発光素子、 を含む。 また、 5 ) 上記発 光素子に用いられるセラミック材料を主成分とする焼結体が窒化アルミニウムを主成分とする 焼結体であることを特徴とする発光素子、 を含む。 また、 6 ) 上記発光^?に用いられるセラ ミック材料を主成分とする焼結体が六方晶系又は三方晶系のうちから選ばれた少なくともいず れかの結晶構造を有する材料を主成分とする! ¾結体であることを Μ [とする発光 、 を含む。 また、 7 ) 上記発光素子に用いられるセラミック材料を主成分とする焼結体力職化 »、 酸化 ベリリウム、 酸化アルミニウム、 炭化珪素、 窒化珪素、 窒化ガリウム、 酸化ジルコニウム、 酸 化マグネシウム、 アルミン酸マグネシウム、 酸化チタン、 チタン酸バリウム、 チタン酸ジルコ ン »、 希土 素酸化物、 酸ィ匕トリウム、 各種フェライト、 ムライト、 フオルステライ卜、 ステアタイト、 結晶化ガラスのうちから選ばれた少なくとも 1種以上を主成分とする焼結体で あることを特徴とする発光素子、 を含む。
本発明による発光素子は上記のように、 窒化ガリウム、 窒化インジウム、 窒化アルミニウム のうちから選ばれた少なくとも 1種以上を主成分とする薄膜からなる少なくとも Ν型半導体層 及び発光層及び Ρ型半導体層を含む積層体をセラミック材料を主成分とする焼結体に直接形成 したものを含む。 また窒化ガリウム、 窒化インジウム、 窒化アルミニウムのうちから選ばれた 少なくとも 1種以上を主成分とする薄膜からなる少なくとも Ν型半導体層及び発光層及び Ρ型 半導体層を含む積層体をあらかじめ窒化ガリウム、 窒化インジウム、 窒化アルミニウムのうち から選ばれた少なくとも 1種以上を主成分とする薄膜が形成されたセラミック材料を主成分と する焼結体に形成したものも含まれる。本発明による発光素子は構成要素である窒化ガリゥム、 窒化インジウム、 窒化アルミニウムのうちから選ばれた少なくとも 1種以上を主成分とする薄 膜からなる積層体として Ν型半導体層及び発光層及び Ρ型半導体層の他にバッファ層を有する ものも含む。 本発明の発光軒は上記バッファ層を必ずしも必要としない。 本発明においては セラミツク材料を主成分とする焼結体にバッファ層を有せず Ν型半導体層及び発光層及び Ρ型 半導体層の積層体を形成した発光素子も含む。 発光素子がバッファ層を有する場合は通常セラ ミック材料を主成分とする焼結体にまずバッファ層を形成しその後 Ν型半導体層及び発光層及 び ρ型半導体層の積層体を形成する。 本発明において発光素子がバッファ層を有する場合、 発 光素子の構成要素である窒化ガリウム、 窒化インジウム、 窒化アルミニウムのうちから選ばれ た少なくとも 1種以上を主成分とする薄膜からなる積層体は少なくともバッファ層及び Ν型半 導体層及び発光層及び Ρ型半導体層を含む構成となる。 通常バッファ層は窒化ガリウム、 窒化 インジウム、 窒化アルミニウムのうちから選ばれた少なくとも 1種以上を主成分とする薄膜を
ェピタキシャル成長させない状態 (すなわち無定形、 多結晶、 配向性多結晶の結晶状態) のも のが用いられる。 上記セラミツク材料を主成分とする焼結体としてあらかじめ窒化ガリゥム、 窒化インジウム、 窒化アルミニウムのうちから選ばれた少なくとも 1種以上を主成分とする薄 膜が形成されたものを用いればバッファ層としては窒化ガリウム、 窒化インジウム、 窒化アル ミニゥムのうちから選ばれた少なくとも 1種以上を主成分とするェピタキシャル成長した (す なわち単結晶状態の) 薄膜でも比較的容易に使用できる。 さらにセラミック材料を主成分とす る焼結体としてあらかじめ窒化ガリウム、 窒化インジウム、 窒化アルミニウムのうちから選ば れた少なくとも 1種以上を主成分とする薄膜が形成されたものを用いればバッファ層としては 炭化珪素、 窒化珪素、 窒化ガリウム、 酸化 、 酸化ベリリウムなど六方晶系又 tt≡方晶 系のうちから選ばれた少なくともいずれかの結晶構造を有する化合物あるいは酸化ジルコニゥ ム、 酸化マグネシウム、 アルミン酸マグネシウム、 酸化チタン、 チタン酸バリウム、 チタン酸 ジルコン雌、 希土 素酸化物、 酸化トリウム、 各種フェライト、 ムライト、 フォルステラ ィト、 ステアタイトなどの化合物を主成分とする薄膜を用いてもよい。
以下、 発光素子について図を用いて説明する。
図 3 9は発光素子の基本的な構成を示す断面図である。 すなわち発光素子作製用基板 3 0に 窒化ガリゥム、 窒化ィンジゥム、 窒化アルミニゥムのうちから選ばれた少なくとも 1種以上を 主成分とする薄膜によりバッファ層 3 1が形成され、その上に窒化ガリウム、窒化インジウム、 窒化アルミニウムのうちから選ばれた少なくとも 1種以上を主成分とする N型又は P型の半導 体特性を有する薄膜により薄麵 3 4が形成される。その上に窒化ガリゥム、窒化ィンジゥム、 窒化アルミニウムのうちから選ばれた少なくとも 1種以上を主成分とする薄膜により発光層 3 6が形成される。 その上に窒化ガリウム、 窒化インジウム、 窒化アルミニウムのうちから選ば れた少なくとも 1種以上を主成分とする P型又は N型の半導体特性を有する薄膜により薄膜層 3 5が形成される。 該薄麵 3 5は薄麵 3 4が N型の半導体特性を有するときは P型に、 薄 膜層 3 4が P型の半導体特性を有するときは N型の半導体特性になるように設定される。 薄膜 層 3 4及ぴ 膜層 3 5にはそれぞれ電極 3 8が設けられる。 このように基板 3 0の上に要すれ ばまずバッファ層 3 1を形成し、 その上に N型半導体層 (P型半導体層) 3 4、 発光層 3 6、 P型半導体層 (N型半導体層) 3 5、 を積層し、 さらに電極 3 8、 を形成し基板を含めて全体 として発光素子 3 2が構成される。 N型半導体層及び P型半^ f本層に形成された電極 3 8に直 流電力を印加することで発光素子が駆動する。 発光の波長は発光層の組成を調整することなど で例えば紫外線領域から可視光領域の広い波長範囲にわたって光を発することができる。 具体 的にいえば例えば 2 5 0 nm〜6 5 0 nmの波長範囲の光を発することができ、 通常 3 0 0 n m〜 6 0 0 nmの波長範囲の光を発するように作製されることが多い。
さらに詳しく説明すると、 図 3 9において発光素子作製用基板 3 0として従来からは例えば サファイアなどが用いられてきた。 本発明においては発光素子作製用基板 3 0として例えば図 3、 図 5〜図 8、 図 1 0〜図 2 0、 図 3 6〜図 3 8に例示するような窒化アルミニウムを主成 分とする焼結体、 及び炭化珪素、 窒化珪素、 窒化ガリウム、 酸化ベリリウム、 酸化亜鉛、 酸化 アルミニウムなど六方晶系又は三方晶系の結晶構造を有するセラミック材料を主成分とする焼 結体、 及びその他に酸化ジルコニウム、 酸化マグネシウム、 アルミン酸マグネシウム、 酸化チ タン、チタン酸バリウム、チタン酸ジルコン隨、酸化イットリウムなどの希土観素酸化物、 酸化トリウム、 各種フェライト、 ムライト、 フォルステライト、 ステア夕イト、 結晶化ガラス などの各種セラミック材料を主成分とする焼結体をそのままの状態で基板としたもの、 あるい はこれらのセラミック材料を主成分とする焼結体からなる基板に窒化ガリゥム、 窒化ィンジゥ ム、 窒化アルミニウムのうちから選ばれた少なくとも 1種以上を主成分とする薄膜を形成して 薄膜基板としたもの、 がある。 基板 3 0の上には MO CVD法、 あるいは MOVP E法、 ある
いはその他の CVD法、 あるいはクロライド V P E法などのハライド VP E法、 あるいは MB E法などの方法により窒化ガリウム、 窒化インジウム、 窒化アルミニウムのうちから選ばれた 少なくとも 1種以上を主成分とする薄膜からなるバッファ層 3 1が形成される。 ノ ソファ薄膜 層 3 1としては通常無定形状態のものが用いられるが、 その他に多結晶、 配向性多結晶など各 種結晶状態のものも用いることができ、 さらにェピタキシャル成長した単結晶状態のものも用 いることができる。 バッファ層 3 1は N型あるいは P型に半 本化した導電性を有するもので あってもよいが必ずしも導電性を有するものでなくともよい。 バッファ層 3 1の上には MO C VD法、 あるいは MOVP E法、 あるいはその他の C VD法、 あるいはクロライド VP E法な どのハライド V P E法、 あるいは MB E法などの方法により窒化ガリウム、 窒化インジウム、 窒化アルミニウムのうちから選ばれた少なくとも 1種以上を主成分とするェピタキシャル成長 した薄膜により構成される N型又は P型の半導体特性を有する薄膜層 3 4が形成されている。 なお、 上記バッファ層 3 1は通常基板 3 0と薄麵 3 4との間の結晶不齢を調整し薄麵 3 4の結晶性や表面平滑性などの特性を向上するために設けられるが、 必要に応じて設ければよ く本発明においては特に設けなくても基板 3 0の上に直接薄膜層 3 4を形成し発光素子を作製 していくことも可能である。 薄膜層 3 4は通常 N型半導体特性を有するよう調整されるが P型 半難であってもよい。 N型半 Si本特性雄常該薄麵 3 4を構 る主成分に例えば S i (珪 素)、 G e (ゲルマニウム)、 S e (セレン)、 T e (テルル)、 O (酸素) などのドナー形成ド 一ビング成分を含有せしめることにより発現される。 薄 3 4の上には窒化ガリウム、 窒化 インジウム、 窒化アルミニウムのうちから選ばれた少なくとも 1種以上を主成分とするェピ夕 キシャル成長した薄膜から構成される発光層 3 6が形成されている。 発光層 3 6を構成する薄 膜は通常ドーピング成分を含まないアンドープ型の薄膜、 あるいはァクセプ夕一形成ドーピン グ成分のうちから選ばれた 1種以上を含むもの、 ドナー形成ドーピング成分のうちから選ばれ た 1種以上を含むもの、 あるいはァクセプ夕一形成ドーピング成分及びドナー形成ドーピング 成分のうちから選ばれたそれぞれ 1種以上を同時に含む (コド一プされた) 薄膜が いら れる。 発光層から発せられる光の波長は発光層として用いられる G a N、 I nN、 A 1 Nの組 成あるいはドーピング成分の種類などによって制御できる。 発光層 3 6は例えばへテロ構造や ダブルへテロ構造、 あるいは単一 井戸構造などのように単一の薄翻から形成されたもの でもよいし、 あるいは例えば多重 井戸構造のように 2層以上で構成されたものでもよい。 単一 »井戸構造の場合、 発光層 3 6は井戸層となる例えば 1 0 O A以下の薄い単一組成の単 一薄^ iからなり N型半導体薄膜の障壁層と P型半導体薄膜の障壁層とで挟まれた構造である。 また発光層 3 6には井戸層及び障壁層となる薄い少なくとも 2以上の異なる組成の薄膜を交互 に積層して構成される多重 井戸構造のものも用い得る。 多重量子井戸構造の場合、 井戸層 及び偉壁層の厚みは井戸層が 1 5 0 A以下好ましくは 1 0 0 A以下さらに好ましくは 7 0 A以 下、 障壁層が 2 0 O A以下好ましくは 1 5 O A以下さらに好ましく 1 0 O A以下のものが通常 用いられる。 また、 多重量子井戸構造の場合、 層にある 2つの薄 は通常井戸層で形成 されることが好ましい。 なお上記へテロ構造やダブルへテロ構造、 あるいは単一量子井戸構造 の発光素子は通常発光ダイオード (L ED) として用いられ、 多重量子井戸構造を有する発光 素子は通常レーザーダイオード (LD) として用いられる。 上記発光層を構成する井戸層及び 障壁層となる薄膜も通常窒化ガリウム、 窒化インジウム、 窒化アルミニウムのうちから選ばれ た少なくとも 1種以上を主成分とするェピタキシャル成長した薄膜から構成されることが好ま しい。 単一 井戸構造及 ϋ 重量子井戸構造の井戸層となる薄膜はドーピング成分を加えな いアンド一プの状態のものが通常用いられるカ、 ¾ドーピング成分を加えてそれぞれ Ν型あ るいは Ρ型に半導体化したものあるいは Ν型及び Ρ型半 本化ドーピング成分を同時に加えて 半導体化したものなども用いることが可能である。 また発光層が多重量子井戸構造の場合障壁
層となる薄膜はドーピング成分を加えないアンドープの状態のものが通常用いられるが、 ¾i: ドーピング成分を加えて N型あるいは P型に半導体化したものあるいはそれぞれ N型及び P型 半導体化ドーピング成分を同時に加えて半導体化したものなども用いることが可能である。 量 子井戸層を構成する井戸層/障壁層としては例えば、 I n G a N/G a N、 I n G a N/ I n G a N (それぞれ糸滅が異なる)、 I n G a N/A 1 G a N、 A 1 G a N/G a N、 などの糸滅 系からなる組み合わせのものが.ある。 さらに、 発光層 3 6の上に窒化ガリゥム、 窒化ィンジゥ ム、 窒化アルミニウムのうちから選ばれた少なくとも 1種以上を主成分とするェピタキシャル 成長した薄膜により構成される薄麵 3 5が形成されている。 薄翻 3 5は前記薄翻 3 4が N型半導体特性を有する場合 P型半導体特性を有するよう調整される。 また前記薄膜層 3 4が P型半導体特性を有する場合 N型半導体特性を有するよう調整される。 P型半導体特性は通常 該薄膜層 3 5を構成する主成分に例えば Mg (マグネシウム)、 B e (ベリリウム)、 C a (力 ルシゥム)、 Z n (亜鉛)、 C d (カドミウム)、 C (炭素) などのァクセプ夕一形成ドーピング 成分を含有せしめることにより発現される。 なお、 上記ドナ一形成ドーピング成分及びァクセ プ夕一形成ドーピング成分は薄膜を N型半導体化あるいは P型半 ¾#:化しさらに該薄膜の抵抗 率を小さくするために主成分に対してどのような割合でも含有させることができるが通常元素 購で 0. 0 0 0 0 1〜: L 0モル%の範囲で含有される。 また、 窒化ガリウム、 窒化インジゥ ム、 窒化アルミニウムのうちから選ばれた少なくとも 1種以上を主成分とする薄膜はドーピン グ成分を含まないアンド一プ型のものであっても自発的に N型の半導体特性を有し導電性が発 現される場合があるが、 発光素子にはこのようなアンド一プ型の薄膜であっても用いることが できる。 上記薄薩 3 4及ぴ 5には A 1、 Au、 P t、 T i、 N i、 C r、 S n、 A 1 /T i、 Au/N i、 Au/T i、 Au/P d、 Au/P t /T iなどから構成される電極 3 8が形成されそこから直流電位が印加されることで素子の発光が行われる。
なお、 上記薄翻 3 4及ぴ蒋膜層 3 5はそれぞ 一の層構成でなく 2以上の複数の層 (例 えば組成が異なる、 など) から構成されたものであってもよい。 より詳しく言えば、 上記薄膜 層 3 4及び薄膜層 3 5は単一の層として構成されたものだけでなく少なくともどちらか一方の 層が例えば電極と接続するためのコンタクト層及び発光層と接続するクラッド層など少なくと も 2層以上の薄 ΒΙβから構成されるものも好適に使用される。 また上記薄膜層 3 4及ぴ 3 5を構成するコンタク卜層及びクラッド層は単一層だけでなく少なくともどちらか一方の層 がそれぞれ少なくとも 2層以上の薄膜層から構成されるものも好適に使用される。 また、 薄膜 層 3 4及び奪膜層 3 5がそれぞ Π —の薄 あるいはどちらか一方だけが単一の薄 ,であ つても発光層 3 6が量子井戸構造の井戸層として用いられる場合の障壁層として機能させるこ ともできる。 例えば、 単一量子井戸構造を有する発光軒を作製しょうとする場合、 図 3 6の 発光層 3 6を例えば 1 0 O A以下の薄い単一組成で単一薄麵からなる井戸層として形成し、 薄膜層 3 4あるいは薄膜層 3 5のうち単一層の薄膜層を該井戸層の障壁層として用いることで 目的とする単一量子井戸構造を有する発光素子を作製することもできる。 また、 薄翻 3 4及
3 5がそれぞれ 2層以上の薄 からなるかあるいはどちらか一方だけが 2層以上の 薄膜層からなる場合であって 2層以上の薄膜層のうち発光層と直接接しているクラッド層を井 戸層の障壁層として用いて単一量子井戸構造を形成することもできる。
上記薄膜層 3 4、 薄膜層 3 5、 及び発光層 3 6はそれぞれ通常発光素子の発光効率を高める ためにェピタキシャル成長した単結晶であることが好ましい。 その結晶性は該薄膜のミラー指 数 (0 0 2 ) の格子面の X線回折ロッキング力一ブの半値幅が 3 6 0 0秒以下、 要すれば 3 0 0秒以下であることが好ましく、 さらにそれ以上の結晶性であることが好ましい。
また、 薄膜層 3 4及 ¾簿膜層 3 5は通常すベて単結晶状態であることが好ましいが上記のよ うに該薄膜層 3 4及び薄膜層 3 5が少なくともコンタク卜層及びクラッド層の 2層以上からな
る場合電極接続用のコンタクト層は必ずしも単結晶状態でなぐ 無定形、 多結晶、 配向性多結 晶の結晶状態であってもよい。
本発明による発光素子は からのサファイアなどからなる基板に代えて上記セラミック材 料を主成分とする焼結体をそのまま基板として用いる、 あるいは該基板に窒化ガリウム、 窒化 インジウム、 窒化アルミニウムのうちから選ばれた少なくとも 1種以上を主成分とする薄膜を 形成して薄膜基板としたものを用いることで、 «έ¾からのサファイアなどの基板を用いて作製 される発光軒に比べて発光効率が少なくとも同等、 あるいは 2〜3倍以上、 あるいは 3〜4 倍以上、 あるいは駄 4〜 5倍以上の優れたものが得られるようになった。 実際発光素子を作 '製していく場合、 上記セラミック材料を主成分とする焼結体からなる基板だけを用意しその上 に順次各薄) USを形成していく方法でもよいし、 上記セラミック材料を主成分とする焼結体か らなる基板の上にあらかじめ窒化ガリウム、 窒化インジウム、 窒化アルミニウムのうちから選 ばれた少なくとも 1種以上を主成分とする単結晶、 無定形、 多結晶、 配向性多結晶などのうち から選ばれたいずれかの結晶状態を有する薄膜を少なくとも 1層以上形成した薄膜基板を用意 し、 その上に順次各薄膜層を形成していく方法であってもよい。
図 40及び図 41は ί ^からのサファイアなどの基板を用いて作製された発光素子の 1例を 示した断面図である。 図 40で例示する構造の発光素子は図 39における薄膜層 35が 2層の 状態で形成されている例である。 通常このような薄■成により単一量子井戸構造の発光素子 が作製される。
図 40において例え【堪板面が C面の (すなわち基板面に対して C軸が垂直の方向の) サフ アイァなどの基板 33の上に MOCVD法、 あるいは MOVPE法、 あるいはその他の CVD 法、 あるいはクロライド VPE法などのハライド VPE法、 あるいは MB Ε法などの方法によ り窒化ガリウム、 窒化インジウム、 窒化アルミニウムのうちから選ばれた少なくとも 1種以上 を主成分とする薄膜からなるバッファ層 31が形成される。 なお、 基板 33はそのまま発光素 子作翻基板 30として用いられる。 バッファ薄 ]3ϋ31としては通常無定形の GaN薄膜を 100A〜150 OA程度の厚みで形成したものが用いられる。 バッファ層 31の上には MO CVD法、 あるいは MOVPE法、 あるいはその他の CVD法、 あるいはクロライド VPE法 などの八ライド VPE法、あるいは MB E法などの方法により窒化ガリウム、窒化インジウム、 窒化アルミニウムのうちから選ばれた少なくとも 1種以上を主成分とするェピタキシャル成長 した薄膜により構成される N型又は P型の半導体特性を有する薄膜層 34が形成される。 薄膜 層 34は単一量子井戸層の障壁層としても機能し得る。 薄膜層 34として通常 S iなどがド一 プされた N型の半導体特性を有するェピタキシャル成長した単結晶 G a N薄膜を 0. 5 m〜 20 m程度の厚みで形成したものが用いられる。 薄 S34の上には MOCVD法、 あるい は MOVPE法、 あるいはその他の CVD法、 あるいはクロライド VPE法などのハライド V PE法、 あるいは MB E法などの方法により窒化ガリウム、 窒化インジウム、 窒化アルミニゥ ムのうちから選ばれた少なくとも 1種以上を主成分とするェピタキシャル成長した薄膜により 構成される発光層 36が形成される。 例えば単一量子井戸構造を有する発光素子を作製する場 合、 発光層 36は井戸層として通常アンド一プのェピタキシャル成長した単結晶 I nGaN混 合組成の薄膜を 5 A〜 20 OA程度の厚みで形成したものが用いられる。 発光層から発せられ る光の波長は I nGaN組成によって変化し、 I n0.45Ga0.55Nの組成で発光波長は 520 nm程度(緑色)、 I n0.20Ga0.80Nの組成で発光波長は 450 nm程度(青色)、 I n0.06 Ga。.94Nの組成で発光波長は 39 Onm程度(紫色)、である。発光層 36の上には MOC V D法、 あるいは MOVPE法、 あるいはその他の CVD法、 あるいはクロライド VPE法など のハライド VP E法、 あるいは MB E法などの方法により窒化ガリウム、 窒化インジウム、 窒 化アルミニウムのうちから選ばれた少なくとも 1種以上を主成分とするェピタキシャル成長し
た薄膜により構成される P型又は N型の半導体特性を有する薄膜層 3 5 - 1が形成される。 薄 膜層 3 5— 1は薄膜層 3 4が N型半導体であるときは P型の半導体、 薄膜層 3 4が P型半導体 であるときは N型の半導体特性に調整される。 薄膜層 3 5— 1は単一 井戸層の障壁層とし ても機能し得る。 m m 3 5 - 1として通常 M gなどがド一プされた p型の半導体特性を有す るェピタキシャル成長した単結晶 A 1 G a N混合組成の薄膜を 0 · 0 2 m〜: 1. 0 m程度 の厚みで形成したものが用いられる。 薄SIIi 3 5— lの上にはM〇CVD法、 あるいは MOV P E法、 あるいはその他の CVD法、 あるいはクロライド VP E法などのハライド V P E法、 あるいは MB E法などの方法により窒化ガリウム、 窒化インジウム、 窒化アルミニウムのうち から選ばれた少なくとも 1種以上を主成分とするェピタキシャル成長した薄膜により構成され る薄膜層 3 5— 1と同じ型の半導体特性を有する薄膜層 3 5— 2が形成される。 薄膜層 3 5— 2は通常コンタクト層として機能する。 薄膜層 3 5— 2として通常 Mgなどがドープされた P 型の半導体特性を有するェピタキシャル成長した単結晶 G a N薄膜を 0. 0 5 ^m〜 5 m程 度の厚みで形成したものが用いられる。 薄 3 4は井戸層の障壁層だけでなく電極を形成す るコンタクト層としても用いられる。 薄 S 3 4及ぴ ^183 5には T i ZA 1あるいは N i /A uなどで構成された電極 3 8が形成される。
なお、 青紫色や紫色あるいは紫外線など波長の短い光を発光する発光軒の場合、 薄藤 3 4及ぴ有翻 3 5— 1及び 膜層 3 5— 2は極力発光の吸収を少なくするために主成分を 1 0 0モル% G a Nでなく A 1 Nと G a Nの混合組成 A 1 G a Nで形成したものが好適に用いられ る。
また、 S i、 G e、 S e、 T e、 Oなどのドナー形成ドーピング成分及び lVIg、 B e、 C a、 Z n、 C d、 Cなどのァクセプター形成ドーピング成分は薄膜を N型半導体化あるいは P型半 導体化しさらに該薄膜の抵抗率を小さくするために主成分に対してどのような割合でも含有さ せることができるが通常元素換算で 0. 0 0 0 0 1〜 1 0モル%の範囲で含有される。
図 4 0に例示されるように、 サファイアなどからなる基板 3 3、 バッファ層 3 1、 N型半導 体特性を有する薄翻 (または P型半導体特性を有する薄膜層) 3 4、 発光層 3 6、 P型半導 体特性を有する薄廳 ほたは N型半導体特性を有する薄膜層) 3 5 - 1 , P型半導体特性を 有する薄麵 (または N型半導体特性を有する薄麵) 3 5— 2、 電極 3 8、 により単一量子 井戸構造などを有する «からの発光素子 3 7が形成されてきた。 電極 3 8に直流電力を印加 することで発光素子が駆動し発光される。
サファイアなどの基板を用いて作製される上記単一量子井戸構造などの «からの発光^? の発光効率は通常 2 %〜 8 %程度である。
図 4 1は従来からのサフアイァなどの基板を用いて作製される発光素子の 1例を示す断面図 である。 図 4 1で例示する構造の発光素子は図 3 9における薄麵 3 4及ぴ 麵 3 5がそれ ぞれ 2層ずつの状態で形成された例である。 通常このような薄勝冓成によりダブルへテロ構造 の発光素子が作製される。
図 4 1において例えば基板面が C面の (すなわち基板面に対して C軸が垂直の方向の) サフ アイァなどの基板 3 3の上に MOCVD法、 あるいは MOVP E法、 あるいはその他の CVD 法、 あるいはクロライド VP E法などのハライド VP E法、 あるいは MB E法などの方法によ り窒化ガリウム、 窒化インジウム、 窒化アルミニウムのうちから選ばれた少なくとも 1種以上 を主成分とする薄膜からなるバッファ層 3 1が形成される。 なお、 基板 3 3はそのまま発光素 子作製用基板 3 0として用いられる。 バッファ薄膜層 3 1としては通常無定形の G a N薄膜を 1 0 0 A〜2 0 0 O A程度の厚みで形成したものが用いられる。 バッファ層 3 1の上には M〇 CVD法、 あるいは MOVP E法、 あるいはその他の CVD法、 あるいはクロライド VP E法 などのハライド VP E法、あるいは MB E法などの方法により窒化ガリゥム、窒化ィンジゥム、
窒化アルミニウムのうちから選ばれた少なくとも 1種以上を主成分とするェピタキシャル成長 した薄膜により構成される N型又は P型の半導体特性を有する薄膜層 34-2が形成される。 薄膜層 34-2は電極と電気的に接続し発光層へ電位を印加するためのコン夕クト層である。 薄膜層 34— 2として通常 S iなどがドープされた N型の半導体特性を有するェピタキシャル 成長した単結晶 G a N薄膜を 0. 5 Π!〜 20 m程度の厚みで形成したものが用いられる。 薄膜層 34— 2の上には MOCVD法、 あるいは MOVPE法、 あるいはその他の CVD法、 あるいはクロライド VP E法などのハラィド VPE法、 あるいは MB E法などの方法により窒 化ガリウム、 窒化インジウム、 窒化アルミニウムのうちから選ばれた少なくとも 1種以上を主 成分とするェピタキシャル成長した薄膜により構成される N型又は P型の半導体特性を有する 薄膜層 34— 1が形成される。薄膜層 34— 1は発光層を挟むクラッド層のうちの一つである。 薄膜層 34— 1として通常 S iなどがド一プされた N型の半導体特性を有するェピタキシャル 成長した単結晶 A 1 G a N薄膜を 0. 02 m〜 1. 0 m程度の厚みで形成したものが用い られる。 wmm 34-1 mmmm 34-2とは同じ型の半導体特性を有する。 mm 34—
1の上には MOCVD法、 あるいは MOVPE法、 あるいはその他の CVD法、 あるいはクロ ライド VP E法などのハラィド VPE法、 あるいは MB E法などの方法により窒化ガリウム、 窒化インジウム、 窒化アルミニウムのうちから選ばれた少なくとも 1種以上を主成分とするェ ピ夕キシャル成長した薄膜により構成されるアンドープ、 あるいは Zn単独ド一プ、 あるいは
S i単独ドープ、 あるいは Znと S iとを同時にドープした発光層 36が形成される。 例えば ダカレヘテロ構造の発光軒を作製する場合発光層 36は通常アンド一プ、 あるいは上記ド一 ピング成分を含むェピタキシャル成長した単結晶 I nGaN混合組成の薄膜を 50人〜 500 OA程度の厚みで形成したものが用いられる。 発光層からの発せられる光の波長は I nGaN 組成、 あるいはドーピング成分の種類によって変化し、 アンドープの I n0.20Ga0.80Nの組 成で発光波長は 450 nm程度 (青色)、 アンド一プの I n0.06Ga0.94Nの組成で発光波長 は 39 Onm程度(紫色)、 Zn あるいは Zn及び S iの同時ドーピングの I n0.06Ga0. 94Nの組成で発光波長は 45 Onm程度 (青色) である。 発光層 36の上には MOCVD法、 あるいは MOVPE法、 あるいはその他の CVD法、 あるいはクロライド VPE法などのハラ イド VP E法、 あるいは MB E法などの方法により窒化ガリウム、 窒化インジウム、 窒化アル ミニゥムのうちから選ばれた少なくとも 1種以上を主成分とするェピタキシャル成長した薄膜 により構成される P型又は N型の半導体特性を有する薄膜層 35-1が形成される。 薄膜層 3 5 - 1は薄膜層 34-1が N型半導体であるときは P型の半導体、 薄膜層 34-1が P型半導 体であるときは N型の半導体特性に調整される。 薄膜層 35-1は発光層を挟むクラッド層と して機能する。 薄膜層 35一 1として通常 Mgなどがドープされた P型の半導体特性を有する ェピタキシャル成長した単結晶 A 1 G a N混合組成の薄膜を 0. 02 m〜 1. 0 zm程度の 厚みで形成したものが用いられる。 薄 35—1の上には MOCVD法(MOVPE法)、 あ るいはその他の CVD法、 あるいはクロライド VPE法などのハライド VPE法、 あるいは M BE法などの方法により窒化ガリウム、 窒化インジウム、 窒化アルミニウムのうちから選ばれ た少なくとも 1種以上を主成分とするェピタキシャル成長した薄膜により構成される薄膜層 3 5— 1と同じ型の半導体特性を有する薄膜層 35— 2が形成される。 薄膜層 35— 2はコンタ クト層として機能する。 薄膜層 35- 2として通常 Mgなどがド一プされた P型の半導体特性 を有するェピタキシャル成長した単結晶 G a N薄膜を 0. 05 m〜 5 xm程度の厚みで形成 したものが用いられる。 薄膜層 34一 2及び 膜層 35-2には T i /A 1あるいは N i /A uなどで構成された電極 38が形成される。
図 41に示す発光素子は発光層 36力 S 2層の半導体薄膜層 34— 1及び 34— 2と 2層の半 導体薄膜層 35— 1及び 35-2とに挟まれておりダブルへテロ構造を有する。
TJP2004/000051
260
なお、 クラッド層である上記薄 Si¾ 34-1及ぴ 膜層 35— 1をさらに 2層で形成しコン タクト層を含め合計それぞれ 3層の薄 11®で発光層を挾んだ構造の発光素子も作製できる。 す なわちこのような例として、 例えば薄膜層 34—1として発光層側に S iなどをドーピングし た I nG aN混合組成の薄膜及びコンタクト層側に S iなどをドーピングした A 1 G aN混合 組成の薄膜、 薄膜層 35-1として発光層側に Mgなどをドーピングした I nG aN混合組成 の薄膜及びコンタクト層側に Mgなどをドーピングした A 1 GaN混合組成の薄膜、 それぞれ 層づつから構成されたものなどである。
なお、 青紫色や紫色あるいは紫外線など波長の短い光を発光する発光軒の場合、 薄翻 3 4一 1、 薄膜層 34— 2、 薄膜層 35—1及び薄膜層 35— 2は極力発光の吸収を少なくする ために主成分を 100モル%GaNでなく A 1Nと GaNの混合組成 A 1 GaNで形成したも のが好適に用いられる。
また、 S i、 Ge、 Se、 Te、 Oなどのドナ一形成ドーピング成分及び ¾ig、 Be、 Ca、 Zn、 Cd、 Cなどのァクセプ夕一形成ドーピング成分は薄膜を N型半導体化あるいは P型半 導体化しさらに該薄膜の抵抗率を小さくするために主成分に対してどのような割合でも含有さ せることができるが通常元素 1^で 0. 00001〜 10モル%の範囲で含有されることが好 ましい。
図 41に例示するように、 サフアイァなどからなる基板 33、 バッファ層 31、 N型半導体 特性を有する薄藤 ほたは P型半導体特性を有する薄麵) 34-2, N型半導体特性を有 する薄膜層 (又は P型半新本特性を有する薄膜層) 34-1, 発光層 36、 P型半 f本特性を 有する薄翻 (または N型半導体特性を有する薄腿) 35-1, P型半導体特性を有する薄 膜層 (または N型半導体特性を有する薄編) 35— 2、 電極 38、 によりダブルへテロ構造 で «からの発光素子 37が形成されてきた。 電極 38に直流電力を印加することで発光素子 力 «動し発光される。
サファイアなどの基板を用いて作製される上記 «からのダブルへテロ構造の発光軒の発 光効率は通常 2 %〜 8 %程度である。
図 42〜図 61図は本発明による窒化アルミニウムを主成分とする焼結体、 六方晶系又は三 方晶系の結晶構造を有するセラミック材料を主成分とする焼結体、 窒化ガリウム、 窒化インジ ゥム、 窒化アルミニウムのうちから選ばれた少なくとも 1種以上を主成分とする薄膜を形成し たセラミック材料を主成分とする焼結体、 などのセラミック材料を主成分とする焼結体を用い て作製された発光素子の例を示す。 図 42〜図 61図には上記の各セラミック材料を主成分と する焼結体を基板とし該基板に発光素子の 要素である窒化ガリゥム、 窒化ィンジゥム、 窒 化アルミニウムのうちから選ばれた少なくとも 1種以上を主成分とする薄膜からなる N型半導 体層及び発光層及び P型半導体層を積層して発光素子が構成される様子が示されている。 図 42は からのサファイアなどの基板に代えてセラミック材料を主成分とする焼結体か らなる基板をそのまま発光素子作製用基板として用いた本発明による発光素子の 1例を示す断 面図である。 すなわち、 図 42においてセラミック材料を主成分とする焼結体からなる基板 4 をそのまま発光素子作製用基板 30として用い、 その他は図 40で示したものと同様な薄膜構 成により本発明による発光素子 39が形成されている様子が示されている。 図 42においてセ ラミック材料を主成分とする焼結体からなる基板 4そのものが発光素子作製用基板 30として 用いられる。
図 42で例示した本発明による発光素子において薄膜層 34、 薄膜層 35— 1、 薄膜層 35 一 2及び発光層 36はそれぞれ通常発光素子の発光効率を高めるためにェピタキシャル成長し た単結晶として形成できる。 その結晶性は該薄膜のミラー指数 (002) の格子面の X線回折 ロッキングカーブの半値幅が 3600秒以下、 通常 300秒以下、 さらに 100秒以下の結晶
性のものが形成できる。
m m s 4、 wmm 3 5 - 1及び^ sis 3 5- 2は通常すベて単結晶状態であることが好ま しいが、 薄Ι® 3 5— 2及び臂 3 4が 2層以上からなる場合 2層のうち電極接続用のコン 夕クト層のほうは必ずしも単結晶状態でなぐ 無定形、 多結晶、 配向性多結晶の結晶状態であ つてもよい。
図 4 2に例示した本発明によるセラミック材料を主成分とする焼結体からなる基板を用いて 作製される上記発光素子の発光効率は通常 8 %以上であり、 サフアイァなどの基板を用いて作 製される からの発光素子の発光効率よりすぐれている。 基板 4として窒化アルミニウムを 主成分とする焼結体を用いた場合少なくとも 1 0 %以上の発光効率を有する発光素子を作製す ることができる。
図 4 3は従来からのサファイアなどの基板に代えてセラミック材料を主成分とする焼結体か らなる基板の上に窒化ガリゥム、 窒化ィンジゥム、 窒化アルミニゥムのうちから選ばれた少な くとも 1種以上を主成分とする薄膜を少なくとも 1層形成したものを発光素子作製用基板とし て用いた本発明による発光素子の 1例を示す断面図である。 すなわち、 図 4 3においてセラミ ック材料を主成分とする能結体からなる基板 4の上に窒化ガリウム、 窒化インジウム、 窒化ァ ルミニゥムのうちから選ばれた少なくとも 1種以上を主成分とする薄膜 5を形成したものを発 光素子作製用基板 3 0として用い、 その他は図 4 0で示したものと同様な薄腿冓成により本発 明による発光舒 3 9が形成されている様子が示されている。 薄膜 5は通常単結晶、 無定形、 多結晶、配向性多結晶のうちから選ばれた少なくともいずれかの結晶状態のものが用いられる。 図 4 3においてセラミツク材料を主成分とする焼結体からなる基板 4及び該基板 4の上に形成 された薄膜 5とにより発光素子作製用基板 3 0が構成される。
図 4 3で例示した本発明による発光素子において薄膜層 3 4、 薄膜層 3 5— 1、 薄膜層 3 5 一 2及び発光層 3 6はそれぞれ通常発光素子の発光効率を高めるためにェピタキシャル成長し た単結晶として形成できる。 その結晶性は該薄膜のミラー指数 ( 0 0 2 ) の格子面の X線回折 ロッキングカーブの半値幅が 3 6 0 0秒以下、 通常 3 0 0秒以下、 さらに 1 0 0秒以下の結晶 性のものが形成できる。
薄膜層 3 4、 薄膜層 3 5 - 1及ぴ¾膜層 3 5 - 2は通常すベて単結晶状態であることが好ま しいが、 薄 m® 3 5— 2及ぴ奪 3 4が 2層以上からなる場合 2層のうち電極接続用のコン タクト層のほうは必ずしも単結晶状態でなぐ 無定形、 多結晶、 配向性多結晶の結晶状態であ つてもよい。
図 4 3に例示した本発明によるセラミック材料を主成分とする焼結体からなる基板を用いて 作製される上記発光素子の発光効率は通常 8 %以上であり、 サファイアなどの基板を用いて作 製される«からの発光素子の発光効率よりすぐれている。 基板 4として窒ィ匕アルミニウムを 主成分とする焼結体を用いた場合少なくとも 1 0 %以上の発光効率を有する発光素子を作製す ることができる。
図 44は »からのサファイアなどの基板に代えてセラミック材料を主成分とする焼結体か らなる基板の上に窒化ガリウム、 窒化インジウム、 窒化アルミニウムのうちから選ばれた少な くとも 1種以上を主成分とする薄膜を少なくとも 2層形成したものを発光素子作製用基板とし て用いた本発明による発光素子の 1例を示す断面図である。 すなわち、 図 4 4においてセラミ ック材料を主成分とする焼結体からなる基板 4の上に窒化ガリウム、 窒化インジウム、 窒化ァ ルミニゥムのうちから選ばれた少なくとも 1種以上を主成分とする薄膜 5を形成し、 その上に さらに窒化ガリウム、 窒化インジウム、 窒化アルミニウムのうちから選ばれた少なくとも: L種 以上を主成分とする薄膜 8を形成した少なくとも薄膜 2層以上が形成されたものを発光素子作 製用基板 3 0として用い、 その他は図 4 0で示したものと同様な薄 ϋ¾成により発光素子 3 9
が形成されている様子が示されている。 薄膜 5及ぴ臂膜 8は通常単結晶、 無定形、 多結晶、 配 向性多結晶のうちから選ばれた少なくともいずれかの結晶状態のものが用いられる。 通常薄膜 8は単結晶状態のものを用いることが好ましい。 その場合薄膜 5として無定形、 多結晶、 配向 性多結晶のうちから選ばれた少なくともいずれかの結晶状態のものを用いることが好ましく、 さらに配向性多結晶状態のものを用いることがより好ましい。 図 4 4においてセラミック材料 を主成分とする焼結体からなる基板 4及び該基板 4の上に形成された薄膜 5及び 膜 8とによ り発光素子作製用基板 3 0が構成される。
図 4 4で例示した本発明による発光素子において薄膜層 3 4、 薄膜層 3 5 - 1 , 薄膜層 3 5 一 2及び発光層 3 6はそれぞれ通常発光素子の発光効率を高めるためにェピタキシャル成長し た単結晶として形成できる。 その結晶性は該薄膜のミラー指数 ( 0 0 2) の格子面の X線回折 ロッキングカーブの半値幅が 3 6 0 0秒以下、 通常 3 0 0秒以下、 さらに 1 0 0秒以下の結晶 性のものが形成できる。
薄膜層 3 4、 薄膜層 3 5— 1及 ϋ簿膜層 3 5— 2は通常すベて単結晶状態であることが好ま しいが、 薄藤 3 5— 2及ぴ育麵 3 4が 2層以上からなる場合 2層のうち電極接続用のコン タクト層のほうは必ずしも単結晶状態でなぐ 無定形、 多結晶、 配向性多結晶の結晶状態であ つてもよい。
図 4 4に例示した本発明によるセラミック材料を主成分とする焼結体からなる基板を用いて 作製される上記発光素子の発光効率は通常 8 %以上であり、 サフアイァなどの基板を用いて作 製される徹からの発光素子の発光効率よりすぐれている。 基板 4として窒化アルミニウムを 主成分とする焼結体を用いた場合少なくとも 1 0 %以上の発光効率を有する発光素子を作製す ることができる。
図 4 5は図 4 4で断面図として示されている本発明による発光素子を斜めから見た様子の 1 例を示す斜視図である。 図 4 5は従来からのサファイアなどの基板に代えてセラミック材料を 主成分とする焼結体からなる基板の上に窒化ガリウム、 窒化インジウム、 窒化アルミニウムの うちから選ばれた少なくとも 1種以上を主成分とする薄膜を少なくとも 2層形成したものを発 光素子作製用基板として用いた例として示されている。 図 4 5において薄膜層 3 4の隅の一部 をエッチングなどで取り除いて電極 3 8が小さく形成されている様子が示されている。 他の電 極 3 8も薄 MS 3 5 - 2の隅の部分に小さく形成されている。 このような電極配置で構成され る発光素子 常発光層全面から発光が行われるような発光ダイオード (L ED) に用いられ る。 図 4 5に例示されているように電極を薄膜層の隅の部分などに小さく形成するか、 あるい は図 4 5には記載されていないが電気的接続を高めるために電極を薄膜層 3 4及び薄膜層 3 5 一 2の広い面積にわたって形成する場合発光層からの発光を ¾iiできるような厚みにまで電極 を薄くして発光層全面からの発光が電極でできるだけ遮断されないようにし、 発光を可能な限 り素子外部に放出されるよう電極を構成することが好ましい。
図 4 6は図 4 4で断面図として示されている本発明による発光素子を斜めから見た様子の 1 例を示す斜視図である。 図 4 6は従来からのサファイアなどの基板に代えてセラミック材料を 主成分とする焼結体からなる基板の上に窒化ガリウム、 窒化インジウム、 窒化アルミニウムの うちから選ばれた少なくとも 1種以上を主成分とする薄膜を少なくとも 2層形成したものを発 光素子作製用基板として用いた例として示されている。 図 4 6は図 4 5示されている本発明に よる発光素子の電極配置を薄膜層の隅に小さく形成するのではなく、 薄麵全体にわたり帯状 に形成した発光素子の例を示している。 図 4 6において薄膜層 3 4の 1辺の部分をすベてエツ チングなどで取り除いて電極 3 8が帯状に形成されており、 もう一方の電極 3 8も薄麵 3 5 ― 2に帯状で形成されている。 このような電極配置で構成される発光素子は薄画 3 5— 2に 形成された電極直下部分の発光層内で光が多重反射され発光層からレーザー光のように一定の
方向にだけ高いエネルギーで発光が行われるレ一ザ一ダイオード (LD) として通常用いられ る。
図 4 6で例示された構造の発光素子をレーザーダイォードとして形成する場合は発光素子作 製用基板 3 0を構成するセラミック基板 4として窒化アルミニウムを主成分とする焼結体から なるものが、好ましい。 すなわち、 «からのサファイアなどの基板を用いてレーザーダイォー ドを作製する場合、 基板とその上に形成される窒化ガリウム、 窒化インジウム、 窒化アルミ二 ゥムのうちから選ばれた少なくとも 1種以上を主成分とする薄膜との間の格子不整合や熱膨張 率などの不一致を軽減するためにあらかじめ S i 02などの薄膜を帯状に形成しその上にあら ためて該窒化ガリウム、 窒化インジウム、 窒化アルミニウムのうちから選ばれた少なくとも 1 種以上を主成分とする薄膜を形成し薄膜中の転位やクラックなどの少ない部分をレーザ一ダイ ォ一ドとして機能する部材として使用していくといういわゆる ELO成長 (E p i t a x i a 1 1 y L a t e r a l O v e r— g r ow t h)法による方法が用いられることが多いカ^ 基板 4として窒ィ匕アルミニウムを主成分とする焼結体からなるものも用いれ 板と該窒化ガ リウム、 窒化インジウム、 窒化アルミニウムのうちから選ばれた少なくとも 1種以上を主成分 とする薄膜との間の格子不整合や熱膨張率などの不一致などが小さいので、 図 4 6に記載され ているように S i〇2などの薄膜を形成せず基板に直接転位やクラックの少ない該窒化ガリウ ム、 窒化インジウム、 窒化アルミニウムのうちから選ばれた少なくとも 1種以上を主成分とす る薄膜が形成できるので、 該薄膜の特定の場所によらず該薄膜のいずれの部分を用いても発光 効率の優れたレーザ一ダイォードが作製できるという効果がある。
また、 レーザ一ダイォ一ドとして、 厚みの薄い例えば 1 0 0 A以下の A 1 G a N混合組成の 薄膜と 1 0 O A以下の G aN薄膜とを数十層以上積層したスーパ一ラテイス構造の薄膜層をそ れぞれ N型及び P型半導体として発光層を挟むように形成する構造のものが高出力で寿命の長 いものが得られ易いが、 本発明においては特に発光^?作製用基板として窒化アルミニウムを 主成分とする焼結体を用いた場合、 このようなスーパーラティス構造の薄膜層を用いて作製さ れるレーザ一ダイォードは勿論、 該スーパ一ラティス構造の薄 は用いず多重量子井戸構造 の発光層以外のクラッド層あるいはコンタク卜層などはそれぞれ単層の薄膜で構成されたもの であっても発光効率が高く高出力で高寿命のレーザーダイオードが作製し得る。
図 4 6で例示された構造の発光素子においても基板に形成される薄膜層 8としては窒化ガリ ゥム、 窒化インジウム、 窒化アルミニウムのうちから選ばれた少なくとも 1種以上を主成分と する単結晶薄膜であることが好ましい。 その場合薄膜 5として無定形、 多結晶、 配向性多結晶 のうちから選ばれた少なくともいずれかの結晶状態のものを用いることが好ましく、 さらに配 向性多結晶状態のものを用いることがより好ましい。
また、 図 4 6で例示された構造の発光素子をレーザーダイォ一ドとして形成する場合は発光 層として薄膜 1層の井戸層からなる単一量子井戸構造でなく、 井戸層と障壁層とを繰り返し積 層した多重量子井戸構造を用いることが好ましい。 また、 発光素子をレーザーダイオードとし て形成する場合は薄翻 3 4、 薄画3 5— 1、 薄膜層 3 4— 2なども ¾それぞれ多層化し て形成したものが用いられる。
図 4 7は従来からのサファイアなどの基板に代えて導通ビアを有するセラミック材料を主成 分とする焼結体からなる基板をそのまま発光素子作製用基板として用いた本発明による発光素 子の 1例を示す断面図である。 すなわち、 図 4 7において導通ピア 3を有するセラミック材料 を主成分とする焼結体からなる基板 9をそのまま発光素子作製用基板 3 0として用い、 その他 は図 4 0で示したものと同様な薄腐冓成により本発明による発光素子 3 9が形成されている様 子が示されている。 図 4 7において導通ビア 3を有するセラミック材料を主成分とする焼結体 からなる基板 9そのものが発光素子作製用基板 3 0として用いられる。
図 4 7に例示した本発明による導通ビア 3を有するセラミック材料を主成分とする焼結体か らなる基板 9を用いて作製される発光素子の場合、 図 4 2〜図 4 6で示したように薄 JM 3 4 の一部をエッチングなどにより取り除いて電極を形成する必要がなぐ 電極 3 8をセラミック 基板 9に形成した上下に電極が己置された構成の発光素子を作製することができる。
図 4 8は ί ^からのサフアイァなどの基板に代えて導通ビアを有するセラミック材料を主成 分とする焼結体からなる基板の上に窒化ガリウム、 窒化インジウム、 窒化アルミニウムのうち から選ばれた少なくとも 1種以上を主成分とする薄膜を少なくとも 1層形成したものを発光素 子作製用基板として用いた本発明による発光素子の 1例を示す断面図である。 すなわち、 図 4 8において導通ビア 3を有するセラミック材料を主成分とする焼結体からなる基板 9の上に窒 化ガリウム、 窒化インジウム、 窒化アルミニウムのうちから選ばれた少なくとも 1種以上を主 成分とする薄膜 5を形成したものを発光素子作製用基板 3 0として用い、 その他は図 4 0で示 したものと同様な薄 成により本発明による発光素子 3 9が形成されている様子が示されて いる。 薄膜 5は通常単結晶、 無定形、 多結晶、 配向性多結晶のうちから選ばれた少なくともい ずれかの結晶状態のものが用いられる。 図 4 8において導通ビア 3を有するセラミック材料を 主成分とする焼結体からなる基板 9の上に窒化ガリウム、 窒化インジウム、 窒化アルミニウム のうちから選ばれた少なくとも 1種以上を主成分とする薄膜 5を形成したものが発光素子作製 用基板 3 0として用いられる。
図 4 8に例示した本発明による導通ビア 3を有するセラミック材料を主成分とする焼結体か らなる基板 9を用いて作製される発光素子の場合、 薄膜 5を導電性とすることで図 4 2〜図 4 6で示したように薄膜層 3 4の一部をエッチングなどにより取り除いて電極を形成する必要が なぐ 電極 3 8をセラミック基板 9に形成した上下に電極が配置された構成の発光^?を作製 することができる。
図 4 9は«からのサファイアなどの基板に代えて導通ビアを有するセラミック材料を主成 分とする焼結体からなる基板の上に窒化ガリウム、 窒化インジウム、 窒化アルミニウムのうち から選ばれた少なくとも 1種以上を主成分とする薄膜を少なくとも 2層形成したものを発光素 子作製用基板として用いた本発明による発光素子の 1例を示す断面図である。 すなわち、 図 4 9において導通ビア 3を有するセラミック材料を主成分とする焼結体からなる基板 9の上に窒 化ガリウム、 窒化インジウム、 窒化アルミニウムのうちから選ばれた少なくとも 1種以上を主 成分とする薄膜 5を形成し、 その上にさらに窒化ガリウム、 窒化インジウム、 窒化アルミニゥ ムのうちから選ばれた少なくとも 1種以上を主成分とする薄膜 8を形成した少なくとも薄膜 2 層以上が形成されたものを発光素子作製用基板 3 0として用い、 その他は図 4 0で示したもの と同様な薄廳冓成により本発明による発光素子 3 9が形成されている様子が示されている。 薄 膜 5 «®常単結晶、 無定形、 多結晶、 配向性多結晶のうちから選ばれた少なくともいずれかの 結晶状態のものが用いられる。 図 4 9において導通ビア 3を有するセラミック材料を主成分と する焼結体からなる基板 9の上に窒化ガリウム、 窒化インジウム、 窒化アルミニウムのうちか ら選ばれた少なくとも 1種以上を主成分とする薄膜 5を形成し、その上にさらに窒化ガリウム、 窒化インジウム、 窒化アルミニウムのうちから選ばれた少なくとも 1種以上を主成分とする薄 膜 8を形成した少なくとも薄膜 2層以上を形成したものが発光素子作製用基板 3 0として用い られる。
図 4 9に例示した本発明による導通ビア 3を有するセラミック材料を主成分とする焼結体か らなる基板 9を用いて作製される発光素子の場合、 薄膜 5及 ϋ簿膜 8を導電性とすることで図 4 2〜図 4 6で示したように薄膜層 3 4の一部をエッチングなどにより取り除いて電極を形成 する必要がなく、 電極 3 8をセラミック基板 9に形成した上下に電極が 3置された構成の発光 素子を作製することができる。
図 4 7〜図 4 9で例示した導通ビアを有するセラミック材料を主成分とする焼結体からなる 基板を用いて作製される本発明による発光素子において薄膜層 3 4、 薄膜層 3 5— 1、 mmm
3 5 _ 2及び発光層 3 6はそれぞれ通常発光素子の発光効率を高めるためにェピタキシャル成 長した単結晶として形成できる。 その結晶性は該薄膜のミラー指数 ( 0 0 2) の格子面の X線 回折ロッキングカーブの半値幅が 3 6 0 0秒以下、 通常 3 0 0秒以下、 さらに 1 0 0秒以下の 結晶性のものが形成できる。 上記薄編 3 4、 薄翻 3 5 - 1及び 麵 3 5 - 2は通常すベ て単結晶状態であることが好ましいが、 薄膜層 3 5— 2及び薄膜層 3 4が 2層以上からなる場 合 2層のうち電極接続用のコンタクト層のほうは必ずしも単結晶状態でなぐ無定形、多結晶、 配向性多結晶の結晶状態であってもよい。
図 4 7〜図 4 9に例示した本発明による導通ビアを有するセラミック材料を主成分とする焼 結体からなる基板を用いて作製される上記発光軒の発光効率は通常 8 %以上であり、 サファ ィァなどの基板を用いて作製される«からの発光素子の発光効率よりすぐれている。 基板 9 として窒化アルミニウムを主成分とする焼結体を用いた場合少なくとも 1 0 %以上の発光効率 を有する発光素子を作製することができる。
図 5 0は従来からのサフアイァなどの基板に代えて導電性を有するセラミツク材料を主成分 とする焼結体からなる基板の上に窒化ガリウム、 窒化インジウム、 窒化アルミニウムのうちか ら選ばれた少なくとも 1種以上を主成分とする薄膜を少なくとも 2層形成したものを発光素子 作製用基板として用いた本発明による発光素子の 1例を示す断面図である。 すなわち、 図 5 0 において導電性を有するセラミック材料を主成分とする焼結体からなる基板 1 3 0の上に窒化 ガリウム、 窒化インジウム、 窒化アルミニウムのうちから選ばれた少なくとも 1種以上を主成 分とする薄膜 5を形成し、 その上にさらに窒化ガリウム、 窒化インジウム、 窒化アルミニウム のうちから選ばれた少なくとも 1種以上を主成分とする薄膜 8を形成した少なくとも薄膜 2層 以上が形成されたものを発光素子作製用基板 3 0として用い、 その他は図 4 0で示したものと 同様な薄騰成により本発明による発光軒 3 9が形成されている様子が示されている。 薄膜 5は通常単結晶、 無定形、 多結晶、 配向性多結晶のうちから選ばれた少なくともいずれかの結 晶状態のものが用いられる。 図 5 0において導電性を有するセラミツク材料を主成分とする焼 結体からなる基板 1 3 0の上に窒化ガリウム、 窒化インジウム、 窒化アルミニウムのうちから 選ばれた少なくとも 1種以上を主成分とする薄膜 5を形成し、 その上にさらに窒化ガリゥム、 窒化インジウム、 窒化アルミニウムのうちから選ばれた少なくとも 1種以上を主成分とする薄 膜 8を形成した少なくとも薄膜 2層以上を形成したものが発光素子作製用基板 3 0として用い られる。
図 5 0に例示した本発明による導電性を有するセラミック材料を主成分とする焼結体からな る基板 1 3 0を用いて作製される発光素子の場合、 薄膜 5及び薄膜 8を導電性とすることで図 4 2〜図 4 6で示したように薄膜層 3 4の一部をエッチングなどにより取り除いて電極を形成 する必要がなぐ 電極 3 8をセラミック基板 9に形成した上下に電極が 置された搆成の発光 素子を作製することができる。 上記導電性を有するセラミック材料を主成分とする焼結体の室 温における ί職率は通常 1 X 1 0 2 Ω · c m以下のものが用いられる。発光層へできるだけ損失 を少なく電力の供給を行うために室温における抵抗率としては 1 X 1 0ェ0 · c m以下のものが 好ましく、 I X 1 0 ° Ω · c m以下のものがより好ましく、 1 X 1 Ο ^ Ω · c m以下のものがさ らに好ましく、 1 X 1 CI -2 Ω · c m以下のものが最も好ましい。
導電性を有するセラミック材料を主成分とする焼結体からなる基板 1 3 0として例えば ¾化 亜鉛を主成分とする焼結体からなるものを用いることができる。 酸化亜鉛を主成分とする焼結 体の場合アルミニウム成分や鉄あるいはクロムなどの遷移金属成分を加えるかアルミニウム成 分と同時に上記遷移金属成分あるいは希土 ¾素成分とを同時に加えることによって室温にお
ける抵抗率 I X 1 0 2Ω · c m以下のものが比較的容易に得られる。 また室温における抵抗率と して 1 X 1 (^ Ω · c m以下のもの、 1 X 1 0 ° Ω · c m以下のもの、 1 X 1 0— c m以下 のもの、さらに 1 X 1 0一2 Ω · c m以下のものも比較的容易に得ることができるので好ましい。 また、 酸化亜鉛を主成分とする焼結体の場合本発明によって明らかとなったように導電性と 同時に光 ¾ 性のものが得られるので発光効率に優れた上下導通タイプの電極配置の発光素子 を作製するための基板として用いることができるので好ましい。
図 5 0で例示した導電性を有するセラミック材料を主成分とする焼結体からなる基板を用い て作製される本発明による発光素子において薄膜層 3 4、 薄膜層 3 5— 1、 薄膜層 3 5— 2及 び発光層 3 6はそれぞれ通常発光素子の発光効率を高めるためにェピタキシャル成長した単結 晶として形成できる。 その結晶性は該薄膜のミラ一指数 ( 0 0 2) の格子面の X線回折ロッキ ングカーブの半値幅が 3 6 0 0秒以下、 通常 3 0 0秒以下、 さらに 1 0 0秒以下の結晶 'I生のも の力 S形成できる。 上記薄 3 4、 薄 III 3 5 - 1及び 膜層 3 5 - 2は通常すベて単結晶状 態であることが好ましいが、 薄1® 3 5— 2及ぴ育膜層 3 4が 2層以上からなる場合 2層のう ち電極接続用のコンタクト層のほうは必ずしも単結晶状態でなぐ 無定形、 多結晶、 配向性多 結晶の結晶状態であつてもよい。
図 5 0に例示した本発明による導電性を有するセラミック材料を主成分とする焼結体からな る基板を用いて作製される上記発光素子の発光効率は通常 8 %以上であり、 サファイアなどの 基板を用いて作製される従来からの発光^?の発光効率よりすぐれている。
図 5 1は徹からのサファイアなどの基板に代えて窒化アルミニウムを主成分とする焼結体 からなる基板の上に各種金属、 合金、 金属窒化物、 金属炭化物、 金属珪化物などの材料を主成 分とする薄膜導電性材料を少なくとも 1層形成したものを発光素子作製用基板として用いた本 発明による発光素子の 1例を示す断面図である。 すなわち、 図 5 1おいて窒化アルミニウムを 主成分とする焼結体からなる基板 1 3の上に薄 電性材料 1 1を形成したものを発光 作 製用基板 3 0として用い、 その他は図 4 0で示したものと同様な薄膨冓成により本発明による 発光素子 3 9が形成されている様子が示されている。 図 5 1において窒化アルミニウムを主成 分とする焼結体からなる基板 1 3の上に薄 電性材料 1 1を形成したものが発光素子作製用 基板 3 0として用いられる。
図 5 1に例示した本発明による薄膜導電性材料 1 1が形成された窒化アルミニウムを主成分 とする焼結体からなる基板 1 3を用いて作製される発光素子の場合、 該薄膜導電性材料 1 1を 反射部材として用いることで発光^?からの発光 板 1 3からは放出されにくくなり、 該基 板 1 3より上の方向から素子外部へ放出され易くなるので例えば面発光レーザ一あるいは平板 状ディスプレイに用いる発光ダイォ一ドなど発光の方向性制御が要求される発光素子が作製し 得るので好ましい。
図 5 2は、 図 5 1に示した薄膜導電性材料 1 1を形成した窒化アルミニウムを主成分とする 焼結体からなる基板 1 3の上に図 4 3及び図 4 8と同様の窒化ガリウム、 窒化インジウム、 窒 化アルミニウムのうちから選ばれた少なくとも 1種以上を主成分とする薄膜を少なくとも 1層 形成したものを発光素子作製用基板 3 0として用いて作製される本発明による発光素子の 1例 を示す断面図である。
また、 薄膜導電性材料 1 1を反射部材として用いた場合の効果については図 5 1で例示した 発光素子と同様である。
図 5 3は、 図 5 1に示した薄膜導電性材料 1 1を形成した窒化アルミニウムを主成分とする 焼結体からなる基板 1 3の上に図 4 4、 図 4 9及び図 5 0と同様、 窒化ガリウム、 窒化インジ ゥム、 窒化アルミニウムのうちから選ばれた少なくとも 1種以上を主成分とする薄膜を少なく とも 1層形成し、 その上にさらに窒化ガリウム、 窒化インジウム、 窒化アルミニウムのうちか
ら選ばれた少なくとも 1種以上を主成分とする薄膜を形成した少なくとも薄膜 2層以上が形成 されたものを発光素子作製用基板 3 0として用いて作製される本発明による発光素子の 1例を 示す断面図である。
また薄膜導電†生材料 1 1を反射部材として用いた場合の効果については図 5 1で例示した発 光素子と同様である。
図 5 1〜図 5 3で例示した薄膜導電性材料が形成された窒化アルミニウムを主成分とする焼 結体からなる基板を用いて作製される本発明による発光素子において薄 JUS 3 4、 薄 SIB 3 5 ― 1、 薄膜層 3 5 - 2及び発光層 3 6はそれぞれ通常発光素子の発光効率を高めるためにェピ タキシャル成長した単結晶として形成できる。 その結晶性は該薄膜のミラー指数 ( 0 0 2 ) の 格子面の X線回折ロッキングカーブの半値幅が 3 6 0 0秒以下、 通常 3 0 0秒以下、 さらに 1 0 0秒以下の結晶性のものが形成できる。 上記薄 SIS 3 4、 薄 Jffl 3 5— 1及び 麵 3 5 - 2は通常すベて単結晶状態であることが好ましいが、 薄麵 3 5— 2及ぴ薦麵 3 4力 層以 上からなる場合 2層のうち電極接続用のコンタクト層のほうは必ずしも単結晶状態でなぐ 無 定形、 多結晶、 配向性多結晶の結晶状態であってもよい。
また、 図 5 1〜図 5 3に例示する薄 電性材料が形成された窒化アルミニウムを主成分と する焼結体からなる基板を用いて作製される発光 の発光効率 ttil常 8 %以上であり、 サフ アイァなどの基板を用いて作製される«からの発光素子の発光効率よりすぐれている。 図 5 4〜図 5 6は、 導通ビア 3を有する窒化アルミニウムを主成分とする焼結体からなる基 板 1 0に図 5 1〜図 5 3で示した薄膜導電性材料 1 1を形成したものを発光素子作製用基板 3 0として用いて作製される本発明による発光素子の例を示す断面図である。 図 5 4〜図 5 6に おいて導通ビア 3を形成することの効果は図 4 7〜図 4 9で例示した発光素子と同様で薄 3 4の一部をエッチングなどに取り除いて電極を形成する必要がなく上下に電極を配置した発 光素子が作製できる。 さらに薄^電性材料 1 1を形成することで該薄 電性材料の上に形 成される発光素子のバッファ層 3 1 mmm 3 4及び発光層 3 6との電気的接続が向上し易 くなるといった ¾1果もある。
図 5 4は、 導通ビア 3を有する窒化アルミニウムを主成分とする焼結体からなる基板 1 0に 薄]^電性材料 1 1を形成したものをそのまま発光素子作製用基板 3 0として用いて作製され る本発明による発光素子の 1例を示したものである。
図 5 5は、 導通ビア 3を有する窒化アルミニウムを主成分とする焼結体からなる基板 1 0に 薄麟電性材料 1 1を形成し、 その上に図 4 3、 図 4 8及び図 5 2と同様の窒化ガリウム、 窒 化インジウム、 窒化アルミニウムのうちから選ばれた少なくとも 1種以上を主成分とする薄膜 を少なくとも 1層形成したものを発光素子作製用基板 3 0として用いて作製される本発明によ る発光素子の 1例を示したものである。
図 5 6は、 導通ビア 3を有する窒化アルミニウムを主成分とする焼結体からなる基板 1 0に 薄! ^電性材料 1 1を形成し、 その上に図 4 4、 図 4 9、 図 5 0及び図 5 3と同様、 窒化ガリ ゥム、 窒化インジウム、 窒化アルミニウムのうちから選ばれた少なくとも 1種以上を主成分と する薄膜を少なくとも 1層形成し、 その上にさらに窒化ガリウム、 窒化インジウム、 窒化アル ミニゥムのうちから選ばれた少なくとも 1種以上を主成分とする薄膜を形成した少なくとも薄 膜 2層が形成されたものを発光素子作製用基板 3 0として用いて作製される本発明による発光 素子の 1例を示したものである。
図 5 4〜図 5 6で例示する発光素子において、 m mm i ιを反射部材として用いた 場合の効果については図 5 1で例示した発光素子と同様である。
図 5 4〜図 5 6で例示した薄膜導電性材料が形成された導通ビアを有する窒化アルミニウム を主成分とする焼結体からなる基板を用いて作製される本発明による発光素子において薄膜層
3 4、 m 3 5— 1、 薄 us 3 5 - 2及び発光層 3 6はそれぞれ通常発光素子の発光効率を 高めるためにェピタキシャル成長した単結晶として形成できる。 その結晶性は該薄膜のミラ一 指数 (0 0 2) の格子面の X線回折ロッキングカーブの半値幅が 3 6 0 0秒以下、 通常 3 0 0 秒以下、 さらに 1 0 0秒以下の結晶性のものが形成できる。 上記薄膜層 3 4、 薄膜層 3 5—1 及ぴ臂膜層 3 5 - 2は通常すベて単結晶状態であることが好ましいが、 薄膜層 3 5 - 2 mm 膜層 3 4が 2層以上からなる場合 2層のうち電極接続用のコンタクト層のほうは必ずしも単結 晶状態でなく、 無定形、 多結晶、 配向性多結晶の結晶状態であってもよい。
また、 図 5 4〜図 5 6で例示する薄膜導電性材料が形成された導通ビアを有する窒化アルミ 二ゥムを主成分とする焼結体からなる基板を用いて作製される発光素子の発光効率は通常 8 % 以上であり、 サファイアなどの基板を用いて作製される従来からの発光素子の発光効率よりす ぐれている。
また、 本発明においては図 5 1〜図 5 6に示される上記薄 電性材料が形成された窒化ァ ルミ二ゥムを主成分とする焼結体からなる基板に代えて、 該薄 電性材料が形成された炭化 珪素、 窒化珪素、 窒化ガリウム、 謝匕亜鉛、 酸化ベリリウムなどの六方晶結晶系及び 化アル ミニゥムなどの三方晶結晶系あるいは六方晶系として分類できる結晶構造を有する各種セラミ ック材料を主成分とする焼結体、 及びその他酸化ジルコニウム、 酸化マグネシウム、 アルミン 酸マグネシウム、 酸化チタン、 チタン酸バリウム、 チタン酸ジルコン麵、 酸化イットリウム などの希土 «化物、 酸ィ匕トリウム、 各種フェライト、 ムライト、 フォルステライト、 ステア タイト、 結晶化ガラス、 など各種セラミック材料を主成分とする焼結体からなる基板を用いて 発光素子を作製することができる。 このような窒化アルミニウムを主成分とする焼結体以外の セラミック材料を主成分とする焼結体からなる基板を用いて作製される発光素子も該薄^ »電 性材料を反射部材として用いることで発光素子からの発光 «S板側からは放出されにくくなり、 該基板より上の方向から素子外部へ放出され易くなるので例えぱ面発光レーザ一あるいは平板 状ディスプレイに用いる発光ダイォードなど発光の方向性制御が要求される発光素子が作製し 得る。
図 5 7は、 図 4 4で示す本発明による発光素子において薄膜層 3 4が薄膜層 3 4 - 1 MM 膜層 3 4— 2の 2層で形成された例を示す断面図である。 薄膜層 3 4 - 2は通常電極 3 8と接 続されるコンタクト層として用いられる。 図 5 7で例示する構成からなる発光素子はダブルへ テロ構造あるいは単一量子井戸構造あるいは多重量子井戸構造などの発光素子として作製し得 る。 ダカレへテロ構造の発光素子の場合薄顧 3 4—1は薄藤 3 5—1とともに発光層 3 6 を挟むクラッド層として用いられる。 また、 図 5 7で例示する構成からなる発光素子が単一量 子井戸構造の発光素子として作製される場合、 該薄薩 3 4 - 1は井戸層として機能する発光 層 3 6の障壁層として用いられる。
図 5 8は、 図 5 7で示す本発明による発光素子において薄膜層 3 4—1が薄膜層 3 4 - 1 - 1及び育 J3U13 4— 1— 2の 2層で形成され、 さらに薄 HS 3 5—1が薄膜層 3 5—1— 1及 ぴ¾膜層 3 5— 1— 2の 2層で形成された例を示す断面図である。 図 5 8で例示する構成から なる発光素子は N型及び P型半導体特性を有するクラッド層がそれぞれ 2層ずつ形成されたダ カレへテロ構造あるいは単一量子井戸構造あるいは多重量子井戸構造などの発光素子として作 製し得る。 ダカレへテロ構造の発光素子の場合薄麵 3 4—1— 1及ぴ 膜層 3 4— 1— 2は 薄膜層 3 5— 1一 1及ぴ 膜層 3 5— 1—2とともに発光層 3 6を挟むクラッド層として用い られる。 また、 図 5 8で例示する構成からなる発光素子が単一量子井戸構造の発光軒として 作製される場合、 該薄膜層 3 4 - 1 - 1 mmm 3 5 - 1 - 1は井戸層として機能する発光 層 3 6の障壁層として用いられる。
また、 図 5 8で示すような多層構成のェピタキシャル成長した窒化ガリウム、 窒化インジゥ
ム、 窒化アルミニウムのうちから選ばれた少なくとも 1種以上を主成分とする薄膜からなる発 光 は発光層として井戸層と障壁層をそれぞ'れ多層積層した多重量子井戸層構造のレーザー ' ダイ才ードとして作製することができる。
本発明において発光素子は窒化ガリウム、 窒化インジウム、 窒化アルミニウムのうちから選 ばれた少なくとも 1種以上を主成分とするェピタキシャル成長した薄膜状の少なくとも N型半 導体層、 発光層、 P型半導体層の 3層以上の積層により構成されている。 また発光素子の外形 の大きさは 0. 0 5 mm角〜 1 Omm角程度、 通常は 0. 1 mm角〜 3 mm角程度の範囲であ り発光素子を構成する各薄 S Sの厚みはそれぞれの薄 Milで異なりそれぞれは 0. 0 0 5 zm 〜2 0 /im程度の範囲であるが各薄膜層が多層化され発光素子となった状態では合計するとそ の厚みは 0. 5 m〜 5 0 m程度で通常は 1 i m〜 2 0 m程度の範囲である。 通常発光素 子の発光層は面形状であり該発光層から発せられた光は 0. 5 xm〜5 0 / m程度の g離をお いて垂直に対峙する基板面に照射されるものと思われる。 この様子を図 5 9及び図 6 0で模式 的に示す。 図 5 9は図 4 2に示されている発光素子の発光層から発せられる光の放出状況を推 測し模式的に記入した断面図である。 図 6 0は図 4 5示されるように斜視図として描かれてい る発光素子の発光層から発せられる光の放出状況を搬則し模式的に記入したものである。 図 5 9及び図 6 0において発光素子 3 9の発光層 3 6は通常面状に形成されており発光層 3 6から 発せられた光 1 4 0は垂直に対峙するセラミックを主成分とする焼結体からなる基板 4の表面 に対して一部 斜め方向から照射されると思われる。 このとき基板 4が仮にサファイアであれ ば基板 4の上に形成される薄膜層 3 1 (あるいは薄麵 3 4) と基板 4との界面 1 5 0におい て発光層 3 6から発せられた光 1 4 0の多くは反射されて薄 あるいは発光層に戻って薄膜 層 3 1、 薄麵3 4、 薄翻 3 5— 1、 薄 ES 3 5— 2あるいは発光層 3 6に閉じ込められて 発光素子の外部へは放出されず発光層から発せられる光は主に薄 3 5 - 2からその一部だ けが素子外部へ放出光 1 4 2として放出される。 そのため発光効率が低いものと思われる。 そ れに対して基板 4が本発明による窒化アルミニウムを主成分とする焼結体、 あるいは炭化珪素、 窒化珪素、 窒化ガリウム、 酸化ベリリウム、 酸化亜鉛、 酸化アルミニウムなど六方晶系又は三 方晶系の結晶構造を有するセラミック材料を主成分とする焼結体、 あるいはその他各種セラミ ック材料からなる焼結体であれば獰膜層 3 1 (あるいは薄膜層 3 4) と基板 3 0との界面 1 5 0において発光層 3 6から発せられた光 1 4 0の多くは反射されず、 さらに基板 4が ¾¾M性 を有している場合は該基板を透過して発光素子の外部へ放出光 1 4 1として放出される。 その 他に発光層から発せられる光の一部は薄 HJ13 5— 2のほうから放出光 1 4 2として、 また一 部は発光層の側面から放出光 1 4 3として素子外部へ放出される。 したがってこのようなセラ ミックを主成分とする焼結体からなる基板を用いて作製した発光素子の発光効率はサフアイァ 基板を用いた場合に比べて高くなると思われる。
このような現象は図 4 3及び図 4 4に例示されるようなセラミックを主成分とする焼結体か らなる基板 4の上に薄膜 5の薄膜 1層あるいは薄膜 5及び 膜 8の薄膜 2層が形成されたもの であってもセラミックを主成分とする焼結体からなる基板 4と薄膜 5との界面で生じるものと 推測される。 すなわち、 上記図 4 3及び図 4 4に例示されるようなセラミックを主成分とする 焼結体からなる基板 4の上に薄膜が少なくとも 1層あるいは 2層以上形成されたものを基板と して用いて作製される発光素子であっても、 発光効率は図 4 2に例示される該薄膜が形成され ていないものと同様 «からのサファイアなどを基板として用いて作製される発光素子の発光 効率と同等、 あるいは 2〜 3倍以上、 あるいは 3〜4倍以上、 あるいは最大 4〜 5倍以上にな るものと推測される。
その他、本発明による電極を広い面積にわたって形成した発光素子の例として図 6 1を示す。 図 6 1は図 4 4で断面図として示されている本発明による発光素子を斜めから見た様子の 1例
を示す斜視図である。 図 6 1は従来からのサファイアなどの基板に代えてセラミック材料を主 成分とする焼結体からなる基板の上に窒化ガリウム、 窒化インジウム、 窒化アルミニウムのう ちから選ばれた少なくとも 1種以上を主成分とする薄膜を少なくとも 2層形成したものを発光 ^作製用基板として用いた例として示されている。 図 6 1において薄膜層 3 4の隅の一部を エッチングなどで取り除いて電極 3 8が帯状に広く形成されている様子が示されている。 もう 一方の電極 3 8は薄膜層 3 5 - 2の上に広い面積にわたって形成されている。 このような広い 電極を用いることにより大きな電流が低損失で発光層に供給し易くなるという利点がある。 広 い面積の電極を用いて発光素子を作製する場合、 発光層からの発光が電極によってできるだけ 遮断されないように透明電極あるいは ½¾ 性の電極を用いることが好ましい。 該透明電極あ るいは光 ¾i性の電極は少なくとも発光素子から発せられる光に対して透明あるいは ¾¾性 を有するものを用いることが好ましい。 したがって電極としては少なくとも波長 5 5 0 nm以 下の光に対して透明であるかあるいは光 ¾ 性を有する導電性材料を用いることが好ましい。 また、 電極として金属や合金など通常では光を透過しにくい材料を用いる場合厚みを少なくと も 1 0 0 nm以下、 好ましくは 1 0 nm以下とし透明性あるいは光 性を発現させることが 好ましい。 さらに上記の広い面積で形成された電極への電力供給を高めるために別に導電性に 優れた材料などを用いて電力供給用 3 8一 1を電極上に設けることも効果がある。
本発明による発光素子の発光効率は上記のように、 各種セラミック材料を主成分とする 結 体からなる基板にあらかじめ形成される窒化ガリウム、 窒化インジウム、 窒化アルミニウムの うちから選ばれた少なくとも 1種以上を主成分とする薄膜の有無あるいは該薄膜の結晶状態に よって影響される。 さらに、 本発明による発光 の発光効率 板として用いられる各種セ ラミック材料からなる焼結体の材質 (主成分)、 組成、 , «ί 性、 焼結体結晶粒子の大き さ、導通ビアの有無、各種セラミック材料からなる ¾結体を基板基板としたときの表面平滑性、 該基板の厚み、 などによっても影響を受けるが、 少なくとも ¾έ¾からのサファイアなどを基板 として用いて作製される発光素子の発光効率と同等、 あるいは 2〜3倍以上、 あるいは 3〜4 倍以上、 あるいは最大 4〜 5倍以上のものが提供できる。
このように本発明により従来からサファイア基板や L i N b〇3基板などを用いて作製され る光導波路よりも紫外線の伝還員失が少なレ洸導波路が提供できるようになった。 また、 « からのサフアイァなどの単結晶基板を用いて作製される発光 ¾ よりも発光効率の優れた発光 素子が提供できるようになつた。
それが実現できた要因は均質な単結晶基板でなく各種セラミック材料を主成分とする結晶粒 子や粒界あるいは添加物などによる粒界相などからなる焼結体を基板として用いその上に窒化 ガリウム、 窒化インジウム、 窒化アルミニウムのうちから選ばれた少なくとも 1種以上を主成 分とする結晶性の高い単結晶薄膜が形成できたことであると思える。 また、 該単結晶薄膜を含 め窒化ガリウム、 窒化インジウム、 窒化アルミニウムのうちから選ばれた少なくとも 1種以上 を主成分とする薄膜と基板との間あるいは該薄膜間に高い接合性が実現されたことも大きな要 因と思える。 このような焼結体として窒化アルミニウムを主成分とするもの、 あるいは炭化珪 素、 窒化珪素、 窒化ガリウム、 酸化ベリリウム、 酸化亜鉛、 酸化アルミニウムなど 7^晶系又 は三方晶系の結晶構造を有する各種セラミック材料を主成分とするものが好適に使用できる。 またその他酸化ジルコニウム、 酸化マグネシウム、 アルミン酸マグネシウム、 酸化チタン、 チ タン酸バリウム、 チタン酸ジルコン酸鉛、 酸ィ匕イットリウム、 酸ィ匕トリウム、 フェライト、 ム ライト、 フォルステライト、 結晶化ガラス、 など各種セラミック材料を主成分とする焼結体な どからなる基板を用いても発光効率に優れた発光素子を作製し得る。 発光素子作製用基板とし て上記各焼結体の中で窒化アルミニウムを主成分とするものがより優れた発光効率を有するの で好ましい。 また、 光導波路においても窒化アルミニウムを主成分とする焼結体からなる基板
を用いること力 S好ましい。
以上説明してきた上記各種セラミック材料からなる焼結体を用いた基板に形成する単結晶薄 膜の結晶性に与える要因をまとめうと以下の通りである。
( 1 ) セラミックの材質 (窒化アルミニウムを主成分とする焼結体か、 あるいは炭化珪素、 窒 化珪素、 窒化ガリウム、 酸化亜鉛、 酸化ベリリウムなどの六方晶系及び 化アルミニウムなど の三方晶系あるいは六方晶系として分類できる結晶構造を有する各種セラミツク材料を主成分 とする焼結体か、 基本的主成分の相違)
( 2 ) セラミックの組成 (主成分の續及び含有量、 添加物あるいは不純物の含有量、 など)
( 3 ) セラミックの 過性
(4) セラミック立子の大きさ
( 5 ) セラミックの密度
(6 ) セラミックの厚み
( 7 ) セラミックの焼成条件
( 8 ) 基板の表面平滑性
( 9) 薄膜の構成 (単一層、 あるいは 2層以上の多層構成か、 など)
( 1 0 ) あらかじめ基板に形成する薄膜の結晶状態
( 1 1 ) 薄膜の厚み
( 1 2) 薄膜の形成条件 (MO CVD法、 クロライド VP E法などのハライド VP E法あるい はスパッタリング法などの薄膜形成方法、 基板温度、 など)
また、 セラミック基板に形成される薄膜の結晶性にあまり影響を与えなにくい因子としては 以下の点が挙げられる。
( 1 3 ) 焼結体中に導通ビアを有しているかどうか (焼結体中に導通ビアが形成されているか どうかにかかわらず、 該焼結体からなる基板には比較的結晶性の優れた薄膜が形成できる)
( 1 4) 薄膜の組成 (窒化ガリウム、 窒化インジウム、 窒化アルミニウムのうちから選ばれた 少なくとも 1種以上を主成分とする組成であればどのような組み合わせであっても比較的結晶 性の優れた薄膜が形成可能である。 また薄膜中に各種ドーピング成分を含んでいるものであつ ても比較的結晶性の優れた薄膜が形成可能である。)
本発明による窒化アルミニウムを主成分とする焼結体からなる基板上あるいは窒化アルミ二 ゥムを主成分とする焼結体を使用した薄膜形成用基板及び ¾膜基板に形成される窒化ガリゥム、 窒化インジウム、 窒化アルミニウムのうちから選ばれた少なくとも 1種以上を主成分とする無 定形、 多結晶、 配向性多結晶、 単結晶など各種結晶状態の薄膜はフィールドェミッション材料 及び冷陰極としても用いることができる。 これは窒化アルミニウムを主成分とする焼結体とい う «では窒化ガリウム、 窒化インジウム、 窒化アルミニウムのうちから選ばれた少なくとも
1種以上を主成分とする無定形、 多結晶、 配向性多結晶、 単結晶など各種結晶状態の薄膜と格 子齡しないと思われていた基板上に窒化ガリウム、 窒化インジウム、 窒化アルミニウムのう ちから選ばれた少なくとも 1種以上を主成分とする単結晶薄膜のミラ一指数 ( 0 0 2 ) の格子 面の X線回折ロッキングカーブの半値幅が 3 0 0秒以下と良好な結晶性を有する単結晶薄膜が 形成できたことによる寄与があってはじめて実現できた。 フィールドエミッション材料あるい は冷陰極の性能は蛍光体を発光させたとこの輝度が高いほどディスプレイに用いたときには優 れるが、 本発明においては上記単結晶を含む各種結晶状態の薄膜のうち窒化アルミニウム及び 窒化アルミニウムを主成分とする無定形、 多結晶、 配向性多結晶、 単結晶など各種結晶状態の 薄膜をフィールドエミッション材料あるいは冷 |¾®を用いたときカラー蛍光体を発色させたと きの輝度は 1 0 0 0カンデラ Zm2以上の高い値が得られ易い。本発明による上記無定形、多結 晶、 配向性多結晶、 単結晶など各種結晶状態の薄膜をフィールドェミッション材料あるいは冷
陰極として用いる場合は該無定形、 多結晶、 配向性多結晶、 単結晶など各種結晶状態の薄膜を S i、 Oなどをドーピングし N型半導体化しておくことが電子を放出し易くする上で好ましい。 本発明において窒化ガリウム、 窒化インジウム、 窒化アルミニウムのうちから選ばれた少なく とも 1種以上を主成分とする無定形、 多結晶、 配向性多結晶、 単結晶など各種結晶状態の薄膜 からなるフィ一ルドエミッション材料あるいは冷 I ®は窒化アルミニウムを主成分とする焼結 体からなる基板上に形成されるので少なくとも 1 0インチ以上の大型サイズでコスト的にも安 価なディスプレイの実現が可能となり産業上の効果が大きい。
本発明は上記のように、 窒化ガリウム、 窒化インジウム、 窒化アルミニウムのうちから選ば れた少なくとも 1種以上を主成分とする単結晶あるいは無定形、 多結晶、 配向性多結晶など各 種結晶状態の薄膜を形成するための基板であって、 該基板が窒化アルミニウムを主成分とする 焼結体であることを體とする薄 »成用基板、 であるが、 さらに窒化アルミニウムを主成分 とする焼結体に窒化ガリウム、 窒化インジウム、 窒化アルミニウムのうちから選ばれた少なく とも 1種以上を主成分とする薄膜が形成されていることを特徴とする薄膜基板、 も含まれる。 該薄膜基板は上記窒化ガリウム、 窒化インジウム、 窒化アルミニウムのうちから選ばれた少な くとも 1種以上を主成分とする発光素子形成用基板として删できる他に窒化ガリウム、 窒化 ィンジゥム、 窒化アルミニウムのうちから選ばれた少なくとも 1種以上を主成分とする単結晶 あるいは無定形、 多結晶、 配向性多結晶など各種結晶状態の薄膜を表面弾性波素子用材料とし て用いた基板、 あるいは窒化ガリウム、 窒化インジウム、 窒化アルミニウムのうちから選ばれ た少なくとも 1種以上を主成分とする単結晶薄膜を誘電体材料 · «材料として用いた回路基 板、 あるいは窒化ガリウム、 窒化インジウム、 窒化アルミニウムのうちから選ばれた少なくと も 1種以上を主成分とする単結晶薄膜を光導波路として用いた基板、 などに使用もできる。 また、 本発明は上記のような単結晶など各種結晶状態の薄膜が形成し得る薄膜形成用基板及 び単結晶など各種結晶状態の薄膜が形成された薄膜基板以外にも、 たとえば含有成分を揮散 ·
|5^¾、 低減化する方法により製造される高 «化され A 1 N«の高い窒化アルミニウムを主 成分とする焼結体も含まれる。 このような焼結体を基板として用いることでより特性の優れた 窒化ガリウム、 窒化インジウム、 窒化アルミニウムのうちから選ばれた少なくとも 1種以上を 主成分とする単結晶をはじめ無定形、 多結晶、 配向性多結晶など各種結晶状態の薄膜が形成し 得る。
実施例 1
セラミック原料粉末として窒化アルミニウム (A 1 N)、 炭化珪素 (S i C)、 窒化珪素 (S i 3N4)、 酸化アルミニウム (A 1 203)、 酸化ジルコニウム (Z r 02)、 酸化疆 (Z n〇)、 酸化マグネシウム (Mg〇)、 酸化ベリリウム (B e〇)、 アルミン酸マグネシウム (MgA l 2 04 :スピネル) の高純度でサブミクロン粒子からなるものを用意した。窒化アルミニウム粉末 は徳山曹達株式会社 (現:株式会社トクャマ) 製 「F」 グレード、 炭化珪素粉末は 島電工 株式会社製 「OY—1 5」 グレード、 窒化珪 ¾ ^末は宇部興産株式会社製 「S N_ E 0 5」 グ レード、 アルミナはィ拔化学株式会社製 「AK P— 3 0」 グレード、 酸化ジルコニウムは安定 化剤として Y203を 3モル%含む東ソー株式会社製部分安定化ジルコニァ 「Τ Ζ— 3 Υ」 ダレ ード、 酸化 Ηま堺化学工業株式会社製「1種」 銘柄、 酸化マグネシウムは関東化学株式会社 製の特級匪粉末、 酸化べリリゥム及びスピネルは株式会社高 |¾¾化^ ^所製の粉末を用い た。 渡は部分安定化ジルコニァを除いて主成分 9 9重量%以上である。 上記窒化アルミニゥ ム粉末には主成分の A 1 N以外に主要不純物として分析の結果酸素が 1 . 0重量%含まれる。前 記原料粉末の!^において窒化アルミニウム粉末の場合は酸素を除いた成分における A 1 Nの 繊である。炭化珪纖末には B 4 C粉末 1. 0重量%とカーボン粉末 1 . 0重量%を加え、 窒 化珪¾ ^末には Y203粉末 2. 0重量%と Α 1 203粉末 2. 0重量%を加え、 酸ィ匕ベリリウム
粉末には C aCO 3粉末 1. 8重量%加えエタノールを溶媒にポールミルで 24時間湿式混合後、 乾燥してエタノールを揮散させた。 これら草 後の混^ ^末にパラフィンワックスを 5重量% 加え成形用粉末を作製し、 該粉末を圧力 50 OKg/cm2で一軸プレス成形し直径 25. 4m mx厚み 1. 5 mm及び ¾:径 32mm X厚み 1. 5 mmの円盤状成形体を得た。 これら成形体 を 300°Cで減圧脱脂後表 1に示す焼成条件で焼成し焼結体を得た。 焼成後の各焼結体の相対 密度はいずれも 99%以上であった。 得られたこれらの焼結体表面を酸化クロム及びアルミナ 研 を用いて鏡面研磨した後アセトンで超音波洗浄し、 薄膜形成用の基板を作製した。 得ら れた各基板の表面粗さを表 1に示した。 次にこの薄膜作製用基板の構成相を X線回折により調 ベた。 その結果窒化アルミニウム粉末を原料として得られた焼結体の示す X線回折パターンは J CPDSファイル番号 25-1133に記載されている結晶相すなわち A IN (Hexag ona l) を主相とするものであった。 炭化珪素を原料として得られた焼結体の示す X線回折 パターンは上記ファイル番号 29-1131に記載されている《— S i C (Hex agon a 1) を主相とするものであった。 窒化珪素を原料として得られた焼結体の示す X線回折パター ンは上記フアイル番号 33-1160に記載されている 3— S i3N4 (Hexagona l) を主相としその他 6. 6 %の不明相からなるものであった。 酸化アルミニウムを原料として得 られた焼結体の示す X線回折パターンは上記フアイル番号 10-173に記載されている a - A 1203 (Tr i gona l) を主相とするものであった。 酸化ジルコニウムを原料として得 られた焼結体の示す X線回折パターンは上記ファイル番号 17— 923に記載されている Z r 〇2 (Te t ragona l) を主相とするものであった。酸化 βを原料として得られた焼結 体の示す X線回折パターンは上記ファイル番号 36-1451に記載されている Ζ η 0 (He xagona 1) を主相とするものであった。 酸化マグネシウムを原料として得られた焼結体 の示す X線回折パターンは上記ファイル番号 4— 829に記載されている Mg〇 (Cub i c) を主相とするものであった。 酸化ベリリウムを原料として得られた焼結体の示す X線回折パ夕 ーンは上記ファイル番号 35-818に記載されている B eO (Hexagona l) を主相 とするものであった。 アルミン酸マグネシウムを原料として得られた焼結体の示す X線回折パ ターンは上記ファイル番号 21— 1152に記載されている MgA 12〇4 (Cub i c) を主 相とするものであった。 又得られたこれら焼結体は明らかに焼結体内部の主成分結晶粒子の方 位があらゆる方向を向いた多結晶体であった。 薄膜作翻基板の X線回折による相構成の結果 について表 1に示した。 次に得られた各基板を用い高周波加熱による MOCVD (有機金属化
^ ^m 装置により窒化ガリウム、 窒化インジウム、 窒化アルミニウム薄膜を基板表 面に直接形成した。 すなわち、 作製した基板を上記装置の反応容器に入れまず水素ガスを流し ながら 1000 で加熱した。その後薄膜作製用原料としてトリメチルガリウム (TMG)、 ト リメチルインジウム (TMI)、 トリメチルアルミニウム (TMA) を用い、 水素あるいは窒素 +水素をキヤリァガスとして上記各 3種類の液体原料中に導入してバブリングさせ、 それぞれ の原料をアンモニアガスとともに高周波加熱による反応部に送り、 窒化ガリウム (GaN) 薄 臌堪板 1000 、 窒化インジウム (I nN) 薄膜は 700 、 窒化アルミニウム (A 1 N) 薄膜は 11001:、 50モル% GaN+50モル% A 1 Nの混晶薄膜は 1050 °Cで形 成した。 薄膜の形成速度はそれぞれ 0. 2〜0. 4 imZ時間、 0. 2〜0. 5 xm/時間、 l〜3 mZ時間、 0. 5〜; L. 5 z/m/時間、 程度である。 形成した各薄膜の厚みは 0. 2 5 mである。 なお窒化アルミニウムを主成分とする焼結体からなる基板に形成する窒化アル ミニゥム薄膜の場合だけ厚み 3 m、 及び 6 /mのものを作製した。 得られた各薄膜の観察を 光学顕微鏡、 電子顕纖を用いて行ったが薄膜内部にはクラックが見られず薄膜と窒化アルミ 二ゥムを主成分とする焼結体及びその他の各種セラミック材料を主成分とする焼結体との接合 界面での剥離も見られない。 得られた各薄膜に粘着テープを接着し引き剥がしテストを行った
が窒化アルミニウムを主成分とする焼結体及びその他の各種セラミック材料を主成分とする焼 結体と薄膜とは界面で剥離するものはなぐ 窒化アルミニウムを主成分とする焼結体及びその 他の各種セラミック材料を主成分とする纖吉体と薄膜とは強固に接合している。 また、 形成さ れた上記各薄膜に T i,P t,Auの薄騰電性材料を形成して金属リードをはんだ付けし垂 直引張り強度を調べたがすべて 2 K g/mm2以上であり窒化アルミニウムを主成分とする焼 結体及びその他の各種セラミック材料を主成分とする焼結体と上記各薄膜とは強固に接合して いる。 薄膜形成後 CuKa線を用いて各薄膜の X線回折パターンを測定して薄膜の結晶状態を 調べ、 さらに各薄膜のミラー指数 (002) 格子面の X線回折ロッキング力一ブをとりその半 値幅を測定した。 窒化アルミニウムを主成分とする焼結体からなる基板に形成された厚み 0. 25 mの窒化アルミニウム薄膜の場合だけ電子線回折を行いその薄膜の結晶状態を調べた。 その結果を表 1に示す。 表 1において各薄膜の X線回折パターン測定の結果酸化ジルコニウム 及び ¾化マグネシウム及びスピネルを主成分とする焼結体からなる基板上に直接形成されたも のは単結晶化しないことが示されている。 それはミラー指数 (002) 格子面からだけでなく (100) 格子面からの回折線が出現していることから多結晶であることは自明である。 それ 以外の焼結体基板上に形成した薄膜はミラ一指数 (002) 格子面からだけの回折線だけしか 出現せず単結晶化している。 されたまたこの単結晶化した薄膜のミラー指数 (002) 格子面 のロッキングカーブの半値幅はいずれの基板においても 3600秒以下であった。 また、 これ ら単結晶薄膜の基板に対する形 位は薄膜が単結晶化したすべての焼結体において該単結晶 薄膜の C軸が基板面に対して垂直の方向であった。 この実験結果から薄膜が単結晶化しなかつ た原因は酸化ジルコニウムの結晶系は正方晶 (Te t r agona l) であり、 酸化マグネシ ゥムとスピネルは立方晶 (Cub i c) であるためと思われる。 その他の基板の主成分は酸化 アルミニウムを除いてすベて六方晶 (Hexagona l) である。 前記酸化アルミニウムの 結晶系は三方晶 (Tr i gona l) であるが六方晶としての分類も可能であるのでその上に 直接形成される薄膜が単結晶化するのは本質的には六方晶及び六方晶として分類できる材料を 主成分とする焼結体からなる基板の場合だけであると思われる。 また、 実験結果から明らかな ように直接その上に形成した薄膜が単結晶化した基板の中で窒化アルミニウムを主成分とする 焼結体からなる基板は特に優れている。 形成された殆どすベての薄膜でミラー指数 (002) 格子面の X線回折ロッキングカーブの半値幅が 300秒以下とシャープで結晶性に優れている。 上記のように各種セラミツク材料を主成分とする焼結体を基板としても窒化ガリゥム、 窒化 インジウム、 窒化アルミニウムを主成分のうちから選ばれた少なくとも 1種以上を主成分とす る単結晶薄膜が該焼結体製基板に直接形成し得ることが ϋかめられた。 その中でも窒化アルミ 二ゥムを主成分とする焼結体を用いて作製される単結晶薄膜の結晶性が最も優れていた。
実施例 2
次に、 窒化アルミニウムを主成分とする焼結体からなる基板上に直接形成される窒化ガリウ ム、 窒化インジウム、 窒化アルミニウムのうちから選ばれた少なくとも 1種以上を主成分とす る単結晶薄膜の結晶性に対して窒化アルミニウムを主成分とする焼結体の組成や焼結体の微構 造、 耀過率などの特性による影響を調べた。 実験に用いた焼結体作製用原料粉末は実施例 1 で翻したのと同じ高繊窒化アルミニウム粉末 〔徳山曹難式会社(現:株式会社トクャマ) 製 「F」 グレード〕 を用意した。 この原料粉末は酸化物 法にて製造されたものである。 こ の原料粉末に戯焼結助剤などの添加物や黒色化剤などを加えエタノールとともにポ一ルミル で 24時間混合後乾燥しエタノールを揮散した後パラフィンワックスを粉末混合体に対して 5 重量%加え成形用粉末を作製し、 直径 25. 4 mm X厚み 1. 5 mm及び直径 32 mm X厚み 1. 5 mmの円形粉末成形体を一軸プレス成形により得た。 その後減圧下 300°Cでパラフィ ンワックスを脱脂し、 焼成用治具として夕ングステン製のセッターを使用して S¾性雰囲気に
ならないよう純窒素雰囲気中で被焼成物である粉末成形体の周囲をタングステン製の枠で囲ん で常圧焼成、 雰囲気加圧焼成 (ガス圧 戈) を行ない各 化アルミニウムを主成分とする焼 結体を作製した。 また、 ホットプレス、 H I P (ホットアイソスタチックプレス:静水圧加圧 焼結) により各種窒化アルミニウムを主成分とする焼結体も作製した。 舰条件の詳細は表 2 に記載されている。 得られた焼結体を直径 2 5. 4mmX厚み 0. 5 mmの寸法に研削、 及び 研磨加工し窒化アルミニウムを主成分とする焼結体からなる基板を作製した。 なお、 得られた 各種窒化アルミニゥム焼結体中には原料粉末中の酸素などの不可避混入成分や希土観素化合 物、 アルカリ土類金属化合物などの焼結助剤、 アルカリ金属、 珪素成分、 モリブデン、 夕ング ステン、 ニオブ、 チタン、 力一ボン、 鉄、 ニッケルなどの成分は殆ど揮散 '随されないで粉 末成形体中とほぼ同量存在している。
このようにして得られた各種基板を用い実施例 1と同様の高周波加熱による MO CVD (有 機金属化学細適) 装置を用いた方法により窒化ガリウム、 窒化インジウム、 窒化アルミ二 ゥムを主成分とする薄膜を基板表面に形成した。 なお、 5 0モル%G a N + 5 0モル% I nN の混晶薄膜 板 8 O t:で形成した。 得られた薄膜は C u K a特性 X線を用いた X線回 折パターン及び電 回折の測定結果すベて単結晶であると認められる。 得られた単結晶薄膜 の観察を光学顕微鏡、 電子顕微鏡を用いて行つたが 結晶薄膜内部にはクラックが見られず単 結晶薄膜と窒化アルミニウムを主成分とする焼結体との接合界面での剥離も見られない。 得ら れた上記単結晶薄膜に粘着テープを接着し引き剥がしテストを行ったが該単結晶薄膜と窒化ァ ルミ二ゥムを主成分とする焼結体との接合界面での剥離や破壊は見られなかった。 また、 形成 された上記各単結晶薄膜に T i /P t /Auの薄騰電性材料を形成して金属リードをはんだ 付けし垂直弓 I張り強度を調べたがすべて 2 K g /mm2以上であり窒化アルミ二ゥムを主成分 とする焼結体と上記各単結晶薄膜とは強固に接合している。
次いでミラ一指数 (0 0 2 ) 格子面の X線回折ロッキング力一ブの半値幅を測定し前記単結晶 薄膜の結晶性を調べた。 これら単結晶薄膜の基板に対する形^位はすべて該単結晶薄膜の C 軸が基板面に対して垂直の方向であつた。
これらの結果を表 2及び表 3に示した。 表 2には試験に供した窒化アルミニウムを主成分と する焼結体からなる基板の作製条件及び基板の特性を示した。 表 3には上記窒化アルミニウム を主成分とする焼結体からなる各種基板を用い、 この基板に形成した窒化ガリウム、 窒化イン ジゥム、 窒化アルミニウムを主成分のうちから選ばれた少なくとも 1種以上を主成分とする単 結晶薄膜の組成、 ,及び結晶性について示した。
表 2及び表 3において窒化アルミニウムを主成分とする焼結体の光 ¾1率 1 %以上の基板を 用いることで直接その上に形成された窒化ガリウム、 窒化インジウム、 窒化アルミニウムのう ちから選ばれた少なくとも 1種以上を主成分とする単結晶薄膜の結晶性はミラー指数 (0 0 2) の格子面の X線回折ロッキングカーブの半値幅が 3 0 0秒以下であることが示されている。 光 透過率が 5 %以上の焼結体では該単結晶薄膜の ( 0 0 2 ) 格子面の X線回折ロッキングカーブ の半値幅が 2 4 0秒以下である。 過率が 1 0 %以上の窒化アルミニウムを主成分とする焼 結体では該単結晶薄膜の (0 0 2 ) 格子面の X線回折ロッキングカーブの半値幅が 2 0 0秒以 下である。 また、 光透過率が 4 0 %以上の窒化アルミニウムを主成分とする焼結体では該単結 晶薄膜の (0 0 2 ) 格子面の X線回折ロッキングカーブの半値幅が 1 5 0秒以下である。 なお、 光麵率の測定は日立製作所製の分光光度計 U— 4 0 0 0を用い積分球内に作製した 窒化アルミニウムを主成分とする基板を入れ該焼結体に入射する光の強度と透過する光をすベ て集めてその強度を測定し、 と入射光との弓艘の百分率比を算出して光 ¾i率とした。 また、 光透過率の値は波長 6 0 5 nmの光に対して測定されたものである。
表 2及び表 3において焼結体中の希土類 素及びアル力リ土類金属の含有量が 化物換算で
それぞれ 25髓%以下の基板では直接その上に形成された窒化ガリウム、 窒化インジウム、 窒化アルミニウムのうちから選ばれた少なくとも 1種以上を主成分とする単結晶薄膜の結晶性 はミラー指数(002)の格子面の X線回折ロッキングカーブの半値幅が 300秒以下である。 また含有量がそれぞれ 12体積%以下の焼結体では該単結晶薄膜の (002) 格子面の X線回 折 CIッキングカーブの半値幅が 240秒以下である。 含有量がそれぞれ 7髓%以下の窒化ァ ルミ二ゥムを主成分とする焼結体では該単結晶薄膜の (002) 格子面の X線回折ロッキング カーブの半値幅が 200秒以下である。
表 2において実験 No. 34、 45、 49、 50、 58、 66で棚した単結晶薄膜を形成 していない窒化アルミニウムを主成分とする焼結体の X線回折において、 実験 No. 34の焼 結体は J CPDSファイル番号 25—1134で示される主相の多結晶 A 1Nと J CPDSフ アイル番号 36— 50で示される多結晶 AL ONの回折線であり、 No. 45では異相は検出 されず J CPDSファイル番号 25— 1134で示される多結晶 A 1 Nの回折線だけであった. が、 No. 49の基板の場合は上記 A 1 Nのほかに YA 1〇3及び Y4A 12〇9の回折線が検出 され、 No. 50の基板の場合は上記 A 1 Nのほかに YA 103及び Y4A 12〇9及び Y2〇3の 回折線が検出され Ν ο . 58の基板の場合は上記 A 1 Nのほかに E r A 103及び E r 4 A 12 09の回折線が検出され、 No. 66の基板の ±給は上記 A INのほかに W (タングステン) の 回折線が検出された。 なお、 No. 34の焼結体中の AL〇Nの含有量は A 1 Nと AL ONの 回折線の最強線ピーク比で計算すると 1. 4%と算定された。 又実験 No.' 37〜40で使用 した単結晶薄膜を形成していない窒化アルミニウムを主成分とする焼結体の X線回折を行うと
J C P D Sフアイル番号 25-1134で示される多結晶 A 1 Nの回折線のほか J C P D Sフ アイル番号 36— 50で示される多結晶 AL ONの回折線が検出された。 AL ONの最強線(3 11) と A 1Nの最強線 (100) の強度比から求めた焼結体中の A L ON含有量はそれぞれ No. 37で 3. 2%、 No. 38で 9. 6%、 No. 39で 19. 1 %、 No. 40で 29.
4%と算出された。
表 2及び表 3においてアル力リ金属あるいは珪素化合物を含有する実験 N o.61、 62、 6 3の窒化アルミニウムを主成分とする焼結体からなる基板上に直接形成された窒化ガリゥム及 び窒化アルミニウム単結晶薄膜の結晶性は (002) 格子面の X線回折ロッキングカーブの半 値幅が 300秒以下である。
表 2及び表 3において実験 No. 65、 66、 68、 70の窒化アルミニウムを主成分とす る焼結体の波長 605 nmの光に対して測定された光透過率 (^i 率) を示すが該光透過率 は 1%より小さく実験 No. 65、 68、 70の焼結体はゼロであるがこれらの基板上に直接 形成された窒化ガリウム及び窒化アルミニウム単結晶薄膜の結晶性は (002) 格子面の X線 回折ロッキングカーブの半値幅が 300秒以下である。
表 2及び表 3において実験に用いた全酸素量が 10重量%以下の窒化アルミニウムを主成分 とする焼結体からなる基板はその上に直接形成される窒化ガリウム、 窒化インジウム、 窒化ァ ルミニゥムのうちから選ばれた少なくとも 1種以上を主成分とする単結晶薄膜のミラー指数
(002) の格子面の X線回折ロッキングカーブの半値幅が 300秒以下である。 全酸素量が 5. 0重量%以下の焼結体で窒化ガリウム、 窒化インジウム、 窒化アルミニウムのうちから選 ばれた少なくとも 1種以上を主成分とする単結晶薄膜のミラー指数 (002) の格子面の X線 回折ロッキングカーブの半値幅は 240秒以下である。 また全酸素量が 3. 0重量%以下の焼 結体で窒化ガリゥム、 窒化ィンジゥム、 窒化アルミニゥムのうちから選ばれた少なくとも 1種 以上を主成分とする単結晶薄膜のミラー指数 (002) の格子面の X線回折ロッキング力一ブ の半値幅が 200秒以下である。
表 2及び表 3において実験に用いた窒化アルミニウムを主成分とする焼結体中の A L 0 N量
が 2 0 %以下の基板はその上に直接形成される窒化ガリウム、 窒化インジウム、 窒化アルミ二 ゥムのうちから選ばれた少なくとも 1種以上を主成分とする単結晶薄膜のミラー指数 ( 0 0 2) の格子面の X線回折ロッキング力一プの半値幅が 3 0 0秒以下である。 また AL ON量が 7 % 以下の焼結体で窒化ガリウム、 窒化インジウム、 窒化アルミニウムのうちから選ばれた少なく とも 1種以上を主成分とする単結晶薄膜のミラ一指数 (0 0 2) の格子面の X線回折ロッキン ダカ一ブの半値幅が 2 0 0秒以下である。
表 2及び表 3において窒化アルミニウムを主成分とする焼結体の相対密度 9 8 %以上の基板 上に直接形成された窒化ガリウム、 窒化インジウム、 窒化アルミニウムのうちから選ばれた少 なくとも 1種以上を主成分とする単結晶薄膜の結晶性は該単結晶薄膜のミラー指数 (0 0 2 ) の格子面の X線ロッキングカーブの半値幅が 3 0 0秒以下であることが示されている。 焼結体 の相対密度 9 9 %以上では該単結晶薄膜のミラ一指数 ( 0 0 2) の格子面の X線ロッキング力 ープの半値幅は 2 4 0秒以下である。 また、 焼結体の相対密度 9 9. 5 %以上で該単結晶薄膜 のミラ一指数 (0 0 2 ) の格子面の X線ロッキングカーブの半値幅は 2 0 0秒以下である。 表 2及び表 3において実験に用いた焼結体中の気孔の大きさは平均 1 m以下で窒化ガリゥ ム、 窒化インジウム、 窒化アルミニウムのうちから選ばれた少なくとも 1種以上を主成分とす る単結晶薄膜の結晶性は該単結晶薄膜のミラー指数 ( 0 0 2) の格子面の X線ロッキング力一 ブの半値幅が 3 0 0秒以下である。 焼結体中の気孔の大きさが平均 0. 7 m以下では該単結 晶薄膜のミラ一指数 ( 0 0 2) の格子面の X線ロッキング力一ブの半値幅は 2 4 0秒以下であ る。 また、 焼結体中の気孔の大きさが平均 0. 5 m以下では該単結晶薄膜のミラー指数 ( 0 0 2 ) の格子面の X線ロッキングカーブの半値幅は 2 0 0秒以下である。
表 2及び表 3において、 舰 が高く又舰時間が長くなれば窒化アルミニウムを主成分 とする焼結体中の A 1 N結晶粒子の大きさは増大する傾向がある。 すなわち 1 9 0 0 °C以上の Stで 3時間以上の «で焼結体中の A 1 N結晶立子の大きさは 8 m以上となる。 又 1 9 0 0 °C以上の温度で 6時間以上の焼成で焼結体中の A 1 N結晶粒子の大きさは 1 5 m以上とな る。 実験に用いた窒化アルミニウムを主成分とする焼結体の A 1 N結晶粒子の大きさは平均 1 m以上で窒化ガリウム、 窒化インジウム、 窒化アルミニウムのうちから選ばれた少なくとも 1種以上を主成分とする単結晶薄膜の結晶性は該単結晶薄膜のミラー指数 ( 0 0 2 ) の格子面 の X線ロッキングカーブの半値幅が 3 0 0秒以下である。 焼結体の A 1 N結晶粒子の大きさが 平均 5 m以上では該単結晶薄膜のミラー指数 (0 0 2 ) の格子面の X線ロッキングカーブの 半値幅は 2 4 0秒以下である。 また、 焼結体の A 1 N結晶粒子の大きさが平均 8 m以上では 該単結晶薄膜のミラ一指数 ( 0 0 2 ) の格子面の X線ロッキングカーブの半値幅は 2 0 0秒以 下である。 また、 焼結体の A 1 N結晶粒子の大きさが平均 1 5 以上では該単結晶薄膜のミ ラー指数 (0 0 2) の格子面の X線ロッキングカーブの半値幅は 1 5 0秒以下のものが得られ る。 なお A 1 N含有量が 8 0体積%より少ない焼結体においては形成される単結晶薄膜の結晶 性が低下するものが見られる。
表 2及び表 3において実験に用いた窒化アルミ二ゥムを主成分とする焼結体の表面平滑度が 平均表面粗さ R a 1 0 0 n m以下の基板はその上に直接形成される窒化ガリゥム、 窒化ィンジ ゥム、 窒化アルミニウムのうちから選ばれた少なくとも 1種以上を主成分とする単結晶薄膜の ミラー指数 (0 0 2 ) の格子面の X線回折ロッキングカーブの半値幅が 3 0 0秒以下である。 実施例 3
窒化アルミ二ゥムを主成分とする焼結体作製用原料粉末として高繊窒化アルミニゥム粉末 〔徳山曹達株式会社 (現:株式会社トクャマ) 製 「H」 グレード〕 を用意した。 この原料粉末 は酸化物 ii¾法にて製造されたものである。 この原料粉末は酸素を 1 . 3重量%不純物として 含む。 この原料粉末に舰 Υ203粉末を 3. 3髓%加えたもの、 E r 203粉末を 4. 0 2体
積%加えたもの、 及び CaC〇3粉末を CaO換算で 0. 6体積%加えたものをトルエンおよび イソプロピルアルコールとともにポールミルで 24時間混合後アクリルバインダーを粉末原料 100重量部に対して 12重量部加えさらに 12時間混合することでペースト化しドクターブ レード法で厚み 0. 75 mmの 3種類の組成を有するグリ一ンシ一トを作製した。 このダリ一 ンシ一トから一辺 35 mmの正方形状のシートを作製しこのシ一トに Y AGレーザ一で表裏面 を貫通する直径 25 m、 50 zm、 250 zm及び 500 mの円形スルーホールを形成し た。 次に溶媒としてひテルピネオール、 ノイング一としてアクリル樹脂を加え導電性成分とし て純タングステン、 50体積%タングステン + 50体積%銅の混合粉末および純銅粉末の 3種 類の粉末を用いて導通ビア用べ一ストを作製して上記のスルーホール内に充填し、 乾燥後、 適 宜窒素又は窒素/水素混合ガスを主成分とする雰囲気中で脱バインダー後 N2中 1820°Cで 2時間常 j«成し導通ビアが内部に形成された窒化アルミニウムを主成分とする焼結体を得た。 なお、 焼成に際しては被焼成物であるスルーホールに導通ビアペーストが充填されたグリーン シートの脱脂物をタングステン製セッターに置き碰舰物とは別に窒化アルミニウム粉末成 形体を同時に置き周囲を夕ングステンの枠で囲んで行つた。 スルーホ一ル内の金属成分は焼結 あるいは溶融凝固により十分緻密化し導電性が発現しており窒化アルミニウムを主成分とする 焼結体とも一体化しており、 導通ビアとして機能している。 得られた焼結体を直径 25. 4m mx厚み 0. 5 mmの寸法に研削、 及び鏡面研磨加工して導通ビアを露出させ表面平滑度 R a =26 nmの導通ビアを有する窒化アルミニウムを主成分とする焼結体からなる基板を作製し た。 その後導通ビアの室温における抵抗を 4端子法で測定し導通ビアの形状から室温における 氐抗率を算出した。 導通ビアの大きさは; «後収縮しそれぞれ直径 20〜23 ΐη, 40〜4 4 m、 209〜215 及び 422 mになっていた。 また上記導通ビアが形成された基 板上に直接実施例 1及び 2で用いたものと同じ MOCVD装置を用いた方法で窒化ガリゥムの 単結晶薄膜を 0. 25 mの厚みで基板の片面に形成した後該単結晶薄膜のミラ一指数 ( 00 2) 格子面の X線回折ロッキングカーブの半値幅を測定した。 それらの結果を表 4に示した。 単結晶薄膜形成後導通ビアが形成されている周囲の単結晶薄膜について観察を行ったがクラッ クゃ導通ビアとの界面における剥離などの不具合は特に見当たらず良好な外観状態であり本発 明による材料を用いた導通ピアは窒化ガリゥム薄膜と良好な接合性を有していることが ¾認さ れた。 該単結晶薄膜のミラー指数 (002) 格子面の X線回折ロッキング力一ブの半値幅はす ベて 300秒以下であり、 導通ビアの室温における抵抗率は 2. 0X 10"6Ω - cm~7. 7 X 10—6Ω · cmの範囲であった。 本実施例において作製した窒化ガリウムを主成分とする薄 膜は導電性を有する。 さらに導通ビアが形成されている各焼結体を用いて作製した該窒化ガリ ゥムを主成分とする薄膜と該薄膜が形成されていない基板面側に露出している導通ビアとの間 には導通がある。 このように本実施例で作製した導電性を有する窒化ガリゥムを主成分とする 単結晶薄膜と導通ビアとは機械的な接合性だけでなく電気的にも接続されていることが萑認さ れた。
実施例 4
実施例 3で作製したグリーンシートから一辺 35 mmの正方形状のシートを作製し空気中 5 00°Cで脱バインダー後、 窒素中 1800°Cで 1時間常圧焼成し窒化アルミニウムを主成分と する焼結体を得た。 得られた焼結体を一辺 25. 4mmX厚み 0. 5 mmの正方形に研削、 及 磨加工し表面平滑度 R a = 25 nmの窒化アルミニウムを主成分とする焼結体からなる基 板を作製した。次に実施例 1及び 2で用いたものと同じ MOCVD装置を用いて窒化ガリゥム、 窒化ィンジゥム、窒化アルミニゥムのうちから選ばれた少なくとも 1種以上を主成分とする 0. 7 nm〜4200 nmの各種厚みの薄膜を基板上に直接形成した。 なお、 50モル% I nN + 50モル%A 1 Nの混晶薄膜 «¾板 820°Cで形成した。 このようにして得られた実験 N
o. 90の 100%窒化アルミニウムを除く薄膜の CuK αによる X線回折パターンを取った がすべてミラー指数 (002) の格子面からの回折線であり単結晶化していた。 なお 100 % 窒化アルミニウム薄膜は電 泉回折で調べたがこれもミラ一指数 (002) の格子面からの回 折だけでミラー指数 (100) の格子面からの回折は見られず単結晶化している。 次に得られ た単結晶薄膜のミラー指数(002)格子面の X線回折ロッキングカーブの半値幅を測定した。 その結果を表 5に示した。 単結晶薄膜の厚みにおいてミラ一指数 (002) 格子面の X線回折 ロッキングカーブの半値幅は 300秒以下である。
実施例 5
窒化アルミニウムを主成分とする焼結体作製用原料粉末として実施例 1、 2、 3で用いた 2 種類の酸化アルミニウムの ¾法による原料のほかにアルミニウム金属の直接窒化法により作 製された 2種類の窒化アルミニウム粉末(東洋アルミニウム株式会社製「TOYALNITE」 及びドイツ S t are k社製「G r a d e Bj) を用意した。 これらの原料のうちアルミニゥ ム金属の直接窒化法により作製された原料粉末は 2種類それぞ 虫で、 また酸化アルミニゥ ムの還元法によるものはアルミニゥム金属の直接窒化法により作製された原料とそれぞれ 50 重量%ずつ混合したものを実施例 1と同様の方法で成形、 脱脂を行った後窒素中 1950°CX 2時間、 30 OKgZcm2でホットプレスを行い窒化アルミニウムを主成分とする 6種類の焼 結体を得た。 得られた焼結体を直径 25. 4mmX厚み 0. 5 mmの寸法に研削、 及 Ό¾Τ磨加 ェし表面平滑度 Ra = 27 nmの窒化アルミニウムを主成分とする焼結体からなる基板を作製 した。 X線回折により原料に 「TOYALNITE」 だけを用いた焼結体は主相が A 1 Nでそ の他 1. 6%の ALONが検出される。 また原料に 「Gr ade B」 だけを用いた焼結体は 主相が A 1 Nでその他 2. 2 %の AL ONが検出される。 又酸化アルミニウムの還元法による ものとアルミニゥム金属の直接窒化法により作製された原料との混合原料から作製された焼結 体も同様主相は A 1 Nであり 1. 2〜: 1. 9%の ALONを含む。 これら 6種類の焼結体の相 対密度はすべて 98%以上である。 又気孔率はすべて 1%以下であった。 次に実施例 1及び 2 で用いたものと同じ MOCVD装置を用いて窒化ガリウム、 窒化インジウム、 窒化アルミニゥ ムのうちから選ばれた少なくとも 1種以上を主成分とする厚み 0. 25 mの単結晶薄膜を基 板上に直接形成した。なお 100%窒化アルミニウムの単結晶薄膜は厚み 6 mmで形成した。 このようにして得られた単結晶薄膜のミラー指数 (002) 格子面の X線回折ロッキング力一 ブの半値幅を測定した。 その結果すベての単結晶薄膜においてミラー指数 (002) 格子面の X線回折ロッキングカーブの半値幅は 300秒以下であった。
実施例 6
実施例 2と同様の原料を用いて新たに常圧 «及びホットプレスによる窒化アルミニウムを 主成分とする焼結体からなる基板を作製し実施例 2と同様に基板の特性を調べさらにこれらの 基板に実施例 1及び実施例 2と同様に窒化ガリウム、 窒化インジウム、 窒化アルミニウムのう ちから選ばれた少なくとも 1種以上を主成分とする単結晶薄膜を形成しその結晶性を調べた。 窒化アルミニウムを主成分とする焼結体を作製するのに際して粉末成形体及び粉末成形体の脱 脂までは実施例 2と同様の方法により行った。 粉末成形体として焼結助剤などの添加物無しの もの、 また焼結助剤などの添加物として MgO、 CaC〇3、 Al2〇3、 Y2〇3、 Er2〇3、 V 2〇s、 Cr 203を用いた。 その詳細は表 6に記載した。 上記各種添加物を含む粉末成形体を脱 脂後、 該粉末成形体を被焼成物として焼成した。 該粉末成形体の焼成に際してタングステン製 のセッターを用い別に用意した窒化アルミニウム粉末だけからなる粉末成形体を該セッター内 に被 «物とともに置きこれらの周囲を夕ングステン製の枠で囲むか、 窒化アルミニゥム製の セッターを用い被; M物の周囲を窒化アルミニゥム製の枠で囲んで焼成を行つた。 常圧誠は 1気圧の N2中 1820°Cで 2時間の条件で行った。又ホットプレスに際しては粉末成形体をい
つたん上記のようにタングステンセッ夕一を用いて 1820°Cで 1時間窒素中で常圧焼成しい つたん焼結体としたものを用いて加圧焼成を行つた。
その結果を表 6に示す。 その結果、 得られた窒化アルミニウムを主成分とする焼結体の)1 έ¾ 過率はすべて 30%以上であった。 実施例 2で作製した添加物を含まないもの、 また添加物と して Mg〇、 CaC03、 Al2〇3、 Y203、 Ε r 2〇3を含む窒化アルミニウムを主成分とする 焼結体の光 率に比べて向上していることが確認された。 本実施例では実施例 2と比べて焼 成雰囲気中に窒化アルミニウム成分が被焼成物以外から供給されたため ¾¾i性がより向上し たものと思われる。 また表 6には記載していないが、 添加物として MgO、 V205、 C r203 を含む粉末成形体をいつたん焼成せずにそのまま窒素雰囲気中 1820°Cで 1時間、 圧力 30 OKgZcm2でホットプレスすることにより得られた窒化アルミニウムを主成分とする焼結 体の光透過率はすべて 0 %であった。
このようにして得られた各種窒化アルミニウムを主成分とする焼結体のうち光 ¾ 率 40 % 以上の窒化アルミニウムを主成分とする焼結体を基板として用いることで直接その上に形成さ れた窒化ガリウム、 窒化インジウム、 窒化アルミニウムのうちから選ばれた少なくとも 1種以 上を主成分とする単結晶薄膜の結晶性はミラー指数 (002) の格子面の X線回折ロッキング カーブの半値幅が 150秒以下であることが示されている。 光¾§率が 60%以上の焼結体で は該単結晶薄膜の (002) 格子面の X線回折ロッキングカーブの半値幅が 130秒以下であ る。 また可視光扁率ゼロの窒化アルミニウム焼結体からなる基板であってもそこに直接形成 される窒化ガリウム、 窒化インジウム、 窒化アルミニウムのうちから選ばれた少なくとも 1種 以上を主成分とする単結晶薄膜の結晶性はミラ一指数 (002) の格子面の X線回折ロッキン グカーブの半値幅が 200秒以下であることが示されている。
実施例 7
実施例 2及び 6において作製した窒化アルミニウムを主成分とする焼結体の波長 300謹 の光に対する光翻率を測定した。 測定は光が紫外線に代わった以外は実施例 2と同様の方法 で行った。 その結果を表 7に示す。 この結果は明らかに可視光¾1率の高い窒化アルミニゥム を主成分とする焼結体からなる基板は紫外光に対する透過率も高い傾向を有することが示され ている。 また、 300 n mの紫外光に対する光透過率は最大 67 %と高いものが得られる。 実施例 8
実施例 1〜 6において作製した窒化アルミ二ゥムを主成分とする焼結体、 及び実施例 1で作 製した炭化珪素、 窒化珪素、 酸化アルミニウム、 酸化亜鉛、 酸化ベリリウムめ各種セラミック 材料を主成分とする焼結体を用意した。 これらの基板の表面平滑性とそこに直接形成される窒 化ガリウム、 窒化インジウム、 窒化アルミニウムのうちから選ばれた少なくとも 1種以上を主 成分とする単結晶薄膜の結晶性との関係を調べた。 基板の表面平滑性は次の 3種類の状態のも のを用いた。 すなわち、 1) 基板表面が焼き放し (as— f i r e) 状態のもの (ただし、 表 面付着物をアルミナ粉を使いブラシで取り除く)、 2) S i Cあるいはアルミナ砥粒を用いてラ ッフ ¾ff磨により基板表面を研削加工した状態のもの、 3) アルミナ、 酸化セリウム、 ダイヤモ ンド、 酸化珪素あるいは酸化クロムを主成分とする研歸 Uを用いて基板表面を鏡面状に加工し た状態のもの、 である。 なお、 ラッフ ¾iF磨に用いた砥粒及びその は窒化アルミニウムを主 成分とする焼結体の場合実施例 1の実験 No. 1〜 5で作製し使用したもの、 実施例 2の実験 No. 62および 64で作製したものは S i Cの #240、 実施例 6の実験 No. 107で作 製したものは S i ( の# 280、 実施例 2の実験 No. 34および 46で作製したもの、 実施 例 4の実験 No. 86〜 92で作製し使用したもの、 実施例 4の実験 No. 100〜102で 作製し使用したものたもの、 実施例 6の実験 No. 105で作製したものは S i Cの #400 を用い、 その他の焼結体では S i Cの #600であった。 炭化珪素を主成分とする焼結体の場
合 S i Cの粒度 # 2 4 0の砥粒を用いた。 窒化珪素を主成分とする焼結体の場合 S i Cの粒度 # 8 0 0の砥粒を用いた。 酸化亜鉛を主成分とする焼結体の場合アルミナの米被 # 4 0 0の砥 粒を用いた。 また、 ラップ研磨を行った窒化アルミニウムを主成分とする焼結体及び窒化珪素 を主成分とする能結体は研肖咖工後 N
2中 1 2 0 0 °Cで 1時間加熱処理を行った。 ラッフ ¾ff磨を 行った炭化珪素を主成分とする焼結体は研削加工後アルゴン中 1 2 0 で 1時間加熱処理を 行った。 ラッフ ¥F磨を行った酸化碰を主成分とする焼結体は研削加工後大気中 1 0 0 0 °Cで 1時間加熱処理を行った。 また、 上記鏡面加工は市販の布製パッドをポリシヤーとして用い研 として以下のものをそれぞれ用いることにより行った。 すなわち、 窒化アルミニウムを主 成分とする焼結体からなる基板の鏡面研磨には粒径 0. 1
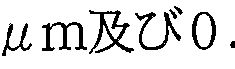
. 2 mの酸化クロムを 主成分とする研 »jを用いた。 炭化珪素を主成分とする焼結体からなる基板の鏡面研磨には粒 径 0. 1 /imのダイヤモンドを主成分とする研麟 j (鏡面 1 ) 及ぴ粒径 0. 0 5 mのコロイ ド状アルミナを主成分とする研 (鏡面 2) を用い、 窒化珪素を主成分とする焼結体からな る基板の鏡 S研磨には 径0. 2 5 mのダイヤモンドを主成分とする研磨剤 (鏡面 3 ) 及び 粒径 0. 0 5 mのコロイド状アルミナを主成分とする研 (鏡面 4) を用い、 酸化アルミ 二ゥムを主成分とする焼結体からなる基板の鏡面研磨に «¾径0. 1 mのダイヤモンドを主 成分とする研 »J (鏡面 5) MWm . 0 2 のコロイド状酸化珪素を主成分とする研磨 剤 (鏡面 6 ) を用い、 酸化亜鉛を主成分とする焼結体からなる基板の鏡画 if磨に〖 ±g0. 5 mの酸化セリウムを主成分とする研^ ij (鏡面 7 ) を用い、 酸化ベリリウムを主成分とする 焼結体からなる基板の鏡丽磨に «½0. 2 5 mのダイヤモンドを主成分とする研翻(鏡 面 8) 及びあ ϋ圣 0. 0 5 mのコロイド状のアルミナを主成分とする研^ (鏡面 9) を用い た。 なお表 8には記載していないが、 窒化アルミニウムを主成分とする焼結体からなる基板の 鏡面研磨に用いた酸化クロムを主成分とする研 «Jのうち粒径 0. 1 mのものを使用した基 板ではすべて表面粗さ R a 2 0 nm以下の表面平滑性を有するものが得られた (実験 N o . 1 9 8〜2 0 0及び実験 N o . 2 1 0〜2 1 1で用いた基 。その他の基板はすべて樹圣 0. 2 mの酸化クロムを主成分とする研 により鏡 磨を行った。 このようにして作製した上 記各基板の表面平滑性 (表面粗さ R aで示す) 及び基板の表面状態を表 8に示した。
上記のような表面状態を有する各基板をァセトン及び I P Aで超音波洗浄後に実施例 1及び 実施例 2と同様に窒化ガリウム、 窒化インジウム、 窒化アルミニウムのうちから選ばれた少な くとも 1種以上を主成分とする薄膜を表 8に示されている厚みで形成しその結晶性を調べた。 以上の実験結果を表 8に示す。 その結果窒化アルミニウムを主成分とする焼結体を用いた基板 においては焼き放し (a s— f i r e ) の状態であってもその表面には直接窒化ガリウム、 窒 化インジウム、 窒化アルミニウムのうちから選ばれた少なくとも 1種以上を主成分とする薄膜 が多結晶化することなく単結晶で形成できる。 また焼き放し (a s— f i r e ) 状態の窒化ァ ルミ二ゥムを主成分とする焼結体を用いた基板の表面平滑性は平均表面粗さ R aで 9 0〜: L 0 0 O nmの範囲にある。 窒化アルミニウムを主成分とする焼結体を用いた基板においては表面 をラップ研磨した状態のものであってもその表面には直接窒化ガリウム、 窒化インジウム、 窒 化アルミニウムのうちから選ばれた少なくとも 1種以上を主成分とする薄膜が多結晶化するこ となく単結晶で形成できる。 また表面をラッフ Iff磨した状態の窒化アルミ二ゥムを主成分とす る焼結体を用いた基板の表面平滑性は平均表面粗さ R aで 1 0 0〜2 0 0 0 nmの範囲にある。 窒化アルミニウムを主成分とする焼結体を用いた基板においては表面を鏡面研磨した状態のも のはその表面には直接窒化ガリウム、 窒化インジウム、 窒化アルミニウムのうちから選ばれた 少なくとも 1種以上を主成分とする薄膜が多結晶化することなく単結晶で形成できる。 また表 面を鏡面研磨した状態の窒化アルミニウムを主成分とする焼結体を用いた基板の表面平滑性は 平均表面粗さ R aで 1 0 0 nm以下の範囲にある。 本実施例の結果が表 8において示されてい
る。 すなわち窒化アルミニウムを主成分とする焼結体を用いた基板において基板の表面状態が 上記 3種類の中で鏡面研磨したものを用いることで基板に直接形成される窒化ガリゥム、 窒化 インジウム、 窒化アルミニウムのうちから選ばれた少なくとも 1種以上を主成分とする単結晶 薄膜はより結晶性のすぐれたものが得られ易いことが示された。 表 8において窒化アルミニゥ ムを主成分とする焼結体を用いた基板の平均表面粗さ R aが 2 0 0 0 nm以下のものには直接 窒化ガリゥム、 窒化ィンジゥム、 窒化アルミニゥムのうちから選ばれた少なくとも 1種以上を 主成分とする単結晶化した薄膜が形成でき該単結晶薄膜のミラー指数 ( 0 0 2 ) の格子面の X 線回折ロッキングカーブの半値幅が 3 6 0 0秒以下の単結晶薄膜が得られることが示されてい る。 窒化アルミニウムを主成分とする焼結体を用いた基板の中で平均表面粗さ R aが 1 0 0 0 nm以下のものには直接窒化ガリウム、 窒化インジウム、 窒化アルミニウムのうちから選ばれ た少なくとも 1種以上を主成分とする単結晶化した薄膜が形成でき該単結晶薄膜のミラ一指数
( 0 0 2) の格子面の X線回折ロッキングカーブの半値幅が 1 0 0 0秒以下の単結晶薄膜が得 られることが示されている。 窒化アルミニウムを主成分とする焼結体を用いた基板の中で平均 表面粗さ R aが 1 0 O nm以下のものには直接窒化ガリウム、 窒化インジウム、 窒化アルミ二 ゥムのうちから選ばれた少なくとも 1種以上を主成分とする単結晶化した薄膜が形成でき該単 結晶薄膜のミラ一指数 ( 0 0 2 ) の格子面の X線回折ロッキングカーブの半値幅が 3 0 0秒以 下の単結晶薄膜が得られることが示されている。 窒化アルミニウムを主成分とする焼結体を用 いた基板の中で平均表面粗さ R aが 6 0 nm以下のものには直接窒化ガリゥム、 窒化ィンジゥ ム、 窒化アルミニウムのうちから選ばれた少なくとも 1種以上を主成分とする単結晶化した薄 膜が形成でき該単結晶薄膜のミラー指数 ( 0 0 2 ) の格子面の X線回折ロッキングカーブの半 値幅が 2 4 0秒以下の単結晶薄膜が得られることが示されている。 窒化アルミニウムを主成分 とする焼結体を用いた基板の中で平均表面粗さ R aが 3 0 nm以下のものには直接窒化ガリゥ ム、 窒化インジウム、 窒化ァリレミニゥムのうちから選ばれた少なくとも 1種以上を主成分とす る単結晶化した薄膜が形成でき該単結晶薄膜のミラ一指数 (0 0 2 ) の格子面の X線回折ロッ キングカーブの半値幅が 2 0 0秒以下の単結晶薄膜が得られることが示されている。 また窒化 アルミニウムを主成分とする焼結体を用いた基板の中で平均表面粗さ R aが 2 0 nm以下のも のには直接窒化ガリウム、 窒化インジウム、 窒化アルミニウムのうちから選ばれた少なくとも
1種以上を主成分とする単結晶化した薄膜が形成でき該単結晶薄膜のミラ一指数 ( 0 0 2 ) の 格子面の X線回折ロッキングカーブの半値幅が 1 5 0秒以下の単結晶薄膜が得られることが示 されている。
表 8において窒化アルミニウムを主成分とする焼結体を用いた基板において基板の表面状態 が上記焼き放し (a s— f i r e)、 ラップ研磨、 鏡藤 if磨という 3種類の中で鏡面研磨したも のを用いることで基板に直接形成される窒化ガリウム、 窒化インジウム、 窒化アルミニウムの うちから選ばれた少なくとも 1種以上を主成分とする単結晶薄膜はより結晶性のすぐれたもの が得られ易いことが示された。 また焼き放し状態の表面状態を有する基板とラッフ Iff磨した表 面状態を有する基板とを比^ Tると焼き放し状態の表面状態を有する基板の方がそこに直接形 成される上記単結晶は結晶性のすぐれたものが得られ易いことが示された。
窒化アルミニウム以外の各種セラミック材料を主成分とする焼結体を用いた基板においては 焼き放しの状態であってもその表面には直接窒化ガリウム、 窒化インジウム、 窒化アルミニゥ ムのうちから選ばれた少なくとも 1種以上を主成分とする薄膜が多結晶化することなく単結晶 で形成できる。 また焼き放し状態の窒化アルミニゥム以外の各種セラミックを主成分とする焼 結体を用いた基板の表面平滑性は平均表面粗さ R aで 9 0〜: L 0 0 0 nmの範囲にある。 窒化 アルミニウム以外の各種セラミックを主成分とする焼結体を用いた基板においては表面をラッ フ¾?磨した状態のものであってもその表面には直接窒化ガリウム、 窒化インジウム、 窒化アル
ミニゥムのうちから選ばれた少なくとも 1種以上を主成分とする薄膜が多結晶化することなく 単結晶で形成できる。 また表面をラッフ研磨した状態の窒化アルミニウム以外の各種セラミッ クを主成分とする焼結体を用いた基板の表面平滑性は平均表面粗さ R aで 8 0〜1 0 0 O nm の範囲にある。 窒化アルミニウム以外の各種セラミックを主成分とする焼結体を用いた基板に おいては表面を鏡丽磨した状態のものはその表面には直接窒化ガリゥム、 窒化ィンジゥム、 窒化アルミニウムのうちから選ばれた少なくとも 1種以上を主成分とする薄膜が多結晶化する ことなく単結晶で形成できる。 また表面を鏡面研磨した状態の窒化アルミニゥム以外の各種セ ラミックを主成分とする焼結体を用いた基板の表面平滑性は平均表面粗さ R aで 1〜1 0 O n mの範囲にある。 表 8において窒化アルミニウム以外の各種セラミックを主成分とする焼結体 を用いた基板の平均表面粗さ R aが 1 0 0 O nm以下のものには直接窒化ガリウム、 窒化イン ジゥム、 窒化アルミニウムのうちから選ばれた少なくとも 1種以上を主成分とする単結晶化し た薄膜が形成でき該単結晶薄膜のミラー指数 ( 0 0 2 ) の格子面の X線回折ロッキングカーブ の半値幅が 3 6 0 0秒以下の単結晶薄膜が得られることが示されている。 窆化アルミニウム以 外の各種セラミックを主成分とする焼結体を用いた基板の中で平均表面粗さ R aが 1 0 0 nm 以下のものには直接窒化ガリウム、 窒化インジウム、 窒化アルミニウムのうちから選ばれた少 なくとも 1種以上を主成分とする単結晶化した薄膜が形成でき該単結晶薄膜のミラー指数 ( 0 0 2 ) の格子面の X線回折ロッキングカーブの半値幅が 1 0 0 0秒以下の単結晶薄膜が得られ ることが示されている。 窒化アルミニウム以外の各種セラミックを主成分とする焼結体を用い た基板の中で平均表面粗さ R aが 1 O nm以下のものには直接窒化ガリウム、窒化インジウム、 窒化アルミニウムのうちから選ばれた少なくとも 1種以上を主成分とする単結晶化した薄膜が 形成でき該単結晶薄膜のミラー指数 (0 0 2) の格子面の X線回折ロッキングカーブの半値幅 が 3 0 0秒以下の単結晶薄膜が得られることが示されている。 窒化アルミニウム以外の各種セ ラミックを主成分とする焼結体を用いた基板の中で平均表面粗さ R aが 5 nm以下のものには 直接窒化ガリウム、 窒化インジウム、 窒化アルミニウムのうちから選ばれた少なくとも 1種以 上を主成分とする単結晶化した薄膜が形成でき該単結晶薄膜のミラー指数 ( 0 0 2 ) の格子面 の X線回折ロッキングカーブの半値幅が 2 4 0秒以下の単結晶薄膜が得られることが示されて いる。
実施例 9
実施例 1〜 6において作製した窒化アルミ二ゥムを主成分とする焼結体、 及び実施例 1で作 製した炭化珪素、 窒化珪素、 酸ィ匕アレミ二ゥム、 酸化 «、 酸化ベリリウムの各種セラミック 材料を主成分とする焼結体を用意した。 これらの基板に対して実施例 1及び実施例 2と同様の 方法により窒化ガリウム、 窒化インジウム、 窒化アルミニウムのうちから選ばれた少なくとも 1種以上を主成分とする単結晶薄膜を直接形成し該単結晶薄膜形成後の厚みと形成された該単 結晶薄膜の結晶性との関係を調べた。 使用した窒化アルミニウム及び各種セラミック材料を主 成分とする焼結体製基板の表面はあらかじめ実施例 8と同様の方法により鏡丽磨してあり、 その表面粗さは表 9に示す通りである。 本実施例で用いた酸化亜鉛を主成分とする焼結体から なる基板は粒径 0. 2 mの酸化セリウムを主成分とする研麟[1を用いて研磨を行ったもので ある。 なお、 本実施例においては実施例 1で示した MO CVD法による成膜条件を変え窒化ガ リウム(G a N)薄膜で《S板 fig l 0 5 0 °C、窒化インジウム(I n N)薄膜では 6 5 0 °C、 窒化アルミニウム (A 1 N) 薄膜では 1 2 0 0 °C、 5 0モル%G a N+ 5 0モル%A 1 Nの混 晶薄膜は 1 1 0 0 °Cで形成した。 薄膜の形成速度はそれぞれ 0. 5〜1 . 5 m/時間、 0. 5〜1 . 5 mZ時間、 2〜6 mZ時間、 :!〜 3 /im/時間、 程度である。 またあらたに、 塩化ガリウム、 塩化インジウム、 塩化アルミニウムを原料に用いたクロライド VP E (塩化物 気相ェピタキシャル成長) 法による窒化ガリウム、 窒化インジウム、 窒化アルミニウムを主成
分とする単結晶薄膜の作製も行った。 気体化した原料のキャリアガスとして窒素、 反応ガスに はアンモニアを用いた。 成膜速度は 1時間あたり 5 m〜2 0 0 xmと急速成膜が可能であつ た。 このクロライド VP E法による単結晶薄膜は実験 N o. 1 9 3、 1 9 5、 1 9 7、 2 0 0、 2 0 2、 2 0 3、 2 0 9、 2 1 0、 2 1 1、 2 1 3、 2 1 5、 2 1 7、 2 2 2で用いた基板上 に形成した。 クロライド VP E法による単結晶薄 «成時の基板 は窒化ガリウム薄膜では 1 1 5 0 °C、 窒化インジウム薄膜では 8 0 0 :、 窒化アルミニウム薄膜では 1 2 8 0°Cで行つ た。 反応チャンノ一として 管を用レ ^外部から高周波により力一ポンセッターを加熱してそ の上に置いた窒化アルミニゥム及び各種セラミック材料を主成分とする焼結体からなる基板を 間接的に加熱する方法により行った。 その結果を表 9に示す。 表 9の結果は明らかに本発明に よる窒化アルミニウムを主成分とする焼結体からなる基板に直接形成された窒化ガリゥム、 窒 化インジウム、 窒化アルミニウムのうちから選ばれた少なくとも 1種以上を主成分とする単結 晶薄膜の結晶性は該単結晶薄膜の厚みが 0. 3 m以上で該窒化ガリウム、 窒化ィンジゥム、 窒化アルミニウムのうちから選ばれた少なくとも 1種以上を主成分とする単結晶薄膜のミラ一 指数 (0 0 2) の格子面の X線回折ロッキングカーブの半値幅が 2 4 0秒以下であることを示 している。 また窒化アルミニウムを主成分とする焼結体からなる基板に直接形成された窒化ガ リウム、 窒化インジウム、 窒化アルミニウムのうちから選ばれた少なくとも 1種以上を主成分 とする単結晶薄膜の結晶性は該単結晶薄膜の厚みが 3. 5 m以上で聽化ガリウム、 窒化ィ ンジゥム、 窒化アルミニウムのうちから選ばれた少なくとも 1種以上を主成分とする単結晶薄 膜のミラー指数 (0 0 2 ) の格子面の X線回折ロッキングカーブの半値幅が 2 0 0秒以下であ ることを示している。 また窒化アルミニウムを主成分とする焼結体からなる基板に直接形成さ れた窒化ガリウム、 窒化インジウム、 窒化アルミニウムのうちから選ばれた少なくとも 1種以 上を主成分とする単結晶薄膜の結晶性は該単結晶薄膜の厚みが 1 0 m以上で該窒化ガリウム、 窒化インジウム、 窒化アルミニウムのうちから選ばれた少なくとも 1種以上を主成分とする単 結晶薄膜のミラー指数 ( 0 0 2 ) の格子面の X線回折ロッキングカーブの半値幅が 1 5 0秒以 下であることを示している。 さらに窒化アルミニウムを主成分とする焼結体からなる基板に直 接形成された窒化ガリウム、 窒化インジウム、 窒化アルミニウムのうちから選ばれた少なくと も 1種以上を主成分とする単結晶薄膜の結晶性は該単結晶薄膜の厚みが 5 0 m以上で該窒化 ガリウム、 窒化インジウム、 窒化アルミニウムのうちから選ばれた少なくとも 1種以上を主成 分とする単結晶薄膜のミラ一指数 (0 0 2 ) の格子面の X線回折ロッキングカーブの半値幅が 1 3 0秒以下であることを示している。
また上記単結晶薄膜形成法においてクロライド VP E法を用いて 5 O O m〜; L O O O m 程度までの厚い薄膜が形成し得ることが ϋ認された。 これはおそらく基板として用いた窒化ァ ルミ二ゥムを主成分とする焼結体が比較的高い光 性を有しているためであろうと思われる。 表 9には示されていないが別に実施例 2の実験 N o . 6 5、 6 8、 及び 7 0で作製した光透過 性に乏しい窒化アルミニウムを主成分とする焼結体からなる基板を用いて上記と同じ条件のク 口ライド VP E法で窒化アルミニウムを主成分とする厚み 5 0 0 m〜l 0 0 0 / mの薄膜の 形成を試みたが、 結晶性はミラー指数 ( 0 0 2) の格子面の; 線回折ロッキングカーブの半値 幅が 1 3 0秒以下と比較的優れている一方該薄膜中にはクラックが見られ、 また基板との間に 剥離も見られた。
また、 上記クロライド V P E法を用いて窒化アルミニウムを主成分とする焼結体からなる基 板^ J として 8 0 0°C及び 9 0 0 °Cで窒化アルミニウムを主成分とする薄膜の形成を試みたが 単結晶化した窒化アルミニウムを主成分とする薄膜は形成できず、 すべて無定形、 多結晶、 あ るいは配向性多結晶などの結晶状態の薄膜であった。 クロライド VP E法により窒化アルミ二 ゥムを主成分とする焼結体からなる基板に窒化アルミニウムを主成分とする単結晶薄膜を形成
する場合基板 ¾を適正に設定することが必要であることが確認された。
一方窒化アルミニウム以外の炭化珪素、 窒化珪素、 酸化亜鉛、 酸化ベリリウム及び酸化アル ミ二ゥムを主成分とするセラミック材料からなる焼結体を用いた基板の場合そこに直接形成さ れた窒化ガリゥム、 窒化ィンジゥム、 窒化アルミニゥムのうちから選ばれた少なくとも 1種以 上を主成分とする単結晶薄膜の厚みが 0. 3 m以上でも該単結晶薄膜の結晶性は良好である ことが示された。 すなわち、 上記窒化アルミニウム以外の炭化珪素、 窒化珪素、 酸化 «、 酸 化ベリリゥム及び酸化アルミニウムを主成分とするセラミック材料からなる焼結体を用いた基 板に直接形成された窒化ガリウム、 窒化インジウム、 窒化アルミニウムのうちから選ばれた少 なくとも 1種以上を主成分とする厚み 0. 3 m以上の単結晶薄膜のミラー指数 (002) の 格子面の X線回折ロッキングカーブの半値幅は 300秒以下であることが示されている。 また、 厚み 3. 5 m以上の単結晶薄膜のミラ一指数 (002) の格子面の X線回折ロッキングカー ブの半値幅は 240秒以下であることが示されている。 さらに、 厚み 10 /zm以上の単結晶薄 膜のミラ一指数 (002) の格子面の X線回折ロッキングカーブの半値幅も 240秒以下であ ることが示されている。
表 9に示された薄膜の観察を光学顕«、 電子顕微鏡を用いて行ったが MOCVD法及びク 口ライド V P E法いずれの方法で作製された薄膜内部にはクラックが見られず ¾膜と窒化アル ミニゥムを主成分とする焼結体及びその他の各種セラミック材料を主成分とする焼結体との接 合界面での剥離も見られない。 得られた各薄膜に粘着テープを接着し引き剥がしテストを行つ たが窒化アルミニゥムを主成分とする焼結体及びその他の各種セラミック材料を主成分とする 焼結体と薄膜とは界面で剥離するものはなぐ 窒化アルミニウムを主成分とする焼結体及びそ の他の各種セラミック材料を主成分とする焼結体と薄膜とは強固に接合している。 また、 形成 された上記各薄膜に T iZP tZAuの薄 電性材料を形成して金属リードをはんだ付けし 垂直引張り強度を調べたがすべて 2 Kg/mm2以上であり窒ィ匕アルミニウムを主成分とする 焼結体及びその他の各種セラミック材料を主成分とする焼結体と上記各薄膜とは強固に接合し ている。
また、 実験 No. 191、 192、 193、 206、 208、 220で作製した薄膜を¾!圣 0. 2 mの酸化クロムを主成分とする研歸 IJを用いて研磨麦、 さらに ϋ圣 0. 02 mのコ ロイド状酸化珪素を主成分とする研鶴で鴒丽磨したところ表面粗さ(R a)がそれぞれ 1. 2nm (実験 No. 191)、 1. 04nm (実験 No. 192)、 0. 94nm (実験 No. 193)、 1. 1謹 (実験 No. 206)、 1. 06謹 (実験 No. 208)、 0. 99 nm (実験 N o. 220) とすべて 2 n m以下であり、 研磨することで平滑性の優れた単結晶薄膜 が形成された薄膜基板が得られること力 認された。
実施例 10
実施例 1〜 6において作製した窒化アルミ二ゥムを主成分とする焼結体、 Rzmmm ιで作 製した炭化珪素、 窒化珪素、 酸化アルミニウム、 酸化亜鉛、 酸化ベリリウムの各種セラミック 材料を主成分とする焼結体を用意した。 これらの基板表面は実施例 8及び実施例 9と同様の方 法で鏡面研磨が施されている。 これらの基板に対して基板 Jtを変えた以外は実施例 1、 実施 例 2又は実施例 9で示したものと同様の条件で MO C VD法及びク口ライド V P E法により窒 化ガリウム、 窒化インジウム、 窒化アルミニウムのうちから選ばれた少なくとも 1種以上を主 成分とする単結晶薄膜を 2層以上上記焼結体基板に形成し、 得られた各単結晶薄膜層の結晶性 について調べた。 クロライド VPE法は厚み 15 mを超える薄膜を形成するときにだけ用い た。 なお、 ドーピング用原料として MOCVD法による薄膜形成ではジメチルベリリウム、 ビ スーシクロペン夕ジェニリレマグネシウム、 ジェチル«、 S iH4を原料として用い、 クロライ ド VP E法による薄膜形成では MgB r2をドーピング用原料として用いて薄膜を形成した。 M
OCVD法を用いて薄膜を形成する場合、 窒化アルミニウムを主成分とする焼結体に直接形成 する 1層目の薄膜は実施例 1と同様の原料、 ガス、 基板温度及びその他の形成条件により行つ た。 また 1層目の上に形成する 2層目及び 3層目の薄膜は G a Nを主成分とするものが基板温 度 950°C、 I nNを主成分とするものが基板温度 750°C、 A 1 Nを主成分とするものが基 板温度 1050°Cとし、 その他はドーピング成分含有の有無にかかわらず用いた原料、 ガス及 ぴ 膜形成条件は実施例 1と同様に行った。 また、 GaN+A 1 Nの混晶を主成分とするもの はドーピング成分含有の有無にかかわらず基板? SJtl 000°C、 GaN+ I nNの混晶«¾板 继 800 °Cとしその麵料、ガス及び形成条件などは実施例 1及び実施例 2と同様に行つた。 なお、 クロライド VP E法による薄膜形成において GaN+A 1 Nを主成分とする混晶に Mg をド一ピング成分として含有する薄膜の形成は基板温度 1200°Cとしその他の原料、 ガス及 び形成条件などは実施例 9と同様に行った。 上記のように 2層以上で形成した単結晶薄翻の 構成は以下の 3通りである。 すなわち、 1) 同一組成の単結晶薄膜を 2回以上に分けて別々に 形成したもの、 2) 主成分である窒化ガリウム、 窒化インジウム、 窒化アルミニウムの誠が 異なるもの、 3) 主成分は同じであるがドーピング剤などの微量成分の含有量が異なるもの、 である。 上記の MOCVD法及びクロライド VP E法による薄膜形成後窒化ガリウム、 窒化ィ ンジゥム、 窒化アルミニウムのうちから選ばれた少なくとも 1種以上を主成分とする成分の他 に Be、 Mg、 Zn、 S iのドーピング成分を有する薄膜が形成された基板を純 N2雰囲気中 7 00°Cで熱処理を行った。 このようにして得た各単結晶薄膜層の結晶性を調べた。 なお 2層以 上の構成の単結晶薄膜のなかで表面層より下部に形成された単結晶薄膜の結晶性は上部の単結 晶薄^ ϋを形成する前に X線回折により調べるかあるいは上部の単結晶薄膜層を研削! ^した 後調べた。 その結果を表 10に示す。 なお、 表 10の薄膨袓成の欄において 1層目のものは焼 結体基板に直接形成されている単結晶薄膜であり、 2層目のものは 1層目の単結晶薄膜上に直 接形成された単結晶薄膜であり、 3層目のものは 2層目の単結晶薄膜上に直接形成された単結 晶薄膜である。 表 10から明らかなように本発明による窒化アルミニウム及び各種セラミック 材料を主成分とする焼結体からなる基板を用いることでこれら基板に 2層以上で形成された窒 化ガリウム、 窒化インジウム、 窒化アルミニウムのうちから選ばれた少なくとも 1種以上を主 成分とする単結晶薄膜の結晶性はすべてミラー指数 (002) の格子面の X線回折ロッキング カーブの半値幅が 300秒以下のものが得られることが示されている。 表 10に示されるよう に、 上記窒化アルミニウム及び各種セラミック材料を主成分とする焼結体からなる基板に 2層 以上の構成で形成された 2層目及び 3層目の各単結晶薄膜層の結晶性は 1層目の単結晶薄膜の 結晶性に比べてより優れた傾向を有することも確認された。 また、 上記基板のうち窒化アルミ ニゥムを主成分とする焼結体を用レ この基板に 2層以上の構成で形成された 2層目及び 3層目 の各単結晶薄膜層の結晶性はミラ一指数 (002) の格子面の X線回折ロッキングカープの半 値幅が 150秒以下であり、 炭化珪素、 窒化珪素、 酸化亜鉛、 酸化ベリリウムなどの六方晶結 晶系及び殿化アルミニウムなどの三方晶結晶系あるいは六方晶系として分類できる結晶系を有 する各種セラミック材料を主成分とする焼結体に比べてさらに優れたものが得られることが示 された。 また、 2層構成としても 200 m程度の比較的厚みの厚い単結晶薄膜が形成し得る ことが 認された。 また S iをドーピングした実験 N o. 237及び 238の 2層目の各単結 晶薄膜の室温における抵抗率を測定したところそれぞれ 0. 6Ω · cm (49. 94モル%0 aN+49. 94モル%AlN+0. 12モル%S i ) 及び 86 Ω · cm (99. 94モル%八 1 N+0. 06モル%30 と半 本化していることが ϋ認された。 また、 Mg、 Be、 Znを ドーピングした実験 No. 240の 3層目、 実験 No. 241の 2層目、 実験 No. 242の 2層目の各薄膜の室温における抵抗率を測定したところそれぞれ 0. 097Ω · cm (99. 9モル%GaN+0. 1モル%Mg:)、 0. 44Ω · cm (99. 9モル%GaN+0. 1モル%
Be), 0. 26Ω · cm (99. 9モル%GaN+0. 1モル%Zn) でありそれぞれ半導体 化していることがt認された。 さらに、 実験 No. 239の 2層目、 実験 No. 241の 3層 目、 実験 N o. 246の 4層目の各薄膜の室温における抵抗率を測定したところそれぞれ 0. 054Ω■ cm (100%GaN), 0. 036 Ω · cm (70モル%G aN+ 30モル% I n N), 0. 011Ω · cm (100% I nN) でありドーピング元素を含まない G a N、 I nN 及び GaN+ I nNは自発的に半導体化していた。
上記のように、本実施例において窒化アルミニウムを主成分とする焼結体あるいは炭化珪素、 窒化珪素、 酸化アルミニウム、 酸化亜鉛、 酸化ベリリウムなど各種セラミック材料を主成分と する焼結体に少なくとも 1層及び 2層の窒化ガリウム、 窒化インジウム、 窒化アルミニウムの うちから選ばれた少なくとも 1種以上を主成分とする単結晶薄膜を形成した薄膜基板はさらに その上に窒化ガリウム、 窒化インジウム、 窒化アルミニウムのうちから選ばれた少なくとも 1 種以上を主成分とする単結晶薄膜が形成可能であることが示された。 また、 上記各種セラミツ ク材料を主成分とする焼結体からなる基板上にあらかじめ形成された 1層及び 2層の窒化ガリ ゥム、 窒化インジウム、 窒化アルミニウムのうちから選ばれた少なくとも 1種以上を主成分と する単結晶薄膜の上に形成される単結晶薄膜の結晶性は、 その下にある単結晶薄膜よりも向上 し易いことが確認された。
このように、 上記窒化アルミニウムを主成分とする焼結体あるいは炭化珪素、 窒化珪素、 酸 化アルミニウム、 酸化亜鉛、 酸化ベリリウムなど各種セラミック材料を主成分とする焼結体に 少なくとも 1層及び 2層の窒化ガリゥム、 窒化ィンジゥム、 窒化アルミニゥムのうちから選ば れた少なくとも 1種以上を主成分とする単結晶薄膜を形成した薄膜基板は窒化ガリウム、 窒化 インジウム、 窒化アルミニウムのうちから選ばれた少なくとも 1種以上を主成分とする単結晶 薄膜を形成するための薄膜形成用基板としても用いることができることが ϋ認された。
実施例 11
窒化アルミニウムを主成分とする焼結体作製用原料粉末として酸化物 (酸化アルミニウム) の 法により難された高繊窒化アルミニウム粉末 〔徳山曹達株式会社 (現:株式会社ト クャマ) 製 「Η」 グレード〕 及び金属アルミニウムの直接窒化法により作製された東洋アルミ ニゥム株式会社製 「TOYALNITE」 を用意し、 焼結助剤として各種希土類 素化合物、 アルカリ土類金属化合物粉末を用意した。 分析の結果 「H」 ダレ一ドには酸素が 1. 2重量% 「TOYALNITE」 には不純物として酸素が 1. 4重量%含まれる。 粉末の平均粒子径は それぞれ 9 01と1. 1 mである。 又その他に添加物として酸化アルミニウム、 カーボ ン、 珪素などを用意した。 これらの原料を用いて実施例 2と同様の方法により各種組成の粉末 成形体を作製した。 またこのようにして得た粉末成形体の一部を用いてできるだけ焼結助剤な どが揮散しないよう実施例 2と同じ方法により 1800°Cで 1時間焼成しあらかじめ焼成済の 焼結体も作製した。 該あらかじめ焼成済の焼結体〖鉢実施例の内容を示す表 11及び表 12の 実験 N o. 283〜 286のサンプルがそれである。 前記のようにして得た粉末成形体及びあ らかじめ焼成済の焼結体を力一ボン製のセッ夕一に置いた後力一ボン製のさやに入れカーボン 炉を用い一酸化炭素 1 O OOp pm含む窒素雰囲気中で各種温度及ぴ诗間条件により高温長時 間焼成し窒化アルミニウムを主成分とする焼結体を得た。 得られた焼結体の組成分析、 X線回 折による A 1 N結晶相の定量、 窒化アルミニウム粒子の大きさ測定を行った。 X線回折による A 1 N結晶相の定量は A 1 N以外の結晶相の回折ピークを測定しそれと A 1 Nの最強回折ピー クとの比を百分率で求め、 全体の結晶相の量から該 A 1 N以外の結晶相の量を差し引くことに より求めた値である。 次に得られた焼結体の表面を 30 nmに鏡面研磨して実施例 2と同様の 方法で波長 605 nmの光に対する光腿率を測定した。 なお、 測定された ½¾ί§率は 率である。 さらに鏡丽磨した基板を用い実施例 1及び実施例 2と同様の方法で窒化ガリウム、
窒化インジウム、 窒化アルミニウムのうちから選ばれた少なくとも 1種以上を主成分とする単 結晶薄膜を形成し該単結晶薄膜の結晶性を調べた。 これらの結果を表 1 1及び表 1 2に示す。 表 1 1には窒化アルミニウムを主成分とする焼結体作翻粉末成形体の組成と誠条件及 られた焼結体の組成、 特性について記したものである。 表 1 2には得られた窒化アルミニウム を主成分とする焼結体を基板として用いたときこれらの基板に形成した単結晶薄膜の組成及び その結晶性が示されている。
すなわち上記の方法により A 1 N純度を高めた窒化アルミニウムを主成分とする焼結体が得 られた。 焼結助剤として用いた希土 ¾素化合物及びアル力リ土類金属化合物を別々に含む粉 末成形体あるいはあらかじめ焼成済みの焼結体においてより低い温度でかつ短い時間で焼結助 剤などの成分が揮散 ·除去され該窒化アルミニウムを主成分とする焼結体の A 1 Nの纖が高 まりやすい傾向がある。
この焼結体を基板として用いて窒化ガリウム、 窒化インジウム、 窒化アルミニウムのうちか ら選ばれた少なくとも 1種以上を主成分とする単結晶薄膜を形成し該単結晶薄膜の結晶性を調 ベた。 その結果、 希土 素化合物及びアルカリ土類金属化合物のうちから選ばれた少なくと も 1種以上の化合物の含有量が元素 で合計 0. 5重量%以下かつ酸!^有量が 0. 9重量% 以下の組成からなる窒化アルミ二ゥムを主成分とする焼結体を得ることができる。 この組成の 基板に直接形成される窒化ガリウム、 窒化インジウム、 窒化アルミニウムのうちから選ばれた 少なくとも 1種以上を主成分とする単結晶薄膜はミラー指数 ( 0 0 2 ) の格子面の X線回折口 ッキングカーブの半値幅が少なくとも 2 4 0秒以下と良好な結晶性を有するものが得られる。 また、 希土 ϋ¾素化合物及びアルカリ土類金属化合物のうちから選ばれた少なくとも 1種以上 の化合物の含有量が元素騰で合計 0. 2重量%以下かつ酸齢有量が 0. 5重量%以下の組 成からなる窒化アルミニウムを主成分とする焼結体を得ることができる。 この組成の基板に直 接形成される窒化ガリウム、 窒化インジウム、 窒化アルミニウムのうちから選ばれた少なくと も 1種以上を主成分とする単結晶薄膜はミラー指数 ( 0 0 2) の格子面の X線回折ロッキング カーブの半値幅が少なくとも 2 0 0秒以下と良好な結晶性を有するものが得られる。 また、 希 土類 素化合物及びアル力リ土類金属化合物のうちから選ばれた少なくとも 1種以上の化合物 の含有量が元素 で合計 0. 0 5重量%以下かつ酸 ¾ ^有量が 0. 2重量%以下の組成から なる窒化アルミニウムを主成分とする焼結体を得ることができる。 この組成の基板に直接形成 される窒化ガリウム、 窒化インジウム、 窒化アルミニウムのうちから選ばれた少なくとも 1種 以上を主成分とする単結晶薄膜はミラー指数 ( 0 0 2 ) の格子面の X線回折ロッキングカーブ の半値幅が 1 5 0秒以下と良好な結晶性を有するものが得られる。 また、 希土類 素化合物及 びアル力リ土類金属化合物のうちから選ばれた少なくとも 1種以上の化合物の含有量が元素換 算で合計 0. 0 2重量%以下かつ酸餘有量が 0. 1重量%以下の組成からなる窒化アルミ二 ゥムを主成分とする焼結体を得ることができる。 この組成の基板に直接形成される窒化ガリゥ ム、 窒化インジウム、 窒化アルミニウムのうちから選ばれた少なくとも 1種以上を主成分とす る単結晶薄膜はミラー指数 ( 0 0 2 ) の格子面の X線回折ロッキングカーブの半値幅が 1 3 0 秒以下と良好な結晶性を有するものが得られる。 さらに、 希土類 素化合物及びアルカリ土類 金属化合物のうちから選ばれた少なくとも 1種以上の化合物の含有量が元素換算で合計 0. 0 0 5重量%以下かつ酸餘有量が 0. 0 5重量%以下の組成からなる窒化アルミニウムを主成 分とする焼結体を得ることができる。 この組成の基板に直接形成される窒化ガリウム、 窒化ィ ンジゥム、 窒化アルミニウムのうちから選ばれた少なくとも 1種以上を主成分とする単結晶薄 膜はミラー指数 (0 0 2 ) の格子面の X線回折ロッキングカーブの半値幅が 1 0 0秒以下と良 好な結晶性を有するものが得られる。
本実施例において得られた A 1 N ¾tを高めた窒化アルミニウムを主成分とする焼結体にお
いて を高めるか«時間を長くすることでその窒化アルミニウム粒子の大きさは増大 した。
すなわち上記 A 1 N酸を高め窒化アルミニウム粒子の大きさが増大した窒化アルミニウム を主成分とする焼結体を基板として用い窒化ガリウム、 窒化インジウム、 窒化アルミニウムの うちから選ばれた少なくとも 1種以上を主成分とする単結晶薄膜を形成し該単結晶薄膜の結晶 性を調べた。 その結果、 A 1 N ¾Sが高く焼結体中の窒化アルミニウム粒子の大きさが平均 5 m以上のものが得られる。 焼結体中の窒化アルミニウム粒子の大きさが平均 5 m以上の基 板において該基板に直接形成される窒化ガリウム、 窒化インジウム、 窒化アルミニウムのうち から選ばれた少なくとも 1種以上を主成分とする単結晶薄膜のミラ一指数 (0 0 2) の格子面 の X線回折ロッキングカーブの半値幅が 2 0 0秒以下と良好なものが得られた。 また、 A 1 N 縮が高く焼結体中の窒化アルミニウム粒子の大きさが平均 8 xm以上のものが得られる。 焼 結体中の窒化アルミニウム立子の大きさが平均 8 m以上の基板において該基板に直接形成さ れる窒化ガリウム、 窒化インジウム、 窒化アルミニウムのうちから選ばれた少なくとも 1種以 上を主成分とする単結晶薄膜のミラ一指数 (0 0 2) の格子面の X線回折ロッキング力一ブの 半値幅が 1 5 0秒以下と良好なものが得られた。 また、 A 1 NMSが高く焼結体中の窒化アル ミニゥム 子の大きさが平均 1 5 m以上のものが得られる。 焼結体中の窒化アルミニウム粒 子の大きさが平均 1 5 /zm以上の基板において該基板に直接形成される窒化ガリウム、 窒化ィ ンジゥム、 窒化アルミニウムのうちから選ばれた少なくとも 1種以上を主成分とする単結晶薄 膜のミラ—指数 (0 0 2) の格子面の X線回折ロッキングカーブの半値幅が 1 3 0秒以下と良 好なものが得られた。 さらに、 A が高く焼結体中の窒化アルミニウム粒子の大きさが 平均 2 5; m以上のものが得られる。 焼結体中の窒化アルミニウム立子の大きさが平均 2 5 n m以上の基板において該基板に直接形成される窒化ガリウム、 窒化インジウム、 窒化アルミ二 ゥムのうちから選ばれた少なくとも 1種以上を主成分とする単結晶薄膜のミラ一指数 (0 0 2) の格子面の X線回折ロッキングカーブの半値幅が 1 0 0秒以下とさらに良好なものが得られた。 本実施例において得られた A 1 N«を高めた窒化アルミニウムを主成分とする焼結体にお いて誠献を高めるか舰時間を長くすることでその窒化アルミニウムを主成分とする焼結 体の波長 2 0 0 nm〜8 0 0 nmの範囲の光における透過率は増大した。
すなわち上記 A 1 N繊を高め 率が増大した窒化アルミニウムを主成分とする焼結体 を基板として用い窒化ガリウム、 窒化インジウム、 窒化アルミニウムのうちから選ばれた少な くとも 1種以上を主成分とする単結晶薄膜を形成し該単結晶薄膜の結晶性を調べた。その結果、 A 1 N純度が高く波長 2 0 0 nm〜8 0 0 nmの範囲の光における透過率 4 0 %以上の可視光 ¾ 率を有する窒化アルミニウムを主成分とする焼結体が得ら 板として用いることで該基 板に直接形成された窒化ガリウム、 窒化インジウム、 窒化アルミニウムのうちから選ばれた少 なくとも 1種以上を主成分とする単結晶薄膜の結晶性はミラー指数 ( 0 0 2) の格子面の X線 回折ロッキングカーブの半値幅が 1 5 0秒以下と良好なものが得られた。 また 6 0 %以上の高 い可視光翻率を有する窒化アルミニウムを主成分とする焼結体が得ら據板として用いるこ とで窒化ガリウム、 窒化インジウム、 窒化アルミニウムのうちから選ばれた少なくとも 1種以 上を主成分とする単結晶薄膜の結晶性はミラ一指数 ( 0 0 2 ) の格子面の X線回折ロッキング カーブの半値幅が 1 3 0秒以下と良好なものが得らた。 また 8 0 %以上の高い可視光透過率を 有する窒化アルミニウムを主成分とする焼結体が得ら s板として用いることで窒化ガリゥム、 窒化インジウム、 窒化アルミニウムのうちから選ばれた少なくとも 1種以上を主成分とする単 結晶薄膜の結晶性はミラ一指数 (0 0 2) の格子面の X線回折ロッキングカーブの半値幅が 1 0 0秒以下と良好なものが得られた。
実験 N o . 2 5 2〜2 5 5及び 2 7 2、 2 7 3、 2 7 5、 2 7 6以外で得られた窒化アルミ
二ゥムを主成分とする焼結体は室温における熱伝導率が 2 0 OW/mK以上の高い特性を有し ていた。 また結晶相として A 1 Nを 9 9 %以上含むもの及び A 1 N単一相の窒化アルミニウム を主成分とする焼結体は室温における熱伝導率が 2 2 OWZmK以上で最大 2 3 7WZmKと さらに高い特性を有するものが得られた。
表 1 1及び表 1 2から明らかなように原料粉末の由来にあまり影響されず、 また粉末成形体 及びあらかじめ焼成済の焼結体いずれを用いても高温長時間 «することで焼結助剤、 酸素な どの揮散 · Ρ鉄、 現象化が生じ窒化アルミニウムを主成分とする焼結体の高 化が進む。 さ らに能結体中の窒化アルミニウム粒子も成長し、 焼結体自他の ¾i率が向上し波長 2 0 O nm 〜8 0 0 nmの範囲の光における 率 8 0 %以上、 最大 8 8 %のものが得られる。 また、 得 られた窒化アルミニウムを主成分とする焼結体からなる基板に形成される窒化ガリゥム、 窒化 インジウム、 窒化アルミニウムのうちから選ばれた少なくとも 1種以上を主成分とする単結晶 薄膜の結晶性も向上する。 該単結晶薄膜の結晶性について得られた窒化アルミニウムを主成分 とする焼結体の組成すなわち A 1 N純度が高くなれば結晶性が増大する。 上記 A 1 N純度だけ でなくそれ以外にも該単結晶薄膜の結晶性について窒化アルミ二ゥム来立子の大きさあるいは光 逸過率の与える影響がより大きく影響する傾向があった。 すなわち窒化アルミニウム粒子の大 きさが大きくなれば該単結晶薄膜の結晶性はさらに増大する。 また窒化アルミニウムを主成分 とする焼結体からなる基板の光 ¾ 率が高くなれば上記窒化アルミニウム粒子の大きさの増大 化と同様該単結晶薄膜の結晶性はさらに増大する。 すなわち、 本実施例で得られた該単結晶薄 膜の結晶性 板として用いた窒化アルミニウムを主成分とする焼結体の組成すなわち A 1 N カ墙くなること、 窒化アルミニウム粒子の大きさが増大化すること、 窒化アルミニウムを 主成分とする焼結体の光顯率が高くなること、 これらの要素がお互い相乗効果で窒化ガリゥ ム、 窒化インジウム、 窒化アルミニウムのうちから選ばれた少なくとも 1種以上を主成分とす る単結晶薄膜の結晶性を高めていると思われる。 すなわち高温、 かつ長時間焼成により焼結体 内部が 質された窒化アルミニウムを主成分とする焼結体を薄膜形成用基板として用いること が結晶性の高い該単結晶薄膜を得るためには有効となり得ることが示された。
(比較例) ' 比較のために実験 N o. 2 6 5と同じ粉末成形体をタングステン製のセッ夕一に置きタンダ ステン製のさやに別に用意した窒化アルミニウム粉末とともに入れ、 タングステン炉材と発熱 体からなるタングステン炉により純窒素雰囲気中で 2 2 0 0 °Cの温度において 8時間焼成した が焼結助剤である酸化ィットリゥムはほとんど揮散 · されず粉末成形体のまま残り高純度 化されていない。 又熱伝導率も 2 0 OWZmK以下と低く光透過性も 6 2 %であり表 1 1の実 験 N o . 2 6 5で作製したものより小さかった。
実施例 1 2
実施例 1〜実施例 1 1で作製し使用した窒化アルミニウムを主成分とする焼結体、 及び炭化 珪素、 窒化珪素、 酸ィ匕ァ Jレミ二ゥム、 酸化亜鉛、 酸化ベリリウムの各種セラミック材料を主成 分とする焼結体を基板として用い窒化ガリウム、 窒化インジウム、 窒化アルミニウムのうちか ら選ばれた少なくとも 1種以上を主成分とする無定形薄膜、 多結晶薄膜及び !H向性多結晶薄膜 の形成を MO CVD法により試みた。 本実施例における MO CVD法は実施例 1、 実施例 2及 び実施例 1 0と同様な原料と装置を用いたものである。 なお、 上記基板の表面は実施例 8及び 実施例 9と同様の方法により鏡面研磨されており、 その表面平滑性は表 1 3に示されている。 さらに該無定形薄膜及び多結晶薄膜、 配向性多結晶薄膜などが形成された基板上に窒化ガリゥ ム、 窒化インジウム、 窒化アルミニウムのうちから選ばれた少なくとも 1種以上を主成分とす る単結晶薄膜の形成を試みた。
まず、窒化ガリウム(G a N)を主成分とする薄膜で 板 として 3 0 0 ° (:〜 7 0 0 °C、
窒ィ匕インジウム (I nN) を主成分とする薄膜で 板 として 300° (〜 600°C、 窒化 アルミニウム (A1N) を主成分とする薄膜で ½¾板 として 350°C〜1000°Cの条件 で薄膜形成を試みた。 表 13の実験 N 0. 287及び 293に示されている 100モル% G a N薄膜 板 40°Cで作製したものである。 実験 No. 288、 289、 290、 29 2、 294、 297、 298、 299、 300、 301に示されている 100モル%A 1 N薄 膜 ¾¾板 370。Cで作製したものである。 実験 No. 296に示されている 100モル% A 1 N薄膜は基板 00°Cで作製したものである。 実験 No. 295に示されている 10 0モル%A 1 N薄膜 板 Jtl 050°Cで作製したものである。 このようにして得られた上 記窒化アルミニウムを主成分とする焼結体及び各種セラミック材料を主成分とする焼結体から なる基板上に直接形成された窒化ガリウム、 窒化インジウム、 窒化アルミニウムのうちから選 ばれた少なくとも 1種以上を主成分とする薄膜 (基板側の薄膨 の結晶状態を X線回折により 調べた。 なお窒化アルミニウムを主成分とする薄膜については結晶状態の判定には電 泉回折 も併用した。 その結果、 明らかに得られた薄膜の結晶状態は無定形あるいは多結晶あるいは配 向性多結晶を示すものであった。 その結果を表 13に示す。 本実施例において、 実験 No. 2 91で用いた基板に直接形成された多結晶状態の A 1 N薄膜は基板面に対して C軸が垂直な方 向に形成されている配向性多結晶であった。 該配向性多結晶薄膜のミラー指数 (002) の格 子面の X線回折ロッキングカーブの半値幅は 4620秒と測定された。 なお、 上記実験 No. 291の窒化アルミニウムを主成分とする焼結体からなる基板へ直接形成された A 1 N配向性 多結晶薄膜の形成は基板温度 550°Cで行ったものである。 なお、 表 13の実験 No. 295 だけは基板に直接形成する薄膜として A 1 N単結晶薄膜の形成を試みたものである。実験 No. 295においては基板温度 1100°Cと前記の条件より高く設定しその他の原料、 ガス及び形 成条件は実施例 1と同様の MOCVD法により薄膜形成を行った。 このようにして得られた表 13に示す実験 N o. 295の 100モル% A 1 N薄膜は基板面に対して C軸が垂直な方向に 形成されている単結晶であり該単結晶薄膜のミラー指数 (002) のネ各子面の X線回折ロッキ ングカーブの半値幅は 127秒と測定された。
このように本実施例において単結晶だけでなく窒化ガリウム、 窒化インジウム、 窒化アルミ ニゥムのうちから選ばれた少なくとも 1種以上を主成分とする無定形、 多結晶、 配向性多結晶 など各種結晶状態の薄膜が上記窒化アルミ二ゥムを主成分とする焼結体及び各種セラミック材 料を主成分とする焼結体上に直接形成された薄膜基板が得られることが明らかにされた。
次に、 実験 No. 293、 299、 301において、 窒化ガリウム及び窒化アルミニウムを 主成分とする無定形薄膜があらかじめ直接形成された窒化アルミニウムを主成分とする焼結体、 酸化アルミニウム及び 化ベリリウムを主成分とする焼結体からなる薄膜基板上に基板 そ れぞれ 450 (実験 No. 293)、 550°C (実験 No. 299、 及び 301) の条件によ り微量のドーピング成分を含む窒化ガリウム及び窒化アルミニウムを主成分とする薄膜をさら に 1層形成した基板を作製した。 その他の形成条件は実施例 1、 実施例 10で示した MOCV D法と同様である。 得られた薄膜は X線回折の結果明らかに基板面に対して C軸が垂直に形成 された配向性多結晶であった。 これら配向性多結晶のミラー数 (002) の格子面の X線回折 ロッキング力一ブの半値幅は実験 No. 293のもので 4540秒、 実験 No. 299のもの で 10820秒、 実験 No. 301のもので 9890秒であった。 このように、 窒化アルミ二 ゥムを主成分とする焼結体からなる基板を用いて形成した配向性多結晶のほうカ戰化アルミ二 ゥム及び酸化ベリリゥムを主成分とする焼結体からなる基板を用いたものより結晶性の優れた ものが得られる傾向を示した。
以上説明したように、 本実施例において窒化ガリウム、 窒化インジウム、 窒化アルミニウム のうちから選ばれた少なくとも 1種以上を主成分とする無定形、 多結晶、 配向性多結晶など各
種結晶状態の薄膜が上記窒化アルミニウムを主成分とする焼結体及び各種セラミック材料を主 成分とする焼結体上に少なくとも 1層あるいは 2層形成された薄膜基板が得られることが明ら かにされた。
次にこのような無定形薄膜及び多結晶薄膜、 配向性多結晶薄膜など各種結晶状態の薄膜が 1 層及び 2層形成された窒化アルミニウムを主成分とする焼結体及び各種セラミック材料を主成 分とする ¾結体からなる薄膜基板に窒化ガリウム、 窒化インジウム、 窒化アルミニウムのうち から選ばれた少なくとも 1種以上を主成分とする単結晶薄膜の形成を MO CVD法により試み た。 この単結晶薄膜形成の試みには実験 N o.2 9 5で作製した 1 0 0モル%A 1 N単結晶薄膜 を形成した基板も用いた。 単結晶薄膜の形成に際して G a N、 I n N、 A 1 Nを主成分とする ものはドーピング成分含有の有無にかかわらず用いた原料、 ガス及び形成条件などは実施例 1 及び実施例 1 0と同様に行った。 一方 G a N+A 1 Nの混晶を主成分とするものはドーピング 成分含有の有無にかかわらず基板温度 1 0 5 G a N+ I n Nの混晶は基板温度 8 3 0 °C としその他原料、ガス及び 成条件などは実施例 1、実施例 2及び実施例 1 0と同様に行った。 このようにして上記無定形薄膜及 Π ^結晶薄膜、 配向性多結晶薄膜など各種結晶状態の薄膜が 形成された基板上にさらに窒化ガリウム、 窒化インジウム、 窒化アルミニウムのうちから選ば れた少なくとも 1種以上を主成分とする薄膜が 1層形成された 板を得た。 このように形成さ れた薄膜を X線回折により分析したところすベて単結晶であることがt認された。 これら単結 晶薄臌堪板面に対して C軸が垂直な方向に形成されている。 得られた単結晶薄膜の結晶性に ついて調べその結果を表 1 3に示した。 なお窒化アルミニウムを主成分とする薄膜については 結晶状態の判定に電子線回折も併用した。 その結果少なくとも表面が単結晶薄膜からなる 2層 構成の薄膜が形成された基板が得られることが明らかとなった。 さらに、 実験 N o . 2 9 3、 2 '9 9及び 3 0 1において 面が単結晶薄膜からなる 3層構成の薄膜が形成された基板が得' られることが明らかとなった。
上記のように 2層構成の薄膜を有し表面側の層に単結晶薄膜を形成した基板の中で実験 N o . 2 9 1及び 2 9 2の基板を選び、 引き続いて上記と同様の条件の MO CVD法を用いて単結晶 薄膜の形成を試みた。 その結果新たに表面側に形成された薄膜は X線回折により明らかに基板 面に対して C軸が垂直な方向に形成されている単結晶であった。 この結果実験 N o . 2 9 1及 び 2 9 2において、 単結晶薄膜を 2層有する薄膜 3層の構成からなる基板が作製できることが 確認された。 実験 N o . 2 9 1及び 2 9 2において最後表面側に形成された単結晶薄膜の結晶 性は最初に形成されている (中間層として形成されている) 単結晶薄膜の結晶性より向上して いる。 すなわち実験 N o . 2 9 1において最初に形成された単結晶薄膜のミラ一指数 ( 0 0 2) の格子面の X線回折ロッキングカーブの半値幅は 9 6秒であるのに対して、 その上に形成され た単結晶薄膜は 9 1秒であった。 また、 実験 N o . 2 9 2において最初に形成された単結晶薄 膜のミラ一指数 (0 0 2 ) の格子面の X線回折ロッキングカーブの半値幅は 9 7秒であるのに 対して、 その上に形成された単結晶薄膜は 8 9秒であった。
表 1 3から明らかなように、 あらかじめ無定形薄膜、 多結晶薄膜及ぴ¾己向性多結晶薄膜が少 なくとも 1層あるいは 2層形成されている窒化アルミニウムを主成分とする焼結体からなる基 板上には窒化ガリウム、 窒化インジウム、 窒化アルミニウムのうちから選ばれた少なくとも 1 種以上を主成分とする単結晶薄膜が形成できる。 その結晶性はテストした基板すベて窒化ガリ ゥム、 窒化インジウム、 窒化アルミニウムのうちから選ばれた少なくとも 1種以上を主成分と する単結晶薄膜のミラ一指数 (0 0 2 ) の格子面の X線回折ロッキングカーブの半値幅が 1 0 0秒以下であった。 通常本実施例で用いた実験 N o . 4 6、 4 9、 1 1 0、 2 6 7及び 2 8 3 で作製した窒化アルミニウムを主成分とする焼結体に窒化ガリウム、 窒化インジウム、 窒化ァ ルミニゥムのうちから選ばれた少なくとも 1種以上を主成分とする単結晶薄膜を直接形成した
場合、 これら単結晶薄膜はそのミラー指数 (0 0 2 ) の格子面の X線回折ロッキングカーブの 半値幅が 1 0 0秒以下となるような高い結晶性のものが得られにくいが、 上記のようにあらか じめ無定形薄膜、 多結晶薄 11¾ぴ«向性多結晶薄膜が少なくとも 1層あるいは 2層形成されて いる窒化アルミニウムを主成分とする焼結体からなる基板を用いることで、 形成される単結晶 薄膜の結晶性は窒化アルミニウムを主成分とする焼結体からなる基板上に直接単結晶薄膜を形 成する場合よりもさらに向上する傾向があることが かめられた。
また、 あらかじめ無定形薄膜、 多結晶薄膜及び ¾己向性多結晶薄膜が少なくとも 1層あるいは 2層形成されている炭化珪素、 窒化珪素、 酸化ベリリウム、 酸化亜鉛、 酸化アルミニウムなど 六方晶系又は三方晶系の結晶構造を有するセラミック材料を主成分とする焼結体からなる基板 上にも窒化ガリウム、 窒化インジウム、 窒化アルミニウムのうちから選ばれた少なくとも 1種 以上を主成分とする単結晶薄膜が形成できる。 その結晶性はテストした基板すべてにおいて窒 化ガリウム、 窒化インジウム、 窒化アルミニウムのうちから選ばれた少なくとも 1種以上を主 成分とする単結晶薄膜のミラ一指数 ( 0 0 2) の格子面の X線回折ロッキングカーブの半値幅 が 2 0 0秒以下であった。 通常実施例 1で作製し、 本実施例で用いた炭化珪素、 窒化珪素、 酸 化ベリリウム、 酸化亜鉛、 酸化アルミニウムなど六方晶系又 方晶系の結晶構造を有するセ ラミック材料を主成分とする焼結体に窒化ガリウム、 窒化インジウム、 窒化アルミニウムのう ちから選ばれた少なくとも 1種以上を主成分とする単結晶薄膜を直接形成した場合、 これら単 結晶薄膜はそのミラー指数 (0 0 2) の格子面の X線回折ロッキングカーブの半値幅が 2 0 0 秒以下となるような高い結晶性のものが得られにくいが、上記のようにあらかじめ無定形薄膜、 多結晶薄厳ぴ¾向性多結晶薄膜が少なくとも 1層あるいは 2層形成されている炭化珪素、 窒 化珪素、 酸化ベリリウム、 酸化菌、 酸化アルミニウムなど六方晶系又 方晶系の結晶構造 を有するセラミック材料を主成分とする焼結体からなる基板を用いることで、 形成される単結 晶薄膜の結晶性は炭化珪素、 窒化珪素、 酸化ベリリウム、 酸化亜鉛、 酸化アルミニウムなど六 方晶系又は三方晶系の結晶構造を有するセラミック材料を主成分とする焼結体からなる基板上 に直接単結晶薄膜を形成する場合よりもさらに向上する傾向があることが 11かめられた。
このように、 あらかじめ無定形薄膜、 多結晶薄膜及ぴ 向性多結晶薄膜を少なくとも 1層あ るいは 2層形成することで炭化珪素、 窒化珪素、 酸化ベリリウム、 酸化亜鉛、 酸化アルミニゥ ムなど六方晶系又は三方晶系の結晶構造を有するセラミック材料を主成分とする焼結体からな る基板には容易に比較的結晶性の優れた窒化ガリウム、 窒化インジウム、 窒化アルミニウムの うちから選ばれた少なくとも 1種以上を主成分とする単結晶薄膜を形成することが確認された。 以上説明してきたことから明らかなように、 本実施例において単結晶、 無定形、 多結晶、 配 向性多結晶など各種結晶状態の窒化ガリウム、 窒化インジウム、 窒化アルミニウムのうちから 選ばれた少なくとも 1種以上を主成分とする薄膜を2層及び3層形成した薄膜基板が容易に得 られる。 この 2層及び 3層に形成された薄膜のうち少なくとも最も表面側の層には優れた結晶 性を有する単結晶薄膜が形成できることカ 認された。 この単結晶薄膜は窒化アルミニウムを 主成分とする焼結体及び炭化珪素、 窒化珪素、 酸化ベリリウム、 酸化亜鉛、 酸化アルミニウム など六方晶系又は三方晶系の結晶構造を有するセラミック材料を主成分とする焼結体からなる 基板に直接形成したものよりより高い結晶性のものが得られることが実験的に確かめられた。 本実施例において、 実験 N o . 2 9 4で使用した窒化アルミニウムを主成分とする焼結体か らなる基板は、 実施例 1 1で示したようにもともと該基板に直接形成される窒化ガリウム、 窒 化インジウム、 窒化アルミニウムのうちから選ばれた少なくとも 1種以上を主成分とする単結 晶薄膜のミラー指数 ( 0 0 2 ) の格子面の X線回折ロッキングカーブの半値幅が 9 2秒と良好 な結晶性を有するが、 窒化アルミニウムを主成分とする焼結体からなる基板にあらかじめ無定 形の薄膜を形成した基板を用いることでその上に形成された単結晶薄膜の結晶性がさらに 8 2
秒、と高まる。 実験 N o . 2 9 5の基板を用いたものは基板に最初直接形成した薄膜を含めすベ ての層が単結晶である。 最初直接形成した単結晶薄膜のミラ一指数 (0 0 2 ) の格子面の X線 回折ロッキングカーブの半値幅は 1 2 7秒であったがその上に形成した単結晶薄膜のミラー指 数 (0 0 2) の格子面の X線回折ロッキングカーブの半値幅が 8 7秒と結晶性はさらに改善さ れた。
上記のように、本実施例において窒化アルミニウムを主成分とする焼結体あるいは炭化珪素、 窒化珪素、 酸化アルミニウム、 酸化亜鉛、 酸化ベリリウムなど各種セラミック材料を主成分と する焼結体に少なくとも 1〜2層の窒化ガリウム、 窒化インジウム、 窒化アルミニウムのうち から選ばれた少なくとも 1種以上を主成分とする薄膜を形成した薄膜基板はさらにその上に窒 化ガリゥム、 窒化ィンジゥム、 窒化アルミニゥムのうちから選ばれた少なくとも 1種以上を主 成分とする薄膜が形成可能であることが示された。 すなわち、 上記窒化アルミニウムを主成分 とする焼結体あるいは炭化珪素、 窒化珪素、 酸化アルミニウム、 酸化 酸化ベリリウムな ど各種セラミック材料を主成分とする焼結体に少なくとも 1〜2層の窒化ガリウム、 窒化イン ジゥム、 窒化アルミニウムのうちから選ばれた少なくとも 1種以上を主成分とする単結晶、 無 定形、 多結晶、 配向性多結晶など各種結晶状態の薄膜を形成した薄膜基板は窒化ガリウム、 窒 化インジウム、 窒化アルミニウムのうちから選ばれた少なくとも 1種以上を主成分とする薄膜 を形成するための基板 (すなわち薄膜形成用基 としても用いることができることが 認さ れた。
実施例 1 3
実施例 1 1で作製した粉末成形体を用い «雰囲気を一酸化炭素 1 5 0 p pmを含む窒素、 水素 6 0 p pmを含む窒素、 炭化水素 2 4 0 p pm含む窒素、 一酸化炭素 1 8 0 0 p pmを含 むアルゴン、 の 4種類のものに代えた以外は実施例 1 1で使用した実験 N o . 2 6 9の粉末成 形体を用い、 実施例 1 1と同様の力一ポンセッ夕一、 力一ボンさや、 力一ポン炉を使用して 2 2 0 0での で 4時間誠し窒化アルミニウムを主成分とする焼結体を得た。 その結果上記 すべての雰囲気で焼成したものが実施例 1と同様ィットリゥム及びカルシウムの含有量はそれ ぞれ 0. 5 p pm以下となった。 窒化アルミニウム粒子も 3 5 〜 4 0 mに成長し光透過 率もすベて 8 0 %を超えた。 さらに各雰囲気中で得られた窒化アルミニウムを主成分とする焼 結体を用いて基板を作製し実施例 1と同様に M〇 C VD法により窒化ガリゥム単結晶薄膜を 0. 5 mの厚みで形成したところ該単結晶薄膜のミラ一指数 ( 0 0 2) の格子面の X線回折ロッ キングカーブの半値幅がすべての基板で 1 0 0秒と良好な結晶性を示した。
実施例 1
窒化アルミニウムを主成分とする焼結体作翻原料粉末として高繊窒化アルミニウム粉末 〔徳山曹達株式会社 (現:株式会社トクャマ) 製 「H」 グレード〕 を用意した。 この原料粉末 は酸化物 M¾法にて製造されたものである。 この原料粉末に Y203粉末を 5重量%だけ加えた ものと、 Υ203粉末 5重量%及び C a C〇3粉末を C a O換算で 0. 5重量%加えたものをトル ェンおよびィソプロピルアルコールとともにポールミルで 2 4時間混合後ァクリルバインダー を粉末原料 1 0 0重量部に対して 1 2重量部加えさらに 1 2時間混合することでペースト化し ドク夕一ブレード法で厚み 0. 8 mmの 2種類の組成を有するグリ一ンシ一トを作製した。 こ のグリーンシ一卜から一辺 3 5 mmの正方形状のシ一卜を作製しこのシートに Y A Gレーザー で表裏面を貫通する直径 2 5 m及び 5 0 mの円形スルーホールを形成した。 次に溶媒とし て《テルピネオ一ル、 ノ ィンダ一としてァクリル樹脂を™し導電性成分としてタングステン 粉末を用いさらに該タングステン粉末に対して上記窒化アルミニウム粉末を 0〜2 0重量%の 範囲で加えて混合し導通ビア用ペーストを作製した。 各混合比の粉末ペーストを上記スルーホ —ルに充填し乾燥後、 ¾ϋ窒素又は窒素/水素混合ガスを主成分とする雰囲気中で脱バインダ
一後、 次の 2つの舰条件で導通ビアを有する窒化アルミニウムを主成分とする焼結体を作製 した。 誠条件は、 1 ) N2雰囲気中 1 8 0 0°Cにおいて 2時間常圧誠する、 2) 一酸化炭素 を 2 0 0 p pm含む窒素雰囲気中 2 2 0 0 において 4時間焼成する、 の 2条件である。 この ようにして導通ビアが内部に形成された窒化アルミニウムを主成分とする焼結体を得た。 いず れの焼結体においてもスルーホール内の導電性成分は十分歉密ィ匕し導電性が発現しており窒化 アルミニウムを主成分とする焼結体とも一体化しており導通ビアとして機能している。 上記 1 8 0 Ot:において 2時間常圧焼成した導通ビアが形成された窒化アルミニウムを主成分とする 焼結体は焼結助剤がほとんど揮散されておらず 率は 5 1 %〜 6 5 %の範囲であつたが、 2 2 0 0 °Cで 4時間焼成したものは焼結助剤が揮散しイットリウム及びカルシウムの含有量が 合計で 5 0 p pm以下になっている。 また窒化アルミニウム粒子も 3 5 m〜4 5 xmに成長 しており、 光透過率も 8 0 %以上であつた。 このようにして得られた焼結体を直径 2 5. 4m m'x厚み 0. 5 mmの寸法に研削、 及 勵ロェして導通ビアを露出させ表面平滑度 R a = 3 O nmの導通ビアを有する窒化アルミニウムを主成分とする焼結体からなる基板を作製した。 その後導通ビアの室温における抵抗を 4¾ΐ法で測定し導通ビアの形状から室温における抵抗 率を算出した。 導通ビアの大きさは焼成後収縮しそれぞれ直径 4 0〜4 4 m及び 2 0〜2 3 mになっていた。 また上記導通ビアが形成された基板上に直接実施例 1及び 2で用いたもの と同じ MO CVD装置を用いた方法で窒化ガリウムの単結晶薄膜を 0. 2 5〃mの厚みで基板 の片面に形成し該単結晶薄膜のミラー指数 ( 0 0 2) 格子面の X線回折ロッキングカーブの半 値幅を測定した。 それらの結果を表 1 4に示した。 単結晶薄膜形成後導通ピアが形成されてい る周囲の単結晶薄膜について観察を行ったがクラックや導通ビアとの界面における剥離などの 不具合は特に見当たらず良好な外観状態であり本発明による材料を用いた導通ビアは窒化ガリ ゥム薄膜と良好な接合性を有していることが ϋ認された。 導通ビアの室温における抵抗率は窒 化アルミ二ゥムの含有量や焼成条件及びスルーホールの径などにより変化したが 6. 8 X 1 0 " 6 Ω · cm〜l 3 2 X 1 0 "6 Ω · c mの範囲であり、 該単結晶薄膜のミラー指数 ( 0 0 2)格子 面の X線回折ロッキングカーブの半値幅はすべて 3 0 0秒以下である。 1 8 0 0 °Cで 2時間焼 成することで得た基板において導通ビア中の窒化アルミ二ゥムの含有量が増えるにしたがつて 基板に形成された該単結晶薄膜の結晶性が向上する傾向が見られ、 窒化アルミニウム粉末を 1 0重量%以上含む導通ピアにおいては該単結晶薄膜のミラー指数 ( 0 0 2 ) 格子面の X線回折 ロッキングカーブの半値幅は 1 5 0秒以下に高まった。 また、 2 2 0 で 4時間焼成するこ とで得られた導通ビアを有する基板に形成された該単結晶薄膜のミラ一指数 ( 0 0 2) 格子面 の X線回折ロッキングカーブの半値幅は 1 0 0秒以下の高い結晶性のものが得られた。 本実施 例において作製した窒ィ匕ガリウムを主成分とする各薄膜の室温における抵抗率は 0. 0 5 9 Q ' c m〜0. 1 0 1 Ω · c mの範囲であり導電性を有する。 また、 導通ビアが形成されてい る各焼結体を用いて作製した該窒化ガリウムを主成分とする薄膜と該薄膜が形成されていない 基板面側に露出している導通ビアとの間には導通がある。 このように本実施例で作製した導電 性を有する窒化ガリウムを主成分とする単結晶薄膜と導通ビアとは機械的な接合性だけでなく 電気的にも接続されていることが確認された。
実施例 1 5
実施例 1 1で用いた酸化物 ¾法による窒化アルミニウム原料粉末に焼結助剤として酸化ィ ットリウムを 5重量%含む混合粉末を用いて外形サイズを直径 3 2mmの円盤状とした各種厚 みの粉末成形体を作製した。 この粉末成形体を実施例 1 1と同様力一ボン製のセッ夕一、 力一 ボン製のさやを用いカーボン炉にて 1 0 0 0 p pmの一酸化炭素を含有する窒素雰囲気中 2 2 0 0 °Cで 8時間焼成した。 その結果、 粉末成形体の厚みが 8 mm以下のもので透光性を有する 焼結体が得られた。 それ以上の厚みのものは黒色化し 性がなぐ 窒化ガリウム、 窒化イン
ジゥム、 窒化アルミニウムのうちから選ばれた少なくとも 1種以上を主成分とする単結晶薄膜 が形成しにくく場合によつては単結晶でない多結晶状態の薄膜になつた。
実施例 16
実施例 1〜 15で作製し使用してきた窒化ルミ二ゥムを主成分とする焼結体を基板に用いそ の上に MOCVD法により A 1
(0≤χ≤1. 0) の化学糸!^であらわされる窒 化ガリゥムと窒化アルミ二ゥムの二成分を主成分とし、 Mgと S iをドーピング元素として上 記組成に対してそれぞれ 10モル%まで、 及び M gと S iの同時ド一プの場合は合計で 10モ ル%までド一プした導電性単結晶薄膜の作製を試みた。 基板として実施例 2で作製した実験 N o. 49の焼結体、 実施例 3で作製した実験 No. 73の焼結体、 実験 No. 75の焼結体、 実験 No. 80の焼結体、 実験 No. 82の焼結体、 実施例 6で作製した実験 No. 110の 焼結体、 実施例 11で作製した実験 No. 284の焼糸吉体、 実施例 14で作製した実験 No. 305の焼結体、 実験 No. 311の焼結体及び実験 No. 317の焼結体を基板として用い た。実験 No. 73の 結体、 実験 No. 75の焼結体、 実験 No. 80の«体、 実験:^0. 82の焼結体、 実験 No. 305の焼結体、 実験 No. 311の焼結体、 実験 N o . 317の 焼結体にはそれぞれ導通ピアが形成され該導通ビアは基板の上下表面に露出している。 単結晶 薄膜の作製条件は実施例 1、 実施例 2及び実施例 10と同様である。 基板形状は実施例 1、 3 及び 14と同様である。 なお薄膜の厚みは 3 mとし、 各焼結体を用いて作製した基板の片面 に形成した。 CVDで薄膜形成後薄膜が形成された基板を純 N
2雰囲気中 700 で熱処理を行 つた。 その結果、 実験 No. 73、 実験 No. 75の焼結体、 実験 No. 80の焼結体、 実験 No. 82の焼結体、 実験 No. 305の各焼結体を用いた基板には上記 Mg及び S iを 10 モル%までド一プした Al
xGa 一
ΧΝ (0≤χ≤1. 0) のすベての誠で単結晶薄膜が形成 でき該単結晶薄膜のミラ一指数 (002) 格子面の X線回折ロッキングカーブの半値幅は 20 0秒以下と良好なものであった。 又、 実験 No. 49及び実験 No. 110の各焼結体を用い た基板には上記 Mg及び S iを 10モル%までド一プした A 1
xGa
1--xN (0≤χ≤1. 0) のすベての組成で単結晶薄膜が形成でき該単結晶薄膜のミラー指数 (002) 格子面の X線回 折ロッキングカーブの半値幅は 150秒以下と良好なものであった。 又実験 No. 284、 実 験 No. 311及び実験 No. 317の各焼結体を用いた基板には上記 Mg及び S iを 10モ ル%までド一プした AlxGa —
ΧΝ (0≤χ≤1. 0) のすベての組成で単結晶薄膜が形成で き該単結晶薄膜のミラー指数 (002) 格子面の X線回折ロッキングカーブの半値幅は 100 秒以下とさらに良好なものであった。 導通ビアが形成されている実験 No. 73の焼結体、 実 験 No. 75の焼結体、 実験 No. 80の焼結体、 実験 No. 82の焼結体、 実験 No. 30 5の焼結体、 実験 No. 311の焼結体、 実験 No. 317の焼結体を用いて作製した単結晶 薄膜について導通ビア周囲の観察を行つたがクラックゃ導通ビアとの界面における剥離などの 不具合は特に見当たらず良好な外観状態であり、本発明による材料を用いた導通ビアは A 1
XG ¾
1_
ΧΝ (0≤χ≤1. 0) の組成を有する単結晶薄膜及び Al
xG
ai—
XN (0≤χ≤1. 0) に S i及び M gをド一プした組成を有する単結晶薄膜と良好な接合性を有していることが歸忍 された。 これらの各猶诚の単結晶薄膜について室温における抵抗率を測定したところ、 Al
x Ga!_
xN (0≤χ≤1. 0) の化学式であらわされる糸滅物に対し Mgを元素騰で 0. 00 001〜10モル%の範囲で含むものは室温における抵抗率 1 X 10
4Ω · cm以下であった。 又その中で A 1 xGa —xN (0≤x≤0. 6) の化学式であらわされる組成物に対して Mgを 元素換算で 0. 00001〜 10モル%の範囲で含む単結晶薄膜は室温における抵抗率が 1 X 10
_1Ω · cm〜: L X 10
2Ω · cmのものカ得られた。 また、
(0. 6≤x ≤ 1. 0 ) の化学式であらわされる組成物に対し S iを元素購で 0. 00001〜0. 5モ ル%の範囲で含む単結晶薄膜は室温における抵抗率 1 Χ 10。Ω · ΟΠΙ〜: ίΧΐ 0
3Ω · οπιの
範囲の抵抗率を示した。 この組成の単結晶薄膜には x=l. 0すなわち主成分が窒化アルミ二 ゥムだけからなり S iを元素換算で 0. 00001モル%〜 0. 5モル%の範囲で含有する薄 膜が含まれ、 室温における抵抗率は 40Ω ·。πι〜200Ω · cmの範囲であった。 また、 A
(0. 6≤χ≤1. 0) の化学式であらわされる組成物に対して Mgと S iを同 ,こ元素換算で 0. 00001〜 10モル%の範囲で含む単結晶薄膜は室温における抵抗率が 1 10一
1 Ω · cm〜: L X 10
3Ω · cmのものが得られた。 また、 A 1
xGa
1--xN (0≤x ≤0. 6) の化学式であらわされる組成物に対して S iを元素醇で 0. 00001〜 10モ ル%の範囲で含む単結晶薄膜は室温における抵抗率が 1 X 10"
3Ω - cm~lX 10
ΧΩ · cm の範囲の比較的低い抵抗値を示した。 また、 A 1
xGa!_
xN (0≤x≤0. 6) の化学式であ らわされる組成物に対して S iと Mgを同時に元素換算で 0. 00001〜10モル%の範囲 で含む単結晶薄膜は室温における抵抗率が 1X 10一
3 Ω· cm〜: LX 10^ · c mの範囲の比 較白勺低い氐抗値を示した。 また、 導通ビアが形成されている実験 No. 73の焼結体、 実験 N o. 75の焼結体、 実験 No. 80の焼結体、 実験 No. 82の焼結体、 実験 No. 305の 焼結体、 実験 No. 311の焼結体、 実験 No. 317の焼結体を用いて作製した単結晶薄膜 は該薄膜が形成されていなレ ^基板面に露出している導通ビアと導通があり本実施例で作製した
5に記した。 表 15において薄膜のド一ビング剤添加量は主成分 A 1 xGa ^ XNに対するモ ル%で示してある。 すなわち、 例えば Mgの添加量が 0. 5モル%であるという意味は形成さ れる薄膜が主成分である AlxGa — XNを 99. 5モル%、 ドーピンク^ ijである Mgを 0. 5 モル%の組成を有するものであることを意味する。
実施例 17
実施例 16で使用した実験 No. 73、 75、 80、 82、 305、 311、 317の導通 ビアを有する各窒化アルミニウムを主成分とする焼結体及び実験 N 0. 49の導通ピアを有し ない窒化アルミニウムを主成分とする焼結体を基板として用い実施例 1、 実施例 2、 実施例 1 0及び実施例 12と同様に窒化ガリウム、 窒化インジウム、 窒化アルミニウムのうちから選ば れた少なくとも 1種以上を主成分とする導電性の単結晶薄膜、 無定形薄膜、 多結晶薄膜及び基 板面に対して C軸が垂直な配向性多結晶薄膜の形成を MOCVD法により試みた。 薄膜は各基 板の片面に単層あるいは 2層 (基板側の層と表面層) で形成した。 なお、 実験 No. 350、 351の窒化インジウム薄膜の形成に際して基板温度それぞれ 320 、 360°Cで行った。 また、実験 No. 347, 356の窒化ガリウム薄膜の形成に際して基板 ¾Jtそれぞれ 340°C、 380 で行った。 各薄 の厚みはそれぞれ 3 mとした。 その結果窒化ガリウム、 窒化ィ ンジゥム、 窒化アルミニウムのうちから選ばれた少なくとも 1種以上を主成分とする薄膜は単 結晶以外の無定形、 多結晶及ぴ 向性多結晶であつても導電性を有するものが窒化アルミニゥ ムを主成分とする焼結体に形成できることが明らかとなった。 また導電性を有する薄膜を 2層 以上の構成で形成できることも明らかとなった。 導通ビアが形成されている実験 No. 73の 焼結体、 実験 No. 75の焼結体、 実験 No. 80の焼結体、 実験 No. 82の焼結体、 実験 No. 305の焼結体、 実験 No. 311の焼結体、 実験 No. 317の焼結体を用いて作製 した単結晶、 無定形及び多結晶の薄膜について導通ビア周囲の観察を行つたがクラックゃ導通 ビアとの界面における剥離などの不具合は特に見当たらず良好な外観状態であり、 本発明によ る材料を用いた導通ビアは窒化ガリウム、 窒化インジウム、 窒化アルミニウムのうちから選ば れた少なくとも 1種以上を主成分とする各種組成の薄膜と良好な接合性を有していることが確 認された。 また、 導通ビアが形成されている実験 No. 73の焼結体、 実験 No. 75の焼結 体、 実験 No. 80の焼結体、 実験 No. 82の焼結体、 実験 No. 305の焼結体、 実験 N
o. 3 1 1の焼結体、 実験 N o . 3 1 7の焼結体を用いて作製した各薄膜は該薄膜が形成され ていない基板面に露出している導通ビアと導通があり本実施例で作製した導電性を有する窒化 ガリウム、 窒化インジウム、 窒化アルミニウムのうちから選ばれた少なくとも 1種以上を主成 分とする各種組成の単結晶薄膜、 無定形薄膜、 多結晶薄膜及び基板面に対して C軸が垂直な配 向性多結晶薄膜と導通ビアとは機械的な接合性だけでなく電気的にも接続されていることが確 認された。 これらの結果を表 1 6に記した。
実施例 1 8
実施例 1 6及び実施例 1 7で使用した導通ビアを有する窒化アルミニウムを主成分とする焼 結体及び導通ビアのない窒化アルミニウムを主成分とする焼結体からなる基板にチタン、 クロ ム、 ニッケル、 モリブデン、 タングステン、 白金、 アルミニウム、 タンタル、 窒化タンタル、 窒化チタン、 金、 銅、 タングステン Z銅合金 (W : 7 0重量% + C u 3 0重量%) などの各種 材料を周波数 1 3. 5 6 MH z , 出力 5 0 0 W〜 1 5 0 0 Wの高周波スパッ夕リング法で基板 の両面に形成し各種薄騰電性材料が形成された窒化アルミニウムを主成分とする焼結体から なる基板を得た。 なお、 基板温度は 2 5 0°C、 減圧チャンバ一内に A r +N2ガスを流しながら スパッタリングを行った。 作製した薄 電性材料の波長 6 0 5 nmの光に対する反射率を測 定し表 1 7に示した。 この各種薄騰電性材料が形成された基板に窒化ガリウム、 窒化インジ ゥム、 窒化アルミニウムのうちから選ばれた少なくとも 1種以上を主成分とし ¾tドーピング 剤を加えた薄膜を上記基板の片面に厚み 3 mで形成した。 その結果各種薄 電性材料があ らかじめ形成された基板であっても無定形、 配向性多結晶及び単結晶薄膜が形成し得ることが 確認された。 また配向性多結晶薄 び単結晶薄膜はそれぞれ基板面に対して C軸が垂直な方 向に形成されていることが 認された。表 1 7にはこのような薄膜の結晶性について調べた結 果を示した。 単結晶薄膜の結晶性は該単結晶薄膜のミラー指数 ( 0 0 2 ) の格子面の X線回折 ロッキングカーブの半値幅が 2 0 0秒以下であった。 なお、 表 1 7に示した窒化ガリウム、 窒 化インジウム、 窒化アルミニウムのうちから選ばれた少なくとも 1種以上を主成分とする薄膜 のうち単結晶として測定されたものは実施例 1 0と同様の条件で形成したものであり、 単結晶 以外の無定形薄膜及び «向性多結晶薄膜は実施例 1 2に記載したものと同じ条件で形成された ものである。 また、 表 1 7には記載されていないがあらかじめ薄 電性材料を形成しその上 に無定形薄] 31¾ぴ¾己向性多結晶薄膜が形成された実験 N o . 3 6 0、 実験 N o. 3 6 2〜3 6 4、 実験 N o. 3 6 6〜3 6 7、 実験 N o. 3 6 9、 実験 N o . 3 7 2の基板を用い、 その上 に実施例 1と同様の方法で 1 0 0モル%G a N及び 1 0 0モル%A 1 N単結晶薄膜を形成した ところ、 いずれも該単結晶薄膜のミラー指数 ( 0 0 2 ) の格子面の X線回折ロッキングカーブ の半値幅が 1 0 0秒以下であった。 表 1 7に示すように形成された窒化ガリウム、 窒化インジ ゥム、 窒化アルミニウムのうちから選ばれた少なくとも 1種以上を主成分とする薄膜について 外観の観察を行つたがクラックゃ薄膜導電性材料との界面における剥離などの不具合は特に見 当たらず良好な外観状態であり、 本発明による材料を用いた薄鹏電性材料は窒化ガリウム、 窒化インジウム、 窒化アルミニウムのうちから選ばれた少なくとも 1種以上を主成分とする各 種組成の薄膜と良好な接合性を有していることが萑認された。 また薄膜導電性材料と窒化ガリ ゥム、 窒化インジウム、 窒化アルミニウムのうちから選ばれた少なくとも 1種以上を主成分と する各 ®組成の薄膜との接合性を確認するためにさらに次のテストを行った。そのテスト法は、 作製した基板にエポキシ樹脂で直径 3 mmの円形アルミニウムピンを接着し垂直引っ張り強度 を測定したがすべて垂直引っ張り強度が 2 K gZmm2以上であり、剥離モ一ドはエポキシ棚旨 と窒化ガリウム、 窒化インジウム、 窒化アルミニウムのうちから選ばれた少なくとも 1種以上 を主成分とする各種組成の薄膜との接着界面あるいはエポキシ樹脂とピントの接着界面あるい はエポキシ樹脂内部であり、 薄膜導電性材料と窒化ガリウム、 窒化インジウム、 窒化アルミ二
ゥムのうちから選ばれた少なくとも 1種以上を主成分とする各種組成の薄膜との間での剥離や 破壊は見られず良好な接合性が形成されていることが確認された。 さらに作製した基板に粘着 テ―プを接着しそのテープを弓 1き剥が 法で接合性のテストを行ったがすべて薄藤電性材 料と窒化ガリウム、 窒化インジウム、 窒化アルミニウムのうちから選ばれた少なくとも 1種以 上を主成分とする各種組成の薄膜との間での剥離や破壊は見られなかった。
また、 導通ビアが形成されている実験 N o . 7 3の焼糸吉体、 実験 N o . 7 5の焼結体、 実験 N o . 8 0の焼結体、 実験 N o . 8 2の焼結体、 実験 N o . 3 0 5の焼結体、 実験 N o . 3 1 1の焼結体、 実験 N o . 3 1 7の焼結体を用いて作製した導電性を有する窒化ガリウム、 窒化 インジウム、 窒化アルミニウムのうちから選ばれた少なくとも 1種以上を主成分とする薄膜は 該薄膜が形成されていない基板面と導通があり本実施例で作製した薄廳電性材料と窒化ガリ ゥム、 窒化インジウム、 窒化アルミニウムのうちから選ばれた少なくとも 1種以上を主成分と する薄膜とは機械的な接合性だけでなく電気的にも接続されていることが ϋ認された。 これら の結果を表 1 7に記した。 本実施例で作製した薄麟電性材料のうちチタン、 クロム、 エッケ ル、 モリブデン、 タングステン、 白金、 アルミニウム、 タンタル、 窒化チタン、 金、 銅は室温 における抵抗率はすべて 1 X 1 0— 3 Ω · c m以下でありドーピング剤を加えるなどして得られ る導電性の窒化ガリウム、 窒化インジウム、 窒化アルミニウムのうちから選ばれた少なくとも 1種以上を主成分とする各種組成の薄膜よりも高い導電性を有しているので、 本発明による薄 麟電性材料を用いることで導電性を有する窒化ガリウム、 窒化インジウム、 窒化アルミニゥ ムのうちから選ばれた少なくとも 1種以上を主成分とする薄膜と該薄膜が形成されていない基 板面とはさらに高い導通性が得られる。 また本発明による薄!^電性材料を電気回路パターン として形成した薄膜形成用基板いて例えば該薄膜形成用基板上に発光素子などの機能^?を形 成すれば、 発光素子を搭載するための回路基板あるいはパッケージ一体型の基板としても機能 する。 したがって通常であれば発光素子などの機能素子を搭載するための回 S縫板あるいはパ ッケージが必要であるが本発明による機能一体型の基板を用いることで回路基板あるい ¾Λ°ッ ケージを別に用意する必要がなくなるという効果が得られる。
上記各結果を表 1 7にまとめて示した。
実施例 1 9
焼結体作製用原料粉末として高繊窒化アルミニウム粉末 (徳山曹達株式会社 (現:株式会 社トクャマ) 製 「Η」 グレード) を用意した。 この原料粉末は酸化物;! ¾法にて製造されたも のである。 この原料粉末は不純物として酸素を 0. 8重量%含む。 この原料粉末に ¾i:希土類 元素化合物、 アルカリ土類金属化合物、 アルミナ、 遷移金属化合物、 アルカリ金属化合物、 珪 素化合物、 などを加えエタノールとともにポールミルで 2 4時間混合後草 しエタノールを揮 散した後パラフィンワックスを粉末混合体に対して 5重量%加え成形用粉末を作製し、 直径 3 6 mmX厚み 2. 0 mmの円形成形体を一軸プレス成形により得た。 その後減圧下 3 0 0 °Cで パラフィンワックスを脱脂し、 被 «物である各種組成の粉末成形体を窒化アルミニウム製の セッタ一及びさやに入れ、 あるいは上記被焼成物をタングステン製、 BN製、 窒化ほう素粉末 を表面にコーティングしたカーボン製のセッ夕一及びさやに入れ該セッ夕一及びさやには別に 用意した窒化アルミニウムだけからなる粉末成形体を同時に置いて窒素雰囲気中で常圧舰し 各種組成の窒化アルミニウムを主成分とする焼結体を得た。 賊は希土 素化合物及びアル カリ土類金属化合物を焼結助剤として加えた粉末成形体は 1 8 0 0 °CX 2時間で行った。また、 希土 IS¾素化合物及びアルカリ土類金属化合物を加えない粉末成形体は 1 9 5 0 °CX 2時間で 焼成した。 得られた焼結体はすべて相対密度 9 5 %以上に緻密ィ匕している。
次に得られた焼結体を直径 2 5. 4mmX厚み 0. 5 mmの寸法に研削、 さらに表面を実施 例 8と同様の粒径 0. 2 zmの酸化クロムを主成分とする研麟 Uによる方法で鏡面研勵ロェし
各種窒化アルミニウムを主成分とする焼結体の全酸素量、 AL ON量、 実施例 2と同様の方法 で波長 6 0 5 nmの光に対する ½¾i率の測定を行った。 また、 一部のサンプルでは熱伝導率 の測定も行った。 この測定結果を表 1 8〜表 2 3に示す。 得られた各 S¾化アルミニウムを主 成分とする焼結体において、 本実施例において粉末成形体に含まれる不純物あるいは加えられ る各種添加物の量は、 実際含まれる不純物あるいは加えられる化合物を酸化物騰あるいは元 素^^したものである。 本実施例で作製した窒化アルミニウムを主成分とする焼結体には原料 粉末中の不純物酸 ^添加した A 1 203に起因する酸素成分、 あるいは添加した希土類 素化 合物及びアル力リ土類金属化合物などの焼結助剤中の金属成分や酸素成分など、 あるいは添加 したアル力リ金属化合物及び ^有化合物中の金属成分や酸素成分など、 あるいは添加した M o、 W、 V、 N b、 T a、 T iの各遷移金属を含む化合物及びカーボンを含む化合物中の金 属成分や力一ボン成分など、 あるいは添加した F e、 N i、 C r、 Mn、 Z r、 H f、 C o、 C u、 Z nなどの不可避金属を含む化合物中の金属成分などは焼成により殆ど揮散 ·除去され ないで粉末成形体中と殆ど同じ量存在していることが確認された。 すなわち、 不純物量及び添 加物量として上記購値を用いたとき、 本実施例において作製された窒化アルミニウムを主成 分とする焼結体中の不純物あるいは添加物の量〖謝末成形体中に含まれる不純物あるいは添加 物の量との差は小さく殆ど同量と見なし得る。 したがって得られた窒化アルミニウムを主成分 とする焼結体の組成としては全酸素量以外特に各表には記載してない。 上記窒化アルミニウム を主成分とする焼結体を作製するとき添加した A 1 203量は酸化物換算により算定したもので あり (すなわち特に騰せずそのままの *)、 窒化アルミニウムを主成分とする能結体中の酸素 量は元素換算で測定したものである。 表 1 8には添加物として A 1 2〇3を単独に用いた例と、 及び A 1 203と希土類 素化合物あるいはアルカリ土類金属化合物とを同時に加えた例も示し てある。 表 1 9には添加物として希土類 素化合物、 アルカリ土類金属化合物をそれぞ ^独 であるいは同時に用いた例が示してある。 表 1 9の実験例では室温における熱伝導率の測定結 果も示されている。 表 2 0には添加物として逢 有化合物と、 アル力リ金属化合物を用いた 例が示してある。 また、 表 2 0には珪素含有化合物と希土 素化合物あるいはアル力リ土類 金属化合物とを同時に加えた例も示してある。 また、 表 2 0にはアルカリ金属化合物と希土類 元素化合物あるいはアルカリ土類金属化合物とを同時に加えた例も示してある。 表 2 1には添 加物として Mo、 W、 V、 N b、 T a、 T iの各遷移金属成分、 及び力一ボンを用いた例が示 してある。 表 2 2には M o、 W、 V、 N b、 T a、 T iの各遷移金属成分及びカーボンと希土 類元素化合物あるいはアルカリ土類金属化合物とを同時に加えた例が示してある。 表 2 3には 添加物として鉄、 ニッケル、 クロム、 マンガン、 ジルコニウム、 ハフニウム、 コバル卜、 銅、 亜鉛の各成分を用いた例が示してある。 また、 表 2 3には鉄、 ニッケル、 クロム、 マンガン、 ジルコニウム、 ハフニウム、 コバルト、 銅、 亜鉛の各成分と希土類 素化合物あるいはアル力 リ土類金属化合物とを同時に用いた例も示してある。 なお、 鏡面研磨後の窒化アルミニウムを 主成分とする焼結体の表面平滑性は平均表面粗さ (R a) = 3 1 nm〜3 6 nmの範囲にあつ た。
表 1 8〜表 2 3で示すように本実施例において実験 N o . 3 9 6を除いて光 ¾ii率 5 0 %以 下の窒化アルミニウムを主成分とする焼結体が得られた。 また比較的多量の酸素 (A l 2〇3と して用いた)、 あるいは希土類 素化合物及びアルカリ土類金属化合物、 あるいは珪^有化合 物及びアルカリ金属化合物、 あるいは M o、 W、 V、 N b、 T a、 T i、 カーボン、 あるいは 鉄、 ニッケル、 クロム、 マンガン、 ジルコニウム、 ハフニウム、 コバルト、 銅、 亜鉛、 を含む ものは光 ¾1率が 1 0 %以下に低下しやすく、 率が 0 %のものも容易に得られた。 表 1
9に示した実験例で作製した窒化アルミニウムを主成分とする焼結体は本発明の範囲に属する ものすベて室温における熱伝導率は 5 0 WZmK以上であり、 最大 1 7 7 WZmKであつた。
次に得られた窒化アルミニウムを主成分とする焼結体を基板として用い実施例 1及び実施例 2と同様の高周波加熱による MO CVD (有機金属化学気相分解) 装置を用いた方法により窒 化ガリウム、 窒化インジウム、 窒化アルミニウムを主成分とする薄膜を基板表面に形成した。 得られた薄膜は C u K a特性 X線を用いた X線回折により結晶性の 面を行った。
その結果表 1 8に示す A 1 203を添加剤として用いた実験例において、 表 1 8に示すように AL ON量が 7 %以下の窒化アルミニウムを主成分とする焼結体においてはミラ一指数 ( 0 0 2 ) の格子面の X線回折ロッキングカーブの半値幅が 2 0 0秒以下の結晶性を有する窒化ガリ ゥム、 窒化インジウム、 窒化アルミニウムを主成分とする単結晶薄膜が形成できた。 また、 A L ON量が 1 2 %以下の窒化アルミニウムを主成分とする焼結体においてはミラ一指数 ( 0 0 2 ) の格子面の X線回折口ッキング力一ブの半値幅が 2 4 0秒以下の結晶性を有する窒化ガリ ゥム、 窒化インジウム、 窒化アルミニウムを主成分とする単結晶薄膜が形成できた。 また、 A L ON量が 2 0 %以下の窒化アルミニウムを主成分とする焼結体においてはミラー指数 ( 0 0 2) の格子面の X線回折ロッキングカーブの半値幅が 3 0 0秒以下の結晶性を有する窒化ガリ ゥム、 窒化インジウム、 窒化アルミニウムを主成分とする単結晶薄膜が形成できた。 また、 酸 素量が 3 %重量以下の窒化アルミニウムを主成分とする焼結体においてはミラ一指数 ( 0 0 2) の格子面の X線回折ロッキングカーブの半値幅が 2 0 0秒以下の結晶性を有する窒化ガリウム、 窒化インジウム、 窒化アルミニウムを主成分とする単結晶薄膜が形成できた。 また、 酸素量が 5重量%以下の窒化アルミニウムを主成分とする焼結体においてはミラー指数 (0 0 2) の格 子面の X線回折ロッキングカーブの半値幅が 2 4 0秒以下の結晶性を有する窒化ガリウム、 窒 化インジウム、 窒化アルミニウムを主成分とする単結晶薄膜が形成できた。 また、 酸素量が 1 0重量%以下の窒化アルミニウムを主成分とする焼結体においてはミラー指数 (0 0 2 ) の格 子面の X線回折ロッキングカープの半値幅が 3 0 0秒以下の結晶性を有する窒化ガリウム、 窒 化ィンジゥム、 窒化アルミニウムを主成分とする単結晶薄膜が形成できた。
窒化アルミ二ゥムを主成分とする焼結体中の全酸素量が多くなるにしたがつて A L O Nの含 有量も増加し全酸素量が 1 0重量%より多くなると AL ONの含有量も 2 0 %より多くなるが 窒化ガリウム、 窒化インジウム、 窒化アルミニウムを主成分とする単結晶薄膜が形成できた。 さらに窒化アルミニウムを主成分とする焼結体中の全酸素量が 2 5重量%より多くなると AL ONの含有量も 5 0 %より多くなり窒化アルミニウムを主成分とする焼結体に形成される窒化 ガリウム、 窒化インジウム、 窒化アルミニウムを主成分とする薄膜は多結晶ィ匕し単結晶薄膜の 形成が困難になり易い。 また、 A 1 2〇3を戦で添加したものより希土類沅素化合物あるいは アル力リ土類金属化合物とを同時に加えた作製した窒化アルミニゥムを主成分とする焼結体を 用いた方が形成される窒化ガリウム、 窒化インジウム、 窒化アルミニウムを主成分とする単結 晶薄膜の結晶性は向上することが確かめられた。
また、 表 1 9に示す希土贩素化合物、 アルカリ土類金属化合物を添加剤として用いた実験 例において、 窒化アルミニウムを主成分とする焼結体中の希土類 素成分の含有量カ壞化物換 算で 7体積%まではミラー指数 (0 0 2 ) の格子面の X線回折ロッキングカーブの半値幅が 2 0 0秒以下の結晶性を有する窒化ガリウム、 窒化インジウム、 窒化アルミニウムを主成分とす る単結晶薄膜が形成できた。 また希土類元素成分の含有量が 化物換算で 1 2体積%まではミ ラー指数 (0 0 2 ) の格子面の X線回折ロッキングカーブの半値幅が 2 4 0秒以下の結晶性を 有する窒化ガリウム、 窒化インジウム、 窒化アルミニウムを主成分とする単結晶薄膜が形成で きた。 また、 希土 素成分の含有量力職化物騰で 2 5体積%まではミラ一指数 ( 0 0 2 ) の格子面の X線回折ロッキング力一ブの半値幅が 3 0 0秒以下の結晶性を有する窒化ガリウム、 窒化インジウム、 窒化アルミニウムを主成分とする単結晶薄膜が形成できた。 また、 窒化アル ミニゥムを主成分とする焼結体中のアル力リ土類金属成分の含有量力職化物騰で 3 t%ま
ではミラ一指数 (0 0 2 ) の格子面の X線回折ロッキングカーブの半値幅が 2 0 0秒以下の結 晶性を有する窒化ガリウム、 窒化インジウム、 窒化アルミニウムを主成分とする単結晶薄膜が 形成できた。 また、 窒化アルミニウムを主成分とする焼結体中のアルカリ土類金属成分の含有 量が 化物換算で 5体積%まではミラー指数 (0 0 2 ) の格子面の X線回折ロッキングカーブ の半値幅が 2 4 0秒以下の結晶性を有する窒化ガリウム、 窒化インジウム、 窒化アルミニウム を主成分とする単結晶薄膜が形成できた。 また、 窒化アルミニウムを主成分とする焼結体中の 希土類沅素成分、 アル力リ土類金属成分の含有量が ¾化物換算でそれぞれ 2 5鎌%まではミ ラー指数 ( 0 0 2 ) の格子面の X線回折ロッキングカーブの半値幅が 3 0 0秒以下の結晶性を 有する窒化ガリウム、 窒化インジウム、 窒化アルミニウムを主成分とする単結晶薄膜が形成で きた。 焼結体中の希土類 素成分、 アルカリ土類金属成分の含有量が多くなるにしたがって窒 化ガリウム、 窒化インジウム、 窒化アルミニウムを主成分とする単結晶薄膜の結晶性が低下す る傾向がある。 窒化アルミニウムを主成分とする焼結体中の希土類 素成分、 アルカリ土類金 属成分の含有量が ¾化物騰でそれぞれ 5 0髓%より多くなると窒化ガリウム、 窒化インジ ゥム、窒化アルミニウムを主成分とする薄膜は多結晶化し単結晶薄膜の形成が困難になり易い。 また、 同じ添加量であれば希土 素化合物、 アルカリ土類金属化合物をそれぞれ戦で添加 したものより希土類元素化合物あるいはアル力リ土類金属化合物とを同時に加えた作製した窒 化アルミニウムを主成分とする瓛吉体を用いた方が形成される窒化ガリゥム、窒化ィンジゥム、 窒化アルミニウムを主成分とする単結晶薄膜の結晶性は向上すること力鳩かめられた。
表 2 0に示すアルカリ金属化合物及び 素化合物を添加剤として用いた実験例において、 窒 化アルミニウムを主成分とする焼結体中のアルカリ金属及ぴ 素成分の含有量が ¾化物換算で それぞれ 5体積%まではミラ一指数 (0 0 2 ) の格子面の X線回折口ッキングカーブの半値幅 が 2 4 0秒以下の結晶性を有する窒化ガリウム、 窒化インジウム、 窒化アルミニウムを主成分 とする単結晶薄膜が形成できた。 また、 窒化アルミニウムを主成分とする焼結体中のアルカリ 金属及び珪素成分の含有量が ¾化物換算でそれぞれ 1 0体積%まではミラ一指数 ( 0 0 2) の 格子面の X線回折ロッキングカーブの半値幅が 3 0 0秒以下の結晶性を有する窒化ガリウム、 窒化インジウム、 窒化アルミニウムを主成分とする単結晶薄膜が形成できた。 焼結体中のアル 力リ金属成分及び 素成分の含有量が多くなるにしたがって窒化ガリゥム、 窒化ィンジゥム、 窒化アルミニウムを主成分とする単結晶薄膜の結晶性が低下する傾向がある。 窒化アルミニゥ ムを主成分とする焼結体中のアルカリ金属成分及び 素成分の含有量が 化物膜でそれぞれ
2 0積%より多くなると窒化ガリウム、 窒化インジウム、 窒化アルミニウムを主成分とする薄 膜は多結晶化し単結晶薄膜の形成が困難になり易い。 また、 アルカリ金属成分及ぴ 素成分を それぞォ 虫で添加したものより希土類 素化合物あるいはアル力リ土類金属化合物とを同時 に加えた作製した窒化アルミニウムを主成分とする焼結体を用いた方が形成される窒化ガリウ ム、 窒化インジウム、 窒化アルミニウムを主成分とする単結晶薄膜の結晶性は向上することが 確かめられた。
表 2 1に示す M o、 W、 V、 N b、 T a、 T iの各遷移金属成分、 及びカーボンを添加剤と して用いた実験例において、窒化アルミニウムを主成分とする焼結体中の Mo、 W、 V、 Nb、 T a、 T iの各遷移金属成分、 及びカーボンの含有量が元素 »でそれぞれ 5体積%まではミ ラー指数 (0 0 2 ) の格子面の X線回折ロッキングカーブの半値幅が 2 0 0秒以下の結晶性を 有する窒化ガリウム、 窒化インジウム、 窒化アルミニウムを主成分とする単結晶薄膜が形成で きた。 また、 窒化アルミニウムを主成分とする焼結体中の M o、 W、 V、 N b、 T a、 T iの 各遷移金属成分、及び力一ボンの含有量が元素露でそれぞれ 1 0髓%まではミラー指数(0 0 2 ) の格子面の X線回折ロッキングカーブの半値幅が 2 4 0秒以下の結晶性を有する窒化ガ リゥム、 窒化ィンジゥム、 窒化アルミニゥムを主成分とする単結晶薄膜が形成できた。 また、
窒化アルミニウムを主成分とする焼結体中の M o、 W、 V、 N b、 T a、 T iの各遷移金属成 分、 及び力一ボンの含有量が元素騰でそれぞれ 2 5籠%まではミラー指数 ( 0 0 2) の格 子面の X線回折ロッキングカーブの半値幅が 3 0 0秒以下の結晶性を有する窒化ガリウム、 窒 化インジウム、 窒化アルミニウムを主成分とする単結晶薄膜が形成できた。 窒化アルミニウム を主成分とする焼結体中の M o、 W、 V、 N b、 T a、 T iの各遷移金属成分、 及び力一ボン の含有量が多くなるにしたがって窒化ガリウム、 窒化インジウム、 窒化アルミニウムを主成分 とする単結晶薄膜の結晶性が低下する傾向がある。 窒化アルミニウムを主成分とする焼結体中 の M o、 W、 V、 N b、 T a、 T iの各遷移金属成分、 及び力一ボンの含有量が元素騰でそ れぞれ 5 (H稀%より多くなると窒化ガリウム、 窒化インジウム、 窒化アルミニウムを主成分 とする薄膜は多結晶化し単結晶薄膜の形成が困難になり易い。
表 2 2に示すM o、 W、 V、 N b、 T a、 T iの各遷移金属成分、 及びカーボンと希土類 素化合物あるいはアル力リ土類金属化合物とを同時に添加剤として加えた実験例において、 窒 化アルミニウムを主成分とする焼結体が M o、 W、 V、 N b、 T a、 T iの各遷移金属成分、 及びカーボン各成分を元素換算でそれぞれ 2 5体積%までの比較的多量に含むものであっても ミラ一指数 ( 0 0 2 ) の格子面の X線回折ロッキングカーブの半値幅が 2 4 0秒以下の結晶性 を有する窒化ガリウム、 窒化インジウム、 窒化アルミニウムを主成分とする単結晶薄膜が形成 でき明確に結晶性の向上が確認された。
表 2 3に示す鉄、 ニッケル、 クロム、 マンガン、 ジルコニウム、ノ、フニゥム、 コバルト、銅、 亜鉛の各成分を添加剤として用いた実験例において、 窒化アルミニウムを主成分とする焼結体 中の鉄、 ニッケル、 クロム、 マンガン、 ジルコニウム、 ハフニウム、 コノルト、 銅、 の各 遷移金属成分の含有量がそれぞれ元素 で 1 0重量%まではミラー指数 ( 0 0 2 ) の格子面 の X線回折ロッキングカーブの半値幅が 2 0 0秒以下の結晶性を有する窒化ガリウム、 窒化ィ ンジゥム、 窒化アルミニウムを主成分とする単結晶薄膜が形成できた。 また、 窒化アルミニゥ ムを主成分とする焼結体中の鉄、 ニッケル、 クロム、 マンガン、 ジルコニウム、 ハフニウム、 コバルト、 銅、 亜鉛の各遷移金属成分の含有量が元素換算でそれぞれ 2 0重量%まではミラ一 指数 ( 0 0 2 ) の格子面の X線回折ロッキングカーブの半値幅が 2 4 0秒以下の結晶性を有す る窒化ガリウム、窒化インジウム、窒化アルミニウムを主成分とする単結晶薄膜が形成できた。 また、 窒化アルミニウムを主成分とする焼結体中の鉄、 ニッケル、 クロム、 マンガン、 ジルコ 二ゥム、 ハフニウム、 コバルト、 銅、 亜鉛の各遷移金属成分の含有量が元素露でそれぞれ 3 0重量%まではミラ一指数 (0 0 2 ) の格子面の X線回折ロッキングカーブの半値幅が 3 0 0 秒以下の結晶性を有する窒化ガリウム、 窒化インジウム、 窒化アルミニウムを主成分とする単 結晶薄膜が形成できた。 焼結体中の鉄、 ニッケル、 クロム、 マンガン、 ジルコニウム、 ハフ二 ゥム、 コバルト、 銅、 亜鉛の各遷移金属成分の含有量が多くなるにしたがって窒化ガリウム、 窒化ィンジゥム、窒化アルミニウムを主成分とする単結晶薄膜の結晶性が低下する傾向がある。 窒化アルミニウムを主成分とする焼結体中の鉄、ニッケル、 クロム、マンガン、 ジルコニウム、 ハフニウム、 コバルト、 銅、 亜鉛の各遷移金属成分の含有量が元素換算でそれぞれ 5 0重量% より多くなると窒化ガリウム、 窒化インジウム、 窒化アルミニウムを主成分とする薄膜は多結 晶化し単結晶薄膜の形成が困難になり易い。 また、 鉄、 ニッケル、 クロム、 マンガン、 ジルコ 二ゥム、 ハフニウム、 コバルト、 銅、 亜鉛の各遷移金属成分をそれぞ 独で添加したものよ り希土観素化合物あるいはアル力リ土類金属化合物とを同時に加えて作製した窒化アルミ二 ゥムを主成分とする焼結体を用いた方が形成される窒化ガリウム、 窒化インジウム、 窒化アル ミ二ゥムを主成分とする単結晶薄膜の結晶性は明らかに向上することが確かめられた。
本実施例において得られた薄膜のうち単結晶薄膜の観察を光学顕微鏡、 電子顕微鐘を用いて 行つたが単結晶薄膜内部にはクラックが見られず単結晶薄膜と窒化アルミ二ゥムを主成分とす
る焼結体との接合界面での剥離も見られない。 得られた上記単結晶薄膜に粘着テープを接着し 引き剥がしテストを行ったが該単結晶薄膜と窒化アルミニウムを主成分とする焼結体との接合 界面での剥離や破壊は見られなかった。
実施例 2 0
実施例 1 8で使用した導通ビアを有する窒化アルミニウムを主成分とする焼結体及び導通ビ ァのなレ窒化アルミニウムを主成分とする焼結体及 ^施例 1 1で作製した実験 N o. 2 6 5、 実験 N o. 2 6 9、 実験 N o. 2 7 1の窒化アルミニウムの續を高めた各焼結体を鏡丽磨 した直径 2 5. 4mmX厚み 0. 5 mmの寸法の基板状に加工したものを用いて実施例 1、 実 施例 2、 実施例 1 0及び実施例 1 2と同様の方法で各種組成及び各種結晶状態を有する窒化ガ リウム、 窒化インジウム、 窒化アルミニウムのうちから選ばれた少なくとも 1種以上を主成分 とする薄膜を上記各焼結体の片面に厚み 3 mで形成し各種薄膜基板を作製した。 この薄膜の 組成及び結晶状態については表 2 4に示す通りである。 さらに別に実施例 1 8で作製したチタ ン、 クロム、 ニッケル、 モリブデン、 タングステン、 白金、 アルミニウム、 タンタル、 窒化タ ンタル、 窒化チタン、 金、 銅、 タングステン Z銅合金 (W : 9 0重量% + C u 1 0重量%) な ど各種導電性材料があらかじめ形成された窒化アルミニウムを主成分とする焼結体からなる基 板に、 さらに窒化ガリウム、 窒化インジウム、 窒化アルミニウムのうちから選ばれた少なくと も 1種以上を主成分とする薄膜が形成された薄膜基板も用意した。 実施例 1 8で作製した薄膜 基板についてその薄藤成及び結晶状態は実施例 1 8と同じであるが、 あらためて表 2 5に再 掲載した。
次に上記のようにして作製あるいは準備した薄膜基板を用い該薄膜基板に形成されている窒 化ガリウム、 窒化インジウム、 窒化アルミニウムのうちから選ばれた少なくとも 1種以上を主 成分とする薄膜の上に実施例 1 8と同様の方法でチタン、 クロム、 ニッケル、 モリブデン、 夕 ングステン、 白金、 アルミニウム、 タンタル、 窒化タンタル、 窒化チタン、 金、 銅などからな る各種薄膜導電性材料を形成した。 この各種薄騰電性材料の構成及び厚みについては表 2 4 及び表 2 5に記載された通りである。 各種薄膜導電性材料を形成後、 用いた薄膜基板に形成さ れている窒化ガリウム、 窒化インジウム、 窒化アルミニウムのうちから選ばれた少なくとも 1 種以上を主成分とする薄膜について外観の観察を行つたがクラックゃ薄 電性材料との界面 における剥離などの不具合は特に見当たらず良好な外観状態であり、 本発明による材料を用い た薄騰電性材料は窒化ガリウム、 窒化インジウム、 窒化アルミニウムのうちから選ばれた少 なくとも 1種以上を主成分とする各種組成の薄膜と良好な接合性を有していること力鳩認され た。 また薄鹏電性材料と窒化ガリウム、 窒化インジウム、 窒化アルミニウムのうちから選ば れた少なくとも 1種以上を主成分とする各種組成の薄膜との接合性を確認するためにさらに次 のテストを行った。 そのテスト法は、 作製した基板表面に形成されている薄膜導電性材料にェ ポキシ樹脂で直径 3mmの円形アルミニウムピンを接着し垂直引っ張り強度を測定したがすべ て垂直弓 Iつ張り強度が 2 Kg Zmm2以上であり、 剥離モードはエポキシ樹脂と窒化ガリウム、 窒化インジウム、 窒化アルミニウムのうちから選ばれた少なくとも 1種以上を主成分とする各 種組成の薄膜との接着界面あるいはエポキシ樹脂とピン卜の接着界面あるいはエポキシ樹脂内 部であり、 薄膜導電性材料と窒化ガリウム、 窒化インジウム、 窒化アルミニウムのうちから選 ばれた少なくとも 1種以上を主成分とする各種組成の薄膜との間での剥離や破壊は見られず良 好な接合性が形成されていることが 認された。 なお形成した薄 電性材料のうち表面に金 及び銅を有する構成のもの (実験 N o. 4 9 4〜4 9 7、 5 0 0、 5 0 2〜5 0 4、 5 1 2〜 5 1 5の各サンプル) については先端に直径 1. 5 mmのパッドを有するコノール製リードを 用いはんだによって該リードと薄 電性材料とを接続して垂直引張り強度を測定した。 その 結果垂直引張り弓鍍はすべて 4 Kg Zmm2以上であり、弓鍍試験後のリ一ド及ぴ 膜基板のリ
ードが接合された部分を観察したところすベてはんだ内あるいははんだとリード間の部分で破 壊しており窒化ガリウム、 窒化インジウム、 窒化アルミニウムのうちから選ばれた少なくとも 1種以上を主成分とする薄膜と薄膜導電性材料との間の剥離や破壊は観察されなかった。 この ことは薄膜導電性材料と上記薄膜との接合強度は本来少なくともを 4 K g/mm2以上で接合 性の高いものであることが歸忍された。 さらに作製した基板表面に形成されている薄 J ^電性 材料に粘着テープを接着しそのテープを引き剥がす方法で接合性のテストを行ったがすべて薄 膜導電性材料と窒化ガリゥム、 窒化ィンジゥム、 窒化アルミニゥムのうちから選ばれた少なく とも 1種以上を主成分とする各種組成の薄膜との間での剥離や破壊は見られなかった。
上記試験結果は薄膜導電性材料と窒化ガリウム、 窒化インジウム、 窒化アルミニウムのうち から選ばれた少なくとも 1種以上を主成分とする薄膜との接合性が高いということだけでなく、 窒化アルミニウムを主成分とする焼結体と薄膜導電性材料との接合性及び窒化アルミニウムを 主成分とする焼結体と窒化ガリウム、 窒化インジウム、 窒化アルミニウムのうちから選ばれた 少なくとも 1種以上を主成分とする薄膜との接合性も高いものであることを証明している。 こ れらの結果を表 2 4及び表 2 5に記した。
また、 本実施例においても導通ピアが形成されている実験 N o . 7 3の焼結体、 実験 N o . 7 5の焼結体、 実験 N o . 8 0の焼結体、 実験 N o . 8 2の焼結体、 実験 N o . 3 0 5の焼結 体、 実験 N o . 3 1 1の焼結体、 実験 N o. 3 1 7の焼結体を用いて作製した導電性を有する 窒化ガリウム、 窒化インジウム、 窒化アルミニウムのうちから選ばれた少なくとも 1種以上を 主成分とする薄膜は該薄膜が形成されていない基板面と導通があり本実施例で作製した薄膜導 電性材料と窒化ガリウム、 窒化インジウム、 窒化アルミニウムのうちから選ばれた少なくとも 1種以上を主成分とする薄膜とは機械的な接合性だけでなく電気的にも接続されていることが 確認された。 本実施例で作製した薄膜導電性材料のうちチタン、 クロム、 ニッケル、 モリブデ ン、 タングステン、 白金、 アルミニウム、 タンタル、 窒化チタン、 金、 銅は室温における抵抗 率はすべて 1 X 1 0 -3 Ω · c m以下でありドーピング剤を加えるなどして得られる導電性の窒 化ガリウム、 窒化インジウム、 窒化アルミニウムのうちから選ばれた少なくとも 1種以上を主 成分とする各種組成の薄膜よりも高い導電性を有しているので、 本発明による薄膜導電性材料 を用いることで導電性を有する窒化ガリウム、 窒化インジウム、 窒化アルミニウムのうちから 選ばれた少なくとも 1種以上を主成分とする薄膜と該薄膜が形成されていなレゝ基板面とはさら に高い導通性が得られる。 また本発明による薄 電性材料を電気回路パターンとして形成し た薄膜形成用基板いて例えば該薄膜形成用基板上に発光素子などの機能 »を形成すれば、 発 光鮮を搭載するための回 s§s板あるいはパッケージ一体型の基板としても機能する。 したが つて通常であれば発光素子などの機能素子を搭載するための回路基板あるいはパッケージが必 要であるが本発明による機能一体型の基板を用いることで回路基板あるいはパッケージを別に 用意する必要がなくなるという効果が得られる。
実施例 2 1
実施例 2において作製した実験 N o . 4 9と実験 N o . 5 8、 及び実施例 1 1において作製 した実験 N o . 2 6 9の各窒化アルミニウムを主成分とする焼結体を直径 2 5. 4mmX厚み 0. 5mmの寸法の基板状に加工しさらに鏡面研磨して、 その上に実施例 1、 実施例 2、 実施 例 1 0及び実施例 1 2で用いたのと同じ MO CVD法により窒化ガリウム、 窒化インジウム、 窒化アルミニウムのうちから選ばれた少なくとも 1種以上を主成分とする各種組成の薄膜を 6 の厚みで形成し薄膜基板を作製した。 また、 ニオブ及びタンタルを含む窒化ガリウム、 窒 化インジウム、 窒化アルミニウムのうちから選ばれた少なくとも 1種以上を主成分とする各種 組成の薄膜も形成した。 ニオブ及び夕ンタルを含む薄膜は実施例 9と同様のク口ライド V P E 法により厚み 6 mで形成した。 ニオブ及びタンタル成分の原料として塩化ニオブ及び塩化夕
ン夕ルを用いた。 これら薄膜は単結晶、 無定形、 配向性多結晶の各結晶状態となるよう形成し た。 なお、 単結晶薄膜を形成するに際してはすべての窒化アルミニウムを主成分とする焼結体 からなる基板にはあらかじめ該基板面対して C軸が垂直な方位を有する実質的に 1 0 0モル% A 1 N組成からなる配向性多結晶薄膜を上記 MO CVD法で厚み 1. 0 m形成した基板を用 いた。 このような配向性多結晶薄膜の上に形成する単結晶薄膜は結晶 C軸の方位を基板面に対 し垂直に形成したものと水平に形成したものの 2種類を作製した。 単結晶以外の無定形、 配向 性多結晶の各結晶状態の薄膜はそのまま直接窒化アルミニウムを主成分とする焼結体からなる 基板に形成した。 配向性多結晶薄膜は基板面に対して C軸が垂直になるよう形成したものであ る (実験 N o. 5 4 6、 5 4 8 )。 形成した各薄膜の外観を したが 膜内のクラックゃ窒化 アルミ二ゥムを主成分とする焼結体との間の剥離などの不具合は見られなかった。 また粘着テ —プを用いて剥離テストを行ったが形成した薄膜と窒化アルミニウムを主成分とする焼結体と の間の剥離はなかった。 なお、 上記窒化アルミニウムを主成分とする焼結体からなる基板に最 初に形成された配向性多結晶 A 1 N薄膜のミラ一指数 (0 0 2 ) の格子面の X線回折ロッキン グカーブの半値幅が 4 2 7 0〜4 7 4 0秒の範囲であった。 一方上記配向性多結晶薄膜の上に 形成された単結晶薄膜の結晶性はミラー指数 ( 0 0 2 ) の格子面の X線回折ロッキングカーブ の半値幅がすべて 3 0 0秒以下であった。
次に形成した薄膜の波長 6 5 0 nmの光に対する屈折率を米国 「S C I (S c i e n t i f i c C omp u t i n g I n t e r n a t i o n a l ) 社」 製の分光光度計 (S p e c t r o p h o t ome t e r ) 「製品名: F i 1 mT e k 4 0 0 0」 を用いて調べた。単結晶薄膜 の結晶 C軸を基板面に対して垂直に形成した薄膜の屈折率は C軸に平行な方向 (すなわち異常 光) の屈折率を、 結晶 C軸を基板面に対して水平に形成した薄膜の屈折率は C軸に垂直な方向 (すなわち常光) の屈折率を測定した。 その結果、 窒化ガリウム、 窒化インジウム、 窒化アル ミニゥムのうちから選ばれた少なくとも 1種以上を主成分とする薄膜において単結晶及び無定 形いずれの結晶状態の薄膜においても、 あるいは単結晶薄膜における結晶 C軸の形成方位によ らず、 窒化ガリゥムあるいは窒化ィンジゥムの含有量が増加すれば屈折率は大きくなり、 窒化 アルミニウムの含有量が増加すれば屈折率は低下し易いこと力 雀かめられた。 また、 ニオブあ るいはタンタルの含有量力増加すれば屈折率が大きくなることが見出された。 形成された薄膜 において、 窒化アルミニウムを主成分とするものにおいて含まれる窒化ガリゥム及び窒化ィン ジゥムのうちから選ばれる少なくとも 1種以上の成分の増加量が主成分に対して 0. 0 1モ ル%以上で少なくとも 1 X 1 0 _5以上の屈折率の増加が認められ、 少なくとも 2 0モル%以下 で屈折率の増加は 2 X 1 0一1以下であった。また、形成された窒化ガリウム、窒化インジウム、 窒化アルミニウムのうちから選ばれる少なくとも 1種以上を主成分とする薄膜においてニオブ 及びタンタルのうちから選ばれる少なくとも 1種以上の成分の含有量が主成分に対して 0. 0 1モル%以上で少なくとも 1 X 1 0一5以上の屈折率の増加が認められ 2 0モル%以下であれ ば屈折率の増加は 2 X 1 0—1以下であった。
また基板面に対して C軸が水平方向に形成された単結晶薄膜の屈折率は垂直方向に形成され たものより屈折率は 0. 0 3〜0. 0 5程度小さい。
また、 無定形より多結晶の薄膜の屈折率の方が大きい傾向があるが、 どちらの結晶状態のも のも 2. 0以下であり単結晶より小さかった。
また、 実験 N o . 5 4 9〜5 7 7で作製した薄膜基板にはクロライド V P E法による薄膜が 形成されているが、 同じ組成の薄膜であっても MOCVD法で形成した薄膜と屈折率は異なり、 クロライド V P E法で作製した薄膜の方が屈折率は大きくなる傾向を示した。
これらの結果を表 2 6に示す。 なお、 表 2 6においてニオブ及びタンタル成分は窒化ニオブ 及び窒化タンタルとみなして記載した。
(比較例)
別に上記本実施例の実験 N o. 49で作製した窒化アルミ二ゥムを主成分とする焼結体から なる基板を用意し、 一部の基板はそのままに一部の基板 実施例と同じ条件で 100モル% A 1 N配向性多結晶薄膜を形成した。その後これら基板に周波数 13. 56MHzの高周波(R F) マグネトロンスパッタリング法により厚み 6. OjLimの L iNb03、 S i〇2、 A 12〇3 薄膜を形成した。 スパッタリングの条件 «S板? Jtを 250°Cとし、 Arガスを圧力 0. 6P a、 電力 1000Wで行った。 その結果、 100モル%A 1 N配向性多結晶薄膜の形成の有無 にかかわらず L i Nb〇3、 S i〇2、 A 1203いずれの薄膜にもクラックが入り光導波路とし て使用することは困難であった。
実施例 22
実施例 2において作製した実験 No. 49と実験 No. 58の窒化アルミニウムを主成分と する焼結体及び実施例 11において作製した実験 No. 269の窒化アルミニウムを主成分と する焼結体を直径 25. 4mmX厚み 0. 5 mmの寸法の基板状に加工しさらに鏡藤 if磨して、 その上に実施例 1、 実施例 2、 実施例 4、 実施例 9、 実施例 12及び実施例 21で用いたのと 同じ MOCVD法及びクロライド VP E法で窒化ガリウム、 窒化インジウム、 窒化アルミニゥ ムのうちから選ばれた少なくとも 1種以上を主成分とする各種組成及び各種結晶状態の薄膜を 形成した薄膜基板を作製した。 MOCVD法で作製した薄膜の厚みは 25 mでありクロライ ド VP E法で作製した薄膜の厚みは 100 mである。 なお、 A 1 N + GaN+ I nNの 3成 分混晶薄膜の形成に際しては基板温度 950°Cで行った。 また、 単結晶薄膜を形成するに際し てはすべての窒化アルミニウムを主成分とする焼結体からなる基板に対してあらかじめ該基板 面に対して C軸が垂直な方位を有し実質的に 100モル%の 1 Nからなる配向性多結晶薄膜 を周波数 13. 56 MHzの高周波 (RF) マグネトロンスパッタリング法により厚み 1. 0 II m形成した基板を用いた。 スパッタリングの条件は夕一ゲットとして高純度 A 1 N焼結体を 用い Ar+N2の混合ガスを N2/Ar = 0.4の混合比で導入しチヤンバ一内圧力 0. 8Pa、 電力 1000Wであった。 基板温度単結晶以外の無定形、 配向性多結晶の各結晶状態の薄膜は そのまま直接窒化アルミニウムを主成分とする焼結体からなる基板に形成した。 配向性多結晶 薄膜は基板面に対して C軸が垂直になるよう形成したものである。 また、 単結晶薄膜はすべて 基板面に対して C軸が垂直になるように形成した。 なお、 上記窒化アルミニウムを主成分とす る焼結体からなる基板に最初に形成された配向性多結晶 A 1N薄膜のミラー指数 (002) の 格子面の X線回折ロッキングカーブの半値幅が 64 0秒〜 7190秒の範囲であった。 形成 した各薄膜の外観を鹏したが薄膜内のクラックゃ窒化アルミ二ゥムを主成分とする焼結体と の間の剥離などの不具合は見られなかった。 また粘着テープを用いて剥離テストを行ったが形 成した薄膜と窒化アルミニウムを主成分とする焼結体との間の剥離はなかった。 また、 形成し た単結晶薄膜の結晶性はミラ一指数 (002) の格子面の X線回折ロッキングカーブの半値幅 がすべて 100秒以下であった。
別に市販されている 1 OmmX 1 OmmX厚み 0. 5 mmのノ ク状窒ィ匕ガリゥム単結晶を 基板として用意した。 このバルク窒化ガリゥム単結晶の結晶 C軸は基板面に対して垂直の方位 であり、 表面は鏡面に研磨してある。 さらに別途昇華法で作製した 3mmX3mmX厚み 0. 5mmのノ^レク状窒化アルミニウム単結晶を基板として用意した。 このノ^レク窒化アルミニゥ ム単結晶の結晶 C軸 板面に対して垂直の方位であり、 表面は鏡面に研磨してある。 これら 窒化ガリウムを主成分とするバルク単結晶及び窒化アルミニウムを主成分とするバルク単結晶 は不純物の含有量は少なく実質的にそれぞれ G a N及び A 1 Nからなるものであつた。
このように準備した上記薄膜基板に形成された薄膜及びバルク単結晶基板の波長 650 nm における屈折率を米国 「SC I (Sc i en t i f i c C omp u t i ng I n t e rn
a t i on a 1) ¾J 製の^ 6光度計 (Spec t ropho t ome t e r) 「製品名: F i 1 mT e k 4000」 を用いて測定した。
次にこれらの薄膜基板及びパルク単結晶基板〖こ対して金属ガリゥム、 窒化ガリゥム、 酸化ガ リウム、 金属インジウム、 窒化インジウム、 酸化インジウム、 金属ニオブ、 窒化ニオブ、 酸化 ニオブ、 金属タンタル、 窒化タンタル、 酸化タンタルの各材料からなるターゲットを用い周波 数 13. 5MHz, 電力 800Wの RFマグネトロンスパッタリング法で基板温度 250°Cに て各種薄膜を厚み 5 Onmで基 面に形成した。スパッタ用ガスとして純 Ar及び混合比 N2 /A r = 0. 02〜0. 80の範囲の N2+ A rの混合ガスを導入しチャンバ一内圧力 0. 9P aの条件で使用した。 酸化ガリウム、 酸化インジウム、 酸化ニオブ、 酸化タンタル、 金属ニォ ブ、 金属タンタルの各薄膜形成では純 A rを用いた。 窒化ガリウム、 窒化インジウム、 窒化ニ ォプ、窒化タンタルの各薄 J¾成では N2+Arの混合ガス^ t組成比を変えながら用いた。 な お、 金属ガリウム及び金属インジウムからなるターゲットはそれぞれ反応性スパッタによる窒 化ガリウム、 窒化インジウム薄膜の形成に用いた。 このようにして得られたスパッタリング薄 膜は光リソグラフィ一によるリフトオフ法を用いて幅 10 mX厚み 50 nmの大きさの線状 として残るようにパ夕一ニングした。 また、 同じスパッタリング薄膜を用い該スパッタリング 薄膜の別の部分が幅 1. 5 mmX厚み 50 nmの線状として残るようパターニングした。なお、 このパターニングしたスパッ夕薄膜の長さは窒化アルミニウムを主成分とする基板を用いたも のでは 25. 4mm、 ノルク状窒化ガリウム単結晶を用いたものでは 10mm、 バルク状窒化 アルミニウム単結晶を用いたものでは 3mmである。 次に窒素雰囲気中 1500°Cで 6時間加 熱した。 加熱 観を調べたが各薄膜と窒化アルミニウムを主成分とする焼結体との間の剥離 などの不具合は見られなかった。 また各薄膜のガリウム、 インジウム、 ニオブ、 タンタル各成 分が形成された部分の外観を観察したがクラックゃ剥離は見られなかった。 またまた粘着テ一 プを用いて剥離テストを行ったが形成した薄膜と窒化アルミニウムを主成分とする焼結体との 間の剥離、 及びガリウム、 インジウム、 ニオブ、 タンタル各成分が形成された薄膜部分の剥離 や破壊はなかった。 加熱後の各バルク単結晶に付いてもガリウム、 インジウム、 ニオブ、 タン タル各成分が形成された部分におけるクラックなど外観上の不具合は見られなかつた。
次に加熱後の薄膜基板及びバルク単結晶基板各サンプルを用いてガリウム、 インジウム、 二 ォブ、 タンタル各成分からなるスパッタリング薄膜が形成された部分のうち幅 1. 5mmのパ 夕一ニングを施した部分の波長 650 nmの光に対する屈折率を測定した。 屈折率測定は米国
「SCI (Sc i en t i f i c C omp u t i n g I n t e rna t i ona l) 社」 製の分光光度計 (Spe c t r opho t ome t e r) 「製品名: F i 1 mT e k 4000」 を用いて行った。 その結果、 はじめに作製した窒化ガリウム、 窒化インジウム、 窒化アルミ二 ゥムのうちから選ばれた少なくとも 1種以上を主成分とする薄膜及びバルク単結晶の屈折率よ りガリウム、 インジウム、 ニオブ及びタンタル成分を有するスパック薄膜を形成後熱処理した 薄膜及びバルク単結晶の屈折率が大きくなることが歸忍された。 またこの結果は、 はじめに作 製した窒化ガリゥム、 窒化ィンジゥム、 窒化アルミニゥムのうちから選ばれた少なくとも 1種 以上を主成分とする薄膜及びバルク単結晶中へガリウム、 インジウム、 ニオブ及びタンタル成 分が拡散し固溶していることを予測させる。 また、 すべてのサンプルにおいて屈折率の増加量 は 0. 002〜0. 012の範囲にあり 2X 10—1以下であった。 従ってはじめに作製した窒 化ガリウム、 窒化インジウム、 窒化アルミニウムのうちから選ばれた少なくとも 1種以上を主 成分とする薄膜及びバルク単結晶中のガリウム、 インジウム成分の増加量、 及びニオブ及び夕 ンタル成分の導入量はそれぞれ窒化ガリウム、 窒化インジウム、 窒化ニオブ、 窒化タンタル換 算で主成分に対して少なくとも 20モル%以下、 0. 1モル%〜5. 0モル%の範囲であると 思われる。 また上記分光光度計 「F i lmTek4000」 による測定で加熱後の薄 Μ¾びパ
ルク単結晶へガリウム成分、 インジウム成分、 ニオブ成分及びタンタル成分が導入された領域 は幅 1 2 xm〜l 8 xmに広がり、 深さ方向へは 0. 5 m〜l 0 mに達しているものと思 われる。
このようにして窒化アルミニウムを主成分とする焼結からなる基板に形成した窒化ガリウム、 窒化インジウム、 窒化アルミニウムのうちから選ばれた少なくとも 1種以上を主成分とする薄 膜にガリウム、 インジウム、 ニオブ、 タンタル各成分を帯状に導入した薄膜基板を得た。 また 窒化ガリウムを主成分とするバルク単結晶及び窒化アルミニウムを主成分とするバルク単結晶 それぞれにガリウム、 インジウム、 ニオブ、 タンタル各成分を帯状に導入したバルク単結晶基 板を得た。
次に上記スパッタリング薄膜により窒化ガリウム、 窒化インジウム、 窒化アルミニウムのう ちから選ばれた少なくとも 1種以上を主成分とする薄膜へガリウム、 インジウム、 ニオブ、 夕 ンタル成分が導入された部分及びバルク単結晶中へガリウム、 インジウム、 ニオブ、 タンタル 成分が導入された部分のうち、 熱処理前のスパッタリング薄膜に幅 1 0 mのパターニングを 施した部分に巿販の発光波長 6 5 O nmの G a A s P系の赤色半導体レーザーを用いて出力 5 0 mWで該赤色光を入力し透過した出力光の減衰量を測定して伝送損失を算出した。 その結果 基板の材質及び組成によらずすべてのサンプルで 6 5 0 nmの赤色光に対して ¾i 性があり伝 纖失もすベてのサンプルで 1 O d B/ c m以下であった。 また薄膜が単結晶の場合その伝送 損失はすべて 5 d BZ c m以下であった。 また窒化アルミ二ゥムを主成分とする焼結体からな る基板として実験 N o . 2 6 9を用いて形成した単結晶薄膜の伝 員失はすべて 3 d B/c m 以下であった。 また窒化アルミニウムを 8 0モル%以上含む単結晶薄膜の伝送損失はすべて 1 d BZ c m以下であった。 また窒化アルミニウムを主成分とするゾリレク単結晶でもすベてのサ ンプルで伝應失は 1 d B/ c m以下であった。この結果、本実施例で作製した窒化ガリゥム、 窒化インジウム、 窒化アルミニウムのうちから選ばれた少なくとも 1種以上を主成分とする薄 膜及びバルク単結晶中へガリウム、 インジウム、 ニオブ、 タンタル成分が混入した部分は埋め 込み型の三次元光導波路として機能することが ϋ認された。 これらの結果を表 2 7に示した。 表 2 7には波長 6 5 0 n mの光を用いて測定した伝送損失の値が示されている。
次に、 上記赤色光による光伝送を確認後さらに市販の波長可変レーザ一光発生装置を用い本 実施例で作製した上記各三 光導波路の紫外光領域における伝醒失を測定した。 測定波長 は 3 8 0 nm、 3 0 0 nm、 2 7 0 nm、 2 5 0 nmの 4種類である。 その結果窒化アルミ二 ゥムを主成分とする焼結体からなる基板に形成された薄膜の中でも窒化アルミニウム含有量の 多い薄膜、 及び窒化アルミニウムを主成分とするバルク単結晶には紫外光に対する高い伝送性 があることが ϋ認された。 窒化ガリウム含有量の多い薄膜、 及び窒化ガリウムを主成分とする バルク単結晶が 3 8 0 nmより波長の短 光に対する伝送性を示さないのに比べて大半の窒化 アルミニウム含有量の多い薄膜、 及び窒化アルミニウムを主成分とするバルク単結晶は高い紫 外光に対する伝送性を示した。 すなわち、 窒化アルミニウムを主成分とする焼結体からなる基 板に形成された薄膜の中で窒化アルミニウムを 5 0モル%以上含む薄膜は少なくとも波長 3 0 O nmまでの紫外光が伝送できその伝還員失は 1 O d BZc m以下であった。 また、 窒化アル ミニゥムを主成分とする焼結体からなる基板に形成された薄膜の中で窒化アルミニウムを 9 0 モル%以上含む薄膜は少なくとも波長 2 7 0 nmまでの紫外光が伝送できその伝送損失は 1 0 d B/ c m以下であった。
また、 窒化アルミニウムを主成分とする焼結体からなる基板に形成された薄膜の中で窒化ァ ルミ二ゥムを主成分としさらに窒化ガリゥムを含む 2成分組成の薄膜において窒化アルミニゥ ムを 5 0モル%以上含むものは少なくとも波長 3 0 0 nmまでの紫外光が伝送できその伝送損 失は 1 O d BZ c m以下であった。 また上記薄膜が単結晶の場合伝送損失は少なくとも 5 d B
/ c m以下であり、 本実施例において実験 N 0. 5 9 0で作製した窒化アルミ二ゥムを 5 0モ ル%含む単結晶薄膜が形成された薄膜基板に形成された光導波路では 2. 4 d BZ c mと 3 d
BZc m以下であった。 また、 窒化アルミニウムを 8 0モル%以上含むものは少なくとも波長 2 7 0 nmまでの紫外光が伝送できその伝送損失は 1 0 d BZ c m以下であった。 また上記薄 膜が単結晶の場合伝送損失は少なくとも 5 d BZ c m以下であり本実施例において実験 N o . 5 8 9で作製した窒化アルミニウムを 8 0モル%含む単結晶薄膜が形成された薄膜基板では波 長 2 7 O nmの光の伝纖失は 0. 9 d B/c mと 3 d B/ c m以下であった。 また、 窒化ァ ルミ二ゥムを 9 0モル%以上含むものは少なくとも波長 2 5 0 nmまでの紫外光が伝送できそ の伝纖失は 1 0 d B / c m以下であつた。 また上記薄膜が単結晶の場合伝週失は少なくと も 5 d B / c m以下であり本実施例におレては実験 N o . 5 8 8及び実験 N o . 6 0 1で作製 した窒化アルミニウムを 9 0モル%含む単結晶薄膜が形成された薄膜基板でも波長 2 5 0 nm の光の伝 員失はそれぞれ 2. 5 d B/ c m, 2. 6 d BZc mと 3 d BZc m以下であった。 このように本発明による窒化アルミニウムを主成分とする焼結体に形成された窒化ガリゥム、 窒化ィンジゥム、 窒化アルミニウムのうちから選ばれた少なくとも 1種以上を主成分とする薄 膜を光導波路とする薄膜基板は高い紫外光に対する伝送性があることが ¾認された。
また、 窒化ガリウム、 窒化アルミニウムのうちから選ばれた少なくとも 1種以上を主成分と する薄膜やバルク単結晶などにニオブ及びタンタルのうちから選ばれた少なくとも 1種以上の 成分を含むものは光導波路として用いうることが萑認された。
また同時に窒化ガリゥム、 窒化アルミニゥムのうちから選ばれた少なくとも 1種以上を主成 分とするパルク単結晶は光導波路として用いうることカ 歸忍された。 その中でも窒化アルミ二 ゥムを主成分とするバルク単結晶は紫外光を伝送し得ることが確認された。
これらの結果を表 2 8に示した。 表 2 8には波長 3 8 0 nm、 3 0 0 nm、 2 7 0 nm、 2 5 0 nmの光を用いて測定した伝送損失の値が示されている。 ミラー指数 (0 0 2 ) の格子面を有する市販のサファイア基板を用意した。 このサファイア 基板は平均表面粗さ R a 1 . 2 nmに鏡面研磨してある。 一部のサフアイァ基板は入手したそ のままの表面状態で、 一部のサファイア基板に 実施例と同じ条件で 1 0 0モル%A 1 N配 向性多結晶薄膜を形成した。 その後これら基板に本実施例と同様に MO C VD法で 1 0 0モ %A 1 N単結晶薄膜を形成しその後高周波スパッタリング法で酸化ガリゥム薄膜をその上に 形成し該スパッタリング薄膜を光リソグラフィ一によるリフトオフ法を用いて幅 1 0 mX厚 み 5 0 nmの大きさの線状にパターニングし、 窒素雰囲気中 1 5 0 0 °Cで熱処理して光導波路 を作製した。 次に本実施例と同様の方法でこの光導波路の伝 員失を測定したが波長 6 5 0 η m、 3 8 0 nm, 3 0 0 nm, 2 7 0 nm、 2 5 0 nmいずれの場合も 1 0 d BZ c mより大 さかった。
このように、 本発明において窒化アルミニウムを主成分とする焼結体に形成した窒化ガリ ゥム、 窒化インジウム、 窒化アルミニウムのうちから選ばれた少なくとも 1種以上を主成分と する薄膜を光導波路として用いたとき、 上記各バルク単結晶を用いて作製した光導波路と比べ て少なくとも同等あるいはそれ以下の低い伝送損失のものが作製し得ることが確認された。 実施例 2 3
実施例 2 2と同様に実施例 1 1において作製した実験 N o . 4 9の窒化アルミニウムを主成 分とする焼結体を直径 2 5. 4mmX厚み 0. 5 mmの寸法の基板状に加工しさらに鏡丽 if磨 したものを用意した。 次に実施例 2 2で用いたのと同じ MO CVD法により実質的に窒化アル ミニゥム 1 0 0モル%からなる単結晶薄膜を厚み 2 5 /zmで形成した薄膜基板を作製した。 こ の薄膜基板に形成された単結晶薄膜の波長 6 5 0 nmの光に対する屈折率は 2. 1 9 0 1 7で
あった。
次に実施例 2 2と同様上記薄膜基板に対して窒化ガリウム、 窒化インジウム、 窒化ニオブ、 窒化夕ンタルの各薄膜を室温においてマグネト口ンスパッ夕リングで厚みを 1. 0 ηπ!〜 1 0 0 0 nmの範囲で変えて基板の全面に形成した。 このようにして得られたスパッタリング薄膜 は光リソグラフィ一によるリフトオフ法を用いて幅 1 O mX長さ 2 5. 4mmの大きさの線 状として残るようにパターエングした。 また、 同じスパッタリング薄膜を用い該スパッタリン グ薄膜の別の部分が幅 1. 5,ズ長さ2 5. 4mmの線状として残るようパ夕一エングした。 その後窒素雰囲気中 1 5 0 0°Cで 6時間加熱した。 加謝^^観を調べたが各薄膜と窒化アルミ 二ゥムを主成分とする焼結体との間の剥離などの不具合は見られなかった。 また各薄膜のガリ ゥム、 インジウム、 ニオブ、 タンタル各成分が形成された部分の外観を観察したがクラックや 剥離は見られなかった。 またまた粘着テープを用いて剥離テストを行ったが形成した薄膜と窒 化アルミニウムを主成分とする焼結体との間の剥離、 及びガリウム、 インジウム、 ニオブ、 タ ン夕ル各成分が形成された薄膜部分の剥離や破壊はなかった。
次に加熱後の薄膜基板各サンプルを用いてガリウム、 インジウム、 ニオブ、 タンタル各成分 からなるスパッタリンク 膜が形成された部分のうち、該スパッタリンク 膜に熱処理前幅 1. 5 mmX長さ 2 5. 4 mmのパ夕一ニングを施した部分の波長 6 5 0 nmの光に対する屈折率 を実施例 2 1及び実施例 2 2で用いたものと同じ分光光度計で測定した。 その結果、 はじめに 作製した実質的に 1 0 0モル%の組成からなる窒化アルミニウム単結晶薄膜の屈折率よりガリ ゥム、 インジウム、 ニオブ及びタンタル成分を有するスパッタ薄膜を形成後熱処理した薄膜の 屈折率が大きくなること力 萑認された。 またガリウム、 インジウム、 ニオブ、 タンタルの各ス パッ夕材料の形颇みが厚くなるにつれて屈折率が大きくなることも確認された。 この結果は、 実施例 2 1で調べた薄腠袓成とそれに伴う屈折率の変化を に考察すればはじめに作製した 実質的に 1 0 0モル%の組成からなる窒化アルミニウム単結晶薄膜中へガリウム、インジウム、 ニオブ及び夕ンタル成分が拡散し導入され組成が変動していることを示唆しているものと思わ れる。 ガリゥム成分を拡散導入したサンプルにおいて屈折率の変化量は 4 X 1 0一5〜 8. 4 X 1 0一2の範囲でありガリゥム成分の含有量は窒化ガリゥム換算で 0. 0 1モル%〜4 0モル% の範囲にあるものと思われる。 また、 インジウム成分を拡散導入したサンプルにおいて屈折率 の変化量は 6 X 1 0— 5〜 9. 4 X 1 0— 2の範囲でありインジウム成分の含有量は窒化ニオブ換 算で 0. 0 1モル%〜2 0モル%の範囲にあるものと思われる。 また、 ニオブ成分を拡散導入 したサンプルにおいて屈折率の変化量は 9 X 1 0 - 5〜1 . 1 X 1 0—1の範囲でありニオブ成分 の含有量は窒化ニオブム換算で 0. 0 1モル%〜2 0モル%の範囲にあるものと思われる。 ま た、 タンタル成分を拡散導入したサンプルにおいて屈折率の変化量は 7 X 1 0—5〜1. 1 X 1 0一1の範囲でありタンタル成分の含有量は窒化タンタル換算で 0. 0 1モル%〜2 0モル%の 範囲にあるものと思われる。 このようにすべてのサンプルにおいて屈折率の増加量は 1 X 1 0一 5〜2 X 1 0一1の範囲にあり、はじめに作製した実質的に 1 0 0モル%の組成からなる窒化アル ミ二ゥム単結晶薄膜中へのガリゥム、 ィンジゥム、 ニオブ及び夕ンタルのうちから選ばれた少 なくとも 1種以上からなる成分が上記の量で導入されているものと思われる。
次に市販の波長可変レーザー光発生装置を用い上記窒化アルミニウムを主成分とする単結晶 薄膜のスパッタリング薄膜によってガリウム、 インジウム、 ニオブ、 タンタル成分が混入され た部分のうち該スパッ夕リング薄膜に熱処理前幅 1 0 zmX長さ 2 5. 4 mmのパターニング を施した部分へ波長 6 5 0 nm、 3 8 0 nm、 3 0 0 nm、 2 5 0 nmの光を入力し、 透過し た出力光の減衰量を測定して伝還員失を算出した。 その結果すベてのサンプルで入射光に対し て羅性があり伝纖失もすベてのサンプルで 3 d B/ c m以下であった。 この結果、 本実施 例で作製した実質的に 1 0 0モル%の組成からなる窒化アルミニウム単結晶薄膜中へガリウム、
ニオブ、 タンタル成分が混入した部分は紫外光及び可視光が伝送可能な埋め込み 型の三次元光導波路として機能することが確認された。 これらの結果を表 2 9に示した。 実施例 2 4
実施例 2 1及び実施例 2 2で用いた実験 N o . 4 9と実験 N o . 5 8及び実験 N o . 2 6 9 の窒化アルミニウムを主成分とする焼結体からなる基板を用意した。 これらの基板すべてに基 W^ 2 8 0 、 ターゲットとして窒化アルミニウム焼結体を用い周波数 1 3. 5 6 MH z、 電力 1 0 0 0Wの条件の R Fスパッタリング法で実質的に 1 0 0モル%組成の窒化アルミニゥ ムからなる配向性多結晶薄膜を厚み 6 m形成した。 この配向性多結晶薄膜は C軸が基板面に 対して垂直に配向しておりミラ一指数 (0 0 2) 面の格子面 X線回折ロッキングカーブの半値 幅は 6 3 6 0秒〜 7 1 5 0秒の範囲であった。 またその屈折率は 1 . 9 3 7〜1 . 9 7 3であ つた。 次にこの配向性多結晶薄膜の上に実施例 2 1と同様 MO CVD法により窒化ガリウム、 窒化インジウム、 窒化アルミニウムのうちから選ばれた少なくとも 1種以上を主成分とし航 ニオブ及び夕ン夕ル成分を含有する各種組成の単結晶薄膜を厚み 2 mで形成した薄膜基板を 作製した。 単結晶薄藤堪板面に対してその結晶 C軸が垂直になるよう形成した。 なお、 実験 N o. 6 6 9〜 6 7 3で用いた窒化アルミ二ゥムを主成分とする焼結体からなる基板には上記 多結晶薄膜は形成されておらず該焼結体に直接 MO C VDによる単結晶薄膜を形成した。 該単 結晶薄膜形成 観を調べたが各配向性多結晶薄厳び単結晶薄膜と窒化アルミ二ゥムを主成 分とする焼結体との間の剥離などの不具合は見られなかった。 また、 各多結晶薄膜と単結晶薄 膜との間の剥離などの不具合は見られなかった。 また、 粘着テープを用いて剥離テストを行つ たが各多結晶薄 »び単結晶薄膜と窒化アルミニウムを主成分とする焼結体との間の剥離、 及 び各多結晶薄膜と単結晶薄膜との間の剥離や破壊はなかった。
このようにして得られた上記単結晶薄膜の屈折率はすべて 2. 1 6以上であり、 実施例 2 1 と同じ組成のものでは窒化アルミニウムを主成分とする焼結体からなる基板の違いによらず実 施例 2 1〜2 3で測定した値と殆ど同じであった。 作製した薄膜基板は形成した単結晶薄膜が 図 2 1及び図 2 3で示すような二次元光導波路として機能し得る形態である。
次に作製した薄膜基板の一部を用いて単結晶薄膜部分のみをイオンミリングで乾式エツチン グし幅 1 0 mの直線状に加工した。 この薄膜基板は加工により得られた単結晶薄膜が図 2 4 及び図 2 5で示すような三 導波路として機能し得る形態である。
次に市販の波長可変レーザー光発生装置を用い上記のようにして作製した薄膜基板の二次元 導波路及び三次元導波路部分に波長 6 5 0 n m、 3 0 0 n m、 2 5 0 nmの光を入力し透過し た出力光の減衰量を測定して伝週失を算出した。 その結果すベてのサンカレで入射光に対し て透過性があり伝送損失もすベてのサンプルで 1 O d B/c m以下であつた。 この結果、 本実 施例で作製した実質的に 1 0 0モル%の組成からなる窒化アルミニウム単結晶薄膜中へガリゥ ム、 インジウム、 ニオブ、 タンタル成分が混入した部分は紫外光及び T視光が伝送可能な二次 元光導波路及び三 光導波路として機能することが確認された。 また、 光導波路としての特 性は窒化アルミニウムを主成分とする焼結体からなる基板の違いによらない。 また、 窒化アル ミニゥムを主成分とする焼結体に直接形成した単結晶薄膜であっても十分紫外光を伝送し得る 光導波路として機能することが確認された。 これらの結果を表 3 0に示した。
実施例 2 5
本実施例は窒化アルミニウムを主成分とする焼結体を基板としその上に窒化ガリゥム、 窒化 ィンジゥム、 窒化アルミニウムのうちから選ばれた少なくとも 1種以上を主成分とする単結晶 薄膜、 無定形薄膜、 多結晶薄膜及び ffi向性多結晶薄膜を MO CVD法だけでなぐ スパッタリ ング法、 イオンプレーティング法による方法であらかじめ形成し、 さらにこれらの薄膜上に窒 ィ匕ガリウム、 窒化インジウム、 窒化アルミニウムのうちから選ばれた少なくとも 1種以上を主
成分とする単結晶薄膜が形成された多層薄膜の例を示す。 本実施例はそのなかでも窒化アルミ 二ゥムを主成分とする基板にあらかじめ形成する薄膜がさらにその上に形成する単結晶薄膜の 結晶性に及ぼす効果についても示す。 なお、 基板として用いた窒化アルミニウムを主成分とす る焼結体は導通ビアを有するものも含まれる。 また、 窒化アルミニウムを主成分とする焼結体 としては焼結助剤成分を含有しかつ A 1 N成分の含有量が比較的多いものを用いた。
まず、 窒化アルミニウムを主成分とする焼結体のうち導通ビアを有しないものとして実施例 2の実験 N o. 4 9、 5 8及び実施例 1 1の実験 N o. 2 5 9、 2 6 1、 2 6 6、 2 6 9で作 製し表面を実施例 8と同様の方法で儀画磨した後フッ « (5 0 %HF+ 5 0 %HN03) に 室温で浸漬後アセトン及び I P Aで超音波洗浄したものを基板として用意した。 これら導通ビ ァのない基板の表面粗さは実験 N o. 4 9のもので R a 2 6 nm、 実験 N o . 5 8のもので R a 2 8 nm、 実験 N o. 2 5 9、 2 6 1、 2 6 6、 2 6 9のもので R a 3 0 nmであった。 次 に導通ビアを有するものとして実施例 3の実験 N o. 8 0、 8 3及び実施例 1 4の実験 N o . 3 0 4で作製し表面を実施例 8と同様の方法で鏡面研磨し塩化メチレンで洗浄したものを基板 として用意した。 表面粗さは実験 N o. 8 0及び実験 N o. 8 3のもので R a 2 6 nm、 実験 N o. 3 0 4のもので R a 3 0 nmであった。 さらに導通ビアを有するものとして実施例 3で 作製したグリーンシ一トのうち E r 2〇 3粉末を 4. 0 2体 含むものを用いこのグリーンシ 一卜に 5 0 mのスルーホールを穿孔して実施例 1 4で作製したタングステンを主成分とする 導通ビア用ペーストのうち A 1 Nを 5. 0重量%含むものを充填し実施例 3と同様 1 8 2 0°C で 2時間常圧焼成し 例 3と同様の寸法に研削、 鏡面研磨し導通ビアを露出させ塩化メチレ ンで洗浄したものを基板として用意した。 この導通ビアを有する基板の表面粗さは R a 3 2 n mであった。
まず、 上記のように用意した各基板に MOCVD法、 スパッタリング法、 イオンプレーティ ング法により窒化ガリウム、 窒化インジウム、 窒化アルミニウムのうちから選ばれた少なくと も 1種以上を主成分とする単結晶薄膜、 無定形薄膜、 多結晶薄 ぴ 向性多結晶など各種結 晶状態の薄膜を形成した。 MOCVD法により薄膜形成を行う場合は実施例 1、 実施例 1 0、 実施例 1 2、 実施例 1 7と同様の原料及び成膜条件を用いた。 スパッタリング法により薄膜形 成を行う場合は周波数 1 3. 5 6 MH zの高周波 (R F) マグネト口ンスパッ夕リング法によ りターゲットとして金属 A 1、 A 1 N焼結体、 0. 0 2モル%の S i成分を含む A 1 N焼結体 を用い微量の A r +N2の混合ガスを N2/A r = 0. 0 2〜: L . 0の混合比で導入しチヤンバ 一内圧力 0. 1〜1. 5 P a、 電力 4 0 0〜1 5 0 0 Wの条件で薄膜形成の検討を行つた。 基 板温度は室温〜 6 0 0での範囲で行った。 また、 イオンプレーティング法により薄膜形成を行 う i胎は薄藤成用原料に金属 A 1を用い A 1金属を溶融し、微量 N2ガスを減圧チャンバ一内 に導入してイオン化電圧 2 0 V〜l 5 0 Vでイオン化し、 基板印加電圧 5 0 0 V〜2 0 0 0 V で金属蒸気を反応窒化することで薄膜形成の検討を行った。 基板 は室温〜 6 0 0 の範囲 で行った。
上記のように窒化アルミニウムを主成分とする焼結体からなる基板に直接形成した薄膜につ いて X線回折により結晶状態を調べ、 さらに作製した薄膜の室温抵抗率及びミラー指数 (0 0 2) の格子面のロッキングカーブの半値幅を測定した。 その結果を表 3 1、 表 3 2、 表 3 3及 び表 3 4に示す。
次に、 上記各種結晶状態の薄膜が形成された窒化アルミニウムを主成分とする焼結体からな る基板に対して、 実施例 1、 実施例 2、 実施例 1 0に示したものと同様の原料及び成膜条件を 用いた M〇 C VD法、 及び実施例 9に示したものと同様の原料及び成膜条件を用いたク口ライ ド VP E法により窒化ガリウム、 窒化インジウム、 窒化アルミニウムのうちから選ばれた少な くとも 1種以上を主成分とする単結晶薄膜の形成を試みた。 形成した各単結晶薄膜について X
線回折により結晶状態を調べ、 さらに作製した薄膜の室 氐抗率及びミラ一指数 (002) の 格子面のロッキングカーブの半値幅を測定した。 これその結果も表 31、 表 32、 表 33及び 表 34に示した。
なお、 表 31及び表 32はドーピング成分を含まない薄膜についての実験結果であり、 表 3 3及び表 34はドーピング成分を含む薄膜についての実験結果である。
表 31の実験 N o. 706〜 709には窒化アルミ二ゥムを主成分とする焼結体からなる基 板に直接厚み 3 xmで形成された A 1 N薄膜の特性が示されている。 実験 N 0. 706の薄膜 板 を室温とし、 Ar+N2の混合ガスをN2ZAr = 0. 6の混合比で導入しチャンバ 一内圧力 0. 5 Pa、 電力 500Wの条件のスパッ夕法で作製したものである。 実験 No. 7 07の薄膜は基板温度を 250°Cとし、 Ar+N2の混合ガスを N 2Z A r = 0. 3の混合比で 導入しチャンバ一内圧力 0. 6 P a、電力 800Wの条件のスパッタ法で作製したものである。 実験 No. 708の薄膜は基板温度を 280°Cとし、 A r +N2の混合ガスを N2ZA r = 0. 4の混合比で導入しチヤンノ一内圧力 0. 8Pa、 電力 1000 Wの条件のスパッ夕法で作製 したものである。 実験 No. 706〜708のスパッタリングでは夕一ゲットに高純度 A 1 N 焼結体を用いた。 実験 No. 709の薄膜はトリメチルアルミニウムを原料とし実施例 1と同 様の条件の M〇 CVD法により作製したものである。 X線回折によりこれら薄膜の結晶性の判 定を行つたが表 31に記載の通りそれぞれ実験 N o. 706のものが無定形、 実験 N o. 70 7のものが多結晶、 実験 No. 708のものが配向性多結晶、 実験 N o. 709のものが単結 晶の結晶状態を示した。 実験 No. 707の多結晶はミラー指数 (002)、 (101)、 (10 2) の格子面からの回折線だけが出現していた。 実験 No. 708及び 709で作製した薄膜 はいずれも C軸が基板面に対して垂直方向に形成されていた。 実験 No. 708及び 709の 薄膜のミラー指数 (002) の格子面の X線回折ロッキングカーブの半値幅はそれぞれ 791 0秒、 187秒であり配向性多結晶薄膜と単結晶薄膜とは結晶の成長方向は同じであっても明 らかに結晶性に差が見られた。
実験 N o. 706〜 709で作製した上記薄膜の外観を調べたがいずれもクラックやひび J れなどの欠陥は見られない。 また、 粘着テープによる剥離テストを行つたがいずれの薄膜も窒 化アルミニウムを主成分とする焼結体からなる基板との間で剥離は見られなかった。 また、 実 験 No. 706〜709で作製した薄膜表面に T iZP t ZAuの薄膜導電性材料を形成して 金属リ一ドをはんだ付けし垂直引張り強度を調べたがすべて 2Kg /mm2以上であり窒化ァ ルミ二ゥムを主成分とする焼結体と上記各薄膜との間は強固に接合している。
表 31の実験 No. 710〜713には実験 No. 706、 707、 及び 708と同じ条件 のスパッタ法で作製したそれぞれ厚み 3 mの A 1N無定形薄膜、 A 1N多結晶薄膜、 A1N 配向性多結晶薄膜が形成された基板、 及び実験 No. 709で作製した厚み 3 mの単結晶薄 膜があらかじめ形成された基板を用い、 その上にさらに上記本実施例の実験 No. 709と同 様の条件の MOCVD法によりそれぞれ厚み 3 xmで形成した A 1 N薄膜の特性が示されてい る。 X線回折の結果これらの薄膜は明らかに基板面に対して C軸が垂直な方向に形成された単 結晶である。 実験 No. 710、 711、 712及び 713で作製したこれら A 1 Nを主成分 とする単結晶薄膜の結晶性はミラ一指数 (002) の格子面の X線回折ロッキングカーブの半 値幅はそれぞれ 89秒、 93秒、 79秒及び 105秒であり、 同様の条件の M〇 C V D法で作 製した実験 N o. 709の A 1 N単結晶薄膜の 187秒より明ら力に優れていた。 このように あらかじめ無定形薄膜、 多結晶薄膜、 配向性多結晶薄膜及び単結晶薄膜の A 1 N薄膜を形成し た窒化アルミ二ゥムを主成分とする焼結体からなる基板を用い、 その上には窒化アルミニゥム を主成分とする単結晶薄膜が形成できその結晶性は窒化アルミニウムを主成分とする焼結体か らなる基板に直接形成した単結晶薄膜よりも高められることが 11認できた。 また、 実験 No.
710〜712において、 基板にあらかじめ形成する薄膜が無定形、 多結晶、 配向性多結晶で ある基板を用いた場合、 その上に形成される A 1N単結晶薄膜のミラー指数 (002) の格子 面の X線回折ロッキングカーブの半値幅は 100秒以下であることが示されており、実験 No. 713に示されているように基板にあらかじめ形成する薄膜が単結晶である基板よりその上に 形成される A 1 N単結晶薄膜の結晶性は優れていた。
実験 No. 710〜713で作製した上記薄膜の外観を調べたがいずれもクラックやひび割 れなどの欠陥は見られない。 また、 粘着テープによる剥離テストを行ったがいずれの薄膜も窒 化アルミニウムを主成分とする焼結体からなる基板との間あるいは薄膜同士の間で剥離は見ら れなかった。 また、 実験 No. 710〜713で作製した薄膜表面に T iZP t/Auの薄膜 導電性材料を形成して金属リ一ドをはんだ付けし垂直弓 I張り強度を調べたがすべて 2Kg/m m2以上であり窒化アルミニウムを主成分とする焼結体と上記各薄膜との間あるいは各薄膜間 は強固に接合している。
表 31の実験 N 0. 714〜 715には窒化アルミニウムを主成分とする焼結体からなる基 板に直接厚み 3 xmで形成された G a N薄膜及び I n N薄膜の特性が示されている。 これらの 薄膜はトリメチルガリゥム及びトリメチルインジゥムを原料とし実施例 1と同様の条件の M〇 CVD法で作製されたものである。 得られたこれらの薄膜は X線回折により明らかにいずれも C軸が基板面に対して垂直方向に形成さ 結晶であることカ鳩認された。 これら単結晶薄膜 のミラ一指数 (002) の格子面の X線回折ロッキングカーブの半値幅は G a N及び I nNそ れぞれ G a Nで 179秒、 I n Nで 190秒であった。 実験 N o . 716及び 717には実験 No. 708と同じスパッ夕条件で作製した A 1 N配向性多結晶薄膜が厚み 3 zxm形成された 基板を用い、 その上にさらに上記本実施例と同様の条件の M〇 C VD法により厚み 3 で形 成した G a N及び I n N各薄膜の特性が示されている。 X線回折の結果これら G a N、 I nN 各薄膜は明らかに基板面に対して C軸が垂直な方向に形成された単結晶である。 これらのあら かじめ配向性多結晶薄膜を形成した基板の上に形成されている G a N及び I nNを主成分とす る単結晶薄膜のミラー指数 (002) の格子面の X線回折ロッキングカーブの半値幅はそれぞ れ 89秒及び 87秒と 100秒以下であり、 同様の条件の M〇 C VD法で作製した実験 N o . 714の G aN単結晶薄膜の 179秒及び実験 No. 715の I nN単結晶薄膜の 190秒よ り明ら力、に優れていた。 また、 実験 No. 718、 719、 720にはそれぞれ実験 No. 7 06、 707、 709と同じ条件で作製した A 1 N無定形薄膜、 多結晶薄膜、 単結晶薄膜があ らかじめ厚み 3 m形成された基板を用い、 その上にさらに上記本実施例と同様の条件の MO CVD法により厚み 3 mで形成した G a N薄膜の特性が示されている。 これらの GaN薄膜 は明らかに基板面に対して C軸が垂直な方向に形成された単結晶である。 これらのあらかじめ 配向性多結晶薄膜を形成した基板の上に形成されている GaNを主成分とする単結晶薄膜のミ ラ一指数 (002) の格子面の X線回折ロッキングカーブの半値幅はそれぞれ 90秒、 92秒 及び 107秒であり、 同様の条件の MOCVD法で作製した実験 No. 714の GaN単結晶 薄膜の 179秒より明らかに優れていた。 また、 実験 No. 716、 718、 719に示され ているように基板にあらかじめ形成する薄膜が無定形、 多結晶、 配向性多結晶である基板を用 いた場合、 その上に形成される GaN単結晶薄膜のミラ一指数 (002) の格子面の X線回折 口ッキングカーブの半値幅は 100秒以下であり、 実験 N 0. 720に示されているように基 板にあらかじめ形成する薄膜が単結晶である基板より、 その上に形成される G a N単結晶薄膜 の結晶性はより優れていた。 このように A 1 Nを主成分とする単結晶薄膜だけでなく GaN及 び I nNを主成分とする単結晶薄膜においても、 窒化アルミニウムを主成分とする焼結体から なる基板に直接形成するよりあらかじめ配向性多結晶薄膜を形成した基板を用い、 その上に形 成する方がより結晶性の優れた単結晶薄膜が作製できることがt認できた。
実験 No. 714〜715で作製した上記薄膜の外観を調べたがクラックやひび割れなどの 欠陥は見られない。 また、 粘着テープによる剥離テストを行ったが窒化アルミニウムを主成分 とする焼結体からなる基板との間で剥離は見られなかった。 実験 No. 716〜720で作製 した上記薄膜の外観を調べたがいずれもクラックやひび割れなどの欠陥は見られない。 また、 粘着テープによる剥離テストを行ったがいずれの薄膜も窒化アルミニウムを主成分とする焼結 体からなる基板との間あるいは薄膜同士の間で剥離は見られなかった。 また、 実験 No. 71 4〜720で作製した薄膜表面に T i/P t /A Uの薄膜導電性材料を形成して金属リードを はんだ付けし垂直弓 Ϊ張り強度を調べたがすべて 2 K g Zmm2以上であり窒化アルミ二ゥムを 主成分とする焼結体と上記各薄膜との間あるいは各薄膜間は強固に接合している。
表 31の実験 No. 721、 722には窒化アルミニウムを主成分とする焼結体からなる基 板【こ厚み 3 mで直接形成された 100モル%A 1 N薄膜の特性が示されている。 この薄膜は MOCVD法及びイオンプレーティング法で形成されたものである。 実験 No. 721に示さ れる A 1 N薄膜は M〇 C VD法により基板温度を 480 °Cとした以外は実施例 1及び実施例 1 2と同様の原料及び成麟件により作製されたものである。 実験 No. 722に示される A 1 N薄膜はイオンプレーティング法により基板 250°C、原料に金属アルミニウムを用い N2 ガスを流量 40 c cZ分で流しながらイオン化電圧 40ポルト、 基板印加電圧 1000ポルト の条件で作製されたものである。 得られた A 1 N薄膜のうち実験 No. 721のものは C軸が 基板面に対して垂直な方向に形成された配向性多結晶であり、 ミラ一指数 (002) の格子面 の X線回折ロッキングカーブの半値幅は 4670秒とスパッ夕法による薄膜より結晶性は優れ ていた。 実験 No. 722のものはミラー指数 (100)、 (002) の回折ピークが出現した 多結晶であった。 実験 N o. 723及び 724においては上記 MO C VD法及びィオンプレー ティング法と同様の条件によりあらかじめ A 1 N配向性多結晶薄膜及び A 1 N多結晶薄膜が形 成された基板を用い、 その上にさらに実施例 1と同様の条件の MOCVD法によりそれぞれ厚 み 3 mで形成された A 1 N薄膜の特性が示されている。 X線回折の結果これら後から形成し た薄膜は明らかに基板面に対して C軸が垂直な方向に形成された単結晶である。 実験 No. 7 23及び 724の A 1 N単結晶薄膜の結晶性は明らかに実験 N o . 709の A 1 N単結晶薄膜 より優れており、 窒化アルミニウムを主成分とする焼結体からなる基板に直接形成するよりあ らかじめ多結晶薄 ぴ¾己向性多結晶薄膜を形成した基板に形成する方がより結晶性の優れた 単結晶薄膜が得られ易いことが確認できた。 あらかじめ形成する多結晶薄膜及び配向性多結晶 薄膜はスパッタリング法だけでなくイオンプレーティング法及び MOCVD法などによるもの であっても、 その上には結晶性の優れた単結晶薄膜を作製できることが萑認できた。
実験 No. 721、 722で作製した上記薄膜の外観を調べたがクラックやひび割れなどの 欠陥は見られない。 また、 粘着テープによる剥離テストを行ったが窒化アルミニウムを主成分 とする焼結体からなる基板との間で剥離は見られなかった。 実験 No. 723、 724で作製 した上記薄膜の外観を調べたがいずれもクラックやひび割れなどの欠陥は見られない。 また、 粘着テープによる剥離テストを行ったがいずれの薄膜も窒化アルミニウムを主成分とする焼結 体からなる基板との間あるいは薄膜同士の間で剥離は見られなかった。 また、 実験 No. 72 1〜724で作製した薄膜表面に T i/P tZAuの薄麟電性材料を形成して金属リードを はんだ付けし垂直引張り強度を調べたがすべて 2 K gZmm2以上であり窒化アルミニウムを 主成分とする焼結体と上記各薄膜との間あるいは各薄膜間は強固に接合している。
表 31の実験 No. 725には窒化アルミニウムを主成分とする焼結体からなる基板に厚み 3 mで直接形成された A 1 N薄膜の特性が示されている。 この A 1 N薄膜は塩化アルミニゥ ムを原料とし実施例 9と同様の条件のクロライド VPE法により作製されたものである。 この 薄膜は X線回折により c軸が基板面に対して垂直方向に形成さ; 結晶であることが ϋ認され
た。 この単結晶薄膜のミラー指数 (002) の格子面の X線回折ロッキングカーブの半値幅は 177秒であった。 実験 No. 726及び 727には実験 No. 706及び実験 No. 708 と同じスパッタ条件で作製したあらかじめ A 1 N無定形薄膜及び A 1 N配向性多結晶薄膜が厚 みそれぞれ 3 m形成された基板を用い、 その上にさらに上記実験 N 0. 725と同様の条件 のクロライド VP E法により厚み 3 mで形成した A 1 N薄膜の特性が示されている。 この薄 膜は X線回折の結果明らかに基板面に対して C軸が垂直な方向に形成された単結晶である。 こ れらの A 1 N無定形薄膜及び A 1 N配向性多結晶薄膜をあらかじめ形成した基板の上に形成さ れている A 1 N単結晶薄膜のミラー指数 (002) の格子面の X線回折ロッキングカーブの半 値幅はそれぞれ 91秒及び 86秒であり、 同様の条件のクロライド VPE法で作製した実験 N o. 725の A 1 N単結晶薄膜の 177秒より明らかにいずれも優れていた。 このように MO CVD法だけでなくクロライド VP E法により作製される単結晶薄膜においても、 窒化アルミ 二ゥムを主成分とする焼結体からなる基板に直接形成するよりあらかじめ無定形薄 ぴ己向 性多結晶薄膜を形成した基板を用い、 その上に形成する方がより結晶性の優れた単結晶薄膜が 作製できることが ϋ認できた。
実験 Ν ο. 725で作製した上記薄膜の外観を調べたがクラックやひび割れなどの欠陥は見 られない。 また、 粘着テープによる剥離テストを行ったが窒化アルミニウムを主成分とする焼 結体からなる基板との間で剥離は見られなかった。 実験 No. 726、 727で作製した上記 薄膜の外観を調べたがいずれもクラックやひび割れなどの欠陥は見られない。 また、 粘着テ一 プによる剥離テストを行ったがいずれの薄膜も窒化アルミニウムを主成分とする焼結体からな る基板との間あるいは薄膜同士の間で剥離は見られなかった。 また、 クロライド VPE法を用 いて作製した上記実験 No. 725〜727で作製した薄膜表面に T i/P t/Auの薄膜導 電性材料を形成して金属リ―ドをはんだ付けし垂直弓 1張り強度を調べたがすべて 2Kg /mm 2以上であり窒化アルミニウムを主成分とする焼結体と上記各薄膜との間あるいは各薄膜間は 強固に接合している。
表 31の実験 No. 728〜731には窒化アルミニウムを主成分とする焼結体からなる基 板に厚み 3 mで直接形成された 100モル% G a N薄膜及び 100モル% I n N薄膜の特性 が示されている。 この薄膜は MOCVD法で形成されたものである。 実験 N 0. 728、 72 9、 730に示される G a N薄膜は基板温度をそれぞれ 330 °C、 380 °C、 440 とした 以外は実施例 1、 実施例 12及び実施例 17と同様の原料及び成 件により作製されたもの である。 また、 実験 No. 731に示される I nN薄膜は基板温度を 420Tとした以外は実 施例 1及び実施例 12と同様の原料及び成 件により作製されたものである。 その結果 X線 回折により G a N薄膜のうち実験 N o. 728のものは無定形であり、 実験 N o . 729のも のはミラー指数 (002)、 (101) の回折ピークを有する多結晶体であった。 また、 得られ た GaN薄膜及び I nN薄膜のうち実験 No. 730及び 731はいずれも C軸が基板面に対 して垂直な方向に形成された配向性多結晶であり、 ミラ一指数 (002) の格子面の X線回折 口ッキングカーブの半値幅は G a N薄膜で 4710秒、 In N薄膜では 4820秒であった。 表 31の実験 No. 732〜739には上記 MOCVD法と同様の条件によりあらかじめ G a N薄 J»び I nN配向性多結晶薄膜が形成された基板を用い、 その上にさらに本実施例の実験 No. 709、 714及び 71.5で薄膜を作製したときと同様の条件の MOCVD法によりそ れぞれ厚み 3 mで作製した A 1N薄膜、 GaN薄膜、 I nN薄膜の特性が示されている。 こ れら後から形成した各薄膜は X線回折の結果明らかにいずれも C軸が基板面に対して垂直な方 向に形成された単結晶であった。 これら単結晶薄膜のミラー指数 (002) の格子面の X線回 折ロッキングカーブの半値幅は表 31に示すとおりいずれも 100秒以下であり高い結晶性を 有するものであった。
このように窒化アルミニウムを主成分とする焼結体からなる基板に無定形、 多結晶、 配向性 多結晶の各結晶状態を有する G a N薄膜及び I nN薄膜あらかじめ直接形成しておくことによ り、 その上には窒化ガリウム、 窒化インジウム及び窒化アルミニウムのうちから選ばれた少な くとも 1種以上を主成分とする単結晶薄膜が形成できその結晶性は窒化アルミニウムを主成分 とする焼結体からなる基板に直接形成した単結晶薄膜よりも高められることが 11認できた。 実験 N o. 728〜 731で作製した上記薄膜の外観を調べたがクラックやひび割れなどの 欠陥は見られない。 また、 粘着テープによる剥離テストを行ったが窒化アルミニウムを主成分 とする焼結体からなる基板との間で剥離は見られなかった。 また、 実験 No. 732〜739 で作製した各薄膜の外観を調べたがいずれもクラックやひび割れなどの欠陥は見られない。 ま た、 粘着テープによる剥離テストを行ったがいずれの薄膜も窒化アルミニウムを主成分とする 焼結体からなる基板との間あるいは薄膜同士の間で剥離は見られなかった。 また、 上記実験 N o. 728〜739で作製した薄膜表面に T i ZP tZAuの薄騰電性材料を形成して金属 リ一ドをはんだ付けし垂直引張り強度を調べたがすべて 2 K g/mm2以上であり窒化アルミ 二ゥムを主成分とする焼結体と上記各薄膜との間あるいは各薄膜間は強固に接合している。 図 62は実験 N o. 706で作製した A 1 N無定形薄膜の 2 Θ/Θスキヤンによって回折角 20 : 10° (度) 〜 70° (度) の範囲で測定した X線回折図形を示すが、 明確なピ一クが 出現せずブロードなパターンとなっており明らかに無定形状態であると思われる。 図 63は実 験 No. 707で作製した A 1 N多結晶薄膜の 2 スキャンによって回折角 20 : 10° (度) 〜70° (度) の範囲で測定した X線回折図形を示すが、 ミラ一指数 (002)、 (10 1)、 (102) 各格子面からのピークが出現しており明らかに多結晶である。 図 64は実験 N o. 708で作製した A 1 N配向性多結晶薄膜の 2 スキャンによって回折角 20 : 10° (度) 〜70° (度) の範囲で測定した X線回折図形を示すが、 ミラ一指数 (002) の格子 面からのピークだけが出現しており明らかに基板面に対して C軸が垂直な方向に形成された配 向性多結晶である。 図 65は実験 N o. 712で作製した A 1 N単結晶薄膜の 2 θ Z 0スキヤ ンによって回折角 20 : 10° (度)〜 70° (度)の範囲で測定した X線回折図形を示すが、 ミラー指数 (002) の格子面からのピークだけが出現し、 そのピークは実験 No. 708の A 1 N配向性多結晶薄膜より飛躍的にシャープであり明らかに基板面に対して C軸が垂直な方 向に形成された単結晶である。 図 66は上記実験 No. 712で作製した単結晶薄膜の ωスキ ヤンによって回折角 17. 88° (度)〜 18. 16° (度) の範囲で測定したミラー指数(0 02) の格子面の X線回折ロッキング力一ブである。 図 66にはこの薄膜のロッキングカーブ の半値幅が 79秒 (79 a r c s e c an t) であることも併記されている。 図 67は実験 N o. 716で作製した G a N単結晶薄膜の 20ノ0スキャンによって回折角 2 Θ : 10° (度) 〜70。 (度) の範囲で測定した X線回折図形を示すが、 ミラー指数 (002) の格子面から のピークだけが出現し、 又そのピークもシャープであり明らかに基板面に対して C軸が垂直な 方向に形成された単結晶である。 図 68は実験 No. 717で作製した I nN単結晶薄膜の 2 スキャンによって回折角 20: 10° (度) 〜70° (度) の範囲で測定した X線回折 図形を示すが、 ミラー指数 (002) の格子面からのピークだけが出現し、 又そのピークもシ ヤープであり明らかに基板面に対して C軸が垂直な方向に形成された単結晶である。 なお、 図 62〜図 68に示す X線回折図形は C u Κ α線を用いて測定されたものである。 図 62〜図 6 5、 及び図 67〜図 68に示す X線回折図形においてそれぞれの図の横軸は回折角度: 20を 示しており、 縦軸は回折 X線の強度 (X— r ay I n t ens i ty) を示している。 図 6 6に示す X線回折図形において横軸は回折角度: ωを示しており、 縦軸は回折 X線の強度 (X — r ay I n t ens i ty) を示している。
本実施例におレて薄膜が形成された状態のままの基板表面の表面粗さを測定したが、 表 31
に示すように作製したすべての基板が表面粗さ R a 10 n m以下であつた。 このようにもとも との窒化アルミ二ゥムを主成分とする焼結体からなる基板の表面粗さよりも大幅に小さくなり 平滑の向上した薄膜基板が得られ易いこと力 ¾|認された。 また、 上記のように窒化アルミニゥ ムを主成分とする焼結体からなる基板に無定形、 多結晶、 配向性多結晶、 単結晶の薄膜があら かじめ形成された基板に対してその上にさらに単結晶薄膜を形成した基板では表面粗さが小さ くなり表面平滑性が 善されることがI認された (実験例 706〜 709、 714:〜 715、 721〜722及び 728〜731で作製した薄膜に対して、 実験例 710〜713、 716 〜719、 723〜724, 726〜727及び 732〜739で作製した基板表面の単結晶 薄膜の表面粗さは小さくなつている)。窒化アルミニゥムを主成分とする焼結体からなる基板に 直接形成される無定形薄膜、 多結晶薄膜、 配向性多結晶薄膜の中では配向性多結晶薄膜を形成 した基板を用いることが好ましい。 本実施例において、 窒化アルミニウムを主成分とする焼結 体からなる基板にあらかじめ A 1 N無定形薄膜及び A 1 N多結晶薄膜を形成した基板を用い、 その上に形成した単結晶薄膜(実験 No. 710、 711、 718、 719、 724、 726) の表面粗さが R a : 2. 0nm〜2. 5 nmの範囲であるのに対して、 あらかじめ配向性多結 晶を形成した基板を用いその上に形成した単結晶薄膜 (実験 No. 712、 716、 717、 720、 727) の表面粗さは R a: 0. 87 ηπ!〜 1. 09 nmの範囲であり表面平滑性が さらに優れていることが ϋ認された。
次に、 窒化アルミニウムを主成分とする焼結体の材質 (組成、 結晶相、 髓過率、 焼結体結 晶立子の大きさ、 など) が異なる基板を用いて形成される薄膜の評価を行った。 薄膜の形成は 前記本実施例に記載されたものと同様の条件により行った。 その結果が表 32の実験 No. 7 40〜757に示されている。 実験 No. 740〜757において、 明らかに、 1) 窒化ァリレ ミニゥムを主成分とする焼結体からなる基板の材質が異なっていてもあらかじめ無定形、 多結 晶、 配向性多結晶を形成した基板を用いその上に形成した単結晶薄膜は A 1 Nだけでなく G a N及び I nNであってもミラ一指数 (002) の格子面の X線回折ロッキングカーブの半値幅 が 100秒以下と高い結晶性のものが得られ、 窒化アルミニウムを主成分とする焼結体からな る基板に直接形成した単結晶薄膜 (実験 No. 740、 744、 749、 753で作製した単 結晶薄膨 の結晶性と比較して少なくとも同等かそれよりもさらに優れることが ϋ認された。 さらに、 2) 窒化アルミニウムを主成分とする焼結体だけからなる基板の表面平滑性より薄膜 を形成した窒化アルミニウムを主成分とする焼結体からなる基板の表面平滑性のほうが優れる ことカ權認された。 3) 窒化アルミニウムを主成分とする焼結体からなる基板に直接形成した 薄膜の表面平滑性よりあらかじめ無定形薄膜、 多結晶薄膜、 配向性多結晶薄膜を形成した基板 の上に形成した薄膜の表面平滑性の方が優れることが確認された。 4) 窒化アルミニウムを主 成分とする焼結体からなる基板にあらかじめ形成した薄膜のうち無定形薄膜及 結晶薄膜を 形成した基板より配向性多結晶薄膜を形成した基板の上に形成した単結晶薄膜の表面平滑性の 方が優れることが確認された。
実験 No. 740〜757で作製した上記薄膜の外観を調べたがいずれもクラックやひび割 れなどの欠陥は見られない。 また、 粘着テープによる剥離テストを行ったがいずれの薄膜も窒 化アルミニウムを主成分とする焼結体からなる基板との間あるいは薄膜同士の間で剥離は見ら れなかった。 また、 形成された上記各単結晶薄膜に Ti/P tZAuの薄膜導電性材料を形成 して金属リ一ドをはんだ付けし垂直引張り強度を調べたがすべて 2Kg Zmm2以上であり窒 化アルミニウムを主成分とする焼結体と上記各薄膜の間あるいは各薄膜同士の間は強固に接合 している。
本実施例において、 上記のような現象は夕ングステン及び銅を主成分とする導通ビアを有す る窒化アルミニウムを主成分とする各種焼結体を基板として用いたものにおいても確認された。
すなわち、 その結果は表 32の実験 No. 758〜765に示されている。 実験 No. 75 8〜765に示されている導通ビアを有する窒化アルミニウムを主成分とする焼結体からなる 基扳にあらかじめ直接形成する薄膜はスパッタリング法及び MOC VD法を用い、 前記本実施 例に記載されたものと同様の条件により作製した。 これらあらかじめ各薄膜が形成された基板 に前記本実施例で示したものと同様の条件による MOCVD法及びクロライド VP E法により A1N、 GaN、 I nN薄膜をさらに形成した。 形成した A 1 N、 GaN、 I nN各薄膜は C 軸が基板面に対して垂直な方向に形成された単結晶であり、 ミラー指数 (002) の格子面の X線回折ロッキングカーブの半値幅はすべて 100秒以下の優れた結晶性を有する単結晶であ つた。 このように導通ビアを有する窒化アルミニゥムを主成分とする焼結体からなる基板にお いても無定形、 多結晶、 配向性多結晶の各結晶状態を有する A 1N薄膜及ぴ 向性多結晶 G a N薄膜及 ϋ¾3向性多結晶 I nN薄膜あらかじめ形成しておくことにより、 その上には窒化ガリ ゥム、 窒化ィンジゥム及び窒化アルミニゥムのうちから選ばれた少なくとも 1種以上を主成分 とする単結晶薄膜が形成できその結晶性は窒化アルミニウムを主成分とする焼結体からなる基 板に直接形成した単結晶薄膜よりも高められることが確認できた。
また、 実験 No. 758〜765において作製した上記単結晶薄膜の表面平滑性は窒化アル ミニゥムを主成分とする焼結体からなる基板の表面平滑性より優れていた。 また、 窒化アルミ 二ゥムを主成分とする焼結体からなる基板にあらかじめ形成した薄膜のうち無定形薄 J3 ¾び多 結晶薄膜を形成した基板 (実験例 760及び 764) より配向性多結晶薄膜を形成した基板の 上に形成した単結晶薄膜の表面平滑性の方が優れる、 ことが確認された。
実験 N o. 758〜 765で作製した上記薄膜の外観を調べたがいずれもクラックやひび割 れなどの欠陥は見られない。 また、 粘着テープによる剥離テストを行ったがいずれの薄膜も窒 化アルミニウムを主成分とする焼結体からなる基板との間あるいは薄膜同士の間で剥離は見ら れなかった。 また、 形成された上記各単結晶薄膜に T iZP tZAuの薄膜導電性材料を形成 して金属リ一ドをはんだ付けし垂直弓 I張り強度を調べたがすべて 2Kg /mm2以上であり窒 化アルミニウムを主成分とする焼結体と上記各薄膜の間あるいは各薄膜同士の間は強固に接合 している。
表 33には、 窒化アルミニウムを主成分とする焼結体からなる基板にドーピング成分を含有 する薄膜を形成した例が示されている。 表 33に記載された各実験における薄膜の厚みは 3 / mになるよう作製した。
実験 No. 766〜775は窒化アルミニウムを主成分とする焼結体からなる基板にドーピ ング成分を含有する薄膜を直接形成した例である。 実験 N o. 766には 0. 02モレ%の S i成分を含有する G aN単結晶をターゲットに用いたスパッタリング法で作製した薄膜の例が 示されている。 実験 No. 767には 0. 02モル%の S i成分を含有する高純度 I nN焼結 体をターゲットに用いたスパッタリング法で作製した薄膜の例が示されている。 実験 No. 7 68には 0. 02モル%の3 i成分を含有する高純度 A 1 N焼結体をターゲットに用いたスパ ッタリング法で作製した薄膜の例が示されている。 実験 No. 766の薄膜は基板温度を室温 とし、 八 +1^2の混合ガスを1^2/八で=0. 6の混合比で導入しチャンパ一内圧力 0. 5P a、 電力 400Wの条件のスパッ夕法で作製したものである。 実験 No. 767の薄膜は基板 温度を 250°Cとし、 Ar+N2の混合ガスをN2/Ar = 0. 3の混合比で導入しチャンバ一 内圧力 0. 6 Pa、 電力 600Wの条件のスパッタ法で作製したものである。 実験 No. 76 8の薄膜 fま基板温度を 280°Cとし、 Ar+N2の混合ガスを N 2/A r = 0. 4の混合比で導 入しチャンバ一内圧力 0. 8 P a、電力 1000Wの条件のスパッ夕法で作製したものである。 上記スパッタリング法で使用した電力は周波数 13. 56MHzの高周波である。 実験 No. 769及び 770は基板温度を 480°Cとしドーピング用原料として S iHLを新たに用いた
以外は前記本実施例と同じ条件の MOC VD法で作製した薄膜の例を示す。 X泉回折の結果、 実験 No. 766で作製した薄膜は無定形、実験 No. 767で作製した薄膜はミラー指数(0 02)、 (101)、 (102) の格子面の回折線が出現している多結晶であった。 これに対して 実験 No. 768、 769、 770で作製した薄膜はミラ一指数 (002) の格子面の回折線 だけが出現しており基板面に対して C軸が垂直に形成された配向性多結晶であった。 これら配 向性多結晶薄膜のミラー指数 (002) の格子面の X線回折ロッキングカーブの半値幅はそれ ぞれ 7930秒、 4560秒、 4390秒であり、 MOC VD法で作製した配向性多結晶薄膜 の方が結晶性に優れていた。 実験 N o. 766〜 770で作製した薄膜はいずれも表 33に示 すように導電性を有していた。 実験 No. 766〜 770で作製した上記薄膜の外観を調べた がいずれもクラックやひび割れなどの欠陥は見られない。 また、 粘着テープによる剥離テスト を行ったがいずれの薄膜も窒化アルミニウムを主成分とする焼結体からなる基板との間で剥離 は見られなかった。 また、 形成された上記各配向性多結晶薄膜に Ti/P t /Auの薄 電 性材料を形成して金属リードをはんだ付けし垂直弓 I張り強度を調べたがすべて 2Kg /mm2 以上であり窒化アルミニウムを主成分とする焼結体と上記各薄膜とは強固に接合している。 実験 No. 771〜775も窒化アルミニウムを主成分とする焼結体からなる基板にドーピ ング成分を含有する薄膜を直接形成した例である。 実験 No. 771の薄膜は基板温度 110 0°C、 実験 No. 772及び 773の薄膜 W¾板 figl 000°C、 実験 No. 774及び 77 5の薄膜は基板温度 840°Cとし、 ドーピング用原料として S iH4、 ビス一シクロペンタジェ ニルマグネシウム、 ジェチル亜鉛を新たに用いその他は実施例 1と同じ条件の MOCVD法で 作製した薄膜の例である。 X線回折の結果これらの薄膜はいずれも基板面に対して C軸が垂直 に形成された単結晶でありミラー指数 (002) の格子面の X線回折ロッキングカーブの半値 幅はそれぞれ 171秒、 157秒、 182秒、 192秒、 197秒であった。 また、 いずれも 表 33に示すように導電性を有していた。 実験 No. 77:!〜 775で作製した上記薄膜の外 観を調べたがいずれもクラックやひび割れなどの欠陥は見られない。 また、 粘着テープによる 剥離テストを行ったがいずれの薄膜も窒化アルミニウムを主成分とする焼結体からなる基板と の間で剥離は見られなかった。 また、 形成された上記各単結晶薄膜に Ti/P tZAuの薄膜 導電性材料を形成して金属リードをはんだ付けし垂直 d漲り強度を調べたがすべて 2Kg/m m2以上であり窒化アルミニゥムを主成分とする焼結体と上記各単結晶薄膜とは強固に接合し ている。
次に、 窒化アルミニウムを主成分とする焼結体からなる基板に上記実験 No. 768及び 7 70と同じドーピング成分を有する同一組成の配向性多結晶薄膜を同じ成膜条件のスパッタリ ング法及び OCVD法によりあらかじめ形成し、 さらにその上に上記実験 No. 771〜7 75と同様の成膜条件の MOCVD法によりドーピング成分を有する単結晶薄膜の形成を試み た。 その結果を表 34に示した。
表 34の実験 N o. 776〜 785に示す上記スパッ夕リング法及び MO C VD法により配 向性多結晶薄膜があらかじめ形成された窒化アルミニゥムを主成分とする焼結体からなる基板 に形成される薄膜はいずれも基板面に対して C軸が垂直に形成された単結晶であった。 これら 単結晶薄膜のミラー指数 (002) の格子面の X線回折ロッキングカーブの半値幅は 80秒〜 95秒の範囲に有り、 実験 No. 771〜775で作製した窒化アルミニウムを主成分とする 焼結体からなる基板に直接形成した単結晶薄膜が 157秒〜 197秒であるのに対して明らか に結晶性が向上していることが確認できた。 また、 配向性多結晶薄膜の上に形成された単結晶 薄膜はいずれも表 34に示すように導電性を有していた。
また、 実験 No. 771〜775で作製した窒化アルミニウムを主成分とする焼結体からな る基板に直接形成した単結晶薄膜の表面粗さが 4. 6nm〜7. 1 nmの範囲にあるのに対し
て実験 N o. 776〜 785で作製した配向性多結晶薄膜の上に形成された単結晶薄膜の表面 粗さは RaO. 87nm〜: 1. 01 nmの範囲であり表面粗さも明らかに改善されることが 認できた。
実験 N o. 776〜 785で作製した薄膜の外観を調べたが基板側にある配向性多結晶薄膜 及び表面にある単結晶薄膜いずれもクラックやひび割れなどの欠陥は見られない。 また、 粘着 テープによる剥離テストを行ったがいずれの薄膜も窒化アルミニウムを主成分とする焼結体か らなる基板との間及ぴ 膜同志の間で剥離は見られなかった。 また、 実験 No. 776〜78 5で作製した単結晶薄膜に T iZP tZAuの薄膜導電性材料を形成して金属リードをはんだ 付けし垂直 I張り強度を調べたがすべて 2Kg /mm2以上であり窒化アルミニゥムを主成分 とする焼結体と配向性薄膜及び 向性薄膜と単結晶薄膜とは強固に接合している。
なお、 表 34には記載していないが、 別^!験 No. 766、 767、 769と同じ組成で 同じ成膜条件のスパッ夕リング法及び MO C VD法により窒化アルミニゥムを主成分とする焼 結体からなる基板 (実験 No. 49で作製したもの) に無定形薄膜、 多結晶薄膜、 配向性多結 晶薄膜をあらかじめ形成し、 さらにその上に上記実験 No. 771〜775で作製したときと 同じ組成で同じ成膜条件の MOCVD法によりドーピング成分を有する単結晶薄膜の形成を試 みた。 その結果、 窒化アルミニウムを主成分とする焼結体からなる基板には前記実験 No. 7 66、 767、 769と同様の無定形薄膜、多結晶薄膜、配向性多結晶薄膜が形成されており、 それらの薄膜上に形成された薄膜はいずれも基板面に対して C軸が垂直に形成された単結晶で あった。 これら単結晶薄膜のミラー指数 (002) の格子面の X線回折ロッキングカーブの半 値幅はすべて 100秒以下でありいずれも実験 N o. 743〜 747で作製し 窒化アルミ二 ゥムを主成分とする焼結体からなる基板に直接形成した単結晶薄膜よりも明らかに結晶性が向 上していることカ權認できた。 また、 上記単結晶薄膜の表面粗さは無定形薄膜の上に形成され たもので Ra2. lnm〜2. 7 nmの範囲に有り、 多結晶薄膜の上に形成されたもので R a 1. 8 ηπ!〜 2. 5 nmの範囲に有り、 配向性多結晶薄膜の上に形成されたもので R a 0. 8 9 nm〜 1. 08 nmの範囲であり表面粗さも明らかに改善されることが歸忍できた。 なお、 上記のようにあらかじめ窒化アルミニウムを主成分とする焼結体からなる基板に形成する薄膜 としては表 31に示したものと同様配向性多結晶である方がその上に形成される単結晶薄膜に より良好な表面平滑性を与える傾向があることが確認された。
このように本実施例において、 ドーピング成分を有する窒化ガリウム、 窒化インジウム、 窒 化アルミニウムのうちから選ばれた少なくとも 1種以上を主成分とする単結晶薄膜を窒化アル ミニゥムを主成分とする焼結体からなる基板に形成する場合でも、 基板に直接形成するよりあ らかじめ配向性多結晶が形成された基板を用いることが有効であることが確認できた。
実施例 26
本実施例においては、 窒化アルミニウムを主成分とする焼結体からなる基板にあらかじめ形 成する薄膜の効果についてさらに検討した。 窒化アルミニウムを主成分とする焼結体からなる 基板として実施例 19で作製した各種組成のものをそのまま用いて検討した。 また新たに実施 例 19と同様の方法により粉末成形体を N2中 1800°Cで 2時間常圧焼成し各種組成の窒化 ルミ二ゥムを主成分とする焼結体を作製し得られた焼結体を実施例 19と同様に鏡面研磨して 薄膜形成用基板として用いた。 なお、 新たに作製した各種窒化アルミニウムを主成分とする焼 結体において実施例 19と同様、 粉末成形体に含まれる不純物あるいは加えられる各種添加物 の量は、 実際含まれる不純物あるいは加えられる化合物を酸化物■あるいは元素換算したも のである。 本実施例で作製した窒化アルミニウムを主成分とする焼結体には原料粉末中の不純 物酸素や添加した A 1203に起因する酸素、 あるいは添加した希 ±ϋ¾素化合物及びアルカリ 土類金属化合物などの焼結助剤中の金属成分や酸素成分など、 あるいは添加したアル力リ金属
化合物及 υ娃^^有化合物中の金属成分や酸素成分など、 あるいは添加した M o、 W、 V、 N b、 T a、 T iの各遷移金属を含む化合物及びカーボンを含む化合物中の金属成分や力一ボン 成分など、 あるいは添加した F e、 N i、 C r、 Mn、 Z r、 H f、 C o、 C u、 Z nなどの 不可避金属を含む化合物中の金属成分などは焼成により殆ど揮散 · されないで粉末成形体 中と殆ど同じ量 していることが 15認された。 すなわち、 本実施例において実施例 1 9と同 様、 不純物量及び添加物量として上記騰値を用いたとき、 作製された窒化アルミニウムを主 成分とする焼結体中の不純物あるいは添加物の量は粉末成形体中に含まれる不純物あるいは添 加物の量との差は小さく殆ど同量と見なし得る。 したがって得られた窒化アルミニウムを主成 分とする焼結体の組成としては全酸素量以外特に各表には記載してない。 本実施例において使 用しまた本実施例において新たに作製した窒化アルミニウムを主成分とする焼結体からなる基 板の詳細は表 3 5〜表 4 0に示した。
これら基板にあらかじめ窒化ガリウム、 窒化インジウム、 窒化アルミニウムのうちから選ば れた少なくとも 1種以上を主成分とする単結晶薄膜、 無定形薄膜、 多結晶薄膜、 配向性多結晶 薄膜を形成し、 さらにその上に形成される単結晶薄膜の特性に及ぼす効果について検討した。 まず、 基板にあらかじめ形成する薄膜としては組成 1 0 0モル%A 1 Nとし実施例 2 5の実験 N o . 7 0 6、 7 0 7及び 7 0 8で行つたスパッ夕リング法及び実験 N o . 7 0 9で行つた M O CVD法と同様の方法により厚み 3 mのものを作製した。 その上に形成する薄膜は実施例 1 9に記載されたものと同じ 1 0 0モル%A 1 N、 1 0 0モル%0 &1^、 1 0 0モル%I nN、 5 0モル% A 1 N+ 5 0モル% G a N、 5 0モル%G a N+ 5 0モル% I n Nとし、 実施例 1 9における窒化アルミニウムを主成分とする焼結体からなる基板と該焼結体基板上に直接形成 した単結晶薄膜と同じ組成の対応になるように作製した。 形成した薄膜の厚みはすべて 3 m であった。 形成法としては実施例 1 9に記載のように実施例 1及び実施例 2と同様の条件によ る MOCVD法により行った。 このようにして作製した薄膜の特性を表 3 5、表 3 6、表 3 7、 表 3 8、 表 3 9、 表 4 0に示した。
次に、 各窒化アルミニウムを主成分とする焼結体からなる基板にあらかじめ形成した A 1 N 薄膜につレて X線回折により分析を行つたところ、 上記実施例 2 5の実験 N 0. 7 0 6、 7 0 7及び 7 0 8と同じ条件のスパッタリング法で作製した A 1 N薄膜は実験 N o . 7 0 6、 7 0 7及び 7 0 8と対応してそれぞれ無定形、 多結晶、 配向性多結晶であること力雕認された。 ま た、 上記実施例 2 5の実験 N o . 7 0 9と同じ条件の MO C VD法で作製した A 1 N薄膜は実 験 N o . 7 0 9と対応して単結晶であることが確認された。 これらの結果を表 3 5〜表 4 0に 記載した。 これらのあらかじめ形成した A 1 N薄膜のうち配向性多結晶及び単結晶薄膜のもの は基板面に対して C軸が垂直に形成されていることが確かめられた。 その結晶性は表 3 5〜表 4 0に示されているように配向性多結晶薄膜のものでミラー指数 ( 0 0 2) の格子面の X線回 折ロッキングカーブの半値幅の測定値は 6 6 4 0秒〜 7 5 5 0秒の範囲にあり、 単結晶薄膜で は 1 3 8秒〜 2 3 5秒の範囲にあった。
次に、 上記各種結晶状態の薄膜をあらかじめ形成した基板を用いさらにその上に形成した薄 膜について X線回折により調べたが、 明らかにすべて基板面に対して C軸が垂直に形成された 単結晶であることが確認された。
表 3 5は添加物として A 1 203を加えた窒化アルミニウムを主成分と焼結体からなる基板を 用いた例が示してある。 表 3 5において実験 N o . 8 0 2及び 8 0 3で用いた A 1 2〇3を酸化 物醇で 5 6体積%添加して作製した窒化アルミ二ゥムを主成分と焼結体からなる基板以外は、 すべて実施例 1 9で作製した表 1 8に記載されている窒化アルミニウムを主成分と焼結体から なる基板をそのまま使用している。表 3 5の各実験に示されているように、あらかじめ無定形、 多結晶、 配向性多結晶、 単結晶など各種結晶状態からなる薄膜を形成した窒化アルミニウムを
主成分とする焼結体からなる基板すべてにおいて、その上には窒化ガリウム、窒化インジウム、 窒化アルミニウムのうちから選ばれた少なくとも 1種以上を主成分とする単結晶薄膜が形成で きた。 該単結晶薄膜はミラ一指数 (0 0 2) の格子面のロッキングカーブの半値幅が 3 0 0秒 以下の結晶性を有するものであった。 また、 該単結晶薄膜の結晶性は同じ窒化アルミニウムを 主成分とする焼結体からなる基板に直接形成したものより向上することが ¾認できた。 本実施 例の表 3 5に記載した窒化アルミニウムを主成分とする焼結体からなる基板の上にあらかじめ 無定形、 多結晶、 配向性多結晶、 単結晶など各種結晶状態からなる薄膜を形成したものを用い たとき、 その上に形成される単結晶薄膜は AL ONを 5 0 %以上含む基板において該単結晶薄 膜のミラー指数 (0 0 2) の格子面のロッキングカーブの半値幅は 1 0 0秒以上であったが、 それ以外の A L〇 Nを 5 0 %以下含む基板は多くのもので 1 0 0秒以下であつた。 また、 添加 物として A 1 2〇 3を加えた窒化アルミニウムを主成分とする焼結体からなる基板がその上に直 接単結晶薄膜が形成できないようなものであっても、 本実施例において表 3 5で示したように あらかじめ無定形、 多結晶、 配向性多結晶など各種結晶状態からなる薄膜を形成したものを基 板として用いれば、 その上には窒化ガリウム、 窒化インジウム、 窒化アルミニウムのうちから 選ばれた少なくとも 1種以上を主成分とする単結晶薄膜が形成できることカ擁認できた。 実施 例 1 9の表 1 8の実験 N o. 3 8 2に示すように A 1 2 O 3 5 0 t%を添加した窒化アルミ二 ゥムを主成分とする焼結体には A 1 N相以外に AL ON相が 5 9 %生成し直接単結晶薄膜の形 成は困難であつたが、 本実施例においては実験 N o . 7 9 9〜8 0 1に示すように同じ基板を 用いてもあらかじめ無定形、 多結晶、 配向性多結晶の A 1 N薄膜を形成しておけばその上には 容易に結晶性の優れた単結晶薄膜を形成することができることが萑認された。 なお、 本実施例 における表 3 5の実験 N o . 8 0 2に示すように A 1 2 O 3を 5 6側%添加した窒化アルミ二 ゥムを主成分とする焼結体には A 1 N相以外に AL ON相が 7 7 %生成していた。 この焼結体 を用いた基板に形成された薄膜はミラー指数 (0 0 2 )、 (1 0 1 )、 ( 1 0 2 ) の格子面からだ けの回折ピークを示す多結晶体であり、 該基板には直接単結晶薄膜の形成は困難であった。 そ れに対して実験 N o. 8 0 3に示すように同じ焼結体からなる基板を用いてもあらかじめ配向 性多結晶の A 1 N薄膜を形成しておけばその上には容易に結晶性の優れた単結晶薄膜を形成す ることができることが確認された。
表 3 6は添加物として希土 ¾素及びアル力リ土類金属を加えた窒化アルミ二ゥムを主成分 と焼結体からなる基板を用いた例が示してある。 表 3 6において実験 N o . 8 2 8及び 8 2 9 で用いた Y 2 O 3を謝匕物換算で 7 2髓%添加して作製した窒化アルミ二ゥムを主成分と焼結 体からなる基板以外は、 すべて実施例 1 9で作製した表 1 9に記載されている窒化アルミニゥ ムを主成分と焼結体からなる基板をそのまま使用している。 表 3 6の各実験に示されているよ うに、 あらかじめ無定形、 多結晶、 配向性多結晶、 単結晶など各種結晶状態からなる薄膜を形 成した窒化アルミニウムを主成分とする焼結体からなる基板すべてにおいて、 その上には窒化 ガリウム、 窒化インジウム、 窒化アルミニウムのうちから選ばれた少なくとも 1種以上を主成 分とする単結晶薄膜が形成できた。 該単結晶薄膜はミラー指数 ( 0 0 2 ) の格子面のロッキン グカーブの半値幅が 3 0 0秒以下の結晶性を有するものであった。 また、 該単結晶薄膜の結晶 性は同じ窒化アルミニゥムを主成分とする焼結体からなる基板に直接形成したものより向上す ることが確認できた。 本実施例の表 3 6に記載した窒化アルミニウムを主成分とする焼結体か らなる基板の上にあらかじめ無定形、 多結晶、 配向性多結晶、 単結晶など各種結晶状態からな る薄膜を形成したものを用いたとき、 その上に形成される単結晶薄膜は希土類元素及びアル力 リ土類金属のうちから選ばれた少なくとも 1種以上の成分を酸化物 で 5 0#¾%以上含む 基板において該単結晶薄膜のミラ一指数 (0 0 2 ) の格子面のロッキングカーブの半値幅は多 くのもので 1 0 0秒以上であったが、 希土類 J£素及びアルカリ土類金属のうちから選ばれた少
なくとも 1種以上の成分を酸化物 で 5 0体積%以下含む基板は多くのもので 1 0 0秒以下 であった。 また、 添加物として希土^ ¾素及びアルカリ土類金属を含有する窒化アルミニウム を主成分とする焼結体からなる基板がその上に直接単結晶薄膜が形成できないようなものであ つても、 本実施例において表 3 6で示したようにあらかじめ無定形、 多結晶、 配向性多結晶な ど各種結晶状態からなる薄膜を直接形成したものを基板として用いれば、 その上には窒化ガリ ゥ厶、 窒化インジウム、 窒化アルミニウムのうちから選ばれた少なくとも 1種以上を主成分と する単結晶薄膜が形成できることが雀認できた。 実施例 1 9における表 1 9中の実験 N o . 3 9 1及 験 N o. 3 9 9に示すように C a C〇 3を酸化物換算で 5 4 Y 2 O 3を酸化物 換算で 5 5髓%添加した窒化アルミニウムを主成分とする焼結体には直接単結晶薄膜の形成 は困難であったが、 本実施例においては実験 N o . 8 1 2〜8 1 4及び実験 N o . 8 2 5〜8 2 7に示すように同じ基板を用いてもあらかじめ無定形、 多結晶、 配向性多結晶の A 1 N薄膜 を形成しておけばその上には容易に結晶性の優れた単結晶薄膜を形成することができることが 確認された。 これら 6つの実験において形成された単結晶薄膜のミラ一指数 (0 0 2 ) の格子 面のロッキングカーブの半値幅はすべて 1 3 0秒以下であった。 なお、 本実施例における表 3 6の実験 N o . 8 2 8に示すように Y2〇 3を 7 2#¾%添加した窒化アルミニウムを主成分と する焼結体を用いた基板に形成された薄膜はミラー指数 (0 0 2)、 (1 0 1 )、 (1 0 2) の格 子面からだけの回折ピークを示す多結晶体であり、 該基板には直接単結晶薄膜の形成は困難で あった。 一方それに対して、 実験 N o . 8 2 9に示すように同じ焼結体からなる基板を用いて もあらかじめ配向性多結晶の A 1 N薄膜を形成しておけばその上には容易に結晶性の優れた単 結晶薄膜を形成することができることが確認された。
表 3 7は添加物としてアルカリ金属及び 素化合物を加えた窒化アルミニウムを主成分と焼 結体からなる基板を用いた例が示してある。 表 3 7において実験 N o . 8 6 1〜8 6 4で用い た S i O 2を酸化物換算で 5 0体積%添加して作製した窒化アルミ二ゥムを主成分と焼結体か らなる基板以外は、 すべて実施例 1 9で作製した表 2 0に記載されている窒化アルミニウムを 主成分と焼結体からなる基板をそのまま使用している。表 3 7の各実験に示されているように、 あらかじめ無定形、 多結晶、 配向性多結晶、 単結晶など各種結晶状態からなる薄膜を形成した 窒化アルミニウムを主成分とする焼結体からなる基板すべてにおいて、 その上には窒化ガリゥ ム、 窒化インジウム、 窒化アルミニウムのうちから選ばれた少なくとも 1種以上を主成分とす る単結晶薄膜が形成できた。 該単結晶薄膜はミラ一指数 (0 0 2 ) の格子面のロッキングカー ブの半値幅が 3 0 0秒以下の結晶性を有するものであった。 また、 該単結晶薄膜の結晶性は同 じ窒化アルミニウムを主成分とする焼結体からなる基板に直接形成したものより向上すること が確認できた。 本実施例の表 3 7に示した窒化アルミニウムを主成分とする焼結体からなる基 板の上にあらかじめ無定形、 多結晶、 配向性多結晶、 単結晶など各種結晶状態からなる薄膜を 形成したものを用いたとき、 その上に形成される単結晶薄膜はアル力リ金属及び珪素のうちか ら選ばれた少なくとも 1種以上の成分を酸化物 で 2 0体積%以上含む基板において該単結 晶薄膜のミラー指数 (0 0 2 ) の格子面のロッキングカーブの半値幅は 1 0 0秒以上であった が、 それ以外のアル力リ金属及ぴ 素のうちから選ばれた少なくとも 1種以上の成分を酸化物 換算で 2 0体積%以下含む基板は多くのもので 1 0 0秒以下であった。 また、 添加物としてァ ルカリ金属及ぴ 素化合物を含有する窒化アルミ二ゥムを主成分とする焼結体からなる基板が その上に直接単結晶薄膜が形成できないようなものであっても、 本実施例において表 3 7で示 したようにあらかじめ無定形、 多結晶、 配向性多結晶など各種結晶状態からなる薄膜を直接形 成したものを基板として用いれば、 その上には窒化ガリウム、 窒化インジウム、 窒化アルミ二 ゥムのうちから選ばれた少なくとも 1種以上を主成分とする単結晶薄膜が形成できることが確 認できた。実施例 1 9の表 2 0の実験 N o. 4 1 2及び 4 1 9に示すように L i 2 C〇3を L i 2
O贿で 25體%、 S iを S i 02娜で 25 ί«%添加した窒化アルミニウムを主成分とす る焼結体を用いた基板に形成された薄膜はミラー指数 (002)、 (101)、 (102) の格子 面からだけの回折ピークを示す多結晶体であり、 該基板には直接単結晶薄膜の形成は困難であ つた。 それに対して、 本実施例においては表 37の実験 Ν 0. 842〜 844及び実験 Ν ο . 851〜853に示すように同じ焼結体からなる基板を用いてもあらかじめ無定形、 多結晶、 配向性多結晶の A 1 N薄膜を形成しておけばその上には容易に結晶性の優れた単結晶薄膜を形 成することができることが ¾認された。 なお、 本実施例における表 37の実験 N o. 861に 示すように S i〇2を 50体積%添加した窒化アルミニウムを主成分とする焼結体には直接単 結晶薄膜の形成は困難であつたが、 実験 No. 862〜864に示すように同じ基板を用いて もあらかじめ無定形、 多結晶、 配向性多結晶の A 1N薄膜を形成しておけばその上には容易に 結晶性の優れた単結晶薄膜を形成することができることが確認された。
表 38は添加物として Mo、 W、 V、 Nb、 Ta、 T iの各遷移金属成分、 及びカーボンを 加えた窒化アルミニウムを主成分と焼結体からなる基板を用いた例が示してある。 表 38にお いて実験 N o. 884〜 887で用いた Wを元素騰で 75 添加して作製した窒化アル ミニゥムを主成分と焼結体からなる基板以外は、 すべて実施例 19で作製した表 21に記載さ れている窒化アルミニウムを主成分と焼結体からなる基板をそのまま使用している。 表 38の 各実験に示されているように、 あらかじめ無定形、 多結晶、 配向性多結晶、 単結晶など各種結 晶状態からなる薄膜を形成した窒化アルミニウムを主成分とする焼結体からなる基板すべてに おいて、 その上には窒化ガリウム、 窒化インジウム、 窒化アルミニウムのうちから選ばれた少 なくとも 1種以上を主成分とする単結晶薄膜が形成できた。 該単結晶薄膜はミラ一指数 (00 2) の格子面のロッキングカーブの半値幅が 300秒以下の結晶性を有するものであった。 ま た、 該単結晶薄膜の結晶性は同じ窒化アルミニウムを主成分とする焼結体からなる基板に直接 形成したものより向上することカ礞認できた。 本実施例の表 38に示した窒化アルミニウムを 主成分とする焼結体からなる基板の上にあらかじめ無定形、 多結晶、 配向性多結晶、 単結晶な ど各種結晶状態からなる薄膜を形成したものを用いたとき、 その上に形成される単結晶薄膜は Mo、 W、 V、 Nb、 Ta、 T iの各遷移金属成分、 及び力一ボンのうちから選ばれた少なく とも 1種以上の成分を元素換算で 50体積%以上含む基板において該単結晶薄膜のミラ一指数 (002) の格子面のロッキングカーブの半値幅は多くのもので 100秒以上であったが、 そ れ以外の Mo、 W、 V、 Nb、 Ta、 T iの各遷移金属成分、 及び力一ボンのうちから選ばれ た少なくとも 1種以上の成分を元素換算で 50体積%以下含む基板は多くのもので 100秒以 下であった。 また、 添加物として Mo、 W、 V、 Nb、 Ta、 T iの各遷移金属成分を含む化 合物及び力一ボンを含有する窒化アルミニウムを主成分とする焼結体からなる基板がその上に 直接単結晶薄膜が形成できないようなものであっても、 本実施例において表 38で示したよう にあらかじめ無定形、 多結晶、 配向性多結晶など各種結晶状態からなる薄膜を直接形成したも のを基板として用いれば、 その上には窒化ガリウム、 窒化インジウム、 窒化アルミニウムのう ちから選ばれた少なくとも 1種以上を主成分とする単結晶薄膜が形成できることが ϋ認できた。 実施例 19の表 21の実験 Ν ο. 431及び 435に示すように Μ οを元素 »で 55 ^貴%、 Wを元素換算で 55機%添加した窒化アルミニウムを主成分とする焼結体を用いた基板に形 成された薄膜はミラー指数 (002)、 (101)、 (102) の格子面からだけの回折ピークを 示す多結晶体であり、 該基板には直接単結晶薄膜の形成は困難であった。 それに対して、 本実 施例においては表 38の実験 Ν ο. 875〜 877及び実験 Ν ο. 881〜 883に示すよう に同じ焼結体からなる基板を用いてもあらかじめ無定形、 多結晶、 配向性多結晶の A 1N薄膜 を形成しておけばその上には容易に結晶性の優れた単結晶薄膜を形成することができることが 確認された。さらに、本実施例における表 38の実験 N o. 884に示すように Wを 75 Μ%
添加した窒化アルミニウムを主成分とする焼結体を用いた基板に形成された薄膜はミラー指数 ( 0 0 2 )、 (1 0 1 )、 ( 1 0 2 ) の格子面からだけの回折ピ一クを示す多結晶体であり、 該基 板には直接単結晶薄膜の形成は困難であった。 それに対して、 実験 N o . 8 8 5〜8 8 7に示 すように同じ基«結体からなるを用いてもあらかじめ無定形、 多結晶、 配向性多結晶の A 1 N薄膜を形成しておけばその上には容易に結晶性の優れた単結晶薄膜を形成することができる ことが ϋ認された。
表 3 9は添加物として M o、 W、 Vの各遷移金属成分、 及びカーボンを加えさらに希土^ 5 素及びアルカリ土類金属成分のうち少なくとも 1種以上を加えた窒化アルミニウムを主成分と 焼結体からなる基板を用いた例が示してある。 表 3 9において実験 N o . 9 1 3〜9 1 6で用 いた Wを元素藤で 6 0髓%及び E r 203を酸化物換算で 3. 6髓%複合添加して作製し た窒化アルミニウムを主成分と焼結体からなる基板以外は、 すべて実施例 1 9で作製した表 2 2に記載されている窒化アルミニウムを主成分と焼結体からなる基板をそのまま使用している。 表 3 9の各実験に示されているように、 あらかじめ無定形、 多結晶、 配向性多結晶、 単結晶な ど各種結晶状態からなる薄膜を形成した窒化アルミニウムを主成分とする焼結体からなる基板 すべてにおいて、 その上には窒化ガリウム、 窒化インジウム、 窒化アルミニウムのうちから選 ばれた少なくとも 1種以上を主成分とする単結晶薄膜が形成できた。 該単結晶薄膜はミラー指 数 (0 0 2) の格子面のロッキングカーブの半値幅が 3 0 0秒以下の結晶性を有するものであ つた。 また、 該単結晶薄膜の結晶性は同じ窒化アルミニウムを主成分とする雄体からなる基 板に直接形成したものより向上することカ職認できた。 本実施例の表 3 9に示した窒化アルミ 二ゥムを主成分とする焼結体からなる基板の上にあらかじめ無定形、 多結晶、 配向性多結晶、 単結晶など各種結晶状態からなる薄膜を形成したものを用いたとき、 その上に形成される単結 晶薄膜は Mo、 W、 Vの各遷移金属成分及び力一ボンの含有量を元素換算で算定し、 希土類沅 素及びアルカリ土類金属成分の含有量を酸化物騰で算定したとき、 これらを合計 5 0鐘% 以上含む基板において該単結晶薄膜のミラ一指数 (0 0 2 ) の格子面のロッキングカーブの半 値幅は 1 0 0秒以上であったが、 上記成分を合計 5 0体積%以下含む基板では多くのもので 1 0 0秒以下であった。 また、 添加物として Mo、 W、 V、 N b、 T a、 T iの各遷移金属成分 を含む化合物及び力一ボンを加えさらに希土類 素及びアル力リ土類金属成分のうち少なくと も 1種以上を含む化合物を複合して含有する窒化アルミニウムを主成分とする焼結体からなる 基板がその上に直接単結晶薄膜が形成できないようなものであっても、 本実施例において表 3 9で示したようにあらかじめ無定形、 多結晶、 配向性多結晶など各種結晶状態からなる薄膜を 直接形成したものを基板として用いれば、 その上には窒化ガリウム、 窒化インジウム、 窒化ァ ルミニゥムのうちから選ばれた少なくとも 1種以上を主成分とする単結晶薄膜が形成できるこ とカ 認できた。 なお、 本実施例における表 3 9の実験 N o . 9 1 3に示すように Wを元素換 算で 6 0ィ機%及び E r 203を酸化物換算で 3. 6#¾%複合添加した窒化アルミニウムを主 成分とする焼結体を用いた基板に形成された薄膜はミラ一指数 (0 0 2)、 (1 0 1 )、 (1 0 2) の格子面からだけの回折ピークを示す多結晶体であり、 該基板には直接単結晶薄膜の形成は困 難であった。 それに対して、 実験 N o . 9 1 4〜9 1 6に示すように同じ焼結体からなる基板 を用いてもあらかじめ無定形、 多結晶、 配向性多結晶の A 1 N薄膜を形成しておけばその上に は容易に結晶性の優れた単結晶薄膜を形成することができることカ擁認された。
表 4 0は添加物として F e、 N i、 C r、 Mn、 Z r、 H f、 C o、 C u、 Z nなどの不可 避金属を含む化合物、 あるいはこれら不可避金属を含む化合物と希土類 J£素化合物及びアル力 リ土類金属化合物のうちの少なくとも 1種以上を複合して含有する窒化アルミニウムを主成分 と焼結体からなる基板を用いた例が示してある。 表 4 0において実験 N o . 9 3 0〜9 3 1で 用いた F eを元素購で 7 2重量%添加して作製した窒化アルミニウムを主成分と焼結体から
なる基板以外は、 すべて実施例 19で作製した表 23に記載されている窒化アルミニウムを主 成分と焼結体からなる基板をそのまま使用している。 表 40の各実験に示されているように、 あらかじめ無定形、 多結晶、 配向性多結晶、 単結晶など各種結晶状態からなる薄膜を形成した 窒化アルミニウムを主成分とする焼結体からなる基板すべてにおいて、 その上には窒化ガリゥ ム、 窒化インジウム、 窒化アルミニウムのうちから選ばれた少なくとも 1種以上を主成分とす る単結晶薄膜が形成できた。 該単結晶薄膜はミラ一指数 (002) の格子面のロッキング力一 ブの半値幅が 300秒以下の結晶性を有するものであった。 また、 該単結晶薄膜の結晶性は同 じ窒化アルミニウムを主成分とする焼結体からなる基板に直接形成したものより向上すること が確認できた。 本実施例の表 40に示した窒化アルミニウムを主成分とする焼結体からなる基 板の上にあらかじめ無定形、 多結晶、 配向性多結晶、 単結晶など各種結晶状態からなる薄膜を 形成したものを用いたとき、その上に形成される単結晶薄膜は Fe、 Ni、 Cr、 Mn、 Z r, Hf、 Co、 Cu、 Znのうちから選ばれた少なくとも 1種以上の成分を元素 で 50重量% 以上含む基板にぉレて該単結晶薄膜のミラー指数 (002) の格子面のロッキングカーブの半 値幅は多くのもので 100秒以上であったが、 そ 外の Fe、 Ni、 Cr、 Mn、 Zr、 H f、 Co、 Cu、 Znのうちから選ばれた少なくとも 1種以上の成分を元素騰で 50重量% 以下含む基板は 100秒以下であった。 また、 添加物として Fe、 N i、 Cr、 Mn、 Zr、 Hf、 Co、 Cu、 Znなどの不可避金属化合物を含む窒化アルミニウムを主成分とする焼結 体からなる基板がその上に直接単結晶薄膜が形成できないようなものであっても、 本実施例に おいて表 40で示したようにあらかじめ無定形、 多結晶、 配向性多結晶など各種結晶状態から なる薄膜を直接形成したものを基板として用いれば、 その上には窒化ガリウム、 窒化インジゥ ム、 窒化アルミニゥムのうちから選ばれた少なくとも 1種以上を主成分とする単結晶薄膜が形 成できることが確認できた。 実施例 19の表 23の実験 N o. 462に示すように F eを元素 換算で 55重量%添加した窒化アルミニウムを主成分とする焼結体を用いた基板に形成された 薄膜はミラ一指数 (002)、 (101)、 (102) の格子面からだけの回折ピークを示す多結 晶体であり、 該基板には直接単結晶薄膜の形成は困難であった。 それに対して、 本実施例にお いて表 40の実験 No. 927〜929に示すように同じ焼結体からなる基板を用いてもあら かじめ無定形、 多結晶、 配向性多結晶の A 1 N薄膜を形成しておけばその上には容易に結晶性 の優れた単結晶薄膜を形成することができることが雀認された。 さらに、 本実施例における表 40の実験 Ν ο. 930に示すように F eを 72重量%添加した窒化アルミニウムを主成分と する焼結体を用いた基板に形成された薄膜はミラー指数 (002)、 (101)、 (102) の格 子面からだけの回折ピークを示す多結晶体であり、 該基板には直接単結晶薄膜の形成は困難で あった。 それに対して、 実験 No. 931に示すように同じ焼結体からなる基板を用いてもあ らかじめの A 1 N配向性多結晶薄膜を形成しておけばその上には容易に結晶性の優れた単結晶 薄膜を形成することができることが萑認された。
本実施例において表 35、 表 36、 表 37、 表 38、 表 39、 表 40に記載した実験で作製 したすベての薄膜の外観を調べたがあらかじめ基板に形成した薄膜及びその上にさらに形成し た薄膜いずれもクラックやひび割れなどの欠陥は見られない。 また、 粘着テープによる剥離テ ストを行ったがいずれの薄膜も窒化アルミニウムを主成分とする焼結体からなる基板との間及 ぴ蒋膜同志の間で剥離は見られな力 た。 また、 基板表面の薄膜に TiZP tZAuの薄膜導 電性材料を形成して金属リ一ドをはんだ付けし垂直弓 I張り強度を調べたがすべて 2Kg /mm 2以上であり窒化アルミニウムを主成分とする嫌吉体とあらかじめ基板に形成した薄膜、及び該 薄膜とその上にさらに形成した薄膜とは強固に接合している。
実施例 27
本実施例は炭化珪素、 窒化珪素、 酸化亜鉛、 酸化ベリリウム、 酸化アルミニウムを主成分と
する焼結体を基板として用い、 これらの基板上にあらかじめ窒化ガリウム、 窒化インジウム、 窒化アルミニゥムのうちから選ばれた少なくとも 1種以上を主成分とする単結晶薄膜、 無定形 薄膜、 多結晶薄膜及び配向性多結晶薄膜を MOCVD法、 スパッタリング法及びイオンプレー ティング法で形成し、 さらにこれらの薄膜が形成された基板上に窒化ガリウム、 窒化インジゥ ム、 窒化アルミニウムのうちから選ばれた少なくとも 1種以上を主成分とする単結晶薄膜の形 成を試みた例を示す。
まず、 実施例 1で作製した炭化珪素、 窒化珪素、 酸化亜鉛、 酸化ベリリウム、 酸化アルミ二 ゥムを主成分とする焼結体からなる基板を用意した。 これらの基板表面は実施例 8及び実施例 9と同様の方法による鏡面研磨が施さ l 匕メチレンで超音波洗浄してある。
次にこのようにして用意した基板の一部を選びその上に実施例 25の実験 N o. 706、 7 07及び 708で行ったスパッタリング法及び実験 No. 709で行った MOCVD法と同様 の条件により 100モル%A 1 Nの薄膜を厚み 3 mであらかじめ形成した。 さらに実験 No. 714、 728、 729、 730で行った MOCVD法と同様の条件により 100モル%G a Nの薄膜を厚み 3 mであらかじめ形成し、 実験 No. 715、 731で行った MOCVD法 と同様の条件により 100モル% I nNの薄膜を厚み 3 mであらかじめ形成した。 次に上記 のようにしてあらかじめ A 1N薄膜、 GaN薄膜、 I nN薄膜が形成された基板と A 1 N薄膜 を形成せずに残しておいた基板とを用いその上にさらに実施例 19に記載されたものと同じ 1 00モル%A 1 N、 100モル%GaN、 100モル% I nN、 50モル%A 1 N+ 50モル% GaN, 50モル%GaN+50モル% I nN各組成の薄膜を MOCVD法により厚み 3 zm 形成した。 MOCVDの条件としては実施例 19に記載のように実施例 1及び実施例 2と同様 の条件であった。
このようにして作製した薄膜の特性を表 41及び表 42に示した。 なお、 表 41にはあらか じめ形成する薄膜として A 1 Nを用いた例が記載されている。 表 42にはあらかじめ形成する 薄膜として G a N及び I n Nを用いた例が記載されている。
表 41に示すように炭化珪素、 窒化珪素、 酸化亜鉛、 酸化ベリリウム、 酸化アルミニウムを 主成分とする焼結体からなる基板に M〇 C VD法によりあらかじめ直接形成された G a N薄膜 は窒化アルミニウムを主成分とする焼結体と同様実施例 25の実験 No. 706、 707、 7 08及び 709で形成された A 1 N薄膜の結晶状態に対応したものが形成された。 すなわち、 実験 N o. 706と同様の条件のスパッ夕リング法により形成した実験 N o. 948、 959、 966、 977の A 1 N薄膜は無定形であり、 実験 N o . 707と同様の条件のスパッタリン グ法により形成した実験 No. 949、 967、 978の A 1 N薄膜はミラ一指数 (002)、
(101)、 (102) の格子面からの回折線だけが出現している多結晶であった。 また、 実験 No. 708と同様の条件のスパッタリング法により形成した A 1 N薄膜はミラー指数 (00 2) の格子面からの回折線だけが出現しており、 基板面に対して C軸が垂直な方向に形成され た配向性多結晶であった。 また、 実験 No. 709と同様の条件の MOCVD法により形成し た実験 No. 951、 969、 980、 989の A 1 N薄膜はミラー指数 (002) の格子面 からの回折線だけが出現しており、 基板面に対して C軸が垂直な方向に形成された単結晶であ ることが確認された。
表 41にはこれら基板にあらかじめ形成された薄膜のうち配向性多結晶及び単結晶状態で形 成された薄膜のミラ一指数 (002) の格子面の X線回折ロッキングカーブの半値幅が記載さ れている。
次にあらかじめ各種結晶状態の A 1 N薄膜を形成した基板、 及び A 1 N薄膜が形成されてい ない炭化珪素、 窒化珪素、 酸化亜鉛、 酸化ベリリウム、 酸化アルミニウムを主成分とする焼結 体からなる基板の上に上記 MOCVD法により形成した 100モル%A 1 N、 100モル%G
a N、 1 0 0モル% I n N、 5 0モル%A 1 N+ 5 0モル%G a N、 5 0モル%G a N+ 5 0 モル% I n N各組成からなる薄膜の結晶性を X線回折により調べた。 その結果、 作製したすべ ての薄膜が基板面に対して C軸が垂直な方向に形成された単結晶であることカ權認された。 そ の結晶†生を見ると、 炭ィ匕珪素、 窒化珪素、 酸化亜鉛、 酸ィ匕ベリリウム、 酸ィ匕アレミ二ゥムを主 成分とする焼結体からなる基板にあらかじめ A 1 N薄膜を形成せず直接基板上に形成した A 1 N、 G a N、 I n N単結晶薄膜のミラー指数 (0 0 2 ) の格子面の X線回折ロッキング力一ブ の半値幅はすべて 2 4 0秒以上であるのに対して、 上記各種セラミツクを主成分とする基板に あらかじめ A 1 N薄膜を形成しさらにその上に形成した A 1 N、 G a N、 I nN単結晶薄膜で はすべて 2 0 0秒以下であり明らかに結晶性の優れた単結晶薄膜が得られることが確認された。 また、 それぞれの焼結体においてあらかじめ形成された A 1 N薄膜の結晶状態が 向性多結晶 である方が単結晶、 無定形及び多結晶であるよりもさらにその上に形成される単結晶はより結 晶性に優れたものが形成され易い傾向を有していることが示された。 以下表 4 1に示された実 験結果に基づさ詳細に述べる。
炭化珪素を主成分とする焼結体からなる基板に直接形成された単結晶薄膜のミラー指数 ( 0 0 2) の格子面の X線回折ロッキングカーブの半値幅は 2 5 5秒〜 2 8 3秒の範囲であるのに 対して、 あらかじめ A 1 N薄膜を形成した基板に形成された単結晶薄膜では 1 3 9秒〜 1 9 2 秒の範囲であり、 明らかに結晶性の向上した単結晶薄膜が得られる。 また、 あらかじめ形成し た A 1 N薄膜が無定形、 多結晶、 単結晶の結晶状態の場合その上に形成された単結晶薄膜のミ ラー指数 (0 0 2 ) の格子面の X線回折ロッキングカーブの半値幅は 1 6 9秒〜 1 9 2秒の範 囲であるのに対して、 配向性多結晶の結晶状態のものの場合は 1 3 9秒〜 1 4 7秒の範囲であ りより結晶性の向上した単結晶薄膜が得られる。
窒化珪素を主成分とする焼結体からなる基板に直接形成された単結晶薄膜のミラー指数 (0 0 2) の格子面の X線回折ロッキングカーブの半値幅は 4 9 3秒〜 6 4 7秒の範囲であるのに 対して、 あらかじめ A 1 N薄膜を形成した基板に形成された単結晶薄膜では 1 6 3秒〜 1 8 8 秒の範囲であり、 明らかに結晶性の向上した単結晶薄膜が得られる。 また、 あらかじめ形成し た A 1 N薄膜が無定形の結晶状態の場合その上に形成された単結晶薄膜のミラ一指数 (0 0 2) の格子面の X線回折ロッキングカープの半値幅は 1 8 8秒のであるのに対して、 配向性多結晶 の結晶状態のものの場合は 1 6 3秒〜 1 6 7秒の範囲でありより結晶性の向上した単結晶薄膜 が、得られる。
酸化アルミ二ゥムを主成分とする焼結体からなる基板に直接形成された単結晶薄膜のミラー 指数 (0 0 2 ) の格子面の X線回折ロッキングカーブの半値幅は 3 7 7秒〜 4 2 6秒の範囲で あるのに対して、 あらかじめ A 1 N薄膜を形成した基板に形成された単結晶薄膜では 1 5 5秒 〜1 9 5秒の範囲であり、 明らかに結晶性の向上した単結晶薄膜が得られる。 また、 あらかじ め形成した A 1 N薄膜が無定形、 多結晶、 単結晶の結晶状態の場合その上に形成された単結晶 薄膜のミラ一指数 ( 0 0 2) の格子面の X線回折ロッキングカーブの半値幅は 1 6 9秒〜 1 9 5秒の範囲であるのに対して、 配向性多結晶の結晶状態のものの場合は 1 5 5秒〜 1 6 3秒の 範囲でありより結晶性の向上した単結晶薄膜が得られる。
酸化亜鉛を主成分とする焼結体からなる基板に直接形成された単結晶薄膜のミラー指数 ( 0 0 2) の格子面の X線回折ロッキングカーブの半値幅は 2 5 8秒〜 2 9 1秒の範囲であるのに 対して、 あらかじめ A 1 N薄膜を形成した基板に形成された単結晶薄膜では 1 3 6秒〜 1 9 6 秒の範囲であり、 明らかに結晶性の向上した単結晶薄膜が得られる。 また、 あらかじめ形成し た A 1 N薄膜が無定形、 多結晶、 単結晶の結晶状態の場合その上に形成された単結晶薄膜のミ ラー指数 (0 0 2) の格子面の X線回折ロッキングカーブの半値幅は 1 8 2秒〜 1 9 6秒の範 囲であるのに対して、 配向性多結晶の結晶状態のものの場合は 1 3 6秒〜 1 4 4秒の範囲であ
りより結晶性の向上した単結晶薄膜が得られる。
酸化ベリリゥムを主成分とする焼結体からなる基板に直接形成された単結晶薄膜のミラー指 数 (002) の格子面の X線回折ロッキングカーブの半値幅は 268秒〜 290秒の範囲であ るのに対して、 あらかじめ A 1 N薄膜を形成した基板に形成された単結晶薄膜では 137秒〜 192秒の範囲であり、 明らかに結晶性の向上した単結晶薄膜が得られる。 また、 あらかじめ 形成した A 1 N薄膜が単結晶の結晶状態の場合その上に形成された単結晶薄膜のミラー指数 (002) の格子面の X線回折ロッキングカーブの半値幅は 202秒であるのに対して、 配向 性多結晶の結晶状態のものの場合は 137秒〜 146秒の範囲でありより結晶性の向上した単 結晶薄膜が得られる。
表 42に示すように炭化珪素、 窒化珪素、 酸化亜鉛、 酸化ベリリウム、 酸化アルミニウムを 主成分とする焼結体からなる基板に MOCVD法によりあらかじめ直接形成された GaN薄膜 は窒化アルミニウムを主成分とする焼結体と同様実施例 25の実験 No. 714、 728、 7 29及び 730で形成された GaN薄膜の結晶状態に対応したものが形成された。 また、 MO CVD法によりあらかじめ直接形成された I nN薄膜も表 42に示すように実施例 25の実験 No. 715及び 731で形成された I nN薄膜の結晶状態に対応したものが形成された。 すなわち、実験 No. 728と同様の条件の MOCVD法により形成した実験 No. 994、 1003、 1010、 1019、 1028の GaN薄膜は無定形であり、 実験 No. 729と 同様の条件の MOCVD法により形成した実験 No. 995、 1004、 1011、 1020、 1029の GaN薄膜はミラ一指数 (002)、 (101) の格子面からの回折線だけが出現し ている多結晶であった。 また、 実験 No. 730と同様の条件の MOCVD法により形成した GaN薄膜はミラー指数 (002) の格子面からの回折線だけが出現しており、 基板面に対し て C軸が垂直な方向に形成された配向性多結晶であった。 また、 実験 No. 714と同様の条 件の M〇 C VD法により形成した実験 N o . 997、 1006、 1013、 1022、 103 1の GaN薄膜はミラー指数 (002) の格子面からの回折線だけが出現しており、 基板面に 対して C軸が垂直な方向に形成された単結晶であることが確認された。
また、 実験 No. 731と同様の条件の M〇 C V D法により形成した実験 N o . 1001、 1008、 1017、 1026、 1035の I nN薄膜はミラ一旨数 (002) の格子面から の回折線だけが出現しており、 基板面に対して C軸が垂直な方向に形成された配向性多結晶で あった。 また、 実験 No. 715と同様の条件の MOCVD法により形成した実験 No. 10
02、 1009、 1018、 1027、 1036の I nN薄膜はミラ一指数 (002) の格子 面からの回折線だけが出現しており、 基板面に対して C軸が垂直な方向に形成された単結晶で あることが確認された。
上記のように表 42にはこれら炭化珪素、 窒化珪素、 酸化亜鉛、 酸化ベリリウム、 酸化アル ミニゥムを主成分とする焼結体からなる基板にあらかじめ直接形成された薄膜の X線回折によ り同定された結晶状態が示されている。 これらの薄膜のうち配向性多結晶及び単結晶として同 定された薄膜のミラー指数 (002) の格子面の X線回折ロッキング力一ブの半値幅が己載さ れている。
次にあらかじめ各種結晶状態の GaN薄 び I nN薄膜を形成した基板、及び GaN薄膜、
1 nN薄膜が形成されていない炭化珪素、 窒化珪素、 酸化亜鉛、 酸化ベリリウム、 酸化アルミ 二ゥムを主成分とする焼結体からなる基板の上に上記 MOCVD法により形成された 100モ %A1N、 100モル%GaN、 100 %ΙηΝ、 50モル%Α 1 Ν+ 50モル%Ga N、 50モル% GaN+50モル% I n N各組成からなる薄膜の結晶性を X線回折により調べ た。 その結果、 作製したすべての薄膜が基板面に対して C軸が垂直な方向に形成された単結晶 であることカ權認された。 その結晶性を見ると、 表 42に示すように炭化珪素、 窒化珪素、 酸
化亜鉛、 酸化ベリリウム、 酸化アルミニウムを主成分とする焼結体からなる基板にあらかじめ 。&?^薄]11¾び11^薄膜を形成せず直接基板上に形成した八11^ GaN、 I nN単結晶薄 膜のミラー指数 (002) の格子面の X線回折ロッキングカーブの半値幅はすべて 240秒以 上であるのに対して、 あらかじめ各種セラミックを主成分とする基板に GaN薄膜及び I nN 薄膜を形成しその上にさらに形成した A 1N、 GaN、 I nN単結晶薄膜ではすべて 200秒 以下であり明らかに結晶性の優れた単結晶薄膜が得られることがI認された。 また、 それぞれ の焼結体においてあらかじめ形成された G aN薄膜及び I nN薄膜の結晶状態として配向性多 結晶である方が単結晶、 無定形及 ϋ 結晶であるよりもさらにその上に形成される単結晶はよ り結晶性に優れたものが形成され易い傾向を有していることが示された。 表 42に示された結 果に基づき以下詳細に述べる。
炭化珪素を主成分とする焼結体からなる基板に直接形成された単結晶薄膜のミラー指数 (0 0 ) の格子面の X線回折ロッキングカーブの半値幅は 255秒〜 283秒の範囲であるのに 対して、 あらかじめ GaN薄膜あるいは I nN薄膜を形成した基板に形成された単結晶薄膜で は 137秒〜 189秒の範囲であり、明らかに結晶性の向上した単結晶薄膜が得られる。また、 あらかじめ形成した GaN薄膜あるいは InN薄膜が無定形、 多結晶、 単結晶の結晶状態の場 合その上に形成された単結晶薄膜の.ミラー指数 (002) の格子面の X線回折ロッキングカー ブの半値幅は 165秒〜 189秒の範囲であるのに対して、 配向性多結晶の結晶状態のものの 場合は 137秒〜 146秒の範囲でありより結晶性の向上した単結晶薄膜が得られる。
窒化珪素を主成分とする焼結体からなる基板に直接形成された単結晶薄膜のミラー指数 (0 02) の格子面の X線回折ロッキングカーブの半値幅は 493秒〜 647秒の範囲であるのに 対して、 あらかじめ GaN薄膜あるいは I nN薄膜を形成した基板に形成された単結晶薄膜で は 141秒〜 189秒の範囲であり、明らかに結晶性の向上した単結晶薄膜が得られる。また、 あらかじめ形成した GaN薄膜あるいは InN薄膜が無定形、 多結晶、 単結晶の結晶状態の場 合その上に形成された単結晶薄膜のミラー指数 (002) の格子面の X線回折ロッキングカー ブの半値幅は 169秒〜 189秒の範囲であるのに対して、 配向性多結晶の結晶状態のものの 場合は 161秒〜 167秒の範囲でありより結晶性の向上した単結晶薄膜が得られる。
酸化アルミニウムを主成分とする焼結体からなる基板に直接形成された単結晶薄膜のミラ一 指数 (002) の格子面の X線回折ロッキングカーブの半値幅は 377秒〜 426秒の範囲で あるのに対して、 あらかじめ GaN薄膜あるいは I nN薄膜を形成した基板に形成された単結 晶薄膜では 154秒〜 190秒の範囲であり、 明らかに結晶性の向上した単結晶薄膜が得られ る。 また、 あらかじめ形成した GaN薄膜あるいは I nN薄膜が無定形、 多結晶、 単結晶の結 晶状態の場合その上に形成された単結晶薄膜のミラ一指数 (002) の格子面の X線回折ロッ キングカーブの半値幅は 170秒〜 190秒の範囲であるのに対して、 配向性多結晶の結晶状 態のものの場合は 154秒〜 165秒の範囲でありより結晶性の向上した単結晶薄膜が得られ る。
酸化亜鉛を主成分とする焼結体からなる基板に直接形成された単結晶薄膜のミラー指数 (0 02) の格子面の X線回折ロッキングカーブの半値幅は 258秒〜 291秒の範囲であるのに 対して、 あらかじめ GaN薄膜あるいは I nN薄膜を形成した基板に形成された単結晶薄膜で は 136秒〜 192秒の範囲であり、明らかに結晶性の向上した単結晶薄膜が得られる。また、 あらかじめ形成した GaN薄膜あるいは I nN薄膜が無定形、 多結晶、 単結晶の結晶状態の場 合その上に形成された単結晶薄膜のミラー指数 (002) の格子面の X線回折ロッキング力一 ブの半値幅は 157秒〜 192秒の範囲であるのに対して、 配向性多結晶の結晶状態のものの 場合は 137秒〜 146秒の範囲でありより結晶性の向上した単結晶薄膜が得られる。
酸化ベリリゥムを主成分とする焼結体からなる基板に直接形成された単結晶薄膜のミラー指
数 (002) の格子面の X線回折ロッキングカーブの半値幅は 268秒〜 290秒の範囲であ るのに対して、 あらかじめ GaN薄膜あるいは I nN薄膜を形成した基板に形成された単結晶 薄膜では 138秒〜 190秒の範囲であり、 明らかに結晶性の向上した単結晶薄膜が得られる。 また、 あらかじめ形成した GaN薄膜あるいは I nN薄膜が無定形、 多結晶、 単結晶の結晶状 態の場合その上に形成された単結晶薄膜のミラ一指数 (002) の格子面の X線回折ロッキン グカーブの半値幅は 160秒〜 190秒の範囲であるのに対して、 配向性多結晶の結晶状態の ものの場合は 138秒〜 147秒の範囲でありより結晶性の向上した単結晶薄膜が得られる。
'本実施例において表 41、 表 42に記載した実験で作製したすべての薄膜の外観を調べたが あらかじめ基板に形成した薄膜及びその上にさらに形成した薄膜いずれもクラックやひび割れ などの欠陥は見られない。 また、 粘着テープによる剥離テストを行ったがいずれの薄膜も窒化 アルミニウムを主成分とする焼結体からなる基板との間及び奪膜同志の間で剥離は見られなか つた。 また、 基板表面の薄膜に Ti/P t/Auの薄膜導電性材料を形成して金属リードをは んだ付けし垂直弓 I張り強度を調べたがすべて 2 K g Zmm2以上であり窒化アルミニゥムを主 成分とする焼結体とあらかじめ基板に形成した薄膜、 及び該薄膜とその上にさらに形成した薄 膜とは強固に接合している。
実施例 28
本実施例は炭化珪素、 窒化珪素、 酸化碰、 酸化ベリリウム、 酸化アルミニウムを主成分と する焼結体を基板として用い、 これらの基板の表面平滑性及びその上に形成される窒化ガリウ ム、 窒化インジウム、 窒化アルミニウムを主成分とする薄膜の層構成がこれら薄膜の結晶性に 及ぼす影響を調べた例を示す。
まず、 実施例 1で作製した炭化珪素、 窒化鶴、 酸化葡、 酸化ベリリウム、 酸化アルミ二 ゥムを主成分とする焼結体からなる基板を用意した。 これらの基板表面は実施例 8及び実施例 9と同様の方法による鏡面研磨が施され塩化メチレンで超音波洗浄してある。 その他、 市販の 布製パッドをポリシャ一として用い研 として以下のものをそれぞれ用いて鏡面研磨した基 板も新たに用意した。 すなわち、 酸化アルミニウムを主成分とする焼結体からなる基板を粒径 0. 05 mのコロイド状アルミナを主成分とする研顧 jを用いて鏡面研磨したもの、 酸化亜 鉛を主成分とする焼結体からなる基板を粒径 0. 05庫の酸化セリゥムを主成分とする研磨 剤を用いて鏡面研磨したもの、 酸化ベリリウムを主成分とする焼結体からなる基板を;^圣 0. 02 mのコロイド状の酸化珪素を主成分とする研麟 IJを用いて鏡面研磨したもの、 も新たに 用意した。
次に用意した上記の表面平滑性の異なる各基板に対して実施例 27に示したものと同様の方 法で薄膜を形成した。 すなわち、 用意した基板の上に実施例 25の実験 No. 706、 707 及び 708で行つたスパッタリング法及び実験 N o. 709、 721で行つた MOCVD法と 同様の条件により 100モル%A 1 Nの薄膜を厚み 3 mであらかじめ形成した。 さらに実験 No. 730で行った MOCVD法と同様の条件により 100モル%G aNの薄膜を厚み 3 mであらかじめ形成し、 実験 No. 731で行った MOCVD法と同様の条件により 100モ ル% I nNの薄膜を厚み 3 mであらかじめ形成した。 次に上記のようにしてあらかじめ A 1 N薄膜、 GaN薄膜、 I nN薄膜が形成された基板を用いその上にさらに実施例 19に記載さ れたものと同じ 100モル%A 1 N、 100モル%GaN、 100モル% I nN、 50モル% A 1N+50モル%GaN、 50モル%GaN+50モル% I nN各組成の薄膜を MOCVD 法により厚み 3 m形成した。 MOCVDの条件としては実施例 19に記載のように実施例 1 及び実施例 2と同様の条件であった。
以上の実験結果をまとめて表 43に示した。
すなわち、 表 43に¾ ^実施例で新たに作製した鏡面研磨面を有する酸化アルミニウムを主
成分とする焼結体、 酸化亜鉛を主成分とする焼結体、 酸化ベリリウムを主成分とする焼結体、 それぞれからなる基板の平均表面粗さ R aがそれぞれ 7. 3nm、 2. 6 nm、 3. 7 nmで あることが示されている。
本実施例において、 基板にあらかじめ直接形成した 100モル%A 1 N薄膜は実施例 25の 実験 No. 706、 707、 708、 709及び 721で作製した A 1 N薄膜の結晶状態に対 応したものが形成された。 すなわち、 実験 No. 706と同様の条件のスパッタリング法によ り形成した A 1N薄膜は無定形であり、 実験 No. 707と同様の条件のスパッタリング法に より形成した A 1N薄膜はミラー指数 (002)、 (101)、 (102) の格子面からの回折線 だけが出現している多結晶であった。 また、 実験 No. 708と同様の条件のスパッタリング 法により形成した A 1N薄膜はミラー指数 (002) の格子面からの回折線だけが出現してお り、 基板面に対して C軸が垂直な方向に形成された配向性多結晶であった。 また、 実験 No. 709と同様の条件の MOCVD法により形成した A 1 N薄膜はミラ一指数 (002) の格子 面からの回折線だけが出現しており、 基板面に対して C軸が垂直な方向に形成された単結晶で あることが 認された。 また、 実験 No. 721と同様の条件の MOCVD法により形成した A 1N薄膜はミラー指数 (002) の格子面からの回折線だけが出現しており、 基板面に対し て C軸が垂直な方向に形成された配向性多結晶であり、 結晶性は同じ配向性多結晶の結晶状態 を示した実験 No. 708のものより向上していた。
基板にあらかじめ直接形成した 100モル% G a N'薄膜は実施例 5の実験 N o . 730で 作製した G a N薄膜の結晶状態に対応したものが形成された。 すなわち、 実験 No. 730と 同様の条件の MOCVD法により形成した GaN薄膜はミラ一指数 (002) の格子面からの 回折線だけが出現しており、 基板面に対して C軸が垂直な方向に形成された配向性多結晶であ っ卞こ。
また、 基板にあらかじめ直接形成した 100モル% I nN薄膜は実施例 25の実験 No. 7 31で作製した I nN薄膜の結晶状態に対応したものが形成された。 すなわち、 実験 No. 7 31と同様の条件の MOCVD法により形成した I nN薄膜はミラー指数 (002) の格子面 からの回折線だけが出現しており、 基板面に対して C軸が垂直な方向に形成された配向性多結 晶であった。
表 43にはこれら基板にあらかじめ形成された薄膜の X線回折により同定された結晶状態が 示されているが、 その中で配向性多結晶及び単結晶として同定された薄膜のミラー指数 (00 2) の格子面の X線回折ロッキングカーブの半値幅が記載されている。
次にあらかじめ各種結晶状態の A 1 N薄膜、 GaN薄膜及び I nN薄膜を形成した炭化珪素、 窒化珪素、 酸化亜鉛、 酸化ベリリウム、 酸化アルミニウムを主成分とする焼結体からなる基板 の上に上記 MOCVD法により形成された 100モル%A 1 N、 100モル%GaN、 100 モル% I nN、 50モル%A 1 N+50モル%GaN、 50モル%G aN+ 50モル% I nN 各組成からなる薄膜の結晶性を X線回折により調べた。 その結果、 作製したすべての薄膜が基 板面に対して C軸が垂直な方向に形成された単結晶であることが ϋ認された。 その結晶性を見 ると、 表 43に示すように炭化珪素、 窒化珪素、 酸化亜鉗、 酸化ベリリウム、 酸化アルミニゥ ムを主成分とする焼結体からなる基板のすべてにおいてその平均表面粗さ R aが小さくなるに つれて向上する傾向があることが ϋ認された。 すなわち R aが 10 nmより大きい基板を用い たときあらかじめ配向性多結晶薄膜を形成した場合であっても形成される単結晶薄膜のミラ一 指数 (002) の格子面の X線回折ロッキング力一ブの半値幅は 150秒より大きいのに対し て、 Raが 10 nm以下のものではあらかじめ配向性多結晶薄膜を形成した場合 150秒以下 と結晶性が向上し、 R aが 5 nm以下のものではあらかじめ形成する薄膜が無定形、 多結晶、 配向性多結晶、 単結晶の結晶状態を有するすべての場合 130秒以下とさらに向上することが
確認された。
表 4 3に示された結果に基づき以下詳細に述べる。
炭化珪素を主成分とする焼結体からなる基板の場合、 平均表面粗さ R aが 6. 8 nmのもの にあらかじめ形成される薄膜の結晶状態が無定形の場合その上にさらに形成された単結晶薄膜 のミラ一指数 ( 0 0 2) の格子面の X線回折ロッキングカーブの半値幅は 1 6 5秒であり結晶 状態が己向性多結晶である薄膜の上からさらに形成した単結晶薄膜のミラ一指数 (0 0 2) の 格子面の X線回折ロッキングカーブの半値幅は 1 3 9秒〜 1 4 5秒の範囲であるのに対して、 平均表面粗さ R aが 2. 9 nmの基板を用いた場合ではあらかじめ形成した無定形薄膜、 多結 晶薄膜、 配向性多結晶薄膜、 単結晶薄膜の上からさらに形成した単結晶薄膜のミラー指数 ( 0 0 2)の格子面の X線回折ロッキングカーブの半値幅は 1 3 0秒以下と結晶性が向上していた。 特にあらかじめ形成した配向性多結晶薄膜の上からさらに形成した単結晶薄膜のミラー指数
( 0 0 2) の格子面の X線回折ロッキングカーブの半値幅は 1 2 0秒以下とさらに向上してい た。
窒化珪素を主成分とする焼結体からなる基板の場合、 平均表面粗さ R aが 1 5 nmのものに あらかじめ形成されている無定形薄膜及び ¾己向性多結晶薄膜の上からさらに形成した単結晶薄 膜のミラ一指数 (0 0 2) の格子面の X線回折ロッキングカーブの半値幅は 1 6 9秒〜 1 8 9 秒の範囲であるのに対して、 平均表面粗さ R aが 4. 4 nmの基板を用いた場合ではあらかじ め形成した無定形薄膜、 多結晶薄膜、 配向性多結晶薄膜、 単結晶薄膜の上からさらに形成した 単結晶薄膜のミラー指数 ( 0 0 2) の格子面の X線回折ロッキングカーブの半値幅は 1 3 0秒 以下と結晶性が向上していた。 特にあらかじめ形成した配向性多結晶薄膜の上からさらに形成 した単結晶薄膜のミラー指数 ( 0 0 2 ) の格子面の X線回折ロッキングカーブの半値幅は 1 2 0秒以下とさらに向上していた。
酸化アルミニウムを主成分とする焼結体からなる基板の場合、 平均表面粗さ R aが 1 l nm のものにあらかじめ形成されている無定形薄膜及び 向性多結晶薄膜の上からさらに形成した 単結晶薄膜のミラ一指数 ( 0 0 2) の格子面の X線回折ロッキングカーブの半値幅は 1 5 4秒 〜1 7 7秒の範囲であるのに対して、 平均表面粗さ R aが 7. 3 nmの基板を用いた場合では あらかじめ形成した薄膜が配向性多結晶に結晶状態のものでその上にさらに形成した単結晶薄 膜のミラ一指数 (0 0 2 ) の格子面の X線回折ロッキングカーブの半値幅は 1 3 5秒〜 1 4 0 秒の範囲であり結晶性が向上していた。 また、 平均表面粗さ R aが 1 . 9 nmの基板を用いた 場合あらかじめ形成した無定形薄膜、 多結晶薄膜、 配向性多結晶薄膜、 単結晶薄膜の上からさ らに形成した単結晶薄膜のミラー指数 ( 0 0 2) の格子面の X線回折ロッキングカーブの半値 幅は 1 3 0秒以下と結晶性が向上していた。 特にあらかじめ形成した配向性多結晶薄膜の上か らさらに形成した単結晶薄膜のミラー指数 (0 0 2) の格子面の X線回折ロッキングカーブの 半値幅は 1 2 0秒以下とさらに向上していた。
酸化亜鉛を主成分とする焼結体からなる基板の場合、 平均表面粗さ R aが 8. 8 nmのもの にあらかじめ形成される薄膜の結晶状態が無定形の塲合その上にさらに形成された単結晶薄膜 のミラー指数 (0 0 2 ) の格子面の X線回折ロッキングカーブの半値幅は 1 7 0秒であり結晶 状態が 向性多結晶である薄膜の上からさらに形成した単結晶薄膜のミラー指数 ( 0 0 2 ) の 格子面の X線回折ロッキングカーブの半値幅は 1 3 7秒〜 1 4 4秒の範囲であるのに対して、 平均表面粗さ R aが 2. 6 nmの基板を用いた場合ではあらかじめ形成した無定形薄膜、 多結 晶薄膜、 配向性多結晶薄膜、 単結晶薄膜の上からさらに形成した単結晶薄膜のミラー指数 ( 0 0 2) の格子面の X線回折ロッキングカーブの半値幅は 1 3 0秒以下と結晶性が向上していた。 特にあらかじめ形成した配向性多結晶薄膜の上からさらに形成した単結晶薄膜のミラ一指数
( 0 0 2 ) の格子面の X線回折ロッキングカーブの半値幅は 1 2 0秒以下とさらに向上してい
た。
酸化ベリリゥムを主成分とする焼結体からなる基板の場合、 平均表面粗さ R aが 9. 4 nm のものにあらかじめ形成される薄膜の結晶状態が無定形の場合その上にさらに形成された単結 晶薄膜のミラー指数 (0 0 2 ) の格子面の X線回折ロッキングカーブの半値幅は 1 6 6秒であ り結晶状態が 向性多結晶である薄膜の上からさらに形成した単結晶薄膜のミラー指数 ( 0 0 2 ) の格子面の X線回折ロッキングカーブの半値幅は 1 3 8秒〜 1 4 1秒の範囲であるのに対 して、平均表面粗さ R a力 S 3. 7 nmの基板を用いた場合ではあらかじめ形成した無定形薄膜、 多結晶薄膜、 配向性多結晶薄膜、 単結晶薄膜の上からさらに形成した単結晶薄膜のミラー指数
( 0 0 2 ) の格子面の X線回折ロッキングカーブの半値幅は 1 3 0秒以下と結晶性が向上して いた。 特にあらかじめ形成した配向性多結晶薄膜の上からさらに形成した単結晶薄膜のミラー 指数 (0 0 2 ) の格子面の X線回折ロッキングカーブの半値幅は 1 2 0秒以下とさらに向上し ていた。 に直接形成された単結晶薄膜のミラー指数 (0 0 2) の格子面の X線回折ロッキング カーブの半値幅は 2 6 8秒〜 2 9 0秒の範囲であるのに対して、 あらかじめ A 1 N薄膜を形成 した基板に形成された単結晶薄膜では 1 3 8秒〜 1 9 0秒の範囲であり、 明らかに結晶性の向 上した単結晶薄膜が得られる。
上記のように本実施例において、 あらかじめ A 1 N薄膜、 G a N薄膜、 I n N薄膜が形成さ れた炭化珪素、 窒化珪素、 酸化亜鉛、 酸化ベリリウム、 酸化アルミニウムを主成分とする焼結 体からなる基板の上からさらに形成される単結晶薄膜の結晶性は該焼結体からなる基板の表面 平滑性の向上により改善される。 一方、 基板の表面平滑性の向上に伴いあらかじめ該焼結体か らなる基板に形成される配向性多結晶の結晶状態を有する A 1 N薄膜、 G a N薄膜、 I n N薄 膜の結晶性も向上する。 すなわち表 4 3に記載されているように炭化珪素、 窒化珪素、 謝匕亜 鉛、 酸化ベリリウム、 酸化アルミニウムを主成分とする焼結体からなる基板の平均表面粗さ R aが 1 O nmより大きい場合、 該基板にあらかじめ形成される上記配向性多結晶の結晶状態を 有する A 1 N薄膜、 G a N薄膜、 I n N薄膜のミラ一指数 ( 0 0 2) の格子面の X線回折ロッ キングカーブの半値幅が 1 0 0 0 0秒より大きくなり易く、 このような結晶性の配向性多結晶 薄膜の上に形成される単結晶薄膜のミラー指数 ( 0 0 2) の格子面の X線回折ロッキングカー ブの半値幅は 1 5 0秒より多きくなり易い傾向を有することが ϋ認された。 また、 炭化珪素、 窒化珪素、 酸化菌、 謝匕ベリリウム、 酸化アルミニウムを主成分とする焼結体からなる基板 の平均表面粗さ R aが 1 O nm以下の場合、 該基板にあらかじめ形成される上記配向性多結晶 の結晶状態を有する A 1 N薄膜、 G a N薄膜、 I n N薄膜のミラ一指数 ( 0 0 2 ) の格子面の X線回折ロッキングカープの半値幅が 1 0 0 0 0秒以下となり易く、 このような結晶性の配向 性多結晶薄膜の上に形成される単結晶薄膜のミラー指数 ( 0 0 2 ) の格子面の X線回折ロッキ ングカーブの半値幅は 1 5 0秒以下のものが形成され易い傾向を有することが歸忍された。 さ らに、 炭化珪素、 窒化珪素、 酸化亜鉛、 酸化ベリリウム、 酸化アルミニウムを主成分とする焼 結体からなる基板の平均表面粗さ R aが 5 nm以下の場合、 該基板にあらかじめ形成される上 記配向性多結晶の結晶状態を有する A 1 N薄膜、 G a N薄膜、 I n N薄膜のミラー指数 (0 0 2 ) の格子面の X線回折ロッキングカーブの半値幅が 8 0 0 0秒以下のものが形成でき、 この ような結晶性の配向性多結晶薄膜の上に形成される単結晶薄膜のミラー指数 ( 0 0 2) の格子 面の X線回折ロッキングカーブの半値幅は 1 3 0秒以下のものが形成され易い傾向を有するこ とが確認された。
本実施例において表 4 3に記載した実験で作製したすべての薄膜の外観を調べたがあらかじ め基板に形成した薄膜及びその上にさらに形成した薄膜いずれもクラックやひび割れなどの欠 陥は見られない。 また、 粘着テープによる剥離テストを行ったがいずれの薄膜も窒化アルミ二 ゥムを主成分とする焼結体からなる基板との間及び薄膜同志の間で剥離は見られなかった。 ま
た、 基板表面の薄膜に T i ZP t ZAuの薄膜導電性材料を形成して金属リードをはんだ付け し垂直引張り強度を調べたがすべて 2 K gZmm2以上であり窒化アルミニウムを主成分とす る焼結体とあらかじめ基板に形成した薄膜、 及び該薄膜とその上にさらに形成した薄膜とは強 固 接合している。
実施例 2 9
本実施例は窒化アルミニウムを主成分とする焼結体からなる基板、及び炭化珪素、窒化珪素、 酸化亜鉛、 酸化ベリリウム、 酸化アルミニウムを主成分とする焼結体からなる基板の中で表面 平滑性が比較的粗いものを用いて、 その上に形成される窒化ガリウム、 窒化インジウム、 窒化 アルミニウムを主成分とする薄膜の層構成によって形成される薄膜の結晶性に及ぼす影響を調 ベた例を示す。 .
まず、 実施例 2の実験 N o . 4 9で作製した窒化アルミニウムを主成分とする焼結体を用意し た。 別に実施例 1で作製した炭化珪素、 窒化珪素、 酸化亜鉛、 酸化ベリリウム、 酸化アルミ二 ゥムを主成分とする焼結体を用意した。 これらの基板の一部は実施例 8で用いた焼き放し (a s— f i r e) 状態及びラップ研磨状態の表面状態を有するものである。 また用意した焼結体 のうち一部のものは薄膜形成面を焼き放し状態のまま、 あるいはラップ研磨、 あるいはブラス ト研磨し、 その後さらに直径 2 5. 4mm厚み 0. 5 mmにカロェして薄膜形成用基板を作製し た。 本実施例において新たに作製した基板のうち焼き放し状態の基板表面を有するもの及びラ ップ研磨は実施例 8と同様の方法により加工を行った。 すなわち焼き放し状態の表面を有する 基板はすべて市販の髓 3 a mのアルミナ粉末を用 、てブラシ掛けにより表面の付着物を取り 除いたものである。 ラッフ W磨された基板のうち窒化アルミニウムを主成分とする焼結体の場 合 S i Cの體# 2 4 0のものを用いて行い、 酸化アルミニウムを主成分とする焼結体の場合 S i Cの髓 # 4 0 0のものを用いて行い、 酸化ベリリゥムを主成分とする焼結体の場合 S i Cの^ ¾# 2 4 0のものを用いて行った。 また、 ブラス卜研磨はサンドブラスト機により窒化 アルミニウムを主成分とする焼結体の場合アルミナの粒度 # 4 0 0のものを用いて行い、 炭化 珪素を主成分とする焼結体の場合アルミナの粒度 # 6 0 0のものを用いて行い、 窒化珪素、 酸 化アルミニウム及び酸化亜鉛を主成分とする焼結体の場合アルミナの粒度 # 8 0 0のものを用 い、 酸化ベリリゥムを主成分とする焼結体の場合アルミナの粒度 # 1 2 0 0のものを用いて行 つ/こ。
次に用意した上記の表面平滑性の異なる各基板に対して実施例 2 5、 2 6、 2 7、 2 8に示 したものと同様の方法で薄膜を形成した。 すなわち、 用意した基板の上に実施例 2 5の実験 N o . 7 0 6、 7 0 7及び 7 0 8で行つたスパッ夕リング法及び実験 N o . 7 0 9で行つた MO CVD法と同様の条件により 1 0 0モル%A 1 Nの薄膜をあらかじめ形成した。 さらに実験 N o . 7 3 0で行った MO CVD法と同様の条件により 1 0 0モル%G a Nの薄膜をあらかじめ 形成した。 なお、 上記基板にあらかじめ形成した薄膜の厚みはそれぞれ 6 / mとした。
次に上記のようにしてあらかじめ A 1 N薄膜、 G a N薄膜、 I n N薄膜が形成された基板を 用いその上にさらに実施例 1 9に記載されたものと同じ 1 0 0モル%A I N, 1 0 0モル%G a N各組成の薄膜を MO CVD法により厚み 3; m形成した。 M〇C VDの条件としては実施 例 1 9に記載のように実施例 1及び実施例 2と同様の条件であった。
以上の実験結果をまとめて表 4 4に示した。
その結果、窒化アルミニウムを主成分とする 結体からなる基板、及び炭化珪素、窒化珪素、 酸化 ¾、 酸化ベリリウム、 酸ィ匕アルミニウムを主成分とする焼結体からなる基板にはその表 面状態によらず、 実験例 7 0 6と同様のスパッタリング法により形成された A 1 N薄膜は無定 形、 実験例 7 0 7と同様のスパッタリング法により形成された A 1 N薄膜は多結晶、 実験例 7 0 8と同様のスパッタリング法により形成された A 1 N薄膜は配向性多結晶と、 実施例 2 5で
作製した薄膜と同様の結晶状態の薄膜が上記各焼結体からなる基板にあらかじめ直接形成され た。
一方、 窒化アルミニウムを主成分とする焼結体を基板として用いた場合、 実験例 7 0 9と同 様の MO CVD法により 1 0 0モル%A 1 N単結晶薄膜の形成を試みたが、 平均表面粗さ R a が 2 0 0 0 nmより大きい基板に形成された薄膜はミラ一指数(0 0 2)、 (1 0 1 )、 (1 0 2) の格子面からだけの回折ピークを示す多結晶体であり、 該基板には直接単結晶薄膜の形成は困 難であった。 それに対して平均表面粗さ R aが 2 0 0 0 nm以下の基板には単結晶薄膜を直接 形成することが可能であった。 また、 平均表面粗さ R aが 2 0 0 O nmより大きい窒化アルミ 二ゥムを主成分とする焼結体からなる基板を用いて、 あらかじめ 1 0 0モル%A 1 Nの無定形、 多結晶、 配向性多結晶の各結晶状態を有する薄膜を形成し、 さらにその上に形成した 1 0 0モ ル% A 1 N薄膜及び 1 0 0モル% G a N薄膜は単結晶ィ匕されており、 該単結晶薄膜のミラ一指 数 (0 0 2) の格子面の X線回折ロッキングカーブの半値幅はすべて 3 0 0秒以下であった。 また、 平均表面粗さ R a力 0 0 0 nm以下の窒化アルミニウムを主成分とする焼結体からな る基板を用いてあらかじめ 1 0 0モル% A 1 Nの無定形、 多結晶、 配向性多結晶の各結晶状態 を有する薄膜を形成し、 さらにその上に形成した 1 0 0モレ%A 1 N薄膜及び 1 0 0モル%G a N薄膜も単結晶化されており該単結晶薄膜のミラー指数 ( 0 0 2 ) の格子面の X線回折ロッ キング力一ブの半値幅は 1 0 0秒以下であった。
さらに、 炭化珪素、 窒化賴、 酸化亜鉛、 酸化ベリリウム、 酸化アルミニウムを主成分とす る焼結体を基板として用いた場合、 実験例 7 0 9と同様の MO CVD法により 1 0 0モル%A 1 N単結晶薄膜の形成を試みたが、 平均表面粗さ R aが 1 0 0 0 nmより大きい基板に形成さ れた薄膜はミラ一キ旨数 (0 0 2 )、 (1 0 1 )、 (1 0 2 ) の格子面からだけの回折ピークを示す 多結晶体であり、 該基板には直接単結晶薄膜の形成は困難であった。 それに対して平均表面粗 さ R aが 1 0 0 0 nm以下の基板には単結晶薄膜を直接形成することカ坷能であった。 また、 平均表面粗さ R aが 1 0 0 O nmより大きい炭化珪素、窒化珪素、酸化 酸化ベリリウム、 酸化アルミ二ゥムを主成分とする焼結体からなる基板を用いて、 あらかじめ 1 0 0モル%A 1 Nの無定形、 多結晶、 配向性多結晶の各結晶状態を有する薄膜を形成し、 さらにその上に形成 した 1 0 0モル%A 1 N薄膜及び 1 0 0モル%G a N薄膜は単結晶化されており、 該単結晶薄 膜のミラー指数 (0 0 2 ) の格子面の X線回折ロッキングカーブの半値幅はすべて 3 0 0秒以 下であった。 また、 平均表面粗さ R aが 1 0 0 O nm以下の炭化珪素、 窒化珪素、 酸化亜鉛、 酸化ベリリウム、 酸化アルミニウムを主成分とする焼結体からなる基板を用いてあらかじめ 1 0 0モル%八1 1^の無定形、 多結晶、 配向性多結晶の各結晶状態を有する薄膜を形成し、 さら にその上に形成した 1 0 0モル%A 1 N薄膜及び 1 0 0モル%G a N薄膜も単結晶化されてお り該単結晶薄膜のミラー指数 (0 0 2 ) の格子面の X線回折ロッキング力一ブの半値幅は 2 0 0秒以下であった。 また、 平均表面粗さ R aが 1 0 0 O nm以下の炭化珪素、 窒化珪素、 酸化 亜鉛、 酸化ベリリウム、 酸化アルミニウムを主成分とする焼結体からなる基板を用いてあらか じめ 1 0 0モル% A 1 Nの配向性多結晶状態を有する薄膜を形成し、 さらにその上に形成した 1 0 0モル%A 1 N薄膜及び 1 0 0モル%G a N薄膜も単結晶化されており該単結晶薄膜のミ ラー指数 (0 0 2 ) の格子面の X線回折ロッキングカーブの半値幅は 1 5 0秒以下であった。 実施例 3 0
本実施例は酸化亜鉛を主成分とする焼結体を基板として用いたとき該基板の組成と該基板に 形成される窒化ガリウム、 窒化インジウム、 窒化アルミニウムを主成分とする薄膜の結晶性に 及ぼす影響を調べた例を示す。
まず、 酸化亜鉛 (Z n〇) 粉末として関東化学株式会ネ懷の特級雷纖粉末を用意し、 アルミ ナ (A l a03) 粉末としてアルコア社製の商品名 「A— 1 6 S GJ を原料として用意し、 実施
例 1と同様の方法によりこれらの粉末を所定の組成になるようポールミルで混合後ノ ワックスを加えて成形用粉末を作製し、 実施例 1と同様の大きさの成形体に一軸プレス成形後 脱脂し、 その後 1 4 6 0 °Cで 1時間大気中で常圧誠してアルミニウム成分を各種割合で含有 する酸化亜鉛を主成分とする焼結体を作製した。 これらの焼結体はいずれも相対密度 9 8 %以 上に緻密化していた。 このようにして作製した酸化亜鉛を主成分とする焼結体はアルミニウム 成分を含まないものでは麟白色であつたが、 アルミニウム成分を含むものでは青色への呈色 が見られるようになりアルミニゥム成分の含有量が増加するにつれてより濃い青色へと呈色が 進み、 3. 0モル%.の A 1 2〇3を含むもので最も濃い青色を呈し、 その後アルミニウム成分の 含有量が増加するにつれて青色ィ匕の程度は弱くなり青白色の色調へと次第に変化した。
その他別に株式会社高纖化^ ff究所製の献 9 9. 9 9 %以上の F e 2〇3粉末及び 9 9. 9 %以上の C r 2〇3粉末を用意した。 また、 希土編素化合物として信越化学工業株式会 社製の¾¾ 9 9. 9 9 %以上の Y203粉末、 « 9 9. 9 9 %以上の E r 203粉末、 ¾¾ 9 9. 9 9 %以上の Yb 2〇3粉末、 ¾]¾ 9 9. 9 9 %以上の D y 2〇3粉末、 « 9 9. 9 9 %以上の H o 203粉末を用意した。 次に本実施例で示した方法と同様の方法により、 上記各粉末を酸化 亜鉛 末及びアルミ: ¾末と共に所定量ポールミルで混合後一軸プレス成形し 1 4 6 で 1 時間大気中常圧誠して 分だけを含有する酸化亜鉛を主成分とする焼結体、 クロム成分だ けを含有する酸化亜鉛を主成分とする焼結体、 イツトリゥム成分だけを含有する酸化亜鉛を主 成分とする焼結体、 エルビウム成分だけを含有する酸ィ^«を主成分とする焼結体、 イツテル ビゥム成分だけを含有する酸化亜鉛を主成分とする焼結体、 アルミニウム成分と鉄成分とを同 時に含有する酸化亜鉛を主成分とする焼結体、 アルミニウム成分とクロム成分とを同時に含有 する酸化亜鉛を主成分とする焼結体、 及びアルミニウム成分と各種希土^ £素成分とを同時に 含む酸化亜鉛を主成分とする焼結体を作製した。
上記のようにして得られた各焼結体の室温における抵抗率を 4端子法で測定した。 その後得 られた各焼結体を ϋ圣 0. 0 2 mのコロイド状酸化珪素を主成分とする研麟 Jで鏡丽磨し、 さらに塩化メチレン及び I P Aで超音波洗浄し基板を作製した。 鏡面研激麦の基板の平均表面 粗さ R aは 6. 9 nm〜7. 7 nmの範囲であった。 研磨後の基板を用いて波長 6 0 5 nmの 光に対する光透過率を実施例 2と同様の方法により測定した。
このようにして得られた酸化亜鉛を主成分とする焼結体からなる基板の特性を表 4 5及び表 4 6に示す。 作製した上記酸化亜鉛を主成分とする焼結体からなる基板のうちアルミニウム成 分だけを含むもの、 及びアルミニウム成分を含まずクロム成分、 鉄成分、 イットリウム成分、 エルビウム成分、 イッテルビウム成分だけを含むものの特性は表 4 5に記載した。 一方、 アル ミニゥム成分とクロム成分、 鉄成分、 各種希土 素成分とを同時に含む酸化亜鉛を主成分と する焼結体からなる基板の特性は表 4 6に記載した。
表 4 5において、 実験 N o . 1 1 5' 0〜1 1 9 3がアルミニゥム成分だけを添加して焼成し た酸化亜鉛を主成分とする焼結体に関する実験結果であり 「組成」 の欄に該焼結体のアルミ二 ゥム成分の含有量が A 1 203換算で示されている。 表 4 5において、 実験 N o. 1 1 9 4〜1 1 9 5が鉄成分だけを添加して誠した酸化亜鉛を主成分とする焼結体に関する実験結果であ り「組成」の檷に該焼結体の鉄成分の含有量が F e 2〇 3露で示されている。表 4 5において、 実験 N o . 1 1 9 6〜1 1 9 7がクロム成分だけを添加して焼成した酸化亜鉛を主成分とする 焼結体に関する実験結果であり 「組成」 の欄に該焼結体のクロム成分の含有量が C r 2〇3換算 で示されている。 表 4 5において、 実験 N o . 1 1 9 8〜1 1 9 9がイットリウム成分だけを 添加して焼成した酸化亜鉛を主成分とする焼結体に関する実験結果であり 「組成」 の欄に該焼 結体のイットリウム成分の含有量が Y203換算で示されている。 表 4 5において、 実験 N o . 1 2 0 0〜1 2 0 1がエルビウム成分だけを添加して !«した酸化亜鉛を主成分とする焼結体
に関する実験結果であり 「組成」 の欄に該焼結体のエルビウム成分の含有量が Er 203藤で 示されている。 表 45において、 実験 No. 1202〜 1203がイッテルビウム成分だけを 添加して焼成した酸化亜鉛を主成分とする焼結体に関する実験結果であり 「組成」 の欄に該焼 結体のィッテルビウム成分の含有量が Y b 203換算で示されている。
表 45に示すように、 本実施例で作製した酸化: «を主成分とする焼結体はアルミニウム成 分を含まないものは電気^ t体であり、 アルミニウム成分の含有量が増加するにつれて抵抗率 が低下し、 A 1203騰で 3. 0モル%のアルミニウム成分を含むもので室温における抵抗率 が 1. 6X 10— 3Ω ·。 mと最も小さくなつた。 その後アルミニゥム成分の含有量が増加する につれて抵抗率が増大化し始め、 A 1203禱で 50. 0モル%のアルミニウム成分を含むも ので電気絶縁体となった。 ·
また、 表 45の実験 No. 1194〜1197で示すようにアルミニウム成分を含まず鉄成 分及びクロム成分をそれぞれ Fe203^で 1. 0モリレ%、 (:1"2〇3換算で1. 0モル%含有 する酸化亜鉛を主成分とする焼結体は導電性を示し室温において 8. 7X 10"^· cm, 3. 4X 10"ΧΩ - cmと比較的低い抵抗率であった。
表 46に示すようにアルミニウム成分と同時に鉄成分、 クロム成分、 各種希土観素成分と を複合で含む酸化亜鉛を主成分とする焼結体はすべて導電性を示し室温における抵抗率 7. 4 X 101 Ω · c m〜 1. 7X 10— 3 Ω · cmの範囲であった。 またその抵抗率はアルミニウム成 分だけを含む酸化 »を主成分とする焼結体の抵抗率に対して余り変化しておらず殆ど同じレ ベルであった。
表 45に示すようにアルミニウム成分を添加せずに «され実質的に原料中あるいは焼結体 製造時に混入する不純物以外は含まない酸化亜鉛を主成分とする焼結体の波長 605 nmの光 に対する光 ¾1率は 16 %であつたがアルミニゥム成分の含有量が増加するにつれ光透過率は 上昇する傾向を示し、 A 12〇3換算で 3. 0モル%のアルミニウム成分を含むものは 56%に 達した。 その後アルミニウム成分の含有量が増加するにつれ光透過率は次第に低下する傾向を 示し、 A 1203購で 50. 0モル%のアルミニウム成分を含む酸化亜鉛を主成分とする焼結 体では光 ¾率が 17%となり、 アルミニウム成分を含まない実質的に酸化亜鉛だけからなる 焼結体の光透過率と殆ど同じになつた。
また、 表 45の実験 No. 1194〜1197で示すようにアルミニウム成分を含まず鉄成 分及びクロム成分をそれぞれ F e 203換算で 1. 0モル%、 C r2〇3麟で 1. 0モル%含有 する酸化亜鉛を主成分とする焼結体の波長 605 nmの光に対する光透過率はそれぞれ 6.
9%、 9. 2%であった。
また、 表 45の実験 N o. 1198〜 1203で示すようにアルミニゥム成分を含まずィッ トリウム成分だけを Y203換算で 0. 04モル%、 エルビウム成分だけを Er203騰で 0.
04モル%及びィッテルビウム成分だけを Y b 2〇 3換算で 0. 04モル%をそれぞれ含有する 酸化 «を主成分とする焼結体の波長 605 nmの光に対する ¾¾ 率は 57 %、 53%、 5
4 %となり、 アルミニウム成分を含まない実質的に酸化亜鉛だけからなる焼結体の ¾¾¾率よ り上昇した。
さらに、 表 46に示すようにアルミニウム成分を A 12〇3換算で 3. 0モル%含み同時に鉄 成分あるいはクロム成分それぞれ Fe2〇3購で 0. 2モリレ%、 Cr2O3 T0. 2モル% 含有する酸化亜鉛を主成分とする焼結体は波長 605 nmの光に対する^ i率は 53 %、 5 5%であり、 アルミニウム成分だけを A 1203纏で 3. 0モル%含む酸化亜鉛を主成分とす る焼結体の光透過率と殆ど同じであった。
また、 表 46に示されているようにアルミニウム成分を A 1203騰で0. 03モル%含み 同時にィットリゥム成分を Y2〇3換算で 0. 0001モル%〜 12. 0モル%の範囲で含む酸
ィ匕亜鉛を主成分とする焼結体は、 イツトリゥム成分を Y203騰で 0. 0 0 0 1モル%含有す るものの波長 6 0 5 nmの光に対する 率は 2 8 %とアルミニウム成分だけを A 1 203換 算で 0. 0 3モル%含む酸化亜鉛を主成分とする焼結体の光 ¾ 率と殆ど同じであった。 さら にィッ卜リゥム成分の含有量が増加するにつれ光 ¾1率も上昇し Y203 で 0. 0 0 0 4モ ル%のイットリウム成分を含むもので 3 7 %、 Υ203換算で 0. 0 0 0 8モル%のイットリウ ム成分を含むもので 4 5 %、 Υ2〇3換算で 0. 0 0 1 5モル%のイットリウム成分を含むもの で 5 6 %、 Υ203換算で 0. 0 0 5モル%のイットリウム成分を含むもので 6 4 %、 Υ203換 算で 0. 0 4モル%のィットリゥム成分を含むもので 6 8 %に達した。 その後ィットリゥム成 分の含有量が増加するにつれ光透過率は次第に低下し Υ203換算で 1 2. 0モル%のィットリ ゥム成分を含む酸化亜鉛を主成分とする焼結体では波長 6 0 5 nmの光に対する光 ¾1率は 2 4 %となり、 アルミニゥム成分だけを A 1 2〇 3換算で 0. 0 3モル%含む酸化亜鉛を主成分と する焼結体の光 ¾M率と殆ど同じとなつた。
また、 表 4 6に示されているようにイットリウム成分を Y2〇3換算で 0. 0 4モル%含み同 時にアルミニゥム成分を A 1 2 O 3霧で 0. 0 0 2モル%〜 5 0. 0モル%の範囲で含む酸化 »を主成分とする焼結体は、 アルミニウム成分を A l 2〇3換算で 0. 0 0 2モ哈有するも のの波長 6 0 5 nmの光に対する 過率は 6 2 %であり、 さらにァリレミニゥム成分の含有量 が増加するにつれ) 率も上昇し A 1 203醇で 1 . 0モル%及び 3. 0モル%のアルミ二 ゥム成分を含むもので 8 4 %に達した。 その後アルミニウム成分の含有量が増加するにつれ光 ¾i率は次第に低下し A 1 2〇3購で 3 0. 0モル%のアルミニウム成分を含むもので光 ¾ii 率は 6 6 %であったが、 A 1 203 で 5 0. 0モル%のアルミニウム成分を含む酸化亜鉛を 主成分とする焼結体では波長 6 0 5 nmの光に対する光透過率は 2 7 %となった。
また、 表 4 6に示されているようにアルミニウム成分を A 1 203換算で0. 1 0モル%含み 同時にエルビウム成分を E r 203 で 0. 0 4モル%含む酸化亜鉛を主成分とする焼結体は 波長 6 0 5 nmの光に対する光透過率は 6 8 %であった。
また、 表 4 6に示されているようにアルミニウム成分を A 1 203藤で 3. 0モル%含み同 時に希土 素成分としてジスプロシゥム成分を D y 2〇 3換算で 0. 0 4モル%、 ホルミゥム 成分を H o 2〇3換算で 0. 0 4モル%、 エルビウム成分を E r 2〇3購で 0. 0 4モル%、 ィ ッテルビウム成分を Y b 2〇3換算で 0. 0 4モル%、 含有するものの波長 6 0 5 nmの光に対 する光 ¾1率はそれぞれ 7 7 %、 8 0 %、 7 8 %、 8 1 %髙いものであった。
また、 表 4 6に示されているようにアルミニウム成分を A 1 2〇3 で 1. 0モル%含みさ らにイットリウム成分を Y203換算で 0. 0 2モル%含みさらにエルビウム成分を E r 2〇3換 算で 0. 0 2モル%含む 3成分を同時に含む酸化亜鉛を主成分とする焼結体の波長 6 0 5 nm の光に対する光透過率は 8 3 %と高いものであった。
次に用意した上記の基板に対して実施例 2 7に示したものと同様の方法で薄膜を形成した。 すなわち、 用意した基板の一部を選びその上に実施例 2 5の実験 N o . 7 0 6、 7 0 7及び 7 0 8で行つたスパッ夕リング法及び実験 N o . 7 0 9で行つた M〇 C VD法と同様の条件によ り 1 0 0モル%A 1 Nの薄膜を厚み 3 mであらかじめ形成した。 さらに実験 N o . 7 2 8、 7 3 0で行った MO CVD法と同様の条件により 1 0 0モル%G a Nの薄膜を厚み 3 xmであ らかじめ形成し、 実験 N o . 7 3 1で行った MO CVD法と同様の条件により 1 0 0モル% I n Nの薄膜を厚み 3 mであらかじめ形成した。 なお、 アルミニウム成分と鉄成分とを同時に 含有する酸化亜鉛を主成分とする焼結体、 アルミニウム成分とクロム成分とを同時に含有する 酸化亜鉛を主成分とする焼結体、 及びアルミニウム成分と各種希土 素成分とを同時に含む 酸化亜铅を主成分とする焼結体からなる基板にあらかじめ形成する薄膜は実施例 2 5の実験 N o . 7 0 8で行ったスパッタリング法による 1 0 0モル% A 1 Nだけを用いた。
次に上記のようにしてあらかじめ窒化アルミニウムを主成分とする薄膜、 窒化ガリゥムを主 成分とする薄膜、 窒化ィンジゥムを主成分とする薄膜を形成した酸化亜鉛を主成分とする焼結 体からなる基板と、 薄膜を形成せずに残しておいた酸化亜鉛を主成分とする焼結体からなる基 板とを用いその上にさらに実施例 19に記載されたものと同じ 100モル%A 1 N、 100モ JVXGaN, 100モル% I nN、 50モル%A 1 N+50モル%GaN、 50モル%GaN + 50モル% I nN各組成の薄膜を MO CVD法により厚み 3 mで形成した。 MOCVDの 条件としては実施例 19に記載のように実施例 1及び実施例 2と同様の条件であった。 このよ うにして作製した薄膜の特性を表 45及び表 46に示した。
本実施例において、 上記各基板にあらかじめ形成した各薄膜はそれぞれの形成条件に対応し た結晶状態のものが形成された。
すなわち、 実験 No. 706と同様の条件のスパッタリング法により形成した A1N薄膜は 無定形であり、 実験 No. 707と同様の条件のスパッタリング法により形成した A 1 N薄膜 はミラー指数 (002)、 (101)、 (102) の格子面からの回折線だけが出現している多結 晶であつた。 また、 実験 N o. 708と同様の条件のスパッ夕リング法により形成した A 1 N 薄膜はミラー指数 (002) の格子面からの回折線だけが出現しており、 基板面に対して C軸 が垂直な方向に形成された配向性多結晶であった。 また、 実験 No. 709と同様の条件の M OCVD法により形成した A 1 N薄膜はミラー指数 (002) の格子面からの回折線だけが出 現しており、 基板面に対して C軸が垂直な方向に形成された単結晶であることが ¾認された。 実験 N o. 728と同様の条件の MOCVD法により形成した G aN薄膜は無定形であり、 実験 No. 730と同様の条件の MOCVD法により形成した GaN薄膜はミラ一指数 (00 2) の格子面からの回折線だけが出現しており、 基板面に対して C軸が垂直な方向に形成され た配向性多結晶であった。
また、 実験 No. 731と同様の条件の MOCVD法により形成した I nN薄膜はミラ一指 数 (002) の格子面からの回折線だけが出現しており、 基板面に対して C軸が垂直な方向に 形成された配向性多結晶であつた。
実験 No. 708と同様のスパッタリング法により形成した 100モ J1/%A 1 N配向性多結 晶薄膜の結晶性を見ると、 表 45に示すように実質的にアルミニウム成分を含まなレゝ酸化亜鉛 を主成分とする焼結体からなる基板を用いた場合、 該配向性多結晶薄膜のミラ一指数 (002) の格子面の X線回折ロッキングカーブの半値幅は 9430秒であった。 アルミニウム成分が増 加するにつれて該配向性多結晶薄膜の結晶性は向上する傾向を示した。 すなわち、 アルミニゥ ム成分を A 12〇3m で 0. 002モル%含む酸化亜鉛を主成分とする焼結体からなる基板を 用いた場合、 該基板に形成される A 1N配向性多結晶薄膜のミラー指数 (002) の格子面の X線回折ロッキングカーブの半値幅は 8190秒であり、 アルミニウム成分を A 1203換算で 0. 008モル%含む酸化亜鉛を主成分とする焼結体からなる基板を用いた場合は 7620秒 と 8000秒以下に低下した。 その後アルミニウム成分の含有量が増加するにつれて該 A 1 N 配向性多結晶薄膜の結晶性はやや向上する傾向を示し A 12 O 3. 0モル%を含む酸化 亜鉛を主成分とする基板を用いた場合では 7320秒〜 7460秒のものが形成され最も結晶 性は向上した。 その後アルミニウム成分の含有量が増加するにつれてやや結晶性は低下する傾 向を示した。 アルミニウム成分の含有量が A 1203騰で 40. 0モル%含む酸化亜鉛を主成 分とする基板を用いた場合で該 A 1 N配向性多結晶薄膜の結晶性は 7530秒〜 7570秒で あった。 しかしながら、 アルミニウム成分を A 1203換算で 50. 0モル%含む酸化亜鉛を主 成分とする焼結体からなる基板に形成した 100モル%A 1 N配向性多結晶薄膜の場合は 92 60秒と結晶性は低下した。
また、 表 46に示すようにアルミニウム成分を A 1203換算で 45. 0モル%以下含み、 さ
らに鉄成分、 クロム成分、 及び希土頻 素成分のうちから選ばれた少なくとも 1種以上の成分 を含む酸化亜鉛を主成分とする焼結体からなる基板を用いた場合でも、 該基板に形成した A 1 N配向性多結晶薄膜のミラ一指数 (0 0 2 ) の格子面の X線回折ロッキングカーブの半値幅は 7 3 8 0秒〜 7 9 2 0秒の範囲でありすべて 8 0 0 0秒以下であった。
次に、 上記の薄膜をあらかじめ形成せずに残しておいた酸化 «を主成分とする焼結体から なる基板を用いて前記 MO CVD法により形成した 1 0 0モル%A I N, 1 0 0モル%G a N、 1 0 0モル% I n N各組成からなる薄膜の結晶性を X線回折により調べた。 その結果、 作製し たすベての薄膜が基板面に対して C軸が垂直な方向に形成された単結晶であることが 認され た。 その結晶性を見ると、 表 4 5に示すようにアルミニウム成分を添加せずに焼成され実質的 に原料中あるいは焼結体 Sit時に混入する不純物以外は含まない酸化亜鉛を主成分とする焼結 体を基板として用いた場合該基板に直接形成される 1 0 0モル%A 1 N単結晶薄膜のミラ一指 数 (0 0 2) の格子面の X線回折ロッキングカーブの半値幅は 2 5 5秒であった。 一方アルミ ニゥム成分を A 1 203換算で 0. 0 0 2モル%含む酸化亜鉛を主成分とする焼結体からなる基 板に直接形成した 1 0 0モル%A 1 N単結晶薄膜の場合は 1 8 7秒と小さくなり結晶性が向上 した。 アルミニウム成分を A 1 203換算で 0. 0 0 8モル%含む酸化 を主成分とする焼結 体からなる基板に直接形成した 1 0 0モル%A 1 N単結晶薄膜の場合は 1 5 9秒であり結晶性 がより向上した。 アルミニウム成分を A l 2〇3丽で 0. 0 3モル%含む酸化 を主成分と する焼結体からなる基板に直接形成した 1 0 0モル%A 1 N単結晶薄膜の場合は 1 3 8秒であ り結晶性がさらに向上した。 また、 アルミニウム成分を A l 203騰で 0. 1モル%含む酸化 亜鉛を主成分とする焼結体からなる基板に直接形成した 1 0 0モル%A 1 N単結晶薄膜の場合 は 1 2 6秒と 1 3 0秒以下になり結晶性が一層向上した。 さらにアルミニウム成分の含有量が 増加するにしたがつて酸化亜鉛を主成分とする焼結体からなる基板に直接形成される単結晶薄 膜のミラー指数 ( 0 0 2 ) の格子面の X線回折ロッキングカーブの半値幅が小さくなつた。 ァ ルミニゥム成分を A 1 203換算で 3. 0モル%含む酸化亜鉛を主成分とする焼結体からなる基 板に直接形成した 1 0 0モル%A 1 N単結晶薄膜の場合で 1 1 2秒と本実施例において最も小 さくなり結晶性が最も優れていた。 その後アルミニゥム成分の含有量が増加するにしたがつて 酸化亜鉛を主成分とする焼結体からなる基板に直接形成される単結晶薄膜のミラ一指数 ( 0 0 2) の格子面の X線回折ロッキングカーブの半値幅が大きくなり、 アルミニウム成分を A 1 2〇 3換算で 4 0. 0モル%含む酸化亜鉛を主成分とする焼結体からなる基板に直接形成した 1 0 0 モル% A 1 N単結晶薄膜の場合は 1 3 6秒となった。 また、 アルミニウム成分を A 1 2〇 3換算 で 5 0. 0モル%含む酸化亜鉛を主成分とする焼結体からなる基板に直接形成した 1 0 0モ ル%八 1 N単結晶薄膜の場合は 2 2 9秒となり 2 0 0秒より大きくなつた。
一方本実施例において表 4 5及び表 4 6に示すようにアルミニウム成分含む酸化亜鉛を主成 分とする焼結体からなる基板は該焼結体中に例えば鉄、 クロム、 あるいは希土類 素などアル ミニゥム以外の成分が含まれていたとしても該基板に直接形成される窒化ガリウム、 窒化イン ジゥム、 窒化アルミニウムのうちから選ばれた少なくとも 1種以上を主成分とする単結晶薄膜 の結晶性が大きく低減化するなどの変化は少ないことが ϋ認された。 言い換えれば、 上記アル ミニゥム成分を含む酸化亜鉛を主成分とする焼結体からなる基板は、 該焼結体中に例えば鉄、 クロム、 あるいは希土^ ¾素などアルミニゥム以外の成分が含まれていたとしてもこれらの成 分によって該基板に直接形成される単結晶薄膜の結晶性に影響を受けにくいものであることが 確認された。
具体的には、 アルミニゥム成分を A 1 203換算で 0. 0 3モル%含み同時にィットリゥム成 分を Y203 で 0. 0 0 0 1モル%〜1 2. 0モル%の範囲で含む酸化亜鉛を主成分とする 焼結体からなる基板に直接形成された 1 0 0モル%Α 1 Ν単結晶薄膜のミラー指数 ( 0 0 2 )
の格子面の X線回折ロッキングカーブの半値幅は 1 3 4秒〜 1 4 5秒の範囲であり、 その結晶 性はアルミニウム成分だけを A 1 2O3^ 0. 0 3モル%含みイットリウム成分を含まない 酸化亜鉛を主成分とする焼結体からなる基板に直接形成された 1 0 0モル%Α 1 Ν単結晶薄膜 の 1 3 8秒から大きく変化する傾向を示さなかった。
さらに、 表 4 5及び表 4 6においてアルミニウム成分を A 1 2〇3換算で 3. 0モル%含み同 時に鉄成分を F e 2〇3^で 0. 2モレ%、 クロム成分を C r 2〇3霧で 0. 2モル%、 イツ トリウム成分を Y203禱で 0. 0 4モル%、ホルミゥム成分を1102〇3購で0 , 0 4モル%、 エルビウム成分を E r 2〇3騰で 0. 0 4モル%、 それぞれ含む酸化亜鉛を主成分とする焼結 体からなる基板に直接形成された 1 0 0モル%A 1 N単結晶薄膜のミラー指数 (0 0 2) の格 子面の X線回折ロッキングカーブの半値幅は 1 1 1秒〜 1 1 7秒の範囲であり、 その結晶性は アルミニウム成分だけを A 1 203換算で 3. 0モル%含む酸化亜鉛を主成分とする焼結体から なる基板に直接形成された 1 0 0モル%A 1 N単結晶薄膜の 1 1 2秒から大きく変化する傾向 を示さなかった。 また、 A 1 203 で 3. 0モル%含み同時にジスプロシウム成分を D y 2〇 3醇で 0. 0 4モル%、 イッテルビウム成分を Yb 2〇3藤で 0. 0 4モル%、 それぞれ含む 酸化亜鉛を主成分とする焼結体からなる基板に直接形成された 1 0 0モル%G aN単結晶薄膜 のミラ一指数 (0 0 2) の格子面の X線回折ロッキングカーブの半値幅は 1 1 6秒及び〜 1 1 3秒であり、 その結晶性はアルミニゥム成分だけを A 1 2〇 3換算で 3. 0モル%含む酸化亜鉛 を主成分とする焼結体からなる基板に直接形成された 1 0 0モル%G aN単結晶薄膜の 1 1 8 秒から大きく変化する傾向を示さなかった。
また、 表 4 5及び表 4 6においてイットリウム成分を Y203換算で 0. 0 4モル%含み同時 にアルミニウム成分を A 1 203換算で 0. 0 0 2モル%〜 5 0. 0モル%の範囲で含む酸化亜 鉛を主成分とする焼結体からなる基板に直接形成された 1 0 0モル%A 1 N単結晶薄膜の結晶 性と、 アルミニウム成分だけを含む酸化亜鉛を主成分とする焼結体からなる基板に直接形成さ れた 1 0 0モル%A 1 N単結晶薄膜の結晶性とを比較してみると、 それぞれ同じ量のアルミ二 ゥム成分を含む酸化 »を主成分とする焼結体からなる基板では 晶性に関してあまり変化 しておらずほとんど同じレベルであった。 例えば、 イットリウム成分を Y203謹で 0. 0 4 モル%含み同時にアルミニゥム成分を A 1 2 O 3換算で 0. 0 0 2モル%含む酸化亜鉛を主成分 とする焼結体からなる基板に直接形成された 1 0 0モル%A 1 N単結晶薄膜のミラ一指数 ( 0 0 2) の格子面の X線回折ロッキングカーブの半値幅は 1 7 5秒であり、 その結晶性はアルミ ニゥム成分だけを A 1 2〇3 で0. 0 0 2モル%含み実質的にイットリウム成分を含まない 酸化亜鉛を主成分とする焼結体からなる基板に直接形成された 1 0 0モル%A 1 N単結晶薄膜 の 1 8 7秒から大きく低減化するなどの変化傾向を示さなかった。.また、 イットリウム成分を Y 2 O 3購で 0. 0 4モル%含み同時にアルミニゥム成分を A 1 2 O 3換算で 0. 1 0モル%含 む酸化亜鉛を主成分とする焼結体からなる基板に直接形成された 1 0 0モル%A 1 N単結晶薄 膜のミラ一指数 (0 0 2) の格子面の X線回折ロッキングカーブの半値幅は 1 2 5秒であり、 その結晶性はアルミニゥム成分だけを A 1 2 O 3騰で 0. 1 0モル%含み実質的にィットリウ ム成分を含まない酸化亜鉛を主成分とする焼結体からなる基板に直接形成された 1 0 0モル% A 1 N単結晶薄膜の 1 2 6秒から大きく低減化するなどの変化傾向を示さなかった。 また、 ィ ットリウム成分を γ2〇 3換算で 0. 0 4モル%含み同時にアルミニウム成分を A 1 2o3
3 0. 0モル%含む酸化亜鉛を主成分とする焼結体からなる基板に直接形成された 1 0 0モ ル%八 1 N単結晶薄膜のミラ一指数 (0 0 2) の格子面の X線回折ロッキングカーブの半値幅 は 1 2 6秒であり、 その結晶性はアルミニゥム成分だけを A 1 2 O 3^ 3 0. 0モル%含み 実質的にィットリゥム成分を含まない酸化亜鉛を主成分とする焼結体からなる基板に直接形成 された 1 0 0モル%A 1 N単結晶薄膜の 1 2 7秒から大きく低減化するなどの変化傾向を示さ
なかった。 すなわち、 アルミニウム成分を A 1 203換算で 0. 0 0 2モル%〜5 0. 0モル% の範囲で含む酸化 を主成分とする焼結体に直接形成される 1 0 0モル%A 1 N単結晶薄膜 の結晶性は、 該酸化亜鉛を主成分とする焼結体にアルミニウム成分以外にィットリゥム成分が 同時に含まれていたとしても殆ど変化せずィットリゥム成分の有無による影響を受けにくい傾 向を有することが崔認された。
さらに、 イットリゥム成分を Y 2 O 3 で 0. 0 モル%含み同時にアルミニゥム成分を A 1 203 で 1. 0モル%含む酸化 を主成分とする焼結体からなる基板に直接形成された 1 0 0モル%G a N単結晶薄膜のミラ一指数 (0 0 2) の格子面の X線回折ロッキングカーブ の半値幅は 1 1 9秒であり、その結晶性はアルミニウム成分だけを A 1 203^ 1. 0モル% 含む酸化亜鉛を主成分とする焼結体からなる基板に直接形成された 1 0 0モル%Α 1 Ν単結晶 薄膜の 1 2 1秒から大きく低減化するなどの変化傾向を示さなかった。
また、 表 4 5及び表 4 6においてアルミニウム成分を Α 1 2〇 3換算で 1. 0モル%含みさら にィットリゥム成分を Y 2〇 3換算で 0. 0 4モル%及びエルビウム成分を E r 203換算で 0. 0 4モル%という 3成分を同時に含む酸化亜鉛を主成分とする焼結体からなる基板に直接形成 される 1 0 0モル%G a N単結晶薄膜のミラ一指数 ( 0 0 2) の格子面の X線回折ロッキング カーブの半値幅は;!;L 6秒であり、 その結晶性はアルミニウム成分だけを A 1 203 3. 0モル%含む酸化 ¾を主成分とする焼結体からなる基板に直接形成された 1 0 0モル%G a N単結晶薄膜の 1 1 8秒から大きく変化する傾向を示さなかった。
その他に、 表 4 5に示すようにアルミニウム成分を含まず F e 2〇3購で 1. 0モル%の鉄 成分を含む酸化亜鉛を主成分とする焼結体を基板に用いた場合は該基板に直接形成した単結晶 薄膜のミラー指数 (0 0 2) の格子面の X線回折ロッキングカーブの半値幅は 2 2 7秒であつ た。 アルミニウム成分を含まず C r 2〇3換算で 1 · 0モル%のクロム成分を含む酸化亜鉛を主 成分とする焼結体を基板に用いた場合は該基板に直接形成した単結晶薄膜のミラ—指数 (0 0 2) の格子面の X線回折ロッキングカーブの半値幅は 2 2 0秒であった。 アルミニウム成分を 含まず Y203換算で 0. 0 4モル%のイットリウム成分を含む酸化亜鉛を主成分とする焼結体 を基板に用いた場合は該基板に直接形成した単結晶薄膜のミラ—指数 (0 0 2) の格子面の X 線回折ロッキングカーブの半値幅は 1 9 2秒と 2 0 0秒以下であった。 アルミニウム成分を含 まず E r 2〇3換算で 0. 0 4モル%のエルビウム成分を含む酸化亜鉛を主成分とする焼結体を 基板に用いた場合は該基板に直接形成した単結晶薄膜のミラー指数 ( 0 0 2) の格子面の X線 回折ロッキングカーブの半値幅は 2 0 6秒であった。 アルミニウム成分を含まず Yb 203換算 で 0. 0 4モル%のイッテルビウム成分を含む酸化亜鉛を主成分とする焼結体を基板に用いた 場合は該基板に直接形成した単結晶薄膜のミラー指数 ( 0 0 2) の格子面の X線回折ロッキン グカーブの半値幅は 2 0 3秒であった。
このように本実施例において実質的にアルミニウム成分を含まず、 鉄、 クロム、 イットリウ ム、エルビウム、イッテルビウムなどの成分を含む酸化 ¾を主成分とする焼結体であっても、 該焼結体を基板として用いたとき該基板には比較的良好な結晶性の窒化ガリウム、 窒化ィンジ ゥム、 窒化アルミニウムのうちから選ばれた少なくとも 1種以上を主成分とする単結晶薄膜が 直接形成されることが ϋ雀認された。 その結晶性はアルミニゥム成分及びその他の成分を添加せ ずに舰され原料中の不純物以外は含まない実質的に酸化亜鉛だけからなる焼結体を基板とし て用い該基板に直接形成された 1 0 0モル%Α 1 Ν単結晶薄膜の 2 5 5秒と比較しても劣って いなかった。
上記のように各種組成の酸化亜鉛を主成分とする焼結体からなる基板に直接形成された 1 0 0モル% A 1 N単結晶薄膜、 1 0 0モル%G a N単結晶薄膜、 1 0 0モル% I n N単結晶薄膜 のミラ一指数 ( 0 0 2) の格子面の X線回折ロッキングカーブの半値幅はすべて 3 0 0秒以下
で結晶性に優れていた。
このような特性を有する上記各種組成の酸化亜鉛を主成分とする焼結体からなる基板を用い たとき、 該基板に直接形成される窒化ガリウム、 窒化インジウム、 窒化アルミニウムのうちか ら選ばれた少なくとも 1種以上を主成分とする単結晶薄膜の結晶性よりも、 該基板にあらかじ め蜜化ガリウム、 窒化インジウム、 窒化アルミニウムのうちから選ばれた少なくとも 1種以上 を主成分とする無定形、 多結晶、 配向性多結晶、 単結晶など各種結晶状態の薄膜を形成しさら にその上に窒化ガリウム、 窒化インジウム、 窒化アルミニウムのうちから選ばれた少なくとも
1種以上を主成分とする単結晶薄膜を形成すれば該単結晶薄膜の結晶性はより優れたものが得 られることカ權認された。 すなわち、 各種組成を有する酸化 «を主成分とする焼結体を基板 として用い、 該基板に直接形成される窒化ガリウム、 窒化インジウム、 窒化アルミニウムのう ちから選ばれた少なくとも 1種以上を主成分とする単結晶薄膜のミラー指数 ( 0 0 2) の格子 面の X線回折ロッキングカーブの半値幅は 2 0 0秒以下になるとは必ずしも限らない。 それに 対して、 このような各種組成を有する酸化亜鉛を主成分とする焼結体を基板として用いても、 該基板にあらかじめ窒化ガリウム、 窒化インジウム、 窒化アルミニウムのうちから選ばれた少 なくとも 1種以上を主成分とする無定形、 多結晶、 配向性多結晶、 単結晶など各種結晶状態の 薄膜を形成しさらにその上に窒化ガリウム、 窒化インジウム、 窒化アルミニウムのうちから選 ばれた少なくとも 1種以上を主成分とする単結晶薄膜を形成すれば該単結晶薄膜のミラー指数 ( 0 0 2 ) の格子面の X線回折ロッキングカーブの半値幅は 2 0 0秒以下のものが形成し得る ことが 認された。
また、 同じ組成の酸化亜鉛を主成分とする焼結体からなる基板を用いて窒化ガリウム、 窒化 ィンジゥム、 窒化アルミニウムのうちから選ばれた少なくとも 1種以上を主成分とする単結晶 薄膜を形成する場合、 該基板に直接形成される窒化ガリゥム、 窒化インジウム、 窒化アルミ二 ゥムのうちから選ばれた少なくとも 1種以上を主成分とする単結晶薄膜の結晶性よりも、 該基 板にあらかじめ窒化ガリウム、 窒化インジウム、 窒化アルミニウムのうちから選ばれた少なく とも 1種以上を主成分とする無定形、 多結晶、 配向性多結晶、 単結晶など各種結晶状態の薄膜 を形成しさらにその上に窒化ガリウム、 窒化インジウム、 窒化アルミニウムのうちから選ばれ た少なくとも 1種以上を主成分とする単結晶薄膜を形成すれば該単結晶薄膜の結晶性はより優 れたものが得られることが確認された。
すなわち、 アルミニウム成分を A 1 203換算で 0. 0 0 1モル%〜4 5. 0モル%の範囲で 含む酸化亜鉛を主成分とする焼結体を基板にあらかじめ窒化ガリウム、 窒化インジウム、 窒化 アルミニウムのうちから選ばれた少なくとも 1種以上を主成分とする無定形、 多結晶、 配向性 多結晶、 単結晶など各種結晶状態の薄膜を形成しその上にさらに窒化ガリウム、 窒化インジゥ ム、 窒化アルミニウムのうちから選ばれた少なくとも 1種以上を主成分とする単結晶薄膜を形 成すれば該単結晶薄膜のミラー指数 ( 0 0 2) の格子面の X線回折ロッキングカーブの半値幅 は 1 3 0秒以下となり易く、 アルミニウム成分を A l 2〇3換算で 0. 0 0 5モル%〜4 5. 0 モル%の範囲で含む酸化亜鉛を主成分とする焼結体を基板として用いたとき該単結晶薄膜のミ ラー指数 (0 0 2 ) の格子面の X線回折ロッキングカーブの半値幅は 1 0 0秒以下のものが形 成され得ることが確認、された。
また、上記量のアルミニゥム成分を含み、その他に 分、 クロム成分、イットリウム成分、 ジスプロシウム成分、 ホルミウム成分、 エルビウム成分、 ィッテルビウム成分などの成分を同 時に含む酸化亜鉛を主成分とする焼結体からなる基板であっても該基板に形成される単結晶薄 膜の結晶性は、前記アルミニウム成分を含みその働こ鉄成分、クロム成分、イットリウム成分、 ジスプロシウム成分、 ホルミウム成分、 エルビウム成分、 イッテルビウム成分などの成分を実 質的には含まなレゝ酸化亜鉛を主成分とする焼結体からなる基板に形成される単結晶薄膜の結晶
性と比較して大きく低減化するなどの変化を受けにくいこと力 萑認された。 すなわち、 上記量 のアルミニウム成分を含有する酸化亜鉛を主成分とする焼結体からなる基板であれば、 たとえ 鉄成分、 クロム成分、 イツ卜リゥム成分、 ジスプロシウム成分、 ホルミウム成分、 エルビウム 成分、 ィッテルビウム成分などアルミニウム成分以外の成分が含まれていたとしてもこれらの 成分によって形成される単結晶薄膜の結晶性は影響を受けにくいものであることが確認された。 より具体的には、 表 4 5に示すようにアルミニウム成分を添加せずに舰され実質的に原料 中あるいは焼結体 S¾i時に混入する不純物以外は含まなレ酸化亜鉛を主成分とする ^^体から なる基板に直接形成された 1 0 0モル%A 1 N単結晶薄膜のミラー指数 ( 0 0 2 ) の格子面の X線回折ロッキングカーブの半値幅は 2 5 5秒であるのに対して、 同じ酸化亜鉛を主成分とす る焼結体からなる基板にあらかじめ 1 0 0モル%A 1 Nの配向性多結晶を形成し、 さらにその 上に形成された 1 0 0モル%A 1 N単結晶薄膜のミラー指数 ( 0 0 2 ) の格子面の X線回折口 ッキングカーブの半値幅は 1 3 6秒と結晶性が向上した。
一方、 アルミニウム成分を A 1 203購で 0 . 0 0 2モル%含む酸化亜鉛を主成分とする焼 結体からなる基板を用いた場合、 該基板に直接形成された 1 0 0モレ%A 1 N単結晶薄膜のミ ラー指数 (0 0 2 ) の格子面の X線回折ロッキングカーブの半値幅は 1 8 7秒であるのに対し て、 同じアルミニウム成分を含む酸化 ¾を主成分とする焼結体からなる基板にあらかじめ 1 0 0モル%A 1 Nの配向性多結晶を形成し、 さらにその上に形成された 1 0 0モル%A 1 N単 結晶薄膜のミラー指数 ( 0 0 2 ) の格子面の X線回折ロッキングカーブの半値幅は 1 0 7秒と 結晶性が向上した。 また、 アルミニウム成分を A 1 2〇 3換算で 0 . 0 0 8モル%含む酸化亜鉛 を主成分とする焼結体からなる基板を用いた場合、 該基板に直接形成された 1 0 0モル%A 1 N単結晶薄膜のミラー指数 ( 0 0 2) の格子面の X線回折ロッキングカーブの半値幅は 1 5 9 秒であるのに対して、 同じアルミニウム成分を含む酸化亜鉛を主成分とする焼結体からなる基 板にあらかじめ 1 0 0モル%A 1 Nの配向性多結晶を形成し、 さらにその上に形成された 1 0 0モル% A 1 N単結晶薄膜のミラー指数 (0 0 2 ) の格子面の X線回折ロッキングカーブの半 値幅は 9 7秒と 1 0 0秒以下となった。 以下アルミニウム成分を A 1 203換算で 0 . 0 0 5モ ル%〜4 5 . 0モル%の範囲で む酸化 を主成分とする焼結体からなる基板を用いた:^、 該基板に直接形成された窒化ガリウム、 窒化インジウム、 窒化アルミニウムのうちから選ばれ だ少なくとも 1種以上を主成分とする単結晶薄膜の結晶性よりも、該基板にあらかじめ無定形、 多結晶、 配向性多結晶、 単結晶のうちから選ばれた少なくともいずれかの結晶状態を有する窒 化ガリウム、 窒化インジウム、 窒化アルミニウムのうちから選ばれた少なくとも 1種以上を主 成分とする薄膜を形成し、 さらにその上に形成された窒化ガリウム、 窒化インジウム、 窒化ァ ルミニゥムのうちから選ばれた少なくとも 1種以上を主成分とする単結晶薄膜のほうが結晶性 はより優れたものが得られ、 該単結晶薄膜の結晶性は該単結晶薄膜のミラー指数 ( 0 0 2 ) の 格子面の X線回折ロッキングカーブの半値幅が 8 6秒〜 9 7秒の範囲でありすべて 1 0 0秒以 下であることが ϋ認された。
また、 含有するアルミニウム成分が A 1 203換算で 5 0 . 0モル%含む酸化亜鉛を主成分と する焼結体からなる基板に直接形成した 1 0 0モル%A 1 N単結晶薄膜の場合は該単結晶薄膜 のミラ一指数 (0 0 2 ) の格子面の X線回折ロッキングカーブの半値幅が 2 2 9秒であるのに 対して、 同じ基板にあらかじめ 1 0 0モル%A 1 N配向性多結晶薄膜を形成しその上に形成し た 1 0 0モル%A 1 N単結晶薄膜では 1 3 4秒と結晶性が向上した。
また、 例えぱ表 4 6に示すようにアルミニウム成分を A 1 203購で 0 . 0 0 2モル%含み さらにその他にィットリゥム成分を Y 2 O 3騰で 0 . 0 4モル%含む組成の酸化亜鉛を主成分 とする焼結体からなる基板を用いた場合、 該基板に直接形成された 1 0 0モル%A 1 N単結晶 薄膜のミラ一指数 ( 0 0 2 ) の格子面の X線回折ロッキングカーブの半値幅は 1 Ί 5秒である
のに対して、 同じアルミニウム成分とィットリゥムを含む酸化亜鉛を主成分とする焼結体から なる基板にあらかじめ 1 0 0モル%A 1 Nの配向性多結晶を形成し、 さらにその上に形成され た 1 0 0モル% A 1 N単結晶薄膜のミラー指数 (0 0 2 ) の格子面の X線回折ロッキング力一 ブの半値幅は 1 0 7秒であり結晶性が向上した。また、アルミニウム成分を A 1 203換算で 0. 0 0 8モル%含みさらにその他にイットリウム成分を Y203換算で 0. 0 4モル%含む組成の 酸化亜鉛を主成分とする焼結体からなる基板を用いた場合、 該基板に直接形成された 1 0 0モ ル%A 1 N単結晶薄膜のミラ一指数 (0 0 2 ) の格子面の X線回折ロッキングカーブの半値幅 は 1 5 7秒であるのに対して、 同じアルミニウム成分とイットリウムを含む酸化亜鉛を主成分 とする焼結体からなる基板にあらかじめ 1 0 0モル%Α 1 Νの配向性多結晶を形成し、 さらに その上に形成された 1 0 0モル%Α 1 Ν単結晶薄膜のミラー指数 (0 0 2 ) の格子面の X線回 折ロッキングカーブの半値幅は 9 6秒と 1 0 0秒以下に結晶性が向上した。 以下表 4 6に示す ように、ァレミニゥム成分を A 1 203纏で 0. 0 3モレ%、 0. 1 0モリレ%、 0. 3 0モレ%、 1 . 0モル%、 3. 0モル%、 1 0. 0モル%、 3 0. 0モル%含みさらにその他に鉄成分、 クロム成分、 イツトリゥム成分、 ジスプロシウム成分、 ホルミウム成分、 エルビウム成分、 ィ ッテルビウム成分のうちのいずれかを含む各種組成の酸化亜铅を主成分とする焼結体からなる 基板を用いた場合、 これら各基板に直接形成された 1 0 0モル%A 1 N単結晶薄膜あるいは 1 0 0モル%G a N単結晶薄膜の結晶性に比べて、 同じアルミニウム成分とその他鉄成分、 クロ ム成分、 イットリウム成分、 ジスプロシウム成分、 ホルミウム成分、 エルビウム成分、 イツテ ルビゥム成分のうちのいずれかを含む酸化亜鉛を主成分とする焼結体からなる基板にあらかじ め 1 0 0モル%A 1 Nの配向性多結晶を形成し、 さらにその上に形成された 1 0 0モル%A 1 N単結晶薄膜あるいは 1 0 0モル%G a N単結晶薄膜の結晶性はより向上し該単結晶薄膜のミ ラ一指数 ( 0 0 2) の格子面の X線回折ロッキングカーブの半値幅はすべて 1 0 0秒以下であ ることが ϋ雀認された。 また、 アルミニウム成分を A 1 203換算で 3. 0モル%含みさらにその 他にイットリウム成分を Y2〇 3換算で 0. 0 4モル%及びエルビウム成分を E r 2〇3換算で 0. 0 4モル%含む組成の酸化亜鉛を主成分とする焼結体からなる基板を用いた場合、 該基板に直 接形成された 1 0 0モ ] /%A 1 N単結晶薄膜のミラ一指数 (0 0 2 ) の格子面の X線回折ロッ キングカーブの半値幅は 1 1 6秒であるのに対して、 同じアルミニウム成分とィットリゥム成 分及びエルビウム成分を含む酸化亜鉛を主成分とする焼結体からなる基板にあらかじめ 1 0 0 モリ 1/%A 1 N無定形薄膜、 1 0 0モル%A 1 N多結晶薄膜、 1 0 0モル%A 1 N配向性多結晶 薄膜を形成し、 さらにその上に形成された 1 0 0モル%A 1 N単結晶あるいは 1 0 0モル%G a N単結晶薄膜のミラー指数 ( 0 0 2 ) の格子面の X線回折ロッキングカーブの半値幅はそれ ぞれ 9 3秒、 9 6秒、 8 7秒とすべて 1 0 0秒以下に向上であった。
その他、 表 4 5及び表 4 6に示したすべての組成の酸化亜鉛を主成分とする焼結体からなる 基板を用いた場合でも、 該基板 直接形成した窒化ガリウム、 窒化インジウム、 窒化アルミ二 ゥムのうちから選ばれた少なくとも 1種以上を主成分とする単結晶薄膜の結晶性よりも、 該基 板にあらかじめ無定形、多結晶、配向性多結晶、単結晶の各種結晶状態からなる窒化ガリウム、 窒化インジウム、 窒化アルミニウムのうちから選ばれた少なくとも 1種以上を主成分とする薄 膜を形成し、 さらにその上に形成した窒化ガリウム、 窒化インジウム、 窒化アルミニウムのう ちから選ばれた少なくとも 1種以上を主成分とする単結晶薄膜のほうが結晶性はより優れたも のが得られる。
例えば、 表 4 5に示すようにアルミニウム成分を含まず F e 203»で1 . 0モル%の鉄成 分を含む酸化亜鉛を主成分とする焼結体からなる基板を用いた場合、 該基板に直接形成された 1 0 0モル%A 1 N単結晶薄膜のミラー指数 (0 0 2) の格子面の X線回折ロッキングカーブ の半値幅は 2 2 7秒であるのに対して、 同じ鉄成分を含む酸化亜鉛を主成分とする焼結体から
なる基板にあらかじめ 1 0 0モル%A 1 Nの配向性多結晶を形成し、 さらにその上に形成され た 1 0 0モル%A 1 N単結晶薄膜のミラー指数 (0 0 2 ) の格子面の X線回折ロッキング力一 ブの半値幅は 1 2 4秒であり結晶性が向上した。アルミニゥム成分を含まず C r 2〇3換算で 1. 0モル%のクロム成分を含む酸化 ¾を主成分とする焼結体からなる基板を用いた場合、 該基 板に直接形成された 1 0 0モル%G a N単結晶薄膜のミラ一指数 (0 0 2 ) の格子面の X線回 折ロッキングカーブの半値幅は 2 2 0秒であるのに対して、 同じクロム成分を含む酸化亜铅を 主成分とする焼結体からなる基板にあらかじめ 1 0 0モル%A 1 Nの配向性多結晶を形成し、 さらにその上に形成された 1 0 0モル%G a N単結晶薄膜のミラー指数 (0 0 2 ) の格子面の X線回折ロッキングカーブの半値幅は 1 1 9秒であり結晶性が向上した。 アルミニウム成分を 含まず Y203換算で 0 · 0 4モル%のイットリウム成分を含む酸化亜鉛を主成分とする焼結体 からなる基板を用いた場合、 該基板に直接形成された 1 0 0モル%Α 1 Ν単結晶薄膜のミラー 指数 ( 0 0 2) の格子面の X線回折ロッキングカーブの半値幅は 1 9 2秒であるのに対して、 同じイットリウム成分を含む酸化亜鉛を主成分とする焼結体からなる基板にあらかじめ 1 0 0 モル% A 1 Nの配向性多結晶を形成し、 さらにその上に形成された 1 0 0モル% A 1 N単結晶 薄膜のミラー指数 ( 0 0 2) の格子面の X線回折ロッキングカーブの半値幅は 1 0 4秒であり 結晶性が向上した。 アルミニウム成分を含まず E r 203換算で 0. 0 4モル%のエルビウム成 分を含む酸化亜鉛を主成分とする焼結体からなる基板を用いた場合、 該基板に直接形成された 1 0 0モル%G a N単結晶薄膜のミラー指数 (0 0 2 ) の格子面の X線回折ロッキングカーブ の半値幅は 2 0 6秒であるのに対して、 同じエルビウム成分を含む酸化亜鉛を主成分とする焼 結体からなる基板にあらかじめ 1 0 0モル%A 1 Nの配向性多結晶を形成し、 さらにその上に 形成された 1 0 0モル%G a N単結晶薄膜のミラ一指数 (0 0 2) のネ各子面の X線回折ロッキ ングカーブの半値幅は 1 0 7秒であり結晶性が向上した。 アルミニウム成分を含まず Y b 203 換算で 0. 0 4モル%のイッテルビウム成分を含む酸化亜鉛を主成分とする焼結体からなる基 板を用いた場合、 該基板に直接形成された 1 0 0モル%A 1 N単結晶薄膜のミラー指数 ( 0 0 2 ) の格子面の X線回折ロッキングカーブの半値幅は 2 0 3秒であるのに対して、 同じイツテ ルビゥム成分を含む酸化亜鉛を主成分とする焼結体からなる基板にあらかじめ 1 0 0モル%A 1 Nの配向性多結晶を形成し、 さらにその上に形成された 1 0 0モル%A 1 N単結晶薄膜のミ ラー指数 (0 0 2) の格子面の X線回折ロッキングカーブの半値幅は 1 0 9秒であり結晶性が 向上した。
なお別に、 本実施例で作製した表 4 5及び表 4 6に示す各種組成の酸化亜鉛を主成分とする 焼結体からなる基板に表 4 5及び表 4 6には記載されているものとは異なる構成の薄膜を形成 した。
すなわち、 表 4 5及び表 4 6に示す各種組成の酸化亜鉛を主成分とする焼結体からなる基板 に上記のように実施例 2 5の実験 N o . 7 0 6、 7 0 7及び 7 0 8で行つたスパッタリング法 及び実験 N o . 7 0 9で行った MO CVD法と同様の条件により 1 0 0モル%A 1 Nの薄膜を 厚み 3 mであらかじめ形成し、 それぞれ実施例 2 5と同様の無定形、 多結晶、 配向性多結晶 及び単結晶状態の窒化アルミニウムを主成分とする薄膜を形成した。また、実験 N o . 7 2 8、 7 3 0で行った MO CVD法と同様の条件により 1 0 0モル%G a Nの薄膜を厚み 3 mであ らかじめ形成し、 それぞれ実施例 2 5と同様の無定形、 及び ¾向性多結晶状態の窒化ガリウム を主成分とする薄膜を形成した。 また、 実験 N o . 7 3 1で行った MO CVD法と同様の条件 により 1 0 0モル% I n Nの薄膜を厚み 3 mであらかじめ形成し、 実施例 2 5と同様の配向 性多結晶状態の窒化インジウムを主成分とする薄膜を形成した。
また、 上記のようにあらかじめ窒化アルミニウムを主成分とする薄膜、 窒化ガリウムを主成 分とする薄膜、 窒化ィンジゥムを主成分とする薄膜を形成した酸化亜鉛を主成分とする焼結体
からなる基板と、 薄膜を形成せずに残しておいた酸化 «を主成分とする焼結体からなる基板 とを用い、 実施例 1 9に記載されたものと同様の MO CVD法によりその上にさらに 1 0 0モ JVX A 1 N、 1 0 0モル%G a N、 1 0 0モル% I n N、 5 0モル%A 1 N+ 5 0モル%G a N、 5 0モル% G a N+ 5 0モル% I n N各組成の単結晶薄膜を厚み 3 mで形成した。 上記の薄膜を表 4 5及び表 4 6に示したものと異なる構成で本実施例で作製した各種組成の 酸化亜鉛を主成分とする焼結体からなる基板に形成した場合も、 同じ酸化亜鉛を主成分とする 焼結体からなる基板に直接形成した窒化ガリウム、 窒化インジウム、 窒化アルミニウムのうち から選ばれた少なくとも 1種以上を主成分とする単結晶薄膜の結晶性より、 あらかじめ窒化ガ リウム、 窒化インジウム、 窒化アルミニウムのうちから選ばれた少なくとも 1種以上を主成分 とする無定形、 多結晶、 配向性多結晶、 単結晶など各種結晶状態の薄膜を形成しその上に形成 した単結晶薄膜のほうが結晶性に優れていることが確認された。
このように本実施例において酸化亜鉛を主成分とする焼結体からなる基板を用いた場合、 該 基板に直接形成した窒化ガリウム、 窒化インジウム、 窒化アルミニウムのうちから選ばれた少 なくとも 1種以上を主成分とする単結晶薄膜の結晶性よりも、 該基板にあらかじめ窒化ガリゥ ム、 窒化インジウム、 窒化アルミニウムのうちから選ばれた少なくとも 1種以上を主成分とす る無定形、 多結晶、 配向性多結晶、 単結晶など各種結晶状態の薄膜を形成しさらにその上に形 成した窒化ガリウム、 窒化インジウム、 窒化アルミニウムのうちから選ばれた少なくとも 1種 以上を主成分とする単結晶薄膜のほうが結晶性はより優れたものが得られることがすべての実 験で確認された。
本実施例において表 4 5及び表 4 6に記載した構成の薄膜及びその他作製したすべての薄膜 の外観を調べたがあらかじめ基板に形成した薄膜及びその上にさらに形成した薄膜いずれもク ラックやひび割れなどの欠陥は見られない。 また、 粘着テープによる剥離テストを行ったがい ずれの薄膜も酸化亜錯を主成分とする焼結体からなる基板との間及び薄膜同志の間で剥離は見 られなかった。 また、 基板表面の薄膜に T i /P t ZAuの薄 ^電性材料を形成して金属リ ―ドをはんだ付けし垂直引張り強度を調べたがすべて 2 K gZmm2以上であり酸化亜鉛を主 成分とする焼結体からなる基板と該基板にあらかじめ形成した薄膜、 及び該薄膜とさらにその 上に形成した単結晶薄膜とは強固に接合している。
実施例 3 1
本実施例は酸化ベリリゥムを主成分とする焼結体を基板として用いたとき該基板の組成と該 基板に形成される窒化ガリゥム、 窒化インジウム、 窒化アルミニウムを主成分とする薄膜の結 晶性に及ぼす影響を調べた例を示す。
まず、 酸化ベリリウム (B e〇) 粉末として実施例 1で用いた株式会社高脑匕 所製 の純度 9 9 %のものを用意し、 マグネシア (M g O) 粉末として株式会社高純度ィ匕学 ¾J ¾所製 の純度 9 9 . 9 9 %のものを用意し、 炭酸カレシゥム (C a C〇3)粉末として株式会社高¾JS 化学石 if^f製の純度 9 9 . 9 9 %のものを用意し、 シリカ (S i〇2)粉末として株式会社アド マテック製の 9 . 9 %の 「S O— E 2」 グレードを用意した。 これらの粉末を所定の組 成になるよう実施例 1と同様の方法によりポールミルで粉碎混合後パラフィンワックスを加え て成形用粉末を作製し、 実施例 1と同様の大きさの成形体に一軸プレス成形籠脂し、 その後 1 5 0 0 で 3時間大気中で常圧焼成してマグネシウム成分、 カルシウム成分、 珪素成分を各 種割合で含有する酸化ベリリウムを主成分とする焼結体を作製した。 これらの焼結体はいずれ も相対密度 9 8 %以上に緻密化していた。 得られた焼結体を実施例 8と同様粒径 0 . 0 5 m のコロイド状のアルミナを主成分とする研磨剤を用いて鏡面研磨し塩化メチレン及び I P Aで 超音波洗浄し基板を作製した。 鏡面研磨した基板の平均表面粗さ R aは 8 . 6 nm〜9 . 5 n mの範囲にあった。 研磨後の基板を用いて波長 6 0 5 nmの光に対する光透過率を実施例 2と
同様の方法により測定した。
このようにして得られた酸化ベリリウムを主成分とする焼結体からなる基板の特性を表 4 7 に示す。
表 4 7に示すようにマグネシウム成分、 カルシウム成分、 珪素成分及びその他の成分を添加 せずに焼成され原料中の不純物以外は含まない実質的に酸化ベリリゥムだけからなる焼結体の 波長 6 0 5 nmの光に対する光透過率は 1 4 %であったがマグネシウム成分、カリレシゥム成分、 珪素成分の含有量が増加するにつれ光透過率も上昇する傾向を示しカルシウム成分を C a〇換 算で 0. 4 5モル%含むものは 5 7 %に達した。 その後マグネシウム成分、 カルシウム成分、 珪素成分の含有量が増加するにつれ光透過率は次第に低下しマグネシウム成分を M g。換算で 3 0. 0モル%含む酸化べリリゥムを主成分とする焼結体では波長 6 0 5 n mの光に対する光 ¾1率は2 4 %となり、 マグネシウム成分を Mg〇換算で 4 0. 0モル%含む酸化ベリリウム を主成分とする焼結体では光 ¾i率が 7. 6 %となった。
また、 本実施例においてマグネシウム成分、 カルシウム成分、 珪素成分のうち少なくとも 1 種以上を酸化物 で合計 3 5. 0モル%以下の範囲で含み、 さらに希土^ ¾素成分のうちか ら選ばれた少なくとも 1種以上の成分を酸化物■で合計 0. 0 0 0 0 5モル%〜5. 0モル% の範囲で含む酸化ベリリウムを主成分とする焼結体は波長 6 0 5 nmの光に対する^ 率 3 0 %以上のものが得られ易いこと力 ¾|認された。 さらに、 8 0 %以上の 過率を有する酸化 ベリリゥムを主成分とする焼結体が製造し得ることも確認された。
すなわち表 4 7に示されるように、 カルシウム成分を C a〇換算で 0. 0 0 0 4モル%含み さらにイットリウム成分を Y203騰で 0. 0 0 0 2モル%同時に含む酸化ベリリウムを主成 分とする焼結体は波長 6 0 5 nmの光に対する光 ¾i 率が 3 5 %であった。 その後ィットリウ ム成分が増加するにつれ ¾¾ 率は増大する傾向を示し、 カルシウム成分を C a〇»で 0. 4 5モル%含みさらにィットリゥム成分を Y 2〇 3 で 0. 0 4 0モル%同時に含む酸化べリ リゥムを主成分とする焼結体は波長 6 0 5 n mの光に対する光透過率が 8 1 %であった。 さら にその後はィットリゥム成分が増加するにつれ光 ¾ϋ率は低下するする傾向を示し、 カルシゥ ム成分を C a O換算で 0. 0 0 0 4モル%含みさらにイットリウム成分を Y203換算で 4. 0 モル%同時に含む酸化ベリリウムを主成分とする焼結体は波長 6 0 5 nmの光に対する 率は 3 7 %であり、 カルシウム成分を C a〇換算で 0. 0 0 0 4モル%含みさらにイットリウ ム成分を Y203購で 6. 0モル%同時に含む酸化ベリリウムを主成分とする焼結体は波長 6 0 5 nmの光に対する光透過率は 2 8 %であった。
また、 上記のようにカルシウム成分を C a O換算で 0. 4 5モル%含みさらにイットリウム 成分を Y203換算で 0. 0 4 0モル%含む酸化ベリリウムを主成分とする焼結体の波長 6 0 5 nmの光に対する光 ¾ 率は 8 1 %であったが、カルシウム成分を C a Ο換算で 0. 4 5モル% 含みさらにィットリゥム以外の希土^素成分を酸化物換算で 0. 0 4 0モル%含む酸化べリ リゥムを主成分とする焼結体の波長 6 0 5 nmの光に対する光透過率も 7 5 %〜 8 0 %と高い ものであった。 すなわち、 カルシウム成分を C a O換算で 0. 4 5モル%含みさらに希土類 素成分としてジスプロシウム成分を D y 203購で 0. 0 4 0モル%同時に含む酸化ベリリウ ムを主成分とする焼結体の波長 6 0 5 nmの光に対する光 ¾i 率は 7 6 %であり、 ホルミウム 成分を H o 203鍵で 0. 0 4 0モル%同時に含む酸化ベリリウムを主成分とする焼結体の光 扁率は 7 5 %であり、 エルビウム成分を E r 203騰で 0. 0 4 0モル%同時に含む酸化べ リリウムを主成分とする焼結体の 率は 8 0 %であり、 イッテルビウム成分を Y b 203換 算で 0. 0 4 0モル%同時に含む酸化ベリリゥムを主成分とする焼結体の光 ¾i率は 7 8 %で あった。 さらに、 カルシウム成分を C a O^ で 0. 4 5モル%含みかっ珪素成分を3 1 02換 算で 0. 2 0モル%含みさらにイットリウム成分を Y2〇3換算で 0. 0 4 0モル%の 3成分を
同時に含む酸化ベリリウムを主成分とする焼結体は波長 6 0 5 nmの光に対する光 率は 8 0 %であった。
次に用意した上記の基板に対して実施例 2 7に示したものと同様の方法で薄膜を形成した。 すなわち、 用意した基板の一部を選びその上に実施例 2 5の実験 N o . 7 0 8で行つたスパッ タリング法と同様の条件により 1 0 0モル%A 1 Nの薄膜を厚み 3 mであらかじめ形成した。 次に上記のようにしてあらかじめ A 1 N薄膜を形成した酸化ベリリウムを主成分とする焼結 体からなる基板と、 A 1 N薄膜を形成せずに残しておいた酸化ベリリゥムを主成分とする焼結 体からなる基板とを用いその上にさらに実施例 1 9に記載されたものと同じ 1 0 0モル%A 1 N、 1 0 0モル%0 & 1^各組成の薄膜を1^0 (3¥0法にょり厚み3 111で形成した。 MO CV Dの条件としては実施例 1 9に記載のように実施例 1及び実施例 2と同様の条件であった。 こ のようにして作製した薄膜の特 f生を表 4 7に示した。
本実施例において、 上記各基板にあらかじめ形成した 1 0 0モル%A 1 N薄膜はミラ一指数
( 0 0 2) の格子面からの回折線だけが出現しており、 明らかに基板面に対して C軸が垂直な 方向に形成された配向性多結晶であった。
上記各基板にあらかじめ形成した A 1 N配向性多結晶薄膜の結晶性を見ると、 表 4 7に示す ように実質的にマグネシウム成分、 カルシウム成分、 珪素成分を含まない酸化ベリリウムを主 成分とする焼結体からなる基板を用いた場合、 該配向性多結晶薄膜のミラ一指数 ( 0 0 2) の 格子面の X線回折ロッキングカーブの半値幅は 9 6 7 0秒であった。 マグネシウム成分、 カル シゥム成分、 珪素成分が増加するにつれて該配向性多結晶薄膜の結晶性は向上する傾向を示し た。 すなわち、 マグネシウム成分を Mg O騰で 0. 0 0 0 1モル%含む酸化ベリリウムを主 成分とする焼結体からなる基板を用いた場合 9 1 2 0秒であつたが、 カルシウム成分を C a〇 換算で 0. 0 0 0 4モル%含む酸化ベリリウムを主成分とする焼結体からなる基板を用いた場 合は 8 5 4 0秒であり、珪素成分を S i 02換算で 0. 0 0 2モル%含む酸化べリリゥムを主成 分とする焼結体からなる基板を用いた場合は 7 7 1 0秒と 8 0 0 0秒以下に低下した。 その後 マグネシウム成分、 カルシウム成分、 珪素成分の含有量が増加するにつれて該 A 1 N配向性多 結晶薄膜の結晶性は少し向上する傾向を示した。カルシウム成分を C a O換算で 0. 4 5モル% かつ珪素成分を S i。2換算で 0. 2モル%含む酸化ベリリウムを主成分とする焼結体からなる 基板を用いた場合は 7 1 9 0秒、と最も向上した。 その後マグネシウム成分、 カルシウム成分、 珪素成分の含有量が増加するにつれて該 A 1 N配向性多結晶薄膜の結晶性はやや低下する傾向 を示した。 マグネシウム成分を M g O算で 3 0. 0モル%含む酸化べリリゥムを主成分とする 焼結体からなる基板に形成した A 1 N配向性多結晶薄膜の場合は 7 6 5 0秒であった。 しかし ながら、 マグネシウム成分を M g O算で 4 0. 0モル%含む酸化ベリリゥムを主成分とする焼 結体からなる基板に形成した A 1 N配向性多結晶薄膜の場合は 9 4 8 0秒と結晶性は低下した。 また、 マグネシウム成分、 カルシウム成分、 珪素成分のうち少なくとも 1種以上の成分を酸 化物換算で合計 3 5. 0モル%以下含み、 さらに希土 素成分のうちから選ばれた少なくと も 1種以上の成分を含む酸化ベリリウムを主成分とする焼結体からなる基板に形成した Λ 1 N 配向性多結晶薄膜の場合、 該配向性多結晶薄膜のミラー指数 ( 0 0 2) の格子面の X線回折口 ッキングカーブの半値幅は 7 2 2 0秒〜 7 9 6 0秒の範囲でありすべて 8 0 0 0秒以下であつ た。
次に、 上記の薄膜をあらかじめ形成せずに残しておいた酸化ベリリウムを主成分とする雄 体からなる基板を用いて前記 MO CVD法により形成した 1 0 0モル%A 1 N、 1 0 0モル% G a N各組成からなる薄膜の結晶性を X線回折により調べた。 その結果、 作製したすべての薄 膜が基板面に対して C軸が垂直な方向に形成された単結晶であることが歸忍された。 その結晶 性を見ると、 表 4 7に示すようにマグネシウム成分、 カルシウム成分、 珪素成分及びその他の
成分を添加せずに焼成され実質的に原料中あるいは焼結体製造時に混入する不純物以外は含ま ない酸化ベリリウムを主成分とする焼結体からなる基板に直接形成され 1 0 0モル%A 1 N単 結晶薄膜のミラ一指数 (0 0 2 ) の格子面の X線回折ロッキングカーブの半値幅は 2 7 0秒で あった。 一方、 マグネシウム成分を M g O換算で 0. 0 0 0 1モル%含む酸化ベリリウムを主 成分とする焼結体からなる基板に直接形成した 1 0 0モル%A 1 N単結晶薄膜の場合は 2 2 1 秒と小さくなり結晶性が向上した。さらに、カルシウム成分を C a O で 0. 0 0 0 4モル% 含む酸化ベリリウムを主成分とする焼結体からなる基板に直接形成した 1 0 0モル%A 1 N単 結晶薄膜の ί胎は 1 9 1秒であり、珪素成分を S i 02換算で0. 0 0 2 0モル%含む酸化ベリ リウムを主成分とする焼結体からなる基板に直接形成した 1 0 0モル%A 1 N単結晶薄膜の場 合は 1 6 8秒とそれぞれ 2 0 0秒以下になり結晶性が向上した。 マグネシウム成分を Mg〇換 算で 0. 0 0 8 0モル%含む酸化ベリリウムを主成分とする焼結体からなる基板に直接形成し た 1 0 0モル%A 1 N単結晶薄膜の場合は 1 4 2秒と 1 5 0秒以下となり結晶性がより向上し た。 カルシウム成分を C a〇換算で 0. 0 2 0モル%含む酸化ベリリウムを主成分とする焼結 体からなる基板に直接形成した 1 0 0モル%A 1 N単結晶薄膜の場合は 1 2 2秒であり、 珪素 成分を S i 02騰で 0. 4 0モル%含む酸化ベリリウムを主成分とする焼結体からなる基板に 直接形成した 1 0 0モル%A 1 N単結晶薄膜の場合は 1 2 7秒と、 それぞれ 1 3 0秒以下にな り結晶性がさらに向上した。 その後マグネシウム成分、 カルシウム成分、 珪素成分の含有量が 増加するにしたがって酸化ベリリゥムを主成分とする焼結体からなる基板に直接形成される単 結晶薄膜のミラ一指数 ( 0 0 2) の格子面の X線回折ロッキングカーブの半値幅が小さくなつ た。 すなわち、 カルシウム成分を C a O換算で 0. 4 5モル%含む酸化ベリリウムを主成分と する焼結体からなる基板に直接形成した 1 0 0モル%A 1 N単結晶薄膜の場合で 1 0 9秒、 力 ルシゥム成分を C a〇麟で 0. 4 5モル%及ぴ 素成分を S i〇 2換算で 0. 2 0モル%同時 に含む酸化ベリリゥムを主成分とする焼結体からなる基板に直接形成した 1 0 0モル%A 1 N 単結晶薄膜の場合で 1 0 8秒と本実施例において直接基板に形成した単結晶薄膜のな力では最 も小さくなり結晶性が最も優れていた。 その後マグネシウム成分、 カルシウム成分、 珪素成分 の含有量が増加するにしたがって酸化ベリリゥムを主成分とする焼結体からなる基板に直接形 成される単結晶薄膜のミラー指数 (0 0 2 ) の格子面の X線回折ロッキングカーブの半値幅が 大きくなり、 マグネシウム成分を M で 3 0. 0モル%含む酸化べリリゥムを主成分と する焼結体からなる基板に直接形成した 1 0 0モル%A 1 N単結晶薄膜の場合は 1 3 2秒とな つた。 また、 マグネシウム成分を Mg O換算で 4 0. 0モル%含む酸化ベリリウムを主成分と する焼結体からなる基板に直接形成した 1 0 0モル%A 1 N単結晶薄膜の場合は 2 1 7秒とな り 2 0 0秒より大きくなつた。
一方本実施例において表 4 7に示すように、 マグネシウム、 カルシウム、 珪素成分のうち少 なくとも 1種以上を含む酸化ベリリウムを主成分とする焼結体からなる基板は該焼結体中に例 えば希土類 素などマグネシウム、 カルシウム、 珪素成分以外の成分が含まれていたとしても 該基板に直接形成される窒化ガリウム、 窒化インジウム、 窒化アルミニウムのうちから選ばれ た少なくとも 1種以上を主成分とする単結晶薄膜の結晶性が大きく低減化するなどの変化は少 ないこと力鳩認された。 言い換えれば、 上記マグネシウム、 カルシウム、 珪素成分のうち少な くとも 1種以上を含む酸化ベリリウムを主成分とする焼結体からなる基板は、 該焼結体中に希 土類元素などマグネシウム、 カルシウム、 珪素成分以外の成分が含まれていたとしてもこれら の成分によって該基板に直接形成される単結晶薄膜の結晶性に影響を受けにくいものであるこ とが確認された。
具体的には、 カルシウム成分を C a で 0. 0 0 0 4モル%含み同時にィットリゥム成 分を Υ203換算で 0. 0 0 0 2モル%、及びカルシウム成分を C a Ο騰で 0. 0 0 0 4モル%
含み同時にイツトリウム成分を Y2〇3換算で 6. 0モル%含む酸化ベリリウムを主成分とする 焼結体からなる基板に直接形成された 100モ Ι/%Α 1 Ν単結晶薄膜のミラー指数 (002) の格子面の X線回折ロッキングカーブの半値幅はそれぞれ 182秒、 189秒であり、 その結 晶' I生はカルシウム成分だけを C a 0換算で 0. 0004モル%含み実質的にィットリゥム成分 を含まない酸化ベリリウムを主成分とする焼結体からなる基板に直接形成された 100モル% A 1 N単結晶薄膜の 191秒から大きく低減化するなどの変化傾向を示さなかった。 また、 力 ルシゥム成分を C a O換算で 0. 0004モル%含み同時にィットリゥム成分を Y 2 O 3換算で 4. 0モル%含む酸化ベリリウムを主成分とする焼結体からなる基板に直接形成された 100 モル%G a N単結晶薄膜のミラー指数 (002) の格子面の X線回折ロッキングカーブの半値 幅は 176秒であり、 その結晶性は上記のカルシウム成分だけを C a O で 0. 0004モ ル%含み実質的にイットリウム成分を含まない酸化ベリリウムを主成分とする焼結体からなる 基板に直接形成された 100モル%A 1 N単結晶薄膜の 191秒と比べて大きく低減化するな どの変化傾向を示さなかった。 また、 カルシウム成分を C a〇換算で 0. 020モル%含み同 時にィットリゥム成分を Y 2〇 3換算でそれぞれ 0. 0010モル%、 0. 0040モル%含む 酸化ベリリウムを主成分とする焼結体からなる基板に直接形成された 100モ 1/%A 1 N単結 晶薄膜のミラ一指数 (002) の格子面の X線回折ロッキングカーブの半値幅はそれぞれ 12 1秒、 120秒であり、 その結晶性はカルシウム成分だけを C a O換算で 0. 020モル%含 み実質的にィットリゥム成分を含まなレゝ酸化ベリリゥムを主成分とする焼結体からなる基板に 直接形成された 100モル%A 1 N単結晶薄膜の 122秒から大きく低減化するなどの変化傾 向を示さなかった。 また、 カルシウム成分を C a〇換算で 0. 020モル%含み同時にイット リウム成分を Y203換算で 0. 010モル%含む酸化ベリリウムを主成分とする焼結体からな る基板に直接形成された 100モル%G a Ν単結晶薄膜のミラ一指数 (002) の格子面の X 線回折ロッキングカーブの半値幅は 118秒であり、 その結晶性はカルシウム成分だけを C a O換算で 0. 020モル%含み実質的にイットリウム成分を含まない酸化ベリリウムを主成分 とする焼結体からなる基板に直接形成された 100モル%A 1 N単結晶薄膜の 122秒から大 きく低減化するなどの変化傾向を示さなかった。 また、 カルシウム成分を C a O換算で 0. 4 5モル%含み同時にイットリウム成分を Y203騰で 0. 040モル%、 ホルミウム成分を Η 0203換算で0. 040モル%、 エルビウム成分を Er203禱で 0. 040モレ%、 それぞ れ含む酸化ベリリウムを主成分とする焼結体からなる基板に直接形成された 100モル%A 1 N単結晶薄膜のミラー指数 (002) の格子面の X線回折ロッキングカーブの半値幅はそれぞ れ 104秒、 107秒、 108秒であり、その結晶性はカルシウム成分だけを C aO で 0. 45モル%含み実質的に上記各種希土類 素成分を含まなレ 化ベリリウムを主成分とする焼 結体からなる基板に直接形成された 100モル%A 1 N単結晶薄膜の 109秒から大きく低減 化するなどの変化傾向を示さなかった。 また、 カルシウム成分を C a O換算で 0. 45モル% 含み同時にジスプロシウム成分を Dy203換算で 0. 040モル%、 イッテルビウム成分を Y b2〇3換算で 0. 040モル%、 それぞれ含む酸化ベリリウムを主成分とする焼結体からなる 基板に直接形成された 100モル%GaN単結晶薄膜のミラ一指数 (002) の格子面の X線 回折ロッキングカーブの半値幅はそれぞれ 110秒、 106秒であり、 その結晶性はカルシゥ ム成分だけを C a〇換算で 0. 45モル%含み実質的に上記各種希土観素成分を含まなレ 化ベリリウムを主成分とする焼結体からなる基板に直接形成された 100モル%A 1 N単結晶 薄膜の 109秒から大きく低減化するなどの変化傾向を示さなかった。 また、 カルシウム成分 を C a 0換算で 0. 45モル%及ぴ 素成分を S i O 2購で 0. 20モル%含みさらに同時に イットリウム成分を Y203換算で 0. 040モル%含む酸化ベリリウムを主成分とする焼結体 からなる基板に直接形成された 100モル%GaN単結晶薄膜のミラ一指数 (002) の格子
面の X線回折口ッキングカーブの半値幅は 1 0 9秒であり、 その結晶性はカルシウム成分を C a O騰で 0. 4 5モル%及び 素成分を S i 02換算で 0. 2 0モル%だけ含み実質的にィッ トリゥム成分を含まない酸化ベリリゥムを主成分とする焼結体からなる基板に直接形成された 1 0 0モル%A 1 N単結晶薄膜の 1 0 8秒から大きく低減化するなどの変化傾向を示さなかつ た。
このようにマグネシウム成分、 カルシウム成分、 珪素成分のうちから選ばれた少なくとも 1 種以上を含む酸化ベリリウムを主成分とする焼結体からなる基板は、 該基板がたとえマグネシ ゥム成分、 カルシウム成分、 珪素成分以外にイットリウムなどの希土觀素成分が同時に含ま れている酸化ベリリウムを主成分とする焼結体からなるものであったとしても、 該基板に直接 形成される窒化ガリゥム、 及び窒化アルミニウムを主成分とする単結晶薄膜の結晶性はあまり 変化せず、 イツトリゥムなどの希土類元素成分含有の有無による影響を受けにくい傾向を有す ることが確認された。
上記のように各種組成の酸化ベリリウムを主成分とする焼結体からなる基板に直接形成され た 1 0 0モル% A 1 N単結晶薄膜、 1 0 0モル% G a N単結晶薄膜のミラー指数 (0 0 2 ) の 格子面の X線回折ロッキングカーブの半値幅はすべて 3 0 0秒以下で結晶性に優れていた。 本実施例において、 このような特性を有する上記各種組成の酸化べリリゥムを主成分とする 焼結体からなる基板を用いたとき、 該基板に直接形成される窒化ガリウム、 窒化アルミニウム のうちから選ばれた少なくとも 1種以上を主成分とする単結晶薄膜の結晶性よりも、 該基板に あらかじめ窒化アルミニウムを主成分とする配向性多結晶薄膜を形成しさらにその上に窒化ガ リウム、 窒化アルミニウムのうちから選ばれた少なくとも 1種以上を主成分とする単結晶薄膜 を形成すれば該単結晶薄膜の結晶性はより優れたものが得られることが 11認された。すなわち、 各種組成を有する酸化ベリリウムを主成分とする焼結体を基板として用い、 該基板に直接形成 される窒化ガリゥム、 窒化アルミニウムのうちから選ばれた少なくとも 1種以上を主成分とす る単結晶薄膜のミラ一指数 ( 0 0 2) の格子面の X線回折ロッキングカーブの半値幅は 2 0 0 秒以下になるとは必ずしも限らない。 それに対して、 このような各種組成を有する酸化べリリ ゥムを主成分とする焼結体を基板として用いても、 該基板にあらかじめ窒化アルミニウムを主 成分とする配向性多結晶薄膜を形成しさらにその上に窒化ガリウム、 窒化アルミニウムのうち から選ばれた少なくとも 1種以上を主成分とする単結晶薄膜を形成すれば該単結晶薄膜のミラ —指数 (0 0 2 ) の格子面の X線回折ロッキングカーブの半値幅は 2 0 0秒以下のものが形成 し得ることが確認された。
また、 同じ誠の酸化ベリリウムを主成分とする焼結体からなる基板を用いて窒化ガリウム、 窒化アルミニウムのうちから選ばれた少なくとも 1種以上を主成分とする単結晶薄膜を形成す る場合、 該基板に直接形成される窒化ガリウム、 窒化アルミニウムのうちから選ばれた少なく とも 1種以上を主成分とする単結晶薄膜の結晶性よりも、 該基板にあらかじめ窒化アルミニゥ ムを主成分とする配向性多結晶薄膜を形成しさらにその上に窒化ガリゥム、 窒化アルミニウム のうちから選ばれた少なくとも 1種以上を主成分とする単結晶薄膜を形成すれば該単結晶薄膜 の結晶性はより優れたものが得られることが確認された。
すなわち、 マグネシウム成分、 カルシウム成分、 珪素成分のうち少なくとも 1種以上を酸化 物 で合計 0. 0 0 0 2モル%〜 3 5. 0モル%の範囲で含む酸化ベリリゥムを主成分とす る焼結体を基板として用い、 その上にあらかじめ窒化アルミニウムを主成分とする配向性多結 晶薄膜を形成し、 さらにその上に窒化ガリウム、 窒化アルミニウムのうちから選ばれた少なく とも 1種以上を主成分とする単結晶薄膜を形成すれば該単結晶薄膜のミラー指数 ( 0 0 2) の 格子面の X線回折ロッキングカーブの半値幅は 1 3 0秒以下の結晶性に優れたものとなり易ぐ マグネシウム成分、 カルシウム成分、 珪素成分のうち少なくとも 1種以上を酸化物換算で合計
0. 0 0 1モル%〜 3 5. 0モル%の範囲で含む酸化べリリゥムを主成分とする焼結体を基板 として用い、 その上にあらかじめ窒化アルミニウムを主成分とする配向性多結晶薄膜を形成し さらにその上に窒化ガリウム、 窒化アルミニウムのうちから選ばれた少なくとも 1種以上を主 成分とする単結晶薄膜を形成すれば該単結晶薄膜のミラ一指数 (0 0 2) の格子面の X線回折 ロッキングカーブの半値幅は 1 0 0秒以下の結晶性に優れたものが比較的容易に形成し得るこ とが 認された。
また、 上記量のマグネシウム成分、 カルシウム成分、 珪素成分を含みその他にイットリウム 成分、 ジスプロシウム成分、 ホルミウム成分、 エルビウム成分、 ィッテルビウム成分などの成 分を同時に含む酸化ベリリゥムを主成分とする焼結体からなる基板であっても該基板に形成さ れる単結晶薄膜の結晶性は、 前記マグネシウム成分、 カルシウム成分、 珪素成分を含みその他 にイットリウム成分、 ジスプロシウム成分、 ホルミウム成分、 エルビウム成分、 イツテルビゥ ム成分などの成分は実質的に含まない酸化ベリリゥムを主成分とする焼結体からなる基板に形 成される単結晶薄膜の結晶性と比較して大きく低減化するなどの変化を受けにくいことが ϋ認 された。 すなわち、 上記量のマグネシウム成分、 カルシウム成分、 珪素成分のうちから選ばれ る少なくとも 1種以上の成分を有する酸化ベリリウムを主成分とする焼結体からなる基板であ れば、 たとえイットリウム成分、 ジスプロシウム成分、 ホルミウム成分、 エルビウム成分、 ィ ッテルビウム成分などマグネシウム成分、 カルシウム成分、 珪素成分以外の成分が含まれてい たとしてもこれらの成分によって形成される窒化ガリウム、 窒化アルミニウムのうちから選ば れた少なくとも 1種以上を主成分とする単結晶薄膜の結晶性は影響を受けにくいものであるこ とが確認された。 ,
より具体的には、 表 4 7に示すようにマグネシウム成分、 カルシウム成分、 珪素成分及びそ の他の成分を添加せずに焼成され実質的に原料中あるいは焼結体製造時に混入する不純物以外 は含まない酸化ベリリウムを主成分とする焼結体からなる基板に直接形成された 1 0 0モル% A 1 N単結晶薄膜のミラ一指数 ( 0 0 2) の格子面の X線回折ロッキングカーブの半値幅は 2 7 0秒であるのに対して、 同じ酸化ベリリウムを主成分とする焼結体からなる基板にあらかじ め 1 0 0モル%A 1 Nの配向性多結晶を形成し、 その上にさらに形成された 1 0 0モル%A 1 N単結晶薄膜のミラー指数 (0 0 2 ) の格子面の X線回折ロッキングカーブの半値幅は 1 3 9 秒と結晶性が向上した。 また、 マグネシウム成分を Mg O換算で 0. 0 0 0 1モル%含む酸化 ベリリウムを主成分とする焼結体からなる基板を用いた場合、 該基板に直接形成された 1 0 0 モル%A 1 N単結晶薄膜のミラ一指数 (0 0 2 ) の格子面の X線回折ロッキングカーブの半値 幅は 2 2 1秒であるのに対して、 同じマグネシウム成分を含む酸化ベリリウムを主成分とする 焼結体からなる基板にあらかじめ 1 0 0モル%A 1 Nの配向性多結晶を形成し、 さらにその上 に形成された 1 0 0モル%A 1 N単結晶薄膜のミラー指数 (0 0 2 ) の格子面の X線回折ロッ キングカーブの半値幅は 1 3 2秒と結晶性が向上した。
さらに、 カルシウム成分を C a O換算で 0. 0 0 0 4モル%含む酸化ベリリウムを主成分と する焼結体からなる基板を用いた場合、 該基板に直接形成された 1 0 0モル%A 1 N単結晶薄 膜のミラー指数 (0 0 2 ) の格子面の X線回折ロッキングカーブの半値幅は 1 9 1秒であるの に対して、 同じカルシウム成分を含む酸化ベリリウムを主成分とする焼結体からなる基板にあ らかじめ 1 0 0モル%A 1 Nの配向性多結晶を形成し、 さらにその上に形成された 1 0 0モ ル% A 1 N単結晶薄膜のミラー指数 ( 0 0 2) の格子面の X線回折ロッキングカーブの半値幅 は 1 2 4秒と結晶性が向上した。 また、 珪素成分を S i 02換算で 0. 0 0 2モル%含む酸化べ リリウムを主成分とする焼結体からなる基板を用いた場合、 該基板に直接形成された 1 0 0モ ル% A 1 N単結晶薄膜のミラー指数 ( 0 0 2) の格子面の X線回折ロッキングカーブの半値幅 は 1 6 8秒であるのに対して、 同じ珪素成分を含む酸化ベリリウムを主成分とする焼結体から
なる基板にあらかじめ 1 0 0モル%A 1 Nの配向性多結晶を形成し、 さらにその上に形成され た 1 0 0モル%A 1 N単結晶薄膜のミラー指数 (0 0 2) の格子面の X線回折ロッキングカー ブの半値幅は 9 6秒と 1 0 0秒以下となった。 以下マグネシウム成分、 カルシウム成分、 珪素 成分のうちから選ばれる少なくとも 1種以上の成分を酸化物 で合計 0. 0 0 1モル%〜 3
5. 0モル%の範囲で含む酸化ベリリゥムを主成分とする焼結体からなる基板を用いた場合、 該基板に直接形成された窒化ガリゥム、 窒化アルミニゥムのうちから選ばれた少なくとも 1種 以上を主成分とする単結晶薄膜の結晶性よりも、 該基板にあらかじめ窒化アルミニウムを主成 分とする配向性多結晶薄膜を形成し、 さらにその上に形成された窒化ガリウム、 窒化アルミ二 ゥムのうちから選ばれた少なくとも 1種以上を主成分とする単結晶薄膜のほうが結晶性はより 優れたものが得られ、 該単結晶薄膜のミラ一指数 (0 0 2) の格子面の X線回折ロッキング力 ープの半値幅が 8 9秒〜 9 7秒の範囲でありすべて 1 0 0秒以下であることが確認された。 また、 マグネシウム成分を Mg O換算で 4 0. 0モル%含む酸化ベリリウムを主成分とする 焼結体からなる基板に直接形成した 1 0 0モル%A 1 N単結晶薄膜の場合は該単結晶薄膜のミ ラー指数 ( 0 0 2) の格子面の X線回折ロッキングカーブの半値幅が 2 1 7秒であるのに対し て、 同じ基板にあらかじめ 1 0 0モル% A 1 N配向性多結晶薄膜を形成しその上に形成した 1 0 0モル%A 1 N単結晶薄膜では 1 4 2秒と結晶性が向上した。
また、 例えば表 4 7に示すようにマグネシウム、 カルシウム、 珪素のうちから選ばれる少な くとも 1種以上の成分を含みさらに希土^素成分を含む酸化ベリリゥムを主成分とする焼結 体からなる基板を用いた場合、 該基板に直接形成された 1 0 0モル%A 1 N単結晶薄膜あるい は 1 0 0モル%G a N単結晶薄膜の結晶性に対して、 同じマグネシウム、 カルシウム、 珪素の うちから選ばれる少なくとも 1種以上の成分及び希土 S¾素成分を含む酸化ベリリウムを主成 分とする焼結体からなる基板にあらかじめ 1 0 0モル%A 1 Nの配向性多結晶を形成し、 さら にその上に形成された 1 0 0モル%A 1 N単結晶薄膜あるいは 1 0 0モル%G a N単結晶薄膜 の結晶性は向上することカ 認された。 例えば、 カルシウム成分を C a O換算で 0. 0 0 0 4 モル%含みさらにその他にイットリウム成分を Y203騰で 0. 0 0 0 2モル%、 4. 0モル%、
6. 0モル%含む組成の酸化ベリリウムを主成分とする焼結体からなる基板を用いた場合、 該 基板に直接形成された 1 0 0モル%Α 1 Ν単結晶薄膜あるいは 1 0 0モル%G a N単結晶薄膜 のミラー指数 (0 0 2 ) の格子面の X線回折ロッキングカーブの半値幅はそれぞれの基板で 1 8 2秒、 1 7 6秒、 1 8 9秒であるのに対して、 同じカルシウム成分及びィットリゥム成分を 含む酸化ベリリゥムを主成分とする焼結体からなる基板にあらかじめ 1 0 0モル%A 1 Nの配 向性多結晶を形成し、 さらにその上に形成された 1 0 0モル%A 1 N単結晶薄膜あるいは 1 0 0モル%G a N単結晶薄膜のミラー指数 (0 0 2) の格子面の X線回折ロッキング力一ブの半 値幅はそれぞれの基板で 1 1 9秒、 1 2 1秒、 1 2 6秒と結晶性が向上した。 さらにカルシゥ ム成分を C a〇換算で 0. 0 2 0モル%含みさらにその他にィットリゥム成分を Y 2〇 3騰で 0. 0 0 1 0モル%、 0. 0 0 4 0モル%、 0. 0 1 0モル%含む組成の酸化ベリリウムを主 成分とする焼結体からなる基板にあらかじめ 1 0 0モル%A 1 N配向性多結晶薄膜を形成した ものを用いた場合はその上に形成した 1 0 0モル%A 1 N単結晶薄膜あるいは 1 0 0モル%G a N単結晶薄膜のミラー指数 ( 0 0 2 ) の格子面の X線回折ロッキングカーブの半値幅はそれ ぞれ 9 3秒、 9 4秒、 9 2秒と 1 0 0秒以下であり、 同じ基板に直接形成したものより結晶性 は向上した。 また、 カルシウム成分を C a O換算で 0. 4 5モル%含みさらにその他にイット リウム成分を Y203 ^で 0. 0 4 0モル%、 ジスプロシウム成分を D y 2〇3換算で 0. 0 4 0モル%、 ホルミウム成分を H o 203換算で 0. 0 4 0モル%、 エルビウム成分を E r 2〇3換 算で 0. 0 4 0モル%、 イッテルビウム成分を Y b 203騰で 0. 0 4 0モル%、 それぞれ含 む組成の酸化ベリリウムを主成分とする焼結体からなる基板にあらかじめ 1 0 0モル%A 1 N
配向性多結晶薄膜 ¾形成したものを用いた場合はその上に形成した 1 0 0モル%A 1 N単結晶 薄膜あるいは 1 0 0モル% G a N単結晶薄膜のミラ一指数 (0 0 2 ) の格子面の X線回折口ッ キングカープの半値幅はそれぞれ 8 8秒、 9 1秒、 9 0秒、 8 9秒、 9 0秒とすべて 1 0 0秒 以下であり、 同じ基板に直接形成したものより結晶性は向上した。
なお、 表 4 7には記載していないが、 本実施例で作製した表 4 7に示す各種組成の酸化ベリ リウムを主成分とする焼結体からなる基板に 1 0 0モル%A 1 N配向性多結晶薄膜だけでなぐ 実施例 2 5の実験 N o . 7 0 6及び 7 0 7で行つたスパッ夕リング法及び実験 N ο'. 7 0 9で 行った MO CVD法と同様の条件により 1 0 0モル%Α 1 Νの薄膜を厚み 3 mであらかじめ 形成し、 それぞれ実施例 2 5と同様の無定形、 多結晶、 及び単結晶状態の窒化アルミニウムを 主成分とする薄膜を形成した。 また、 実験 N o . 7 2 8、 7 3 0で行った MO CVD法と同様 の条件により 1 0 0モル%G a Nの薄膜を厚み 3 zmであらかじめ形成し、 それぞれ実施例 2 5と同様の無定形、 及 D«向性多結晶状態の窒化ガリウムを主成分とする薄膜を形成した。 ま た、 実験 N o . 7 3 1で行った MOCVD法と同様の条件により 1 0 0モル% I nNの薄膜を 厚み 3 mであらかじめ形成し、 実施例 2 5と同様の配向性多結晶状態の窒化インジウムを主 成分とする薄膜を形成した。
また、 上記のようにあらかじめ窒化アルミニウムを主成分とする薄膜、 窒化ガリウムを主成 分とする薄膜、 窒化ィンジゥムを主成分とする薄膜を形成した酸化ベリリゥムを主成分とする 焼結体からなる基板と、 薄膜を形成せずに残しておいた酸化ベリリウムを主成分とする焼結体 からなる基板とを用い、 実施例 1 9に記載されたものと同様の MO CVD法によりさらにその 上に 1 0 0モル%A 1 N及び 1 0 0モル%G a Nだけでなく 1 0 0モル% I n N, 5 0モル% A 1 N+ 5 0モル% G a N、 5 0モル% G a N+ 5 0モル% I n N各組成の単結晶薄膜を厚み 3 mで形成した。
上記構成の薄膜を表 4 7に示した同じ酸化ベリリウムを主成分とする焼結体からなる基板に 形成したときも、 あらかじめ形成される薄膜が 1 0 0モル%A 1 N配向性多結晶でさらにその 上に形成される薄膜が 1 0 0モル%A 1 Nあるいは 1 0 0モル%G a N単結晶薄膜の構成から なるものと同様の効果を有することが確認された。 例えば同じ酸化ベリリウムを主成分とする 焼結体からなる基板に直接形成した窒ィ匕ガリウム、 窒化インジウム、 窒化アルミニウムのうち から選ばれた少なくとも 1種以上を主成分とする単結晶薄膜の結晶性より、 あらかじめ窒化ガ リウム、 窒化インジウム、 窒化アルミニウムのうちから選ばれた少なくとも 1種以上を主成分 とする無定形、 多結晶、 配向性多結晶、 単結晶など各種結晶状態の薄膜を形成しその上に形成 した単結晶薄膜のほうが結晶性に優れていることが確認された。
このように本実施例において酸化ベリリウムを主成分とする焼結体からなる基板を用いた場 合、 該基板に直接形成した窒化ガリウム、 窒化インジウム、 窒化アルミニウムのうちから選ば れた少なくとも 1種以上を主成分とする単結晶薄膜の結晶性よりも、 該基板にあらかじめ窒化 ガリウム、 窒化インジウム、 窒化アルミニウムのうちから選ばれた少なくとも 1種以上を主成 分とする無定形、 多結晶、 配向性多結晶、 単結晶など各種結晶状態の薄膜を形成しさらにその 上に形成した窒化ガリウム、 窒化インジウム、 窒化アルミニウムのうちから選ばれた少なくと も 1種以上を主成分とする単結晶薄膜のほうが結晶性はより優れたものが得られることがすベ ての実験で確認された。
本実施例において表 4 7に記載した構成の薄膜及びその他に作製したすべての薄膜の外観を 調べたがあらかじめ基板に形成した薄膜及びその上にさらに形成した薄膜いずれもクラックや ひび割れなどの欠陥は見られない。 また、 粘着テープによる剥離テストを行ったがいずれの薄 膜も酸化ベリリゥムを主成分とする焼結体からなる基板との間及び奪膜同志の間で剥離は見ら れなかった。 また、 基板表面の薄膜に T i /P t /Auの薄膜導電性材料を形成して金属リ一
ドをはんだ付けし垂直引張り強度を調べたがすべて 2 K g/mm2以上であり酸化ベリリゥム を主成分とする焼結体からなる基板と該基板にあらかじめ形成した薄膜、 及び該薄膜とさらに その上に形成した単結晶薄膜とは強固に接合している。
実施例 3 2
本実施例は酸化アルミニウムを主成分とする焼結体を基板として用いたとき該基板の組成と 該基板に形成される窒化ガリウム、 窒化インジウム、 窒化アルミニウムを主成分とする薄膜の 結晶性に及ぼす影響を調べた例を示す。
まず、 酸化アルミニウム (A 1 203) 粉末として日本 属株式会社製の 「A— 3 1」 ダレ ードを用意し、 マグネシア (M g O) 粉末として株式会社高純度化学 ¾ ^所製の純度 9 9. 9 9 %のものを用意し、 炭酸カレシゥム (C a C〇3)粉末として株式会ネ土高«化学 ¾J ¾所製の 純度 9 9. 9 9 %のものを用意し、 シリカ (S i〇2)粉末として株式会社アドマテック製の純 度 9 9. 9 %の 「S O_ E 2」 グレードを用意した。 これらの粉末を所定の組成になるよう実 施例 1と同様の方法によりポールミルで粉碎混合後パラフィンワックスを加えて成形用粉末を 作製し、 実施例 1と同様の大きさの成形体に一軸プレス成形後脱脂し、 その後 1 5 5 0 °Cで 3 時間大気中で常圧焼成してマグネシウム成分、 カルシウム成分、 珪素成分を各種割合で含有す る酸化アルミニウムを主成分とする焼結体を作製した。 これらの歸吉体はいずれも相対密度 9 8 %以上に緻密化していた。 得られた焼結体を実施例 2 8と同様雌 0. 0 5 のコロイド 状のアルミナを主成分とする研 を用いて鏡面研磨し塩化メチレン及び I P Aで超音波洗浄 し基板を作製した。 鏡面研磨した基板の平均表面粗さ R aは 6. 7 nm〜7. 6 nmの範囲に あった。 研磨後の基板を用いて波長 6 0 5 nmの光に対する光 率を実施例 2と同様の方法 により測定した。
このようにして得られた酸化アルミニゥムを主成分とする焼結体からなる基板の特性を表 4 8に示す。
表 4 8に示すようにマグネシウム成分、 カルシウム成分、 珪素成分及びその他の成分を添加 せずに焼成され実質的に原料中あるいは雌体製造時に混入する不純物以外は含まな 酸化ァ ルミ二ゥムを主成分とする焼結体の波長 6 0 5 nmの光に対する光透過率は 1 8 %であったが マグネシウム成分、 カルシウム成分、 珪素成分の含有量が増加するにつれ光透過率も上昇する 傾向を示しマグネシウム成分を M g O換算で 1 . 2 0モル%含むものは 5 7 %に達した。 その 後マグネシウム成分、 カルシウム成分、 珪素成分の含有量が増加するにつれ光 率は次第に 低下しカルシウム成分を C a O換算で 2 0. 0モル%及ぴ 素成分を S i 02麟で 2 0. 0モ ル%同時に含む酸化アルミニウムを主成分とする焼結体では波長 6 0 5 nmの光に対する光透 過率は 2 2 %となり、 マグネシウム成分を M g O腿で 2 0. 0モル%及び 素成分を S i〇 2 換算で 3 0. 0モル%同時に含む酸化アルミニウムを主成分とする焼結体では光翻率が 6. 4 %となった。
また、 本実施例においてマグネシウム成分、 カルシウム成分、 珪素成分のうち少なくとも 1 種以上を酸化物 で合計 4 5. 0モル%以下の範囲で含みさらに希土 ¾素成分のうちから 選ばれた少なくとも 1種以上の成分を酸化物換算で合計 0. 0 0 0 2モル%〜1 0. 0モル% の範囲で含む酸化アルミニウムを主成分とする焼結体の ^過率は、 上記と同じ量のマグネシ ゥム成分、 カルシウム成分、 珪素成分のうち少なくとも 1種以上を含むが実質的に希土類元素 成分を含まない酸化アルミニウムを主成分とする焼結体の光 ¾i率と比較して減少するなどの 変化がほとんど見られないことが 11認された。 すなわち、 カルシウム成分を C a O換算で 0. 0 5 0モル%含む酸化アルミニウムを主成分とする焼結体の波長 6 0 5 nmの光に対する光透 過率は 3 6 %であるが、 カルシウム成分を C a O換算で 0. 0 5 0モル%及びィットリゥム成 分を Υ?.〇3騰で 0. 0 4モル%同時に含む酸化アルミニウムを主成分とする焼結体の髓過
率は 3 7 %とほとんど変化せず、酸化アルミニウムを主成分とする焼結体にマグネシウム成分、 カルシウム成分、 珪素成分以外に希土 IS¾素成分が含まれることによる影響はあまり見られな いことが ¾認された。 さらに、 マグネシウム成分を M g O換算で 1. 2 0モル%含む酸化アル ミニゥムを主成分とする焼結体の波長 6 0 5 nmの光に対する光 ¾i率は 5 7 %と比較的高い 光透過率を有していたが、 マグネシウム成分を M g。換算で 1 . 2 0モル%及びィットリゥム 成分を Y203換算で 0. 0 4モル%同時に含む酸化アルミニウムを主成分とする焼結体の避 過率も 5 9 %、 マグネシウム成分を M g〇■で 1. 2 0モル%及びホルミゥム成分を H o 2〇 3瞎で 0. 0 4モル%同時に含む酸化アルミニウムを主成分とする條結体の光醒率も 5 6 %、 マグネシウム成分を M g。換算で 1 . 2 0モル%及びィッテルビウム成分を Y b 2 O 3換算で 0. 0 4モル%同時に含む酸化アルミニウムを主成分とする焼結体の髓過率も 5 8 %、 と比較的 高ぐ イットリウムをはじめとする希土 IB¾素成分が含まれることによって光 ¾Μ率が大きく 低下し悪い影響を与えるという現象は見られなかった。
表 4 8において、 カルシウム成分を C a〇換算で 0. 0 5 0モル%含みさらにイットリウム 成分を Y203購で 8. 0モル%同時に含む酸化アルミニウムを主成分とする焼結体は波長 6 0 5 n mの光に対する腿過率は 3 6 %であり、カルシウム成分を C a O換算で 0. 0 5モル% 含みさらにイットリウム成分を Y203纏で 1 2. 0モル%同時に含む酸化アルミニウムを主 成分とする能結体は波長 6 0 5 nmの光に対する光 ¾ϋ率は 2 7 %であった。 このように、 本 実施例においてマグネシウム成分、 カルシウム成分、 珪素成分のうち少なくとも 1種以上を酸 化物 »で合計 4 5. 0モル%以下の範囲で含み、 さらに希土類 素成分のうちから選ばれた 少なくとも 1種以上の成分を酸化物換算で合計 0. 0 0 0 2モル%〜1 0. 0モル%の範囲で 含む酸化アルミニウムを主成分とする焼結体は波長 6 0 5 nmの光に対する光翻率 3 0 %以 上のものが作製し得ることが確認された。
さらに、 本実施例においてマグネシウム成分、 カルシウム成分、 珪素成分のうち少なくとも いずれか 2種以上を含み、 同時に希土航素成分のうちから選ばれた少なくとも 1種以上の成 分を含む酸化アルミニウムを主成分とする焼結体はより高い光透過率を有するものが作製し得 ることが確認された。 また、 最高 8 0 %以上の光透過率を有する酸化アルミニウムを主成分と する焼結体が製造し得ることも確認された。 すなわち、 表 4 8に示されるように、 マグネシゥ ム成分を Mg〇換算で 0. 6 0モル%、 カルシウム成分を C a〇換算で 0. 8 0モル%及び 素成分を S i 02露で 0. 8 0モル%同時に含み、さらにイットリウム成分を Y203購で 0. 0 0 8 0モル%、 ジスプロシゥム成分を D y 2 O 3換算で 0. 0 4 0モル%それぞれ含む酸化ァ ルミ二ゥムを主成分とする焼結体は波長 6 0 5 nmの光に対する光透過率がそれぞれ 5 7 %、 7 8 %に増大した。 また、 マグネシウム成分を M g。換算で 0. 6 0モル%及ぴ 素成分を S 1 o2 o. 2 0モル%同時に含みさらにイットリウム成分を Y203ii ^で 0. 0 4モル% 含む酸化アルミニウムを主成分とする焼結体は波長 6 0 5 nmの光に対する) 率が 6 9 % であった。 さらに、 マグネシウム成分を M g〇換算で 1 . 0モル%及びカルシウム成分を C a O騰で 0. 2 0モル%同時に含み、 さらにィットリウムなどの希土観素成分を酸化物換算 で 0. 0 4 0モル%含む酸化アルミニウムを主成分とする焼結体の波長 6 0 5 nmの光に対す る光 ¾1率は 8 1 %〜 8 2 %の高いものであった。 すなわち、 上記量のマグネシウム成分及び カルシウム成分と同時に希土類 素成分としてイットリウム成分を Y203換算で 0. 0 4 0モ ル%含む酸化アルミニウムを主成分とする焼結体は波長 6 0 5 nmの光に対する光 ¾ii率が 8 2 %であり、 エルビウム成分を E r 203霧で 0. 0 4モル%同時に含む酸化アルミニウムを 主成分とする焼結体では光透過率が 8 1 %であった。
次に用意した上記の基板に対して実施例 2 7に示したものと同様の方法で薄膜を形成した。 すなわち、 用意した基板の一部を選びその上に実施例 2 5の実験 N o . 7 0 8で行つたスパッ
タリング法と同様の条件により 1 0 0モル%A 1 Nの薄膜を厚み 3 mであらかじめ形成した。 次に上記のようにしてあらかじめ A 1 N薄膜を形成した酸化アルミニウムを主成分とする焼 結体からなる基板と、 A 1 N薄膜を形成せずに残しておいた酸化アルミニウムを主成分とする 焼結体からなる基板とを用いその上にさらに実施例 1 9に記載されたものと同じ 1 0 0モル% A 1 N、 1 0 0モル%G a N各組成の薄膜を MO CVD法により厚み 3 mで形成した。 MO C VDの条件としては実施例 1 9に記載のように実施例 1及び実施例 2と同様の条件であった。 このようにして作製した薄膜の特性を表 4 8に示した。
本実施例において、 上記各基板にあらかじめ形成した 1 0 0モル%A 1 N薄膜はミラ一指数 ( 0 0 2 ) の格子面からの回折線だけが出現しており、 明らかに基板面に対して C軸が垂直な 方向に形成された配向性多結晶であった。
上記各基板にあらかじめ形成した A 1 N配向性多結晶薄膜の結晶性を見ると、 表 4 8に示す ように実質的にマグネシウム成分、 カルシウム成分、 珪素成分を含まな 酸化アルミニウムを 主成分とする焼結体からなる基板を用いた場合、 該配向性多結晶薄膜のミラー指数 ( 0 0 2 ) の格子面の X線回折ロッキングカーブの半値幅は 9 7 2 0秒であった。 マグネシウム成分、 力 ルシゥム成分、 珪素成分が増加するにつれて該配向性多結晶薄膜の結晶性は向上する傾向を示 した。 すなわち、 カルシウム成分を C a O換算で 0. 0 0 0 5モル%含む酸化アルミニウムを 主成分とする焼結体からなる基板を用いた場合 9 2 4 0秒であつたが、珪素成分を S i 02購 で 0. 0 0 2 0モル%含む酸化アルミ二ゥムを主成分とする焼結体からなる基板を用いた場合 は 8 6 6 0秒であり、 マグネシウム成分を Mg〇購で 0. 0 1 0モル%含む酸化アルミニゥ ムを主成分とする焼結体からなる基板を用いた場合は 7 8 1 0秒と 8 0 0 0秒以下に低下した。 その後マグネシウム成分、 カルシウム成分、 珪素成分の含有量が増加するにつれて該 A 1 N配 向性多結晶薄膜の結晶性は少し向上する傾向を示した。 マグネシウム成分を Mg で 1 . . 0モル%及びカルシウム成分を C a O麟で 0. 2 0モル%同時に含む酸化アルミニウムを主 成分とする焼結体からなる基板を用いた場合は 7 2 4 0秒と最も向上した。 その後マグネシゥ ム成分、 カルシウム成分、 珪素成分の含有量が増加するにつれて該 A 1 N配向性多結晶薄膜の 結晶性はやや低下する傾向を示した。 カルシウム成分を C a O算で 2 0. 0モル%及び 素成 分を S 1 02騰で 2 0. 0モル%同時に含む酸化アルミニウムを主成分とする焼結体からなる 基板に形成した A 1 N配向性多結晶薄膜の場合は 7 8 3 0秒であった。 しかしながら、 マグネ シゥム成分を M g〇算で 2 0. 0モル%及び 素成分を S i O 2麟で 3 0. 0モル%同時に含 む酸化アルミニウムを主成分とする焼結体からなる基板に形成した A 1 N配向性多結晶薄膜の ±易合は 9 3 7 0秒と結晶性は低下した。
また、 マグネシウム成分、 カルシウム成分、 珪素成分のうち少なくとも 1種以上の成分を酸 ィ匕物購で合計 4 5. 0モル%以下含み、 さらに希土類 素成分のうちから選ばれた少なくと も 1種以上の成分を含む酸化アルミニウムを主成分とする焼結体からなる基板に形成した A 1 N配向性多結晶薄膜の結晶性と、 上記と同じ量のマグネシウム成分、 カルシウム成分、 珪素成 分のうち少なくとも 1種以上の成分を含むが実質的に希土 S¾素成分を含まない酸化アルミ二 ゥムを主成分とする焼結体からなる基板に形成した A 1 N配向性多結晶薄膜の結晶性とを比較 した場合、 その結晶性はあまり変化せず、 酸化アルミニウムを主成分とする焼結体にマグネシ ゥム成分、 カルシウム成分、 珪素成分以外に希土類 素成分が含まれることによる影響はあま り見られないことカ權認された。 ' 本実施例において、 これらマグネシウム成分、 カルシウム成分、 珪素成分のうち少なくとも 1種以上の成分を含みさらに希土類沅素成分を含む酸化アルミニウムを主成分とする焼結体か らなる基板に形成した該配向性多結晶薄膜のミラー指数 (0 0 2 ) の格子面の X線回折ロッキ ングカーブの半値幅は 7 0 7 0秒〜 7 8 3 0秒の範囲でありすべて 8 0 0 0秒以下であった。
次に、 上記の薄膜をあらかじめ形成せずに残しておいた酸化アルミニウムを主成分とする焼 結体からなる基板を用いて前記 MO C VD法により形成した 1 0 0モル%A 1 N、 1 0 0モ ル%G a N各組成からなる薄膜の結晶性を X線回折により調べた。 その結果、 作製したすべて の薄膜が基板面に対して C軸が垂直な方向に形成された単結晶であることが確認された。 その 結晶性を見ると、 表 4 8に示すようにマグネシウム成分、 カルシウム成分、 珪素成分及びその 他の成分を添加せずに焼成され実質的に原料中あるいは焼結体製造時に混入する不純物以外は 含まない酸化アルミニウムを主成分とする焼結体からなる基板に直接形成され 1 0 0モル%A I N単結晶薄膜のミラー指数 ( 0 0 2 ) の格子面の X線回折ロッキングカーブの半値幅は 2 7 4秒であった。 一方、 カルシウム成分を C a〇 で 0. 0 0 0 5モル%含む酸化アルミニゥ ムを主成分とする焼結体からなる基板に直接形成した 1 0 0モル%A 1 N単結晶薄膜の場合は 2 1 5秒と小さくなり結晶性が向上した。さらに、珪素成分を S i〇2騰で 0. 0 0 2 0モル% 含む酸化アルミニウムを主成分とする焼結体からなる基板に直接形成した 1 0 0モル%A 1 N 単結晶薄膜の場合は 1 8 7秒であり、 マグネシウム成分を M g O換算で 0. 0 1 0モル%含む 酸化アルミニウムを主成分とする焼結体からなる基板に直接形成した 1 0 0モル%A 1 N単結 晶薄膜の場合は 1 5 6秒とそれぞれ 2 0 0秒以下になり結晶性が向上した。 カルシウム成分を C a O騰で 0. 0 5 0モル%含む酸化アルミ二ゥムを主成分とする焼結体からなる基板に直 接形成した 1 0 0モル%A 1 N単結晶薄膜の場合は 1 4 0秒と 1 5 0秒以下となり結晶性がよ り向上した。 マグネシウム成分を Mg O で 0. 1 2モル%含む酸化アルミニウムを主成分 とする焼結体からなる基板に直接形成した 1 0 0モル%A 1 N単結晶薄膜の場合は 1 1 9秒で あり、 マグネシウム成分を M g O換算で 0. 6 0モル%及ぴ 素成分を S i〇 2騰で 0. 2 0 モル%含む酸化アルミニウムを主成分とする焼結体からなる基板に直接形成した 1 0 0モル% A 1 N単結晶薄膜の: は 1 1 6秒と、それぞれ 1 3 0秒以下になり結晶性がさらに向上した。 その後マグネシウム成分、 カルシウム成分、 珪素成分の含有量が増加するにしたがつて酸化ァ ルミ二ゥムを主成分とする焼結体からなる基板に直接形成される単結晶薄膜のミラー指数 ( 0 0 2 ) の格子面の X線回折ロッキングカーブの半値幅が小さくなつた。 すなわち、 マグネシゥ ム成分を Mg 0購で 1 . 2 0モル%含む酸化アルミニウムを主成分とする焼結体からなる基 板に直接形成した 1 0 0モル%A 1 N単結晶薄膜の場合で 1 1 4秒、 マグネシウム成分を M g
1. 0 0モル%及びカルシウム成分を C a 0. 2 0モル%及同時に含む酸化 アルミニウムを主成分とする焼結体からなる基板に直接形成した 1 0 0モル%A 1 N単結晶薄 膜の場合で 1 1 3秒と本実施例において直接基板に形成した単結晶薄膜のな力、では最も小さく なり結晶性が最も優れていた。 その後マグネシウム成分、 カルシウム成分、 珪素成分の含有量 が増加するにしたがつて酸化アルミ二ゥムを主成分とする焼結体からなる基板に直接形成され る単結晶薄膜のミラー指数 ( 0 0 2 ) の格子面の X線回折ロッキングカーブの半値幅が大きく なり、 カルシウム成分を C a O ^で 2 0. 0モル%及ぴ 素成分を S i〇2^で 2 0. 0モ ル%同時に含む酸化アルミニウムを主成分とする焼結体からなる基板に直接形成した 1 0 0モ ル%八1:^単結晶薄膜の場合は 1 4 1秒となった。 また、 マグネシウム成分を Mg O換算で 2 0. 0モル%及ぴ 素成分を S i〇2纏で 3 0. 0モル%同時に含む酸化アルミニウムを主成 分とする焼結体からなる基板に直接形成した 1 0 0モル%A 1 N単結晶薄膜の場合は 2 2 6秒 となり 2 0 0秒より大きくなつた。
一方本実施例において表 4 8に示すように、 マグネシウム、 カルシウム、 珪素成分のうち少 なくとも 1種以上を含む酸化アルミニウムを主成分とする焼結体からなる基板は該焼結体中に 例えば希土類 素などマグネシウム、 カルシウム、 珪素成分以外の成分が含まれていたとして も該基板に直接形成される窒化ガリウム、 窒化インジウム、 窒化アルミニウムのうちから選ば れた少なくとも 1種以上を主成分とする単結晶薄膜の結晶性が大きく低減化するなどの変化は
少ないことカ雕認された。 言い換えれば、 上記マグネシウム、 カルシウム、 珪素成分のうち少 なくとも 1種以上を含む酸化アルミニウムを主成分とする焼結体からなる基板は、 該焼結体中 に希土類元素などマグネシウム、 カルシウム、 珪素成分以外の成分が含まれていたとしてもこ れらの成分によつて該基板に直接形成される単結晶薄膜の結晶性に影響を受けにくいものであ ることが確認された。
具体的に言えば、 カルシウム成分を C a〇 で 0. 0 5 0モル%含み同時にィットリゥム 成分を Y 2〇 3換算でそれぞれ 0. 0 4 0モル%、 8. 0 0モル%及び 1 2. 0モリレ%含む酸化 アルミニウムを主成分とする焼結体からなる基板に直接形成された 1 0 0モル%A 1 N単結晶 薄膜のミラ一指数 ( 0 0 2) の格子面の X線回折ロッキングカーブの半値幅はそれぞれ 1 3 7 秒、 1 2 7秒、 1 3 4秒であり、 その結晶性はカルシウム成分を C a O換算で 0. 0 5モル% 含み実質的にィットリゥム成分を含まない酸化アルミニウムを主成分とする焼結体からなる基 板に直接形成された 1 0 0モル%A 1 N単結晶薄膜の 1 4 0秒から大きく低減化するなどの変 化傾向を示さなかった。 また、 マグネシウム成分を M g O換算で 1. 2 0モル%含み同時にィ ットリウム成分を Y203^で 0. 0 4 0モル%含む酸化アルミニウムを主成分とする焼結体 からなる基板、 及びマグネシウム成分を Mg〇^^で 1 . 2 0モル%含み同時にイツテルビゥ ム成分を Y b 2〇3換算で 0. 0 4 0モル%含む酸化アルミニウムを主成分とする焼結体からな る基板に直接形成された 1 0 0モル%G a N単結晶薄膜のミラー指数 (0 0 2 ) の格子面の X 線回折ロッキングカーブの半値幅はそれぞれ 1 1 2秒、 及び 1 1 5秒であり、 その結晶性はマ グネシゥム成分だけを M 〇換算で 1. 2 0モル%含み実質的にィットリゥム成分を含まない 酸化アルミニウムを主成分とする焼結体からなる基板に直接形成された 1 0 0モル%A 1 N単 結晶薄膜の 1 1 4秒と比べて大きく低減化するなどの変化傾向を示さなかった。 また、 マグネ シゥム成分を M g O換算で 1 . 2 0モル%含み同時にホルミゥム成分を H o 2〇 3換算で 0. 0 4 0モル%含む酸化アルミニウムを主成分とする焼結体からなる基板に直接形成された 1 0 0 モル% A 1 N単結晶薄膜のミラ一指数 (0 0 2 ) の格子面の X線回折ロッキングカーブの半値 幅は 1 1 5秒であり、 その結晶性はマグネシゥム成分だけを M g〇換算で 1 . 2 0モル%含み 実質的にィットリゥムなどの希土麵素成分を含まない酸化アルミニウムを主成分とする焼結 体からなる基板に直接形成された 1 0 0モル%A 1 N単結晶薄膜の 1 1 4秒と比べて大きく低 減化するなどの変化傾向を示さなかった。 また、 珪素成分を S i 02^ ^で 0. 0 0 2 0モル% 同時に含みさらにイットリウム成分を Y2〇 3騰で 0. 0 0 0 5モル%含む酸化アルミニウム を主成分とする焼結体からなる基板に直接形成された 1 0 0モル%Α 1 Ν単結晶薄膜のミラー 指数 (0 0 2) の格子面の X線回折ロッキングカーブの半値幅は 1 6 1秒であり、 その結晶性 は珪素成分を S i 02藤で0. 0 0 2 0モル%含み実質的にイットリウム成分を含まない酸化 アルミニウムを主成分とする焼結体からなる基板に直接形成された 1 0 0モル%A 1 N単結晶 薄膜の 1 8 7秒から大きく低減化するなどの変化傾向を示さなかった。
また、 マグネシウム成分を Mg O換算で 0. 6 0モル%かつカルシウム成分を C a O換算で 0. 8 0モル%かつ珪素成分を S i 0
2換算で 0. 8 0モル%同時に含み、 さらにィットリゥム 成分を Y
20
3換算で 0. 0 0 8 0モル%、 ジスプロシウム成分を D y
2〇
3騰で 0. 0 4 0モ ル%含む酸化アルミニウムを主成分とする焼結体からなる基板に直接形成された 1 0 0モル% A 1 N単結晶薄膜のミラー指数 (0 0 2) の格子面の X線回折ロッキングカーブの半値幅はそ れぞれ 1 1 1秒、 1 1 3秒であり、 その結晶性はマグネシウム成分を Mg O換算で 0. 6 0モ ル%かつカルシウム成分を C a〇換算で 0. 8 0モル%かつ珪素成分を S i〇
2換算で 0. 8 0 モル%同時に含み実質的にィットリゥム成分を含まなレ酸化アルミニウムを主成分とする焼結 体からなる基板に直接形成された 1 0 0モル%A 1 N単結晶薄膜の 1 2 0秒から大きく低減化 するなどの変化傾向を示さなかった。 また、 マグネシウム成分を Mg O で 0. 6 0モル%
かつ珪素成分を S i O
2藤で 0. 2 0モル%同時に含み、 さらにィットリゥム成分を Y
2 O
3換 算で 0. 0 4 0モル%含む酸化アルミニウムを主成分とする焼結体からなる基板に直接形成さ れた 1 0 0モル%A 1 N単結晶薄膜のミラー指数 (0 0 2 ) の格子面の X線回折ロッキング力 —プの半値幅は 1 1 2秒であり、その結晶性はマグネシウム成分を Mg〇換算で 0. 6 0モル% かつ珪素成分を S i 0
2藤で 0. 2 0モル%同時に含み実質的にイットリウム成分を含まない 酸化アルミニウムを主成分とする焼結体からなる基板に直接形成された 1 0 0モル%A 1 N単 結晶薄膜の 1 1 6秒から大きく低減化するなどの変化傾向を示さなかった。 また、 マグネシゥ ム成分を Mg O換算で 1 . 0 0モル%かつカルシウム成分を C a O換算で 0. 2 0モル%同時 に含み、 さらにイットリウム成分を Y
20
3換算で 0. 0 4 0モル%含む酸化アルミニウムを主 成分とする焼結体からなる基板に直接形成された 1 0 0モル%Α 1 Ν単結晶薄膜のミラー指数 ( 0 0 2 ) の格子面の X線回折ロッキングカーブの半値幅は 1 0 7秒であり、 その結晶性はマ グネシゥム成分を M g O換算で 1 . 0 0モル%かつカルシウム成分を C a 0換算で 0. 2 0モ ル%同時に含み実質的にィットリゥムなどの希土類 素成分を含まない酸化アルミニウムを主 成分とする焼結体からなる基板に直接形成された 1 0 0モル%A 1 N単結晶薄膜の 1 1 3秒か ら大きく低減化するなどの変化傾向を示さなかった。 また、 マグネシウム成分を Mg
1. 0 0モル%かつカルシウム成分を C a O換算で 0ノ 2 0モル%同時に含み、 さらにエルビ ゥム成分を E r 0
3騰で 0. 0 4 0モル%含む酸化アルミニウムを主成分とする焼結体からな る基板に直接形成された 1 0 0モル%G a N単結晶薄膜のミラー指数 (0 0 2) の格子面の X 線回折ロッキングカーブの半値幅は 1 0 9秒であり、 その結晶性はマグネシウム成分を Mg〇 換算で 1 . 0 0モル%かつカルシウム成分を C a〇換算で 0. 2 0モル%同時に含み実質的に イツトリゥムなどの希土類 素成分を含まない酸化アルミニウムを主成分とする焼結体からな る基板に直接形成された 1 0 0モル%A 1 N単結晶薄膜の 1 1 3秒から大きく低減化するなど の変化傾向を示さなかつた。
このようにマグネシウム成分、 カルシウム成分、 珪素成分のうちから選ばれた少なくとも 1 種以上を含む酸化アルミニウムを主成分とする焼結体からなる基板は、 該基板がたとえマグネ シゥム成分、 カルシウム成分、 珪素成分以外にィットリゥムなどの希土類元素成分が同時に含 まれている酸化アルミニウムを主成分とする焼結体からなるものであったとしても、 該基板に 直接形成される窒化ガリゥム、 及び窒化アルミニウムを主成分とする単結晶薄膜の結晶性はあ まり変化せず、 イツトリゥムなどの希土^ ¾素成分含有の有無による影響を受けにくい傾向を 有すること力 ¾|認された。
上記のように各種組成の酸化アルミ二ゥムを主成分とする焼結体からなる基板に直接形成さ れた 1 0 0モル%A 1 N単結晶薄膜、 1 0 0モル%G a N単結晶薄膜のミラ一指数 ( 0 0 2 ) の格子面の X線回折ロッキングカーブの半値幅はすべて 3 0 0秒以下で結晶性に優れていた。 本実施例において、 このような特性を有する上記各種組成の酸化アルミニウムを主成分とす る焼結体からなる基板を用いたとき、 該基板に直接形成される窒化ガリウム、 窒化アルミニゥ ムのうちから選ばれた少なくとも 1種以上を主成分とする単結晶薄膜の結晶性よりも、 該基板 にあらかじめ窒化アルミニウムを主成分とする配向性多結晶薄膜を形成しさらにその上に窒化 ガリウム、 窒化アルミニウムのうちから選ばれた少なくとも 1種以上を主成分とする単結晶薄 膜を形成すれば該単結晶薄膜の結晶性はより優れたものが得られることが ϋ認された。 すなわ ち、 各種組成を有する酸化アルミニウムを主成分とする焼結体を基板として用い、 該基板に直 接形成される窒化ガリウム、 窒化アルミニウムのうちから選ばれた少なくとも 1種以上を主成 分とする単結晶薄膜のミラ一指数 ( 0 0 2) の格子面の X線回折ロッキングカーブの半値幅は 2 0 0秒以下になるとは必ずしも限らない。 それに対して、 このような各種組成を有する酸化 アルミニウムを主成分とする焼結体を基板として用いても、 該基板にあらかじめ窒化アルミ二
ゥムを主成分とする配向性多結晶薄膜を形成しさらにその上に窒化ガリゥム、 窒化アルミニゥ ムのうちから選ばれた少なくとも 1種以上を主成分とする単結晶薄膜を形成すれば該単結晶薄 膜のミラ一指数 (0 0 2 ) の格子面の X線回折ロッキングカーブの半値幅は 2 0 0秒以下のも のが形成し得ること力 萑認された。
また、 同じ組成の酸化アルミニウムを主成分とする焼結体からなる基板を用いて窒化ガリゥ ム、 窒化アルミニウムのうちから選ばれた少なくとも 1種以上を主成分とする単結晶薄膜を形 成する場合、 該基板に直接形成される窒化ガリウム、 窒化アルミニウムのうちから選ばれた少 なくとも 1種以上を主成分とする単結晶薄膜の結晶性よりも、 該基板にあらかじめ窒化アルミ 二ゥムを主成分とする配向性多結晶薄膜を形成しさらにその上に窒化ガリゥム、 窒化アルミ二 ゥムのうちから選ばれた少なくとも 1種以上を主成分とする単結晶薄膜を形成すれば該単結晶 薄膜の結晶性はより優れたものが得られることが確認された。
すなわち、 マグネシウム成分、 カルシウム成分、 珪素成分のうち少なくとも 1種以上を酸化 物購で合計 0. 0 0 1モル%〜4 5. 0モル%の範囲で含む酸化アルミニウムを主成分とす る焼結体を基板として用い、 その上にあらかじめ窒化アルミニウムを主成分とする配向性多結 晶薄膜を形成し、 さらにその上に窒化ガリウム、 窒化アルミニウムのうちから選ばれた少なく とも 1種以上を主成分とする単結晶薄膜を形成すれば該単結晶薄膜のミラー指数 ( 0 0 2) の 格子面の X線回折ロッキングカーブの半値幅は 1 3 0秒以下の結晶性に優れたものとなり易ぐ マグネシウム成分、 カルシウム成分、 珪素成分のうち少なくとも 1種以上を酸化物換算で合計 0. 0 0 5モル%〜4 5. 0モル%の範囲で含む酸化アルミニウムを主成分とする焼結体を基 板として用い、 その上にあらかじめ窒化アルミニウムを主成分とする配向性多結晶薄膜を形成 しさらにその上に窒化ガリウム、 窒化アルミニウムのうちから選ばれた少なくとも 1種以上を 主成分とする単結晶薄膜を形成すれば該単結晶薄膜のミラー指数 ( 0 0 2) の格子面の X線回 折ロッキングカーブの半値幅は 1 0 0秒以下の結晶性に優れたものが比較的容易に形成し得る ことが確認された。
また、 上記量のマグネシウム成分、 カルシウム成分、 珪素成分を含みその他にイットリウム 成分、 ジスプロシウム成分、 ホルミゥム成分、 エルビウム成分、 ィッテルビウム成分などの成 分を同時に含む酸化アルミニウムを主成分とする焼結体からなる基板であっても該基板に形成 される単結晶薄膜の結晶性は、 前記マグネシウム成分、 カルシウム成分、 珪素成分を含みその 他にイットリウム成分、 ジスプロシウム成分、 ホルミゥム成分、 エルビウム成分、 イツテルビ ゥム成分などの成分は実質的に含まない酸化アルミニウムを主成分とする焼結体からなる基板 に形成される単結晶薄膜の結晶性と比較して大きく低減化するなどの変化を受けにくいことが 確認された。 すなわち、 上記量のマグネシウム成分、 カルシウム成分、 珪素成分のうちから選 ばれる少なくとも 1種以上の成分を有する酸化アルミニウムを主成分とする焼結体からなる基 板であれば、 たとえイットリウム成分、 ジスプロシウム成分、 ホルミゥム成分、 エルビウム成 分、 ィッテルビウム成分などマグネシウム成分、 カルシウム成分、 珪素成分以外の成分が含ま れていたとしてもこれらの成分によって形成される窒化ガリウム、 窒化アルミニウムのうちか ら選ばれた少なくとも 1種以上を主成分とする単結晶薄膜の結晶性は影響を受けにくいもので あることが確認された。
より具体的には、 表 4 8に示すようにマグネシウム成分、 カルシウム成分、 珪素成分及びそ の他の成分を添加せずに焼成され実質的に原料中あるいは焼結体製造時に混入する不純物以外 は含まない酸ィ匕アルミニウムを主成分とする焼結体からなる基板に直接形成された 1 0 0モ ル%八1?^単結晶薄膜のミラ一指数 (0 0 2 ) の格子面の X線回折ロッキングカーブの半値幅 は 2 7 4秒であるのに対して、 同じ酸化アルミニウムを主成分とする焼結体からなる基板にあ らかじめ 1 0 0モル%A 1 Nの配向性多結晶を形成し、 その上にさらに形成された 1 0 0モ
ル% A I N単結晶薄膜のミラー指数 (0 0 2 ) の格子面の X線回折ロッキングカーブの半値幅 は 1 4 2秒と結晶性が向上した。 また、 カルシウム成分を C a O換算で 0. 0 0 0 5モル%含 む酸化アルミニウムを主成分とする焼結体からなる基板を用いた塲合、 該基板に直接形成され た 1 0 0モル%A 1 N単結晶薄膜のミラー指数 (0 0 2 ) の格子面の X線回折ロッキングカー ブの半値幅は 2 1 5秒であるのに対して、 同じカルシウム成分を含む酸化アルミニウムを主成 分とする焼結体からなる基板にあらかじめ 1 0 0モル%A 1 Nの配向性多結晶を形成し、 さら にその上に形成された 1 0 0モル%A 1 N単結晶薄膜のミラー指数 (0 0 2 ) の格子面の X線 回折ロッキング力一ブの半値幅は 1 3 3秒と結晶性が向上した。
さらに、 珪素成分を S i〇2»で 0. 0 0 2 0モル%含む酸化アルミニウムを主成分とする 焼結体からなる基板を用いた場合、 該基板に直接形成された 1 0 0モル%A 1 N単結晶薄膜の ミラー指数 ( 0 0 2) の格子面の X線回折ロッキングカーブの半値幅は 1 8 7秒であるのに対 して、 同じカルシウム成分を含む酸化アルミニウムを主成分とする焼結体からなる基板にあら かじめ 1 0 0モル%A 1 Nの配向性多結晶を形成し、 その上にさらに形成された 1 0 0モル% A 1 N単結晶薄膜のミラー指数 (0 0 2 ) の格子面の X線回折ロッキング力一ブの半値幅は 1 2 2秒と結晶性が向上した。 また、 マグネシウム成分を Mg O換算で 0. 0 1 0モル%含む酸 化アルミニウムを主成分とする焼結体からなる基板を用いた場合、 該基板に直接形成された 1 0 0モル%A 1 N単結晶薄膜のミラー指数 (0 0 2) の格子面の X線回折ロッキングカーブの 半値幅は 1 5 6秒であるのに対して、 同じマグネシウム成分を含む酸化アルミニウムを主成分 とする焼結体からなる基板にあらかじめ 1 0 0モル%A 1 Nの配向性多結晶を形成し、 さらに その上に形成された 1 0 0モル%A 1 N単結晶薄膜のミラー指数 (0 0 2 ) の格子面の X線回 折ロッキングカーブの半値幅は 9 6秒と 1 0 0秒以下となった。 以下マグネシウム成分、 カル シゥム成分、 珪素成分のうちから選ばれる少なくとも 1種以上の成分を酸化物^:で合計 0. 0 0 1モル%〜4 5. 0モル%の範囲で含む酸化アルミニウムを主成分とする焼結体からなる 基板を用いた場合、 該基板に直接形成された窒化ガリゥム、 窒化アルミニウムのうちから選ば れた少なくとも 1種以上を主成分とする単結晶薄膜の結晶性よりも、 該基板にあらかじめ窒化 アルミニウムを主成分とする配向性多結晶薄膜を形成し、 さらにその上に形成された窒化ガリ ゥム、 窒化アルミニウムのうちから選ばれた少なくとも 1種以上を主成分とする単結晶薄膜の ほうが結晶性はより優れたものが得られ 該単結晶薄膜のミラー指数 (0 0 2) の格子面の X 線回折ロッキングカーブの半値幅が 9 0秒〜 9 7秒の範囲でありすべて 1 0 0秒以下であるこ とが確認された。
また、 マグネシウム成分を M g〇換算で 2 0. 0モル%及び珪素成分を S i〇 2 で 3 0. 0モル%同時に含む酸化アルミニウムを主成分とする焼結体からなる基板に直接形成した 1 0 0モル% A 1 N単結晶薄膜の場合は該単結晶薄膜のミラ一指数 ( 0 0 2) の格子面の X線回折 ロッキングカープの半値幅が 2 2 6秒であるのに対して、 同じ基板にあらかじめ 1 0 0モル% A 1 N配向性多結晶薄膜を形成しその上に形成した 1 0 0モル%A 1 N単結晶薄膜では 1 4 7 秒と結晶性が向上した。
また、 表 4 8に示すようにマグネシウム、 カルシウム、 珪素のうちから選ばれる少なくとも 1種以上の成分を含みさらに希土類 素成分のうちから選ばれた少なくとも 1種以上の成分を 含む酸化アルミニウムを主成分とする焼結体からなる基板を用いた場合でも、 該基板に直接形 成された 1 0 0モル%A 1 N単結晶薄膜あるいは 1 0 0モル%G a N単結晶薄膜の結晶性より も、 同じマグネシウム、 カルシウム、 珪素のうちから選ばれる少なくとも 1種以上の成分を含 みさらに希土 IS¾素成分のうちから選ばれた少なくとも 1種以上の成分を含む酸化アルミニゥ ムを主成分とする焼結体からなる基板にあらかじめ 1 0 0モル%A 1 N配向性多結晶薄膜ある いは 1 0 0モル% G a N配向性多結晶薄膜を形成し、 さらにその上に 1 0 0モル% A 1 N単結
晶薄膜あるいは 1 0 0モル%G a N単結晶薄膜を形成すれば該単結晶薄膜の結晶性は向上する ことがt認された。例えば表 4 8に示すように珪素成分を S i 02購で 0. 0 0 2 0モル%含 みさらにその他にィットリゥム成分を Y 2〇 3換算で 0. 0 0 0 5モル%含む組成の酸化アルミ 二ゥムを主成分とする焼結体からなる基板にあらかじめ 1 0 0モル%A 1 N配向性多結晶薄膜 を形成したものを用いた場合はその上に形成した単結晶薄膜のミラ一指数 (0 0 2 ) の格子面 の X線回折ロッキングカーブの半値幅は 1 0 4秒と向上した。 さらにカルシウム成分を C a O 膽で 0. 0 5 0モル%含みさらにその他にィットリゥム成分を Y 2 O 3醇で 0. 0 4 0モル% 含む組成の酸化アルミニウムを主成分とする焼結体からなる基板にあらかじめ 1 0 0モル%A 1 N配向性多結晶薄膜を形成したものを用いた場合はその上に形成した単結晶薄膜のミラー指 数 (0 0 2) の格子面の X線回折ロッキングカーブの半値幅は 9 5秒と 1 0 0秒以下に向上し た。 また、 マグネシウム成分を Mg〇 で 1 . 2 0モル%含みさらにその他にイットリウム 成分を Y2〇3騰で 0. 0 4 0モル%、ィッテルビゥム成分を¥ 13203騰で0. 0 4 0モル% それぞれ含む組成の酸化アルミニウムを主成分とする焼結体からなる基板にあらかじめ 1 0 0 モル% G a N配向性多結晶薄膜を形成したものを用いた場合はその上に形成した単結晶薄膜の ミラ一指数 (0 0 2 ) の格子面の X線回折ロッキングカーブの半値幅はそれぞれ 8 9秒、 9 0 秒とすべて 1 0 0秒以下であった。
また、 表 4 8に示すようにマグネシウム、 カルシウム、 珪素のうちから選ばれる少なくとも 2種以上の成分を含みさらに希土 素成分のうちから選ばれた少なくとも 1種以上の成分を 含む酸化アルミニウムを主成分とする焼結体からなる基板を用いた場合でも、 該基板に直接形 成された 1 0 0モル%A 1 N単結晶薄膜あるいは 1 0 0モル%G a N単結晶薄膜の結晶性より も、 同じマグネシウム、 カルシウム、 珪素のうちから選ばれる少なくとも 2種以上の成分を含 みさらに希土類 素成分のうちから選ばれた少なくとも 1種以上の成分を含む酸化アルミニゥ ムを主成分とする焼結体からなる基板にあらかじめ 1 0 0モル%A 1 N配向性多結晶薄膜ある いは 1 0 0モル% G a N配向性多結晶薄膜を形成し、 さらにその上に 1 0 0モル% A 1 N単結 晶薄膜あるいは 1 0 0モル%G a N単結晶薄膜を形成すれば該単結晶薄膜の結晶性は向上する ことが T表認された。 例えば、 マグネシウム成分を M g〇換算で 0. 6 0モル%かつカルシウム 成分を C a〇換算で 0. 8 0モル%かつ珪素成分を S i O 2換算で 0. 8 0モル%含みさらにそ の他にィットリゥム成分を Y203換算で 0. 0 0 8 0モル%、 ジスプロシウム成分を D y 203 換算で 0. 0 4 0モル%含む組成の酸化アルミニウムを主成分とする焼結体からなる基板を用 いた場合、 該基板に直接形成された 1 0 0モル%A 1 N単結晶薄膜のミラー指数 ( 0 0 2) の 格子面の X線回折ロッキングカーブの半値幅はそれぞれ 1 1 1秒、 1 1 3秒であるのに対して、 同じ成分を含む酸化アルミニウムを主成分とする焼結体からなる基板にあらかじめ 1 0 0モ ル%八 1 Nの配向性多結晶を形成し、 その上にさらに形成された 1 0 0モル%A 1 N単結晶薄 膜のミラー指数 (0 0 2 ) の格子面の X線回折ロッキングカーブの半値幅はそれぞれ 9 2秒、 9 0秒と結晶性が向上した。 また、 マグネシウム成分を M g〇換算で 0. 6 0モル%かつ珪素 成分を S i 02換算で0. 2 0モル%含みさらにその他にイットリウム成分を Y203換算で 0. 0 4 0モル%含む組成の酸化アルミニウムを主成分とする焼結体からなる基板を用いた場合、 該基板に直接形成された 1 0 0モル% A 1 N単結晶薄膜のミラー指数 (0 0 2 ) の格子面の X 線回折ロッキングカーブの半値幅は 1 1 2秒であるのに対して、 同じ成分を含む酸化アルミ二 ゥムを主成分とする焼結体からなる基板にあらかじめ 1 0 0モル%A 1 Nの配向性多結晶を形 成し、 その上にさらに形成された 1 0 0モル% A 1 N単結晶薄膜のミラー指数 (0 0 2 ) の格 子面の X線回折ロッキングカーブの半値幅は 9 1秒と結晶性が向上した。 また、 マグネシウム 成分を M g 0換算で 1. 0モル%かつカルシウム成分を C a 0娜で 0. 2 0モル%含みさら にその他にイットリウム成分を Y203換算で 0. 0 4 0モル%含む組成の酸化アルミニウムを
主成分とする焼結体からなる基板を用いた場合、 該基板に直接形成された 1 0 0モレ%A 1 N 単結晶薄膜のミラー指数 ( 0 0 2) の格子面の X線回折ロッキングカーブの半値幅は 1 0 7秒 であるのに対して、 同じ成分を含む酸化アルミニウムを主成分とする焼結体からなる基板にあ らかじめ 1 0 0モル%A 1 Nの配向性多結晶を形成し、 その上にさらに形成された 1 0 0モ ル%八1 1単結晶薄膜のミラ一指数 ( 0 0 2 ) の格子面の X線回折ロッキングカーブの半値幅 は 8 8秒と結晶性が向上した。 また、 マグネシウム成分を M g〇換算で 1. 0モル%かつカル シゥム成分を C a O換算で 0. 2 0モル%含みさらにその他にエルビウム成分を E r 203換算 で 0. 0 4 0モル%含む組成の酸化アルミニウムを主成分とする焼結体からなる基板を用いた 場合、 該基板に直接形成された 1 0 0モル%G a N単結晶薄膜のミラー指数 (0 0 2) の格子 面の X線回折ロッキングカーブの半値幅は 1 0 7秒であるのに対して、 同じ成分を含む酸化ァ ルミ二ゥムを主成分とする焼結体からなる基板にあらかじめ 1 0 0モル%G a Nの配向性多結 晶を形成し、 その上にさらに形成された 1 0 0モル%G a N単結晶薄膜のミラー指数 (0 0 2) の格子面の X線回折口ッキングカーブの半値幅は 8 9秒と結晶性が向上した。
なお、 表 4 8には記載していないが、 本実施例で作製した表 4 8に示す各種組成の酸化アル ミニゥムを主成分とする焼結体からなる基板に 1 0 0モル%A 1 N配向性多結晶薄膜だけでな く、 実施例 2 5の実験 N o. 7 0 6及び 7 0 7で行つたスパッタリング法及び実験 N o . 7 0 9で行った MO CVD法と同様の条件により 1 0 0モル%A 1 Nの薄膜を厚み 3 mであらか じめ形成し、 それぞれ実施例 2 5と同様の無定形、 多結晶、 及 結晶状態の窒化アルミニゥ ムを主成分とする薄膜を形成した。 また、 実験 N o . 7 2 8、 7 3 0で行った MO CVD法と 同様の条件により 1 0 0モル%G aNの薄膜を厚み 3 であらかじめ形成し、 それぞれ実施 例 2 5と同様の無定形、及 ϋ¾己向性多結晶状態の窒化ガリウムを主成分とする薄膜を形成した。 また、 実験 N o . 7 3 1で行った MO CVD法と同様の条件により 1 0 0モル% I n Nの薄膜 を厚み 3 mであらかじめ形成し、 実施例 2 5と同様の配向性多結晶状態の窒化インジウムを 主成分とする薄膜を形成した。
また、 上記のようにあらかじめ窒化アルミニウムを主成分とする薄膜、 窒化ガリウムを主成 分とする薄膜、 窒化ィンジゥムを主成分とする薄膜を形成した酸化アルミニウムを主成分とす る焼結体からなる基板と、 薄膜を形成せずに残しておいた酸化アルミニウムを主成分とする焼 結体からなる基板とを用い、 実施例 1 9に記載されたものと同様の MOCVD法によりその上 にさらに 1 0 0モル%A 1 N及び 1 0 0モル%G a Nだけでなく 1 0 0モル% I n N、 5 0モ ル% A 1 N+ 5 0モル% G a N、 5 0モル% G a N+ 5 0モル% I n N各組成の単結晶薄膜を 厚み 3 ^ mで形成した。
上記構成の薄膜を表 4 8に示した同じ酸化アルミニウムを主成分とする焼結体からなる基板 に形成したときも、 あらかじめ形成される薄膜が 1 0 0モル%A 1 N配向性多結晶でその上に さらに形成される薄膜が 1 0 0モル%A 1 Nあるいは 1 0 0モル%G a N単結晶薄膜の構成か らなるものと同様の効果を有することが ϋ認された。 例えば同じ酸化アルミニウムを主成分と する焼結体からなる基板に直接形成した窒化ガリウム、 窒化インジウム、 窒化アルミニウムの うちから選ばれた少なくとも 1種以上を主成分とする単結晶薄膜の結晶性より、 あらかじめ窒 化ガリウム、 窒化インジウム、 窒化アルミニウムのうちから選ばれた少なくとも 1種以上を主 成分とする無定形、 多結晶、 配向性多結晶、 単結晶など各種結晶状態の薄膜を形成しその上に 形成した単結晶薄膜のほうが結晶性に優れていることが確認された。
このように本実施例において酸化アルミニウムを主成分とする焼結体からなる基板を用いた 場合、 該基板に直接形成した窒化ガリウム、 窒化インジウム、 窒化アルミニウムのうちから選 ばれた少なくとも 1種以上を主成分とする単結晶薄膜の結晶性よりも、 該基板にあらかじめ窒 化ガリウム、 窒化インジウム、 窒化アルミニウムのうちから選ばれた少なくとも 1種以上を主
00051
369
成分とする無定形、 多結晶、 配向性多結晶、 単結晶など各種結晶状態の薄膜を形成しその上に さらに形成した窒化ガリウム、 窒化インジウム、 窒化アルミニウムのうちから選ばれた少なく とも 1種以上を主成分とする単結晶薄膜のほうが結晶性はより優れたものが得られることがす ベての実験で確認された。
本実施例において表 4 8に記載した構成の薄膜及びその他に作製したすべての薄膜の外観を 調べたがあらかじめ基板に形成した薄膜及びその上にさらに形成した薄膜いずれもクラックや ひび割れなどの欠陥は見られない。 また、 粘着テープによる剥離テストを行ったがいずれの薄 膜も酸化アルミニウムを主成分とする焼結体からなる基板との間及ぴ¾膜同志の間で剥離は見 られなかった。 また、 基板表面の薄膜に T i ZP t ZAuの薄膜導電性材料を形成して金属リ 一ドをはんだ付けし垂直引張り強度を調べたがすべて 2 K gZmm2以上であり酸化アルミ二 ゥムを主成分とする焼結体からなる基板と該基板にあらかじめ形成した薄膜、 及び該薄膜とそ の上にさらに形成した単結晶薄膜とは強固に接合している。
実施例 3 3
本実施例は酸化ジルコニウム、 酸化マグネシウム、 アルミン酸マグネシウム、 酸化イツトリ ゥムを主成分とする焼結体からなる基板についてその ¾¾ϋ性を調べ、 これらの基板を用いて 窒化ガリウム、 窒化インジウム、 窒化アルミニウムのうちから選ばれた少なくとも 1種以上を 主成分とする無定形、 多結晶、 配向性多結晶、 単結晶のうちから選ばれた少なくともいずれか の結晶状態を有する薄膜をあらかじめ形成し、 その上に窒化ガリウム、 窒化インジウム、 窒化 アルミニウムのうちから選ばれた少なくとも 1種以上を主成分とする単結晶薄膜の形成を試み た例を示すものである。
酸化ジルコニウム、 酸化マグネシウム、 アルミン酸マグネシウムを主成分とする焼結体から なる基板は実施例 1で作製した焼結体と本実施例であらたに作製した焼結体を用いて作製した もののそれぞれ 2種類を用意した。 酸化ィットリゥムを主成分とする焼結体からなる基板は本 実施例で新たに作製した。
本実施例においては以下に示す方法により酸化ジルコニウム、 酸化マグネシウム、 アルミン 酸マグネシウム、 酸化ィットリゥムを主成分とする焼結体をあらたに作製した。 すなわち、 実 施例 1で用いたものと同じ安定化剤として Υ 2 Ο 3を 3モル%含む酸化ジルコニウム原料を用意 し、 実施例 1と同様原料粉末に焼結助剤は加えずパラフィンワックスを加えて成形用粉末を作 製し、 粉末を一軸プレス成形繊脂し、 1 4 0 0°Cで 2時間、 圧力 1 5 0 KgZcm2、 大気 中でホットプレスして酸化ジルコニウムを主成分とする焼結体を作製した。 次に実施例 1で用 いたものと同じ酸化マグネシウム原料を用意し、 焼結助剤として C a Oと Y203をそれぞれ 1 重量%ずつ加えて実施例 1と同様にポールミルで粉碎混合し、 その後パラフィンワックスを加 えた粉末を一軸プレス成形後脱脂し、 1 6 0 0°Cで 6時間大気中で常圧焼成して酸化マグネシ ゥムを主成分とする焼結体を作製した。 次に実施例 1で用いたものと同じアルミン酸マグネシ ゥム原料を用意し、 酸化マグネシウムの場合と同様に焼結助剤として C a Oと Y203をそれぞ れ 0. 1重量%ずつ加えてポールミルで粉碎混合し、 その後パラフィンワックスを加えて成形 用粉末を作製し、一軸プレス成形籠脂し、 1 6 5 0°Cで 8時間水素気流中で常圧 «してァ ルミン酸マグネシウムを主成分とする焼結体を作製した。 次に実施例 3 0で用いたものと同じ Y2〇3粉末、 D y2〇3粉末、 Ho 2〇3粉末を用意し、 主成分ととして上記 Y203粉末だけを用 いてポールミルで粉碎後パラフィンワックスを加えて成形用粉末を作製し、 一軸プレス成形後 脱脂し、 1 6 0 0°Cで 3時間大気中で常圧 «して酸化イットリウムを主成分とする焼結体を 作製した。 また別に上記 Y203粉末 9 9. 5重量%に能結助剤として Dy 203及び Η ο 2〇3粉 末それぞれ 0. 2 5重量%ずつ加えてポールミルで粉碎混合し、 その後パラフィンワックスを 加えて成形用粉末を作製し、 一軸プレス成形謹脂し、 2 1 0 0°Cで 3時間水素気流中で常圧
焼成して酸ィ匕ィットリゥムを主成分とする焼結体を作製した。
次に実施例 1及び本実施例で作製した各焼結体を研削加工後粒径 0. 0 5 のコロイド状 酸化アルミニウムからなる研 を用いて鏡面研磨しァセトン及びィソプロピルアルコールで 洗浄して直径 2 5. 4mm厚み 0. 5 mmの円盤状基板を作製した。
このようにして作製した基板について波長 6 0 5 nmの光に対する光 ¾ 性を測定したがす ベての基板は光 ¾ 性を有することが 11認された。 その後これらの基板に実施例 2 7と同様の 方法で窒化ガリゥム、 窒化ィンジゥム、 窒化アルミニゥムのうちから選ばれた少なくとも 1種 以上を主成分とする無定形、 多結晶、 配向性多結晶のうちから選ばれた少なくともいずれかの 結晶状態を有する薄膜をあらかじめ厚み 3 m形成し、 さらにその上に厚み 3 mで窒化ガリ ゥム、 窒化インジウム、 窒化アルミニウムのうちから選ばれた少なくとも 1種以上を主成分と する単結晶薄膜の形成を試みた。 その結果明らかに本実施例で作製した酸化ジルコニウム、 酸 化マグネシウム、 アルミン酸マグネシウムを主成分とする焼結体からなる基板には単結晶薄膜 が形成できることが ϋ歸忍された。
これらの結果を表 4 9に示した。
酸化ジルコニウム、 酸化マグネシウム、 ァレミン酸マグネシウム、 酸ィ匕イットリウムを主成 分とする焼結体からなる基板も平均表面粗さ R aが 1 0 nm以下のものが作製し得ることが ¾ 認された。 また、 本実施例で作製した酸化ジルコニウム、 酸化マグネシウムを主成分とする焼 結体からなる基板は平均表面粗さ R aが 5 nm以下のものが作製し得ることカ雕認された。 ま た ¾¾i率も 2 0 %以上、酸化ジルコニウムを主成分とする! ¾結体からなる基板で最高 5 9 %、 酸化マグネシウム主成分とする焼結体からなる基板で最高 8 3 %、 アルミン酸マグネシウムを 主成分とする焼結体からなる基板では最高 7 9 %、 酸化イットリウムを主成分とする焼結体か らなる基板で最高 8 2 %のものが作製し得ることが確認された。
また、 酸ィ匕ジ Jレコニゥム、 酸ィ匕マグネシウム、 アルミン酸マグネシウム、 及び酸化イツトリ ゥムを主成分とする焼結体からなる基板に対して窒化ガリウム、 窒化インジウム、 窒化アルミ ニゥムのうちから選ばれた少なくとも 1種以上を主成分とする薄膜は無定形、 多結晶、 配向性 多結晶の各結晶状態であれば ¾接形成し得ることが ¾認された。 上記窒化ガリウム、 窒化イン ジゥム、 窒化アルミニウムのうちから選ばれた少なくとも 1種以上を主成分とする無定形、 多 結晶、 配向性多結晶のうちから選ばれた少なくともいずれかの結晶状態の薄膜あらかじめ形成 しその上に窒化ガリウム、 窒化インジウム、 窒化アルミニウムのうちから選ばれた少なくとも 1種以上を主成分とする薄膜を形成すれば該薄膜は単結晶状態のものが形成でき該単結晶薄膜 のミラー指数 (0 0 2) の格子面の X線回折ロッキングカーブの半値幅はすべて 2 0 0秒以下 の結晶性のものが形成できることが崔認、された。 また平均表面粗さ 5 nm以下の基板では該単 結晶薄膜のミラー指数 (0 0 2 ) の格子面の X線回折ロッキングカーブの半値幅はすべて 1 5 0秒以下の結晶性のものが形成できることが確認された。
本実施例において表 4 9に記載した構成の薄膜すベての外観を調べたがあらかじめ基板に形 成した薄膜及びその上にさらに形成した薄膜いずれもクラックやひび割れなどの欠陥は見られ ない。 また、 粘着テープによる剥離テストを行ったがいずれの薄膜も各酸化ジルコニウム、 酸 化マグネシウム、 アルミン酸マグネシウム、 及び 化イットリウムを主成分とする焼結体から なる基板との間及ぴ 膜同志の間で剥離は見られなかった。 また、 基板表面の薄膜に T i ZP t /A uの薄膜導電性材料を形成して金属リ一ドをはんだ付けし垂直弓 I張り強度を調べたがす ベて 2 K g /mm2以上であり酸化ジルコニウム、酸化マグネシウム、アルミン酸マグネシウム、 及び酸化ィットリゥムを主成分とする焼結体からなる基板と該基板にあらかじめ形成した薄膜、 及び該薄膜とさらにその上に形成した単結晶薄膜とは強固に接合していること力 崔認された。 実施例 3 4
本実施例は窒ィ匕アルミ二ゥムを主成分とする焼結体を基板として用いて発光^?を作製しそ の発光効率を調べた例を示す。
まず、 基板として本発明で作製した窒化アルミニウムを主成分とする焼結体を用いそれぞれ 組成 (窒化アルミニウム成分含有量)、 ¾¾1率の異なるものを用意した。 また導通ビアを有す るものも用意した。 用意した基板の形状は直径 2 5. 4mm厚み 0. 5mmの円盤状であり実 施例 8と同様酸化クロムを主成分とする研^!を用いる方法により鏡画磨及びその後の洗浄 が施してある。 その平均表面粗さは R a 1 9 ηπ!〜 3 3 nmの範囲にある。 用意した基板に 1 層目の薄膜として 施例 2 5の実験 N o . 7 0 6、 7 0 7、 7 0 8、 7 0 9及び 7 3 0に 示したものと同様のスパッタリング法あるいは MO CVD法により窒化ガリウムあるいは窒化 アルミニウムのうちから選ばれたいずれかを主成分とする無定形、 多結晶、 配向性多結晶、 単 結晶のうちから選ばれた少なくともいずれかの結晶状態を有する薄膜を厚み 3 m形成した。 その後 これら薄膜を形成した基板の上からさらに 2層目として実施例 1で示したものと同 じ方法で窒化ガリウムあるいは窒化アルミニウムのうちから選ばれたいずれかを主成分とする 単結晶薄膜を厚み 3 m形成した。 なお、 上記薄膜を形成せず窒化アルミニウムを主成分とす る焼結体をそのまま基板として用いたもの、 あるいは 2層目の単結晶薄膜を形成していない薄 膜 1層だけのものもある。 また、 用意した別の基板に対して実施例 1 8及び実施例 2 0に示し たものと同様のスパッタリング法により遊 r、 M o、 W、 WZC u合金、 R u、 R h、 P d、 O s、 I r、 P t、 T i、 N i各薄麟電性材料を厚み 0. 5 m形成し、 さらに該薄膜 導電性材料の上に ¾1:窒化ガリウム、 あるいは窒化アルミニウムのうちから選ばれた少なくと も 1種以上を主成分とする配向性多結晶薄膜を 1層目の薄膜として実施例 2 5の実験 N o . 7 0 8及び 7 3 0に示したものと同様のスパッタリング法あるいは MO CVD法で厚み 3 m形 成した。 その上にさらに 2層目として実施例 1で示したものと同じ MO CVD法で; i g窒化ガ リウム、 窒化アルミニウムのうちから選ばれた少なくとも 1種以上を主成分とする単結晶薄膜 を厚み 3 m形成した。 これらの窒化アルミ二ゥムを主成分とする焼結体の上に 窒化ガリ ゥムあるいは窒化アルミニウムのうちから選ばれたいずれかを主成分とする薄膜及び Ζ又は C r、 Mo、 W、 W/C u合金、 R u、 R h、 P d、 O s、 I r、 P t、 T i、 N i各薄麟電 性材料が形成された基板を用いて発光素子の作製を試みた。 比較のために市販されている基板 表面が C面の (すなわち C軸が基板面に対して垂直な) 直径 2 5. 4mm、 厚み 0. 5 mm、 平均表面粗さ R a 1. 2 nmの京セラ株式会社製サフアイァ基板も用意しその上に発光素子の 作製を試みた。 該サファイア基板はそのままの表面状態のものと、 窒化ガリウム、 窒化アルミ ニゥムのうちから選ばれた少なくとも 1種以上を主成分とする薄膜を本実施例による方法で表 面に 1層及び 2層形成したものとを用意し発光素子の作製を行つた。
発光素子作製に用いる上記各基板の特性を表 5 0に示した。 表 5 0には本実施例で用いた基 板の由来 (作製した実験 N o. ) も示されている。 表 5 0における各基板の ¾¾1率は波長 6 0 5 nmの光に対するものである。
次に用意した上記各基板を実施例 1で用いたものと同じ MO CVD装置の反応容器内に入れ H2を流しながら 9 5 0°C〜1 0 5 0 °Cで予備加熱を行った。その後上記各基板にバッファ層と してトリメチルガリウムをガリウム原料とし、 H2をキャリアガスとし、 反応ガスに NH3を用 いて上記実施例 1で用いたものと同じ装置の MO CVD法により基板? 5 2 0 °Cで G a N膜 を厚み 5 0 0 A形成した。 形成したバッファ層の上にトリメチルガリウムを主原料としさらに S i H4ガスをドーピング成分用原料として用い基板温度を 1 0 0 0 °Cとした以外は上記と同 じ条件の MO CVD法によりコンタクト層及び単一量子井戸の障壁層となる S iドーピングの ェピタキシャル成長 G a N薄膜を厚み 5 m形成した。 その上にトリメチルガリウム及びトリ メチルインジウムを主原料としドーピング成分を用いず基板温度を 8 0 0でとした以外は上記
と同じ条件の MOCVD法により発光層である単一量子井戸の井戸層となるアンド一プのェピ タキシャル成長 I n G a Nの 2成分混合組成薄膜を厚み 30 A形成した。 なお発光層となる I nGaN薄膜の組成は I n0.06Ga0.94N、 I n0.20Ga0.80N、 I n0.45Ga0.55Nの 3 種類のものを作製した.。 その上にトリメチルガリゥム及びトリメチルアルミニゥムを主原料と しさらにビスーシク口ペンタジェニルマグネシウム (Mg C p 2) をドーピング成分用原料に用 い基板温度を 1050°Cとした以外は上記と同じ条件の MOCVD法により単一量子井戸の障 壁層となる Mgドーピングのェピタキシャル成長 A 1'0.20Ga0. S0N組成の薄膜を厚み 0. 1 5 m形成した。 その上にトリメチルガリゥムを主原料としさらにビス一シクロペン夕ジェニ ルマグネシウム (MgCp2) をドーピング成分用原料に用い基板 Sを 100 O とした以外 は上記と同じ条件の MOCVD法によりコンタクト層となる Mgドーピングのェピタキシャル 成長 GaN薄膜を厚み 0. 5 形成した。 その後薄膜が形成された基板を反応容器から取り 出し N2中 700°Cで加熱を行った。次に、 このようにして作製した Mgドープ P型 GaN薄膜 層の上に所定の形状のマスクを形成し、 上記 S iドーピングの GaN薄^) iが露出するまでェ ツチングを行って該 S iドーピングの GaN薄膜層に T i /A 1の金属薄膜 2層で電極を作製 した。 また最上層に形成されている Mgドーピング GaN薄膜層には N iZAuの金属薄膜 2 層で電極を作製した。 その後薄膜が形成された基板を外形 ImmX 1mmの大きさのチップに 切断して単一量子井戸構造の発光ダイオード (LED) を作製した。 作製した発光ダイオード のうち薄膜層を形成していない基板を用いたものは図 42に例示するような構成のものである。 また、 薄膜層を 1層だけ形成した基板を用いたものは図 43に例示するような構成のものであ る。 また、 薄膜層を 2層形成した基板を用いたものは図 44に例示するような構成のものであ る。 また、 薄膜導電性材料を形成しさらに薄膜層を 2層形成した基板を用いたものは図 53に 例示するような構成のものである。また、電極は図 45に例示するような配置で形成してある。 なお、導通ビアを有する基板を用いたものは上記のようなエッチングによる電極形成を行わず、 S iドーピングの G a N薄膜層ではなく図 47〜図 49、 及び図 54〜図 56に示すように窒 化アルミニウムを主成分とする焼結体に T iZP tZAuの金属薄膜 3層で電極を形成し発光 素子の上下に電極を配置した形態の単一量子井戸構造の発光素子を作製した。 上下に電極を配 置した形態の発光素子チップの大きさも外形 1 mmx lmmである。 サファイア基板を用いて 作製した発光ダイオードは図 40に示すような構成であり、 電極は窒化アルミニウムを主成分 とする焼結体からなる基板を用いて作製した発光ダイォードと同様図 45に例示するような配 置で形成してある。
次に作製した発光ダイオードのうち発光層となる I nGaN薄膜の組成が I n0.20Ga0.80 Nのものを用いて直流電位を印加し発光を試みた。 その結果作製したいずれの発光ダイォード も電圧 3. 5ポル] ^〜 3. 8ポルトを印加することで中心波長 450 nmの発光が得られた。 次に上記発光層を有するすべての単一 井戸構造の発光ダイォ一ドについて該ダイォードを 駆動させるために入力される動作電流とそのとき発光素子から放出される発光出力とを測定し 発光効率を算定した。その結果を表 50の実験 N o. 1421〜実験 N o . 1459に示した。 表 50の実験 N o. 1457〜 1459はサフアイァ基板を用いて作製した発光ダイォードの 結果である。 なお、 表 50の動作電流は動作電圧 3. 6ポルトで発光ダイオードを駆動させた ときのものである。 その結果、 サファイア基板を用いて作製した単一量子井戸構造の発光ダイ ォードの場合発光効率は該サフアイァ基板の表面に窒化ガリゥム、 窒化アルミニウム薄膜を形 成していないもので 6. 7%、 窒化ガリウム、 窒化アルミニウム薄膜を 1層及び 2層形成した ものであっても 6. 9%〜7. 4%の範囲で薄膜の有無によらず小さかったが、 本発明による 窒化アルミニゥムを主成分とする焼結体からなる基板を用レ ^て作製した発光ダイォ一ドはすべ て発光効率 10 %以上であった。 表 50に示すようにサフアイァ基板の光透過率は 90 %以上
であり非常に高い。 それに対して窒化アルミニウムを主成分とする焼結体からなる基板は光透 過率を有しないかあるいは光透過率が 1 0 %以下のものであっても該窒化アルミニウムを主成 分とする焼結体からなる基板を用いて作製される発光素子の発光効率は 1 0 %以上でありサフ アイァ基板を用いて作製される発光素子よりも大きい。
また、 本発明による窒化アルミニウムを主成分とする焼結体からなる基板にあらかじめ窒化 ガリゥム、 窒化アルミニウム薄膜を形成せずそのまま用いて作製した発光ダイォードでも発光 効率 1 0 %以上であった。 さらに窒化ガリウムあるいは窒化アルミニウムを少なくとも 1層以 上形成した基板を用いることで作製した発光ダイォードの発光効率は向上した。 また薄膜 1層 だけ形成した基板より窒化アルミニウムを主成分とする焼結体からなる基板にあらかじめ窒化 ガリウムあるいは窒化アルミニウムを主成分とし無定形、 多結晶、 配向性多結晶、 単結晶のう ちから選ばれた少なくともいずれかの結晶状態の薄膜を形成し、 その上にさらに窒化ガリウム あるいは窒化アルミニウムを主成分とする単結晶薄膜を形成した薄膜 2層構成の基板を用いる ことで、 該基板に形成される発光素子の発光効率はさらに向上することが確認された。
焼結体からなる基板にあらかじめ窒化ガリウムあるいは窒化アルミニウムを主成分とし無定形、 多結晶、 配向性多結晶、 単結晶のうちから選ばれた少なくともいずれかの結晶状態の薄膜を形 成し、 その上にさらに窒化ガリゥムあるいは窒化アルミニウムを主成分とする単結晶薄膜を形 成した薄膜 2層構成の基板を用いることで、'その上に作製される発光素子の発光効率は 1 2 % 以上のものが得られることが HI認された。 また、 窒化アルミニウム成分を 5 0#¾%以上含有 する窒化アルミニウムを主成分とする焼結体からなる基板にあらかじめ窒化ガリウムあるいは 窒化アルミニウムを主成分とし無定形、 多結晶、 配向性多結晶、 単結晶のうちから選ばれた少 なくともいずれかの結晶状態の薄膜を形成した基板を用いることで、 その上に作製される発光 素子の発光効率は 1 2 %以上のものが得られることが II認された。 また、 窒化アルミ二ゥム成 分を 5 CH機%以上含有する窒化アルミニウムを主成分とする焼結体からなる基板にあらかじ め窒化ガリウムあるいは窒化アルミニウムを主成分とし配向性多結晶状態の薄膜を形成した基 板を用いることで、 その上に作製される発光素子の発光効率は 1 5 %以上のものが得られるこ とが確認された。
また、 窒化アルミニウム成分を 5 0体積%以上含有する窒化アルミニウムを主成分とする焼 結体からなる基板にあらかじめ窒化ガリウムあるいは窒化アルミニウムを主成分とし無定形、 多結晶、 配向性多結晶、 単結晶のうちから選ばれた少なくともいずれかの結晶状態の薄膜を形 成し、 その上にさらに窒化ガリゥムあるいは窒化アルミニウムを主成分とする単結晶薄膜を形 成した薄膜 2層構成の基板を用いることで、 その上に作製される発光素子の発光効率は 1 5 % 以上のものが得られることが確認された。
本実施例において、 本発明による窒化アルミニウムを主成分とする焼結体からなる基板の光 透過率が 1 %より小さいか実質的に光¾¾性を有しないもの、 あるいは) 率が 1 %以上の 基板を用いても発光効率 1 0 %以上の発光軒を作製できた。 また、 上記基板の光 ¾i 率が大 きいものほど該基板の上に作製される発光素子の発光効率は向上することが確認された。 すな わち、 窒化アルミニウムを主成分とする焼結体の耀過率が 1 0 %以上のものを基板として用 いたときその上に作製される発光素子の発光効率は 1 2 %以上のものが得られることが ϋ雀認さ れた。 また、 窒化アルミニウムを主成分とする焼結体の 過率 2 0 %以上のものを基板とし て用いたときその上に作製される発光素子の発光効率は 1 5 %以上のものが得られることが確 認された。 また、 窒化アルミニウムを主成分とする焼結体の光 ¾1率 3 0 %以上のものを基板 として用いたときその上に作製される発光素子の発光効率は 2 0 %以上のものが得られること が確認された。 また、 窒化アルミニウムを主成分とする焼結体の 過率 4 0 %以上のものを
0051
374
基板として用いたときその上に作製される発光素子の発光効率は 25 %以上のものが得られる ことが 認された。 また、 窒化アルミニウムを主成分とする焼結体の ¾¾1率 50%以上のも のを基板として用いたときその上に作製される発光素子の発光効率は 3.0 %以上のものが得ら れることが 認された。 率 60%以上の 性を有する窒化アルミニウムを主成分と する焼結体ものを基板として用いたときその上に作製される発光素子の発光効率は 40 %以上 のものが得られることが ϋ認された。 また、 本実施例において 率 88%の窒化アルミ二 ゥムを主成分とする焼結体からなる基板を用いたときその上には本実施例における最大の発光 効率 62 %を有する発光素子が作製された。
薄騰電性材料を形成した本発明による窒化アルミニウムを主成分とする焼結体からなる基 板を用いて作製した発光ダイオードもすベて発光効率 10%以上であった。 薄 ^電性材料を 形成した基板を用いて作製した発光ダイオード 板側からの発光はほとんど見られずその反 対側の P型 GaN薄編及び発光層側面のほうからの発光が観察された。 また、 薄膜導電性材 料を形成した基板を用いて作製した発光ダイォードの発光効率は同じ基板で該薄膜導電性材料 を形成していなレ基板を用いて作製した発光ダイォードの発光効率よりも低下することはなか つ/こ。
また、 導通ビアを有する基板を用いて作製した上下に電極を配した形態の発光ダイォードで あっても発光効率が特に低下するような傾向は見られず、 発光ダイォ一ドとして十分^ i¾でき ることが確認された。
なお、表 50には記載していないが発光層となる I nGaN薄膜の組成を I n。.。6Ga。.94 N、及び In。.45Ga。.55Nとして作製した単一量子井戸構造の発光ダイオードの場合、 中心 発光波長がそれぞれ 390 nmゝ及び 520 nmと変化したが、発光層の組成が I n0.20Ga0. 8()Nのものと同様本発明による窒化アルミニウムを主成分とする焼結体からなる基板を用いて 作製した発光ダイォードの場合すベてのものが発光効率 10%以上であつたのに対して、 サフ アイァ基板 (窒化ガリウム、 窒化アルミニウム薄膜を形成していない) を用いて作製された発 光ダイオードがそれぞれ 6. 6%、 6. 1%であったのに比べて発光効率が高かった。
次に用意した上記のセラミック材料を主成分とする基板及び比較のために用意したサフアイ ァ基板を用い、 別途ダカレヘテロ構造の発光軒の作製を行った。 すなわち、 用意した上記基 板を実施例 1で用いたものと同じ MOCVD装置の反応容器内に入れ H2を流しながら 95 0°C〜1050°Cで予備加熱を行った。 その後上記各基板にバッファ層としてトリメチルガリ ゥムをガリウム原料とし、 H2をキャリアガスとし、 反応ガスに NH3を用いて上記実施例 1で 用いたものと同じ装置の MOCVD法により基板 500°Cで GaN膜を厚み 500 A形成 した。形成したバッファ層の上にトリメチルガリウムを主原料としさらに S iH4ガスをド一ピ ング成分用原料として用い基板温度を 1050でとした以外は上記と同じ条件の MOCVD法 によりコンタクト層となる S iドーピングのェピタキシャル成長 GaN薄膜を厚み 4 m形成 した。その上にトリメチルガリウム及びトリメチルアルミニウムを主原料としさらに S iH4^ スをド一ピング成分用原料として用い基板温芰を 1050°Cとした以外は上記と同じ条件の M OCVD法によりクラッド層となる S iドーピングのェピタキシャル成長 A 10.15Ga0.85N 組成の薄膜を厚み 0. 15^m形成した。 その上にトリメチルガリウム及びトリメチルインジ ゥムを主原料としさらに S i H4ガス及びジェチル亜鉛をドーピング成分用原料として用い基 板温度を 800°Cとした以外は上記と同じ条件の MOCVD法により発光層となるェピタキシ ャル成長 I n0.06Ga0.94N組成の薄膜を厚み 50 OA形成した。その上にトリメチルガリウ ム及びトリメチルアルミニウムを主原料としさらにビスーシクロペンタジェニルマグネシウム
(MgCp2)をドーピング成分用原料として用い基板 &gを 1050°Cとした は上記と同 じ条件の MOCVD法によりクラッド層となる Mgドーピングのェピタキシャル成長 A 1。 15
G a 0. 85N組成の薄膜を厚み 0 · 1 5 m形成した。 その上にトリメチルガリゥムを主原料と しさらにビス——ンクロペンタジェニルマグネシウム (Mg C 2) をドーピング成分用原料とし て用レゝ基板^^を 1 0 5 0°Cとした以外は上記と同じ条件の MO CVD法によりコンタクト層 となる Mgドーピングのェピタキシャル成長 G a N薄膜を厚み 0. 5 m形成した。 その後薄 膜が形成された基板を反応容器から取り出し N2中 7 0 O tで加熱を行った。次に、 このように して作製した Mgド一プ Ρ型 G a N薄麵の上に所定の形状のマスクを形成し、 上記 S iドー ビングの G a N薄 が露出するまでエッチングを行って該 S iドーピングの G a N薄膜層に T i /A lの金属薄膜 2層で電極を作製した。 また最上層に形成されている Mgドーピング G a N薄膜層には N i /A uの金属薄膜 2層で電極を作製した。 その後薄膜が形成された基板を l mmx l mmの大きさのチップに切断してダブルへテロ構造の発光ダイオード (L ED) を 作製した。 作製した発光ダイオードのうち薄膜層を 2層形成した基板を用いたものは図 5 7に 例示するような構成のものである。 また、 薄膜層を形成していない基板を用いたものは図 5 7 の薄膜素 5及び薄膜層 8が形成されていないような構成のものである。 また、 薄 電性材料 を形成しさらに薄膜層を 2層形成した基板を用いたものは図 5 7の基板 4と薄膜層 5との間に 薄!^電性材料を形成したような構成のものである。 また、 電極は図 4 5に例示するような配 置で形成してある。 なお、 導通ピアを有する基板を用いたものは上記のようなエッチングによ る電極形成を行わず、 S iドーピングの G a N薄膜層ではなく図 4 7〜図 4 9、 及び図 5 4〜 図 5 6に示すように窒化アルミニウムを主成分とする焼結体に T i ZP t ZAuの金属薄膜 3 層で電極を形成し発光素子の上下に電極を配置した形態のダブルへテロ構造の発光素子を作製 した。 サファイア基板を用いて作製した発光ダイオードは図 4 1に示すような構成であり、 電 極は窒化アルミニウムを主成分とする焼結体からなる基板を用いて作製した発光ダイオードと 同様図 4 5に例示するような配置で形成してある。
次に作製した発光ダイ才ードに直流電位を印加して発光を試みた。 作製したいずれの発光ダ ィォ一ドも電圧 3. 5ポルト〜 3. 8ポルトを印加することで中心波長 4 5 0 nmの発光が得 られた。 次に作製したすべての上記ダカレへテロ構造の発光ダイォードについて該ダイォード を駆動させるために入力される動作電流とそのとき発光素子から放出される発光出力とを測定 し発光効率を算定した。 その結果を表 5 0の実験 N o . 1 4 6 0〜実験 N o . 1 4 7 0に示し た。 表 5 0の実験 N o . 1 4 6 9及び 1 4 7 0はサフアイァ基板を用いて作製した発光ダイォ ードの結果である。 なお、 表 5 0の動作電流は動作電圧 3. 6ポルトで発光ダイオードを駆動 させたときのものである。 その結果、 窒化ガリウム、 窒化アルミニウム薄膜を形成していない サフアイァ基板を用いて作製したダブルへテロ構造の発光ダイォードの場合発光効率は 5. 4 %であり、 窒化ガリゥム薄膜を形成したサファィァ基板を用いて作製したダブルへテロ構造 の発光ダイオードの場合発光効率は 5. 9 %であったが、 本発明による窒化アルミニウムを主 成分とする焼結体からなる基板を用いて作製したダブルへテロ構造の発光ダイオードはすべて 発光効率 1 0 %以上であった。 その他、 窒化アルミニウムを主成分とする焼結体からなる基板 の組成(窒化アルミニウム成分の含有量)、 基板の上に形成される薄藤成、 基板の) ¾Si率な どは発光素子の発光効率に対して上記単一量子井戸構造のつた。 表 5 0に示すようにサフアイ ァ基板の光 »率は 9 0 %以上であり非常に高い。 それに対して窒化アルミニウムを主成分と する焼結体からなる基板は光透過率を有しないかあるいは光¾1率が 1 0 %以下のものであつ ても該窒化アルミニウムを主成分とする焼結体からなる基板を用いて作製される発光素子の発 光効率は 1 0 %以上でありサフアイァ基板を用いて作製される発光素子よりも大きい。
また、 本発明による窒化アルミニウムを主成分とする焼結体からなる基板にあらかじめ窒化 ガリゥム、 窒化アルミニウム薄膜を形成せずそのまま用いて作製した発光ダイォ一ドでも発光 効率 1 0 %以上であった。 さらに窒化ガリウムあるいは窒化アルミニウムを少なくとも 1層以
上形成した基板を用いることで作製した発光ダイォードの発光効率は向上した。 また薄膜 1層 だけ形成した基板より窒化アルミニウムを主成分とする焼結体からなる基板にあらかじめ窒化 ガリウムあるいは窒化アルミニウムを主成分とし無定形、 多結晶、 配向性多結晶、 単結晶のう ちから選ばれた少なくともいずれかの結晶状態の薄膜を形成し、 その上にさらに窒化ガリウム あるいは窒化アルミニウムを主成分とする単結晶薄膜を形成した薄膜 2層構成の基板を用いる ことで、 該基板に形成される発光素子の発光効率はさらに向上することが確認された。
次に、 基板として実施例 2の実験 No. 49で作製した窒化アルミニウムを主成分とする基 板を用い、 実施例 25と同様のスパッタリング法を用いて厚み 3 mの 100モル%A 1 N配 向性多結晶薄膜をまず形成した。 その後スパッタリングチャンバ一から基板を取り出し実施例 1と同様の MOCVD法により厚み 25 mの基板面に対して C軸が垂直な方向の 100モ ル%八 1 N単結晶薄膜を形成した。 該 A 1N単結晶薄膜のミラー指数 (002) の格子面の X 線回折ロッキングカーブの半値幅は 84秒であった。 形成した A 1N単結晶薄膜を粒径 0. 1 mの酸化クロムを主成分とする研^ IJ及び ¾ί圣 0. 02 zmのコロイド状 S i〇2を主成分と する研^ (Iで鏡面研磨しァセトン及びィソプロピルアルコールで超音波洗浄して平均表面粗さ Ral. 2 nmの薄膜基板を作製した。 なお、 研藤表面の A 1 N単結晶薄膜は 9 //mの厚み で残っていた。 この薄膜基板を発光素子作製用基板として用い、 さらに比較のために上記のサ ファイア基板を用い、 レーザ一ダイオードの作製を行った。 なお、 用いたサファイア基板には バッファ層の上に ELO法を行うための S i 02膜などは施さずサファイアそのままの状態で 使用した。 このようにして用意した上記 2種類の基板を実施例 1で用いたものと同じ MOCV D装置の反応容器内に入れ H2を流しながら 1000°Cで予備加熱を行った。その後上記各基板 にバッファ層としてトリメチルガリゥムをガリゥム原料とし、 H2をキャリアガスとし、 反応ガ スに NH3を用いて上記実施例 1で用いたものと同じ装置の MOCVD法により基板温度 50 0°CでGaN膜を厚み500 A形成した。 形成したバッファ層の上にトリメチルガリウムを主 原料としさらに S i H4ガスをドーピング成分用原料として用い基板温度を 1050°Cとした 以外は上記と同じ条件の MO C VD法によりコンタクト層となる S iドーピングのェピタキシ ャル成長 G a N薄膜を厚み 6 m形成した。 その上にトリメチルガリゥム及びトリメチルアル ミニゥムを主原料としさらに S iH4ガスをドーピング成分用原料として用い基板温度を 10 5 Otとした以外は上記と同じ条件の MOCVD法により第 2のクラッド層となる S iド一ピ ングのェピタキシャル成長 A 10. 15Ga0.85N組成の薄膜を厚み 0. 1 m形成した。その上 にトリメチルガリゥム及びトリメチルアルミニウムを主原料としさらに S i H4ガスをドーピ ング成分用原料として用い基板温度を 105 Ot:とした以外は上記と同じ条件の MOCVD法 によりそれぞれ S iドーピングのェピタキシャル成長した A 10.15Ga0.85N薄 ¾び GaN 薄膜をそれぞれ厚み 20Aで交互に 150層積層してスーパーラテイス層を形成した。 その上 にトリメチルガリゥムを主原料としさらに S i H4ガスをドービング成分用原料として用い基 板 を 1000 °Cとした以外は上記と同じ条件の MO C V D法により第 1のクラッド層とな る S iド一ビングのェピタキシャル成長した G a N薄膜を厚み 0. 1 m形成した。 その上に トリメチリレガリゥム及びトリメチルインジゥムを主原料としさらに S i H4ガスをド一ピング 成分用原料として用レ基板 を 800°Cとした以外は上記と同じ条件の MOCVD法により 発光層となるェピタキシャル成長した I n0.15Ga0.85N (S iドーフ:) /In0.02Ga0.9 8N (S iドーフ の多重量子井戸を形成した。 この多重 »井戸の構成は井戸層となる In 0. 15Ga0.85N薄膜を厚み 30Aで 6層、障觀となる I n0.02Ga0.98N薄膜を厚み 85 Aで 5層それぞれを交互に積み重ねて形成されたものである。 その上にトリメチルガリゥムを主原 料としさらにビスーシクロペンタジェニルマグネシウム (MgC 2) をドーピング成分用原料 として用い基板温芰を 1000°Cとした以外は上記と同じ条件の MOCVD法により第 1のク
ラッド層となる Mgドーピングのェピタキシャル成長 G a N薄膜を厚み 0. 1 / m形成した。 その上にトリメチルガリゥム及びトリメチルアルミニウムを主原料としさらにビスーシクロべ ン夕ジェニルマグネシウム (MgCp2) をド一ビング成分用原料として用い基板温度を 105 0°Cとした以外は上記と同じ条件の M〇C VD法によりそれぞれ Mgドーピングのェピタキシ ャル成長した A 10. 15Ga0.85]>1薄 び0&1^薄膜をそれぞれ厚み2 OAで交互に 150層 積層してスーパーラティス層を形成した。 その上にトリメチルガリゥム及びトリメチルアルミ 二ゥムを主原料としさらにビス一シクロペンタジェニルマグネシウム (MgCp2) をドーピン グ成分用原料として用い基板温度を 1050°Cとした以外は上記と同じ条件の MOCVD法に より第 2のクラッド層となる Mgドーピングのェピタキシャル成長 A 10. 15Ga0.85N組成の 薄膜を厚み 0. 05 m形成した。 その上にトリメチルガリウムを主原料としさらにビス一シ クロペンタジェニルマグネシウム (MgCp2) をドーピング成分用原料として用い基板温度を 1000°Cとした以外は上記と同じ条件の MOCVD法によりコンタクト層となる Mgドーピ ングのェピタキシャル成長 G a N薄膜を厚み 0. 2 m形成した。 その後薄膜が形成された基 板を反応容器から取り出し N2中 700 で加熱を行った。次に、熱処理装置から取り出した後、 最上層の Mgド一プ P型 GaN薄膜層に図 46で示したような帯状の電極が形成できるような 形状のマスクを形成し、上記 S iドーピングの GaN薄膜層が露出するまでエッチングを行い、 その後該 S iドーピングの GaN薄膜層に T iZA 1の金属薄膜 2層で図 46に示すような帯 状の電極を作製した。 また最上層に形成され tいる Mgドーピング G a N薄膜層には N i /A uの金属薄膜 2層で図 46に示すような幅 10 mの帯状の電極を作製した。 電極形成後、 基 板を 0. 45mmX 0. 45 mmの大きさのチップに切断し、 帯状電極の長手方向に垂直な切 断両端面を鏡面研磨してミラ一を形成しレーザ一ダイォ一ドを作製した。 次に作製したレーザ —ダイォ一ドに直流電位を印加して発光を試みた。 その結¾»からのサファイアを基板とし て用いて作製したものは動作電圧 4. 7ポリレト、 動作電流 70mAで波長 402 nm出力 8m Wのレーザー光の発振が確認された。 このように からのサファイアを基板として用いて作 製したレーザーダイォードの発光効率は 2. 4%であった。 それに対して本発明による窒化ァ ルミ二ゥムを主成分とする焼結体からなる基板の表面に A 1 N単結晶薄膜が形成された薄膜基 板を用いて作製したレーザ一ダイオードの場合、 動作電圧 4. 3ポルト、 動作電流 70mAで 波長 402 nm出力 49 mWのレ一ザ一光の発振が ϋ認された。 このように本発明による窒ィ匕 アルミニウムを主成分とする焼結体からなる薄膜基板を用いて作製したレーザーダイオードの 発光効率は 16. 3 %であった。
またサファイア基板に上記と同じようにバッファ層として GaN膜を厚み 50 OA形成し、 その上に幅 10 mの帯状 S i 02薄膜を 10 mの間隔で形成したものを基板として用意し ELO法によるレーザ一ダイオードの作製を試みた。 該 S i〇2薄膜の厚み 0. 1 mである。 このようにあらかじめ帯状 S i 02薄膜を等間隔に形成したサファイア基板を用いて上記と同 じ方法でまずコンタクト層となる S iドープの GaN薄膜を 6 m形成しその後も上記と同じ 方法でレーザーダイオードを作製し発光を試みた。 なお、 作製したレーザーダイオードの P型 GaN薄麵に形成した電極は窒化ガリウム、 窒化インジウム、 窒化アルミニウムェピ夕キシ ャル薄膜中に転位やひずみの少ないと思われる帯状 S i 02薄膜の隙間部分に相当する位置に 形成した。 その結果該レーザーダイオードでは動作電圧 4. 4ポルト、 動作電流 70mAで波 長 402 nmのレーザー光出力 22mWが観測された。 発光効率は 7. 1 %である。 このよう に からのサフアイァ基板を用いた場合、 E L 0法を用いて作製されたレーザーダイォード であっても発光効率は比較的小さかった。
実施例 35
本実施例は炭化珪素、 窒化珪素、 酸化亜鉛、 酸化ベリリウム、 酸化アルミニウム、 酸化ジル
コニゥム、 酸化マグネシウム、 アルミン酸マグネシウム、 酸化イットリウムそれぞれを主成分 とする焼結体を基板として用いて発光素子の作製を試みその発光効率を調べた例を示す。 まず、 基板として本発明で作製した炭化珪素、 窒化珪素、 酸化亜鉛、 酸化ベリリウム、 酸化 アルミニウム、 酸化ジルコニウム、 酸化マグネシウム、 アルミン酸マグネシウム、 酸化イット リウムを主成分とする各焼結体を用いそれぞれ組成(各セラミック主成分の含有 *)、 m rn の異なるものを用意した。 用意した基板の形状は直径 2 5. 4mm厚み 0. 5 mmの円盤状で あり鏡面研磨及びその後の洗浄が施してある。 各基板の平均表面粗さ R aはそれぞれの由来、 すなわち実施例 1、 実施例 8、 実施例 3 0、 実施例 3 1、 実施例 3 2、 実施例 3 3で示された ものと同様である (実施例 1で作製した酸化ジルコニウムを主成分とする焼結体からなる基板 の R aが 3 6 nm、 酸化マグネシウムを主成分とする焼結体からなる基板が R a 6 0 nm、 ァ ルミン酸マグネシウムを主成分とする焼結体からなる基板が R a 6 3 nmであり、 残りのすべ ての基板はそれ以下の平均表面粗さである)。用意した基板に 1層目の薄膜として ¾i ^施例 2 5の実験 N o . 7 0 6、 7 0 7、 7 0 8、 7 0 9及び 7 3 0に示したものと同様のスパッタリ ング法あるいは MO CVD法により窒化ガリウムあるいは窒化アルミニウムのうちから選ばれ たいずれかを主成分とする無定形、 多結晶、 配向性多結晶、 単結晶のうちから選ばれた少なく ともいずれかの結晶状態を有する薄膜を厚み 3 形成した。 その後 ¾tこれら薄膜を形成し た基板の上からさらに 2層目として実施例 1で示したものと同じ方法で窒化ガリゥムあるいは 窒化アルミニウムのうちから選ばれたいずれかを主成分とする単結晶薄膜を厚み 3 zxm形成し た。 なお、 上記薄膜を形成せず焼結体をそのまま基板として用いたもの、 あるいは 2層目の単 結晶薄膜を形成していない薄膜 1層だけのものもある。
発光素子作製に用いる上記各基板の特性を表 5 1に示した。 表 5 1には本実施例で用いた基 板の由来(作製した実験 N o . ) も示されている。 各基板の平均表面粗さ R aはそれぞれの由来 すなわち実施例 1、 実施例 8、 実施例 3 0、 実施例 3 1、 実施例 3 2、 実施例 3 3で示された ものと同様である (実施例 1で作製した酸化ジルコニウムを主成分とする焼結体からなる基板 の R aが 3 6 nm、 酸化マグネシウムを主成分とする焼結体からなる基板が R a 6 0 nm、 ァ ルミン酸マグネシウムを主成分とする焼結体からなる基板が R a 6 3 nmであり、 残りのすべ ての基板はそれ以下の平均表面粗さである)。表 5 1における各基板の光 ¾i率は波長 6 0 5 η mの光に対するものである。
以下、 本実施例で用意した各基板を用いて実施例 3 4と同様にして単一量子井戸構造の発光 舒の作製を試みた。
すなわち、 まず用意した上記各基板を実施例 1で用いたものと同じ MO CVD装置の反応容 器内に入れ H2を流しながら 9 5 0 °C〜1 0 5 0°Cで予備加熱を行った。その後上記各基板にバ ッファ層としてトリメチルガリゥムをガリゥム原料とし、 H2をキャリアガスとし、反応ガスに NH3を用いて上記実施例 1で用いたものと同じ装置の MO C VD法により基板温度 5 2 0 °C で G a N膜を厚み 5 0 O A形成した。 形成したバッファ層の上にトリメチルガリウムを主原料 としさらに S i H4ガスをドーピング成分用原料として用い基板温度を 1 0 0 0 °Cとした以外 は上記と同じ条件の MO CVD法によりコンタクト層及び単一量子井戸の障壁層となる S iド 一ビングのェピタキシャル成長 G a N薄膜を厚み 5 m形成した。 その上にトリメチルガリゥ ム及び卜リメチルインジウムを主原料としド一ピング成分を用いず基板温度を 8 0 0 °Cとした 以外は上記と同じ条件の MO CVD法により発光層である単一量子井戸の井戸層となるアンド ープのェピタキシャル成長 I n G a Nの 2成分混合組成薄膜を厚み 3 0 A形成した。 なお発光 層となる I n G a N薄膜の組成は I n 0. 06 G a 0. 94N、 I η 0· 20 G a 0. 80N、 I n 0. 45 G a。 5 5 Nの 3種類のものを作製した。 その上にトリメチルガリゥム及びトリメチルアルミニウムを 主原料としさらにビス一シクロペンタジェニリレマグネシウム (M g C p 2) をドーピング成分用
原料に用い基板温度を 1 0 5 0 °Cとした以外は上記と同じ条件の MO C VD法により単一量子 井戸の障壁層となる Mgドーピングのェピタキシャル成長 A 1 0. 2 0 G a 0. 8 0N糸!^の薄膜を厚 み 0 . 1 5 m形成した。 その上にトリメチルガリウムを主原料としさらにビス一シクロペン 夕ジェニルマグネシウム (M g C p 2) をドーピング成分用原料に用い基 «Sを 1 0 0 0 °Cと した以外は上記と同じ条件の MO CVD法によりコンタクト層となる M gドーピングのェピ夕 キシャル成長 G a N薄膜を厚み 0. 5 形成した。 その後薄膜が形成された基板を反応容器 から取り出し N2中 7 0 0 °Cで加熱を行った。次に、 このようにして作製した M gドープ P型 G a N薄膜層の上に所定の形状のマスクを形成し、 上記 S iド一ビングの G a N薄膜層が露出す るまでエッチングを行って該 S iドーピングの G a N薄膜層に T i /A 1の金属 2層で電極を 作製した。 また最上層に形成されている Mgドーピング G a N薄膜層には N i /Auの金属 2 層で電極を作製した。 その後薄膜が形成された基板を外形 I mmX 1 mmの大きさのチップに 切断して単一量子井戸構造の発光ダイォードを作製した。 作製した発光ダイォ一ドのうち薄膜 層を形成していない基板を用いたものは図 4 2に例示するような構成のものである。 また、 薄 膜層を 1層だけ形成した基板を用いたものは図 4 3に例示するような構成のものである。 また、 薄膜層を 2層形成した基板を用いたものは図 4 4に例示するような構成のものである。 また電 極は図 4 5に例示するような配置で形成してあり、 実施例 3 4において窒化アルミニウムを主 成分とする焼結体からなる基板を用いて作製した発光ダイォ一ドと同様のものである。 なお、 実験 N o . 1 4 9 3及び実験 N o . 1 4 9 5で作製した発光^? ttS板として導電性を有する 酸化亜鉛を主成分とする焼結体を用い、 基板にあらかじめ形成される薄膜も S iドーピングの 導電性を有する G a N薄膜を用いた。 実験 N o . 1 4 9 3及び実験 N o . 1 4 9 5において作 製した発光ダイオードの構成は図 5 0に示すようなものであり、 上記のようなエッチングによ る電極形成を行わず電極は各酸化亜鉛を主成分とする焼結体に T i /P t ZAuの金属薄膜 3 層で直接形成することで発光素子の上下に電極を配置した形態の単一 井戸構造の発光ダイ ォードである。 この上下に電極を配置した形態の発光ダイォードチップの大きさも外形 1 mm X I mmである。
次に作製した発光ダイオードのうち発光層となる I n G a N薄膜の組成が I n 0. 20 G a 0. 8 0 Nのものを用いて直流電位を印加し発光を試みた。 その結果作製したいずれの発光ダイォ一ド も電圧 3 . 5ボルト〜 3 . 8ポルトを印加することで中心波長 4 5 0 nmの発光が得られた。 次に上記発光層を有するすべての単一量子井戸構造の発光ダイォードについて該ダイォードを 駆動させるために入力される動作電流とそのとき発光素子から放出される発光出力とを測定し 発光効率を算定した。 その結果を表 5 1に示した。 なお、 表 5 1の動作電流は動作電圧 3. 6 ポルトで発光ダイオードを駆動させたときのものである。 その結果、 サファイア基板を用いて 作製した単一量子井戸構造の発光ダイォードの場合発光効率は実施例 3 4で示すように 6 . Ί %〜Ί . 4 %の範囲であったが、、 本発明による炭化珪素、 窒化珪素、 酸化亜鉛、 酸化べリリ ゥム、 酸化アルミニウム、 酸化ジルコニウム、 酸化マグネシウム、 アルミン酸マグネシウム、 酸化ィットリゥムそれぞれを主成分とする各焼結体からなる基板を用いて作製した発光ダイォ ードはすべて発光効率 8 %以上でありサファイア基板を用いて作製されたものより高かった。 実施例 3 4の表 5 0に示すようにサファイア基板の光腿率は 9 0 %以上であり非常に高い。 それに対して炭化珪素、 窒化珪素、 酸化 «、 酸化ベリリウム、 酸化アルミニウム、 酸化ジル コニゥム、 酸化マグネシウム、 ァリレミン酸マグネシウム、 酸化イットリウムそれぞれを主成分 とする各焼結体からなる基板は ¾¾¾率を有しないかあるいは ¾¾ 率が 1 0 %以下のもので あっても該炭化珪素、 窒化珪素、 酸化亜鉛、 酸化ベリリウム、 酸化アルミニウム、 酸化ジルコ 二ゥム、 酸化マグネシウム、 アルミン酸マグネシウムそれぞれを主成分とする焼結体からなる 基板を用いて作製される発光ダイォードの発光効率は 8 %以上でありサファイア基板を用いて
作製されるものよりよりも大きかつた。
また、本発明による酸化亜鉛を主成分とする焼結体からなる基板にあらかじめ窒化ガリウム、 窒化アルミニウム薄膜を形成せずそのまま用いて作製した発光ダイォードでも発光効率 8 %以 上であった。 さらに窒化ガリゥムあるいは窒化アルミニウムを少なくとも 1層以上形成した基 板を用いることで作製した発光ダイオードの発光効率は向上した。また、炭化珪素、窒化珪素、 酸化亜鉛、 酸化ベリリウム、 酸化アルミニウム、 酸化ジルコニウム、 酸化マグネシウム、 アル ミン酸マグネシウム、 酸化イットリウムそれぞれを主成分とする焼結体からなる基板に薄膜 1 層だけ形成した基板より、 上記同じ炭化珪素、 窒化珪素、 酸化亜鉛、 酸化ベリリウム、 酸化ァ ルミ二ゥム、 酸化ジルコニウム、 酸化マグネシウム、 アルミン酸マグネシウムそれぞれを主成 分とする焼結体からなる基板にあらかじめ窒化ガリウムあるいは窒化アルミニウムを主成分と し無定形、 多結晶、 配向性多結晶、 単結晶のうちから選ばれた少なくともいずれかの結晶状態 の薄膜を形成し、 その上にさらに窒化ガリウムあるいは窒化アルミニウムを主成分とする単結 晶薄膜を形成した薄膜 2層構成の基板を用いることで、 該基板に形成される発光素子の発光効 率はより向上することカ權認された。
本実施例において、 発光ダイォード作製に用いた酸化亜鉛を主成分とする焼結体中の酸化亜 鉛成分の含有量は 5 5. 0モル%以上であり、 該焼結体からなる基板を用いて作製された発光 ダイオードの発光効率は 8 %以上であることが確認された。 また、 発光ダイオード作製に用い た酸化ベリリウムを主成分とする焼結体中の酸化ベリリウム成分の含有量は 6 5. 0モル%以 上であり、 該焼結体からなる基板を用いて作製された発光ダイォードの発光効率は 8 %以上で あることが ϋ認された。 また、 発光ダイオード作製に用いた酸化アルミニウムを主成分とする 焼結体中の酸化アルミニウム成分の含有量は 5 5. 0モル%以上であり、 該焼結体からなる基 板を用いて作製された発光ダイォードの発光効率は 8 %以上であることが確認された。
本実施例において、 本発明による炭化珪素、 窒化珪素、 酸化疆、 酸化ベリリウム、 酸化アル ミニゥム、 酸化ジルコニウム、 酸化マグネシウム、 アルミン酸マグネシウム、 酸化イットリウ ムそれぞれを主成分とする 結体からなる基板の 過率が 1 %より小さいか実質的に光透過 性を有しないもの、 あるいは光透過率が 1 %以上のものを基板として用いても発光効率 8 %以 上の発光素子を作製できた。 また、 上記基板の光透過率が大きいものほど該基板の上に作製さ れる発光素子の発光効率は向上することが 認された。 すなわち、 炭化珪素、 窒化珪素、 酸化 亜鉛、 酸化ベリリウム、 酸化アルミニウム、 酸化ジルコニウム、 酸化マグネシウム、 アルミン 酸マグネシウム、 酸化イットリウムを主成分とする各焼結体において光透過率が 1 0 %以上の ものを基板として用いたときその上に作製される発光素子の発光効率は 1 0 %以上のものが得 られることが it認された。 また、 炭化珪素、 窒化珪素、 酸化亜鉛、 酸化ベリリウム、 酸化アル ミニゥム、 酸化ジルコニウム、 酸化マグネシウム、 アルミン酸マグネシウム、 酸化イットリウ ムを主成分とする各焼結体において光透過率 2 0 %以上のものを基板として用いたときその上 に作製される発光素子の発光効率は 1 2 %以上のものが得られることが萑認された。 また、 炭 化珪素、 窒化珪素、 酸化亜鉛、 酸化ベリリウム、 酸化アルミニウム、 酸化ジルコニウム、 酸化 マグネシウム、 アルミン酸マグネシウム、 酸化イットリウムを主成分とする各焼結体において 光透過率 3 0 %以上のものを基板として用いたときその上に作製される発光素子の発光効率は 1 5 %以上のものが得られることが1認された。 また、 炭化珪素、 窒化珪素、 酸化亜鉛、 酸化 ベリリウム、 酸化アルミニウム、 酸化ジルコニウム、 酸化マグネシウム、 アルミン酸マグネシ ゥム、 酸化ィットリゥムを主成分とする各焼結体において光 率 4 0 %以上のものを基板と して用いたときその上に作製される発光素子の発光効率は 2 0 %以上のものが得られることが 確認された。 また、 炭化珪素、 窒化珪素、 酸化亜鉛、 酸化ベリリウム、 酸化アルミニウム、 酸 化ジルコニウム、 酸化マグネシウム、 アルミン酸マグネシウム、 酸化イットリウムを主成分と
する各焼結体において光 ¾i 率 5 0 %以上のものを基板として用いたときその上に作製される 発光 の発光効率は 2 5 %以上のものが得られることが 認された。 ¾S過率が 6 0 %以上 の¾¾ 性を有する炭化珪素、 窒化珪素、 酸化亜鉛、 酸化ベリリウム、 酸化アルミニウム、 酸 化ジルコニウム、 酸化マグネシウム、 アルミン酸マグネシウム、 酸化イットリウムを主成分と する各焼結体を基板として用いたときその上に作製される発光素子の発光効率は 3 0 %以上の ものが得られることが1認された。 また、 本実施例において 率 8 4 %の酸化亜鉛を主成 分とする焼結体からなる基板を用いたときその上には本実施例における最大の発光効率 5 5 % を有する発光素子が作製された。 また、 本実施例において光 ¾1率 8 1 %の酸化ベリリウムを 主成分とする焼結体からなる基板を用いたときその上には発光効率 5 2 %を有する発光素子が 作製された。 また、 本実施例において光 ¾ 率 8 2 %の酸化アルミニウムを主成分とする焼結 体からなる基板を用いたときその上には発光効率 5 1 %を有する発光素子が作製された。 また、 本実施例において光翻率 5 9 %の酸化ジルコニウムを主成分とする焼結体からなる基板を用 いたときその上には発光効率 2 7 %を有する発光素子が作製された。 また、 本実施例において 光 ¾31率 8 3 %の酸化マグネシウムを主成分とする焼結体からなる基板を用いたときその上に は発光効率 5 1 %を有する発光軒が作製された。 また、 本実施例において)1^率 8 1 %の アルミン酸マグネシウムを主成分とする焼結体からなる基板を用いたときその上には発光効率 5 0 %を有する発光^?が作製された。 また、 本実施例において 過率 8 3 %の酸化イット リゥムを主成分とする焼結体からなる基板を用いたときその上には発光効率 5 1 %を有する発 光素子が作製された。
また、 導電性を有する酸化亜鉛を主成分とする焼結体を用いて作製した上下に電極を配した 形態の発光ダイォードであっても発光効率が特に低下するような傾向は見られず、 発光ダイォ —ドとして十分使用できることが歸忍された。
なお、 別に本発明による炭化珪素、 窒化珪素、 酸化亜鉛、 酸化ベリリウム、 酸化アルミニゥ ム、 酸化ジルコニウム、 酸化マグネシウム、 アルミン酸マグネシウムを主成分とする各焼結体 からなる基板を用いて発光層となる I n G a N膜の組成だけを I n。 2 0 G a。 80Nから I n。 06 G a 0. 94N、及び I n 0. 45 G a 0. 55Nに代えて単一 井戸構造の発光ダイオードを作製し たが、 中心発光波長がそれぞれ 3 9 0 nm、 及び 5 2 0 n mと変化した以外本実施例の最初に 作製した発光層の組成が I n 0. 20G a 0. 80Nの発光ダイオードと同様すベてのものが発光効率 8 %以上であった。
また用意した上記の炭化珪素、 窒化珪素、 酸化亜鉛、 酸化ベリリウム、 酸化アルミニウム、 酸化ジルコニウム、 酸化マグネシウム、 アルミン酸マグネシウム、 酸化イットリウムを主成分 とする各焼結体を基板として用い、 別 施例 3 4と同様のダブルへテロ構造の発光ダイォー ドの作製を行った。 該発光ダイオードの作製に際して «¾ 5 1に示すすべての基板を用いた。 発光ダイオード作製に用いた基板としては、炭化珪素、窒化珪素、酸化 ¾、酸化ベリリウム、 酸化アルミニウム、 酸化ジルコニウム、 酸化マグネシウム、 アルミン酸マグネシウム、 酸化ィ ットリウムを主成分とする各焼結体に、 表 5 1に示すような薄膜を形成した薄膜基板としたも のである。 その結果、 作製したすべてのダブルへテロ構造の発光ダイオードにおいて発光効率 は 8 %以上であり、 実施例 3 においてサフアイァを基板として作製したダブルへテロ構造の 発光ダイォ一ドの発光効率が 5. 4 %であったのでそれよりも明らかに優れていた。
実施例 3 6
本実施例は窒化ガリウムを主成分とする焼結体についてその特性を調べた例を示す。
最初に窒化ガリゥムの原料粉末を次の方法により用意した。
1 ) まず高純度化学石 if^所製の純度 4 Nの金属ガリウムを用意した。 加熱部と反応部を有す る石英管製の反応容器の加熱部に該金属ガリゥムをアルミナ容器に入れて置き、 水素 5 \m%
を含むアルゴンガス気流中 1200^で加熱して金属ガリウムを気化させてアルゴンガス気流 で反応部に導き、反応部に窒素ガスを導入して気化した金属ガリウム 1100°Cで反応させた。 その結果 の低い反応容器の出口付近に灰白色粉末の析出が認められ、 X線回折の結果窒化 ガリウムであることカ擁認された。 粉末の平均 ¾!圣は 14 mであった。 なお、 反応容器は 1 本の石英管であり加熱部と反応部とは直接つながっており、 容器の入り口にはァリレゴンガスな どのキャリアガス導入口を設け、 容器の反応部には窒素ガス、 アンモニアガスなどの反応ガス の導入口が設けてある。 容器の加熱部と反応部は外部ヒータ一で加熱される。 容器のガス出入 り口部分には特に加熱用のヒ一夕一は設けず自然 されされている。 得られた粉末をポール ミルで粉砕し平均樹圣 1. 7 の窒化ガリウム粉末を作製した。 また、 この窒化ガリウム粉 末には酸素が 1. 1重量%含まれていた。 かくして金属の直接窒化法による窒化ガリゥム粉末 を作製した。
2) つぎに高 化 ^^所製の «4Νの酸化ガリウム (Ga203) 粉末と市販のカーボ ンブラック粉末を用意し、 酸化ガリウム粉末 300グラムとカーボンブラック粉末 90グラム とをポールミルで草試混合した。 この混 ^^末をカーボン容器に入れカーボン製の加熱炉にて 窒素ガス中 1350°Cで 5時間加熱し反応させた。 加謝麦混合粉末を取り出しその後大気中 5 00°Cで 2時間加熱して残留していたカーボンブラックを酸化除去した。 残った粉末を X線回 折で分析したところ明らかに窒化ガリウムのピークだけであることが確認された。 またこの粉 末の平均粒径は 0. 9 mであった。 またこの粉末の酸素含有量は 0. 8重量%であった。 か くして酸化物 法による窒化ガリウム粉末を作製した。
3)次に高,舊化^ f¾所製の績 5 Nの三塩化ガリウム (GaC l3) を用意した。 該三塩 化ガリゥムを石英容器中に入れて 90 °Cで加熱して溶融し水素 20体積%を含む窒素ガスでバ プリングして三塩化ガリゥム気体を石英管製の反応容器に導き、 反応容器にアンモニアガスを 導入して気化した三塩化ガリウムと 1050°Cで反応させた。 その結果? の低い反応容器の 出口付近に灰白色粉末の析出が認められ、 Χί泉回折の結果窒化ガリウムであること力 歸忍され た。 粉末の平均粒径は 0. 4〃mであった。 またこの粉末の酸餘有量は 1. 3重量%であつ た。 かくして化学輸送法による窒化ガリウム粉末を作製した。
次に希土 ¾素成分として信越化学工業株式会社製の纖 99. 99%以上の Y203粉末、 Er203粉末、 Yb2〇3粉末、 Dy2〇3粉末、 Ho203粉末を用意し、 アルカリ土類金属成分 として CaC〇3粉末、 珪素成分として S i3N4粉末、 アルミニウム成分として A 1 N粉末、遷 移金属成分として Mo03粉末を用意し、 これらの粉末を本実施例で作製した窒化ガリウム原料 粉末に Ml表 52に示した量を加えてエタノールを溶媒にしてポールミルで 24時間湿式混合 後、 乾燥してエタノールを揮散させた。 これら乾燥後の混合粉末にパラフィンワックスを 5重 量%加え成形用粉末を作製し、款粉末を圧力 50 OKgZcm2で一軸プレス成形し直径 32m mX厚み 1. 5 mmの円盤状成形体を得た。 なお、 成形用粉末及び成形体として上記各添加成 分を加えず本実施例で作製した 3種類の窒化ガリウム原料粉末だけをそのまま使用したものに ついても作製した。 これら成形体を 300°Cで減圧脱脂後窒素雰囲気中 1450°Cで 2時間常 圧焼成し窒化ガリゥムを主成分とする焼結体を得た。 焼成後の焼結体はいずれの原料を用いた ものも 99%以上の相対密度に緻密化していた。 得られたこれらの焼結体表面をコロイド状シ リカからなる研 を用いて鏡面研磨した後アセトンで超音波洗浄し基板を作製した。 鏡面研 磨後の焼結体の平均表面粗さ は 17nm〜24n mの範囲であつた。 得られた焼結体の室 温における抵抗率、 波長 605 nmの光に対する光透過性を測定した。
室温における抵抗率は表 52に示すように作製したすべての窒化ガリゥムを主成分とする焼 結体で 1 X 108Ω · cm以下であった。 さらに珪素を含む窒化ガリウムを主成分とする焼結体 が 1Χ104Ω · cm以下の導電性を有することが 認された。 また、 珪素を元素藤で 0. 0
0 0 0 1モル%〜 1 0. 0モル%の範囲含む窒化ガリゥムを主成分とする焼結体では室温にお ける抵抗率が少なくとも 1 X 1 0 3Ω · cm以下のものが得られ易い。 また、 珪素を元素 で 0. 0 0 0 0 1モル%〜 7. 0モル%の範囲含む窒化ガリゥムを主成分とする焼結体では室温 における抵抗率が少なくとも 1 X 1 0 · cm以下のものが得られた。 また、 珪素を元素娜 で 0. 0 0 0 0 1モル%~ 5. 0モル%の範囲含む窒化ガリゥムを主成分とする焼結体では室 温における抵抗率が少なくとも 1 X 1 00Ω · cm以下のものが得られた。 また、珪素を元素換 算で 0. 0 0 0 0 1モル%〜 3. 0モル%の範囲で含む窒化ガリゥムを主成分とする焼結体で は室温における抵抗率が少なくとも 1 X 1 Ο ^ Ω · cm以下のものが得られた。 さらに作製し た窒化ガリウムを主成分とする焼結体において最高で室温における抵抗率が 1 . 4 X 1 0—3 Ω · cmの高い導電性を有するものが得られた。
また、 作製した殆どの窒化ガリゥムを主成分とする焼結体で ¾¾ 生を有するものが得られ た。 その中で添加物を含まず金属元素として実質的にガリゥム成分だけからなる窒化ガリゥム を主成分とする焼結体であっても 過性を有するものが得られた。 添加物としてアルカリ土 類金属及び希土類 素成分は窒化ガリゥムを主成分とする焼結体の光 ¾1性に有効に働き、 ァ ルカリ土類金属及び希土類 素のうちから選ばれた少なくとも 1種以上の成分を酸化物換算で 3 0. 0モル%以下含む窒化ガリウムを主成分とする焼結体では 率 1 0 %以上のものが 作製し得る。 また、 上記アルカリ土類金属成分及び希土類 素成分のうちから選ばれた少なく とも 1種以上の成分を酸化物換算で 2 0. 0モル%以下含む窒化ガリウムを主成分とする焼結 体はさらに 性が向上し易くなり¾¾§率 2 0 %以上のものが得られた。 また、 アルカリ 土類金属成分及 土類 素成分のうちから選ばれた少なくとも 1種以上の成分を酸化物換算 で 1 5. 0モル%以下含む窒化ガリゥムを主成分とする焼結体では光透過率 3 0 %以上のもの が得られた。 また、 アルカリ土類金属成分及び希土 ϋ¾素成分のうちから選ばれた少なくとも 1種以上の成分を酸化物換算で 1 0. 0モル%以下含む窒化ガリゥムを主成分とする焼結体で は½¾¾率 4 0 %以上のものが得られた。 また、 アルカリ土類金属成分及び希土^ ¾素成分の うちから選ばれた少なくとも 1種以上の成分を酸化物^ で 8. 0モル%以下含む窒化ガリウ ムを主成分とする焼結体では光逐過率 5 0 %以上のものが得られた。 また、 アルカリ土類金属 成分及び希土類 素成分のうちから選ばれた少なくとも 1種以上の成分を酸化物換算で 6. 0 モル%以下含む窒化ガリゥムを主成分とする焼結体では光透過率 6 0 %以上のものが得られる ことが ¾認、された。 本実施例において酸化イットリウムを Υ2〇3 で 0. 0 1モル%含む窒 化ガリウムを主成分とする焼結体は光 ¾1率 8 6 %と最大のものが得られた。 アルカリ土類金 属成分及び希土 素成分が同時に含まれる窒化ガリウムを主成分とする焼結体であってもそ れぞれ単独で含まれるものと同様良好な光透過性を有することが確認された。
また、 モリブデン成分を有する窒化ガリウムを主成分とする焼結体では舰過率 1 0 %以上 のものが得られた。 また、 窒化珪素を含有する窒化ガリウムを主成分とする焼結体でも光透過 率 1 0 %以上のものが得られた。 また、 窒化アルミニウムを含有する窒化ガリウムを主成分と する焼結体でも光 ¾i率 1 0 %以上のものが得られた。
本実施例において作製した窒化珪素を珪素 i ^で 0. 0 1モル%及び 化ィットリゥムを Y2
03騰で 0. 0 1モル%同時に含む窒化ガリウムを主成分とする焼結体は ½¾1率 8 2 %室温 における抵抗率 1. 7 X 1 0— 2 Ω · c mと高い;)16¾1率と同時に髙ぃ導電性を有するものもの であった。また、窒化珪素を珪素 で 0. 0 1モル%及び 化カルシウムを C a O で 0. 2モル及び%酸化ィットリウムを Y 2 O 3換算で 0. 2モル%計 3種類の成分を同時に含む窒化 ガリウムを主成分とする焼結体も光 ¾ 率 7 6 %室温における抵抗率 2. 4 X 1 0— 2 Ω■ c m と高い光透過率と同時に高い導電性を有するものものであった。
その後作製した基板にスパッタリング法及び MOCVD法を用いて実施例 2 5と同様の条件
で窒化ガリウム、 窒化インジウム、 窒化アルミニウムのうちから選ばれた少なくとも 1種以上 を主成分とする単結晶、 無定形、 多結晶、 配向性多結晶のうちから選ばれた少なくともいずれ かの結晶状態を有する薄膜を厚み 3 zm形成した。 その結果明らかに本実施例で作製した窒化 ガリウムを主成分とする焼結体には単結晶薄膜が直接形成できることが 認された。 またその 他無定形、 多結晶、 配向性多結晶のうちから選ばれた少なくともいずれかの結晶状態を有する 薄膜も形成し得ることが確認された。 窒化ガリウムを主成分とする配向性多結晶薄膜の結晶性 は窒化アルミニウムを主成分とするものよりも優れた傾向を有し易い現象が見られた。 次に、 このような各種結晶状態の薄膜を形成した基板の中から β選択してさらにその上に厚み 3 n mで窒化ガリウム、 窒化インジウム、 窒化アルミニウムのうちから選ばれた少なくとも 1種以 上を主成分とする単結晶薄膜の形成を試みた。 その結果明らかにあらかじめ窒化ガリウム、 窒 化インジウム、 窒化アルミニウムのうちから選ばれた少なくとも 1種以上を主成分とする単結 晶、 無定形、 多結晶、 配向性多結晶のうちから選ばれた少なくともいずれかの結晶状態を有す る薄膜を形成した窒化ガリゥムを主成分とする焼結体にはより結晶性の優れた単結晶薄膜が形 成できることが確認された。 これらの結果を表 5 2に示した。 なお、 表 5 2に示した無定形、 多結晶、 配向性多結晶のうちから選ばれた少なくともいずれかの結晶状態を有する薄膜はスパ ッタリング法により形成したものであり、 単結晶薄膜は MO CVD法で形成したものである。 スパッ夕リング法による G a N薄膜を形成するに際して用いたスパッ夕リングターゲットは本 実施例で作製した酸化物 法による原料粉末を用いて添加物を用いずに作製した窒化ガリウ ムを主成分とする焼結体を用いて作製したものである。 スパッタリング法による G a N薄膜の 作製条件としてはスパッタリング夕一ゲッ卜として上記窒化ガリゥムを主成分とする焼結体を 用いた以外は実施例 2 5と同様に行った。 表 5 2において示した本実施例で作製した窒化ガリ ゥムを主成分とする焼結体にはミラー指数 ( 0 0 2) の格子面の X線回折ロッキングカーブの 半値幅が 3 0 0秒以下の結晶性に優れた窒化ガリウム、 窒化インジウム、 窒化アルミニウムの うちから選ばれた少なくとも 1種以上を主成分とする単結晶薄膜が直接形成できることが歸忍 された。 また、 アル力リ土類金属成分及び希土 |g¾素成分のうちから選ばれた少なくとも 1種 以上の成分を酸化物 で 3 0. 0モル%以下含むものを用いたときその上にはミラ一指数(0 0 2) の格子面の X線回折ロッキングカーブの半値幅が 2 0 0秒以下の結晶性に優れた窒化ガ リウム、 窒化インジウム、 窒化アルミニウムのうちから選ばれた少なくとも 1種以上を主成分 とする単結晶薄膜が直接形成できる。 さらに、 アルカリ土類金属成分及び希土 ¾素成分のう ちから選ばれた少なくとも 1種以上の成分を酸化物換算で 2 0. 0モル%以下含窒化ガリウム を主成分とする焼結体を用いたときその上にはミラー指数 (0 0 2) の格子面の X線回折ロッ キングカーブの半値幅が 1 5 0秒以下の結晶性に優れた単結晶薄膜が直接形成できる。 また、 アルカリ土類金属成分及び希土航素成分のうちから選ばれた少なくとも 1種以上の成分を酸 化物 で 1 0. 0モル%以下含窒化ガリウムを主成分とする焼結体を用いたときその上には ミラ一指数 ( 0 0 2) の格子面の X線回折ロッキングカーブの半値幅が 1 3 0秒以下の結晶性 に優れた単結晶薄膜が 接形成できることが 認された。 また、 アルカリ土類金属成分及び希 土類 素成分が同時に含まれる窒化ガリウムを主成分とする焼結体であってもそれぞれ単独で 含まれるものと同様その上に形成される単結晶薄膜の結晶性は良好なものであることか«認さ れた。
また、 モリブデン成分を有する窒化ガリゥムを主成分とする焼結体ではその上にミラー指数 ( 0 0 2) の格子面の X線回折ロッキングカーブの半値幅が 3 0 0秒以下の結晶性に優れた単 結晶薄膜カ埴接形成できた。 また、 窒化珪素を含有する窒化ガリウムを主成分とする焼結体で もその上にミラー指数 (0 0 2 ) の格子面の X線回折ロッキングカーブの半値幅が 3 0 0秒以 下の結晶性に優れた単結晶薄膜が直接形成できた。 また、 窒化アルミニウムを含有する窒化ガ
リウムを主成分とする焼結体でもその上にミラー指数 (0 0 2 ) の格子面の X線回折ロッキン グカーブの半値幅が 3 0 0秒以下の結晶性に優れた単結晶薄膜が直接形成できた。
さらに同じ窒化ガリゥムを主成分とする焼結体を用いあらかじめ窒化ガリゥム、 窒化ィンジ ゥム、 窒化アルミニウムのうちから選ばれた少なくとも 1種以上を主成分とする単結晶、 無定 形、 多結晶、 配向性多結晶薄膜を形成したものの上に窒化ガリウム、 窒化インジウム、 窒化ァ ルミニゥムのうちから選ばれた少なくとも 1種以上を主成分とする単結晶薄膜を形成したとき、 該単結晶薄膜の結晶性は直接窒化ガリゥムを主成分とする焼結体に形成したものより優れたも のが得られた。
また本実施例において、 窒化ガリウムを主成分とする焼結体に形成した窒化ガリウム、 窒化 ィンジゥム、 窒化アルミニウムのうちから選ばれた少なくとも 1種以上を主成分とする単結晶 薄膜の結晶性は纏化ガリウムを主成分とする焼結体の光透過性が向上すればそれに伴つて向 上し易いことが確認された。
その他、 表 5 2には示してないが実施例 2 5と同様無定形、 多結晶、 配向性多結晶のうちか ら選ばれた少なくともいずれかの結晶状態を有する窒化ガリゥムを主成分とする薄膜が M〇 C VD法を用いても好適に窒化ガリゥムを主成分とする焼結体に形成し得ることも確認された。 MO CVD法を用いて形成した配向性多結晶薄膜の結晶性はミラ一指数 ( 0 0 2 ) の格子面の X線回折ロッキングカーブの半値幅が 4 0 0 0秒〜 6 0 0 0秒でありスパッタリング法を用い て形成したものより優れていた。
本実施例において表 5 2に記載した構成の薄膜、 その他本実施例で作製した薄膜すベての外 観を調べたがあらかじめ基板に形成した薄膜及びその上にさらに形成した薄膜いずれもクラッ クやひび割れなどの欠陥は見られない。 また、 粘着テープによる剥離テストを行ったがいずれ の薄膜も窒化ガリウムを主成分とする焼結体からなる基板との間及び,膜同志の間で剥離は見 られなかった。 また、 基板表面の薄膜に T i ZP t ZAuの薄膜導電性材料を形成して金属リ ―ドをはんだ付けし垂直引張り強度を調べたがすべて 2 K g/mm2以上であり窒化ガリゥム を主成分とする焼結体からなる基板と該基板にあらかじめ形成した薄膜、 及び該薄膜とさらに その上に形成した単結晶薄膜とは強固に接合していることが確認された。
実施例 3 7
本実施例は窒化ガリゥムを主成分とする焼結体を用レて作製した発光素子の発光効率に及ぼ す^化ガリゥムを主成分とする焼結体の^ 1性の効果及び該窒化ガリゥムを主成分とする 焼結体に形成する薄膜の効果に付いて調べた例を示す。
実施例 3 6で作製した窒化ガリウムを主成分とする焼結体のうちから 選択しこれらの焼 結体にスパッタリング法及び MO C VD法を用いて実施例 3 6と同様の方法で窒化ガリゥム、 窒化インジウム、 窒化アルミニウムのうちから選ばれた少なくとも 1種以上を主成分とする単 結晶、 無定形、 多結晶、 配向性多結晶の結晶状態を有する薄膜を厚み 3 ^ mで形成し、 さらに その上に ¾M〇C VD法により窒化ガリゥム、 窒化アルミニウムのうちから選ばれた少なく とも 1種以上を主成分とする単結晶を厚み 3 m形成して発光^?用作製に供する窒化ガリウ ムを主成分とする焼結体からなる基板を作製した。 すなわち、 上記窒化ガリウムあるいは窒化 アルミニウムのうちから選ばれたいずれかを主成分とする無定形、 多結晶、 配向性多結晶のう ちから選ばれた少なくともいずれかの結晶状態を有する薄膜の形成はすべてスパッタリング法 により行ない、 G a N薄膜を形成するときのスパッタリングターゲットとして実施例 3 6で作 製した窒化ガリゥムを主成分とする焼結体を用いた。 なお上記窒化ガリゥムを主成分とする焼 結体に薄膜を形成せずそのまま基板として用いたものもある。 また 2層目の単結晶薄膜を形成 していないものもある。
このようにして作製した基板を用いて実施例 3 4及び実施例 3 5と同様の方法で窒化ガリウ
ム、 窒化インジウム、 窒化アルミニウムのうちから選ばれた少なくとも 1種以上を主成分とす る薄膜からなる少なくとも N型半導体層及び発光層及び P型半導体層を含む積層体を形成し発 光層として単一量子井戸構造を有する発光素子を作製した。 次に得られた各発光素子に実施例 3 4及び実施例 3 5と同様に 3. 5ボルト〜 3. 8ポルトの電位を印加し発光効率を調べた。 これらの結果を表 5 3に示した。 なお、 表 5 3に示されている動作電流は動作電圧 3. 6ポル 卜で発光素子を駆動させたときのものである。
その結果明らかに窒化ガリウムを主成分とする焼結体を用いて作製した発光素子の発光効率 はサファイア基板を用いて作製したものより優れていた。 また、 本窒化ガリウムを主成分とす る焼結体を用いて作製した発光素子の発光効率は該窒化ガリウムを主成分とする焼結体の光透 過性が向上するにつれて増大することが1認された。 また、 窒化ガリウムを主成分とする焼結 体にあらかじめ窒化ガリウム、 窒化インジウム、 窒化アルミニウム薄膜を形成せずそのまま用 いて作製した発光素子でも発光効率 1 0 %以上であった。 さらに窒化ガリウム、 窒化インジゥ ムあるいは窒化アルミニウムを少なくとも 1層以上形成した窒化ガリゥムを主成分とする焼結 体を用いることで作製した発光素子の発光効率は向上した。 また薄膜 1層だけ形成したものよ り窒化ガリゥムを主成分とする焼結体にあらかじめ窒化ガリゥム、 窒化ィンジゥムあるいは窒 化アルミニウムを主成分とし無定形、 多結晶、 配向性多結晶、 単結晶のうちから選ばれた少な くともいずれかの結晶状態の薄膜を形成し、 その上にさらに窒化ガリゥムあるいは窒化アルミ 二ゥムを主成分とする単結晶薄膜を形成した薄膜 2層構成の基板を用いることで、 該基板に形 成される発光素子の発光効率はさらに向上することが 11認された。 また、 窒化ガリウム、 窒化 インジウム、 窒化アルミニウムのうちから選ばれた少なくとも 1種以上を主成分とする薄膜を 形成した窒化ガリゥムを主成分とする焼結体を用いて作製した発光素子において、 望化ガリゥ ムを主成分とする薄膜を形成した窒化ガリウムを主成分とする焼結体を用いて作製した発光素 子の発光効率の方が窒化アルミニウムを主成分とする薄膜を形成した窒化ガリウムを主成分と する焼結体を用いて作製した発光素子の発光効率よりも優れている傾向があることが歸忍され た。
実施例 3 8
本実施例はセラミック材料を主成分とする焼結体に窒化ガリゥムを主成分とする薄膜を形成 したものを基板として用いて作製した発光素子の発光効率に及ぼす効果に付いて調べた例を示 す。
実施例 3 4及び実施例 3 5で用いた窒化アルミニウム、 炭化珪素、 窒化珪素、 酸化亜鉛、 酸 化ベリリウム、 酸化アルミニウム、 酸化ジルコニウム、 酸化マグネシウム、 アルミン酸マグネ シゥム、 酸化イットリウムそれぞれを主成分とする焼結体を発光素子作製用の基板として誠 用意した。 これらの焼結体の表面状態としては実施例 3 4及び実施例 3 5で用いたものと同じ 鏡面研磨されたものをそのまま用いた。 このようにして用意した各焼結体に実施例 3 4、 実施 例 3 5及び実施例 3 7と同様の方法でスパッタリング法あるいは MO CVD法により窒化ガリ ゥムあるいは窒化アルミニウムのうちから選ばれたいずれかを主成分とする無定形、 多結晶、 配向性多結晶、 単結晶のうちから選ばれた少なくともいずれかの結晶状態を有する薄膜を厚み 3 m形成した。 その後 これら薄膜を形成した焼結体の上からさらに 2層目として実施例 3 4、 3 5及び 3 7で示したものと同じ MO CVD法により窒化ガリウムあるいは窒化アルミ 二ゥムのうちから選ばれたいずれかを主成分とする単結晶薄膜を厚み 3 m形成し発光^?作 製用の基板として用意した。 なお、 上記窒化ガリウムあるいは窒化アルミニウムのうちから選 ばれたいずれかを主成分とする無定形、 多結晶、 配向性多結晶のうちから選ばれた少なくとも いずれかの結晶状態を有する薄膜の形成はすべてスパッ夕リング法により行ない、 G a N薄膜 を形成するときのスパッタリングターゲッ卜として実施例 3 6で作製した窒化ガリウムを主成
分とする焼結体を用いた。 また、 上記焼結体に 2層目の単結晶薄膜を形成していないものもあ る。
このようにして作製した基板を用いて実施例 3 4、 実施例 3 5及び、実施例 3 7と同様の方法 で窒化ガリウム、 窒化インジウム、 窒化アルミニウムのうちから選ばれた少なくとも 1種以上 を主成分とする薄膜からなる少なくとも N型半導体層及び発光層及び P型半導体層を含む積層 体を形成し発光層として単一量子井戸構造を有する発光軒を作製した。 次に得られた各発光 素子に実施例 3 4、 実施例 3 5及び実施例 3 7と同様に 3 . 5ポルト〜 3 . 8ポルトの電位を 印加し発光効率を調べた。 これらの結果を表 5 4及び表 5 5に示した。 表 5 4は窒化アルミ二 ゥムを主成分とする焼結体を用いて作製した発光 についてのものである。 表 5 5はその他 炭化珪素、 窒化珪素、 酸化亜鉛、 酸化ベリリウム、 酸化アルミニウム、 酸化ジルコニウム、 酸 化マグネシウム、 アルミン酸マグネシウム、 酸化イットリウムそれぞれを主成分とする焼結体 についてのものである。 なお、 表 5 4及び表 5 5に示されている動作電流は動作電圧 3 . 6ポ ルトで発光素子を駆動させたときのものである。
その結果、 明らかに実施例 3 4、 実施例 3 5及び本実施例で作製した発光素子のうち窒化ガ リウムあるいは窒化ガリウムを主成分とする薄膜を形成した窒化アルミニウム、 炭化珪素、 窒 化珪素、 酸化亜鉛、 酸化ベリリウム、 酸化アルミニウム、 酸化ジルコニウム、 酸化マグネシゥ ム、 アルミン酸マグネシウム、 酸化イットリウムそれぞれを主成分とする焼結体からなる基板 を用いて作製された発光^?の発光効率は窒化インジウム、 窒化アルミニウムのうちから選ば れた少なくとも 1種以上を主成分とする薄膜を形成した上記各セラミック材料を主成分とする 焼結体からなる基板を用いて作製された発光素子の発光効率と少なくとも同等かよりも優れて いることカ權認された。 すなわち、 例えば窒化ガリウムを主成分とする配向性多結晶薄膜 1層 と単結晶薄膜 1層の合計 2層を形成した光 ¾ 率 5 4 %の窒化アルミ二ゥムを主成分とする焼 結体を用いて作製した発光軒の発光効率は同じ耀過率 5 4 %の窒化アルミニウムを主成分 とする焼結体に窒化アルミ二ゥムを主成分とする配向性多結晶薄膜 1層と単結晶薄膜 1層の合 計 2層を形成したものを用いて作製した発光素子の魏効率に比べて 6 %向上していた。 また、 窒化ガリゥムを主成分とする配向性多結晶薄膜 1層と単結晶薄膜 1層の合計 2層を形成した光 腿率 8 4 %の酸化亜鉛を主成分とする焼結体を用レゝて作製した発光素子の発光効率は同じ光 mmrn 8 4 %の酸化亜鉛を主成分とする焼結体に窒化アルミニゥムを主成分とする配向性多結 晶薄膜 1層と単結晶薄膜 1層の合計 2層を形成したものを用いて作製した発光素子の発光効率 に比べて 1 0 %向上していた。
実施例 3 9
本実施例は発光素子を作製するために用いられる比較的表面粗さの大きいセラミック材料を 主成分とする焼結体を用いて作製した発光素子の発光効率に及ぼす効果に付いて調べた例を示 す。
セラミック材料を主成分とする焼結体としては実施例 3 4、 実施例 3 5、 実施例 3 7及び実 施例 3 8で用いたものと同じ窒化アルミニウム、 炭化珪素、 窒化珪素、 窒化ガリウム、 酸化亜 鉛、 酸化ベリリウム、 酸化アルミニウム、 酸化ジルコニウム、 酸化マグネシウム、 アルミン酸 マグネシウム、 酸化イットリウムそれぞれを主成分とする焼結体を 意した。 これらの焼 結体の表面に iildJin:を施し表面状態が焼き放し (a s— ί i r e ) のもの、 鏡面研磨したも の、 サンドブラスト研磨したもの、 ラップ研磨したもの、 苛性ソーダでエッチングしたもの、 規則的な凹凸を形成したものを用意した。 焼き放し状態の表面を有する焼結体はすべて市販の 粒度 3 mのアルミナ粉末を用いてブラシ掛けにより表面の付着物を取り除いたものである。 鏡面研磨した焼結体は実施例 3 4、 3 5、 3 7及び 3 8で用いたものと同じものを用いた。 サ ンドプラスト研磨は窒化アルミニウム、 酸化亜鉛及び窒化ガリゥムを主成分とする焼結体では
アルミナ研 の ¾g# 6 0 0、 # 1 2 0 0及び # 5 0 0 0の 3種類のものを用い、炭化珪素、 窒化珪素、 酸化ベリリウム、 酸化アルミニウム、 酸化ジルコニウム、 酸化マグネシウム、 アル ミン酸マグネシウム、 酸化イットリウムそれぞれを主成分とする焼結体ではアルミナ研顧 Jの 驢 # 1 2 0 0のものを用い、 その他の条件は実施例 2 9と同様の方法で作製した。 ラッフ 磨した焼結体は髓# 4 0 0の炭化珪素研^を用いその他は実施例 2 9と同様の方法で作製 した。 苛性ソーダでエッチングした焼結体は粒度 # 8 0 0のアルミナ研 jを用いてラップ研 磨したものを 5 N濃度の 9 0 苛性ソーダ水溶液に 1分間浸漬しその後蒸留水で洗浄して作製 した。 規則的な凹凸を形成した焼結体は用意した各焼結体に市販のレジストを塗布後光リソグ ラフィ一により 2 m間隔で 1 /xm幅の窓が直角に規則的に交差した網目状のものを形成し、 S F 6 + 02プラズマでエッチングして幅 1 mで深さ 0. 5 mの規則的な網目状の窪みを形 成 ( 1 mX 1 mの正方形で高さ 0. 5 mの突起を 2 m間隔で規則的に形成) したもの である。 その形態は図 7 3に示すようなものである。 次にこれらの焼結体の平均表面粗さ R a を測定した。 その測定結果を表 5 6に示す。 表 5 6において用いたセラミック材料を主成分と する焼結体の平均表面粗さ R aは 7 9 nm〜 3 2 4 0 nmの範囲にあった。
このようにして用意した各セラミック材料を主成分とする焼結体に実施例 3 4、 3 5、 3 7 及び 3 8と同様に窒化ガリウム、 窒化アルミニウムのうちから選ばれた少なくとも 1種以上を 主成分とする無定形、 配向性多結晶のうちから選ばれた少なくともいずれかの結晶状態を有す る薄膜をスパッタリング法で形成し鏡面研磨して 3 mの厚みとしその上に窒化ガリウム、 窒 化アルミニウムのうちから選ばれた少なくとも 1種以上を主成分とする単結晶薄膜を MO CV D法で厚み 3 m形成し発光素子作製用基板を用意した。 なお、 スパッタリング法で G a N薄 膜を形成するときのスパッ夕リング夕一ゲットとして実施例 3 6で作製した窒化ガリウムを主 成分とする焼結体を用いた。 また、 表 5 6に示すようになお上記各焼結体に薄膜を形成せずそ のまま基板として用いたものもある。 また 2層目の単結晶薄膜を形成せずスパッ夕リング法に よる薄膜 1層だけのものもある。
その後このようにして形成した単結晶薄膜の上に実施例 3 4、 実施例 3 5、 実施例 3 7及び 実施例 3 8と同様の方法で窒化ガリゥム、 窒化インジウム、 窒化アルミニウムのうちから選ば れた少なくとも 1種以上を主成分とする薄膜からなる少なくとも N型半導体層及び発光層及び P型半導体層を含む積層体を形成し発光層として単一量子井戸構造を有する発光素子を作製し た。 次に作製した各発光素子に実施例 3 4、 実施例 3 5、 実施例 3 7及び実施例 3 8と同様に 3. 5ポルト〜 3. 8ポルトの電位を印加し発光効率を調べた。 これらの結果を表 5 6に示し た。 なお、 表 5 6に示されている動作電流は動作電圧 3. 6ポルトで発光素子を駆動させたと きのものである。
その結果表 5 6に示すように、 本実施例において表面粗さが比較的大きいセラミック材料を 主成分とする焼結体を用いて作製した発光軒の発光効率は、 実施例 3 4、 実施例 3 5、 実施 例 3 7あるいは実施例 3 8で作製した同じセラミック材料を主成分とする焼結体であってもそ の表面粗さが小さいものを用いて作製した発光軒に比べて明らかに少なくとも同等かより優 いることが崔認された。 例えば実施例 3 5で作製した表面粗さが小さい光透過率 6 8 %の酸ィ匕 亜鉛を主成分とする焼結体を用いて作製した発光素子に比べて本実施例で作製した同じ ¾S過 率を有し表面粗さを大きくした酸化亜鉛を主成分とする焼結体を用いて作製した発光素子の発 光効率は 2 2 %向上した。 また、 表面粗さが比較的大きいセラミック材料を主成分とする焼結 体のうち光 ¾i 率 8 8 %の窒化アルミニウムを主成分とする焼結体及び 過率 8 6 %の窒化 ガリゥムを主成分とする焼結体を用いて作製した発光素子で発光効率として最大 7 3 %のもの が得られた。 また、 舰過率 8 4 %の酸化亜鉛を主成分とする焼結体、 率 8 3 %の酸ィ匕 マグネシウムを主成分とする焼結体、 光透過率 8 1 %のアルミン酸マグネシウムを主成分とす
る焼結体及び光透過率 8 3 %の酸化ィットリゥムを主成分とする焼結体を用いて作製した発光 素子で最大 7 0 %〜 7 1 %の発光効率を有するものが得られた。 その他、 光 ¾1率 8 1 %の酸 化ベリリウムを主成分とする焼結体を用いて作製した発光素子で最大 6 9 %の発光効率を有す るものが得られた。 また、 ¾¾ϋ率 7 8 %の酸化アルミニウムを主成分とする焼結体を用いて 作製した発光素子で最大 6 6 %の発光効率を有するものが得られた。 また、 ¾¾§率5 9 %の 酸化ジルコニウムを主成分とする焼結体を用いて作製した発光素子で最大 4 %の発光効率を 有するものが得られた。 また、 ½¾ 率 0 %の炭化珪素を主成分とする焼結体及び窒化珪素を 主成分とする焼結体を用いて作製した発光素子でも表面粗さを大きくすることで実施例 3 8で 作製した表面粗さの小さい焼結体を用いて作製した発光素子に比べてそれぞれ; 0. 0 % 及び 1 6. 4 %発光効率が向上することが確認された。
次に、 本実施例で作製した表 5 6に示すすべての各種表面粗さを有するセラミック材料を主 成分とする焼結体に対して MO CVD法により窒化ガリウム、 窒化アルミニウムのうちから選 ばれた少なくとも 1種以上を主成分とする単結晶薄膜を直接形成することを試みた。すなわち、 水素あるいは窒素 +水素のキャリアガス、 及び反応ガスであるアンモニア、 及び主原料である トリメチルガリウムあるいはトリメチルアルミニウムの供給方法以外は実施例 3 4、 実施例 3 5、 実施例 3 7及び実施例 3 8と同様の MO CVD法を用いた。 なお、 実施例 3 4、 実施例 3 5、 実施例 3 7及び実施例 3 8で用いた M〇 C VD法において上記主原料や反応ガスの供給は セラミツク材料を主成分とする焼結体からなる基板に対して特定の方向から供給するという方 法でなく、 反応容器である石英ガラス管の入り口から出口方向へと行ない主原料や反応ガスを 容器全体に広げるという方法であり、 セラミック材料を主成分とする焼結体からなる基板は容 器の内部に置かれている。 一方本実施例において、 窒化ガリウム、 窒化アルミニウムのうちか ら選ばれた少なくとも 1種以上を主成分とする単結晶薄膜を本実施例で作製した表面粗さの大 きいセラミック材料を主成分とする焼結体に対して直接形成することを試みるに際して、 上記 主原料や反応ガスをセラミック材料を主成分とする焼結体からなる基板に対して特定の方向か ら供給するという方法を用いた。 すなわち、 石英ガラス製の反応容器内に置かれた窒化アルミ 二ゥムを主成分とする焼結体、 炭化珪素を主成分とする焼結体、 窒化珪素を主成分とする焼結 体、 窒化ガリウムを主成分とする焼結体、 酸化亜鉛を主成分とする焼結体、 酸化ベリリウムを 主成分とする焼結体、 及び 化アルミニウムを主成分とする焼結体に対してはこれら焼結体か らなる基板面に対して垂直及び 4 5度の 2方向になるように石英ガラス製の供給管を別に配置 し、 主原料のトリメチルガリゥムあるいはトリメチルアルミニウムを水素あるいは窒素 +水素 のキヤリァガスとともに、 さらに反応ガスであるアンモニアを上記各セラミック材料を主成分 とする焼結体からなる基板に供給し単結晶薄膜の形成を試みた。 また、 酸化ジルコニウムを主 成分とする焼結体、 酸化マグネシウムを主成分とする焼結体、 アルミン酸マグネシウムを主成 分とする焼結体、 及び 化ィットリゥムを主成分とする焼結体に対してはこれら焼結体からな る基板面に対して垂直及び水平及び 4 5度の 3方向になるように石英ガラス製の供給管を別に 配置し、 主原料のトリメチルガリゥムあるいはトリメチルアルミニウムを水素あるいは窒素 + 水素のキャリアガスとともに、 さらに反応ガスであるァンモニァを上記各セラミツク材料を主 成分とする焼結体からなる基板に供給し単結晶薄膜の形成を試みた。 その結果、 薄 J»成を試 みたすベてのセラミツク材料を主成分とする焼結体には窒化ガリゥム及び窒化アルミニゥムを 主成分とする単結晶薄膜が直接形成し得ることが^ tかめられた。 すなわち、 少なくとも表 5 6 に示した表面粗さを有するセラミック材料を主成分とする焼結体であってもその表面には窒化 ガリウム及び窒化アルミニウムを主成分とする単結晶薄膜が直接形成し得ることが確かめられ た。 形成された単結晶薄膜はミラー指数 (0 0 2 ) の格子面の X線回折ロッキングカーブの半 値幅として少なくとも 3 0 0秒以下と比較的結晶性に優れたものであった。 また、 直接形成し
た薄膜の厚みとしては少なくとも 0. I n m以上のものが単結晶として形成し得ることが か められた。
上記のように無定形、 配向性多結晶のうちから選ばれた少なくともいずれかの結晶状態を有 する薄膜をあらかじめ形成しなくても表 5 6に示す各種表面粗さを有する窒化ガリゥム及び窒 化アルミ二ゥムを主成分とする単結晶薄膜が直接形成し得ることが ¾かめられた。 すなわち本 実施例により、 セラミック材料を主成分とする焼結体からなる基板面に対して垂直及び水平及 び斜めのうちから選ばれた少なくとも 2以上の方向になるように薄膜の原料となるガリゥム成 分及びアルミニウム成分を供給することで、 比較的表面粗さの大きいセラミック材料を主成分 とする焼結体であってもその表面には窒化ガリウム及び窒化アルミニウムを主成分とする単結 晶薄膜が直接形成し得ることが確かめられた。
次に表 5 6に示した各種セラミック材料を主成分とする焼結体のうち窒化アルミニウムを主 成分とする撫結体 率 8 8 %、 7 4 %、 5 4 %及び 3 4 %の 4衝、 窒化ガリウムを主成 分とする焼結体 0¾¾i率 8 6 %及び 7 6 %の 2衝、酸化アルミニウムを主成分とする撫吉体
(¾¾§率7 8 %)、 酸化マグネシウムを主成分とする焼結体 (光醒率 8 3 %)、 及び谶化ィ ットリウムを主成分とする 吉体(¾¾i率 8 3 %)、 を選びそれぞれの焼結体について表 5 6 に示した表面状態を有するものすべてに対して窒化ガリウム及び窒化アルミニウムを主成分と する単結晶薄膜を上記 MOCVD法により直接形成しその後鏡面研磨して厚み 3 mとした。 その後形成した単結晶薄膜の上に実施例 3 4、 実施例 3 5、 実施例 3 7及び実施例 3 8と同様 の方法で窒化ガリウム、 窒化インジウム、 窒化アルミニウムのうちから選ばれた少なくとも 1 種以上を主成分とする薄膜からなる少なくとも N型半導体層及び発光層及び P型半導体層を含 む積層体を形成し発光層として単一量子井戸構造を有する発光素子を作製した。 次に作製した 各発先^?に実施例 3 4、実施例 3 5、実施例 3 7及び、実施例 3 8と同様に 3. 5ポリレト〜 3. 8ポルトの電位を印加し発光効率を調べた。 その結果、 率 8 8 %を有する窒化アルミ二 ゥムを主成分とする焼結体を用いて作製した発光素子では発光効率 6 6 %〜7 2 %であった。 光藤率 7 4 %を有する窒化アルミニウムを主成分とする焼結体を用いて作製した発光素子で は発光効率 6 0 %〜6 2 %であった。 光翻率 5 4 %を有する窒化アルミ二ゥムを主成分とす る焼結体を用いて作製した発光素子では発光効率 4 5 %〜 5 1 %であった。 光逸過率 3 4 %を 有する窒化アルミニウムを主成分とする焼結体を用いて作製した発光素子では発光効率 3 8 % 〜4 1 %であった。 ½¾1率 8 6 %を有する窒化ガリウムを主成分とする焼結体を用いて作製 した発光素子では発光効率 6 7 %〜 7 1 %であった。 光 ¾1率 7 6 %を有する窒化ガリゥムを 主成分とする焼結体を用いて作製した発光素子では発光効率 6 4 %〜6 7 %であった。 光 ¾1 率 7 8 %を有する酸化アルミニウムを主成分とする焼結体を用いて作製した発光素子ではブラ スト研磨したもので発光効率 6 4 %プラズマ加工したもので 6 7 %であった。 光透過率 8 3 % を有する酸化マグネシウムを主成分とする焼結体を用いて作製した発光素子では焼き放し ( a s — f i r e ) のもので発光効率 6 8 %ブラス卜研磨したもので 7 0 %であった。 また光透過 率 8 3 %を有する酸化ィットリゥムを主成分とする焼結体を用いて作製した発光素子ではラッ フ 磨したもので発光効率 7 1 %ブラスト研磨したもので 6 9 %であった。 このように表面粗 さの大きいセラミック材料を主成分とする焼結体にも窒化ガリウム及び窒化アルミニウムを主 成分とする単結晶薄膜が直接形成可能であり高い発光効率を有する発光^?が作製し得ること が かめられた。
実施例 4 0
本実施例は発光素子を作製するために用いられる比較的表面粗さの大きいセラミック材料を 主成分とする焼結体を用いて作製した発光素子の発光効率に及ぼす効果について調べた例を示 す。 より詳しく言えば、 表面粗さの大きい粉末成形体を用いて作製した表面粗さの大きいセラ
ミック材料を主成分とする焼結体、 及びホットプレス法で作製した表面粗さの大きいセラミツ ク材料を主成分とする焼結体について単結晶薄膜の形成状態について調べ、 さらにこれら表面 粗さの大きいセラミック材料を主成分とする焼結体を用いて作製した発光素子の発光効率に及 ぼす効果について調べた例を示す。
まず、 窒化アルミニウム、 窒化ガリウム、 酸化亜鉛、 酸化ベリリウム、 酸化アルミニウム、 酸化マグネシウム、 アルミン酸マグネシウム及び酸化ィットリゥムを主成分とする成形用粉末 を用意した。 窒化アルミニウムを主成分とする成形用粉末は実施例 2の実験 No. 49で作製 した Y 2〇 3を 3. 3髓%含有するもの、実施例 6の実験 N o. 108-109で作製した Y 2 〇 3を 0. 2 含有するもの、 及ぴ ¾ ^例 11の実験 N o. 260〜 262で作製した酸ィ匕 物 S¾法による原料を用いた Y203を 1. 0重量%含有するものの 3種類である。 窒化ガリウ ムを主成分とする成形用粉末は実施例 36の実験 Ν ο. 1538〜 1539で作製した Υ203 を 0. 01モレ%含有するもの、 及び実施例 36の実験 Ν ο. 1566〜 1567で作製した Ca〇を 0. 2モル%、 Y203を 0. 2モル%及び S i 3Ν4を 0. 01モル%同時に含有する ものの 2種類である。 酸化亜鉛を主成分とする成形用粉末は実施例 30の実験 No. 1218 〜1219で作製した Al 203を 0. 03モル%及び Y203を 0. 04モル%同時に含有する もの、 及び実施例 30の実験 No. 1240〜1241で作製した Al 203を 3. 0モル%及 び Y203を 0. 04モル%同時に含有するものの 2種類である。 酸化ベリリウムを主成分とす る成形用粉末は実施例 31の実験 Ν ο. 1306〜 1307で作製した C a Οを 0.45モル% 及び Y2〇3を 0. 04モル%同時に含有するものである。 酸化アルミニウムを主成分とする成 形用粉末は実施例 32の実験 Ν 0. 1332〜 1333で作製した M g 0を 0. 12モル%含 有するもの、及び実施例 32の実験 No. 1376〜 1377で作製した Mg〇を 1. 0モル%、 Ca〇を 0. 2モル%及び Y203を 0. 04モル%同時に含有するものの 2種類である。 酸化 マグネシウムを主成分とする成形用粉末は実施例 33の実験 Ν ο. 1394〜 1400で作製 した CaOを 1. 0重量%及び Y203を 1. 0重量%同時に含有するものである。 アルミン酸 マグネシウムを主成分とする成形用粉末は実施例 33の実験 No. 1404〜1410で作製 した CaOを 0. 1重量%及び Y203を 0. 1重量%同時に含有するものである。 酸化イット リゥムを主成分とする成形用粉末は実施例 33の実験 Ν ο . 1414-1420で作製した D y2〇3を 0. 25重量%及び Ho203を 0. 25重量%同時に含有するものである。
次に上下のパンチに一辺 2 mの正方形で高さ 2 xmの凹凸が規則的に形成された内径 32 mmの炭化タングステン製の成形用金型を用意し上記の成形用粉末を用いて圧力 50 OKg/ cm2で一軸プレス成形を行った。その結果、金型に施された形状と同様一辺 2 mの正方形で 高さ 2 mの凹凸が表面に形成された窒化アルミニウム、 窒化ガリウム、 酸化亜鉛、 酸化ベリ リウム、 酸化アルミニウム、 酸化マグネシウム、 アルミン酸マグネシウム及び ¾化イットリウ ムを主成分とする粉末成形体を得た。 得られた成形体の直径は 32 mm厚みは 0 · 6 mmであ る。
次に作製した各粉末成形体を脱脂後以下に示す条件で焼成した。 窒化アルミ二ゥムを主成分 とする粉末成形体の場合、 Y2〇3を 3. 3 #5^%含有するもの、 及び Υ2〇3を 0. 2籠%含 有するものは 1気圧の Ν2中 1800 で 2時間常圧焼成を行った。 また Υ203を 1. 0重量% 含有するものは 1気圧の Ν2中 2200°Cで 8時間常圧焼成した。窒化ガリウムを主成分とする 粉末成形体の場合、 2種類の組成を有するいずれのものも 1気圧の N2中 1450 で 2時間常 圧焼成した。 酸化亜鉛を主成分とする粉末成形体の場合、 2種類の組成を有するいずれのもの も大気中 1460°Cで 1時間常圧 «した。酸化ベリリウムを主成分とする粉末成形体の場合、 大気中 1500 で 3時間常圧舰した。酸化アルミニウムを主成分とする粉末成形体の場合、 M g 0を 0. 12モル%含有するものは 1気圧の水素中 1820 °Cで 5時間常圧焼成した。 ま
た MgOを 1· 0モル%、 〇&0を0. 2モル%及び Υ203を 0. 04モル%同時に含有する ものは大気中 1550°Cで 3時間常圧! «した。 酸化マグネシウムを主成分とする粉末成形体 の場合、 大気中 1600°Cで 6時間常圧 «した。 アルミン酸マグネシウムを主成分とする粉 末成形体の場合、 水素気流中 1650°Cで 8時間常圧焼成した。 酸化イットリウムを主成分と する粉末成形体の場合、 水素気流中 2100°Cで 3時間常圧 した。 得られた各焼結体は十 分〖こ緻密ィ匕していた。 次に、 焼成後得られた各焼結体をブラシで水洗洗浄して付着物を取り除 いた。
このようにして窒化アルミニウム、 窒化ガリウム、 酸化亜鉛、 酸化ベリリウム、 酸化アルミ 二ゥム、 酸化マグネシウム、 アルミン酸マグネシウム及び酸化イットリウムを主成分とする焼 き放し (a s— f i r e) 状態の焼結体を得た。 これら各焼結体の表面には一辺 1 · 6 amの 正方形で高さ 1. 6 /xmの凹凸のが規則的に形成されていることが$認された。 形成された凹 凸は図 73に例示したものと同様の形状を有していた。 その後得られた各焼結体の一部を鏡面 研磨し光透過率を測定したが凹凸形状が形成された表面粗さの大きなものであっても光 ¾i率 はほとんど減じることなく十分大きいことが確認された。 その結果を表 57に示した。
また別に実施例 3においてドク夕一ブレード法で作製した窒化アルミニウムを主成分とし E r 203を 4. 02体積%含有するグリーンシートを用意した。 また実施例 14においてドク夕 一ブレ一ド法で作製した窒化アルミ二ゥムを主成分とし Y 2 O 3を 5. 0重量%含有するダリ一 ンシートと窒化アルミニウムを主成分とし Y203を 5. 0重量%及び CaOを 0. 5重量%同 時に含有するグリーンシ一トとを用意した。 次に上記のようにドクターブレード法で作製した グリーンシートをパンチに一辺 2 mの正方形で高さ 2 a mの凹凸が規則的に形成された上記 の金型に入れ 60°Cに加熱しながら圧力 10Kg,cm2で加圧し、その結果金型に施された形 状と同様一辺 2 mの正方形で高さ 2 mの凹凸が表面に形成された窒化アルミニウムを主成 分とする 3種類のグリーンシートを得た。 次にこれらのシート成形体を窒素中で脱バインダー 後 Er203を 4. 02髓%含有するシートについては 1赃の N 2中 1820 で 2時間、 Y 203を 5.0重量%含有するシ一卜については 1躯の N2中 1800°Cで 8時間、 Y203を 5. 0重量%及び CaOを 0. 5重量%同時に含有するシートについては 1気圧の N2中 2200°C で 4時間常圧焼成した。 得られた各焼結体は十分に緻密化していた。 次に、 鐘後得られた各 焼結体をブラシで水洗洗浄して付着物を取り除いた。
このようにして窒化アルミニウムを主成分とする焼き放し (as— f i r e) 状態の焼結体 を得た。 これら各焼結体の表面には一辺 1. 6 mの正方形で高さ 1. 6 mの凹凸のが規則 的に形成されていることが ϋ認された。 形成された凹凸は図 73に例示したものと同様の形状 を有していた。 その後得られた窒化アルミニウムを主成分とする各焼結体の一部を鏡画开磨し 光透過率を測定したが凹凸形状が形成された表面粗さの大きなものであっても光透過率はほと んど減じることなく十分大きいことが萑認された。 その結果を表 57に示した。
次に内径 25. 4mmのホットプレス用高密度黒鉛型を用意した。 このカーボン型の上下パ ンチは粒度 # 400のアルミナ研 »jを用いたサンドプラスト研磨により表面が平均表面粗さ Ra = 2940 nmの状態にしてある。 また別に実施例 6の実験 N o. 105〜 106で作製 した窒化アルミニウムを主成分とし CaOを 0. 2体積%含有する成形用粉末を用意した。 こ の成形用粉末と前記実施例 6の実験 No. 108〜109で作製した窒化アルミニウムを主成 分とし Y203を 0. 2#¾%含有する成形用粉末とを直径 25. 4mmx厚み 1. 0mmの大 きさに圧力 50 OKgZcm2で予備成形し脱脂後カーボン型に入れ 1気圧の N2中 1820°C で 4時間、圧力 300Kg/cm2でホットプレスを行った。得られた焼結体は十分に緻密化し ていた。次に、ホットプレス後得られた各焼結体をブラシで水洗洗浄して付着物を取り除いた。 このようにしてホットプレス法により 2種類の組成の窒化アルミニウムを主成分とする焼き
放し (a s— f i r e) 状態の焼結体を得た。 これらの焼結体の平均表面粗さは C a 0を 0. 2體%含有する成形用粉末から作製したもので R a = 3 1 2 O nmであり、 Y2〇3を 0. 2 含有する成形用粉末から作製したもので R a = 2 7 9 0 nmであった。 いずれの焼結体 もカーボン型のパンチの表面耝さとほとんど同じであることが萑認された。 その後得られた各 窒化アルミニウムを主成分とする焼結体の一部を鏡面研磨し ½¾ 率を測定したが上記のよう に表面粗さの大きなものであっても光 ¾ 率は減じることなく十分大きいことカ權認された。 その結果を表 5 7に示した。
上記のようにして得られた表面粗さの大きレゝ粉末成形体を用いて作製した焼き放し (a s— f i r e ) 状態で表面粗さの大きいセラミック材料を主成分とする焼結体を基板として用い M O C VD法により窒化ガリゥム及び窒化アルミ二ゥムを主成分とする単結晶薄膜の形成を試み た。 また、 表面粗さの大きい力一ボン型を用いたホットプレス法で作製した表面粗さの大きい セラミック材料を主成分とする焼結体に対しても MO CVD法で窒化ガリウム及び窒化アルミ 二ゥムを主成分とする単結晶薄膜の形成を試みた。 単結晶薄膜の形成は以下に述べる 2つの方 法で行った。 すなわち、 1つの方法は上記各セラミック材料を主成分とする焼結体に MO CV D法であらかじめ窒化ガリウムあるいは窒化アルミニウムを主成分とする無定形薄膜あるいは 配向性多結晶薄膜を形成したものを用い、 該無定形薄膜あるいは配向性多結晶薄膜の上に窒化 ガリゥム及び窒化アルミ二ゥムを主成分とする単結晶薄膜の形成を M〇 C VD法により試みる という方法である。 もう 1つの方法は上記各セラミック材料を主成分とする焼結体に直接窒化 ガリウム及び窒化アルミニウムを主成分とする単結晶薄膜を MO CVD法により試みるという 方法である。 上記方法のうち、 あらかじめ窒化ガリウムあるいは窒化アルミニウムを主成分と する無定形薄膜あるいは配向性多結晶薄膜をセラミック材料を主成分とする焼結体に形成する 方法としては M〇 C V D法を用いたが、 該 MO CVD法は基板温度を変えた以外は実施例 2 5 で示したものと同じ方法である。 すなわち、 窒化アルミニウムを主成分とする配向性多結晶薄 膜を形成する場合基板!^を 6 2 0°Cとした。 また、 窒化アルミニウムを主成分とする無定形 薄膜を形成する場合基板温度を 4 9 0 °Cとした。 また、 窒化ガリウムを主成分とする配向性多 結晶薄膜を形成する場合基板温度を 5 6 0 °Cとした。 さらに、 窒化ガリウムを主成分とする無 定形薄膜を形成する場合基板 芰を 4 3 0 Cとした。
上記あらかじめ窒化ガリウムあるいは窒化アルミニウムを主成分とする無定形薄膜あるいは 配向性多結晶薄膜を形成したものの上に窒化ガリウム及び窒化アルミニウムを主成分とする単 結晶薄膜を形成を試みる場合、 主原料、 キャリアガス、 及び反応ガスの供給は実施例 3 4、 実 施例 3 5、 実施例 3 7及び実施例 3 8と同様の方法により行った。 一方、 各セラミック材料を 主成分とする焼結体に直接窒化ガリウム及び窒化アルミニウムを主成分とする単結晶薄膜の形 成を試みる場合は、 主原料のトリメチルガリゥムあるいはトリメチルアルミニウム、 水素ある いは窒素 +水素のキヤリァガス、 及び反応ガスであるアンモニアの供給は実施例 3 9と同様の 方法で行った。 すなわち、 石英ガラス製の反応容器内に置かれた窒化アルミニウムを主成分と する焼結体、 窒化ガリウムを主成分とする焼結体、 酸化亜鉛を主成分とする焼結体、 酸化ベリ リゥムを主成分とする焼結体、及び酸化アルミニウムを主成分とする焼結体に対して 原料、 キヤリァガス、及び反応ガスの供給がこれら焼結体からなる基板面に対して垂直及び 4 5度の 2方向からになるように石英ガラス製の供給管を別に配置し、 単結晶薄膜の形成を試みた。 ま た、 石英ガラス製の反応容器内に置かれた酸化マグネシウムを主成分とする焼結体、 アルミン 酸マグネシウムを主成分とする焼結体、 及び ¾化イットリウムを主成分とする焼結体に対して は主原料のトリメチルガリゥムあるいはトリメチルアルミニウム、 水素あるいは窒素 +ΖΚ素の キヤリァガス、 及び反応ガスであるアンモニアの供給がこれら焼結体からなる基板面に対して 垂直及び水平及び4 5度の3方向からになるように石英ガラス製の供給管を別に配置し、 単結
晶薄膜の形成を試みた。 その結果、 本実施例で作製した窒化アルミニウムを主成分とする慰吉 体、 窒化ガリウムを主成分とする 結体、 酸化 ffiiを主成分とする焼結体、 酸化ベリリウムを 主成分とする能結体、 酸化アルミニウムを主成分とする德結体、 酸化マグネシウムを主成分と する焼結体、 アルミン酸マグネシウムを主成分とする焼結体、 及び酸化イットリウムを主成分 とする 結体すベての鷉吉体にはあらかじめ窒化ガリゥムあるいは窒化アルミニウムを主成分 とする無定形薄膜あるいは配向性多結晶薄膜を形成したものだけでなく、 直接窒化ガリゥム及 び窒化アルミニウムを主成分とする単結晶薄膜が形成し得ること力鳩かめられた。 上記各セラ ミック材料を主成分とする 結体に直接形成された単結晶薄 S Tあってもミラー指数 (0 0 2) の格子面の X線回折ロッキングカーブの半値幅として少なくとも 3 0 0秒以下と比較的結晶性 に優れたものであった。 各セラミック材料を主成分とする 結体に直接形成された単結晶薄膜 は多くのもので半値幅が 1 0 0秒以下であった。 また、 本実施例で作製した窒化アルミニウム を主成分とする難体、窒化ガリゥムを主成分とする 結体、酸ィ ^を主成分とする焼結体、 酸化ベリリウムを主成分とする; ^結体、 酸化アルミニウムを主成分とする 体に直接形成さ れた単結晶薄膜は主原料あるいは反応ガスの供給方向を特に限定せず反応容器に自発的に広が るような方法で供給することにより形成したものに比べてミラー指数 (0 0 2) の格子面の X 線回折ロッキングカーブの半値幅が減少し結晶性が向上していることカ權認された。 これ 面状態にかかわらず ¾膜形成法をより 化することで結晶性に優れた単結晶薄膜がセラミッ ク材料を主成分とする嫌吉体に形成し得ることを示していると言える。 この状況が表 5 7に示 されている。 なお、 表 5 7においてセラミック材料を主成分とする 体に直接形成された第 1層目の薄膜は鏡面研磨して厚み 3 mとした。 その上に形成された第 2層目の薄膜の厚みは 3 mである。
また、 本実施例で作製したセラミック材料を主成分とする焼結体に形成されたすベての薄膜 の外観を調べたがいずれもクラックやひび割れなどの欠陥は見られない。 また、 粘着テープに よる剥離テストを行ったがいずれの薄膜も該セラミック材料を主成分とする; ¾ 体からなる基 板との間あるいは 2層で形成された薄膜間で剥離は見られなかった。 また、 作製した薄膜表面 に T i /P t ZAuの薄 電性材料を形成して金属リードをはんだ付けし垂直引張り強度を 調べたがすべて 2 Kg/mm2以上であり本実施例で作製したセラミック材料を主成分とする 結体と各薄膜との間あるいは各薄膜間は強固に接合している。
次に、 本実施例で作製した表面粗さの大きい粉末成形体を用いて作製した焼き放し (a s— f i r e) で表面粗さの大きいセラミック材料を主成分とする焼結体に窒化ガリウム及び窒化 アルミニウムを主成分とする単結晶薄膜を厚み 3 m形成したもの、 及びホットプレス法で作 製した表面粗さの大きいセラミック材料を主成分とする; ¾結体に窒化ガリゥム及び窒化アルミ 二ゥムを主成分とする単結晶薄膜を厚み 3 m形成したものを用い、 その上に実施例 3 9と同 様の方法で単一 *ΐ井戸職の 素子を形成してその発光効率を調べた。 その結果、 本歸包 例で作製したセラミック材料を主成分とする焼結体を用いて作製した発光軒であっても、 実 施例 3 9で作製した一旦焼成した後のセラミック材料を主成分とする焼結体を加工して表面粗 さを大きくしたものと比較して発光効率はほとんど減少せず、 実施例 3 9で作製した発光素子 と同様高い発光効率を有する発光素子が作製できることが萑認された。
以上、 表 5 7に本実施例の結果をまとめて示した。
実施例 3 9及 ^施例 4 0で例示したように、 本発明において比較的表面粗さの大きいセラ ミック材料を主成分とする搬吉体に形成された窒化ガリウム、 窒化インジウム、 窒化アルミ二 ゥムのうちから選ばれた少なくとも 1種以上を主成分とする薄膜であっても該薄膜にはクラッ ク、 ひび など生じにくく、 該薄膜と該セラミック材料を主成分とする焼結体との間で剥離 などの不具合も生じにくく強固に接合する。
以上本発明を実施例により説明した。
〔表 1〕
*) 電子線回折による
〔表 2〕
窒化アルミニウムを主成分とする焼結体からなる基板の特性
粉末成形体の特性 窒化アルミニウムを主成分とする焼結体の特性
添実焼
加験成,
物条 N
①②③④⑤⑥件の o
曇111111:
* 1) は酸化物換算による。
* 2) 64〜70の添加物の添加量は元素換算によるものである。
* 3)
950"CX 4時間、 N2中常圧焼成
95 O X 12時間、 N2中ガス圧焼成 (9Kg/cm3)
80 O^CX 2時間、 N2中ホットプレス (300Kg/cm3
900 X 3時間、 H I P焼成 (200 OKg/cm3) 90 O X 4時間、 N2中常圧焼成
800"CX 1時間、 N2中常圧焼成 .
〔表 3〕
窒化アルミニウムを主成分とする焼結体に 形成された単結晶薄膜の特性
実験 薄膜 (002)X線回折
No. 薄膜の組成 厚み ロッキングカーブ
( m) の半値幅
(秒) 2 100 % G a N 0. 2 5 180 3 100%GaN 0. 25 142 4 100 % G a N 0. 25 189 5 100 %G aN 0. 25 156 6 100 %G aN 0. 25 175 7 100 %G aN 0. 25 169· 8 100 % G a N 0. 25 181 9 100 %G aN 0. 25 187 0 100%GaN 0. 25 774 1 100%GaN 0. 25 185 2 50モリレ%。 aN 0. 25 233 + 50モレ0 /01 nN
3 100 % I n N 0. 25 189 4 50モル%G aN 6. 0 194 +50モル%A 1 N
45 100 % G a N 0. 25 188
46 100 % G a N 0. 25 137
47 100 %G aN 0. 25 184
48 100 % G a N 0. 25 179
49 100 %G aN 0. 25 195
50 20モル%GaN 6. 0 170 + 80モル%A 1 N
51 100 %G aN 0. 25 167
52 50モル%Ga f 0. 25 . 161 + 50モル。/ ϋ I n N
53 100%GaN 0. 25 652
54 100 % G a N 0. 25 183
55 100%GaN 0. 25 194
56 100 ¾G aN 0. 25 216
57 100 G aN 0. 25 226
58 100 % G a N 0. 25 167
59 100 G aN 0. 25 190
60 100 % G a N 0. 25 155
61 100%GaN 0. 25 224
62 100 GaN 0. 25 216
63 100 % G a N 0. 25 189
64 100%GaN 0. 25 169 '
65 100%GaN 0. 25 186
66 100 % G a N 0. 25 178
67 100%GaN 0. 25 19-9
68 100%GaN 0. 25 197
69 100 % G a N 0. 25 191
70 100 % G a N Ό. 25 179
〔表 4〕
スルー 導通ビア (002)X線回折 実験 導通ビア 焼結助剤 ホール の ロッキングカーブ
No. 材料 の 抵抗率 の
大きさ (1 0- 6Ω · cm) 半値幅
(μ,ΐΐύ (室温) (秒)
7 1 1 0 0 % Υ2θ3 2 5 7. 4 1 8 9
72 タンダ 5 0 6. 9 1 9 6
7 3 E r 203 2 5 7. 7 2 0 7
74 25 0 6. 6 2 2 6
7 5 5 0体積% Y203 2 5 4. 9 1 7 7
7 6 タンダ 50 4. 4 1 9 2
7 7 ステン E r 203 2 5 5. 0 2 0 0
78 + 5 0 4. 8 2 3 3
7 9 5 0体積% C aO 2 5 5. 6 1 6 7 銅
80 Y2〇3 2 5 3. 4 2 0 1
8 1 25 0 2. 9 2 2 3
82 1 0 0 % E r 203 2 5 3. 9 2 2 5
8 3 銅 5 0 3. 1 2 3 9
84 C aO 2 5 2. 7 1 5 5
8 5 50 0 2. 0 1 74
〔表 5〕
*) 電子線回折による
窒化アルミニウムを主成分とする焼結体からなる基板の特性 窒化アルミニウムを主成分とする焼結体 粉末成形体の特性 作製された窒ィヒアルミニウムを主成分とする焼結体の特性 に形成された単結晶薄膜の特性 実験 粉末成形体中の 気孔 A 1 N 表面の (002)
N o . 添加物 焼成 相対密度 平均 粒子の 全酸素量 ALON 平滑度 光 薄膜 X線回折 及び添加量 条件 大きさ 平均 里 R a 透過率 薄膜の組成 厚み ロッキング 大きさ カーブ
(体積%) * 1 ) 氺 3) (%) (μ.τη) (重 つ (%) (nm) (%) ( ) の半値 te
(¾>) 丄 U d 添加物なし ② 9 9. 6 0. ¾ 3. 0 0. 8 1. 6 27 62 100 %G aN 0. 2 5 127
1 04 MgO (0. 4) ① 99. 6 <0. 5 2. 4 0. 9 1. 5 29 33 5 0モル%GaN 0. 2 5 1 52
+ 50七ル0 /oA 1 N
10 5 C a C03 (0. 2) ② 99. 6 <0. 5 2. 5 0. 9 0. 5 28 69 1 00 G aN 0. 25 122
10 6 C aCOs (0. 2) ③ 99. 4 <0. 5 2. 4 0. 8 0. 4 27 54 100%GaN 0. 2 5 1 34
1 0 7 A 1203 (0. 4) ① 99. 7 <0. 5 2. 9 1. 0 2. 2 29 62 100 %G aN 0. 2 5 140
108 Y203 (0. 2) ② 99. 7 <0. 5 1. 9 0. 8 0. 6 26 74 100 GaN 0. 2 5 122
109 Y203 (0. 2) ③ 9 9. 6 < 0 - 5 2. 3 0. 8 0. 5 28 56 100 %G aN 0. 2 5 141
110 E r 203 (3. 0) ② 99. 8 <0. 5 2. 0 1. 9 0. 0 26 67 50モル%GaN 0. 2 5 127
+50モル%I nN
1 11 E r 203 (3. 0) ③ 99. 6 <0. 5 2. 3 1. 9 0. 0 27 58 1 00%GaN 0. 2 5 1 31
L 12 V2Os (0. 5) ① 99. 6 <0. 5 2. 9 0. 9 1. 4 3 1 39 10 0 % I nN 0. 2 5 1 57
* 2)
1 1 3 C r 2Os (1. 0) ① 99. 4 <0. 5 2. 2 0. 8 2. 0 33 3 1 10 0'%GaN 0. 25 186
* 2)
* 1) 添加物の量は酸化物換算による t 但し *2) を記した実験 No. 112 113は元素換算である。 ( ) 内に添加量を示した
* 3 ) 焼成条件:
① 1820^X2時間、 1気圧 N2中ホットプレス (圧力: 30 OKgZcm2)
ΐ 900 x 2時間、 1気圧 N2中ホットプレス (圧力: 30 OKg/cm2)
③ 182 CTCX2時間、 N2中常圧焼成
〔表 7〕
窒化アルミ二ゥムを主成分とする 実験 焼結体の特性
No. 使用した基板 紫外線透過率 実施例 実験
No. 〔300
114 実施例 2 32 12
115 実施例 2 33 24
116 実施例 2 34 41
117 実施例 2 35 37
118 実施例 2 38 3. 6
119 実施例 2 44 17
120 実施例 2 46 44
121 実施例 2 49 28
122 実施例 2 54 16
123 実施例 2 55 21
124 実施例 2 56 20
125 実施例 2 58 26
126 実施例 2 60 8. 5
127 実施例 2 61 6. 2
128 実施例 2 62 30
129 実施例 2 67 1. 9
130 実施例 2 69 7. 6
131 実施例 6 103 49
132 実施例 6 104 29
133 実施例 6 105 62
134 実施例 6 106 46
135 実施例 6 107 49
136 実施例 6 108 67
137 実施例 6 109 50
138 実施例 6 110 54
139 実施例 6 111 47
〔表 8〕
焼結体基板の特性 各種焼結体に形成された薄膜の特性 使用した基板 薄膜 麵 (002)X線回折 実験 主成分 作製した実施例 表面の の の ロッキングカーブ
No. 実施例 実験 平滑度 形成 薄膜の組成 厚み の
No. No. a 位置 半値幅
(nm) ( m) (秒)
1層目 1 00%GaN 1. 0 1 81 3 5 実施例 1 1〜5 34 2層目 50モル%GaN 1. 0 1 19 十 50モル0 /01 nN
3 6 実施例 2 34 2 5 1層目 1 00 % A 1 N 6, 0 1 59
2層目 1 00%G aN 2. 0 1 37
1層目 1 00 % A 1 1 5. 0 140 37 実施例 2 46 Z 8 2層目 49. 94モル%G
+ 49. 94モル。/。 A 1 N 3. 0 1 02
+ 0. 1 2モル%S i
1層目 1 0 0 % A 1 1 5. 0 1 32 38 実施例 2 62 22 2層目 9 9. 94モル1 ½A I N 6. 0 1 23
+ 0. 06モル%S i
1層目 1 00 % A 1 7. 0 1 36 39 実施例 2 64 1 7 2層目 1 0 0 % A 1 7. 0 1 07
3層目 100%Ga 1. 0 1 0 5
1層目 1 00 % A 1 N 1. 0 1 86 窒化
93 2層目 99. 9モル%GaN 3. 0 149 アルミ
40 実施例 4 〜9 9 29 + 0. 1モル。/。 S i
ニゥム
3層目 9 9. 9モル。/。GaN 3. 0 124 + 0. 1モル0 /0Mg
1眉目 1 0 0%GaN 6. 0 140
1 00 2層目 99. 9モル%G aN 1. 0 1 7 1 実施例 4 〜; L 02 2 6 + 0. 1モル0 /0B e
3層目 70モル%G aN 1. 0 1 1 6 +30モル%I nN
1眉目 1 00 % A 1 N 3. 0 1 24 4 2 実施例 6 1 0 3 1 6 2眉目 99. 9モル%G aN 1 00 1 21 氺) + 0. 1モル%Z n
1眉目 1 00 % A 1 N 1 5. 0 1 22 43 実施例 6 1 0 5 2 7 69. 9モル%GaN 1 07
2翻 + 30モル%I nN 3. 0
+ 0. 1モル%Mg
1翻 1 00 % A 1 1 5. 0 1 0
2 4 4 実施例 6 1 0 7 23 7 9. 9モル%GaNf 1 1 7 ) 2層目 + 20モル。/。 A 1 N 6 0
+ 0. 1モル%Mg
2 4 5 実施例 6 1 08- 22 1層目 1 00 % A 1 N 1 0. 0 1 14
2層目 1 0 0%G aN ' 2 00 1 1 0
1 09 1層目 99. 96モル%A 1 N 1 5. 0 1 32 実施例 6 + 0. 04モル%S i
246 27 2顧 70モル。/。 GaN 6. 0 1 23
+ 30モル。/。 I nN
3眉目 1 00 % I n N 3. 0 1 07 炭化 1 1 1層目 1 00 % A 1 N 0. 5 272
247 珪素 実施例 1 〜: 1 3 6. 8 2翻 50モル。 /。GaN 1. 0 2 37
+50モル%A 1 N
248 蜜化 実施例 1 14 1 5 1層目 1 00 % A 1 N 0. 5 724 珪素 〜: L 6 2層目 1 00%G aN 1. 0 205
1層目 1 00 % A 1 1. 0 39 1 酸化 . 1 7 2層目 99. 97モル。/。 A 1 N 6. 0 2 04
249 アルミ 実施例 1 〜1 9 1 1 + 0. 03モル%S i
ニゥム 3屑目 50モル%Ga 1 5. 0 1 90
+ 50モル%A 1
酸化 . 22 1層目 1 00 %A 1 0. 5 289
2 5 0 亜鉛 実施例 1 〜24 8. 8 2層目 50モル%GaN 1. 0 20 1
+ 50モル。/。 A 1
1層目 1 00%A 1 N 1. 0 2 76 酸化 27 2層目 9 9. 99モル。/。A 1 N 6. 0 2 1 0
25 1 ベリ 実施例 1 〜2 9 9, 4 + 0. 0 1モル%S i
リウム 3層目 50モル G aN 1 5. 0 1 7 7
+50モル%A 1
*) クロライド VPE法による
〔表 11〕 405
窒化アルミニウムを主成分とする焼結体基板の特性
粉末成形体又は烧成済み焼結体 窒化アルミニウムを主成分とする焼結体の特性
* 1) 焼結助剤の含有量は酸化物換算したものである。
* 2) 焼成条件:
① 1800で> 2時間 ⑤ 1 9 5 OCX 1 2時間 ⑨ 220 O X 4時間
② 1 80 O X 12時間 ⑥ 2 1 0 O X 4時間 ⑩ 220 0 :x 8時間
③ 1 800^X 24時間 ©21 00"€>< 1 2時間 ©2200V.X 12時間 ©1 95 CCX 4時間 (1)21 00で 24時間
* 3) 焼結体中の焼結助剤の含有量は 100万分の 1単位の重量割合で示した。
又含有量は元素換算での値である。
* 4) 焼成済み焼結体の組成は粉末成形体の時の配合組成で助剤の量は酸化物換算したものである。
〔表 12〕 窒化アルミニウムを主成分とする焼結体に 形成された単結晶薄膜の特性
実験 麵 (002)X線回折
No. 薄膜の組成 厚み ロッキングカーブ の半値幅
(秒)
252 100 % G a N 0. 25 192
253 100%GaN 0. 25 117
254 100%GaN 0. 25 187
255 100%GaN 0. 25 122
256 100 GaN 0. 25 145
257 100%GaN 0. 25 .96
258 100%GaN 0. 25 97
259 100%GaN 0. 25 91
260 100 ¾ I n N 0. 25 139
261 100 ¾ G a N 0. 25 98
262 100%GaN 0. 25 94
263 100%GaN 0. 25 161
264 100%GaN 0. 25 90
265 100%GaN 0. 25 93
266 50モル%GaN 0. 25 144
+ 50モル% I n N
267 100%GaN 0. 25 124
268 50モル%GaN 6. 0 95
+ 50モル%A 1 N
269 100 % G a N ' 0. 25 92
270 100¾GaN 0 25 94
271 100 GaN 0. 25 98
272 100 GaN 0, 25 147
273 100%GaN 0. 25 137
274 100 % G a N 0. 25 132
275 100%GaN 0. 25 143
276 100%GaN 0. 25 140
277 100%GaN 0. 25 135
278 100 % G a N 0. 25 93
279 100%GaN 0. 25 90
280 100 GaN 0. 25 126
+ 50モリレ0 /01 n N
281 100%GaN 0. 25 96
282 100%GaN 0, 25 89
283 100 % G a N 0. 25 111
284 100%GaN 0. 25 91
285 100%GaN 0. 25 95
286 100%GaN 0. 25 89
〔表 13〕
焼結体基板の特性 各種焼結体に形成された薄膜の構成と薄膜の結晶性
使用した基板 纖 単結晶薄膜及び 実験 作製した実施例 表面の の 薄膜の 薄膜の 配向性多結晶薄膜
No. 主成分 実施例 実験 平滑度 形成 萍膜の組成 結晶状態 厚み (0 02)Χ線回折
No. No. R a 位置 ロッキング力一ブ
(nm) の半値幅 (秒) 実施例 基板側 1 0 0%GaN 無定形 0. 2 5 3 7 2 46 29 表面層 50モル。/ aG aN 単結晶 0. 2 5 94
+ 50モル。/。 I n N
8 8 実施例 46 2 9 基板側 1 0 0 % A 1 無定^ 2. 5
2 表面層 1 0 0%GaN 単結晶 0. 2 5 9 7 基板側 1 0 0 % A 1 N 無定形 2. 5 ― 8 9 実施例 49 26 49, 94モル%GaN
2 表面層 + 49. 94モル0 /oA 1 N 単結晶 2. 5 9 3
+ 0 ·. 1 2モル%S ϊ
実施例 基板側 1 0 0%A 1 N 無定形 2. 5
9 0 2 49 2 6 表面層 99. 94モル。/ uA I N 単結晶 2. 5 9 2
+ 0. 0 6モル%S i
基板側 1 00 % A 1 配向性多結 2. 5 462 0 9 1 実施例 1 1 0 22 晶
6 中間層 1 0 0 % A 1 N 単結晶 2. 5 9 6 表面層 1 00%G aN 単結晶 0. 2 5 9 1 窒化
基板側 1 00 A 1 無定^ 2. 5 ― アルミ
実施例 中間層 99. 9モル。/。GaN 単結晶 0. 2 5 9 7 ニゥム
2 9 2 6 1 1 0 22 + 0. 1モル%S i
表面層 9 9. 9モル%G aN 単結晶 2. 5 8 9
+ 0. 1モル。/。 Mg
基板側 1 0 0%G aN 無定形 0. 2 5
実施例 中間層 99. 9モル%G aN 配向性多結 2. 5 4540
2 9 3 1 1 2 67 3 0 + 0. 1モル。/。 B e 晶
表面層 7 0モル%G aN 単結晶 2. 5 9 0
+ 3 0モル。/。 I nN
実施例 基板側 1 0 0%A 1 N 無定^ 2. 5
2 94 1 1 269 30 表面層 99. 9モル%G aN 0. 2 5 8 2
+ 0. 1モル%Mg
基板側 1 00%A 1 N 単結晶 2. 5 1 2 7
2 9 5 実施例 2 83 3 0 6 9. 9モル。/。 G aN
1 1 表面層 + 3 0モル。/。 I n N 単結晶 0. 2 5 8 7 十 0. 1モル%Mg
基板側 1 00 % A 1 N 多結晶 2. 5 -
2 9 6 実施例 283 3 0 表面層 7 9. 9モル。/。 GaN
1 1 +2 0モル%A 1 N 単結晶 2. 5 8 9
+ 0. 1モル%Mg
炭化 実施例 1 1 基板側 1 00%A 1 無定^ 2. 5 ―
2 9 7 珪素 1 〜1 3 6. 8 表面層 5 0モル%G aN 単結晶 2. 5 18 9
+5 0モル%A 1 N
2 9 8 窒化 実施例 14 1 5 基板側 1 00 % A 1 N 無定^ 2. 5 ― 珐素 1 〜1 6 表面層 1 00%GaN 単結晶 0. 2 5 1 9 2 基板側 1 00 % A 1 N 無定形 2. 5
酸化 実施例 1 7 中間層 9 9. 97モル%A 1 N 配向性 2. 5 1 0 82 0
2 99 アルミ 1 〜: L 9 1 1 + 0. 03モル%S i 多結晶
ニゥム 表面層 50モル%G a 単結晶 2. 5 1 6 5
+5 0モル%A 1 N
酸化 実施例 22 據側 1 00 %A 1 N 無定形 2. 5
3 0 0 亜鉛 1 〜24 8. 8 表面層 50モル%G aN 単結晶 2. 5 1 74
+ 5 0モル。/。 A 1 N
基板側 1 00 % A 1 N 無定形 2. 5
酸化 実施例 2 7 中問層 9 9. 9 9モル。/。 A 1 配向性多結 2. 5 98 9 0
3 0 1 ペリ 1 〜2 9 9. 4 + 0. 0 1モル%S i 晶
リウム 表面層 5 0モル%G aN 単結晶 2. 5 146
+50モル%A 1 N
〔表 14〕
導通ビア用
タンダ グリーン ダリ一ン スルー 焼成後 (002)X線回折 実験 ステン シート シー卜 ホール 導通ビアの ロッキンク
No. ペース卜 中の の 径 室温抵抗率 カーブの 中の 焼結助剤 焼成条件 X 10— 6 半値幅
A1N含有量 ( m) ( Ω · c m) (秒)
(重量%)
302 0. 0 25 7. 0 191
303 1. 0 25 7. 5 192
304 5. 0 Y2〇3 1800°C 25 9. 1 175
305 10. 0 5重量% X2時間 25 37 146
306 20. 0 25 69 131
307 30. 0 25 132 122
308 0. 0 25 6. 8 95
309 0. 1 Υ203 2200°C 25 6. 9 92
310 1. 0 5重量% X4時間 25 7. 4 92
311 5. 0 + 25 9. 7 93
312 10. 0 C a〇 25 43 87
313 1. 0 0.5重量% 1800 50 8. 0 184
314 5. 0 X2時間 50 9. 0 166
315 0. 1 50 6. 9 97
316 1. 0 Y2〇3 2200°C 50 6. 9 94
317 5. 0 X4時間 50 8. 2 91
318 10. 0 50 32 89
〔表 15〕
使用した基板 窒化アルミニウムを主成分とする焼結体に形成された薄膜の特性
n 単結晶薄膜の組成 単結晶薄膜 単結晶薄膜の 夹驟 実験 主成分: ド一ビング剤 の室温 (002) X線回折
IN 0. 実施例 No. A 1 XG a !_X における 口ツキノク の組成 種類 添加量 抵 m率 カーフの 牛値幅 f
(x) (モル%) Κ ΐ · c rn / 1Λ
3丄 g 実施例 2 49 0. 1 Mg 0. 1 0 079 141 o
Z Ό 実施例 3 73 0. 1 Mg 2. 0 0. 92 17 D o 1 実施例 3 73 0. 9 S i 0. 02 56 163 i o o 実施例 3 73 0. 6 M g 0. 01 5. 4 17丄
S l 0. 01
6 o Z o 6 o 実施例 3 75 八 0. 2 Mg 0. 3 1 · 0 154 o ώ 4 実施例 3 75 0. 7 S l 0. 03 8. 5 144 n e
Z 0 実施例 3 75 0. 1 Mg 0. 08 0 , 009 1 o U
S l 0. 1
o β 0 実施例 3 80 0. 6 Mg 0. 2 77 177 o 実施例 3 80 0. 1 S i 7 · 0 0 06 181
O o O 実施例 3 80 0. 0 Mg 0. 1 0. 007 188
S i 0 ' 5
o y 実施例 3 82 0. 3 Mg 0 · 2 3. 1 186 o d U 実施例 3 82 0. 8 S 0. 01 49 179 1 実施例 3 82 0. 5 Mg 0 · 5 2 · 6 179
S l 0. 1
6 o 6 o Δ 実施例 6 110 f M g 5. 1 117 o o o o o o
¾Jta 'U丄 丄 o 4 U . L) 1 U - U U U Ϊ3 V . U 丄 4 O Ό 'rt 夹/ !T也 丄 4 Q Π U o U . U M g U . 丄 Π A 7 丄 D 0 q o c
O 夹ffiWJ丄 4 o o n U ¾e u . z 1 V - U 0 Π Π 7 丄 C) t q c c
o Ό O U O VI s 0 u . 1 0 Λ 丄 O
S i 0. 05
Q Q 7 実施例 14 311 0. 6 Mg 0. 12 33 90
338 実施例 14 311 1. 0 S i 0. 02 85 88
339 実施例 14 311 0. 8 Mg 0. 02 29 89
S i 0. 02
340 実施例 14 317 0. 1 Mg 0. 5 0. 90 88
341 実施例 14 317 1. 0 S i 0. 005 194 85
342 実施例 14 317 0. 3 Mg 0. 4 2. 0 87
S i 0. 05
〔表 16〕
焼結体基板 窒化アルミニウムを主成分とする焼結体に形成された
各種結晶状態薄膜の特性
実験 使用した基板 薄膜の 単結晶薄膜の 薄膜
No. の 室温におけ (002) X線回折 実施例 鐘 の 薄膜の組成 る抵抗率 ロッキング No. No. 構成 カーブの
(Ω · cm) 半値幅 (秒)
343 実施例 49 単層 99. 94モル% I n N 無定形 0. 006
2 + 0. 06モル%S i
344 実施例 49 単層 99. 94モル% I n N 配向性 0. 004
2 + 0. 06モル%S i 多結晶
345 実施例 49 単層 99. 94モル% I n N 単結晶 0. 003 137
2 + 0. 06モル%S i
346 実施例 73 99. 98モル%A 1 N 無定形 126
3 + 0. 02モル%S i
基板側 100%G aN 無定形 0. 12
347 実施例 73 79. 90モル%G aN
3 + 19.98モル% I n N 単結晶 0. 36 85
+ 0. 12モル%Mg
実施例 19. 98モル%G aN
348 3 75 単層 + 79.90モル% I n N 無定形 0. 16
+ 0. 12モル%Mg
実施例' 49. 94モル%GaN
349 3 80 + 49.94モル% A 1 N 無定形 0. 74 ―
+ 0. 12モル%S i
350 実施例 80 単層 100 % I n N 無定形 0. 022 一
3
351 実施例 82 単層 100 % I n N 配向性 0. 016 ―
3 多結晶
実施例 49. 94モル%GaN
352 14 304 単層 + 49.94モル0 /oA 1 N 無定形 3. 2 一
+ 0. 12モル%Mg
353 実施例 304 単層 100 % I n N 単結晶 0. 014 169
14
354 実施例 304 単層 100%G aN 単結晶 0. 048 170
14
355 実施例 311 単層 99. 98モル% A 1 N 配向性 94
14 + 0. 02モル%S i 多結晶
356 実施例 基板側 100%GaN 多 晶 0. 09
14 317 99. 98モル% A 1 N 単結晶 77 81
+ 0. 02モル%S i
〔表 17〕
使用 薄膜導電性材料の特性 薄膜導電性材料の上に形成された窒化ガリゥム、 窒化ィンジゥム、 基板 窒化アルミニウムを主成分とする薄膜の特性
実験 薄膜の 薄膜 薄膜の 薄膜導電性
No. 実験 薄膜導電性 厚み 抵抗率 の (002) X線回折 材料との接 No. 材料の構成 反射率 組成 結晶 ロッキング 合強度:
(Ω · cm; 状態 カーブの 垂直引張り (j m) 半値幅 (秒) (Kg/mm2)
357 49 T i 0. 1 on
0. 052 単結晶 144 3. 1
358 73 T i 0. 2 100モル%遍 単結晶 172 3. 2
359 73 T i 0. 1 99.94 %GaN 0. 009 単結晶 160 3. 0
360 75 C r 0. 2 99,9 モル。/。 InN 0. 007 無定形 _ 3. 1
+0.06モル0 /oSi
19.98モル0 /olnN
361 75 N i 2. 0 64 +79.9 i*%GaN 0. 34 単結晶 150 2. 8
+0.12モル0 /oMg
19.98モル0 /oGaN
362 80 Mo 0. 6 53 +79.9モル0/ JnN 0. 085 無定形 3. 0
+0.12モル%Mg
49.94 »%GaN
363 80 W 1. 0 ■ 52 +49.94 ¾ル层 0. 57 無定形 一 3. 3
+0.12モル0 /oSi
364 82 W 0. 5 54 100モル%InN 0. 020 無定形 2. 9
365 82 P t 0. 5 77 50モル0 /oGaN 単結晶 179 2. 7
+50モル%A1N
366 110 A 1 3. 0 92 99.98モル0 /0颜 116 無定形 2. 6
+0.02モル0 /oSi
367 284 N i— C r 0. 8 100 »%A1N 無定形 2. 8
49.94 W%GaN
368 305 T a 0. 6 +49,94モル駕 0. 42 単結晶 164 3. 1
+0.12モル0 /oSi
369 305 Ta2N 0. 5 100モル0 /oGaN 0. 060 無定形 2. 9
370 305 T i N 0. 5 100モル%InN 0. 014 単結晶 166 2. 9
T i (密着) 0. 1 49.94 »%GaN
371 311 P t (Λ' 1)7) 0. 2 91 +49.94モル眉 3. 2 単結晶 90 2. 4
Au (低抵抗) 0. 6 +0.12モル0/ oMg
T i (密着) 0. 1 69.86 »%GaN 配向性
372 311 W ('、'リア) 0. 5 90 +29.94モル AI 1. 6 多結晶 4790 2. 8
Au (低抵抗) 0. 8 +0.20モ )l<%Mg
W : 70wt% 69.86モル%GaN
373 317 C u: 30wt 0. 5 74 +29.94モル扁 0. 56 単結晶 89 2. 6 合金 +0.20モル0/。 Si
374 317 Cr (密着) 0. 1 91 99.90モル%GaN 0. 73 単結晶 89 3. 0
Cu (低抵抗) 0. 8 +0.10モル%Mg
:表 1 8〕
* 1 の量は 化物 による。
* 2) 実験 No. 387~409の焼結体における AL ONの生成 fiはすべてゼロである。
表 20〕
*2) 実験 No. 410~423の焼結体における ALONの生成量はすべてゼロである。
〔表 21〕
* 1) 添加物の量は元素換算による。
* 2 ) 実験 Ν ο. 424 448の焼結体における AL ONの生成量はすべてゼロである c
〔表 22〕
但し、 アル力リ土類金属及び希土類金属成分の添加量は酸化物換算による。
* 2) 実験 No. 449〜457の焼結体における AL ONの生成量はすべてゼロである:
:表 23〕
* 1) 添加物の量は元素換算による重量%で示してある。
但し、 アル力リ土類金属及び希土類金属成分の添加量は酸化物換算による体積%で示す。
*2) 実験 No. 458〜475の焼結体における ALONの生成量はすぺてゼロである。
〔表 24〕
各種組成の薄膜が形成された窒ィヒアルミニウム焼結体 窒化ガリウム、 窒化インジウム、 使用した 薄膜の特性 窒化アルミニウムを主成分とする薄膜 実験 窒化アルミ 上に形成された薄膜導電性材料の特性
J ニゥム焼結体 薄膜 薄膜 薄膜導電性 薄膜との 薄膜の組成 の の 材料の組成 厚み 接合強度:
(焼結体を作製 厚み 結晶状態 及び構成 ( m) 垂直引張り し/こ実 No.) (Mm) (Kg/mm2)
476 269 100モル%A1N 3. 0 単結晶 T i 0. 2 4. 2
477 49 100 l)\%Am 3. 0 無定形 T i 0. 2 3. 6
478 49 100モル0 /oGaN 3. 0 単結晶 T i 0. 2 4. 0
479 49 100モル%GaN 3. 0 無定形 T i 0. 2 2. 9
480 49 100モル%InN 3. 0 単結晶 T i 0. 2 4. 0
481 73 99.90モル0 /oGaN 3. 0 単結晶 T i 0. 2 3. 5
+0.10モル%Mg
482 73 100 ΐΛ%Α1Ν 3. 0 単結晶 C r 0. 5 2. 8
49.94モル0 /oGaN
483 75 +49.94モル A1N 3. 0 単結晶 C r 0. 2 3. 1
+0.12モル%Mg
484 75 50 iJ^/oGaN 3. 0 無定形 N i 5. 0 2. 7
+ 50モル0 /0篇
485 80 100モル0 /oAlN 3. 0 配向性 Mo 1. 0 3. 7 多結晶
486 82 99.94モル。/。 GaN 3. 0 無定形 W 2. 0 3. 8
+0.06モル0 /oSi
487 265 100モル%颜 3. 0 単結晶 W 0. 5 3. 9
488 82 99.98モル0/ οΑΙΝ 3. 0 単結晶 P t 0. 5 2. 5
+0.02モル0/ oSi
489 110 100モル0/ οΑΙΝ 3. 0 単結晶 A 1 16 4. 4
490 284 100モル%A1N 3 · 0 単 晶 N i -C r 0. 5 3. 2
491 271 50モル0/ oGaN 3. 0 単結晶 T a 0. 6 3. 4
+ 50モル0/ oIuN
y 305 100モル%GaN 3. 0 単結晶 Ta2N 0. 5 3. 0
49 o 305 100モル%ΙηΝ 3. 0 無定形 T i N 0. 5 4. 0
T i (密着) 0. 1
y 311 1UUセル%AiJ ά . U 単結晶 P t ()、'リア) 0. 2 5. 1
Au (低抵抗) 0. 6
T i (密着) 0. 1
495 311 100モル0 /0細 3. 0 単結晶 W (ハ'リア) 0. 5 5. 4
Au (低抵抗) 0. 8
49.94モル0 /oGaN T i (密着) 0. 1
496 317 +49.94モル颜 3. 0 単結晶 N i (ハ'リア) 1. 8 5. 2
+0.12モル0 /oSi Au (低抵抗) 0. 6
497 317 100モル%GaN 3. 0 単結晶 C r (密着) 0. 1 4. 4
Cu (低抵抗) 0. 8
:表 25〕 419
薄膜導電性材料をあらかじめ形成した A 1 Nを主成分と 窒化ガリウム、 窒化インジウム、 する焼結体からなる基板に形成された各種組成の薄膜 窒化アルミ二ゥムを主成分とする薄膜上 あらかじめ形成された 薄膜の特性 1 に形成された薄膜導電性材料の特性 実験 薄膜導電性材料
No. A 1 N o ¾腫 薄膜導電性 薄膜との
焼結体 薄膜導電性 薄 IIの組成 の 材料の組成 厚み 接合強度: 反射率 作製した 材料の構成 結晶状態 及ぴ構成 ( m) 垂直引張り 実験 No. (Kg/mm2)
498 3 5 7 T i 100リモル%GaN T i N 0 2 3. 9 54
499 358 Τ i 100モル%A1N 単結晶 T i 0 2 4. 0
500 3 59 Τ i 999 モル%(^3_^ 単結晶 C r (密着) 0 1 4. 2 90
+0.06モル0/ oSi Cu (低抵抗) 0 8
5 0 1 360 C r 99.94モル0/ οΙιιΜ 無ハ、、定形 P t 0 5 3. 2 78
+0.06モル%Si
19.98モル%ΙιιΝ T i (密着) 0 1
502 36 1 N i +79.9モル%GaN 単結晶 p t (ハ'リア) 0 2 5. 9 92
+0.12モル0 /oMg Au (低抵抗) 0 6
19.98モル0 /oGaN T i (密着) 0 1
503 362 Mo +79.9モル0/ olnN 無定形 W (Λ'リア) 0 5 5. 6 90
+0.12モル0 /oMg A u (低抵抗) 0 8
499 モル%( 3_!^ T i (密着) 0 1
504 363 ψ +4994モル 定形 N lT i ( ア) 1 8 5. 3 9 1
+01 レ oん CJi A 11 (低氏桥) 0 6
5 0 5 364 ψ C r 0 5 2 6
506 36 5 p t 平 口 Ν ϊ 1 0 67 リ
507 366 A 1 /il 赃 形 Mo 0 5 3. 5 5 5
+002モル%fH
508 367 N i - C r innモル%A1N 辆定形 W 0 2 3. 8 53
499 モル% kNT
5 09 36 8 T a +49.94モル A1N 単結晶 A 1 12 4. 0 9 1
+0.12モル%Si
5 1 0 36 9 T a2N 100モル0 /oGaN 無定形 N i— C r 0 5 3. 3
5 1 1 37 0 T i N 100モル%InN 単結晶 Ta2N 0 . 5 3. 1
T i (密着) 49.94モル0 /oGaN T i (密着) 0 . 1
5 1 2 37 1 P t (Λ*リア) +49.94 WAIN 単結晶 P t 、'リア) 0 2 5. 5 90
Au (低抵抗) +0.12モル0 /oMg Au (低抵抗) 0 6
T i (密着) 69.86モル0 /oGaN 配向性 T i (密着) 0 . 1
513 372 W (ハ'リア) +29.94モル A1N 多結晶 w (ハ'リア) 0 . 5 5. 2 90
Au (低抵抗) +0.20モル0 /oMg Au (低抵抗) 0 8
W 70wt% 69.86モル%GaN W 90wt%
5 14 37 3 +29.94モル颜 単結晶 C u lOwt 0 . 5 5. 7 62
+0.20モル%Si 合金
5 1 5 374 C r (密着) 99.90モル0 /oGaN 単結晶 C r (密着) 0 • 1 4. 4 9 2
Cu (低抵抗) +0.10モル%Mg Cu (低抵抗) 0 • 8
〔表 2 6〕 420
* 1) 実験 No. 599 612の A 1 N焼結体からなる基板にはクロライド VP E法により単結晶 が形成されている。
〔表 28〕 422
使用した基板の特性 三次元光導波路の紫外光伝送特性 実験 •基板 基板に形成した スパッ夕 導波路部分 伝送損失 (dBZcm)
No. の 薄膜の組成 膜材料 の屈折率 測定波長 (nm)
性状 (拡散材料) (650nm) 380 300 270 250
578 100モル%A 1 N GaN 2. 196 0. 3 0. 3 0. 7 1. 6
579 100モル%A 1 I nN 2. 198 0. 5 0. 6 0. 8 1. 8
580 100モル%A 1 N NbN 2. 200 0. 7 0. 7 0. 8 1. 9
581 100モル ¾A 1 N TaN 2. 198 0. 7 0. 8 0. 9 2. 1
582 100モル%A 1 N GaN 2. 196 0. 3 0. 3 0. 7 1. 5
583 100モル%A 1 I nN 2. 199 0. 4 0. 6 0. 9 1. 9
584 100モル%A 1 N GaN 1. 883 3. 6 4. 3 5. 2 8. 2
585 100モル%A 1 I nN 1. 878 3. 9 4. 7 5. 8 8. 9
586 100モル%A 1 NbN 1. 881 4. 1 4. 8 6. 1 9..4
587 99モル? ίΑ 1 Ν GaN 2. 196 0. 4 0. 4 0. 8 1. 6
+ 1モル%GaN
588 90モル%A 1 QaN 2. 216 0. 4 0. 5 0. 8 2. 5
+10モル%GaN
589 80モル%A 1 GaN 2. 250 0. 4 0. 5 0. 9 4. 4
+ 20モル? iGaN
590 50モル%A 1 GaN 2. 329 1. 1 2. 4
+ 50モル%G aN
591 100モル? iGaN I nN 2. 472 2. 4
窒化
592 100モル%GaN NbN 2. 475 2. 3
アルミ
593 100モル%GaN TaN 2. 477 2. 7 一 - ニゥム -
594 100モル%GaN' NbN 2, 122 8. 2
を主成分
595 90モル ¾A 1 N GaN 2. 266 0. 6 0. 6 2. 4 一 とする
+ 10モル% I nN
焼結体
99モル ¾A 1 N
を用いた
596 + 0. 5モル ¾GaN GaN 2. 204 0. 4 0. 4 0. 9 ■2. 1 薄膜基板
+ 0. 5モル% I nN
90モル%A 1
597 +5モル%GaN NbN 2. 247 0. 5 0. 6 1. 7 2. 7
+ 5モル% I nN
70モル%A 1
598 + 1 5モル%G aN TaN 2. 354 0. 8 7. 6 - 一 + 15モル% I nN
599 100モル%A 1 N GaN 2, 209 0. 2 0. 2 0. 4 1. 6
600 99モル%A 1 N GaN 2. 213
+ 1モル%GaN 0. 2 0. 2 0. 5 1. 9
601 90モル%A 1 GaN 2. .224 0. 3 0. 3 1. 3 2. 6
+ 10モル%GaN
602 100モル%A 1 N GaN 2. 210 ≤0. 2 0. 2 0. 4 2. 1
603 100モル%A 1 N I nN 2. 207 ≤0. 2 0. 2 0. 6 2. 5
604 100モル? iA 1 N NbN 2. 209 ≤0. 2 0. 2 0. 6 2. 4
605 100モル%A 1 N TaN 2. 210 ≤0. 2 0. 2 0. 7 2. 6
606 100モル%A 1 N Ga203 2. 208 ≤0. 2 0. 2 0. 5 2. 2
607 100モル%A 1 I n203 2. 209 ≤0. 2 0. 2 0. 6 2. 7
608 100モル%A 1 Nb205 2. 211 ≤0. 2 0. 2 0. 8 2. 5
609 100モル%A 1 N Ta2Os 2. 210 ≤0. 2 0. 2 0. 7 2. 6
610 100モル%A 1 ■ Nb 2. 211 ≤0. 2 0. 2 0. 7 2. 6
611 100モル%A 1 Ta 2. 213 ≤0. 2 0. 2 0. 7 2. 7
612 100モル%GaN I nN 2. 492 1. 6 - - 一
613 形成せず GaN 2. 220 ≤0. 2 0. 2 0. 3 1. 8
614 形成せず I nN 2. 219 ≤0. 2 0. 2 0. 5 2. 1
615 形成せず NbN 2. 223 ≤0. 2 0. 2 0. 5 2. 0
616 A 1 形成せず TaN 2. 218 ≤0. 2 0. 2 0. 5 2. 1
617 パルク 形成せず Ga.2Oa 2. 221 ≤0. 2 0. 2 0. 4 1. 9
618 単結晶 .形成せず I n 203 2. 217 ≤0. 2 0. 2 0. 6 2. 2
619 形成せず Nb206 2. 222 ≤0. 2 0. 2 0. 5 2. 3
620 形成せず Ta2Os 2. 219 ≤0. 2 0. 2 0. 5 2. 4
621 形成せず Ga 2. 213 ≤0. 2 0. 2 0. 3 1. 8
622 形成せず Nb 2. 221 ≤0. 2 0. 2 0. 5 2. 2
623 GaN 形成せず I nN 2. 504 1. 9
624 パルク 形成せず NbN 2. 506 2. 0
1625 単結晶 形成せず TaN 2. 507 1. 8
〔表 29〕
* 1) スパッ夕膜を形成する前の単結晶薄膜の波長 650 nmの光に対する 屈折率は 2. 19017である。
〔表 30〕 424
使用した 窒化ガリウム、 窒化インジウム、 窒化アルミニウムを主成分とする薄膜光導波路の特性
* 1) 実験 No. 669〜673の窒化アルミニウム焼結体基板には窒化アルミニウム多結晶薄 は形成されていない。
〔表 31〕 425
使用した
A 1 N
基板の内容 6
7
8
9
0 2
3
4
5
6
7
8
9
0 実験 No.
49で作製
のもの
2
3
4
5
6
7
8
9
0
2
3
4
5
6
7
8
9
: 1) I P:イオンプレーティング法の略である。 2) CV:クロライド VPE法の略である。
〔表 32〕 426
* 1) CV:クロライド VPE法の略である。
* 2) A 1 N: 5. 0重量%含有のタングステン導通ビアを形成した E: sO。: 4. 02体積%含有の A 1 N焼結体。
〔表 33〕
窒化アルミニウムを主成分とする焼結体に形成した薄膜の特性
薄膜 薄膜 単結晶薄膜、及ぴ 薄膜基板 実験 使用した の 薄膜 薄膜 の 配向性多結晶の の 0. A 1 形成状態 の 薄膜の組成 の 抵抗率 (002)X線回折 表面粗さ 基板の内容 及び 作製方法 結晶 ロッキングカーブ
形成位置 状態 (Ω · cm) の半値幅 Ra
(秒) nm)
766 単層 スパッタ 99. 98モル ¾GaN 無定形 0. 14 一 4. 4
+ 0. 02モル%S i
767 単層 スパッタ 99. 98モル% I nN 多結晶 0. 084 ― 3. 7
+ 0. 02モル%S i
768 単眉 スパッタ 99. 98モル%A 1 配向性 115 7930 1 , 5
+ 0. 02モル%S i 多結晶
769 単層 MOCVD 99. 98モル ¾A 1 N 配向性 91 4560 1. 7
+ 0. 02モル%S i 多結晶
実験 No. ■¾ y . y 9 -tノレ; ¾ A 1 IN
770 4 qで 鰓 単層 MOCVD + 49. 99モル%GaN 多結晶 0. 87 4390 1. 6 したもの + 0. 02モル%S i
771 単層 MOCVD 99. 98モル%A 1 N 単結晶 89 171 7. 1
+ 0. 02モル% S i
772 単層 MOCVD 99. 98モル? iGaN 単結晶 0. 019 157 6. 3
+ 0. 02モル%S i
773 単層 MOCVD 99. 98モル? iG aN 単結晶 0. 116 182 5. 9
+ 0. 02モル ¾Mg
79. 90モル%GaN
774 単層 MOCVD + 19. 98モル%I nN 単結晶 0. 052 192 4. 8
+ 0. 12モル%Mg,
79. 99モル。/。 GaN
775 単層 MOCVD + 19. 99モル% I n N 単結晶 0. 006 197 4. 6
+ 0. 01モル%S i
+ 0. 01モル%Zn
W
428
〔表 34〕
窒化アルミニウムを主成分とする焼結体に形成した薄膜の特性
薄膜 薄膜 単結晶薄膜、及び 薄膜基板 実験 使用した の 薄膜 難 の 配向性多結晶の の
No. A 1 N 形成状態 の 薄膜の粗成 の 抵抗率 (002)X線回折 表面粗さ 基板の内容 及び 作製方法 結晶 ロッキングカープ
形成位置 状態 (Ω · cm) の半値幅 Ra
(秒) ^nm) 基板側 スパヅタ 99. 98モル%A 1 N 配向性 104 8330 1 9
776 + 0. 02モル%S ί 多結晶
表面層 MOCVD 99. 98モル%A 1 単結晶 82 88 0. 94
+ 0. 02モル%S i
基板側 スパッタ 99. 98モル%A 1 N 配向性 106 7920 1. 6
777 + 0. 0 βモル%S i 多結晶
表面層 MOCVD 99. 98モル%GaN 単結晶 0. 013 90 1. 01
+ 0. 0 έモル%S i
基板側 スパッタ 99. 98モル%A 1 N 配向性 99 8070 1. 7
778 + 0. 02モル%S i 多結晶
表面層 MOCVD 99. 98モル%GaN 単結晶 0. 099 87 0. 92
+ 0. 02モル%Mg
基板側 スパッ夕 99. 98モル%A 1 N 配向性 107 7750 1. 5
+ 0. 02モル%S i 多結晶
779 79. 90モル0/。 G aN
表面層 MOCVD + 19. 98モル% I n N 単結晶 0. 043 95 0. 87
+ 0. 12モル%Mg
基板側 スパッタ 99. 98モル%A I N 配向性 111 8130 1. 6 実験 No. + 0. 02モル%S i 多結晶
780 49で作製 79. 99モル%GaN
したもの 表面層 MOCVD + 19. 99モル0/。 I nN 単結晶 0. 005 89 0. 91
+ 0. 01モル%S i
+ 0. 01モル%Zn
49. 99モル%A 1 N 配向性
基板側 MOCVD + 49. 99モル%GaN 多結晶 0. 84 4490 1. 8
781 + 0 02モル%S i
表面層 MOCVD 99. 98モル A 1 N ¾¾¾ 79 82" 1. 00
+ 0. 02モル%S i
49. 99モル%A 1 N 配向性
基板側 MOCVD + 49. 99モル%GaN 多結晶 0. 79 4520 1. 9
782 十 0. 02モル%S i
表面層 MOCVD 99. 98モル%GaN 単結晶 0. 010 84 0. 96
+ 0. 02モル%S i
49. 99モル%A l'N 配向性
基板側 MOCVD + 49. 99モル%GaN 多結晶 0. 92 4170 1. 6
783 + 0. 02モル%S i
表面眉 MOCVD 99. 98モル%G aN 単結晶 0. 093 81 0. 95
+ 0. 02モル%Mg
49. 99モル%A IN 配向性
基板側 MOCVD + 49. 99モル%GaN 多結晶 0. 80 4710 1. 6
784 + 0. 02モル%S i
79. 90モル。/。GaN
表面層 MOCVD + 19. 98モル。/。 I nN 単結晶 0. 036 32 0. S 8
+ 0. 12モル%Mg
49. 99モル%A 1 N 配向性
基板側 MOCVD + 49. 99モル%GaN 多結晶 0. 93 4560 1. 7
+ 0. 02モル%S i
785 79. 99モル%GaN
表面層 MOCVD + 19. 99モル0メ01 n N 単結晶 0. 005 80 0. 90
+ 0. 01モル%S i
+ 0. 01モル%Zn
〔表 3 5〕
る。
〔表 36〕
* 1 添加 の Sは酸化物換算による。
〔表 3 7〕
* の による。
〔表 38〕
* 1) 添加物の量は元素換算による。
〔表 3 9〕
* 1 ) 添加物の量は元素換算による。
但し、 アル力リ土類金属及び希土類金属成分の添加量は酸化物換算による。
〔表 4 0〕
1 ) 添加物の量は元素換算による重量%で示してある。
但し、 アル力リ土類金属及び希土類金属成分の添加 は酸化物換算による体積%で示す。
〔表 41〕
焼結体基板の特性 各種焼結体からなる基板に^成した薄膜の特性
あらかじめ各種基板に形成した あらかじめ各種基板に形成した
実験 表面の A 1 N薄膜 A 1 N薄膜の上からさらに形成した薄膜
No. 主成分 平滑度
Ra 結晶状摔 口 キンク'カープ の 荷臈の翊成 キンク'为一ブ (nm) の半値轉 厚み の半値幅
(秒) 、" m) (秒)
945 (^成せず) 3, 0- 100モル%Α 1 Ν 255
946 (形成せず) 3. 0 100モリレ%0 aN 279
947 (形成せず) 3 0 100モレ% I nN 283
948 無定形 3 0 100モル%A 1 N 169
949 炭化珪素 6. 8 多結晶 3. 0 100モル%A 1 186
950 配向性多結晶 9640 3. 0 100モ 1^%A 1 N 140
951 単結晶 262 3 0 100モル%A 1 N 192
952 実施例 11 配向性多結晶 9900 3. 0 10
、 で作製 J 0モル%GaN 147
953 配向性多結晶 9780 3. 0 100モル% I nN 144
954 (形成せず) 3. 0 50モル0 /οΑΙΝ+50モル0 /oGaN 269
955 配向性多結晶 9540 3. 0 50モル0/ οΑΙΝ+50モル0 /0GaN 139
956 (形成せず) 3. 0 100モル%A 1 N 493
957 (形成せず) 3 0 100モル%G aN 508
958 窒化珪素 15 (形成せず) 3 0 100モレ% I nN 647
959 無定^ 3. 0 100モル%A 1 188
960 " 実施例 1, 配向性多結晶 10880 3. 0 100モル%A 1 N 163
961 で作製 J 配向性多結晶 11830 3. 0 100モル%G aN 166
962 配向性多結晶 12070 3. 0 100モル I nN 167
963 (形成せず) 3. 0 100モル%A 1 N 389
964 (形成せず) ― 3. 0 100モル%GaN 421
965 (^成せず) 3. 0 100モル% I nN 426
966 無定形 3. 0 100モル%A 1 N 169
967 酸化 多結晶 3, 0 100モル%A 1 N 174
968 アルミ 11 配向性多結晶 10490 3. 0 100モル%A 1 N 155
969 ニゥム 単結晶 344 3. 0 100モル%A 1 N 195
970 配向性多結晶 10720 3. 0 100モリレ%0 aN 161
971 配向性多結晶 11310 3. 0 100モル% I nN 163
972 実施例 1
L (形成せず) 3. 0 50モル%AlISf+50モル0/ oGaN 377
973 で-作製 」 配向性多結晶 10550 3. 0 50モル%Al>i+50モル%GaN 159
974 (形成せず) 3. 0 100モル%A 1 N 258
975 ( 成せず) 3. 0 100モル%G a N 291
976 (形成せザ) 3 , 0 100 ^z) % I nN 285
977 ^1形 3. 0 100モル% A 1 182
978 酸化亜鉛 結晶 3 0 100モル A 1 N 189
979 8. 8 配向性多結晶 9450 3. 0 100モル%A 1 N 139
980 単結晶 261 3. 0 100モル%A 1 N 196
981 実施例 1 配向性多結晶 9800 3. 0 100モル GaN 144
982 で作製 _J 配向性多結晶 9740 3. 0 100モル% I nN 142
983 (形成せず) 3. 0 50モル0 /0扁+50モル0 /oGaN 275
984 配向性多結晶 9510 3. 0 50モル0 /oAlN+50モル0 /oGaN 136
985 (形成せず) 3. 0 100モル%A 1 N 268
986 (形成せず) 3. 0 100モル%GaN 284
987 (形戍せず) 3. 0 100モル% I nN 290
988 酸化 配向性多結晶 9520 3. 0 100モル%A 1 140 -
989 ペリリウム 9. 4 単結晶 271 3. 0 100モル%A 1 N 202
990 配向性多結晶 9810 3. 0 100モル%GaN 146
991 配向性多結晶 9690 3. 0 100モル% I nN 143
992 実施例 Γ '(形成せず) 3. 0 50モル%AlN+50モル%GaN 275
993 で作製
ノ 配向性多結晶 9580 3. 0 50モル。AiN+50モル%GaN 137
〔表 4 2〕
〔表 43〕 437
焼結体基板の特性 各種焼結体からなる基板に^成した薄膜の特性
表面の あらかじめ基板に形成した薄膜 あらかじめ基板に形成した溥膜 実験 平滑度 の上からさらに形成した薄膜
No. 主成分 難の (002)X線回折 (002)X線回折
Ra 薄膜の組成 形成方法 結晶状態 ロッキングカーブ 薄膜の組成 ロッキングカープ
(nm) の半値幅 (秒) の半値幅 (秒)
1037 100モル0 /0趣 スパッ夕 無定形 ― 100モル%A1N 165
1038 6. 8 100モル%A1N スパヅ夕 配向性多結晶 9590 100モル%A1N 139
1039 100モル0 /0細 MOCVB 配向性多結晶 7820 100モル0 /0GaN 132
1040 炭化珪素 100モル0 /0趣 スパッ夕 無定彤 - 100モル0/。 A1N 124
1041 100モル0 /0趣 スパッタ 多結晶 一 100モル%A1N 126
1042 100モル0 /0纖 スパ'クタ 配向性多結晶 7710 100モル0 /0篇 109
1043 実施例 1 2. 9 100モル%Α1Ν OCVD 単結晶 207 100モル0 /0趣 127 .
1044 で作製 100モル0 /0趣 MOCVD 配向性多結晶 6620 100モル0 /0GaN 107
1045 100モル0 /0GaN MOCVD 配向性多結晶 6880 100モル0 /0GaN 116
1046 100モル%InN MOCVD 配向性多結晶 6910 100モル%GaN 113
1047 100モル%A1N スパッタ 無定形 100モル%A1N 189
1048 15 100モル0 /0颜 スパッタ 配向性多結晶 11910 100モル0 /0細 169
1049 窒化珪素 100モ)%編 スパッタ 配向性多結晶 12030 100モル0 /0GaN 173
1050 100モル%A1N スパッタ 無定形 ― 100 Ϊ^%Α1Ν 125
1051 100 ΐル0 /0扁 スパッタ 多結晶 - 100モル0 /0細 128
1052 実施例: f| 4. 4 100モル0 /0篇 スパッタ 配向性多結晶 7760 100モル%Α1Ν 110
1053 しで作製 」 100モル0 /0通 MOCVD 単結晶 15 100モル%扁 129
1054 100モル%Α1Ν スパッタ 配向性多結晶 7680 100 %GaN 109
1055 100モル0 /0(3aN MOCVD 配向性多結晶 6780 100モル0 /oGaN 113
1056 100モル0 /0細 スパッ夕 無定形 ― 100モル0 /0趣 177
1057 11 100モル%A1N スパッ夕 配向性多結晶 10630 100モル%颜 159
1058 100モル%A1 スパッ夕 配向性多結晶 10570 100モル0 /oGaN 154
1059 100モル%A1N スパッ夕 無定形 ― 100モル%扁 157
1060 酸化 100モル0 /0趣 スパッタ 多結晶 100モル%A1N 162
1061 アルミ 7. 3 100モル%A1N スパヅ夕 配向性多結晶 9480 100モル0 /0蕭 136
1062 ニゥム 100モル0 /oAlN MOCVD 単結晶 247 100モル0 /οΑΙΝ 186
1063 100 ΐ^%ΑΐΝ MOCVD 配向性多結晶 7460 100モル0 /oGaN 132
1064 100モル0 /oGaN MOCVD 配向性多結晶 7630 100モル0 /oGaN 134
1065 100モル0 /0趣 スパッタ 無定形 - 100モル0 /0 1 3
1 066 100モル%趣 スパッ夕 多結晶 - 100モル%崖 126 実施例
1067 100モル0 /0颜 スパッタ 配向性多結晶 7580 100モル0/ 0扁 106 で作
1068 sa j
100モル%趣 MOCVD 単結晶 205 100モル0 /0扁 127
1069 1, 9 100モル0 /οΑΙΝ MOCVD 配向性多結晶 6550 100モル0 /oGaN 105
1070 100モル0/ 0篇 スパッタ 配向性多結晶 7710 50モル0 /oGaN 109
+50モル%InN
1071 100モル0 /oGaN MOCVD 配向性多結晶 6760 100モル%GaN 111
1072 100モル%InN MOCVD 配向性多結晶 6860 100モル%GaN 116
1073 100モル%A1 スパッ夕 無定形 一 100モル%A1N 170
1074 8. 8 100 ΐί^οΑΙΝ スパッ夕 配向性多結晶 9560 100モル%A1N 137
1075 100 ΐル%删 スパッ夕 配向性多結晶 9420 100モル0 /oGaN 135
1076 酸化亜鉛 100モル0 /0細 スパッ夕 無定形 一 100モル%A1N 1 2 1
1077 100モル0 /0細 スパッ夕 多結晶 ― 100モル0 /0雇 124
1078 100モル%Α1Ν スパッタ 配向性多結晶 7510 100モル0/ 0颜 104
1079 '実施例 Γ 100 ΐΛ%Α1Ν MOCVD 単 晶 211 100モ 扁 127
1080 で作製 2. 6 100モル0 /οΑΙΝ MOCVD 配向性多結晶 6480 100モル%GaN 103
1081 100モル0 /0擺 スパッタ 配向性多結晶 7600 50モ! N 107
+50モル%GaN
1082 100モル0 /oGaN MOCVD 配向性多結晶 6730 100モル%GaN 110
1083 100モル0 /oInN MOCVB 配向性多結晶 6790 100モル0 /oGaN 113
1084 100モル0 /οΑΙΝ スパッ夕 無定形 100モル。/ 0屬 166
1085 9. 4 100モル0 /0細 スパッ夕 配向性多結晶 9750 100モル0 /0扁 141
1086 酸化 100モル。/。 A1N スパッ夕 配向性多結晶 9570 100モル0 /0GaN 138
1087 ペリ 100モル。/。 A1N スパッタ 無定形 100モル%A1N 1 4
1088 リウム 100モル。/。 A1N スパッ夕 多結晶 100モル0 /οΑΙΝ 127
1089 3. 7 100モル%A1N スパッタ 配向性多結晶 7650 100モ)%A1N 111
1090 実施例 Γ| 100モル%A1N MOCVD 単結晶 216 100モル0 /0篇 128
1091 で作製 1 100モル0 /0細 スパッ夕 配向性多結晶 7690 100モル0 /oGaN 109
1092 100モル。 /oGaN MOCVD 配向性多結晶 6320 100モル0 /oGaN 114
〔表 4 4〕 438
酸化亜鉛を主成分とする 酸化亜鉛を主成分とする焼結体からなる基板に形成した薄膜の特性 焼結体からなる基板の特性
実験 組成 あらかじめ酸化亜鉛を主成分とする焼結体 あらかじめ基板に形成した薄膜
No. rアルミニウム 1 '抵抗率 光透過率 からなる基板に形成した薄膜 の上からさらに形成した薄膜 成分含有 s J (002)X線回折 (002)Χ線回折
(モル%; (Ω · cm) 薄膜の組成 結晶状態 ロッキングカーブ 鹉膜の組成 ロッキングカーブ
A l 203換算) (室温) (¾) の半値幅 (秒) の半値幅 (秒)
1150 0. 000 > 16 (形成せず) 一 ― 100 ΐ> ΑΐΝ 255
1151 1X108 100モル0 /0趣 配向性多結晶 9430 100モル%Α1Ν 136
1152 6. 8 (^成せず) - 100モル%Α1Ν 187
1153 0. 002 X 101 22 100モル%A1N 無定形 100モル0 /0颜 126
1154 100モル0 /0颜 配向性多結晶 8190 100モル%Α1Ν 107
1155 0. 008 7. 9 24 (形成せず) 一 - 100モル0/ 0颜 159
1 156 100 100モル。/。 A1N 配向性多結晶 7620 100 ΐΙ^/οΑΙΝ 97
1 157 0. 03 7. 4 27 (形成せず〉 一 一 100モル%GaN 138
1158 X 10一1 100モル0 /0細 配向性多結晶 7690 100モル%GaN 95
1159 8. 4 (^成せず) - 一 100 ΐ^%Α1Ν 126
1160 0. 10 X 10— 2 36 100モル%A1N 配向性多結晶 7490 100モル%Α1Ν 94
1161 100モル%A1N 配向性多結晶 7650 100モル0 /oGaN 93
1 1 62 0. 3 0 7. 7 44 (形成せず) - , - 100モル。/ QAIN 1 25
1163 X 10— 3 100モル0/ 0細 配向性多結晶 7540 100モル%扁 93
1164 2. 9 (形成せず) 100モル0/。細 1 1
1165 1. 0 X 1 o— 3 53 100 %Α1Ν 無定形 100 β Α1Ν 96
1166 100モル0 /οΑΙΝ 配向性多結晶 7470 100モル0 /0蕭 89
1167 (Ji成せず) ― 100モル%趣 112
1168 (形成せず) ― ― 100モル0ノ oGaN 118
1169 (^成せず) - ― 100モル%InN 119
1170 100モル0/ 0細 無定^ ― 100モル0 /0篇 94
1171 100モル0/ 0扁 多結晶 ― 100モル0 /οΑΙΝ 96
1172 1. 6 100モル0 /0趣 配向性多結晶 7350 100モル0 /0蕭 86
1 173 3. 0 X 10一3 56 100モル0 /0編 配向性多結晶 7320 100モル%GaN 88
1174 100モル%A1N 配向性多結晶 7460 100モル%ΙηΝ 89
1175 100モル0 /0扁 配向性多結晶 7390 50モル%Α1Ν 87
+50モル0/ oGaN
1176 100モル0 /0扁 単結晶 115 100モル0趣 96
1177 100モル%GaN 無定形 ― 100モル0/ 0篇 93
1178 100モル0/ 0GaN 配向性多結晶 7180 100 ΐ^%Α1Ν 88
1179 100モル0 /olnN 配向性多結晶 7240 100モル0/ 0細 90
1180 (形成せず) - - 100モル0 /0篇 118
1181 6. 3 100モル%扁 配向性多結晶 7410 100モル0/ 0Α1Ν 88
1182 10. 0 X 10一3 52 100モル0 /0趣 配向性多結晶 7390 100 ΐル0 /oGaN 91
1183 100モル0 /0扁 配向性多結晶 7440 50モル0/。 GaN 89
+50モル0 /olnN
1184 20. 0 8. 9 42 (形成せず) 一 - 100モル0 /olnN 119
1185 X 10一3 100モル0 /0細 配向性多結晶 7510 100モル%InN 92
1186 8. 2 (形成せず) - 100モル0/ 0GaN 127
1187 30, 0 X 10-2 33 100モル0/ 0篇 無定形 - 100モル0 /oGaN 96
1188 100モル%A1N 配向性多結晶 7500 100モル%GaN 91
1189 7. 8 (形成せず) - ― 100モル °/οΑ1Ν 136
1190 40. 0 X 10— 1 31 100モル%A1N 配向性多結晶 7570 100モル0 /οΑΙΝ 94
1191 100モル0 /0趣 配向性多結晶 7530 100モル%InN 97
1192 50. 0 > 17 (形成せず) 100モル%Α1Ν 229
1193 1 X 108 100モル0/ 0細 配向性多結晶 9260 100モル%Α1Ν 134
1194 1. 0 8. 7 6. 9 (形成せず) 100モ 扁 227
1195 (Fe 203) X 10一1 100モル0 /0細 配向性多結晶 8710 100モル0/ 0扁 124
1196 1. 0 3. 4 9. 2 (形成せず) 100モル0 /oGaN 220
1197 (C r 203) X 10 100モル0 /0篇 配向性多結晶 8890 100モル%GaN 119
1198 0. 04 > 57 (形成せず) 100モル0/。篇 192
1199 (Y203) 1 X 108 100モル0 /0細 配向性多結晶 7770 100モル%Α1Ν 104
1200 0. 04 > 53 (形成せず) 100モル0 /oGaN 206
1201 (Er 203) 1X 108 100モル0 /0趣 配向性多結品 7940 100 tJl- GaN 107
1202 0. 04 > 54 (形成せず) 100モル%Α1Ν 203
1203 (Yb203) 1 X 108 100モル。/。 A1N 配向性多結晶 7860 100 β ΑΐΝ 109
〔表 4 6〕 440
酸化アルミニウムを主成分とする焼結体からなる基板特性 基板に形成した雜膜の特性 焼結体組成 予め基板に形成 あらかじめ基板に形成した薄膜 実験 〔成分含有 i2〕 光透過率 した A1N配向性 の上からさらに形成した簿膜
No. (モル ;酸化物換算) 多結晶薄膜の (002)X線回折 含有成分 (%) ロッキングカープ 薄膜の組成 ロッキングカーブ マグネシウム カルシウム 珪素 その他の成分 の半値幅 (秒) の半値幅 (秒)
1322 0. 0000 0. 0000 0, 0000 0. 0000 18 一(形成せず) 100モル0 /0崖 274
1323 (添加せず) 9720 100モル%A1N 142
1324 0. 0000 0. 0005 0. 0000 0. 0000 17 一(形成せず) 100モル0 /0應 215
1325 (添加せず) 9240 100モル0/ 0應 133
1326 0, 0000 0. 0000 0. 0020 0. 0000 24 一(^成せず) 100モル0 /οΑΙΝ 187
1327 (添加せず) 8660 100モル0/ 0扁 122
1328 0. 010 0. 000 0. 000 0. 000 43 一(形成せず) 100モル0 /0颜 156
1329 (添加せず) 7810 100モル0 /οΑΙΝ 96
1330 0. 000 0. 050 0. 000 0. 000 36 ― (^成せず) 100モル0/ 0扁 140
1331 '(添加せず) 7830 100モル%扁 97
1332 0. 12 0. 00 0. 00 0. 00
o 51 ― (形成せず) 100モル0 /oGaN 119
1333 (添加せず) 7350 100モル0 /0GaN 92 o
1334 0. 60 0. 00 0. 20 0. 00 47 ― (形成せず) 100モル0/ 0扁 116
1335 (添加せず) 7310 100モル%眉 93
1336 1. 20 0. 00 0. 00 0. 00 57 一(形成せず) 100 tJ^/oGaN 114
1337 (添加せず) 7260 100モル0 /oGaN 90
1338 1. 00 0. 20 0. 00 0. 00 55 ― (形成せず) 100モル0 /οΑΙΝ 113
1339 (添加せず) 7240 100モル%A1N 91
1340 0. 00 1. 00 1, 00 0. 00 27 一(形成せず) 100モル0/ 0扁 124
1341 (添加せず) 7690 100モル%A1N 96
1342 0. 60 0. 80 0. 80 0. 00 46 一(形成せず) 100モル0 /oGaN 120
1343 (添加せず) 7740 100モル0 /oGaN 94
1344 3. 00 0. 00 0. 00 0. 00 52 一(^成せず) 100モル%A1N 117
1345 (添加せず) 7270 100モル0/ 0扁 92
1346 2. 00 2. 00 4. 00 0. 00 50 一(形成せず) 100モル0/ 0扁 119
1347 (添加せず) 7480 100モル0 /οΑΙΝ 93
1348 10. 00 0. 00 0. 00 0. 00 47 ― (形成せず) 100 D oAlN 1 4
1349 (添加せず) 7520 100 WoAm 96
1350 6. 00 2. 00 8. 00 0. 00 41 ― (^成せず) 100モル%GaN 125
1351 (添加せず) 7450 100モル0 /0GaN 92
1352 2. 00 2. 00 26. 00 0. 00 44 - (形成せず) 100モル0 /0眉 126
1353 (添加せず) 7670 100モル%A1N 96
1354 0. 00 20. 00, 20. 00 0. 00 22 ― (形成せず) 100 ΐ^%Α1Ν 1 1
1355 (添加せず) 7830 100モル%遍 97
1356 20. 00 0. 00 30. 00 0. 00 6. 4 一(形成せず) 100モル%Α1Ν 226
1357 (添加せず) 9370 100モル0 /οΑΙΝ 1 7
1358 0. 000 0. 050 0. 000 37 ― (形成せず) 100モル%趣 137
1359 7760 100モル0 /0應 95
1360 1. 20 0. 00 0. 00 0. 040 59 - (形成せず) 100モル0 /oGaN 112
1361 (Y203) 7250 100モル0 /oGaN 89
1362 1. 20 0. 00 0. 00 0. 040 56 - (形成せず) 100モル0/ 0颜 115
1363 (Ho203) 7310 100モル0 /0颜 91
1364 1. 20 0. 00 0. 00 0. 0 0 58 - (形成せず) 100モル%GaN 115
1365 (Yb203) 7290 100モル0 /oGaN 90
1366 0. 000 1. 00 1. 00 0. 0005 33 一(形成せず) 100モル0 /0眉 118
1367 (Y2O3) 7600 100モル0 /οΑΙΝ 94
1368 0. 60 0. 80 0. 80 0. 0080 57 一 (^成せず) 100 ¾%A1N 111
1369 (Y2O3) 7390 100モル0 /0雇 92
1370 0. 60 0. 00 0. 20 0. 0 0 69 一(形成せず) 100 /οΑΙΝ 112
1371 (Y203) 7480 100モル0/ 0扁 91
1372 0. 000 1. 0Ό 1. 00 8. 0 36 - (形成せず) 100 ^%GaN 121
1373 (Y2O3) 7680 100モ GaN 94
1374 0. 000 1. 00 1. 00 12. 0 27 ― (形成せず) 100モル0 /0簾 124
1375 (Y2O3) 7830 100モル%A1N 97
1376 1. 00 0. 20 0. 00 0. 0 0 82 ― (形成せず) 100モ οΑΙΝ 107
1377 (Y2O3) 7070 100モル%AIN 88
1378 1. 00 0. 20 0. 00 0. 040 78 一(形成せず) 100モル0 /0扁 113
1379 (Dy203) 7240 100モ 應 90
1380 1. 00 0. 20 0. 00 0. 040 81 ― (形成せず) 100モル0 /0GaN 109
1381 (Er2Oa) 7160 100モル0 /oGaN 89
〔表 49〕
焼結体基板の特性 各種焼結体からなる基板に形成した薄膜の特性
あらかじめ基板に形成した薄膜 あらかじめ基板に形成 主成分 平均 した薄膜の上からさらに 実験 表面 光 ^成した薄膜
No. 〔焼結助剤、 粗さ 透過率 (0 0 2) (0 0 2) 及び添加剤〕 薄膜 X線回折 5線回折 薄膜の組成 の 結晶状態 ロッキング 薄膜の組成 ロッキング
(焼成法) 形成方法 カーブ カーブ
R a (%) の半値幅 の半値幅 (nm) (秒) (秒)
1 3 8 2 酸化 100 %Α1Ν スパッ夕 無定形 ― 100モル%A1N 1 8 7
1 3 8 3 ジルコニウム 7. 1 2 7 100モル0 /0趣 スパッ夕 配向性多結晶 9 6 7 0 100モル%A1N 1 8 0
1 3 84 〔γ2ο3〕 100モル0 /0細 MOCVD 配向性多結晶 7 9 7 0 100モル0 /oGaN 1 6 3 (大気中焼成)
1 3 8 5 酸化 100モル0 /0細 スパッ夕 無定形 100モル%A1N 1 3 7
1 3 8 6 ジルコニウム 100モル%Α1Ν スパッ夕 多結晶 - 100 ¾[<%Α1Ν 1 3 8
1 3 8 7 〔γ2ο3〕 4. 2 5 9 100モル0編 スパッタ 配向性多結晶 7 8 2 0 100モル0 /0趣 1 3 3
1 3 8 8 100モル0 /0趣 MOCVD 配向性多結晶 6 5 7 0 100モル0 /oGaN 1 1 8
1 3 8 9 (ホット 100 %GaN MOCVD 配向性多結晶 6 8 0 0 100モル%GaN 1 2 0
1 3 9 0 プレス) 100モル0 /oInN MOCVD 配向性多結晶 7 0 9 0 100モル0 /oGaN 1 2
1 3 9 1 酸化 100モル0颜 スパッ夕 無定形 100モル%Α1Ν 1 8 5
1 3 9 2 マグネシウム 7. 9 34 100モル0 /0趣 スパッ夕 配向性多結晶 942 0 100モル0 /0超 1 7 1
1 3 9 3 〔助剤なし〕 100モル%編 スパッ夕 配向性多結晶 9 24 0 100モル0 /oGaN 1 6 6 (大気中焼成)
1 3 94 100モル%A1N スパッタ 無定形 一 100モル0 /0趣 1 3 9
1 3 9 5 . 酸化 100モル0 /0篇 スパッ夕 多結晶 一 100モル%篇 1 4
1 3 9 6 マグネシウム 100モル0 /0顺 スパッ夕 配向性多結晶 7 8 S 0 100モル0 /0扁 1 1 9
1 3 9 7 〔C aO 4. 4 8 3 100モル0 /0細 MOCVD 配向性多結晶 6 940 100モル0 /oGaN 1 2 0
1 3 9 8 + Y203〕 100モル0/ 0顺 スパッタ 配向性多結晶 7 7 3 0 50モル0/ oGaN 1 2 2
+50モル%InN
1 3 9 9 (大気中焼成) 100モル%GaN MOCVD 配向性多結晶 6 9 5 0 100モル0 /oGaN 1 5
1 0 0 100モル%InN MOCVD 配向性多結晶 7 1 7 0 100モル%GaN 1 2 6
1 0 1 アルミン酸 100モル0/ 0顺 スパッ夕 無定形 100モル%A1N 1 9 1
1 40 2 マグネシウム 8. 4 3 2 100モル。/。 A1N スパヅ夕 配向性多結晶 944 0 100モル0 /0細 1 5 7
140 3 〔助剤なし〕 100モル0/ 0扁 スパッ夕 配向性多結晶 9 6 2 0 100モル%GaN 1 54 (大気中焼成)
1 404 100モル0 /0細 スパッ夕 無定形 100モル0 /0趣 1 44
1 40 5 アルミン酸 100モル0 /0娜 スパッ夕 多結晶 100モル0 /0扁 1 49
1 0 6 マグネシウム 100モル0 /0颜 スパッ夕 配向性多結晶 8 5 9 0 100モル%A1N 1 34
140 7 〔C a〇 5. 7 7 9 100モル0 /0續 MOCVD 配向性多結晶 7 1 6 0 100モル%GaN 1 24
140 8 +γ2ο3〕 100モル0 1N スパッ夕 配向性多結晶 7 9 7 0 50モル0/。趣 1 2 8
+50モル%GaN
1 4 0 9 (水索中焼成〉 100モル0 /oGaN MOCVD 配向性多結晶 7 140 100 iJ^/oGaN 1 2 2
14 1 0 100モル0/ JnN MOCVD 配向性多結晶 7 3 1 0 100モル0 /oGaN 1 2 9
1 41 1 酸化 100モル%A1N スパッ夕 無定形 100モル%A1N 1 7 7
14 1 2 イツ卜リウム 6. 9 42 100モル0 /0細 スパッ夕 配向性多結晶 9 3 3 0 100モル0 /0趣 1 5 2
14 1 3 〔助剤なし〕 100 B%A1N スパッタ 配向性多結晶 94 1 0 100モル%GaN 1 5 5 (大気中焼成)
1 14 100モル%扁 スパッ夕 無定形 100モル%A1N 1 3 9
14 1 5 酸化 100モル0 /0細 スパッタ 多結晶 100モル0 /0趣 1 4 1
141 6 イツ卜リウム 100モル0 /0扁 スパッ夕 配向性多結晶 7 7 6 0 100モル%A1N 1 2 6
1 1 7 〔Dy 2〇3 7. 6 ' 8 2 100モル ¾腿 MOCVD 配向性多結晶 6 5 1 0 100モル0 /oGaN 1 1 5
1 1 8 +Ho 203〕 100モル%GaN MOCVD 配向性多結晶 6 740 100モル%A1N 1 1 2
14 1 9 100モル0 /oGaN MOCVD 配向性多結晶 6 6 9 0 100モル。 /QGaN 1 1 7
142 0 (水素中焼成) 100モル%InN MOCVB 配向性多結晶 7 1 7 0 100モル%GaN 1 2 1
〔表 50〕 444
発光素子作製に用いた窒化アルミニウムを主成分とする焼結体からなる墓板の特性
窒化アルミニウムを主成分と 基板に形成した薄膜の特性 作製した発光素子の特性 する焼結体からなる基板の特性 薄膜
* 1) 導通ビアが形成されている
* 2) A 1 N単一相 (助剤が拇散しており A 1 N100%に近い。 表 11に組成についての詳細を示す)。
* 3) A 1N単一相 (助剤が揮散しており A 1 N100%に近い。 助剤の Y Ca成分それぞれ 0. 5 ppm以下である)。
* 4),タングステン: 90重量%、 銅: 10重量%の組成を有する W/Cu合金である。
* 5) タングステン: Ί 0重遞%、 銅: 30重量%の組成を有する W/Cu合金である。
* 6) 基板にあらかじめ形成した第 1層目の薄膜の結晶状態はそれぞれ、 無定形: A、 多結晶: P、 配向性多結晶: 0、 単結晶: Sで示した。 なお、 実験 No. 1455 1456 1468で形成した G aN薄膜は S iド一プの導電性を有するものである。
〔表 51〕 445
発光素子作製に用いた各種セラミック材料を主成分とする焼結体からなる基板の特性
各種セラミック材料を主成分とする 基板に形成した薄膜の特性 作製した発光素子の特性 焼結体からなる基板め特性
* 1) 重 S%で示す。 * 2) : 99. 0 (突験 No,
ホ 3) 焼結助剤を用いず原料だけで作製 (実験 No. 50〜1 1 5 1で作製)。 * 4) : 9 9. 992 (実験 No. 1 1 56で作製のもの〉。 氺 5) 9 9. 9 (卖験 No 1 5 9〜: L 1 6 1で作製のもの)。 * 6) : 99. 7 (突験 No. 1 1 62- 1 1 63で作製のもの)。 氺 7) 97. 0 (突験 NO 1'67〜: L 1 79で作製のもの)。 * 8) : 99. 93 (実験 No, 1 1 8- 12 1 9で作製のもの)。 氺 9) 9 9. 66 (実験 No 23 6〜: I 237で作製のもの)。 * 1 0) : 9 6. 96 (実験 No. 1 240' 1241で作製のもの)。
* 1 1) 00 (実験 No 262〜1 263で作製のもの)。 * 12) : 99. 55 (実験 No. 1 276' 1 7 7で作製のもの)。 氺 1 3) 99. 5 1 ((突突験験 NNoo. 1 3 1 2〜1 3 1 3で作製のもの)。 * 14) : 99. 5 1 (実験 No. 1 30 6' 1 30 7で作製のもの)。 * 1 5) 98. 80 ((実実験験 NNoo. 1 336〜1 337で作製のもの)。 Ψ 1 6) : 98. 7 6 (実験 No. 1 37 8' 1 379で作製のもの)。 * 1 7): 98. 76 (突験 No. 1376〜1377で作製)。 * 1 8)焼結助剤を用いず原料だけで作製(実験 No. 1 12〜141 3で作製)。 * 1 9) 基板にあらかじめ形成した第 1屈目の薄膜の結晶状態はそれぞれ、 無定^: A、 多結晶: P、 配向性多結晶:〇 単結晶: Sで示した。 なお、 実験 No. 1492、 1495で形成した GaN雜膜はすべて S iド一プの導!!性を有するものである。
W 200
〔表 5 2〕 446 原料
N c の
作製法
5 1 8
5 1 9
5 2 0
5 2 金屈の
5 2 2 直接
5 2 3 窒化法
5 2 4
5 2 5
5 2 6
5 2 7
5 2 8
5 2 9
5 3 0
5 3
5 3 2
5 3 3
5 3 4
1 5 3 5
5 3 6
5 3 7
5 3 8
5 3 9
5 4 0
5 4;
5 4 2
酸化物
5 4 3
還元法
5 4 4
5 4 5
5 4 6
5 4 7
5 4 8
5 4 9
5 5 0
5 5
5 5 2
5 5 3
5 5 4
5 5 5
5 5 6
5 5 7
5 5 8
5 5 9
5 6 0
5 6
5 6 2
5 6 3
5 6 4
5 6 5
5 6 6
5 6 7 化学
5 6 8 輸送法
5 6 9
5 7 0
* ) アルカリ土類金屈成分及び希土類元素成分の含有量は酸化物換算、 その他の成分の含有^は金屈元素換算による。
〔表 5 3〕 447
発光素子作製に用レた窒化ガリウムを主成分とする焼結体からなる基板の特性
窒ィヒガリウムを主成分とする 基板に形成した薄膜の特性 作製した発光素子の特性 実験 焼結体からなる基板の特性
による。
* 2 ) 結晶状態;〔S:単結晶、 A:無定形、 P:多結晶、 〇:配向性多結晶〕
〔表 5 4〕 448
.に組成についての詳細を示す)。
* 2 ) 基板にあらかじめ形成した 1屑目薄膜の結晶状態は、 無定形: A、 多結晶: P、 配向性多結晶: 0、 単結晶: Sで示した,
〔表 5 5〕 449
発光素子作製に用いた各種セラミック材料を主成分とする焼結体からなる基板の特性
各種セラミック材料を主成分とする 基板に形成した薄膜の特性 作製した発光素子の特性 実験 焼結体からなる基板の特性
* 2): 99. 0 (実験 No. 1194〜: L 195で作製のもの)。
* 3):焼結助剤を用いず原料だけで作製 (実験 No. 1 150- 151で作製)。
* 6) : 99 7 (実験 No. 1 162〜: L 163で作製のもの)。
3) : 99 93 (実験 N 1218〜: 1219で作製のもの)。
* 10) 96. 96 (卖験 No. 1 240〜1241で作製のもの)。
* 14) 99. 51 (実験 No. 1 306〜: L 307で作製のもの)。
* 16) 98. 76 (実験 N . 1378〜1379で作製のもの)。
* 19) 基板にあらかじめ形成した第 1層目の薄膜の結晶状態はそれぞれ、 無定形: A、 多結晶: P、 配向性多結晶:〇、 単結晶: Sで示した。
〔表 5 6〕 450
発光素子作製に用いた各種セラミック材料を主成分とする焼結体からなる基板の特性
各蓰セラミック材料を主成分とする 基板に形成した薄膜の特性 作製した発光素子の特性 突験 焼結体からなる基板の特性
* ら 形 した 1層目の薄膜の結晶状態はそれぞれ、 無定形: A、 配向性多結晶: 0で示した,
〔表 5 7〕 451
発光素子作製に用いた各種セラミック材料を主成分とする焼結体からなる基板の特性
各種セラミック材料を主成分とする 基板に形成した薄膜の特性 作製した発光素子の特性 実験 焼結体からなる基板の特性
*) 基板に fi接形成した第 1 S目の薄鹏の結晶状態はそれぞれ、 無定形: A、 配向性多結晶: 0、 単結晶: Sで示した。
さらに本発明を補足すれば、 本発明による例えば窒化アルミニウム、 炭化珪素、 窒化珪素、 窒化ガリウム、 酸化亜鉛、 謝匕アルミニウム、 酸化ベリリウム、 酸化ジルコニウム、 酸化マグ ネシゥム、 アルミン酸マグネシウム、酸化チタン、チタン酸バリウム、チタン酸ジルコン 酸化イットリウムなどの希土類 素酸化物、 酸ィ匕トリウム、 各種フェライト、 ムライト、 フォ ルステライト、 ステア夕イト、 結晶化ガラス、 などのセラミック材料を主成分とする焼結体は 光 ¾1性を有するものが得られるが、 このような ¾¾ 性を有するセラミック材料は薄膜形成 用基板あるいは薄膜基板あるいは発光軒作製用基板として用い得ることは以前から説明して きた。 本発明において 「¾¾M性を有するセラミック材料を主成分とする焼結体」 とは通常光 透過率 1 %以上のセラミック材料を主成分とする焼結体を意味するが、 上記例えば窒化アルミ 二ゥム、 炭化賴、窒化珪素、窒化ガリウム、酸化碰、酸化アルミニウム、酸化ベリリウム、 酸化ジルコニウム、 酸化マグネシウム、 アルミン酸マグネシウム、 酸化チタン、 チタン酸バリ ゥム、,チタン酸ジルコン酸鉛、 酸化イットリウムなどの希土類 素酸化物、 酸化トリウム、 各 種フェライト、 ムライト、 フオルステライト、 ステアタイト、 結晶化ガラス、 などの各種セラ ミック材料を主成分とする焼結体は光 率が 1 %より小さいかあるいは実質的に ¾1 ^性が 無いものすなわち光 率 0 %のものであっても薄膜形成用基板あるいは薄膜基板あるいは発 光素子作 基板として用い得る。 また、 上記例示した^ 生を有するセラミック材料を主 成分とする焼結体のうち例えば襯化ジルコニウム、 酸化マグネシウム、 アルミン酸マグネシゥ ム、 酸化チタン、 チタン酸バリウム、 チタン酸ジルコン酸鉛、 酸化イットリウムなどの希土類 元素酸化物、 酸化トリウム、 各種フェライト、 ムライト、 フォルステライト、 ステア夕イト、 結晶化ガラス、 などの各種セラミック材料を主成分とする焼結体には直接窒化ガリウム、 窒化 ィンジゥム、 窒化アルミニウムのうちから選ばれた少なくとも 1種以上を主成分とする単結晶 薄膜を形成することは通常困難な場合が多いが、 あらかじめ窒化ガリウム、 窒化インジウム、 窒化アルミニウムのうちから選ばれた少なくとも 1種以上を主成分とする無定形、 多結晶、 配 向性多結晶状態のうちから選ばれた少なくとも ずれかの薄膜を形成しておけば上記例えば 化ジルコニウム、 酸化マグネシウム、 アルミン酸マグネシウム、 酸化チタン、 チタン酸バリゥ ム、 チタン酸ジルコン酸鉛、 酸化イットリウムなどの希土類 素酸化物、 酸化トリウム、 各種 フェライト、 ムライト、 フォルステライト、 ステアタイト、 結晶化ガラス、 などの各種セラミ ック材料を主成分とする焼結体には該焼結体の光透過率がたとえ 1 %より小さいかあるいは光 透過率 0 %のものであつても窒化ガリウム、 窒化インジウム、 窒化アルミニウムのうちから選 ばれた少なくとも 1種以上を主成分とする単結晶薄膜の形成を比較的容易に行うことが可能と なる。 本発明において単結晶、 無定形、 多結晶、 配向性多結晶状態のうちから選ばれた少なく ともいずれかの薄膜を形成したセラミック材料を主成分とする焼結体には該焼結体の "ffi 率 がたとえ 1 %より小さいかあるいは光透過率 0 %のものであつてもェピタキシャル成長した窒 化ガリウム、 窒化インジウム、 窒化アルミニウムのうちから選ばれた少なくとも 1種以上を主 成分とする薄膜の積層が可能となり、 その結果発光効率が従来からのサファイア基板などを用 いて作製される発光素子と比べて少なくとも同等以上のものが作製し得る。
(本発明の態様)
本発明は上記のように、 1 ) 窒化ガリウム、 窒化インジウム、 窒化アルミニウムを主成分と する薄膜を形成するための基板、 2 ) 上記薄膜形成用基板の材料、 3 ) 窒化ガリウム、 窒化ィ ンジゥム、 窒化アルミニウムを主成分とする薄膜が形成された薄膜基板、 4) 窒化ガリウム、 窒化インジウム、 窒化アルミニウムを主成分とする薄膜により構成される光導波路、 5 ) 窒化 ガリウム、窒化インジウム、窒化アルミニウムを主成分とする薄膜により構成される発光軒、 に関するものである。 より詳細にいえば、 1 ) 窒化ガリウム、 窒化インジウム、 窒化アルミ二 ゥムを主成分とする薄膜を形成するための基板、 2) 窒化アルミニウムを主成分とする焼結体
を用いた薄 細基板の 方法、 3) 生の窒化アルミニウムを主成分とする焼結体、
4) 光透過性の酸化亜鉛を主成分とする焼結体、 5 ) 窒化ガリウム、 窒化インジウム、 窒化ァ ルミ二ゥムを主成分とする薄膜が形成された薄膜基板、 6 ) 薄膜基板の製造方法、 7 ) 窒化ガ リウム、 窒化インジウム、 窒化アルミニウムを主成分とする薄膜により構成される光導波路、 8 ) 窒化ガリウム、 窒化インジウム、 窒化アルミニウムを主成分とする薄膜により構成される 発光素子、に関するものである。今まで説明してきたように本発明の態様は下記の内容を含む。 以下本発明の態様について詳細を説明する。
項 1 . 窒化ガリウム、 窒化インジウム、 窒化アルミニウムのうちから選ばれた少なくとも 1 種以上を主成分とする単結晶薄膜を形成するための基板であって、 該基板がセラミック材料を 主成分とする焼結体からなることを特徴とする薄膜形成用基板。
項 2 . 窒化ガリウム、 窒化インジウム、 窒化アルミニウムのうちから選ばれた少なくとも 1 種以上を主成分とする単結晶薄膜を形成するための基板であって、 該基板が窒化ガリウム、 窒 化ィンジゥム、 窒化アルミニウムのうちから選ばれた少なくとも 1種以上を主成分とする薄膜 を形成したセラミック材料を主成分とする焼結体からなることを特徴とする項 1に記載された 項 3 . セラミック材料を主成分とする焼結体に形成された窒化ガリウム、 窒化インジウム、 窒化アルミニウムのうちから選ばれた少なくとも 1種以上を主成分とする薄膜が無定形、 多結 晶、 配向性多結晶、 単結晶のうちから選ばれる少なくともいずれかの結晶状態を有することを 特徴とする項 2に記載された薄膜形成用基板。
項 4. セラミック材料を主成分とする焼結体に形成された窒化ガリウム、 窒化インジウム、 窒化アルミニウムのうちから選ばれた少なくとも 1種以上を主成分とする薄膜の少なくとも一 部が単結晶であることを特徴とする項 2又は 3に記載されたいずれかの薄膜形成用基板。
項 5 . セラミツク材料を主成分とする焼結体に形成された窒化ガリゥム、 窒化インジウム、 窒化アルミニウムのうちから選ばれた少なくとも 1種以上を主成分とする薄膜が 1層からなる ことを特徴とする項 2、 3又は 4に記載されたいずれかの薄膜形成用基板。
項 6 . セラミック材料を主成分とする焼結体に形成された窒化ガリウム、 窒化インジウム、 窒化アルミニウムのうちから選ばれた少なくとも 1種以上を主成分とする薄膜が少なくとも 2 以上の層からなることを特徴とする項 2、 3又は 4に記載されたいずれかの薄 成用基板。 項 7 . セラミック材料を主成分とする焼結体に形成された窒化ガリウム、 窒化インジウム、 窒化アルミニウムのうちから選ばれた少なくとも 1種以上を主成分とする薄膜が少なくとも 2 以上の層からなり、 各層がそれぞれ無定形、 多結晶、 配向性多結晶、 単結晶のうちから選ばれ る少なくともいずれかの結晶状態を有することを とする項 6に記載された薄膜形成用基板。 項 8 . セラミック材料を主成分とする焼結体に形成された窒化ガリウム、 窒化インジウム、 窒化アルミニウムのうちから選ばれた少なくとも 1種以上を主成分とする薄膜が少なくとも 2 以上の層からなり、該セラミツク材料を主成分とする焼結体に直接形成された薄 が無定形、 多結晶、 配向性多結晶、 単結晶のうちから選ばれる少なくともいずれかの結晶状態を有するこ とを特徴とする項 6又は 7に記載されたいずれかの薄膜形成用基板。
項 9 . セラミック材料を主成分とする焼結体に形成された窒化ガリウム、 窒化インジウム、 窒化アルミニウムのうちから選ばれた少なくとも 1種以上を主成分とする薄膜が少なくとも 2 以上の層からなり、該セラミック材料を主成分とする焼結体に直接形成された薄 MBが無定形、 多結晶、 配向性多結晶のうちから選ばれる少なくともいずれかの結晶状態を有することを特徴 とする項 6、 7又は 8に記載されたいずれかの薄膜形成用基板。
項 1 0 .セラミック材料を主成分とする焼結体に形成された窒化ガリウム、窒化インジウム、 窒化アルミニウムのうちから選ばれた少なくとも 1種以上を主成分とする薄膜が少なくとも 2
以上の層からなり、 該セラミック材料を主成分とする焼結体に直接形成さ ήた薄膜層が 向性 多結晶であることを特徴とする項 6、 7、 8又は 9に記載されたいずれかの薄膜形成用基板。 項 11.セラミック材料を主成分とする焼結体に形成された窒化ガリウム、窒化インジウム、 窒化アルミニウムのうちから選ばれた少なくとも 1種以上を主成分とする薄膜が少なくとも 2 以上の層からなり、 少なくとも 1層が単結晶であることを特徴とする項 6、 7、 8、 9又は 1 0に記載されたいずれかの薄膜形成用基板。
項 12.セラミック材料を主成分とする焼結体に形成された窒化ガリウム、窒化インジウム、 窒化アルミニウムのうちから選ばれた少なくとも 1種以上を主成分とする薄膜が少なくとも 2 以上の層からなり、 最上層の薄膜が単結晶であることを とする項 6、 7、 8、 9、 10又 は 11に記載されたいずれかの薄膜形成用基板。
項 13.セラミック材料を主成分とする焼結体に形成された窒化ガリウム、窒化インジウム、 窒化アルミニウムのうちから選ばれた少なくとも 1種以上を主成分とする薄膜が少なくとも単 結晶薄膜層を有し該単結晶薄膜層の厚みが 300 ^m^満であることを特徴とする項 2、 3、
4、 5、 6、 7、 8、 9、 10、 11又は 12に記載されたいずれかの薄膜形成用基板。 項 14. セラミック材料を主成分とする焼結体に形成された薄膜が少なくとも 0. lnm以 上の厚みを有することを とする項 2、 3、 4、 5、 6、 7、 8、 9、 10、 11、 12又 は 13に記載されたいずれかの薄膜形成用基板。
項 15. セラミック材料を主成分とする焼結体に形成された薄膜が少なくとも窒化ガリウム を含むかあるいは窒化ガリウムを主成分とする薄膜を有することを特徴とする項 2、 3、 4、
5、 6、 7、 8、 9、 10、 11、 12、 13又は 14に記載されたいずれかの薄膜形成用基 板。
項 16. セラミック材料を主成分とする焼結体に形成された単結晶薄膜のミラ一指数 (00 2) の格子面の X線回折ロッキングカーブの半値幅が 3600秒以下であることを特徴とする 項 2、 3、 4、 5、 6、 7、 8、 9、 10、 11、 12、 13、 14又は 15に記載されたい ずれかの薄膜形成用基板。
項 17. セラミック材料を主成分とする焼結体に形成された単結晶薄膜のミラ一指数 (00 2) の格子面の X線回折ロッキングカープの半値幅が 300秒以下であることを特徴とする項 16に記載された薄膜形成用基板。
項 18. 平均表面粗さが R a 2000 nm以下のセラミック材料を主成分とする焼結体から なることを特徴とする項 1、 2、 3、 4、 5、 6、 7、 8、 9、 10、 11、 12、 13、 1 415、 16又は 17に記載されたいずれかの薄膜形成用基板。
項 19. 平均表面粗さが R a 1000 nm以下のセラミック材料を主成分とする焼結体から なることを特徴とする項 18に記載された薄膜形成用基板。
項 20. 平均表面粗さが R a 100 nm以下のセラミック材料を主成分とする焼結体からな ることを特徴とする項 18又は 19に記載されたいずれかの薄膜形成用基板。
項 21. 平均表面粗さが R a 20 nm以下のセラミック材料を主成分とする焼結体からなる ことを特徴とする項 18、 19又は 20に記載されたいずれかの薄膜形成用基板。
項 22. 平均表面粗さが Ra 5 nm以下のセラミック材料を主成分とする焼結体からなるこ とを特徴とする項 18、 19、 20又は 21に記載されたいずれかの薄膜形成用基板。
項 23. 表面粗さの大きいセラミック材料を主成分とする焼結体からなることを特徴とする 項 1、 2、 3、 4、 5、 6、 7、 8、 9、 10、 11、 12、 13、 14、 15、 16、 17、 18、 19又は 20に記載されたいずれかの薄膜形成用基板。
項 24. 平均表面粗さが R a 70 nm以上のセラミック材料を主成分とする焼結体からなる ことを特徴とする項 1、 2、 3、 4、 5、 6、 7、 8、 9、 10、 11、 12、 14、 15、
1 6、 1 7、 1 8、 1 9、 2 0又は 2 3に記載されたいずれかの薄膜形成用基板。 項 2 5. 平均表面粗さが R a 1 0 0 O nmより大きいセラミック材料を主成分とする焼結体 からなることを特徴とする項 2 4に記載された薄膜形成用基板。
項 2 6. 平均表面粗さが R a 2 0 0 0 nmより大きいセラミック材料を主成分とする焼結体 からなることを特徴とする項 2 4又は 2 5に記載されたいずれかの薄膜形成用基板。
項 2 7. 表面が焼き放し (a s— f i r e)、 ラップ研磨、 ブラスト研磨、 鏡面研磨、 ィ匕学腐 食及びプラズマガスによる腐食のうちから選ばれた少なくともいずれかの状態のセラミック材 料を主成分とする焼結体からなることを特徴とする項 1、 2、 3、 4、 5、 6、 7、 8、 9、 1 0、 1 1、 1 2、 1 3、 1 4、 1 5、 1 6、 1 7、 1 8、 1 9、 2 0、 2 1、 2 2、 2 3、 2 4、 2 5又は 2 6に記載されたいずれかの薄膜形成用基板。
項 2 8. 窒化ガリウム、 窒化インジウム、 窒化アルミニウムのうちから選ばれた少なくとも 1種以上を主成分とする薄膜を形成するための基板であって、 該基板が光 性を有するセラ ミック材料を主成分とする焼結体からなることを特徴とする薄膜形成用基板。
項 2 9. 光 Mi 性を有するセラミック材料を主成分とする焼結体からなる薄膜形成用基板に 形成される窒化ガリウム、 窒化インジウム、 窒化アルミニウムのうちから選ばれた少なくとも 1種以上を主成分とする薄膜が無定形、 多結晶、 配向性多結晶、 単結晶のうちから選ばれる少 なくともいずれかの結晶状態を有することを,とする項 2 8に記載された薄膜形成用基板。 項 3 0. 光 ¾ 性を有するセラミック材料を主成分とする焼結体からなる薄膜形成用基板に 形成される窒化ガリウム、 窒化インジウム、 窒化アルミニウムのうちから選ばれた少なくとも 1種以上を主成分とする薄膜の少なくとも一部が単結晶であることを特徴とする項 2 8又は 2 9に記載されたいずれかの薄膜形成用基板。
項 3 1. 窒化ガリウム、 窒化インジウム、 窒化アルミニウムのうちから選ばれた少なくとも 1種以上を主成分とする薄膜を形成するための基板であって、 該基板が窒化ガリウム、 窒化ィ ンジゥム、 窒化アルミニウムのうちから選ばれた少なくとも 1種以上を主成分とする薄膜を形 成した光透過性を有するセラミック材料を主成分とする焼結体からなることを特徴とする項 2 8、 2 9又は 3 0に記載されたいずれかの薄膜形成用基板。
項 3 2.光醒性を有するセラミック材料を主成分とする焼結体に形成された窒化ガリウム、 窒化インジウム、 窒化アルミニウムのうちから選ばれた少なくとも 1種以上を主成分とする薄 膜が無定形、 多結晶、 配向性多結晶、 単結晶のうちから選ばれる少なくともいずれかの結晶状 態を有することを特徴とする項 3 1に記載された薄膜形成用基板。
項 3 3.光¾1性を有するセラミック材料を主成分とする焼結体に形成された窒化ガリウム、 窒化インジウム、 窒化アルミニウムのうちから選ばれた少なくとも 1種以上を主成分とする薄 膜の少なくとも一部が単結晶であることを特徴とする項 3 1又は 3 2に記載されたいずれかの 薄膜形成用基板。
項 3 4. 光 ¾ 性を有するセラミック材料を主成分とする焼結体に形成された窒化ガリウム、 窒化インジウム、 窒化アルミニウムのうちから選ばれた少なくとも 1種以上を主成分とする薄 膜が 1層からなることを特徴とする項 3 1、 3 2又は 3 3に記載されたいずれかの薄膜形成用 項 3 5. 性を有するセラミック材料を主成分とする焼結体に形成された窒化ガリウム、 窒化インジウム、 窒化アルミニウムのうちから選ばれた少なくとも 1種以上を主成分とする薄 膜が少なくとも 2以上の層からなることを特徴とする項 3 1、 3 2又は 3 3に記載されたいず れかの薄膜形成用基板。
項 3 6. 光透過性を有するセラミック材料を主成分とする焼結体に形成された窒化ガリウム、 窒化インジウム、 窒化アルミニウムのうちから選ばれた少なくとも 1種以上を主成分とする薄
膜が少なくとも 2以上の層からなり、 各層がそれぞれ無定形、 多結晶、 配向性多結晶、 単結晶 のうちから選ばれる少なくともいずれかの結晶状態を有することを特徴とする項 3 5に記載さ れた薄膜形成用基板。
項 3 7. ¾¾ 性を有するセラミック材料を主成分とする焼結体に形成された窒化ガリウム、 窒化ィンジゥム、 窒化アルミニウムのうちから選ばれた少なくとも 1種以上を主成分とする薄 膜が少なくとも 2以上の層からなり、 該¾¾1性を有するセラミック材料を主成分とする焼結 体に直接形成された薄膜層が無定形、 多結晶、 配向性多結晶、 単結晶のうちから選ばれる少な くともいずれかの結晶状態を有することを特徴とする項 3 5又は 3 6記載されたいずれかの薄 膜形成用基板。
項 3 8. ¾¾¾性を有するセラミック材料を主成分とする焼結体に形成された窒化ガリウム、 窒化ィンジゥム、 窒化アルミニウムのうちから選ばれた少なくとも 1種以上を主成分とする薄 膜が少なくとも 2以上の層からなり、 性を有するセラミック材料を主成分とする焼結 体に直接形成された薄蘭が無定形、 多結晶、 配向性多結晶のうちから選ばれる少なくともい ずれかの結晶状態を有することを特徴とする項 3 5、 3 6又は 3 7に記載されたいずれかの薄 膜形成用基板。
項 3 9. 性を有するセラミック材料を主成分とする焼結体に形成された窒化ガリウム、 窒化インジウム、 窒化アルミニウムのうちから選ばれた少なくとも 1種以上を主成分とする薄 膜が少なくとも 2以上の層からなり、 該 ½¾ 性を有するセラミック材料を主成分とする焼結 体に直接形成された薄膜層が 向性多結晶であることを特徴とする項 3 5、 3 6、 3 7又は 3 8に記載されたいずれかの薄膜形成用基板。
項 4 0.光 ¾1性を有するセラミック材料を主成分とする能結体に形成された窒化ガリウム、 窒化インジウム、 窒化アルミニウムのうちから選ばれた少なくとも 1種以上を主成分とする薄 膜が少なくとも 2以上の層からなり、少なくとも 1層が単結晶であることを M [とする項 3 5、 3 6、 3 7、 3 8又は 3 9に記載されたいずれかの薄膜形成用基板。
項 4 1. 性を有するセラミック材料を主成分とする焼結体に形成された窒化ガリウム、 窒化ィンジゥム、 窒化アルミニウムのうちから選ばれた少なくとも 1種以上を主成分とする薄 膜が少なくとも 2以上の層からなり、 最上層の薄膜が単結晶であることを特徴とする項 3 5、
3 6、 3 7、 3 8、 3 9又は 4 0に記載されたいずれかの薄膜形成用基板。
項 4 2. 光 性を有するセラミック材料を主成分とする焼結体に形成された窒化ガリウム、 窒化インジウム、 窒化アルミニウムのうちから選ばれた少なくとも 1種以上を主成分とする薄 膜が少なくとも単結晶薄 を有し該単結晶薄 IISの厚みが 3 0 0 m^満であることを特徴 とする項 3 1、 3 2、 3 3、 3 4、 3 5、 3 6、 3 7、 3 8、 3 9、 4 0又は 4 1に記載され たいずれかの薄膜形成用基板。
項 4 3. 過性を有するセラミック材料を主成分とする焼結体に形成された薄膜が少なく とも 0. 1 nm以上の厚みを有することを特徴とする項 3 1、 3 2、 3 3、 3 4、 3 5、 3 6、 3 7、 3 8、 3 9、 4 0、 4 1又は 4 2に記載されたいずれかの薄膜形成用基板。
項 4 4. 光 ¾i性を有するセラミック材料を主成分とする焼結体に形成された薄膜が少なく とも窒化ガリウムを含むかあるいは窒化ガリウムを主成分とする薄膜を有することを特徴とす る項 3 1、 3 2、 3 3、 3 4、 3 5、 3 6、 3 7、 3 8、 3 9、 4 0、 4 1、 4 2又は 4 3に 記載されたいずれかの薄膜形成用基板。
項 4 5. 光透過性を有するセラミック材料を主成分とする焼結体に形成された単結晶薄膜の ミラー指数 ( 0 0 2) の格子面の X線回折ロッキングカープの半値幅が 3 6 0 0秒以下である ことを特徴とする項 3 1、 3 2、 3 3、 3 4、 3 5、 3 6、 3 7、 3 8、 3 9、 4 0、 4 1、
4 2、 4 3又は 4 4に記載されたいずれかの薄膜形成用基板。
項 46. 光透過性を有するセラミック材料を主成分とする焼結体に形成された単結晶薄膜の ミラ一指数 (002) の格子面の X線回折ロッキング力一ブの半値幅が 300秒以下であるこ とを特徴とする項 45に記載された薄膜形成用基板。
項 47. 平均表面粗さが R a 2000 nm以下の光透過性を有するセラミツク材料を主成分 とする焼結体からなることを赚とする項 28、 29、 30、 31、 32、 33、 34、 35、 36、 37、 38、 39、 40、 41、 42、 43、 44、 45又は 46に記載されたいずれ かの薄膜形成用基板。
項 48. 平均表面粗さが R a 1000 nm以下の光腿性を有するセラミック材料を主成分 とする焼結体からなることを特徴とする項 47に記載された薄膜形成用基板。
項 49. 平均表面粗さが R a 100 nm以下の ¾¾ 性を有するセラミック材料を主成分と する焼結体からなることを特徴とする項 47又は 48に記載されたいずれかの薄膜形成用基板。 項 50. 平均表面粗さが R a 20 nm以下の光透過性を有するセラミック材料を主成分とす る焼結体からなることを特徴とする項 47、 48又は 49に記載されたいずれかの薄膜形成用 項 51. 平均表面粗さが R a 5 nm以下の光透過性を有するセラミツク材料を主成分とする 焼結体からなることを特徴とする項 47、 48、 49又は 50に記載されたいずれかの薄膜形 成用基板。
項 52. 表面粗さの大きい 過性を有するセラミック材料を主成分とする焼結体からなる ことを特徴とする項 28、 29、 30、 31、 32、 33、 34、 35、 36、 37、 38、 39、 40、 41、 42、 43、 44、 45、 46、 47、 48又は 49に記載されたいずれ かの薄膜形成用基板。
項 53. 平均表面粗さが R a 70 nm以上の光透過性を有するセラミック材料を主成分とす る能結体からなることを特徴とする項 28、 29、 30、 31、 32、 33、 34、 35、 3 6、 37、 38、 39、 40、 41、 42、 43、 44, 45、 46、 47、 48、 49又は 52に記載されたいずれかの薄膜形成用基板。
項 54. 平均表面粗さが R a 1000 nmより大きいう 過性を有するセラミック材料を主 成分とする焼結体からなることを特徴とする項 53に記載された薄膜形成用基板。
項 55. 平均表面粗さが R a 2000 nmより大きい光透過性を有するセラミック材料を主 成分とする焼結体からなることを特徴とする項 53又は 54に記載されたいずれかの薄膜形成 用基板。
項 56. 表面が焼き放し (as— f i r e)、 ラッフ ¾f磨、 ブラスト研磨、 鏡面研磨、 ィ匕学腐 食及びプラズマガスによる腐食のうちから選ばれた少なくともいずれかの状態の光透過性を有 するセラミック材料を主成分とする焼結体からなることを特徴とする項 28、 29、 30、 3 1、 32、 33、 34、 35、 36、 37、 38、 39、 40、 41、 42、 43、 44、 4
5、 46、 47、 48、 49、 50、 51、 52、 53、 54、 55又は 56に記載されたい ずれかの薄膜形成用基板。
項 57. セラミック材料を主成分とする焼結体あるいは光透過性を有するセラミック材料を 主成分とする焼結体が ¾¾ϋ率 1%以上のものであることを とする項 1、 2、 3、 4、 5、
6、 7、 8、 9、 10、 11、 12、 13、 14、 15、 16、 17、 18、 19、 20、 2 1、 22、 23、 24、 25、 26、 27、 28、 29、 30、 31、 32、 33、 34、 3 5、 36、 37、 38、 39、 40、 41、 42、 43、 44、 45、 46、 47、 48、 4 9、 50、 51、 52、 53、 54、 55又は 56に記載されたいずれかの薄膜形成用基板。 項 58. セラミック材料を主成分とする焼結体あるいは光透過性を有するセラミック材料を 主成分とする焼結体が光透過率 10%以上のものであることを特徴とする項 57に記載された
薄膜形成用基板。
項 59. セラミック材料を主成分とする焼結体あるいは光 ¾ 性を有するセラミック材料を 主成分とする焼結体が光 ¾ 率 20%以上のものであることを とする項 57又は 58に記 載されたいずれかの薄膜形成用基板。.
項 60. セラミック材料を主成分とする焼結体あるいは光 Mil性を有するセラミック材料を 主成分とする焼結体が光透過率 30 %以上のものであることを特徴とする項 57、 58又は 5 9記載されたいずれかの薄膜形成用基板。
項 61. セラミック材料を主成分とする焼結体あるいは 性を有するセラミック材料を 主成分とする焼結体が光 ¾1率 40 %以上のものであることを ^とする項 57、 58、 59 又は 60に記載されたいずれかの薄膜形成用基板。
項 62. セラミック材料を主成分とする焼結体あるいは光 ¾i 性を有するセラミック材料を 主成分とする焼結体が光¾§率 50%以上のものであることを特徴とする項 57、 58、 59、 60又は 61に記載されたいずれかの薄膜形成用基板。
項 63. セラミック材料を主成分とする焼結体あるいは光 ¾1性を有するセラミック材料を 主成分とする焼結体が光 »率 60%以上のものであることを特徴とする項 57、 58、 59、 60, 61又は 62に記載されたいずれかの薄膜形成用基板。
項 64. セラミック材料を主成分とする焼結体あるいは)1 έ¾ 生を有するセラミック材料を 主成分とする焼結体が光 ¾i率 80%以上のものであることを特徴とする項 57、 58、 59、 60、 61、 62又は 63に記載されたいずれかの薄膜形成用基板。
項 65. セラミック材料を主成分とする焼結体あるいは光 ¾i性を有するセラミック材料を 主成分とする焼結体が ¾¾ 率 1%未満のものであることを ^とする項 1、 2、 3、 4、 5、 .
6、 7、 8、 9、 10、 11、 12、 13、 14、 15、 16、 17、 18、 19、 20、 2 1、 22、 23、 24、 25、 26、 27、 28、 29、 30、 31、 32、 33、 34、 3 5、 36、 37、 38、 .39、 40、 41、 42、 43、 44、 45、 46、 47、 48、 4 9、 50、 51、 52、 53、 54、 55又は 56に記載されたいずれかの薄膜形成用基板。 項 66. セラミック材料を主成分とする焼結体が光 ¾i 率 0%であることを特徴とする項 6 5に記載された薄膜形成用基板。
項 67. ¾Si性あるいは 過率が少なくとも波長 200 ηπ!〜 800 nmの範囲の光に 対してのものであることを特徴とする項 28、 29、 30、 31、 32、 33、 34、 35、 36、 37、 38、 39、 40、 41、 42、 43、 44、 45、 46、 47、 48、 49、 50、 51、 52、 53、 54、 55、 56、 57、 58、 59、 60、 61、 62、 63、 64、 65又は 66に記載されたいずれかの薄膜形成用基板。
項 68. セラミック材料を主成分とする焼結体及び光 ¾ 性を有するセラミック材料を主成 分とする焼結体がそれぞれ窒化アルミニウムを主成分とする焼結体、 六方晶系又 方晶系の うちから選ばれた少なくともいずれかの結晶構造を有するセラミック材料を主成分とする焼結 体、 及び 化ジルコニウム、 酸化マグネシウム、 アルミン酸マグネシウム、 酸化チタン、 チタ ン酸バリウム、 チタン酸ジルコン 、 希土 素酸化物、 酸化トリウム、 各種フェライト、 ムライト、 フォルステライト、 ステア夕イト、 結晶化ガラスのうちから選ばれた少なくとも 1 種以上を主成分とする焼結体、 のうちから選ばれた少なくともいずれかであることを ^とす る項 1、 2、 3、 4、 5、 6、 7、 8、 9、 10、 11、 12、 13、 14、 15、 16、 1
7、 18、 19、 20、 21、 22、 23、 24、 25、 26、 27、 28、 29、 30、 3 1、 32、 33、 34、 35、 36、 37、 38、 39、 40、 41、 42、 43、 44、 4 5、 46、 47、 48、 49、 50、 51、 52、 53、 54、 55、 56、 57、 58、 5 9、 60、 61、 62、 63、 64、 65、 66又は 67に記載されたいずれかの薄膜形成用
項 69. 六方晶系又は≡方晶系のうちから選ばれた少なくともいずれかの結晶構造を有する セラミック材料を主成分とする焼結体が 化亜鉛、 酸化ベリリウム、 酸化アルミニウム、 炭化 珪素、 窒化珪素、 窒化ガリウムのうちから選ばれた少なくとも 1種以上を主成分とする焼結体 であることを特徴とする項 68に記載された薄膜形成用基板。
項 70. セラミック材料を主成分とする焼結体及び光 性を有するセラミック材料を主成 分とする焼結体がそれぞれ窒化アルミニウム、酸化碰、酸化ベリリウム、酸化アルミニウム、 炭化珪素、 窒化珪素、 窒化ガリウム、 酸化ジルコニウム、 酸化マグネシウム、 アルミン酸マグ ネシゥム、 酸化イットリウムのうちから選ばれた少なくとも 1種以上を主成分とする焼結体で あることを特徴とする項 68又は 69に記載されたいずれかの薄膜形成用基板。
項 71. セラミック材料を主成分とする焼結体及び光 ¾i性を有するセラミック材料を主成 分とする焼結体がそれぞれ窒化アルミニウムを主成分とする焼結体であるることを特徴とする 項 1、 2、 3、 4、 5、 6、 7、 8、 9、 10、 11、 12、 13、 14、 15、 16、 17、 18、 19、 20、 21、 22、 23、 24、 25、 26、 27、 28、 29、 30、 31、 32、 33、 34、 35、 36、 3377、、 3388、、 39、 40、 41、 42、 43、 44、 45、 46、 47、 48、 49、 50、 51、 5522、、 53、 54、 55、 56、 57、 58、 59、 60、 61、 62、 63、 64、 65、 6666、、 67、 68又は 70に記載されたいずれかの薄 膜形成用基板。
項 72. 窒化アルミニウムを主成分とする焼結体が光 ¾i性を有するものである, .とを とする項 71に記載された薄膜形成用基板。
項 73. 窒化アルミニウムを主成分とする焼結体が光透過率 1%以上のものであることを特 徵とする項 71又は 72に記載されたいずれかの薄膜形成用基板。
項 74. 窒化アルミニウムを主成分とする焼結体が光透過率 5%以上のものであることを特 徴とする項 71、 72又は 73に記載されたいずれかの薄膜形成用基板。
項 75. 窒化アルミニウムを主成分とする焼結体が 率 10%以上のものであることを 特徴とする項 71、 72、 73又は 74に記載されたいずれかの薄膜形成用基板。
項 76. 窒化アルミニウムを主成分とする焼結体が 率 20%以上のものであることを 特徴とする項 71、 72、 73、 74又は 75に記載されたいずれかの薄膜形成用基板。 項 77. 窒化アルミニウムを主成分とする焼結体が光 ¾i率 30%以上のものであることを 特徴とする項 71、 72、 73、 74、 75又は 76に記載されたいずれかの薄膜形成用基板。 項 78. 窒化アルミニウムを主成分とする焼結体が光 ¾ii率 40 %以上のものであることを 特徴とする項 71、 72、 73、 74、 75、 76又は 77に記載されたいずれかの薄膜形成 用基板。
項 79. 窒化アルミニウムを主成分とする焼結体が光 ¾ 率 50%以上のものであることを 特徴とする項 71、 72、 73、 74、 75、 76、 77又は 78に記載されたいずれかの薄 膜形成用基板。
項 80. 窒化アルミニウムを主成分とする焼結体が光 ¾1率 60%以上のものであることを 特徴とする項 71、 72、 73、 74、 75、 76、 77、 78又は 79に記載されたいずれ かの薄膜形成用基板。
項 81. 窒化アルミニウムを主成分とする焼結体が光 率 80%以上のものであることを 特徴とする項 71、 72、 73、 74、 75、 76、 77、 78、 79又は 80に記載された いずれかの薄膜形成用基板。
項 82. 窒化アルミニウムを主成分とする焼結体が光 ¾li率 85%以上のものであることを 特徴とする項 71、 72、 73、 74、 75、 76、 77、 78、 79、 80又は 81に記載
されたいずれかの薄膜形成用基板。
項 8 3. 窒化アルミニウムを主成分とする焼結体が光 ¾ί§率 1 %未満のものであることを特 徵とする項 7 1又は 7 2に記載されたいずれかの薄膜形成用基板。
項 8 4. 窒化アルミニウムを主成分とする焼結体が ¾ ^率 0 %のものであることを特徴と する項 8 3に記載された薄膜形成用基板。
項 8 5. 光 性あるいは光 ¾ϋ率が少なくとも波長 2 0 0 ηπ!〜 8 0 0 nmの範囲の光に 対してのものであることを特徴とする項 7 2、 7 3、 7 4、 7 5、 7 6、 7 7、 7 8、 7 9、 8 0、 8 1、 8 2、 8 3又は 8 4に記載されたいずれかの薄膜形成用基板。
項 8 6. 窒化ガリウム、 窒化インジウム、 窒化アルミニウムのうちから選ばれた少なくとも 1種以上を主成分とする薄膜を形成するための基板であって、 該基板が窒化ガリウム、 窒化ィ ンジゥム、 窒化アルミニウムのうちから選ばれた少なくとも 1種以上を主成分とする薄膜を形 成した窒化アルミニウムを主成分とする 結体からなることを特徴とする項 7 1、 7 2、 7 3、 7 4、 7 5、 7 6、 7 7、 7 8、 7 9、 8 0、 8 1、 8 2、 8 3、 8 4又は 8 5に記載された いずれかの薄膜形成用基板。
項 8 7. 窒化アルミニウムを主成分とする焼結体に形成されている窒化ガリウム、 窒化イン ジゥム、 窒化アルミニウムのうちから選ばれた少なくとも 1種以上を主成分とする薄膜が単結 晶、 無定形、 多結晶、 配向性多結晶のうちから選ばれる少なくともいずれかの結晶状態を有す るものであることを特徴とする項 8 6に記載された薄膜形成用基板。
項 8 8. 窒化アルミニウムを主成分とする焼結体が窒化アルミニウムを 2 0體%以上含む ものであることを特徴とする項 7 1、 7 2、 7 3、 7 4、 7 5、 7 6、 7 7、 7 8、 7 9、 8 0、 8 1、 8 2、 8 3、 8 4、 8 5、 8 6又は 8 7に記載されたいずれかの薄膜形成用基板。 項 8 9. 窒化アルミニウムを主成分とする焼結体が窒化アルミニウムを 5 0体積%以上含む ものであることを特徴とする項 8 8に記載された薄膜形成用基板。
項 9 0. 窒化アルミ二ゥムを主成分とする焼結体が希土類元素あるいはアル力リ土類金属の うちから選ばれた少なくとも 1種以上の成分を酸化物 で 8 0体積%以下含むものであるこ とを特徴とする項 7 1、 7 2、 7 3、 7 4、. 7 5、 7 6、 7 7、 7 8、 7 9、 8 0、 8 1、 8 2、 8 3、 8 4、 8 5、 8 6、 8 7、 8 8又は 8 9に記載されたいずれかの薄膜形成用基板。 項 9 1. 窒化アルミニウムを主成分とする焼結体が希土 素あるいはアルカリ土類金属の うちから選ばれた少なくとも 1種以上の成分を酸化物■で 5 0#¾%以下含むものであるこ とを特徴とする項 9 0に記載された薄膜形成用基板。
項 9 2. 窒化アルミニウムを主成分とする焼結体が希土 素あるいはアルカリ土類金属の うちから選ばれた少なくとも 1種以上の成分を酸化物換算で 2 5体積%以下含むものであるこ とを特徴とする項 9 0又は 9 1に記載されたいずれかの薄膜形成用基板。
項 9 3. 窒化アルミニウムを主成分とする焼結体が希土類 £素のうちから選ばれた少なくと も 1種以上の成分とアルカリ土類金属のうちから選ばれた少なくとも 1種以上の成分とを同時 に含むものであることを特徴とする項 9 0、 9 1又は 9 2に記載されたいずれかの薄膜形成用 項 9 4. 窒化アルミニウムを主成分とする焼結体がアルカリ金属あるいは珪素のうちから選 ばれた少なくとも 1種以上の成分を酸化物換算で 5 0体 以下含むものであることを特徴と する項 7 1、 7 2、 7 3、 7 4、 7 5、 7 6、 7 7、 7 8、 7 9、 8 0、 8 1、 8 2、 8 3、 8 4、 8 5、 8 6、 8 7、 8 8、 8 9、 9 0、 9 1、 9 2又は 9 3に記載されたいずれかの薄 膜形成用基板。
項 9 5. 窒化アルミニウムを主成分とする焼結体がアルカリ金属あるいは珪素のうちから選 ばれた少なくとも 1種以上の成分を酸化物 で 3 0体讀%以下含むものであることを特徴と
する項 94に記載された薄膜形成用基板。
項 96. 窒化アルミニウムを主成分とする焼結体がアルカリ金属あるいは珪素のうちから選 ばれた少なくとも 1種以上の成分を酸化物換算で 20体積%以下含むものであることを特徴と する項 94又は 95に記載されたいずれかの薄膜形成用基板。
項 97. 窒化アルミニウムを主成分とする焼結体がアルカリ金属あるいは珪素のうちから選 ばれた少なくとも 1種以上の成分を酸化物 で 10#¾%以下含むからなることを,とす る項 94、 95又は 96に記載されたいずれかの薄膜形成用基板。
項 98. 窒化アルミニウムを主成分とする能結体がアルカリ金属あるいは珪素のうちから選 ばれた少なくとも 1種以上の成分を含み同時に希土類 素あるいはアルカリ土類金属のうちか ら選ばれた少なくとも 1種以上の成分を含むものであることを特徴とする項 90、 91、 92、 93、 94、 95、 96又は 97に記載されたいずれかの薄膜形成用基板。
項 99.窒化アルミニウムを主成分とする焼結体が Mo、 W、 V (バナジウム)、 Nb、 Ta、 T i、 カーボンのうちから選ばれた少なくとも 1種以上の成分を元素,で 80体積%以下含 むものであることを特徴とする項 71、 72、 73、 74、 75、 76、 77、 78、 79、 80、 81、 82、 83、 84、 85、 86、 87、 88、 89、 90、 91、 92、 93、 94、 95、 96、 97又は 98に記載されたいずれかの薄膜形成用基板。
項 100. 窒化アルミニウムを主成分とする能結体が Mo、 W、 V ひナジゥム)、 Nb、 T a、 T i、 カーボンのうちから選ばれた少なくとも 1種以上の成分を元素換算で 50ィ«%以 下含むものであることを特徴とする項 99に記載された薄膜形成用基板。
項 101. 窒化アルミニウムを主成分とする焼結体が Mo、 W、 V、 Nb、 Ta、 Ti、 力 一ボンのうちから選ばれた少なくとも 1種以上の成分を元素■で 25#¾%以下含むもので あることを特徵とする項 99又は 100に記載されたいずれかの薄膜形成用基板。
項 102. 窒化アルミニウムを主成分とする焼結体が Mo、 W、 V、 Nb、 Ta、 Ti、 力 —ボンのうちから選ばれた少なくとも 1種以上の成分を含み同時に希土类阮素あるいはアル力 リ土類金属のうちから選ばれた少なくとも 1種以上の成分を含むものであることを とする 項 90、 91、 92、 93、 99、 100又は 101に記載されたいずれかの薄藤成用基板。 項 103. 窒化アルミニウムを主成分とする焼結体が希土 ¾素及び Mo、 W、 V (バナジ ゥム)、 Nb、 Ta、 T の遷移金属成分を元素換算で 80重量%以下含むものであること を難とする項 71、 72、 73、 74、 75、 76、 77、 78、 79、 80、 81、 82、 83、 84、 85、 86、 87、 88、 89、 90、 91、 92、 93、 94、 95、 96、 97、 98、 99、 100、 101又は 102に記載されたいずれかの薄膜形成用基板。 項 104. 窒化アルミニウムを主成分とする焼結体が希土 |S¾素及び Mo、 W、 V (パナジ ゥム)、 Nb、 Ta、 T iiiWの遷移金属成分を元素騰で 50重量%以下含むものであること を特徴とする項 103に記載された薄膜形成用基板。
項 105. 窒化アルミニウムを主成分とする焼結体が希土^ ¾素及 ζ Μο、 W、 V、 Nb、 Ta、 T i以外の遷移金属成分を元素換算で 30重量%以下含むものであることを 1« [とする 項 103又は 104に記載されたいずれかの薄膜形成用基板。
項 106. 窒化アルミニウムを主成分とする焼結体が希土類 素及び Mo、 W、 V、 Nb、 T a、 T i以外の遷移金属成分を含み同時に希土類 Jf;素あるいはアル力リ土類金属のうちから 選ばれた少なくとも 1種以上の成分を含むものであることを特徴とする項 90、 91、 92、 93、 103、 104又は 105に記載されたいずれかの薄膜形成用基板。
項 107. 希土 ϋ¾素及び Mo、 W、 V、 Nb、 Ta、 T i以外の遷移金属成分が鉄、 ニッ ゲル、 クロム、 マンガン、 ジルコニウム、 ハフニウム、 コノルト、 銅、 亜鉛のうちから選ばれ た少なくとも 1種以上であることを特徴とする項 103、 104、 105又は 106に記載さ
れたいずれかの薄膜形成用基板。
項 108. 窒化アルミニウムを主成分とする焼結体力戰 ^"有量 30重量%以下のものであ ることを纖とする項 71、 72、 73、 74、 75、 76、 77、 78、 79、 80、 81、 82、 83、 84、 85、 86、 87、 88、 89、 90、 91、 92、 93、 94、 95、 96、 97、 98、 99、 100、 101、 102、 103、 104、 105、 106又は 1 07に記載されたいずれかの薄膜形成用基板。
項 109. 窒化アルミニウムを主成分とする焼結体が ¾ ^有量 25重量%以下のものであ ることを特徴とする項 108に記載された薄膜形成用基板。
項 110. 窒化アルミニウムを主成分とする焼結体が ^^有量 10重量%以下のものであ ることを特徴とする項 108又は 109に記載されたいずれかの薄膜形成用基板。
項 111. 窒化アルミニウムを主成分とする焼結体力壞素を含み同時に希土類 素あるいは アルカリ土類金属のうちから選ばれた少なくとも 1種以上の成分を同時に含むものであること を特徴とする項 90、 91、 92、 93、 108、 109又は 110に記載されたいずれかの 薄膜形成用基板。
項 112. 窒化アルミニウムを主成分とする焼結体が ALON含有量 80%以下のものであ ることを特徴とする項 71、 72、 73、 74、 75、 76、 77、 78、 79、 80、 81、 82、 83、 84、 85、 86、 87、 88、 89、 90、 91、 92、 93、 94、 95、 96、 97、 98、 99、 100、 101、 102、 103、 104、 105、 106、 10 7、 108、 109、 110又は 111に記載されたいずれかの薄膜形成用基板。
項 113. 窒化アルミニウムを主成分とする焼結体が AL ON含有量 50%以下のものであ ることを特徴とする項 112に記載された薄膜形成用基板。
項 114. 窒化アルミニウムを主成分とする焼結体が A L ON含有量 20 %以下のものであ ることを特徴とする項 112又は 113に記載されたいずれかの薄膜形成用基板。
項 115. 窒化アルミニゥムを主成分とする焼結体が A LONを含み同時に希土類元素ある いはアルカリ土類金属のうちから選ばれた少なくとも 1種以上の成分を含むものであることを 特徴とする項 90、 91、 92、 93、 112、 113又は 114に記載されたいずれかの薄 膜形成用基板。
項 116. 窒化アルミニウムを主成分とする焼結体が室温における熱伝導率 5 OWZmK以 上のものであることを ^とする項 71、 72、 73、 74、 75、 76、 77、 78、 79、 80、 81、 82、 83、 84、 85、 86、 87、 88、 89、 90、 91、 92、 93、 94、 95、 96、 97、 98、 99、 100、 101、 102、 103、 104、 105、 106、 107、 108、 109、 110、 111、 112、 113、 114又は 115に記 載されたいずれかの薄膜形成用基板。
項 117. 窒化アルミニウムを主成分とする焼結体が室温における熱伝導率 10 OWZmK 以上のものであることを特徴とする項 116に記載された薄膜形成用基板。
項 118. 窒化アルミニウムを主成分とする焼結体が室温における熱伝導率 15 OWZmK 以上のものであることを特徴とする項 116又は 117に記載されたいずれかの薄膜形成用基 板。
項 119. 窒化アルミニウムを主成分とする焼結体が室温における熱伝導率 17 OW/mK 以上のものであることを特徴とする項 116、 117又は 118に記載されたいずれかの薄膜 形成用基板。
項 120. 窒化アルミニウムを主成分とする焼結体が窒化アルミニウムを 95体積%以上含 むものであることを特徴とする項 71、 72、 73、 74、 75、 76、 77、 78、 79、 80、 81、 82、 83、 84、 85、 86、 87、 88、 89、 90、 91、 92、 93、
94、 95、 96、 97、 98、 99、 100、 101、 102、 103、 104、 105、 106、 107、 108、 109、 110、 111、 112、 113、 114、 115、 11 6、 117、 118又は 119に記載されたいずれかの薄膜形成用基板。
項 121. 窒化アルミニウムを主成分とする焼結体が希土類 素及びアルカリ土類金属のう ちから選ばれた少なくとも 1種以上の成分を元素換算で合計 0. 5重量%以下かつ酸素を 0. 9重量%以下含むものであることを體とする項 71、 72、 73、 74、 75、 76、 77、
78、 79、 80、 81、 82、 83、 84、 85、 86、 87、 88、 89、 90、 91、
92、 93、 94、 95、 96、 97、 98、 99、 100、 101、 102、 103、 10
4、 105、 106、 107、 108、 109、 110、 111、 112、 113、 114、
115、 116、 117、 118、 119又は 120に記載されたいずれかの薄藤成用基板。 項 122. 窒化アルミニウムを主成分とする焼結体が希土類 素及びアルカリ土類金属のう ちから選ばれた少なくとも 1種以上の成分を元素; f»で合計 0. 2重量%以下かつ酸素を 0. 5重量%以下含むものであることを特徴とする項 121に記載された薄膜形成用基板。
項 123. 窒化アルミニウムを主成分とする焼結体が希土^ ¾素及びアルカリ土類金属のう ちから選ばれた少なくとも 1種以上の成分を元素匪で合計 0. 05重量%以下かつ酸素を 0. 2重量%以下含むものであることを特徴とする項 121又は 122に記載されたいずれかの薄 膜形成用基板。
項 124. 窒化アルミニウムを主成分とする焼結体が希土 ||¾素及びアルカリ土類金属のう ちから選ばれた少なくとも 1種以上の成分を元素^^で合計 0· 02重量%以下かつ酸素を 0. 1重量%以下含むものであることを特徴とする項 121、 122又は 123に記載されたいず れかの薄膜形成用基板。
項 125. 窒化アルミニウムを主成分とする焼結体が希土航素及びアルカリ土類金属のう ちから選ばれた少なくとも 1種以上の成分を元素 で合計 0. 005重量%以下かつ酸素を
0、 05重量%以下含むものであることを特徴とする項 121、 122、 123又は 124に 記載されたいずれかの薄膜形成用基板。
項 126. 窒化アルミニウムを主成分とする焼結体がアルカリ金属あるいは珪素のうちから 選ばれた少なくとも 1種以上の成分を元素騰で合計 0. 2重量%以下かつ酸素を 0. 9重量% 以下含むものであることを特徴とする項 71、 72、 73、 74、 75、 76、 77、 78、
79、 80、 81、 82、 83、 84、 85、 86、 87、 88、 89、 90、 91、 92、
93、 94、 95、 96、 97、 98、 99、 100、 101、 102、 103、 104、 1
05、 106、 107、 108、 109、 110、 111、 112、 113、 114、 115、
116、 117、 118、 119、 120、 121、 122、 123、 124又は 125に記 載されたいずれかの薄膜形成用基板。
項 127. 窒化アルミニウムを主成分とする焼結体が Mo、 W、 V (バナジウム)、 Nb、 T a、 Ti、 力一ボンのうちから選ばれた少なくとも 1種以上の成分を元素換算で合計 0. 2重 量%以下かつ酸素を 0. 9重量%以下含むものであることを とする項 71、 72、 73、 74、 75、 76、 77、 78、 79、 80、 81、 82、 83、 84、 85、 86、 87、 88、 89、 90、 91、 92、 93、 94、 95、 96、 97、 98、 99、 100、 10
1、 102、 103、 104、 105、 106、 107、 108、 109、 110、 111、 112、 113、 114、 115、 116、 117、 118、 119、 120、 121、 12
2、 123、 124、 125又は 126に記載されたいずれかの薄膜形成用基板。
項 128. 窒化アルミニウムを主成分とする觸吉体が Fe、 Ni、 Co、 Mn、 Cr、 Zr、 Hf、 Cu、 Znのうちから選ばれた少なくとも 1種以上の成分を元素醇で合計 0. 2重量% 以下かつ酸素を 0. 9重量%以下含むものであることを赚とする項 71、 72、 73、 74、
75、 76、 77、 78、 79、 80、 81、 82、 83、 84、 85、 86、 87、 88、 89、 90、 91、 92、 93、 94、 95、 96、 97、 98、 99、 100、 101、 1
02、 103、 104、 105、 106、 107、 108、 109、 110、 111、 112、 113、 114、 115、 116、 117、 118、 119、 120、 121、 122、 12
3、 124、 125、 126又は 127に記載されたいずれかの薄膜形成用基板。
項 129. 窒化アルミニウムを主成分とする焼結体が結晶相として A 1 Nを 95%以上含む ものであることを とする項 71、 72、 73、 74、 75、 76、 77、 78、 79、 8
0、 81、 82、 83、 84、 85、 86、 87、 88、 89、 90、 91、 92、 93、 9
4、 95、 96、 97、 98、 99、 100、 101、 102、 103、 104、 105、 1 06、 107、 108、 109、 110、 111、 112、 113、 114、 115、 116、 117、 118、 119、 120、 121、 122、 123、 124、 125、 126、 12 7又は 128に記載されたいずれかの薄膜形成用基板。
項 130. 窒化アルミニウムを主成分とする焼結体が結晶相として A 1 Nを 98%以上含む ものであることを特徴とする項 119に記載された薄膜形成用基板。
項 131. 窒化アルミニウムを主成分とする焼結体が実質的に A 1 Nの単一相からなること を難とする項 71、 72、 73、 74、 75、 76、 77、 78、 79、 80、 81、 82、 83、 84、 85、 86、 87、 88、 89、 90、 91、 92、 93、 94、 95、 96、 97、 98、 99、 100、 101、 102、 103、 104、 105、 106、 107、 1
08、 109、 110、 111、 112、 113、 114、 115、 116、 117、 118、 119、 120、 121、 122、 123、 124、 125、 126、 127、 128、 12 9又は 130に記載されたいずれかの薄膜形成用基板。 ' 項 132. 窒化アルミニウムを主成分とする焼結体が室温における熱伝導率 20 OW/mK 以上のものであることを特徴とする項 71、 72、 73、 74、 75、 76、 77、 78、 7
9、 80、 81、 82、 83、 84、 85、 86、 87、 88、 89、 90、 91、 92、 9 3、 94、 95、 96、 97、 98、 99、 100、 101、 102、 103、 104、 10
5、 106、 107、 108、 109、 110、 111、 112、 113、 114、 115、 116、 117、 118、 119、 120、 121、 122、 123、 124、 125、 12
6、 127、 128、 129、 130又は 131に記載されたいずれかの薄膜形成用基板。 項 133. 窒化アルミニウムを主成分とする焼結体が室温における熱伝導率 22 OW/mK 以上のものであることを特徴とする項 132に記載された薄膜形成用基板。
項 134. 窒化アルミニウムを主成分とする焼結体が相対密度 95%以上のものであること を纖とする項 71、 72、 73、 74、 75、 76、 77、 78、 79、 80、 81、 82、 83、 84、 85、 86、 87、 88、 89、 90、 91、 92、 93、 94、 95、 96、 97、 98、 99、 100、 101、 102、 103、 104、 105、 106、 107、 1
08、 109、 110、 111、 112、 113、 114、 115、 116、 117、 118、 119、 120、 121、 122、 123、 124、 125、 126、 127、 128、 12
9、 130、 131、 132又は 133に記載されたいずれかの薄膜形成用基板。
項 135. 窒化アルミニウムを主成分とする焼結体が相対密度 98%以上のものであること を特徴とする項 134に記載された薄膜形成用基板。
項 136. 窒化アルミニウムを主成分とする焼結体が空孔の平均大きさ 1 m以下のもので あることを體とする項 71、 72、 73、 74、 75、 76、 77、 78、 79、 80、 8
1、 82、 83、 84、 85、 86、 87、 88、 89、 90、 91、 92、 93、 94、 9 5、 96、 97、 98、 99、 100、 101、 102、 103、 104、 105、 106、 107、 108、 109、 110、 111、 112、 113、 114、 115、 116、 11
7、 118、 119、 120、 121、 122、 123、 124、 125、 126、 127、 128、 129、 130、 131、 132、 133、 134又は 135に記載されたいずれか の薄膜形成用基板。
項 137. 窒化アルミニウムを主成分とする焼結体が窒化アルミニウム粒子の大きさ平均 1 m以上のものであることを特徴とする項 71、 72、 73、 74、 75、 76、 77、 78、 79、 80、 81、 82、 83、 84、 85、 86、 87、 88、 89、 90、 91、 92、 93、 94、 95、 96、 97、 98、 99、 100、 101、 102、 103、 104、 1
05、 106、 107、 108、 109、 110、 111、 112、 113、 114、 115、 116、 117、 118、 119、 120、 121、 122、 123、 124、 125、 12
6、 127、 128、 129、 130、 131、 132、 133、 134又は 135に記載さ れたいずれかの薄膜形成用基板。
項 138. 窒化アルミニウム粒子の大きさが平均 5 以上であることを特徴とする項 13 7に記載された薄膜形成用基板。
項 139. 窒化アルミニウム粒子の大きさが平均 8 m以上であることを特徴とする項 13 7又は 138に記載されたいずれかの薄膜形成用基板。
項 140. 窒化アルミニウム粒子の大きさが平均 15 m以上であることを特徴とする項 1 37、 138又は 139に記載されたいずれかの薄膜形成用基板。
項 141. 窒化アルミニウム粒子の大きさが平均 25 /m以上であることを特徴とする項 1 37、 138、 139又ま 140に記載されたいずれかの薄膜形成用基板。
項 142. 窒化アルミニウムを主成分とする焼結体が窒化アルミニウム粒子の大きさ平均 1 00 m以下のものであることを特徴とする項 71、 72、 73、 74、 75、 76、 77、 78、 79、 80、 81、 82、 83、 84、 85、 86、 87、 88、 89、 90、 91、 92、 93、 94、 95、 96、 97、 98、 99、 100、 101、 102、 103、 10
4、 105、 106、 107、 108、 109、 110、 111、 112、 113、 114、 115、 116、 117、 118, 119、 120、 121、 122、 123、 124、 12
5、 126、 127、 128、 129、 130、 131、 132、 133、 134、 135、 136、 137、 138、 139、 140又は 141に記載されたいずれかの薄藤成用基板。 項 143. 平均表面粗さ Ra 2000 nm以下の窒化アルミニウムを主成分とする焼結体か らなることを特徴とする項 71、 72、 73、 74、 75、 76、 77、 78、 79、 80、 81、 82、 83、 84、 85、 86、 87、 88、 89、 90、 91、 92、 93、 94、 95、 96、 97、 98、 99、 100、 101、 102、 103、 104, 105、 106、 107、 108、 109、 110、 111、 112、 113、 114、 115、 116、 11
7、 118、 119、 120、 121、 122、 123、 124、 125、 126、 127、 128、 129、 130、 131、 132、 133、 134、 135、 136、 137、 13
8、 139、 140、 141又ま 142に記載されたいずれかの薄膜形成用基板。
項 144. 窒化アルミニウムを主成分とする焼結体の平均表面粗さが R a 1000 nm以下 であることを特徴とする項 143に記載された薄膜形成用基板。
項 145. 窒化アルミニウムを主成分とする焼結体の平均表面粗さが R 100 nm以下で あることを特徴とする項 143又は 144に記載されたいずれかの薄膜形成用基板。
項 146. 窒化アルミニウムを主成分とする焼結体の平均表面粗さが R a 20 nm以下であ ることを特徴とする項 143、 144又は 145に記載されたいずれかの薄膜形成用基板。 項 147. 表面粗さの大きい窒化アルミニウムを主成分とする焼結体からなることを特徴と する項 71、 72、 73、 74、 75、 76、 77、 78、 79、 80、 81、 82、 83、 84、 85、 86、 87、 88、 89、 90、 91、 92、 93、 94、 95、 96、 97、
W
466
98、 99、 100、 101、 102、 103、 104、 105、 106、 107、 108、 109、 110、 111、 112、 113、 114、 115、 116、 117、 118、 11 9、 120、 121、 122、 123、 124, 125、 126、 127、 128、 129、 130、 131、 132、 133、 134、 135、 136、 137、 138、 139、 14 0、 141、 142、 143、 144又は 145に記載されたいずれかの薄膜形成用基板。 項 148. 平均表面粗さ R a 70 nm以上の窒化アルミニウムを主成分とする焼結体からな ることを とする項 71、 72、 73、 74、 75、 76、 77、 78、 79、 80、 81、
82、 83、 84、 85、 86、 87、 88、 89、 90、 91、 92、 93、 94、 95、
96、 97、 98、 99、 100、 101、 102、 103、 104、 105、 106、 10
7、 108、 109、 110、 111、 112、 113、 114、 115、 116、 117、
118、 119、 120、 121、 122、 123、 124、 125、 126、 127、 12
8、 129、 130、 131、 132、 133、 134, 135、 136、 137、 138、 139、 140、 141、 142、 143、 144、 145又は 147に記載されたいずれか の薄膜形成用基板。
項 149. 窒化アルミニウムを主成分とする焼結体の平均表面粗さが R a 1000 nmより 大きいことを特徴とする項 148に記載された薄膜形成用基板。
項 150. 窒化アルミニウムを主成分とする焼結体の平均表面粗さが R a2000nmより 大きいことを特徴とする項 148又は 149に記載された薄膜形成用基板。
項 151. 窒化アルミニウムを主成分とする焼結体の表面が焼き放し (a s— f i r e;)、 ラ ッフ ¥磨、 ブラスト研磨、 鏡面研磨、 化学腐食及びプラズマガスによる腐食のうちから選ばれ た少なくともいずれかの状態であることを特徴とする項 71、 72、 73、 74、 75、 76、 77、 78、 79、 80、 81、 82、 83、 84、 85、 86、 87、 88、 89、 90、 91、 92、 93、 94、 95、 96、 97、 98、 99、 .100、 101、 102、 103、 104、 105、 106、 107、 108、 109、 110、 111、 112、 113、 11
4、 115、 116、 117、 118、 119、 120、 121、 122、 123、 124、 125、 126、 127、 128、 129、 130、 131、 132、 133、 134、 13
5、 136、 137、 138、 139、 140、 141、 142、 143、 144、 145、 146、 147、 148、 149又は 150に記載されたいずれかの薄膜形成用基板。
項 152. 窒化アルミニウムを主成分とする焼結体の表面が鏡面研磨された状態であること を特徴とする項 151に記載された薄膜形成用基板。
項 153. 厚みが 8. 0mm以下の窒化アルミニウムを主成分とする; ¾結体からなることを 特徴とする項 71、 72、 73、 74、 75、 76、 77、 78、 79、 80、 81、 82、
83、 84、 85、 86、 87、 88、 89、 90、 91、 92、 93、 94、 95、 96、
97、 98、 99、 100、 101、 102、 103、 104、 105、 106、 107、 1
08、 109、 110、 111、 112、 113、 114、 115、 116、 117、 118、
119, 120、 121、 122、 123、 124、 125、 126、 127、 128、 12
9、 130、 131、 132、 133、 134、 135、 136、 137、 138、 139、 140、 141、 142、 143、 144、 145、 146、 147、 148、 149、 15 0、 151又は 152に記載されたいずれかの薄膜形成用基板。
項 154. 窒化アルミニウムを主成分とする焼結体の厚みが 2. 5mm以下であることを特 徴とする項 153に記載された薄膜形成用基板。
項 155. 窒化アルミニウムを主成分とする焼結体の厚みが 1. 0 mm以下であることを特 徴とする項 153又は 154に記載されたいずれかの薄膜形成用基板。
項 156. 厚みが 0. 01mm以上の窒化アルミニウムを主成分とする焼結体からなること
を體とする項 71、 72、 73、 74、 75、 76、 77、 78、 79、 80、 81、 82、 83、 84、 85、 86、 87、 88、 89、 90、 91、 92、 93、 94、 95、 96、 97、 98、 99、 100、 101、 102、 103、 104、 105、 106、 107、 1
08、 109、 110、 111、 112、 113、 114、 115、 116、 117、 118、 119、 120、 121、 122、 123、 124、 125、 126、 127、 128、 12
9、 130、 131、 132、 133、 134、 135、 136、 137、 138、 139、 140、 141、 142、 143、 144、 145、 146、 147、 148、 149、 15 0、 151、 152、 153、 154又は 155に記載されたいずれかの薄膜形成用基板。 項 157. 窒化アルミニウムを主成分とする焼結体の厚みが 0. 05mm以上であることを 特徴とする項 156に記載された薄膜形成用基板。
項 158. 窒化アルミニウムを主成分とする焼結体が厚み 8. 0mm以下でありかつ光 率が 1%以上であることを特徴とする項 153、 154、 155、 156又は 157に記載さ れたいずれかの薄膜形成用基板。
項 159. 窒化アルミニウムを主成分とする焼結体が厚み 0. 0 lmm以上でありかつ光透 過率が 40%以上であることを特徴とする項 153、 154、 155、 156、 157又は1 58に記載されたいずれかの薄膜形成用基板。
項 160. 窒化ガリウム、 窒化インジウム、 窒化アルミニウムのうちから選ばれた少なくと も 1種以上を主成分とする薄膜を形成するための基板であって、 該基板は導通ビアを有する窒 化アルミニウムを主成分とする焼結体からなることを特徴とする項 71、 72、 73、 74、 75、 76、 77、 78、 79、 80、 81、 82、 83、 84、 85、 86、 87、 88、 89、 90、 91、 92、 93、 94、 95、 96、 97、 98、 99、 100、 101、 1
02、 103、 104、 105、 106、 107、 108、 109、 110、 111、 112、 113、 114、 115、 116、 117、 118、 119、 120、 121、 122、 12
3、 124、 125、 126、 127、 128、 129、 130、 131、 132、 133、 134、 135、 136、 137、 138、 139、 140、 141、 142、 143、 14
4、 145、 146、 147、 148、 149、 150、 151、 152、 153、 154、 155、 156、 157、 158又は 159に記載されたいずれかの薄膜形成用基板。
項 161. 窒化ガリウム、 窒化インジウム、 窒化アルミニウムのうちから選ばれた少なくと も 1種以上を主成分とする薄膜を形成するための基板であって、 該基板は窒化アルミニウムを 主成分とする焼結体からなり、 該基板中には基板の上下表面を電気的に接続する導通ビアを有 することを特徴とする項 160に記載された薄膜形成用基板。
項 162. 導通ビアが金、 銀、 銅、 アルミニウム、 鉄、 コバルト、 ニッケル、 ルテニウム、 ロジウム、 パラジウム、 オスミウム、 イリジウム、 白金、 モリブデン、 タングステン、 クロム、 チタン、 窒化チタン、 窒化ジルコニウムのうちから選ばれた少なくとも 1種以上を主成分とす る材料からなることを特徴とする項 160又は 161に記載されたいずれかの薄膜形成用基板。 項 163. 導通ビアが金、 銀、 銅、 アルミニウム、 鉄、 コバルト、 ニッケル、 ルテニウム、 ロジウム、 パラジウム、 オスミウム、 イリジウム、 白金、 モリブデン、 タングステン、 窒化チ タン、 窒化ジルコニウムのうちから選ばれた少なくとも 1種以上を主成分とし、 さらに窒化ァ ルミ二ゥム、 炭化珪素、 窒化珪素、 窒化ガリウム、 酸化亜鉛、 酸化ベリリウム、 酸化アルミ二 ゥム、 希土類 素化合物、 アル力リ土類金属化合物のうちから選ばれた少なくとも 1種以上の 材料を含有することを特徴とする項 160、 161又は 162に記載されたいずれかの薄膜形 成用基板。
項 164. 導通ビアがモリブデン、 タングステン、 銅、 窒化チタン、 窒化ジルコニウムのう ちから選ばれた少なくとも 1種以上を主成分とする材料からなることを,とする項 160、
161、 162又は 163に記載されたいずれかの薄膜形成用基板。
項 165. 導通ビアがモリブデン、 タングステン、 銅、 窒化チタン、 窒化ジルコニウムのう ちから選ばれた少なくとも 1種以上を主成分とし、 さらに窒化アルミニウム、 酸化アルミニゥ ム、 希土類 素化合物、 アルカリ土類金属化合物のうちから選ばれた少なくとも 1種以上の材 料を含有することを特徴とする項 160、 161、 162、 163又は 164に記載されたい ずれかの薄膜形成用基板。
項 166. 導通ビアが室温における抵抗率 1 X 10一3 Ω · cm以下の導電性材料からなるこ とを特徴とする項 160、 161、 162、 163、 164又は 165に記載されたいずれか の薄膜形成用基板。
項 167. 導通ビアが室温における抵抗率 1 X 10_4Ω · cm以下の導電性材料からなるこ とを特徴とする項 166に記載された薄膜形成用基板。
項 168. 導通ビアが室温における抵抗率 1 X 10— 5Ω · cm以下の導電性材料からなるこ とを特徴とする項 166又は 167に記載されたいずれかの薄膜形成用基板。
項 169. 導通ビアの大きさが 500
60、 161、
162、 163、 164、 165、 166、 167又は 168に記載されたいずれかの薄膜形 成用基板。
項 170. 導通ビアの大きさが 250 m以下であることを特徴とする項 169に記載され た薄膜形成用基板。
項 171. 導通ビアの大きさが 100 m以下であることを特徴とする項 169又は 170 に記載されたいずれかの薄膜形成用基板。
i 72. 導通ビアの大きさが 50 zm以下であることを特徴とする項 169、 170又は 171に記載されたいずれかの薄膜形成用基板。
項 173. 導通ビアの大きさが、 25 m以下であることを mとする項 169、 170、 1 71又は 172に記載されたいずれかの薄膜形成用基板。
項 174. 導通ビアの大きさが 1 m以上であることを特徴とする項 160、 161、 16 2、 163、 164、 165、 166、 167、 168、 169、 170、 171、 172又 は 173に記載されたいずれかの薄膜形成用基板。
項 175. 窒化ガリウム、 窒化インジウム、 窒化アルミニウムのうちから選ばれた少なくと も 1種以上を主成分とする薄膜が導通ビアの表面にも形成可能であることを特徴とする項 16 0、 161、 162、 163、 164、 165、 166、 167、 168、 169、 170、
171、 172、 173又は 174に記載されたいずれかの薄膜形成用基板。
項 176. 薄騰電性材料が形成された窒化アルミニウムを主成分とする焼結体からなるこ とを S [とする項 71、 72、 73、 74、 75、 76、 77、 78、 79、 80、 81、 8 2、 83、 84、 85、 86、 87、 88、 89、 90、 91、 92、 93、 94、 95、 9 6、 97、 98、 99、 100、 101、 102、 103、 104、 105、 106、 107、 108、 109、 110、 111、 112、 113、 114、 115、 116、 117、 11
8、 119、 120、 121、 122、 123、 124、 125、 126、 127、 128、 129、 130、 131、 132、 133、 134、 135、 136、 137、 138、 13
9、 140、 141、 142、 143、 144、 145、 146、 147、 148、 149、 150、 151、 152、 153、 154, 155、 156、 157、 158、 159、 16 0、 161、 162、 163、 164、 165、 166、 167、 168、 169、 170、 171、 172、 173、 174又は 175に記載されたいずれかの薄膜形成用基板。
項 177. 薄 電性材料が金属、 合金、 金属窒化物のうちから選ばれた少なくとも 1種以 上の材料からなることを特徴とする項 176に記載された薄膜形成用基板。
項 1 78. 薄騰電性材料が金、 銀、 銅、 アルミニウム、 鉄、 コバルト、 ニッケル、 ルテニ ゥム、 ロジウム、 パラジウム、 オスミウム、 イリジウム、 白金、 タンタル、 モリブデン、 タン ダステン、 クロム、 チタン、 ニッケル—クロム合金、 窒化チタン、 窒化ジルコニウム、 窒化夕 ンタル、 のうちから選ばれた少なくとも 1種以上を主成分とする材料からなることを とす る項 1 76又は 177に記載されたいずれかの薄膜形成用基板。
項 179. 薄膜導電性材料が少なくとも 2層以上で構成されていることを特徴とする項 17 6、 1 77又は 1 78に記載されたいずれかの薄膜形成用基板。
項 180.薄騰電性材料の厚みが 20 m以下であることを特徴とする項 176、 177、 178又は 179に記載されたいずれかの薄膜形成用基板。
項 181. 薄 電性材料と窒化ガリウム、 窒化インジウム、 窒化アルミニウムのうちから 選ばれた少なくとも 1種以上を主成分とする薄膜との接合強度が垂直引張り法で 2 KgZmm 2以上であることを特徴とする項 176、 177、 178、 179又は 180に記載されたいず れかの薄膜形成用基板。
項 182. 窒化アルミニウムを主成分とする粉末成形体又は焼結体を非酸化性雰囲気中 15 00°C以上の で 10分間以上 «することにより得られる窒化アルミニウムを主成分とす る焼結体からなることを 1とする項 71、 72、 73、 74、 75、 76、 77、 78、 7 9、 80、 81、 82、 83、 84、 85、 86、 87、 88、 89、 90、 91、 92、 9 3、 94、 95、 96、 97、 98、 99、 100、 101、 102、 103、 104、 10
5、 106、 107、 108、 109、 1 10、 1 1 1、 1 12、 1 13、 1 14、 1 15、 1 16、 1 17、 1 18、 1 19、 120、 121、 122、 123、 124、 125、 12
6、 127、 1 28、 129、 130、 131、 132、 133、 134、 135、 136、 137、 138、 139、 140、 141、 142、 143、 144、 145、 146、 14
7、 148、 149、 150、 151、 1 52、 153、 154、 155、 1 56、 157、 158、 1 59、 160、 16 1、 162、 163、 164、 165、 166、 167、 16
8、 169、 1 70、 171、 172、 173、 174、 175、 176、 177、 178、 179、 180又は 181に記載されたいずれかの薄膜形成用基板。
項 183. 窒化アルミニウムを主成分とする焼結体が窒化アルミニウムを主成分とする粉末 成形体又は焼結体を非酸化性雰囲気中 1750で以上の焼成 で 3時間以上加熱することに より得られることを特徴とする項 182に記載された薄膜形成用基板。
項 184. 窒化アルミニウムを主成分とする焼結体が希土類 素化合物及びアルカリ土類金 属化合物のうちから選ばれた少なくとも 1種以上の化合物を含む窒化アルミニウムを主成分と する粉末成形体又は焼結体を非酸化性雰囲気中 1750°C以上の温度で 3時間以上焼成し含ま れる成分のうち少なくとも希土 IS¾素化合物及びアルカリ土類金属化合物及び酸素を揮散 .除 去し減少せしめることにより得られることを特徴とする項 7 1、 72、 73、 74、 75、 7 6、 77、 78、 79、 80、 81、 82、 83、 84、 85、 86、 87、 88、 89、 9 0、 91、 92、 93、 94、 95、 96、 97、 98、 99、 100、 101、 102、 1
03、 104、 105、 106、 107、 108、 109、 1 10、 11 1、 1 12、 1 13、 1 14、 1 15、 1 16、 1 17、 1 18、 1 19、 120、 121、 122、 123、 12
4、 125、 126、 127、 128、 129、 130、 131、 132、 133、 134、 135、 136、 137、 138、 139、 140、 141、 142、 143、 144、 14
5、 146、 147、 148、 149、 150、 15 1、 1 52、 153、 1 54、 155、 1 56、 1 57、 158、 159、 160、 161、 162、 163、 164、 165、 16
6、 167、 168、 169、 170、 171、 172、 173、 174, 175、 176、 177、 178、 179、 180、 181、 182又は 183に記載されたいずれかの薄膜形
成用基板。
項 185. セラミック材料を主成分とする焼結体及び光透過性を有するセラミック材料を主 成分とする焼結体がそれぞれ六方晶系又は三方晶系のうちから選ばれた少なくともいずれかの 結晶構造を有するセラミック材料を主成分とする焼結体であることを TOとする項 1、 2、 3、 4、 5、 6、 7、 8、 9、 10、 11、 12、 13、 14、 15、 16、 17、 18、 19、 20、 21、 22、 23、 24、 25、 26、 27、 28、 29、 30、 31、 32、 33、 34、 35、 36、 37、 38、 39、 40、 41、 42、 43、 44、 45、 46、 47、 48、 49、 50、 51、 52、 53、 54、 55、 56、 57、 58、 59、 60、 61、 62、 63、 64、 65、 66、 67、 68、 69又は 70に記載されたいずれかの薄膜形成 用基板。
項 186. 六方晶系又は三方晶系のうちから選ばれた少なくともいずれかの結晶構造を有す るセラミック材料を主成分とする; ¾結体が 化亜鉛、 酸化ベリリウム、 酸化アルミニウム、 炭 化珪素、 窒化珪素、 窒化ガリウムのうちから選ばれた少なくとも 1種以上を主成分とする焼結 体からなることを特徴とする項 185に記載された薄膜形成用基板。
項 187. セラミック材料を主成分とする焼結体力壞化亜鉛を主成分とする焼結体であるこ とを特徴とする項 185又は 186に記載されたいずれかの薄膜形成用基板。
項 188. 酸化 «を主成分とする焼結体が光 ¾i性を有することを特徴とする項 186又 は 187に記載されたいずれかの薄膜形成用基板。
項 189. 酸化亜鉛を主成分とする焼結体が光 率 1%以上のものであることを [とす る項 186、 187又は 188に記載されたいずれかの薄膜形成用基板。
項 190. 酸化亜鉛を主成分とする焼結体が光 率 10%以上のものであることを特徴と する項 189に記載された薄膜形成用基板。
項 191. 酸化亜鉛を主成分とする焼結体が光透過率 20%以上のものであることを特徴と する項 189又は 190に記載されたいずれかの薄膜形成用基板。
項 192. 酸化亜鉛を主成分とする焼結体が光 ¾i率 30%以上のものであることを特徴と する項 189、 190又は 191に記載されたいずれかの薄膜形成用基板。
項 193. 酸化亜鉛を主成分とする焼結体が光透過率 40%以上のものであることを特徴と する項 189、 190、 191又は 192に記載されたいずれかの薄膜形成用基板。
項 194. 酸化亜鉛を主成分とする焼結体が光透過率 50%以上のものであることを特徴と する項 189、 190、 191、 192又は 193に記載されたいずれかの薄膜形成用基板。 項 195. 酸化亜鉛を主成分とする焼結体が光透過率 60%以上のものであることを特徴と する項 189、 190、 191、 192、 193又は 194に記載されたいずれかの薄膜形成 用基板。
項 196. 酸化亜鉛を主成分とする焼結体が光 ¾i率 80%以上のものであることを特徴と する項 189、 190、 191、 192、 193、 194又は 195に記載されたいずれかの 薄膜形成用基板。
項 197. 酸化亜鉛を主成分とする焼結体が光 ¾i率 1%未満のものであることを特徴とす る項 186、 187又は 188に記載されたいずれかの薄膜形成用基板。
項 198. 酸化亜鉛を主成分とする焼結体が光透過率 0%のものであることを特徴とする項 197に記載された薄膜形成用基板。
項 199. 酸化«を主成分とする焼結体が導電性を有するものであることを特徴とする項 186、 187、 188、 189、 190、 191、 192、 193、 194、 195、 19 6、 197又は 198に記載されたいずれかの薄膜形成用基板。
項 200.酸化亜鉛を主成分とする搬吉体が室温における抵抗率 1 X 102Ω · cm以下のも
のであることを ^[とする項 186、 187、 188、 189、 190、 191、 192、 1 93、 194、 195、 196、 197、 198又は 199に記載されたいずれかの薄膜形成 用基板。
項 201.酸化亜鉛を主成分とする焼結体が室温における抵抗率 1 X 10。Ω · cm以下のも のであることを特徴とする項 200に記載された薄膜形成用基板。
項 202. 酸化亜鉛を主成分とする焼結体が室温における抵枋率 1 X 1 Ο^Ω - cm以下の ものであることを特徴とする項 200又は 201に記載されたいずれかの薄膜形成用基板。 項 203. 酸化亜鉛を主成分とする焼結体が室温における厳率 1 X 10— 2Ω · cm以下の ものであることを特徴とする項 200, 201又は 202に記載されたいずれかの薄膜形成用 項 204. 酸化亜鉛を主成分とする焼結体が光¾^ '生を有し力つ導電性を有するものである ことを特徴とする項 186、 187、 188、 189、 190、 191、 192、 193、 1 94、 195、 196、 197、 198、 199、 200、 201、 202又は 203に記載 されたいずれかの薄膜形成用基板。
項 205. 酸化亜鉛を主成分とする焼結体がアルミニウム成分を含むものであることを « とする項 186、 187、 188、 189、 190、 191、 192、 193、 194、 19 5、 196、 197、 198、 199、 200、 201、 202、 203又は 204に記載さ れたいずれかの薄膜形成用基板。
項 206. 酸化亜鉛を主成分とする焼結体が 化亜鉛成分を Z n〇換算で 55. 0モル%以 上含有するものであることを特徴とする項 186、 187、 188、 189、 190、 191、 192、 193、 194、 195、 196、 197、 198、 199、 200、 201、 20 2、 203、 204又は 205に記載されたいずれかの薄膜形成用基板。
項 207. 酸化 «を主成分とする焼結体がアルミニウム成分を A 1203騰で 45. 0モ ル%以下含むものであることを [とする項 186、 187、 188、 189、 190、 19 1、 192、 193、 194、 195、 196、 197、 198、 199、 200、 201、 202、 203、 204、 205又は 206に記載されたいずれかの薄膜形成用基板。
項 208. 酸化亜鉛を主成分とする焼結体がアルミニウム成分を A 12〇3換算で 0. 001 モル%〜45. 0モル%の範囲含むものであることを特徴とする項 207に記載された薄膜形 成用基板。
項 209. 酸化亜鉛を主成分とする焼結体がアルミニウム成分を A 1203換算で 0. 005 モル%〜45. 0モル%の範囲含むものであることを特徴とする項 207又は 208に記載さ れたいずれかの薄膜形成用基板。
項 210. 酸化亜鉛を主成分とする焼結体がアルミニウム成分を A 12〇3 で0. 02モ ル%〜45. 0モル%の範囲含むものであることを特徴とする項 207、 208又は 209に 記載されたいずれかの薄膜形成用基板。
項 211. 酸化亜鉛を主成分とする焼結体がアルミニウム成分を A 12〇3騰で 0. 08モ ル%〜35. 0モル%の範囲含むものであることを特徴とする項 207、 208、 209又は 210に記載されたいずれかの薄膜形成用基板。
項 212. 酸化亜鉛を主成分とする焼結体がアルカリ土類金属成分、 希土類 素成分、 遷移 金属成分及び 素成分のうちから選ばれた少なくとも 1種以上の成分を含むものであることを 特徴とする項 186、 187、 188、 189、 190、 191、 192、 193、 194、 195、 196、 197、 198、 199、 200、 201、 202、 203、 204、 20 5、 206、 207、 208、 209、 210又は 211に記載されたいずれかの薄膜形成用
項 213. 酸化 ¾を主成分とする焼結体が希土類 素成分及び遷移金属成分のうちから選 ばれた少なくとも 1種以上の成分を含むものであることを特徴とする項 212に記載された薄 膜形成用基板。
項 214. 酸化 βを主成分とする焼結体が希土^ ¾素成分のうちから選ばれた少なくとも 1種以上の成分を含むものであることを特徴とする項 212又は 213に記載されたいずれか の薄膜形成用基板。
項 215. 酸化 ¾を主成分とする焼結体が希土 ¾素成分のうちから選ばれた少なくとも 1種以上の成分を含む光透過性を有するものであることを特徴とする項 214に記載された薄 膜形成用基板。
項 216. 酸化亜鉛を主成分とする焼結体が希土類 素成分のうちから選ばれた少なくとも 1種以上の成分を含む^ 率 30%以上のものであることを特徴とする項 214又は 215 に記載されたいずれかの薄膜形成用基板。
項 217. 性あるいは光 ¾ 率が少なくとも波長 200 nm〜800 nmの範囲の光 に対してのものであることを特徴とする項 188、 189、 190、 191、 192、 193、 194、 195、 196、 197、 204、 215又は 216に記載されたいずれかの薄膜形 成用基板。
項 218. 酸化 ¾を主成分とする焼結体が遷移金属成分のうちから選ばれた少なくとも 1 種以上の成分を含むものであることを特徴とする項 212又は 213に記載されたいずれかの 薄膜形成用基板。
項 219. 酸化亜鉛を主成分とする焼結体が希土類 J£素成分及び遷移金属成分のうちから選 ばれた少なくとも 1種以上の成分を酸化物換算で 10. 0モル%以下含むものであることを特 徴とする項 212、 213、 214、 215、 216又は 218に記載されたいずれかの薄膜 形成用基板。
項 220. 酸化亜鉛を主成分とする焼結体がアルミニウム成分を含み、 同時に希土類元素成 分及び遷移金属成分のうちから選ばれた少なくとも 1種以上の成分を含むものであることを特 徴とする項 186、 187、 188、 189、 190、 191、 192、 193、 194、 1 95、 196、 197、 198、 199、 200、 201、 202、 203、 204、 205、 206、 207、 208、 209、 210、 211、 212、 213、 214、 215、 21 6、 217、 218又は 219に記載されたいずれかの薄膜形成用基板。
項 221. 酸化亜鉛を主成分とする焼結体がアルミニウム成分を含み同時に希土類 素成分 のうちから選ばれた少なくとも 1種以上の成分を含むものであることを特徴とする項 220に 記載された薄膜形成用基板。
項 222. 酸化亜鉛を主成分とする焼結体がアルミニウム成分を含み同時に遷移金属成分の うちから選ばれた少なくとも 1種以上の成分を含むものであることを ii [とする項 220に記 載された薄膜形成用基板。
項 223. 酸化亜鉛を主成分とする焼結体が希土 m¾素成分及び遷移金属成分のうちから選 ばれた少なくとも 1種以上の成分を酸化物換算で 10. 0モル%以下含むものであることを特 徴とする項 220、 221又は 222に記載されたいずれかの薄膜形成用基板。
項 224. 酸化亜鉛を主成分とする焼結体が希土^ ¾素成分のうちから選ばれた少なくとも 1種以上の成分を酸化物 で 10. 0モル%以下含むものであることを特徴とする項 223 に記載された薄膜形成用基板。
項 225. 酸化亜鉛を主成分とする焼結体が遷移金属成分のうちから選ばれた少なくとも 1 種以上の成分を酸化物換算で 10. 0モル%以下含むものであることを特徴とする項 223又 は 224に記載されたいずれかの薄膜形成用基板。
項 226· 遷移金属成分が鉄及びクロムのうちから選ばれた少なくとも 1種以上の成分であ ることを特徴とする項 212、 213、 218、 219、 220、 222、 223又は 225 に記載されたいずれかの薄膜形成用基板。
項 227. 酸化亜鉛を主成分とする焼結体がアルミニゥム成分を A 12 O 3換算で 45. 0モ ル%以下含み、 同時に希土類 素成分のうちから選ばれた少なくとも 1種以上の成分を酸化物 騰で 10. 0モル%以下含むものであることを; 1¾| [とする項 220、 221、 222、 22 3、 224、 225又は 226に記載されたいずれかの薄膜形成用基板。
項 228 · 酸化亜鉛を主成分とする焼結体がアルミニゥム成分を A 12〇 3換算で 45. 0モ ル%以下含み、 同時に希土類 £素成分のうちから選ばれた少なくとも 1種以上の成分を酸化物 換算で 0. 0002モル%〜10. 0モル%の範囲含むものであることを特徴とする項 227 に記載された薄膜形成用基板。
項 229. 酸化亜鉛を主成分とする焼結体がアルミニウム成分を A 1203換算で 45. 0モ ル%以下含み、 同時に希土類 素成分のうちから選ばれた少なくとも 1種以上の成分を酸化物 で 0. 0006モル%〜6. 0モル%の範囲含むものであることを特徴とする項 227又 は 228に記載されたいずれかの薄膜形成用基板。
項 230. 酸化亜鉛を主成分とする焼結体がアルミニゥム成分を A 12 O 3換算で 45. 0モ ル%以下含み、 同時に希土 M¾素成分のうちから選ばれた少なくとも 1種以上の成分を酸化物 換算で 0. 001モル%〜6. 0モル%の範囲含むものであることを特徴とする項 227、 2 28又は 229に記載されたいずれかの薄膜形成用基板。
項 231. 酸化亜鉛を主成分とする焼結体がアルミニウム成分を A 1203鍵で 45. 0モ ル%以下含み、 同時に希土^素成分のうちから選ばれた少なくとも 1種以上の成分を酸化物 換算で 0. 002モル%〜3. 0モル%の範囲含むものであることを特徴とする項 227、 2 28、 229又は 230に記載されたいずれかの薄膜形成用基板。
項 232. 酸化碰を主成分とする焼結体がアルミニウム成分を A 1203換算で 0. 001 モル%〜45. 0モル%の範囲含み、 同時に希土類元素成分のうちから選ばれた少なくとも 1 種以上の成分を含むものであることを特徴とする項 220、 221、 222、 223、 224、 225、 226、 227、 228、 229、 230又は 231に記載されたいずれかの薄膜形 成用基板。
項 233. セラミック材料を主成分とする焼結体が 化ベリリウムを主成分とする焼結体で あることを特徴とする項 185又は 186に記載されたいずれかの薄膜形成用基板。
項 234. 酸化ベリリウムを主成分とする焼結体が光透過性を有することを特徴とする項 1 86又は 233に記載されたいずれかの薄膜形成用基板。
項 235. 酸化ベリリゥムを主成分とする焼結体が光 率 1 %以上のものであることを特 徴とする項 186、 233又は 234に記載されたいずれかの薄膜形成用基板。
項 236. 酸化べリリウムを主成分とする焼結体が光透過率 10 %以上のものであることを 特徴とする項 235に記載された薄膜形成用基板。
項 237. 酸化べリリゥムを主成分とする焼結体が ¾¾1率 20 %以上のものであることを 特徵とする項 235又は 236に記載されたいずれかの薄膜形成用基板。
項 238. 酸化ベリリゥムを主成分とする焼結体が光透過率 30 %以上のものであることを 特徴とする項 235、 236又は 237に記載されたいずれかの薄膜形成用基板。
項 239. 酸化べリリゥムを主成分とする焼結体が光 ¾1率 40 %以上のものであることを 特徴とする項 235、 236、 237又は 238に記載されたいずれかの薄膜形成用基板。 項 240. 酸化ベリリウムを主成分とする焼結体が光 ¾i率 50%以上のものであることを 特徴とする項 235、 236、 237、 238又は 239に記載されたいずれかの薄膜形成用
項 241. 酸化べリリゥムを主成分とする焼結体が光透過率 60 %以上のものであることを 特徵とする項 235、 236、 237、 238、 239又は 240に記載されたいずれかの薄 膜形成用基板。
項 242. 酸化ベリリウムを主成分とする焼結体が光 ¾ 率 80 %以上のものであることを 特徴とする項 235、 236、 237、 238、 239、 240又は 241に記載されたいず れかの薄膜形成用基板。
項 243. 酸化ベリリウムを主成分とする焼結体が光 ¾1率 1 %未満のものであることを特 徴とする項 185、 186、 233又は 234に記載されたいずれかの薄膜形成用基板。 項 244. 酸化べリリゥムを主成分とする焼結体が光 率 0 %のものであることを特徴と する項 243に記載された薄膜形成用基板。
項 245. 光 性あるいは光 ¾i率が少なくとも波長 200 nm〜800 nmの範囲の光 に対してのものであることを特徴とする項 234、 235、 236、 237、 238、 239、 240、 241、 242、 243又は 244に記載されたいずれかの薄膜形成用基板。
項 246. 酸化ベリリウムを主成分とする焼結体がマグネシウム成分、 カルシウム成分及び 珪素成分のうちから選ばれた少なくとも 1種以上の成分を含むものであることを特徴とする項 186、 233、 234、 235、 236、 237、 238、 239、 240、 241、 24 2、 243、 244又は 245に記載されたいずれかの薄膜形成用基板。
項 247.酸化ベリリウムを主成分とする焼結体が ¾化ベリリウム成分を Be〇騰で 65. 0モル%以上含むものであることを特徴とする項 186、 233、 234、 235、 236、
237、 238、 239、 240、 241、 242、 243、 244、 245又は 246に記 載されたいずれかの薄膜形成用基板。
項 248. 酸化ベリリゥムを主成分とする焼結体がマグネシウム成分、 カルシウム成分、 珪 素成分のうちから選ばれた少なくとも 1種以上の成分を酸化物騰で合計 35. 0モル%以下 含むものであることを特徴とする項 186、 233、 234、 235、 236、 237、 23 8、 239、 240、 241、 242、 243、 244、 245、 246又は 247に記載さ れたいずれかの薄膜形成用基板。
項 249. 酸化ベリリゥムを主成分とする焼結体がマグネシウム成分、 カルシウム成分、 珪 素成分のうちから選ばれた少なくとも 1種以上の成分を酸化物 で合計 0. 0002モル% 〜35. 0モル%の範囲含むものであることを特徴とする項 248に記載された薄膜形成用基 板。
項 250. 酸化ベリリウムを主成分とする焼結体がマグネシウム成分、 カルシウム成分、 珪 素成分のうちから選ばれた少なくとも 1種以上の成分を酸化物 で合計 0. 001モル%〜 35. 0モル%の範囲含むものであることを特徴とする項 248又は 249に記載されたいず れかの薄膜形成用基板。
項 251. 酸化ベリリウムを主成分とする焼結体がマグネシウム成分、 カルシウム成分、 珪 素成分のうちから選ばれた少なくとも 1種以上の成分を酸化物 で合計 0. 004モル%〜
35. 0モル%の範囲含むものであることを特徴とする項 248、 249又は 250に記載さ れたいずれかの薄膜形成用基板。
項 252. 酸化ベリリウムを主成分とする焼結体がマグネシウム成分、 カルシウム成分、 珪 素成分のうちから選ばれた少なくとも 1種以上の成分を酸化物^:で合計 0. 015モル%〜 25. 0モル%の範囲含むものであることを特徴とする項 246、 247、 248、 249、 250又は 251に記載されたいずれかの薄膜形成用基板。
項 253. 酸化ベリリウムを主成分とする焼結体がマグネシウム成分、 カルシウム成分、 珪
素成分のうちから選ばれた少なくとも 1種以上の成分を含み、 同時に希土類 素成分のうちか ら選ばれた少なくとも 1種以上の成分を含むものであることを特徴とする項 1 8 6、 2 3 3、 2 3 4、 2 3 5、 2 3 6、 2 3 7、 2 3 8、 2 3 9、 2 4 0、 2 4 1、 2 4 2、 2 4 3、 2 4
4、 2 4 5、 2 4 6、 2 4 7、 2 4 8、 2 4 9、 2 5 0、 2 5 1又は 2 5 2に記載されたいず れかの薄膜形成用基板。
項 2 5 4. 酸ィ匕ベリリウムを主成分とする焼結体がマグネシウム成分、 カルシウム成分、 珪 素成分のうちから選ばれた少なくとも 1種以上の成分を含み、 同時に希土類 素成分のうちか ら選ばれた少なくとも 1種以上の成分を酸化物■で 5. 0モル%以下含むものであることを 特徴とする項 2 5 3に記載された薄膜形成用基板。
項 2 5 5. 酸化ベリリウムを主成分とする焼結体がマグネシウム成分、 カルシウム成分、 珪 素成分のうちから選ばれた少なくとも 1種以上の成分を酸化物 で 3 5. 0モル%以下含み、 同時に希土 ¾素成分のうちから選ばれた少なくとも 1種以上の成分を酸化物 で 5 · 0モ ル%以下含むものであることを特徴とする項 2 5 3又は 2 5 4に記載されたいずれかの薄膜形 成用基板。
項 2 5 6. 酸化ベリリウムを主成分とする焼結体がマグネシウム成分、 カルシウム成分、 珪 素成分のうちから選ばれた少なくとも 1種以上の成分を酸化 で 3 5. 0モル%以下含み、 同時に希土^ 5素成分のうちから選ばれた少なくとも 1種以上の成分を酸化物換算で 0. 0 0 0 0 5モル%〜5. 0モル%の範囲含むものであることを特徴とする項 2 5 3、 2 5 4又は 2 5 5に記載されたいずれかの薄膜形成用基板。
項 2 5 7. 酸化ベリリウムを主成分とする焼結体がマグネシウム成分、 カルシウム成分、 珪 素成分のうちから選ばれた少なくとも 1種以上の成分を酸化猶算で 3 5. 0モル%以下含み、 同時に希土 素成分のうちから選ばれた少なくとも 1種以上の成分を酸化物騰で 0 , 0 0 0 5モル%〜3. 0モル%の範囲含むものであることを特徴とする項 2 5 3、 2 5 4、 2 5 5 又は 2 5 6に記載されたいずれかの薄膜形成用基板。
項 2 5 8. 酸化ベリリゥムを主成分とする焼結体がマグネシウム成分、 カルシウム成分、 珪 素成分のうちから選ばれた少なくとも 1種以上の成分を酸化 で 3 5. 0モル%以下含み、 同時に希土類 素成分のうちから選ばれた少なくとも 1種以上の成分を酸化物 で 0. 0 0 2モル%〜3. 0モル%の範囲含むものであることを特徴とする項 2 5 3、 2 5 4、 2 5 5、 2 5 6又は 2 5 7に記載されたいずれかの薄膜形成用基板。
項 2 5 9. 酸化ベリリウムを主成分とする焼結体がマグネシウム成分、 カルシウム成分、 珪 素成分のうちから選ばれた少なくとも 1種以上の成分を酸化物騰で 3 5. 0モル%以下含み、 同時に希土 素成分のうちから選ばれた少なくとも 1種以上の成分を酸化物■で 0. 0 0 5モル%〜3. 0モル%の範囲含むものであることを特徴とする項 2 5 3、 2 5 4、 2 5 5、 2 5 6、 2 5 7又は 2 5 8に記載されたいずれかの薄膜形成用基板。
項 2 6 0. 酸化ベリリウムを主成分とする焼結体がマグネシウム成分、 カルシウム成分、 珪 素成分のうちから選ばれた少なくとも 1種以上の成分を酸化物 で 0. 0 0 0 2モル%〜3
5. 0モル%の範囲含み、 同時に希土類 素成分のうちから選ばれた少なくとも 1種以上の成 分を含むものであることを特徴とする項 2 5 3、 2 5 4、 2 5 5、 2 5 6、 2 5 7、 2 5 8又 は 2 5 9に記載されたいずれかの薄膜形成用基板。
項 2 6 1 . セラミック材料を主成分とする焼結体が 化アルミニウムを主成分とする焼結体 であることを特徴とする項 1 8 5又は 1 8 6に記載されたいずれかの薄膜形成用基板。
項 2 6 2. 酸化アルミニウムを主成分とする焼結体が光 性を有することを特徴とする項 1 8 6又は 2 6 1に記載されたいずれかの薄膜形成用基板。
項 2 6 3. 酸化アルミニウムを主成分とする焼結体が光透過率 1 %以上のものであることを
特徴とする項 186、 261又は 262に記載されたいずれかの薄膜形成用基板。 項 264. 酸化アルミニウムを主成分とする焼結体が光 ¾ϋ率 10 %以上のものであること を特徴とする項 263に記載された薄膜形成用基板。
項 265. 酸化アルミニウムを主成分とする焼結体が 過率 20%以上のものであること を特徴とする項 263又は 264に記載されたいずれかの薄膜形成用基板。
項 266. 酸化アルミニウムを主成分とする焼結体が ½¾i率 30%以上のものであること を特徴とする項 263, 264又は 265に記載されたいずれかの薄膜形成用基板。
項 267. 酸化アルミニウムを主成分とする焼結体が 率 40%以上のものであること を特徴とする項 263、 264、 265又は 266に記載されたいずれかの薄膜形成用基板。 項 268. 酸化アルミニウムを主成分とする焼結体が光 ¾i率 50%以上のものであること を特徴とする項 263、 264、 265、 266又は 267に記載されたいずれかの薄膜形成 用基板。
項 269. 酸化アルミニウムを主成分とする焼結体力 率 60%以上のものであること を特徴とする項 263、 264、 265、 266、 267又は 268に記載されたいずれかの 薄膜形成用基板。
項 270. 酸化アルミニウムを主成分とする焼結体が) 率 80%以上のものであること を體とする項 263、 264、 265、 266、 267、 268又は 269に記載されたい ずれかの薄膜形成用基板。
項 271. 酸化アルミニウムを主成分とする焼結体が光 Mil率 1%未満のものであることを 特徴とする項 185、 186、 261又は 262に記載されたいずれかの薄膜形成用基板。 項 272. 酸化アルミニウムを主成分とする焼結体が ½¾i率 0%のものであることを特徴 とする項 271に記載された薄膜形成用基板。
項 273. 光 性あるいは光 ¾ii率が少なくとも波長 200 nm〜800 nmの範囲の光 に対してのものであることを特徴とする項 262、 263、 264、 265、 266、 267、 268、 269、 270、 271又は 272に記載されたいずれかの薄膜形成用基板。
項 274. 酸化アルミニウムを主成分とする焼結体がマグネシウム成分、 カルシウム成分及 び 素成分のうちから選ばれた少なくとも 1種以上の成分を含むものであることを特徴とする 項 261、 262、 263、 264、 265、 266、 267、 268、 269、 270、 2 71、 272又は 273に記載されたいずれかの薄膜形成用基板。
項 275. 酸化アルミニウムを主成分とする焼結体が ¾化アルミニウム成分を A 1203購 で 55. 0モル%以上含むものであることを特徴とする項 186、 261、 262、 263、 264、 265、 266、 267、 268、 269、 270、 271、 272、 273又は 2 74に記載されたいずれかの薄膜形成用基板。
項 276. 酸化アルミニウムを主成分とする焼結体がマグネシウム成分、 カルシウム成分、 珪素成分のうちから選ばれた少なくとも 1種以上の成分を酸化物換算で合計 45. 0モル%以 下含むものであることを特徴とする項 186、 261、 262、 263、 264、 265、 2 66、 267、 268、 269、 270、 271、 272、 273、 274又は 275に記載 されたいずれかの薄膜形成用基板。
項 277. 酸化アルミニウムを主成分とする焼結体がマグネシウム成分、 カルシウム成分、 珪素成分のうちから選ばれた少なくとも 1種以上の成分を酸化物 で合計 0. 001モル% 〜45. 0モル%の範囲含むものであることを特徴とする項 276に記載された薄膜形成用基 板。
項 278. 酸化アルミニウムを主成分とする焼結体がマグネシウム成分、 カルシウム成分、 珪素成分のうちから選ばれた少なくとも 1種以上の成分を酸化物^:で合計 0. 005モル%
〜4 5. 0モル%の範囲含むものであることを特徴とする項 2 7 6又は 2 7 7に記載されたい ずれかの薄膜形成用基板。
項 2 7 9. 酸化アルミニウムを主成分とする焼結体がマグネシウム成分、 カルシウム成分、 珪素成分のうちから選ばれた少なくとも 1種以上の成分を酸化物 で合計 0. 0 2モル%〜 4 5. 0モル%の範囲含むものであることを特徴とする項 2 7 6、 2 7 7又は 2 7 8に記載さ れたいずれかの薄膜形成用基板。
項 2 8 0. 酸化アルミニウムを主成分とする焼結体がマグネシウム成分、 カルシウム成分、 珪素成分のうちから選ばれた少なくとも 1種以上の成分を酸化物^^で合計 0. 0 8モル%〜 3 5. 0モル%の範囲含むものであることを特徴とする項 2 7 6、 2 7 7、 2 7 8又は 2 7 9 に記載されたいずれかの薄膜形成用基板。
項 2 8 1 . 酸化アルミニウムを主成分とする焼結体力雙化アルミニウムを主成分としその他 にマグネシウム成分、 カルシウム成分、 珪素成分のうちから選ばれた少なくとも 1種以上の成 分を含み、 同時に希土類 素成分のうちから選ばれた少なくとも 1種以上の成分を含むもので あることを^とする項 1 8 6、 2 6 1、 2 6 2、 2 6 3、 2 6 4、 2 6 5、 2 6 6、 2 6 7、 2 6 8、 2 6 9、 2 7 0、 2 7 1、 2 7 2、 2 7 3、 2 7 4、 2 7 5、 2 7 6、 2 7 7、 2 7 8、 2 7 9又は 2 8 0に記載されたレずれかの薄膜形成用基板。
項 2 8 2. 酸化アルミニウムを主成分とする焼結体がマグネシウム成分、 カルシウム成分、 珪素成分のうちから選ばれた少なくとも 1種以上の成分を含み、 同時に希土類 素成分のうち から選ばれた少なくとも 1種以上の成分を酸化物換算で 1 0. 0モル%以下含むものであるこ とを特徴とする項 2 8 1に記載された薄膜形成用基板。
項 2 8 3. 酸化アルミニウムを主成分とする焼結体がマグネシウム成分、 カルシウム成分、 珪素成分のうちから選ばれた少なくとも 1種以上の成分を酸化物換算で 4 5. 0モル%以下含 み、同時に希土類 J£素成分のうちから選ばれた少なくとも 1種以上の成分を酸化 で 1 0. 0モル%以下含むものであることを特徴とする項 2 8 1又は 2 8 2に記載されたいずれかの薄 膜形成用基板。
項 2 8 4. 酸化アルミニウムを主成分とする焼結体がマグネシウム成分、 カルシウム成分、 珪素成分のうちから選ばれた少なくとも 1種以上の成分を酸化物^^で 4 5. 0モル%以下含 み、 同時に希土類 素成分のうちから選ばれた少なくとも 1種以上の成分を酸化物騰で 0. 0 0 0 2モル%〜1 0. 0モル%の範囲含むものであることを特徴とする項 2 8 1、 2 8 2又 は 2 8 3に記載されたいずれかの薄膜形成用基板。
項 2 8 5. 酸化アルミニウムを主成分とする焼結体がマグネシウム成分、 カルシウム成分、 珪素成分のうちから選ばれた少なくとも 1種以上の成分を酸化物換算で 4 5. 0モル%以下含 み、 同時に希土 ¾素成分のうちから選ばれた少なくとも 1種以上の成分を酸化物^:で 0. 0 0 1モル%〜6. 0モル%の範囲含むものであることを特徴とする項 2 8 1、 2 8 2、 2 8 3又は 2 8 4に記載されたいずれかの薄膜形成用基板。
項 2 8 6. 酸化アルミニウムを主成分とする焼結体がマグネシウム成分、 カルシウム成分、 珪素成分のうちから選ばれた少なくとも 1種以上の成分を酸化物^:で 4 5. 0モル%以下含 み、 同時に希土 素成分のうちから選ばれた少なくとも 1種以上の成分を酸化物換算で 0. 0 0 5モル%〜6. 0モル%の範囲含むものであることを特徴とする項 2 8 1、 2 8 2、 2 8 3 , 2 8 4又は 2 8 5に記載されたいずれかの薄膜形成用基板。
項 2 8 7. 酸化アルミニウムを主成分とする焼結体がマグネシウム成分、 カルシウム成分、 珪素成分のうちから選ばれた少なくとも 1種以上の成分を酸化物^で 4 5. 0モル%以下含 み、 同時に希土類 素成分のうちから選ばれた少なくとも 1種以上の成分を酸化物騰で 0. 0 1モル%〜6. 0モル%の範囲含むものであることを [とする項 2 8 1、 2 8 2、 2 8 3、
284、 285又は 286に記載されたいずれかの薄膜形成用基板。
項 288. 酸化アルミニウムを主成分とする焼結体がマグネシウム成分、 カルシウム成分、 珪素成分のうちから選ばれた少なくとも 1種以上の成分を酸化物 で 0. 001モル%〜 4 5. 0モル%の範囲含み、 同時に希土類 素成分のうちから選ばれた少なくとも 1種以上の成 分を含むものであることを [とする項 281、 282、 283、 284、 285、 286又 は 287に記載されたいずれかの薄膜形成用基板。
項 289. 酸化アルミニウムを主成分とする焼結体がマグネシウム成分、 カルシウム成分、 珪素成分のうちから選ばれた少なくともいずれか 2種以上の成分を含むものであることを特徴 とする項 186、 261、 262、 263、 264、 265、 266、 267、 268、 26 9、 270、 271、 272、 273、 274, 275、 276、 277、 278、 279、 280、 281、 282、 283、 284、 285、 286、 287又は 288に記載された いずれかの薄膜形成用基板。
項 290. セラミック材料を主成分とする焼結体が窒化ガリウムを主成分とする焼結体であ ることを特徴とする項 185又は 186に記載されたいずれかの薄膜形成用基板。
項 291. 窒化ガリウムを主成分とする焼結体が光 ¾ 性を有することを特徴とする項 29 0に記載された薄膜形成用基板。
項 292. 窒化ガリウムを主成分とする焼結体が光 ¾ 率 1%以上を有するものであること を特徴とする項 290又は 291に記載されたいずれかの薄膜形成用基板。
項 293. 窒化ガリウムを主成分とする撫裙体が導電性を有することを ii [とする項 290、 291又は 292に記載されたいずれかの薄膜形成用基板。
項 294. 窒化ガリウムを主成分とする 結体が室温における抵抗率 1 X 104Ω · cm以下 を有するものであることを特徴とする項 290、 291、 292又は 293に記載されたいず れかの薄膜形成用基板。
項 295. 窒化ガリウムを主成分とする焼結体がアルカリ土類金属及び希土類 素のうちか ら選ばれた少なくとも 1種以上の成分を含有することを特徴とする項 290、 291、 292、 293又は 294に記載されたいずれかの薄膜形成用基板。
項 296. 窒化ガリウムを主成分とする焼結体が ¾、 カドミウム、 炭素、 珪素、 ゲルマ二 ゥム、 セレン、 及びテルルのうちから選ばれた少なくとも 1種以上の成分を含有することを特 徴とする項 290、 291、 292、 293、 294又は 295に記載されたいずれかの薄膜 形成用基板。
項 297. 窒化ガリウムを主成分とする焼結体がアルミニウム、 インジウム、 及び酸素のう ちから選ばれた少なくとも 1種以上の成分を含有することを特徴とする項 290、 291、 2 92、 293、 294、 295又は 296に記載されたいずれかの薄膜形成用基板。
項 298. 窒化ガリウムを主成分とする焼結体が遷移金属のうちから選ばれた少なくとも 1 種以上の成分を含有することを特徴とする項 290、 291、 292、 293、 294、 29 5、 296又は 297に記載されたいずれかの薄膜形成用基板。
項 299. 窒化ガリウムを主成分とする焼結体が金属ガリウムの直接窒化による窒化ガリウ ムを主成分とする粉末を原料として作製されたものであることを特徴とする項 290、 291、 292、 293、 294、 295、 296、 297又は 298に記載されたいずれかの薄膜形 成用基 ® o
項 300. 窒化ガリウムを主成分とする焼結体が mi匕ガリウムの^ ΰ窒化による窒化ガリウ ムを主成分とする粉末を原料として作製されたものであることを 1数とする項 290、 291、 292、 293、 294、 295、 296、 297又は 298に記載されたいずれかの薄膜形 成用基板。
項 301. 窒化ガリウムを主成分とする焼結体が気体状のガリウム化合物の窒化による窒化 ガリウムを主成分とする粉末を原料として作製されたものであることを特徴とする項 290、 291、 292、 293、 294、 295、 296、 297又は 298に記載されたいずれか の薄膜形成用基板。
項 302. 平均表面粗さ R a 2000 nm以下の六方晶系又 方晶系のうちから選ばれた 少なくともいずれかの結晶構造を有するセラミック材料を主成分とする焼結体からなることを 特徴とする項 185、 186、 187、 188、 189、 190、 191、 192、 193、
194, 195、 196、 197、 198、 199、 200、 201、 202、 203、 20
4、 205、 206、 207、 208、 209、 210、 211、 212、 213、 214、 215、 216、 217、 218、 219、 220、 221、 222、 223、 224、 22
5、 226、 227、 228、 229、 230、 231、 232、 233、 234、 235、
236、 237、 238、 239、 240、 241、 242、 243、 244、 245、 24
6、 247、 248、 249、 250、 251、 252、 253、 254、 255、 256、 257、 258、 259、 260、 261、 262、 263、 264、 265、 266、 26
7、 268、 269、 270、 271、 272、 273、 274、 275、 276、 277、 278、 279、 280、 281、 282、 283、 284、 285、 286、 287、 28
8、 289、 290、 291、 292、 293、 294, 295、 296、 297、 298、 299、 300又は 301に記載されたいずれかの薄膜形成用基板。
項 303. 六方晶系又は三方晶系のうちから選ばれた少なくともいずれかの結晶構造を有す るセラミック材料を主成分とする焼結体の平均表面粗さが R a 100 Onm以下であることを 特徴とする項 302に記載された薄膜形成用基板。
項 304. 六方晶系又は三方晶系のうちから選ばれた少なくともいずれかの結晶構造を有す るセラミック材料を主成分とする能結体の平均表面粗さが Ral 0 Onm以下であることを特 徴とする項 302又は 303に記載されたいずれかの薄膜形成用基板。
項 305. 六方晶系又は三方晶系のうちから選ばれた少なくともいずれかの結晶構造を有す るセラミック材料を主成分とする焼結体の平均表面粗さが R a 1 Onm以下であることを特徴 とする項 302、 303又は 304に記載されたいずれかの薄膜形成用基板。
項 306. 六方晶系又は三方晶系のうちから選ばれた少なくともいずれかの結晶構造を有す るセラミック材料を主成分とする焼結体の平均表面粗さが R a 5 nm以下であることを特徴と する項 302、 303、 304又は 305に記載されたいずれかの薄膜形成用基板。
項 307. 表面粗さの大きい六方晶系又は三方晶系のうちから選ばれた少なくともいずれか の結晶構造を有するセラミック材料を主成分とする焼結体からなることを特徴とする項 185、 186、 187、 188、 189、 190、 191、 192、 193、 194、 195、 19
6、 197、 198、 199、 200、 201、 202、 203、 204、 205、 206、 207、 208、 209、 210、 211、 212、 213、 214、 215、 216、 21
7、 218、 219、 220、 221、 222、 223、 224、 225、 226、 227、 228、 229、 230、 231、 232、 233、 234、 235、 236、 237、 23
8、 239、 240、 241、 242、 243、 244、 245、 246、 247、 248、 249、 250、 251、 252、 253、 254、 255、 256、 257、 258、 25
9、 260、 261、 262、 263、 264、 265、 266、 267、 268、 269、 270、 271、 272、 273、 274、 275、 276、 277、 278、 279、 28
0、 281、 282、 283、 284, 285、 286、 287、 288、 289、 290、 291、 292、 293、 294, 295、 296、 297、 298、 299、 300、 30
1、 302、 303又は 304に記載されたいずれかの薄膜形成用基板。
項 308. 平均表面粗さ R a 70 nm以上の六方晶系又 方晶系のうちから選ばれた少な くともいずれかの結晶構造を有するセラミック材料を主成分とする焼結体からなることを特徴 とする項 185、 186、 187、 188、 189、 190、 191、 192、 193、 19
4、 195、 196、 197、 198、 199、 200、 201、 202、 203、 204、 205、 206、 207、 208、 209、 210/211、 212、 213、 214、 21
5、 216、 217、 218、 219、 220、 221、 222、 223、 224、 225、 226、 227、 228、 229、 230、 231、 232、 233、 234、 235、 23
6、 237、 238、 239、 240、 241、 242、 243、 244、 245、 246、 247、 248、 249、 250、 251、 252、 253、 254、 255、 256、 25
7、 258、 259、 260、 261、 262、 263、 264、 265、 266、 267、 268、 269、 270、 271、 272、 273、 274、 275、 276、 277、 27
8、 279、 280、 281、 282、 283、 284, 285、 286、 287、 288、 289、 290、 291、 292、 293、 294、 295、 296、 297、 298、 29
9、 300、 301、 302、 303、 304又は 307に記載されたいずれかの薄膜形成用 項 309. 六方晶系又 方晶系のうちから選ばれた少なくともいずれかの結晶構造を有す るセラミック材料を主成分とする焼結体の平均表面粗さが R a 1000 nmより大きいことを 特徴とする項 308に記載された薄膜形成用基板。
項 310. 六方晶系又は三方晶系のうちから選ばれた少なくともいずれかの結晶構造を有す るセラミック材料を主成分とする焼結体の平均表面粗さが R a 2000 nmより大きいことを 特徴とする項 308又は 309に記載されたいずれかの薄膜形成用基板。
項 311. 六方晶系又は三方晶系のうちから選ばれた少なくともいずれかの結晶構造を有す るセラミック材料を主成分とする焼結体の表面が焼き放し (a s-f i r e)、 ラップ研磨、 ブ ラスト研磨、 鏡面研磨、 化学腐食及びプラズマガスによる腐食のうちから選ばれた少なくとも いずれかの状態であることを特徴とする項 302、 303、 304、 305、 306、 307、 308、 309又は 310に記載されたいずれかの薄膜形成用基板。
項 312. 六方晶系又 方晶系のうちから選ばれた少なくともいずれかの結晶構造を有す るセラミック材料を主成分とする焼結体の表面が鏡面研磨された状態であることを特徴とする 項 311に記載された薄膜形成用基板。
項 313. 六方晶系又は三方晶系のうちから選ばれた少なくともいずれかの結晶構造を有す るセラミック材料を主成分とする焼結体力壞化亜鉛、 酸化ベリリウム、 酸化アルミニウム、 炭 化珪素、 窒化珪素、 窒化ガリウムうちから選ばれた少なくとも 1種以上を主成分とする焼結体 からなることを赚とする項 302、 303、 304、 305、 306、 307、 308、 3 09、 310、 311又は 312に記載されたいずれかの薄膜形成用基板。
項 314. セラミック材料を主成分とする焼結体及び 過性を有するセラミック材料を主 成分とする焼結体がそれぞれ酸化ジルコニウム、酸化マグネシウム、アルミン酸マグネシウム、 酸化チタン、 チタン酸バリウム、 チタン酸ジルコン酸鉛、 希土纖化物、 酸化トリウム、 各種 フェライト、 ムライト、 フォルステライト、 ステアタイト、 結晶化ガラスのうちから選ばれた 少なくとも 1種以上を主成分とする焼結体であることを特徴とする項 1、 2、 3、 4、 5、 6、 7、 8、 9、 10、 11、 12、 13、 14、 15、 16、 17、 18、 19、 20、 21、
22、 23、 24、 25、 26、 27、 28、 29、 30、 31、 32、 33、 34、 35、
36、 37、 38、 39、 40、 41、 42、 43、 44、 45、 46、 47、 48、 49、
50、 51、 52、 53、 54、 55、 56、 57、 58、 59、 60、 61、 62、 63、
64、 65、 66、 67、 68、 69又は 70に記載されたいずれかの薄膜形成用基板。
項 3 i s . セラミック材料を主成分とする焼結体が 化ジルコニウム、 酸化マグネシウム、 アルミン酸マグネシウム、 酸化ィットリウムのうちから選ばれた少なくとも 1種以上を主成分 とする焼糸吉体であることを特徴とする項 3 1 4に記載された薄膜形成用基板。
項 3 1 6. 平均表面粗さ R a 2 0 0 0 nm以下の酸化ジルコニウム、 酸化マグネシウム、 ァ ルミン酸マグネシウム、 酸化チタン、 チタン酸バリウム、 チタン酸ジルコン,、 希土 »化 物、 酸化トリウム、 各種フェライト、 ムライト、 フォルステライト、 ステア夕イト、 結晶化ガ ラスのうちから選ばれた少なくとも 1種以上を主成分とする焼結体からなることを特徴とする 項 3 1 4又は 3 1 5に記載されたいずれかの薄膜形成用基板。
項 3 1 7. 酸化ジルコニウム、 酸化マグネシウム、 アルミン酸マグネシウム、 酸化チタン、 チタン酸バリウム、 チタン酸ジルコン酸鉛、 希土 «化物、 酸ィ匕トリウム、 各種フェライト、 ムライト、 フォルステライト、 ステアタイト、 結晶化ガラスのうちから選ばれた少なくとも 1 種以上を主成分とする焼結体の平均表面粗さが R a 1 0 0 0 nm以下であることを特徴とする 項 3 1 6に記載された薄膜形成用基板。
項 3 1 8. 酸化ジルコニウム、 酸ィ匕マグネシウム、 アルミン酸マグネシウム、 酸化チタン、 チタン酸バリウム、 チタン酸ジルコン 、 希土賺化物、 酸化トリウム、 各種フェライト、 ムライト、 フォルステライト、 ステアタイト、 結晶化ガラスのうちから選ばれた少なくとも 1 種以上を主成分とする焼結体の平均表面粗さが R a 1 0 0 nm以下であることを特徴とする項 3 1 6又は 3 1 7に記載されたいずれかの薄膜形成用基板。
項 3 1 9. 酸化ジルコニウム、 酸ィ匕マグネシウム、 アルミン酸マグネシウム、 酸化チタン、 チタン酸パリウム、 チタン酸ジルコン酸鉛、 希土 «化物、 酸化トリウム、 各種フェライト、 ムライト、 フォルステラィ卜、 ステア夕イト、 結晶化ガラスのうちから選ばれた少なくとも 1 種以上を主成分とする焼結体の平均表面粗さが R a 1 0 nm以下であることを特徴とする項 3 1 6、 3 1 7又は 3 1 8に記載されたいずれかの薄膜形成用基板。
項 3 2 0. 酸化ジルコニウム、 酸化マグネシウム、 アルミン酸マグネシウム、 酸化チタン、 チタン酸バリウム、 チタン酸ジルコン «、 希土纖化物、 酸化トリウム、 各種フェライト、 ムライト、 フオルステライト、 ステアタイト、 結晶化ガラスのうちから選ばれた少なくとも 1 種以上を主成分とする焼結体の平均表面粗さが R a 5 nm以下であることを特徴とする項 3 1 6、 3 1 7、 3 1 8又は 3 1 9に記載されたいずれかの薄膜形成用基板。
項 3 2 1 . 表面粗さの大きレ酸化ジルコニウム、 酸化マグネシウム、 アルミン酸マグネシゥ ム、 酸化チタン、 チタン酸バリウム、 チタン酸ジルコン麵、 希土纖化物、 酸化トリウム、 各種フェライト、 ムライト、 フォルステライト、 ステアタイト、 結晶化ガラスのうちから選ば れた少なくとも 1種以上を主成分とする焼結体からなることを特徴とする項 3 1 4、 3 1 5、 3 1 6、 3 1 7又は 3 1 8に記載されたいずれかの薄膜形成用基板。
項 3 2 2. 平均表面粗さ R a 7 O nm以上の酸化ジルコニウム、 酸化マグネシウム、 アルミ ン酸マグネシウム、 酸化チタン、 チタン酸バリウム、 チタン酸ジルコン酸鉛、 希土鍵化物、 酸ィ匕トリウム、 各種フェライト、 ムライト、 フォルステライト、 ステア夕イト、 結晶化ガラス のうちから選ばれた少なくとも 1種以上を主成分とする焼結体からなることを特徴とする項 3 1 4、 3 1 5、 3 1 6、 3 1 7、 3 1 8又は 3 2 1に記載されたいずれかの薄膜形成用基板。 項 3 2 3. 酸化ジルコニウム、 酸化マグネシウム、 アルミン酸マグネシウム、 酸化チタン、 チタン酸パリゥム、 チタン酸ジルコン 、 希土賺化物、 酸化トリウム、 各種フェライト、 ムライト、 フオルステライト、 ステア夕イト、 結晶化ガラスのうちから選ばれた少なくとも 1 種以上を主成分とする焼結体の平均表面粗さが R a 1 0 0 0 nmより大きいことを特徴とする 項 3 2 2に記載された薄膜形成用基板。
項 3 2 4. 酸化ジルコニウム、 酸化マグネシウム、 アルミン酸マグネシウム、 酸化チタン、
6、 2 7 7、 2 7 8、 2 7 9、 2 8 0、 2 8 1、 2 8 2、 2 8 3、 2 8 4、 2 8 5、 2 8 6、
2 8 7、 2 8 8、 2 8 9、 2 9 0、 2 9 1、 2 9 2、 2 9 3、 2 9 4、 2 9 5、 2 9 6、 2 9
7、 2 9 8、 2 9 9、 3 0 0、 3 0 1、 3 0 2、 3 0 3、 3 0 4、 3 0 5、 3 0 6、 3 0 7、
3 0 8、 3 0 9、 3 1 0、 3 1 1、 3 1 2、 3 1 3、 3 1 4、 3 1 5、 3 1 6、 3 1 7、 3 1
8、 3 1 9、 3 2 0、 3 2 1、 3 2 2、 3 2 3、 3 2 4、 3 2 5又は 3 2 6に記載されたいず れかの薄膜形成用基板。
項 3 2 8. 基板に形成される窒化ガリウム、 窒化インジウム、 窒化アルミニウムのうちから 選ばれた少なくとも 1種以上を主成分とする薄膜の少なくとも一部が単結晶であることを特徴 とする項 3 2 7に記載された薄膜形成用基板。
項 3 2 9. 基板に形成される窒化ガリウム、 窒化インジウム、 窒化アルミニウムのうちから 選ばれた少なくとも 1種以上を主成分とする薄膜の少なくとも一部が単結晶でありさらに無定 形、 多結晶、 配向性多結晶のうちから選ばれたいずれか少なくとも 1種以上の結晶状態からな ることを特徴とする項 3 2 7又は 3 2 8に記載されたいずれかの薄膜形成用基板。
項 3 3 0. 基板に形成される窒化ガリウム、 窒化インジウム、 窒化アルミニウムのうちから 選ばれた少なくとも 1種以上を主成分とする薄膜の全てが単結晶であることを特徴とする項 3
2 8に記載された薄膜形成用基板。
項 3 3 1 . 基板に形成される窒化ガリウム、 窒化インジウム、 窒化アルミニウムのうちから 選ばれた少なくとも 1種以上を主成分とする薄膜の少なくとも一部が無定形であることを特徴 とする項 3 2 7、 3 2 8又は 3 2 9に記載されたいずれかの薄膜形成用基板。
項 3 3 2. 基板に形成される窒化ガリウム、 窒化インジウム、 窒化アルミニウムのうちから 選ばれた少なくとも 1種以上を主成分とする薄膜の少なくとも一部が無定形でありさらに単結 晶、 多結晶、 配向性多結晶のうちから選ばれたいずれか少なくとも 1種以上の結晶状態からな ることを特徴とする項 3 3 1に記載された薄膜形成用基板。
項 3 3 3. 基板に形成される窒化ガリゥム、 窒化インジウム、 窒化アルミニウムのうちから 選ばれた少なくとも 1種以上を主成分とする薄膜の全てが無定形であることを特徴とする項 3
3 2に記載された薄膜形成用基板。
項 3 3 4. 基板に形成される窒化ガリウム、 窒化インジウム、 窒化アルミニウムのうちから 選ばれた少なくとも 1種以上を主成分とする薄膜の少なくとも一部が多結晶であることを特徴 とする項 3 2 7、 3 2 8、 3 2 9、 3 3 1又は 3 3 2に記載されたいずれかの薄膜形成用基板。 項 3 3 5. 基板に形成される窒化ガリウム、 窒化インジウム、 窒化アルミニウムのうちから 選ばれた少なくとも 1種以上を主成分とする薄膜の少なくとも一部が多結晶でありさらに単結 晶、 無定形、 配向性多結晶のうちから選ばれたいずれか少なくとも 1種以上の結晶状態からな ることを特徴とする項 3 3 4に記載された薄膜形成用基板。
項 3 3 6. 基板に形成される窒化ガリウム、 窒化インジウム、 窒化アルミニウムのうちから 選ばれた少なくとも 1種以上を主成分とする薄膜の全てが多結晶であることを特徴とする項 3 3 4に記載された薄膜形成用基板。
項 3 3 7. 基板に形成される窒化ガリウム、 窒化インジウム、 窒化アルミニウムのうちから 選ばれた少なくとも 1種以上を主成分とする薄膜の少なくとも一部が 向性多結晶であること を特徴とする項 3 2 7、 3 2 8、 3 2 9、 3 3 1、 3 3 2、 3 3 4又は 3 3 5に記載されたい ずれかの薄膜形成用基板。
項 3 3 8. 基板に形成される窒化ガリウム、 窒化インジウム、 窒化アルミニウムのうちから 選ばれた少なくとも 1種以上を主成分とする薄膜の少なくとも一部が配向性多結晶でありさら に単結晶、 無定形、 多結晶のうちから選ばれたいずれか少なくとも 1種以上の結晶状態からな ることを特徴とする項 3 3 7に記載された薄膜形成用基板。
482
チタン酸バリウム、 チタン酸ジルコン膽、 希土鍵化物、 酸化トリウム、 各種:
ムライト、 フォルステライト、 ステアタイト、 結晶化ガラスのうちから選ばれた少なくとも 1 種以上を主成分とする焼結体の平均表面粗さが R a 2000 nmより大きいことを特徴とする 項 322又は 323に記載されたいずれかの薄膜形成用基板。
項 325. 酸化ジルコニウム、 酸化マグネシウム、 アルミン酸マグネシウム、 酸化チタン、 チタン酸バリウム、 チタン酸ジルコン隨、 希土鍵化物、 酸化トリウム、 各種フェライト、 ムライト、 フォルステライト、 ステア夕イト、 結晶化ガラスのうちから選ばれた少なくとも 1 種以上を主成分とする能結体の表面が焼き放し(a s— f i r e;)、ラッフ开磨、ブラスト研磨、 鏡面研磨、 ィ匕学腐食及びプラズマガスによる腐食のうちから選ばれた少なくともいずれかの状 態であることを特徴とする項 314、 315、 316、 317、 318、 319、 320、 3 21、 322、 323又は 324に記載されたいずれかの薄膜形成用基板。
項 326. 酸化ジルコニウム、 酸化マグネシウム、 アルミン酸マグネシウム、 酸化チタン、 チタン酸バリウム、 チタン酸ジルコン mi 希土鍵化物、 酸化トリウム、 各種フェライト、 ムライト、 フオルステライト、 ステアタイト、 結晶化ガラスのうちから選ばれた少なくとも 1 種以上を主成分とする焼結体の表面が鏡面研磨された状態であることを特徴とする項 325に 記載された薄膜形成用基板。
項 327. 窒化ガリウム、 窒化インジウム、 窒化アルミニウムのうちから選ばれた少なくと も 1種以上を主成分とする薄膜を形成するための基板であって、 該基板に形成される窒化ガリ ゥム、 窒化インジウム、 窒化アルミニウムのうちから選ばれた少なくとも 1種以上を主成分と する薄膜が少なくとも単結晶、 無定形、 多結晶、 配向性多結晶のうちから選ばれたいずれかの 結晶状態であることを ¾とする項 1、 2、 3、 4、 5、 6、 7、 8、 9、 10、 11、 12、
13、 14、 15、 16、 17、 18、 19、 20、 21、 22、 23、 24、 25、 26、 27、 28、 29、 30、 31、 32、 33、 3344、、 35、 36、 37、 38、 39、 40、 41、 42、 43、 44、 45、 46、 47、 4488、、 49、 50、 51、 52、 53、 54、
55、 56、 57、 58、 59、 60、 61、 6622、、 63、 64、 65、 66、 67、 68、
69、 70、 71、 72、 73、 74、 75、 7766、、 77、 78、 79、 80、 81、 82、
83、 84、 85、 86、 87、 88、 89、 9900、、 91、 92、 93、 94、 95、 96、
97、 98、 99、 100、 01、 102、 103、 104、 10055、、 106、 107、 1 08、 109、 110、 11 , 112、 113、 114、 115、 1 1166、、 117、 118、
119、 120、 121、 122、 123、 124、 125、 126、 127、 128、 12 9、 130、 131、 132、 133、 134、 135、 136、 137、 138、 139、 140、 141、 142、 143、 144、 145、 146、 147、 148、 149、 15
0、 151、 152、 153、 154、 155、 156、 157、 158、 159、 160、 161、 162、 163、 164、 165、 166、 167、 168、 169、 170、 17
1、 172、 173、 174、 175、 176、 177、 178、 179、 180、 181、 182、 183、 184、 185、 186、 187、 188、 189、 190、 191、 19
2、 193、 194, 195、 196、 197、 198、 199、 200、 201、 202、 203、 204、 205、 206、 207、 208、 209、 210、 211、 212、 21
3、 214、 215、 216、 217、 218、 219、 220、 221、 222、 223、 224、 225、 226、 227、 228、 229、 230、 231、 232、 233、 23
4、 235、 236、 237、 238、 239、 240、 241、 242、 243、 244、 245、 246、 247、 248、 249、 250、 251、 252、 253、 254、 25
5、 256、 257、 258、 259、 260、 261、 262、 263、 264、 265、 266、 267、 268、 269、 270、 271、 272、 273、 274、 275、 27
項 3 3 9. 基板に形成される窒化ガリウム、 窒化インジウム、 窒化アルミニウムのうちから 選ばれた少なくとも 1種以上を主成分とする薄膜の全てが配向性多結晶であることを特徴とす る項 3 3 7に記載された薄膜形成用基板。
項 3 4 0. 基板に形成される窒化ガリウム、 窒化インジウム、 窒化アルミニウムのうちから 選ばれた少なくとも 1種以上を主成分とする薄膜の少なくとも一部が単結晶であり該薄膜の単 結晶部分が窒化アルミ二ゥムを主成分とする焼結体からなる基板に直接形成されることを特徴 とする項 3 2 7、 3 2 8、 3 2 9、 3 3 0、 3 3 1、 3 3 2、 3 3 4、 3 3 5、 3 3 7又は 3 3 8に記載されたいずれかの薄膜形成用基板。
項 3 4 1 . 基板に形成される窒化ガリウム、 窒化インジウム、 窒化アルミニウムのうちから 選ばれた少なくとも 1種以上を主成分とする薄膜の少なくとも一部が単結晶であり該薄膜の単 結晶部分が六方晶系又は三方晶系のうちから選ばれた少なくとも ゝずれかの結晶構造を有する セラミック材料を主成分とする焼結体からなる基板に直接形成されることを特徴とする項 3 2 7、 3 2 8、 3 2 9、 3 3 0、 3 3 1、 3 3 2、 3 3 4、 3 3 5、 3 3 7又は 3 3 8に記載さ れたいずれかの薄膜形成用基板。
項 3 4 2. 基板に形成される窒化ガリウム、 窒化インジウム、 窒化アルミニウムのうちから 選ばれた少なくとも 1種以上を主成分とする薄膜の少なくとも 1部が無定形、 多結晶、 配向性 多結晶のうちから選ばれた少なくともいずれかの結晶状態であり該薄膜の無定形、 多結晶、 配 向性多結晶のうちから選ばれた少なくともいずれかの結晶状態の部分が窒化アルミニゥムを主 成分とする焼結体からなる基板に直接形成されることを とする項 3 2 7、 3 2 8、 3 2 9、 3 3 1、 3 3 2、 3 3 3、 3 3 4、 3 3 5、 3 3 6、 3 3 7、 3 3 8又は 3 3 9に記載された いずれかの薄膜形成用基板。
項 3 4 3. 基板に形成される窒化ガリウム、 窒化インジウム、 窒化アルミニウムのうちから 選ばれた少なくとも 1種以上を主成分とする薄膜の少なくとも 1部が無定形、 多結晶、 配向性 多結晶のうちから選ばれた少なくともいずれかの結晶状態であり該薄膜の無定形、 多結晶、 配 向性多結晶のうちから選ばれた少なくともいずれかの結晶状態の部分が六方晶系又は三方晶系 のうちから選ばれた少なくともいずれかの結晶構造を有するセラミック材料を主成分とする焼 結体からなる基板に直接形成されることを^とする項 3 2 7、 3 2 8、 3 2 9、 3 3 1、 3 3 2、 3 3 3、 3 3 4、 3 3 5、 3 3 6、 3 3 7、 3 3 8又は 3 3 9に記載されたいずれかの 薄膜形成用基板。
項 3 4 4. 基板に形成される窒化ガリウム、 窒化インジウム、 窒化アルミニウムのうちから 選ばれた少なくとも 1種以上を主成分とする薄膜の少なくとも 1部が無定形、 多結晶、 配向性 多結晶のうちから選ばれた少なくともいずれかの結晶状態であり該薄膜の無定形、 多結晶、 配 向性多結晶のうちから選ばれた少なくともいずれかの結晶状態の部分が;) ¾¾1性を有するセラ ミック材料を主成分とする能結体からなる基板に直接形成されることを特徴とする項 3 2 7、 3 2 8、 3 2 9、 3 3 1、 3 3 2、 3 3 3、 3 3 4、 3 3 5、 3 3 6、 3 3 7、 3 3 8又は 3 3 9に記載されたいずれかの薄膜形成用基板。
項 3 4 5. 基板に形成される窒化ガリウム、 窒化インジウム、 窒化アルミニウムのうちから 選ばれた少なくとも 1種以上を主成分とする薄膜が少なくとも 2以上の層から構成されること を ¾とする項 3 2 7、 3 2 8、 3 2 9、 3 3 0、 3 3 1、 3 3 2、 3 3 3、 3 3 4、 3 3 5、 3 3 6、 3 3 7、 3 3 8、 3 3 9、 3 4 0、 3 4 1、 3 4 2、 3 4 3又は 3 4 4に記載された いずれかの薄膜形成用基板。
項 3 4 6. 2以上の層から構成される薄膜の各層が単結晶、 無定形、 多結晶、 配向性多結晶 の中から選ばれた少なくともいずれかの結晶状態であることを特徴とする項 3 4 5に記載され た薄膜形成用基板。
項 347. 2以上の層から構成される薄膜において基板に直接形成される薄膜が単結晶、 無 定形、 多結晶、 配向性多結晶の中から選ばれた少なくともいずれかの結晶状態であることを特 徴とする項 345又は 346に記載されたいずれかの薄膜形成用基板。
項 348. 2以上の層から構成される薄膜において基板に直接形成される薄膜が無定形、 多 結晶、 配向性多結晶の中から選ばれた少なくともいずれかの結晶状態であることを赚とする 項 345、 346又は 347に記載されたいずれかの薄膜形成用基板。
項 349. 2以上の層から構成される薄膜において基板に直接形成される薄膜が無定形、 多 結晶、 配向性多結晶の中から選ばれた少なくともいずれかの結晶状態でありその上に形成され る薄膜が単結晶であることを特徴とする項 345、 346、 347又は 348に記載されたい ずれかの薄膜形成用基板。
項 350. 2以上の層から構成される薄膜において基板に直接形成される薄膜が無定形であ りその上に形成される薄膜が単結晶であることを特徴とする項 349に記載された薄膜形成用 項 351. 2以上の層から構成される薄膜において基板に直接形成される薄膜が多結晶であ りその上に形成される薄膜が単結晶であることを特徴とする項 349に記載された薄膜形成用 項 352. 2以上の層から構成される薄膜において基板に直接形成される薄膜カ观向性多結 晶でありその上に形成される薄膜が単結晶であることを特徴とする項 349に記載された薄膜 形成用基板。
項 353. 2以上の層から構成される薄膜において基板に直接形成される薄膜が無定形、 多 結晶、 配向性多結晶の中から選ばれた少なくともいずれかの結晶状態でありその上に形成され る薄膜が単結晶である構成の薄膜において該単結晶からなる薄膜が 2以上の層からなることを 特徴とする項 345、 346、 347、 348、 349、 350、 351又は 352に記載さ れたいずれかの薄膜形成用基板。
項 354. 2以上の層から構成される薄膜において少なくとも 2以上の層が単結晶からなる ものであることを特徴とする項 345、 346、 347、 348、 349、 350、 351、 352又は 353に記載されたいずれかの薄膜形成用基板。
項 355. 2以上の層から構成される薄膜において基板に直接形成される薄膜が単結晶から なるものであることを特徴とする項 345、 346、 347又は 354に記載されたいずれか の薄膜形成用基板。
項 356. 2以上の層から構成される薄膜においてすベての層が単結晶からなるものである ことを特徴とする項 345、 346、 347、 354又は 355に記載されたいずれかの薄膜 形成用基板。
項 357. 2以上の層から構成される薄膜のうち少なくとも 2層が異なる組成からなるもの であることを特徴とする項 345、 346、 347、 348、 349、 350、 351、 35 2、 353、 354、 355又は 356に記載されたいずれかの薄膜形成用基板。
項 358. 基板に形成される薄膜の少なくとも一部が単結晶からなり該単結晶薄膜の結晶 C 軸が基板面に対して垂直な方向に形成されることを特徴とする項 327、 328、 329、 3 30、 331、 332、 334、 335、 337、 338、 340、 341、 342、 343、 344、 345、 346、 347、 348、 349、 350、 351、 352、 353、 35 4、 355、 356又は 357に記載されたいずれかの薄膜形成用基板。
項 359. 基板に形成される薄膜の全てが単結晶からなり該単結晶薄膜の結晶 C軸が基板面 に対して垂直な方向に形成されることを特徴とする項 358に記載された薄膜形成用基板。 項 360. 基板に形成される薄膜の少なくとも一部が単結晶からなり該単結晶薄膜の結晶 C
軸が基板面に対して水平な方向に形成されることを特徴とする項 327、 328、 329、 3 30、 331、 332、 334、 335、 337、 338、 340、 341、 342、 343、 344、 345、 346、 347、 348、 349、 350、 351、 352、 353、 35 4、 355、 356又は 357に記載されたいずれかの薄膜形成用基板。
項 361. 基板に形成される薄膜の全てが単結晶からなり該単結晶薄膜の結晶 C軸が基板面 に対して水平な方向に形成されることを特徴とする項 360に記載された薄膜形成用基板。 項 362. 窒化ガリウム、 窒化インジウム、 窒化アルミニウムのうちから選ばれた少なくと も 1種以上を主成分とする薄膜を形成するための基板であって、 該基板に形成される薄膜が導 電性を有することを 15 [とする項 1、 2、 3、 4、 5、 6、 7、 8、 9、 10、 11、 12、
13、 14、 15、 16、 17、 18、 19、 20、 21、 22、 23、 24、 25、 26、
27、 28、 29、 30、 31、 32、 33、 34、 35、 36、 37、 38、 39、 40、 41、 42、 43、 44、 45、 46、 47、 48、 49、 50、 51、 52、 53、 54、
55、 56、 57、 58、 59、 60、 61、 62、 63、 64、 65、 66、 67、 68、
69、 70、 71、 72、 73、 74、 75、 76、 77、 78、 79、 80、 81、 82、
83、 84、 85、 86、 87、 88、 89、 90、 91、 92、 93、 94、 95、 96、
97、 98、 99、 100、 10 : 1、 102、 103、 104、 105、 106、 : 07、 1 08、 109、 110、 111、 1 2、 113、 114、 115、 116、 117、 118、 119、 120、 121、 122、 123、 124、 125、 126、 127、 128、 12
9、 130、 131、 132、 133、 134、 135、 136、 137、 138、 139、 140、 141、 142、 143、 144、 145、 146、 147、 148、 149、 15
0、 151、 152、 153、 154、 155、 156、 157、 158、 159、 160、 161、 162、 163、 164、 165、 166、 167、 168、 169、 170、 17
1、 172、 173、 174, 175、 176、 177、 178、 179、 180、 181、 182、 183、 184、 185、 186、 187、 188、 189、 190、 191、 19
2、 193、 194、 195、 196、 197、 198、 199、 200、 201、 202、 203、 204、 205、 206、 207、 208、 209、 210、 211、 212、 21
3、 214、 215、 216、 217、 218、 219、 220、 221、 222、 223、 224、 225、 226、 227、 228、 229、 230、 231、 232、 233、 23
4、 235、 236、 237、 238、 239、 240、 241、 242、 243、 244、 245、 246、 247、 248、 249、 250、 251、 252、 253、 254、 25
5、 256、 257、 258、 259、 260、 261、 262、 263、 264、 265、 266、 267、 268、 269、 270、 271、 272、 273、 274、 275、 27
6、 277、 278、 279、 280、 281、 282、 283、 284、 285、 286、
287、 288、 289、 290、 291、 292、 293、 294、 295、 296、 29
7、 298、 299、 300、 301、 302、 303、 304、 305、 306、 307、
308、 309、 310、 311、 312、 313、 314、 315、 316、 317、 31
8、 319、 320、 321、 322、 323、 324、 325、 326、 327、 328、 329、 330、 331、 332、 333、 334、 335、 336、 337、 338、 33
9、 340、 341、 342、 343、 344、 345、 346、 347、 348、 349、 350、 351、 352、 353、 354、 355、 356、 357、 358、 359、 36 0又は 361に記載されたいずれかの薄膜形成用基板。
項 363. 薄膜が半導体化されることで導電性を有していることを特徴とする項 347に記 載された薄膜形成用基板。
項 364. 薄膜がマグネシウム、 ベリリウム、 カルシウム、 »、 カドミウム、 炭素、 珪素、
ゲルマニウム、 セレン、 テルル、 酸素のうちから選ばれた少なくとも 1種以上のドーピング成 分〖こより半 本化され導電性を有していることを とする項 362又は 363に記載された いずれかの薄膜形成用基板。
項 365. 薄膜がマグネシウム、 ベリリウム、 カリレシゥム、 亜鉛、 カドミウム、 炭素のうち から選ばれた少なくとも 1種以上のドーピング成分により P型に半導体化され導電性を有して いることを特徴とする項 362, 363又は 364に記載されたいずれかの薄膜形成用基板。 項 366. 薄膜が 素、 ゲルマニウム、 セレン、 テルル、 酸素のうちから選ばれた少なくと も 1種以上のドーピング成分により N型に半導体化され導電性を有していることを特徴とする 項 362、 363又は 364に記載されたいずれかの薄膜形成用基板。
項 367. 薄膜が主成分に対してドーピング成分を元素換算で 0. 00001〜 10モル% の範囲含むものであることを特徴とする項 362、 363、 364、 365又は 366に記載 されたいずれかの薄膜形成用基板。
項 368. 薄膜が少なくとも 2以上の層で構成され該薄膜のうち少なくとも 1層が導電性を 有することを特徴とする項 327、 328、 329、 330、 331、 332、 333、 33
4、 335、 336、 337、 338、 339、 340、 341、 342、 343、 344、 345、 346、 347、 348、 349、 350、 351、 352、 353、 354、 35
5、 356、 357、 358、 359、 360、 361、 362、 363、 364、 365又 は 366に記載されたいずれかの薄膜形成用基板。
項 369. 導電性を有する薄膜の室温における抵抗率が 1 X 104Ω · cm以下であることを 特徴とする項 362、 363、 364、 365、 366、 367又は 368に記載されたいず れかの薄膜形成用基板。
項 370. 導電性を有する薄膜の室温における 率が 1 X 102Ω · cm以下であることを 特徴とする項 369に記載された薄膜形成用基板。
項 371. 導電性を有する薄膜の室温における ί®¾率が 1 X 10ΧΩ · cm以下であることを 特徴とする項 369又は 370に記載されたいずれかの薄膜形成用基板。
項 372. 導電性を有する薄膜の室温における抵抗率が 1 X 10°Ω· cm以下であることを 特徴とする項 369、 370又は 371に記載されたいずれかの薄膜形成用基板。
項 373. 窒化ガリウム、 窒化インジウム、 窒化アルミニウムのうちから選ばれた少なくと も 1種以上を主成分とする薄膜を形成するための基板であって、 該基板に形成される薄膜が A 1 xGa!_xN (0≤χ≤1. 0) のィ匕学式であらわされる組成物を主成分とするものであるこ とを [とする項 1、 2、 3、 4、 5、 6、 7、 8、 9、 10、 11、 12、 13、 14、
5、 16、 17、 18、 19、 20、 21、 22、 23、 24、 25、 26、 27、 28、 9、 30、 31、 32、 33、 34、 35、 36、 37、 38、 39、 40、 41、 42、 3、 44、 45、 46、 47、 48、 49、 50、 51、 52、 53、 54、 55、 56、 7、 58、 59、 60、 61、 62、 63、 64、 65、 66、 6 Ίヽ 68、 69、 70、 1、 72、 73、 74、 75、 76、 77、 78、 79、 80、 81、 82、 83、 84、 5、 86、 87、 88、 89、 90、 91、 92、 93、 94、 95、 96、 97、 98、
9、 100、 101、 102、 103、 104, 105、 106、 107、 108、 109、 110、 1: 1、 112、 113、 114、 115、 116、 117、 118、 11 9, 12 0、 121、 122、 123、 124、 125、 126、 127、 128、 129、 130、
131、 132、 133、 134、 135、 136、 137、 138、 139、 140、 14
1、 142、 143、 144、 145、 146、 147、 148、 149、 150、 151、 152、 153、 154、 155、 156、 157、 158、 159、 160、 161、 16
2、 163、 164、 165、 166、 167、 168、 169、 170、 171、 172、
173、 174、 175、 176、 177、 178、 179、 180、 181、 182、 18
3、 184、 185、 186、 187、 188、 189、 190、 191、 192、 193、 194、 195、 196、 197、 198、 199、 200、 201、 202、 203、 20
4、 205、 206、 207、 208、 209、 210、 211、 212、 213、 214、 215、 216、 217、 218、 219、 220、 221、 222、 223、 224、 22
5、 226、 227、 228、 229、 230、 231、 232、 233、 234、 235、 236、 237、 238、 239、 240、 241、 242、 243、 244、 245、 24
6、 247、 248、 249、 250、 251、 252、 253、 254、 255、 256、 257、 258、 259、 260、 261、 262、 263、 264、 265、 266、 26
7、 268、 269、 270、 271、 272、 273、 274、 275、 276、 277、 278、 279、 280、 281、 282、 283、 284、 285、 286、 287、 28
8、 289、 290、 291、 292、 293、 294, 295、 296、 297、 298、
299、 300、 301、 302、 303、 304、 305、 306、 307、 308、 30
9、 310、 311、 312、 313、 314、 315、 316、 317、 318、 319、
320、 321、 322、 323、 324、 325、 326、 327、 328、 329、 33
0、 331、 332、 333、 334、 335、 336、 337、 338、 339、 340、 341、 342、 343、 344、 345、 346、 347、 348、 349、 350、 35
1、 352、 353、 354、 355、 356、 357、 358、 359、 360、 361、 362、 363、 364、 365、 366、 367、 368、 369、 370、 371又は 3 72に記載されたいずれかの薄膜形成用基板。
項 374. 薄膜が AlxGa — ΧΝ (0≤χ≤1. 0) の化学式であらわされる組成物を主成 分としさらに Mg (マグネシウム)、 Be (ベリリウム)、 Zn (亜鉛) のうちから選ばれた少 なくとも 1種以上の成分を該組成物に対して元素換算で 0. 00001〜: L 0モル%の範囲で 含むものであることを特徴とする項 373に記載された薄膜形成用基板。
項 375. 薄膜が AlxGa — ΧΝ (0≤χ≤1. 0) の化学式であらわされる組成物を主成 分としさらに S i (珪素) を IR成物に対して元素換算で 0. 00001〜 10モル%の範囲 で含むものであることを特徴とする項 373又は 374に記載されたいずれかの薄膜形成用基 板。
項 376. 薄膜が A lxGai一 χΝ (0≤χ≤1. 0) の化学式であらわされる組成物を主成 分としさらに |¾且成物に対して Mg、 Be、 Znのうちから選ばれた少なくとも 1種以上の成 分及び S iとを同時に合計で元素換算で 0. 00001〜10モル%の範囲で含むものである ことを特徴とする項 373, 374又は 375に記載されたいずれかの薄膜形成用基板。 項 377. 薄膜が A lxGa!_xN (0≤x≤0. 6) での化学式あらわされる組成物を主成 分とするものであることを特徴とする項 373、 374、 375又は 376に記載されたいず れかの薄膜形成用基板。
項 378. 薄膜が AlxGa 一 XN (0≤χ≤0. 6) での化学式あらわされる組成物を主成 分としさらに Mg、 Be、 Znのうちから選ばれた少なくとも 1種以上の成分を M且成物に対 して元素 で 0. 00001〜: L 0モル%の範囲で含むものであることを特徴とする項 37 7に記載された薄膜形成用基板。
項 379. 薄膜が AlxGai一 XN (0≤χ≤0. 6) の化学式であらわされる組成物を主成 分としさらに S iを該組成物に対して元素換算で 0. 00001〜 10モル%の範囲で含むも のであることを特徴とする項 377又は 378に記載されたいずれかの薄膜形成用基板。 項 380. 薄膜が AlxGa 一 XN (0≤x≤0. 6) の化学式であらわされる組成物を主成 分としさらに ¾且成物に対して M g、 Be、 Znのうちから選ばれた少なくとも 1種以上の成
分及び S iとを同時に合計で元素換算で 0. 00001〜10モル%の範囲で含むものである ことを特徴とする項 377, 378又は 379に記載されたいずれかの薄膜形成用基板。
項 381. 薄膜が AlxGai— XN (0. 6≤x≤l. 0) の化学式であらわされる組成物を 主成分とするものであることを特徴とする項 373、 374、 375又は 376に記載された いずれかの薄膜形成用基板。
項 382. 薄膜が AlxGai_xN (0. 6≤x≤l. 0) の化学式であらわされる組成物を 主成分としさらに Mg、 Be、 Znのうちから選ばれた少なくとも 1種以上の成分を識且成物 に対して元素換算で 0. 00001〜0. 5モル%の範囲で含むものであることを特徴とする 項 381に記載された薄膜形成用基板。
項 383.
(0. 6≤x≤l. 0) の化学式であらわされる組成物を 主成分としさらに S iを識且成物に対して元素換算で 0. 00001〜0. 5モル%の範囲で 含むものであることを特徴とする項 381又は 382に記載されたいずれかの薄膜形成用基板。 項 384.
(0. 6≤x≤l. 0) の化学式であらわされる組成物を 主成分としさらに識且成物に対して Mg、 Be、 Znのうちから選ばれた少なくとも 1種以上 の成分及び S iとを同時に合計で元素換算で 0. 00001〜 10モル%の範囲で含むもので あることを特徴とする項 381、 382又は 383に記載されたいずれかの薄膜形成用基板。 項 385. 窒化ガリウム、 窒化インジウム、 窒化アルミニウムのうちから選ばれた少なくと も 1種以上を主成分とする薄膜を形成するための基板であって、 該基板に形成される薄膜の厚 みが 0. 5 nm以上であることを特徴とする項 1、 2、 3、 4、 5、 6、 7、 8、 9、 10、
11、 12、 13、 14、 15、 16、 17、 18、 19、 20、 21、 22、 23、 24、
25、 26、 27、 28、 29、 30、 31、 32、 33、 34、 35、 36、 37、 38、
39、 40、 41、 42、 43、 44、 45、 46、 47、 48、 49、 50、 51、 52、
53、 54、 55、 56、 57、 58、 59、 60、 61、 62、 63、 64、 65、 66、
67、 68、 69、 70、 71、 72、 73、 74、 75、 76、 77、 78、 79、 80、 81、 82、 83、 84、 85、 86、 87、 88、 89、 90、 91、 92、 93、 94、 95、 96、 97、 98、 99、 100、 101、 102、 103、 104、 105、 106、 107、 108、 109、 1: 0、 111、 112、 113, 114、 115、 116、 11 7、 118、 119、 120、 121、 122、 123、 124、 125、 126、 127、
128, 1 29, 13 0、 1 31、 132、 1 33、 1 34、 135、 136 , 137 、 13 8、 139 , 140、 141、 14 2、 143、 144. 145、 14 6、 147、 1 48、 149、 150, 15 52、 153, 154、 1 55、 156、 157、 158 、 15 9, 160 , 161、 162、 16 3、 164 , 165 . 166, 16 7、 168、 1 69、 170、 171, 17 2、 173、 174、 1 75、 1 76、 177、 178、 179 、 18 0、 181. 182, 183、 184 185、 186 > 18 7、 18 8、 189、 190、 191、 192, 19 3、 194、 195、 196, 1 97、 198、 199、 200、 20 1, 202. 203, 204、 205, 206、 207、 20 8、 20 9、 210、 211、 212、 213, 21 4、 215、 216, 217, 218、 219、 220. 221、 22
2、 223 , 224, 225、 226, 227、 228. 229, 23 0、 231, 232、 233, 2 34、 23 5、 236、 237, 238、 2 39、 240、 241、 242、 24
3、 244 , 245, 246、 4 7、 248、 249. 25 0、 25 1、 252, 2 53、 254、 255, 25 6、 257、 258, 259, 2 60、 261、 262 , 263 、 26 4> 265 , 266、 267、 26 8、 269、 270 > 27 1、 27 2、 273, 2 74、 275、 276, 27 7、 278、 279, 2 80、 281、 282、 283. 284 、 28 5, 286. 287, 288、 289, 290、 291. 292, 29 3、 294、 295、
296、 297、 298、 299、 300、 301、 302、 303、 304、 305、 30
6、 307、 308、 309、 310、 311、 312、 313、 314、 315、 316、 317、 318、 319、 320、 321、 322、 323、 324、 325、 326、 32
7、 328、 329、 330、 331、 332、 333、 334、 335、 336、 337、
338、 339、 340、 341、 342、 343、 344、 345、 346、 347、 34
8、 349、 350、 351、 352、 353、 354、 355、 356、 357、 358、 359、 360、 361、 362、 363、 364、 365、 366、 367、 368、 36
9、 370、 371、 372、 373、 374、 375、 376、 377、 378、 379、 380、 381、 382、 383又は 384に記載されたいずれかの薄膜形成用基板。
項 386. 形成される薄膜の厚みが 0. 3 以上であることを とする項 385に記載 された薄膜形成用基板。
項 387. 形成される薄膜の厚みが 3. 5 zm以上であることを とする項 385又は 3 86に記載されたいずれかの薄膜形成用基板。
項 388. 形成される薄膜の厚みが 10 m以上であることを特徴とする項 385、 386 又ま387に記載されたいずれかの薄膜形成用基板。
項 389.形成される薄膜の厚みが 50 m以上であることを特徴とする項 385、 386、 387又は 388に記載されたいずれかの薄膜形成用基板。
項 390. 窒化ガリウム、 窒化インジウム、 窒化アルミニウムのうちから選ばれた少なくと も 1種以上を主成分とする薄膜を形成するための基板であって、 基板に形成される薄膜の厚み が 1000 zm以下であることを特徴とする項 1、 2、 3、 4、 5、 6、 7、 8、 9、 10、
11、 12、 13、 14、 15、 16、 17、 18、 19、 20、 21、 22、 23、 24、 25、 26、 27、 28、 29、 30、 31、 32、 33、 34、 35、 36、 37、 38、 39、 40、 41、 42、 43、 44、 45、 46、 47、 48、 49、 50、 51、 52、
53、 54、 55、 56、 57、 58、 59、 60、 61、 62、 63、 64、 65、 66、
67、 68、 69、 70、 71、 72、 73、 74、 75、 76、 77、 78、 79、 80、 81、 82、 83、 84、 85、 86、 87、 88、 89、 90、 91、 92、 93、 94、 95、 96、 97、 98、 99、 100、 101、 110022、、 110033、、 104、 05、 ] 06、 107、 108、 109、 110、 111、 112、 1133、、 11114、 115、 116、 11
7、 118、 119、 120、 121、 122、 123、 124、 125、 126、 127、 128、 129、 130、 131、 132、 133、 134、 135、 136、 137、 13
8、 139、 140、 141、 142、 143、 144、 145、 146、 147、 148、 149、 150、 151、 152、 153、 154、 155、 156、 157、 158、 15
9、 160、 161、 162、 163、 164、 165、 166、 167、 168、 169、 170、 171、 172、 173、 174、 175、 176、 177、 178、 179、 18
0、 181、 182、 183、 184、 185、 186、 187、 188、 189、 190、 191、 192、 193、 194、 195、 196、 197、 198、 199、 200、 20
1、 202、 203、 204, 205、 206、 207、 208、 209、 210、 211、 212、 213、 214、 215、 216、 217、 218、 219、 220、 221、 22
2、 223、 224、 225、 226、 227、 228、 229、 230、 231、 232、 233、 234、 235、 236、 237、 238、 239、 240、 241、 242、 24
3、 244、 245、 246、 247、 248、 249、 250、 251、 252、 253、 254、 255、 256、 257、 258、 259、 260、 261、 262、 263、 26
4、 265、 266、 267、 268、 269、 270、 271、 272、 273、 274、 275、 276、 277、 278、 279、 280、 281、 282、 283、 284、 28
5、 286、 287、 288、 289、 290、 291、 292、 293、 294, 295、
296、 297、 298、 299、 300、 301、 302、 303、 304、 305、 30
6、 307、 308、 309、 310、 311、 312、 313、 314、 315、 316、 317、 318、 319、 320、 321、 322、 323、 324、 325、 326、 32
7、 328、 329、 330、 331、 332、 333、 334、 335、 336、 337、
338、 339、 340、 341、 342、 343、 344、 345、 346、 347、 34
8、 349、 350、 351、 352、 353、 354、 355、 356、 357、 358、 359、 360、 361、 362、 363、 364、 365、 366、 367、 368、 36
9、 370、 371、 372、 373、 374、 375、 376、 377、 378、 379、 380、 381、 382、 383、 384、 385、 386、 387、 388又は 389に記 載されたいずれかの薄膜形成用基板。
項 391. 薄膜がそれぞれの厚み 1000 m以下の薄膜層からなることを,とする項 3 90に記載された薄膜形成用基板。
項 392. 薄固すベての厚みが 1000 以下であることを特徴とする項 390又は 3 91に記載されたいずれかの薄膜形成用基板。
項 393. 薄膜の厚みが 500; m以下であることを特徴とする項 390、 391又は 39 2に記載されたいずれかの薄膜形成用基板。
項 394. 薄膜がそれぞれの厚み 500 m以下の薄 ]31 からなることを特徴とする項 39 3に記載された薄膜形成用基板。
項 395. 薄 すべての厚みが 500 m以下であることを特徴とする項 393又は 39 4に記載されたいずれかの薄膜形成用基板。
項 396.薄膜の厚みが 30 O zm^であることを繊とする項 390、 391、 392、 393、 394又は 395に記載されたいずれかの薄膜形成用基板。
項 397. 薄膜がそれぞれの厚み 300 満の薄 からなることを特徴とする項 39 6に記載された薄膜形成用基板。
項 398. 薄麵すべての厚みが 300 m未満であることを特徴とする項 396又は 39 7に記載されたいずれかの薄膜形成用基板。
項 399. 窒化ガリウム、 窒化インジウム、 窒化アルミニウムのうちから選ばれた少なくと も 1種以上を主成分とする薄膜を形成するための基板であって、 該基板に形成される薄膜がミ ラー指数 (002) の格子面の X線回折ロッキングカーブの半値幅 3600秒以下の単結晶薄 膜を少なくとも有することを特徴とする項: 2、 3、 4、 7、 8、 9、 10、 11、
12、 13、 14、 15、 16、 17、 18、 19、 20、 22、 23、 24、 25、
26、 27、 28、 29、 30、 31、 32、 33、 34、 35 、 36、 37、 38、 39、
40、 41、 42、 43、 44、 45、 46、 47、 48、 49、 50、 51、 52、 53、
54、 55、 56、 57、 58、 59、 60、 61、 62、 63、 64、 65、 66、 67、
68、 69、 70、 71、 72、 73、 74、 75、 76、 77、 78、 79、 80、 81、
82、 83、 84、 85、 86、 87、 88、 89、 90、 91、 92、 93、 94、 95、
96、 97、 98、 99、 00、 101、 102、 103、 104、 105, 1 06, 10
7、 108、 109、 110、 1 1、 1 ] 2、 113、 114、 115、 116、 117、
118、 119、 120、 121、 122、 123、 124、 125, 126, 127, 12
8、 129、 130、 131、 132、 133、 134、 135、 136 , 137、 138、 139、 140、 141、 142、 143、 144、 145、 146、 147、 148、 14
9、 150、 151、 152、 153、 154、 155、 156. 157、 158、 159、 160、 161、 162、 163、 164、 165、 166、 167, 168, 169, 17
0、 171、 172、 173、 174, 175、 176、 177、 178、 179、 180、 181、 182、 183、 184、 185、 186、 187、 188、 189、 190、 19
1、 192、 193、 194、 195、 196、 197、 198、 199、 200、 201、 202、 203、 204、 205、 206、 207、 208、 209、 210、 211、 21
2、 213、 214、 215、 216、 217、 218、 219、 220、 221、 222、 223、 224、 225、 226、 227、 228、 229、 230、 231、 232、 23
3、 234、 235、 236、 237、 238、 239、 240、 241、 242、 243、 244、 245、 246、 247、 248、 249、 250、 251、 252、 253、 25
4、 255、 256、 257、 258、 259、 260、 261、 262、 263、 264、 265、 266、 267、 268、 269、 270、 271、 272、 273、 274, 27
5、 276、 277、 278、 279、 280、 281、 282、 283、 284、 285、
286、 287、 288、 289、 290、 291、 292、 293、 294、 295、 29
6、 297、 298、 299、 300、 301、 302、 303、 304, 305、 306、
307、 308、 309、 310、 311、 312、 313、 314、 315、 316、 31
7、 318、 319、 320、 321、 322、 323、 324、 325、 326、 327、 328、 329、 330、 331、 332、 333、 334、 335、 336、 337、 33
8、 339、 340、 341、 342、 343、 344、 345、 346、 347、 348、 349、 350、 351、 352、 353、 354、 355、 356、 357、 358、 35
9、 360、 361、 362、 363、 364、 365、 366、 367、 368、 369、 370、 371、 372、 373、 374, 375、 376、 377、 378、 379、 38 0、 381、 382、 383、 384、 385、 386、 387、 388、 389、 390、 391、 392、 393、 394、 395、 396、 397又は 398に記載されたいずれか の薄膜形成用基板の製造方法。
項 400. 単結晶薄膜のミラ一指数 (002) の格子面の X線回折ロッキングカーブの半値 幅が 300秒以下であることを特徴とする項 399に記載された薄膜形成用基板。
項 401. 単結晶薄膜のミラー指数 (002) の格子面の X線回折ロッキングカーブの半値 幅が 240秒以下であることを mとする項 399又は 400に記載されたいずれかの薄膜形 成用基板。
項 402. 単結晶薄膜のミラ一指数 (002) の格子面の X線回折ロッキングカーブの半値 幅が 200秒以下であることを特徴とする項 399, 400又は 401に記載されたいずれか の薄膜形成用基板。
項 403. 単結晶薄膜のミラー指数 (002) の格子面の X線回折ロッキングカーブの半値 幅が 150秒以下であることを特徴とする項 399、 400、 401又は 402に記載された いずれかの薄膜形成用基板。
項 404. 単結晶薄膜のミラー指数 (002) の格子面の X線回折ロッキングカーブの半値 幅が 130秒以下であることを體とする項 399、 400、 401、 402又は 403に記 載されたいずれかの薄膜形成用基板。
項 405. 単結晶薄膜のミラー指数 (002) の格子面の X線回折ロッキングカーブの半値 幅が 100秒以下であることを特徴とする項 399、 400、 401、 402、 403又は 4 04に記載されたいずれかの薄膜形成用基板。
項 406. 窒化ガリゥム、 窒化ィンジゥム、 窒化アルミニゥムのうちから選ばれた少なくと も 1種以上を主成分とする薄膜を形成するための基板であって、 該基板に形成される薄膜がガ リウム、 インジウム、 アルミニウムのうちから選ばれた少なくとも 1種以上の成分を含む有機 化合物を主原料としアンモニア、 窒素、 水素のうちから選ばれた少なくとも 1種以上を反応ガ
スとして形成されるものである ' .とを特徴とする項: 2、 3、 4、 5、 6、 7、 8、 9、
0、 11、 12、 13、 14、 15、 16、 17、 18、 19、 20、 21、 22、 23、 2 4、 25、 26、 27、 28、 29、 30、 31、 32、 33、 34, 35、 36、 37、 3 8、 39、 40、 41、 42、 43、 44、 45、 46、 47、 48、 49、 50、 51、 5 2、 53、 54、 55、 56、 57、 58、 59、 60、 61、 62、 63、 64、 65、 6 6、 67、 68、 69、 70、 71、 72、 73、 74、 7 '5、 76、 77、 78、 79、 8 0、 81、 82、 83、 84、 85、 86、 87、 88、 89、 90、 91、 92、 93、 9 4、 95、 96、 97、 98、 99、 100、 01、 102、 103、 104、 05、 1
06、 107、 ] 08、 109、 110、 11、 112、 113、 114、 115、 116、 117、 118、 1 9、 120、 121、 122、 123、 124、 125、 126、 12
7、 128、 129、 130、 131、 132、 133、 134、 135、 136、 137、 138、 139、 140、 141、 142、 143、 144、 145、 146、 147、 14
8、 149、 150、 151、 152、 153、 154、 155、 156、 157、 158、 159、 160、 161、 162、 163、 164、 165、 166、 167、 168、 16
9、 170、 171、 172、 173、 174、 175、 176、 177、 178、 179、 180、 181、 182、 183、 184、 185、 186、 187、 188、 189、 19
0、 191、 192、 193、 194、 195、 196、 197、 198、 199、 200、 201、 202、 203、 204, 205、 206、 207、 208、 209、 210、 21
1、 212、 213、 214、 215、 216、 217、 218、 219、 220、 221、 222、 223、 224、 225、 226、 227、 228、 229、 230、 231、 23
2、 233、 234、 235、 236、 237、 238、 239、 240、 241、 242、 243、 244、 245、 246、 247、 248、 249、 250、 251、 252、 25
3、 254、 255、 256、 257、 258、 259、 260、 261、 262、 263、 264、 265、 266、 267、 268、 269、 270、 271、 272、 273、 27
4、 275、 276、 277、 278、 279、 280、 281、 282、 283、 284、
285、 286、 287、 288、 289、 290、 291、 292、 293、 294、 29
5、 296、 297、 298、 299、 300、 301、 302、 303、 304、 305、
306、 307、 308、 309、 310、 311、 312、 313、 314、 315、 31
6、 317、 318、 319、 320、 321、 322、 323、 324、 325、 326、 327、 328、 329、 330、 331、 332、 333、 334、 335、 336、 33
7、 338、 339、 340、 341、 342、 343、 344、 345、 346、 347、 348、 349、 350、 351、 352、 353、 354、 355、 356、 357、 35
8、 359、 360、 361、 362、 363、 364, 365、 366、 367、 368、 369、 370、 371、 372、 373、 374, 375、 376、 377、 378、 37
9、 380、 381、 382、 383、 384、 385、 386、 387、 388、 389、 390、 391、 392、 393、 394、 395、 396、 397、 398、 399、 40 0、 401、 402、 403、 404又は 405に記載されたいずれかの薄膜形成用基板。 項 407. ガリウム、 インジウム、 アルミニウムのうちから選ばれた少なくとも 1種以上の 成分を含む有機化合物がトリメチルガリゥム、 卜リメチルインジウム、 トリメチルアルミニゥ ムのうちから選ばれた少なくとも 1種以上であることを特徴とする項 406に記載された薄膜 形成用基板。
項 408. 窒化ガリウム、 窒化インジウム、 窒化アルミニウムのうちから選ばれた少なくと も 1種以上を主成分とする薄膜を形成するための基板であって、 該基板に形成される薄膜がガ リウム、 インジウム、 アルミニウムのうちから選ばれた少なくとも 1種以上の成分のハロゲン
化物を主原料としアンモニア、 窒素、 水素のうちから選ばれた少なくとも 1種以上を反応ガス として形成されるものであることを とする項 1、 2、 3、 4、 5、 6、 7、 8、 9、 10、
11、 12、 13、 14、 15、 16、 17、 18、 19、 20、 21、 22、 23、 24、 25、 26、 27、 28、 29、 30、 31、 32、 33、 34、 35、 36、 37、 38、 39、 40、 41、 42、 43、 44、 45、 46、 47、 48、 49、 50、 51、 52、 53、 54、 55、 56、 57、 58、 59、 60、 61、 62、 63、 64、 65、 66、 67、 68、 69、 70、 71、 72、 73、 74、 75、 76、 77、 78、 79、 80、 81、 82、 83、 84、 85、 86、 87、 88、 89、 90、 91、 92、 93、 94、 95、 96、 97、 98、 99、 100、 101、 102、 103、 104、 05、 106、 107、 108、 109、 110、 111、 112、 113、 114、 115、 116、 11
7、 118、 119、 120、 121、 122、 123、 124、 125、 126、 127、 128、 129、 130、 131、 132、 133、 134, 135、 136、 137、 13
8、 139、 140、 141、 142、 143、 144、 145、 146、 147、 148、 149、 150、 151、 152、 153、 154、 155、 156、 157、 158、 15
9、 160、 161、 162、 163、 164、 165、 166、 167、 168、 169、 170、 171、 172、 173、 174、 175、 176、 177、 178、 179、 18
0、 181、 182、 183、 184、 185、 186、 187、 188、 189、 190、 191、 192、 193、 194、 195、 196、 197、 198、 199、 200、 20
1、 202、 203、 204、 205、 206、 207、 208、 209、 210、 211、 212、 213、 214、 215、 216、 217、 218、 219、 220、 221、 22
2、 223、 224、 225、 226、 227、 228、 229、 230、 231、 232、 233、 234、 235、 236、 237、 238、 239、 240、 241、 242、 24
3、 244、 245、 246、 247、 248、 249、 250、 251、 252、 253、 254、 255、 256、 257、 258、 259、 260、 261、 262、 263、 26
4、 265、 266、 267、 268、 269、 270、 271、 272、 273、 274、 275、 276、 277、 278、 279、 280、 281、 282、 283、 284、 28
5、 286、 287、 288、 289、 290、 291、 292、 293、 294, 295、
296、 297、 298、 299、 300、 301、 302、 303、 304、 305、 30
6、 307、 308、 309、 310、 311、 312、 313、 314、 315、 316、 317、 318、 319、 320、 321、 322、 323、 324、 325、 326、 32
7、 328、 329、 330、 331、 332、 333、 334、 335、 336、 337、
338、 339、 340、 341、 342、 343、 344、 345、 346、 347、 34
8、 349、 350、 351、 352、 353、 354、 355、 356、 357、 358、 359、 360、 361、 362、 363、 364、 365、 366、 367、 368、 36
9、 370、 371、 372、 373、 374、 375、 376、 377、 378、 379、 380、 381、 382、 383、 384、 385、 386、 387、 388、 389、 39 0、 391、 392、 393、 394、 395、 396、 397、 398、 399、 400、 401、 402、 403、 404又は 405に記載されたいずれかの薄膜形成用基板。
項 409. ガリゥム、 ィンジゥム、 アルミニゥムのうちから選ばれた少なくとも 1種以上の 成分を含むノ、ロゲン化物が塩化ガリウム、 塩化インジウム、 塩化アルミニウムのうちから選ば れた少なくとも 1種以上であることを特徴とする項 408に記載された薄膜形成用基板。 項 410. 窒化ガリウム、 窒化インジウム、 窒化アルミニウムのうちから選ばれた少なくと も 1種以上を主成分とする薄膜を形成するための基板の $¾i方法であって、 該基板が原料とし て酸化アルミニウムの ¾法によるもの及び金属アルミニウムの直接窒化法によるもののなか
から選ばれたいずれかをそれぞ 虫で用いるかあるいは酸化アルミニウムの ¾法によるも の及び金属アルミニウムの直接窒化法によるものを混合して用いるか少なくともいずれかの原 料を用いて M される窒化アルミニウムを主成分とする焼結体からなることを とする薄膜 形成用基板の製造方法。
項 411. 窒化ガリウム、 窒化インジウム、 窒化アルミニウムのうちから選ばれた少なくと も 1種以上を主成分とする薄膜を形成するための基板の難方法であって、 該基板が窒化アル ミニゥムを主成分とする粉末成形体又は焼結体を非酸化性雰囲気中焼成温度 1500°C以上で 10分間以上焼成することで得られる窒化アルミ二ゥムを主成分とする焼結体からなることを 特徴とする薄膜形成用基板の製造方法。
項 412. 窒化ガリウム、 窒化インジウム、 窒化アルミニウムのうちから選ばれた少なくと も 1種以上を主成分とする薄膜を形成するための基板の難方法であって、 該基板が原料とし て酸化アルミニウムの ¾法によるもの及び金属アルミニウムの直接窒化法によるものから選 ばれたものをそれぞ; W独で用いるかあるいは酸化アルミニウムの ¾法によるもの及び金属 アルミニウムの直接窒化法によるものを混合して用レ ^るか少なくともレずれかの原料を用いて される窒化アルミニウムを主成分とする粉末成形体又は焼結体を非酸化性雰囲気中誠温 度 1500°C以上で 10分間以上焼成することで得られる窒化アルミニウムを主成分とする焼 結体からなることを體とする項 410は 411に記載されたいずれかの薄膜形成用基板の製 造方法。
項 413. 窒化アルミニウムを主成分とする焼結体が 性を有することを特徴とする項 410、 411又は 412に記載されたいずれかの薄膜形成用基板の製造方法。
項 414. 窒化アルミニウムを主成分とする焼結体が 率 1 %以上を有することを體 とする項 410、 411、 412又は 413に記載されたいずれかの薄«成用基板の製造方 法。
項 415. 窒化アルミニウムを主成分とする焼結体が光 ¾ϋ率 5 %以上を有することを特徴 とする項 414に記載された薄膜形成用基板の製造方法。
項 416. 窒化アルミニウムを主成分とする焼結体が光 率 10%以上を有することを特 徴とする項 414又は 415に記載されたいずれかの薄膜形成用基板の製造方法。
項 417. 窒化アルミニウムを主成分とする焼結体が光透過率 20 %以上を有することを特 徴とする項 414, 415又は 416に記載されたいずれかの薄膜形成用基板の製造方法。 項 418. 窒化アルミニウムを主成分とする焼結体が) 率 30%以上を有することを特 徴とする項 414、 415、 416又は.417に記載されたいずれかの薄膜形成用基板の製造 方法。
項 419. 窒化アルミニウムを主成分とする焼結体が 率 40%以上を有することを特 徴とする項 414、 415、 416、 417又は 418に記載されたいずれかの薄膜形成用基 板の製造方法。
項 420. 窒化アルミニウムを主成分とする焼結体が) ^過率 50 %以上を有することを特 徴とする項 414、 415、 416、 417、 418又は 419に記載されたいずれかの薄膜 形成用基板の製造方法。
項 421. 窒化アルミニウムを主成分とする焼結体が光透過率 60 %以上を有することを特 徴とする項 414、 415、 416、 417、 418、 419又は 420に記載されたいずれ かの薄膜形成用基板の製造方法。
項 422. 窒化アルミニウムを主成分とする焼結体が光 ¾i率 80%以上を有することを特 徴とする項 414、 415、 416、 417、 418、 419、 420又は 421に記載され たいずれかの薄膜形成用基板の製造方法。
項 423. 窒化アルミニウムを主成分とする焼結体が 過率 85%以上を有することを特 徴とする項 414、 415、 416、 417、 418、 419、 420、 421又は 422に 記載されたいずれかの薄膜形成用基板の製造方法。
項 424. 窒化アルミニウムを主成分とする粉末成形体又は焼結体を窒化アルミニウム成分 を含む非酸化性雰囲気中;«#^ 1500°C以上で 10分間以上; «することで得られる窒化 アルミニウムを主成分とする焼結体からなることを特徴とする項 410、 411、 412、 4 13、 414、 415、 416、 417、 418、 419、 420、 421、 422又は 42 3に記載されたいずれかの薄膜形成用基板の製造方法。
項 425. 窒化アルミニウム成分が被 «物である窒化アルミニウムを主成分とする粉末成 形体又は焼結体から舰雰囲気である非酸化性雰囲気中に供給され 該非酸化性雰囲気中焼成 ¾ l 500C以上で 10分間以上被«物を することで得られる窒化アルミニウムを主 成分とする焼結体からなることを特徴とする項 424に記載された薄膜形成用基板の製造方法。 項 426. 窒化アルミニウム成分が被 «物である窒化アルミニウムを主成分とする粉末成 形体又は焼結体以外から誠雰囲気である非酸化性雰囲気中に供給され、 該非酸化性雰囲気中 焼成 ¾1500°C以上で 10分間以上被 «物を焼成することで得られる窒化アルミニウム を主成分とする焼結体からなることを特徴とする項 424に記載された薄膜形成用基板の製造 方法。
項 427. 窒化アルミニウムを主成分とする粉末成形体又は焼結体を窒化アルミニウムを主 成分とする材料からなる 器あるいは焼成治具を用いて «することを特徴とする項 42 4又は 426に記載されたいずれかの薄膜形成用基板の製造方法。
項 428. 被 物である窒化アルミニウムを主成分とする粉末成形体又は焼結体と謝皮焼 成物以外の窒化アルミニウムを主成分とする粉末、 あるいは窒化アルミニウムを主成分とする 粉末成形体、 あるいは窒化アルミ二ゥムを主成分とする焼結体のうちから選ばれた少なくとも いずれか 1以上のものとを «容器ある ゝは焼成治具内に同時に存在させて焼成することを特 徴とする項 426又は 427に記載されたいずれかの薄膜形成用基板の製造方法。
項 429. 窒化アルミニウムを主成分とする粉末成形体又は焼結体を窒化アルミニウム、 夕 ングステン、 モリブデン、 窒化ほう素、 窒化ほう素を塗布した力一ボンのうちから選ばれた少 なくとも 1種以上を主成分とする材料からなる焼成容器あるいは! «治具を用いて焼成するこ とを [とする項 424、 425、 426、 427又は 428に記載されたいずれかの薄膜形 成用基板の製造方法。
項 430. 窒化アルミニウムを主成分とする粉末成形体をいつたん焼成して窒化アルミニゥ ムを主成分とする焼結体となし、 該焼結体をホットプレス法あるいは熱間静水圧加圧 (HI P) 法によりカロ JEWすることを特徴とする項 410、 411、 412、 413、 414、 415、 416、 417、 418、 419、 420、 421、 422、 423、 424、 425、 42 6、 427、 428又は 429に記載されたいずれかの薄膜形成用基板の製造方法。
項 431. 窒化ガリウム、 窒化インジウム、 窒化アルミニウムのうちから選ばれた少なくと も 1種以上を主成分とする薄膜を形成するための基板の難方法であって、 該基板が窒化アル ミニゥムを主成分とする粉末成形体又は焼結体を非酸化性雰囲気中焼成温度 175 以上で 3時間以上加熱することを特徴とする項 410、 411、 412、 413、 414、 415、 416、 417、 418、 419、 420、 421、 422、 423、 424、 425、 42 6、 427、 428、 429又は 430に記載されたいずれかの薄膜形成用基板の^ i方法。 項 432. 窒化ガリウム、 窒化インジウム、 窒化アルミニウムのうちから選ばれた少なくと も 1種以上を主成分とする薄膜を形成するための基板の難方法であって、 該基板が希土 素化合物及びアルカリ土類金属化合物のうちから選ばれた少なくとも 1種以上の化合物を含む
窒化アルミニウムを主成分とする粉末成形体又は焼結体を非酸化性雰囲気中焼成温度 175 0 °C以上で 3時間以上焼成し含まれる成分のうち少なくとも希土^素化合物及びアル力リ土 類金属化合物及ぴ麼素のうちから選ばれた少なくとも 1種以上の成分を飛散 · [^し減少させ ることで得られる窒化アルミニウムを主成分とする焼結体からなることを特徴とする項 410、 411、 412、 413、 414、 415、 416、 417、 418、 419、 420、 42 1、 422、 423、 424、 425、 426、 427、 428、 429、 430又は 431 に記載されたいずれかの薄膜形成用基板の製造方法。
項 433. 焼成 が 1900°C以上であることを特徴とする項 431又は 432に記載さ れたいずれかの薄膜形成用基板の製造方法。
項 434. 焼成温度が 2050°C以上であることを特徴とする項 431, 432又は 433 に記載されたいずれかの薄膜形成用基板の製造方法。
項 435. 焼成 が 2100°C以上であることを特徴とする項 431、 432、 433又 は 434に記載されたいずれかの薄膜形成用基板の製造方法。
項 436. 窒化ガリウム、 窒化インジウム、 窒化アルミニウムのうちから選ばれた少なくと も 1種以上を主成分とする薄膜を形成するための基板の継方法であって、 該基板が希土^; 素化合物のうちから選ばれた少なくとも 1種以上の化合物及びアルカリ土類金属化合物のうち から選ばれた少なくとも 1種以上の化合物を同時に含む窒化アルミニウムを主成分とする粉末 成形体又は焼結体を非酸化性雰囲気中焼成温度 1750°C以上で 3時間以上焼成し含まれる成 分のうち少なくとも希土^ δ素化合物及びアル力リ土類金属化合物及び酸素のうちから選ばれ た少なくとも 1種以上の成分を飛散 · |¾し減少させることで得られる窒化アルミニウムを主 成分とする焼結体からなることを特徴とする項 410、 411、 412、 413、 414、 4 15、 416、 417、 418、 419、 420、 421、 422、 423、 424、 425、 426、 427、 428、 429、 430、 431、 432、 433、 434又は 435に記 載されたいずれかの薄膜形成用基板の製造方法。
項 437. 窒化ガリウム、 窒化インジウム、 窒化アルミニウムのうちから選ばれた少なくと も 1種以上を主成分とする薄膜を形成するための基板の製造方法において、 該薄膜を形成する ための基板が窒化アルミニゥムを主成分とする粉末成形体を舰して得られる窒化アルミニゥ ムを主成分とする焼結体からなるものであって、 麵末成形体は窒化アルミニゥム原料粉末を 主成分とするグリーンシートからなるものであることを難とする項 410、 411、 412、 413、 414、 415、 416、 417、 418、 419、 420、 421、 422、 42 3、 424、 425、 426、 427、 428、 429、 430、 431、 432、 433、 434、 435又は 436に記載されたいずれかの薄膜形成用基板の製造方法。
項 438. 窒化ガリウム、 窒化インジウム、 窒化アルミニウムのうちから選ばれた少なくと も 1種以上を主成分とする薄膜を形成するための基板の製造方法において、'該薄膜を形成する ための基板が窒化アルミニウムを主成分とする粉末成形体を舰して得られる焼結体をさらに 焼成して得られる窒化アルミニウムを主成分とする焼結体からなるものであって、 該粉末成形 体は窒化アルミニウム原料粉末を主成分とするグリーンシートからなるものであることを特徴 とする項 410、 411、 412、 413、 414、 415、 416、 417、 418、 41 9、 420、 421、 422、 423、 424、 425、 426、 427、 428、 429、 430、 431、 432、 433、 434、 435、 436又は 437に記載されたいずれか の薄膜形成用基板の製造方法。
項 439. 焼成温度 1750 以上で 10時間以上焼成を行うことを特徴とする項 410、 411、 412、 413、 414、 415、 416、 417、 418、 419、 420、 42 1、 422、 423、 424、 425、 426、 427、 428、 429、 430、 431、
432、 433、 434、 435、 436、 437又は 438に記載されたいずれかの薄膜形 成用基板の製造方法。
項 440. 焼成 1900°C以上で 6時間以上 «を行うことを特徴とする項 410、 4 11、 412、 413、 414、 415、 416、 417、 418、 419、 420、 421、 422、 423、 424、 425、 426、 427、 428、 429、 430、 431、 43 2、 433、 434、 435、 436、 437、 438又は 439に記載されたいずれかの薄 膜形成用基板の製造方法。
項 441. 焼成^^ 2050°C以上で 4時間以上;^を行うことを特徴とする項 410、 4 11、 412、 413、 414、 415、 416、 417、 418、 419、 420、 421、 422、 423、 424、 425、 426、 427、 428、 429、 430、 431、 43 2、 433、 434、 435、 436、 437、 438、 439又は 440に記載されたいず れかの薄膜形成用基板の S¾i方法。
項 442. 焼成温度 2100°C以上で 3時間以上焼成を行うことを特徴とする項 410、 4 11、 412、 413、 414、 415、 416、 417、 418、 419、 420、 421、 422、 423、 424、 425、 426、 427、 428、 429、 430、 431、 43
2、 433、 434、 435、 436、 437、 438、 439、 440又は 441に記載さ れたいずれかの薄膜形成用基板の製造方法。
項 443. 焼成雰囲気が窒素、 ヘリウム、 ネオン、 アルゴンのうちから選ばれた少なくとも 1種以上を含むものであることを [とする項 410、 411、 412、 413、 414、 4 15、 416、 417、 418、 419、 420、 421、 422、 423、 424、 425、 426、 427、 428、 429、 430、 431、 432、 433、 434、 435、 43 6、 437、 438、 439、 440、 441又は 442に記載されたいずれかの薄膜形成用 基板の製造方法。
項 444. 焼成雰囲気が 性雰囲気であることを特徴とする項 410、 411、 412、 413、 414、 415、 416、 417、 418、 419、 420、 421、 422、 42
3、 424、 425、 426、 427、 428、 429、 430、 431、 432、 433、 434、 435、 436、 437、 438、 439、 440、 441、 442又は 443に記 載されたいずれかの薄膜形成用基板の製造方法。
項 445. 焼成雰囲気が水素、 炭素、 一酸化炭素、 炭化水素のうちから選ばれた少なくとも 1種以上を含むものであることを特徴とする項 410、 411、 412、 413、 414、 4
15、 416、 417、 418、 419、 420、 421、 422、 423、 424、 425、 426、 427、 428、 429、 430、 431、 432、 433、 434、 435、 43
6、 437、 438、 439、 440、 441、 442、 443又は 444に記載されたいず れかの薄膜形成用基板の製造方法。
項 446. 焼成雰囲気が水素、 炭素、 一酸化炭素、 炭化水素のうちから選ばれた少なくとも 1種以上を 0. 1 ppm以上含むものであることを特徴とする項 443、 444又は 445に 記載されたいずれかの薄膜形成用基板の製造方法。
項 447. 焼成される窒化アルミニウムを主成分とする粉末成形体又は焼結体の最小寸法が 8 mm以下であることを特徴とする項 410、 411、 412、 413、 414、 415、 4
16、 417、 418、 419、 420、 421、 422、 423、 424、 425、 426、 427、 428、 429、 430、 431、 432、 433、 434、 435、 436、 43
7、 438、 439、 440、 441、 442、 443、 444、 445又は 446に記載さ れたいずれかの薄膜形成用基板の製造方法。
項 448. 焼成される窒化アルミニウムを主成分とする粉末成形体又は焼結体が板状であり
その厚みが 8 mm以下であることを特徴とする項 410、 411、 412、 413、 414、 415、 416、 417、 418、 419、 420、 421、 422、 423、 424、 42 5、 426、 427、 428、 429、 430、 431、 432、 433、 434、 435、
436、 437、 438、 439、 440、 441、 442、 443、 444、 445、 44 6又は 447に記載されたいずれかの薄膜形成用基板の製造方法。
項 449. 希土 ¾素及びアル力リ土類金属のうちから選ばれた少なくとも 1種以上の成分 の含有量が元素 で合計 0. 5重量%以下、 酸 有量が元素 で 0. 9重量%以下、 結 晶相として A 1Nを 95%以上、 窒化アルミニウム粒子の大きさが 5 m以上、 かつ 性 を有することを特徴とする窒化アルミニウムを主成分とする焼結体。
項 450. 希土^ ¾素及びアルカリ土類金属のうちから選ばれた少なくとも 1種以上の成分 の含有量が元素換算で合計 0. 2重量%以下、 酸素 有量が 0. 5量%以下であることを特 徴とする項 449に記載された窒化アルミニウムを主成分とする焼結体。
項 451. 希土類 素及びアルカリ土類金属のうちから選ばれた少なくとも 1種以上の成分 の含有量が元素騰で合計 0. 05重量%以下、 酸素 S 有量が 0. 2量%以下であることを 特徴とする項 449又は 450に記載されたいずれかの窒化アルミニウムを主成分とする焼結 体。
項 452. 希土 ¾素及びアルカリ土類金属のうちから選ばれた少なくとも 1種以上の成分 の含有量が元素換算で合計 0. 02重量%以下、 酸素量含有量が 0. 1量%以下であることを 特徴とする項 449, 450又は 451に記載されたいずれかの窒化アルミニウムを主成分と する焼結体。
項 453. 希土類 素及びアルカリ土類金属のうちから選ばれた少なくとも 1種以上の成分 の含有量が元素換算で合計 0. 005重量%以下、 酸素量含有量が 0. 05量%以下であるこ とを赚とする項 449、 450、 451又は 452に記載されたいずれかの窒化アルミニゥ ムを主成分とする焼結体。
項 454. 光 ¾i率が 1%以上であることを特徴とする項 449、 450、 451、 452 又は 453に記載されたいずれかの窒化アルミニウムを主成分とする焼結体。
項 455. 光 ¾1率が 5 %以上であることを特徵とする項 454に記載された窒化アルミ二 ゥムを主成分とする焼結体。
項 456. 光 ¾ 率が 10%以上であることを とする項 454又は 455に記載された いずれかの窒化アルミ二ゥムを主成分とする焼結体。
項 457. 光 ¾i率が 20%以上であることを特徴とする項 454、 455又は 456に記 載されたいずれかの窒化アルミニウムを主成分とする焼結体。
項 458. 光 ¾i率が 30%以上であることを辦教とする項 454、 455、 456又は 4
57に記載されたいずれかの窒化アルミニウムを主成分とする焼結体。
項 459. 光 ¾1率が、 40%以上であることを特徴とする項 454、 455、 456、 45 7又は 458に記載されたいずれかの窒化アルミニウムを主成分とする焼結体。
項 460. 光 ¾i率が 50%以上であることを特徴とする項 454、 455、 456、 45 7、 458又は 459に記載されたいずれかの窒化アルミニウムを主成分とする焼結体。 項 461. 光 ¾ 率が 60%以上であることを f [とする項 454、 455、 456、 45 7、 458、 459又は 460に記載されたいずれかの窒化アルミニウムを主成分とする焼結 体。
項 462. 光 率が 80%以上であることを特徴とする項 454、 455、 456、 45 7、 458、 459、 460又は 461に記載されたいずれかの窒化アルミニウムを主成分と する焼結体。
項 463. 光醒率が 85%以上であることを赚とする項 454、 455、 456、 45 7、 458、 459、 460、 461又は 462に記載されたいずれかの窒化アルミニウムを 主成分とする焼結体。
項 464. 光 J¾ 性あるいは光醒率が少なくとも波長 200 nm〜800 nmの範囲の光 に対してのものであることを特徴とする項 449、 454、 455、 456、 457、 458、 459、 460、 461、 462又は 463に記載されたいずれかの窒化アルミニウムを主成 分とする焼結体。
項 465.結晶相として A 1Nを 98%以上含む事を特徴とする項 454、 455、 456、 457、 458、 459、 460、 461、 462、 463又は 464に記載されたいずれか の窒化アルミニゥムを主成分とする焼結体。
項 466. 結晶相が実質的に A 1 N単一相であることを特徴とする項 465に記載された窒 化アルミニゥムを主成分とする焼結体。
項 467. 窒化アルミニウム粒子の大きさが 8 m以上であることを特徴とする項 449、 450、 451、 452、 453、 454、 455、 456、 457、 458、 459、 46 0、 461、 462、 463、 464、 465又は 466に記載されたいずれかの窒化アルミ 二ゥムを主成分とする焼結体。
に記載されたいずれかの窒化アルミニウムを主成分とする焼結体。
項 468. 窒化アルミニウム粒子の大きさが 15 zm以上であることを とする項 467 に記載された窒化アルミニウムを主成分とする焼結体。
項 469. 窒化アルミニウム粒子の大きさが 25 m以上であることを特徴とする項 467 又は 468に記載されたいずれかの窒化アルミニウムを主成分とする焼結体。
項 470. 窒化アルミニウム粒子の大きさが 1ひ 0 m以下であることを特徴とする項 44 9、 450、 451、 452、 453、 454、 455、 456、 457、 458、 459、 460、 461、 462、 463、 464、 465、 466、 467、 468又は 469に記 載されたいずれかの窒化アルミニウムを主成分とする焼結体。
項 471. 室温における熱伝導率が 20 OWZmK以上であることを とする項 449、 450、 451、 452、 453、 454、 455、 456、 457、 458、 459、 46
0、 461、 462、 463、 464、 465、 466、 467、 468、 469又は 470 に記載されたいずれかの窒化アルミニウムを主成分とする焼結体。
項 472. 室温における熱伝導率が 22 OWZmK以上であることを特徴とする項 471に 記載された窒化アルミニウムを主成分とする焼結体。
項 473. 平均表面粗さ Ra 200 Onm以下であることを難とする項 449、 450、 451、 452、 453、 454、 455、 456、 457、 458、 459、 460、 46
1、 462、 463、 464、 465、 466、 467、 468、 469、 470、 471又 は 472に記載されたいずれかの窒化アルミニウムを主成分とする焼結体。
項 474. 平均表面粗さ R a 1000 nm以下であることを i [とする項 473に記載され た窒化アルミニウムを主成分とする焼結体。
項 475. 平均表面粗さ R a 100 nm以下であることを特徴とする項 473又は 474に 記載されたいずれかの窒化アルミニウムを主成分とする焼結体。
項 476. 平均表面粗さ 2 Onm以下であることを特徴とする項 473、 474又は 475 に記載されたいずれかの窒化アルミニウムを主成分とする焼結体。
項 477.表面粗さが大きいことを籠とする項 449、 450、 451、 452、 453、 454、 455、 456、 457、 458、 459、 460、 461、 462、 463、 46 4、 465、 466、 467、 468、 469、 470、 471、 472、 473、 474又
は 475に記載されたいずれかの窒化アルミニウムを主成分とする焼結体。
項 478. 平均表面粗さ R aが 7 Onm以上であることを とする項 449、 450、 4 51、 452、 453、 454、 455、 456、 457、 458、 459、 460、 461、 462、 463、 464、 465、 466、 467、 468、 469、 470、 471、 47 2、 473、 474、 475又は 477に記載されたいずれかの窒化アルミニウムを主成分と する焼結体。
項 479. 平均表面粗さ R aが 1000 nmより大きいことを特徴とする項 478に記載さ れた窒化アルミニウムを主成分とする焼結体。
項 480. 平均表面粗さ R aが 2000 nmより大きいことを特徴とする項 478又は 47 9に記載されたいずれかの窒化アルミニウムを主成分とする焼結体。
項 481. 表面が焼き放し (a s— f i r e)、 ラッフ ¾T磨、 ブラスト研磨、 鏡面研磨、 化学 腐食及びプラズマガスによる腐食のうちから選ばれた少なくともいずれかの状態であることを 特徴とする項 449、 450、 451、 452、 453、 454、 455、 456、 457、 458、 459、 460、 461、 462、 463、 464、 465、 466、 467、 46 8、 469、 470、 471、 472、 473、 474、 475、 476、 477、 478、 479又は 480に記載されたいずれかの窒化アルミニウムを主成分とする焼結体。
項 482. 表面の少なくとも一部が鏡面研磨された状態であることを特徴とする項 481に 記載された窒化アルミニウムを主成分とする焼結体。
項 483. 表面の少なくとも一部が平均表面粗さ R a 2000 nmより大きい平滑度である ことを特徴とする項 449、 450、 451、 452、 453、 454、 455、 456、 4 57、 458、 459、 460、 461、 462、 463、 464、 465、 466、 467、 468、 469、 470、 471、 472、 473、 474、 475、 476、 477、 47 8、 479、 480、 481又は 482に記載されたいずれかの窒化アルミニウムを主成分と する焼結体。
項 484. 希土類 素化合物及びアルカリ土類金属化合物のうちから選ばれた少なくとも 1 種以上の化合物を含む窒化アルミニウムを主成分とする粉末成形体又は焼結体を非酸化性雰囲 気中焼成温度 1750°C以上で 3時間以上焼成し含まれる成分のうち少なくとも希土^素化 合物及びアルカリ土類金属化合物及ぴ避素のうちから選ばれた少なくとも 1種以上の成分を飛 散 ·Ι^¾し減少させることにより得られることを特徴とする項 449、 450、 451、 45
2、 453、 454、 455、 456、 457、 458、 459、 460、 461、 462、 463、 464、 465、 466、 467、 468、 469、 470、 471、 472、 47
3、 474、 475、 476、 477、 478、 479、 480、 481、 482又は 483 に記載されたいずれかの窒化アルミニウムを主成分とする焼結体。
項 485. 希土類 素化合物のうちから選ばれた少なくとも 1種以上の化合物及びアルカリ 土類金属化合物のうちから選ばれた少なくとも 1種以上の化合物を同時に含む窒化アルミニゥ ムを主成分とする粉末成形体又は焼結体を非酸化性雰囲気中焼成温度 1750°C以上で 3時間 以上舰することを體とする項 484に記載された窒化アルミニウムを主成分とする焼結体。 項 486. 焼成温度 1750°C以上で 3時間以上焼成される粉末成形体又は焼結体の原料が 酸化アルミニウムの還元法によるもの及び金属アルミニウムの直接窒化法によるもののうちか ら選ばれた 1種だけか、 あるいは酸化アルミ二ゥムの jl^法によるもの及び金属アルミニゥム の直接窒化法によるものの両方を混合したもの、 いずれかであることを特徴とする項 484又 は 485に記載されたいずれかの窒化アルミニウムを主成分とする焼結体。
項 487. 焼成温度 1750°C以上で 10時間以上焼成を行うことを特徴とする項 484、 485又は 486に記載されたいずれかの窒化アルミニウムを主成分とする焼結体。
項 488. 焼成 1900°C以上で 6時間以上 «を行うことを特徴とする項 484、 4 85, 486又は 487に記載されたいずれかの窒化アルミニウムを主成分とする焼結体。 項 489. 焼成温度 2050°C以上で 4時間以上焼成を行うことを特徴とする項 484、 4 85、 486、 487又は 488に記載されたいずれかの窒化アルミニウムを主成分とする焼 結体。
項 490. 焼成 2100°C以上で 3時間以上 «を行うことを特徴とする項 484、 4 85、 486、 487、 488又は 489に記載されたいずれかの窒化アルミニウムを主成分 とする焼結体。
項 491. 焼成雰囲気が窒素、 ヘリウム、 ネオン、 アルゴンのうちから選ばれた少なくとも 1種以上を含むものであることを ^とする項 484、 485、 486、 487、 488、 4 89又は 490に記載されたいずれかの窒化アルミニウムを主成分とする焼結体。
項 492. 焼成雰囲気が ^性雰囲気であることを特徴とする項 484、 485、 486、 487、 488、 489、 490又は 491に記載されたいずれかの窒化アルミニウムを主成 分とする焼結体。
項 493. 焼成雰囲気が水素、 炭素、 一酸化炭素、 炭化水素のうちから選ばれた少なくとも 1種以上を含むものであることを とする項 484、 485、 486、 487、 488、 4 89、 490、 491又は 492に記載されたいずれかの窒化アルミニウムを主成分とする焼 結体。
項 494. 焼成雰囲気が水素、 炭素、 一酸化炭素、 炭化水素のうちから選ばれた少なくとも 1種以上を 0. 1 ppm以上含むものであることを特徴とする項 491、 492又は 493に 記載されたいずれかの窒化アルミニウムを主成分とする焼結体。
項 495. 焼成 750°C以上で 3時間以上 «される窒化アルミニウムを主成分とす る粉末成形体又は焼結体の最小寸法が 8mm以下であることを特徴とする項 484、 485、 486、 487、 488、 489、 490、 491、 492、 493又は 494に記載された いずれかの窒化アルミニウムを主成分とする焼結体。
項 496. 焼成温度 1750°C以上で 3時間以上焼成される窒化アルミニウムを主成分とす る粉末成形体又は焼結体が板状でありその厚みが 8mm以下であることを特徵とする項 484、 485、 486、 487、 488、 489、 490、 491、 492、 493、 494又は 4 95に記載されたいずれかの窒化アルミニウムを主成分とする焼結体。
項 497. 少なくともアルミニウム成分を含みかつ光 性を有する酸化亜鉛を主成分とす る焼結体。
項 498. 酸化 を Zn〇換算で 55. 0モル%以上含むことを特徴とする項 497に記 載された酸化亜鉛を主成分とする焼結体。
項 499. アルミニウム成分を A 12〇3 で 45. 0モル%以下含むことを特徴とする項 497又は 498に記載されたいずれかの酸化亜鉛を主成分とする焼結体。
項 500. アルミニウム成分を A 1203騰で 0. 001モル%〜45. 0モル%の範囲含 むことを特徴とする項 499に記載された酸化亜鉛を主成分とする焼結体。
項 501. アルミニウム成分を A 1203換算で 0. 005モル%〜45. 0モル%の範囲含 むことを糊数とする項 499又は 500に記載されたいずれかの酸化 を主成分とする焼結 体。
項 502. アルミニウム成分を A12〇3騰で 0. 02モル%〜45. 0モル%の範囲含む ことを特徴とする項 499, 500又は 501に記載されたいずれかの酸化亜鉛を主成分とす る焼結体。
項 503. アルミニウム成分を A 1203購で0. 08モル%〜35. 0モル%の範囲含む
ことを特徴とする項 499、 500、 501又は 502に記載されたいずれかの酸化亜鉛を主 成分とする焼結体。
項 504. アルミニゥム成分を含み同時に希土類 素成分及び遷移金属成分のうちから選ば れた少なくとも 1種以上の成分を含むことを特徴とする項 497、 498、 499、 500、 501又は 502に記載されたいずれかの酸化亜鉛を主成分とする焼結体。
項 505. アルミニウム成分を含み同時に希土類元素成分のうちから選ばれた少なくとも 1 種以上の成分を含むことを特徴とする項 504に記載された酸化亜鉛を主成分とする焼結体。 項 506. 希土類 素成分がイットリウム、 ジスプロシウム、 ホルミウム、 エルビウム、 ィ ッテルビウムのうちから選ばれた少なくとも 1種以上の成分であることを特徴とする項 504 又は 505に記載されたいずれかの酸化亜鉛を主成分とする焼結体。
項 507. アルミニゥム成分を含み同時に遷移金属成分のうちから選ばれた少なくとも 1種 以上の成分を含むことを特徴とする項 504に記載された酸化亜鉛を主成分とする焼結体。 項 508. 希土 素成分及び遷移金属成分のうちから選ばれた少なくとも 1種以上の成分 を酸化物 で 10. 0モル%以下含むことを特徴とする項 504、 505、 506又は 50 7に記載されたいずれかの酸化亜鉛を主成分とする焼結体。
項 509. 希土^素成分のうちから選ばれた少なくとも 1種以上の成分を酸化物騰で 1 0. 0モル%以下含むことを特徴とする項 508に記載された酸化亜鉛を主成分とする焼結体。 項 510. 遷移金属成分のうちから選ばれた少なくとも 1種以上の成分を酸化物購で 10. 0モル%以下含むことを特徴とする項 508又は 509に記載されたいずれかの酸化亜鉛を主 成分とする焼結体。
項 511. 遷移金属成分が鉄及びクロムのうちから選ばれた少なくとも 1種以上の成分であ ることを i [とする項 504、 507、 508又は 510に記載されたいずれかの酸化 ¾を 主成分とする焼結体。
項 512. アルミニウム成分を A 12〇3換算で 45. 0モル%以下含み、 同時に希土^素 成分のうちから選ばれた少なくとも 1種以上の成分を酸化物 »で 10. 0モル%以下含むこ とを特徴とする項 504、 505、 506、 507、 508、 509、 510又は 511に記 載されたいずれかの酸化亜鉛を主成分とする焼結体。
項 513. 希土類 素成分のうちから選ばれた少なくとも 1種以上の成分を酸化 «算で 0. 0002モル%〜 10. 0モル%の範囲含むことを特徴とする項 512に記載された酸化亜鉛 を主成分とする焼結体。
項 514. 希土類 素成分のうちから選ばれた少なくとも 1種以上の成分を酸化物 で 0. 0006モル%〜6. 0モル%の範囲含むことを特徴とする項 512又は 513に記載された いずれかの酸化亜鉛を主成分とする焼結体。
項 515. 希土 ¾素成分のうちから選ばれた少なくとも 1種以上の成分を酸化物 ^ で0. 001モル%〜6. 0モル%の範囲含むことを特徴とする項 512、 513又は 514に記載 されたいずれかの酸化亜鉛を主成分とする焼結体。
項 516. 希土類 素成分のうちから選ばれた少なくとも 1種以上の成分を酸化物露で 0. 002モル%〜3. 0モル%の範囲含むことを特徴とする項 512、 513、 514又は 51 5に記載されたいずれかの酸化亜鉛を主成分とする焼結体。
項 517. アルミニウム成分を A 1203観で 0. 001モル%〜45. 0モル%の範囲含 み、 同時に希土類 素成分のうちから選ばれた少なくとも 1種以上の成分を含むことを特徴と する項 504、 505、 506、 507、 508、 509、 510、 511、 512、 513、 514、 515又は 516に記載されたいずれかの酸化亜鉛を主成分とする焼結体。
項 518. 率が 1%以上であることを赚とする項 497、 498、 499、 500、
501、 502、 503、 504、 505、 506、 507、 508、 509、 510、 51 1、 512、 513、 514、 515、 516又は 517に記載されたいずれかの酸化 »を 主成分とする焼結体。
項 519. 光 ¾i率が 10%以上であることを特徴とする項 518に記載された酸化亜鉛を 主成分とする焼結体。
項 520. 率が 20%以上であることを とする項 518又は 519に記載された いずれかの酸化亜鉛を主成分とする焼結体。
項 521. 光 ¾ϋ率が 30%以上であることを ^[とする項 518、 519又は 520に記 載されたいずれかの酸化亜鉛を主成分とする焼結体。
項 522. 光透過率が 40%以上であることを特徴とする項 518、 519、 520又は 5 21に記載されたいずれかの酸化亜鉛を主成分とする焼結体。
項 523. ¾¾1率が 50%以上であることを特徴とする項 518、 519、 520、 52 1又は 522に記載されたいずれかの酸化亜鉛を主成分とする焼結体。
項 524. 光腿率が 60%以上であることを f (とする項 518、 519、 520、 52 1、 522又は 523に記載されたいずれかの酸化亜鉛を主成分とする焼結体。
項 525. 光 ¾ 率が 80%以上であることを特徴とする項 518、 519、 520、 52
1、 522、 523又は 524に記載されたいずれかの酸化亜鉛を主成分とする焼結体。 項 526. 光 性あるいは光 ¾i 率が少なくとも波長 200 nm〜800 nmの範囲の光 に対してのものであることを特徴とする項 497、 518、 519、 520、 521、 522、 523、 524又は 525に記載されたいずれかの酸化亜鉛を主成分とする焼結体。
項 527. 導電性を有することを特徴とする項 497、 498、 499、 500、 501、 502、 503、 504、 505、 506、 507、 508、 509、 510、 511、 51
2、 513、 514、 515、 516、 517、 518、 519、 520、 521、 522、 523、 524、 525又は 526に記載されたいずれかの酸化亜鉛を主成分とする焼結体。 項 528. 室温における抵抗率が 1 X 102Ω · c m以下であることを特徴とする項 497、
498、 499、 500、 501、 502、 503、 504、 505、 506、 507、 50 8、 509、 510、 511、 512、 513、 514、 515、 516、 517、 518、
519、 520、 521、 522、 523、 524、 525、 526又は 527に記載された いずれかの酸化亜鉛を主成分とする焼結体。
項 529. 室温における抵抗率が IX 10°Ω - c m以下であることを特徴とする項 528に 記載された酸化亜鉛を主成分とする焼結体。
項 530. 室温における抵抗率が 1 X 10— 2Ω · cm以下であることを とする項 528 又は 529に記載されたいずれかの酸化亜鉛を主成分とする焼結体。
項 531. ½¾i性を有しかつ導電性を有することを霞とする項 497、 498、 499、 500、 501、 502、 503、 504、 505、 506、 507、 508、 509、 51 0、 511、 512、 513、 514、 515、 516、 517、 518、 519、 520、 521、 522、 523、 524、 525、 526、 527、 528、 529又は 530に記 載されたいずれかの酸化亜鉛を主成分とする焼結体。
項 532. 光 ¾i性を有することを特徴とする窒化ガリウムを主成分とする焼結体。
項 533. 光 ¾1率が 1%以上であることを特徴とする項 532に記載された窒化ガリウム を主成分とする焼結体。
項 534. 光 Mil率が 5%以上であることを特徴とする項 533に記載された窒化ガリウム を主成分とする焼結体。
項 535. 光 ¾i率が 10 %以上であることを特徴とする項 533又は 534に記載された
いずれかの窒化ガリゥムを主成分とする焼結体。
項 536. 光 率が 20 %以上であることを鎌とする項 533、 534又は 535に記 載されたいずれかの窒化ガリウムを主成分とする焼結体。
項 537. 光 ¾ϋ率が 30%以上であることを特徴とする項 533、 534、 535又は 5 36に記載されたいずれかの窒化ガリゥムを主成分とする焼糸吉体。
項 538. 光 率が 40%以上であることを特徴とする項 533、 534、 535、 53 6又は 537に記載されたいずれかの窒化ガリウムを主成分とする焼結体。
項 539. 光 率が 50%以上であることを特徴とする項 533、 534、 535、 53 6、 537又は 538に記載されたいずれかの窒化ガリウムを主成分とする焼結体。
項 540. 光翻率が 60%以上であることを特徴とする項 533、 534、 535、 53 6、 537、 538又は 539に記載されたいずれかの窒化ガリゥムを主成分とする焼結体。 項 541. 光 ¾ 率が 80%以上であることを赚とする項 533、 534、 535、 53 6、 537、 538、 539又は 540に記載されたいずれかの窒化ガリゥムを主成分とする 焼結体。
項 542. 光顯率が 85%以上であることを特徴とする項 533、 534、 535、 53 6、 537、 538、 539、 540又は 541に記載されたいずれかの窒化ガリゥムを主成 分とする焼結体。
項 543. 光 M率が 1 %未満の窒化ガリゥムを主成分とする焼結体。
項 544. 光 ¾1率が 0%の項 543に記載された窒化ガリウムを主成分とする焼結体。 項 545. ¾¾ 性あるいは光 ¾ 率が少なくとも波長 200 nm〜800 nmの範囲の光 に対してのものであることを特徵とする項 532、 533、 534、 535、 536、 537、
538、 539、 540、 541、 542、 543又は 544に記載されたいずれかの窒化ガ リゥムを主成分とする焼結体。
項 546. 導電性を有することを特徴とする窒化ガリウムを主成分とする焼結体。
項 547. 室温における抵抗率 1 X 104Ω · cm以下を有することを特徴とする項 532、
533、 534、 535、 536、 537、 538、 539、 540、 541、 542、 54
3、 544、 545又は 546に記載されたいずれかの窒化ガリゥムを主成分とする焼結体。 項 548.室温における抵抗率 1 X 101 Ω · c m以下を有することを ί(#^ [とする項 546又 は 547に記載されたいずれかの窒化ガリウムを主成分とする焼結体。
項 549. 室温における抵坊率 1 X 10。 Ω · c m以下を有することを特徴とする項 546、
547又は 548に記載されたいずれかの窒化ガリゥムを主成分とする焼結体。
項 550.室温における抵抗率 1 X 10 2 Ω · c m以下を有することを樹敫とする項 546、
547、 548又は 549に記載されたいずれかの窒化ガリゥムを主成分とする焼結体。 項 551. 性を有しかつ導電性を有することを體とする項 532、 533、 534、
535、 536、 537、 538、 539、 540、 541、 542、 543、 544、 54
5、 546、 547、 548、 549又は 550に記載されたいずれかの窒化ガリゥムを主成 分とする焼結体。
項 552. ガリウム成分を GaN換算で 55. 0モル%以上含む窒化ガリウムを主成分とす る焼結体。
項 553. アルカリ土類金属及び希土 素のうちから選ばれた少なくとも 1種以上の成分 を含有することを特徴とする窒化ガリゥムを主成分とする焼結体。
項 554. アル力リ土類金属及び希土類 素のうちから選ばれた少なくとも 1種以上の成分 を酸ィ匕物換算で 30モレ%以下含有することを,とする項 532、 533、 534、 535、 536、 537、 538、 539、 540、 541、 542、 543、 544、 545、 54
6、 547、 548、 549、 550、 551、 552又は 553に記載されたいずれかの窒 化ガリゥムを主成分とする焼結体。
項 555. アルカリ土類金属及び希土類 素のうちから選ばれた少なくとも 1種以上の成分 を酸化物,で 20モル%以下含有することを特徴とする項 553又は 554に記載されたい ずれかの望化ガリゥムを主成分とする焼結体。
項 556. アル力リ土類金属及び希土類 素のうちから選ばれた少なくとも 1種以上の成分 を酸ィ匕物 で 10モル%以下含有することを とする項 553、 554又は 555に記載 されたいずれかの窒化ガリゥムを主成分とする焼結体。
項 557. 亜鉛、 カドミウム、 炭素、 珪素、 ゲルマニウム、 セレン、 及びテルルのうちから 選ばれた少なくとも 1種以上の成分を含有することを特徴とする窒化ガリウムを主成分とする 焼結体。
項 558. 亜鉛、 カドミウム、 炭素、 珪素、 ゲルマニウム、 セレン、 及びテルルのうちから 選ばれた少なくとも 1種以上の成分を元素換算で 10モル%以下含有することを特徴とする項 532、 533、 534、 535、 536、 537、 538、 539、 540、 541、 54 2、 543、 544、 545、 546、 547、 548、 549、 550、 551、 552、 553、 554、 555、 556又は 557に記載されたいずれかの窒化ガリウムを主成分と する焼結体。 · 項 559. 亜鉛、 カドミウム、 炭素、 珪素、 ゲルマニウム、 セレン、 及びテルルのうちから 選ばれた少なくとも 1種以上の成分を元素^:で 0. 00001モル%〜7モル%の範囲含有 することを特徴とする項 557又は 558に記載されたいずれかの窒化ガリウムを主成分とす る焼結体。
項 560. 亜鉛、 カドミウム、 炭素、 珪素、 ゲルマニウム、 セレン、 及びテルルのうちから 選ばれた少なくとも 1種以上の成分を元素換算で 0. 00001モル%〜 5モル%の範囲含有 することを特徴とする項 557, 558又は 559に記載されたいずれかの窒化ガリウムを主 成分とする焼結体。
項 561. 亜鉛、 カドミウム、 炭素、 珪素、 ゲルマニウム、 セレン、 及びテルルのうちから 選ばれた少なくとも 1種以上の成分を元素 で 0. 00001モル%〜3モル%の範囲含有 することを難とする項 557、 558、 559又は 560に記載されたいずれかの窒化ガリ ゥムを主成分とする焼結体。
項 562. アルミニウム、 インジウム、 及び酸素のうちから選ばれた少なくとも 1種以上の 成分を含有することを特徴とする窒化ガリゥムを主成分とする焼結体。
項 563. アルミニウム、 インジウム、 及び酸素のうちから選ばれた少なくとも 1種以上の 成分を元素換算で 40モル%以下含有することを特徴とする項 532、 533、 534、 53
5、 536、 537、 538、 539、 540、 541、 542、 543、 544、 545、 546、 547、 548、 549、 550、 551、 552、 553、 554、 555、 55
6、 557、 558、 559、 560、 561又は 562に記載されたいずれかの窒化ガリウ ムを主成分とする焼結体。
項 564. 遷移金属のうちから選ばれた少なくとも 1種以上の成分を含有することを特徴と する窒化ガリゥムを主成分とする焼結体。
項 565. 遷移金属のうちから選ばれた少なくとも 1種以上の成分を元素換算で 10モル% 以下含有することを とする項 532、 533、 534、 535、 536、 537、 538、 539、 540、 541、 542、 543、 544、 545、 546、 547、 548、 54 9、 550、 551、 552、 553、 554, 555、 556、 557、 558、 559、 560、 561、 562、 563又は 564に記載されたいずれかの窒化ガリゥムを主成分と
する焼結体。
項 5 6 6. 遷移金属がマンガン、 コノルト、 ニッケル、 鉄、 クロム、 チタン、 モリブデン、 タングステン、 ニオブ、 タンタル、 バナジウムのうちから選ばれた少なくとも 1種以上である ことを特徴とする項 5 6 4又は 5 6 5に記載されたいずれかの窒化ガリウムを主成分とする焼 結体。
項 5 6 7. 金属ガリウムの直接窒化による窒化ガリウムを主成分とする粉末を原料として作 製されたものであることを特徴とする窒化ガリウムを主成分とする焼結体。
項 5 6 8. 酸化ガリウムの ¾¾窒化による窒化ガリウムを主成分とする粉末を原料として作 製されたものであることを特徴とする窒化ガリウムを主成分とする焼結体。
項 5 6 9. 気体状のガリウム化合物の窒化による窒化ガリウムを主成分とする粉末を原料と して作製されたものであることを特徴とする窒化ガリゥムを主成分とする焼結体。
項 5 7 0. 酸餘有量 1 0重量%以下の窒化ガリウムを主成分とする粉末を原料として作製 されたものであることを特徴とする窒化ガリウムを主成分とする焼結体。
項 5 7 1 . 平均樹圣 1 0 im以下の窒化ガリウムを主成分とする粉末を原料として作製され たものであることを特徴とする窒化ガリゥムを主成分とする焼結体。
項 5 7 2. 酸餘有量 1 0重量%以下の窒化ガリウムを主成分とする粉末。
項 5 7 3. 平均粒径 1 0; m以下の窒化ガリウムを主成分とする粉末。
項 5 7 4. 金属ガリウムと窒素含有物質とを窒化反応せしめることを i [とする窒化ガリウ ムを主成分とする粉末の製造方法。
項 5 7 5. 酸化ガリウムを 剤及び窒¾ 有物質とを用いて窒化反応せしめることを とする窒化ガリゥムを主成分とする粉末の製造方法。
項 5 7 6. 気体状のガリウム化合物を窒^有物質と窒化反応せしめることを特徴とする窒 化ガリゥムを主成分とする粉末の製造方法。
項 5 7 7. セラミック材料を主成分とする焼結体に窒化ガリゥム、 窒化インジウム、 窒化ァ ルミニゥムのうちから選ばれた少なくとも 1種以上を主成分とする単結晶薄膜が形成されてい ることを特徴とする薄膜基板。
項 5 7 8. 窒化ガリウム、 窒化インジウム、 窒化アルミニウムのうちから選ばれた少なくと も 1種以上を主成分とする薄膜を形成したセラミック材料を主成分とする焼結体に窒化ガリゥ ム、 窒化インジウム、 窒化アルミニウムのうちから選ばれた少なくとも 1種以上を主成分とす る単結晶薄膜が形成されていることを特徴とする項 5 7 7に記載された薄膜基板。
項 5 7 9. セラミック材料を主成分とする焼結体に形成された窒化ガリウム、 窒化インジゥ ム、 窒化アルミニゥムのうちから選ばれた少なくとも 1種以上を主成分とする薄膜が無定形、 多結晶、 配向性多結晶、 単結晶のうちから選ばれる少なくともいずれかの結晶状態を有するこ とを特徴とする項 5 7 8又は 5 7 9に記載されたいずれかの薄膜基板。
項 5 8 0. セラミック材料を主成分とする焼結体に形成された窒化ガリウム、 窒化インジゥ ム、 窒化アルミニウムのうちから選ばれた少なくとも 1種以上を主成分とする薄膜が少なくと も単結晶薄膜を有することを特徴とする項 5 7 8又は 5 7 9に記載されたいずれかの薄膜基板。 項 5 8 1 . セラミック材料を主成分とする焼結体に形成された窒化ガリウム、 窒化インジゥ ム、 窒化アルミニウムのうちから選ばれた少なくとも 1種以上を主成分とする薄膜が 1層から なることを特徴とする項 5 7 8、 5 7 9又は 5 8 0に記載されたいずれかの薄膜基板。
項 5 8 2. セラミック材料を主成分とする焼結体に形成された窒化ガリウム、 窒化インジゥ ム、 窒化アルミニウムのうちから選ばれた少なくとも 1種以上を主成分とする薄膜が少なくと も無定形であることを特徴とする項 5 8 1に記載された薄膜基板。
項 5 8 3. セラミック材料を主成分とする焼結体に形成された窒化ガリウム、 窒化インジゥ
ム、 窒化アルミニウムのうちから選ばれた少なくとも 1種以上を主成分とする薄膜が多結晶で あることを特徴とする項 5 8 1に記載された薄膜基板。
項 5 8 4. セラミック材料を主成分とする焼結体に形成された窒化ガリウム、 窒化インジゥ ム、 窒化アルミニウムのうちから選ばれた少なくとも 1種以上を主成分とする薄膜が 向性多 結晶であることを特徴とする項 5 8 1に記載された薄膜基板。
項 5 8 5. セラミック材料を主成分とする焼結体に形成された窒化ガリウム、 窒化インジゥ ム、 窒化アルミニウムのうちから選ばれた少なくとも 1種以上を主成分とする薄膜が単結晶で あることを特徴とする項 5 8 1に記載された薄膜基板。
項 5 8 6. セラミック材料を主成分とする焼結体に形成された窒化ガリウム、 窒化インジゥ ム、 窒化アルミニウムのうちから選ばれた少なくとも 1種以上を主成分とする薄膜が少なくと も 2以上の層からなることを特徴とする項 5 7 8、 5 7 9又は 5 8 0に記載されたいずれかの 項 5 8 7. セラミック材料を主成分とする焼結体に形成された窒化ガリウム、 窒化インジゥ ム、 窒化アルミニウムのうちから選ばれた少なくとも 1種以上を主成分とする薄膜が少なくと も 2以上の層からなり、 各層がそれぞれ無定形、 多結晶、 配向性多結晶、 単結晶のうちから選 ばれる少なくともいずれかの結晶状態を有することを特徴とする項 5 8 6に記載された薄膜基 板。
項 5 8 8. セラミック材料を主成分とする焼結体に形成された窒化ガリウム、 窒化インジゥ ム、 窒化アルミニウムのうちから選ばれた少なくとも 1種以上を主成分とする薄膜が少なくと も 2以上の層からなり、 該セラミック材料を主成分とする焼結体に直接形成された薄麵が無 定形、 多結晶、 配向性多結晶、 単結晶のうちから選ばれる少な'くともいずれかの結晶状態を有 することを特徴とする項 5 8 6又は 5 8 7に記載されたいずれかの薄膜基板。 ' 項 5 8 9. セラミック材料を主成分とする焼結体に形成された窒化ガリウム、 窒化インジゥ ム、 窒化アルミニウムのうちから選ばれた少なくとも 1種以上を主成分とする薄膜が少なくと も 2以上の層からなり、 該セラミック材料を主成分とする焼結体に直接形成された薄 が無 定形、 多結晶、 配向性多結晶のうちから選ばれる少なくともいずれかの結晶状態を有すること を特徴とする項 5 8 6、 5 8 7又は 5 8 8に記載されたいずれかの薄膜基板。
項 5 9 0. セラミック材料を主成分とする焼結体に形成された窒化ガリウム、 窒化インジゥ ム、 窒化アルミニウムのうちから選ばれた少なくとも 1種以上を主成分とする薄膜が少なくと も 2以上の層からなり、 該セラミック材料を主成分とする焼結体に直接形成された薄 が配 向性多結晶であることを ^とする項 5 8 6、 5 8 7、 5 8 8又は 5 8 9に記載されたいずれ かの薄膜基板。
項 5 9 1. セラミック材料を主成分とする能結体に形成された窒化ガリウム、 窒化インジゥ ム、 窒化アルミニゥムのうちから選ばれた少なくとも 1種以上を主成分とする薄膜が少なくと も 2以上の層からなり、 少なくとも 1層が単結晶であることを特徴とする項 5 8 6、 5 8 7、 5 8 8、 5 8 9又は 5 9 0に記載されたいずれかの薄膜基板。
項 5 9 2. セラミック材料を主成分とする焼結体に形成された窒化ガリウム、 窒化インジゥ ム、 窒化アルミニウムのうちから選ばれた少なくとも 1種以上を主成分とする薄膜が少なくと も 2以上の層からなり、 最上層の薄膜が単結晶であることを特徴とする項 5 8 6、 5 8 7、 5 8 8、 5 8 9、 5 9 0又は 5 9 1に記載されたいずれかの薄膜基板。
項 5 9 3. セラミック材料を主成分とする焼結体に形成された窒化ガリウム、 窒化インジゥ ム、 窒化アルミニウムのうちから選ばれた少なくとも 1種以上を主成分とする薄膜が少なくと も単結晶薄 を有し該単結晶薄 の厚みが 3 0 0 m未満であることを とする項 5 7 8、 5 7 9、 5 8 0、 5 8 1、 5 8 2、 5 8 3、 5 8 4, 5 8 5、 5 8 6、 5 8 7、 5 8 8、
589、 590、 591又は 592に記載されたいずれかの薄膜基板。
項 594. セラミック材料を主成分とする焼結体に形成された窒化ガリウム、 窒化インジゥ ム、 窒化アルミニウムのうちから選ばれた少なくとも 1種以上を主成分とする薄膜が少なくと も単結晶薄膜層を有し該単結晶薄膜層の厚みが 200 m以下であることを特徴とする項 59 3に記載された薄膜基板。
項 595. セラミック材料を主成分とする焼結体に形成された薄膜が少なくとも 0. lnm 以上の厚みを有することを特徴とする項 578、 579、 580、 581、 582、 583、 584、 585、 586、 587、 588、 589、 590、 591、 592、 593又は 5 94に記載されたいずれかの薄膜基板。
項 596. セラミック材料を主成分とする焼結体に形成された薄膜が少なくとも 0. 5nm 以上の厚みを有することを特徴とする項 595に記載された薄膜基板。
項 597. セラミツク材料を主成分とする焼結体に形成された薄膜が少なくとも 3 im 以上の厚みを有することを特徴とする項 595又は 596に記載されたいずれかの薄膜基板。 項 598. セラミック材料を主成分とする焼結体に形成された薄膜が少なくとも 3. bum 以上の厚みを有することを特徴とする項 595、 596又は 597に記載されたいずれかの薄 項 599. セラミツク材料を主成分とする焼結体に形成された薄膜が少なくとも 10 m以 上の厚みを有することを特徴とする項 595、 596、 597又は 598に記載されたいずれ かの薄膜基板。
項 600. セラミック材料を主成分とする炼結体に形成された薄膜が少なくとも 50 m以 上の厚みを有することを特徴とする項 595、 596、 597、 598又は 599記載された いずれかの薄膜基板。
項 601. セラミック材料を主成分とする焼結体に形成された薄膜が少なくとも窒化ガリウ ムを含有するものであることを特徴とする項 578、 579、 580、 581、 582、 58 3、 584, 585、 586、 587、 588、 589、 590、 591、 592、 593、 594、 595、 596、 597、 598、 599又は 600記載されたいずれかの薄膜基板。 項 602. セラミック材料を主成分とする焼結体に形成された薄膜が少なくとも窒化ガリウ ムを含むかあるいは窒化ガリウムを主成分とする薄膜を有することを特徴とする項 578, 5 79、 580、 581、 582、 583、 584、 585、 586、 587、 588、 589、 590、 591、 592、 593、 594、 595、 596、 597、 598、 599、 60 0又は 601記載されたいずれかの薄膜基板。
項 603. セラミック材料を主成分とする焼結体に形成された薄膜が窒化ガリウムを主成分 とするものであることを特徴とする項 601又は 602に記載されたいずれかの薄膜基板。 項 604. セラミック材料を主成分とする焼結体に形成された単結晶薄膜のミラ一指数 (0 02) の格子面の X線回折ロッキングカーブの半値幅が 3600秒以下であることを特徴とす る項 578、 579、 580、 581、 582、 583、 584、 585、 586、 587、 588、 589、 590、 591、 592、 593、 594, 595、 596、 597、 59 8、 599、 600、 601、 602又は 603に記載されたいずれかの薄膜基板。
項 605. セラミック材料を主成分とする焼結体に形成された単結晶薄膜のミラー指数 (0 02) の格子面の X線回折ロッキングカーブの半値幅が 300秒以下であることを特徴とする 項 604に記載された薄膜基板。
項 606. セラミック材料を主成分とする焼結体に形成された単結晶薄膜のミラー指数 (0 02) の格子面の X線回折ロッキングカーブの半値幅が 240秒以下であることを特徴とする 項 604又は 605に記載されたいずれかの薄膜基板。
項 607. セラミック材料を主成分とする焼結体に形成された単結晶薄膜のミラ一指数 (0 02) の格子面の X線回折ロッキング力一ブの半値幅が 200秒以下であることを特徴とする 項 604、 605又は 606に記載されたいずれかの薄膜基板。
項 608. セラミック材料を主成分とする焼結体に形成された単結晶薄膜のミラ一指数 (0 02) の格子面の X線回折ロッキングカーブの半値幅が 150秒以下であることを特徴とする 項 604、 605、 606又は 607に記載されたいずれかの薄膜基板。
項 609. セラミック材料を主成分とする焼結体に形成された単結晶薄膜のミラー指数 (0 02) の格子面の X線回折ロッキングカーブの半値幅が 130秒以下であることを特徴とする 項 604、 605、 606、 607又は 608に記載されたいずれかの薄膜基板。
項 610. セラミック材料を主成分とする焼結体に形成された単結晶薄膜のミラー指数 (0 02) の格子面の X線回折ロッキングカーブの半値幅が 100秒以下であることを特徴とする 項 604、 605、 606、 607、 608又は 609に記載されたいずれかの薄膜基板。 項 611. セラミック材料を主成分とする焼結体の平均表面粗さが R a 2000 nm以下で あることを體とする項 577、 578、 579、 580、 581、 582、 583、 584、 585、 586、 587、 588、 589、 590、 591、 592、 593、 594、 59
5、 596、 597、 598、 599、 600、 601、 602、 603、 604、 605、 606、 607、 608、 609又は 610に記載されたいずれかの薄膜基板。
項 612. セラミック材料を主成分とする焼結体の平均表面粗さが R a 1000 nm以下で あることを特徴とする項 611に記載された薄膜基板。
項 613. セラミツク材料を主成分とする焼結体の平均表面粗さが R a 100 nm以下であ ることを特徴とする項 611又は 612に記載されたいずれかの薄膜基板。
項 614. セラミツク材料を主成分とする焼結体の平均表面粗さが R a 20腿以下である ことを特徴とする項 611、 612又は 613に記載されたいずれかの薄膜基板。
項 615. セラミツク材料を主成分とする焼結体の平均表面粗さが R a 10 nm以下である ことを特徴とする項 611、 612、 613又ま 614に記載されたいずれかの薄膜基板。 項 616. セラミツク材料を主成分とする焼結体の平均表面粗さが R a 5 nm以下であるこ とを特徴とする項 611、 612、 613、 614又は 615に載されたいずれかの薄膜基板。 項 617. セラミック材料を主成分とする焼結体が表面粗さの大きいものであるごとを特徴 とする項 577、 578、 579、 580、 581、 582、 583、 584、 585、 58
6、 587、 588、 589、 590、 591、 592、 593、 594、 595、 596、 597、 598、 599、 600、 601、 602、 603、 604、 605、 606、 60
7、 608、 609、 610、 611、 612又は 613に記載されたいずれかの薄膜基板。 項 618. セラミック材料を主成分とする焼結体の平均表面粗さが R a 70 nm以上である ことを特徴とする項 577、 578、 579、 580、 581、 582、 583、 584、 5 85、 586、 587、 588、 589、 590、 591、 592, 593、 594, 595、 596、 597、 598、 599、 600、 601、 602、 603、 604、 605、 60 6、 607、 608、 609、 610、 611、 612、 613又は 617に記載されたいず れかの薄膜基板。
項 619. セラミック材料を主成分とする焼結体の平均表面粗さが R a 100 Onmより大 きいことを特徴とする項 618に記載された薄膜基板。
項 620. セラミック材料を主成分とする焼結体の平均表面粗さが R a 2000 nmより大 きいことを特徴とする項 618又は 619に記載されたいずれかの薄膜基板。
項 621. セラミック材料を主成分とする焼結体の表面が焼き放し (a s— f i r e)、 ラッ フ ¥F磨、 ブラスト研磨、 鏡面研磨、 化学腐食及びプラズマガスによる腐食のうちから選ばれた
少なくともいずれかの状態であることを赚とする項 5 7 7、 5 7 8、 5 7 9、 5 8 0、 5 8
1、 5 8 2、 5 8 3、 5 8 4, 5 8 5、 5 8 6、 5 8 7、 5 8 8、 5 8 9、 5 9 0、 5 9 1、
5 9 2、 5 9 3、 5 9 4、 5 9 5、 5 9 6、 5 9 7、 5 9 8、 5 9 9、 6 0 0、 6 0 1、 6 0
2、 6 0 3、 6 0 4、 6 0 5、 6 0 6、 6 0 7、 6 0 8、 6 0 9、 6 1 0、 6 1 1、 6 1 2、
6 1 3、 6 1 4、 6 1 5、 6 1 6、 6 1 7、 6 1 8、 6 1 9又は 6 2 0に記載されたいずれか 項 6 2 2. セラミック材料を主成分とする焼結体の表面が鏡面研磨された状態であることを 特徴とする項 6 2 1に記載された薄膜基板。
項 6 2 3. 光翻性を有するセラミック材料を主成分とする焼結体に窒化ガリウム、 窒化ィ ンジゥム、 窒化アルミニウムのうちから選ばれた少なくとも 1種以上を主成分とする薄膜が形 成されていることを特徴とする薄膜基板。
項 6 2 4. 窒化ガリゥム、 窒化ィンジゥム、 窒化アルミニゥムのうちから選ばれた少なくと も 1種以上を主成分とする薄膜が無定形、 多結晶、 配向性多結晶、 単結晶のうちから選ばれる 少なくともいずれかの結晶状態を有することを特徴とする項 6 2 3に記載された薄膜基板。 項 6 2 5. 窒化ガリゥム、 窒化ィンジゥム、 窒化アルミニゥムのうちから選ばれた少なくと も 1種以上を主成分とする薄膜が単結晶であることを特徴とする項 6 2 3又は 6 2 4に記載さ れたいずれかの薄膜基板。
項 6 2 6. 窒化ガリゥム、 窒化ィンジゥム、 窒化アルミニゥムのうちから選ばれた少なくと も 1種以上を主成分とする薄膜を形成した光透過性を有するセラミック材料を主成分とする焼 結体に窒化ガリウム、 窒化インジウム、 窒化アルミニウムのうちから選ばれた少なくとも 1種 以上を主成分とする薄膜が形成されていることを特徴とする項 6 2 3 , 6 2 4又は 6 2 5に記 載されたいずれかの薄膜基板。
項 6 2 7. 光¾¾性を有するセラミック材料を主成分とする焼結体に形成された窒化ガリゥ ム、 窒化インジウム、 窒化アルミニウムのうちから選ばれた少なくとも 1種以上を主成分とす る薄膜が無定形、 多結晶、 配向性多結晶、 単結晶のうちから選ばれる少なくともいずれかの結 晶状態を有することを特徴とする項 6 2 6に記載された薄膜基板。
項 6 2 8. 光 ¾i 性を有するセラミック材料を主成分とする焼結体に形成された窒化ガリウ ム、 窒化インジウム、 窒化アルミニウムのうちから選ばれた少なくとも 1種以上を主成分とす る薄膜の少なくとも一部が単結晶であることを特徴とする項 6 2 6又は 6 2 7に記載されたい ずれかの薄膜基板。
項 6 2 9. 光 ¾1性を有するセラミック材料を主成分とする焼結体に形成された窒化ガリウ ム、 窒化インジウム、 窒化アルミニウムのうちから選ばれた少なくとも 1種以上を主成分とす る薄膜が 1層からなることを特徴とする項 6 2 6、 6 2 7又は 6 2 8に記載されたいずれかの 項 6 3 0. 光 ¾ii性を有するセラミック材料を主成分とする焼結体に形成された窒化ガリウ ム、 窒化インジウム、 窒化アルミニウムのうちから選ばれた少なくとも 1種以上を主成分とす る薄膜が少なくとも無定形であることを特徴とする項 6 2 9に記載された薄膜基板。
項 6 3 1 . 光 ¾i性を有するセラミック材料を主成分とする焼結体に形成された窒化ガリウ ム、 窒化インジウム、 窒化アルミニウムのうちから選ばれた少なくとも 1種以上を主成分とす る薄膜が多結晶であることを特徴とする項 6 2 9に記載された薄膜基板。
項 6 3 2. 光 ¾ 性を有するセラミック材料を主成分とする焼結体に形成された窒化ガリウ ム、 窒化インジウム、 窒化アルミニウムのうちから選ばれた少なくとも 1種以上を主成分とす る薄膜が配向性多結晶であることを特徴とする項 6 2 9に記載された薄膜基板。
項 6 3 3. 光 ¾1性を有するセラミック材料を主成分とする焼結体に形成された窒化ガリウ
ム、 窒化インジウム、 窒化アルミニウムのうちから選ばれた少なくとも 1種以上を主成分とす る薄膜が単結晶であることを特徴とする項 6 2 9に記載された薄膜基板。
項 6 3 4. 性を有するセラミック材料を主成分とする焼結体に形成された窒化ガリウ ム、 窒化インジウム、 窒化アルミニウムのうちから選ばれた少なくとも 1種以上を主成分とす る薄膜が少なくとも 2以上の層からなることを特徴とする項 6 2 6 , 6 2 7又は 6 2 8に記載 されたいずれかの薄膜基板。
項 6 3 5. 光 ¾i性を有するセラミック材料を主成分とする焼結体に形成された窒化ガリウ ム、 窒化インジウム、 窒化アルミニウムのうちから選ばれた少なくとも 1種以上を主成分とす る薄膜が少なくとも 2以上の層からなり、 各層がそれぞれ無定形、 多結晶、 配向性多結晶、 単 結晶のうちから選ばれる少なくともいずれかの結晶状態を有することを特徴とする項 6 3 4に 記載された薄膜基板。
項 6 3 6. 光 ¾i性を有するセラミック材料を主成分とする焼結体に形成された窒化ガリウ ム、 窒化インジウム、 窒化アルミニウムのうちから選ばれた少なくとも 1種以上を主成分とす る薄膜が少なくとも 2以上の層からなり、 該¾¾1性を有するセラミック材料を主成分とする 焼結体に直接形成された薄翻が無定形、 多結晶、 配向性多結晶、 単結晶のうちから選ばれる 少なくともいずれかの結晶状態を有することを特徴とする項 6 3 4又は 6 3 5記載されたいず れかの薄膜基板。
項 6 3 7. 性を有するセラミック材料を主成分とする焼結体に形成された窒化ガリウ ム、 窒化インジウム、 窒化アルミニウムのうちから選ばれた少なくとも 1種以上を主成分とす る薄膜が少なくとも 2以上の層からなり、 性を有するセラミック材料を主成分とする 焼結体に直接形成された薄編が無定形、 多結晶、 配向性多結晶のうちから選ばれる少なくと もいずれかの結晶状態を有することを特徴とする項 6 3 4, 6 3 5又は 6 3 6に記載されたい ずれかの薄膜基板。
項 6 3 8. 光透過性を有するセラミック材料を主成分とする焼結体に形成された窒化ガリウ ム、 窒化インジウム、 窒化アルミニウムのうちから選ばれた少なくとも 1種以上を主成分とす る薄膜が少なくとも 2以上の層からなり、 該光透過性を有するセラミック材料を主成分とする 焼結体に直接形成された薄 SISが配向性多結晶であることを とする項 6 3 4、 6 3 5、 6 3 6又は 6 3 7に記載されたいずれかの薄膜基板。
項 6 3 9. 光 ¾M性を有するセラミック材料を主成分とする焼結体に形成された窒化ガリウ ム、 窒化インジウム、 窒化アルミニウムのうちから選ばれた少なくとも 1種以上を主成分とす る薄膜が少なくとも 2以上の層からなり、 少なくとも 1層が単結晶であることを特徴とする項
6 3 4、 6 3 5、 6 3 6、 6 3 7又は 6 3 8に記載されたいずれかの薄膜基板。
項 6 4 0. 光 性を有するセラミック材料を主成分とする焼結体に形成された窒化ガリウ ム、 窒化インジウム、 窒化アルミニウムのうちから選ばれた少なくとも 1種以上を主成分とす る薄膜が少なくとも 2以上の層からなり、 最上層の薄膜が単結晶であることを特徴とする項 6 3 4、 6 3 5、 6 3 6、 6 3 7、 6 3 8又は 6 3 9に記載されたいずれかの薄膜基板。
項 6 4 1. 光 ¾i性を有するセラミック材料を主成分とする焼結体に形成された窒化ガリウ ム、 窒化インジウム、 窒化アルミニウムのうちから選ばれた少なくとも 1種以上を主成分とす る薄膜が少なくとも単結晶薄膜層を有し該単結晶薄膜層の厚みが 3 0 0 m未満であることを 特徴とする項 6 2 6、 6 2 7、 6 2 8、 6 2 9、 6 3 0、 6 3 1、 6 3 2、 6 3 3、 6 3 4、
6 3 5、 6 3 6、 6 3 7、 6 3 8、 6 3 9又は 6 4 0に記載されたいずれかの薄膜基板。 項 6 4 2. 光 ¾i 性を有するセラミック材料を主成分とする焼結体に形成された窒化ガリウ ム、 窒化インジウム、 窒化アルミニウムのうちから選ばれた少なくとも 1種以上を主成分とす る薄膜が少なくとも単結晶薄膜層を有し該単結晶薄 の厚みが 2 0 0 m以下であることを
特徴とする項 641に記載された薄膜基板。
項 643. 光 ¾性を有するセラミック材料を主成分とする焼結体に形成された薄膜が少な くとも 0. lnm以上の厚みを有することを特徴とする項 626、 627、 628、 629、 630、 631、 632、 633、 634、 635、 636、 637、 638、 639、 64 0、 641又は 642に記載されたいずれかの薄膜基板。
項 644. ;)1^性を有するセラミック材料を主成分とする焼結体に形成された薄膜が少な くとも 0. 5 nm以上の厚みを有することを特徴とする項 643に記載された薄膜基板。 項 645. 光 ¾性を有するセラミック材料を主成分とする焼結体に形成された薄膜が少な くとも 0. 3 m以上の厚みを有することを特徴とする項 643又は 644に記載されたいず れかの薄膜基板。
項 646. 光 ¾i性を有するセラミック材料を主成分とする焼結体に形成された薄膜が少な くとも 3. 5 m以上の厚みを有することを特徴とする項 643、 644又は 645に記載さ れたいずれかの薄膜基板。
項 647. 光 ¾1性を有するセラミック材料を主成分とする焼結体に形成された薄膜が少な くとも 10 m以上の厚みを有することを特徴とする項 643、 644、 645又は 646に 記載されたいずれかの薄膜基板。
項 648. 光 ¾i性を有するセラミック材料を主成分とする焼結体に形成された薄膜が少な くとも 50 m以上の厚みを有することを特徴とする項 643、 644、 645、 646又は 647に記載されたいずれかの薄膜基板。
項 649. 光 ¾1性を有するセラミック材料を主成分とする焼結体に形成された薄膜が少な くとも窒化ガリウムを含有するものであることを赚とする項 626、 627、 628、 62 9、 630、 631、 632、 633、 634、 635、 636、 637、 638、 639、 640、 641、 642、 643、 644、 645、 646、 647又は 648に記載された いずれかの薄膜基板。
項 650. 光透過性を有するセラミック材料を主成分とする焼結体に形成された薄膜が少な くとも窒化ガリゥムを含むかあるいは窒化ガリゥムを主成分とする薄膜を有することを特徴と する項 626、 627、 628、 629、 630、 631、 632、 633、 634、 635、 636、 637、 638、 639、 640、 641、 642、 643、 644、 645、 64 6、 647、 648又は 649に記載されたいずれかの薄膜基板。
項 651. 光 ¾i性を有するセラミック材料を主成分とする焼結体に形成された薄膜が窒化 ガリウムを主成分とするものであることを特徴とする項 649又は 650に記載されたいずれ かの薄膜基板。
項 652. 光 ¾l 性を有するセラミック材料を主成分とする焼結体に形成された単結晶薄膜 のミラー指数 (002) の格子面の X線回折ロッキングカーブの半値幅が 3600秒以下であ ることを赚とする項 626、 627、 628、 629、 630、 631、 632、 633、 634、 635、 636、 637、 638、 639、 640、 641、 642、 643、 64 4、 645、 646、 647、 648、 649、 650又は 651に記載されたいずれかの薄 項 653. 光 ¾i性を有するセラミック材料を主成分とする焼結体に形成された単結晶薄膜 のミラ一指数 (002) の格子面の X線回折ロッキングカーブの半値幅が 300秒以下である ことを特徴とする項 652に記載された薄膜基板。
項 654. 光 ¾ 性を有するセラミック材料を主成分とする焼結体に形成された単結晶薄膜 のミラ一指数 (002) の格子面の X線回折ロッキングカーブの半値幅が 240秒以下である ことを特徴とする項 652又〖ま 653に記載されたいずれかの薄膜基板。
項 655. ¾¾1性を有するセラミック材料を主成分とする焼結体に形成された単結晶薄膜 のミラ一指数 (002) の格子面の X線回折ロッキングカーブの半値幅が 200秒以下である ことを特徴とする項 652、 653又は 654に記載されたいずれかの薄膜基板。
項 656. 光 ¾ii性を有するセラミック材料を主成分とする焼結体に形成された単結晶薄膜 のミラ一指数 (002) の格子面の X線回折ロッキングカーブの半値幅が 150秒以下である ことを特徴とする項 652、 653、 654又は 655に記載されたいずれかの薄膜基板。 項 657. 光 ¾1性を有するセラミック材料を主成分とする焼結体に形成された単結晶薄膜 のミラ一指数 (002) の格子面の X線回折ロッキングカーブの半値幅が 130秒以下である ことを特徴とする項 652、 653、 654、 655又は 656に記載されたいずれかの薄膜 板。
項 658. 光 ¾ii性を有するセラミック材料を主成分とする焼結体に形成された単結晶薄膜 のミラー指数 (002) の格子面の X線回折ロッキングカーブの半値幅が 100秒以下である ことを特徴とする項 652、 653、 654、 655、 656又は 657に記載されたいずれ かの薄膜基板。
項 659. 光透過性を有するセラミック材料を主成分とする焼結体の平均表面粗さが R a 2 00 Onm以下であることを ^[とする項 623、 624、 625、 626、 627、 628、 629、 630、 631、 632、 633、 634、 635、 636、 637、 638、 63 9、 640、 641、 642、 643、 644、 645、 646、 647、 648、 649、 650、 651、 652、 653、 654、 655、 656、 657又は 658に記載された いずれかの薄膜基板。
項 660. 光透過性を有するセラミック材料を主成分とする焼結体の平均表面粗さが R a 1 000 nm以下であることを特徴とする項 659に記載された薄膜基板。
項 661. 光透過性を有するセラミック材料を主成分とする焼結体の平均表面粗さが R a 1 00 nm以下であることを特徴とする項 659又は 660に記載されたいずれかの薄膜基板。 項 662. 光 ¾M性を有するセラミック材料を主成分とする焼結体の平均表面粗さが R a 2 0 nm以下であることを ^とする項 659、 660又は 661に記載されたいずれかの薄膜 項 663. 光 ¾i性を有するセラミック材料を主成分とする焼結体の平均表面粗さが R a 1 0 nm以下であることを特徴とする項 659、 660、 661又は 662に記載されたいずれ かの薄膜基板。
項 664. 光透過性を有するセラミック材料を主成分とする焼結体の平均表面粗さが R a 5 nm以下であることを特徴とする項 659、 660、 661、 662又は 663に記載された いずれかの薄膜基板。
項 665. 光透過性を有するセラミック材料を主成分とする焼結体が表面粗さの大きいもの であることを特徴とする項 623、 624、 625、 626、 627、 628、 629、 63
0、 631、 632、 633、 634、 635、 636、 637、 638、 639、 640、 641、 642、 643、 644、 645、 646、 647、 648、 649、 650、 65
1、 652、 653、 654、 655、 656、 657、 658、 659、 660又は 661 に記載されたいずれかの薄膜基板。
項 666. 光 性を有するセラミック材料を主成分とする焼結体の平均表面粗さが R a 7 Onm以上であることを特徴とする項 623、 624、 625、 626、 627、 628、 6 29、 630、 631、 632、 633、 634、 635、 636、 637、 638、 639、 640、 641、 642、 643、 644、 645、 646、 647、 648、 649、 65 0、 651、 652、 653、 654, 655、 656、 657、 658、 659、 660、
661又は 665に記載されたいずれかの薄膜基板。
項 667. 光 性を有するセラミック材料を主成分とする焼結体の平均表面粗さが R a 1 000 nmより大きいことを特徴とする項 666に記載された薄膜基板。
項 668. 光 性を有するセラミック材料を主成分とする焼結体の平均表面粗さが R a 2 000 nmより大きいことを特徴とする項 666又は 667に記載されたいずれかの薄膜基板。 項 669. 光»性を有するセラミック材料を主成分とする焼結体の表面が焼き放し (as -f i r e), ラップ研磨、 ブラス卜研磨、 鏡面研磨、 化学腐食及びプラズマガスによる腐食の うちから選ばれた少なくともいずれかの状態であることを特徴とする項 623、 624、 62
5、 626、 627、 628、 629、 630、 631、 632、 633、 634、 635、 636、 637、 638、 639、 640、 641、 642、 643、 644、 645、 64
6、 647、 648、 649、 650、 651、 652、 653、 654、 655、 656、 657、 658、 659、 660、 661、 662、 663、 664、 665、 667又は 6 68に記載されたいずれかの薄膜基板。
項 670. 光 ¾i性を有するセラミック材料を主成分とする焼結体の表面が鏡面研磨された 状態であることを特徴とする項 669に記載された薄膜基板。
項 671. セラミック材料を主成分とする焼結体あるいは ½¾i性を有するセラミック材料 を主成分とする焼結体が光 ¾ 率 1 %以上のものであることを特徴とする項 577、 578、
579、 580、 581、 582、 583、 584, 585、 586、 587、 588、 58 9、 590、 591、 592、 593、 594、 595、 596、 597、 598、 599、
600、 601、 602、 603、 604、 605、 606、 607、 608、 609、 61
0、 611、 612、 613、 614、 615、 616、 617、 618、 619、 620、 621、 622、 623、 624、 625、 626、 627、 628、 629、 630、 63
1、 632、 633、 634、 635、 636、 637、 638、 639、 640、 641、 642、 643、 644、 645、 646、 647、 648、 649、 650、 651、 65
2、 653、 654、 655、 656、 657、 658、 659、 660、 661、 662、 663、 664、 665、 667、 668、 669又は 670に記載されたいず、れかの薄膜基 板。
項 672. セラミック材料を主成分とする焼結体あるいは光 ¾ϋ性を有するセラミック材料 を主成分とする焼結体が光 ¾i率 10%以上のものであることを特徴とする項 671に記載さ れた薄膜基板。
項 673. セラミツク材料を主成分とする焼結体あるいは光 ¾性を有するセラミック材料 を主成分とする焼結体が光透過率 20%以上のものであることを特徴とする項 671又は 67 2に記載されたいずれかの薄膜基板。
項 δ 74. セラミック材料を主成分とする焼結体あるいは ½¾ 性を有するセラミック材料 を主成分とする焼結体が光 ¾Μ率 30 %以上のものであることを特徴とする項 671、 672 又は 673記載されたいずれかの薄膜基板。
項 675. セラミック材料を主成分とする焼結体あるいは 性を有するセラミック材料 を主成分とする焼結体が ¾¾ 率 40%以上のものであることを とする項 671、 672、 673又は 674に記載されたいずれかの薄膜基板。
項 676. セラミック材料を主成分とする焼結体あるいは^ §性を有するセラミック材料 を主成分とする炼結体が光 ¾1率 50%以上のものであることを特徴とする項 671、 672、 673、 674又は 675に記載されたいずれかの薄膜基板。
項 677. セラミック材料を主成分とする焼結体あるいは 性を有するセラミック材料 を主成分とする; ¾結体が光¾1率 60%以上のものであることを特徴とする項 671、 672、
673、 674、 675又は 676に記載されたいずれかの薄膜基板。
項 678. セラミック材料を主成分とする焼結体あるいは) fe¾M性を有するセラミック材料 を主成分とする能結体が ¾¾¾率 80%以上のものであることを籠とする項 671、 672、 673、 674、 675、 676又は 677に記載されたいずれかの薄膜基板。
項 679. セラミック材料を主成分とする焼結体あるいは ¾¾ 性を有するセラミック材料 を主成分とする焼結体が)1 έ¾Μ率 1 %未満のものであることを體とする項 577、 578、
579、 580、 581、 582、 583、 584, 585、 586、 587、 588、 58 9、 590、 591、 592、 593、 594、 595、 596、 597、 598、 599、
600、 601、 602、 603、 604、 605、 606、 607、 608、 609、 61
0、 611、 612、 613、 614、 615、 616、 617、 618、 619、 620、 621、 622、 623、 624、 625、 626、 627、 628、 629、 630、 63
1、 632、 633、 634、 635、 636、 637、 638、 639、 640、 641、 642、 643、 644、 645、 646、 647、 648、 649、 650、 651、 65
2、 653、 654, 655、 656、 657、 658、 659、 660、 661、 662, 663、 664、 665、 667、 668、 669又は 670に記載されたいずれかの薄膜基 板。
項 680. セラミック材料を主成分とする焼結体が光 ¾i率 0%であることを特徴とする項 679に記載された薄膜基板。
項 681. ^■ffi 性あるいは光 ¾i 率が少なくとも波長 200 nm〜800 nmの範囲の光 に対してのものであることを特徴とする項 623、 624、 625、 626、 627、 628、 629、 630、 631、 632、 633、 634、 635、 636、 637、 638、 63 9、 640、 641、 642、 643、 644、 645、 646、 647、 648、 649、 650、 651、 652、 653、 654、 655、 656、 657、 658、 659、 66 0、 661、 662、 663、 664、 665、 667、 668、 669、 670、 671、 672、 673、 674、 675、 676、 677、 678、 679又は 680に記載された いずれかの薄膜基板。
項 682. セラミツク材料を主成分とする能結体及び光透過性を有するセラミック材料を主 成分とする焼結体がそれぞれ窒化アルミニウムを主成分とする焼結体、 六方晶系又は三方晶系 のうちから選ばれた少なくともいずれかの結晶構造を有するセラミック材料を主成分とする焼 結体、 及び谢匕ジルコニウム、 酸化マグネシウム、 アルミン酸マグネシウム、 酸化チタン、 チ タン酸バリウム、チタン酸ジルコン麟、希土贩素酸化物、酸化トリウム、各種フェライト、 ムライト、 フォルステライト、 ステア夕イト、 結晶化ガラスのうちから選ばれた少なくとも 1 種以上を主成分とする焼結体、 のうちから選ばれた少なくともいずれかであることを,とす る項 577、 578、 579、 580、 581、 582、 583、 584、 585、 586、
587、 588、 589、 590、 591、 592、 593、 594、 595、 596、 59
7、 598、 599、 600、 601、 602、 603、 604, 605、 606、 607、
608、 609、 610、 611、 612、 613、 614、 615、 616、 617、 61
8、 619、 620、 621、 622、 623、 624、 625、 626、 627、 628、 629、 630、 631、 632、 633、 634、 635、 636、 637、 638、 63
9、 640、 641、 642、 643、 644、 645、 646、 647、 648、 649、 650、 651、 652、 653、 654, 655、 656、 657、 658、 659、 66 0、 661、 662、 663、 664、 665、 667、 668、 669、 670、 671、 672、 673、 674、 675、 676、 677、 678、 679、 680又は 681に記 載されたいずれかの薄膜基板。
項 683. 六方晶系又は三方晶系のうちから選ばれた少なくともいずれかの結晶構造を有す るセラミック材料を主成分とする焼結体が 化亜鉛、 酸化ベリリウム、 酸化アルミニウム、 炭 化珪素、 窒化珪素、 窒化ガリウムのうちから選ばれた少なくとも 1種以上を主成分とする焼結 体であることを特徴とする項 682に記載された薄膜基板。
項 684. セラミック材料を主成分とする焼結体及び 過性を有するセラミック材料を主 成分とする焼結体がそれぞれ窒化アルミニウム、 酸化菌、 酸化ベリリウム、 酸化アルミニゥ ム、 炭化珪素、 窒化珪素、 窒化ガリウム、 酸化ジルコニウム、 酸化マグネシウム、 アルミン酸 マグネシウム、 酸化イットリウムのうちから選ばれた少なくとも 1種以上を主成分とする焼結 体であることを特徴とする項 682又は 683に記載されたいずれかの薄膜基板。
項 685. 窒化アルミニウムを主成分とする焼結体に窒化ガリウム、 窒化インジウム、 窒化 アルミニウムのうちから選ばれた少なくとも 1種以上を主成分とする薄膜が形成されているこ とを特徴とする項 682又は 684に記載されたいずれかのい薄膜基板。
項 686. 窒化アルミニウムを主成分とする焼結体が基板状であることを特徴とする項 68 5に記載された薄膜基板。
項 687. 窒化ガリウム、 窒化インジウム、 窒化アルミニウムのうちから選ばれた少なくと も 1種以上を主成分とする薄膜が単結晶、 無定形、 多結晶、 配向性多結晶のうちから選ばれる 少なくともいずれかの結晶状態を有することを特徴とする項 685又は 686に記載されたい ずれかの薄膜基板。
項 688. 窒化ガリウム、 窒化インジウム、 窒化アルミニウムのうちから選ばれた少なくと も 1種以上を主成分とする薄膜の少なくとも一部が単結晶であることを特徴とする項 687に 記載された薄膜基板。
項 689. 窒化アルミニウムを主成分とする焼結体が ½ϋ過性を有することを特徵とする項 682、 684、 685、 686、 687又は 688に記載されたいずれかの薄膜基板。 項 690. 窒化アルミニウムを主成分とする焼結体の光透過率が 1 %以上であることを とする項 685、 686、 687、 688又は 689に記載されたいずれかの薄膜基板。 項 691. 窒化アルミニウムを主成分とする焼結体の光透過率が 5 %以上であることを とする項 690に記載された薄膜基板。
項 692. 窒化アルミニゥムを主成分とする焼結体の光透過率が 10 %以上であることを特 徴とする項 690又は 691に記載されたいずれかの薄膜基板。
項 693. 窒化アルミニウムを主成分とする焼結体の光透過率が 20 %以上であることを特 徵とする項 690、 691又は 692に記載されたいずれかの薄膜基板。
項 694. 窒化アルミ二ゥムを主成分とする焼結体の光透過率が 30 %以上であることを特 徵とする項 690、 691、 692又は 693に記載されたいずれかの薄膜基板。
項 695. 窒化アルミニウムを主成分とする焼結体の 3^過率が 40%以上であることを特 徵とする項 690、 691、 692、 693又は 694に記載されたいずれかの薄膜基板。 項 696. 窒化アルミ二ゥムを主成分とする焼結体の 率が 50 %以上であることを特 徴とする項 690、 691、 692、 693、 694又は 695に記載されたいずれかの薄膜 項 697. 窒化アルミ二ゥムを主成分とする焼結体の) ^過率が 60 %以上であることを特 徴とする項 690、 691、 692、 693、 6' 94、 695又は 696に記載されたいずれ かの薄膜基板。
項 698. 窒化アルミニウムを主成分とする焼結体の ½¾i率が 80%以上であることを特 徴とする項 690、 691、 692、 693、 694、 695、 696又は 697に記載され たいずれかの薄膜基板。
項 6 9 9. 窒化アルミニウムを主成分とする焼結体の 過率が 8 5 %以上であることを特 徴とする項 6 9 0、 6 9 1、 6 9 2、 6 9 3、 6 9 4、 6 9 5、 6 9 6、 6 9 7又は 6 9 8に 記載されたいずれかの薄膜基板。
項 7 0 0. 窒化アルミニウムを主成分とする焼結体に窒化ガリウム、 窒化インジウム、 窒化 アルミニウムのうちから選ばれた少なくとも 1種以上を主成分とする薄膜が形成されている薄 膜基板であって、 該窒化アルミニウムを主成分とする焼結体の ¾¾i率が 1 %未満であること を特徴とする項 6 8 5、 6 8 6、 6 8 7、 6 8 8又は 6 8 9に記載されたいずれかの薄膜基板。 項 7 0 1 . 窒化アルミニウムを主成分とする焼結体の 率が 0 %であることを特徴とす る項 7 0 0に記載された薄膜基板。
項 7 0 2. 光¾1性あるいは光 ¾i 率が少なくとも波長 2 0 0 nm〜8 0 0 nmの範囲の光 に対してのものであることを特徴とする項 6 8 9、 6 9 0、 6 9 1、 6 9 2、 6 9 3、 6 9 4、 6 9 5、 6 9 6、 6 9 7、 6 9 8、 6 9 9、 7 0 0又は 7 0 1に記載されたいずれかの薄膜基 板。
項 7 0 3. 窒化アルミニウムを主成分とする焼結体に窒化ガリウム、 窒化インジウム、 窒化 アルミニウムのうちから選ばれた少なくとも 1種以上を主成分とする薄膜が形成されている薄 膜基板であって、 MS化アルミニウムを主成分とする焼結体が窒化アルミニウムを 2 0f«% 以上含有するものであることを特徴とする項 6 8 5、 6 8 6、 6 8 7、 6 8 8、 6 8 9、 6 9 0、 6 9 1、 6 9 2、 6 9 3、 6 9 4、 6 9 5、 6 9 6、 6 9 7、 6 9 8、 6 9 9、 7 0 0、 7 0 1又は 7 0 2に記載されたいずれかの薄膜基板。
項 7 0 4. 窒化アルミニウムを主成分とする焼結体が窒化アルミニウムを 5 0髓%以上含 有するものであることを特徴とする項 7 0 3に記載された薄膜基板。
項 7 0 5. 窒化アルミニウムを主成分とする焼結体が希土默素あるいはアルカリ土類金属 のうちから選ばれた少なくとも 1種以上の成分を酸化物^:で 8 0体積%以下含有するもので あることを特徴とする項 7 0 3又は 7 0 4に記載されたいずれかの薄膜基板。
項 7 0 6. 窒化アルミニウムを主成分とする焼結体が希土類 J£素あるいはアルカリ土類金属 のうちから選ばれた少なくとも 1種以上の成分を酸化物^^で 5 0体積%以下含有するもので あることを特徴とする項 7 0 5に記載された薄膜基板。
項 7 0 7. 窒化アルミニウムを主成分とする焼結体が希土 素あるいはアルカリ土類金属 のうちから選ばれた少なくとも 1種以上の成分を酸化物,で 2 5#¾%以下含有するもので あることを特徴とする項 7 0 5又は 7 0 6に記載されたいずれかの薄膜基板。
項 7 0 8. 窒化アルミニウムを主成分とする焼結体が希土 素のうちから選ばれた少なく とも 1種以上の成分とアルカリ土類金属のうちから選ばれた少なくとも 1種以上の成分とを同 時に含有するものであることを特徴とする項 7 0 5 , 7 0 6又は 7 0 7に記載されたいずれか の薄膜基板。
項 7 0 9. 窒化アルミニウムを主成分とする焼結体がアルカリ金属あるいは珪素のうちから 選ばれた少なくとも 1種以上の成分を酸化物換算で 5 0 以下含有するものであることを 特徴とする項 7 0 3、 7 0 4、 7 0 5、 7 0 6、 7 0 7又は 7 0 8に記載されたいずれかの薄 項 7 1 0. 窒化アルミニウムを主成分とする焼結体がアルカリ金属あるいは珪素のうちから 選ばれた少なくとも 1種以上の成分を酸化物換算で 3 0体積%以下含有するものであることを 特徴とする項 7 0 9に記載された薄膜基板。
項 7 1 1 . 窒化アルミニウムを主成分とする焼結体がアルカリ金属あるいは珪素のうちから 選ばれた少なくとも 1種以上の成分を酸化物換算で 2 0体 以下含有するものであることを 特徴とする項 7 0 9又は 7 1 0に記載されたいずれかの薄膜基板。
項 712. 窒化アルミニウムを主成分とする焼結体がアルカリ金属あるいは珪素のうちから 選ばれた少なくとも 1種以上の成分を酸化物換算で 10体積%以下含有するものであることを 特徴とする項 709、 710又は 711に記載されたいずれかの薄膜基板。
項 713. 窒化アルミニウムを主成分とする焼結体がアルカリ金属あるいは珪素のうちから 選ばれた少なくとも 1種以上の成分を含み同時に希土類 素あるいはアルカリ土類金属のうち から選ばれた少なくとも 1種以上の成分を含有するものであることを とする項 705、 7 06、 707、 708、 709、 710、 711又は 712に記載されたいずれかの薄膜基板。 項 714. 窒化アルミニウムを主成分とする; ¾結体が Mo、 W、 V ひナジゥム)、 Nb、 T a、 T i、 力一ボンのうちから選ばれた少なくとも 1種以上の成分を元素換算で 80体積%以 下含有するものであることを特徴とする項 703、 704、 705、 706、 707、 708、 709、 710、 711、 712又は 713に記載されたいずれかの薄膜基板。
項 715. 窒化アルミニウムを主成分とする焼結体が Mo、 W、 V (バナジウム)、 Nb、 T a、 T i、 力一ボンのうちから選ばれた少なくとも 1種以上の成分を元素換算で 50#¾%以 下含有するものであることを特徴とする項 714に記載された薄膜基板。
項 716. 窒化アルミニウムを主成分とする焼結体が Mo、 W、 V、 Nb、 Ta、 Ti、 力 一ボンのうちから選ばれた少なくとも 1種以上を含む成分を元素 で 25#¾%以下含有す るものであることを特徴とする項 714又は 715に記載されたいずれかの薄膜基板。
項 717. 窒化アルミニウムを主成分とする焼結体が Mo、 W、 V、 Nb、 Ta、 Ti、 力 一ボンのうちから選ばれた少なくとも 1種以上の成分を含み同時に希土類 素あるいはアル力 リ土類金属のうちから選ばれた少なくとも 1種以上の成分を含有するものであることを特徴と する項 705、 706、 707、 708、 714、 715又は 716に記載されたいずれかの 項 718. 窒化アルミニウムを主成分とする焼結体が希土類 素及 D¾VIo、 W、 V (バナジ ゥム)、 Nb、 Ta、 Tii の遷移金属成分を元素 で 80重量%以下含有するものである ことを特徴とする項 703、 704、 705、 706、 707、 708、 709、 710、 7 11、 712、 713、 714、 715、 716又は 717に記載されたいずれかの薄膜基板。 項 719. 窒化アルミニウムを主成分とする焼結体が希土^ 5素及び Mo、 W、 V (バナジ ゥム)、 Nb、 Ta、 T i以外の遷移金属成分を元素換算で 50重量%以下含有するものである ことを特徴とする項 718に記載された薄膜基板。
項 720. 窒化アルミニウムを主成分とする焼結体が希土類 J£素及び Mo、 W、 V、 Nb、 Ta、 T i以外の遷移金属成分を 30重量%以下含有するものであることを特徴とする項 71 8又は 719に記載されたいずれかの薄膜基板。
項 721. 窒化アルミニウムを主成分とする焼結体が希土類 素及び Mo、 W、 V、 Nb、 Ta、 T i以外の遷移金属成分を含み同時に希土類 素あるいはアルカリ土類金属のうちから 選ばれた少なくとも 1種以上の成分を含有するものであることを,とする項 705、 706、 707、 708、 718、 719又は 720に記載されたいずれかの薄膜基板。
項 722. 希土 素及び o、 W、 V、 Nb、 Ta、 T i以外の遷移金属成分が鉄、 ニッ ゲル、 クロム、 マンガン、 ジルコニウム、 ハフニウム、 コバルト、 銅、 亜鉛のうちから選ばれ た少なくとも 1種以上であることを特徴とする項 718、 719、 720又は 721に記載さ れたいずれかの薄膜基板。
項 723. 窒化アルミニウムを主成分とする焼結体が ¾素を 30重量%以下含有するもので あることを ^とする項 703、 704、 705、 706、 707、 708、 709、 710、 711、 712、 713、 714、 715、 716、 717、 718、 719、 720、 72 1又は 722に記載されたいずれかの薄膜基板。
項 724. 窒化アルミニウムを主成分とする焼結体が 素を 25重量%以下含有するもので あることを特徴とする項 723に記載された薄膜基板。
項 725. 窒化アルミニウムを主成分とする焼結体が 素を 10重量%以下含有するもので あることを特徴とする項 723又は 724に記載されたいずれかの薄膜基板。
項 726. 窒化アルミニウムを主成分とする焼結体が ¾素を含み同時に希土類 素あるいは アルカリ土類金属のうちから選ばれた少なくとも 1種以上の成分を同時に含有するものである ことを特徴とする項 705、 706、 707、 708、 723、 724又は 725に記載され たいずれかの薄膜基板。
項 727. 窒化アルミニウムを主成分とする焼結体が ALONを 80%以下含有するもので あることを [とする項 703、 704、 705、 706、 707、 708、 709、 710、 711、 712、 713、 714、 715、 716、 717、 718、 719、 720、 72
1、 722、 723、 724、 725又は 726に記載されたいずれかの薄膜基板。
項 728. 窒化アルミ二ゥムを主成分とする焼結体が A L O Nを 50 %以下含有するもので あることを特徴とする項 727に記載された薄膜基板。
項 729. 窒化アルミニウムを主成分とする焼結体が ALONを 20%以下含有するもので あることを特徴とする項 727又は 728に記載されたいずれかの薄膜基板。
項 730. 窒化アルミニウムを主成分とする焼結体が AL ONを含み同時に希土類 素ある いはアルカリ土類金属のうちから選ばれた少なくとも 1種以上の成分を含有するものであるこ とを特徴とする項 705、 706、 707、 708、 727、 728又は 729に記載された いずれかの薄膜基板。
項 731. 窒化アルミニウムを主成分とする焼結体に窒化ガリウム、 窒化インジウム、 窒化 アルミニウムのうちから選ばれた少なくとも 1種以上を主成分とする薄膜が形成されている薄 膜基板であって、 該窒化アルミニウムを主成分とする焼結体の室温における熱伝導率が 50W ZmK以上であることを特徴とする項 685、 686、 687、 688、 689、 690、 6 91、 692、 693、 694、 695、 696、 697、 698、 699、 700、 701、 702、 703、 704、 705、 706、 707、 708、 709、 710、 711、 71
2、 713、 714、 715、 716、 717、 718、 719、 720、 721、 Ί 22、 723、 724、 725、 726、 727、 728、 729又は 730に記載されたいずれか 項 732. 窒化アルミニウムを主成分とする焼結体の室温における熱伝導率が 10 OW/m K以上であることを特徴とする項 731に記載された薄膜基板。
項 733. 窒化アルミニウムを主成分とする焼結体の室温における熱伝導率が 15 OW/m K以上であることを特徴とする項 731又は 732に記載されたいずれかの薄膜基板。
項 734. 窒化アルミニウムを主成分とする焼結体の室温における熱伝導率が 17 OW/m K以上であることを特徴とする項 731、 732又は 733に記載されたいずれかの薄膜基板。 項 735. 窒化アルミニウムを主成分とする焼結体が希土 素及びアルカリ土類金属のう ちから選ばれた少なくとも 1種以上の成分を元素換算で合計 0. 5重量%以下かつ酸素を 0. 9重量%以下含 #Tるものであることを ^[とする項 685、 686、 687、 688、 68 9、 690、 691、 692、 693、 694, 695、 696、 697、 698、 699、 700、 701、 702、 703、 704, 705、 706、 707、 708、 709、 71
0、 711、 712、 713、 714、 715、 716、 717、 718、 719、 720、 721、 722、 723、 724、 725、 726、 727、 728、 729、 730、 73
1、 732、 733又は 734に記載されたいずれかの薄膜基板。
項 736. 窒化アルミニウムを主成分とする焼結体が希土 H¾素及びアルカリ土類金属のう
ちから選ばれた少なくとも 1種以上の成分を元素^:で合計 0. 2重量%以下かつ酸素を 0. 5重量%以下含有するものであることを特徴とする項 735に記載された薄膜基板。
項 737. 窒化アルミニウムを主成分とする焼結体が希土類 素及びアルカリ土類金属のう ちから選ばれた少なくとも 1種以上の成分を元素 »で合計 0. 05重量%以下かつ酸素を 0. 2重量%以下含有するものであることを特徴とする項 735又は 736に記載されたいずれか 項 738. 窒化アルミニウムを主成分とする焼結体が希土類 素及びアルカリ土類金属のう ちから選ばれた少なくとも 1種以上の成分を元素 で合計 0. 02重量%以下かつ酸素を 0. 1重量%以下含有するものであることを特徴とする項 735、 736又は 737に記載された いずれかの薄膜基板。
項 739. 窒化アルミニウムを主成分とする焼結体が希土 ||¾素及びアルカリ土類金属のう ちから選ばれた少なくとも 1種以上の成分を元素 で合計 0. 005重量%以下かつ酸素を 0. 05重量%以下含有するものであることを とする項 735、 736、 737又は 73 8に記載されたいずれかの薄膜基板。
項 740. 窒化アルミニウムを主成分とする焼結体がアルカリ金属あるいは珪素のうちから 選ばれた少なくとも 1種以上の成分を元素換算で合計 0. 2重量%以下かつ酸素を 0. 9重量% 以下含有するものであることを體とする項 685、 686、 687、 688、 689、 69
0、 691、 692、 693、 694, 695、 696、 697、 698、 699、 700、 701、 702、 703、 704、 705、 706、 707、 708、 709、 710、 71
1、 712、 713、 714、 715, 716、 717、 718、 719、 720、 721、 722、 723、 724、 725、 726、 727、 728、 729、 730、 731、 73
2、 733、 734、 735、 736、 737、 738又は 739に記載されたいずれかの薄 項 741. 窒化アルミニウムを主成分とする焼結体が Mo、 W、 V ひナジゥム)、 Nb、 T a、 Ti、 カーボンのうちから選ばれた少なくとも 1種以上の成分を元素換算で合計 0. 2重 量%以下かつ酸素を 0. 9重量%以下含有するものであることを特徴とする項 685、 686、
687、 688、 689、 690、 691、 692、 693、 694、 695、 696、 69
7、 698、 699、 700、 701、 702、 703、 704, 705、 706、 707、
708、 709、 710、 711、 712、 713、 714、 715、 716、 717、 71
8、 719、 720、 721、 722、 723、 724、 725、 726、 727、 728、 729、 730、 731、 732、 733、 734、 735、 736、 737、 738、 73 9又は 740に記載されたいずれかの薄膜基板。
項 742. 窒化アルミニウムを主成分とする焼結体が F e、 N i、 Co、 Mnのうちから選 ばれた少なくとも 1種以上の成分を元素換算で合計 0. 2SI %以下かつ酸素を 0. 9重量% 以下含有するものであることを特徴とする項 685、 686、 687、 688、 689、 69
0、 691、 692、 693、 694, 695、 696、 697、 698、 699、 700、 701、 702、 703、 704、 705、 706、 707、 708、 709、 710、 71
1、 712、 713、 714、 715、 716、 717、 718、 719、 720、 721、 722、 723、 724、 725、 726、 727、 728、 729、 730、 731、 73
2、 733、 734、 735、 736、 737、 738、 739、 740又は 741に記載さ れたいずれかの薄膜基板。
項 743. 窒化アルミニウムを主成分とする焼結体が結晶相として A 1 Nを 95%以上含有 するものであることを特徴とする項 685、 686、 687、 688、 689、 690、 69 1、 692、 693、 694, 695、 696、 697、 698、 699、 700、 701、
702、 703、 704、 705、 706、 707、 708、 709、 710、 711、 71
2、 713、 714、 715、 716、 717、 718、 719、 720、 721、 722、 723、 724、 725、 726、 727、 728、 729、 730、 731、 732、 73
3、 734、 735、 736、 737、 738、 739、 740、 741又は 742に記載さ れたいずれかの薄膜基板。
項 744. 窒化アルミニウムを主成分とする焼結体が結晶相として A 1 Nを 98 %以上含有 するものであることを特徴とする項 743に記載された薄膜基板。
項 745. 窒化アルミニウムを主成分とする焼結体の結晶相が実質的に A 1 N単一相からな るものであることを赚とする項 685、 686、 687、 688、 689、 690、 691、
692、 693、 694, 695、 696、 697、 698、 699、 700、 701、 70
2、 703、 704、 705、 706、 707、 708、 709、 710、 711、 712、 713、 714、 715、 716、 717、 718、 719、 720、 721、 722、 72
3、 724、 725、 726、 727、 728、 729、 730、 731、 732、 733、
734、 735、 736、 737、 738、 739、 740、 741、 742、 743又は 7 44に記載されたいずれかの薄膜基板。
項 746. 窒化アルミニウムを主成分とする焼結体の室温における熱伝導率が 20 OWXm K以上であることを [とする項 685、 686、 687、 688、 689、 690、 691、
692、 693、 694, 695、 696、 697、 698、 699、 700、 701、 70
2、 703、 704、 705、 706、 707、 708、 709、 710、 711、 712、
713、 714、 715、 716、 717、 718、 719、 720、 721、 722、 72
3、 724、 725、 726、 727、 728、 729、 730、 731、 732、 733、 734、 735、 736、 737、 738、 739、 740、 741、 742、 743、 74 4又〖ま 745に記載されたいずれかの薄膜基板。
項 747. 窒ィ匕アルミニウムを主成分とする焼結体の室温における熱伝導率が 22 OW/m K以上であることを特徴とする項 746に記載された薄膜基板。
項 748· 窒化アルミニウムを主成分とする焼結体が相対密度 95 %以上のものであること を體とする項 685、 686、 687、 688、 689、 690、 691、 692、 693、
694, 695、 696、 697、 698、 699、 700、 701、 702、 703、 70
4、 705、 706、 707、 708、 709、 710、 711、 712、 713、 714、
715、 716、 717、 718、 719、 720、 721、 722、 723、 724、 72
5、 726、 727、 728、 729、 730、 731、 732、 733、 734、 735、 736、 737、 738、 739、 740、 741、 742、 743、 744、 745、 74 6又は 747に記載されたいずれかの薄膜基板。
項 749. 窒化アルミニウムを主成分とする焼結体が相対密度 98%以上のものであること を特徴とする項 748に記載された薄膜基板。
項 750. 窒化アルミニウムを主成分とする焼結体中の空孔が 1 m以下であることを M とする項 685、 686、 687、 688、 689、 690、 691、 692、 693、 69
4、 695、 696、 697、 698、 699、 700、 701、 702、 703、 704、 705、 706、 707、 708、 709、 710、 711、 712、 713、 714、 71
5、 716、 717、 718、 719、 720、 721、 722、 723、 724、 725、 726、 727、 728、 729、 730、 731、 732、 733、 734、 735、 73
6、 737、 738、 739、 740、 741、 742、 743、 744、 745、 746、 747、 748又は 749に記載されたいずれかの薄膜基板。
項 751. 窒化アルミニウムを主成分とする焼結体中の窒化アルミニウム粒子の大きさが平
均 1 m以上であることを體とする項 685、 686、 687、 688、 689、 690、 691、 692、 693、 694、 695、 696、 697、 698、 699、 700、 70
1、 702、 703、 704, 705、 706、 707、 708、 709、 710、 71 1、 712、 713、 714、 71 5、 716、 717、 718、 719、 720、 721、 72
2、 723、 724, 725、 726、 727> 728、 729、 730、 731、 732、 733、 734、 735、 736、 737、 738、 739、 740、 741、 742、 74
3、 744、 745、 746、 747、 748、 749又は 750に記載されたいずれかの薄 項 752. 窒化アルミニウムを主成分とする焼結体中の窒化アルミニウム粒子の大きさが平 均 5 m以上であることを特徴とする項 751に記載された薄膜基板。
項 753. 窒化アルミニウムを主成分とする焼結体中の窒化アルミニウム粒子の大きさが平 均 8 m以上であることを特徴とする項 751又は 752に記載されたいずれかの薄膜基板。 項 754. 窒化アルミニウムを主成分とする焼結体中の窒化アルミニウム粒子の大きさが平 均 15 m以上であることを特徴とする項 751, 752又は 753に記載されたいずれかの 項 755. 窒化アルミニウムを主成分とする焼結体中の窒化アルミニウム粒子の大きさが平 均 25 m以上であることを特徴とする項 751、 752、 753又は 754に記載されたい ずれかの薄膜基板。
項 756. 窒化アルミニウムを主成分とする焼結体中の窒化アルミニウム粒子の大きさが平 均 100 /xm以下であることを特徴とする項 685、 686、 687、 688、 689、 69
0、 69 1、 692、 693、 694、 695、 696、 697、 698、 699、 700、 701、 702、 703、 704、 705、 706、 707、 708、 709、 710、 7 1
1、 712、 713、 7 14、 715、 716、 71 7、 718、 719、 720、 721、 722、 723、 724、 725、 726、 727、 728、 729、 730、 731、 73
2、 733、 734、 735、 736、 737、 738、 739、 740、 741、 742、 743、 744、 745、 746、 747、 748、 749、 750、 751、 752、 75
3、 754又は 755に記載されたいずれかの薄膜基板。
項 757. 窒化アルミニウムを主成分とする焼結体の平均表面粗さが R a 2000 nm以下 であることを特徴とする項 685、 686、 687、 688、 689、 690、 69 1、 69
2、 693、 694, 695、 696、 697、 698、 699、 700、 701、 702、 703、 704、 705、 706、 707、 708、 709、 710、 71 1、 712、 7 1
3、 714、 7 15、 7 16、 717、 718、 7 1 9、 720、 721、 722、 723、 724, 725、 726、 727、 728、 729、 730、 731、 732、 733、 73
4、 735、 736、 737、 738、 739、 740、 741、 742、 743、 744、 745、 746、 747、 748、 749、 750、 751、 752、 753、 754、 75 5又は 756に記載されたいずれかの薄膜基板。
項 758. 窒化アルミニウムを主成分とする焼結体の平均表面粗さが R a 1000 nm以下 であることを特徴とする項 757に記載された薄膜基板。
項 759. 窒化アルミニウムを主成分とする焼結体の平均表面粗さが R a 100 nm以下で あることを特徴とする項 757又は 758に記載されたいずれかの薄膜基板。
項 760. 窒化アルミニウムを主成分とする焼結体の平均表面粗さが R a 50 nm以下であ ることを特徴とする項 757、 758又は 759に記載されたいずれかの薄膜基板。
項 761. 窒化アルミニウムを主成分とする焼結体の平均表面粗さが R a 20 nm以下であ ることを特徴とする項 757、 758、 759又は 760に記載されたいずれかの薄膜基板。
項 762. 表面粗さの大きい窒化アルミニウムを主成分とする焼結体からなることを特徴と する項 685、 686、 687、 688、 689、 690、 691、 692、 693、 694、
695、 696、 697、 698、 699、 700、 701、 702、 703、 704, 70
5、 706、 707、 708、 709、 710、 711、 712、 713、 714、 715、
716、 717、 718、 719、 720、 721、 722、 723、 724、 725、 72
6、 727、 728、 729、 730、 731、 732、 733、 734、 735、 736、 737、 738、 739、 740、 741、 742、 743、 744、 745、 746、 74
7、 748、 749、 750、 751、 752、 753、 754、 755、 756、 757、 758又は 759に記載されたいずれかの薄膜基板。
項 763. 窒化アルミニウムを主成分とする焼結体の平均表面粗さが R a 70 nm以上であ ることを體とする項 685、 686、 687、 688、 689、 690、 691、 692、
693、 694、 695、 696、 697、 698、 699、 700、 701、 702、 70
3、 704、 705、 706、 707、 708、 709、 710、 711、 712、 713、
714、 715、 716、 717、 718、 719、 720、 721、 722、 723、 72
4、 725、 726、 727、 728、 729、 730、 731、 732、 733、 734、 735、 736、 737、 738、 739、 740、 741、 742、 743、 744、 74
5、 746、 747、 748、 749、 750、 751、 752、 753、 754、 755、 756、 757、 758、 759又は 762に記載されたいずれかの薄膜基板。
項 764. 窒化アルミニウムを主成分とする焼結体の平均表面粗さが R a 1000 nmより 大きいことを特徴とする項 763に記載された薄膜基板。
項 765. 窒化アルミニウムを主成分とする焼結体の平均表面粗さが R a 2000 nmより 大きいことを特徴とする項 763又は 764に記載された薄膜基板。
項 766. 窒化アルミニウムを主成分とする焼結体の表面が焼き放し (a s _ f i r e)、 ラ ッフ ¾ff磨、 ブラスト研磨、 鏡面研磨、 化学腐食及びプラズマガスによる腐食のうちから選ばれ た少なくともいずれかの状態であることを とする項 685、 686、 687、 688、 6 89、 690、 691、 692、 693、 694、 695、 696、 697、 698、 699、 700、 701、 702、 703、 704、 705、 706、 707、 708、 709、 71
0、 711、 712、 713、 714、 715、 716、 717、 718、 719、 720、 721、 722、 723、 724、 725、 726、 727、 728、 729、 730、 73
1、 732、 733、 734、 735、 736、 737、 738、 739、 740、 741、 742、 743、 744、 745、 746、 747、 748、 749、 750、 751、 75
2、 753、 754、 755、 756、 757、 758、 759、 760、 761、 762、 763、 764又は 765に記載されたいずれかの薄膜基板。
項 767. 窒化アルミニウムを主成分とする焼結体の表面が鏡面研磨された状態であること を特徴とする項 766に記載された薄膜基板。
項 768. 窒化アルミニウムを主成分とする焼結体に窒化ガリウム、 窒化インジウム、 窒化 アルミニウムのうちから選ばれた少なくとも 1種以上を主成分とする薄膜が形成されている薄 膜基板であって、 化アルミニウムを主成分とする焼結体の厚みが 8ノ 0mm以下であるこ とを特徴とする項 685、 686、 687、 688、 689、 690、 691、 692、 69
3、 694, 695、 696、 697、 698、 699、 700、 701、 702、 703、 704、 705、 706、 707、 708、 709、 710、 711、 712、 713、 71
4、 715、 716、 717、 718、 719、 720、 721、 722、 723、 724、 725、 726、 727、 728、 729、 730、 731、 732、 733、 734、 73
5、 736、 737、 738、 739、 740、 741、 742、 743、 744、 745、
746、 747、 748、 749、 750、 751、 752、 753、 754、 755、 75 6、 757、 758、 759、 760、 761、 762、 763、 764又は 765に記載さ れたいずれかの薄膜基板。
項 769. 窒化アルミ二ゥムを主成分とする焼結体の厚みが 5. 0 mm以下であることを特 徴とする項 768に記載された薄膜基板。
項 770. 窒化アルミニウムを主成分とする焼結体の厚みが 2. 5mm以下であることを特 徴とする項 768又は 769に記載されたいずれかの薄膜基板。
項 771. 窒化アルミニウムを主成分とする焼結体の厚みが 1. 0mm以下であることを特 徴とする項 768、 769又は 770に記載されたいずれかの薄膜基板。
項 772. 窒化アルミニウムを主成分とする焼結体に窒化ガリウム、 窒化インジウム、 窒化 アルミニウムのうちから選ばれた少なくとも 1種以上を主成分とする薄膜が形成されている薄 膜基板であって、 ¾化アルミニウムを主成分とする焼結体の厚みが 0. 01mm以上である ことを特徴とする項 685、 686、 687、 688、 689, 690、 691、 692、 6 93、 694、 695、 696、 697、 698、 699、 700、 701、 702、 703、 704、 705、 706、 707、 708、 709、 710、 711、 712、 713、 71
4、 715、 716、 717、 718、 719、 720、 721、 722、 723、 724、 725、 726、 727、 728、 729、 730、 731、 732、 733、 734、 73
5、 736、 737、 738、 739、 740、 741、 742、 743、 744、 745、 746、 747、 748、 749、 750、 751、 752、 753、 754、 755、 75
6、 757、 758、 759、 760、 761、 762、 763、 764、 765、 766、 767、 768、 769、 770又は 771に記載されたいずれかの薄膜基板。
項 773. 窒化アルミニウムを主成分とする焼結体の厚みが 0. 02mm以上であることを 特徴とする項 772に記載された薄膜基板。
項 774. 窒化アルミニウムを主成分とする焼結体の厚みが 0. 05mm以上であることを 特徴とする項 772又は 773に記載されたいずれかの薄膜基板。
項 775. 窒化アルミニウムを主成分とする焼結体の厚みが 8. 0mm以下でありかつ遞 過率が 1%以上であることを特徴とする項 768、 769、 770、 771、 772、 773 又は 774に記載されたいずれかの薄膜基板。
項 776. 窒化アルミニウムを主成分とする焼結体の厚みが 0. 01mm以上でありかつ光 率が 40%以上であることを特徴とする項 768、 769、 770、 771、 772、 7 73、 774又は 775に記載されたいずれかの薄膜基板。
項 777. 窒化アルミニウムを主成分とする焼結体に窒化ガリウム、 窒化インジウム、 窒化 アルミニウムのうちから選ばれた少なくとも 1種以上を主成分とする薄膜が形成されている薄 膜基板であって、 該窒化アルミニウムを主成分とする焼結体は導通ビアを有するものであるこ とを體とする項 685、 686、 687、 688、 689、 690、 691、 692、 69
3、 694, 695、 696、 697、 698、 699、 700、 701、 702、 703、 704、 705、 706、 707、 708、 709、 710、 711、 712、 713、 71
4、 715、 716、 717、 718、 719、 720、 721、 722、 723、 724、 725、 726、 727、 728、 729、 730、 731、 732、 733、 734. 73
5、 736、 737、 738、 739、 740、 741、 742、 743、 744、 745、 746、 747、 748、 749、 750、 751、 752、 753、 754、 755、 75
6、 757、 758、 759、 760、 761、 762、 763、 764、 765、 766、 767、 7.68、 769、 770、 771、 772, 773, 774、 775又は 776に記 載されたいずれかの薄膜基板。
項 7 7 8. 窒化アルミニウムを主成分とする焼結体に窒化ガリウム、 窒化インジウム、 窒化 アルミニウムのうちから選ばれた少なくとも 1種以上を主成分とする薄膜が形成されている薄 膜基板であって、 窒化アルミニウムを主成分とする焼結体 板状でありかつ導通ビアを有す ることを特徴とする項 7 7 7に記載された薄膜基板。
項 7 7 9. 導通ビア 板の上下表面を電気的に接続するよう窒化アルミニウムを主成分と する焼結体に形成されていることを特徴とする項 7 7 7又は 7 7 8に記載されたいずれかの薄 項 7 8 0. 導通ビアが金、 銀、 銅、 アルミニウム、 鉄、 コバルト、 ニッケル、 ルテニウム、 ロジウム、 八"ラジウム、 オスミウム、 イリジウム、 白金、 モリブデン、 タングステン、 クロム、 チタン、 窒化チタン、 窒化ジルコニウムのうちから選ばれた少なくとも 1種以上を主成分とす る材料からなることを特徴とする項 7 7 7 , 7 7 8又は 7 7 9に記載された薄膜基板。
項 7 8 1 . 導通ビアが金、 銀、 銅、 アルミニウム、 鉄、 コバルト、 ニッケル、 ルテニウム、 ロジウム、 パラジウム、 オスミウム、 イリジウム、 白金、 モリブデン、 タングステン、 クロム、 チタン、窒化チタン、窒化ジルコニウムのうちから選ばれた少なくとも 1種以上を主成分とし、 さらに窒化アルミニウム、 炭化珪素、 窒化珪素、 窒化ガリウム、 酸化亜鉛、 酸化ベリリウム、 酸化アルミニウム、 希土贩素化合物、 アルカリ土類金属化合物のうちから選ばれた少なくと も 1種以上の材料を含有することを特徴とする項 7 8 0に記載された薄膜基板。
項 7 8 2. 導通ビアがモリブデン、 タングステン、 銅、 窒化チタン、 窒化ジルコニウムのう ちから選ばれた少なくとも 1種以上を主成分とする材料からなることを とする項 5 2 5又 は 7 8 1に記載されたいずれかの薄膜基板。
項 7 8 3. 導通ビアがモリブデン、 タングステン、 銅、 窒化チタン、 窒化ジルコニウムのう ちから選ばれた少なくとも 1種以上を主成分とし、 さらに窒化アルミニウム、 酸化アルミニゥ ム、 希土類 素化合物、 アルカリ土類金属化合物のうちから選ばれた少なくとも 1種以上の成 分を含有するものであることを特徴とする項 7 8 0 , 7 8 1又は 7 8 2に記載されたいずれか 項 7 8 4. 導通ビアが室温における抵抗率 1 X 1 0一3 Ω · c m以下の導電性材料からなるこ とを特徴とする項 7 7 7、 7 7 8、 7 7 9、 7 8 0、 7 8 1、 7 8 2又は 7 8 3に記載された 項 7 8 5. 導通ビアが室温における抵抗率 1 X 1 0— 4Ω · c m以下の導電性材料からなるこ とを特徴とする項 7 8 4に記載された薄膜基板。
項 7 8 6. 導通ビアが室温における抵抗率 1 X 1 0 _5 Ω · c m以下の導電性材料からなるこ とを特徴とする項 7 8 4又は 7 8 5に記載されたいずれかの薄膜基板。
項 7 8 7. 導通ビアの大きさが 5 0 0 m以下であることを特徴とする項 7 7 7、 7 7 8、 7 7 9、 7 8 0、 7 8 1、 7 8 2、 7 8 3、 7 8 4、 7 8 5又は 7 8 6に記載された薄膜基板。 項 7 8 8. 導通ビアの大きさが 2 5 0 m以下であることを特徴とする項 7 8 7に記載され 項 7 8 9. 導通ビアの大きさが 1 0 0 m以下であることを特徴とする項 7 8 7又は 7 8 8 に記載されたいずれかの薄膜基板。
項 7 9 0. 導通ビアの大きさが 5 0 m以下であることを [とする項 7 8 7、 7 8 8又は
7 8 9に記載されたいずれかの薄膜基板。
項 7 9 1 . 導通ビアの大きさが 2 5 m以下であることを赚とする項 7 8 7、 7 8 8、 7
8 9又は 7 9 0に記載されたいずれかの薄膜基板。
項 7 9 2. 導通ビアの大きさが 1 m以上であることを特徴とする項 7 7 7、 7 7 8、 7 7 9、 7 8 0、 7 8 1、 7 8 2、 7 8 3、 7 8 4 , 7 8 5、 7 8 6、 7 8 7、 7 8 8、 7 8 9、
790又は 791に記載されたいずれかの薄膜基板。
項 793. 薄膜が導通ビアの表面に形成されていることを とする項 777、 778、 7 79、 780、 781、 782、 783、 784、 785、 786、 787、 788、 789、 790、 791又は 792に記載されたいずれかの薄膜基板。
項 794. 窒化アルミニウムを主成分とする焼結体に窒化ガリウム、 窒化インジウム、 窒化 アルミニウムのうちから選ばれた少なくとも 1種以上を主成分とする薄膜が形成されている薄 膜基板であって、 該窒化アルミニウムを主成分とする焼結体に薄騰電性材料が形成されてい ることを iff ^とする項 685、 686、 687、 688、 689、 690、 691、 692、
693、 694、 695、 696、 697、 698、 699、 700、 701、 702、 70
3、 704, 705、 706、 707、 708、 709、 710、 711、 712、 713、
714、 715、 716、 717、 718、 719、 720、 721、 722、 723、 72
4、 725、 726、 727、 728、 729、 730、 731、 732、 733、 734、 735、 736、 737、 738、 739、 740、 741、 742、 743、 744、 74
5、 746、 747、 748、 749、 750、 751、 752、 753、 754、 755、 756、 757、 758、 759、 760、 761、 762、 763、 764、 765、 76
6、 767、 768、 769、 770、 771、 772、 773、 774, 775、 776、 777、 778、 779、 780、 781、 782、 783、 784、 785、 786、 78
7、 788、 789、 790、 791、 792又は 793に記載されたいずれかの薄膜基板。 項 795. 薄騰電性材料が窒化アルミニウムを主成分とする焼結体の少なくとも表面に形 成されていることを特徴とする項 794に記載された薄膜基板。
項 796. 窒化アルミニウムを主成分とする焼結体に窒化ガリウム、 窒化インジウム、 窒化 アルミニウムのうちから選ばれた少なくとも 1種以上を主成分とする薄膜が形成されている薄 膜基板であって、 該薄膜の表面及び/又は内部に薄膜導電性材料が形成されていることを特徴 とする項 685、 686、 687、 688、 689、 690、 691、 692、 693、 69
4、 695、 696、 697、 698、 699、 700、 701、 702、 703、 704、 705、 706、 707、 708、 709、 710、 711、 712、 713、 714、 71
5、 716、 717、 718、 719、 720、 721、 722、 723、 724、 725、 726、 727、 728、 729、 730、 731、 732、 733、 734、 735、 73
6、 737、 738、 739、 740、 741、 742、 743、 744、 745、 746、 747、 748、 749、 750、 751、 752、 753、 754、 755、 756、 75
7、 758、 759、 760、 761、 762、 763、 764, 765、 766、 767、 768、 769、 770、 771、 772、 773、 774, 775、 776、 777、 77
8、 779、 780、 781、 782、 783、 784, 785、 786、 787、 788、 789、 790、 791、 792、 793、 794又は 795に記載されたいずれかの薄膜基 板。
項 797. 窒化アルミニウムを主成分とする焼結体に窒化ガリウム、 窒化インジウム、 窒化 アルミニウムのうちから選ばれた少なくとも 1種以上を主成分とする薄膜が形成された薄膜基 板であって、 窒化アルミニウムを主成分とする焼結体に薄膜導電性材料が形成され、 さらに窒 化ガリウム、 窒化インジウム、 窒化アルミニウムのうちから選ばれた少なくとも 1種以上を主 成分とする薄膜の表面及び Z又は内部に薄 電性材料が形成されていることを特徴とする項 794、 795又は 796に記載されたいずれかの薄膜基板。
項 798. 薄膜導電性材料が金属、 合金、 金属窒化物のうちから選ばれた少なくとも 1種以 上の材料からなることを特徴とする項 794、 795、 796又は 797に記載されたいずれ かの薄膜基板。
項 799. 薄騰電性材料が金、 銀、 銅、 アルミニウム、 鉄、 コバルト、 ニッケル、 ルテニ ゥム、 ロジウム、 パラジウム、 オスミウム、 イリジウム、 白金、 タンタル、 モリブデン、 タン ダステン、 クロム、 チタン、 ニッケル一クロム合金、 窒化チタン、 窒化ジルコニウム、 窒化夕 ンタル、 のうちから選ばれた少なくとも 1種以上を主成分とする材料からなることを特徴とす る項 794、 795、 796、 797又は 798に記載されたいずれかの薄膜基板。
項 800. 薄 電性材料が少なくとも 2以上の層で構成されていることを特徴とする項 7 94、 795、 796、 797、 798又は 799に記載されたいずれかの薄膜基板。
項 801.薄麟電性材料の厚みが 20 m以下であることを特徴とする項 794、 795、 796、 797、 798、 799又は 800に記載されたいずれかの薄膜基板。
項 802. 薄麟電性材料と窒化ガリウム、 窒化インジウム、 窒化アルミニウムのうちから 選ばれた少なくとも 1種以上を主成分とする薄膜との接合強度が 2 K gZmm2以上であるこ とを特徴とする項 794、 795、 796、 797、 798、 799、 800又は 801に記 載されたいずれかの薄膜基板。
項 803. 六方晶系又は三方晶系のうちから選ばれた少なくともいずれかの結晶構造を有す るセラミック材料を主成分とする焼結体に窒化ガリウム、 窒化インジウム、 窒化アルミニウム のうちから選ばれた少なくとも 1種以上を主成分とする薄膜が形成されていることを,とす る項 682、 683又は 684に記載されたいずれかの薄膜基板。
項 804. 六方晶系又は三方晶系のうちから選ばれた少なくともいずれかの結晶構造を有す るセラミック材料を主成分とする焼結体が基板状であることを特徴とする項 803に記載され 項 805. 窒化ガリゥム、 窒化ィンジゥム、 窒化アルミニゥムのうちから選ばれた少なくと も 1種以上を主成分とする薄膜が単結晶、 無定形、 多結晶、 配向性多結晶のうちから選ばれる 少なくともいずれかの結晶状態を有することを特徴とする項 803又は 804に記載されたい ずれかの薄膜基板。
項 806. 窒化ガリゥム、 窒化ィンジゥム、 窒化アルミニゥムのうちから選ばれた少なくと も 1種以上を主成分とする薄膜の少なくとも一部が単結晶であることを特徴とする項 805に 記載された薄膜基板。
項 807. 六方晶系又は三方晶系のうちから選ばれた少なくともいずれかの結晶構造を有す るセラミック材料を主成分とする焼結体が光透過性を有することを特徴とする項 682, 68
3、 684、 803、 804、 805又は 806に記載されたいずれかの薄膜基板。
項 808. 六方晶系又は三方晶系のうちから選ばれた少なくともいずれかの結晶構造を有す るセラミツク材料を主成分とする焼結体の)16¾ϋ率が 1 %以上であることを特徴とする項 80 3、 804、 805、 806又は 807に記載されたいずれかの薄膜基板。
項 809. 六方晶系又は三方晶系のうちから選ばれた少なくともいずれかの結晶構造を有す るセラミツク材料を主成分とする焼結体の 過率が 5 %以上であることを特徴とする項 80 8に記載された薄膜基板。
項 810. 六方晶系又は三方晶系のうちから選ばれた少なくともいずれかの結晶構造を有す るセラミツク材料を主成分とする焼結体の 過率が 10 %以上であることを,とする項 8 08又は 809に記載されたいずれかの薄膜基板。
項 811. 六方晶系又は三方晶系のうちから選ばれた少なくともいずれかの結晶構造を有す るセラミック材料を主成分とする焼結体の) 率が 20 %以上であることを特徴とする項 8 08、 809又は 810に記載されたいずれかの薄膜基板。
項 81.2. 六方晶系又は三方晶系のうちから選ばれた少なくともいずれかの結晶構造を有す るセラミック材料を主成分とする焼結体の ¾¾1率が 30 %以上であることを特徴とする項 8
08、 809、 810又は 811に記載されたいずれかの薄膜基板。
項 813. 六方晶系又は三方晶系のうちから選ばれた少なくともいずれかの結晶構造を有す るセラミツク材料を主成分とする焼結体の ¾¾ 率が 40 %以上であることを特徴とする項 8 08、 809、 810、 811又は 812に記載されたいずれかの薄膜基板。
項 814. 六方晶系又は三方晶系のうちから選ばれた少なくともいずれかの結晶構造を有す るセラミック材料を主成分とする焼結体の ¾¾i率が 50 %以上であることを特徴とする項 8 08、 809、 810、 811、 812又は 813に記載されたいずれかの薄膜基板。
項 815. 六方晶系又は三方晶系のうちから選ばれた少なくともいずれかの結晶構造を有す るセラミック材料を主成分とする焼結体の 率が 60 %以上であることを特徴とする項 8 08、 809、 810、 811、 812、 813又は 814に記載されたいずれかの薄膜基板。 項 816. 六方晶系又 方晶系のうちから選ばれた少なくともいずれかの結晶構造を有す るセラミツク材料を主成分とする焼結体の 過率が 80 %以上であることを特徴とする項 8 08、 809、 810、 811、 812、 813、 814又は 815に記載されたいずれかの 項 817. 六方晶系又は三方晶系のうちから選ばれた少なくともいずれかの結晶構造を有す るセラミック材料を主成分とする焼結体の ½¾ 率が 85 %以上であることを特徴とする項 8 08、 809、 810、 811、 812、 813、 814、 815又は 816に記載されたい ずれかの薄膜基板。
項 818. 六方晶系又は三方晶系のうちから選ばれた少なくともいずれかの結晶構造を有す るセラミック材料を主成分とする焼結体に窒化ガリウム、 窒化インジウム、 窒化アルミニウム のうちから選ばれた少なくとも 1種以上を主成分とする薄膜が形成されている薄膜基板であつ て、 該六方晶系又は三方晶系のうちから選ばれた少なくともいずれかの結晶構造を有するセラ ミック材料を主成分とする焼結体の光 ¾i率が 1 %未満であることを特徴とする項 803、 8 04、 805、 806又は 807に記載されたいずれかの薄膜基板。
項 819. 六方晶系又は三方晶系のうちから選ばれた少なくともいずれかの結晶構造を有す るセラミック材料を主成分とする焼結体の ¾S過率が 0%であることを特徴とする項 818に 記載された薄膜基板。
項 820. 光透過性あるいは光透過率が少なくとも波長 200 nm〜800 nmの範囲の光 に対してのものであることを特徴とする項 807、 808、 809、 810、 811、 812、 813、 814、 815、 816、 817、 818又は 819に記載されたいずれかの薄膜基 板。
項 821. 六方晶系又は三方晶系のうちから選ばれた少なくともいずれかの結晶構造を有す るセラミック材料を主成分とする焼結体の平均表面粗さが R a 1000 nm以下であることを 特徴とする項 803、 804、 805、 806、 807、 808、 809、 810、 811、 812、 813、 814、 815、 816、 817、 818、 819又は 820に記載された いずれかの薄膜基板。
項 822. 六方晶系又は三方晶系のうちから選ばれた少なくともいずれかの結晶構造を有す るセラミック材料を主成分とする焼結体の平均表面粗さが R a 10 Onm以下であることを特 徴とする項 821に記載された薄膜基板。
項 823. 六方晶系又は三方晶系のうちから選ばれた少なくともいずれかの結晶構造を有す るセラミツク材料を主成分とする焼結体の平均表面粗さが R a 30 nm以下であることを特徴 とする項 821又は 822に記載されたいずれかの薄膜基板。
項 824. 六方晶系又は三方晶系のうちから選ばれた少なくともいずれかの結晶構造を有す るセラミック材料を主成分とする焼結体の平均表面粗さが R a 1 Onm以下であることを特徴
とする項 821、 822又は 823に記載されたいずれかの薄膜基板。
項 825. 六方晶系又は三方晶系のうちから選ばれた少なくともいずれかの結晶構造を有す るセラミック材料を主成分とする焼結体の平均表面粗さが R a 5 nm以下であることを特徴と する項 821、 822、 823又は 824に記載されたいずれかの薄膜基板。
項 826. 表面粗さの大きい六方晶系又は三方晶系のうちから選ばれた少なくともいずれか の結晶構造を有するセラミック材料を主成分とする焼結体からなることを特徴とする項 803、 804、 805、 806、 807、 808、 809、 810、 811、 812、 813、 81 4、 815、 816、 817、 818、 819、 820、 821、 822、 823、 824又 は 825に記載されたいずれかの薄膜基板。
項 827. 六方晶系又は三方晶系のうちから選ばれた少なくともいずれかの結晶構造を有す るセラミック材料を主成分とする焼結体の平均表面粗さが R a 70 nm以上であることを特徴 とする項 803、 804、 805、 806、 807、 808、 809、 810、 811、 81 2、 813、 814、 815、 816、 817、 818、 819、 820、 821、 822、 823、 824、 825又は 826に記載されたいずれかの薄膜基板。
項 828. 六方晶系又は三方晶系のうちから選ばれた少なくともいずれかの結晶構造を有す るセラミック材料を主成分とする焼結体の平均表面粗さが R a 1000 nmより大きいことを 特徴とする項 827に記載された薄膜基板。
項 829. 六方晶系又は三方晶系のうちから選ばれた少なくともいずれかの結晶構造を有す るセラミック材料を主成分とする焼結体の平均表面粗さが R a 2000 nmより大きいことを 特徴とする項 827又は 828に記載された薄膜基板。
項 830. 六方晶系又は三方晶系のうちから選ばれた少なくともいずれかの結晶構造を有す るセラミック材料を主成分とする焼結体の表面が焼き放し (a s_f i re)、 ラッフ ¾Jf磨、 ブ ラスト研磨、 鏡面研磨、 化学腐食及びプラズマガスによる腐食のうちから選ばれた少なくとも いずれかの状態であることを特徴とする項 803、 804、 805、 806、 807、 808、 809、 810、 811、 812、 813、 814、 815、 816、 817、 818、 81 9、 820、 821、 822、 823、 824、 825、 826、 827, 828又は 829 に記載されたいずれかの薄膜基板。
項 831. 六方晶系又は三方晶系のうちから選ばれた少なくともいずれかの結晶構造を有す るセラミツク材料を主成分とする焼結体の表面が鏡面研磨された状態であることを特徴とする 項 830に記載された薄膜基板。
項 832. 六方晶系又は三方晶系のうちから選ばれた少なくともいずれかの結晶構造を有す るセラミック材料を主成分とする焼結体が 化亜鉛、 酸化ベリリウム、 酸化アルミニウム、 炭 化珪素、 窒化珪素、 窒化ガリゥムのうちから選ばれた少なくとも 1種以上を主成分とする焼結 体からなることを赚とする項 803、 804、 805、 806、 807、 808、 809、 810、 811、 812、 813、 814、 815、 816、 817、 818、 819、 82 0、 821、 822、 823、 824、 825、 826、 827、 828、 829、 830又 は 831に記載されたいずれかの薄膜基板。
項 833. 六方晶系又は三方晶系のうちから選ばれた少なくともいずれかの結晶構造を有す るセラミック材料を主成分とする焼結体が 化亜鉛を主成分とする焼結体であることを と する項 803、 804又は 832に記載されたいずれかの薄膜基板。
項 834. 酸化亜鉛を主成分とする焼結体が) ¾¾ 性を有するものであることを特徴とする 項 803、 804、 832又は 833に記載されたいずれかの薄膜基板。
項 835. 酸化亜鉛を主成分とする焼結体が光 ¾1率 1%以上を有するものであることを特 徴とする項 832、 833又は 834に記載されたいずれかの薄膜基板。
項 836. 酸化亜鉛を主成分とする焼結体が光 ¾i 率 10%以上を有するものであることを 特徴とする項 835に記載された薄膜基板。
項 837. 酸化亜鉛を主成分とする焼結体が光 ¾i率 20%以上を有するものであることを 特徴とする項 835又は 836に記載されたいずれかの薄膜基板。
項 838. 酸化亜鉛を主成分とする; ¾結体が光 率 30%以上を有するものであることを 特徴とする項 835、 836又は 837に記載されたいずれかの薄膜基板。
項 839. 酸化亜鉛を主成分とする焼結体が光 ¾ii率 40%以上を有するものであることを 特徴とする項 835、 836、 837又は 838に記載されたいずれかの薄膜基板。
項 840. 酸化亜鉛を主成分とする焼結体が光 ¾率 50 %以上を有するものであることを 特徴とする項 835、 836、 837、 838又は 839に記載されたいずれかの薄膜基板。 項 841. 酸化亜鉛を主成分とする焼結体が光 ¾i率 60 %以上を有するものであることを 特徴とする項 835、 836、 837、 838、 839又は 840に記載されたいずれかの薄 項 842. 酸化亜鉛を主成分とする焼結体が光透過率 80 %以上を有するものであることを 特徴とする項 835、 836、 837、 838、 839、 840又は 841に記載されたいず れかの薄膜基板。
項 843. 酸化亜鉛を主成分とする焼結体が光 率 1 %未満であることを特徴とする項 8
32、 8' 33又は 834に記載されたいずれかの薄膜基板。
項 844. 酸化 «を主成分とする焼結体の光醒率が 0 %であることを特徴とする項 56 2に記載された薄膜基板。
項 845. 酸化 を主成分とする焼結体が導電性を有するものであることを特徴とする項 832、 833、 834、 835、 836、 837、 838、 839、 840、 841、 84 2、 843又は 844に記載されたいずれかの薄膜基板。
項 846.酸 [^鉛を主成分とする!^体が室温における抵抗率 1 X 102Ω · cm以下であ ることを特徴とする項 832、 833、 834、 835、 836、 837、 838、 839、 840、 841、 842、 843、 844又は 845に記載されたいずれかの薄膜基板。 項 847. 酸化亜鉛を主成分とする焼結体が光透過性を有しかつ導電性を有するものである ことを特徴とする項 832、 833、 834、 835、 836、 837、 838、 839、 8 40、 841、 842、 843、 844、 845又は 846に記載されたいずれかの薄膜基板。 項 848. 酸化亜鉛を主成分とする焼結体が少なくともアルミニウム成分を含むものである ことを特徴とする項 832、 833、 834、 835、 836、 837、 838、 839、 8
40、 841、 842、 843、 844、 845、 846又は 847に記載されたいずれかの 項 849. 酸化亜鉛を主成分とする焼結体が ¾化亜鉛成分を Z n〇換算で 55. 0モル%以 上含むものであることを特徴とする項 832、 833、 834、 835、 836、 837、 8 38、 839、 840、 841、 842、 843、 844、 845、 846、 847又は 84 8に記載されたいずれかの薄膜基板。
項 850. 酸化亜鉛を主成分とする焼結体がアルミニゥム成分を A 1203換算で 45. 0モ ル%以下含むものであることを特徴とする項 848又は 849に記載されたいずれかの薄膜基 板。
項 851. 酸化亜鉛を主成分とする焼結体がアルミニウム成分を A 1203 で0. 001 モル%〜45. 0モル%の範囲含むものであることを特徴とする項 850に記載された薄膜基 板。
項 852. 酸化亜鉛を主成分とする焼結体がアルミニウム成分を A 1203騰で 0. 005
モル%〜4 5. 0モル%の範囲含むものであることを特徴とする項 8 5 0又は 8 5 1に記載さ れたいずれかの薄膜基板。
項 8 5 3. 酸化亜鉛を主成分とする焼結体がアルミニゥム成分を A 1 203換算で 0. 0 2モ ル%〜4 5. 0モル%の範囲含むものであることを特徴とする項 8 5 0、 8 5 1又は 8 5 2に 記載されたいずれかの薄膜基板。
項 8 5 4. 酸化亜鉛を主成分とする焼結体がアルミニウム成分を A 1 203換算で 0. 0 8モ ル%〜3 5. 0モル%の範囲含むものであることを特徴とする項 8 5 0、 8 5 1、 8 5 2又は 8 5 3に記載されたいずれかの薄膜基板。
項 8 5 5. 酸化亜鉛を主成分とする焼結体がアルカリ土類金属成分、 希土類 素成分、 遷移 金属成分及び 素成分のうちから選ばれた少なくとも 1種以上の成分を含むものであることを 特徴とする項 8 3 2、 8 3 3、 8 3 4、 8 3 5、 8 3 6、 8 3 7、 8 3 8、 8 3 9、 8 4 0、 8 4 1、 8 4 2、 8 4 3、 8 4 4、 8 4 5、 8 4 6、 8 4 7、 8 4 8、 8 4 9、 8 5 0、 8 5 1、 8 5 2、 8 5 3又は 8 5 4に記載されたいずれかの薄膜基板。
項 8 5 6. 酸化 «を主成分とする焼結体が希土類 素成分及び遷移金属成分のうちから選 ばれた少なくとも 1種以上の成分を含むものであることを特徴とする項 8 5 5に記載された薄 項 8 5 7. 酸化亜鉛を主成分とする 結体が希土類 素成分のうちから選ばれた少なくとも 1種以上の成分を含むものであることを,とする項 8 5 5又は 8 5 6に記載されたいずれか 項 8 5 8. 酸化亜鉛を主成分とする焼結体が希土類 素成分のうちから選ばれた少なくとも 1種以上の成分を含む光 ¾1性を有するものであることを特徴とする項 8 5 7に記載された薄 項 8 5 9. 酸化亜鉛を主成分とする焼結体が希土類 素成分のうちから選ばれた少なくとも 1種以上の成分を含む光透過率 3 0 %以上を有するものであることを特徴とする項 8 5 7又は 8 5 8に記載されたいずれかの薄膜基板。
項 8 6 0. 光 ¾1性あるいは光 ¾i率が少なくとも波長 2 0 0 nm〜8 0 0 nmの範囲の光 に対してのものであることを特徴とする項 8 3 4、 8 3 5、 8 3 6、 8 3 7、 8 3 8、 8 3 9、 8 4 0、 8 4 1、 8 4 2、 8 4 3、 8 4 4、 8 5 8又は 8 5 9に記載されたいずれかの薄膜基 板。
項 8 6 1 . 酸化亜鉛を主成分とする焼結体が遷移金属成分のうちから選ばれた少なくとも 1 種以上の成分を含むものであることを特徴とする項 8 5 5又は 8 5 6に記載されたいずれかの 項 8 6 2. 酸化亜鉛を主成分とする焼結体が希土 11¾素成分及び遷移金属成分のうちから選 ばれた少なくとも 1種以上の成分を酸化物換算で 1 0. 0モル%以下含むものであることを特 徴とする項 8 5 5、 8 5 6、 8 5 7、 8 5 8、 8 5 9、 8 6 0又は 8 6 1に記載されたいずれ かの薄膜基板。
項 8 6 3. 酸化亜鉛を主成分とする焼結体がアルミニウム成分を含み、 同時に希土 素成 分及び遷移金属成分のうちから選ばれた少なくとも 1種以上の成分を含むものであることを特 徴とする項 8 4 8、 8 4 9、 8 5 0、 8 5 1、 8 5 2、 8 5 3、 8 5 4、 8 5 5、 8 5 6、 8 5 7、 8 5 8、 8 5 9、 8 6 0、 8 6 1又は 8 6 2に記載されたいずれかの薄膜基板。
項 8 6 4. 酸化亜鉛を主成分とする焼結体がアルミニウム成分を含み同時に希土類 J£素成分 のうちから選ばれた少なくとも 1種以上の成分を含むものであることを特徴とする項 8 6 3に 記載された薄膜基板。
項 8 6 5. 酸化亜鉛を主成分とする焼結体がアルミニウム成分を含み同時に遷移金属成分の
うちから選ばれた少なくとも 1種以上の成分を含むものであることを特徴とする項 863に記 項 866. 酸化亜鉛を主成分とする焼結体が希土類 素成分及び遷移金属成分のうちから選 ばれた少なくとも 1種以上の成分を酸化物換算で 10. 0モル%以下含むものであることを特 徴とする項 863、 864又は 865に記載されたいずれかの薄膜基板。
項 867, 酸化 を主成分とする焼結体が希土 ¾素成分のうちから選ばれた少なくとも 1種以上の成分を酸化物 で 10. 0モル%以下含むものであることを特徴とする項 866 に記載された薄膜基板。
項 868. 酸化 «を主成分とする焼結体が遷移金属成分のうちから選ばれた少なくとも 1 種以上の成分を酸化物換算で 10. 0モル%以下含むものであることを特徴とする項 866又 は 867に記載されたいずれかの薄膜基板。
項 869. 遷移金属成分が鉄及びクロムのうちから選ばれる少なくとも 1種以上の成分であ ることを特徴とする項 855、 856、 861、 862、 863、 865、 866又は 868 に記載されたいずれかの薄膜基板。
項 870. 酸化亜鉛を主成分とする焼結体がアルミニウム成分を A 12〇3騰で 45. 0モ ル%以下含み、 同時に希土 素成分のうちから選ばれた少なくとも 1種以上の成分を酸化物 換算で 10. 0モル%以下含むものであることを特徴とする項 863、 864、 865又は 8 66記載されたいずれかの薄膜基板。
.項871. 酸化亜鉛を主成分とする焼結体がアルミニウム成分を A 1203麟で 45. 0モ ル%以下含み、 同時に希土類 素成分のうちから選ばれた少なくとも 1種以上の成分を酸化物 換算で 0. 0002モル%〜10. 0モル%の範囲含むものであることを特徴とする項 870 に記載された薄膜基板。
項 872. 酸化 、を主成分とする焼結体がアルミニウム成分を A 1203購で 45. 0モ ル%以下含み、 同時に希土 素成分のうちから選ばれた少なくとも 1種以上の成分を酸化物 換算で 0. 0006モル%〜6. 0モル%の範囲含むものであることを^とする項 870又 は 871に記載されたいずれかの薄膜基板。
項 873. 酸化亜鉛を主成分とする焼結体がアルミニウム成分を A 12〇3換算で 45. 0モ ル%以下含み、 同時に希土類 J£素成分のうちから選ばれた少なくともか 1種以上の成分を酸化 物換算で 0. 001モル%〜6. 0モル%の範囲含むものであることを特徴とする項 870、 871又は 872に記載されたいずれかの薄膜基板。
項 874. 酸化亜鉛を主成分とする焼結体がアルミニウム成分を A 12〇3 で 45. 0モ ル%以下含み、 同時に希土 ¾素成分のうちから選ばれた少なくとも 1種以上の成分を酸化物 換算で 0. 002モル%〜3. 0モル%の範囲含むものであることを とする項 870、 8 71、 872又は 873に記載されたいずれかの薄膜基板。
項 875. 酸化亜鉛を主成分とする焼結体がアルミニウム成分を A 1203換算で 0. 001 モル%〜 45. 0モル%の範囲含み、 同時に希土類 J£素成分のうちから選ばれた少なくとも 1 種以上の成分を含むものであることを特徴とする項 863、 864、 865、 866、 867、 868、 869、 870、 871、 872、 873又は 874に記載されたいずれかの薄膜基 板。
項 876. 六方晶系又は三方晶系のうちから選ばれた少なくともいずれかの結晶構造を有す るセラミック材料を主成分とする焼結体が «化ベリリウムを主成分とする焼結体であることを 特徴とする項 803, 804又は 832に記載されたいずれかの薄膜基板。
項 877. 酸化ベリリウムを主成分とする焼結体が光 ¾i性を有するものであることを ¾ とする項 803、 804、 832又は 876に記載されたいずれかの薄膜基板。
項 878. 酸化ベリリゥムを主成分とする焼結体が光 ¾ϋ率 1 %以上を有するものであるこ とを特徴とする項 832、 876又は 877に記載されたいずれかの薄膜基板。
項 879. 酸化ベリリゥムを主成分とする焼結体が光透過率 10 %以上を有するものである ことを特徴とする項 878に記載された薄膜基板。
項 880. 酸化ベリリウムを主成分とする焼結体が光透過率 20 %以上を有するものである ことを特徴とする項 878又は 879に記載されたいずれかの薄膜基板。
項 881. 酸化ベリリウムを主成分とする焼結体が光透過率 30%以上を有するものである ことを特徴とする項 878、 879又は 880に記載されたいずれかの薄膜基板。
項 882. 酸化ベリリウムを主成分とする焼結体が光透過率 40 %以上を有するものである ことを特徴とする項 878、 879、 880又は 881に記載されたいずれかの薄膜基板。 項 883. 酸化ベリリゥムを主成分とする焼結体が光透過率 50 %以上を有するものである ことを特徴とする項 878、 879、 880、 881又は 882に記載されたいずれかの薄膜 項 884. 酸化ベリリウムを主成分とする焼結体が光透過率 60 %以上を有するものである ことを特徴とする項 878、 879、 880、 881、 882又は 883に記載されたいずれ かの薄膜基板。
項 885. 酸化ベリリウムを主成分とする焼結体が光 ¾ 率 80 %以上を有するものである ことを特徴とする項 878、 879、 880、 881、 882、 883又は 884に記載され たいずれかの薄膜基板。
項 886. 酸化ベリリウムを主成分とする焼結体に窒化ガリウム、 窒化インジウム、 窒化ァ ルミニゥムのうちから選ばれた少なくとも 1種以上を主成分とする薄膜が形成されている薄膜 基板であって、 靈化ベリリウムを主成分とする焼結体の光 ¾ii率が 1 %未満であることを特 徴とする項 832、 876又は 877に記載されたいずれかの薄膜基板。
項 887. 酸化ベリリウムを主成分とする焼結体の光醒率が 0 %であることを特徴とする 項 886に記載された薄膜基板。
項 888. 光 性あるいは光 ¾ 率が少なくとも波長 200謹〜 800謹の範囲の光 に対してのものであることを特徴とする項 877、 878、 879、 880、 881、 882、 883、 884、 885、 886又は 887に記載されたいずれかの薄膜基板。
項 889. 酸化ベリリゥムを主成分とする焼;結体がマグネシウム成分、 カルシウム成分及び 珪素成分のうちから選ばれた少なくとも 1種以上の成分を含むものであることを特徴とする項 832、 876、 877、 878、 879、 880、 881、 882、 883、 884、 88 5、 886、 887又は 888に記載されたいずれかの薄膜基板。
項 890.酸化ベリリウムを主成分とする焼結体が ¾化ベリリウム成分を B eO で 65. 0モル%以上含むものであることを特徴とする項 832、 876、 877、 878、 879、 880、 881、 882、 883、 884、 885、 886、 887、 888又は 889に記 載されたいずれかの薄膜基板。
項 891. 酸化ベリリウムを主成分とする焼結体がマグネシウム成分、 カルシウム成分、 珪 素成分のうちから選ばれた少なくとも 1種以上の成分を酸化物 で合計 35. 0モル%以下 含むものであることを特徴とする項 832、 876、 877、 878、 879、 880、 88 1、 882、 883、 884、 885、 886、 887、 888、 889又は 890に記載さ れたいずれかの薄膜基板。
項 892. 酸化ベリリウムを主成分とする焼結体がマグネシウム成分、 カルシウム成分、 珪 素成分のうちから選ばれた少なくとも 1種以上の成分を酸化物騰で合計 0. 0002モル% 〜 35. 0モル%の範囲含むものであることを特徴とする項 891に記載された薄膜基板。
項 8 9 3. 酸化ベリリウムを主成分とする焼結体がマグネシウム成分、 カルシウム成分、 珪 素成分のうちから選ばれた少なくとも 1種以上の成分を酸化物換算で合計 0. 0 0 1モル%〜 3 5. 0モル%の範囲含むものであることを特徴とする項 8 9 1又は 8 9 2に記載されたいず れかの薄膜基板。
項 8 9 4. 酸化ベリリウムを主成分とする焼結体がマグネシウム成分、 カルシウム成分、 珪 素成分のうちから選ばれた少なくとも 1種以上の成分を酸化物 で合計 0. 0 0 4モル%〜 3 5. 0モル%の範囲含むものであることを特徴とする項 8 9 1、 8 9 2又は 8 9 3に記載さ れたいずれかの薄膜基板。
項 8 9 5. 酸化ベリリウムを主成分とする焼結体がマグネシウム成分、 カルシウム成分、 珪 素成分のうちから選ばれた少なくとも 1種以上の成分を酸化物 で合計 0. 0 1 5モル%〜 2 5. 0モル%の範囲含むものであることを特徴とする項 8 9 1、 8 9 2、 8 9 3又は 8 9 4 に記載されたいずれかの薄膜基板。
項 8 9 6. 酸化ベリリウムを主成分とする焼結体がマグネシウム成分、 カルシウム成分、 珪 素成分のうちから選ばれた少なくとも 1種以上の成分を含み、 同時に希土類 素成分のうちか ら選ばれた少なくとも 1種以上の成分を含むものであることを とする項 8 3 2、 8 7 6、 8 7 7、 8 7 8、 8 7 9、 8 8 0、 8 8 1、 8 8 2、 8 8 3、 8 8 4、 8 8 5、 8 8 6、 8 8 7、 8 8 8、 8 8 9、 8 9 0、 8 9 1、 8 9 2、 8 9 3、 8 9 4又は 8 9 5に記載されたいず れかの薄膜基板。
項 8 9 7. 酸化ベリリウムを主成分とする焼結体がマグネシウム成分、 カルシウム成分、 珪 素成分のうちから選ばれた少なくとも 1種以上の成分を含み、 同時に希土類 素成分のうちか ら選ばれた少なくとも 1種以上の成分を酸化物換算で 5. 0モル%以下含むものであることを 特徴とする項 8 9 6に記載された薄膜基板。
項 8 9 8. 酸化ベリリゥムを主成分とする焼結体がマグネシウム成分、 カルシウム成分、 珪 素成分のうちから選ばれた少なくとも 1種以上の成分を酸化物 で 3 5.. 0モル%以下含み、 同時に希土類 素成分のうちから選ばれた少なくとも 1種以上の成分を酸化物■で 5. 0モ ル%以下含むものであることを特徴とする項 8 9 6又は 8 9 7 6に記載されたいずれかの薄膜 項 8 9 9. 酸化ベリリウムを主成分とする焼結体がマグネシウム成分、 カルシウム成分、 珪 素成分のうちから選ばれた少なくとも 1種以上の成分を酸化物換算で 3 5. 0モル%以下含み、 同時に希土類 J£素成分のうちから選ばれた少なくとも 1種以上の成分を酸化物購で 0. 0 0 0 0 5モル%〜5. 0モル%の範囲含むものであることを特徴とする項 8 9 6、 8 9 7又は 8 9 8に記載されたいずれかの薄膜基板。
項 9 0 0. 酸化ベリリウムを主成分とする焼結体がマグネシウム成分、 カルシウム成分、 珪 素成分のうちから選ばれた少なくとも 1種以上の成分を酸化物換算で 3 5. 0モル%以下含み、 同時に希土 素成分のうちから選ばれた少なくとも 1種以上の成分を酸化物換算で 0. 0 0 0 5モル%〜3. 0モル%の範囲含むものであることを特徴とする項 8 9 6、 8 9 7、 8 9 8 又は 8 9 9に記載されたいずれかの薄膜基板。
項 9 0 1 . 酸化ベリリウムを主成分とする焼結体がマグネシウム成分、 カルシウム成分、 珪 素成分のうちから選ばれた少なくとも 1種以上の成分を酸化物換算で 3 5. 0モル%以下含み、 同時に希土 ¾素成分のうちから選ばれた少なくとも 1種以上の成分を酸化物換算で 0. 0 0 2モル%〜3. 0モル%の範囲含むものであることを特徴とする項 8 9 6、 8 9 7、 8 9 8、 8 9 9又は 9 0 0に記載されたいずれかの薄膜基板。
項 9 0 2. 酸化ベリリウムを主成分とする焼結体がマグネシウム成分、 カルシウム成分、 珪 素成分のうちから選ばれた少なくとも 1種以上の成分を酸化物騰で 3 5. 0モル%以下含み、
同時に希土類 素成分のうちから選ばれた少なくとも 1種以上の成分を酸化% ^で 0. 00 5モル%〜3. 0モル%の範囲含むものであることを特徴とする項 896、 897、 898、 899、 900又は 901に記載されたいずれかの薄膜基板。
項 903. 酸化ベリリウムを主成分とする焼結体がマグネシウム成分、 カルシウム成分、 珪 素成分のうちから選ばれた少なくとも 1種以上の成分を酸化物換算で 0. 0002モル%〜 3 5. 0モル%の範囲含み、 同時に希土類元素成分のうちから選ばれた少なくとも 1種以上の成 分を含むものであることを特徴とする項 896、 897、 898、 899、 900、 901又 は 902に記載されたいずれかの薄膜基板。
項 904. 六方晶系又は三方晶系のうちから選ばれた少なくともいずれかの結晶構造を有す るセラミツク材料を主成分とする 結体力職化アルミニウムを主成分とする焼結体であること を特徴とする項 803、 804又は 832に記載されたいずれかの薄膜基板。
項 905. 酸化アルミニウムを主成分とする焼結体が)16^1性を有するものであることを特 徴とする項 803、 804、 832又は 904に記載されたいずれかの薄膜基板。
項 906. 酸化アルミニウムを主成分とする焼結体が ¾¾M率 1%以上を有するものである ことを特徴とする項 832、 904又は 905に記載されたいずれかの薄膜基板。
項 907. 酸化アルミニウムを主成分とする焼結体が光透過率 10%以上を有するものであ ることを特徴とする項 906に記載された薄膜基板。
項 908. 酸化アルミニウムを主成分とする焼結体が 率 20%以上を有するものであ ることを特徴とする項 906又は 907に記載されたいずれかの薄膜基板。
項 909. 酸化アルミニウムを主成分とする焼結体が 過率 30%以上を有するものであ ることを特徴とする項 906、 907又は 908に記載されたいずれかの薄膜基板。
項 910. 酸化アルミニウムを主成分とする焼結体が光 ¾ 率 40%以上を有するものであ ることを特徴とする項 906、 907、 908又は 909に記載されたいずれかの薄膜基板。 項 911. 酸化アルミニウムを主成分とする焼結体が光透過率 50 %以上を有するものであ ることを特徴とする項 906、 907、 908、 909又は 910に記載されたいずれかの薄 項 912. 酸化アルミニウムを主成分とする焼結体が 率 60%以上を有するものであ ることを特徴とする項 906、 907、 908、 909、 910又は 911に記載されたいず れかの薄膜基板。
項 913. 酸化アルミニウムを主成分とする焼結体が光透過率 80%以上を有するものであ ることを特徴とする項 906、 907、 908、 909、 910、 911又は 912に記載さ れたいずれかの薄膜基板。
項 914. 酸化アルミニウムを主成分とする焼結体に窒化ガリウム、 窒化インジウム、 窒化 アルミニウムのうちから選ばれた少なくとも 1種以上を主成分とする薄膜が形成されている薄 膜基板であって、 該酸化アルミニウムを主成分とする焼結体の光 ¾i率が 1 %未満であること を特徴とする項 832、 904又は 905に記載されたいずれかの薄膜基板。
項 915. 酸化アルミニウムを主成分とする焼結体の 率が 0%であることを特徴とす る項 914に記載された薄膜基板。
項 916. 光 ¾i性あるいは光 ¾1率が少なくとも波長 200 nm〜800 nmの範囲の光 に対してのものであることを [とする項 905、 906、 907、 908、 909、 910、 911、 912、 913、 914又は 915に記載されたいずれかの薄膜基板。
項 917. 酸化アルミニウムを主成分とする焼結体がマグネシウム成分、 カルシウム成分及 ぴ 素成分のうちから選ばれた少なくとも 1種以上の成分を含むものであることを特徴とする 項 832、 904、 905、 906、 907、 908、 909、 910、 911、 912、 9
1 3、 9 1 4、 9 1 5又は 9 1 6に記載されたいずれかの薄膜基板。
項 9 1 8. 酸化アルミニウムを主成分とする能結体力職化アルミニウム成分を A 1 203騰 で 5 5. 0モル%以上含むものであることを特徴とする項 8 3 2、 9 0 4、 9 0 5、 9 0 6、 9 0 7、 9 0 8、 9 0 9、 9 1 0、 9 1 1、 9 1 2、 9 1 3、 9 1 4、 9 1 5、 9 1 6又は 9 1 7に記載されたいずれかの薄膜基板。
項 9 1 9. 酸ィ匕アルミニウムを主成分とする焼結体がマグネシウム成分、 カルシウム成分、 珪素成分のうちから選ばれた少なくとも 1種以上の成分を酸化物換算で合計 4 5. 0モル%以 下含むものであることを 1:とする項 8 3 2、 9 0 4、 9 0 5、 9 0 6、 9 0 7、 9 0 8、 9 0 9、 9 1 0、 9 1 1、 9 1 2、 9 1 3、 9 1 4、 9 1 5、 9 1 6、 9 1 7又は 9 1 8に記載 されたいずれかの薄膜基板。
項 9 2 0. 酸化アルミニウムを主成分とする焼結体がマグネシウム成分、 カルシウム成分、 珪素成分のうちから選ばれた少なくとも 1種以上の成分を酸化物 で合計 0. 0 0 1モル% 〜4 5. 0モル%の範囲含むものであることを特徴とする項 9 1 9に記載された薄膜基板。 項 9 2 1 . 酸化アルミニウムを主成分とする焼結体がマグネシウム成分、 カルシウム成分、 珪素成分のうちから選ばれた少なくとも 1種以上の成分を酸化物 で合計 0. 0 0 5モル% 〜4 5. 0モル%の範囲含むものであることを特徴とする項 9 1 9又は 9 2 0に記載されたい ずれかの薄膜基板。
項 9 2 2. 酸化アルミニウムを主成分とする焼結体がマグネシウム成分、 カルシウム成分、 珪素成分のうちから選ばれた少なくとも 1種以上の成分を酸化物■で合計 0. 0 2モル%〜 4 5. 0モル%の範囲含むものであることを特徴とする項 9 1 9 , 9 2 0又は 9 2 1に記載さ れたいずれカゝの薄膜基板。
項 9 2 3. 酸化アルミニウムを主成分とする焼結体がマグネシウム成分、 カルシウム成分、 珪素成分のうちから選ばれた少なくとも 1種以上の成分を酸化物換算で合計 0. 0 8モル%〜 3 5. 0モル%の範囲含むものであることを特徴とする項 9 1 9、 9 2 0、 9 2 1又は 9 2 2 に記載されたいずれかの薄膜基板。
項 9 2 4. 酸化アルミニウムを主成分とする焼結体がマグネシゥム成分、 カルシウム成分、 珪素成分のうちから選ばれた少なくとも 1種以上の成分を含み、 同時に希土類 素成分のうち から選ばれた少なくとも 1種以上の成分を含むものであることを とする項 8 3 2、 9 0 4、 9 0 5、 9 0 6、 9 0 7、 9 0 8、 9 0 9、 9 1 0、 9 1 1、 9 1 2、 9 1 3、 9 1 4, 9 1 5、 9 1 6、 9 1 7、 9 1 8、 9 1 9、 9 2 0、 9 2 1、 9 2 2又は 9 2 3に記載されたいず れかの薄膜基板。
項 9 2 5. 酸化アルミニウムを主成分とする焼結体がマグネシウム成分、 カルシウム成分、 珪素成分のうちから選ばれた少なくとも 1種以上の成分を含み、 同時に希土類 素成分のうち から選ばれた少なくとも 1種以上の成分を酸化物換算で 1 0. 0モル%以下含むものであるこ とを特徴とする項 9 2 4に記載された薄膜基板。
項 9 2 6. 酸化アルミニウムを主成分とする焼結体がマグネシウム成分、 カルシウム成分、 珪素成分のうちから選ばれた少なくとも 1種以上の成分を酸化物■で 4 5. 0モル%以下含 み、 同時に希土 素成分のうちから選ばれた少なくとも 1種以上の成分を酸化物騰で 1 0. 0モル%以下含むものであることを特徴とする項 9 2 4又は 9 2 5に記載されたいずれかの薄 項 9 2 7. 酸化アルミニウムを主成分とする焼結体がマグネシウム成分、 カルシウム成分、 珪素成分のうちから選ばれた少なくとも 1種以上の成分を酸化物 で 4 5. 0モル%以下含 み、 同時に希土 I ^素成分のうちから選ばれた少なくとも 1種以上の成分を酸化物換算で 0. 0 0 0 2モル%〜1 0. 0モル%の範囲含むものであることを特徴とする項 9 2 4、 9 2 5又
は 926に記載されたいずれかの薄膜基板。
項 928. 酸化アルミニウムを主成分とする焼結体がマグネシウム成分、 カルシウム成分、 珪素成分のうちから選ばれた少なくとも 1種以上の成分を酸化物,で 45. 0モル%以下含 み、 同時に希土類沅素成分のうちから選ばれた少なくとも 1種以上の成分を酸化物騰で 0. 001モル%〜6. 0モル%の範囲含むものであることを特徴とする項 924、 925、 92 6又は 927に記載されたいずれかの薄膜基板。
項 929. 酸ィ匕アルミニウムを主成分とする焼結体がマグネシウム成分、 カルシウム成分、 珪素成分のうちから選ばれた少なくとも 1種以上の成分を酸化物 で 45. 0モル%以下含 み、 同時に希土類 素成分のうちから選ばれた少なくとも 1種以上の成分を酸化物騰で 0. 005モル%〜6. 0モル%の範囲含むものであることを特徴とする項 924、 925、 92 6、 927又は 928に記載されたいずれかの薄膜基板。
項 930. 酸ィ匕アルミニウムを主成分とする焼結体がマグネシウム成分、 カルシウム成分、 珪素成分のうちから選ばれた少なくとも 1種以上の成分を酸化物 »で 45. 0モル%以下含 み、 同時に希土 素成分のうちから選ばれた少なくとも 1種以上の成分を酸化物 «で 0. 01モル%〜6. 0モル%の範囲含むものであることを特徴とする項 924、 925、 926、 927、 928又は 929に記載されたいずれかの薄膜基板。
項 931. 酸化アルミニウムを主成分とする焼結体がマグネシウム成分、 カルシウム成分、 珪素成分のうちから選ばれた少なくとも 1種以上の成分を酸化物 で 0. 001モル%〜4 5. 0モル%の範囲含み、 同時に希土類 素成分のうちから選ばれた少なくとも 1種以上の成 分を含むものであることを特徴とする項 924、 925、 926、 927、 928、 929又 は 930に記載されたいずれかの薄膜基板。
項 932. 酸化アルミニウムを主成分とする焼結体がマグネシウム成分、 カルシウム成分、 珪素成分のうちから選ばれた少なくともいずれか 2種以上の成分を含むものであることを特徴 とする項 832、 904、 905、 906、 907、 908、 909、 910、 911、 91
2、 913、 914、 915、 916、 917、 918、 919、 920、 921、 922、 923、 924、 925、 926、 927、 928、 929、 930又は 931に記載された いずれかの薄膜基板。
項 933. 六方晶系又は三方晶系のうちから選ばれた少なくともいずれかの結晶構造を有す るセラミツク材料を主成分とする焼結体が窒化ガリゥムを主成分とする焼結体であることを特 徴とする項 803、 804又は 832に記載されたいずれかの薄膜基板。
項 934. 窒化ガリウムを主成分とする焼結体が光 ¾ϋ性を有することを特徴とする項 80
3、 804、 832又は 933に記載されたいずれかの薄膜基板。
項 935. 光透過率が 1 %以上であることを特徴とする項 832、 933又は 934に記載 されたいずれかの薄膜基板。
項 936. 窒化ガリウムを主成分とする焼結体の光 率が 5%以上であることを特徴とす る項 935に記載された薄膜基板。
項 937. 窒化ガリゥムを主成分とする焼結体の光 ¾ 率が 10 %以上であることを特徴と する項 935又は 936に記載されたいずれかの薄膜基板。
項 938. 窒化ガリウムを主成分とする焼結体の ¾¾M率が 20%以上であることを特徴と する項 935、 936又は 937に記載されたいずれかの薄膜基板。
項 939. 窒化ガリウムを主成分とする焼結体の光 ¾i率が 30%以上であることを特徴と する項 935、 936、 937又は 938に記載されたいずれかの薄膜基板。
項 940. 窒化ガリウムを主成分とする焼結体の ¾S過率が 40%以上であることを特徴と する項 935、 936、 937、 938又は 939に記載されたいずれかの薄膜基板。
項 941. 窒化ガリゥムを主成分とする焼結体の 率が 50 %以上であることを特徴と する項 935、 936、 937、 938、 939又は 940に記載されたいずれかの薄膜基板。 項 942. 窒化ガリウムを主成分とする焼結体の 過率が 60%以上であることを特徴と する項 935、 936、 937、 938、 939、 940又は 941に記載されたいずれかの 項 943. 窒化ガリゥムを主成分とする焼結体の 率が 80 %以上であることを特徴と する項 935、 936、 937、 938、 939、 940、 941又は 942に記載されたい ずれかの薄膜基板。
項 944. 窒化ガリウムを主成分とする焼結体の 過率が 85%以上であることを特徴と する項 935、 936、 937、 938、 939、 940、 941、 942又は 943に記載 されたいずれかの薄膜基板。
項 945. 窒化ガリゥムを主成分とする焼結体の) 率が 1 %未満の項 832、 933又 は 934に記載されたいずれかの薄膜基板。
項 946. 窒化ガリゥムを主成分とする焼結体の) ¾¾ 率が 0 %の項 945に記載された薄 項 947. 窒化ガリゥムを主成分とする焼結体の ¾¾¾性あるいは光 ¾ 率が少なくとも波 長 20 Οηπ!〜 80 Onmの範囲の光に対してのものであることを特徴とする項 934、 93 5、 936、 937、 938、 939、 940、 941、 942、 943、 944、 945又 ま946に記載されたいずれかの薄膜基板。
項 948. 窒化ガリウムを主成分とする; 結体が導電性を有することを«とする項 832、 933、 934、 935、 936、 937、 938、 939、 940、 941、 942、 94 3、 944、 945、 946又は 947に記載されたいずれかの薄膜基板。
項 949. 窒化ガリウムを主成分とする焼結体が室温における抵抗率 1 X 104Ω · cm以下 を有することを特徴とする項 832、 933、 934、 935、 936、 937、 938、 9 39、 940、 941、 942、 943、 944、 945、 946、 947又は 948に記載 されたいずれかの薄膜基板。
項 950. 窒化ガリウムを主成分とする焼結体が室温における抵抗率 1 X 10ΧΩ · cm以下 を有することを特徴とする項 948又は 949に記載されたいずれかの薄膜基板。
項 951. 窒化ガリウムを主成分とする 結体が室温における抵抗率 1 X 10。Ω · cm以下 を有することを特徴とする項 948、 949又は 950に記載されたいずれかの薄膜基板。 項 952. 窒化ガリウムを主成分とする焼結体が室温における抵抗率 1 X 10一2 Ω · cm以 下を有することを特徴とする項 948、 949、 950又は 951に記載されたいずれかの薄 項 953. 窒化ガリウムを主成分とする焼結体が ¾¾M性を有しかつ導電性を有することを 特徴とする項 832、 933、 934、 935、 936、 937、 938、 939、 940、 941、 942、 943、 944、 945、 946、 947、 948、 949、 950、 95 1又は 952に記載されたいずれかの薄膜基板。
項 954.窒化ガリウムを主成分とする焼結体がガリウム成分を GaN で 55. 0モル% 以上含むことを特徴とする項 832、 933、 934、 935、 936、 937、 938、 9 39、 940、 941、 942、 943、 944、 945、 946、 947、 948、 949、 950、 951、 952又は 953に記載されたいずれかの薄膜基板。
項 955. 窒化ガリウムを主成分とする焼結体がアルカリ土類金属及び希土類 素のうちか ら選ばれた少なくとも 1種以上の成分を含有することを樹敷とする項 832、 933、 934、 935、 936、 937、 938、 939、 940、 941、 942、 943、 944、 94
5、 946、 947、 948、 949、 950、 951、 952、 953又は 954に記載さ れたいずれかの薄膜基板。
項 956. 窒化ガリウムを主成分とする焼結体がアルカリ土類金属及び希土類 素のうちか ら選ばれた少なくとも 1種以上の成分を酸化物換算で 30モル%以下含有することを特徴とす る項 955に記載された薄膜基板。
項 957. 窒化ガリウムを主成分とする焼結体がアルカリ土類金属及 土 素のうちか ら選ばれた少なくとも 1種以上の成分を酸化物 で 20モル%以下含有することを特徴とす る項 955又は 956に記載されたいずれかの薄膜基板。
項 958. 窒化ガリウムを主成分とする焼結体がアルカリ土類金属及び希土 素のうちか ら選ばれた少なくとも 1種以上の成分を酸化物 で 10モル%以下含有することを特徴とす る項 955、 956又は 957に記載されたいずれかの薄膜基板。
項 959. 窒化ガリウムを主成分とする焼結体が亜鉛、 カドミウム、 炭素、 珪素、 ゲルマ二 ゥム、 セレン、 及びテルルのうちから選ばれた少なくとも 1種以上の成分を含有することを特 徴とする項 832、 933、 934、 935、 936、 937、 938、 939、 940、 9 41、 942、 943、 944、 945、 946、 947、 948、 949、 950、 951、 952、 953、 954、 955、 956、 957又は 958に記載されたいずれかの薄膜基 板。
項 960. 窒化ガリウムを主成分とする焼結体が亜鉛、 カドミウム、 炭素、 珪素、 ゲルマ二 ゥム、 セレン、 及びテルルのうちから選ばれた少なくとも 1種以上の成分を元素換算で 10モ レ%以下含有することを特徴とする項 959に記載された薄膜基板。
項 961. 窒化ガリウムを主成分とする焼結体が亜鉛、 カドミウム、 炭素、 珪素、 ゲルマ二 ゥム、 セレン、 及びテルルのうちから選ばれた少なくとも 1種以上の成分を元素換算で 0. 0 0001モル%〜 7モル%の範囲含有することを とする項 959又は 960に記載された いずれかの薄膜基板。
項 962. 窒化ガリウムを主成分とする焼結体が亜鉛、 カドミウム、 炭素、 珪素、 ゲルマ二 ゥム、 セレン、 及びテルルのうちから選ばれた少なくとも 1種以上の成分を元素換算で 0. 0 0001モル%〜 5モル%の範囲含有することを特徴とする項 959、 960又は 961に記 載されたいずれかの薄膜基板。
項 963. 窒化ガリウムを主成分とする焼結体が亜鉛、 カドミウム、 炭素、 珪素、 ゲルマ二 ゥム、 セレン、 及びテルルのうちから選ばれた少なくとも 1種以上の成分を元素換算で 0. 0 0001モル%〜 3モル%の範囲含有することを特徴とする項 959、 960又は 961に記 載されたいずれかの薄膜基板。
項 964. 窒化ガリウムを主成分とする焼結体がアルミニウム、 インジウム、 及び ¾素のう ちから選ばれた少なくとも 1種以上の成分を含有することを特徴とする項 832、 933、 9 34、 935、 936、 937、 938、 939、 940、 941、 942、 943、 944、 945、 946、 947、 948、 949、 950、 951、 952、 953、 954、 95 5、 956、 957、 958、 959、 960、 961、 962又は 963に記載されたいず れかの薄膜基板。
項 965. 窒化ガリウムを主成分とする焼結体がアルミニウム、 インジウム、 及び 素のう ちから選ばれた少なくとも 1種以上の成分を元素換算で 40モル%以下含有することを特徴と する項 964に記載された薄膜基板。
項 966. 窒化ガリウムを主成分とする焼結体がアルミニウム、 インジウム、 及び 素のう ちから選ばれた少なくとも 1種以上の成分を元素換算で 30モル%以下含有することを特徴と する項 964又は 965に記載されたいずれかの薄膜基板。
項 967. 窒化ガリウムを主成分とする焼結体が遷移金属のうちから選ばれた少なくとも 1 種以上の成分を含有することを特徴とする項 832、 933、 934、 935、 936、 93
7、 938、 939、 940、 941、 942、 943、 944、 945、 946、 947、 948、 949、 950、 951、 952、 953、 954、 955、 956、 957、 95
8、 959、 960、 961、 962、 963、 964、 965又は 966に記載されたいず れかの薄膜基板。
項 968. 窒化ガリウムを主成分とする焼結体が遷移金属のうちから選ばれた少なくとも 1 種以上の成分を元素 で 10モル%以下含有することを特徴とする項 967に記載された薄 項 969. 窒化ガリウムを主成分とする焼結体に含まれる遷移金属がマンガン、 コバルト、 ニッケル、 鉄、 クロム、 チタン、 モリブデン、 タングステン、 ニオブ、 タンタル、 バナジウム のうちから選ばれた少なくとも 1種以上であることを特徴とする項 967又は 968に記載さ れたいずれかの薄膜基板。
項 970. 窒化ガリウムを主成分とする焼結体が金属ガリウムの直接窒化による窒化ガリウ ムを主成分とする粉末を原料として作製されたものであることを,とする項 803、 804、
832、 933、 934、 935、 936、 937、 938、 939、 940、 941、 94
2、 943、 944、 945、 946、 947、 948、 949、 950、 951、 952、
953、 954、 955、 956、 957、 958、 959、 960、 961、 962、 96
3、 964、 965、 966、 967、 968又は 969に記載されたいずれかの薄膜基板。 に記載されたいずれかの薄膜基板。
項 971. 窒化ガリウムを主成分とする焼結体力職化ガリウムの 窒化による窒化ガリウ ムを主成分とする粉末を原料として作製されたものであることを糊数とする項 803、 804、
832、 933、 934、 935、 936、 937、 938、 939、 940、 941、 94
2、 943、 944、 945、 946、 947、 948、 949、 950、 951、 952、
953、 954、 955、 956、 957、 958、 959、 960、 961、 962、 96
3、 964、 965、 966、 967、 968又は 969に記載されたいずれかの薄膜基板。 に記載されたいずれかの薄膜基板。
項 972. 窒化ガリゥムを主成分とする焼結体が気体状のガリゥム化合物の窒化による窒化 ガリウムを主成分とする粉末を原料として作製されたものであることを特徴とする項 803、
804、 832、 933、 934、 935、 936、 937、 938、 939、 940、 94
1、 942、 943、 944、 945、 946、 947、 948、 949、 950、 951、
952、 953、 954、 955、 956、 957、 958、 959、 960、 961、 96
2、 963、 964、 965、 966、 967、 968又は 969に記載されたいずれかの薄 項 973. 窒化ガリウムを主成分とする焼結体力戰 有量 10重量%以下の窒化ガリウム を主成分とする粉末を原料として作製されたものであることを特徴とする項 970、 971又 は 972に記載されたいずれかの薄膜基板。
項 974. 窒化ガリウムを主成分とする焼結体力戰餘有量 10重量%以下の窒化ガリウム を主成分とする粉末を原料として作製されたものであることを とする項 973に記載され 項 975. 窒化ガリウムを主成分とする焼結体が平均樹圣 10 以下の窒化ガリウムを主 成分とする粉末を原料として作製されたものであることを特徴とする項 970、 971、 97 2、 973又は 974に記載されたいずれかの薄膜基板。
項 976. 窒化ガリウムを主成分とする焼結体が平均粒径 5. 0 m以下の窒化ガリウムを
主成分とする粉末を原料として作製されたものであることを とする項 9 7 5に記載された 項 9 7 7. 窒化ガリウムを主成分とする焼結体が平均粒径 2. 0 m以下の窒化ガリウムを 主成分とする粉末を原料として作製されたものであることを特徴とする項 9 7 5又は 9 7 6に 記載されたいずれかの薄膜基板。
項 9 7 8. 窒化ガリウムを主成分とする焼結体が平均樹圣 1 . 0 m以下の窒化ガリウムを 主成分とする粉末を原料として作製されたものであることを特徴とする項 9 7 5、 9 7 6又は 9 7 7に記載されたいずれかの薄膜基板。
項 9 7 9. 酸化ジルコニウム、 酸ィ匕マグネシウム、 アルミン酸マグネシウム、 酸化チタン、 チタン酸バリウム、 チタン酸ジルコン酸鉛、 希土 «化物、 酸化トリウム、 各種フェライト、 ムライト、 フォルステライト、 ステアタイト、 結晶化ガラスのうちから選ばれた少なくとも 1 種以上を主成分とする焼結体に窒化ガリウム、 窒化インジウム、 窒化アルミニウムのうちから 選ばれた少なくとも 1種以上を主成分とする薄膜が形成されていることを特徴とする項 6 8 2 又は 6 8 4に記載されたいずれかの薄膜基板。
項 9 8 0. 酸化ジルコニウム、 酸化マグネシウム、 アルミン酸マグネシウム、 酸化チタン、 チタン酸バリウム、 チタン酸ジルコン難、 希土讓化物、 酸化トリウム、 各種フェライト、 ムライト、 フオルステライ卜、 ステアタイト、 結晶化ガラスのうちから選ばれた少なくとも 1 種以上を主成分とするが基板状であることを特徴とする項 9 7 9に記載された薄膜基板。 項 9 8 1 . 窒化ガリウム、 窒化インジウム、 窒化アルミニウムのうちから選ばれた少なくと も 1種以上を主成分とする薄膜が単結晶、 無定形、 多結晶、 配向性多結晶のうちから選ばれる 少なくともいずれかの結晶状態を有することを特徴とする項 9 7 9又は 9 8 0に記載されたい ずれかの薄膜基板。
項 9 8 2. 窒化ガリウム、 窒化インジウム、 窒化アルミニウムのうちから選ばれた少なくと も 1種以上を主成分とする薄膜の少なくとも一部が単結晶であることを特徴とする項 9 8 1に 記載された薄膜基板。
項 9 8 3. 酸化ジルコニウム、 酸化マグネシウム、 アルミン酸マグネシウム、 酸化チタン、 チタン酸バリウム、 チタン酸ジルコン醒、 希土讓化物、 酸化トリウム、 各種フェライト、 ムライト、 フオルステライト、 ステア夕イト、 結晶化ガラスのうちから選ばれた少なくとも 1 種以上を主成分とする焼結体が 性を有することを特徴とする項 9 7 9、 9 8 0、 9 8 1 又は 9 8 2に記載されたいずれかの薄膜基板。
項 9 8 4. 酸化ジルコニウム、 酸化マグネシウム、 アルミン酸マグネシウム、 酸化チタン、 チタン酸バリウム、 チタン酸ジルコン酸鉛、 希土讓化物、 酸化トリウム、 各種フェライト、 ムライト、 フォルステライト、 ステアタイト、 結晶化ガラスのうちから選ばれた少なくとも 1 種以上を主成分とする焼結体の ¾¾i率が 1 %以上であることを體とする項 9 7 9、 9 8 0、 9 8 1、 9 8 2又は 9 8 3に記載されたいずれかの薄膜基板。
項 9 8 5. 酸化ジルコニウム、 酸化マグネシウム、 アルミン酸マグネシウム、 酸化チタン、 チタン酸バリウム、 チタン酸ジルコン酸鉛、 希土讓化物、 酸化トリウム、 各種フェライト、 ムライト、 フォルステライト、 ステアタイト、 結晶化ガラスのうちから選ばれた少なくとも 1 種以上を主成分とする焼結体の光 ¾i率が 5 %以上であることを特徴とする項 9 8 4に記載さ れた薄膜基板。
項 9 8 6. 酸化ジルコニウム、 酸化マグネシウム、 アルミン酸マグネシウム、 酸化チタン、 チタン酸バリウム、 チタン酸ジルコン難、、 希土鐘化物、 酸化トリウム、 各種フェライト、 ムライト、 フォルステライト、 ステアタイト、 結晶ィ匕ガラスのうちから選ばれた少なくとも 1 種以上を主成分とする焼結体の光透過率が 1 0 %以上であることを特徴とする項 9 8 4又は 9
8 5に記載されたいずれかの薄膜基板。
項 9 8 7. 酸化ジルコニウム、 酸化マグネシウム、 アルミン酸マグネシウム、 酸化チタン、 チタン酸バリウム、 チタン酸ジルコン薩、 希土讓化物、 酸化トリウム、 各種フェライト、 ムライト、 フォルステライト、 ステアタイト、 結晶化ガラスのうちから選ばれた少なくとも 1 種以上を主成分とする焼結体の^ 1率が 2 0 %以上であることを特徴とする項 9 8 4、 9 8
5又〖ま 9 8 6に記載されたいずれかの薄膜基板。
項 9 8 8. 酸ィ匕ジルコニウム、 酸化マグネシウム、 アルミン酸マグネシウム、 酸化チタン、 チタン酸バリウム、 チタン酸ジルコン 、 希土謙化物、 酸化トリウム、 各種フェライト、 ムライト、 フォルステライト、 ステアタイト、 結晶化ガラスのうちから選ばれた少なくとも 1 種以上を主成分とする焼結体の 率が 3 0 %以上であることを特徴とする項 9 8 4, 9 8
5、 9 8 6又は 9 8 7に記載されたいずれかの薄膜基板。
項 9 8 9. 酸化ジルコニウム、 酸化マグネシウム、 アルミン酸マグネシウム、 酸化チタン、 チタン酸バリウム、 チタン酸ジルコン醒、 希土讓化物、 酸化トリウム、 各種フェライト、 ムライト、 フォルステライト、 ステアタイト、 結晶化ガラスのうちから選ばれた少なくとも 1 種以上を主成分とする焼結体の ¾¾¾率が 4 0 %以上であることを特徴とする項 9 8 4、 9 8
5、 9 8 6、 9 8 7又は 9 8 8に記載されたいずれかの薄膜基板。
項 9 9 0. 酸化ジルコニウム、 酸化マグネシウム、 アルミン酸マグネシウム、 酸化チタン、 チタン酸バリウム、 チタン酸ジルコン歸、 希土難化物、 酸化トリウム、 各種フェライト、 ムライト、 フォルステライト、 ステアタイト、 結晶化ガラスのうちから選ばれた少なくとも 1 種以上を主成分とする焼結体の 率が 5 0 %以上であることを特徵とする項 9 8 4, 9 8
5、 9 8 6、 9 8 7、 9 8 8又は 9 8 9に記載されたいずれかの薄膜基板。
項 9 9 1 . 酸ィ匕ジルコニウム、 酸化マグネシウム、 アルミン酸マグネシウム、 酸化チタン、 チタン酸バリウム、 チタン酸ジルコン酸鉛、 希土纖化物、 酸化トリウム、 各種フェライト、 ムライト、 フォルステラィ卜、 ステアタイト、 結晶化ガラスのうちから選ばれた少なくとも 1 種以上を主成分とする焼結体の光透過率が 6 0 %以上であることを特徴とする項 9 8 4、 9 8
5、 9 8 6、 9 8 7、 9 8 8、 9 8 9又は 9 9 0に記載されたいずれかの薄膜基板。
項 9 9 2. 酸化ジルコニウム、 酸化マグネシウム、 アルミン酸マグネシウム、 酸化チタン、 チタン酸バリウム、 チタン酸ジルコン蘭、 希土纖化物、 酸化トリウム、 各種フェライト、 ムライト、 フォルステライト、 ステアタイト、 結晶化ガラスのうちから選ばれた少なくとも 1 種以上を主成分とする焼結体の 率が 8 0 %以上であることを特徴とする項 9 8 4, 9 8
5、 9 8 6、 9 8 7、 9 8 8、 9 8 9、 9 9 0又は 9 9 1に記載されたいずれかの薄膜基板。 項 9 9 3. 酸化ジルコニウム、 酸化マグネシウム、 アルミン酸マグネシウム、 酸化チタン、 チタン酸バリウム、 チタン酸ジルコン,、 希土画化物、 酸化トリウム、 各種フェライト、 ムライト、 フォルステライト、 ステアタイト、 結晶化ガラスのうちから選ばれた少なくとも 1 種以上を主成分とする焼結体の ¾¾¾率が 8 5 %以上であることを特徴とする項 9 8 4, 9 8
5、 9 8 6、 9 8 7、 9 8 8、 9 8 9、 9 9 0、 9 9 1又は 9 9 2に記載されたいずれかの薄 項 9 9 4. 酸化ジルコニウム、 酸化マグネシウム、 アルミン酸マグネシウム、 酸化チタン、 チタン酸バリウム、 チタン酸ジルコン 、 希土謹化物、 酸化トリウム、 各種フェライト、 ムライト、 フォルステライト、 ステアタイト、 結晶化ガラスのうちから選ばれた少なくとも 1 種以上を主成分とする焼結体に窒化ガリウム、 窒化インジウム、 窒化アルミニウムのうちから 選ばれた少なくとも 1種以上を主成分とする薄膜が形成されている薄膜基板であって、 該酸化 ジレコニゥム、酸化マグネシウム、 ァリレミン酸マグネシウム、酸化チタン、チタン酸バリウム、 チタン酸ジフレコン «、 希土 «化物、 酸ィ匕トリウム、 各種フェライト、 ムライト、 フォルス
テライト、 ステアタイト、 結晶化ガラスのうちから選ばれた少なくとも 1種以上を主成分とす る焼結体の ¾¾¾率が 1 %未満であることを特徴とする項 979、 980、 981、 982又 は 983に記載されたいずれかの薄膜基板。
項 995. 酸化ジルコニウム、 酸化マグネシウム、 アルミン酸マグネシウム、 酸化チタン、 チタン酸バリウム、 チタン酸ジルコン酸鉛、 希土 ¾化物、 酸化トリウム、 各種フェライト、 ムライト、 フォルステライト、 ステアタイト、 結晶化ガラスのうちから選ばれた少なくとも 1 種以上を主成分とする焼結体の光 率が 0%であることを特徴とする項 994に記載された 項 996. 光 性あるいは光 率が少なくとも波長 200 nm〜800 nmの範囲の光 に対してのものであることを特徴とする項 984、 985、 986、 987、 988、 989、 990、 991、 992、 993、 994又は 995に記載されたいずれかの薄膜基板。 項 997. 酸化ジルコニウム、 酸化マグネシウム、 アルミン酸マグネシウム、 酸化チタン、 チタン酸バリウム、 チタン酸ジルコン »、 希土難化物、 酸化トリウム、 各種フェライト、 ムライト、 フォルステライト、 ステアタイト、 結晶ィ匕ガラスのうちから選ばれた少なくとも 1 種以上を主成分とする焼結体の平均表面粗さが R a 1000 nm以下であることを,とする 項 979、 980、 981、 982、 983、 984、 985、 986、 987、 988、 9 89、 990、 991、 992、 993、 994、 995又は 996に記載されたいずれかの 項 998. 酸化ジルコニウム、 酸化マグネシウム、 アルミン酸マグネシウム、 酸化チタン、 チタン酸バリウム、 チタン酸ジルコン酸鉛、 希土纖化物、 酸化トリウム、 各種フェライト、 ムライト、 フォルステラィト、 ステアタイト、 結晶化ガラスのうちから選ばれた少なくとも 1 種以上を主成分とする焼結体の平均表面粗さが R a 100 nm以下であることを特徴とする項 997に記載された薄膜基板。
項 999. 酸化ジルコニウム、 酸化マグネシウム、 アルミン酸マグネシウム、 酸化チタン、 チタン酸バリウム、 チタン酸ジルコン酸鉛、 希土讓化物、 酸化トリウム、 各種フェライト、 ムライト、 フォルステライト、 ステアタイト、 結晶化ガラスのうちから選ばれた少なくとも 1 種以上を主成分とする焼結体の平均表面粗さが R a 30 nm以下であることを特徴とする項 9 97又は 998に記載されたいずれかの薄膜基板。
項 1000.酸化ジルコニウム、酸化マグネシウム、アルミン酸マグネシウム、酸化チタン、 チタン酸バリウム、 チタン酸ジルコン蘭、 希土讓化物、 酸化トリウム、 各種フェライト、 ムライト、 フォルステライト、 ステアタイト、 結晶化ガラスのうちから選ばれた少なくとも 1 種以上を主成分とする焼結体の平均表面粗さが R a 10 nm以下であることを特徴とする項 9 97、 998又は 999に記載されたいずれかの薄膜基板。
項 1001.酸化ジルコニウム、酸化マグネシウム、アルミン酸マグネシウム、酸化チタン、 チタン酸バリウム、 チタン酸ジルコン酸鉛、 希土讓化物、 酸化トリウム、 各種フヱライト、 ムライト、 フォルステライト、 ステアタイト、 結晶化ガラスのうちから選ばれた少なくとも 1 種以上を主成分とする焼結体の平均表面粗さが R a 5 nm以下であることを特徴とする項 99 7、 998、 999又は 1000に記載されたいずれかの薄膜基板。
項 1002. 表面粗さの大きい酸化ジルコニウム、 酸化マグネシウム、 アルミン酸マグネシ ゥム、酸化チタン、チタン酸バリウム、チタン酸ジルコン 、希土鍵化物、酸化トリウム、 各種フェライト、 ムライト、 フォルステライト、 ステア夕イト、 結晶化ガラスのうちから選ば れた少なくとも 1種以上を主成分とする焼結体からなることを特徴とする項 979、 980、 981、 982、 983、 984、 985、 986、 987、 988、 989、 990、 99 1、 992、 993、 994、 995、 996、 997又は 998に記載されたいずれかの薄
項 1003.酸化ジルコニウム、酸化マグネシウム、 アルミン酸マグネシウム、酸化チタン、 チタン酸バリウム、 チタン酸ジルコン麵、 希土讓化物、 酸化トリウム、 各種フェライト、 ムライト、 フォルステライト、 ステアタイト、 結晶化ガラスのうちから選ばれた少なくとも 1 種以上を主成分とする焼結体の平均表面粗さが R a 70 nm以上であることを特徴とする項 9 79、 980、 981、 982、 983、 984、 985、 986、 987、 988、 989、 990、 991、 992、 993、 994、 995、 996、 997又は 998に記載された いずれかの薄膜基板。
項 1004.酸化ジルコニウム、酸化マグネシウム、 アルミン酸マグネシウム、酸化チタン、 チタン酸バリウム、 チタン酸ジルコン酸鉛、 希土難化物、 酸化トリウム、 各種フヱライト、 ムライト、 フオレステライト、 ステア夕イト、 結晶化ガラスのうちから選ばれた少なくとも 1 種以上を主成分とする焼結体の平均表面粗さが R a 100 Onmより大きいことを特徴とする 項 1003に記載された薄膜基板。
項 1005.酸化ジルコニウム、酸化マグネシウム、アルミン酸マグネシウム、酸化チタン、 チタン酸バリウム、 チタン酸ジルコン »、 希土纖化物、 酸化トリウム、 各種フェライト、 ムライト、 フォルステライト、 ステアタイト、 結晶化ガラスのうちから選ばれた少なくとも 1 種以上を主成分とする焼結体の平均表面粗さが R a 2000 nmより大きいことを特徴とする 項 1003又は 1004に記載された薄膜基板。
項 1006.酸化ジルコニウム、酸化マグネシウム、 アルミン酸マグネシウム、酸化チタン、 チタン酸バリウム、 チタン酸ジルコン離 希土靈化物、 酸化トリウム、 各種フェライト、 ムライト、 フオルステライト、 ステアタイト、 結晶化ガラスのうちから選ばれた少なくとも 1 種以上を主成分とする焼結体の表面が焼き放し(a s-f i r e),ラッフ ¾ff磨、ブラスト研磨、 鏡面研磨、 ィ匕学腐食及びプラズマガスによる腐食のうちから選ばれた少なくともいずれかの状 態であることを特徴とする項 979 980、 981 982 983 984 985 9 86 987、 988、 989 990、 991、 992 993、 994 995 996 997 998 999 1000、 1001 1002 1003、 1004又は 1005 に記載されたいずれかの薄膜基板。
項 1007.酸化ジルコニウム、酸化マグネシウム、 アルミン酸マグネシウム、酸化チタン、 チタン酸バリウム、 チタン酸ジルコン酸鉛、 希土謹化物、 酸化トリウム、 各種フェライト、 ムライト、 フォルステライト、 ステア夕イト、 結晶ィ匕ガラスのうちから選ばれた少なくとも 1 種以上を主成分とする焼結体の表面が鏡面研磨された状態であることを ¾とする項 1006 ί己載された薄膜基板。
項 1008. セラミック材料を主成分とする焼結体及び光 ¾Μ性を有するセラミック材料を 主成分とする焼結体のうちから選ばれた少なくともいずれかの焼結体に窒化ガリウム、 窒化ィ ンジゥム、 窒化アルミニウムのうちから選ばれた少なくとも 1種以上を主成分とする薄膜が形 成されている薄膜基板であって、 該窒化ガリウム、 窒化インジウム、 窒化アルミニウムのうち から選ばれた少なくとも 1種以上を主成分とする薄膜が単結晶、 無定形、 多結晶、 配向性多結 晶のうちから選ばれる少なくともいずれかの結晶状態を有することを糊敫とする項 577, 5 78 579 580 581 582、 583 584、 585 586 587、 588 589 590 591 592、 593 594 595 596 597 598 59 9 600 601 602 603、 604 605 606 607 608 609 610 611 612 613 614 615 616、 617 618 619 62 0 621 62—2 623 624、 625 626 627 628、 629 630 631 632 633 634 635 636 637、 638 639、 640、 64
1、 642、 643、 644、 645、 646、 647、 648、 649、 650、 651、 652、 653、 654, 655、 656、 657、 658、 659、 660、 661、 66
2、 663、 664、 665、 666、 667、 668、 669、 670、 671、 672、
673、 674、 675、 676、 677、 678、 679、 680、 681、 682、 68
3、 684、 685、 686、 687、 688、 689、 690、 691、 692、 693、 694、 695、 696、 697、 698、 699、 700、 701、 702、 703、 70
4、 705、 706、 707、 708、 709、 710、 711、 712、 713、 714、 715、 716、 717、 718、 719、 720、 721、 Ί 22、 723、 724、 72
5、 726、 727、 728、 729、 730、 731、 732、 733、 734、 735、
736、 737、 738、 739、 740、 741、 742、 743、 744、 745、 74
6、 747、 748、 749、 750、 751、 752、 753、 754、 755、 756、 757、 758、 759、 760、 761、 762、 763、 764、 765、 766、 76
7、 768、 769、 770、 771、 772、 773、 774, 775、 776、 777、 778、 779、 780、 781、 782、 783、 784, 785、 786、 787、 78
8、 789、 790、 791、 792、 793、 794、 795、 796、 797、 798、
799、 800、 801、 802、 803、 804, 805、 806、 807、 808、 80
9、 810、 811、 812、 813、 814、 815、 816、 817、 818、 819、
820、 821、 822、 823、 824、 825、 826、 827、 828、 829、 83
0、 831、 832、 833、 834、 835、 836、 837、 838、 839、 840、 841、 842、 843、 844、 845、 846、 847、 848、 849、 850、 85
1、 852、 853、 854、 855、 856、 857、 858、 859、 860、 861、 862、 863、 864. 865、 866、 867、 868、 869、 870、 871、 87
2、 873、 874, 875、 876、 877、 878、 879、 880、 881、 882、
883、 884、 885、 886、 887、 888、 889、 890、 891、 892、 89
3、 894、 895、 896、 897、 898、 899、 900、 901、 902、 903、 904、 905、 906、 907、 908、 909、 910、 911、 912、 913、 91
4、 915、 916、 917、 918、 919、 920、 921、 922、 923、 924、
925、 926、 927、 928、 929、 930、 931、 932、 933、 934、 93
5、 936、 937、 938、 939、 940、 941、 942、 943、 944、 945、 946、 947、 948、 949、 950、 951、 952、 953、 954、 955、 95
6、 957、 958、 959、 960、 961、 962、 963、 964、 965、 966、 967、 968、 969、 970、 971、 972、 973、 974、 975、 976、 97
7、 978、 979、 980、 981、 982、 983、 984, 985、 986、 987、 988、 989、 990、 991、 992、 993、 994、 995、 996、 997、 99
8、 999、 1000、 1001、 1002、 1003、 1004、 1005、 1006又は 1007に記載されたいずれかの薄膜基板。
項 1009. 窒化ガリウム、 窒化インジウム、 窒化アルミニゥムのうちから選ばれた少なく とも 1種以上を主成分とする薄膜の少なくとも一部が単結晶であることを特徴とする項 100 8に記載された薄膜基板。
項 1010. 窒化ガリウム、 窒化インジウム、 窒化アルミニウムのうちから選ばれた少なく とも 1種以上を主成分とする薄膜の少なくとも一部が単結晶でありさらに無定形、 多結晶、 配 向性多結晶のうちから選ばれたいずれか少なくとも 1種以上の結晶状態を有することを特徴と する項 1008又は 1009に記載されたいずれかの薄膜基板。
項 1011. 窒化ガリウム、 窒化インジウム、 窒化アルミニウムのうちから選ばれた少なく
とも 1種以上を主成分とする薄膜がすべて単結晶であることを特徴とする項 1008、 100 9又は 1010に記載されたいずれかの薄膜基板。
項 1012. 窒化ガリウム、 窒化インジウム、 窒化アルミニウムのうちから選ばれた少なく とも 1種以上を主成分とする薄膜の少なくとも一部が無定形であることを特徴とする項 100 8、 1009又は 1010に記載されたいずれかの薄膜基板。
項 1013. 窒化ガリウム、 窒化インジウム、 窒化アルミニウムのうちから選ばれた少なく とも 1種以上を主成分とする薄膜の少なくとも一部が無定形でありさらに単結晶、 多結晶、 配 向性多結晶のうちから選ばれたいずれか少なくとも 1種以上の結晶状態を有することを特徴と する項 1012に記載された薄膜基板。
項 1014. 薄膜の全てが無定形であることを特徴とする項 681に記載された薄膜基板。 項 1015. 窒化ガリウム、 窒化インジウム、 窒化アルミニウムのうちから選ばれた少なく とも 1種以上を主成分とする薄膜の少なくとも一部が多結晶であることを特徴とする項 100 8、 1009、 1010、 1012又は 1013に記載されたいずれかの薄膜基板。
項 1016. 窒化ガリウム、 窒化インジウム、 窒化アルミニウムのうちから選ばれた少なく とも 1種以上を主成分とする薄膜の少なくとも一部が多結晶でありさらに単結晶、 無定形、 配 向性多結晶のうちから選ばれたいずれか少なくとも 1種以上の結晶状態を有することを特徴と する項 1015に記載された薄膜基板。
項 1017. 窒化ガリウム、 窒化インジウム、 窒化アルミニウムのうちから選ばれた少なく とも 1種以上を主成分とする薄膜の全てが多結晶であることを特徴とする項 684に記載され 項 1018. 窒化ガリウム、 窒化インジウム、 窒化アルミニウムのうちから選ばれた少なく とも 1種以上を主成分とする薄膜の少なくとも一部が配向性多結晶であることを特徴とする項 1008、 1009、 1010、 1012、 1013、 1015又は 1016に記載されたい ずれかの薄膜基板。
項 1019. 窒化ガリウム、 窒化インジウム、 窒化アルミニウムのうちから選ばれた少なく とも 1種以上を主成分とする薄膜の少なくとも一部が己向性多結晶でありさらに単結晶、 無定 形、 多結晶のうちから選ばれたいずれか少なくとも 1種以上の結晶状態を有することを特徴と する項 1018に記載された薄膜基板。
項 1020. 窒化ガリウム、 窒化インジウム、 窒化アルミニウムのうちから選ばれた少なく とも 1種以上を主成分とする薄膜の全てが配向性多結晶であることを ^とする項 1018に 記載された薄膜基板。
項 1021. 窒化ガリウム、 窒化インジウム、 窒化アルミニウムのうちから選ばれた少なく とも 1種以上を主成分とする薄膜の少なくとも一部が単結晶であり該薄膜の単結晶部分が窒化 アルミニウムを主成分とする焼結体に直接形成されていることを特徴とする項 1008、 10 09、 1010、 1011、 1012、 1013、 1015、 1016、 1018又は 101 9に記載されたいずれかの薄膜基板。
項 1022. 窒化ガリウム、 窒化インジウム、 窒化アルミニウムのうちから選ばれた少なく とも 1種以上を主成分とする薄膜の少なくとも^ ¾が単結晶であり該薄膜の単結晶部分が六方 晶系又は三方晶系のうちから選ばれた少なくともいずれかの結晶構造を有するセラミック材料 を主成分とする焼結体に直接形成されていることを特徴とする項 1008、 1009、 101 0、 1011、 1012、 1013、 1015、 1016、 1018又ま 1019に記載され たいずれかの薄膜基板。
項 1023. 窒化ガリウム、 窒化インジウム、 窒化アルミニウムのうちから選ばれた少なく とも 1種以上を主成分とする薄膜の少なくとも 1部が無定形、 多結晶、 配向性多結晶のうちか
ら選ばれた少なくともいずれかの結晶状態であり該薄膜の無定形、 多結晶、 配向性多結晶のう ちから選ばれた少なくともレ ^ずれかの結晶状態のものが窒化アルミ二ゥムを主成分とする焼結 体に直接形成されることを難とする項 1008、 1009、 1010、 1012、 1013、
1014、 1015、 1016、 1017、 1018、 1019、 1020又は 1021に記 載されたいずれかの薄膜基板。
項 1024. 窒化ガリウム、 窒化インジウム、 窒化アルミニウムのうちから選ばれた少なく とも 1種以上を主成分とする薄膜の少なくとも 1部が無定形、 多結晶、 配向性多結晶のうちか ら選ばれた少なくともいずれかの結晶状態であり該薄膜の無定形、 多結晶、 配向性多結晶のう ちから選ばれた少なくともレゝずれかの結晶状態のものが六方晶系又は三方晶系のうちから選ば れた少なくともいずれかの結晶構造を有するセラミック材料を主成分とする焼結体に直接形成 されることを特徴とする項 1008、 1009、 1010、 1012、 1013、 1014、
1015、 1016、 1017、 1018、 1019、 1020又は 1022に記載されたい ずれかの薄膜基板。
項 1025. 窒化ガリウム、 窒化インジウム、 窒化アルミニウムのうちから選ばれた少なく とも 1種以上を主成分とする薄膜の少なくとも 1部が無定形、 多結晶、 配向性多結晶のうちか ら選ばれた少なくともいずれかの結晶状態であり該薄膜の無定形、 多結晶、 配向性多結晶のう ちから選ばれた少なくともいずれかの結晶状態のものが光 ¾1性を有するセラミック材料を主 成分とする焼結体に直接形成されることを « [とする項 1008、 1009、 1010、 10 12、 1013、 1014、 1015、 1016、 1017、 1018、 1019又は 102 0に記載されたいずれかの薄膜基板。
項 1026. 形成されている窒化ガリウム、 窒化インジウム、 窒化アルミニウムのうちから 選ばれた少なくとも 1種以上を主成分とする薄膜が単一層であることを特徴とする項 577、 578、 579、 580、 581、 582、 583、 584、 585、 586、 587、 58
8、 589、 590、 591、 592、 593、 594、 595、 596、 597、 598、
599、 600、 601、 602、 603、 604, 605、 606、 607、 608、 60
9、 610、 611、 612、 613、 614、 615、 616、 617、 618、 619、
620、 621、 622、 623、 624、 625、 626、 627、 628、 629、 63
0、 631、 632、 633、 634、 635、 636、 637、 638、 639、 640、 641、 642、 643、 644、 645、 646、 647、 648、 649、 650、 65
1、 652、 653、 654、 655、 656、 657、 658、 659、 660、 661、 662、 663、 664、 665、 666、 667、 668、 669、 670、 671、 67
2、 673、 674, 675、 676、 677、 678、 679、 680、 681、 682、
683、 684、 685、 686、 687、 688、 689、 690、 691、 692、 69
3、 694, 695、 696、 697、 698、 699、 700、 701、 702、 703、 704、 705、 706、 707、 708、 709、 710、 711、 712、 713、 71
4、 715、 716、 717、 718、 719、 720、 721、 722、 723、 724、
725、 726、 727、 728、 729、 730、 731、 732、 733、 734、 73
5、 736、 737、 738、 739、 740、 741、 742、 743、 744、 745、 746、 747、 748、 749、 750、 751、 752、 753、 754、 755、 75
6、 757、 758、 759、 760、 761、 762、 763、 764, 765、 766、 767、 768、 769、 770、 771、 772、 773、 774, 775、 776、 77
7、 778、 779、 780、 781、 782、 783、 784, 785、 786、 787、 788、 789、 .790、 791、 792、 793、 794, 795、 796、 797、 79
8、 799、 800、 801、 802、 803、 804、 805、 806、 807、 808、
809、 810、 811、 812、 813、 814、 815、 816、 817、 818、 81 9、 820、 821、 822、 823、 824、 825、 826、 827、 828、 829、 830、 831、 832、 833、 834、 835、 836、 837、 838、 839、 84
0、 841、 842、 843、 844、 845、 846、 847、 848、 849、 850、 851、 852、 853、 854、 855、 856、 857、 858、 859、 860、 86
1、 862、 863、 864, 865、 866、 867、 868、 869、 870、 871、 872、 873、 874, 875、 876、 877、 878、 879、 880、 881、 88
2、 883、 884, 885、 886、 887、 888、 889、 890、 891、 892、
893、 894、 895、 896、 897、 898、 899、 900、 901、 902、 90
3、 904、 905、 906、 907、 908、 909、 910、 911、 912、 913、 914、 915、 916、 917、 918、 919、 920、 921、 922、 923、 92
4、 925、 926、 927、 928、 929、 930、 931、 932、 933、 934、
935、 936、 937、 938、 939、 940、 941、 942、 943、 944、 94
5、 946、 947、 948、 949、 950、 951、 952、 953、 954、 955、 956、 957、 958、 959、 960、 961、 962、 963、 964、 965、 96
6、 967、 968、 969、 970、 971、 972、 973、 974、 975、 976、
977、 978、 979、 980、 981、 982、 983、 984, 985、 986、 98
7、 988、 989、 990、 991、 992、 993、 994、 995、 996、 997、 998、 999、 1000、 1001、 1002、 1003、 1004、 1005、 1006、 1007、 1008、 1009、 1010、 1011、 1012、 1013、 1014、 10 15、 1016、 1017、 1018、 1019、 1020、 1021、 1022、 1023、
1024又は 1025に記載されたいずれかの薄膜基板。
項 1027. 形成されている窒化ガリウム、 窒化インジウム、 窒化アルミニウムのうちから 選ばれた少なくとも 1種以上を主成分とする薄膜が少なくとも 2以上の層から構成されている ことを特徴とする項 577、 578、 579、 580、 581、 582、 583、 584、 5 85、 586、 587、 588、 589、 590、 591、 592、 593、 594、 595、
596、 597、 598、 599、 600、 601、 602、 603、 604、 605、 60
6、 607、 608、 609、 610、 611、 612、 613、 614、 615、 616、 617、 618、 619、 620、 621、 622、 623、 624、 625、 626、 62
7、 628、 629、 630、 631、 632、 633、 634、 635、 636、 637、
638、 639、 640、 641、 642、 643、 644、 645、 646、 647、 64
8、 649、 650、 651、 652、 653、 654、 655、 656、 657、 658、 659、 660、 661、 662、 663、 664, 665、 666、 667、 668、 66
9、 670、 671、 672、 673、 674、 675、 676、 677、 678、 679、
680、 681、 682、 683、 684、 685、 686、 687、 688、 689、 69
0、 691、 692、 693、 694、 695、 696、 697、 698、 699、 700、 701、 702、 703、 704, 705、 706、 707、 708、 709、 710、 71
1、 712、 713、 714, 715、 716、 717、 718、 719、 720、 721、
722、 723、 724、 725、 726、 727、 728、 729、 730、 731、 73
2、 733、 734、 735、 736、 737、 738、 739、 740、 741、 742、 743、 744、 745、 746、 747、 748、 749、 750、 751、 752、 75
3、 754, 755、 756、 757、 758、 759、 760、 761、 762、 763、 764、 765、 766、 767、 768、 769、 770、 771、 772、 773、 77
4、 775、 776、 777、 778、 779、 780、 781、 782、 783、 784、
785, 786、 787、 788、 789、 790、 791、 792、 793、 794、 79
5、 796、 797、 798、 799、 800、 801、 802、 803、 804、 805、
806、 807、 808、 809、 810、 811、 812、 813、 814、 815、 81
6、 817、 818、 819、 820、 821、 822、 823、 824, 825、 826、 827、 828、 829、 830、 831、 832、 833、 834、 835、 836、 83
7、 838、 839、 840、 841、 842、 843、 844、 845、 846、 847、 848、 849、 850、 851、 852、 853、 854、 855、 856、 857、 85
8、 859、 860、 861、 862、 863、 864、 865、 866、 867、 868、 869、 870、 871、 872、 873、 874、 875、 876、 877、 878、 87
9、 880、 881、 882、 883、 884、 885、 886、 887、 888、 889、
890、 891、 892、 893、 894、 895、 896、 897、 898、 899、 90
0、 901、 902、 903、 904、 905、 906、 907、 908、 909、 910、 911、 912、 913、 914、 915、 916、 917、 918、 919、 920、 92
1、 922、 923、 924、 925、 926、 927、 928、 929、 930、 931、
932、 933、 934、 935、 936、 937、 938、 939、 940、 941、 94
2、 943、 944、 945、 946、 947、 948、 949、 950、 951、 952、 953、 954、 955、 956、 957、 958、 959、 960、 961、 962、 96
3、 964、 965、 966、 967、 968、 969、 970、 971、 972、 973、 974, 975、 976、 977、 978、 979、 980、 981、 982、 983、 98
4、 985、 986、 987、 988、 989、 990、 991、 992、 993、 994、
995、 996、 997、 998、 999、 1000、 1001、 1002、 1003、 10 04、 1005、 1006、 1007、 1008、 1009、 1010、 1011、 1012、
,1013、 1014、 1015、 1016、 1017、 1018、 1019、 1020、 10 21、 1022、 1023、 1024又は 1025に記載されたいずれかの薄膜基板。
項 1028. 少なくとも 2以上の層から構成されている薄膜のうち少なくとも 2層がそれぞ れ組成が異なるかあるいはそれぞれ結晶状態が異なるか少なくともいずれかであることを特徴 とする項 1027に記載された薄膜基板。
項 1029. 少なくとも 2以上の層から構成されている薄膜のうち少なくとも 2層がそれぞ れ異なる組成であることを ^とする項 1027又は 1028に記載されたいずれかの薄膜基 板。
項 1030. 少なくとも 2以上の層から構成されている薄膜のうち少なくとも 2層がそれぞ れ異なる組成で力、つ結晶状態は同じであることを特徴とする項 1027、 1028又は 102 9に記載されたいずれかの薄膜基板。
項 1031. 少なくとも 2以上の層から構成されている薄膜のうち少なくとも 2層がそれぞ れ異なる組成でかつ結晶状態も異なることを特徴とする項 1027、 1028、 1029又は
1030に記載されたいずれかの薄膜基板。
項 1032. 少なくとも 2以上の層から構成されている薄膜のうち少なくとも 2層が同じ組 成であることを特徴とする項 1027又は 1028に記載されたいずれかの薄膜基板。
項 1033. 少なくとも 2以上の層から構成されている薄膜のうち少なくとも 2層が同じ組 成で結晶状態はそれぞれ異なることを特徴とする項 1027、 1028又は 1032に記載さ れたいずれかの薄膜基板。
項 1034. 少なくとも 2以上の層から構成されている薄膜のうち少なくとも 2層がそれぞ れ同じ組成でかつ同じ結晶状態であることを特徴とする項 1027に記載された薄膜基板。 項 1035. 少なくとも 2以上の層から構成されている薄膜の各層がそれぞ l^結晶、 配向
性多結晶、 多結晶、 無定形の中から選ばれた少なくともいずれかの結晶状態を有することを特 徴とする項 1027、 1028、 1029、 1030、 1031、 1032、 1033又は1 034に記載されたいずれかの薄膜基板。
項 1036. 少なくとも 2以上の層から構成されている薄膜においてセラミック材料を主成 分とする焼結体及び光透過性を有するセラミック材料を主成分とする焼結体に直接形成されて いる薄膜層が単結晶、 配向性多結晶、 多結晶、 無定形の中から選ばれた少なくともいずれかの 結晶状態を有するものであることを特徴とする項 1027、 1028、 1029、 1030、 1031、 1032、 1033、 1034又は 1035に記載されたいずれかの薄膜基板。 項 1037. 少なくとも 2以上の層から構成されている薄膜においてセラミック材料を主成 分とする焼結体及び光 ¾i性を有するセラミツク材料を主成分とする焼結体に直接形成されて いる薄膜層が己向性多結晶、 多結晶、 無定形の中から選ばれた少なくともいずれかの結晶状態 を有するものであることを特徴とする項 1036に記載されたいずれかの薄膜基板。
項 1038. 少なくとも 2以上の層から構成されている薄膜においてセラミック材料を主成 分とする焼結体及び光 ¾性を有するセラミツク材料を主成分とする焼結体に直接形成されて いる薄膜層がB向性多結晶であることを特徴とする項 1036又は 1037に記載されたいず れかの薄膜基板。
項 1039. 少なくとも 2以上の層から構成されている薄膜においてセラミック材料を主成 分とする焼結体及び光透過性を有するセラミック材料を主成分とする焼結体に窒化ガリウム、 窒化ィンジゥム、 窒化アルミニウムのうちから選ばれた少なくとも 1種以上を主成分とする単 結晶、 配向性多結晶、 多結晶、 無定形のうちから選ばれる少なくともいずれかの結晶状態を有 する薄膜が少なくとも 1層以上形成され さらにその上に窒化ガリウム、 窒化インジウム、 窒 化アルミニウムのうちから選ばれた少なくとも 1種以上を主成分とする単結晶薄膜が少なくと も 1層以上形成されていることを體とする項 1027、 1028、 1029、 1030、 1 031、 1032、 1033、 1034、 1035、 1036、 1037又は 1038に記載 されたいずれかの薄膜基板。
項 1040. 少なくとも 2以上の層から構成されている薄膜においてセラミック材料を主成 分とする焼結体及び光 性を有するセラミック材料を主成分とする焼結体に窒化ガリゥム、 窒化ィンジゥム、 窒化アルミ二ゥムのうちから選ばれた少なくとも 1種以上を主成分とする配 向性多結晶、 多結晶、 無定形のうちから選ばれる少なくともいずれかの結晶状態を有する薄膜 が少なくとも 1層以上形成され、 さらにその上に窒化ガリウム、 窒化インジウム、 窒化アルミ ニゥムのうちから選ばれた少なくとも 1種以上を主成分とする単結晶薄膜が少なくとも 1層以 上形成されていることを特徴とする項 1039に記載された薄膜基板。
項 1041. 少なくとも 2以上の層から構成されている薄膜においてセラミック材料を主成 分とする焼結体及び光¾^ '生を有するセラミック材料を主成分とする焼結体に窒化ガリウム、 窒化インジウム、 窒化アルミニウムのうちから選ばれた少なくとも 1種以上を主成分とする無 定形薄膜が少なくとも 1層以上形成され さらにその上に窒化ガリウム、 望化インジウム、 窒 化アルミニウムのうちから選ばれた少なくとも 1種以上を主成分とする単結晶薄膜が少なくと も 1層以上形成されていることを特徴とする項 1039又は 1040に記載されたいずれかの 項 1042. 少なくとも 2以上の層から構成されている薄膜においてセラミック材料を主成 分とする焼結体、及び ¾¾¾性を有するセラミック材料を主成分とする條結体に窒化ガリゥム、 窒化ィンジゥム窒化アルミニウムのうちから選ばれた少なくとも 1種以上を主成分とする多結 晶薄膜が少なくとも 1層以上形成され、 さらにその上に窒化ガリウム、 室化インジウム、 窒化 アルミニウムのうちから選ばれた少なくとも 1種以上を主成分とする単結晶薄膜が少なくとも
層以上形成されていることを,とする項 1039又は 1040に記載されたいずれかの薄 項 1043. 少なくとも 2以上の層から構成されている薄膜においてセラミック材料を主成 分とする焼結体及び光透過性を有するセラミック材料を主成分とする焼結体に窒化ガリウム、 窒化インジウム、 窒化アルミニウムのうちから選ばれた少なくとも 1種以上を主成分とする配 向性多結晶薄膜が少なくとも 1層以上形成され、 さらにその上に窒化ガリゥム、 窒化ィンジゥ ム、 窒化アルミニウムのうちから選ばれた少なくとも 1種以上を主成分とする単結晶薄膜が少 なくとも 1層以上形成されていることを特徴とする項 1039又は 1040に記載されたいず れかの薄膜基板。
項 1044. 少なくとも 2以上の層から構成されている薄膜のなかでセラミック材料を主成 分とする焼結体及び ¾¾i性を有するセラミック材料を主成分とする焼結体に形成される該薄 膜が少なくとも 1層以上の単結晶薄膜層を有する薄膜において、 該単結晶薄翻は少なくとも 2以上の層からなることを特徴とする項 1027、 1028、 1029、 1030、 1031、 1032、 1033、 1034、 1035、 1036、 1037、 1038、 1039、 10 40、 1041、 1042又は 1043に記載されたいずれかの薄膜基板。
項 1045. 少なくとも 2以上の層から構成されてレる薄膜においてセラミック材料を主成 分とする焼結体及び光透過性を有するセラミック材料を主成分とする焼結体に窒化ガリゥム、 窒化インジウム、 窒化アルミニウムのうちから選ばれた少なくとも 1種以上を主成分とする単 結晶、 配向性多結晶、 多結晶、 無定形のうちから選ばれる少なくともいずれかの結晶状態を有 する薄膜が少なくとも 1層以上形成され、 さらにその上に窒化ガリウム、 窒化インジウム、 窒 化アルミニウムのうちから選ばれた少なくとも 1種以上を主成分とする単結晶、配向性多結晶、 多結晶、 無定形のうちから選ばれる少なくともいずれかの結晶状態を有する薄膜が少なくとも 1層以上形成されていることを特徴とする項 1027、 1028、 1029、 1030、 10 31、 1032、 1033、 1034、 1035、 1036、 1037、 1038、 1039、 1040、 1041、 1042、 1043又は 1044に記載されたいずれかの薄膜基板。 項 1046. 少なくとも 2以上の層から構成されている薄膜においてセラミック材料を主成 分とする焼結体及び光透過性を有するセラミック材料を主成分とする焼結体に窒化ガリゥム、 窒化インジウム、 窒化アルミニウムのうちから選ばれた少なくとも 1種以上を主成分とする単 結晶、 配向性多結晶、 多結晶、 無定形のうちから選ばれる少なくともいずれかの結晶状態を有 する薄膜が少なくとも 1層以上形成され さらにその上に窒化ガリウム、 窒化インジウム、 窒 化アルミニウムのうちから選ばれた少なくとも 1種以上を主成分とする単結晶、配向性多結晶、 多結晶、 無定形のうちから選ばれる少なくともいずれかの結晶状態を有する薄膜が少なくとも 1層以上形成され、 さらにその上に窒化ガリウム、 窒化インジウム、 窒化アルミニウムのうち から選ばれた少なくとも 1種以上を主成分とする単結晶薄膜が少なくとも 1層以上形成されて いることを體とする項 1027、 1028、 1029、 1030、 1031、 1032、 1 033、 1034、 1035、 1036、 1037、 1038、 1039、 1040、 104
1、 1042、 1043、 1044又は 1045に記載されたいずれかの薄膜基板。
項 1047. 少なくとも 2以上の層から構成されている薄膜においてすベての層が単結晶だ けから構成されていることを特徴とする項 1027、 1028、 1029、 1030、 103
2、 1034、 1035、 1036、 1039又は 1044に記載されたいずれかの薄膜基板。 項 1048. 窒化ガリウム、 窒化インジウム、 窒化アルミニウムのうちから選ばれた少なく とも 1種以上を主成分とする単結晶薄膜が基板の表面に形成されていることを特徴とする項 5 77、 578、 579、 580、 581、 582、 583、 584、 585、 586、 587、 588、 589、 590、 591、 592、 593、 594、 595、 596、 597、 59
8、 599、 600、 601、 602、 603、 604、 605、 606、 607、 608、 609、 610、 611、 612、 613、 614, 615、 616、 617、 618、 61
9、 620、 621、 622、 623、 624、 625、 626、 627、 628、 629、 630、 631、 632、 633、 634、 635、 636、 637、 638、 639、 64
0、 641、 642、 643、 644、 645、 646、 647、 648、 649、 650、 651、 652、 653、 654、 655、 656、 657、 658、 659、 660、 66
1、 662、 663、 664、 665、 666、 667、 668、 669、 670、 671、 672、 673、 674, 675、 676、 677、 678、 679、 680、 681、 68
2、 683、 684, 685、 686、 687、 688、 689、 690、 691、 692、
693、 694、 695、 696、 697、 698、 699、 700、 701、 702、 70
3、 704、 705、 706、 707、 708、 709、 710、 711、 712、 713、
714、 715、 716、 717、 718、 719、 720、 721、 722、 723、 72
4、 725、 726、 727、 728、 729、 730、 731、 732、 733、 734、 735、 736、 737、 738、 739、 740、 741、 742、 743、 744、 74
5、 746、 747、 748、 749、 750、 751、 752、 753、 754、 755、 756、 757、 758、 759、 760、 761、 762、 763、 764、 765、 76
'6、 767、 768、 769、 770、 771、 772、 773、 774、 775、 776、 777、 778、 779、 780、 781、 782、 783、 784、 785、 786、 78
7、 788、 789、 790、 791、 792、 793、 794, 795、 796、 797、
798、 799、 800、 801、 802、 803、 804、 805、 806、 807、 80
8、 809、 810、 811、 812、 813、 814、 815、 816、 817、 818、 819、 820、 821、 822、 823、 824、 825、 826、 827、 828、 82
9、 830、 831、 832、 833、 834、 835、 836、 837、 838、 839、 840、 841、 842、 843、 844、 845、 846、 847、 848、 849、 85
0、 851、 852、 853、 854, 855、 856、 857、 858、 859、 860、 861、 862、 863、 864、 865、 866、 867、 868、 869、 870、 87
1、 872、 873、 874, 875、 876、 877、 878、 879、 880、 881、
882、 883、 884、 885、 886、 887、 888、 889、 890、 891、 89
2、 893、 894, 895、 896、 897、 898、 899、 900、 901、 902、
903、 904、 905、 906、 907、 908、 909、 910、 911、 912、 91
3、 914、 915、 916、 917、 918、 919、 920、 921、 922、 923、 924, 925、 926、 927、 928、 929、 930、 931、 932、 933、 93
4、 935、 936、 937、 938、 939、 940、 941、 942、 943、 944、 945、 946、 947、 948、 949、 950、 951、 952、 953、 954、 95
5、 956、 957、 958、 959、 960、 961、 962、 963、 964、 965、 966、 967、 968、 969、 970、 971、 972、 973、 974, 975、 97
6、 977、 978、 979、 980、 981、 982、 983、 984、 985、 986、 987、 988、 989、 990、 991、 992、 993、 994、 995、 996、 99
7、 998、 999、 1000、 1001、 1002、 1003、 1004、 1005、 10 06、 1007、 1008、 1009、 1010、 1011、 1012、 1013、 1014、 1015、 1016、 1017、 1018、 1019、 1020、 1021、 1022、 10 23、 1024、 1025、 1026、 1027、 1028、 1029、 1030、 1031、 1032、 1033、 1034、 1035、 1036、 1037、 1038、 1039、 10 40、 1041、 1042、 1043、 1044、 1045、 1046又は 1047に記載さ
れたいずれかの雞基板。
項 1049. 窒化ガリウム、 窒化インジウム、 窒化アルミニウムのうちから選ばれた少なく とも 1種以上を主成分とする単結晶薄膜の C軸が基板面に対して垂直な方向に形成されている ことを特徴とする項 577、 578、 579、 580、 581、 582、 583、 584、 5 85、 586、 587、 588、 589、 590、 591、 592、 593、 594、 595、
596、 597、 598、 599、 600、 601、 602、 603、 604、 605、 60
6、 607、 608、 609、 610、 611、 612、 613、 614、 615、 616、 617、 618、 619、 620、 621、 622、 623、 624、 625、 626、 62
7、 628、 629、 630、 631、 632、 633、 634, 635、 636、 637、
638、 639、 640、 641、 642、 643、 644、 645、 646、 647、 64
8、 649、 650、 651、 652、 653、 654、 655、 656、 657、 658、 659、 660、 661、 662、 663、 664、 665、 666、 667、 668、 66
9、 670、 671、 672、 673、 674、 675、 676、 677、 678、 679、
680、 681、 682、 683、 684、 685、 686、 687、 688、 689、 69
0、 691、 692、 693、 694、 695、 696、 697、 698、 699、 700、 701、 702、 703、 704, 705、 706、 707、 708、 709、 710、 71
1、 712、 713、 714、 715、 716、 717、 718、 719、 720、 721、
722、 723、 724、 725、 726、 727、 728、 729、 730、 731、 73
2、 733、 734、 735、 736、 737、 738、 739、 740、 741、 742、 743、 744、 745、 746、 747、 748、 749、 750、 751、 752、 75
3、 754s 755、 756、 757、 758、 759、 760、 761、 762、 763、 764, 765、 766、 767、 768、 769、 770、 771、 772、 773、 77
4、 775、 776、 777、 778、 779、 780、 781、 782、 783、 784、
785、 786、 787、 788、 789、 790、 791、 792、 793、 794, 79
5、 796、 797、 798、 799、 800、 801、 802、 803、 804、 805、
806、 807、 808、 809、 810、 811、 812、 813、 814、 815、 81
6、 817、 818、 819、 820、 821、 822、 823、 824、 825、 826、 827、 828、 829、 830、 831、 832、 833、 834、 835、 836、 83
7、 838、 839、 840、 841、 842、 843、 844、 845、 846、 847、 848、 849、 850、 851、 852、 853、 854、 855、 856、 857、 85
8、 859、 860、 861、 862、 863、 864、 865、 866、 867、 868、 869、 870、 871、 872、 873、 874, 875、 876、 877、 878、 87
9、 880、 881、 882、 883、 884, 885、 886、 887、 888、 889、
890、 891、 892、 893、 894、 895、 896、 897、 898、 899、 90
0、 901、 902、 903、 904、 905、 906、 907、 908、 909、 910、 911、 912、 913、 914、 915、 916、 917、 918、 919、 920、 92
1、 922、 923、 924、 925、 926、 927、 928、 929、 930、 931、
932、 933、 934、 935、 936、 937、 938、 939、 940、 941、 94
2、 943、 944、 945、 946、 947、 948、 949、 950、 951、 952、 953、 954、 955、 956、 957、 958、 959、 960、 961、 962、 96
3、 964、 965、 966、 967、 968、 969、 970、 971、 972、 973、 974, 975、 976、 977、 978、 979、 980、 981、 982、 983、 98
4、 985、 986、 987、 988、 989、 990、 991、 992、 993、 994、 995、 996、 997、 998、 999、 1000、 1001、 1002、 1003、 10
04、 1005、 1006、 1007、 1008、 1009、 1010、 1011、 1012、 1013、 1014、 1015、 1016、 1017、 1018、 1019、 1020、 10 21、 1022、 1023、 1024, 1025、 1026、 1027、 1028、 1029、 1030、 1031、 1032、 1033、 1034、 1035、 1036、 1037、 10 38、 1039、 1040、 1041、 1042、 1043、 1044、 1045、 1046、 1047又は 1048に記載されたいずれかの薄膜基板。
項 1050. 窒化ガリウム、 窒化インジウム、 窒化アルミニウムのうちから選ばれた少なく とも 1種以上を主成分とする単結晶薄膜の C軸が基板面に対して水平な方向に形成されている ことを特徴とする項 577、 578、 579、 580、 581、 582、 583、 584、 5 85、 586、 587、 588、 589、 590、 591、 592、 593、 594、 595、
596、 597、 598、 599、 600、 601、 602、 603、 604、 605、 60
6、 607、 608、 609、 610、 611、 612、 613、 614, 615、 616、 617、 618、 619、 620、 621、 622、 623、 624、 625、 626、 62
7、 628、 629、 630、 631、 632、 633、 634、 635、 636、 637、
638、 639、 640、 641、 642、 643、 644、 645、 646、 647、 64
8、 649、 650、 651、 652、 653、 654、 655、 656、 657、 658、 659、 660、 661、 662、 663、 664、 665、 666、 667、 668、 66
9、 670、 671、 672、 673、 674, 675、 676、 677、 678、 679、
680、 681、 682、 683、 684、 685、 686、 687、 688、 689、 69
0、 691、 692、 693、 694、 695、 696、 697、 698、 699、 700、 701、 702、 703、 704, 705、 706、 707、 708、 709、 710、 71
1、 712、 713、 714、 715、 716、 717、 718、 719、 720、 721、
722、 723、 724、 725、 726、 727、 728、 729、 730、 731、 73
2、 733、 734、 735、 736、 737、 738、 739、 740、 741、 742、 743、 744、 745、 746、 747、 748、 749、 750、 751、 752、 75
3、 754、 755、 756、 757、 758、 759、 760、 761、 762、 763、 764、 765、 766、 767、 768、 769、 770、 771、 772、 773、 77
4、 775、 776、 777、 778、 779、 780、 781、 782、 783、 784、
785、 786、 787、 788、 789、 790、 791、 792、 793、 794, 79
5、 796、 797、 798、 799、 800、 801、 802、 803、 804、 805、
806、 807、 808、 809、 810、 811、 812、 813、 814、 815、 81
6、 817、 818、 819、 820、 821、 822、 823、 824, 825、 826、 827、 828、 829、 830、 831、 832、 833、 834、 835、 836、 83
7、 838、 839、 840、 841、 842、 843、 844、 845、 846、 847、 848、 849、 850、 851、 852、 853、 854、 855、 856、 857、 85
8、 859、 860、 861、 862、 863、 864, 865、 866、 867、 868、 869、 870、 871、 872、 873、 874, 875、 876、 877、 878、 87
9、 880、 881、 882、 883、 884, 885、 886、 887、 888、 889、
890、 891、 892、 893、 894、 895、 896、 897、 898、 899、 90
0、 901、 902、 903、 904、 905、 906、 907、 908、 909、 910、 911、 912、 913、 914、 915、 916、 917、 918、 919、 920、 92
1、 922、 923、 924, 925、 926、 927、 928、 929、 930、 931、
932、 933、 934、 935、 936、 937、 938、 939、 940、 941、 94
2、 943、 944、 945、 946、 947、 948、 949、 950、 951、 952、
953、 954, 955、 956、 957、 958、 959、 960、 961、 962、 96
3、 964, 965、 966、 967、 968、 969、 970、 971、 972、 973、 974、 975、 976、 977、 978、 979、 980、 981、 982、 983、 98
4、 985、 986、 987、 988、 989、 990、 991、 992、 993、 994、
995、 996、 997、 998、 999、 1000、 1001、 1002、 1003、 10 04、 1005、 1006、 1007、 1008、 1009、 1010、 1011、 1012、 1013、 1014、 1015、 1016、 1017、 1018、 1019、 1020、 10 21、 1022、 1023、 1024、 1025、 1026、 1027、 1028、 1029、 1030、 1031、 1032、 1033、 1034、 1035、 1036、 1037、 10 38、 1039、 1040、 1041、 1042、 1043、 1044、 1045、 1046、
1047又は 1048に記載されたいずれかの薄膜基板。
項 1051. 窒化ガリウム、 窒化インジウム、 窒化アルミニウムのうちから選ばれた少なく とも 1種以上を主成分とする配向性多結晶薄膜の C軸が基板面に対して垂直な方向に形成され ていることを特徴とする項 577、 578、 579、 580、 581、 582、 583、 58
4、 585、 586、 587、 588、 589、 590、 591、 592、 593、 594、
595、 596、 597、 598、 599、 600、 601、 602、 603、 604、 60.
5、 606、 607、 608、 609、 610、 611、 612、 613、 614、 615、 616、 617、 618、 619、 620、 621、 622、 623、 624、 625、 62
6、 627、 628、 629、 630、 631、 632、 633、 634, 635、 636、
637、 638、 639、 640、 641、 642、 643、 644、 645、 646、 64
7、 648、 649、 650、 651、 652、 653、 654、 655、 656、 657、 658、 659、 660、 661、 662、 663、 664, 665、 666、 667、 66
8、 669、 670、 671、 672、 673、 674、 675、 676、 677、 678、
679、 680、 681、 682、 683、 684、 685、 686、 687、 688、 68
9、 690、 691、 692、 693、 694、 695、 696、 697、 698、 699、
700、 70 1、 702、 703、 704、 705、 706、 707、 708、 709、 71
0、 711、 712、 713、 714、 715、 716、 7 17、 718、 719、 720、 721、 722、 723、 724、 725、 726、 727, 728、 729、 730、 73
1、 732、 733、 734、 735、 736、 737、 738、 739、 740、 741、 742、 743、 744、 745、 746、 747、 748、 749、 750、 751、 75
2、 753、 754、 755、 756、 757、 758、 759、 760、 761、 762、 763、 764, 765、 766、 767、 768、 769、 770、 771、 772、 77
3、 774、 775、 776、 777、 778、 779、 780、 781、 782、 783、
784, 785、 786、 787、 788、 789、 790、 791、 792、 793、 79
4、 795、 796、 797、 798、 799、 800、 801、 802、 803、 804、
805、 806、 807、 808、 809、 810、 811、 812、 813、 814、 81
5、 816、 817、 818、 819、 820、 821、 822、 823、 824、 825、 826、 827、 828、 829、 830、 831、 832、 833、 834、 835、 83
6、 837、 838、 839、 840、 841、 842、 843、 844、 845、 846、 847、 848、 849、 850、 851、 852、 853、 854、 855、 856、 85
7、 858、 859、 860、 861、 862、 863、 864、 865、 866、 867、 868、 869、 870、 871、 872、 873、 874、 875、 876、 877、 87
8、 879、 880、 881、 882、 883、 884. 885、 886、 887、 888、 889、 890、 891、 892、 893、 894、 895、 896、 897、 898、 89
9、 900、 901、 902、 903、 904、 905、 906、 907、 908、 909、 910、 911、 912、 913、 914、 915、 916、 917、 918、 919、 92
0、 921、 922、 923、 924, 925、 926、 927、 928、 929、 930、 931、 932、 933、 934、 935、 936、 937、 938、 939、 940、 94
1、 942、 943、 944、 945、 946、 947、 948、 949、 950、 951、 952、 953、 954, 955、 956、 957、 958、 959、 960、 961、 96
2、 963、 964、 965、 966、 967、 968、 969、 970、 971、 972、 973、 974、 975、 976、 977、 978、 979、 980、 981、 982、 98
3、 984、 985、 986、 987、 988、 989、 990、 991、 992、 993、 994、 995、 996、 997、 998、 999、 1000、 1001、 1002、 100
3、 1004、 1005、 1006、 1007、 1008、 1009、 1010、 1011、 1012、 1013、 1014、 1015、 1016、 1017、 1018、 1019、 10 20、 1021、 1022、 1023、 1024、 1025、 1026、 1027、 1028、 1029、 1030、 1031、 1032、 1033、 1034、 1035、 1036、 10 37、 1038、 1039、 1040、 1041、 1042、 1043、 1044、 1045、 1046、 1047又は 1048に記載されたいずれかの薄膜基板。
項 1052. 窒化ガリウム、 窒化インジウム、 窒化アルミニウムのうちから選ばれた少なく とも 1種以上を主成分とする配向性多結晶薄膜の C軸が基板面に対して水平な方向に形成され ていることを特徴とする項 577、 578、 579、 580、 581、 582、 583、 58
4、 585、 586、 587、 588、 589、 590、 591、 592、 593、 594、
595、 596、 597、 598、 599、 600、 601、 602、 603、 604、 60
5、 606、 607、 608、 609、 610、 611、 612、 613、 614、 615、 616、 617、 618、 619、 620、 621、 622、 623、 624、 625、 62
6、 627、 628、 629、 630、 631、 632、 633、 634、 635、 636、
637、 638、 639、 640、 641、 642、 643、 644、 645、 646、 64
7、 648、 649、 650、 651、 652、 653、 654、 655、 656、 657、 658、 659、 660、 661、 662、 663、 664、 665、 666、 667、 66
8、 669、 670、 671、 672、 673、 674, 675、 676、 677、 678、
679、 680、 681、 682、 683、 684、 685、 686、 687、 688、 68
9、 690、 691、 692、 693、 694, 695、 696、 697、 698、 699、
700、 701、 702、 703、 704, 705、 706、 707、 708、 709、 71
0、 711、 712、 713、 714、 715、 716、 717、 718、 719、 720、 721、 722、 723、 724、 725、 726、 727、 728、 729、 730、 73
1、 732、 733、 734、 735、 736、 737、 738、 739、 740、 741、 742、 743、 744、 745、 746、 747、 748、 749、 750、 751、 75
2、 753、 754, 755、 756、 757、 758、 759、 760、 761、 762、 763、 764, 765、 766、 767、 768、 769、 770、 771、 772、 77
3、 774, 775、 776、 777、 778、 779、 780、 781、 782、 783、
784, 785、 786、 787、 788、 789、 790、 791、 792、 793、 79
4、 795、 796、 797、 798、 799、 800、 801、 802、 803、 804、
805、 806、 807、 808、 809、 810、 811、 812、 813、 814、 81
5、 816、 817、 818、 819、 820、 821、 822、 823、 824、 825、 826、 827、 828、 829、 830、 831、 832、 833、 834、 835、 83
6、 837、 838、 839、 840、 841、 842、 843、 844、 845、 846、
847、 848、 849、 850、 851、 852、 853、 854、 855、 856、 85
7、 858、 859、 860、 861、 862、 863、 864, 865、 866、 867、 868、 869、 870、 871、 872、 873、 874、 875、 876、 877、 87
8、 879、 880、 881、 882、 883、 884, 885、 886、 887、 888、
889、 890、 891、 892、 893、 894、 895、 896、 897、 898、 89
9、 900、 901、 902、 903、 904、 905、 906、 907、 908、 909、 910、 911、 912、 913、 914、 915、 916、 917、 918、 919、 92
0、 921、 922、 923、 924, 925、 926、 927、 928、 929、 930、 931、 932、 933、 934、 935、 936、 937、 938、 939、 940、 94
1、 942、 943、 944、 945、 946, 947、 948、 949、 950、 951、
952、 953、 954, 955、 956、 957、 958、 959、 960、 961、 96
2、 963、 964、 965、 966、 967、 968、 969、 970、 971、 972、 973、 974、 975、 976、 977、 978、 979、 980、 981、 982、 98
3、 984、 985、 986、 987、 988、 989、 990、 991、 992、 993、 994、 995、 996、 997、 998、 999、 1000、 1001、 1002、 100 3、 1004、 1005、 1006、 1007、 1008、 1009、 1010、 1011、 1012、 1013、 1014、 1015、 1016、 1017、 1018、 1019、 10 20、 1021、 1022、 1023、 1024、 1025、 1026、 1027、 1028、 1029、 1030、 1031、 1032、 1033、 1034、 1035、 1036、 10 37、 1038、 1039、 1040、 1041、 1042、 1043、 1044、 1045、 1046、 1047又は 1048に記載されたいずれかの薄膜基板。
項 1053. 形成されている窒化ガリウム、 窒化インジウム、 窒化アルミニウムのうちから 選ばれた少なくとも 1種以上を主成分とする薄膜が導電性を有することを特徴とする項 577、 578、 579、 580、 581、 582、 583、 584, 585、 586、 587、 58
8、 589、 590、 591、 592、 593、 594、 595、 596、 597、 598、
599、 600、 601、 602、 603、 604、 605、 606、 607、 608、 60
9、 610、 611、 612、 613、 614、 615、 616、 617、 618、 619、
620、 621、 622、 623、 624, 625、 626、 627、 628、 629、 63
0、 631、 632、 633、 634、 635、 636、 637、 638、 639、 640、 641、 642、 643、 644、 645、 646、 647、 648、 649、 650、 65
1、 652、 653、 654、 655、 656、 657、 658、 659、 660、 661、 662、 663、 664, 665、 666、 667、 668、 669、 670、 671、 67
2、 673、 674, 675、 676、 677、 678、 679、 680、 681、 682、
683、 684、 685、 686、 687、 688、 689、 690、 691、 692、 69
3、 694, 695、 696、 697、 698、 699、 700、 701、 702、 703、 704、 705、 706、 707、 708、 709、 710、 711、 712、 713、 71
4、 715、 716、 717、 718、 719、 720、 721、 722、 723、 724、
725、 726、 727、 728、 729、 730、 731、 732、 733、 734, 73
5、 736、 737、 738、 739、 740、 741、 742、 743、 744、 745、 746、 747、 748、 749、 750、 751、 752、 753、 754、 755、 75
6、 757、 758、 759、 760、 761、 762、 763、 764、 765、 766、 767、 768、 769、 770、 771、 772、 773、 774, 775、 776、 77
7、 778、 779、 780、 781、 782、 783、 784, 785、 786、 787、 788、 789、 790、 791、 792、 793、 794、 795、 796、 797、 79
8、 799、 800、 801、 802、 803、 804、 805、 806、 807、 808、 809、 810、 811、 812、 813、 814、 815、 816、 817、 818、 81
9、 820、 821、 822、 823、 824, 825、 826、 827、 828、 829、 830、 831、 832、 833、 834、 835、 836、 837、 838、 839、 84
0、 841, 842、 843、 844、 845、 846、 847、 848、 849、 850、 851、 852、 853、 854、 855、 856、 857、 858、 859、 860、 86
1、 862、 863、 864、 865、 866、 867、 868、 869、 870、 871, 872、 873、 874. 875、 876、 877、 878、 879、 880、 881、 88
2、 883、 884, 885、 886、 887、 888、 889、 890、 891、 892、
893、 894、 895、 896、 897、 898、 899、 900、 901、 902、 90
3、 904、 905、 906、 907、 908、 909、 910、 911、 912、 913、
914, 915、 916、 917、 918、 919、 920、 921、 922、 923、 92
4、 925、 926、 927、 928、 929、 930、 931、 932、 933、 934、 935、 936、 937、 938、 939、 940、 941、 942、 943、 944、 94
5、 946、 947、 948、 949、 950、 951、 952、 953、 954、 955、 956、 957、 958、 959、 960、 961、 962、 963、 964, 965、 96
6、 967、 968、 969、 970、 971、 972、 973、 974、 975、 976、 977、 978、 979、 980、 981、 982、 983、 984、 985、 986、 98
7、 988、 989、 990、 991、 992、 993、 994、 995、 996、 997、 998、 999、 1000、 1001、 1002、 1003、 1004、 1005、 1006、 1007、 1008、 1009、 1010、 1011、 1012、 1013、 1014、 10 15、 1016、 1017、 1018、 1019、 1020、 1021、 1022、 1023、 1024、 1025、 1026、 1027、 1028、 1029、 1030、 1031、 10 32、 1033、 1034、 1035、 1036、 1037、 1038、 1039、 1040、 1041、 1042、 1043、 1044、 1045、 1046、 1047、 1048、 10 49、 1050、 1051又は 1052に記載されたいずれかの薄膜基板。
項 1054. 窒化ガリウム、 窒化インジウム、 窒化アルミニウムのうちから選ばれた少なく とも 1種以上を主成分とする薄膜が半導体化されることで導電性を有していることを特徴とす る項 1053に記載された薄膜基板。
項 1055. 窒化ガリウム、 窒化インジウム、 窒化アルミニウムのうちから選ばれた少なく とも 1種以上を主成分とする薄膜がマグネシウム、 ベリリウム、 カルシウム、 亜鉛、 力ドミゥ ム、 炭素、 珪素、 ゲルマニウム、 セレン、 テルル、 酸素のうちから選ばれた少なくとも 1種以 上のドーピング剤により導電性を有していることを特徴とする項 1053又は 1054に記載 されたいずれかの薄膜基板。
項 1056. 窒化ガリウム、 窒化インジウム、 窒化アルミニウムのうちから選ばれた少なく とも 1種以上を主成分とする薄膜が P型あるいは N型に半導体化され導電性を有していること を特徴とする項 1053、 1054又は 1055に記載されたいずれかの薄膜基板。
項 1057. 窒化ガリウム、 窒化インジウム、 窒化アルミニウムのうちから選ばれた少なく とも 1種以上を主成分とする薄膜が少なくとも 2以上の層で構成されているもののうち少なく とも 1層が導電性を有することを繊とする項 1027、 1028、 1029、 1030、 1 031、 1032、 1033、 1034、 1035、 1036、 1037、 1038、 103 9、 1040、 1041、 1042、 1043、 1044、 1045、 1046、 1047、 1048、 1049、 1050、 1051、 1052、 1053、 1054、 1055又は 1 056に記載されたいずれかの薄膜基板。
項 1058. 導電性を有する窒化ガリウム、 窒化インジウム、 窒化アルミニウムのうちから 選ばれた少なくとも 1種以上を主成分とする薄膜の室温における抵抗率が 1 X 104Ω . cm以 下であることを特徴とする項 1053、 1054、 1055、 1056又は 1057に記載さ れたいずれかの薄膜基板。
項 1059. 導電性を有する窒化ガリウム、 窒化インジウム、 窒化アルミニウムのうちから 選ばれた少なくとも 1種以上を主成分とする薄膜の室温における抵抗率が 1 X 102Ω · cm以 下であることを特徴とする項 1058に記載された薄膜基板。
項 1060. 導電性を有する窒化ガリウム、 窒化インジウム、 窒化アルミニウムのうちから 選ばれた少なくとも 1種以上を主成分とする薄膜の室温における ί厳率が 1 XI O^- cm以 下であることを特徴とする項 1058又は 1059に記載されたいずれかの薄膜基板。
項 1061. 導電性を有する窒化ガリウム、 窒化インジウム、 窒化アルミニウムのうちから 選ばれた少なくとも 1種以上を主成分とする薄膜の室温における抵抗率が 1 X 10。Ω · cm以 下であることを とする項 1058、 1059又は 1060に記載されたいずれかの薄膜基 板。
項 1062.
(0≤χ≤1. 0) の化学式であらわさ れる組成物を主成分とするものであることを特徴とする項 577、 578、 579、 580、 581、 582、 583、 584、 585、 586、 587、 588、 589、 590、 59
1、 592、 593、 594、 595、 596、 597、 598、 599、 600、 601、 602、 603、 604、 605、 606、 607、 608、 609、 610、 611、 61
2、 613、 614、 615、 616、 617、 618、 619、 620、 621、 622、 623、 624、 625、 626、 627、 628、 629、 630、 631、 632、 63
3、 634、 635、 636、 637、 638、 639、 640、 641、 642、 643、 644、 645、 646、 647、 648、 649、 650、 651、 652、 653、 65
4、 655、 656、 657、 658、 659、 660、 661、 662、 663、 664、 665、 666、 667、 668、 669、 670、 671、 672、 673、 674. 67
5、 676、 677、 678、 679、 680、 681、 682、 683、 684、 685、
686、 687、 688、 689、 690、 691、 692、 693、 694、 695、 69
6、 697、 698、 699、 700、 701、 702、 703、 704、 705、 706、
707、 708、 709、 710、 711、 712、 713、 714、 715、 716、 71
7、 718、 719、 720、 721、 722、 723、 724、 725、 726, 727、 728、 729、 730、 731、 732、 733、 734、 735、 736、 737、 73
8、 739、 740、 741、 742、 743、 744、 745、 746、 747、 748、 749、 750、 751、 752、 753、 754、 755、 756、 757、 758、 75
9、 760、 761、 762、 763、 764、 765、 766、 767、 768、 769、
770、 771、 772、 773、 774、 775、 776, 777、 778、 779、 78
0、 781、 782、 783、 784、 785、 786、 787、 788、 789、 790、 791、 792、 793、 794, 795、 796、 797、 798、 799、 800、 80
1、 802、 803、 804、 805、 806、 807、 808、 809、 810、 811、 812、 813、 814、 815、 816、 817、 818、 819、 820、 821、 82
2、 823、 824, 825、 826、 827、 828、 829、 830、 831、 832、
833、 834、 835、 836、 837、 838、 839、 840、 841、 842、 84
3、 844、 845、 846、 847、 848、 849、 850、 851、 852、 853、 854、 855、 856、 857、 858、 859、 860、 861、 862、 863、 86
4、 865, 866、 867、 868、 869、 870、 871、 872、 873、 874、
875、 876、 877、 878、 879、 880、 881、 882、 883、 884, 88
5、 886、 887、 888、 889、 890、 891、 892、 893、 894、 895、
896、 897、 898、 899、 900、 901、 902、 903、 904、 905、 90
6、 907、 908、 909、 910、 911、 912、 913、 914、 915、 916、 917、 918、 919、 920、 921、 922、 923、 924、 925、 926、 92
7、 928、 929、 930、 931、 932、 933、 934、 935、 936、 937、
938、 939、 940、 941、 942、 943、 944、 945、 946、 947、 94
8、 949、 950、 951、 952、 953、 954、 955、 956、 957、 958、 959、 960、 961、 962、 963、 964、 965、 966、 967、 968、 96
9、 970、 971、 972、 973、 974、 975、 976、 977、 978、 979、 980、 981、 982、 983、 984、 985、 986、 987、 988、 989、 99 0、 991、 992、 993、 994, 995、 996、 997、 998、 999、 1000、 1001、 1002、 1003、 1004、 1005、 1006、 1007、 1008、 10 09、 1010、 1011、 1012、 1013、 1014、 1015、 1016、 1017、 1018、 1019、 1020、 1021、 1022、 1023、 1024、 1025、 10 26、 1027、 1028、 1029、 1030、 1031、 1032、 1033、 1034、 1035、 1036、 1037、 1038、 1039、 1040、 1041、 1042、 10 43、 1044、 1045、 1046、 1047、 1048、 1049、 1050、 1051、 1052、 1053、 1054、 1055、 1056、 1057、 1058、 1059、 10 60又は 1061に記載されたいずれかの薄膜基板。
項 1063.
(0≤χ≤1. 0) の化学式であらわさ れる組成物を主成分としさらにドーピング成分を該組成物に対して元素換算で 0 - 00001 〜10モル%の範囲で含むものであることを特徴とする項 1062に記載された薄膜基板。 項 1064. 形成されている薄膜が A 1 xGai一
ΧΝ (0≤χ≤0. 6) での化学式あらわさ れる組成物を主成分とするものであることを特徴とする項 1062又は 1063に記載された いずれかの薄膜基板。
項 1065. 形成されている薄膜が AlxGai一 ΧΝ (0≤χ≤0. 6) での化学式あらわさ れる組成物を主成分としさらにドーピング成分を該組成物に対して元素換算で 0. 00001 〜10モル%の範囲で含むものであることを特徴とする項 1064に記載された薄膜基板。 項 1066. 形成されている薄膜が A 1 xGai一 ΧΝ (0. 6≤χ≤1. 0) の化学式であら わされる組成物を主成分とするものであることを特徴とする項 1062又は 1063に記載さ れたいずれかの薄膜基板。
項 1067. 形成されている薄膜が AlxGai— ΧΝ (0. 6≤χ≤1. 0) の化学式であら わされる組成物を主成分としさらにドーピング成分を ¾且成物に対して元素購で 0. 000 01〜10モル%の範囲で含むものであることを特徴とする項 1066に記載された薄膜基板。 項 1068. ドーピング成分を少なくとも 2種以上同時に含有することを特徴とする項 10 62、 1063、 1064、 1065、 1066又は 1067に記載されたいずれかの薄膜基 板。
項 1069. ドーピング成分が Mg、 Be、 Ca、 Zn、 Cd、 (:、 S i、 Ge、 Se、 T e、〇のうちから選ばれた少なくとも 1種以上であることを ^[とする項 1063、 1065、 1067又は 1068に記載されたいずれかの薄膜基板。
項 1070. ドーピング成分が Mg、 Be、 Zn、 S iのうちから選ばれた少なくとも 1種 以上であることを特徴とする項 1069に記載された薄膜基板。
項 1071. 形成されている薄膜が Aし Ga — XN (0≤x≤0. 6) の化学式であらわさ
れる組成物を主成分としさらに Mg、 Zn、 S iのうちから選ばれた少なくとも 1種以上の成 分を該組成物に対して 0· 0001〜; L 0モル%の範囲で含むものであることを特徴とする項 1062、 1063、 1064、 1065、 1068、 1069又は 1070に記載されたい ずれかの薄膜基板。
項 1072.
(0≤x≤0. 6) の化学式であらわさ れる組成物を主成分としさらに該組成物に対して M g、 Zn、 S iのうちから選ばれた少なく ともいずれか 2種以上の成分を同時に合計で 0. 0001〜 10モル%の範囲で含むものであ ることを特徴とする項 1071に記載された薄膜基板。
項 1073.
(0. 6≤x≤l. 0) の化学式であら わされる組成物を主成分としさらに M且成物に対して Mg、 Zn、 S iのうちから選ばれた少 なくとも 1種以上の成分を合計で元素換算で 0. 00001〜 10モル%の範囲で含むもので あることを體とする項 1062、 1066、 1067、 1068、 1069又は 1070に 記載されたいずれかの薄膜基板。
項 1074. 形成されている薄膜が AlxGa — XN (0. 6≤x≤l. 0) の化学式であら わされる組成物を主成分としさらに識且成物に対して Mg、 Zn、 S iのうちから選ばれた少 なくともいずれか 2種以上の成分を同時に合計で元素換算で 0. 00001〜: L 0モル%の範 囲で含むものであることを特徴とする項 1073に記載された薄膜基板。
項 1075.
(0. 6≤x≤l. 0) の化学式であら わされる組成物を主成分としさらに S iを薩成物に対して元素換算で 0. 00001〜 0. 5モル%の範囲で含むものであることを特徴とする項 1073又は 1074に記載されたいず れかの薄膜基板。
項 1076. 表面の薄膜が平均表面粗さ Ra 2 Onm以下であることを體とする項 577、 578、 579、 580、 581、 582、 583、 584、 585、 586、 587、 58
8、 589、 590、 591、 592、 593、 594、 595、 596、 597、 598、
599、 600、 601、 602、 603、 604, 605、 606、 607、 608、 60
9、 610、 611、 612、 613、 614、 615、 616、 617、 618、 619、
620、 621、 622、 623、 624、 625、 626、 627、 628、 629、 63
0、 631、 632、 633、 634、 635、 636、 637、 638、 639、 640、 641、 642、 643、 644、 645、 646、 647、 648、 649、 650、 65
1、 652、 653、 654、 655、 656、 657、 658、 659、 660、 661、 662、 663、 664、 665、 666、 667、 668、 669、 670、 671、 67
2、 673、 674、 675、 676、 677、 678、 679、 680、 681、 682、
683、 684, 685、 686、 687、 688、 689、 690、 691、 692、 69
3、 694、 695、 696、 697、 698、 699、 700、 701、 702、 703、 704、 705、 706、 707、 708、 709、 710、 711、 712、 713、 71
4、 715、 716、 717、 718、 719、 720、 721、 722、 723、 724、
725、 726、 727、 728、 729、 730、 731、 732、 733、 734、 73
5、 736、 737、 738、 739、 740、 741、 742、 743、 744、 745、 746、 747、 748、 749、 750、 751、 752、 753、 754、 755、 75
6、 757、 758、 759、 760、 761、 762、 763、 764, 765、 766、 767、 768、 769、 770、 771、 772、 773、 774, 775、 776、 77
7、 778、 779、 780、 781、 782、 783、 784、 785、 786、 787、 788、 789、 790、 791、 792、 793、 794、 795、 796、 797、 79
8、 799、 800、 801、 802、 803、 804、 805、 806、 807、 808、
809、 810、 811、 812、 813、 814、 815、 816、 817、 818、 81 9、 820、 821、 822、 823、 824, 825、 826、 827、 828、 829、 830、 831、 832、 833、 834、 835、 836、 837、 838、 839、 84
0、 841、 842、 843、 844、 845、 846、 847、 848、 849、 850、 851、 852、 853、 854, 855、 856、 857、 858、 859、 860、 86
1、 862、 863、 864, 865、 866、 867、 868、 869、 870、 871、 872、 873、 874、 875、 876、 877、 878、 879、 880、 881、 88
2、 883、 884, 885、 886、 887、 888、 889、 890、 891、 892、
893、 894、 895、 896、 897、 898、 899、 900、 901、 902、 90
3、 904, 905、 906、 907、 908、 909、 910、 911、 912、 913、 914、 915、 916、 917、 918、 919、 920、 921、 922、 923、 92
4、 925、 926、 927、 928、 929、 930、 931、 932、 933、 934、
935、 936、 937、 938、 939、 940、 941、 942、 943、 944、 94
5、 946、 947、 948、 949、 950、 951、 952、 953、 954、 955、 956、 957、 958、 959、 960、 961、 962、 963、 964、 965、 96
6、 967、 968、 969、 970、 971、 972、 973、 974、 975、 976、 977、 978、 979、 980、 981、 982、 983、 984、 985、 986、 98
7、 988、 989、 990、 991、 992、 993、 994、 995、 996、 997、
998、 999、 1000、 1001、 1002、 1003、 1004、 1005、 1006、 1007、 1008、 1009、 1010、 1011、 1012、 1013、 1014、 10 15、 1016、 1017、 1018、 1019、 1020、 1021、 1022、 1023、 1024、 1025、 1026、 1027、 1028、 1029、 1030、 1031、 10 32、 1033、 1034、 1035、 1036、 1037、 1038、 1039、 1040、 1041、 1042、 1043、 1044、 1045、 1046、 1047、 1048、 10 49、 1050、 1051、 1052、 1053、 1054、 1055、 1056、 1057、 1058、 1059、 1060、 1061、 1062、 1063、 1064、 1065、 10 66、 1067、 1068、 1069、 1070、 1071、 1072、 1073、 1074 又は 1075に記載されたいずれかの薄膜基板。
項 1077. 表面の薄膜が平均表面粗さ R a 10 nm以下であることを特徴とする項 107 6に記載された薄膜基板。
項 1078. 表面の薄膜が平均表面粗さ R a 5 nm以下であることを特徴とする項 1076 又は 1077に記載されたいずれかの薄膜基板。
項 1079. 表面の薄膜が平均表面粗さ R a 3 nm以下であることを [とする項 1076、
1077又は 1078に記載されたいずれかの薄膜基板。
項 1080.表面の薄膜が平均表面粗さ R a 2 nm以下であることを體とする項 1076、 1077、 1078又は 1079に記載されたいずれかの薄膜基板。
項 1081. 表面の薄膜が平均表面粗さ R a 1 nm以下であることを體とする項 1076、 1077、 1078、 1079又は 1080に記載されたいずれかの薄膜基板。
項 1082.形成されている薄膜の厚みが 0. 5 nm以上であることを とする項 577、 578、 579、 580、 581、 582、 583、 584、 585、 586、 587、 58
8、 589、 590、 591、 592、 593、 594、 595、 596、 597、 598、
599、 600、 601、 602、 603、 604、 605、 606、 607、 608、 60
9、 610、 611、 612、 613、 614、 615、 616、 617、 618、 619、
620、 621、 622、 623、 624, 625、 626、 627、 628、 629、 63
0、 631、 632、 633、 634、 635、 636、 637、 638、 639、 640、 641、 642、 643、 644、 645、 646、 647、 648、 649、 650、 65
1、 652、 653、 654, 655、 656、 657、 658、 659、 660、 661、 662、 663、 664, 665、 666、 667、 668、 669、 670、 671、 67
2、 673、 674. 675、 676、 677、 678、 679、 680、 681、 682、
683、 684、 685、 686、 687、 688、 689、 690、 691、 692、 69
3、 694、 695、 696、 697、 698、 699、 700、 701、 702、 703、 704、 705、 706、 707、 708、 709、 710、 711、 712、 713、 71
4、 715、 716、 717、 718、 719、 720、 721、 722、 723、 724、
725、 726、 727、 728、 729、 730、 731、 732、 733、 734, 73
5、 736、 737、 738、 739、 740、 741、 742、 743、 744、 745、 746、 747、 748、 749、 750、 751、 752、 753、 754、 755、 75
6、 757、 758、 759、 760、 761、 762、 763、 764, 765、 766、 767、 768、 769、 770、 771、 772、 773、 774、 775、 776、 77
7、 778、 779、 780、 781、 782、 783、 784, 785、 786、 787、
788、 789、 790、 791、 792、 793、 794、 795、 796、 797、 79
8、 799、 800、 801、 802、 803、 804, 805、 806、 807、 808、
809、 810、 811、 812、 813、 814、 815、 816、 817、 818、 81
9、 820、 821、 822、 823、 824、 825、 826、 827、 828、 829、 830、 831、 832、 833、 834、 835、 836、 837、 838、 839、 84
0、 841、 842、 843、 844、 845、 846、 847、 848、 849、 850、 851、 852、 853、 854, 855、 856、 857、 858、 859、 860、 86
1、 862、 863、 864、 865、 866、 867、 868、 869、 870、 871、 872、 873、 874, 875、 876、 877、 878、 879、 880、 881、 88
2、 883、 884、 885、 886、 887、 888、 889、 890、 891、 892、
893、 894, 895、 896、 897、 898、 899、 900、 901、 902、 90
3、 904、 905、 906、 907、 908、 909、 910、 911、 912、 913、 914、 915、 916、 917、 918、 919、 920、 921、 922、 923、 92
4、 925、 926、 927、 928、 929、 930、 931、 932、 933、 934、
935、 936、 937、 938、 939、 940、 941、 942、 943、 944、 94
5、 946、 947、 948、 949、 950、 951、 952、 953、 954、 955、 956、 957、 958、 959、 960、 961、 962、 963、 964、 965、 96
6、 967、 968、 969、 970、 971、 972、 973、 974、 975、 976、 977、 978、 979、 980、 981、 982、 983、 984、 985、 986、 98
7、 988、 989、 990、 991、 992、 993、 994、 995、 996、 997、 998、 999、 1000、 1001、 1002、 1003、 1004、 1005、 1006、 1007、 1008、 1009、 1010、 1011、 1012、 1013、 1014、 10 15、 1016、 1017、 1018、 1019、 1020、 1021、 1022、 1023、 1024、 1025、 1026、 1027、 1028、 1029、 1030、 1031、 10 32、 1033、 1034、 1035、 1036、 1037、 1038、 1039、 1040、 1041、 1042、 1043、 1044、 1045、 1046、 1047、 1048、 10 49、 1050、 1051、 1052、 1053、 1054、 1055、 1056、 1057、 1058、 1059、 1060、 1061、 1062、 1063、 1064、 1065、 10 66、 1067、 1068、 1069、 1070、 1071、 1072、 1073、 1074、
1075、 1076、 1077、 1078、 1079、 1080又は 1081に記載されたい ずれかの薄膜基板。
項 1083. 形成されている薄膜の厚みが 0. 3 m以上であることを特徴とする項 108 2に記載された薄膜基板。
項 1084. 形成されている薄膜の厚みが 3. 以上であることを i [とする項 108
2又は 1083に記載されたいずれかの薄膜基板。
項 1085. 形成されている薄膜の厚みが 10 xm以上であることを ^とする項 1082、 1083又は 1084に記載されたいずれかの薄膜基板。
項 1086. 形成されている薄膜の厚みが 50 m以上であることを鎌とする項 1082、 1083、 1084又は 1085に記載されたいずれかの薄膜基板。
項 1087. 形成されている薄膜の厚みが 1000 以下であることを特徴とする項 57
7、 578、 579、 580、 581、 582、 583、 584、 585、 586、 587、
588、 589、 590、 591、 592、 593、 594、 595、 596、 597、 59
8、 599、 600、 601、 602、 603、 604、 605、 606、 607、 608、
609、 610、 611、 612、 613、 614、 615、 616、 617、 618、 61
9、 620、 621、 622、 623、 624、 625、 626、 627、 628、 629、 630、 631、 632、 633、 634、 635、 636、 637、 638、 639、 64
0、 641、 642、 643、 644、 645、 646、 647、 648、 649、 650、 651、 652、 653、 654, 655、 656、 657、 658、 659、 660、 66
1、 662、 663、 664, 665、 666、 667、 668、 669、 670、 671、 672、 673、 674, 675、 676、 677、 678、 679、 680、 681、 68
2、 683、 684, 685、 686、 687、 688、 689、 690、 691、 692、
693、 694、 695、 696、 697、 698、 699、 700、 701、 702、 70
3、 704, 705、 706、 707、 708、 709、 710、 711、 712、 713、 714、 715、 716、 717、 718、 719、 720、 721、 Ί 22、 723、 72
4、 725、 726、 727、 728、 729、 730、 731、 732、 733、 734、
735、 736、 737、 738、 739、 740、 741、 742、 743、 744、 74
5、 746、 747、 748、 749、 750、 751、 752、 753、 754、 755、 756、 757、 758、 759、 760、 761、 762、 763、 764、 765、 76
6、 767、 768、 769、 770、 771、 772、 773、 774, 775、 776、 777、 778、 779、 780、 781、 782、 783、 784、 785、 786、 78
7、 788、 789、 790、 791、 792、 793、 794, 795、 796、 797、
798、 799、 800、 801、 802、 803、 804、 805、 806、 807、 80
8、 809、 810、 811、 812、 813、 814、 815、 816、 817、 818、 819、 820、 821、 822、 823、 824、 825、 826、 827、 828、 82
9、 830、 831、 832、 833、 834、 835、 836、 837、 838、 839、
840、 841、 842、 843、 844、 845、 846、 847、 848、 849、 85
0、 851、 852、 853、 854、 855、 856、 857、 858、 859、 860、 861、 862、 863、 864、 865、 866、 867、 868、 869、 870、 87
1、 872、 873、 874, 875、 876、 877、 878、 879、 880、 881、
882、 883、 884、 885、 886、 887、 888、 889、 890、 891、 89
2、 893、 894, 895、 896、 897、 898、 899、 900、 901、 902、
903、 904、 905、 906、 907、 908、 909、 910、 911、 912、 91
3、 914、 915、 916、 917、 918、 919、 920、 921、 922、 923、
924、 925、 926、 927、 928, 929, 930、 931、 932、 933、 93
4、 935、 936、 937、 938、 939、 940、 941、 942、 943、 944、 945、 946、 947、 948、 949、 950、 951、 952、 953、 954、 95
5、 956、 957、 958、 959、 960、 961、 962、 963、 964、 965、 966、 967、 968、 969、 970、 971、 972、 973、 974、 975、 97
6、 977、 978、 979、 980、 981、 982、 983、 984、 985、 986、
987、 988、 989、 990、 991, 992、 993、 994、 995、 996、 99
7、 998、 999、 1000、 1001、 1002、 1003、 1004、 1005、 10 06、 1007、 1008、 1009、 1010、 1011、 1012、 1013、 1014、 1015、 1016、 1017、 1018、 1019、 1020、 1021、 1022、 10 23、 1024、 1025、 1026、 1027、 1028、 1029、 1030、 1031、 1032、 1033、 1034、 1035、 1036、 1037、 1038、 1039、 10 40、 1041、 1042、 1043、 1044、 1045、 1046、 1047、 1048、 1049、 1050、 1051、 1052、 1053、 1054、 1055、 1056、 10 57、 1058、 1059、 1060、 1061、 1062、 1063、 1064、 1065、 1066、 1067、 1068、 1069、 1070、 1071、 1072、 1073、 10 74、 1075、 1076、 1077、 1078、 1079、 1080又は 1081に記載さ れたいずれかの薄膜基板。
項 1088. 薄膜がそれぞれの厚み 1000 以下の薄 l Sからなることを特徴とする項 1087に記載された薄膜基板。
項 1089. 薄藤すべての厚みが 1000 m以下であることを特徴とする項 1087又 は 1088に記載されたいずれかの薄膜基板。
項 1090. 薄膜の厚みが 500 m以下であることを特徴とする項 1087、 1088又 は 1089に記載されたいずれかの薄膜基板。
項 1091. 薄膜がそれぞれの厚み 500 m以下の薄膜層からなることを とする項 1 090に記載された薄膜基板。
項 1092. 薄 すべての厚みが 500 zm以下であることを特徴とする項 1090又は
1091に記載されたいずれかの薄膜基板。
項 1093. 薄膜の厚みが 300 満であることを特徴とする項 1087、 1088、 1089、 1090、 1091又は 1092に記載されたいずれかの薄膜基板。
項 1094. 薄膜がそれぞれの厚み 300 zm未満の薄膜層からなることを特徴とする項 1 093に記載された薄膜基板。
項 1095. 薄 すべての厚みが 300 m未満であることを i [とする項 1093又は 1094に記載されたいずれかの薄膜基板。
項 1096. 薄膜の厚みが 200 以下であることを特徴とする項 1087、 1088、 1089、 1090、 1091、 1092、 1093、 1094又は 1095に記載されたい ずれかの薄膜基板。
項 1097. 薄膜がそれぞれの厚み 200 以下の薄膜層からなることを特徴とする項 1
096に記載された薄膜基板。
項 1098. 薄 すべての厚みが 200 m以下であることを特徴とする項 1096又は
1097に記載されたいずれかの薄膜基板。
項 1099. 形成されている窒化ガリウム、 窒化インジウム、 窒化アルミニウムのうちから 選ばれた少なくとも 1種以上を主成分とする単結晶薄膜のミラ一指数 (002) の格子面の X 線回折ロッキングカーブの半値幅が 3600秒以下であることを樹敫とする項 577、 578、
579、 580、 581、 582、 583、 584、 585、 586、 587、 588、 58 9、 590、 591、 592、 593、 594、 595、 596、 597、 598、 599、
600、 601、 602、 603、 604、 605、 606、 607、 608、 609、 61
0、 611、 612、 613、 614、 615、 616、 617、 618、 619、 620、 621、 622、 623、 624、 625、 626、 627、 628、 629、 630、 63
1、 632、 633、 634、 635、 636、 637、 638、 639、 640、 641、 642、 643、 644、 645、 646、 647、 648、 649、 650、 651、 65
2、 653、 654, 655、 656、 657、 658、 659、 660、 661、 662、
663、 664、 665、 666、 667、 668、 669、 670、 671、 672、 67
3、 674, 675、 676、 677、 678、 679、 680、 681、 682、 683、 684、 685、 686、 687、 688、 689、 690、 691、 692、 693、 69
4、 695、 696、 697、 698、 699、 700、 701、 702、 703、 704、
705、 706、 707、 708、 709、 710、 711、 712、 713、 714、 71
5、 716、 717、 718、 719、 720、 721、 722、 723、 724、 725、 726、 727、 728、 729、 730、 731、 732、 733、 734、 735、 73
6、 737、 738、 739、 740、 741、 742、 743、 744、 745、 746、 747、 748、 749、 750、 751、 752、 753、 754、 755、 756、 75
7、 758、 759、 760、 761、 762、 763、 764、 765、 766、 767、 768、 769、 770、 771、 772、 773、 774、 775、 776、 777、 77
8、 779、 780、 781、 782、 783、 784、 785、 786、 787、 788、
789、 790、 791、 792、 793、 794、 795、 796、 797、 798、 79
9、 800、 801、 802、 803、 804、 805、 806、 807、 808、 809、 810、 811、 812、 813、 814、 815、 816、 817、 818、 819、 82
0、 821、 822、 823、 824、 825、 826、 827、 828、 829、 830、 831、 832、 833、 834、 835、 836、 837、 838、 839、 840、 84
1、 842、 843、 844、 845、 846、 847、 848、 849、 850、 851、
852、 853、 854, 855、 856、 857、 858、 859、 860、 861、 86
2、 863、 864、 865、 866、 867、 868、 869、 870、 871、 872、
873、 874, 875、 876、 877、 878、 879、 880、 881、 882、 88
3、 884、 885、 886、 887、 888、 889、 890、 891、 892、 893、 894、 895、 896、 897、 898、 899、 900、 901、 902、 903、 90
4、 905、 906、 907、 908、 909、 910、 911、 912、 913、 914、 915、 916、 917、 918、 919、 920、 921、 922、 923、 924、 92
5、 926、 927、 928、 929、 930、 931、 932、 933、 934、 935、
936、 937、 938、 939、 940、 941、 942、 943、 944、 945、 94
6、 947、 948、 949、 950、 951、 952、 953、 954、 955、 956、 957、 958、 959、 960、 961、 96.2、 963、 964、 965、 966、 96
7、 968、 969、 970、 971、 972、 973、 974, 975、 976、 977、 978、 979、 980、 981、 982、 983、 984、 985、 986、 987、 98
8、 989、 990、 991、 992、 993、 994、 995、 996、 997、 998、 999、 1000、 1001、 1002、 1003、 1004、 1005、 1006、 100 7、 1008、 1009、 1010、 1011、 1012、 1013、 1014、 1015、 1016、 1017、 1018、 1019、 1020、 1021、 1022、 1023、 10 24、 1025、 1026、 1027、 1028、 1029、 1030、 1031、 1032、
1033、 1034、 1035、 1036、 1037、 1038、 1039、 1040、 10 41、 1042、 1043、 1044、 1045、 1046、 1047、 1048、 1049、 1050、 1051、 1052、 1053、 1054、 1055、 1056、 1057、 10 58、 1059、 1060、 1061、 1062、 1063、 1064、 1065、 1066、 1067、 1068、 1069、 1070、 1071、 1072、 1073、 1074、 10 75、 1076、 1077、 1078、 1079、 1080、 1081、 1082、 1083、 1084、 1085、 1086、 1087、 1088、 1089、 1090、 1091、 10 92、 1093、 1094、 1095、 1096、 1097又は 1098に記載されたいずれ かの薄膜基板。
項 1100. 形成されている窒化ガリウム、 窒化インジウム、 窒化アルミニウムのうちから 選ばれた少なくとも 1種以上を主成分とする単結晶薄膜のミラ一指数 (002) の格子面の X 線回折ロッキングカーブの半値幅が 300秒以下であることを特徴とする項 1099に記載さ れた薄膜基板。
項 1101. 形成されている窒化ガリウム、 窒化インジウム、 窒化アルミニウムのうちから 選ばれた少なくとも 1種以上を主成分とする単結晶薄膜のミラ一指数 (002) の格子面の X 線回折ロッキングカーブの半値幅が 240秒以下であることを特徴とする項 1099又は 11 00に記載されたいずれかの薄膜基板。
項 1102. 形成されている窒化ガリウム、 窒化インジウム、 窒化アルミニウムのうちから 選ばれた少なくとも 1種以上を主成分とする単結晶薄膜のミラー指数 (002) の格子面の X 線回折ロッキングカーブの半値幅が 200秒以下であることを特徴とする項 1099、 110 0又は 1101に記載されたいずれかの薄膜基板。
項 1103. 形成されている窒化ガリウム、 窒化インジウム、 窒化アルミニウムのうちから 選ばれた少なくとも 1種以上を主成分とする単結晶薄膜のミラー指数 (002) の格子面の X 線回折ロッキング力一ブの半値幅が 150秒以下であることを特徴とする項 1099、 110 0、 1101又は 1102に記載されたいずれかの薄膜基板。
項 1104. 形成されている窒化ガリウム、 窒化インジウム、 窒化アルミニウムのうちから 選ばれた少なくとも 1種以上を主成分とする単結晶薄膜のミラー指数 (002) の格子面の X 線回折ロッキングカーブの半値幅が 130秒以下であることを特徴とする項 1099、 110 0、 1101、 1102又は 1103に記載されたいずれかの薄膜基板。
項 1105. 形成されている窒化ガリウム、 窒化インジウム、 窒化アルミニウムのうちから 選ばれた少なくとも 1種以上を主成分とする単結晶薄膜のミラ一指数 (002) の格子面の X 線回折ロッキング力一ブの半値幅が 100秒以下であることを特徴とする項 1099、 110 0、 1101、 1102、 1103又は 1104に記載されたいずれかの薄膜基板。
項 1106. セラミック材料を主成分とする焼結体及び光 ¾ii性を有するセラミック材料を 主成分とする焼結体のうちから選ばれた少なくともいずれかの焼結体に窒化ガリウム、 窒化ィ ンジゥム、 窒化アルミニウムのうちから選ばれた少なくとも 1種以上を主成分とする薄膜が形 成されている薄膜基板であって、 該薄膜基板は窒化ガリウム、 窒化インジウム、 窒化アルミ二 ゥムのうちから選ばれた少なくとも 1種以上を主成分とする薄膜を形成するために用いられる ものであることを特徴とする項 577、 578、 579、 580、 581、 582、 583、 584、 585、 586、 587、 588、 589、 590、 591、 592、 593、 59
4、 595、 596、 597、 598、 599、 600、 601、 602、 603、 604、 605、 606、 607、 608、 609、 610、 611、 612、 613、 614, 61
5、 616、 617、 618、 619、 620、 621、 622、 623、 624, 625、 626、 627、 628、 629、 630、 631、 632、 633、 634、 635、 63
6、 637、 638、 639、 640、 641、 642、 643、 644、 645、 646、 647、 648、 649、 650、 651、 652、 653、 654、 655、 656、 65
7、 658、 659、 660、 661、 662、 663、 664、 665、 666、 667、 668、 669、 670、 671、 672、 673、 674、 675、 676、 677、 67
8、 679、 680、 681、 682、 683、 684, 685、 686、 687、 688、
689、 690、 691、 692、 693、 694, 695、 696、 697、 698、 69
9、 700、 701、 702、 703、 704, 705、 706、 707、 708、 709、 710、 711、 712、 713、 714、 715、 716、 717、 718、 719、 72
0、 721、 722、 723、 724、 725、 726、 727、 728、 729、 730、 731、 732、 733、 734、 735、 736、 737、 738、 739、 740、 74
1、 742、 743、 744、 745、 746、 747、 748、 749、 750、 751、
752、 753、 754、 755、 756、 757、 758、 759、 760、 761、 76
2、 763、 764, 765、 766、 767、 768、 769、 770、 771、 772、
773、 774, 775、 776、 777、 778、 779、 780、 781、 782、 78
3、 784, 785、 786、 787、 788、 789、 790、 791、 792、 793、 794、 795、 796、 797、 798、 799、 800、 801、 802、 803、 80
4、 805、 806、 807、 808、 809、 810、 811、 812、 813、 814、 815、 816、 817、 818、 819、 820、 821、 822、 823、 824, 82
5、 826、 827、 828、 829、 830、 831、 832、 833、 834、 835、
836、 837、 838、 839、 840、 841、 842、 843、 844、 845、 84
6、 847、 848、 849、 850、 851、 852、 853、 854、 855、 856、 857、 858、 859、 860、 861、 862、 863、 864、 865、 866、 86
7、 868、 869、 870、 871、 872、 873、 874、 875、 876、 877、 878、 879、 880、 881、 882、 883、 884、 885、 886、 887、 88
8、 889、 890、 891、 892、 893、 894、 895、 896、 897、 898、
899、 900、 901、 902、 903、 904、 905、 906、 907、 908、 90
9、 910、 911、 912、 913、 914、 915、 916、 917、 918、 919、
920、 921、 922、 923、 924、 925、 926、 927、 928、 929、 93
0、 931、 932、 933、 934、 935、 936、 937、 938、 939、 940、 941、 942、 943、 944、 945、 946、 947、 948、 949、 950、 95
1、 952、 953、 954、 955、 956、 957、 958、 959、 960、 961、 962、 963、 964、 965、 966、 967、 968、 969、 970、 971、 97
2、 973、 974, 975、 976、 977、 978、 979、 980、 981、 982、 983、 984、 985、 986、 987、 988、 989、 990、 991、 992、 99
3、 994、 995、 996、 997、 998、 999、 1000、 1001、 1002、 1
003、 1004、 1005、 1006、 1007、 1008、 1009、 1010、 101 1、 1012、 1013、 1014、 1015、 1016、 1017、 1018、 1019、
1020、 1021、 1022、 1023、 1024、 1025、 1026、 1027、 10 28、 1029、 1030、 1031、 1032、 1033、 1034、 1035、 1036、 1037、 1038、 1039、 1040、 1041、 1042、 1043、 1044、 10 45、 1046、 1047、 1048、 1049、 1050、 1051、 1052、 1053、 1054、 1055、 1056、 1057、 1058、 1059、 1060、 1061、 10 62、 1063、 1064, 1065、 1066、 1067、 1068、 1069、 1070、 1071、 1072、 1073、 1074、 1075、 1076、 1077、 1078、 10
7 9、 1 0 8 0、 1 0 8 1、 1 0 8 2、 1 0 8 3、 1 0 8 4, 1 0 8 5、 1 0 8 6、 1 0 8 7、 1 0 8 8、 1 0 8 9、 1 0 9 0、 1 0 9 1、 1 0 9 2、 1 0 9 3、 1 0 9 4、 1 0 9 5、 1 0 9 6、 1 0 9 7、 1 0 9 8、 1 0 9 9、 1 1 0 0、 1 1 0 1、 1 1 0 2、 1 1 0 3、 1 1 0 4 又は 1 1 0 5に記載されたいずれかの薄膜基板。
項 1 1 0 7. セラミック材料を主成分とする焼結体及び光 Mil性を有するセラミック材料を 主成分とする焼結体のうちから選ばれた少なくともいずれかの焼結体に窒化ガリウム、 窒化ィ ンジゥム、 窒化アルミニウムのうちから選ばれた少なくとも 1種以上を主成分とする薄膜が形 成されている薄膜基板であって、 該薄膜が少なくとも単結晶、 配向性多結晶、 多結晶、 無定形 のうちから選ばれた少なくともいずれかの結晶状態であることを特徴とする項 1 1 0 6に記載 された窒化ガリゥム、 窒化ィンジゥム、 窒化アルミニゥムのうちから選ばれた少なくとも 1種 以上を主成分とする薄膜を形成するために用いられる薄膜基板。
項 1 1 0 8. セラミック材料を主成分とする焼結体及び光 性を有するセラミック材料を 主成分とする焼結体のうちから選ばれた少なくともいずれかの焼結体に窒化ガリウム、 窒化ィ ンジゥム、 窒化アルミニウムのうちから選ばれた少なくとも 1種以上を主成分とする薄膜が形 成されている薄膜基板であって、 該薄膜基板の表面に形成されている薄膜は単結晶であること を體とする項 1 1 0 6又は 1 1 0 7に記載されたいずれかの窒化ガリウム、窒化インジウム、 窒化アルミニウムのうちから選ばれた少なくとも 1種以上を主成分とする薄膜を形成するため に用いられる薄膜基板。
項 1 1 0 9. セラミック材料を主成分とする焼結体及び光透過性を有するセラミック材料を 主成分とする焼結体のうちから選ばれた少なくともいずれかの焼結体に窒化ガリウム、 窒化ィ ンジゥム、 窒化アルミニゥムのうちから選ばれた少なくとも 1種以上を主成分とする薄膜が形 成されている薄膜基板であって、 該薄膜基板の表面に形成されている薄膜は配向性多結晶であ ることを特徴とする項 1 1 0 6又は 1 1 0 7に記載されたいずれかの窒化ガリウム、 窒化イン ジゥム、 窒化アルミニウムのうちから選ばれた少なくとも 1種以上を主成分とする薄膜を形成 するために用いられる薄膜基板。
項 1 1 1 0. セラミック材料を主成分とする焼結体及び光 ¾ 性を有するセラミック材料を 主成分とする焼結体のうちから選ばれた少なくともいずれかの焼結体に窒化ガリウム、 窒化ィ ンジゥム、 窒化アルミニウムのうちから選ばれた少なくとも 1種以上を主成分とする薄膜が形 成されている薄膜基板であって、 該薄膜基板の表面に形成されている薄膜は多結晶であること を籠とする項 1 1 0 6又は 1 1 0 7に記載されたいずれかの窒化ガリウム、窒化インジウム、 窒化アルミニウムのうちから選ばれた少なくとも 1種以上を主成分とする薄膜を形成するため に用いられる薄膜基板。
mi n i. セラミック材料を主成分とする焼結体及び光 ¾ϋ性を有するセラミック材料を 主成分とする焼結体のうちから選ばれた少なくともいずれかの焼結体に窒化ガリウム、 窒化ィ ンジゥム、 窒化アルミニウムのうちから選ばれた少なくとも 1種以上を主成分とする薄膜が形 成されている薄膜基板であって、 該薄膜基板の表面に形成されている薄膜は無定形であること を赚とする項 1 1 0 6又は 1 1 0 7に記載されたいずれかの窒化ガリウム、窒化インジウム、 窒化アルミニウムのうちから選ばれた少なくとも 1種以上を主成分とする薄膜を形成するため に用いられる薄膜基板。
項 1 1 1 2. セラミック材料を主成分とする焼結体及び光 ¾ 性を有するセラミック材料を 主成分とする焼結体のうちから選ばれた少なくともいずれかの焼結体に窒化ガリウム、 窒化ィ ンジゥム、 窒化アルミニウムのうちから選ばれた少なくとも 1種以上を主成分とする薄膜が形 成されている薄膜基板であって、 形成されている薄膜が少なくとも窒化ガリゥムを含むかある いは窒化ガりゥムを主成分とするものであることを特徴とする項 5 7 7、 5 7 8、 5 7 9、 5
80、 581、 582、 583、 584, 585、 586、 587、 588、 589、 590、 591、 592、 593、 594、 595、 596、 597、 598、 599、 600、 60
1、 602、 603、 604、 605、 606、 607、 608、 609、 610、 611、 612、 613、 614、 615、 616、 617、 618、 619、 620、 621、 62
2、 623、 624、 625、 626、 627、 628、 629、 630、 631、 632、 633、 634、 635、 636、 637、 638、 639、 640、 641、 642、 64
3、 644、 645、 646、 647、 648、 649、 650、 651、 652、 653、 654、 655、 656、 657、 658、 659、 660、 661、 662、 663、 66
4、 665、 666、 667、 668、 669、 670、 671、 672、 673、 674、 675、 676、 677、 678、 679、 680、 681、 682、 683、 684、 68
5、 686、 687、 688、 689、 690、 691、 692、 693、 694、 695、
696、 697、 698、 699、 700、 701、 702、 703、 704、 705、 70
6、 707、 708、 709、 710、 711、 712、 713、 714、 715、 716、 717、 718、 719、 720、 721、 722、 723、 724、 725、 726、 72
7、 728、 729、 730、 731、 732、 733、 734、 735、 736、 737、
738、 739、 740、 741、 742、 743、 744、 745、 746、 747、 74
8、 749、 750、 751、 752、 753、 754、 755、 756、 757、 758、 759、 760、 761、 762、 763、 764, 765、 766、 767、 768、 76
9、 770、 771、 772、 773、 774、 775、 776、 777、 778、 779、
780、 781、 782、 783、 784、 785、 786、 787、 788、 789、 79
0、 791、 792、 793、 794、 795、 796、 797、 798、 799、 800、 801、 802、 803、 804、 805、 806、 807、 808、 809、 810、 81
1、 812、 813、 814、 815、 816、 817、 818、 819、 820、 821、
822、 823、 824、 825、 826、 827、 828、 829、 830、 831、 83
2、 833、 834、 835、 836、 837、 838、 839、 840、 841、 842、 843、 844、 845、 846、 847、 848、 849、 850、 851、 852、 85
3、 854、 855、 856、 857、 858、 859、 860、 861、 862、 863、 864、 865、 866、 867、 868、 869、 870、 871、 872、 873、 87
4、 875、 876、 877、 878、 879、 880、 881、 882、 883、 884、
885、 886、 887、 888、 889、 890、 891、 892、 893、 894, 89
5、 896、 897、 898、 899、 900、 901、 902、 903、 904、 905、
906、 907、 908、 909、 910、 911、 912、 913、 914、 915、 91
6、 917、 918、 919、 920、 921、 922、 923、 924, 925、 926、 927、 928、 929、 930、 931、 932、 933、 934、 935、 936、 93
7、 938、 939、 940、 941、 942、 943、 944、 945、 946、 947、 948、 949、 950、 951、 952、 953、 954、 955、 956、 957、 95
8、 959、 960、 961、 962、 963、 964、 965、 966、 967、 968、 969、 970、 971、 972、 973、 974、 975、 976、 977、 978、 97
9、 980、 981、 982、 983、 984、 985、 986、 987、 988、 989、 990、 991、 992、 993、 994、 995、 996, 997、 998、 999、 10 00、 1001、 1002、 1003、 1004、 1005、 1006、 1007、 1008、 1009、 1010、 1011、 1012、 1013、 1014、 1015、 1016、 10 17、 1018、 1019、 1020、 1021、 1022、 1023、 1024、 1025、 1026、 1027、 1028、 1029、 1030、 1031、 1032、 1033、 10
34、 1035、 1036、 1037、 1038、 1039、 1040、 1041、 1042、 1043、 1044、 1045、 1046、 1047、 1048、 1049、 1050、 10 51、 1052、 1053、 1054、 1055、 1056、 1057、 1058、 1059、 1060、 1061、 1062、 1063、 1064、 1065、 1066、 1067、 10 68、 1069、 1070、 1071、 1072、 1073、 1074、 1075、 1076、 1077、 1078、 1079、 1080、 1081、 1082、 1083、 1084, 10 85、 1086、 1087、 1088、 1089、 1090、 1091、 1092、 1093、 1094、 1095、 1096、 1097、 1098、 1099、 1100、 1101、 11 02、 1103、 1104、 1105、 1106、 1107、 1108、 1109、 1110 又は 1111に記載されたいずれかの薄膜基板。
項 1113. 薄膜が A lxGay I yN (0<y≤l)で表わされる組成を有することを 特徴とする項 1112に記載された薄膜基板。
項 1114. 薄膜が窒化ガリウムを 50モル%以上含むを特徵とする項 1112又は 111 3に記載されたいずれかの薄膜基板。
項 1115. 少なくとも窒化ガリウムを含むかあるいは窒化ガリウムを主成分とする薄膜が 無定形、 多結晶、 配向性多結晶、 単結晶のうちから選ばれた少なくともいずれかの結晶状態で あることを特徴とする項 1112、 1113又は 1114に記載されたいずれかの薄膜基板。 項 1116. 少なくとも窒化ガリウムを含むかあるいは窒化ガリウムを主成分とする薄膜が 単結晶であることを特徴とする項 1115に記載された薄膜基板。
項 1117. 最上層の薄膜が少なくとも窒化ガリウムを含むかあるいは窒化ガリウムを主成 分とするものであることを特徴とする項 1112、 1113、 1114、 1115又は 111 6に記載されたいずれかの薄膜基板。
項 1118. 最上層の薄膜が少なくとも窒化ガリウムを含むかあるいは窒化ガリウムを主成 分とする単結晶であることを特徴とする項 1117に記載された薄膜基板。
項 1119. セラミック材料を主成分とする焼結体及び光透過性を有するセラミック材料を 主成分とする焼結体のうちから選ばれた少なくともいずれかの焼結体に窒化ガリウム、 窒化ィ ンジゥム、 窒化アルミニウムのうちから選ばれた少なくとも 1種以上を主成分とする薄膜が形 成されている薄膜基板であって、 該薄膜が単結晶、 無定形、 多結晶、 配向性多結晶のうちから 選ばれた少なくともいずれか 2以上の結晶状態が同時に混在しているものからなることを特徴 とする項 577、 578、 579、 580、 581、 582、 583、 584、 585、 58
6、 587、 588、 589、 590、 591、 592、 593、 594、 595、 596、
597、 598、 599、 600、 601、 602、 603、 604、 605、 606、 60
7、 608、 609、 610、 611、 612、 613、 614、 615、 616、 617、 618、 619、 620、 621、 622、 623、 624, 625、 626、 627、 62
8、 629、 630、 631、 632、 633、 634、 635、 636、 637、 638、
639、 640、 641、 642、 643、 644、 645、 646、 647、 648、 64
9、 650、 651、 652、 653、 654, 655、 656、 657、 658、 659、
660、 661、 662、 663、 664, 665、 666、 667、 668、 669、 67
0、 671、 672、 673、 674, 675、 676、 677、 678、 679、 680、 681、 682、 683、 684, 685、 686、 687、 688、 689、 690、 69
1、 692、 693、 694、 695、 696、 697、 698、 699、 700、 701、
702、 703、 704、 705、 706、 707、 708、 709、 710、 711、 71
2、 713、 714、 715、 716、 717、 718、 719、 720、 721、 722、 723、 724、 725、 726、 727、 728、 729、 730、 731、 732、 73
3、 734、 735、 736、 737、 738、 739、 740、 741、 742、 743、 744、 745、 746、 747、 748、 749、 750、 751、 752、 753、 75
4、 755、 756、 757、 758、 759、 760、 761、 762、 763、 764、 765、 766、 767、 768、 769、 770、 771、 772、 773、 774, 77
5、 776、 777、 778、 779、 780、 781、 782、 783、 784、 785、
786、 787、 788、 789、 790、 791、 792、 793、 794、 795、 79
6、 797、 798、 799、 800、 801、 802、 803、 804、 805、 806、
807、 808、 809、 810、 811、 812、 813、 814、 815、 816、 81
7、 818、 819、 820、 821、 822、 823、 824、 825、 826、 827、 828、 829、 830、 831、 832、 833、 834、 835、 836、 837、 83
8、 839、 840、 841、 842、 843、 844、 845、 846、 847、 848、 849、 850、 851、 852、 853、 854、 855、 856、 857、 858、 85
9、 860、 861、 862、 863、 864、 865、 866、 867、 868, 869、
870、 871、 872、 873、 874、 875、 876、 877、 878、 879、 88
0、 881、 882、 883、 884, 885、 886、 887、 888、 889、 890、 891、 892、 893、 894、 895、 896、 897、 898、 899、 900、 90
1、 902、 903、 904、 905、 906、 907、 908、 909、 910、 911、 912、 913、 914、 915、 916、 917、 918、 919、 920、 921、 92
2、 923、 924, 925、 926、 927、 928、 929、 930、 931、 932、
933、 934、 935、 936、 937、 938、 939、 940、 941、 942、 94
3、 944、 945、 946、 947、 948、 949、 950、 951、 952、 953、 954, 955、 956、 957、 958、 959、 960、 961、 962、 963、 96
4、 965、 966、 967、 968、 969、 970、 971、 972、 973、 974、 975、 976、 977、 978、 979、 980、 981、 982、 983、 984、 98
5、 986、 987、 988、 989、 990、 991、 992、 993、 994、 995、 996、 997、 998、 999、 1000、 1001、 1002、 1003、 1004、 1
005、 1006、 1007、 1008、 1009、 1010、 1011、 1012、 101 3、 1014、 1015、 1016、 1017、 1018、 1019、 1020、 1021、
1022、 1023、 1024、 1025、 1026、 1027、 1028、 1029、 10 30、 1031、 1032、 1033、 1034、 1035、 1036、 1037、 1038、 1039、 1040、 1041、 1042、 1043、 1044、 1045、 1046、 10 47、 1048、 1049、 1050、 1051、 1052、 1053、 1054、 1055、 1056、 1057、 1058、 1059、 1060、 1061、 1062、 1063、 10 64、 1065、 1066、 1067、 1068、 1069、 1070、 1071、 1072、 1073、 1074, 1075、 1076、 1077、 1078、 1079、 1080、 10 81、 1082、 1083、 1084、 1085、 1086、 1087、 1088、 1089、 1090、 1091、 1092、 1093、 1094、 1095、 1096、 1097、 10 98、 1099、 1100、 1101、 1102、 1103、 1104、 1105、 1106、 1107、 1108、 1109、 1110、 1111、 1112、 1113、 1114、 11 15、 1116、 1117又は 1118に記載されたいずれかの薄膜基板。
項 1120. セラミック材料を主成分とする焼結体及び光¾1性を有するセラミック材料を 主成分とする焼結体のうちから選ばれた少なくともいずれかの焼結体に窒化ガリウム、 窒化ィ ンジゥム、 窒化アルミニウムのうちから選ばれた少なくとも 1種以上を主成分とする薄膜が単 一層あるいは少なくとも 2以上の層で形成されている薄膜基板であって、 該薄膜の少なくとも
1以上の層が単結晶、 無定形、 多結晶、 配向性多結晶のうちから選ばれた少なくともいずれか 2以上の結晶状態が同時に混在しているものからなることを特徴とする項 1119に記載され 項 1121. セラミック材料を主成分とする焼結体及び光¾性を有するセラミック材料を 主成分とする焼結体のうちから選ばれた少なくともいずれかの焼結体に窒化ガリウム、 窒化ィ ンジゥム、 窒化アルミニウムのうちから選ばれた少なくとも 1種以上を主成分とする薄膜が形 成されている薄膜基板であって、該焼結体が基板状であることを [とする項 577、 578、
579、 580、 581、 582、 583、 584、 585、 586、 587、 588、 58 9、 590、 591、 592、 593、 594、 595、 596、 597、 598、 599、
600、 601、 602、 603、 604、 605、 606、 607、 608、 609、 61
0、 611、 612、 613、 614、 615、 616、 617、 618、 619、 620、 621、 622、 623、 624、 625、 626、 627、 628、 629、 630、 63
1、 632、 633、 634、 635、 636、 637、 638、 639、 640、 641、 642、 643、 644、 645、 646、 647、 648、 649、 650、 651、 65
2、 653、 654, 655、 656、 657、 658、 659、 660、 661、 662,
663、 664、 665、 666、 667、 668、 669、 670、 671、 672、 67
3、 674. 675、 676、 677、 678、 679、 680、 681、 682、 683、 684、 685、 686、 687、 688、 689、 690、 691、 692、 693、 69
4、 695、 696、 697、 698、 699、 700、 701、 702、 703、 704、
705、 706、 707、 708、 709、 710、 711、 712、 713、 714、 71
5、 716、 717、 718、 719、 720、 721、 722、 723、 724、 725、 726、 727、 728、 729、 730、 731、 732、 733、 734、 735、 73
6、 737、 738、 739、 740、 741、 742、 743、 744、 745、 746、 747、 748、 749、 750、 751、 752、 753、 754、 755、 756、 75
7、 758、 759、 760、 761、 762、 763、 764、 765、 766、 767、 768、 769、 770、 771、 772、 773、 774、 775、 776、 777、 77
8、 779、 780、 781、 782、 783、 784、 785、 786、 787、 788、
789、 790、 791、 792、 793、 794, 795、 796、 797、 798、 79
9、 800、 801、 802、 803、 804、 805、 806、 807、 808、 809、 810、 811、 812、 813、 814、 815、 816、 817、 818、 819、 82
0、 821、 822、 823、 824、 825、 826、 827、 828、 829、 830、 831、 832、 833、 834、 835、 836、 837、 838、 839、 840、 84
1、 842、 843、 844、 845、 846、 847、 848、 849、 850、 851、
852、 853、 854、 855、 856、 857、 858、 859、 860、 861、 86
2、 863、 864、 865、 866、 867、 868、 869、 870、 871、 872、 873、 874, 875、 876、 877、 878、 879、 880、 881、 882、 88
3、 884, 885、 886、 887、 888、 889、 890、 891、 892、 893、
894, 895、 896、 897、 898、 899、 900、 901、 902、 903、 90
4、 905、 906、 907、 908、 909、 910、 911、 912、 913、 914、 915、 916、 917、 918、 919、 920、 921、 922、 923、 924, 92
5、 926、 927、 928、 929、 930、 931、 932、 933、 934、 935、
936、 937、 938、 939、 940、 941、 942、 943、 944、 945、 94
6、 947、 948、 949、 950、 951、 952、 953、 954、 955、 956、 957、 958、 959、 960、 961、 962、 963、 964、 965、 966、 96
7、 968、 969、 970、 971、 972、 973、 974、 975、 976、 977、 978、 979、 980、 981、 982、 983、 984、 985、 986、 987、 98
8、 989、 990、 991、 992、 993、 994、 995、 996、 997、 998、 999、 1000、 1001、 1002、 1003、 1004、 1005、 1006、 100 7、 1008、 1009、 1010、 1011、 1012、 1013、 1014、 1015、 1016、 1017、 1018、 1019、 1020、 1021、 1022、 1023、 10 24, 1025、 1026、 1027、 1028、 1029、 1030、 1031、 1032、 1033、 1034、 1035、 1036、 1037、 1038、 1039、 1040、 10 41、 1042、 1043、 1044、 1045、 1046、 1047、 1048、 10.49、 1050、 1051、 1052、 1053、 1054、 1055、 1056、 1057、 10 58、 1059、 1060、 1061、 1062、 1063、 1064, 1065、 1066、 1067、 1068、 1069、 1070、 1071、 1072、 1073、 1074、 10 75、 1076、 1077、 1078、 1079、 1080、 1081、 1082、 1083、 1084、 1085、 1086、 1087、 1088、 1089、 1090、 1091、 10 92、 1093、 1094、 1095、 1096、 1097、 1098、 1099、 1100、 1101、 1102、 1103、 1104、 1105、 1106、 1107、 1108、 11
09、 1110、 1111、 1112、 1113、 1114、 1115、 1116、 1117、 1118、 1119又は 1120記載されたいずれかの薄膜基板。
項 1122. セラミツク材料が金属元素及び半金属元素のうちから選ばれた少なくとも 1種 以上の元素と非金属元素のうちから選ばれた少なくとも 1種以上の元素との組成物、 あるいは 金属元素のうちから選ばれた少なくとも 1種以上の元素と半金属元素のうちから選ばれた少な くとも 1種以上の元素との組成物、 あるいは半金属元素のうちから選ばれた少なくともいずれ か 2種以上の元素との組成物であることを ^とする項 577、 578、 579、 580、 5 81、 582、 583、 584、 585、 586、 587、 588、 589、 590、 591、
592、 593、 594、 595、 596、 597、 598、 599、 600、 601、 60
2、 603、 604、 605、 606、 607、 608、 609、 610、 611、 612、 613、 614、 615、 616、 617、 618、 619、 620、 621、 622、 62
3、 624、 625、 626、 627、 628、 629、 630、 631、 632、 633、
634、 635、 636、 637、 638、 639、 640、 641、 642、 643、 64
4、 645、 646、 647、 648、 649、 650、 651、 652、 653、 654、 655、 656、 657、 658、 659、 660、 661、 662、 663、 664, 66
5、 666、 667、 668、 669、 670、 671、 672、 673、 674, 675、 676、 677、 678、 679、 680、 681、 682、 683、 684、 685、 68
6、 687、 688、 689、 690、 691、 692、 693、 694、 695、 696、
697、 698、 699、 700、 701、 702、 703、 704, 705、 706、 70
7、 708、 709、 710、 711、 712、 713、 714、 715、 716、 717、 718、 719、 720、 721、 722、 723、 724、 725、 726、 727、 72
8、 729、 730、 731、 732、 733、 734、 735·、 736、 737、 738、
739、 740、 741、 742、 743、 744、 745、 746、 747、 748、 74
9、 750、 751、 752、 753、 754、 755、 756、 757、 758、 759、 760、 761、 762、 763、 764、 765、 766、 767、 768、 769、 77
0、 771、 772、 773、 774, 775、 776、 777、 778、 779、 780、 781、 782、 783、 784, 785、 786、 787、 788、 789、 790、 79
1、 792、 793、 794, 795、 796、 797、 798、 799、 800、 801、
802、 803、 804、 805、 806、 807、 808、 809、 810、 811、 81
2、 813、 814、 815、 816、 817、 818、 819、 820、 821、 822、 823、 824、 825、 826、 827、 828、 829、 830、 831、 832、 83
3、 834、 835、 836、 837、 838、 839、 840、 841、 842、 843、 844、 845、 846、 847、 848、 849、 850、 851、 852、 853、 85
4、 855、 856、 857、 858、 859、 860、 861、 862、 863、 864、 865、 866、 867、 868、 869、 870、 871、 872、 873、 874、 87
5、 876、 877、 878、 879、 880、 881、 882、 883、 884、 885、
886、 887、 888、 889、 890、 891、 892、 893、 894, 895、 89
6、 897、 898、 899、 900、 901、 902、 903、 904、 905、 906、
907、 908、 909、 910、 911、 912、 913、 914、 915、 916、 91
7、 918、 919、 920、 921、 922、 923、 924、 925、 926、 927、 928、 929、 930、 931、 932、 933、 934、 935、 936、 937、 93
8、 939、 940、 941、 942、 943、 944、 945、 946、 947、 948、 949、 950、 951、 952、 953、 954、 955、 956、 957、 958、 95
9、 960、 961、 962、 963、 964、 965、 966、 967、 968、 969、
970、 971、 972、 973、 974、 975、 976、 977、 978、 979、 98
0、 981、 982、 983、 984、 985、 986、 987、 988、 989、 990、 991、 992、 993、 994、 995、 996、 997、 998、 999、 1000、 1
001、 1002、 1003、 1004, 1005、 1006、 1007、 1008、 100 9、 1010、 1011、 1012、 1013、 1014、 1015、 1016、 1017、
1018、 1019、 1020、 1021、 1022、 1023、 1024、 1025、 10 26、 1027、 1028、 1029、 1030、 1031、 1032、 1033、 1034、 1035、 1036、 1037、 1038、 1039、 1040、 1041、 1042、 10 43、 1044、 1045、 1046、 1047、 1048、 1049、 1050、 1051、 1052、 1053、 1054、 1055、 1056、 1057、 1058、 1059、 10 60、 1061、 1062、 1063、 1064、 1065、 1066、 1067、 1068、 1069、 1070、 1071、 1072、 1073、 1074、 1075、 1076、 10 77、 1078、 1079、 1080、 1081、 1082、 1083、 1084、 1085、 1086、 1087、 1088、 1089、 1090、 1091、 1092、 1093、 10 94、 1095、 1096、 1097、 1098、 1099、 1100、 1101、 1102、 1103、 1104、 1105、 1106、 1107、 1108、 1109、 1110、 11 11、 1112、 1113、 1114、 1115、 1116、 1117、 1118、 1119、 1120又は 1121に記載されたいずれかの薄膜基板。
項 1123. 半金属元素が 素、 炭素、珪素、ゲルマニウム、 ヒ素、 アンチモン、 ビスマス、 セレン、 テルル、 ポロニウムのうちから選ばれた少なくとも 1種以上であることを if#ii [とする 項 1122に記載された薄膜基板。
項 1124. 半金属元素が炭素、 珪素のうちから選ばれた少なくとも 1種以上であることを 特徴とする項 1123に記載された薄膜基板。 .
項 1125. 非金属元素が窒素、 りん、 酸素、 硫黄、 フッ素、 塩素、 臭素、 沃素、 ァスタチ ンのうちから選ばれた少なくとも 1種以上であることを特徴とする項 1121、 1122又は 1124に記載されたいずれかの薄膜基板。
項 1126. 非金属元素が窒素、 酸素のうちから選ばれた少なくとも 1種以上であることを 特徴とする項 1125に記載された薄膜基板。
項 1127. セラミック材料が窒化物、 炭化物、 酸化物、 硼化物、 珪化物のうちから選ばれ た少なくともいずれかであることを特徴とする項 1122、 1123、 1124、 1125又 は 1126に記載されたいずれかの薄膜基板。
項 1128. セラミック材料を主成分とする焼結体及び光透過性を有するセラミック材料を 主成分とする焼結体のうちから選ばれた少なくともいずれかの焼結体に窒化ガリウム、 窒化ィ ンジゥム、 窒化アルミニウムのうちから選ばれた少なくとも 1種以上を主成分とする薄膜が形 成されている薄膜基板であって、 該焼結体が導電性を有することを特徴とする項 577、 57
8、 579、 580、 581、 582、 583、 584, 585、 586、 587、 588、
589、 590、 591、 592、 593、 594、 595、 596、 597、 598、 59
9、 600、 601、 602、 603、 604、 605、 606、 607、 608、 609、 610、 611、 612、 613、 614、 615、 616、 617、 618、 619、 62
0、 621、 622、 623、 624, 625、 626、 627、 628、 629、 630、 631、 632、 633、 634、 635、 636、 637、 638、 639、 640、 64
1、 642、 643、 644、 645、 646、 647、 648、 649、 650、 651、
652、 653、 654、 655、 656、 657、 658、 659、 660、 661、 66
2、 663、 664, 665、 666、 667、 668、 669、 670、 671、 672、 673、 674, 675、 676、 677、 678、 679、 680、 681、 682、 68
3、 684、 685、 686、 687、 688、 689、 690、 691、 692、 693、
694, 695、 696、 697、 698、 699、 700、 701、 702、 703、 70
4、 705、 706、 707、 708、 709、 710、 711、 712、 713、 714、 715、 716、 717、 718、 719、 720、 721、 722、 723、 724、 72
5、 726、 727、 728、 729、 730、 731、 732、 733、 734、 735、
736、 737、 738、 739、 740、 741、 742、 743、 744、 745、 74
6、 747、 748、 749、 750、 751、 752、 753、 754、 755、 756、 757、 758、 759、 760、 761、 762、 763、 764、 765、 766、 76
7、 768、 769、 770、 771、 772、 773、 774、 775、 776、 777、 778、 779、 780、 781、 782、 783、 784, 785、 786、 787、 78
8、 789、 790、 791、 792、 793、 794、 795、 796、 797、 798、
799、 800、 801、 802、 803、 804、 805、 806、 807、 808、 80
9、 810、 811、 812、 813、 814、 815、 816、 817、 818、 819、
820、 821、 822、 823、 824, 825、 826、 827、 828、 829、 83
0、 831、 832、 833、 834、 835、 836、 837、 838、 839、 840、 841、 842、 843、 844、 845、 846、 847、 848、 849、 850、 85
1、 852、 853、 854、 855、 856、 857、 858、 859、 860、 861、 862、 863、 864、 865、 866、 867、 868、 869、 870、 871、 87
2、 873、 874, 875、 876、 877、 878、 879、 880、 881、 882、
883、 884, 885、 886、 887、 888、 889、 890、 891、 892、 89
3、 894、 895、 896、 897、 898、 899、 900、 901、 902、 903、 904、 905、 906、 907、 908、 909、 910、 911、 912、 913、 91
4、 915、 916、 917、 918、 919、 920、 921、 922、 923、 924、
925、 926、 927、 928、 929、 930、 931、 932、 933、 934、 93
5、 936、 937、 938、 939、 940、 941、 942、 943、 944、 945、 946、 947、 948、 949、 950、 951、 952、 953、 954、 955、 95
6、 957、 958、 959、 960、 961、 962、 963、 964, 965、 966、
967、 968、 969、 970、 971、 972、 973、 974、 975、 976、 97
7、 978、 979、 980、 981、 982、 983、 984, 985、 986、 987、 988、 989、 990、 991、 992、 993、 994、 995、 996、 997、 99
8、 999、 1000、 1001、 1002、 1003、 1004、 1005、 1006、 1
007、 1008、 1009、 1010、 1011、 1012、 1013、 1014、 101 5、 1016、 1017、 1018、 1019、 1020、 1021、 1022、 1023、 1024、 1025、 1026、 1027、 1028、 1029、 1030、 1031、 10 32、 1033、 1034、 1035、 1036、 1037、 1038、 1039、 1040、 1041、 1042、 1043、 1044、 1045、 1046、 1047、 1048、 10 49、 1050、 1051、 1052、 1053、 1054、 1055、 1056、 1057、
1058、 1059、 1060、 1061、 1062、 1063、 1064、 1065、 10 66、 1067、 1068、 1069、 1070、 1071、 1072、 1073、 1074、 1075、 1076、 1077、 1078、 1079、 1080、 1081、 1082、 10 83、 1084、 1085、 1086、 1087、 1088、 1089、 1090、 1091、 1092、 1093、 1094、 1095、 1096、 1097、 1098、 1099、 11 00、 1101、 1102、 1103、 1104、 1105、 1106、 1107、 1108、 1109、 1110、 1111、 1112、 1113、 1114、 1115、 1116、 11 17、 1118、 1119、 1121、 1122、 1123、 1124、 1125、 1126 又は 1127に記載されたいずれかの薄膜基板。
項 1129. セラミック材料を主成分とする焼結体あるいは光透過性を有するセラミック材 料を主成分とする焼結体が室温において 1 X 104Ω· cm以下の抵抗率を有することを と する項 1128に記載された薄膜基板。
項 1130. セラミック材料を主成分とする焼結体あるいは光透過性を有するセラミック材 料を主成分とする焼結体が室温において 1 X 102 Ω . c m以下の抵抗率を有することを特徴と する項 1128又は 1129に記載されたいずれかの薄膜基板。
項 1131. セラミック材料を主成分とする焼結体あるいは光透過性を有するセラミック材 料を主成分とする焼結体が室温において 1 X 101Ω · c m以下の抵抗率を有することを と する項 1128、 1129又は 1130に記載されたいずれかの薄膜基板。
項 1132. セラミック材料を主成分とする焼結体あるいは)1 S¾性を有するセラミック材 料を主成分とする焼結体が室温において 1 X 10。Ω · cm以下の抵抗率を有することを と する項 1128、 1129、 1130又は 1131に記載されたいずれかの薄膜基板。
項 1133. セラミック材料を主成分とする焼結体あるいは)■άΜ過性を有するセラミック材 料を主成分とする焼結体が室温において 1 X 10— 2Ω · cm以下の抵抗率を有することを特徴 とする項 1128、 1129、 1130、 1131又は 1132に記載されたいずれかの薄膜 項 1134. セラミック材料を主成分とする焼結体あるいは光透過性を有するセラミック材 料を主成分とする焼結体が導電性を有しかつ光 ¾i性を有することを特徴とする項 1128、 1129、 1130、 1131、 1132又は 1133に記載されたいずれかの薄膜基板。 項 1135. 窒化アルミニウムを主成分とする焼結体に窒化ガリウム、 窒化インジウム、 窒 化アルミニウムのうちから選ばれた少なくとも 1種以上を主成分とする薄膜により光導波路が 形成されていることを特徴とする薄膜基板。
項 1136. 光導波路が窒化ガリウム、 窒化インジウム、 窒化アルミニウムのうちから選ば れた少なくとも 1種以上を主成分とする単結晶、 無定形、 多結晶、 配向性多結晶のうちから選 ばれた少なくともいずれかの結晶状態を有する薄膜からなることを特徴とする項 1135に記
載された薄膜基板。
項 1137. 光導波路が窒化ガリウム、 窒化インジウム、 窒化アルミニウムのうちから選ば れた少なくとも 1種以上を主成分とする単結晶薄膜からなることを特徴とする項 1135又は 1136に記載されたいずれかの薄膜基板。
項 1138. 窒化アルミニウムを主成分とする焼結体に窒化ガリウム、 窒化インジウム、 窒 化アルミニウムのうちから選ばれた少なくとも 1種以上を主成分とする単結晶薄膜により光導 波路が形成されている薄膜基板であって、 魏導波路〖堪板面に対して C軸が垂直な方向に形 成された単結晶薄膜からなることを特徴とする項 1137に記載された薄膜基板。
項 1139. 窒化アルミニウムを主成分とする焼結体に窒化ガリウム、 窒化インジウム、 窒 化アルミニウムのうちから選ばれた少なくとも 1種以上を主成分とする単結晶薄膜により光導 波路が形成されている薄膜基板であって、 魏導波路 板面に対して C軸が水平な方向に形 成された単結晶薄膜からなることを特徴とする項 1137に記載された薄膜基板。
項 1140. 光導波路が窒化ガリウム及び窒化アルミニウムのうちから選ばれた少なくとも 1種以上を主成分とするものであることを特徴とする項 1135、 1136、 1137、 11 38又は 1139に記載されたいずれかの薄膜基板。
項 1141. 光導波路が A 1
(0. 0≤χ≤1. 0) の化学式であらわされる組 成物を主成分とするものであることを « [とする項 1135、 1136、 1137、 1138、
1139又は 1140に記載されたいずれかの薄膜基板。
項 1142. 光導波路が AlxGa -χΝ (0. 5≤x≤l. 0) の化学式であらわされる組 成物を主成分とするものであることを特徴とする項 1141に記載された薄膜基板。
項 1143. 光導波路が A 1
(0. 8≤x≤l. 0) の化学式であらわされる組 成物を主成分とするものであることを特徴とする項 1141又は 1142に記載されたいずれ かの薄膜基板。
項 1144.
(0. 9≤x≤l. 0) の化学式であらわされる組 成物を主成分とするものであることを特徴とする項 1141、 1142又は 1143に記載さ れたいずれかの薄膜基板。
項 1145. 光導波路が窒化アルミニウムを主成分とするものであることを特徴とする項 1 135、 1136、 1137、 1138、 1139、 1140、 1141、 1142、 114 3又は 1144に記載されたいずれかの薄膜基板。
項 1146. 光導波路が窒化ガリウム、 窒化インジウム、 窒化アルミニウムのうちから選ば れた少なくとも 1種以上を主成分としさらにガリウム、 インジウム、 ニオブ及びタンタルのう ちから選ばれた少なくとも 1種以上の成分を含有する薄膜からなることを特徴とする項 113 5、 1136、 1137、 1138、 1139、 1140、 1141、 1142、 1143、
1144又は 1145に記載されたいずれかの薄膜基板。
項 1147. 光導波路が窒化ガリウム、 窒化インジウム、 窒化アルミニウムのうちから選ば れた少なくとも 1種以上を主成分としさらにガリゥム、 ィンジゥム、 ニオブ及び夕ンタルのう ちから選ばれた少なくとも 1種以上の成分を熱拡散あるいはイオン注入により含有せしめた薄 膜からなることを特徴とする項 1146に記載された薄膜基板。
項 1148. 光導波路が窒化ガリウム、 窒化インジウム、 窒化アルミニウムのうちから選ば れた少なくとも 1種以上を主成分としさらにガリウム、 インジウム、 ニオブ及びタンタルのう ちから選ばれた少なくとも 1種以上の成分を主成分に対して窒化物 で 20モル%以下含む 薄膜からなることを特徴とする項 1146又は 1147に記載されたいずれかの薄膜基板。 項 1149. 光導波路が窒化ガリウム、 窒化インジウム、 窒化アルミニウムのうちから選ば れた少なくとも 1種以上を主成分としさらにニオブ及びタンタルのうちから選ばれた少なくと
も 1種以上の成分を含む薄膜からなることを特徴とする項 1135、 1136、 1137、 1 138、 1139、 1140、 1141、 1142、 1143、 1144、 1145、 114 6、 1147又は 1148に記載されたいずれかの薄膜基板。
項 1150. ニオブ及び夕ンタルのうちから選ばれた少なくとも 1種以上の成分の含有量が 主成分に対して窒化物換算で 20モル%以下であることを特徴とする項 1149に記載された 項 1151. 光導波路が窒化ガリウム及び窒化アルミニウムのうちから選ばれた少なくとも 1種以上を主成分としさらにガリウム、 インジウム、 ニオブ及びタンタルのうちから選ばれた 少なくとも 1種以上の成分を含有する薄膜からなることを特徴とする項 1146、 1147、 1148、 1149又は 1150に記載されたいずれかの薄膜基板。
項 1152. 光導波路が窒化ガリウム及び窒化アルミニウムのうちから選ばれた少なくとも 1種以上を主成分としさらにガリウム、 インジウム、 ニオブ及びタンタルのうちから選ばれた 少なくとも 1種以上の成分を窒化物換算で 20モル%以下含有する薄膜からなることを特徴と する項 1151に記載された薄膜基板。
項 1153. 光導波路が窒化アルミニウムを主成分としさらにガリウム、 インジウム、 ニォ ブ及びタンタルのうちから選ばれた少なくとも 1種以上の成分を含有する薄勵ゝらなることを 特徴とする項 1146、 1147、 1148、 1149、 1150、 1151又は 1152に 記載されたいずれかの薄膜基板。
項 1154. 光導波路が窒化アルミニウムを主成分としさらにガリウム、 インジウム、 ニォ ブ及び夕ンタルのうちから選ばれた少なくとも 1種以上の成分を窒化物 で 20モル%以下 含有する薄膜からなることを特徴とする項 1153に記載された薄膜基板。
項 1155. 窒化アルミニウムを主成分とする焼結体に窒化ガリウム、 窒化インジウム、 窒 化アルミニウムのうちから選ばれた少なくとも 1種以上を主成分とする薄膜により光導波路が 形成された薄膜基板であって、 該薄膜基板は光導波路と魏導波路より屈折率の小さいクラッ ド層とからなることを特徴とする項 1135、 1136、 1137、 1138、 1139、 1 140、 1141、 1142、 1143、 1144、 1145、 1146、 1147、 114 8、 1149、 1150、 1151、 1152、 1153又は 1154に記載されたいずれか 項 1156. クラッド層が窒化ガリウム、 窒化インジウム、 窒化アルミニウムのうちから選 ばれた少なくとも 1種以上を主成分とする薄膜からなることを特徴とする項 1155に記載さ れた薄膜基板。
項 1157. 光導波路が窒化ガリウム、 窒化インジウム、 窒化アルミニウムのうちから選ば れた少なくとも 1種以上を主成分とする薄膜からなり、 I ^導波路はクラッド層よりガリウム、 インジウム、 ニオブ及びタンタルのうちから選ばれた少なくとも 1種以上の成分を多く含むも のであることを特徴とする項 1156に記載された薄膜基板。
項 1158. 光導波路が窒化ガリウム、 窒化インジウム、 窒化アルミニウムのうちから選ば れた少なくとも 1種以上を主成分とする薄膜からなり、該光導波路はクラッド層よりガリウム、 インジウム、 ニオブ及びタンタルのうちから選ばれた少なくとも 1種以上の成分を窒化物換算 で 20モル%以下の範囲で多く含むものであることを特徴とする項 1156又は 1157に記 載されたいずれかの薄膜基板。
項 1159. クラッド層が窒化アルミニウムを主成分とする薄膜からなることを特徴とする 項 1155、 1156、 1157又は 1158に記載されたいずれかの薄膜基板。
項 1160. クラッド層が窒化アルミニウムを主成分とする薄膜からなり、 光導波路は該ク ラッド層よりも屈折率の大きい窒化アルミニウムを主成分とする薄膜からなることを特徴とす
る項 1155、 1156、 1157、 1158又は 1159に記載されたいずれかの薄膜基板。 項 1161. クラッド層が窒化アルミニウムを主成分とする薄膜からなり、 光導波路は該ク ラッド層よりもガリウム、 インジウム、 ニオブ及びタンタルのうちから選ばれた少なくとも 1 種以上の成分を多く含む窒化アルミニウムを主成分とする薄膜からなることを赚とする項 1 155、 1156、 1157、 1158、 1159又は 1160に記載されたいずれかの薄膜 項 1162. クラッド層が窒化アルミニウムを主成分とする薄膜からなり、 光導波路は窒化 アルミニウムを主成分とする単結晶薄膜からなることを特徴とする項 1155、 1156、 1 157、 1158、 1159、 1160又は 1161に記載されたいずれかの薄膜基板。 項 1163. 光導波路に電極が形成されていることを特徴とする項 1155、 1156、 1 157、 1158、 1159、 1160又は 1161に記載されたいずれかの薄膜基板。 項 1164. クラッド層に電極が形成されていることを特徴とする項 1155、 1156、 1157、 1158、 1159、 1160、 1161又は 1162に記載されたいずれかの薄 項 1165. 光導波路及びクラッド層に電極が形成されていることを體とする項 1163 又は 1164に記載されたいずれかの薄膜基板。
項 1166. 電極がバッファ層を介して形成されていることを特徴とする項 1163、 11 64又は 1165に記載されたいずれかの薄膜基板。
項 1167. バッファ層が S i 02及び A 1203、 のうちから選ばれた少なくとも 1種以上か らなることを特徴とする項 1166に記載された薄膜基板。
項 1168. 窒化ガリウム、 窒化インジウム、 窒化アルミニウムのうちから選ばれた少なく とも 1種以上を主成分とする薄膜に該薄膜より屈折率の小さい誘電体が形成されている薄膜基 板であって、 M電体が形成されている部分の薄膜を光導波路として用いることを«とする 項 1135、 1136、 1137、 1138、 1139、 1140、 1141、 1142、 1 143、 1144、 1145、 1146、 1147、 1148、 1149、 1150、 115 1、 1152、 1153、 1154、 1155、 1156、 1157、 1158、 1159、 1160、 1161、 1162、 1163、 1164、 1165、 1166又は 1167に記 載されたいずれかの薄膜基板。
項 1169. 窒化ガリウム、 窒化インジウム、 窒化アルミニウムのうちから選ばれた少なく とも 1種以上を主成分とする薄膜の 2箇所以上に金属が形成され該金属が形成されていない部 分の薄膜を光導波路として用いることを特徴とする項 1135、 1136、 1137、 113 8、 1139、 1140、 1141、 1142、 1143、 1144、 1145、 1146、 1147、 1148、 1149、 1150、 1151、 1152、 1153、 1154、 11 55、 1156、 1157、 1158、 1159、 1160、 1161、 1162、 1163、 1164、 1165、 1166又は 1167に記載されたいずれかの薄膜基板。
項 1170. 窒化ガリウム、 窒化インジウム、 窒化アルミニウムのうちから選ばれた少なく とも 1種以上を主成分とする薄膜の 2箇所以上に電極が形成され該電極の形成されている部分 の該薄膜を光導波路として用いることを特徴とする項 1135、 1136、 1137、 113 8、 1139、 1140、 1141、 1142、 1143、 1144、 1145、 1146、 1147、 1148、 1149、 1150、 1151、 1152、 1153、 1154、 11 55、 1156、 1157、 1158、 1159、 1160、 1161、 1162、 1163、 1164、 1165、 1166又は 1167に記載されたいずれかの薄膜基板。
項 1171. セラミック材料を主成分とする焼結体及びは ¾1 生を有するセラミック材料 を主成分とする焼結体のうちから選ばれた少なくともいずれかの焼結体に窒ィ匕ガリウム、 窒化
窒化アルミニウムのうちから選ばれた少なくとも 1種以上を主成分とする薄膜が 形成されている薄膜基板の 方法であって、 該薄膜がガリウム、 インジウム、 アルミニウム のうちから選ばれた少なくとも 1種以上の成分の有機化合物を主原料としアンモニア、 窒素、 水素のうちから選ばれた少なくとも 1種以上を反応ガスとして作製されるものであることを特 徴とする薄膜基板の製造方法。
項 1 1 7 2 . 主原料の有樹匕合物がガリウム、 インジウム、 アルミニウムのうちから選ばれ た少なくとも 1種以上の成分のアルキル化物であることを特徴とする項 1 1 7 1に記載された 項 1 1 7 3 . 主原料の有衞匕合物がトリメチルガリウム、 卜リメチルインジウム、 トリメチ ルアルミニウムのうちから選ばれた少なくとも 1種以上を主成分とするものであることを特徴 とする項 1 1 7 1又は 1 1 7 2に記載されたいずれかの薄膜基板の製造方法。
項 1 1 7 4. セラミック材料を主成分とする焼結体及びは¾¾1性を有するセラミック材料 を主成分とする焼結体のうちから選ばれた少なくともいずれかの焼結体に窒化ガリウム、 窒化 インジウム、 窒化アルミニウムのうちから選ばれた少なくとも 1種以上を主成分とする薄膜が 形成されている薄膜基板の纖方法であって、 該薄膜がガリウム、 インジウム、 アルミニウム のうちから選ばれた少なくとも 1種以上の成分のハロゲン化物を 料としアンモニア、窒素、 水素のうちから選ばれた少なくとも 1種以上を反応ガスとして作製されるものであることを特 徵とする薄膜基板の製造方法。
項 1 1 7 5 . 主原料のハロゲン化物がフッ化物、 塩化物、 ¾ (匕物及び沃化物のうちから選ば れた少なくとも 1種以上からなることを特徴とする項 1 1 7 4に記載された薄膜基板の難方 法。
項 1 1 7 6 . 主原料のハロゲン化物が塩化ガリウム、 ^(匕ガリウム、 塩化インジウム、 ^(匕 インジウム、 塩化アルミニウム、 :¾{匕アルミニウムのうちから選ばれた少なくとも 1種以上を 主成分とするものであることを mとする項 1 1 7 4又は 1 1 7 5に記載されたいずれかの薄 膜基板の製造方法。
項 1 1 7 7 . 主原料がハロゲン元素を含む有衞匕合物からなることを餓とする項 1 1 7 1、 1 1 7 2、 1 1 7 3、 1 1 7 4、 1 1 7 5又は 1 1 7 6に記載されたいずれかの薄膜基板の製 造方法。
項 1 1 7 8 . 窒化アルミニウムを主成分とする焼結体に窒化ガリウム、 窒化インジウム、 窒 化アルミニウムを主成分とする薄膜により光導波路が形成された薄膜基板の難方法であって、 該光導波路が窒化ガリウム、 窒化インジウム、 窒化アルミニウムを主成分とする薄膜にガリウ ム、 ィンジゥム、 ニオブ及び夕ンタルのうちから選ばれた少なくとも 1種以上の成分を熱拡散 あるいはイオン注入のうちから選ばれた少なくともいずれかの方法により含有せしめた薄膜か らなることを特徴とする薄膜基板の製造方法。
項 1 1 7 9 . 窒化ガリウム、 窒化インジウム、 窒化アルミニウムのうちから選ばれた少なく とも 1種以上を主成分としさらにニオブ及びタンタルのうちから選ばれた少なくとも 1種以上 の成分を含むことを特徴とする光導波路。
項 1 1 8 0 . 窒化ガリウム、 窒化アルミニウムのうちから選ばれた少なくとも 1種以上を主 成分としさらにニオブ及びタンタルのうちから選ばれた少なくとも 1種以上の成分を含むこと を特徴とする項 1 1 7 9に記載された光導波路。
項 1 1 8 1 . 窒化アルミニウムを主成分としさらにニオブ及びタンタルのうちから選ばれた 少なくとも 1種以上の成分を含むことを特徴とする項 1 1 Ί 9又は 1 1 8 0に記載されたいず れかの光導波路。
項 1 1 8 2. ニオブ及び夕ンタルのうちから選ばれた少なくとも 1種以上の成分の含有量が
主成分に対して 20モル%以下であることを特徴とする項 1179、 1180又は 1181に 記載されたいずれかの光導波路。
項 1183. 窒化ガリウム、 窒化インジウム、 窒化アルミニウムのうちから選ばれた少なく とも 1種以上を主成分としさらにニオブ及びタンタルのうちから選ばれた少なくとも 1種以上 の成分を含む光導波路であって、 義導薦は単結晶、 無定形、 多結晶、 配向性多結晶のうち から選ばれた少なくともいずれかの結晶状態を有することを とする項 1179、 1180、 1181又は 1182に記載されたいずれかの光導波路。
項 1184. 結晶状態が単結晶であることを特徴とする項 1183に記載された光導波路。 項 1185. 窒化アルミニウムを主成分としさらにガリウム及びインジウムのうちから選ば れた少なくとも 1種以上の成分を含む単結晶からなることを とする項 1183又は 118 4に記載されたいずれかの光導波路。
項 1186. 窒化アルミニウムを主成分としさらにガリゥム及びィンジゥムのうちから選ば れた少なくとも 1種以上の成分を主成分に対して 20モル%以下含む単結晶からなることを特 徴とする項 1183、 1184又は 1185に記載されたいずれかの光導波路。
項 1187. 窒化ガリウム、 窒化インジウム、 窒化アルミニウムのうちから選ばれた少なく とも 1種以上を主成分としさらにニオブ及びタンタルのうちから選ばれた少なくとも 1種以上 の成分を含むことを特徴とするとする光導波路であって、 該光導波路は薄膜からなることを特 徵とする項 1179、 1180、 1181、 1182、 1183、 1184、 1185又は 1 186に記載されたいずれかの光導波路。
項 1188. 窒化ガリウム、 窒化インジウム、 窒化アルミニウムのうちから選ばれた少なく とも 1種以上を主成分とする薄 ϋ ^らなる少なくとも Ν型半導体層及び発光層及び Ρ型半導体 層を含む積層体により構成される発光素子であって、 該 Ν型半 ¾本層及び発光層及び Ρ型半導 体層の積層体がセラミック材料を主成分とする焼結体に形成されていることを とする発光 素子。
項 1189. セラミック材料を主成分とする焼結体が基板状であることを特徴とする項 11 88に記載された発光素子。
項 1190. セラミック材料を主成分とする焼結体が光透過性を有することを特徴とする項 1188又は 1189に記載されたいずれかの発光素子。
項 1191. セラミツク材料を主成分とする焼結体が 6¾過率 1 %以上のものであることを 特徴とする 1188、 1189項 1190に記載されたいずれかの発光素子。
項 1192. セラミック材料を主成分とする焼結体が光 ¾ 率 10%以上のものであること を特徴とする項 1191に記載された発光素子。
項 1193. セラミック材料を主成分とする焼結体が光透過率 20%以上のものであること を特徴とする項 1191又は 1192に記載されたいずれかの発光素子。
項 1194. セラミック材料を主成分とする焼結体が光 ¾ 率 30%以上のものであること を特徴とする項 1191、 1192又は 1193記載されたいずれかの発光素子。
項 1195. セラミック材料を主成分とする焼結体が光 ¾1率 40%以上のものであること を特徴とする項 1191、 1192、 1193又は 1194記載されたいずれかの発光素子。 項 1196. セラミック材料を主成分とする焼結体が光 ¾i率 50%以上のものであること を特徴とする項 1191、 1192、 1193、 1194又は 1195記載されたいずれかの 発光素子。
項 1197. セラミック材料を主成分とする焼結体が光 ¾ 率 60%以上のものであること を ^[とする項 1191、 1192、 1193、 1194、 1195又は 1196記載された いずれかの発光素子。
項 1198. セラミック材料を主成分とする焼結体が¾¾過率 80%以上のものであること を特徴とする項 1191、 1192、 1193、 1194、 1195、 1196又は 1197 記載されたいずれかの発光素子。
項 1199. セラミック材料を主成分とする焼結体が光 ¾i 率 85%以上のものであること を とする項 1191、 1192、 1193、 1194、 1195、 1196、 1197又 は 1198記載されたいずれかの発光素子。
項 1200. セラミツク材料を主成分とする焼結体力 率 1 %未満のものであることを 特徴とする項 1188、 1189、 1190、 1191、 1192、 1193、 1194、 1 195、 1196、 1197、 1198又は 1199に載されたいずれかの発光素子。
項 1201. セラミック材料を主成分とする焼結体が ¾¾ 率 0%であることを特徴とする 項 1200に記載された発光素子。
項 1202. ¾¾1性あるいは 率が少なくとも波長 200 nm〜800 nmの範囲の 光に対してのものであることを特徴とする項 1190、 1191、 1192、 1193、 11 94、 1195、 1196、 1197、 1198、 1199、 1200又は 1201に載され たいずれかの発光素子。
項 1203. セラミック材料を主成分とする焼結体の平均表面粗さが R a 2000 nm以下 であることを特徵とする項 1188、 1189、 1190、 1191、 1192、 1193、 1194、 1195、 1196、 1197、 1198、 1199、 1200、 1201又は 1 202に載されたいずれかの発光素子。
項 1204. セラミック材料を主成分とする焼結体の平均表面粗さが R a 1000 nm以下 であることを特徴とする項 1203に載された発光素子。
項 1205. セラミック材料を主成分とする焼結体の平均表面粗さが R a 100 nm以下で あることを特徴とする項 1203又は 1204に記載されたいずれかの発光^?。
項 1206. セラミック材料を主成分とする焼結体の平均表面粗さが R a 20 nm以下であ ることを特徴とする項 1203、 1204又は 1205に記載されたいずれかの発光素子。 項 1207. セラミック材料を主成分とする焼結体の平均表面粗さが R a 10 nm以下であ ることを特徴とする項 1203、 1204、 1205又は 1206に記載されたいずれかの発 光素子。
項 1208. セラミック材料を主成分とする焼結体の平均表面粗さが R a 5 nm以下である ことを特徴とする項 1203、 1204、 1205、 1206又は 1207に載されたいずれ かの発光 。
項 1209. セラミック材料を主成分とする焼結体が表面粗さの大きいものであることを特 徵とする項 1188、 1189、 1190、 1191、 1192、 1193、 1194、 11 95、 1196、 1197、 1198、 1199、 1200、 1201、 1202、 1203、 1204又は 1205に載されたいずれかの発光素子。
項 1210. セラミック材料を主成分とする焼結体の平均表面粗さが R a 70 nm以上であ ることを ^とする項 1188、 1189、 1190、 1191、 1192、 1193、 11 94、 1195、 1196、 1197、 1198、 1199、 1200、 1201、 1202、 1203、 1204、 1205又は 1209に載されたいずれかの発光素子。
項 1211. セラミック材料を主成分とする焼結体の平均表面粗さが Ral 00 Onmより 大きいことを特徴とする項 1210に記載された発光素子。
項 1212. セラミック材料を主成分とする焼結体の平均表面粗さが R a 2000 nmより 大きいことを特徴とする項 1210又は 1211に記載されたいずれかの発光素子。
項 1213. セラミック材料を主成分とする焼結体の表面が焼き放し (a s— f i r e)、 ラ
ッフ Iff磨、 ブラスト研磨、 鏡面研磨、 化学腐食及びプラズマガスによる腐食のうちから選ばれ た少なくともいずれかの状態であることを特徴とする項 1188、 1189、 1190、 11 91、 1192、 1193、 1194、 1195、 1196、 1197、 1198、 1199、 1200、 1201、 1202、 1203、 1204、 1205、 1206、 1207、 12
08、 1209、 1210、 1211又は 1212に載されたいずれかの発光素子。
項 1214. セラミック材料を主成分とする焼結体の表面が鏡面研磨された状態であること を特徴とする項 1200に記載された発光素子。
項 1215. セラミック材料を主成分とする焼結体がう 性を有しかつ表面粗さの大きい ものであることを特徴とする項 1188、 1189、 1190、 1191、 1192、 119 3、 1194、 1195、 1196、 1197、 1198、 1199、 1200、 1201、
1202、 1203、 1204、 1205、 1206、 1207、 1208、 1209、 12 10、 1211、 1212、 1213又は 1214に記載されたいずれかの発光素子。
項 1216. セラミック材料を主成分とする焼結体が導電性を有することを特徴とする項 1 188、 1189、 1190、 1191、 1192、 1193、 1194、 1195、 119 6、 1197、 1198、 1199、 1200、 1201、 1202、 1203、 1204、
1205、 1206、 1207、 1208、 1209、 1210、 1211、 1212、 12 13、 1214又は 1215記載されたいずれかの発光素子。
項 1217. セラミック材料を主成分とする! ¾結体が室温において 1 X 104Ω · cm以下の 抵抗率を有することを特徴とする項 1188、 1189、 1190、 1191、 1192、 1 193、 1194、 1195、 1196、 1197、 1198、 1199、 1200、 120 1、 1202、 1203、 1204、 1205、 1206、 1207、 1208、 1209、 1210、 1211、 1212、 1213、 1214、 1215又は 1216記載されたいず れかの発光素子。
項 1218. セラミック材料を主成分とする 結体が室温において 1 X 102Ω · cm以下の 抵抗率を有することを特徴とする項 1217に記載された発光素子。
項 1219. セラミック材料を主成分とする 結体が室温において 1 X 10°Ω · cm以下の ί氐抗率を有することを特徴とする項 1216、 1217又は 1218に記載されたいずれかの 発光素子。
項 1220. セラミック材料を主成分とする焼結体が室温において 1 X 10_ · cm以下 の氐抗率を有することを,とする項 1216、 1217、 1218又は 1219に記載され たいずれかの発光素子。
項 1221. セラミック材料を主成分とする焼結体が室温において 1 X 10- 2Ω · cm以下 の ί氐抗率を有することを特徴とする項 1216、 1217、 1218、 1219又は 1220 に記載されたいずれかの発光素子。
項 1222. セラミック材料を主成分とする焼結体が光 ¾ 性を有しかつ導電性を有するこ とを特徴とする項 1188、 1189、 1190、 1191、 1192、 1193、 1194、 1195、 1196、 1197、 1198、 1199、 1200、 1201、 1202、 12 03、 1204、 1205、 1206、 1207、 1208、 1209、 1210、 1211、 1212、 1213、 1214、 1215、 1216、 1217、 1218、 1219、 12
20又は 1221に記載されたいずれかの発光素子。
項 1223. セラミック材料を主成分とする焼結体が窒化ガリウム、 窒化インジウム、 窒化 アルミニウムのうちから選ばれた少なくとも 1種以上を主成分とする薄膜を形成したものであ ることを特徴とする項 1188、 1189、 1190、 1191、 1192、 1193、 11 94、 1195、 1196、 1197、 1198、 1199、 1200、 1201、 1202、
1203、 1204、 1205、 1206、 1207、 1208、 1209、 1210、 12 11、 1212、 1213、 1214、 1215、 1216、 1217、 1218、 1219、 1220、 1221又は 1222に記載されたいずれかの発光素子。
項 1224. セラミック材料を主成分とする焼結体に形成された窒化ガリウム、 窒化インジ ゥム、窒化アルミニウムのうちから選ばれた少なくとも 1種以上を主成分とする薄膜が単結晶、 無定形、 多結晶、 配向性多結晶のうちから選ばれる少なくともいずれかの結晶状態を有するこ とを特徴とする項 1223に記載された発光^?。
項 1225. セラミック材料を主成分とする焼結体に形成された窒化ガリウム、 窒化インジ ゥム、 窒化アルミニウムのうちから選ばれた少なくとも 1種以上を主成分とする薄膜の少なく とも一部が単結晶からなることを特徴とする項 1223又は 1224に記載されたいずれかの 発光素子。
項 1226. セラミック材料を主成分とする焼結体に形成された窒化ガリウム、 窒化インジ ゥム、 窒化アルミニウムのうちから選ばれた少なくとも 1種以上を主成分とする薄膜が単結晶 だけからなることを特徴とする項 1225に記載された発光素子。
項 1227. セラミック材料を主成分とする焼結体に形成された窒化ガリウム、 窒化インジ ゥム、 窒化アルミニウムのうちから選ばれた少なくとも 1種以上を主成分とする薄膜が単一層 であることを特徴とする項 1223、 1224、 1225又は 1226に記載されたいずれか の発光素子。
項 1228. セラミック材料を主成分とする焼結体に形成された窒化ガリウム、 窒化インジ ゥム、 窒化アルミニウムのうちから選ばれた少なくとも 1種以上を主成分とする薄膜が少なく とも 2以上の層から構成されていることを特徴とする項 1223、 1224、 1225又は 1
226に記載されたいずれかの発光素子。
項 1229. 少なくとも 2以上の層から構成されている薄膜の各層がそれぞ 結晶、 配向 性多結晶、 多結晶、 無定形の中から選ばれた少なくともいずれかの結晶状態を有することを特 徴とする項 1228に記載された発光素子。
項 1230. 少なくとも 2以上の層から構成されている薄膜においてセラミック材料を主成 分とする焼結体に直接形成されている窒化ガリウム、 窒化インジウム、 窒化アルミニウムのう ちから選ばれた少なくとも 1種以上を主成分とする薄膜が無定形、 多結晶、 配向性多結晶、 単 結晶のうちから選ばれる少なくともいずれかの結晶状態を有することを特徴とする項 1228 又は 1229に記載されたいずれかの発光素子。
項 1231. セラミック材料を主成分とする焼結体に直接形成されている窒化ガリウム、 窒 化インジウム、 窒化アルミニウムのうちから選ばれた少なくとも 1種以上を主成分とする薄膜 が無定形であることを特徴とする項 1224、 1225、 1226、 1227、 1228、 1 229又は 1230に記載されたいずれかの発光素子。
項 1232. セラミック材料を主成分とする焼結体に直接形成されている窒化ガリウム、 窒 ィ匕インジウム、 窒化アルミニウムのうちから選ばれた少なくとも 1種以上を主成分とする薄膜 力 S多結晶であることを特徴とする項 1224、 1225、 1226、 1227、 1228、 1 229又は 1230に記載されたいずれかの発光素子。
項 1233. セラミック材料を主成分とする焼結体に直接形成されている窒化ガリウム、 窒 ィ匕インジウム、 窒化アルミニウムのうちから選ばれた少なくとも 1種以上を主成分とする薄膜 が配向性多結晶であることを特徴とする項 1224、 1225、 1226、 1227、 122 8、 1229又は 1230に記載されたいずれかの発光素子。
項 1234. セラミック材料を主成分とする焼結体に直接形成されている窒化ガリウム、 窒 ィ匕インジウム、 窒化アルミニウムのうちから選ばれた少なくとも 1種以上を主成分とする薄膜
が単結晶であることを特徴とする項 1 2 2 4、 1 2 2 5、 1 2 2 6、 1 2 2 7、 1 2 2 8、 1 2 2 9又は 1 2 3 0に記載されたいずれかの発光素子。
項 1 2 3 5. 少なくとも 2以上の層から構成されている薄膜においてセラミック材料を主成 分とする焼結体に窒化ガリウム、 窒化インジウム、 窒化アルミニウムのうちから選ばれた少な くとも 1種以上を主成分とする単結晶、 配向性多結晶、 多結晶、 無定形のうちから選ばれる少 なくともいずれかの結晶状態を有する薄膜が少なくとも 1層以上形成され、 さらにその上に窒 化ガリウム、 窒化インジウム、 窒化アルミニウムのうちから選ばれた少なくとも 1種以上を主 成分とする単結晶、 配向性多結晶、 多結晶、 無定形のうちから選ばれる少なくともいずれかの 結晶状態を有する薄膜が少なくとも 1層以上形成されていることを特徴とする項 1 2 2 8、 1 2 2 9、 1 2 3 0、 1 2 3 1、 1 2 3 2、 1 2 3 3又は 1 2 3 4に記載されたいずれかの発光 素子。
項 1 2 3 6. 少なくとも 2以上の層から構成されている薄膜においてセラミック材料を主成 分とする焼結体に窒化ガリウム、 窒化インジウム、 窒化アルミニウムのうちから選ばれた少な くとも 1種以上を主成分とする単結晶、 配向性多結晶、 多結晶、 無定形のうちから選ばれる少 なくともいずれかの結晶状態を有する薄膜が少なくとも 1層以上形成され さらにその上に窒 化ガリウム、 窒化インジウム、 窒化アルミニウムのうちから選ばれた少なくとも 1種以上を主 成分とする単結晶薄膜が少なくとも 1層以上形成されていることを特徴とする項 1 2 3 5に記 載されたいずれかの発光素子。
項 1 2 3 7. 少なくとも 2以上の層から構成されている薄膜においてセラミック材料を主成 分とする焼結体に窒化ガリウム、 窒化インジウム、 窒化アルミニウムのうちから選ばれた少な くとも 1種以上を主成分とする配向性多結晶、 多結晶、 無定形のうちから選ばれる少なくとも いずれかの結晶状態を有する薄膜が少なくとも 1層以上形成され、 さらにその上に窒化ガリゥ ム、 窒化インジウム、 窒化アルミニウムのうちから選ばれた少なくとも 1種以上を主成分とす る単結晶薄膜が少なくとも 1層以上形成されていることを特徴とする項 1 2 3 6に記載された 発光素子。
項 1 2 3 8. 少なくとも 2以上の層から構成されている薄膜においてセラミック材料を主成 分とする焼結体に窒化ガリウム、 窒化インジウム、 窒化アルミニウムのうちから選ばれた少な くとも 1種以上を主成分とする無定形薄膜が少なくとも 1層以上形成され、 さらにその上に窒 化ガリウム、 窒化インジウム、 窒化アルミニウムのうちから選ばれた少なくとも 1種以上を主 成分とする単結晶薄膜が少なくとも 1層以上形成されていることを特徴とする項 1 2 3 6又は
1 2 3 7に記載されたいずれかの発光素子。
項 1 2 3 9. 少なくとも 2以上の層から構成されている薄膜においてセラミック材料を主成 分とする焼結体に窒化ガリウム、 窒化インジウム、 窒化アルミニウムのうちから選ばれた少な くとも 1種以上を主成分とする多結晶薄膜が少なくとも 1層以上形成され、 さらにその上に窒 化ガリウム、 窒化インジウム、 窒化アルミニウムのうちから選ばれた少なくとも 1種以上を主 成分とする単結晶薄膜が少なくとも 1層以上形成されていることを特徴とする項 1 2 3 6又は 1 2 3 7に記載されたいずれかの発光素子。
項 1 2 4 0. 少なくとも 2以上の層から構成されている薄膜においてセラミック材料を主成 分とする焼結体に窒化ガリウム、 窒化インジウム、 窒化アルミニウムのうちから選ばれた少な くとも 1種以上を主成分とする配向性多結晶薄膜が少なくとも 1層以上形成され、 さらにその 上に窒化ガリウム、 窒化インジウム、 窒化アルミニウムのうちから選ばれた少なくとも 1種以 上を主成分とする単結晶薄膜が少なくとも 1層以上形成されていることを特徴とする項 1 2 3 6又は 1 2 3 7に記載されたいずれかの発光素子。
項 1 2 4 1. 少なくとも 2以上の層から構成されている薄膜においてすベての層が単結晶だ
けから構成されていることを特徴とする項 1228、 1229、 1230、 1231、 123 2、 1233、 1234、 1235、 1236、 1237、 1238、 1239又は 1240 に記載されたいずれかの発光素子。
項 1242. セラミツク材料を主成分とする焼結体に形成された窒化ガリゥム、 窒化インジ ゥム、 窒化アルミニウムのうちから選ばれた少なくとも 1種以上を主成分とする薄膜の最上層 は単結晶薄膜であることを體とする項 1224、 1225、 1226、 1227、 1228、 1229、 1230、 1231、 1232、 1233、 1234、 1235、 1236、 12 37、 1238、 1239、 1240又は 1241に記載されたいずれかの発光素子。
項 1243. セラミック材料を主成分とする焼結体に形成された窒化ガリゥム、 窒化ィンジ ゥム、 窒化アルミニウムのうちから選ばれた少なくとも 1種以上を主成分とする単結晶薄膜の C軸がセラミック材料を主成分とする焼結体面に対して垂直な方向に形成されていることを特 徴とする項 1224、 1225、 1226、 1227、 1228、 1229、 1230、 12 31、 1232、 1233、 1234、 1235、 1236、 1237、 1238、 1239、 1240、 1241又は 1242に記載されたいずれかの発光^?。
項 1244. セラミック材料を主成分とする焼結体に形成された窒化ガリウム、 窒化インジ ゥム、 窒化アルミニウムのうちから選ばれた少なくとも 1種以上を主成分とする単結晶薄膜の C軸がセラミツク材料を主成分とする焼結体面に対して水平な方向に形成されていることを特 徴とする項 1224、 1225、 1226、 1227、 1228、 1229、 1230、 12 31、 1232、 1233、 1234、 1235、 1236、 1237、 1238、 1239、 1240、 1241又は 1242に記載されたいずれかの発光素子。
項 1245. セラミック材料を主成分とする焼結体に形成された窒化ガリウム、 窒化インジ ゥム、 窒化アルミニウムのうちから選ばれた少なくとも 1種以上を主成分とする配向性多結晶 薄膜の C軸がセラミック材料を主成分とする焼結体面に対して垂直な方向に形成されているこ とを特徴とする項 1224、 1225、 1227、 1228、 1229、 1230、 1231、 1232、 1233、 1234、 1235、 1236、 1237、 1238、 1239、 12 40又は 1242に記載されたいずれかの発光素子。
項 1246. セラミック材料を主成分とする焼結体に形成された窒化ガリウム、 窒化インジ ゥム、 窒化アルミニウムのうちから選ばれた少なくとも 1種以上を主成分とする配向性多結晶 薄膜の C軸がセラミック材料を主成分とする焼結体面に対して水平な方向に形成されているこ とを特徴とする項 1224、 1225、 1227、 1228、 1229、 1230、 1231、 1232、 1233、 1234, 1235、 1236、 1237、 1238、 1239、 12 40又は 1242に記載されたいずれかの発光素子。
項 1247. セラミック材料を主成分とする焼結体に形成された窒化ガリウム、 窒化インジ ゥム、 窒化アルミニウムのうちから選ばれた少なくとも 1種以上を主成分とする薄膜が導電性 を有することを とする項 1223、 1224、 1225、 1226、 1227、 1228、 1229、 1230、 1231、 1232、 1233、 1234, 1235、 1236、 12 37、 1238、 1239、 1240、 1241、 1242、 1243、 1244、 1245 又は 1246に記載されたいずれかの発光素子。
項 1248. セラミック材料を主成分とする焼結体に形成された窒化ガリウム、 窒化インジ ゥム、 窒化アルミニウムのうちから選ばれた少なくとも 1種以上を主成分とする薄膜の室温に おける纖率が 1 X 104Ω · cm以下であることを特徴とする項 1223、 1224、 122 5、 1226、 1227、 1228、 1229、 1230、 1231、 1232、 1233、 1234、 1235、 1236、 1237、 1238、 1239、 1240、 1241、 12 42、 1243、 1244、 1245、 1246又は 1247に記載されたいずれかの発光素
子。 . ' 項 1249. セラミック材料を主成分とする焼結体に形成された窒化ガリウム、 窒化インジ ゥム、 窒化アルミニウムのうちから選ばれた少なくとも 1種以上を主成分とする薄膜の室温に おける ί厳率が 1 X 102 Ω · c m以下であることを [とする項 1247又は 1248に記載 されたいずれかの発光素子。
項 1250. セラミック材料を主成分とする焼結体に形成された窒化ガリウム、 窒化インジ ゥム、 窒化アルミニウムのうちから選ばれた少なくとも 1種以上を主成分とする薄膜の室温に おける抵抗率が 1 X 101 Ω · c m以下であることを特徴とする項 1247、 1248又は 12
49に記載されたいずれかの発光素子。
項 1251. セラミック材料を主成分とする焼結体に形成された窒化ガリウム、 窒化インジ ゥム、 窒化アルミニウムのうちから選ばれた少なくとも 1種以上を主成分とする薄膜の室温に おける ί氐坊率が、 1 X 100Ω · cm以下であることを特徴とする項 1247、 1248、 124 9又は 1250に記載されたいずれかの発光素子。
項 1252. セラミック材料を主成分とする焼結体に形成された薄膜が少なくとも窒化ガリ ゥムを含有するものであることを纖とする項 1223、 1224、 1225、 1226、 1 227、 1228、 1229、 1230、 1231、 1232、 1233、 1234, 123 5、 1236、 1237、 1238、 1239、 1240、 1241、 1242、 1243、 1244、 1245、 1246、 1247、 1248、 1249又は 1250に記載されたい ずれかの発光素子。
項 1253. セラミック材料を主成分とする焼結体に形成された薄膜が少なくとも窒化ガリ ゥムを含むかあるいは窒化ガリウムを主成分とする薄膜を有することを ϋ (とする項 1223、 1224、 1225、 1226、 1227、 1228、 1229、 1230、 1231、 12 32、 1233、 1234、 1235、 1236、 1237、 1238、 1239、 1240、 1241、 1242、 1243、 1244、 1245、 1246、 1247、 1248、 12 49、 1250又は 1251に記載されたいずれかの発光素子。
項 1254. セラミック材料を主成分とする焼結体に形成された薄膜が窒化ガリウムを主成 分とするものであることを特徴とする項 1252又は 1253に記載されたいずれかの発光素 子。
項 1255. セラミック材料を主成分とする 結体に形成された薄膜が A 1 xGay Inx_x_ yN (0<y≤l) で表わされる組成を有することを體とする項 1252、 1253又は 12
54に記載されたいずれかの発光素子。
項 1256. セラミック材料を主成分とする焼結体に形成された薄膜が窒化ガリウムを 50 モル%以上含むを體とする項 1252、 1253、 1254又は 1255に記載されたいず れかの発光素子。
項 1257. セラミック材料を主成分とする焼結体に形成された少なくとも窒化ガリウムを 含むかあるいは窒化ガリウムを主成分とする薄膜が無定形、 多結晶、 配向性多結晶、 単結晶の うちから選ばれた少なくともいずれかの結晶状態であることを特徴とする項 1252、 125 3、 1254、 1255又は 1256に記載されたいずれかの発光素子。
項 1258. セラミック材料を主成分とする焼結体に形成された少なくとも窒化ガリウムを 含むかあるいは窒化ガリウムを主成分とする薄膜が単結晶であることを特徴とする項 1257 に記載された発光素子。
項 1259. セラミック材料を主成分とする焼結体に形成された薄膜の最上層が少なくとも 窒化ガリゥムを含むかあるいは窒化ガリゥムを主成分とするものであることを特徴とする項 1 252、 1253、 1254、 1255、 1256、 1257又は 1258に記載されたいず
れかの発光素子。
項 1260. セラミック材料を主成分とする焼結体に形成された薄膜の最上層が少なくとも 窒化ガリゥムを含むかあるいは窒化ガリゥムを主成分とする単結晶であることを特徴とする項 1259に記載された発光素子。
項 1261. セラミック材料を主成分とする焼結体に形成された薄膜が A 1XG a (0 ≤x≤l. 0) の化学式であらわされる組成物を主成分とするものであることを特徴とする項 1223、 1224、 1225、 1226、 1227、 1228、 1229、 1230、 12 31、 1232、 1233、 1234、 1235、 1236、 1237、 1238、 1239、 1240、 1241、 1242、 1243、 1244、 1245、 1246、 1247、 12 48、 1249、 1250、 1251、 1252、 1253、 1254、 1255、 1256、 1257、 1258、 1259又は 1260に記載されたいずれかの発光素子。
項 1262. セラミック材料を主成分とする焼結体に形成された窒化ガリウム、 窒化インジ ゥム、 窒化アルミニウムのうちから選ばれた少なくとも 1種以上を主成分とする薄膜が少なく とも単結晶薄膜層を有し該単結晶薄 の厚みが 300 未満であることを特徴とする項 1 223、 1224, 1225、 1226、 1227、 1228、 1229、 1230、 123 1、 1232、 1233、 1234、 1235、 1236、 1237、 1238、 1239、
1240、 1241、 1242、 1243、 1244、 1245、 1246、 1247、 12 48、 1249、 1250、 1251、 1252、 1253、 1254、 1255、 1256、 1257、 1258、 1259、 1260又は 1261に記載されたいずれかの発光素子。 項 1263. セラミック材料を主成分とする焼結体に形成された窒化ガリウム、 窒化インジ ゥム、 窒化アルミニウムのうちから選ばれた少なくとも 1種以上を主成分とする薄膜が少なく とも単結晶薄膜層を有し該単結晶薄膜層の厚みが 200 m以下であることを特徴とする項 1
262に記載された発光素子。
項 1264. セラミック材料を主成分とする焼結体に形成された薄膜が少なくとも 0. In m以上の厚みを有することを特徴とする項 1223、 1224、 1225、 1226、 122 7、 1228、 1229、 1230、 1231、 1232、 1233、 1234, 1235、 1236、 1237、 1238、 1239、 1240、 1241、 1242、 1243、 12 44、 1245、 1246、 1247、 1248、 1249、 1250、 1251、 1252、 1253、 1254、 1255、 1256、 1257、 1258、 1259、 1260、 12 61、 1262又は 1263に記載されたいずれかの発光素子。
項 1265. セラミック材料を主成分とする焼結体に形成された薄膜が少なくとも 0. 5n m以上の厚みを有することを特徴とする項 1264に記載された発光素子。
項 1266. セラミック材料を主成分とする焼結体に形成された薄膜が少なくとも 0. 3 m以上の厚みを有することを特徴とする項 1264又は 1265に記載されたいずれかの発光 軒。
項 1267. セラミック材料を主成分とする焼結体に形成された薄膜が少なくとも 3. 5ιι m以上の厚みを有することを特徴とする項 1264、 1265又は 1266に記載されたいず れかの発光素子。
項 1268. セラミック材料を主成分とする焼結体に形成された薄膜が少なくとも 10 m 以上の厚みを有することを特徴とする項 1264、 1265、 1266又は 1267に記載さ れたいずれかの発光素子。
項 1269. セラミック材料を主成分とする焼結体に形成された薄膜が少なくとも 50 βτη 以上の厚みを有することを特徴とする項 1264、 1265、 1266、 1267又は 126 8に記載されたいずれかの発光素子。
項 1270. セラミック材料を主成分とする焼結体に形成された窒化ガリウム、 窒化インジ ゥム、 窒化アルミニウムのうちから選ばれた少なくとも 1種以上を主成分とする薄膜の厚みが 100 O m以下であることを特徴とする項 1223、 1224、 1225、 1226、 12 27、 1228、 1229、 1230、 1231、 1232、 1233、 1234、 1235、 1236、 1237、 1238、 1239、 1240、 1241、 1242、 1243、 12 44、 1245、 1246、 1247、 1248、 1249、 1250、 1251、 1252、 1253、 1254、 1255、 1256、 1257、 1258、 1259、 1260、 12 61、 1262、 1263、 1264、 1265、 1266、 1267、 1268又は 126 9に記載されたいずれかの発光素子。
項 1271. セラミック材料を主成分とする焼結体に形成された薄膜の厚みが 500 m以 下であることを特徴とする項 1270に記載された発光泰チ。
項 1272. セラミック材料を主成分とする焼結体に形成された薄膜が単結晶、 無定形、 多 結晶、 配向性多結晶のうちから選ばれた少なくともいずれか 2以上の結晶状態が同時に混在し ているものからなることを とする項 1223、 1224、 1225、 1226、 1227、 1228、 1229、 1230、 1231、 1232、 1233、 1234、 1235、 12
36、 1237、 1238、 1239、 1240、 1241、 1242、 1243、 1244、 1245、 1246、 1247、 1248、 1249、 1250、 1251、 1252、 12
53、 1254、 1255、 1256、 1257、 1258、 1259、 1260、 1261、 1262、 1263、 1264、 1265、 1266、 1267、 1268、 1-269、 12 70又は 1271に記載されたいずれかの発光素子。
項 1273. セラミック材料を主成分とする焼結体に形成された薄膜が単一層あるいは少な くとも 2以上の層からなり、 該薄膜の少なくとも 1以上の層が単結晶、 無定形、 多結晶、 配向 性多結晶のうちから選ばれた少なくともいずれか 2以上の結晶状態が同時に混在しているもの からなることを體とする項 1223、 1224、 1225、 1226、 1227、 1228、 1229、 1230、 1231、 1232、 1233、 1234、 1235、 1236、 12
37、 1238、 1239、 1240、 1241、 1242、 1243、 1244、 1245、 1246、 1247、 1248、 1249、 1250、 1251、 1252、 1253、 12
54、 1255、 1256、 1257、 1258、 1259、 1260、 1261、 1262、 1263、 1264、 1265、 1266、 1267、 1268、 1269、 1270、 12 71又は 1272に記載されたいずれかの発光素子。
項 1274. セラミック材料を主成分とする焼結体に形成された窒化ガリウム、 窒化インジ ゥム、 窒化アルミニウムのうちから選ばれた少なくとも 1種以上を主成分とする単結晶薄膜の ミラー指数 (002) の格子面の X線回折ロッキングカーブの半値幅が 3600秒以下である ことを特 ί敫とする項 1223、 1224、 1225、 1226、 1227、 1228、 122 9、 1230、 1231、 1232、 1233、 1234、 1235、 1236、 1237、 1238、 1239、 1240、 1241、 1242、 1243、 1244、 1245、 12 46、 1247、 1248、 1249、 1250、 1251、 1252、 1253、 1254、 1255、 1256、 1257、 1258、 1259、 1260、 1261、 1262、 12 63、 1264, 1265、 1266、 1267、 1268、 1269、 1270、 1271、 1272又は 1273に記載されたいずれかの発光素子。
項 1275. セラミック材料を主成分とする焼結体に形成された窒化ガリウム、 窒化インジ ゥム、 窒化アルミニウムのうちから選ばれた少なくとも 1種以上を主成分とする単結晶薄膜の ミラー指数 (002) の格子面の X線回折ロッキングカーブの半値幅が 300秒以下であるこ とを特徴とする項 1274に記載された発光素子。
項 1276. セラミック材料を主成分とする焼結体に形成された窒化ガリゥム、 窒化インジ ゥム、 窒化アルミニウムのうちから選ばれた少なくとも 1種以上を主成分とする単結晶薄膜の ミラー指数 (002) の格子面の X線回折ロッキングカーブの半値幅が 240秒以下であるこ とを特徴とする項 1274又は 1275に記載されたいずれかの発光素子。
項 1277. セラミック材料を主成分とする焼結体に形成された窒化ガリウム、 窒化インジ ゥム、 窒化アルミニウムのうちから選ばれた少なくとも 1種以上を主成分とする単結晶薄膜の ミラー指数 (002) の格子面の X線回折ロッキングカーブの半値幅が 200秒以下であるこ とを特徴とする項 1274、 1275又は 1276に記載されたいずれかの発光素子。
項 1278. セラミック材料を主成分とする焼結体に形成された窒化ガリウム、 窒化インジ ゥム、 窒化アルミニウムのうちから選ばれた少なくとも 1種以上を主成分とする単結晶薄膜の ミラー指数 (002) の格子面の X線回折ロッキングカーブの半値幅が 150秒以下であるこ とを とする項 1274、 1275、 1276又は 1277に記載されたいずれかの発光素 子。
項 1279. セラミツク材料を主成分とする焼結体に形成された窒化ガリゥム、 窒化インジ ゥム、 窒化アルミニウムのうちから選ばれた少なくとも 1種以上を主成分とする単結晶薄膜の ミラ一指数 (002) の格子面の X線回折ロッキングカーブの半値幅が 130秒以下であるこ とを特徴とする項 1274、 1275、 1276、 1277又は 1278に記載されたいずれ かの発光素子。
項 1280. セラミック材料を主成分とする焼結体に形成された窒化ガリウム、 窒化インジ ゥム、 窒化アルミニウムのうちから選ばれた少なくとも 1種以上を主成分とする単結晶薄膜の ミラ一指数 (002) の格子面の X線回折ロッキング力一ブの半値幅が 100秒以下であるこ とを特徴とする項 1274、 1275、 1276、 1277、 1278又は 1279に記載さ れたいずれかの発光素子。
項 1281. セラミック材料を主成分とする焼結体が窒化ガリゥム、 窒化インジウム、 窒化 アルミニウムのうちから選ばれた少なくとも 1種以上を主成分とする単結晶薄膜を形成したも のであることを特徴とする項 1223、 1224、 1225、 1226、 1227、 1228、 1229、 1230、 1231、 1232、 1233、 1234、 1235、 1236、 12 37、 1238、 1239、 1240、 1241、 1242、 1243、 1244、 1245、 1246、 1247、 1248、 1249、 1250、 1251、 1252、 1253、 12 54、 1255、 1256、 1257、 1258、 1259、 1260、 1261、 1262、 1263、 1264、 1265、 1266、 1267、 1268、 1269、 1270、 12 71、 1272、 1273、 1274、 1275、 1276、 1277、 1278、 1279 又は 1280に記載されたいずれかの発光素子。
項 1282. 焼結体の主成分であるセラミック材料が金属元素及び半金属元素のうちから選 ばれた少なくとも 1種以上の元素と非金属元素のうちから選ばれた少なくとも 1種以上の元素 との組成物、 あるいは金属元素のうちから選ばれた少なくとも 1種以上の元素と半金属元素の うちから選ばれた少なくとも 1種以上の元素との組成物、 あるいは半金属元素のうちから選ば れた少なくともいずれか 2種以上の元素との組成物であることを特徴とする項 1188、 11 89、 1190、 1191、 1192、 1193、 1194、 1195、 1196、 1197、 1198、 1199、 1200、 1201、 1202、 1203、 1204、 1205、 12 06、 1207、 1208、 1209、 1210、 1211、 1212、 1213、 1214、 1215、 1216、 1217、 1218、 1219、 1220、 1221、 1222、 12 23、 1224、 1225、 1226、 1227、 1228、 1229、 1230、 1231、 1232、 1233、 1234、 1235、 1236、 1237、 1238、 1239、 12
40、 1241、 1242、 1243、 1244、 1245、 1246、 1247、 1248、 1249、 1250、 1251、 1252、 1253、 1254、 1255、 1256、 12 57、 1258、 1259、 1260、 1261、 1262、 1263、 1264、 1265、
1266、 1267、 1268、 1269、 1270、 1271、 1272、 1273、 12
74、 1275、 1276、 1277、 1278、 1279、 1280又は 1281に記載さ れたいずれかの発光素子。
項 1283. 半金属元素が 素、 炭素、珪素、 ゲルマニウム、 ヒ素、 アンチモン、 ビスマス、 セレン、 テルル、 ポロニウムのうちから選ばれた少なくとも 1種以上であることを特徴とする 項 1282に記載された発光素子。
項 1284. 半金属元素が炭素、 珪素のうちから選ばれた少なくとも 1種以上であることを 特徴とする項 1283に記載された発光素子。
項 1285. 非金属元素が窒素、 りん、 酸素、 硫黄、 フッ素、 塩素、 難、 沃素、 ァス夕チ ンのうちから選ばれた少なくとも 1種以上であることを特徴とする項 1219、 1220、 1
283又は 1284に記載されたいずれかの発光素子。
項 1286. 非金属元素が窒素、 酸素のうちから選ばれた少なくとも 1種以上であることを 特徴とする項 1285に記載された発光素子。
項 1287. セラミック材料が窒化物、 炭化物、 酸化物、 硼化物、 珪化物のうちから選ばれ た少なくともいずれかであることを特徴とする項 1188、 1189、 1190、 1191、 1192、 1193、 1194、 1195、 1196、 1197、 1198、 1199、 12 00、 1201、 1202、 1203、 1204、 1205、 1206、 1207、 1208、 1209、 1210、 1211、 1212、 1213、 1214、 1215、 1216、 12 17、 1218、 1219、 1220、 1221、 1222、 1223、 1224、 1225、 1226、 1227、 1228、 1229、 1230、 1231、 1232、 1233、 12 34、 1235、 1236、 1237、 1238、 1239、 1240、 1241、 1242、 1243、 1244、 1245、 1246、 1247、 1248、 1249、 1250、 12 51、 1252、 1253、 1254、 1255、 1256、 1257、 1258、 1259、 1260、 1261、 1262、 1263、 1264、 1265、 1266、 1267、 12 68、 1269、 1270、 1271、 1272、 1273、 1274、 1275、 1276、 1277、 1278、 1279、 1280、 1281、 1282、 1283、 1284, 12
85又は 1286に記載されたいずれかの発光素子。
項 1288. セラミック材料が窒化物、 炭化物、 酸化物のうちから選ばれた少なくともいず れかであることを特徴とする項 1287に記載された発光素子。
項 1289. セラミック材料を主成分とする焼結体が窒化アルミニウムを主成分とする ¾結 体であることを とする項 1188、 1189、 1190、 1191、 1192、 1193、 1194、 1195、 1196、 1197、 1198、 1199、 1200、 1201、 12 02、 1203、 1204、 1205、 1206、 1207、 1208、 1209、 1210、 1211、 1212、 1213、 1214、 1215、 1216、 1217、 1218、 12 19、 1220、 1221、 1222、 1223、 1224、 1225、 1226、 1227、 1228、 1229、 1230、 1231、 1232、 1233、 1234、 1235、 12 36、 1237、 1238、 1239、 1240、 1241、 1242、 1243、 1244、 1245、 1246、 1247、 1248、 1249、 1250、 1251、 1252、 12 53、 1254, 1255、 1256、 1257、 1258、 1259、 1260、 1261、 1262、 1263、 1264, 1265、 1266、 1267、 1268、 1269、 12 70、 1271、 1272、 1273、 1274、 1275、 1276、 1277、 1278、
1279、 1280、 1281、 1282、 1283、 1284. 1285、 1286、 12 87又は 1288に記載されたいずれかの発光素子。
項 1290. セラミック材料を主成分とする焼結体が六方晶系又は三方晶系のうちから選ば れた少なくともいずれかの結晶構造を有する材料を主成分とする焼結体であることを特徴とす る項 1188、 1189、 1190、 1191、 1192、 1193、 1194、 1195、 1196、 1197、 1198、 1199、 1200、 1201、 1202、 1203、 12 04、 1205、 1206、 1207、 1208、 1209、 1210、 1211、 1212、 1213、 1214、 1215、 1216、 1217、 1218、 1219、 1220、 12 21、 1222、 1223、 1224、 1225、 1226、 1227、 1228、 1229、 1230、 1231、 1232、 1233、 1234, 1235、 1236、 1237、 12 38、 1239、 1240、 1241、 1242、 1243、 1244、 1245、 1246、 1247、 1248、 1249、 1250、 1251、 1252、 1253、 1254、 12 55、 1256、 1257、 1258、 1259、 1260、 1261、 1262、 1263、 1264, 1265、 1266、 1267、 1268、 1269、 1270、 1271、 12 72、 1273、 1274, 1275、 1276、 1277、 1278、 1279、 1280、 1281、 1282、 1283、 1284、 1285、 1286、 1287又は 1288に記 載されたいずれかの発光素子。
項 1291. 六方晶系文は三方晶系のうちから選ばれた少なくともいずれかの結晶構造を有 する材料を主成分とする焼結体が 化 »、 酸化ベリリウム、 酸化アルミニウム、 炭化珪素、 窒化珪素、 窒化ガリウムのうちから選ばれた少なくとも 1種以上を主成分とする焼結体である ことを特徴とする項 1290に記載された発光素子。
項 1292.セラミック材料を主成分とする焼結体力職化ジフレコニゥム、酸化マグネシウム、 アルミン酸マグネシウム、 酸化チタン、 チタン酸バリウム、 チタン酸ジルコン醒、 希土類 素酸化物、 酸化トリウム、 各種フェライト、 ムライト、 フォルステライト、 ステアタイト、 結 晶ィ匕ガラスのうちから選ばれた少なくとも 1種以上を主成分とする焼結体であることを特徴と する項 1188、 1189、 1190、 1191、 1192、 1193、 1194、 1195、 1196、 1197、 1198、 1199、 1200、 1201、 1202、 1203、 12 04、 1205、 1206、 1207、 1208、 1209、 1210、 1211、 1212、 1213、 1214、 1215、 1216、 1217、 1218、 1219、 1220、 12 21、 1222、 1223、 1224、 1225、 1226、 1227、 1228、 1229、 1230、 1231、 1232、 1233、 1234、 1235、 1236、 1237、 12 38、 1239、 1240、 1241、 1242、 1243、 1244、 1245、 1246、 1247、 1248、 1249、 1250、 1251、 1252、 1253、 1254、 12 55、 1256、 1257、 1258、 1259、 1260、 1261、 1262、 1263、
1264, 1265、 1266、 1267、 1268、 1269、 1270、 1271、 12 72、 1273、 1274, 1275、 1276、 1277、 1278、 1279、 1280、 1281、 1282、 1283、 1284、 1285、 1286、 1287又は 1288に記 載されたいずれかの発光素子。
項 1293. セラミック材料を主成分とする焼結体が窒化アルミニウム、 酸化亜鉛、 酸化べ リリウム、 酸化アルミニウム、 炭化珪素、 窒化珪素、 窒化ガリウム、 酸化ジルコニウム、 酸化 マグネシウム、 アルミン酸マグネシウム、 酸化ィットリウムのうちから選ばれた少なくとも 1 種以上を主成分とする焼結体であることを特徴とする項 1289、 1290、 1291又は 1
292に記載されたいずれかの発光素子。
項 1294. セラミック材料を主成分とする焼結体が光透過性を有するものであることを特
徴とする項 1188、 1189、 1190、 1191、 1192、 1193、 1194、 11 95、 1196、 1197、 1198、 1199、 1200、 1201、 1202、 1203、 1204、 1205、 1206、 1207、 1208、 1209、 1210、 1211、 12 12、 1213、 1214、 1215、 1216、 1217、 1218、 1219、 1220、 1221、 1222、 1223、 1224、 1225、 1226、 1227、 1228、 12 29、 1230、 1231、 1232、 1233、 1234、 1235、 1236、 1237、 1238、 1239、 1240、 1241、 1242、 1243、 1244、 1245、 12 46、 1247、 1248、 1249、 1250、 1251、 1252、 1253、 1254、 1255、 1256、 1257、 1258、 1259、 1260、 1261、 1262、 12 63、 1264、 1265、 1266、 1267、 1268、 1269、 1270、 1271、 1272、 1273、 1274、 1275、 1276、 1277、 1278、 1279、 12 80、 1281、 1282、 1283、 1284, 1285、 1286、 1287、 1288、 1289、 1290、 1291、 1292又は 1293に記載されたいずれかの発光素子。 項 1295. セラミック材料を主成分とする焼結体が表面粗さの大きいものであることを特 徵とする項 1188、 1189、 1190、 1191、 1192、 1193、 1194、 11 95、 1196、 1197、 1198、 1199、 1200、 1201、 1202、 1203、 1204、 1205、 1206、 1207、 1208、 1209、 1210、 1211、 12 12、 1213、 1214、 1215、 1216、 1217、 1218、 1219、 1220、 1221、 1222、 1223、 1224、 1225、 1226、 1227、 1228、 12 29、 1230、 1231、 1232、 1233、 1234、 1235、 1236、 1237、 1238、 1239、 1240、 1241、 1242、 1243、 1244、 1245、 12 46、 1247、 1248、 1249、 1250、 1251、 1252、 1253、 1254、 1255、 1256、 1257、 1258、 1259、 1260、 1261、 1262、 12 63、 1264, 1265、 1266、 1267、 1268、 1269、 1270、 1271、 1272、 1273、 1274、 1275、 1276、 1277、 1278、 1279、 12 80、 1281、 1282、 1283、 1284、 1285、 1286、 1287、 1288、 1289、 1290、 1291、 1292、 1293又は 1294に記載されたいずれかの発 光素子。
項 1296. セラミック材料を主成分とする焼結体が窒化ガリウム、 窒化インジウム、 窒化 アルミニウムのうちから選ばれた少なくとも 1種以上を主成分とする薄膜を形成したものであ ることを體とする項 1188、 1189、 1190、 1191、 1192、 1193、 11 94、 1195、 1196、 1197、 1198、 1199、 1200、 1201、 1202、 1203、 1204、 1205、 1206、 1207、 1208、 1209、 1210、 12 11、 1212、 1213、 1214、 1215、 1216、 1217、 1218、 1219、 1220、 1221、 1222、 1223、 1224、 1225、 1226、 1227、 12 28、 1229、 1230、 1231、 1232、 1233、 1234、 1235、 1236、 1237、 1238、 1239、 1240、 1241、 1242、 1243、 1244、 12 45、 1246、 1247、 1248、 1249、 1250、 1251、 1252、 1253、 1254、 1255、 1256、 1257、 1258、 1259、 1260、 1261、 12 62、 1263、 1264、 1265、 1266、 1267、 1268、 1269、 1270、 1271、 1272、 1273、 1274、 1275、 1276、 1277、 1278、 12 79、 1280、 1281、 1282、 1283、 1284、 1285、 1286、 1287、 1288、 1289、 1290、 1291、 1292、 1293、 1294又は 1295に記 載されたいずれかの発光素子。
項 1297. セラミック材料を主成分とする焼結体が窒化ガリウム、 窒化インジウム、 窒化 アルミニウムのうちから選ばれた少なくとも 1種以上を主成分とする単結晶薄膜を形成したも のであることを體とする項 1188、 1189、 1190、 1191、 1192、 1193、 1194、 1195、 1196、 1197、 1198、 1199、 1200、 1201、 12 02、 1203、 1204、 1205、 1206、 1207、 1208、 1209、 1210、 1211、 1212、 1213、 1214、 1215、 1216、 1217、 1218、 12 19、 1220、 1221、 1222、 1223、 1224、 1225、 1226、 1227、 1228、 1229、 1230、 1231、 1232、 1233、 1234、 1235、 12 36、 1237、 1238、 1239、 1240、 1241、 1242、 1243、 1244、 1245、 1246、 1247、 1248、 1249、 1250、 1251、 1252、 12 53、 1254、 1255、 1256、 1257、 1258、 1259、 1260、 1261、 1262、 1263、 1264、 1265、 1266、 1267、 1268、 1269、 12 70、 1271、 1272、 1273、 1274、 1275、 1276、 1277、 1278、 1279、 1280、 1281、 1282、 1283、 1284、 1285、 1286、 12 87、 1288、 1289、 1290、 1291、 1292、 1293、 1294、 1295 又は 1296に記載されたいずれかの発光 。
項 1298. セラミック材料を主成分とする焼結体が窒化アルミニウムを主成分とする焼結 体であることを置とする項 1289、 1293、 1294、 1295、 1296又は 129 7に記載されたいずれかの発光素子。
項 1299. 窒化アルミニウムを主成分とする焼結体が光 ¾ 生を有するものであることを 特徴とする項 1298に記載された発光素子。
項 1300. 窒化アルミニウムを主成分とする焼結体が表面粗さの大きいものであることを 特徴とする項 1298又は 1299に記載されたいずれかの発光素子。
項 1301. 窒化アルミニウムを主成分とする焼結体が窒化ガリウム、 窒化インジウム、 窒 化アルミニウムのうちから選ばれた少なくとも 1種以上を主成分とする薄膜を形成したもので あることを特徴とする項 1298、 1299又は 1300に記載されたいずれかの発光 »。 項 1302. 窒化アルミニウムを主成分とする焼結体が窒化ガリウム、 窒化インジウム、 窒 化アルミニウムのうちから選ばれた少なくとも 1種以上を主成分とする単結晶薄膜を形成した ものであることを特徴とする項 1298、 1299、 1300又は 1301に記載されたいず れかの発光素子。
項 1303. 窒化アルミニウムを主成分とする焼結体が窒化アルミニウムを 2 (H機%以上 含有するものであることを [とする項 1298、 1299、 1300又は 1301に記載さ れたいずれかの発光素子。
項 1304. 窒化アルミニウムを主成分とする焼結体が窒化アルミニウムを 5 CH機%以上 含有するものであることを特徴とする項 1303に記載された発光素子。
項 1305. 窒化アルミニウムを主成分とする焼結体が導通ビアを有するものであることを 特徴とする項 1298、 1299、 1300、 1301、 1302、 1303又は 1304に 記載されたいずれかの発光素子。
項 1306. 窒化アルミニウムを主成分とする焼結体が薄騰電性材料を有するものである ことを特徴とする項 1298、 1299、 1300、 1301、 1302、 1303、 130 4又は 1305に記載されたいずれかの発光素子。
項 1307. 薄騰電性材料が金属、 合金、 金属窒化物のうちから選ばれた少なくとも 1種 以上の材料からなることを特徴とする項 1306に記載された発光素子。
項 1308. 薄麟電性材料が金、 銀、 銅、 アルミニウム、 鉄、 コバルト、 ニッケル、 ルテ
二ゥム、 ロジウム、 パラジウム、 オスミウム、 イリジウム、 白金、 タンタル、 モリブデン、 夕 ングステン、 クロム、 チタン、 ニッケル〜クロム合金、 窒化チタン、 窒化ジルコニウム、 窒化 タンタル、 のうちから選ばれた少なくとも 1種以上を主成分とする材料からなることを特徴と する項 1306又は 1307に記載されたいずれかの発光素子。
項 1309. セラミック材料を主成分とする焼結体が六方晶系又は三方晶系のうちから選ば れた少なくともいずれかの結晶構造を有する材料を主成分とする焼結体であることを特徴とす る項 1290、 1291、 1293、 1294、 1295、 1296又は 1297に記載され たいずれかの発光素子。
項 1310. 六方晶系又は三方晶系のうちから選ばれた少なくともいずれかの結晶構造を有 する材料を主成分とする焼結体が光 ¾性を有するものであることを特徴とする項 1309に 記載された発光素子。
項 1311. 六方晶系又は三方晶系のうちから選ばれた少なくともいずれかの結晶構造を有 する材料を主成分とする焼結体が表面粗さの大きいものであることを特徴とする項 1309又 は 1310に記載されたいずれかの発光素子。
項 1312. 六方晶系又は三方晶系のうちから選ばれた少なくともいずれかの結晶構造を有 する材料を主成分とする焼結体が窒化ガリウム、 窒化インジウム、 窒化アルミニウムのうちか ら選ばれた少なくとも 1種以上を主成分とする薄膜を形成したものであることを特徴とする項 1309、 1310又は 1311に記載されたいずれかの発光素子。
項 1313. 六方晶系又は三方晶系のうちから選ばれた少なくともいずれかの結晶構造を有 する材料を主成分とする焼結体が窒化ガリゥム、 窒化インジウム、 窒化アルミニウムのうちか ら選ばれた少なくとも 1種以上を主成分とする単結晶薄膜を形成したものであることを特徴と する項 1309、 1310、 1311又は 1312に記載されたいずれかの発光素子。
項 1314. 六方晶系又 方晶系のうちから選ばれた少なくともいずれかの結晶構造を有 する材料を主成分とする焼結体が 化 »、 酸化ベリリウム、 謝匕アルミニウム、 炭化珪素、 窒化珪素、 窒化ガリウムのうちから選ばれた少なくともいずれかを主成分とする焼結体である ことを特徴とする項 1309、 1310、 1311、 1312又は 1313に記載されたいず れかの発光素子。
項 1315. 六方晶系又は三方晶系のうちから選ばれた少なくともいずれかの結晶構造を有 する材料を主成分とする焼結体力戰化亜鉛を主成分とする焼結体であることを特徴とする 13 14に記載された発光素子。
項 1316. 酸化亜鉛を主成分とする焼結体が)1 Mi性を有するものであることを とす る項 1315に記載された発光素子。
項 1317. 酸化亜鉛を主成分とする焼結体が表面粗さの大きいものであることを特徴とす る項 1315又は 1316に記載されたいずれかの発光素子。
項 1318. 酸化亜鉛を主成分とする焼結体が窒化ガリウム、 窒化インジウム、 窒化アルミ ニゥムのうちから選ばれた少なくとも 1種以上を主成分とする薄膜を形成したものであること を特徴とする項 1315、 1316又は 1317に記載されたいずれかの発光素子。
項 1319. 酸化亜鉛を主成分とする焼結体が窒化ガリウム、 窒化インジウム、 窒化アルミ ニゥムのうちから選ばれた少なくとも 1種以上を主成分とする単結晶薄膜を形成したものであ ることを特徴とする項 1315、 1316、 1317又は 1319に記載されたいずれかの発 光素子。
項 1320. 酸化亜鉛を主成分とする焼結体が導電性を有するものであることを特徴とする 項 1315、 1316、 1317、 1318又は 1319に記載されたいずれかの発光軒。 項 1321. 酸化亜鉛を主成分とする焼結体が室温において 1 X 102Ω · cm以下の抵抗率
であることを特徴とする項 1315、 1316、 1317、 1318、 1319又は 1320 に記載されたいずれかの発光素子。
項 1322. 酸化亜鉛を主成分とする焼結体が光 ¾ϋ性を有しかつ導電性を有するものであ ることを特徴とする項 1315、 1316、 1317、 1318、 1319、 1320又は1 321に記載されたいずれかの発光素子。
項 1323. 酸化亜鉛を主成分とする焼結体が ¾化亜鉛成分を Ζ η〇換算で 55. 0モル% 以上含有するものであることを體とする項 1315、 1316、 1317、 1318、 13 19、 1320、 1321又は 1322に記載されたいずれかの発光素子。
項 1324. 六方晶系又は三方晶系のうちから選ばれた少なくともいずれかの結晶構造を有 する材料を主成分とする焼結体が 化ベリリウムを主成分とする焼結体であることを,とす る項 1314に記載された発光素子。
項 1325. 酸化ベリリウムを主成分とする焼結体が光 ¾i 性を有するものであることを特 徴とする項 1324に記載された発光素子。
項 1326. 酸化ベリリウムを主成分とする焼結体が表面粗さの大きいものであることを特 徵とする項 1324又は 1325に記載されたいずれかの発光素子。
項 1327. 酸化ベリリウムを主成分とする焼結体が窒化ガリウム、 窒化インジウム、 窒化 アルミニウムのうちから選ばれた少なくとも 1種以上を主成分とする薄膜を形成したものであ ることを特徴とする項 1324、 1325又は 1326に記載されたいずれかの発光素子。 項 1328. 酸化ベリリウムを主成分とする焼結体が窒化ガリウム、 窒化インジウム、 窒化 アルミニウムのうちから選ばれた少なくとも 1種以上を主成分とする単結晶薄膜を形成したも のであることを特徴とする項 1324、 1325、 1326又は 1327に記載されたいずれ かの発光素子。
項 1329. 酸化ベリリウムを主成分とする焼結体力壞化ベリリウム成分を BeO^:で 6 5. 0モル%以上含有するものであることを特徴とする項 1324、 1325、 1326、 1 327、 1328又は 1329に記載されたいずれかの発光素子。
項 1330. 六方晶系又は三方晶系のうちから選ばれた少なくともいずれかの結晶構造を有 する材料を主成分とする焼結体が 化アルミ二ゥムを主成分とする焼結体であることを特徴と する項 1314に記載された発光素子。
項 1331. 酸化アルミニウムを主成分とする焼結体が光 ¾ 生を有するものであることを 特徴とする項 1318に記載された発光素子。
項 1332. 酸化アルミニウムを主成分とする焼結体が表面粗さの大きいものであることを 特徴とする項 1330又は 1331に記載されたいずれかの発光素子。
項 1333. 酸化アルミニウムを主成分とする焼結体が窒化ガリウム、 窒化インジウム、 窒 化アルミニウムのうちから選ばれた少なくとも 1種以上を主成分とする薄膜を形成したもので あることを特徴とする項 1330、 1331又は 1332に記載されたいずれかの発光^?。 項 1334. 酸化アルミニウムを主成分とする焼結体が窒化ガリウム、 窒化インジウム、 窒 化アルミニウムのうちから選ばれた少なくとも 1種以上を主成分とする単結晶薄膜を形成した ものであることを特徴とする項 1330、 1331、 1332又は 13 '33に記載されたいず れかの発光素子。
項 1335. 酸化アルミニウムを主成分とする焼結体力戰化アルミニウム成分を A 12〇3換 算で 55. 0モル%以上含有するものであることを特徴とする項 1330、 1331、 133 2、 1333又は 1334に記載されたいずれかの発光素子。
項 1336. 六方晶系又は三方晶系のうちから選ばれた少なくともいずれかの結晶構造を有 する材料を主成分とする焼結体が炭化珪素を主成分とする焼結体であることを とする項 1
314に記載された発光素子。
項 1337. 炭化珪素を主成分とする焼結体が ^性を有するものであることを tとす る項 1336に記載された発光素子。
項 1338. 炭化珪素を主成分とする焼結体が表面粗さの大きいものであることを特徴とす る項 1336又は 1337に記載されたいずれかの発光素子。
項 1339. 炭化珪素を主成分とする鰌吉体が窒化ガリウム、 窒化インジウム、 窒化アルミ ニゥムのうちから選ばれた少なくとも 1種以上を主成分とする薄膜を形成したものであること を特徴とする項 1336、 1337又は 1338に記載されたいずれかの発光素子。
項 1340. 炭化珪素を主成分とする焼結体が窒化ガリウム、 窒化インジウム、 窒化アルミ ニゥムのうちから選ばれた少なくとも 1種以上を主成分とする単結晶薄膜を形成したものであ ることを特徴とする項 1336、 1337、 1338又は 1339に記載されたいずれかの発 光素子。
項 1341. 六方晶系又は三方晶系のうちから選ばれた少なくともいずれかの結晶構造を有 する材料を主成分とする焼結体が窒化珪素を主成分とする焼結体であることを とする項 1 314に記載された発光素子。
項 1342. 窒化珪素を主成分とする! ^結体が ¾¾¾性を有するものであることを特徴とす る項 1341に記載された発光素子。
項 1343. 窒化珪素を主成分とする焼結体が表面粗さの大きいものであることを特徴とす る項 1341又は 1342に記載されたいずれかの発光素子。
項 1344. 窒化珪素を主成分とする焼結体が窒化ガリウム、 窒化インジウム、 窒化アルミ ニゥムのうちから選ばれた少なくとも 1種以上を主成分とする薄膜を形成したものであること を特徴とする項 1341、 1342又は 1343に記載されたいずれかの発光素子。
項 1345. 窒化珪素を主成分とする焼結体が窒化ガリウム、 窒化インジウム、 窒化アルミ ニゥムのうちから選ばれた少なくとも 1種以上を主成分とする単結晶薄膜を形成したものであ ることを とする項 1341、 1342、 1343又は 1344に記載されたいずれかの発 光素子。
項 1346. 六方晶系又は三方晶系のうちから選ばれた少なくともいずれかの結晶構造を有 する材料を主成分とする焼結体が窒化ガリウムを主成分とする焼結体であることを特徴とする 1314に記載された発光素子。
項 1347. 窒化ガリウムを主成分とする焼結体が光 ¾ 性を有するものであることを特徴 とする項 1346に記載された発光素子。
項 1348. 窒化ガリウムを主成分とする焼結体が表面粗さの大きいものであることを とする項 1346又は 1347に記載されたいずれかの発光素子。
項 1349. 窒化ガリウムを主成分とする焼結体が窒化ガリウム、 窒化インジウム、 窒化ァ ルミニゥムのうちから選ばれた少なくとも 1種以上を主成分とする薄膜を形成したものである ことを特徴とする項 1346、 1347又は 1348に記載されたいずれかの発光素子。 項 1350. 窒化ガリウムを主成分とする焼結体が窒化ガリウム、 窒化インジウム、 窒化ァ ルミニゥムのうちから選ばれた少なくとも 1種以上を主成分とする単結晶薄膜を形成したもの であることを特徴とする項 1346、 1347、 1348又は 1349に記載されたいずれか の発光素子。
項 1351. 窒化ガリウムを主成分とする焼結体が導電性を有するものであることを特徴と する項 1346、 1347、 1348、 1349又は 1350に記載されたいずれかの発光素 子。
項 1352. 窒化ガリウムを主成分とする焼結体が室温において 1 X 102Ω · cm以下の抵
抗率であることを特徴とする項 1346、 1347、 1348、 1349、 1350又は 13 51に記載されたいずれかの発光素子。
項 1353. 窒化ガリウムを主成分とする焼結体が光 ¾ 性を有しかつ導電性を有するもの であることを特徴とする項 1346、 1347、 1348、 1349、 1350、 1351又 は 1352に記載されたいずれかの発光素子。
項 1354. 窒化ガリウムを主成分とする焼結体が窒化ガリウム成分を GaN換算で 55. 0モル%以上含有するものであることを i [とする項 1346、 1347、 1348、 134 9、 1350、 1351、 1352又は 1353に記載されたいずれかの発光素子。
項 1355. セラミック材料を主成分とする焼結体力職化ジルコニウムを主成分とする能結 体であることを TOとする項 1292、 1293、 1294、 1295、 1296又は 129 7に記載されたいずれかの発光素子。
項 1356. 酸化ジルコニウムを主成分とする焼結体が光 ¾1性を有するものであることを 特徴とする項 1355に記載された発光素子。
項 1357. 酸化ジルコニウムを主成分とする焼結体が表面粗さの大きいものであることを 特徴とする項 1355又は 1356に記載されたいずれかの発光素子。
項 1358. 酸化ジルコニウムを主成分とする焼結体が窒化ガリウム、 窒化インジウム、 窒 化アルミニウムのうちから選ばれた少なくとも 1種以上を主成分とする薄膜を形成したもので あることを特徴とする項 1355、 1356又は 1357に記載されたいずれかの発光素子。 項 1359. 酸化ジルコニウムを主成分とする焼結体が窒化ガリウム、 窒化インジウム、 窒 化アルミニウムのうちから選ばれた少なくとも 1種以上を主成分とする単結晶薄膜を形成した ものであることを ^とする項 1355、 1356、 1357又は 1358に記載されたいず れかの発光素子。
項 1360. セラミック材料を主成分とする焼結体力雙化マグネシウムを主成分とする焼結 体であることを特徴とする項 1292、 1293、 1294、 1295、 1296又は 129 7に記載されたいずれかの発光素子。
項 1361. 酸化マグネシウムを主成分とする焼結体が光 ¾ 性を有するものであることを 特徴とする項 1360に記載された発光素子。
項 1362. 酸化マグネシウムを主成分とする焼結体が表面粗さの大きいものであることを 特徴とする項 1360又は 1361に記載されたいずれかの発光素子。
項 1363. 酸化マグネシウムを主成分とする焼結体が窒化ガリウム、 窒化インジウム、 窒 化アルミニウムのうちから選ばれた少なくとも 1種以上を主成分とする薄膜を形成したもので あることを特徴とする項 1360、 1361又は 1362に記載されたいずれかの発光素子。 項 1364. 酸化マグネシウムを主成分とする焼結体が窒化ガリウム、 窒化インジウム、 窒 化アルミニウムのうちから選ばれた少なくとも 1種以上を主成分とする単結晶薄膜を形成した ものであることを難とする項 1360、 1361、 1362又は 1363に記載されたいず れかの発光素子。
項 1365. セラミック材料を主成分とする焼結体がアルミン酸マグネシウムを主成分とす る焼結体であることを特徴とする項 1292、 1293、 1294、 1295、 1296又は 1297に記載されたいずれかの発光素子。
項 1366. アルミン酸マグネシウムを主成分とする焼結体が光透過性を有するものである ことを特徴とする項 1365に記載された発光素子。
項 1367. アルミン酸マグネシウムを主成分とする焼結体が表面粗さの大きいものである ことを特徴とする項 1365又は 1366に記載されたいずれかの発光素子。
項 1368. アルミン酸マグネシウムを主成分とする焼結体が窒化ガリゥム、 窒化ィンジゥ
ム、 窒化アルミニウムのうちから選ばれた少なくとも 1種以上を主成分とする薄膜を形成した ものであることを特徴とする項 1 3 6 5、 1 3 6 6又は 1 3 6 7に記載されたいずれかの発光 項 1 3 6 9. アルミン酸マグネシウムを主成分とする焼結体が窒化ガリウム、 窒化インジゥ ム、 窒化アルミニウムのうちから選ばれた少なくとも 1種以上を主成分とする単結晶薄膜を形 成したものであることを特徴と.する項 1 3 6 5、 1 3 6 6、 1 3 6 7又は 1 3 6 8に記載され たいずれかの発光素子。
項 1 3 7 0. セラミック材料を主成分とする焼結体が 化イットリウムを主成分とする炼結 体であることを特徴とする項 1 2 9 2、 1 2 9 3、 1 2 9 4、 1 2 9 5、 1 2 9 6又は 1 2 9 7に記載されたいずれかの発光素子。
項 1 3 7 1. 酸化イットリウムを主成分とする焼結体が光 ¾i性を有するものであることを 特徴とする項 1 3 7 0に記載された発光素子。
項 1 3 7 2. 酸化イットリウムを主成分とする焼結体が表面粗さの大きいものであることを 特徴とする項 1 3 7 0又は 1 3 7 1に記載されたいずれかの発光素子。
項 1 3 7 3. 酸化イットリウムを主成分とする焼結体が窒化ガリウム、 窒化インジウム、 窒 化アルミニウムのうちから選ばれた少なくとも 1種以上を主成分とする薄膜を形成したもので あることを特徴とする項 1 3 7 0、 1 3 7 1又は 1 3 7 2に記載されたいずれかの発光素子。 項 1 3 7 4. 酸化イットリウムを主成分とする焼結体が窒化ガリウム、 窒化インジウム、 窒 化アルミニウムのうちから選ばれた少なくとも 1種以上を主成分とする単結晶薄膜を形成した ものであることを特徴とする項 1 3 7 0、 1 3 7 1、 1 3 7 2又は 1 3 7 3に記載されたいず れかの発光素子。
項 1 3 7 5. 窒化ガリウム、 窒化インジウム、 窒化アルミニウムのうちから選ばれた少なく とも 1種以上を主成分とする薄膜からなる少なくとも N型半導体層及び発光層及び P型半導体 層を含む積層体により構成される発光素子であって、 該 N型半導体層及び発光層及び P型半導 体層の積層体が ¾¾ 生を有するセラミック材料を主成分とする焼結体に形成されていること を特徴とする発光素子。
項 1 3 7 6. 光透過性を有するセラミック材料を主成分とする焼結体が基板状であることを 特徴とする項 1 3 7 5に記載された発光素子。
項 1 3 7 7. 光透過性を有するセラミック材料を主成分とする焼結体が光透過率 1 %以上の ものであることを特徴とする項 1 3 7 5又は 1 3 7 6に記載されたいずれかの発光素子。 項 1 3 7 8. 光 ®¾性を有するセラミック材料を主成分とする焼結体が光透過率 1 0 %以上 のものであることを特徴とする項 1 3 7 7に記載された発光素子。
項 1 3 7 9. 光 性を有するセラミック材料を主成分とする焼結体が光透過率 2 0 %以上 のものであることを特徴とする項 1 3 7 7又は 1 3 7 8に記載されたいずれかの発光素子。 項 1 3 8 0. 光 ¾1性を有するセラミック材料を主成分とする焼結体が光透過率 3 0 %以上 のものであることを特徴とする項 1 3 7 7、 1 3 7 8又は 1 3 7 9記載されたいずれかの発光 奉ネ - 項 1 3 8 1 . 光 ¾i性を有するセラミック材料を主成分とする焼結体が光 ¾1率 4 0 %以上 のものであることを iff i [とする項 1 3 7 7、 1 3 7 8、 1 3 7 9又は 1 3 8 0に記載されたい ずれかの発光素子。
項 1 3 8 2. 光透過性を有するセラミック材料を主成分とする焼結体が光 率 5 0 %以上 のものであることを特徴とする項 1 3 7 7、 1 3 7 8、 1 3 7 9、 1 3 8 0又は 1 3 8 1に記 載されたいずれかの発光素子。
項 1 3 8 3. 光 性を有するセラミック材料を主成分とする焼結体が光 ¾ 率 6 0 %以上
のものであることを特徴とする項 1377、 1378、 1379、 1380、 1381又は 1 382に記載されたいずれかの発光素子。
項 1384. ¾¾ϋ性を有するセラミック材料を主成分とする焼結体力 ^^Mii率 80%以上 のものであることを特徴とする項 1377、 1378、 1379、 1380、 1381、 13 82又は 1383に記載されたいずれかの発光素子。
項 1385. ¾¾ 性を有するセラ
1%未満の ものであることを鍾とする項 1375、 1376、 項 1377、 1378、 1379、 13 80、 1381、 1382、 1383又は 1384に記載されたいずれかの発光素子。
項 1386. 性あるいは 率が少なくとも波長 200 nm〜800 nmの範囲の 光に対してのものであることを體とする項 1375、 1376、 項 1377、 1378、 1
379、 1380、 1381、 1382、 1383、 1384又は 1385に記載されたいず れかの発光素子。
項 1387. 窒化ガリウム、 窒化インジウム、 窒化アルミニウムのうちから選ばれた少なく とも 1種以上を主成分とする薄膜からなる少なくとも N型半導体層及び発光層及び P型半導体 層を含む積層体により構成される発光素子であって、 該 N型半導体層及び発光層及び P型半導 体層の積層体が表面粗さの大きい 1 έ¾Ι性を有するセラミック材料を主成分とする焼結体に形 成されていることを特徴とする項 1375、 1376、 項 1377、 1378、 1379、 1
380、 1381、 1382、 1383、 1384、 1385又は 1386に記載されたいず れかの発光素子。
項 1388. 性を有するセラミック材料を主成分とする焼結体の平均表面粗さが R a
200 Onm以下であることを體とする項 1375、 1376、 項 1377、 1378、 1
379、 1380、 1381、 1382、 1383、 1384、 1385、 1386又は 13 87に記載されたいずれかの発光素子。
項 1389. 過性を有するセラミック材料を主成分とする焼結体の平均表面粗さが R a 1000 nm以下であることを特徴とする項 1388に記載された発光素子。
項 1390. 光透過性を有するセラミック材料を主成分とする焼結体の平均表面粗さが R a 100 nm以下であることを特徴とする項 1388又は 1389に記載されたいずれかの発光 素子。
項 1391. 性を有するセラミック材料を主成分とする焼結体の平均表面粗さが R a 20 nm以下であることを特徴とする項 1388、 1389又は 1390に記載されたいずれ かの発光素子。
項 1392. 光透過性を有するセラミック材料を主成分とする焼結体の平均表面粗さが R a 1 Onm以下であることを籠とする項 1388、 1389、 1390又は 1391に記載さ れたいずれかの発光素子。
項 1393. 性を有するセラミック材料を主成分とする焼結体の平均表面粗さが R a
5 nm以下であることを特徴とする項 1388、 1389、 1390、 1391又は 1392 に記載されたいずれかの発光素子。
項 1394. ¾¾i性を有するセラミック材料を主成分とする焼結体が表面粗さの大きいも のであることを赚とする項 1375、 1376、 1377、 1378、 1379、 1380、 1381、 1382、 1383、 1384、 1385、 1386、 1387、 1388、 13 89又は 1390に記載されたいずれかの発光素子。
項 1395. 光 ¾1性を有するセラミック材料を主成分とする焼結体の平均表面粗さが R a 7 Onm以上であることを 敷とする項 1375、 1376、 1377、 1378、 1379、 1380、 1381、 1382、 1383、 1384、 1385、 1386、 1387、 13
88、 1389、 1390又は 1394に記載されたいずれかの発光素子。
項 1396. 光透過性を有するセラミック材料を主成分とする焼結体の平均表面粗さが R a
1000 nmより大きいことを特徴とする項 1395に記載された発光素子。
項 1397. ¾¾1性を有するセラミック材料を主成分とする焼結体の平均表面粗さが R a
2000 nmより大きいことを特徴とする項 1395又は 1396に記載されたいずれかの発 光素子。
項 1398. ½¾i性を有するセラミック材料を主成分とする焼結体の表面が焼き放し (a s— f i r e)、 ラップ研磨、 ブラス卜研磨、 鏡面研磨、 化学腐食及びプラズマガスによる腐食 のうちから選ばれた少なくともいずれかの状態であることを特徴とする項 1375、 1376、 1377、 1378、 1379、 1380、 1381、 1382、 1383、 1384, 13 85、 1386、 1387、 1388、 1389、 1390、 1391、 1392、 1393、 1394、 1395、 1396又は 1397に記載されたいずれかの発光素子。
項 1399. 光透過性を有するセラミック材料を主成分とする焼結体の表面が鏡面研磨され た状態であることを特徴とする項 1398に記載された発光素子。
項 1400. 窒化ガリウム、 窒化インジウム、 窒化アルミニウムのうちから選ばれた少なく とも 1種以上を主成分とする薄膜からなる少なくとも N型半 (本層及び発光層及び P型半導体 層を含む積層体により構成される発光素子であって、 該 N型半導体層及び発光層及び P型半導 体層の積層体が窒化ガリウム、 窒化インジウム、 窒化アルミニウムのうちから選ばれた少なく とも 1種以上を主成分とする薄膜が形成された ¾¾i性を有するセラミック材料を主成分とす る焼結体に形成されていることを特徴とする項 1375、 1376、 1377、 1378、 1
379、 1380、 1381、 1382、 1383、 1384、 1385、 1386、 138 7、 1388、 1389、 1390、 1391、 1392、 1393、 1394、 1395、 1396、 1397、 1398又は 1399に記載されたいずれかの発光素子。
項 1401. ½¾i性を有するセラミック材料を主成分とする焼結体に形成された窒化ガリ ゥム、 窒化インジウム、 窒化アルミニウムのうちから選ばれた少なくとも 1種以上を主成分と する薄膜が無定形、 多結晶、 配向性多結晶、 単結晶のうちから選ばれる少なくともいずれかの 結晶状態を有することを特徴とする項 1400に記載された発光素子。
項 1402. 光 性を有するセラミック材料を主成分とする焼結体に形成された窒化ガリ ゥム、 窒化インジウム、 窒化アルミニウムのうちから選ばれた少なくとも 1種以上を主成分と する薄膜の少なくとも一部が単結晶であることを特徴とする項 1400又は 1401に記載さ れたいずれかの発光素子。
項 1403. 光 ¾i性を有するセラミック材料を主成分とする焼結体に形成された窒化ガリ ゥム、 窒化インジウム、 窒化アルミニウムのうちから選ばれた少なくとも 1種以上を主成分と する薄膜が 1層からなることを特徴とする項 1400、 1401又は 1402に記載されたい ずれかの発光素子。
項 1404. 性を有するセラミック材料を主成分とする焼結体に形成された窒化ガリ ゥム、 窒化インジウム、 窒化アルミニウムのうちから選ばれた少なくとも 1種以上を主成分と する薄膜が無定形であることを特徴とする項 1403に記載された発光素子。
項 1405. 光 ¾1性を有するセラミック材料を主成分とする焼結体に形成された窒化ガリ ゥム、 窒化インジウム、 窒化アルミニウムのうちから選ばれた少なくとも 1種以上を主成分と する薄膜が多結晶であることを特徴とする項 1403に記載された発光素子。
項 1406. 性を有するセラミック材料を主成分とする焼結体に形成された窒化ガリ ゥム、 窒化インジウム、 窒化アルミニウムのうちから選ばれた少なくとも 1種以上を主成分と する薄膜が 向性多結晶であることを特徴とする項 1403に記載された発光素子。
項 1407. ½¾i性を有するセラミック材料を主成分とする焼結体に形成された窒化ガリ ゥム、 窒化インジウム、 窒化アルミニウムのうちから選ばれた少なくとも 1種以上を主成分と する薄膜が単結晶であることを特徴とする項 1403に記載された発光素子。
項 1408. :)·6¾ί1性を有するセラミック材料を主成分とする焼結体に形成された窒化ガリ ゥム、 窒化インジウム、 窒化アルミニウムのうちから選ばれた少なくとも 1種以上を主成分と する薄膜が少なくとも 2以上の層からなることを特徴とする項 1400、 1401又は 140 2に記載されたいずれかの発光素子。
項 1409. 性を有するセラミック材料を主成分とする焼結体に形成された窒化ガリ ゥム、 窒化インジウム、 窒化アルミニウムのうちから選ばれた少なくとも 1種以上を主成分と する薄膜が少なくとも 2以上の層からなり、 各層がそれぞれ無定形、 多結晶、 配向性多結晶、 単結晶のうちから選ばれる少なくともいずれかの結晶状態を有することを特徴とする項 140 8に記載された発光素子。
項 1410. ¾¾ 性を有するセラミック材料を主成分とする焼結体に形成された窒化ガリ ゥム、 窒化インジウム、 窒化アルミニウムのうちから選ばれた少なくとも 1種以上を主成分と する薄膜が少なくとも 2以上の層からなり、 性を有するセラミック材料を主成分とす る焼結体に直接形成された薄翻が無定形、 多結晶、 配向性多結晶、 単結晶のうちから選ばれ る少なくともいずれかの結晶状態を有することを特徴とする項 1408又は 1409記載され たいずれかの発光素子。
項 1411. ¾¾i性を有するセラミック材料を主成分とする焼結体に形成された窒化ガリ ゥム、 窒化インジウム、 窒化アルミニウムのうちから選ばれた少なくとも 1種以上を主成分と する薄膜が少なくとも 2以上の層からなり、 該½¾1性を有するセラミック材料を主成分とす る焼結体に直接形成された薄藤が無定形、 多結晶、 配向性多結晶のうちから選ばれる少なく ともいずれかの結晶状態を有することを特徴とする項 1408、 1409又は 1410に記載 されたいずれかの発光素子。
項 1412. ¾¾1性を有するセラミック材料を主成分とする焼結体に形成された窒化ガリ ゥム、 窒化インジウム、 窒化アルミニウムのうちから選ばれた少なくとも 1種以上を主成分と する薄膜が少なくとも 2以上の層からなり、 該光 ¾i 性を有するセラミック材料を主成分とす る焼結体に直接形成された薄 が 向性多結晶であることを特徴とする項 1408、 140 9、 1410又は 1411に記載されたいずれかの発光素子。
項 1413. ¾¾ 性を有するセラミック材料を主成分とする焼結体に形成された窒化ガリ ゥム、 窒化インジウム、 窒化アルミニウムのうちから選ばれた少なくとも 1種以上を主成分と する薄膜が少なくとも 2以上の層からなり、 少なくとも 1層が単結晶であることを特徴とする 項 1408、 1409、 1410、 1411又は 1412に記載されたいずれかの発光素子。 項 1414. 性を有するセラミック材料を主成分とする焼結体に形成された窒化ガリ ゥム、 窒化インジウム、 窒化アルミニウムのうちから選ばれた少なくとも 1種以上を主成分と する薄膜が少なくとも 2以上の層からなり、 最上層の薄膜が単結晶であることを特徴とする項 1408、 1409、 1410、 1411、 1412又は 1413に記載されたいずれかの発 光素子。
項 1415. ¾¾1性を有するセラミック材料を主成分とする焼結体に形成された窒化ガリ ゥム、 窒化インジウム、 窒化アルミニウムのうちから選ばれた少なくとも 1種以上を主成分と する薄膜が少なくとも単結晶薄 を有し該単結晶薄 ΙΙβの厚みが 300 m^満であること を とする項 1400、 1401、 1402、 1403、 1404、 1405、 1406、 1407、 1408、 1409、 1410、 1411、 1412、 1413又は 1414に記 載されたいずれかの発光素子。
項 1416. 性を有するセラミック材料を主成分とする焼結体に形成された窒化ガリ ゥム、 窒化インジウム、 窒化アルミニウムのうちから選ばれた少なくとも 1種以上を主成分と する薄膜が少なくとも単結晶薄 Elを有し該単結晶薄 MSの厚みが 200 m以下であること を特徴とする項 1415に記載された発光素子。
項 1417. 光 性を有するセラミック材料を主成分とする焼結体に形成された薄膜が少 なくとも 0. 1 nm以上の厚みを有することを とする項 1400、 1401、 1402、 1403、 1404、 1405、 1406、 1407、 1408、 1409、 1410、 14 11、 1412、 1413、 1414、 1415又は 1416に記載されたいずれかの発光素 子。
項 1418. ¾¾ϋ性を有するセラミック材料を主成分とする焼結体に形成された薄膜が少 なくとも 0. 5 nm以上の厚みを有することを特徴とする項 1417に記載された発光素子。 項 1419. ¾¾ϋ性を有するセラミック材料を主成分とする焼結体に形成された薄膜が少 なくとも 0. 3 m以上の厚みを有することを特徴とする項 1417又は 1418に記載され たいずれかの発光素子。
項 1420. 性を有するセラミック材料を主成分とする焼結体に形成された薄膜が少 なくとも 3. 5 m以上の厚みを有することを特徴とする項 1417、 1418又は 1419 に記載されたいずれかの発光素子。
項 1421. ¾¾¾性を有するセラミック材料を主成分とする焼結体に形成された薄膜が少 なくとも 10 m以上の厚みを有することを特徴とする項 1417、 1418、 1419又は 1420に記載されたいずれかの発光素子。
項 1422. 光 性を有するセラミック材料を主成分とする焼結体に形成された薄膜が少 なくとも 50 m以上の厚みを有することを特徴とする項 1417、 1418、 1419、 1 420又は 1421に記載されたいずれかの発光素子。
項 1423. 光 ¾1性を有するセラミック材料を主成分とする焼結体に形成された薄膜が少 なくとも窒化ガリウムを含有するものであることを特徴とする項 1400、 1401、 140 2、 1403、 1404、 1405、 1406、 1407、 1408、 1409、 1410、 1411、 1412、 1413、 1414、 1415、 1416、 1417、 1418、 14 19、 1420、 1421又は 1422に記載されたいずれかの発光素子。
項 1424. 性を有するセラミック材料を主成分とする焼結体に形成された薄膜が少 なくとも窒化ガリウムを含むかあるいは窒化ガリウムを主成分とする薄膜を有することを特徴 とする項 1400、 1401、 1402、 1403、 1404、 1405、 1406、 140 7、 1408、 1409、 1410、 1411、 1412、 1413、 1414、 1415、 1416、 1417、 1418、 1419、 1420、 1421、 1422又は 1423に記 載されたいずれかの発光素子。
項 1425. 光«性を有するセラミック材料を主成分とする焼結体に形成された薄膜が窒 化ガリウムを主成分とするものであることを特徴とする項 1423又は 1424に記載された いずれかの発光素子。
項 1426. 性を有するセラミック材料を主成分とする焼結体に形成された薄膜が A lxGay I n — yN (0く y≤l) で表わされる組成を有することを とする項 1423、 1424又は 1425に記載されたいずれかの発光素子。
項 1427. βί 性を有するセラミック材料を主成分とする焼結体に形成された薄膜が窒 化ガリウムを 50モル%以上含むを特徴とする項 1423、 1424、 1425又は 1426 に記載されたいずれかの発光素子。
項 1428. 光 M '生を有するセラミック材料を主成分とする焼結体に形成された少なくと
も窒化ガリウムを含むかあるいは窆化ガリウムを主成分とする薄膜が無定形、 多結晶、 配向性 多結晶、 単結晶のうちから選ばれた少なくともいずれかの結晶状態であることを特徴とする項 1423、 1424、 1425、 1426又は 1427に記載されたいずれかの発光素子。 項 1429. 光 ¾1性を有するセラミック材料を主成分とする焼結体に形成された少なくと も窒化ガリゥムを含むかあるいは窆化ガリゥムを主成分とする薄膜が単結晶であることを特徴 とする項 1428に記載された発光素子。
項 1430. 光 性を有するセラミック材料を主成分とする焼結体に形成された最上層の 薄膜が少なくとも窒化ガリウムを含むかあるいは窒化ガリウムを主成分とするものであること を [とする項 1423、 1424、 1425、 1426、 1427、 1428又は 1429 に記載されたいずれかの発光素子。
項 1431. 光 ¾i 性を有するセラミック材料を主成分とする焼結体に形成された最上層の 薄膜が少なくとも窒化ガリゥムを含むかあるいは窒化ガリゥムを主成分とする単結晶であるこ とを特徴とする項 1430に記載された発光素子。
項 1432. 光 ¾ 性を有するセラミック材料を主成分とする焼結体に形成された薄膜が単 結晶、 無定形、 多結晶、 配向性多結晶のうちから選ばれた少なくともいずれか 2以上の結晶状 態が同時に混在しているものからなることを有することを特徴とする項 1400、 1401、 1402、 1403、 1404、 1405、 1406、 1407、 1408、 1409、 14 10、 1411、 1412、 1413、 1414、 1415、 1416、 1417、 1418、 1419、 1420、 1421、 1422、 1423、 1424、 1425、 1426、 14 27、 1428、 1429、 1430又は 1431に記載されたいずれかの発光素子。
項 1433. 光 性を有するセラミック材料を主成分とする焼結体に形成された薄膜が単 一層あるいは少なくとも 2以上の層からなり、 該薄膜の少なくとも 1以上の層が単結晶、 無定 形、 多結晶、 配向性多結晶のうちから選ばれた少なくともいずれか 2以上の結晶状態が同時に 混在しているものからなることを特徴とする項 1400、 1401、 1402、 1403、 1 404、 1405、 1406、 1407、 1408、 1409、 1410、 1411、 141 2、 1413、 1414、 1415、 1416、 1417、 1418、 1419、 1420、 1421、 1422、 1423、 1424、 1425、 1426、 1427、 1428、 14 29、 1430、 1431又は 1432に記載されたいずれかの発光素子。
項 1434. 光 ¾ 性を有するセラミック材料を主成分とする焼結体に形成された単結晶薄 膜のミラ一指数 (002) の格子面の X線回折ロッキングカーブの半値幅が 3600秒以下で あることを特徴とする項 1400、 1401、 1402、 1403、 1404、 1405、 1 406、 1407、 1408、 1409、 1410、 1411、 1412、 1413、 141 4、 1415、 1416、 1417、 1418、 1419、 1420、 1421、 1422、 1423、 1424、 1425、 1426、 1427、 1428、 1429、 1430、 14 31、 1432又は 1433に記載されたいずれかの発光素子。
項 1435. 光¾1性を有するセラミック材料を主成分とする焼結体に形成された単結晶薄 膜のミラ一指数 (002) の格子面の X線回折ロッキングカーブの半値幅が 300秒以下であ ることを特徴とする項 1434に記載された発光素子。
項 1436. 性を有するセラミック材料を主成分とする焼結体に形成された単結晶薄 膜のミラ一指数 (002) の格子面の X線回折ロッキングカーブの半値幅が 240秒以下であ ることを特徴とする項 1434又は 1435に記載されたいずれかの発光素子。
項 1437. 光透過性を有するセラミック材料を主成分とする焼結体に形成された単結晶薄 膜のミラ一指数 (002) の格子面の X線回折ロッキングカーブの半値幅が 200秒以下であ ることを特徴とする項 1434、 1435又は 1436に記載されたいずれかの発光素子。
項 1438. ¾¾ 性を有するセラミック材料を主成分とする焼結体に形成された単結晶薄 膜のミラ—指数 (002) の格子面の X線回折ロッキングカーブの半値幅が 150秒以下であ ることを特徴とする項 1434、 1435、 14367又は 1437に記載されたいずれかの 発光素子。
項 1439. ¾¾ 性を有するセラミック材料を主成分とする焼結体に形成された単結晶薄 膜のミラー指数 (002) の格子面の X線回折ロッキングカーブの半値幅が 130秒以下であ ることを特徴とする項 1434、 1435、 1436、 1437又は 1438に記載されたい ずれかの発光素子。
項 1440. ¾¾ 性を有するセラミック材料を主成分とする焼結体に形成された単結晶薄 膜のミラー指数 (002) の格子面の X線回折ロッキングカーブの半値幅が 100秒以下であ ることを特徴とする項 1434、 1435、 1436、 1437、 1438又は 1439に記 載されたいずれかの発光素子。
項 1441. ¾¾ 性を有するセラミック材料を主成分とする焼結体が窒化アルミニウムを 主成分とする焼結体であることを特徴とする項 1375、 1376、 1377、 1378、 1 379、 1380、 1381、 1382、 1383、 1384、 1385、 1386、 138 7、 1388、 1389、 1390、 1391、 1392、 1393、 1394、 1395、 1396、 1397、 1398、 1399、 1400、 1401、 1402、 1403、 14 04、 1405、 1406、 1407、 1408、 1409、 1410、 1411、 1412、 1413、 1414、 1415、 1416、 1417、 1418、 1419、 1420、 14 21、 1422、 1423、 1424、 1425、 1426、 1427、 1428、 1429、 1430、 1431、 1432、 1433、 1434、 1435、 1436、 1437、 14 38、 1439又は 1440に記載されたいずれかの発光素子。
項 1442. 光 ¾i性を有するセラミック材料を主成分とする焼結体が六方晶系又は三方晶 系のうちから選ばれた少なくともいずれかの結晶構造を有するセラミック材料を主成分とする 焼結体であることを特徴とする項 1375、 1376、 1377、 1378、 1379、 13 80、 1381、 1382、 1383、 1384、 1385、 1386、 1387、 1388、 1389、 1390、 1391、 1392、 1393、 1394、 1395、 1396、 13 97、 1398、 1399、 1400、 1401、 1402、 1403、 1404、 1405、 1406、 1407、 1408、 1409、 1410、 1411、 1412、 1413、 14 14、 1415、 1416、 1417、 1418、 1419、 1420、 1421、 1422、 1423、 1424、 1425、 1426、 1427、 1428、 1429、 1430、 14 31、 1432、 1433、 1434、 1435、 1436、 1437、 1438、 1439 又は 1440に記載されたいずれかの発光素子。
項 1443. 光 ¾ 性を有する六方晶系又は三方晶系のうちから選ばれた少なくともいずれ かの結晶構造を有するセラミック材料を主成分とする焼結体力戰化亜鉛、 酸化ベリリウム、 酸 化アルミニウム、 炭化珪素、 窒化珪素、 窒化ガリウムのうちから選ばれた少なくとも 1種以上 を主成分とする焼結体であることを特徴とする項 1442に記載された発光素子。
項 1444. ½¾i性を有するセラミック材料を主成分とする焼結体力職化ジルコニウム、 酸化マグネシウム、 アルミン酸マグネシウム、 酸化チタン、 チタン酸バリウム、 チタン酸ジル コン ra、希土 IS¾素酸化物、酸ィ匕トリウム、各種フェライト、 ムライト、 フオルステライト、 ステアタイト、 結晶化ガラスのうちから選ばれた少なくとも 1種以上を主成分とする焼結体で あることを特徴とする項 1375、 1376、 1377、 1378、 1379、 1380、 1 381、 1382、 1383、 1384、 1385、 1386、 1387、 1388、 138 9、 1390、 1391、 1392、 1393、 1394, 1395、 1396、 1397、
1398、 1399、 1400、 1401、 1402、 1403、 1404、 1405、 14 06、 1407、 1408、 1409、 1410、 1411、 1412、 1413、 1414、 1415、 1416、 1417、 1418、 1419、 1420、 1421、 1422、 14 23、 1424、 1425、 1426、 1427、 1428、 1429、 1430、 1431、 1432、 1433、 1434、 1435、 1436、 1437、 1438、 1439又は 1 440に記載されたいずれかの発光素子。
項 1445. 性を有するセラミック材料を主成分とする焼結体が窒化アルミニウム、 酸化:«、 酸化ベリリウム、 酸化アルミニウム、 炭化珪素、 窒化珪素、 窒化ガリウム、 酸化ジ ルコニゥム、 酸化マグネシウム、 アルミン酸マグネシウム、 酸化イットリウムのうちから選ば れた少なくとも 1種以上を主成分とする焼結体であることを特徴とする項 1441、 1442、 1443又は 1444に記載されたいずれかの発光素子。
項 1446. 窒化ガリウム、 窒化インジウム、 窒化アルミニウムのうちから選ばれた少なく とも 1種以上を主成分とする薄膜からなる少なくとも N型半導体層及び発光層及び P型半導体 層を含む積層体により構成される発光素子であって、 該 N型半導体層及び発光層及び P型半導 体層の積層体が表面粗さの大きいセラミック材料を主成分とする焼結体に形成されていること を特徴とする発光素子。
項 1447. 表面粗さの大きいセラミック材料を主成分とする焼結体が基板状であることを 特徴とする項 1446に記載された発光素子。
項 1448. セラミツク材料を主成分とする焼結体の平均表面粗さが R a 2000 nm以下 であることを特徴とする項 1446又は 1447に記載されたいずれかの発光素子。
項 1449. セラミック材料を主成分とする焼結体の平均表面粗さが R a 1000 nm以下 であることを特徴とする項 1448に記載された発光素子。
項 1450. セラミック材料を主成分とする焼結体の平均表面粗さが R a 100 nm以下で あることを特徴とする項 1448又は 1449に記載されたいずれかの発光素子。
項 1451. セラミック材料を主成分とする焼結体の平均表面粗さが R a 70 nm以上であ ることを特徴とする項 1446、 1447、 1448、 1449又は 1450に記載されたい ずれかの発光素子。
項 1452. セラミック材料を主成分とする焼結体の平均表面粗さが R a 1000 nmより 大きいことを特徴とする項 1451に記載された発光素子。
項 1453. セラミック材料を主成分とする焼結体の平均表面粗さが R a 2000 nmより 大きいことを特徴とする項 1451又は 1452に記載されたいずれかの発光素子。
項 1454. セラミック材料を主成分とする!^結体の表面が焼き放し (a s— f i r e)、 ラ ッフ Iff磨、 ブラスト研磨、 鏡面研磨、 ィ匕学腐食及びプラズマガスによる腐食のうちから選ばれ た少なくともいずれかの状態であることを^ [とする項 1446、 1447、 1448、 14 49、 1450、 1451、 1452又は 1453に記載されたいずれかの発光素子。
項 1455. 表面粗さの大きいセラミック材料を主成分とする焼結体が 過率 0%である ことを特徴とする項 1446、 1447、 1448、 1449、 1450、 1451、 145 2、 1453又は 1454に記載されたいずれかの発光素子。
項 1456. 窒化ガリウム、 窒化インジウム、 窒化アルミニウムのうちから選ばれた少なく とも 1種以上を主成分とする薄膜からなる少なくとも N型半導体層及び発光層及び P型半導体 層を含む積層体により構成される発光素子であって、 該 N型半導体層及び発光層及び P型半導 体層の積層体が窒化ガリゥム、 窒化ィンジゥム、 窒化アルミ二ゥムのうちから選ばれた少なく とも 1種以上を主成分とする薄膜が形成された表面粗さの大きいセラミック材料を主成分とす る焼結体に形成されていることを特徴とする項 1446、 1447、 1448、 1449、 1
4 5 0、 1 4 5 1、 1 4 5 2、 1 4 5 3、 1 4 5 4又は 1 4 5 5に記載されたいずれかの発光 素子。
項 1 4 5 7. 表面粗さの大きいセラミック材料を主成分とする焼結体に形成された窒化ガリ ゥム、 窒化インジウム、 窒化アルミニウムのうちから選ばれた少なくとも 1種以上を主成分と する薄膜が無定形、 多結晶、 配向性多結晶、 単結晶のうちから選ばれる少なくともいずれかの 結晶状態を有することを特徴とする項 1 4 5 6に記載された発光素子。
項 1 4 5 8. 表面粗さの大きいセラミック材料を主成分とする焼結体に形成された窒化ガリ ゥム、 窒化インジウム、 窒化アルミニウムのうちから選ばれた少なくとも 1種以上を主成分と する薄膜の少なくとも一部が単結晶であることを特徴とする項 1 4 5 6又は 1 4 5 7に記載さ れたいずれかの発光素子。
項 1 4 5 9. 表面粗さの大きいセラミック材料を主成分とする焼結体に形成された窒化ガリ ゥム、 窒化インジウム、 窒化アルミニウムのうちから選ばれた少なくとも 1種以上を主成分と する薄膜が 1層からなることを とする項 1 4 5 6、 1 4 5 7又は 1 4 5 8に記載されたい ずれかの発光素子。
項 1 4 6 0. 表面粗さの大きいセラミック材料を主成分とする焼結体に形成された窒化ガリ ゥム、 窒化インジウム、 窒化アルミニウムのうちから選ばれた少なくとも 1種以上を主成分と する薄膜が無定形であることを特徴とする項 1 4 5 9に記載された発光素子。
項 1 4 6 1 . 表面粗さの大きいセラミック材料を主成分とする焼結体に形成された窒化ガリ ゥム、 窒化インジウム、 窒化アルミニウムのうちから選ばれた少なくとも 1種以上を主成分と する薄膜が多結晶であることを特徴とする項 1 4 5 9に記載された発光素子。
項 1 4 6 2. 表面粗さの大きいセラミック材料を主成分とする焼結体に形成された窒化ガリ ゥム、 窒化インジウム、 窒化アルミニウムのうちから選ばれた少なくとも 1種以上を主成分と する薄膜が ¾己向性多結晶であることを特徴とする項 1 4 5 9に記載された発光素子。
項 1 4 6 3. 表面粗さの大きいセラミック材料を主成分とする焼結体に形成された窒化ガリ ゥム、 窒化インジウム、 窒化アルミニウムのうちから選ばれた少なくとも 1種以上を主成分と する薄膜が単結晶であることを特徴とする項 1 4 5 9に記載された発光素子。
項 1 4 6 4. 表面粗さの大きいセラミック材料を主成分とする焼結体に形成された窒化ガリ ゥム、 窒化インジウム、 窒化アルミニウムのうちから選ばれた少なくとも 1種以上を主成分と する薄膜が少なくとも 2以上の層からなることを特徴とする項 1 4 5 6、 1 4 5 7又は 1 4 5 8記載されたいずれかの発光素子。
項 1 4 6 5. 表面粗さの大きいセラミック材料を主成分とする焼結体に形成された窒化ガリ ゥム、 窒化インジウム、 窒化アルミニウムのうちから選ばれた少なくとも 1種以上を主成分と する薄膜が少なくとも 2以上の層からなり、 各層がそれぞれ無定形、 多結晶、 配向性多結晶、 単結晶のうちから選ばれる少なくともいずれかの結晶状態を有することを特徴とする項 1 4 6 4に記載された発光素子。
項 1 4 6 6. 表面粗さの大きいセラミック材料を主成分とする焼結体に形成された窒化ガリ ゥム、 窒化インジウム、 窒化アルミニウムのうちから選ばれた少なくとも 1種以上を主成分と する薄膜が少なくとも 2以上の層からなり、 該表面粗さの大きいセラミック材料を主成分とす る焼結体に直接形成された薄膜層が無定形、 多結晶、 配向性多結晶、 単結晶のうちから選ばれ る少なくともいずれかの結晶状態を有することを特徴とする項 1 4 6 4又は 1 4 6 5記載され たいずれかの発光素子。
項 1 4 6 7. 表面粗さの大きいセラミック材料を主成分とする焼結体に形成された窒化ガリ ゥム、 窒化インジウム、 窒化アルミニウムのうちから選ばれた少なくとも 1種以上を主成分と する薄膜が少なくとも 2以上の層からなり、 該表面粗さの大きいセラミック材料を主成分とす
る焼結体に直接形成された薄膜層が無定形、 多結晶、 配向性多結晶のうちから選ばれる少なく ともいずれかの結晶状態を有することを纖とする項 1464、 1465又は 1466に記載 されたいずれかの発光素子。
項 1468. 表面粗さの大きいセラミック材料を主成分とする焼結体に形成された窒化ガリ ゥム、 窒化インジウム、 窒化アルミニウムのうちから選ばれた少なくとも 1種以上を主成分と する薄膜が少なくとも 2以上の層からなり、 該表面粗さの大きいセラミック材料を主成分とす る焼結体に直接形成された薄膜層が己向性多結晶であることを とする項 1464、 146 5、 1466又は 1467に記載されたいずれかの発光素子。
項 1469. 表面粗さの大きいセラミック材料を主成分とする焼結体に形成された窒化ガリ ゥム、 窒化インジウム、 窒化アルミニウムのうちから選ばれた少なくとも 1種以上を主成分と する薄膜が少なくとも 2以上の層からなり、 少なくとも 1層が単結晶であることを とする 項 1464、 1465、 1466、 1467又は 1468に記載されたいずれかの発光素子。 項 1470. 表面粗さの大きいセラミック材料を主成分とする焼結体に形成された窒化ガリ ゥム、 窒化インジウム、 窒化アルミニウムのうちから選ばれた少なくとも 1種以上を主成分と する薄膜が少なくとも 2以上の層からなり、 最上層の薄膜が単結晶であることを特徴とする項 1464、 1465、 1466、 1467、 1468又は 1469に記載されたいずれかの発 光素子。
項 1471. 表面粗さの大きいセラミック材料を主成分とする焼結体に形成された窒化ガリ ゥム、 窒化インジウム、 窒化アルミニウムのうちから選ばれた少なくとも 1種以上を主成分と する薄膜が少なくとも単結晶薄 を有し該単結晶薄 の厚みが 300 m*満であること を特徴とする項 1456、 1457、 1458、 1459、 1460、 1461、 1462、 1463、 1464、 1465、 1466、 1467、 1468、 1469又は 1470に記 載されたいずれかの発光素子。
項 1472. 表面粗さの大きいセラミック材料を主成分とする焼結体に形成された窒化ガリ ゥム、 窒化インジウム、 窒化アルミニウムのうちから選ばれた少なくとも 1種以上を主成分と する薄膜が少なくとも単結晶薄膜層を有し該単結晶薄膜層の厚みが 200 xm以下であること を特徴とする項 1471に記載された発光素子。
項 1473. 表面粗さの大きいセラミック材料を主成分とする焼結体に形成された薄膜が少 なくとも 0. 1 nm以上の厚みを有することを特徴とする項 1456、 1457、 1458、 1459、 1460、 1461、 1462、 1463、 1464、 1465、 1466、 14 67、 1468、 1469、 1470、 1471又は 1472に記載されたいずれかの発光素 子。
項 1474. 表面粗さの大きいセラミック材料を主成分とする焼結体に形成された薄膜が少 なくとも 0. 5 n m以上の厚みを有することを特徴とする項 1473に記載された発光素子。 項 1475. 表面粗さの大きいセラミック材料を主成分とする焼結体に形成された薄膜が少 なくとも 0. 3 m以上の厚みを有することを とする項 1473又は 1474に記載され たいずれかの発光素子。
項 1476. 表面粗さの大きいセラミック材料を主成分とする焼結体に形成された薄膜が少 なくとも 3. 5 m以上の厚みを有することを特徴とする項 1473、 1474又は 1475 に記載されたいずれかの発光素子。
項 1477. 表面粗さの大きいセラミック材料を主成分とする焼結体に形成された薄膜が少 なくとも 10 m以上の厚みを有することを特徴とする項 1473、 1474、 1475又は 1476に記載されたいずれかの発光素子。
項 1478. 表面粗さの大きいセラミック材料を主成分とする焼結体に形成された薄膜が少
なくとも 50 m以上の厚みを有することを特徴とする項 1473、 1474、 1475、 1 476又は 1477に記載されたいずれかの発光素子。
項 1479. 表面粗さの大きいセラミック材料を主成分とする焼結体に形成された薄膜が少 なくとも窒化ガリウムを含有するものであることを特徴とする項 1456、 1457、 145 8、 1459、 1460、 1461、 1462、 1463、 1464、 1465、 1466、 1467、 1468、 1469、 1470、 1471、 1472、 1473、 1474、 14 75、 1476、 1477又は 1478に記載されたいずれかの発光素子。
項 1480. 表面粗さの大きいセラミック材料を主成分とする焼結体に形成された薄膜が少 なくとも窒化ガリゥムを含むかあるいは窒化ガリゥムを主成分とする薄膜を有することを特徴 とする項 1456、 1457、 1458、 1459、 1460、 1461、 1462、 146 3、 1464、 1465、 1466、 1467、 1468、 1469、 1470、 1471、 1472、 1473、 1474、 1475、 1476、 1477、 1478又は 1479に記 載されたいずれかの発光素子。
項 1481. 表面粗さの大きいセラミック材料を主成分とする焼結体に形成された薄膜が窒 化ガリウムを主成分とするものであることを特徴とする項 1479又は 1480に記載された いずれかの発光素子。
項 1482. 表面粗さの大きいセラミック材料を主成分とする焼結体に形成された薄膜が A
とする項 1479、 1480又は 1481に記載されたいずれかの発光素子。
項 1483. 表面粗さの大きいセラミック材料を主成分とする焼結体に形成された薄膜が窒 化ガリゥムを 50モル%以上含むを特徴とする項 1479、 1480、 1481又は 1482 に記載されたいずれかの発光素子。
項 1484. 表面粗さの大きいセラミック材料を主成分とする焼結体に形成された少なくと も窒化ガリウムを含むかあるいは窒化ガリウムを主成分とする薄膜が無定形、 多結晶、 配向性 多結晶、 単結晶のうちから選ばれた少なくともいずれかの結晶状態であることを特徴とする項 1479、 1480、 1481、 1482又は 1483に記載されたいずれかの発光素子。 項 1485. 表面粗さの大きいセラミック材料を主成分とする焼結体に形成された少なくと も窒化ガリゥムを含むかあるいは窒化ガリゥムを主成分とする薄膜が単結晶であることを特徴 とする項 1484に記載された発光素子。
項 1486. 表面粗さの大きいセラミック材料を主成分とする焼結体に形成された最上層の 薄膜が少なくとも窒化ガリゥムを含むかあるいは窒化ガリゥムを主成分とするものであること を特徴とする項 1479、 1480、 1481、 1482、 1483、 1484又は 1485 に記載されたいずれかの発光素子。
項 1487. 表面粗さの大きいセラミック材料を主成分とする焼結体に形成された最上層の 薄膜が少なくとも窒化ガリゥムを含むかあるいは窒化ガリゥムを主成分とする単結晶であるこ とを特徴とする項 1486に記載された発光素子。
項 1488. 表面粗さの大きいセラミック材料を主成分とする焼結体に形成された薄膜が単 結晶、 無定形、 多結晶、 配向性多結晶のうちから選ばれた少なくともいずれか 2以上の結晶状 態が同時に混在しているものからなることを有することを特徴とする項 1456、 1457、 1458、 1459、 1460、 1461、 1462、 1463、 1464、 1465、 14 66、 1467、 1468、 1469、 1470、 1471、 1472、 1473、 1474、 1475、 1476、 1477、 1478、 1479、 1480、 1481、 1482、 14 83、 1484、 1485、 1486又は 1487に記載されたいずれかの発光素子。
項 1489. 表面粗さの大きいセラミック材料を主成分とする焼結体に形成された薄膜が単
一層あるいは少なくとも 2以上の層からなり、 該薄膜の少なくとも 1以上の層が単結晶、 無定 形、 多結晶、 配向性多結晶のうちから選ばれた少なくともいずれか 2以上の結晶状態が同時に 混在しているものからなることを とする項 1456、 1457、 1458、 1459、 1 460、 1461、 1462、 1463、 1464、 1465、 1466、 1467、 1 6 8、 1469、 1470、 1471、 1472、 1473、 1474、 1475、 1476、 1477、 1478、 1479、 1480、 1481、 1482、 1483、 1484、 14 85、 1486、 1487又は 1488に記載されたいずれかの発光素子。
項 1490. 表面粗さの大きいセラミック材料を主成分とする焼結体に形成された単結晶薄 膜のミラ一指数 (002) の格子面の X線回折ロッキングカーブの半値幅が 3600秒以下で あることを難とする項 1456、 1457、 1458、 1459、 1460、 1461、 1 462、 1463、 1464、 1465、 1466、 1467、 1468、 1469、 147 0、 1471、 1472、 1473、 1474、 1475、 1476、 1477、 1478、 1479、 1480、 1481、 1482、 1483、 1484、 1485、 1486、 14 87、 1488又は 1489に記載されたいずれかの発光素子。
項 1491. 表面粗さの大きいセラミック材料を主成分とする焼結体に形成された単結晶薄 膜のミラ一指数 (002) の格子面の X線回折ロッキングカーブの半値幅が 300秒以下であ ることを特徴とする項 1490に記載された発光素子。 '
項 1492. 表面粗さの大きいセラミック材料を主成分とする焼結体に形成された単結晶薄 膜のミラー指数 (002) の格子面の X線回折ロッキングカーブの半値幅が 240秒以下であ ることを特徴とする項 1490又は 1491に記載されたいずれかの発光素子。
項 1493. 表面粗さの大きいセラミック材料を主成分とする焼結体に形成された単結晶薄 膜のミラー指数 (002) の格子面の X線回折ロッキングカーブの半値幅が 200秒以下であ ることを特徴とする項 1490、 1491又は 1492に記載されたいずれかの発光素子。 項 1494. 表面粗さの大きいセラミック材料を主成分とする焼結体に形成された単結晶薄 膜のミラ一指数 (002) の格子面の X線回折ロッキング力一ブの半値幅が 150秒以下であ ることを特徴とする項 1490、 1491、 1492又は 1493に記載されたいずれかの発 光素子。
項 1495. 表面粗さの大きいセラミック材料を主成分とする焼結体に形成された単結晶薄 膜のミラー指数 (002) の格子面の X線回折ロッキングカーブの半値幅が 130秒以下であ ることを特徴とする項 1490、 1491、 1492、 1493又は 1494に記載されたい ずれかの発光素子。
項 1496. 表面粗さの大きいセラミック材料を主成分とする焼結体に形成された単結晶薄 膜のミラー指数 (002) の格子面の X線回折ロッキングカーブの半値幅が 100秒以下であ ることを特徴とする項 1490、 1491、 1492、 1493、 1494又は 1495に記 載されたいずれかの発光素子。
項 1497. 表面粗さの大きいセラミック材料を主成分とする焼結体が窒化アルミニウムを 主成分とする焼結体であることを特徴とする項 1446、 1447、 1448、 1449、 1 450、 1451、 1452、 1453、 1454、 1455、 1456、 1457、 145 8、 1459、 1460、 1461、 1462、 1463、 1464、 1465、 1466、 1467、 1468、 1469、 1470、 1471、 1472、 1473、 1474、 14 75、 1476、 1477、 1478、 1479、 1480、 1481、 1482、 1483、 1484、 1485、 1486、 1487、 1488、 1489、 1490、 1491、 14 92、 1493、 1494、 1495又は 1496に記載されたいずれかの発光素子。
項 1498. 表面粗さの大きいセラミック材料を主成分とする焼結体が六方晶系又 方晶
系のうちから選ばれた少なくともいずれかの結晶構造を有するセラミック材料を主成分とする 焼結体であることを體とする項 1446、 1447、 1448、 1449、 1450、 14 51、 1452、 1453、 1454、 1455、 1456、 1457、 1458、 1459、 1460、 1461、 1462、 1463、 1464、 1465、 1466、 1467、 14 68、 1469、 1470、 1471、 1472、 1473、 1474、 1475、 1476、 1477、 1478、 1479、 1480、 1481、 1482、 1483、 1484、 14 85、 1486、 1487、 1488、 1489、 1490、 1491、 1492、 1493、 1494、 1495又は 1496に記載されたいずれかの発光素子。
項 1499. 表面粗さの大きい六方晶系又は三方晶系のうちから選ばれた少なくともいずれ かの結晶構造を有するセラミック材料を主成分とする焼結体力職化亜鉛、 酸化ベリリウム、 酸 化アルミニウム、 炭化珪素、 窒化珪素、 窒化ガリウムのうちから選ばれた少なくとも 1種以上 を主成分とする焼結体であることを特徵とする項 1498に記載された発光素子。
項 1500. 表面粗さの大きいセラミック材料を主成分とする焼結体力戰化ジルコニウム、 酸ィ匕マグネシウム、 アルミン酸マグネシウム、 酸化チタン、 チタン酸バリウム、 チタン酸ジル コン蘭、希土類 素酸化物、謝匕トリウム、各種フェライト、 ムライ卜、 フオルステライト、 ステアタイト、 結晶化ガラスのうちから選ばれた少なくとも 1種以上を主成分とする焼結体で あることを特徴とする項 1446、 1447、 1448、 1449、 1450、 1451、 1 452、 1453、 1454、 1455、 1456、 1457、 1458、 1459、 146 0、 1461、 1462、 1463、 1464、 1465、 1466、 1467、 1468、 1469、 1470、 1471、 1472、 1473、 1474、 1475、 1476、 14
77、 1478、 1479、 1480、 1481、 1482、 1483、 1484、 1485、 1486、 1487、 1488、 1489、 1490、 1491、 1492、 1493、 14 94、 1495又は 1496に記載されたいずれかの発光素子。
項 1501. 表面粗さの大きいセラミック材料を主成分とする焼結体が窒化アルミニウム、 酸化菌、 酸化ベリリウム、 酸ィ匕アルミニウム、 炭化珪素、 窒化珪素、 窒化ガリウム、 酸化ジ ルコニゥム、 酸化マグネシウム、 アルミン酸マグネシウム、 酸化イットリウムのうちから選ば れた少なくとも 1種以上を主成分とする能結体であることを特徴とする項 1497、 1498、 1499又は 1500に記載されたいずれかの発光素子。
項 1502. 表面粗さの大きいセラミック材料を主成分とする焼結体が)1^過性を有するこ とを特徴とする項 1446、 1447、 1448、 1449、 1450、 1451、 1452、 1453、 1454、 1455、 1456、 1457、 1458、 1459、 1460、 14 61、 1462、 1463、 1464、 1465、 1466、 1467、 1468、 1469、 1470、 1471、 1472、 1473、 1474、 1475、 1476、 1477、 14
78、 1479、 1480、 1481、 1482、 1483、 1484、 1485、 1486、 1487、 1488、 1489、 1490、 1491、 1492、 1493、 1494、 14 95、 1496、 1497、 1498、 1499、 1500又は 1501に記載されたいずれ かの発光素子。
項 1503. 窒化ガリウム、 窒化インジウム、 窒化アルミニウムのうちから選ばれた少なく とも 1種以上を主成分とする薄膜からなる少なくとも N型半導体層及び発光層及び P型半導体 層を含む積層体により構成される発光素子であって、 該 N型半導体層及び発光層及び P型半導 体層の積層体が窒化ガリウム、 窒化インジウム、 窒化アルミニウムのうちから選ばれた少なく とも 1種以上を主成分とする薄膜が形成されたセラミック材料を主成分とする焼結体に形成さ れていることを特徴とする発光素子。
項 1504. セラミック材料を主成分とする焼結体に形成された窒化ガリウム、 窒化インジ
ゥム、窒化アルミニウムのうちから選ばれた少なくとも 1種以上を主成分とする薄膜が無定形、 多結晶、 配向性多結晶、 単結晶のうちから選ばれる少なくともいずれかの結晶状態を有するこ とを特徴とする項 1 5 0 3に記載された発光素子。
項 1 5 0 5. セラミック材料を主成分とする焼結体に形成された窒化ガリウム、 窒化インジ ゥム、 窒化アルミニウムのうちから選ばれた少なくとも 1種以上を主成分とする薄膜の少なく とも一部が単結晶であることを特徴とする項 1 5 0 3又は 1 5 0 4に記載されたいずれかの発 光素子。
項 1 5 0 6. セラミック材料を主成分とする焼結体に形成された窒化ガリウム、 窒化インジ ゥム、 窒化アルミニウムのうちから選ばれた少なくとも 1種以上を主成分とする薄膜が 1層か らなることを とする項 1 5 0 3、 1 5 0 4又は 1 5 0 5に記載されたいずれかの発光 ¾?。 項 1 5 0 7. セラミック材料を主成分とする焼結体に形成された窒化ガリウム、 窒化インジ ゥム、 窒化アルミニウムのうちから選ばれた少なくとも 1種以上を主成分とする薄膜が少なく とも無定形であることを特徴とする項 1 5 0 6に記載された発光素子。
項 1 5 0 8. セラミック材料を主成分とする焼結体に形成された窒化ガリウム、 窒化インジ ゥム、 窒化アルミニウムのうちから選ばれた少なくとも 1種以上を主成分とする薄膜が多結晶 であることを特徴とする項 1 5 0 6に記載された発光素子。
項 1 5 0 9. セラミック材料を主成分とする焼結体に形成された窒化ガリウム、 窒化インジ ゥム、 窒化アルミニウムのうちから選ばれた少なくとも 1種以上を主成分とする薄膜が ¾H向性 多結晶であることを特徴とする項 1 5 0 6に記載された発光素子。
項 1 5 1 0. セラミック材料を主成分とする焼結体に形成された窒化ガリウム、 窒化インジ ゥム、 窒化アルミニウムのうちから選ばれた少なくとも 1種以上を主成分とする薄膜が単結晶 であることを特徴とする項 1 5 0 6に記載された発光素子。
項 1 5 1 1. セラミック材料を主成分とする焼結体に形成された窒化ガリゥム、 窒化インジ ゥム、 窒化アルミニウムのうちから選ばれた少なくとも 1種以上を主成分とする薄膜が少なく とも 2以上の層からなることを特徴とする項 1 5 0 3、 1 5 0 4又は 1 5 0 5に記載されたい ずれかの発光素子。
項 1 5 1 2. セラミック材料を主成分とする焼結体に形成された窒化ガリウム、 窒化インジ ゥム、 窒化アルミニウムのうちから選ばれた少なくとも 1種以上を主成分とする薄膜が少なく とも 2以上の層からなり、 各層がそれぞれ無定形、 多結晶、 配向性多結晶、 単結晶のうちから 選ばれる少なくともいずれかの結晶状態を有することを特徴とする項 1 5 1 1に記載された発 光素子。
項 1 5 1 3. セラミック材料を主成分とする焼結体に形成された窒化ガリウム、 窒化インジ ゥム、 窒化アルミニウムのうちから選ばれた少なくとも 1種以上を主成分とする薄膜が少なく とも 2以上の層からなり、 該セラミック材料を主成分とする焼結体に直接形成された薄膜層が 無定形、 多結晶、 配向性多結晶、 単結晶のうちから選ばれる少なくともいずれかの結晶状態を 有することを特徴とする項 1 5 1 1又は 1 5 1 2記載されたいずれかの発光素子。
項 1 5 1 4. セラミック材料を主成分とする焼結体に形成された窒化ガリウム、 窒化インジ ゥム、 窒化アルミニウムのうちから選ばれた少なくとも 1種以上を主成分とする薄膜が少なく とも 2以上の層からなり、 該セラミツク材料を主成分とする焼結体に直接形成された薄膜層が 無定形、 多結晶、 配向性多結晶のうちから選ばれる少なくともいずれかの結晶状態を有するこ とを特徴とする項 1 5 1 1、 1 5 1 2又は 1 5 1 3に記載されたいずれかの発光素子。
項 1 5 1 5. セラミック材料を主成分とする焼結体に形成された窒化ガリウム、 窒化インジ ゥム、 窒化アルミニウムのうちから選ばれた少なくとも 1種以上を主成分とする薄膜が少なく とも 2以上の層からなり、 該セラミツク材料を主成分とする焼結体に直接形成された薄膜層が
配向性多結晶であることを特徴とする項 1511、 1512、 1513又は 1514に記載さ れたいずれかの発光素子。
項 1516. セラミック材料を主成分とする焼結体に形成された窒化ガリウム、 窒化インジ ゥム、 窒化アルミニウムのうちから選ばれた少なくとも 1種以上を主成分とする薄膜が少なく とも 2以上の層からなり、 少なくとも 1層が単結晶であることを とする項 1511、 15 12、 1513、 1514又は 1515に記載されたいずれかの発光素子。
項 1517. セラミック材料を主成分とする焼結体に形成された窒化ガリウム、 窒化インジ ゥム、 窒化アルミニウムのうちから選ばれた少なくとも 1種以上を主成分とする薄膜が少なく とも 2以上の層からなり、 最上層の薄膜が単結晶であることを特徴とする項 1511、 151 2、 1513、 1514、 1515又は 1516に記載されたいずれかの発光素子。
項 1518. セラミック材料を主成分とする焼結体に形成された窒化ガリウム、 窒化インジ ゥム、 窒化アルミニウムのうちから選ばれた少なくとも 1種以上を主成分とする薄膜が少なく とも単結晶薄膜層を有し該単結晶薄膜層の厚みが 300 m未満であることを とする項 1 503、 1504、 1505、 1506、 1507、 1508、 1509、 1510、 151 1、 1512、 1513、 1514、 1515、 1516又は 1517に記載されたいずれか の発光軒。
項 1519. セラミック材料を主成分とする焼結体に形成された窒化ガリウム、 窒化インジ ゥム、 窒化アルミニウムのうちから選ばれた少なくとも 1種以上を主成分とする薄膜が少なく とも単結晶薄膜層を有し該単結晶薄膜層の厚みが 200 以下であることを ^とする項 1 518に記載された発光素子。
項 1520. セラミック材料を主成分とする焼結体に形成された薄膜が少なくとも 0. In m以上の厚みを有することを特徴とする項 1503、 1504、 1505、 1506、 150 7、 1508、 1509、 1510、 1511、 1512、 1513、 1514、 1515、 1516、 1517、 1518又は 1519に記載されたいずれかの発光素子。
項 1521. セラミック材料を主成分とする焼結体に形成された薄膜が少なくとも 0. 5n m以上の厚みを有することを特徴とする項 1520に記載された発光素子。
項 1522. セラミック材料を主成分とする焼結体に形成された薄膜が少なくとも 0. 3 m以上の厚みを有することを特徴とする項 1520又は 1521に記載されたいずれかの発光 項 1523. セラミック材料を主成分とする焼結体に形成された薄膜が少なくとも 3. 5 m以上の厚みを有することを特徴とする項 1520、 1521又は 1522に記載されたいず れかの発光素子。
項 1524. セラミック材料を主成分とする焼結体に形成された薄膜が少なくとも 10 m 以上の厚みを有することを特徴とする項 1520、 1521、 1522又は 1523に記載さ れたいずれかの発光素子。
項 1525. セラミック材料を主成分とする焼結体に形成された薄膜が少なくとも 50 m 以上の厚みを有することを特徴とする項 1520、 1521、 1522、 1523又は 152 4に記載されたいずれかの発光素子。
項 1526. セラミック材料を主成分とする焼結体に形成された薄膜が少なくとも窒化ガリ ゥムを含有するものであることを特徴とする項 1503、 1504、 1505、 1506、 1 507、 1508、 1509s 1510、 1511、 1512、 1513、 1514, 151 5、 1516、 1517、 1518、 1519、 1520、 1521、 1522、 1523、 1524又は 1525に記載されたいずれかの発光素子。
項 1527. セラミック材料を主成分とする焼結体に形成された薄膜が少なくとも窒化ガリ
ゥムを含むかあるいは窒化ガリウムを主成分とする薄膜を有することを特徴とする項 1503、 1504、 1505、 1506、 1507、 1508、 1509、 1510、 1511、 15 12、 1513、 1514、 1515、 1516、 1517、 1518、 1519、 1520、 1521、 1522、 1523、 1524、 1525又は 1526に記載されたいずれかの発 光素子。
項 1528. セラミック材料を主成分とする焼結体に形成された薄膜が窒化ガリウムを主成 分とするものであることを とする項 1526又は 1527に記載されたいずれかの発光素 子。
項 1529. セラミック材料を主成分とする焼結体に形成された薄膜が A lxGayI r^— x一 yN (0<y≤l) で表わされる組成を有することを特徴とする項 1526、 1527又は 15
28に記載されたいずれかの発光素子。
項 1530. セラミック材料を主成分とする焼結体に形成された薄膜が窒化ガリウムを 50 モル%以上含むを特徴とする項 1526、 1527、 1528又は 1529に記載されたいず れかの発光素子。
項 1531. セラミック材料を主成分とする焼結体に形成された少なくとも窒化ガリウムを 含むかあるいは窒化ガリウムを主成分とする薄膜が無定形、 多結晶、 配向性多結晶、 単結晶の うちから選ばれた少なくともいずれかの結晶状態であることを特徴とする項 1526、 152 7、 1528、 1529又は 1530に記載されたいずれかの発光素子。
項 1532. セラミック材料を主成分とする焼結体に形成された少なくとも窒化ガリウムを 含むかあるいは窒化ガリウムを主成分とする薄膜が単結晶であることを特徴とする項 1531 に記載された発光素子。
項 1533. セラミック材料を主成分とする焼結体に形成された薄膜の最上層が少なくとも 窒化ガリウムを含むかあるいは窒化ガリウムを主成分とするものであることを特徴とする項 1 526、 1527、 1528、 1529、 1530、 1531又は 1532に記載されたいず れかの発光素子。
項 1534. セラミック材料を主成分とする焼結体に形成された薄膜の最上層が少なくとも 窒化ガリゥムを含むかあるいは窒化ガリゥムを主成分とする単結晶であることを特徴とする項 1533に記載された発光素子。
項 1535. セラミック材料を主成分とする焼結体に形成された薄膜が単結晶、 無定形、 多 結晶、 配向性多結晶のうちから選ばれた少なくともいずれか 2以上の結晶状態が同時に混在し ているものからなることを糊毁とする項 1503、 1504、 1505、 1506、 1507、 1508、 1509、 1510、 1511、 1512、 1513、 1514、 1515、 15
16、 1517、 1518、 1519、 1520、 1521、 1522、 1523、 1524、 1525、 1526、 1527、 1528、 1529、 1530、 1531、 1532、 15
33又は 1534に記載されたいずれかの発光素子。
項 1536. セラミック材料を主成分とする焼結体に形成された薄膜が単一層あるいは少な くとも 2以上の層からなり、 該薄膜の少なくとも 1以上の層が単結晶、 無定形、 多結晶、 配向 性多結晶のうちから選ばれた少なくともいずれか 2以上の結晶状態が同時に混在しているもの からなることを ^とする項 1503、 1504、 1505、 1506、 1507、 1508、 1509、 1510、 1511、 1512、 1513、 1514、 1515、 1516、 15
17、 1518、 1519、 1520、 1521、 1522、 1523、 1524、 1525、 1526、 1527、 1528、 1529、 1530、 1531、 1532、 1533、 15 34又は 1535に記載されたいずれかの発光素子。
項 1537.セラミック材料を主成分とする能結体に形成された単結晶薄膜のミラー指数(0
02) の格子面の X線回折ロッキングカーブの半値幅が 3600秒以下であることを特徴とす る項 1503、 1504、 1505、 1506、 1507、 1508、 1509、 1510、 1511、 1512、 1513、 1514、 1515、 1516、 1517、 1518、 15 19、 1520、 1521、 1522、 1523、 1524、 1525、 1526、 1527、 1528、 1529、 1530、 1531、 1532、 1533、 1534、 1535又は 1 536に記載されたいずれかの発光素子。
項 1538·セラミック材料を主成分とする能結体に形成された単結晶薄膜のミラー指数(0 02) の格子面の X線回折ロッキングカーブの半値幅が 300秒以下であることを とする 項 1537に記載された発光素子。
項 1539.セラミック材料を主成分とする;^結体に形成された単結晶薄膜のミラー指数(0 02) の格子面の X線回折ロッキングカーブの半値幅が 240秒以下であることを特徴とする 項 1537又は 1538に記載されたいずれかの発光素子。
項 1540.セラミツク材料を主成分とする焼結体に形成された単結晶薄膜のミラー指数 ( 0 02) の格子面の X線回折ロッキングカーブの半値幅が 200秒以下であることを特徴とする 項 1537、 1538又は 1539に記載されたいずれかの発光素子。
項 1541.セラミック材料を主成分とする飾体に形成された単結晶薄膜のミラ一指数(0 02) の格子面の X線回折ロッキングカーブの半値幅が 150秒以下であることを特徴とする 項 1537、 1538、 1539又は 1540に記載されたいずれかの発光素子。
項 1542.セラミック材料を主成分とする焼結体に形成された単結晶薄膜のミラー指数(0
02) の格子面の X線回折ロッキングカーブの半値幅が 130秒以下であることを とする 項 1537、 1538、 1539、 1540又は 1541に記載されたいずれかの発光素子。 項 1543.セラミック材料を主成分とする 結体に形成された単結晶薄膜のミラ一指数(0 02) の格子面の X線回折ロッキングカーブの半値幅が 100秒以下であることを特徴とする 項 1537、 1538、 1539、 1540、 1541又は 1542に記載されたいずれかの 発光軒。
項 1544. セラミック材料を主成分とする焼結体が窒化アルミニウムを主成分とする 結 体であることを ^とする項 1503、 1504、 1505、 1506、 1507、 1508、
1509、 1510、 1511、 1512、 1513、 1514、 1515、 1516、 15
17、 1518、 1519、 1520、 1521、 1522、 1523、 1524、 1525、 1526、 1527、 1528、 1529、 1530、 1531、 1532、 1533、 15
34、 1535、 1536、 1537、 1538、 1539、 1540、 1541、 1542 又は 1543に記載されたいずれかの発光素子。
項 1545. セラミック材料を主成分とする焼結体が六方晶系又は三方晶系のうちから選ば れた少なくともいずれかの結晶構造を有するセラミック材料を主成分とする焼結体であること を特徴とする項 1503、 1504、 1505、 1506、 1507、 1508、 1509、 1510、 1511、 1512、 1513、 1514、 1515、 1516、 1517、 15
18、 1519、 1520、 1521、 1522、 1523、 1524、 1525、 1526、 1527、 1528、 1529、 1530、 1531、 1532、 1533、 1534、 15
35、 1536、 1537、 1538、 1539、 1540、 1541、 1542又は 154 3に記載されたいずれかの発光素子。
項 1546. 六方晶系又 方晶系のうちから選ばれた少なくともいずれかの結晶構造を有 するセラミック材料を主成分とする焼結体が 化亜鉛、 酸化ベリリウム、 酸化アルミニウム、 炭化珪素、 窒化珪素、 窒化ガリウムのうちから選ばれた少なくとも 1種以上を主成分とする焼 結体であることを特徴とする項 1545に記載された発光素子。
004鳩 051
618
項 1547.セラミック材料を主成分とする焼結体が 化ジルコニウム、酸化マグネシウム、 アルミン酸マグネシウム、 酸化チタン、 チタン酸バリウム、 チタン酸ジルコン 、 希土類 素酸化物、 酸化トリウム、 各種フェライト、 ムライト、 フォルステライト、 ステアタイト、 結 晶化ガラスのうちから選ばれた少なくとも 1種以上を主成分とする焼結体であることを と する項 1503、 1504、 1505、 1506、 1507、 1508、 1509、 1510、 1511、 1512、 1513、 1514、 1515、 1516、 1517、 1518、 15 19、 1520、 1521、 1522、 1523、 1524、 1525、 1526、 1527、 1528、 1529、 1530、 1531、 1532、 1533、 1534、 1535、 15 36、 1537、 1538、 1539、 1540、 1541、 1542又は 1543に記載さ れたいずれかの発光素子。
項 1548. セラミック材料を主成分とする焼結体が窒化アルミニウム、 酸化亜鉛、 酸化べ リリウム、 酸化アルミニウム、.炭化珪素、 窒化珪素、 窒化ガリウム、 酸化ジルコニウム、 酸化 マグネシウム、 アルミン酸マグネシウム、 酸化ィットリウムのうちから選ばれた少なくとも 1 種以上を主成分とする焼結体であることを [とする項 1544、 1545、 1546又は 1 547に記載されたいずれかの発光素子。
項 1549. セラミック材料を主成分とする焼結体が光 性を有することを特徴とする項 1503、 1504、 1505、 1506、 1507、 1508、 1509、 1510、 15 11、 1512、 1513、 1514、 1515、 1516、 1517、 1518、 1519、 1520、 1521、 1522、 1523、 1524、 1525、 1526、 1527、 15 28、 1529、 1530、 1531、 1532、 1533、 1534、 1535、 1536、
1537、 1538、 1539、 1540、 1541、 1542、 1543、 1544、 15 45、 1546、 1547又は 1548に記載されたいずれかの発光素子。
項 1550. セラミック材料を主成分とする焼結体が表面粗さの大きいものであることを特 徴とする項 1503、 1504、 1505、 1506、 1507、 1508、 1509、 15 10、 1511、 1512、 1513、 1514、 1515、 1516、 1517、 1518、 1519、 1520、 1521、 1522、 1523、 1524、 1525、 1526、 15 27、 1528、 1529、 1530、 1531、 1532、 1533、 1534、 1535、 1536、 1537、 .1538、 1539、 1540、 1541、 1542、 1543、 15 44、 1545、 1546、 1547、 1548又は 1549に記載されたいずれかの発光素 子。
項 1551. セラミック材料を主成分とする焼結体が光 ¾Μ性を有しかつ表面粗さの大きい ものであることを樹敷とする項 1503、 1504、 1505、 1506、 1507、 150 8、 1509、 1510、 1511、 1512、 1513、 1514、 1515、 1516、 1517、 1518、 1519、 1520、 1521、 1522、 1523、 1524、 15
25、 1526、 1527、 1528、 1529、 1530、 1531、 1532、 1533、 1534、 1535、 1536、 1537、 1538、 1539、 1540、 1541、 15 42、 1543、 1544、 1545、 1546、 1547、 1548、 1549又は 155 0に記載されたいずれかの発光^?。
項 1552. 窒化ガリウム、 窒化インジウム、 窒化アルミニウムのうちから選ばれた少なく とも 1種以上を主成分とする薄膜からなる少なくとも N型半導体層及び発光層及び P型半導体 層を含む積層体により構成される発光^?であって、 該 N型半導体層及び発光層及び P型半導 体層の積層体が窒化ガリゥム、 窒化ィンジゥム、 窒化アルミニゥムのうちから選ばれた少なく とも 1種以上を主成分とする単結晶薄膜が形成されたセラミック材料を主成分とする焼結体に 形成されていることを特徴とする発光素子。
項 1553. セラミック材料を主成分とする焼結体に形成された窒化ガリウム、 窒化インジ ゥム、 窒化アルミニウムのうちから選ばれた少なくとも 1種以上を主成分とする単結晶薄膜が 1層からなることを特徴とする項 1552に記載された発光素子。
項 1554. セラミック材料を主成分とする焼結体に形成された窒化ガリウム、 窒化インジ ゥム、 窒化アルミニウムのうちから選ばれた少なくとも 1種以上を主成分とする単結晶薄膜が 少なくとも 2以上の層からなることを特徴とする項 1553に記載された発光素子。
項 1555. セラミック材料を主成分とする焼結体に形成された窒化ガリウム、 窒化インジ ゥム、 窒化アルミニウムのうちから選ばれた少なくとも 1種以上を主成分とする単結晶薄膜が 少なくとも 2以上の層からなり、 少なくとも 1層は単結晶であることを特徴とする項 1554 に記載された発光素子。
項 1556. セラミック材料を主成分とする焼結体に形成された窒化ガリウム、 窒化インジ ゥム、 窒化アルミニウムのうちから選ばれた少なくとも 1種以上を主成分とする単結晶薄膜が 少なくとも 2以上の層からなり、 少なくとも 1層は単結晶でありその他に無定形、 多結晶、 配 向性多結晶、 単結晶のうちから選ばれる少なくともいずれかの結晶状態を有する層からなるこ とを特徴とする項 1554又は 1555に記載されたいずれかの発光素子。
項 1557 セラミック材料を主成分とする焼結体に形成された窒化ガリウム、 窒化インジ ゥム、 窒化アルミニウムのうちから選ばれた少なくとも 1種以上を主成分とする単結晶薄膜が 少なくとも 2以上の層からなり、 該セラミック材料を主成分とする焼結体に直接形成された薄 膜層が無定形、 多結晶、 配向性多結晶、 単結晶のうちから選ばれる少なくともいずれかの結晶 状態を有することを特徴とする項 1554、 1555又は 1556記載されたいずれかの発光 素子。
項 1558. セラミック材料を主成分とする焼結体に形成された窒化ガリウム、 窒化インジ ゥム、 窒化アルミニゥムのうちから選ばれた少なくとも 1種以上を主成分とする単結晶薄膜が 少なくとも 2以上の層からなり、 該セラミック材料を主成分とする焼結体に直接形成された薄 膜層が無定形、 多結晶、 配向性多結晶のうちから選ばれる少なくともいずれかの結晶状態を有 することを [とする項 1554、 1555、 1556又は 1557に記載されたいずれかの 発光素子。
項 1559. セラミック材料を主成分とする焼結体に形成された窒化ガリウム、 窒化インジ ゥム、 窒化アルミニウムのうちから選ばれた少なくとも 1種以上を主成分とする単結晶薄膜が 少なくとも 2以上の層からなり、 該セラミック材料を主成分とする焼結体に直接形成された薄 漏力 己向性多結晶であることを特徴とする項 1554、 1555、 1556、 1557又は 1558に記載されたいずれかの発光素子。
項 1560. セラミック材料を主成分とする焼結体に形成された窒化ガリウム、 窒化インジ ゥム、 窒化アルミニウムのうちから選ばれた少なくとも 1種以上を主成分とする単結晶薄膜が 少なくとも 2以上の層からなり、 すべての層が単結晶であることを特徴とする項 1554、 1 555、 1556又は 1557に記載されたいずれかの発光素子。
項 1561. セラミック材料を主成分とする焼結体に形成された窒化ガリウム、 窒化インジ ゥム、 窒化アルミニウムのうちから選ばれた少なくとも 1種以上を主成分とする単結晶薄膜が 少なくとも 2以上の層からなり、 最上層の薄膜が単結晶であることを特徴とする項 1554、 1555、 1556、 1557、 1558、 1559又は 1560に記載されたいずれかの発 光軒。
項 1562. セラミック材料を主成分とする焼結体に形成された窒化ガリウム、 窒化インジ ゥム、 窒化アルミニウムのうちから選ばれた少なくとも 1種以上を主成分とする単結晶薄膜の 厚みが 300 満であることを特徴とする項 1552、 1553、 1554、 1555、
1556、 1557、 1558、 1559、 1560又は 1561に記載されたいずれかの発 光素子。
¾1563. セラミック材料を主成分とする焼結体に形成された窒化ガリウム、 窒化インジ ゥム、 窒化アルミニウムのうちから選ばれた少なくとも 1種以上を主成分とする単結晶薄膜の 厚みが 200 m以下であることを特徴とする項 1562に記載された発光素子。
項 1564. セラミック材料を主成分とする焼結体に形成された単結晶薄膜が少なくとも 0. 1 nm以上の厚みを有することを特徴とする項 1552、 1553、 1554、 1555、 1 556、 1557、 1558、 1559、 1560、 1561、 1562又は 1563に記載 されたいずれかの発光素子。
項 1565. セラミック材料を主成分とする焼結体に形成された単結晶薄膜が少なくとも 0. 5 nm以上の厚みを有することを特徴とする項 1564に記載された発光素子。
項 1566. セラミック材料を主成分とする焼結体に形成された単結晶薄膜が少なくとも 0. 3 m以上の厚みを有することを特徴とする項 1564又は 1565に記載されたいずれかの 発光耔。
項 1567. セラミック材料を主成分とする焼;結体に形成された単結晶薄膜が少なくとも 3.
5 m以上の厚みを有することを特徴とする項 1564、 1565又は 1566に記載された いずれかの発光素子。
項 1568. セラミック材料を主成分とする焼結体に形成された単結晶薄膜が少なくとも 1 0 m以上の厚みを有することを特徴とする項 1564、 1565、 1566又は 1567に 記載されたいずれかの発光素子。
項 1569. セラミック材料を主成分とする焼結体に形成された単結晶薄膜が少なくとも 5
0 m以上の厚みを有することを特徴とする項 1564、 1565、 1566、 1567又は
1568に記載されたいずれかの発光素子。
項 1570. セラミック材料を主成分とする焼結体に形成された単結晶薄膜が少なくとも窒 化ガリウムを含有するものであることを特徴とする項 1552、 1553、 1554、 155 5、 1556、 1557、 1558、 1559、 1560、 1561、 1562、 1563、 1564、 1565、 1566、 1567、 1568又は 1569に記載されたいずれかの発 光素子。
項 1571. セラミック材料を主成分とする焼結体に形成された単結晶薄膜が少なくとも窒 化ガリゥムを含むかあるいは窒化ガリゥムを主成分とする単結晶薄膜を有することを特徴とす る項 1552、 1553、 1554、 1555、 1556、 1557、 1558、 1559、 1560、 1561、 1562、 1563、 .1564、 1565、 1566、 1567、 15
68、 1569又は 1570に記載されたいずれかの発光素子。
項 1572. セラミック材料を主成分とする焼結体に形成された単結晶薄膜が窒化ガリウム を主成分とするものであることを特徴とする項 1570又は 1571に記載されたいずれかの 発光素子。
項 1573. セラミック材料を主成分とする焼結体に形成された単結晶薄膜が A lxGayI n x yN (0<y≤l)で表わされる組成を有することを糊敷とする項 1570、 1571又 は 1572に記載されたいずれかの発光素子。
項 1574. セラミック材料を主成分とする焼結体に形成された単結晶薄膜が窒化ガリウム を 50モル%以上含むを特徴とする項 1570、 1571、 1572又は 1573に記載され たいずれかの発光素子。
項 1575. セラミック材料を主成分とする焼結体に形成された最上層の単結晶薄膜が少な くとも窒化ガリウムを含むかあるいは窒化ガリウムを主成分とするものであることを特徴とす
る項 1552、 1553、 1554、 1555、 1556、 1557、 1558、 1559、 1560、 1561、 1562、 1563、 1564、 1565、 1566、 1567、 15 68、 1569、 1570、 1571、 1572、 1573又は 1574に記載されたいずれ かの発光素子。
項 1576. セラミック材料を主成分とする焼結体に形成された単結晶薄膜が単結晶とその 他に無定形、 多結晶、 配向性多結晶のうちから選ばれた少なくともいずれか 1以上の結晶状態 のものとが混在しているものであることを有することを 1¾とする項 1552、 1553、 1 554, 1555、 1556、 1557、 1558、 1559、 1560、 1561、 156 2、 1563、 1564、 1565、 1566、 1567、 1568、 1569、 1570、 1571、 1572、 1573、 1574又は 1575に記載されたいずれかの発光素子。 項 1577. セラミック材料を主成分とする焼結体に形成された単結晶薄膜が単一層あるい は少なくとも 2以上の層からなり、 該単結晶薄膜の少なくとも 1以上の層が単結晶とその他に 無定形、 多結晶、 配向性多結晶のうちから選ばれた少なくともいずれか 1以上の結晶状態のも のとが混在しているものからなることを特徴とする項 1552、 1553、 1554、 155 5、 1556、 1557、 1558、 1559、 1560、 1561、 1562、 1563、 1564、 1565、 1566、 1567、 1568、 1569、 1570、 1571、 15 72、 1573、 1574、 1575又は 1576に記載されたいずれかの発光素子。
項 1578.セラミック材料を主成分とする焼結体に形成された単結晶薄膜のミラー指数(0 02) の格子面の X線回折ロッキングカーブの半値幅が 3600秒以下であることを ^とす る項 1552、 1553、 1554、 1555、 1556、 1557、 1558、 1559、 1560、 1561、 1562、 1563、 1564、 1565、 1566、 1567、 15 68、 1569、 1570、 1571、 1572、 1573、 1574、 1575、 1576 又は 1577に記載されたいずれかの発光素子。
項 1579.セラミック材料を主成分とする; ¾結体に形成された単結晶薄膜のミラ一指数(0 02) の格子面の X線回折ロッキングカーブの半値幅が 300秒以下であることを特徴とする 項 1578に記載された発光素子。
項 1580.セラミック材料を主成分とする焼結体に形成された単結晶薄膜のミラー指数(0 02) の格子面の X線回折ロッキング力一ブの半値幅が 240秒以下であることを,とする 項 1578又は 1579に記載されたいずれかの発光素子。
項 1581.セラミック材料を主成分とする焼結体に形成された単結晶薄膜のミラー指数(0 02) の格子面の X線回折ロッキングカーブの半値幅が 200秒以下であることを特徴とする 項 1578、 1579又は 1580に記載されたいずれかの発光素子。
項 1582.セラミック材料を主成分とする焼結体に形成された単結晶薄膜のミラー指数(0 02) の格子面の X線回折ロッキングカーブの半値幅が 150秒以下であることを特徴とする 項 1578、 1579、 1580又は 1581に記載されたいずれかの発光素子。
項 1583.セラミック材料を主成分とする焼結体に形成された単結晶薄膜のミラ一指数(0 02) の格子面の X線回折ロッキングカーブの半値幅が 130秒以下であることを特徴とする 項 1578、 1579、 1580、 1581又は 1582に記載されたいずれかの発光素子。 項 1584.セラミック材料を主成分とする焼結体に形成された単結晶薄膜のミラー指数(0 02) の格子面の X線回折ロッキングカーブの半値幅が 100秒以下であることを とする 項 1578、 1579、 1580、 1581、 1582又は 1583に記載されたいずれかの 発光素子。
項 1585. セラミック材料を主成分とする焼結体が窒化アルミニウムを主成分とする醫 体であることを體とする項 1552、 1553、 1554、 1555、 1556、 1557、
1558、 1559、 1560、 1561、 1562、 1563、 1564, 1565、 15
66、 1567、 1568、 1569、 1570、 1571、 1572、 1573、 1574、 1575、 1576、 1577、 1578、 1579、 1580、 1581、 1582、 15 8 SXUl 584に記載されたいずれかの発光素子。
項 1586. セラミック材料を主成分とする焼結体が六方晶系又は三方晶系のうちから選ば れた少なくともいずれかの結晶構造を有するセラミック材料を主成分とする焼結体であること を [とする項 1552、 1553、 1554、 1555、 1556、 1557、 1558、 1559、 1560、 1561、 1562、 1563、 1564, 1565、 1566、 15
67、 1568、 1569、 1570、 1571、 1572、 1573、 1574, 1575、 1576、 1577、 1578、 1579、 1580、 1581、 1582、 1583又は 1 584に記載されたいずれかの発光素子。
項 1587. 六方晶系又は三方晶系のうちから選ばれた少なくともいずれかの結晶構造を有 するセラミック材料を主成分とする焼結体力雙化亜鉛、 酸化ベリリウム、 酸化アルミニウム、 炭化珪素、 窒化珪素、 窒化ガリウムのうちから選ばれた少なくとも 1種以上を主成分とする焼 結体であることを特徴とする項 1586に記載された発光素子。
項 1588.セラミック材料を主成分とする麵体が ¾化ジルコニウム、酸化マグネシウム、 アルミン酸マグネシウム、 酸化チタン、 チタン酸バリウム、 チタン酸ジルコン 、 希土航 素酸化物、 酸化トリウム、 各種フェライト、 ムライト、 フォルステライト、 ステアタイト、 結 晶化ガラスのうちから選ばれた少なくとも 1種以上を主成分とする焼結体であることを特徴と する項 1552、 1553、 1554、 1555、 1556、 1557、 1558、 1559、 1560、 1561、 1562、 1563、 1564、 1565、 1566、 1567、 15
68、 1569、 1570、 1571、 1572、 1573、 1574、 1575、 1576、 1577、 1578、 1579、 1580、 1581、 1582、 1583又は 1584に記 載されたいずれかの発光素子。
項 1589. セラミック材料を主成分とする焼結体が窒化アルミニウム、 酸化亜鉛、 酸化べ リリウム、 酸化アルミニウム、 炭化珪素、 窒化珪素、 窒化ガリウム、 酸化ジルコニウム、 酸化 マグネシウム、 アルミン酸マグネシウム、 酸化ィットリウムのうちから選ばれた少なくとも 1 種以上を主成分とする焼結体であることを特徴とする項 1585、 1586、 1587又は 1 588に記載されたいずれかの発光素子。
項 1590. セラミック材料を主成分とする焼結体が ½¾i性を有することを特徴とする項 1552、 1553、 1554、 1555、 1556、 1557、 1558、 1559、 15 60、 1561、 1562、 1563、 1564、 1565、 1566、 1567、 1568、 1569、 1570、 1571、 1572、 1573、 1574、 1575、 1576、 15 77、 1578、 1579、 1580、 1581、 1582、 1583、 1584, 1585、 1586、 1587、 1588又は 1589に記載されたいずれかの発光素子。
項 1591. セラミック材料を主成分とする焼結体が表面粗さの大きいものであることを特 徴とする項 1552、 1553、 1554、 1555、 1556、 1557、 1558、 15 59、 1560、 1561、 1562、 1563、 1564, 1565、 1566、 1567、 1568、 1569、 1570、 1571、 1572、 1573、 1574, 1575、 15 76、 1577、 1578、 1579、 1580、 1581、 1582、 1583、 1584、 1585、 1586、 1587、 1588、 1589又は 1590に記載されたいず'れかの発 光素子。
項 1592. セラミック材料を主成分とする焼結体が ½¾ 性を有し力り表面粗さの大きい ものであることを特徴とする項 1552、 1553、 1554、 1555、 1556、 155
7、 1558、 1559、 1560、 1561、 1562、 1563、 156 , 1565、 1566、 1567、 1568、 1569、 1570、 1571、 1572、 1573、 15 74、 1575、 1576、 1577、 1578、 1579、 1580、 1581、 1582、 1583、 1584、 1585、 1586、 1587、 1588、 1589、 1590又は 1 591に記載されたいずれかの発光素子。
項 1593. セラミック材料を主成分とする焼結体に窒化ガリウム、 窒化インジウム、 窒化 アルミニウムのうちから選ばれた少なくとも 1種以上を主成分とする薄膜からなる少なくとも N型半導体層及び発光層及び P型半導体層カ墳層されている発光軒であって、 該 N型半導体 層及び発光層及び P型半 本層のうちから選ばれた少なくともいずれかの層が単一層であるこ とを特徴とする項 1188、 1189、 1190、 1191、 1192、 1193、 1194、 1195、 1196、 1197、 1198、 1199、 1200、 1201、 1202、 12 03、 1204、 1205、 1206、 1207、 1208、 1209、 1210、 1211、 1212、 1213、 1214、 1215、 1216、 1217、 1218、 1219、 12 20、 1221、 1222、 1223、 1224、 1225、 1226、 1227、 1228、 1229、 1230、 1231、 1232、 1233、 1234、 1235、 1236、 12 37、 1238、 1239、 1240、 1241、 1242、 1243、 1244、 1245、 1246、 1247、 1248、 1249、 1250、 1251、 1252、 1253、 12 54、 1255、 1256、 1257、 1258、 1259、 1260、 1261、 1262、 1263、 1264、 1265、 1266、 1267、 1268、 1269、 1270、 12 71、 1272、 1273、 1274, 1275、 1276、 1277、 1278、 1279、 1280、 1281、 1282、 1283、 1284, 1285、 1286、 1287、 12 88、 1289、 1290、 1291、 1292、 1293、 1294、 1295、 1296、 1297、 1298、 1299、 1300、 1301、 1302、 1303、 1304、 13 05、 1306、 1307、 1308、 1309、 1310、 1311、 1312、 1313、 1314、 1315、 1316、 1317、 1318、 1319、 1320、 1321、 13 22、 1323、 1324、 1325、 1326、 1327、 1328、 1329、 1330、 1331、 1332、 1333、 1334、 1335、 1336、 1337、 1338、 13 39、 1340、 1341、 1342、 1343、 1344、 1345、 1346、 1347、 1348、 1349、 1350、 1351、 1352、 1353、 1354、 1355、 13 56、 1357、 1358、 1359、 1360、 1361、 1362、 1363、 1364、 1365、 1366、 1367、 1368、 1369、 1370、 1371、 1372、 13 73、 1374、 1375、 1376、 1377、 1378、 1379、 1380、 1381、 1382、 1383、 1384、 1385、 1386、 1387、 1388、 1389、 13 90、 1391、 1392、 1393、 1394、 1395、 1396、 1397、 1398、 1399、 1400、 1401、 1402、 1403、 1404、 1405、 1406、 14 07、 1408、 1409、 1410、 1411、 1412、 1413、 1414、 1415、 1416、 1417、 1418、 1419、 1420、 1421、 1422、 1423、 14 24、 1425、 1426、 1427、 1428、 1429、 1430、 1431、 1432、 1433、 1434、 1435、 1436、 1437、 1438、 1439、 1440、 14 41、 1442、 1443、 1444、 1445、 1446、 1447、 1448、 1449、 1450、 1451、 1452、 1453、 1454、 1455、 1456、 1457、 14 58、 1459、 1460、 1461、 1462、 1463、 1464、 1465、 1466、 1467、 1468、 1469、 1470、 1471、 1472、 1473、 1474、 14 75、 1476、 1477、 1478、 1479、 1480、 1481、 1482、 1483、
1484、 1485、 1486、 1487、 1488、 1489、 1490、 1491、 14 92、 1493、 1494、 1495、 1496、 1497、 1498、 1499、 1500、 1501、 1502、 1503、 1504, 1505、 1506、 1507、 1508、 15 09、 1510、 1511、 1512、 1513、 1514、 1515、 1516、 1517、 1518、 1519、 1520、 1521、 1522、 1523、 1524、 1525、 15 26、 1527、 1528、 1529、 1530、 1531、 1532、 1533、 1534、 1535、 1536、 1537、 1538、 1539、 1540、 1541、 1542、 15 43、 1544、 1545、 1546、 1547、 1548、 1549、 1550、 1551、 1552、 1553、 1554, 1555、 1556、 1557、 1558、 1559、 15 60、 1561、 1562、 1563、 1564、 1565、 1566、 1567、 1568、 1569、 1570、 1571、 1572、 1573、 1574、 1575、 1576、 15 77、 1578、 1579、 1580、 1581、 1582、 1583、 1584、 1585、 1586、 1587、 1588、 1589、 1590、 1591又は 1592に記載されたい ずれかの発光素子。
項 1594. セラミック材料を主成分とする焼結体に窒化ガリウム、 窒化インジウム、 窒化 アルミニウムのうちから選ばれた少なくとも 1種以上を主成分とする薄膜からなる少なくとも N型半導体層及び発光層及び P型半導体層が 層されている発光素子であって、 該 N型半導体 層及び発光層及び P型半導体層のうちから選ばれた少なくともいずれかの層が少なくとも 2以 上の層からなることを特徴とする項 1188、 1189、 1190、 1191、 1192、 1 193、 1194、 1195、 1196、 1197、 1198、 1199、 1200、 120 1、 1202、 1203、 1204、 1205、 1206、 1207、 1208、 1209、 1210、 1211、 1212、 1213、 1214、 1215、 1216、 1217、 12 18、 1219、 1220、 1221、 1222、 1223、 1224、 1225、 1226、 1227、 1228、 1229、 1230、 1231、 1232、 1233、 1234、 12 35、 1236、 1237、 1238、 1239、 1240、 1241、 1242、 1243、 1244、 1245、 1246、 1247、 1248、 1249、 1250、 1251、 12 52、 1253、 1254、 1255、 1256、 1257、 1258、 1259、 1260、 1261、 1262、 1263、 1264、 1265、 1266、 1267、 1268、 12 69、 1270、 1271、 1272、 1273、 1274、 1275、 1276、 1277、 1278、 1279、 1280、 1281、 1282、 1283、 1284、 1285、 12 86、 1287、 1288、 1289、 1290、 1291、 1292、 1293、 1294, 1295、 1296、 1297、 1298、 1299、 1300、 1301、 1302、 13 03、 1304、 1305、 1306、 1307、 1308、 1309、 1310、 1311、 1312、 1313、 1314、 1315、 1316、 1317、 1318、 1319、 13 20、 1321、 1322、 1323、 1324、 1325、 1326、 1327、 1328、 1329、 1330、 1331、 1332、 1333、 1334、 1335、 1336、 13 37、 1338、 1339、 1340、 1341、 1342、 1343、 1344、 1345、 1346、 1347、 1348、 1349、 1350、 1351、 1352、 1353、 13 54、 1355、 1356、 1357、 1358、 1359、 1360、 1361、 1362、 1363、 1364、 1365、 1366、 1367、 1368、 1369、 1370、 13 71、 1372、 1373、 1374, 1375、 1376、 1377、 1378、 1379、 1380、 1381、 1382、 1383、 1384、 1385、 1386、 1387、 13 88、 1389、 1390、 1391、 1392、 1393、 1394、 1395、 1396、 1397、 1398、 1399、 1400、 1401、 1402、 1403、 1404、 14
05、 1406、 1407、 1408、 1409、 1410、 1411、 1412、 1413、 141 , 1415、 1416、 1417、 1418、 1419、 1420、 1421、 14 22、 1423、 1424、 1425、 1426、 1427、 1428、 1429、 1430、 1431、 1432、 1433、 1434、 1435、 1436、 1437、 1438、 14 39、 1440、 1441、 1442、 1443、 1444、 1445、 1446、 1447、 1448、 1449、 1450、 1451、 1452、 1453、 1454、 1455、 14 56、 1457、 1458、 1459、 1460、 1461、 1462、 1463、 1464、 1465、 1466、 1467、 1468、 1469、 1470、 1471、 1472、 14 73、 1474、 1475、 1476、 1477、 1478、 1479、 1480、 1481、 1482、 1483、 1484、 1485、 1486、 1487、 1488、 1489、 14 90、 1491、 1492、 1493、 1494、 1495、 1496、 1497、 1498、
1499、 1500、 1501、 1502、 1503、 1504、 1505、 1506、 15
07、 1508、 1509、 1510、 1511、 1512、 1513、 1514、 1515、 1516、 1517、 1518、 1519、 1520、 1521、 1522、 1523、 15
24、 1525、 1526、 1527、 1528、 1529、 1530、 1531、 1532、 1533、 1534、 1535、 1536、 1537、 1538、 1539、 1540、 15 41、 1542、 1543、 1544、 1545、 1546、 1547、 1548、 1549、 1550、 1551、 1552、 1553、 1554、 1555、 1556、 1557、 15 58、 1559、 1560、 1561、 1562、 1563、 1564、 1565、 1566、 1567、 1568、 1569、 1570、 1571、 1572、 1573、 1574、 15 75、 1576、 1577、 1578、 1579、 1580、 1581、 1582、 1583、 1584, 1585、 1586、 1587、 1588、 1589、 1590、 1591、 15 92又は 1593に記載されたいずれかの発光素子。
項 1595. N型半導体層及び発光層及び P型半導体層のうちから選ばれた少なくともいず れかの層が窒化ガリウム、 窒化インジウム、 窒化アルミニウムのうちから選ばれた少なくとも 1種以上を主成分とするェピタキシャル成長した単結晶薄膜からなることを特徴とする項 15 93又は 1594に記載されたいずれかの発光素子。
項 1596. セラミック材料を主成分とする焼結体に窒化ガリウム、 窒化インジウム、 窒化 アルミニウムのうちから選ばれた少なくとも 1種以上を主成分とする薄膜からなる少なくとも N型半導体層及び発光層及び P型半導体層が 層されている発光素子であって、 該 N型半導体 層及び発光層及び P型半導体層の積層体とセラミック材料を主成分とする焼結体との間に窒化 ガリウム、 窒化インジウム、 窒化アルミニウムのうちから選ばれた少なくとも 1種以上を主成 分とする薄膜によりバッファ層が形成されていることを特徴とする項 1188、 1189、 1 190、 1191、 1192、 1193、 1194、 1195、 1196、 1197、 119
8、 1199、 1200、 1201、 1202、 1203、 1204、 1205、 1206、 1207、 1208、 1209、 1210、 1211、 1212、 1213、 1214、 12 15、 1216、 1217、 1218、 1219、 1220、 1221、 1222、 1223、 1224、 1225、 1226、 1227、 1228、 1229、 1230、 1231、 12 32、 1233、 1234、 1235、 1236、 1237、 1238、 1239、 1240、 1241、 1242、 1243、 1244、 1245、 1246、 1247、 1248、 12 49、 1250、 1251、 1252、 1253、 1254、 1255、 1256、 1257、 1258、 1259、 1260、 1261、 1262、 1263、 1264、 1265、 12 66、 1267、 1268、 1269、 1270、 1271、 1272、 1273、 1274、 1275、 1276、 1277、 1278、 1279、 1280、 1281、 1282、 12
83、 1284、 1285、 1286、 1287、 1288、 1289、 1290、 1291、 1292、 1293、 1294, 1295、 1296、 1297、 1298、 1299、 13 00、 1301、 1302、 1303、 1304、 1305、 1306、 1307、 1308、 1309、 1310、 1311、 1312、 1313、 1314、 1315、 1316、 13 17、 1318、 1319、 1320、 1321、 1322、 1323、 1324、 1325、 1326、 1327、 1328、 1329、 1330、 1331、 1332、 1333、 13 34、 1335、 1336、 1337、 1338、 1339、 1340、 1341、 1342、 1343、 1344、 1345、 1346、 1347、 1348、 1349、 1350、 13 51、 1352、 1353、 1354、 1355、 1356、 1357、 1358、 1359、 1360、 1361、 1362、 1363、 1364、 1365、 1366、 1367、 13 68、 1369、 1370、 1371、 1372、 1373、 1374、 1375、 1376、 1377、 1378、 1379、 1380、 1381、 1382、 1383、 1384、 13 85、 1386、 1387、 1388、 1389、 1390、 1391、 1392、 1393、 1394、 1395、 1396、 1397、 1398、 1399、 1400、 1401、 14 02、 1403、 1404、 1405、 1406、 1407、 1408、 1409、 1410、 1411、 1412、 1413、 1414、 1415、 1416、 1417、 1418、 14 19、 1420、 1421、 1422、 1423、 1424、 1425、 1426、 1427、 1428、 1429、 1430、 1431、 1432、 1433、 1434、 1435、 14 36、 1437、 1438、 1439、 1440、 1441、 1442、 1443、 1444、 1445、 1446、 1447、 1448、 1449、 1450、 1451、 1452、 14 53、 1454、 1455、 1456、 1457、 1458、 1459、 1460、 1461、 1462、 1463、 1464、 1465、 1466、 1467、 1468、 1469、 14 70、 1471、 1472、 1473、 1474、 1475、 1476、 1477、 1478、 1479、 1480、 1481、 1482、 1483、 1484、 1485、 1486、 14 87、 1488、 1489、 1490、 1491、 1492、 1493、 1494、 1495、 1496、 1497、 1498、 1499、 1500、 1501、 1502、 1503、 15 04、 1505、 1506、 1507、 1508、 1509、 1510、 1511、 1512、 1513、 1514、 1515、 1516、 1517、 1518、 1519、 1520、 15 21、 1522、 1523、 1524、 1525、 1526、 1527、 1528、 1529、 1530、 1531、 1532、 1533、 1534, 1535、 1536、 1537、 15 38、 1539、 1540、 1541、 1542、 1543、 1544、 1545、 1546、 1547、 1548、 1549、 1550、 1551、 1552、 1553、 1554、 15 55、 1556、 1557、 1558、 1559、 1560、 1561、 1562、 1563、 1564、 1565、 1566、 1567、 1568、 1569、 1570、 1571、 15 72、 1573、 1574、 1575、 1576、 1577、 1578、 1579、 1580、 1581、 1582、 1583、 1584、 1585、 1586、 1587、 1588、 15 89、 1590、 1591、 1592、 1593、 1594又は 1595に記載されたいずれ かの発光素子。
項 1597. バッファ層が単結晶、 配向性多結晶、 多結晶、 無定形のうちから選ばれる少な くともいずれかの結晶状態を有する薄膜からなることを特徴とする項 1596に記載された発 光素子。
項 1598. ノ ソファ層が 向性多結晶、 多結晶、 無定形のうちから選ばれる少なくともい ずれかの結晶状態を有する薄膜からなることを! Mとする項 1596又は 1597に記載され たいずれかの発光素子。
項 1 5 9 9. バッファ層が無定形薄膜からなることを 毁とする項 1 5 9 6、 1 5 9 7又は 1 5 9 8に記載されたいずれかの発光素子。
項 1 6 0 0. 窒化アルミニウムを主成分とする焼結体に形成された窒化ガリウム、 窒化イン ジゥム、 窒化アルミニウムのうちから選ばれた少なくとも 1種以上を主成分とする単結晶薄膜 からなることを特徴とするフィーレドエミッション材料。
項 1 6 0 1. 窒化アルミニウムを主成分とする焼結体に形成された窒化ガリウム、 窒化イン ジゥム、 窒化アルミニウムのうちから選ばれた少なくとも 1種以上を主成分とする N型に半導 体化された単結晶薄膜からなることを特徴とする項 1 6 0 0に記載されたフィールドエミッシ 3ン材料。
項 1 6 0 2. 窒化ガリウム、 窒化インジウム、 窒化アルミニウムのうちから選ばれた少なく とも 1種以上を主成分とする単結晶薄膜がさらに珪素を含むものであることを特徴とする項 1 6 0 0又は 1 6 0 1に記載されたいずれかのフィールドェミッション材料。
元来本発明はセラミック材料を主成分とする焼結体に窒化ガリウム、 窒化インジウム、 窒化 アルミニウムのうちから選ばれた少なくとも 1種以上を主成分とする単結晶薄膜が形成し得る ことを見出すことによりなされたものである。 またこのようなセラミック材料を主成分とする 焼結体には窒化ガリウム、 窒化インジウム、 窒化アルミニウムのうちから選ばれた少なくとも 1種以上を主成分とする単結晶以外の例えば無定形、 多結晶、 配向異性多結晶のうちから選ば れた少なくともいずれかの結晶状態を有する薄膜が形成し得る。 本発明においては単結晶以外 の各種結晶状態の薄膜を形成するための基板も提供し得る。 以下それらについて説明する。 項 1 6 0 3. 窒化ガリウム、 窒化インジウム、 窒化アルミニウムのうちから選ばれた少なく とも 1種以上を主成分とする薄膜を形成するための基板であって、 該基板がセラミック材料を 主成分とする焼結体からなることを特徴とする薄膜形成用基板。
項 1 6 0 4. セラミック材料を主成分とする焼結体からなる薄膜形成用基板に形成される窒 化ガリウム、 窒化インジウム、 窒化アルミニウムのうちから選ばれた少なくとも 1種以上を主 成分とする薄膜が無定形、 多結晶、 配向性多結晶、 単結晶のうちから選ばれる少なくともいず れかの結晶状態を有することを特徴とする項 1 6 0 3に記載された薄膜形成用基板。
項 1 6 0 5. セラミック材料を主成分とする焼結体からなる薄膜形成用基板に形成される窒 化ガリウム、 窒化インジウム、 窒化アルミニウムのうちから選ばれた少なくとも 1種以上を主 成分とする薄膜の少なくとも一部が単結晶であることを特徴とする項 1 6 0 3又は 1 6 0 4に 記載されたいずれかの薄膜形成用基板。
項 1 6 0 6. セラミック材料を主成分とする焼結体からなる薄膜形成用基板に形成される窒 ィ匕ガリウム、 窒化インジウム、 窒化アルミニウムのうちから選ばれた少なくとも 1種以上を主 成分とする薄膜のすべてが単結晶であることを特徴とする項 1 6 0 3、 1 6 0 4又は 1 6 0 5 に記載されたいずれかの薄膜形成用基板。
項 1 6 0 7. セラミック材料を主成分とする焼結体が基板状であることを特徴とする項 1 6 0 3、 1 6 0 4、 1 6 0 5又は 1 6 0 6に記載されたいずれかの薄膜形成用基板。
項 1 6 0 8. セラミック材料が金属元素及び半金属元素のうちから選ばれた少なくとも 1種 以上の元素と非金属元素のうちから選ばれた少なくとも 1種以上の元素との組成物、 あるいは 金属元素のうちから選ばれた少なくとも 1種以上の元素と半金属元素のうちから選ばれた少な くとも 1種以上の元素との組成物、 あるいは半金属元素のうちから選ばれた少なくともいずれ か 2種以上の元素との組成物であることを特徴とする項 1 6 0 3、 1 6 0 4、 1 6 0 5、 1 6 0 6又は 1 6 0 7に記載されたいずれかの薄膜形成用基板。
項 1 6 0 9. 半金属元素が 素、 炭素、珪素、 ゲルマニウム、 ヒ素、 アンチモン、 ビスマス、 セレン、 テルル、 ポロニウムのうちから選ばれた少なくとも 1種以上であることを销敷とする
項 1608に記載された薄膜形成用基板。
項 1610. 半金属元素が炭素、 珪素のうちから選ばれた少なくとも 1種以上であることを 特徴とする項 1606に記載された薄膜形成用基板。
項 1611. 非金属元素が窒素、 りん、 酸素、 硫黄、 フッ素、 塩素、 難、 沃素、 ァス夕チ ンのうちから選ばれた少なくとも 1種以上であることを特徴とする項 1608、 1609又は 1610に記載されたいずれかの薄膜形成用基板。
項 1612. 非金属元素が窒素、 酸素のうちから選ばれた少なくとも 1種以上であることを 特徴とする項 1611に記載された薄膜形成用基板。
項 1613. セラミック材料が窒化物、 炭化物、 酸化物、 硼化物、 及び 化物のうちから選 ばれた少なくともいずれかであることを特徴とする項 1603、 1604、 1605、 160 6、 1607、 1608、 1609、 1610、 1611又は 1612に記載されたいずれか の薄膜形成用基板。
項 1614. セラミック材料が窒化物、 炭化物、 及び 化物のうちから選ばれた少なくとも いずれかであることを特徴とする項 1613に記載された薄膜形成用基板。
項 1615. セラミック材料が窒化アルミニウム、 六方晶系又は三方晶系のうちから選ばれ た少なくともいずれかの結晶構造を有する材料、 酸化ジルコニウム、 酸化マグネシウム、 アル ミン酸マグネシウム、酸化チタン、チタン酸バリウム、チタン酸ジルコン職、希土謙化物、 酸ィ匕トリウム、 各種フェライト、 ムライト、 フォルステライト、 ステア夕イト、 及び結晶化ガ ラスのうちから選ばれた少なくとも 1種以上であることを特徴とする項 1603、 1604、 1605、 1606、 1607、 1608、 1609、 1610、 1611、 1612、 16 13又は 1614に記載されたいずれかの薄膜形成用基板。
項 1616. 六方晶系又は三方晶系のうちから選ばれた少なくともいずれかの結晶構造を有 する材料が 化亜鉛、 酸化ベリリウム、 酸化アルミニウム、 炭化珪素、 窒化珪素、 及び窒化ガ リウムのうちから選ばれた少なくとも 1種以上であることを特徴とする項 1615に記載され た薄膜形成用基板。
項 1617. セラミック材料が窒化アルミニウム、 酸化亜鉛、 酸化ベリリウム、 酸化アルミ 二ゥム、 炭化珪素、 窒化珪素、 窒化ガリウム、 酸化ジルコニウム、 酸化マグネシウム、 アルミ ン酸マグネシウム、 及び酸化ィットリゥムのうちから選ばれた少なくともいずれかであること を ^とする項 1603、 1604、 1605、 1606、 1607、 1608、 1609、
1610、 1611、 1612、 1613、 1614、 1615又は 1616に記載されたい ずれかの薄膜形成用基板。
項 1618. セラミック材料を主成分とする焼結体が窒化アルミニウムを主成分とする焼結 体であることを霞とする項 1603、 1604、 1605、 1606、 1607、 1608、 1609、 1610、 1611、 1612、 1613、 1614、 1615、 1616又は 1 617に記載されたいずれかの薄膜形成用基板。
項 1619. セラミック材料を主成分とする焼結体が六方晶系又 方晶系のうちから選ば れた少なくともいずれかの結晶構造を有する材料を主成分とする焼結体であることを特徴とす る項 1603、 1604、 1605、 1606、 1607、 1608、 1609、 1610、
1611、 1612、 1613、 1614、 1615、 1616又は 1617に記載されたい ずれかの薄膜形成用基板。
項 1620. 六方晶系又は三方晶系のうちから選ばれた少なくともいずれかの結晶構造を有 する材料を主成分とする焼結体力壞化菌、 酸化ベリリウム、 酸化アルミニウム、 炭化珪素、 窒化珪素、 及び窒化ガリウムのうちから選ばれた少なくとも 1種以上を主成分とする焼結体で あることを特徴とする項 1619に記載された薄膜形成用基板。
項 1621.セラミック材料を主成分とする羅体力獺化ジルコニウム、酸化マグネシウム、 アルミン酸マグネシウム、 酸化チタン、 チタン酸バリウム、 チタン酸ジルコン 、 希土鍵 化物、 酸ィ匕トリウム、 各種フェライト、 ムライト、 フォルステライト、 ステア夕イト、 及び結 晶化ガラスのうちから選ばれた少なくとも 1種以上を主成分とする焼結体であることを特徴と する項 1603、 1604、 1605、 1606、 1607、 1608、 1609、 1610、 1611、 1612、 1613、 1614、 1615、 1616又は 1617に記載されたい ずれかの薄膜形成用基板。
項 1622. セラミック材料を主成分とする焼結体が窒化アルミニウム、 酸化亜鉛、 酸化べ リリウム、 酸化アルミニウム、 炭化珪素、 窒化珪素、 窒化ガリウム、 酸化ジルコニウム、 酸化 マグネシウム、 ァリレミン酸マグネシウム、 酸化チタン、 チタン酸バリウム、 チタン酸ジルコン 酸鉛、 希土 «化物、 酸ィ匕トリウム、 各種フェライト、 ムライト、 フォルステライト、 ステア タイト、 及び結晶化ガラスのうちから選ばれた少なくとも 1種以上を主成分とする焼結体であ ることを特徴とする項 1603、 1604、 1605、 1606、 1607、 1608、 16 09、 1610、 1611、 1612、 1613、 1614、 1615、 1616、 1617、 1618、 1619、 1620又は 1621に記載されたいずれかの薄膜形成用基板。
項 1623. セラミック材料を主成分とする焼結体が光透過性を有することを特徴とする項 1603、 1604、 1605、 1606、 1607、 1608、 1609、 1610、 16 11、 1612、 1613、 1614、 1615、 1616、 1617、 1618、 1619、 1620、 1621又は 1622に記載されたいずれかの薄膜形成用基板。
項 1624. セラミツク材料を主成分とする焼結体が光透過率 1 %以上のものであることを 特徴とする項 1603、 1604、 1605、 1606、 1607、 1608、 1609、 1 610、 1611、 1612、 1613、 1614、 1615、 1616、 1617、 161 8、 1619、 1620、 1621、 1622又は 1623に記載されたいずれかの薄膜形成 用基板。
項 1625. セラミツク材料を主成分とする焼結体が光 ¾i 率 5 %以上のものであることを 特徴とする項 1624に記載された薄膜形成用基板。
項 1626. セラミック材料を主成分とする焼結体が光 Mil率 1 Q%以上のものであること を特徴とする項 1624又は 1625に記載されたいずれかの薄膜形成用基板。
項 1627. セラミック材料を主成分とする焼結体が光透過率 20 %以上のものであること を特徴とする項 1624、 1625又は 1626に記載されたいずれかの薄膜形成用基板。 項 1628. セラミック材料を主成分とする焼結体が光 M 率 30%以上のものであること を特徴とする項 1624、 1625、 1626又は 1627に記載されたいずれかの薄膜形成 用基板。
項 1629. セラミツク材料を主成分とする焼結体が ¾¾i率 40 %以上のものであること を特徴とする項 1624、 1625、 1626、 1627又は 1628に記載されたいずれか の薄膜形成用基板。
項 1630. セラミツク材料を主成分とする焼結体が 率 50 %以上のものであること を赚とする項 1624、 1625、 1626、 1627、 1628又は 1629に記載され たいずれかの薄膜形成用基板。
項 1631. セラミツク材料を主成分とする焼結体力 率 60 %以上のものであること を特徴とする項 1624、 1625、 1626、 1627、 1628、 1629又は 1630 に記載されたいずれかの薄膜形成用基板。
項 1632. セラミツク材料を主成分とする焼結体力 率 80 %以上のものであること を特徴とする項 1624、 1625、 1626、 1627、 1628、 1629、 1630又
は 1631に記載されたいずれかの薄膜形成用基板。
項 1633. セラミツク材料を主成分とする焼結体力 άΜϋ率 85 %以上のものであること を特徴とする項 1624、 1625、 1626、 1627、 1628、 1629、 1630、 1631又は 1632に記載されたいずれかの薄膜形成用基板。
項 1634. セラミック材料を主成分とする焼結体が 率 1 %未満のものであることを 特徴とする項 1603、 1604、 1605、 1606、 1607、 1608、 1609、 1 610、 1611、 1612、 1613、 1614、 1615、 1616、 1617、 161
8、 1619、 1620、 1621、 1622又は 1623に記載されたいずれかの薄膜形成 用基板。
項 1635. セラミック材料を主成分とする 体が光透過率 0 %のものであることを 教 とする項 1634に記載された薄膜形成用基板。
項 1636. 性あるいは 率が少なくとも波長 200 nm〜800 nmの範囲の 光に対してのものであることを特徴とする項 1623、 1624、 1625、 1626、 16 27、 1628、 1629、 1630、 1631、 1632、 1633、 1634又は 163 5に記載されたいずれかの薄膜形成用基板。
項 1637. セラミック材料を主成分とする焼結体の平均表面粗さが R a 2000 nm以下 であることを特徴とする項 1603、 1604、 1605、 1606、 1607、 1608、 1609、 1610、 1611、 1612、 1613、 1614、 1615、 1616、 16 17、 1618、 1619、 1620、 1621、 1622、 1623、 1624、 1625、 1626, 1627、 1628、 1629、 1630、 1631、 1632、 1633、 16 34、 1635又は 1636に記載されたいずれかの薄膜形成用基板。
項 1638. セラミック材料を主成分とする焼結体の平均表面粗さが R a 1000腿以下 であることを特徴とする項 1637に記載された薄膜形成用基板。
項 1639. セラミック材料を主成分とする焼結体の平均表面粗さが R a 100 nm以下で あることを特徴とする項 1637又は 1638に記載されたいずれかの薄膜形成用基板。 項 1640. セラミック材料を主成分とする焼結体の平均表面粗さが R a 20 nm以下であ ることを體とする項 1637、 1638又は 1639に記載されたいずれかの薄膜形成用基 板。
項 1641. セラミック材料を主成分とする焼結体の平均表面粗さが R a 10 nm以下であ ることを特徴とする項 1637、 1638、 1639又は 1640に記載されたいずれかの薄 膜形成用基板。
項 1642. セラミック材料を主成分とする焼結体の平均表面粗さが R a 5 nm以下である ことを特徴とする項 1637、 1638、 1639、 1640又は 1641に載されたいずれ かの薄膜形成用基板。
項 1643. セラミック材料を主成分とする焼結体が表面粗さの大きいものであることを特 徴とする項 1603、 1604、 1605、 1606、 1607、 1608、 1609、 16 10、 1611、 1612、 1613、 1614、 1615、 1616、 1617、 1618、 1619、 1620、 1621、 1622、 1623、 1624、 1625、 1626、 16 27、 1628、 1629、 1630、 1631、 1632、 1633、 1634、 1635、 1636、 1637、 1638又は 1639に記載されたいずれかの薄膜形成用基板。
項 1644. セラミツク材料を主成分とする焼結体の平均表面粗さが R a 70 nm以上であ ることを特徴とする項 1603、 1604、 1605、 1606、 1607、 1608、 16
09、 1610、 1611、 1612、 1613、 1614、 1615、 1616、 1617、 1618、 1619、 1620、 1621、 1622、 1623、 1624、 1625、 16
26、 1627、 1628、 1629、 1630、 1631、 1632、 1633、 1634、 1635、 1636、 1637、 1638、 1639又は 1643に記載されたいずれかの薄 膜形成用基板。
項 1645. セラミック材料を主成分とする焼結体の平均表面粗さが R a 1000 nmより 大きいことを特徴とする項 1644に記載された薄膜形成用基板。
項 1646. セラミツク材料を主成分とする焼結体の平均表面粗さが R a 2000 nmより 大きいことを特徴とする項 1644又は 1645に記載されたいずれかの薄膜形成用基板。 項 1647. セラミック材料を主成分とする焼結体の表面が焼き放し (a s— ί i r e)、 ラ ッフif磨、 ブラスト研磨、 鏡面研磨、 化学腐食及びプラズマガスによる腐食のうちから選ばれ た少なくともいずれかの状態であることを特徴とする項 1603、 1604、 1605、 16 06、 1607、 1608、 1609、 1610、 1611、 1612、 1613、 1614、 1615、 1616、 1617、 1618、 1619、 1620、 1621、 1622、 16 23、 1624、 1625、 1626、 1627、 1628、 1629、 1630、 1631、 1632、 1633、 1634、 1635、 1636、 1637、 1638、 1639、 16 40、 1641、 1642、 1643、 1644、 1645又 ½:1646に記載されたいずれ かの薄膜形成用基板。
項 1648. セラミツク材料を主成分とする焼結体の表面が鏡面研磨された状態であること を特徴とする項 1647に記載された薄膜形成用基板。
項 1649. セラミック材料を主成分とする焼結体力 ,^^!性を有しかつ表面粗さの大きい ものであることを特徴とする項 1603、 1604、 1605、 1606、 1607、 160 8、 1609、 1610、 1611、 1612、 1613、 1614、 1615、 1616、 1617、 1618、 1619、 1620、 1621、 1622、 1623、 1624, 16 25、 1626、 1627、 1628、 1629、 1630、 1631、 1632、 1633、 1634、 1635、 1636、 1637、 1638、 1639、 1643、 1644、 16 45又は 1646に記載されたいずれかの薄膜形成用基板。
項 1650. セラミック材料を主成分とする焼結体が導電性を有することを特徴とする項 1 603、 1604、 1605、 1606、 1607、 1608、 1609、 1610、 161 1、 1612、 1613、 1614、 1615、 1616、 1617、 1618、 1619、 1620、 1621、 1622、 1623、 1624、 1625、 1626、 1627、 16 28、 1629、 1630、 1631、 1632、 1633、 1634、 1635、 1636、 1637、 1638、 1639、 1640、 1641、 1642、 1643、 1644、 16 45、 1646、 1647、 1648又は 1649に記載されたいずれかの薄]»成用基板。 項 1651. セラミック材料を主成分とする焼結体が室温において 1 X 104Ω · cm以下の 抵抗率を有することを特徴とする項 1603、 1604、 1605、 1606、 1607、 1 608、 1609、 1610、 1611、 1612、 1613、 1614、 1615、 161 6、 1617、 1618、 1619、 1620、 1621、 1622、 1623、 1624、 1625、 1626、 1627、 1628、 1629、 1630、 1631、 1632、 16 33、 1634、 1635、 1636、 1637、 1638、 1639、 1640、 1641、 1642、 1643、 1644、 1645、 1646、 1647、 1648、 1649又は 1 650に記載されたいずれかの薄膜形成用基板。
項 1652. セラミック材料を主成分とする 結体が室温において 1 X 102Ω · cm以下の 抵抗率を有することを特徴とする項 1651に記載された薄膜形成用基板。
項 1653. セラミック材料を主成分とする焼結体が室温において 1 X 10ΧΩ - cm以下の 抵ぉ率を有することを特徴とする項 1651又は 1652に記載されたいずれかの薄膜形成用
項 1654. セラミツク材料を主成分とする焼結体が室温において 1 X 100 Ω · c m以下の 抵抗率を有することを特徴とする項 1651、 1652又は 1653に記載されたいずれかの 薄膜形成用基板。
項 1655. セラミック材料を主成分とする焼結体が室温において 1 X 1 · cm以下 の抵抗率を有することを特徴とする項 1651、 1652、 1653又は 1654に記載され たいずれかの薄膜形成用基板。
項 1656. セラミック材料を主成分とする焼結体が室温において 1 X 10— 2Ω · cm以下 の抵抗率を有することを體とする項 1651、 1652、 1653、 1654又は 1655 に記載されたいずれかの薄膜形成用基板。
項 1657. セラミック材料を主成分とする焼結体が ¾¾M性を有しかつ導電性を有するこ とを特徴とする項 1603、 1604、 1605、 1606、 1607、 1608、 1609、 1610、 1611、 1612、 1613、 1614、 1615、 1616、 1617、 16 18、 1619、 1620、 1621、 1622、 1623、 1624, 1625、 1626、 1627、 1628、 1629、 1630、 1631、 1632、 1633、 1634、 16 35、 1636、 1637、 1638、 1639、 1640、 1641、 1642、 1643、 1644、 1645、 1646、 1647、 1648、 1649、 1650、 1651、 16 52、 1653、 1654、 1655又は 1656に記載されたいずれかの薄膜形成用基板。 項 1658. セラミック材料を主成分とする焼結体が光 性及び導電性を有しさらに表面 粗さの大きいものであることを特徴とする項 1603、 1604、 1605、 1606、 16 07、 1608、 1609、 1610、 1611、 1612、 1613、 1614、 1615、 1616、 1617、 1618、 1619、 1620、 1621、 1622、 1623、 16 24、 1625、 1626、 1627、 1628、 1629、 1630、 1631、 1632、 1633、 1634、 1635、 1636、 1637、 1638、 1639、 1643、 16 44、 1645、 1646、 1647、 1648、 1649、 1650、 1651、 1652、 1653、 1654、 1655、 1656又は 1657に記載されたいずれかの薄膜形成用基 板。
項 1659. セラミック材料を主成分とする焼結体が窒化ガリウム、 窒化インジウム、 窒化 アルミニウムのうちから選ばれた少なくとも 1種以上を主成分とする薄膜を形成したものであ ることを赚とする項 1603、 1604、 1605、 1606、 1607、 1608、 16 09、 1610、 1611、 1612、 1613、 1614、 1615、 1616、 1617、 1618、 1619、 1620、 1621、 1622、 1623、 1624、 1625、 16 26、 1627、 1628、 1629、 1630、 1631、 1632、 1633、 1634, 1635、 1636、 1637、 1638、 1639、 1640、 1641、 1642、 16 43、 1644、 1645、 1646、 1647、 1648、 1649、 1650、 1651、 1652、 1653、 1654、 1655、 1656、 1657又は 1658に記載されたい ずれかの薄膜形成用基板。
項 1660. セラミック材料を主成分とする焼結体に形成された窒化ガリウム、 窒化インジ ゥム、窒化アルミニウムのうちから選ばれた少なくとも 1種以上を主成分とする薄膜が単結晶、 無定形、 多結晶、 配向性多結晶のうちから選ばれる少なくともいずれかの結晶状態を有するこ とを特徴とする項 1659に記載された薄膜形成用基板。
項 1661. セラミック材料を主成分とする焼結体に形成された窒化ガリウム、 窒化インジ ゥム、 窒化アルミニウムのうちから選ばれた少なくとも 1種以上を主成分とする薄膜の少なく とも一部が単結晶からなることを特徴とする項 1659又は 1660に記載されたいずれかの
薄膜形成用基板。
項 1662. セラミック材料を主成分とする焼結体に形成された窒化ガリウム、 窒化インジ ゥム、 窒化アルミニウムのうちから選ばれた少なくとも 1種以上を主成分とする薄膜が単結晶 だけからなることを特徴とする項 1659、 1660又は 1661に記載されたいずれかの薄 膜形成用基板。
項 1663. セラミック材料を主成分とする焼結体に形成された窒化ガリウム、 窒化インジ ゥム、 窒化アルミニウムのうちから選ばれた少なくとも 1種以上を主成分とする薄膜が単一層 であることを特徴とする項 1659、 1660、 1661又は 1662に記載されたいずれか の薄膜形成用基板。
項 1664. セラミック材料を主成分とする焼結体に形成された窒化ガリゥム、 窒化インジ ゥム、 窒化アルミニウムのうちから選ばれた少なくとも 1種以上を主成分とする薄膜が少なく とも 2以上の層から構成されていることを特徴とする項 1659、 1660、 1661又は1 662に記載されたいずれかの薄膜形成用基板。
項 1665. 少なくとも 2以上の層から構成されている薄膜の各層がそれぞ; W結晶、 配向 性多結晶、 多結晶、 無定形の中から選ばれた少なくともいずれかの結晶状態を有することを特 徵とする項 1664に記載された薄膜形成用基板。
項 1666. 少なくとも 2以上の層から構成されている薄膜においてセラミック材料を主成 分とする焼結体に直接形成されている窒化ガリウム、 窒化インジウム、 窒化アルミニウムのう ちから選ばれた少なくとも 1種以上を主成分とする薄膜が無定形、 多結晶、 配向性多結晶、 単 結晶のうちから選ばれる少なくともいずれかの結晶状態を有することを i¾とする項 1664 又は 1665に記載されたいずれかの薄膜形成用基板。
項 1667. セラミック材料を主成分とする焼結体に直接形成されている窒化ガリゥム、 窒 化インジウム、 窒化アルミニウムのうちから選ばれた少なくとも 1種以上を主成分とする薄膜 が無定形であることを特徴とする項 1660、 1661、 1662、 1663、 1664、 1 65又は 1666に記載されたいずれかの薄膜形成用基板。
項 1668. セラミック材料を主成分とする焼結体に直接形成されている窒化ガリウム、 窒 化インジウム、 窒化アルミニウムのうちから選ばれた少なくとも 1種以上を主成分とする薄膜 が多結晶であることを特徴とする項 1660、 1661、 1662、 1663、 1664、 1 65又は 1666に記載されたいずれかの薄膜形成用基板。
項 1669. セラミック材料を主成分とする焼結体に直接形成されている窒化ガリウム、 窒 化ィンジゥム、 窒化アルミニゥムのうちから選ばれた少なくとも 1種以上を主成分とする薄膜 が ¾己向性多結晶であることを特徴とする項 1660、 1661、 1662、 1663、 166 4、 165又は 1666に記載されたいずれかの薄膜形成用基板。
項 1670. セラミック材料を主成分とする焼結体に直接形成されている窒化ガリウム、 窒 化インジウム、 窒化アルミニウムのうちから選ばれた少なくとも 1種以上を主成分とする薄膜 が単結晶であることを特徴とする項 1660、 1661、 1662、 1663、 1664、 1 65又は 1666に記載されたいずれかの薄膜形成用基板。
項 1671. 少なくとも 2以上の層から構成されている薄膜においてセラミック材料を主成 分とする焼結体に窒化ガリウム、 窒化インジウム、 窒化アルミニウムのうちから選ばれた少な くとも 1種以上を主成分とする単結晶、 配向性多結晶、 多結晶、 無定形のうちから選ばれる少 なくともいずれかの結晶状態を有する薄膜が少なくとも 1層以上形成され、 さらにその上に窒 化ガリウム、 窒化インジウム、 窒化アルミニウムのうちから選ばれた少なくとも 1種以上を主 成分とする単結晶、 配向性多結晶、 多結晶、 無定形のうちから選ばれる少なくともいずれかの 結晶状態を有する薄膜が少なくとも 1層以上形成されていることを特徴とする項 1664、 1
665、 1666、 1667、 1668、 1669又は 1670に記載されたいずれかの薄膜 形成用基板。
項 1672. 少なくとも 2以上の層から構成されている薄膜においてセラミック材料を主成 分とする焼結体に窒化ガリウム、 窒化インジウム、 窒化アルミニウムのうちから選ばれた少な くとも 1種以上を主成分とする単結晶、 配向性多結晶、 多結晶、 無定形のうちから選ばれる少 なくともいずれかの結晶状態を有する薄膜が少なくとも 1層以上形成され、 さらにその上に窒 化ガリウム、 窒化インジウム、 窒化アルミニウムのうちから選ばれた少なくとも 1種以上を主 成分とする単結晶薄膜が少なくとも 1層以上形成されていることを特徴とする項 1671に記 載されたいずれかの薄膜形成用基板。
項 1673. 少なくとも 2以上の層から構成されている薄膜においてセラミック材料を主成 分とする焼結体に窒化ガリウム、 窒化インジウム、 窒化アルミニウムのうちから選ばれた少な くとも 1種以上を主成分とする配向性多結晶、 多結晶、 無定形のうちから選ばれる少なくとも いずれかの結晶状態を有する薄膜が少なくとも 1層以上形成され、 さらにその上に窒化ガリゥ ム、 窒化インジウム、 窒化アルミニウムのうちから選ばれた少なくとも 1種以上を主成分とす る単結晶薄膜が少なくとも 1層以上形成されていることを特徴とする項 1672に記載された 薄膜形成用基板。
項 1674. 少なくとも 2以上の層から構成されている薄膜においてセラミック材料を主成 分とする焼結体に窒化ガリウム、 窒化インジウム、 窒化アルミニウムのうちから選ばれた少な くとも 1種以上を主成分とする無定形薄膜が少なくとも 1層以上形成され、 さらにその上に窒 化ガリウム、 窒化インジウム、 窒化アルミニウムのうちから選ばれた少なくとも 1種以上を主 成分とする単結晶薄膜が少なくとも 1層以上形成されていることを特徴とする項 1672又は 1673に記載されたいずれかの薄膜形成用基板。
項 1675. 少なくとも 2以上の層から構成されている薄膜においてセラミック材料を主成 分とする焼結体に窒化ガリウム、 窒化インジウム、 窒化アルミニウムのうちから選ばれた少な くとも 1種以上を主成分とする多結晶薄膜が少なくとも 1層以上形成され、 さらにその上に窒 化ガリウム、 窒化インジウム、 窒化アルミニウムのうちから選ばれた少なくとも 1種以上を主 成分とする単結晶薄膜が少なくとも 1層以上形成されていることを特徴とする項 1672又は 1673に記載されたいずれかの薄膜形成用基板。
項 1676. 少なくとも 2以上の層から構成されている薄膜においてセラミック材料を主成 分とする焼結体に窒化ガリウム、 窒化インジウム、 窒化アルミニウムのうちから選ばれた少な くとも 1種以上を主成分とする配向性多結晶薄膜が少なくとも 1層以上形成され、 さらにその 上に窒化ガリウム、 窒化インジウム、 窒化アルミニウムのうちから選ばれた少なくとも 1種以 上を主成分とする単結晶薄膜が少なくとも 1層以上形成されていることを特徴とする項 167 2又は 1673に記載されたいずれかの薄膜形成用基板。
項 1677. 少なくとも 2以上の層から構成されている薄膜においてすベての層が単結晶だ けから構成されていることを特徴とする項 1664、 1665、 1666、 1667、 166 8、 1669、 1670、 1671、 1672、 1673、 1674、 1675又は 1676 に記載されたいずれかの薄膜形成用基板。
項 1678. セラミック材料を主成分とする焼結体に形成された窒化ガリウム、 窒化インジ ゥム、 窒化アルミニウムのうちから選ばれた少なくとも 1種以上を主成分とする薄膜の最上層 は単結晶薄膜であることを とする項 1660、 1661、 1662、 1663、 1664、 1665、 1666、 1667、 1668、 1669、 1670、 1671、 1672、 16 73、 1674、 1675、 1676又は 1677に記載されたいずれかの薄膜形成用基板。 項 1679. セラミック材料を主成分とする焼結体に形成された窒化ガリウム、 窒化インジ
ゥム、 窒化アルミニウムのうちから選ばれた少なくとも 1種以上を主成分とする単結晶薄膜の c軸がセラミック材料を主成分とする焼結体面に対して垂直な方向に形成されていることを特 徵とする項 1660、 1661、 1662、 1663、 1664、 1665、 1666、 16 67、 1668、 1669、 1670、 1671、 1672、 1673、 1674、 1675、 1676、 1677又は 1678に記載されたいずれかの薄膜形成用基板。
項 1680. セラミック材料を主成分とする焼結体に形成された窒化ガリウム、 窒化インジ ゥム、 窒化アルミニウムのうちから選ばれた少なくとも 1種以上を主成分とする単結晶薄膜の C軸がセラミック材料を主成分とする焼結体面に対して水平な方向に形成されていることを特 徴とする項 1660、 1661、 1662、 1663、 1664、 1665、 1666、 16 67、 1668、 1669、 1670、 1671、 1672、 1673、 1674、 1675、 1676、 1677又は 1678に記載されたいずれかの薄膜形成用基板。
項 1681. セラミック材料を主成分とする焼結体に形成された窒化ガリウム、 窒化インジ ゥム、 窒化アルミニウムのうちから選ばれた少なくとも 1種以上を主成分とする配向性多結晶 薄膜の C軸がセラミック材料を主成分とする焼結体面に対して垂直な方向に形成されているこ とを特徴とする項 1660、 1661、 1662、 1663、 1664、 1665、 1666、 1667、 1668、 1669、 1670、 1671、 1672、 1673、 1674, 16 75、 1676、 1677又は 1678に記載されたいずれかの薄膜形成用基板。
項 1682. セラミック材料を主成分とする焼結体に形成された窒化ガリウム、 窒化インジ ゥム、 窒化アルミニウムのうちから選ばれた少なくとも 1種以上を主成分とする配向性多結晶 薄膜の C軸がセラミツク材料を主成分とする焼結体面に対して水平な方向に形成されているこ とを とする項 1660、 1661、 1662、 1663、 1664、 1665、 1666、 1667、 1668、 1669、 1670、 1671、 1672、 1673、 1674、 16 75、 1676、 1677又は 1678に記載されたいずれかの薄膜形成用基板。
項 1683. セラミック材料を主成分とする焼結体に形成された窒化ガリウム、 窒化インジ ゥム、 窒化アルミニウムのうちから選ばれた少なくとも 1種以上を主成分とする薄膜が導電性 を有することを とする項 1659、 1660、 1661、 1662、 1663、 1664、 1665、 1666、 1667、 1668、 1669、 1670、 1671、 1672、 16 73、 1674, 1675、 1676、 1677、 1678、 1679、 1680、 1681 又は 1682に記載されたいずれかの薄膜形成用基板。
項 1684. セラミック材料を主成分とする焼結体に形成された窒化ガリウム、 窒化インジ ゥム、 窒化アルミニウムのうちから選ばれた少なくとも 1種以上を主成分とする薄膜の室温に おける抵抗率が 1 X 104Ω · cm以下であることを特徴とする項 1659、 1660、 166 1、 1662、 1663、 1664、 1665、 1666、 1667、 1668、 1669、 1670、 1671、 1672、 167.3、 1674、 1675、 1676、 1677、 16
78、 1679、 1680、 1681、 1682又は 1683に記載されたいずれかの薄膜形 成用基板。
項 1685. セラミック材料を主成分とする焼結体に形成された窒化ガリウム、 窒化インジ ゥム、 窒化アルミニウムのうちから選ばれた少なくとも 1種以上を主成分とする薄膜の室温に おける抵抗率が 1 X 102Ω · cm以下であることを特徴とする項 1683又は 1684に記載 されたいずれかの薄膜形成用基板。
項 1686. セラミック材料を主成分とする焼結体に形成された窒化ガリウム、 窒化インジ ゥム、 窒化アルミニウムのうちから選ばれた少なくとも 1種以上を主成分とする薄膜の室温に おける抵抗率が 1 X 10ΧΩ · cm以下であることを特徴とする項 1683、 1684又は 16
85に記載されたいずれかの薄膜形成用基板。
項 1687. セラミック材料を主成分とする焼結体に形成された窒化ガリウム、 窒化インジ ゥム、 窒化アルミニウムのうちから選ばれた少なくとも 1種以上を主成分とする薄膜の室温に おける抵抗率が 1 X 10°Ω · cm以下であることを ^とする項 1683、 1684、 168 5又は 1686に記載されたいずれかの薄膜形成用基板。
項 1688. セラミック材料を主成分とする焼結体に形成された薄膜が少なくとも窒化ガリ ゥムを含有するものであることを體とする項 1659、 1660、 1661、 1662、 1 663、 1664、 1665、 1666、 1667、 1668、 1669、 1670、 167 1、 1672、 1673、 1674、 1675、 1676、 1677、 1678、 1679、 1680、 1681、 1682、 1683、 1684、 1685、 1686又は 1687に記 載されたいずれかの薄膜形成用基板。
項 1689. セラミック材料を主成分とする焼結体に形成された薄膜が少なくとも窒化ガリ ゥムを含むかあるいは窒化ガリウムを主成分とする薄膜を有することを特徴とする項 1659、 1660、 1661、 1662、 1663、 1664、 1665、 1666、 1667、 16 68、 1669、 1670、 1671、 1672、 1673、 1674, 1675、 1676、 1677、 1678、 1679、 1680、 1681、 1682、 1683、 1684, 16 85、 1686、 1687又は 1688に記載されたいずれかの薄膜形成用基板。
項 1690. セラミック材料を主成分とする焼結体に形成された薄膜が窒化ガリウムを主成 分とするものであることを特徴とする項 1688又は 1689に記載されたいずれかの薄膜形 成用基板。
項 1691. セラミック材料を主成分とする焼結体に形成された薄膜が A 1 xGay I ι^— x_ yN (0<y≤l) で表わされる組成を有することを特徴とする項 1688、 1689又は 16 90に記載されたいずれかの薄膜形成用基板。
項 1692. セラミック材料を主成分とする焼結体に形成された薄膜が窒化ガリウムを 50 モル%以上含むを特徴とする項 1688、 1689、 1690又は 1691に記載されたいず れかの薄膜形成用基板。
項 1693. セラミック材料を主成分とする焼結体に形成された少なくとも窒化ガリウムを 含むかあるいは窒化ガリウムを主成分とする薄膜が無定形、 多結晶、 配向性多結晶、 単結晶の うちから選ばれた少なくともいずれかの結晶状態であることを特徴とする項 1688、 168 9、 1690、 1691又は 1692に記載されたいずれかの薄膜形成用基板。
項 1694. セラミック材料を主成分とする焼結体に形成された少なくとも窒化ガリウムを 含むかあるいは窒化ガリウムを主成分とする薄膜が単結晶であることを特徴とする項 1693 に記載された薄膜形成用基板。
項 1695. セラミック材料を主成分とする焼結体に形成された薄膜の最上層が少なくとも 窒化ガリゥムを含むかあるいは窒化ガリゥムを主成分とするものであることを特徴とする項 1 688、 1689、 1690、 1691、 1692、 1693又は 1694に記載されたいず れかの薄膜形成用基板。
項 1696. セラミック材料を主成分とする焼結体に形成された薄膜の最上層が少なくとも 窒化ガリゥムを含むかあるいは窒化ガリゥムを主成分とする単結晶であることを特徴とする項 1695に記載された薄膜形成用基板。
項 1697. セラミック材料を主成分とする焼結体に形成された薄膜が A 1 xGa1--xN (0 ≤x≤l. 0) の化学式であらわされる組成物を主成分とするものであることを特徴とする項 1659、 1660、 1661、 1662、 1663、 1664、 1665、 1666、 16 67、 1668、 1669、 1670、 1671、 1672、 1673、 1674、 1675、 1676、 1677、 1678、 1679、 1680、 1681、 1682、 1683、 16
84、 1685、 1686、 1687、 1688、 1689、 1690、 1691、 1692、 1693、 1694、 1695又は 1696に記載されたいずれかの薄膜形成用基板。
項 1698. セラミック材料を主成分とする焼結体に形成された窒化ガリウム、 窒化インジ ゥム、 窒化アルミニウムのうちから選ばれた少なくとも 1種以上を主成分とする薄膜が少なく とも単結晶薄膜層を有し該単結晶薄膜層の厚みが 300 xm未満であることを [とする項 1 659、 1660、 1661、 1662、 1663、 1664, 1665、 1666、 166 7、 1668、 1669、 1670、 1671、 1672、 1673、 1674, 1675、 1676、 1677、 1678、 1679、 1680、 1681、 1682、 1683、 16 84、 1685、 1686、 1687、 1688、 1689、 1690、 1691、 1692、 1693、 1694、 1695、 1696又は 1697に記載されたいずれかの薄膜形成用基 板。
項 1699. セラミック材料を主成分とする焼結体に形成された窒化ガリウム、 窒化インジ ゥム、 窒化アルミニウムのうちから選ばれた少なくとも 1種以上を主成分とする薄膜が少なく とも単結晶薄膜層を有し該単結晶薄膜層の厚みが 200 m以下であることを i¾とする項 1 698に記載された薄膜形成用基板。
項 1700. セラミック材料を主成分とする焼結体に形成された薄膜が少なくとも In m以上の厚みを有することを特徴とする項 1659、 1660、 1661、 1662、 166 3、 1664、 1665、 1666、 1667、 1668、 1669、 1670、 1671、 1672、 1673、 1674、 1675、 1676、 1677、 1678、 1679、 16 80、 1681、 1682、 1683、 1684、 1685、 1686、 1687、 1688、 1689、 1690、 1691、 1692、 1693、 1694、 1695、 1696、 16 97、 1698又は 1699に記載されたいずれかの薄膜形成用基板。
項 1701. セラミック材料を主成分とする焼結体に形成された薄膜が少なくとも 0 · 5 n m以上の厚みを有することを特徴とする項 1700に記載された薄膜形成用基板。
項 1702. セラミック材料を主成分とする焼結体に形成された薄膜が少なくとも 0. 3 m以上の厚みを有することを特徴とする項 1700又は 1701に記載されたいずれかの薄膜 形成用基板。
項 1703. セラミック材料を主成分とする焼結体に形成された薄膜が少なくとも 3. 5 m以上の厚みを有することを特徴とする項 1700、 1701又は 1702に記載されたいず れかの薄膜形成用基板。
項 1704. セラミック材料を主成分とする焼結体に形成された薄膜が少なくとも 10 m 以上の厚みを有することを特徴とする項 1700、 1701、 1702又は 1703に記載さ れたいずれかの薄膜形成用基板。
項 1705. セラミック材料を主成分とする焼結体に形成された薄膜が少なくとも 50 urn 以上の厚みを有することを特徴とする項 1700、 1701、 1702、 1703又は 170 4に記載されたいずれかの薄膜形成用基板。
項 1706. セラミック材料を主成分とする焼結体に形成された窒化ガリウム、 窒化インジ ゥム、 窒化アルミニウムのうちから選ばれた少なくとも 1種以上を主成分とする薄膜の厚みが 100 O zm以下であることを特徴とする項 1659、 1660、 1661、 1662、 16 63、 1664、 1665、 1666、 1667、 1668、 1669、 1670、 1671、 1672、 1673、 1674、 1675、 1676、 1677、 1678、 1679、 16 80、 1681、 1682、 1683、 1684、 1685、 1686、 1687、 1688、 1689、 1690、 1691、 1692、 1693、 1694、 1695、 1696、 16 97、 1698、 1699、 項 1700.、 1701、 1702、 1703、 1704又は 17
05に記載されたいずれかの薄膜形成用基板。
項 1707. セラミック材料を主成分とする焼結体に形成された薄膜の厚みが 500 m以 下であることを特徴とする項 1706に記載された薄膜形成用基板。
項 1708. セラミック材料を主成分とする焼結体に形成された薄膜が単結晶、 無定形、 多 結晶、 配向性多結晶のうちから選ばれた少なくともいずれか 2以上の結晶状態が同時に混在し ているものからなることを [とする項 1659、 1660、 1661、 1662、 1663、
1664, 1665、 1666、 1667、 1668、 1669、 1670、 1671、 16
72、 1673、 1674、 1675、 1676、 1677、 1678、 1679、 1680、 1681、 1682、 1683、 1684、 1685、 1686、 1687、 1688、 16
89、 1690、 1691、 1692、 1693、 1694、 1695、 1696、 1697、 1698、 1699、 1700、 1701、 1702、 1703、 1704、 1705、 17
06又は 1707に記載されたいずれかの薄膜形成用基板。
項 1709. セラミック材料を主成分とする焼結体に形成された薄膜が単一層あるいは少な くとも 2以上の層からなり、 該薄膜の少なくとも 1以上の層が単結晶、 無定形、 多結晶、 配向 性多結晶のうちから選ばれた少なくともいずれか 2以上の結晶状態が同時に混在しているもの からなることを M [とする項 1659、 1660、 1661、 1662、 1663、 1664、
1665、 1666、 1667、 1668、 1669、 1670、 1671、 1672、 16
73、 1674、 1675、 1676、 1677、 1678、 1679、 1680、 1681、 1682、 1683、 1684、 1685、 1686、 1687、 1688、 1689、 16
90、 1691、 1692、 1693、 1694、 1695、 1696、 1697、 1698、 1699、 1700、 1701、 1702、 1703、 1704、 1705、 1706、 17
07又は 1708に記載されたいずれかの薄膜形成用基板。
項 1710. セラミック材料を主成分とする焼結体に形成された窒化ガリウム、 窒化インジ ゥム、 窒化アルミニウムのうちから選ばれた少なくとも 1種以上を主成分とする単結晶薄膜の ミラ一指数 (002) の格子面の X線回折ロッキングカーブの半値幅が 3600秒以下である ことを特徵とする項 1659、 1660、 1661、 1662、 1663、 1664、 166 5、 1666、 1667、 1668、 1669、 1670、 1671、 1672、 1673、
1674, 1675、 1676、 1677、 1678、 1679、 1680、 1681、 16 82、 1683、 1684、 1685、 1686、 1687、 1688、 1689、 1690、 1691、 1692、 1693、 1694、 1695、 1696、 1697、 1698、 16 99、 1700、 1701、 1702、 1703、 1704、 1705、 1706、 1707、 1708又は 1709に記載されたいずれかの薄膜形成用基板。
項 1711. セラミック材料を主成分とする焼結体に形成された窒化ガリウム、 室化インジ ゥム、 窒化アルミニウムのうちから選ばれた少なくとも 1種以上を主成分とする単結晶薄膜の ミラ一指数 (002) の格子面の X線回折ロッキングカーブの半値幅が 300秒以下であるこ とを特徴とする項 1710に記載された薄膜形成用基板。
項 1712. セラミック材料を主成分とする焼結体に形成された窒化ガリウム、 窒化インジ ゥム、 窒化アルミニウムのうちから選ばれた少なくとも 1種以上を主成分とする単結晶薄膜の ミラー指数 (002) の格子面の X線回折ロッキングカーブの半値幅が 240秒以下であるこ とを特徴とする項 1710又は 1711に記載されたいずれかの薄膜形成用基板。
項 1713. セラミック材料を主成分とする焼結体に形成された窒化ガリウム、 窒化インジ ゥム、 窒化アルミニウムのうちから選ばれた少なくとも 1種以上を主成分とする単結晶薄膜の ミラー指数 (002) の格子面の X線回折ロッキングカーブの半値幅が 200秒以下であるこ とを特徴とする項 1710、 1711又は 1712に記載されたいずれかの薄膜形成用基板。
項 1714. セラミック材料を主成分とする焼結体に形成された窒化ガリウム、 窒化インジ ゥム、 窒化アルミニウムのうちから選ばれた少なくとも 1種以上を主成分とする単結晶薄膜の ミラ一指数 (002) の格子面の X線回折ロッキングカーブの半値幅が 150秒以下であるこ とを特徴とする項 1710、 1711、 1712又は 1713に記載されたいずれかの薄膜形 成用基板。
項 1715. セラミック材料を主成分とする焼結体に形成された窒化ガリウム、 窒化インジ ゥム、 窒化アルミニウムのうちから選ばれた少なくとも 1種以上を主成分とする単結晶薄膜の ミラー指数 (002) の格子面の X線回折ロッキング力一ブの半値幅が 130秒以下であるこ とを特徴とする項 1710、 1711、 1712、 1713又は 1714に記載されたいずれ かの薄膜形成用基板。
項 1716. セラミック材料を主成分とする焼結体に形成された窒化ガリゥム、 窒化インジ ゥム、 窒化アルミニウムのうちから選ばれた少なくとも 1種以上を主成分とする単結晶薄膜の ミラ一指数 (002) の格子面の X線回折ロッキングカーブの半値幅が 100秒以下であるこ とを特徴とする項 1710、 1711、 1712、 1713、 1714又は 1715に記載さ れたいずれかの薄膜形成用基板。
項 1717. セラミック材料を主成分とする焼結体が窒化ガリウム、 窒化インジウム、 窒化 アルミニウムのうちから選ばれた少なくとも 1種以上を主成分とする単結晶薄膜を形成したも のであることを とする項 1659、 1660、 1661、 1662、 1663、 1664、 1665、 1666、 1667、 1668、 1669、 1670、 1671、 1672、 16 73、 1674, 1675、 1676、 1677、 1678、 1679、 1680、 1681、 1682、 1683、 1684, 1685、 1686、 1687、 1688、 1689、 16 90、 1691、 1692、 1693、 1694、 1695、 1696、 1697、 1698、 1699、 1700、 1701、 1702、 1703、 1704、 1705、 1706、 17 07、 1708、 1709、 1710、 1711、 1712、 1713、 1714又は 1 Ί 1 5に記載されたいずれかの薄膜形成用基板。
また、 上記項 1〜項 70で示された本発明による薄膜形成用基板に用いられるセラミック材 料を主成分とする焼結体及び光 性を有するセラミック材料を主成分とする焼結体つレゝてよ り詳細に説明する。
項 1718. セラミック材料を主成分とする焼結体が窒化アルミニウムを主成分とする能結 体であることを とする項 1、 2、 3、 4、 5、 6、 7、 8、 9、 10、 11、 12、 13、 14、 15、 16、 17、 18、 19、 20、 21、 22、 23、 24、 25、 26、 27、 57、 58、 59、 60、 61、 62、 63、 64、 65、 66、 67、 68又は 70に記載 されたいずれかの薄膜形成用基板。
項 1719. セラミック材料を主成分とする焼結体が六方晶系又は三方晶系のうちから選ば れた少なくともいずれかの結晶構造を有するセラミック材料を主成分とする焼結体であること を難とする項 1、 2、 3、 4、 5、 6、 7、 8、 9、 10、 11、 12、 13、 14、 15、 16、 17、 18、 19、 20、 21、 22、 23、 24、 25、 26、 27、 57、 58、 59、 60、 61、 62、 63、 64、 65、 66、 67、 68、 69又は 70に記載された いずれかの薄膜形成用基板。
項 1720. 六方晶系又は三方晶系のうちから選ばれた少なくともいずれかの結晶構造を有 するセラミック材料を主成分とする焼結体力雙化 »、、 酸化ベリリウム、 酸化アルミニウム、 炭化珪素、 窒化珪素、 窒化ガリウムのうちから選ばれた少なくとも 1種以上を主成分とする焼 結体であることを特徴とする項 1719に記載された薄膜形成用基板。
項 1721.セラミック材料を 分とする^;結体力 化ジルコニウム、酸化マグネシウム、
アルミン酸マグネシウム、 酸化チタン、 チタン酸バリウム、 チタン酸ジルコン酸鉛、 希土 ¾ 素酸化物、 酸化トリウム、 各種フェライト、 ムライト、 フォルステライト、 ステア夕イト、 結 晶ィ匕ガラスのうちから選ばれた少なくとも 1種以上を主成分とする焼結体であることを特徴と する項 1、 2、 3、 4、 5、 6、 7、 8、 9、 10、 11、 12、 13、 14、 15、 16、 17、 18、 19、 20、 21、 22、 23、 24、 25、 26、 27、 57、 58、 59、
60、 61、 62、 63、 64、 65、 66、 67、 68又は 70に記載されたいずれかの薄 膜形成用基板。
項 1722. セラミック材料を主成分とする焼結体が窒化アルミニウム、 酸化亜鉛、 酸化べ リリウム、 酸化アルミニウム、 炭化珪素、 窒化珪素、 窒化ガリウム、 酸化ジルコニウム、 酸ィ匕 マグネシウム、 アルミン酸マグネシウム、 酸化イットリウムのうちから選ばれた少なくとも 1 種以上を主成分とする焼結体であることを特徴とする項 1718、 1719、 1720又は 1
721に記載されたいずれかの薄膜形成用基板。
項 1723. ¾¾性を有するセラミック材料を主成分とする焼結体が窒化アルミニウムを 主成分とする焼結体であることを特徴とする項 28、 29、 30、 31、 32、 33、 34、 35、 36、 37、 38、 39、 40、 41、 42、 43、 44、 45、 46、 47、 48、 49、 50、 51、 52、 53、 54、 55、 56、 57、 58、 59、 60、 61、 62、 63、 64、 65、 66、 67、 68又は 70に記載されたいずれかの薄膜形成用基板。 項 1724. セラミック材料を主成分とする焼結体が六方晶系又 方晶系のうちから選ば れた少なくともいずれかの結晶構造を有するセラミック材料を主成分とする焼結体であること を とする項 28、 29、 30、 31、 32、 33、 34、 35、 36、 37、 38、 39、 40、 41、 42、 43、 44、 45、 46、 47、 48、 49、 50、 51、 52、 53、 54、 55、 56、 57、 58、 59、 60、 61、 62、 63、 64、 65、 66、 67、 68、 69又は 70に記載されたいずれかの薄膜形成用基板。
項 1725. 六方晶系又は三方晶系のうちから選ばれた少なくともいずれかの結晶構造を有 するセラミック材料を主成分とする焼結体力職化 »、 酸化ベリリウム、 酸化アルミニウム、 炭化珪素、 窒化珪素、 窒化ガリウムのうちから選ばれた少なくとも 1種以上を主成分とする焼 結体であることを特徴とする項 1 Ί 24に記載された薄膜形成用基板。
項 1726. ¾¾ϋ性を有するセラミック材料を主成分とする焼結体が ¾化ジルコニウム、 酸化マグネシウム、 アルミン酸マグネシウム、 酸化チタン、 チタン酸バリウム、 チタン酸ジル コン隱、希土類 素酸ィ匕物、酸化トリウム、各種フェライト、 ムライト、 フオレステライト、 ステアタイト、 結晶化ガラスのうちから選ばれた少なくとも 1種以上を主成分とする焼結体で あることを特徴とする項 28、 29、 30、 31、 32、 33、 34、 35、 36、 37、 3 8、 39、 40、 41、 42、 43、 44、 45、 46、 47、 48、 49、 50、 51、 5 2、 53、 54、 55、 56、 57、 58、 59、 60、 61、 62、 63、 64、 65、 6 6、 67、 68又は 70に記載されたいずれかの薄膜形成用基板。
項 1727. 性を有するセラミック材料を主成分とする焼結体が窒化アルミニウム、 酸化亜鉛、 酸化ベリリウム、 酸化アルミニウム、 炭化珪素、 窒化珪素、 窒化ガリウム、 酸化ジ ルコニゥム、 酸化マグネシウム、 アルミン酸マグネシウム、 酸化イットリウムのうちから選ば れた少なくとも 1種以上を主成分とする焼結体であることを 1数とする項 1723、 1724、 1725又は 1726に記載されたいずれかの薄膜形成用基板。
また本発明は、 上記項 1〜項 409、 及び 1603〜項 1717に記載された本発明によ る薄膜形成用基板として、 「窒化ガリウム、 窒化インジウム、 窒化アルミニウムのうちから選ば れた少なくとも 1種以上を主成分とする薄膜を形成するための基板であって、 該基板は窒化ガ リウム、 窒化インジウム、 窒化アルミニウムのうちから選ばれた少なくとも 1種以上を主成分
とする薄膜が形成されたセラミック材料を主成分とする焼結体からなることを特徴とする薄膜 形成用基 ¾、 を提供し得る。 また上記セラミック材料を主成分とする能結体に形成された窒化 ガリウム、 窒化インジウム、 窒化アルミニウムのうちから選ばれた少なくとも 1種以上を主成 分とする薄膜として無定形、 多結晶、 配向性多結晶、 単結晶のうちから選ばれた少なくともい ずれかの結晶状態を有するものを提供し得る。
また上記本発明による薄膜形成用基板は、 「窒化ガリウム、 窒化インジウム、 窒化アルミニゥ ムのうちから選ばれた少なくとも 1種以上を主成分とする薄膜を形成するための基板であって、 該基板は窒化ガリウム、 窒化インジウム、 窒化アルミニウムのうちから選ばれた少なくとも 1 種以上を主成分とする薄膜が形成された光 ¾ 性を有するセラミック材料を主成分とする焼結 体からなることを特徴とする薄 基 、 を含む。 また上記 性を有するセラミック 材料を主成分とする焼結体に形成された窒化ガリウム、 窒化インジウム、 窒化アルミニウムの うちから選ばれた少なくとも 1種以上を主成分とする薄膜として無定形、 多結晶、 配向性多結 晶、 単結晶のうちから選ばれた少なくともいずれかの結晶状態を有するものを提供し得る。 また上記本発明による薄藤成用基板は、 「窒化ガリウム、 窒化インジウム、 窒化アルミニゥ ムのうちから選ばれた少なくとも 1種以上を主成分とする薄膜を形成するための基板であって、 該基板は表面粗さの大きいセラミック材料を主成分とする焼結体からなることを特徴とする薄 膜形成用基板」、 を含む。
また上記本発明による薄膜形成用基板は、 「窒化ガリウム、 窒化インジウム、 窒化アルミニゥ ムのうちから選ばれた少なくとも 1種以上を主成分とする薄膜を形成するための基板であって、 該基板は窒化ガリウム、 窒化インジウム、 窒化アルミニウムのうちから選ばれた少なくとも 1 種以上を主成分とする薄膜が形成された表面粗さの大きいセラミック材料を主成分とする焼結 体からなることを特徴とする薄膨成用基 ¾J、 を含む。 また上記表面粗さの大きいセラミック 材料を主成分とする焼結体に形成された窒化ガリウム、 窒化インジウム、 窒化アルミニウムの うちから選ばれた少なくとも 1種以上を主成分とする薄膜として無定形、 多結晶、 配向性多結 晶、 単結晶のうちから選ばれた少なくともいずれかの結晶状態を有するものを提供し得る。 また上記本発明による薄膜形成用基板は、 「窒化ガリウム、 窒化インジウム、 窒化アルミニゥ ムのうちから選ばれた少なくとも 1種以上を主成分とする薄膜を形成するための基板であって、 該基板は光 ¾i 性を有しかつ表面粗さの大きいセラミック材料を主成分とする焼結体からなる ことを特徴とする薄膜形成用基板」、 を含む。
また上記本発明による薄膜形成用基板は、 「窒化ガリウム、 窒化インジウム、 窒化アルミニゥ ムのうちから選ばれた少なくとも 1種以上を主成分とする薄膜を形成するための基板であって、 該基板は窒化ガリウム、 窒化インジウム、 窒化アルミニウムのうちから選ばれた少なくとも 1 種以上を主成分とする薄膜が形成された光透過性を有しかつ表面粗さの大きいセラミック材料 を主成分とする能結体からなることを特徴とする薄 J»成用基 fc、 を含む。 また上記 ¾¾ 性 を有しかつ表面粗さの大きいセラミック材料を主成分とする焼結体に形成された窒化ガリゥム、 窒化インジウム、 窒化アルミニウムのうちから選ばれた少なくとも 1種以上を主成分とする薄 膜として無定形、 多結晶、 配向 結晶、 単結晶のうちから選ばれた少なくともいずれかの結 晶状態を有するものを提供し得る。
また上記本発明による薄膜形成用基板に用いるセラミック材料を主成分とする焼結体、 ym 過性を有するセラミック材料を主成分とする焼結体及び表面粗さの大きいセラミック材料を主 成分とする焼結体として、 「窒化アルミニウム、 六方晶系又 方晶系のうちから選ばれた少な くともいずれかの結晶構造を有する材料を主成分とする焼結体、 酸化ジルコニウム、 酸化マグ ネシゥム、 アルミン酸マグネシウム、酸化チタン、チタン酸バリウム、チタン酸ジルコン 、 希土靈化物、酸化トリウム、 各種フェライト、ムライト、 フォルステライト、ステア夕イト、
結晶化ガラスのうちから選ばれた少なくとも 1種以上を主成分とする焼結体」、 を含む。
上記六方晶系又は三方晶系のうちから選ばれた少なくともいずれかの結晶構造を有する材料 を主成分とする焼結体としては少なくとも酸化 ffi 酸化ベリリウム、 酸化アルミニウム、 炭 ィ匕珪素、 窒化珪素、 窒化ガリウムのうちから選ばれた少なくとも 1種以上を主成分とする焼結 体が、用い得る。
希土 ¾化物を主成分とする焼結体としては少なくとも酸化ィットリゥムを主成分とする焼 結体が用い得る。
さらに本発明は、 「セラミック材料を主成分とする焼結体に窒化ガリウム、 窒化インジウム、 窒化アルミニウムのうちから選ばれた少なくとも 1種以上を主成分とする薄膜が形成されてい る薄膜基 «J、 を提供し得る。 また上記セラミック材料を主成分とする焼結体に形成されている 窒化ガリウム、 窒化インジウム、 窒化アルミニウムのうちから選ばれた少なくとも 1種以上を 主成分とする薄膜として無定形、 多結晶、 配向性多結晶、 単結晶のうちから選ばれた少なくと もいずれかの結晶状態を有するものを提供し得る。 産業上の利用可能性
本発明により窒化ガリウム、 窒化インジウム、 窒化アルミニウムのうちから選ばれた少なく とも 1種以上を主成分とする単結晶薄膜あるいは各種結晶状態の薄膜が窒化アルミニウムを主 成分とする焼結体からなる基板、 あるいは各種セラミック材料を主成分とする焼結体からなる 基板の上に形成できることが示された。 この単結晶薄膜は発光^?の一部として使用、 あるい は光導波路として使用できる程度の高い結晶性を有する。 このような窒化アルミニウムを主成 分とする焼結体からなる基板あるいは各種セラミック材料を主成分とする焼結体からなる基板、 及び該基板に単結晶薄膜あるいは各種結晶状態の薄膜が形成された薄膜基板は、 いずれの基板 を用いてもその上には窒化ガリウム、 窒化インジウム、 窒化アルミニウムのうちから選ばれた 少なくとも 1種以上を主成分とする窒化物半導体からなる発光^?が作製可能となった。 この 発光 の発光効率は従来からのサファイアなどのバルク状単結晶基板を用いて作製される発 光素子と比較して発光効率が少なくとも同等か、 最大 4〜5倍以上と大きく向上できた。 した がつて« ^困難と考えられていた家庭用の照明などの一般照明に発光^?が用いられる道が実 質的に開かれた。 また、 窒化アルミニウムを主成分とする焼結体からなる基板に形成された窒 化アルミニウムを主成分とする薄膜を用いることにより紫外光を低損失で伝送できる光導波路 が作製できるようになった。 このように本発明による窒化アルミニウムをはじめとする各種セ ラミック材料を主成分とする焼結体からなる基板、 及び該基板に窒化ガリウム、 窒化インジゥ ム、 窒化アルミニウムのうちから選ばれた少なくとも 1種以上を主成分とする単結晶薄膜ある いは各種結晶状態の薄膜が形成された薄膜基板は、 上記のような発光軒あるいは光導波路を はじめその他に薄膜をフィールドエミツション材料として用いたディスプレイ、 表面弹性波素 子、 あるいは回路基板など広範な用途に応用できるので産業上に与える効果は大きい。
また、 本発明による基板を用いて発光素子を製造する場合の効果をまとめるとは次の通りで ある。
1 ) 基板に形成される窒化ガリウム、 窒化インジウム、 窒化アルミニウムのうちから選ばれた 少なくとも 1種以上を主成分とする単結晶薄膜の結晶性が高いため発光素子の発光効率が高ま る。
2 ) 基板に形成される窒化ガリウム、 窒化インジウム、 窒化アルミニウムのうちから選ばれた 少なくとも 1種以上を主成分とする単結晶薄膜の結晶方位を制御できる。
3 ) ¾¾1率の高い基板を用いることができるの発光素子からの光が基板にあまり吸収される ことなく素子外部に効率よく放出でき発光素子の発光効率が向上する。
4) 基板の熱伝導率が高いので発光素子に高い電力が印加でき発光素子の発光出力を高めるこ とができる。
5 ) 基板の熱膨張率が窒化ガリウム、 窒化インジウム、 窒化アルミニウムのうちから選ばれた 少なくとも 1種以上を主成分とする単結晶薄膜と近いので該単結晶薄膜に熱膨張率差による転 位や亀裂などの発生が少なくなり発光素子の発光効率が高まる。
6 ) 基板に上下面を電気的に接続するための導通ビアを設けることができ、 さらに導電性の酸 ィ匕亜鉛を主成分とする焼結体を基板として用いることができるので発光素子の P及び N電極を 素子の片面だけでなく素子の上下面に配置できる。 したがって電極を形成するために素子の一 部をエッチングする必要がなく、 基板を切断するだけでそのまま素子が作製でき製造工程が簡 田 匕される上にエッチング中に生じやすい素子のダメージの恐れが減少する。
7 ) 窒化ガリウム、 窒化インジウム、 窒化アルミニウムのうちから選ばれた少なくとも 1種以 上を主成分とする窒化物半導体からなる発光素子の発光効率が »からのサフアイァなどの単 結晶基板を用いたものと少なくとも同等か、 最大 4〜 5倍以上に向上した上、 基板がセラミツ ク材料を主成分とする焼結体であるためより従来からのサファイアなどの単結晶基板を用いた もの安いコストで製造できる。