-
Die
vorliegende Erfindung bezieht sich auf ein Verfahren zum Herstellen
einer Halbleiterformtafel, die zusammen mit Formmaterial für eine Halbleitervorrichtung
verwendet wird, wobei das Auftreten von internen Hohlräumen in
dem Formharzteil verhindert werden kann, wobei eine Halbleiterformtafel
erhalten wird und eine Halbleitervorrichtung mit einer großen Zuverlässigkeit
im Gebrauch erreicht werden kann.
-
Eine
Halbleitertafel ist aus der
JP
08039549 bekannt. Darin sind unterschiedliche Teilchen
(Partikel)-Größen zu einer
Tafel kombiniert.
-
Aus
der
JP 60257548 ist
ein Herstellungsverfahren zum Bewegen von Material zum Dichten bekannt. Darin
ist die Temperatur ein wichtiger Parameter.
-
Die
JP 597009 offenbart eine
hochdichte Harzpalettendichthalbleiterbaugruppe, die unter Hochdruckvakuum
aus einem Pulvermaterial der Tafel geformt ist.
-
Aus
der deutschen Druckschrift
DE
4414939 A1 ist ein Verfahren zum Verdichten einer geschmolzenen
Mischung einer Epoxidharz-Pulverzusammensetzung offenbart.
-
Die
GB 1065672 offenbart einen
Verdichter für
pulvrige Substanzen.
-
Die
US 6297296 B1 offenbart
einen anorganischen Füller,
eine Epoxyharzzusammensetzung und eine Halbleitervorrichtung.
-
Die
US 5645787 -Druckschrift
offenbart einen Prozess zum Herstellen von Halbleitervorrichtungen
unter Nutzung von Harztafeln.
-
Herkömmlicherweise
werden Pulvermaterialien durch Vermengen und Schmelzkneten eines
Epoxidharzes, eines Phenolharzes und eines anorganischen Füllers oder
etwas Ähnlichem
vorbereitet und dann ausgerollt, gekühlt, wobei das resultierende
Material pulverisiert wird und als Formmaterial für eine Halbieiterelementevorrichtung
wie z. B. ein IC, LSI oder dergleichen verwendet wird. Die Halbleitervorrichtung
kann mit dem Harz, unter direktem Zuführen des auf diese Art erhaltenen
pulvrigen Materials in eine Formmaschine zur Herstellung von Packungen
ausgeformt werden, wobei es jedoch allgemeiner ist, ein Verfahren
zu verwenden, in welchem die Halbleitervorrichtung mit dem Harz
unter Herstellung einer Tafel schon im vorhinein unter Pressen des
Materials in eine notwendige Größe, um das
Ausformen in einer Form gewünschter
Formgebung zu erreichen, und nachfolgendem Einführen desselben in eine Formmaschine
zum Paketausformen gebracht ist.
-
Die
im Vorhinein durch Formpressen hergestellte Tafel wird in diesem
Sinne als Formmaterial verwendet, da Hohlräume zwischen den pulverisierten
Partikeln des Formmaterials komprimiert werden, um in der komprimierten
Formtafel kleiner zu werden, wobei die Menge der so genannten „Luft", die in der Tafel
enthalten ist, dadurch reduziert wird. Dementsprechend, wenn solch
eine Tafel als Formtafel verwendet wird, bleiben so gut wie keine
Hohlräume
im Inneren und auf der Oberfläche
des Pakets nach dem Formen, und die Zuverlässigkeit nach dem Formen und
die Ausbeute des Formschritts werden deutlich erhöht.
-
Da
mittlerweile ein Verdünnen
von Halbleitervorrichtungen voranschreitet, werden in einem solchen dünnen Paket
zwangsläufig
auch die Dicken der Formharzlagen gering (dünn). Das heißt, dass
selbst die Hohlräume,
die bislang keine Probleme bereitet haben, nun erheblichen Anlass
für Probleme
in diesen dünnartigen Paketen
darstellen. Entsprechend besteht ein Bedürfnis nach verbesserten Tafeln
in punkto Dichte, um das Verhältnis
auftretender Hohlräume
zu reduzieren. Es wurde z. B. vorgeschlagen, um die Tafeldichte
zu erhöhen,
eine hochdichte Tafel durch das Regulieren der Füllstrukturen der Partikel mittels
dem Beschränken
der Partikelgrößenverteilung
in dem pulverisierten Material vor dem Herstellen der Tafel zu erreichen
(siehe Ref. 1). Alternativ dazu ist auch ein Verfahren zum Herstellen
eines Epoxyharz-Formmaterials vorgeschlagen worden, in welchem die
Temperatur des aus einer Knetvorrichtung entlassenen Materials näher bestimmt
wird und charakteristische Eigenschaften des Formmaterials durch
Kühlen
und Pulverisieren dieses abgegebenen Materials beschränkt werden
(siehe Ref. 2).
- Referenz 1:
- JP-A-8-39549
- Referenz 2:
- JP-A-2002-220475
-
Die
Abkürzung "JP-A" wird hier verwendet,
um zu kennzeichnen, dass ungeprüfte
japanische Patentanmeldungen gemeint sind.
-
Trotzdem
werden die vorab beschriebenen Effekte nur schwer in den bestehenden
hochdichten Regionen einer Tafel erhalten, so dass die aktuelle
Situation die ist, dass es notwendig war, auf eine hohe Verdichtung
mittels Druckkräfte
zu vertrauen. Als Folge hat das Dichteverhältnis der Tafel bereits das
Niveau von 94 % erreicht, bezogen auf das reale spezifische Gewichtsverhältnis, und
noch höhere
Druckbeaufschlagung führt
zum Herstellen von Verwertungen und zum Zerbrechen des Formapparates,
und es können
auch Probleme bei der Ausbeute pro Zeit während der Herstellung der Tafeln
auftreten, so dass in der vorliegenden Situation die Begrenzungen
bei den Tafelherstellungsapparaten selber liegen.
-
Die
vorliegende Erfindung wurde in Anbetracht der obigen Situation getätigt. Die
vorliegende Erfindung sieht ein Verfahren zum Herstellen einer Halbleitertafel
vor, welche das Auftreten von Hohlräumen im Inneren des Pakets
durch Vergrößerung der
Dichte der Tafel reduziert, wobei dadurch eine Halbleitertormtafel hergestellt
wird und eine Halbleitervorrichtung mit hoher Verlässlichkeit
bei der Nutzung derselben erreicht wird.
-
Um
die vorstehenden Aufgaben zu lösen,
ist das erste Ausführungsbeispiel
der vorliegenden Erfindung ein Verfahren nach Anspruch 1.
-
Das
heißt,
dass die vorliegenden Erfinder eine Vielzahl von Studien durchgeführt haben,
mit dem Ziel, eine Tafel hoher Dichte zu erhalten, die durch die
herkömmlichen
Tafelherstellformapparate limitiert waren. Als Folge wurde herausgefunden,
dass es unmöglich
ist, Tafeln mit noch größerer Dichte
herzustellen, nur unter Komprimieren der abgekühlten und ausgehärteten pulverisierten
Partikel, wodurch die Luft aus dem Pulver entfernt wurde, und zwar
lediglich unter Verwendung herkömmlicher
Unterdrucksetzungsmaßnahmen
zum Zeitpunkt des pulverisierten Materials als eine Harzzusammensetzung
für einen
Halbleiterformling in einer Tafel. Als Folge der weiter durchgeführten Studien,
die auf dem Gefundenen basierten, fanden die Erfinder das Nachfolgende
zum ersten Mal heraus. In Bezug auf ein Formmaterial vor dem Herstellen
der Tafel, kann ein Verfahren, in welchem ein geknetetes und ausgeschüttetes Material,
in welchem die Komponenten der Formel für das vorgenannte Formmaterial
in einem geschmolzenen Stadium sind, in eine Schichtform mit einem
hohen Dichteverhältnis
mittels Rollen gebracht werden, die gerollte Schicht pulverisiert
werden und in eine Tafelform gebracht werden, das die Erfolge erreicht,
dass die Luft in dem Pulver aus dem pulverisierten Material stark entfernt
wird und, was noch bedeutsamer ist, dass die Tafel noch eine höhere Dichte
aufweist, obwohl die Drücke
zum Herstellen geringer werden, wodurch das Verwenden desselben
eine Herstellung einer Halbleitertormtafel, unter Verhinderung von
dem Auftreten von Hohlräumen
in dem Paket wahrscheinlich werden lässt, wenn eine elementare Halbleitervorrichtung
hergestellt wird. Dadurch wird die vorliegende Erfindung erreicht.
-
Nachfolgend
werden bestimmte Ausführungsbeispiele
der Erfindung im Detail beschrieben.
-
Die
Halbleiterformtafel, die entsprechend Anspruch 1 hergestellt ist,
ist unter Nutzung einer Epoxidharzzusammensetzung, die Epoxidharz
(Komponente A), ein Phenolharz (Komponente B) und einen anorganischen
Füller
(Komponente C) als wesentliche Komponenten aufweist, hergestellt,
mittels Kneten und Formen in eine Folienform mit einer spezifischen
Dicke, Pulverisieren dieses Produkts und dann Umformen des pulverisierten
Materials in eine Tafelform durch Tafelformen.
-
Das
vorhergehend genannte Epoxidharz (Komponente A) ist nicht im Besonderen
beschränkt
und herkömmlich
bekannte Epoxidharzsorten können
verwendet werden. Beispiele hiervon umfassen unterschiedliche Arten
(20) von Epoxidharz, wie z. B. der Cresol Novolak-Art, Phenol Novolak-Art,
des Bisphenol A-Typs, des Biphenyl-Typs, des Triphenylmethan-Typs,
des Naphthalin-Typs oder dergleichen. Diese können alleine, zu zweit oder
zu mehreren, in Kombination miteinander verwendet werden.
-
Das
Phenolharz (Komponente B), das zusammen mit dem zuvor genannten
Epoxidharz (Komponente A) verwendet wird, übt einen Effekt als Härtungsmittel
für das
zuvor genannte Epoxidharz aus. Es ist nicht im Besonderen limitiert
und seine Beispiele umfassen herkömmliche bekannte Materialien
wie Phenol Novolak, Cresol Novolak, Bisphenol A-Typ Novolak, Naphthol
Novolak, Phenolaralkylharz und dergleichen. Diese können allein
oder in Kombination miteinander verwendet werden. Kombinationen
von zwei oder mehr Materialien werden möglich.
-
Es
ist wünschenswert,
die zuvor genannten Epoxidharze (Komponente A) und Phenolharze (Komponente
B) mit einem Mischverhältnis
zu mischen, so dass die Hydro xylgruppe äquivalent mit dem Härter wird, mit
einem Verhältnis
von 0,5 bis 2,0, basierend auf einem Element der Epoxidgruppe in
dem Epoxidharz. Noch weiter bevorzugt ist das Verhältnis von
0,8 bis 1,2.
-
Der
anorganische Füller
(Komponente C), der zusammen mit dem zuvor genannten Epoxidharz
(Komponente A) und dem Phenolharz (Komponente B) verwendet wird,
ist nicht besonders limitiert, und herkömmlich bekannte Füller können exemplarisch
verwendet werden, wie z. B. Quarzglaspulver, Talg, Siliziumdioxidpulver
(fusioniertes Silicapulver, kristallines Silicapulver und dergleichen),
Aluminiumoxidpulver, Aluminiumnitridpulver, Siliconnitridpulver
und dergleichen. Auch diese können
allein oder in Kombination miteinander (zwei oder mehr) verwendet
werden. Zwischen diesen ist es wünschenswert,
die zuvor genannten Silicapulver aus dem Gesichtspunkt, dass der
lineare Ausdehnungskoeffizient des erhaltenen Produkts reduziert
werden kann, zu verwenden. Zwischen den zuvor genannten Silicapulvern
ist es im Besonderen wünschenswert,
fusioniertes Silicapulver im Zustand hoher Gepacktheit und hoher
Flüssigkeit
zu verwenden. Wenn die zuvor genannten fusionierten Silicapulver,
sphärische
fusionierte Silicapulver und pulverisierte fusionierte Silicapulver
exemplarisch verwendet werden, ist es wünschenswert, die sphärisch fusionierten
Silicapulver in Anbetracht der Flüssigkeit zu verwenden. Im Besonderen
ist es wünschenswert,
eine durchschnittliche Partikelgröße im Bereich von 10 bis 60 μm zu verwenden,
insbesondere im Bereich von 15 bis 45 μm. In diesem Zusammenhang kann die
zuvor genannte durchschnittliche Partikelgröße z. B. unter Verwendung einer
Laser-Diffraktions-Scatteringmethode in einem Partikelgrößenverteilmessapparat
ermittelt werden.
-
Es
ist ferner wünschenswert,
den Inhalt des zuvor genannten anorganischen Füllers (Komponente C) auf einen
Bereich von 50 bis 95 Gew.-%, vorzugsweise 70 bis 90 Gew.-%, basierend
auf der gesamten Epoxidharzzusammenstellung festzulegen.
-
Entsprechend
der vorgenannten Erfindung können
zusätzlich
zu den bereits genannten Komponenten A bis C weitere Zusatzstoffe
wie Härtungsbeschleuniger,
halogenbasierte Flammhemmer wie z. B. bromiertes Epoxidharz oder
dergleichen enthalten sein, wobei ein Flammhemmassistenzmittel wie
z. B. ein Antimontrioxid oder dergleichen Verwendung finden kann,
wobei ein Pigment wie z. B. Ruß oder
dergleichen Verwendung finden kann, ein Silanverbindungsmittel wie
z. B. ein β-(3,4-Epoxycyclohexyl)ethyltrimethoxysilan, γ-Glycidoxypropyltrimethoxysilan
oder dergleichen Verwendung finden, und als Ablösemittel Karnaubawachs oder
dergleichen Verwendung finden kann, wobei dies alles optionale Zusatzmittel
sind, und auf die jeweiligen Bedürfnisse
eingehen.
-
Der
zuvor genannte Härtbeschleuniger
ist nicht weiter beschränkt.
Beispiele dessen umfassen Imidazole wie z. B. 2-Methylimidazol oder
dergleichen, Triethanolamin, organische Phosphorkomponenten wie
z. B. Tetraphenylphosphonium, Tetraphenylborat, Triphenylphosphin
und dergleichen, Diazabicycloalkin-Komponenten wie z. B. 1,8-Diazabicyclo[5.4.0]undecen-7,
1,5-Diazabicyclo[4.3.0]nonen-5 und dergleichen. Diese Komponenten
können
zusammen oder in Kombination miteinander (zwei oder mehr) verwendet
werden. Zusätzlich
ist es bevorzugt, das Mischverhältnis
dieses Härtbeschleunigers
in einem Verhältnis
von 0,1 bis 1,0 Gew.-%, basierend auf der Gesamtepoxidharzmischung
zu wählen.
-
Die
Halbleitertormtafel, die durch das Verfahren der vorliegenden Erfindung
erhalten ist, ist mit den zuvor genannten Komponenten hergestellt,
und zwar z. B. in der nachfolgenden Art. Das bedeutet, dass die
zuvor genannten jeweiligen Komponenten in einem vorbestimmten Verhältnis gemischt
werden, unter Verwendung eines Mixers oder dergleichen trockenvermengt
werden und dann unter Verwendung eines Doppelschraubenkneters mit
einer Harztemperatur von 90 bis 120°C zusammengeknetet werden. Als
Nächstes
wird das geknetete Material aus dem zuvor genannten Kneter abgelassen,
und zwar in eine Rollform, so dass eine Folienform erreicht wird,
in der Art, dass das Schichtdickenverhältnis 98 % oder mehr beträgt, wobei
dann die genannte Folie luftgekühlt
und pulverisiert wird.
-
Nachfolgend
wird die Halbleiterformtafel durch Formen derselben aus dem erreichten
pulverisierten Material in eine Tafelform unter Verwendung einer
Tafelformmaschine hergestellt, die eine Kompression bis zu einer
vorbestimmten Tafelhöhe
in der Weise durchführt,
dass das gewünschte
Tafeldichteverhältnis
erreicht werden kann.
-
Wie
im Vorhergehenden beschrieben, wird die Rollformfolie in eine Folie
mit einem Dichteverhältnis von
98 % oder mehr geformt. In diesem Fall ist es bevorzugt, die Folie
mittels Rollen mit einer Dicke von 1,0 oder weniger herzustellen.
Konventionelle Folien durch Rollformen haben grundsätzlich eine
Dicke von 2 mm oder mehr, wobei das Schichtdickenverhältnis in
diesem Fall ungefähr
93 bis 97 % beträgt.
Nach der vorlie genden Erfindung wird es möglich, Foliendichteverhältnisse
von 98 bis 99 % zu erhalten, wenn die Foliendicke 1 mm ist, oder
ein Foliendichteverhältnis
von 99 bis 100 % zu erhalten, in dem Fall, dass die Foliendicke
0,7 bis 0,5 mm beträgt.
Es ist weiter bevorzugt, die Schichtdicke auf 0,7 mm oder sogar
weniger in Bezug auf das Foliendichteverhältnis zu wählen. Die untere Grenze der
Folie ist grundsätzlich
0,2 mm. Es wird daher möglich, eine
hochdichte Form, mit einem Foliendichteverhältnis von 98 % oder mehr, zu
erhalten, und zwar mittels Rollens zu einer Folie von 1 mm oder
weniger, weil die Hohlräume,
die im Inneren des gekneteten Materials verteilt sind, von dem Kneter
ausgetrieben werden und die Hohlräume, die durch eingeschlossene
Luftblasen während
des Transfers zu der Rollvorrichtung gebildet sind, effizient unter
Rollen der Folienform in einem geschmolzenen Stadium entfernt werden
können.
-
In
vorstehend beschriebenem Verfahren zum Setzen des Schichtdickenverhältnisses
auf 98 % oder mehr, kann ein Verfahren durch Verbesserung der Knetleistung,
abgebend bei einer hohen Temperatur oder dergleichen, zusätzlich zum
Festlegen der Foliendicke auf 1,0 mm oder weniger beispielhaft erläutert werden. Erläuternde
Beispiele davon umfassen Dekompressieren oder entgasende Behandlung
in einem Kneter, Verlängerung
der Knetzeiten, Erhöhung
der Knettemperatur oder ähnliche
Verfahren.
-
In
diesem Zusammenhang wird das Foliendichteverhältnis wie nachfolgend erläutert gemessen
und berechnet.
-
Das
bedeutet, dass die spezifische Dichte einer Folie bei spezifischen
Dichtemessmethoden (basierend auf JIS K 6911) gemessen wird, in
welchen die spezifische Dichte aufgrund der Masse, wie sie in der
Folie in Luft und in Wasser befindlich vorliegt, errechnet wird,
und wobei das Foliendichteverhältnis über ihr
Verhältnis
mit dem warenspezifischen Gewichtswert des verdichteten Formmaterials
(gehärtetes
Produkt aus der Harzmischung), das in derselben Art erhalten wurde.
Im Weiteren, was lediglich der Erläuterung dienen soll, wird die
spezifische Dichte der Folie mit den zuvor genannten spezifischen
Dichtemessmethoden erreicht. Auf der anderen Seite wird ein gehärtetes Produkt
aus der vorgenannten Harzmischung unter den nachfolgenden Formbedingungen
geformt: Temperatur 175°C × 2 Minuten;
6,865 MPa; Nachhärten
bei 175°C
für 5 Stunden, wobei
das wahre spezifische Gewicht des verdichteten Formaterials über die
spezifische Dichtemessmethode wie zuvor beschrieben ermittelt wird.
Nachfolgend wird das Foliendichteverhältnis aus diesen gemessenen Werten
basierend auf der nachfolgenden Formel ermittelt: Foliendichteverhältnis (%)
= [(spezifische Dichte der Folie)/(wahre spezifische Dichte des
verdichteten Formmaterials)] × 100.
-
Zum
Pulverisieren der Folie können
normale Pulverisierer mit einer Härte, größer als die eines Füllers, verwendet
werden, wobei Beispiele eines Pulverisierers eine Hammermühle umfassen.
Die Partikelgröße der pulverisierten
Harzmischung kann durch Prüfung
der Partikelgrößenverteilung
mit einem JIS Standardsieb ermitelt werden.
-
Nach
der vorliegenden Erfindung hat das pulverisierte Material vorzugsweise
50 % an Gewicht oder weniger als die pulverisierten Partikel, die
auf dem 1 mm Sieb befindlich sind, ohne durch das Sieb zu gelangen,
wobei dies basierend auf dem Gesamtgewicht des pulverisierten Materials
ist. Wenn die Menge größer als
50 % ist, so kann es eine Tendenz geben, dass, selbst wenn das Foliendichteverhältnis als
hoch kontrolliert ist, Hohlräume
zwischen den Partikeln verbleiben können, wobei die Hohlräume während des
Formens die Tendenz haben, größer zu werden.
-
Das
pulverisierte Material hat vorzugsweise ein Gewicht von 10 bis 40
%, noch bevorzugter von 20 bis 25 %, und an pulverisierten Partikeln,
die durch das 0,125 mm Sieb passen, basierend auf dem Gesamtgewicht
des pulverisierten Materials. Die feinen Partikel füllen die
Hohlräume
zwischen den größeren Partikeln, so
dass die Luftmenge, die zwischen die Tafeln während des Formens eingezogen
werden, reduziert werden können.
Wenn trotzdem die Menge an feinen Partikeln 40 % oder mehr überschreitet,
kann die Hauptdichte gering werden, was zu einer Zunahme an Luftblasen
führen
kann und zu einem deutlichen schwierigeren Ausformen der Tafeln
führen
kann. Weitergehend, in Bezug auf den Kompressionsdruck und die Tafeldichteverteilung,
ist es besonders bevorzugt, die Menge der Partikel mit einer Partikelgröße von 0,95
mm oder weniger auf 95 Gew.-% oder weniger, basierend auf dem Gesamtgewicht
an pulverisierten Material, zu drücken.
-
Das
Dichteverhältnis
der zuvor genannten Tafel, die tafelausgeformt ist, ist auf 94 %
oder weniger als 98 % gesetzt. Besonders bevorzugt sind 96 % oder
mehr und weniger als 98 %. Der Grund, warum das Dichteverhältnis des
zuvor genannten tablettartig ausgeformten Tabletts weniger als 98
% ist, wird nachfolgend erläutert.
Das heißt,
(1) selbst wenn das Dichteverhältnis
auf 99 bis 100 % gelegt ist, sehr hohe Unterdrucksetzung erforderlich
ist, um eine Tafeldichte von 98 % oder mehr zu erreichen, was unmöglich ist oder
nicht wünschenswert
vor dem Hintergrund der Vorrichtung, (2) wichtige Komponenten in
dem Material von der Knetvorrichtung entfernt werden, und Wasser
während
der Lagerung aufgrund der vergrößerten Oberfläche wegen
der Pulverisierung absorbiert wird, so dass die flüchtigen
Komponenten zum Zeitpunkt des Tafelausformens in der Harzmischung
enthalten sind. Wenn eine so zusammengesetzte Harzmischung in eine
Tafel mit einer großen Dichte
von 98 % oder mehr geformt ist, kann ein Ausgasen oder eine Entfeuchtung
kaum noch später
durchgeführt
werden, und die flüchtigen
Komponenten können
kaum von der hochdichten Schicht während der Harzverflüssigung
zum Zeitpunkt des Formens separiert werden, und sind letztendlich
geeignet, als Hohlräume
zu verbleiben.
-
In
diesem Zusammenhang wird das vorgenannte Tafeldichteverhältnis wie
nachfolgend erläutert
gemessen und berechnet. Da die Tafel in einer säulenartigen Form ausgeformt
ist, wird die hauptspezifische Masse der Tafel aus dem Durchmesser,
der Höhe
und dem Gewicht der Tafel berechnet, wobei das Tafeldichteverhältnis durch
das Verhältnis
mit dem wahren spezifischen Gewichtswert des verdichteten Formmaterials
(gehärtetes
Produkt der Harzzusammensetzung) ermittelt wird. Weiter beispielhaft
wird das Tafeldichteverhältnis aus
dem hauptspezifischen Gewicht der Tafel berechnet, und zwar in der
vorstehend genannten Art, wobei das wahre spezifische Gewicht des
verdichteten Vormaterials mittels des vorgenannten Verfahrens berechnet
wird, wobei dieses auf nachfolgender Formel basiert: Tafeldichteverhältnis (%)
= [(hauptspezifisches Gewicht der Tafel)/(wahres spezifisches Gewicht
des verdichteten Formmaterials)] × 100.
-
Der
zuvor genannte Druck zur Zeit des Tafelausformens, und zwar in eine
Tafelform unter Verdichtung, ist nicht limitiert, aber es ist wünschenswert,
einen Bereich von z. B. 245 bis 784 MPa zu nutzen.
-
Es
ist daher im Rahmen der vorliegenden Erfindung möglich, effizient den Aufbau
von internen Hohlräumen
in einem Halbleiter, der unter Nutzung dieser Tafel ausgeformt ist,
zu verhindern, wenn alle der entsprechenden Werte bezüglich des
Schichtdickenverhältnisses
und des Tafeldichtenverhältnisses
die zuvor genannten Bereiche befriedigen. Das heißt, wenn
einer der zuvor genannten Werte außerhalb des genannten Bereiches
liegt, sich die Effekte der Erfindung nicht einstellen können. Zum
Beispiel ist es schwierig, die Bildung von internen Hohlräumen in
der Halbleitervorrichtung zu verhindern, wenn das Schichtdickenverhältnis vor
der Pulverisierung weniger als 98 % ist, selbst wenn das Dichteverhältnis der
letztendlich erreichten Tafel 97 % ist.
-
Die
Größe der Halbleiterformtafel
der vorliegenden Erfindung ist nicht im Besonderen eingegrenzt,
solange eine ungefähre
säulenförmige Ausgestaltung
gewählt
ist, wobei ein Bereich von 7 bis 30 mm im Durchmesser und 10 bis
45 mm in der Höhe
bevorzugt wurde.
-
Das
Ausformen einer elementaren Halbleitervorrichtung unter Nutzung
einer Halbleiterformtafel nach vorstehender Art ist nicht begrenzt
und kann mittels eines bekannten Formverfahrens, wie z. B. Transferformens
oder dergleichen, ausgeführt
werden.
-
Als
Nächstes
werden Beispiele der Erfindung zusammen mit Vergleichsbeispielen
beschrieben.
-
Jede
der Komponenten, die nachfolgend gezeigt ist, wurde angefertigt.
Biphenylartiges
Epoxidharz:
Epoxidäquivalent
173, Schmelzpunkt 100°C.
Phenol
Novolakharz:
Hydroxylgruppenäquivalent 107, Schmelzpunkt
60°C.
Härtbeschleuniger:
Triphenylphosphin
Camaubawachs
Anorganischer
Füller:
Fusioniertes
sphärisches
Silicapulver (durchschnittliche Partikelgröße 20 μm)
Ruß
Silanverbindungsmittel:
γ-Glycidoxypropyltrimethoxysilan
-
Erfindungsgemäße Beispiele
1 bis 6 und vergleichende Beispiele 1 bis 6
-
Entsprechende
Komponenten sind in der nachfolgenden Tabelle 1 dargestellt, wobei
diese in einen Mixer gebracht wurden, und zwar mit einem Verhältnis wie
in ebensolcher Tafel gezeigt, und trockenvermischt wurden, wobei
dann die zuvor genannte Mischung in einen Doppelschraubenkneter
eingeführt
wurde und, bei einer Harztemperatur von 110°C, schmelzgeknetet wurde. Als
Nächstes
wurde das geknetete Material aus der Knetvorrichtung ausgelassen
(entladen) und in eine Folienform mittels Rollens unter Verwendung
eines Kalanderrollers mit einem Durchmesser von 150 mm im Durchmesser
ausgeformt. In diesem Fall wurde der Spalt, der hebende Druck und Ähnliches
des Rollers so eingestellt, dass die Folie eine Dicke wie nachfolgend
in der Tabelle 2 aufgeführt
erreichte. Als Nächstes
wurde das zuvor genannte schmelzgeknetete Material in eine Folienform
umgeformt, luftgekühlt,
unter Nutzung einer Hammermühle
pulverisiert und dann in eine Tafelform geformt. Dieses Tafel-herstellende
Ausformen war durch eine rotierende Tablett-herstellende Maschine
erreicht (hergestellt durch Kikusui Seisakusho, 33 nachfolgende
Bauart), wobei darin das Ausformen der Tafeln kontinuierlich ausgeführt wurde,
wobei ein Drehteller rotiert, auf welchem ein Paar an Mörsem und
Stößeln jeweils paarweise
oder in größerer Anzahl
zusammengestellt sind. Nachfolgend wurde eine Halbleitertormtafel
durch Komprimieren bis zu einem gewünschten Tafeldichteverhältnis erreicht. Tabelle
1
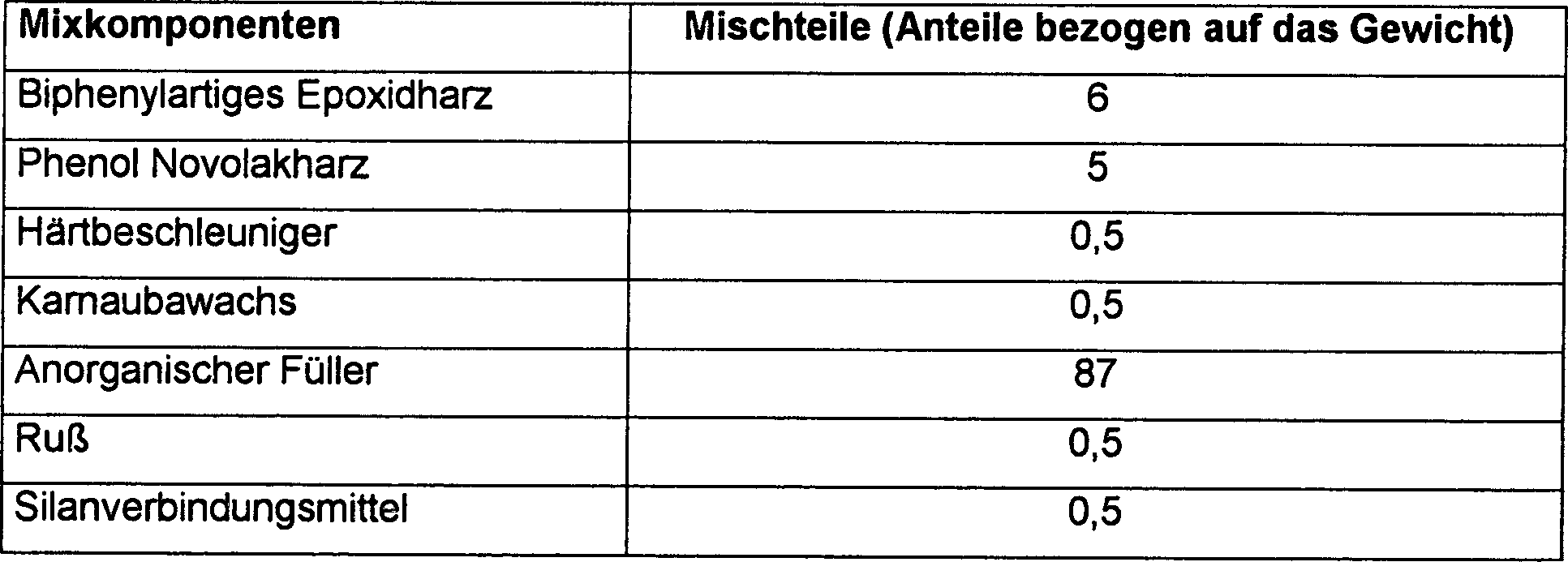
-
Betreffend
jede der entsprechenden Halbleiterformtafeln, die in vorstehender
Art erreicht werden, wurde das Tafeldichteverhältnis gemessen und in Einklang
mit der vorgehend beschriebenen Methode kalkuliert; auch das vorgenannte
Foliendichteverhältnis
zum Zeitpunkt des Rollformens wurde in eine jeweilige Folienform
in Einklang mit dem vorbe schriebenen Verfahren gemessen und kalkuliert.
In diesem Zusammenhang wurde die vorgenannte Schichtdicke mit einer
Schieblehre nach dem Luftabkühlen
des in Folienform umgeformten Materials gemessen. Die Ergebnisse
sind in nachfolgenden Tabellen 2 und 3 aufgeführt.
-
Unter
Verwendung jeder der jeweiligen Halbleitertormtafeln, die in diesem
Zusammenhang erreicht wurden, wurde eine Halbleitervorrichtung (20
Muster) unter den nachfolgenden Bedingungen separiert.
-
Nachfolgend
wurde das Innere der so erreichten Halbleitervorrichtungen unter
Nutzung eines Röntgenapparates
untersucht, um die Anzahl an inneren Hohlräumen mit einer Größe von 100 μm oder größer zu zählen, wobei
dabei ein durchschnittlicher Wert der Anzahl an inneren Hohlräumen in
20 Mustern der Halbleitervorrichtung berechnet wurde. Die Ergebnisse
sind in nachfolgender Tabelle 2 und 3 dargestellt.
Halbleitervorrichtungsgröße: | 144
Pin Quad Flat Package (144 Pin QFP) |
| 20
mm × 20
mm |
Chipgröße: | 7,5
mm × 7,5
mm |
Transferformbedingung: | Temperatureinstellung
bei 175°C
für 90
Sekunden |
Formdruck: | 6865
MPa |
Formmaschine: | Vielkolbensystem,
hergestellt durch TOWA |
-
Fünfzig ausgeformte
Tafeln (14 mm im Durchmesser; gewünschtes Gewicht: 6 g) wurden
ausgeformt und jede der Tafeln wurde gewogen. In Übereinstimmung
mit den nachfolgenden Kriterien wurde die Gewichtsverteilung bestimmt
und die Ergebnisse sind in den Tabellen 2 und 3 wiedergegeben.
- A: (Maximumwert-Minimumwert)/durchschnittlicher
Wert < 0,3 %
- B: 0,3 % ≤ (Maximumwert-Minimumwert)/durchschnittlichen
Wert < 0,5 %
- C: 0,5 % ≤ (Maximumwert-Minimumwert)/durchschnittlichen
Wert < 2,0 %
- D: 2,0 % ≤ (Maximumwert-Minimumwert)/durchschnittlichen
Wert
-
Der
Verdichtungsdruck, der für
das Ausformen der Tafeln benötigt
wird, wurde für
jede der Tafeln der erfindungsgemäßen Beispiele und der vergleichenden
Beispiele gemes sen. Die Ergebnisse wurden in den nachfolgenden Tabellen
2 und 3 als relative Werte, bezogen auf den Wert des vergleichenden
Beispiels 1, als 1 dargestellt. Tabelle
2
Tabelle
3
-
Wie
in den vorgenannten Ergebnissen ersichtlich wurden innere Hohlräume nicht
ausgeformt oder sehr klein, wenn ausgeformt, in den Halbleitervorrichtungen
gefunden, die hergestellt wurden aus einer Tafel mit einem Tafeldichteverhältnis von
94 % oder mehr und weniger als 98 %, wobei diese Vorrichtungen aus
einem pulverisierten Material hergestellt wurden, umfassend einer
gerollten Folie mit einem Foliendichteverhältnis von 98 % oder mehr.
-
Auf
der anderen Seite wurden Halbleitervorrichtungen unter Verwendung
von Tafeln hergestellt, die entweder ein Foliendichteverhältnis von
weniger als 98 % oder ein Tafeldichteverhältnis von weniger als 94 % oder
98 % oder mehr aufwiesen, wobei interne Hohlräume in großen Mengen im Vergleich zu
den erfindungsgemäßen Beispielen
ausgeformt wurden.
-
Wie
in dem Vorhergehenden beschrieben ist, in Einklang mit der vorliegenden
Erfindung, eine Halbleiterformtafel durch Rollformen eines gekneteten
Materials aus einer Epoxyharzzusammensetzung in eine Folienform
hergestellt, wobei ein Foliendichteverhältnis von 98 % oder mehr vorliegt,
wobei die vorgenannte folienförmige
verdichtete Masse pulverisiert wurde, und dann das pulverisierte
Material in eine Tafelform mit einem Tafeldichteverhältnis von
94 % oder mehr und weniger als 98 % gebracht wurde. Dadurch, nämlich durch das
Bestimmen des Foliendichteverhältnisses
auf dem vorgenannten Bereich, wird es möglich, eine hochdichte Tafel
zu erhalten, was mit konventionellen Tafelherstelltechniken schwierig
zu realisieren ist und mit einer Tafelherstellvorrichtung schwierig
ist, wenn pulverisiertes Material verwendet wird. Entsprechend wird
eine Halbleitervorrichtung mittels Harzformens und unter Verwendung
einer Tafel hergestellt, wobei das Herstellverfahren der vorliegenden
Erfindung weniger Hohlraumentstehungen hervorruft und eine höhere Verlässlichkeit aufweist.
-
Zusätzlich wird
es leichter, das Foliendichteverhältnis auf eine hohe Dichte
von 98 % oder mehr einzustellen, wenn die Dicke der zuvor genannten
rollausgeformten Folie 1 mm oder weniger ist.
-
Bestimmte
Abwandlungen der Erfindung, die detailliert in Bezug auf die speziellen
Ausgestaltungsbeispiele beschrieben wurden, sind für einen
Fachmann offensichtlich, wobei eine Vielzahl von Änderungen
und Modifikationen durchgeführt
werden können,
ohne von dem Schutzbereich der Ansprüche abzuweichen.