DESCRIPTION
GROUP III NITRIDE SEMICONDUCTOR LIGHT-EMITTING DEVICE AND PRODUCING METHOD THEREOF
Cross Reference to related Applications: This application is an application filed under 35 U.S.C. § 111(a) claiming the benefit pursuant to 35 U.S.C. § 119(e) (1) of the filing date of Provisional Application No.60/556,023 filed March 25, 2004 pursuant to 35 U.S.C § 111(b).
Technical Field: The present invention relates to a Group III nitride semiconductor light-emitting device comprising a stacked structure including two Group III nitride semiconductor layers having different electric conductive types and a light-emitting layer which is stacked between the two Group III nitride semiconductor layers and which comprises a Group III nitride semiconductor, and to a producing method thereof.
Background Art: Conventionally, Group III nitride semiconductor light-emitting devices, such as light-emitting diodes (LEDs) which emit short wave light of blue band or green band and laser diodes (LDs) , utilize, for example, gallium indium nitride (GaYInzN: 0<Y, Z≤l, Y+Z=l) as a light-emitting layer (JP-B SHO 55-3834, for example) . A light-emitting portion comprises the light emitting layer and two clad layers made of Group III nitride semiconductors having different electric conductivities and disposed on both sides of the light-emitting layer. The clad
layers for forming the light-emitting portion of such a double hetero (DH) structure are made of aluminum gallium nitride
(AlχGaγN: 0<X, Y≤l, X+Y=l), for example. In a stacked structure for forming the Group III nitride semiconductor light-emitting device of pn junction type DH structure that has the light-emitting portion o f DH structure having a light-emitting layer between an n-type clad layer and a p-type clad layer, the substrate is mainly made of sapphire (0.-AI2O3 monocrystal) or silicon carbide (SiC) monocrystal. This is because the material has optical transparencypermitting light from the light-emitting layer to pass and has heat resistance capable of withstanding high-temperature crystal growth of the Group III nitride semiconductor layer. In the case of the conventional Group III nitride semiconductor light-emittingdevice, the substrateused for forming the stacked structure for the light-emitting device is formed such that it remains as a plate body for mechanically supporting the stacked structure thereon even after the device-forming step. The Group III nitride semiconductor light-emitting device allowing the substrate of sapphire crystal or SiC crystal to remain is suitable for maintaining the mechanical supporting force for the stacked structure, but has a drawback of reduced emissio efficiency resulting frominduction of light absorption with respect to short-wavelength ultraviolet rays. The present invention has been accomplished in view of the above circumstances, and it is an object of the invention to provide a Group III nitride semiconductor light-emitting device having a function for mechanically supporting a subject like a substrate, capable of reducing light absorption with respect to short-wavelength ultraviolet rays and capable of
enhancing the light-emitting efficiency. It is also an object of the invention to provide a producing method of the Group III nitride semiconductor light-emitting device and provide an LED lamp.
Disclosure of the Invention: To achievethe above object, thepresent inventionprovides a Group III nitride semiconductor light-emitting device comprising at least a stacked structure including two Group III nitride semiconductor layers having different electric conductive types and a light-emitting layer which is stacked between the two Group III nitride semiconductor layers and which comprises a Group III nitride semiconductor, a crystal substrate used for providing the stacked structure thereon and removed from the stacked structure, and a plate body made of transparent material with respect to light emitted from the light—emitting layer and formed on a surface of the stacked structure exposed after removal of the crystal substrate, whereby light emitted from the light-emitting layer is taken out from the plate body. In the Group III nitride semiconductor light—emitting device, the plate body is made of glass. In the first or second mentioned Group III nitride semiconductor light-emitting device, the removal of the crystal substrate is attained through laser beams irradiated onto a junction interface between the stacked structure and the crystal substrate. Any one of the first to third mentioned Group III nitride semiconductor light-emitting device further comprises an ohmic electrodeprovidedon a surface of the stacked structure opposite from the plate body.
In the fourth mentioned Group III nitride semiconductor light-emitting device, the ohmic electrode is provided at its front surface with a metal reflection film. In the fifth mentioned Group III nitride semiconductor light-emitting device, the metal reflection film is provided at its front surface with a gold film. The present invention also provides a producing method of a Group III nitride semiconductor light-emitting de /ice comprising the steps ofproviding on a crystal substrate a stacked structure including two Group III nitride semiconductor layers having different electric conductive types and a light-emitting layer which is stacked between the two Group III nitxide semiconductor layers and which comprises an Group III nitxide semiconductor, removing the crystal substrate from the stacked structure to expose a surface of the stacked structure, forming a plate body made of material transparent with respect to light emitted from the light-emitting layer on the exposed surface of the stacked structure, and taking out light emitted from the light-emitting layer from the plate body. The present invention also provides an LED lamp provided with any one of the first to sixth mentioned Group III nitxide semiconductor light-emitting devices. The lump has a sub-mount formed preponderantly of S i on which the Group III nitride semiconductor light-emitting deΛice is mounted in a flip manner. According to the present invention, the plate body xaade of material transparent with respect to light emitted from, the light-emitting layer is formed on the surface of the stacked structure exposed after removal of the crystal substrate used for providing the stacked structure. Thus, the plate body can
mechanically support the stacked structure, reduce the light absorptionwith respect to the short-wavelengthultraviolet rays and enhance the light-emitting efficiency. Since it is possible to select a material for the plate bodyhaving substantiallythe same thermal expansion coefficient as the stacked structure, even if current flows for a long time, crack by the thermal stress is not generated in the stacked structure, resulting in enhancement of the reliability of the device . The LED lamp can be obtained by merely mounting the light-emitting device on the sub-mount and thus, the LED lamp can easily be produced.
Brief Description of the Drawings: Fig.1 is a schematic cross section showing the structure of a stacked structure formed on a sapphire substrate. Fig.2 is a schematic cross section showing the structure of an LED according to the present invention obtained by chipping the stacked structure shown in Fig. 1. Fig. 3 is a plan view of the LED. Fig.4 is a cross section of a LED lamp formed by mounting the LED.
Best Mode for Carrying out the Invention: An embodiment of the present invention will be described in detail. A Group III nitride semiconductor light-emitting device of the present invention comprises a stacked structure on a crystal substrate for use in a light-emitting device having (a) a first Group III nitride semiconductor layer of a first
conductive type, (b) a second Group III nitride semiconductor layer of a second conductive type and (c) a light-emitting layer made of a Group III nitride semiconductor and sandwiched between the first and secondGroup III nitride semiconductors . The first and second Group III nitride semiconductor layers have functions as a clad layer or a contact layer. Examples of material of the crystal substrate for forming the stacked structure thereon are monocrystal oxide, such as sapphire andlithiumgalliumoxide (LiGa02) , andGroup III nitride semiconductor monocrystal, such as 3C crystal type cubic monocrystal silicon carbide (3C-SiC) , 4H or 6H crystal type hexagonal monocrystal SiC (4H-SiC, βH-Sic) , silicon (Si) monocrystal, gallium phosphide (GaP) , gallium arsenide (GaAs) . When the first Group III nitride semiconductor layer forming the stacked structure is provided on a crystal substrate having no relation to lattice matching, a buffer layer for moderating lattice mismatch is provided. When the GaN-based first Group III nitride semiconductor layer is allowed to grow on the sapphire substrate, for example, the first Group III nitride semiconductor layer is stacked on the substrate surface through a GaN buffer layer provided by a seeding process (SP) technique (JP-A 2003-243302) . It is also effective for moderating the lattice mismatch with respect to a substrate even if a low temperature buffer layer is made of AIN instead of GaN. When the buffer layer is made of AIN, the layer thickness of the low temperature buffer layer is in the range of 1 n or more and 100 nm or less, preferably in the range of 2 nm or more and 50 nm or less, and more preferably in the range of 2 nm or more and 5 nm or less.
It is preferable that the surfa e of the low temperature buffer layer is flat rather than finesly uneven. For example, it is suitable that the surface roughiness is 0.10 μm or less, more preferably 0.05μmor less, in terms of Ra. Alow temperature buffer layer having a surface of sucti small roughness can be obtained by providing a monocrystal layer at a boundary with respect to the crystal substrate at the time of growth at low temperature of 350°C to 450°C, for exampl e . The surface roughness can be obtained using a measuring devic e, such as an atomic force microscope (AFM) . The low temperaturre buffer layer having a flat surface of small roughness is advantageous for stacking an upper layer having excellent surface flatness . For example, a base layer having a smooth and flat surface and having no uneven portion can grow on the surface of a Ga-3Sf low temperature buffer layer having small roughness. Abase layer having a flat surface^ e.g. a GaN layerprovided on a buffer layer contributes to providing a first or second electric conductive type Group III nitxide semiconductor layer having flat surface. If the firrst Group III nitride semiconductor layer is an n-type layer, the second Group III nitride semiconductor layer is a p- type layer of opposite electric conductive type. The layex thickness of the base layer which is advantageous for providing the first and second Group III nitride semiconductor layers having flat surfaces is 0.5 μm or more and 5 μm or less, preferably 1 μm or more and 3 μm or less, in the case of a GaN layer. The first or second Group III nitride semiconductor layer having flat surface can be utilized as an n-type or p-type clad layer which is suitable for stacking a quantum well structure made of an excellently flat and extremely thin well layer. Fuirther, it can be utilized
as an n-type or p-type contact layer which is suitable for forming input and output electrodes having excellent adhesion. An undoped layer to which impurities are not intentionally added can be utilized as the first and second Group III nitride semiconductor layers. The n-type or p-type Group III nitride semiconductor layer intentionally doped with impurities to control electric conduction, carrier concentration and resistance value can also be utilized. First and second Group III nitride semiconductor layers doped with n-type or p-type impurities so that the atom concentration in the layer becomes lxlO18 cm-3 or more and 5xl019 cm-3 or less are suitable for forming a clad layer used for obtaining a light-emitting device having a low forward voltage and high reliability in terms of operation. It is necessary that the first and second Group III nitride semiconductor layers used as the clad layer are made of material having band gap greater than that of the material of the light-emitting layer, but it is unnecessary that the Group III nitride semiconductor layers are made of the same material . For example, an n-type clad layer may be made of n-type GaYInzN (0 Y, Z≤l, Y+Z=l), and a p-type clad layer may be made of p-type AlxGaYN (0<X, Y≤l, X+Y=l) , for example. If the first or second electric conductive type clad layers made of different Group III nitride semiconductor material are utilized, asymmetric light-emitting portions in terms of band structure can be formed. The first and secondGroup III nitride semiconductor layers having high concentration impurities in the above atom concentration range and having low resistance are effective as contact layers. A Group III nitride semiconductor layer of low resistance in which carrier concentration is lxlO18 cm-3 or more is especially advantageous for forming an ohmic electrode of
low contact resistance. Examples of n-type impurities which, can be utilized for obtaining a low resistant n-type Group III nitride semiconductor layer are Group IN elements, such as silicon (Si) and germanium (Ge) and Group NI elements, such as selenium (Se) . Examples of p-type impurities are Group II elements, such as magnesium (Mg) and beryllium (Be) . It is preferable that the thickness of the contact layer is equal to or greater than such a depth that allows thematerial constituting the ohmic electrode to be dispersed in and enter it. When an ohmic electrode is formed by alloying heat-treatment, the thickness is equal to or greater than the depth of alloy front . Suitable thickness is 10 nm or more. A light-emitting layer provided between the first and second Group III nitride semiconductor layers is made of gallium indium nitride (GaγInzΝ: 0<Y, Z≤l, Y+Z=l), gallium nitrogen phosphide (GaNι-aPa: 0≤a<l) orAlxGaγInzNι-aMa (0<X, Y, Z≤l, X+Y+Z=l,
M represents a Group V element other than nitrogen, O≤ a<l) .
The light-emitting layer may be made of a single quantum well (SQW) layer or a multi-quantum well (MQW) structure. When the well layer of the quantum well structure is made of Ga
YIn
zN, the indium composition ratio (=Z) is adjusted in viewof a desired emission wavelength and set greater in accordance as the wavelength of light is longer. The entire thickness of the light-emitting layer of the multi-quantum well structure having a well layer of Ga
YIn
zN is preferably 100 nm or more and 500 nm or less. The quantum well structure of the light-emitting layex can be formed by forming a layer to be attached to the first or second Group III nitride semiconductor layer as a barriex layer or a well layer . The starting end layer (lowermost layer )
of the quantum well structure may be either a barrier layer or a well layer. Similarly, the terminal end layer (uppermost layer) of the quantum well structure may be either a barrier layer or a well layer. There is no problem even if compositions of the starting endlayer andthe terminal endlayer are different . Aquantumwell structure comprising a well layer having excellent crystallinity because of being undoped and a barrier layer doped with impurities can avoid an adverse affect caused by the piezo effect and can contribute to giving rise to a Group III nitride semiconductor light-emitting device having excellent strength and stable emission wavelength. The well layer and the barrier layer can be made of thin film such as of GaNι-
aP
a (0<a<l) or Al
xGa
YIn
zNi-
aM
a (O≤X, Y, Z≤l, X+Y+Z=l, Mrepresents a GroupVelement other than nitrogen, 0≤a<l) as well as Ga
YIn
zN (O≤Y, Z≤l,
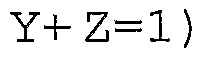
. The Group III nitride semiconductor layers constituting the stacked structure can grow by vapor phase growing means, such as metal-organic chemical vapor deposition (MOCVD) , vapor phase epitaxy (VPE) and molecular beam epitaxy (MBE) . In order to obtain a layer of a wide range of film thickness on order of from some nm of the thickness of a well layer of quantum well structure light-emitting layer to μm suitable for the thickness of the first or second Group III nitride semiconductor layer, the MOCVD means or MBE means is suitable. Among them, the MOVPE means is suitable for vapor deposition of a Group III nitride semiconductor layer containing arsenic (AS) and phosphorus (P) exhibitinghigh volatility other than nitrogen. TheMOCVD means under normal pressure (substantially atmospheric pressure) or of reduced pressure system can be utilized. In the present invention, since the crystal substrate used for forming the stacked structure for the light-emitting device
is removed, it is unnecessary to use optically transparent crystal as a substrate. Since it is rather necessary to remove originally existing substrate (crystal substrate used for forming the stacked structure) , it is preferable that a substrate is made of crystal that can readily be lifted off with ease by etching means, such as wet etching or dry etching including; high frequency plasma etching, or laser radiation means. What is advantageous for exfoliation by the laser radiation means is a crystal substratehaving coefficient ofthermal expansion which is clearly different from that of the structure layer of the stacked structure. In the present invention, after the originally existing crystal substrate is removed, a plate body having mechanical strength is attached onto the uppermost layer of the stacked structure so as to reinforce the mechanical supporting force for the stacked structure. As the plate body to be attached, a glass plate body that is transparent with respect to light emitted from the light-emitting layer can be cited. Preparatory cleaning of the surface of the stacked layer or the surface of the plate body to be attached onto the stacked layer can facilitate the junction thereof . For example, in order to strongly attach the plate body onto the Group III nitride semiconductor layer (the stacked structure) , they are pressurized under external pressure of 1 kg/cm
2 to 5 kg/ cm
2 or heated to high temperature of 500°C to 1000°C. Otherwise, application of temperature, pressure and voltage as well as an anode bonding method may be adopted. In this case, by forming between the plate body and the light-emitting layer a layer of GaN, AIN, GaAINor the like which strengthens the junctionbetween the two, it is possible to attach themwithout adversely affecting
their characteristics. It is also possible to attach the plate body after an adhesive layer, such as silicone resin, is formed on the surface of the stacked structure. To remove the substrate used for forming the stacked structure, polishing means or lifting means can be used. For example, a sapphire substrate can be polished using polishing powder composed mainly of silica, alumina or diamond powder. To lift off a crystal substr ate used for forming the stacked structure from the same, laser radiationmeans is suitable. A.s laser beams suitable for radiation for lifting off, pulsed laser beams, carbon dioxide gas (C0
2) laser beams, excimer laser beams and the like can be cited. Of t-hese, excimer laser beam using argon fluoride (ArF) , krypton fl oride (KrF) or the like as the excitation gas is preferred. T e wavelength of the laser beams is preferably 193 nm or 248 nm. When the crystal substrate to be lifted off using laser beams is thick, since the laser beams are readily absorbed, a region to be lifted off cannot be heated effectively. Therefore, in order to effectively lift off the crystal substrate off the stacked structure by irradiating the laser beams, the thickness of the crystal substrate is preferably
100 μm to 300 μm. When the surface of the crystal substrate is uneven or has a small flaw, the absorption of laser beam is varied, and the. crystal substrate is lifted off unevenly. As described above, in the embodiment of the present invention, the crystal substrate used for forming the stacked structure is removedto expose the surface of the sacked structure, and the plate body made of ir.ate.rial which is transparent with respect to light emitted from the light-emitting layer is then formed on the exposed surface. Thus, the plate body can
mechanically support the stacked structure thereon to reduce the absorption of light with respect to short-wavelength ultraviolet light and to enhance the light-emitting efficiency. It is possible to select material for the plate body having substantially the same thermal expansion coefficient as that of the stacked structure. Therefore, crack by thermal stress is not generated in the stacked structure even if current flows through it over a long period of time. Thus, the reliability can be enhanced. Although the crystal substrateused for formingthe stacked structure is completely removed and the plate body is provided as described in the foregoing, it is not always necessary to completely remove the crystal substrate, and the stacked structure may be thinned rather than removed. If the crystal substrate used for forming the stacked structure is thinned, it is possible to obtain a Group III nitride semiconductor light-emitting device that can reduce absorption of light passing through the crystal substrate and excelling in efficiency of taking out light from the light-emitting layer to the outside and in electrostatic blocking voltage. Thus, it is preferable that n-type or p-type conductive monocrystal which is optically transparent is used as the substrate. The crystal substrate left standing has both a function of mechanically supporting the stacked structure thereon and a function of permitting light from the light-emitting layer to pass through it. If the crystal substrate left standing is thinned, the trans ittance of light is increased, and this is preferable for obtaining a Group III nitride semiconductor light-emittingdevice excellent in efficiencyof takingout light. If the crystal substrate is thinned, however, the function of
the crystal substrate for supporting the stacked structure thereon is reduced. Thus, it is preferable that the thickness of the crystal substrate left standing is lOOμm to 3O0 μm for maintaining both the functions.
Examples : The present invention will be described based on a case in which a glass substrate is attached onto the uppermost layer of the stacked structure as a plate body to form a Group III nitride semiconductor light-emitting device. Fig.1 is a schematic cross section showing the structure of a stacked structure formed on a sapphire substrate. Fig.2 is a schematic cross section showing the structure of an LED according to the present invention obtained by chipping the stacked structure shown in Fig. 1. Fig. 3 is a plan view of the LED. Fig. 4 is a sectional view of a LED lamp formed by mounting the LED. First, as shown in Fig.1, an aluminum nitride (AlN) layer
101 was formed on a (0001) crystal face of an electric insulating sapphire substrate 100 about 350 μm in thickness using seeding process (SP) means by means of the ordinary pressure-reduced
MOCVD method at 900°C. The thickness of the AIN layer 101 was 5 nm. A buffer layer 102 of gallium nitride (GaN) having thickness of 18 nm was formed on the AlN layer 101 at 1050°C. An n-type contact layer 103 of n-type aluminum gallium nitride mixed crystal (Alo.01Gao.99N) having an aluminum composition ratio of 0.01 was formed on the GaN buffer layer
102 so that the atom concentration of silicon (Si) in the layer became lxlO18 cm-3. The contact layer 103 was allowed to grow at 1050°C by the ordinary pressure-reduced MOCVD method. The
thickness of the n-type contact layer 103 was set to about 2.5 μm. An n-type clad layer 104 of n-type Al0.ιoGa0.9oN was stacked on the n-type Alo.01Gao.99N contact layer 103. The n-type clad layer 104 was formed by doping so that the atom concentration of Si in the layer became lxlO18 cm-3. The thickness of the n-type clad layer 104 formed by the ordinary pressure-reduced MOCVD method was set to about 0.5 μm. An n-type light-emitting layer 105 comprising a barrier layer of n-type AlxGaYN and a well layer of n—type GaYInzN was stackedonthen-typeAlo.ioGa0.9oNcladlayer 104. The composition ratio (=Z) of indium (In) in the well layer was adjusted so that ultraviolet light having wavelength of 360 nm to 370 nm could be emitted from the quantum well structure. The quantum well structure was formed, with the thickness of the well layer set to about 5 nm and the thickness of the barrier layer set to 15 nm. A p-type AlXιGaYιN clad layer 106 intentionally doped with p-type Mg impurities and having thickness of 2.5 nm was formed on the quantum well structure light-emitting layer 105. The aluminum composition ratio (=X1) in the layer 106 was set to about 0.10 (=10%) . The Mg was doped so that the atom concentration in the layer 106 became 5x1018 cm-3. A p-type contact layer 107 of Alx2GaY2N (X1>X2>0) doped with Mg and having a smaller composition ratio of Al was formed on the p-type clad layer 106. The atom concentration of Mg in the contact layer
107 was set to about 2xl019 cm-3. A thin film of platinum (Pt) was formed on the surface of the p-type contact layer 107 as a p-type ohmic electrode film 108 by the ordinary high frequency sputtering means. On the
p-type ohmic electrode filmwas provided a metal reflection film 109 for reflecting light from the multi-quantum well structure light-emitting layer 105 toward the crystal substrate 100. The metal reflection film 109 was made from rhodium (Rh) coated film. The n-type contact layer 103 was covered with a mask and etched by dry etching, and an n-type ohmic electrode 113 made of Cr-Ti-Au was formed on the etched surface of the layer 103 (Fig. 3) . The outermost layer of the n-type ohmic electrode 113 is made of gold (Au) . A gold film 110 for junction was formed on the metal reflection film 109, and the stacked structure 11 from the sapphire substrate 100 to themetal reflection film 109 as formed as a former step. Then, the back surface of the sapphire substrate 100 mechanically supporting the stacked structure 11 thereon was ground. The back surface of the sapphire substrate 100 was polished over 130 μm to 150 μm using colloidal silica containing fine silicon oxide particles having an average particle diameter of 0.5 μm. With this polishing, the thickness of the sapphire substrate 100 was thinned to 210110 μm. After the back surface of the sapphire substrate 100 was ground, a glass plate was attached onto the opposite metal reflection film 109 using water-soluble adhesive to temporarily reinforce the mechanical supporting force for the stacked structure 11. Excimer laser beams having wavelength of 248 nm were irradiated onto the junction interface between the sapphire substrate 100 and the GaN buffer layer 102 from the surface of the thinly polished sapphire substrate 100. With this, the polished and thinned sapphire substrate 100 was lifted off from
the portion of the AlN layer 101 and the GaN buffer layer 102 utilizing the difference of the thermal expansion coefficient between the sapphire substrate 100 and the stacked structure 11 thereon. A fluorescent glass plate emitting three colors of RGB with respect to ultraviolet light of around 370 nm was bonded as the plate body 111 onto the surface using anode bondingmethod. The anode bonding method using the voltage of 340 V and the temperature of about 300°C that is relatively low enables the two to be bonded excellently. The spin coating method was used as the method for dispersing fluorescent material to apply the material onto the glass plate surface. Αs another method for dispersing fine particles onto the glass plate, fine particles of lOnm or less are dispersed by sol-gel method. With this, it is possible to prevent coagulation of particles and to produce the surface having extremely excellent characteristics. Then, the glass plate which was temporarily provided on the surface of the metal reflection film 109 of the stacked structure 11 was removed and the electrode surface was cleaned to complete he LED wafer. Next, division grooves or dividing the device were formed on the semiconductor side by an ordinary laser scribe method. Mechanical pressure was applied to the groove using an ordinary breaker to divide the device into Group III nitride semiconductor light-emitting devices (chips) 12 (hereinafter referred to as "LEDs 12") which were substantially square in plan view and had one side length of about 350 μm. With this, was completed to complete a Group III nitride semiconductor white LED 12 (Figs.
2 and 3) of pn junction type DH structure having the sapphire substrate 100 removed from it and the stacked structure 11
mechanically supported on the fluorescent glass plate of the plate body 111 attached onto the stacked structure 11. Since the LED 12 was formed at its entire surface with devices utilizing the attached plate body 111, high-brightness white LED devices having extremely excellent color rendering properties could be formed. Next, the LED lamp 10 was formed utilizing this LED 12. The p-type ohmic electrode 108 (metal reflection film 109, gold film 110) provided on the front surface of the LED 12 and the n-type ohmic electrode 113 (stacked structure 11) were mounted on the Au ball bump 21 formed on the Si sub-mount 23 as shown in Fig. 4. A circuit capable of flowing device driving current between the p-type ohmic electrode 108 (metal reflection film 109, gold film 110) and the n-type ohmic electrode 113 was formed. The surfaces of the p-type ohmic electrode 108 (metal reflection film 109, gold film 110) and n-type ohmic electrode 113 had gold (Au) films. Thus, they could be bonded easily. Then, the device was sealed with epoxy resin 22 containing an inhibitor to prevent deterioration by ultraviolet light to complete a light-emitting diode (LED) lamp 10. When the device driving current was allowed to flowbetween the n-type ohmic elecrode 113 and the p-type ohmic electrode 108 (metal reflection film 109, gold film 110) in the forward direction, it could be dispersed flatly in a wide range of region of the light-emitting layer 105. When the device driving current of 20 mA was allowed to flow to emit light from the LED 12, the emissionoutputmeasuredwithrespect to ultraviolet lighthaving a wavelength of about 370 nm reached about 20 lumens/watt (lm/W) . The forward direction voltage Vf when the forward current of 20 mA was allowed to flow was as low as about 3.4 V.
The sapphire substrate 100 used for providing the stacked structure 11 was removed to expose the surface of the stacked structure onwhich the plate body 111 made ofmaterial transparent with respect to the light emitted from the light-emitting layer 105 was formed. Thus, it was possible to reduce the absorption of light with respect to short-wavelength ultraviolet light and enhance the light-emitting efficiency, with the stacked structure mechanically support on the plate body 111. The driving current could be dispersed flatly in the wide range of region of the light-emitting layer 105 and the light-emitting region was widened to provide an LED having s strong light-emitting output. Material having substantially the same thermal expansion coefficient as the stacked structure 11 could be selected for the plate body 111. Thus, even if current should be allowed to flow for a long time, no crack which might be caused due to thermal stress was generated in the stacked structure 11. Thus, the reliability could be enhanced. In the LED 12, since the plate body 111 was made of glass having a refraction index of 1.5, tb-e light taking-out efficiency was increased. Thus, a device having extremely excellent light-emitting characteristics could be formed. That is, the refraction index of 1.5 of the plate body 111 was between the refraction indices of the GaN and. epoxy resin which are main materials of the stacked structure 11. Since the reflection at the boundary between the plate hody 111 and the GaN (stacked structure 11) and the boundary between the plate body 111 and the epoxy resin 22 is reduced and thus, the light taking-out efficiency can be enhanced.
Industrial Applicability If the LED having the structure of the present invention is utilized, it is possible to select appropriate materials in view of various characteristics, such as the light taking-out efficiency, multi-color emission characteristics and electrostatic countermeasures, to enable a light-emitting device to be completed.
In the LED lamp, since its surface is covered with fluorescent glass having high endurance with respect to ultraviolet light, a reliable lamp having less degeneration of resin canbe obtained.