HIGH THERMAL DIFFUSIVITY, HIGH TOUGHNESS AND LOW CRACK RISK DURING HEAT TREATMENT TOOL STEEL
Field of the invention The present invention relates to a tool steel and its heat treatment, delivering very high thermal diffusivity and high mechanical and tribological properties, while presenting a low crack risk during heat treatment.
The present invention relates to a tool steel as described in WO2012095532A1 or WO2010112319A1 where high levels of thermal diffusivity, mechanical resistance, wear resistance and/or toughness are attained while having a low cracking risk during the heat treatment.
Summary
Tool steels under service are normally subjected to high thermo-mechanical loads. Therefore they require a good combination of different properties which in general terms are considered opposed, the best well-known being yield strength and toughness. These loads can also often lead to thermal shock or thermal fatigue in combination of many other degradation mechanisms as wear or sinking to mention some.
For many metal shaping applications in which there is a heat extraction from the manufactured product, thermal diffusivity plays a crucial role. This property has been traditionally considered opposite to hardness and wear resistance. Thermal diffusivity is related to other material properties like bulk density, specific heat and thermal conductivity. The presence of undesired impurities has also a significance influence on its value. On the other hand, tool steels used in material shaping processes wear is mainly produced by abrasion and/or adhesion, although other mechanisms might also be present. In order to improve wear resistance of the steel some hard particles embedded in the matrix are typically used, such has carbides, borides, nitrides or a combination of them. Their volume fraction in respect to the matrix as well as their morphology is very
important. A fine and homogeneous distribution within the matrix highly increases wear resistance while big agglomerations, sharp shapes or precipitation on grain boundaries weakens the matrix and lowers not only wear resistance but also toughness.
To solve out some of these problems, the inventors have applied some compositional rules described in WO2012095532A1 or WO2010112319A1 which provides a good compromise between thermal diffusivity and the desired mechanical property.
Even when these properties are found together, the correct thermo mechanical processing plays a capital role. And the last heat treatment often occurs after the steel has undergone some shaping often trough machining. Depending on the application, one of the most critical properties to be achieved is toughness. For most of the steels the best compromise to reach acceptable levels of toughness is believed to be obtainable when performing a purely or at least mainly martensitic heat treatment followed by a specific tempering. The meta- stable martensite is a very strong but brittle micro structure due to the trapping of interstitial carbon within its tetragonal structure because of the non-diffusion nature of the transformation when cooling from austenite. When this structure is relaxed through the proper tempering cycle, retained carbon is homogeneously expelled by means of diffusion and the resulting micro structure is composed of tempered martensite plus a fine carbide distribution. Therefore, it is particularly interesting to obtain a pure martensitic or at least mainly martensitic structure after quenching.
This compromise is easily found in small pieces where cooling rates of center and nuclei of the work-piece are fast and similar to each other. Unfortunately, most of the applications of tool steels, such as metal injection, hot stamping or forging, amongst many others, require huge pieces of big dimensions, especially when sufficient strength is required. For that, hardenability of the material is of extreme importance. For heavy sections, it is often impossible to obtain a pure martensitic micro structure through the whole cross-section as the cooling during quenching has to be very severe and sometimes leads to cracks. Therefore, the result is typically a mixed micro structure which lead to low fracture toughness which at its time leads to a lower fatigue resistance.
On the other hand, some work-pieces have very complex shapes. For example, plastic injection molds can have a great deal of inner channels and interconnected cavities. These differences on shapes and thickness of the walls in the mold experiment different heating and cooling rates during heat treatment which induce residual stresses on the piece, whether compressive or tractive, which at the end can easily lead to cracks on the surface or the nuclei of the work-piece.
Hardenability of steels is direct influenced by time available before ferritic-perlitic and bainitic transformations occurs. If the ferritic-perlitic transformation occurs at small interval of time, the first phases to form are composed of ferrite and perlite; depending on the cooling rate there is also the possibility of crossing a critical carbide precipitation zone which takes place at grain boundaries. Carbide precipitation at grain boundaries is very detrimental for all mechanical properties of the steel because carbides behave as fragile ceramic particles and promote fragile and intergranular fracture which propagates very quickly leading to a catastrophic failure. Afterwards, if not all the mass has been transformed, the residual austenite can transform to bainite. The resulting micro structure is a mixture of different microstructures which leads to a bad toughness. On the other hand, if the bainitic transformation also occurs at low times and cooling is not severe enough, austenite is more likely to transform to bainite. Although this structure is much stronger than ferrite and perlite, it is still less than martensite. Therefore, for most of tool steels applications, quenching has to be severe enough to ensure the piece does not enter in these phase transformation zones to ensure that final structure after quenching is mainly martensite.
For commercial steels, the ferritic-perlitic and the bainitic transformations occur at considerably high times which allow a less severe cooling rate. For the steels described in WO2012095532A1 or WO2010112319A1 which are of interest in many applications for having a good compromise between thermal diffusivity and mechanical properties these phase transformation zones occur very quickly after the beginning of quenching. Therefore the hardening cycle of these steels have to be more severe. Under normal conditions, severity of the quench is directly proportional to cracking probability. The aim of the present invention is to develop a heat treatment for the steels of the mentioned inventions which allows to obtain a final micro structure with high amounts of martensite, or at least lower bainite, but which reduces the risk of cracks.
Another important point which influences in the manufacturing of a work-piece is the distortion which accompanies the heat treatment. The first step of the hardening cycle, that is the austenitization implies a volume change, in first instance an expansion through the thermal expansion coefficient and the raising temperature and in second instance a contraction due to the higher density of the austenite (a compact face centered cube structure) in comparison to the original annealed structure (which is mainly a non- compact body centered cube structure). The following quenching entails also an implicit two instances volume change, due to the dropping temperature and due to the density difference between both the starting austenite and final martensite (non-compact tetragonal structure). Because of this metallurgical fact, hardening can often not be the final step of the manufacturing process as final dimensions after treatment would not agree with requirements. Because of these reasons, conventional ways of manufacturing a work piece comprise a first step of an initial rough machining to get rid of most of the unnecessary bulk material; heat treating and final machining to specified dimensions. This combination of steps raises the final price of the manufacturing. An intermediate solution was thought to be found on pre-hardening the steel to avoid the final heat treatment that induces distortion. But this hardness can again not be too high, typically not more than 45HRc, since the machining would still be very costly. Another way is found in reducing thermal gradients within the quenching process. Then, the materials quenched to an intermediate temperature near the martensitic transformation, hold for homogenization and then quenched until martensite formation starts. By this way, distortion is considerably reduced. For tool steels with enough hardenability in both the ferritic and bainitic domains, and for big complex tool geometries, it is common to execute a so called martempering heat treatment process (see Figure 1), where quenching is interrupted to reduce the temperature difference between surface and core before the martensitic transformation.
Unfortunately, for the steels described in WO2012095532A1 or WO2010112319A1 this strategy is not effective because hardenability of these steels, at least in the bainitic domain, is often not high enough to even ensure some martensite in the final micro structure.
The inventors have surprisingly seen that a way of having a fast enough cooling to avoid the formation of stable structures like ferrite-perlite but keeping the crack risk as low as possible is by providing a material with enough hardenability in the ferrite
domain, which on top should be provided with austenite stabilization at a temperature range above the beginning of the bainite formation transformation, then cooling the material fast enough to this intermediate temperature, normally between 400°-700°C (how fast it needs to be cooled to this temperature is a function of the size and geometry of the tool, the amount of ferrite allowed and the hardenability in the ferritic domain, from salt bath to slow oven cooling, normally a rate close to the slowest permissible one should be preferred but often the employed rate is decided on practical reasons and available equipment). Then a very fast cooling from this temperature to a temperature below Ms, or at least below the temperature of the bainitic nose (lower bainite might be an acceptable structure for some applications), should be performed. The cooling has to be faster than is normally the case in a martempering. Also during the holding time at the intermediate temperature it has to be made sure that no part of the tool gets to a lower temperature where bainitic transformation can take place, since in a martempering this is rather unimportant. The inventors have found that when applying this special heat treatment to some of the steels described in the patents WO2012095532A1 or WO2010112319A1, a very good compromise can be attained of the mechanical and physical relevant properties, like amongst others: toughness, hardness, thermal conductivity, wear resistance, while strongly decreasing their sensitivity to cracking during the last heat treatment required to increase hardness after rough machining
State of the art
Until the development of high thermal conductivity tool steels (EP 1887096 Al), the only known way to increase thermal conductivity of a tool steel was keeping its alloying content low and consequently, showing poor mechanical properties, especially at high temperatures. Tool steels capable of surpassing 42 HRc after a tempering cycle at 600°C or more, were considered to be limited to a thermal conductivity of 30 W/mK and thermal diffusivity of 8 mm 2 /s and 6.5 mm 2 /s for hardness above 42 HRc and 52 HRc respectively. Tool steels of the present invention have a thermal diffusivity above 8 mm 2 /s and, often, above 12 mm 2 /s for hardness over 52 HRc, and even more than 16 mm /s for hardness over 42 HRc, furthermore presenting a very good wear resistance and good hardenability. Thermal diffusivity is considered the most relevant thermal
property since it is easier to measure accurately and because most of the tools are used in cyclic processes, so that the thermal diffusivity is much more important for evaluating performance of the tool than can be thermal conductivity.
Steels described in WO2010112319A1 are a family of tool material with improved resistance to thermal fatigue and thermal shock, which can be combined with better resistance to mechanical collapse or wear. The problem of obtaining simultaneously high thermal conductivity, toughness and mechanical problems is solved by applying certain compositional rules and thermo-mechanical treatments within the compositional range described in the mentioned invention. Steels described in WO2012095532A1 are a family of tool material with higher resistance to wear combined with high thermal diffusivity and good levels of toughness, obtained by applying certain compositional rules and thermo-mechanical treatments within the compositional range described in the mentioned invention.
The present invention provides a way to attain the properties described in WO2010112319A1 or WO2012095532A1 to some of the steels of the cited inventions, but in a way in which the risk of cracking complex geometries in the heat treatment is strongly reduced, due to a strong reduction of the thermal gradients.
Detailed description of the invention
In tool steels, and mainly in hot work tool steels, toughness is one of the most important characteristics, specially fracture toughness and notch sensitivity, and even more so where thermal fatigue is one of the most relevant failure mechanism and therefore directly proportional to tool life. Under normal conditions, higher toughness is achieved in detrimental of yield strength, which at the same time decreases with increasing temperature. In that respect, the best compromise between both properties is conventionally achieved through a mainly tempered martensite structure. That means that it is important to avoid the formation of other microstructures like stable ferrite- pearlite or metastable bainite during cooling after austenitisation in the heat treatment process.
For some applications where heat extraction rate has an important impact on the economics of the process, for example for plastic injection moulding or hot stamping, amongst many others, the use of tool steels with high thermal conductivity is definitely
a gain in tool life and also in productivity, as the piece is cooled more rapidly and the machine can decrease production cycle. Attaining a mainly martensitic micro structure during quenching is dependent on the hardenability of the steel being hardened, the geometry of the piece and the cooling media employed. As previously said for big cross-sections, either materials with very high hardenability are used or very fast quenching rates are necessary. The high thermal conductivity steels aimed at in the present invention, present a moderate to high hardenability on the ferritic domain and a low to at most moderate hardenability on the bainitic domain. As previously mentioned for complex geometries, which are very common in the tooling industry amongst others, a very fast quenching rate can easily lead to cracking. The present invention suits especially well when using steels presenting high thermal conductivity, above 35 W/mK, preferably 38 W/mK, more preferably 42 W/mK, more preferably 48 W/mK and even 52 W/mk. The present invention is well indicated in particular when using thermal conductivity steels, within the following composition range, all percentages being indicated in weight percent:
%Ceq = 0.16 - 1.9 %Ni = 0 - 6 %W = 0 - 10 %V = 0 - 4
% C = 0.16 - 1.9 %Si = 0 - 1.4 Ti = 0 - 2 Nb = 0 - 1.5
%N = 0 - 1.0 Mn = 0 - 3 Ta = 0 - 3
Cu = 0 - 2
%B = 0 - 0.6 %A1 = 0 - 2.5 Zr = 0 - 3
Cr < 3.0 Mo = 0 - 10 Hf = 0 - 3 Co = 0 - 6, the rest consisting of iron and trace elements, where the sum of trace elements is not higher than 2%, and wherein Ceq = %C + 0.86 * %N +1.2 * %B and wherein Mo + ½ %W > 2.0
Note that in metallurgical terms, composition of steels is normally given in terms of Ceq, which is defined as carbon upon the structure considering not only carbon itself, or nominal carbon, but also all elements which have a similar effect on the cubic structure of the steel, normally being B and/or N.
In the meaning of this patent, trace elements refer to any element, otherwise indicated, in a quantity less than 2%. For some applications, trace elements are preferable to be less than
1,4%, more preferable less than 0,9% and sometimes even more preferable to be less than 0, 78%. Possible elements considered to be trace elements are H, He, Xe, Be, O, F, Ne, Na, Mg, P, S, CI, Ar, K, Ca, Sc, Fe, Zn, Ga, Ge, As, Se, Br, Kr, Rb, Sr, Y, Tc, Ru, Rh, Pd, Ag, Cd, In, Sn, Sb, Te, I, Xe, Cs, Ba, La, Ce, Pr, Nd, Pm, Sm, Eu, Gd, Tb, Dy, Ho, Er, Tm, Yb, Lu, Re, Os, Ir, Pt, Au, Hg, Tl, Pb, Bi, Po, At, Rn, Fr, Ra, Ac, Th, Pa, U, Np, Pu, Am, Cm, Bk, Cf, Es, Fm, Md, No, Lr, Rf, Db, Sg, Bh, Hs, Mt alone and/or in combination. For some applications, some trace elements or even trace elements in general can be quite detrimental for a particular relevant property (like it can be the case sometimes for thermal conductivity and toughness). For such applications it will be desirable to keep trace elements below a 0,4 %, preferably below a 0,2%, more preferably below 0,14 % or even below 0,06%. Needless to say being below a certain quantity includes also the absence of the element. In many applications, the absence of most of the trace elements or even all of them will be obvious and/or desirable. As mentioned every trace element is considered a single entity and thus very often for a given application different trace elements will have different maximum weight percent admissible values. Trace elements can be added intentionally to search for a particular functionality including also cost reduction or its presence (when present) can be unintentional and related mostly to impurity of the alloying elements and scraps used for the production of the alloy. The reason for the presence of different trace elements can be different for one same alloy. It happens often that two steels representing two very different technological advances, and therefore aiming at very different applications, moreover each being absolutely useless for the objective application of the other, can coincide in the compositional range. In most cases the actual composition will never coincide even if the compositional ranges do more or less interfere, in other cases the actual composition could even coincide and the difference would come from the thermo-mechanical treatments applied.
It should be clear that from all the possible compositions within the range only those where the micro structure described in the present invention is attainable are of interest. Accordingly, a first aspect of the invention is directed to a process of manufacturing a tool steel comprising the steps of: a) providing a steel material having the following composition:
%Ceq = 0.16 - 1.9 % C = 0.16 - 1.9 %N = 0 - 1.0 %B = 0 - 0.6
%Cr < 3.0 %Ni = 0 - 6 %Si = 0 - 1.4 %Mn = 0 - 3
%A1 = 0 - 2.5 %Mo = 0 - 10 %W = 0 - 10 %Ti = 0 - 2
%Ta = 0 - 3 %Zr = 0 - 3 %Hf = 0 - 3 %V = 0 - 4
%Nb = 0 - 1.5 %Cu = 0 - 2 %Co = 0 - 6, the rest consisting of iron and trace elements, where the sum of trace elements is not higher than 2%, and wherein
%Ceq = %C + 0.86 * %N +1.2 * %B and
%Mo + ½ %W > 2.0, characterized in that the process further comprises the steps of: b) applying to the steel material a heat treatment comprising at least partially austenitizing the steel;
c) cooling the steel material
- to a temperature Tint lower than AC1; and
- at a cooling speed S,
which avoid more than a 20% ferritic/perlitic transformation; and
d) quenching the steel material with a quenching rate Qrate and to a temperature Tiow to ensure that the formation of structures other than martensite or lower bainite is kept below 30%.
Some further compositional rules have to be taken into account for an improved performance in certain applications. For example when it comes to the %Ceq content, if extreme thermal diffusivity is seek it is preferably to have a value between 0.25% and 0.30%. or even a value between 0.26 to 0.29%. On the other hand for applications requiring high toughness it is better to keep %Ceq below 1.5% and preferably below 0.9% or even below 0.68. If toughness should be very high the %Ceq should better be kept below 0,52%, preferably below 0,44 or even below 0,38%. %Ceq has a strong effect in reducing the temperature at which martensitic transformation starts, thus higher values of
%Ceq will be desirable for either high wear resistance applications or applications where a fine bainite is desirable. In such cases it is desirable to have a minimum of 0.41% of Ceq often more than 0.52% and even more than 0.81%. If some other elements that reduce the martensite transformation temperature are present (like for example %Ni) then the same effect can be obtained with lower %Ceq (same levels as described before). For some applications where conductivity is to be maximized in combination with high strength at high temperatures it is interesting to have %W present. In particular for those applications amongst others, %W should be more than 2%, more preferably more than 2.1% and even more than 2.3%. For applications where high wear abrasion at temperature is desirable, then it is better to have %W more than 2.5%, preferably more than 3% and even more than 3,5%. Also the %Moeq (%Mo + ½ · %W) levels should be higher for maximum thermal conductivity, normally above 3.0% often above 3.5%, preferably above 4% or even 4.5%. Depending on W price raising and for applications requiring high alloying content with high conductivity and strength, %Mo is desirable to be more than 4.5%, more preferably more than 4.8% and even more than 5.8%. Also %W has an effect on the deformation during heat treatment attainable, since the atomic radii mismatch is greater than that of %Mo. Thus for some applications requiring control of the deformation during the heat treatment it can be convenient to have %W smaller than 0.9%, preferably smaller than 0.7%, more preferably smaller than 0.4 or even no intentional %W at all. When it comes to %Cr, normally higher levels are preferred to somewhat improve the ambient resistance and the hardenability in the bainitic domain. Applications requiring high thermal conductivity with this kind of steels will prefer a lower %Cr, normally less than 2.8% preferably less than 1.8% and even less than 0.48%. For applications benefiting from extreme high thermal diffusivity %Cr should be kept below 0.28% preferably below 0.08% or even below 0.02%. A special attention has to be placed in elements that increase hardenability by slowing the kinetics of the austenite decomposition into ferrite/perlite. Very effective in this sense is %Ni and somewhat less %Mn. Thus for heavy sections where a slow transition between austenitization temperature and stopping temperature is needed, it is often desirable to have %Ni present. The effect of %Ni is not linear in retarding the austenite decomposition and the point at which the influence becomes very large also depend on other alloying elements, but generally for a large slowing in the austenite decomposition a minimum %Ni content of normally 2%, preferably 2.1% and even 2.3% is desirable. Depending on the application, if transition has to be very slow then %Ni content
is advisable to be more than 2.5, more preferably more than 2.8 and even more preferably more than 3.2. %Ni also helps reduce the thermal expansion coefficient, but this happens at higher levels of %Ni content. This is very interesting for applications suffering from thermal fatigue amongst others. For these applications %Ni contents above 3.2%, preferably above 3.6% and even above 4.1% are desirable. If %Mn is chosen for this goal higher amounts are required to attain the same effect, and its influence on thermal conductivity is also more noticeable. For applications where the steel is to attain very high temperatures (even in excess of 400 °C) during service it might be very interesting to have %Co present which tends to increase tempering resistance amongst others and presents the odd effect of affecting the thermal diffusivity not very negatively or even positively for high temperatures. Although for some compositions an amount of 0.8% might suffice, normally it is desirable to have a minimum of 1,0% preferably 1,5% and for some applications even more than 2.7%. Also for applications where wear resistance is important it is advantageous to use strong carbide formers if price sensitiveness of the application, and the reduced toughness allow, then Zr+%Hf+%Nb+%Ta should be above 0.2%, preferably 0.8% and even 1.2%. Also %V is good carbide former that tends to form quite fine colonies but has a higher incidence on thermal conductivity than some of the former, but in applications where thermal conductivity should be high but is not required to be extremely high and wear resistance and toughness are both important, it will generally be used with a content above 0.1%, preferably 0.22% and even more than 0.38%. For very high wear resistance applications it can be used with a content higher than 0.55% or even 1.2%. Other elements may be present, especially those with little effect on the objective of the present invention. In general it is expected to have less than 2.5% of other elements (elements not specifically cited), preferably less than 1.8%, more preferably less than 0.45% and even less than 0.2% or eventually none at all other than the unavoidable levels due to impurity of materials used for the manufacturing.
For applications requiring very high thermal conductivity with good mechanical properties, especially at high temperatures it is important to have a good balance between %Ceq and %Moeq. Normally %Moeq should be higher than 4.8%, preferably higher than 5.2%, more preferably higher than 5,7% and even higher than 6,2%. The ratio %Moeq/%Ceq should in principle be higher than 12.5, preferably higher than 15, more preferably higher than 17 and even higher than 20 when %Ceq is smaller than 0.36. For %Ceq higher or equal to
0.36 then Moeq/ Ceq should be higher than 10, preferably higher than 11.6, more preferably higher than 12.4 or even higher than 17.
So, for such kind of steels, unusually high final tempering-like temperatures (final tranche of the heat treatment to raise hardness) end up being used, often above 600°C, even when hardness over 50 HRc are chosen. In steels of the present invention it is usual to achieve hardness of 47 HRc, even more than 52 HRc, and often more than 53 HRc and with the embodiments regarded as particularly advantageous due to their wear resistance, hardness above 54HRc, and often more than 56 HRc are possible with even one tempering cycle above 590°C, giving a low scattering structure characterized by a thermal diffusivity greater than 8 mim/s and, generally, more than 9 mrm/s, or even more than 10 mrm/s, when particularly well executed then greater than 11 mrm/s, even greater than 12 mrm/s an occasionally above 12,5 mrm/s. As well as achieving hardness greater than 46 HRc, even more than 50 HRc with the last tempering cycle above 600°C, often above 640°C, and sometimes even above 660 °C, presenting a low scattering structure characterized by a thermal diffusivity higher than 10 mrm/s, or even than 12 mrm/s, when particularly well executed then greater than 14 mrm/s, even greater than 15 mrm/s and occasionally above 16 mrm/s. Those alloys can present even higher hardness with lowering tempering temperatures, but for most of the intended applications a high tempering resistance is very desirable. As can be seen in the examples with some very particular embodiments with high carbon and high alloying, leading to a high volume fraction of hard particles, hardness above 60 HRc with low scattering structures characterized by thermal diffusivity above 8mrm/s and generally more than 9mrm/s are possible in the present invention.
In general terms, hardenability is the ability of a steel to partially or completely transform from austenite to some fraction of martensite at a given depth below the surface, when cooled under a given condition. A steel of a high hardenability can transform to a high fraction of martensite to depths of several millimetres under relatively slow cooling, such as an oil quench, whereas a steel of low hardenability may only form a high fraction of martensite to a depth of less than a millimetre, even under rapid cooling such as a water quench. Hardenability therefore describes the capacity of the steel to harden in depth under a given set of conditions. Steels with high hardenability are needed for large high strength
components, such as large extruder screws for injection moulding of polymers, pistons for rock breakers, mine shaft supports, aircraft undercarriages, and also for small high precision components such as die-casting moulds, drills and presses for stamping coins. High hardenability allows slower quenches to be used (e.g. oil quench), which reduces the distortion and residual stress from thermal gradients. Steels with low hardenability may be used for smaller components, such as chisels and shears, or for surface hardened components such as gears.
Hardenability can be evaluated from the time-temperature-transformation (TTT) diagrams and/or even more convenient the continuous-cooling transformation (CTT) diagrams. These diagrams represent which types of phase changes will occur in a material as it is cooled whether isothermally (TTT) or at different rates (CTT). The form of the diagrams depends on the steel's composition and are represented by a high temperature stable phases domain, known as ferrite-pearlite domain, connected to a low temperature stable phases, known as bainite domain (upper bainite, lower bainite or any of its variants); it is also to be seen start and finish temperature of un- stable phases such as martensite, as a function of time. An example of a conventional tool steel is given in Figure 3. As mentioned, for some applications, high hardenability is needed in other to obtain mechanical properties in the final piece. Therefore, it is required that during quenching no stable phases (not high temperature neither low temperature stable phases) are formed. Therefore, in the meaning of this patent, hardenability will be differentiated between ferritic-perlitic hardenability, which will refer to the ability of cooling without transforming to ferrite and/or pearlite, and bainitic hardenability, which will refer to the ability of cooling without transforming to bainite.
Steels which the present invention relates to are steels which have small ferritic hardenability and much less bainitic hardenability. In normal conditions, to attain high amounts of martensite in the structure, very sever quenching conditions should be used, but such severe conditions are detrimental for other aspects, particularly the risk of cracking which increases with the severity of the quench. In such cases, other strategies in order to obtain a mainly martensitic microstructure but without risking that the piece cracks, have to be sought. A typical common treatment is martempering but this treatment only works well for steels with low ferritic hardenability but good bainitic hardenability. The steels to which the present invention, as it was described, have poor ferritic hardenability and even
less bainitic hardenability. Therefore, a martempering treatment is not successful for achieving the required propertieson the final product. The inventors have seen that, for the steels of the present invention, final properties can be achieved by means of the described heat treatment. The inventors have surprisingly seen that if composition is chosen from the range described in the following pages in order to obtain specific mechanical and/or thermal properties, which is also later on described, it happens that the phase transformation diagrams adopt a unique shape, where the ferritic-perlitic domain is separated from the bainitic domain, leaving a zone in-between where no transformation occurs and where the stable phase is austenite. Because of this fact, solving strategies for commercial steels are not valid for the steels of the present invention and new strategies are not trivial.
The inventors have surprisingly seen that when composition is correctly chosen to induce this domain separation, it is possible to cool the austenitized material to a temperature above the bainitic transformation, namely Tjnt (the necessary cooling rate depending on the hardenability on the ferritic domain), for example within a temperature range around 470°C-700°C and depending on steel composition, hold at this temperature or within the temperature range to better homogenize the temperature of the core and that of the surface followed by a rapid cooling into the martensitic or lower bainite transformation. Because of stopping at intermediate temperatures, thermal gradient is lower, both in respect to the austenitisation and even more interesting when trying to attain the martensitic transformation. This strategy does not only allow for the final microstructure to have a higher martensite or at least lower bainite content because homogeneous fast cooling rates to a determined temperature are easier to be obtained when thermal gradient within the piece and when the starting temperature is lower, but also highly minimizes crack risk because distortion produced by volume changes associated to inhomogeneous temperature distribution within the piece are also minimized.
To not stress the nomenclature often in this document reference has been made to the ferritic transformation of the steel upon cooling to Tjnt. It is clear to the specialist metallurgist, depending on the specific composition chosen and especially on the Ceq, whether the word ferrite/ferritic should incorporate or be replaced by the word perlitic. In some instances it has been specified in the text.
The austenitization temperature for tool steels is normally well above Ac3 since it is often convenient to bring most carbides into dissolution before quenching. Depending on final application, it will be more interesting to austenitise at lower temperatures, even between AC1 and AC3 (where an incomplete austenitization takes place). Typically the austenitization temperatures will be above AC3, but often below the temperature of complete carbide dissolution, even in absence of primary carbides, as grain growth is directly proportional to temperature. Small grains sizes are normally accompanied by higher strength so lower temperatures are more convenient for this purpose. If it is accompanied with short time, once the core has reached the temperature, even better. For some applications, these values are below 1040 °C, preferably below 1020 °C, more preferablu below 1000°C and even below 990 °C. On the contrary and depending on steel's composition, if austenitization temperature is smaller than the dissolution temperature of some kind of carbides, for example M6C carbides, carbides do not have the possibility of redistributing themselves along the matrix. High temperature carbides tend to agglomerate caused by metallurgical segregations and it normally has a negative effect on toughness. Better performance of carbides is found for small sizes, due to an increase of strength through phase boundaries. It is even better if embodiment within the matrix is homogeneous all along. Therefore, for some applications it is more convenient to ensure a maximum dissolution of carbides into austenite so that the precipitate at the desired place during the next steps of the heat treatment. In such cases it will be desirable to use an austenitazing temperature above 1060°C, preferably above 1080 °C, more preferably above 1110 °C and for some special compositions even above 1120 °C. The heating up and austenitization can be carried out in any type of furnace, atmospheric, protected atmosphere, salt bath, vacuum Uneven heating or overheating from specified temperature should be avoided. Heating rate must be controlled; especially around the AC3 range because contraction of the body centered cubic structure from ferrite transforms to the face centered cubic structure of austenite may produce micro cracks that can grow afterwards.
Once the austenization has been performed in the preferred way, the material is subjected to a cooling to an intermediate temperature Tint. This temperature has to be such that no massive transformation of austenite occurs. Such temperature can be determined by means of thermodinamical simulation programs or experimentally determined by means of a
dilatometric test so that no massive ferrite transformation occurs during the process. In the present invention depending on the hardenability of the composition chosen the upper limit for Tint will in fact be ACi. For other compositions with less hardenability and depending on the composition (positioning of the ferrite transformation domain in the TTT diagram) the upper limit for Tint will be ACi-20 °C, preferably ACi-60 °C and more preferably ACr 110 °C or even ACi-180 °C. If values of ACi are not present, normally Tint will be limited to 780 °C, preferably to 700 °C, more preferably 625 °C and even to 590 °C. When it comes to the lower limit for Tint, this is fixed by the bainite transformation curve (which should include any kind of transformation below the ferritic transformation and above Ms, like for example Wittmanstatten ferrite transformation amongst others). If we call such temperature TBsws, then it is generally desired for Tint to be higher that TBsws, preferably at least 10 °C higher, preferably 18 °C higher, more preferably 35°C higher and even 58 °C. As long as no massive transformation of the austenite occurs, Tint can also be somewhat lower than TBsws, generally not more than 10 °C lower, but occasionally up to 40 °C lower. In the absence of proper TTT characterization, then the lower limit of Tint can be chosen to be 470 °C, preferably 510 °C and even 540 °C. for very specific cases, Tint can be below 460°C, preferably below 445°C, more preferably below 420°C and even below 400°C. So Tint is in reality a temperature interval, and the holding temperature in one particular heat treatment can also change within this interval. The holding time at this temperature once the core has reached the temperature can vitiate from a few minutes (more than 2 minutes, preferably more than 10 minutes, more preferably more than 20 minutes and even more preferably more than 30 minutes) to several hours (more than 1 hour, preferably more than 2 hours and even more than 11 hours) or even days (1 day, even 2 days) if desired, depending on the heat-treated piece size and the lack of transformation at Tjnt. It is not the best performance but for some pieces, due to economic reasons or where the economic costs have great importance, it might be necessary not to wait until nuclei reaches Tint and starting the rapid cooling even if some part of the piece has not reached Tint. The cooling speed S to reach Tjnt depends on the piece geometry, the hardenability of the material in the ferritic domain, the presence of other undesirable transformations (like grain boundary precipitation amongst others), and the means to be disposed of. So from slow cooling in the heating furnace (less than 58°C/min, preferably less than 43°C/min, more preferably less than 31°C/min and even more preferably less than 10°C/min) to fast cooling in a molten metal (more than 77°C/min, preferably more than 89°C/min, more preferably more
than 110°C/min and even more preferably more than 180°C/min), anything in the middle is possible (to mention some examples, transference to another furnace with setpoint near Tint, salt bath...)- Sometimes for complex geometries it will be desirable to have a moderate cooling,enough fastto avoid undesirable transformations (ferritic/perlitic) but not too much to avoid distortion. In this situation, it is preferred to cool more than 5°C/min, preferably more than 28°C/h, more preferably more than 48°C/min and even 67°C/min. Speed will be chosen in terms of the % ferrite/perlite transformation desired, normally to avoid more than 20% of ferritic/perlitic transformation. Normally less than 15% ferrite is desirable, preferably less than 11%, more preferably less than 7% and most preferred is less than 2% or even none. It has to be made sure that no significant parts of the component being heat treated will drop its temperature below Tint while this is not desirable, and that makes gas (for example N2, He, Ar, compressed air,...) cooling a candidate for a few of the compositions, but a more laborious one since good temperature regulation systems are needed. At this point is when the quenching step takes place, but instead of taking place from a high temperature like the austenitization temperature it takes place from an intermediate temperature. So the risk of cracking is severely reduced and also desirable microstructures can be attained for a given composition for bigger cross sections.
The quenching is performed from Tjnt to Tlow- Tiow has to be chosen to give the desired properties for a given application, so very many different microstructures can be chosen, but they have in common that one should reach the transformation point with so much metastable austenite as possible. Especially, the areas of the TTT diagram leading to upper bainite or other likely transformations (from the temperature time point of view) like for example the formation of Widmanstatten ferrite, should be avoided. So Tiow is generally chosen to be below the temperature at which the so called bainitic nose takes place (bainitic nose is the temperature at which bainitic transformation starts with the least amount of time. More accurately for other applications it is the lowest temperature at which more than a 20% of upper bainite can be attained that is chosen as upper limit for Tiow We will name here TBNUB the smallest of the two temperatures (that of the bainitic nose and that at which a 20% of upper bainite is still possible), such to ensure that the formation of structures other than martensite or lower bainite is kept below 30%. Then Tiow will normally be below TBNUB, preferably below TBNUB -8 °C, more preferably below
TBNUB -18 °C and even below TBNUB -52 °C. If the TTT diagrams are not at hand, then as an approximation, Tiow will often be chosen to be below 450 °C, preferably below 380 °C, more preferably below 360 °C and often even below 220 °C. As said for some applications Tiow is chosen to be as low as possible with the means at hand. Tiow is purposely chosen, for some applications it is preferred value is as low as possible, but not for all applications. Besides the preferred microstructure another reason to choose a higher Tiow is often to control the stresses generated through the volume change during martensitic transformation. Also to have an immediate relaxation of the martensite to prevent the formation of cracks. Quenching has to be done in a narrow window of time to minimize undesirable phase transformation. So cooling rate Qrate has to be such to ensure that the formation of structures other than martensite or lower bainite is kept below 30%. The reaction has to be thermodynamically favorable and kinetically accessible. Therefore desirable cooling rate is mainly dependent on cooling media, work-piece size, Tjnt, Tiow and thermal conductivity of steel (at the given moment, which is not going to be all too large specially if most carbides where dissolved during austenitization). Sometimes the desirable cooling rate cannot be attained with the means at disposal and some transformation to undesirable structures occurs. It is desirable than less than a 30% of austenite transforms to undesirable structures at this stage, preferably less than a 18 %, mor preferably less than a 8% and obviously even none at all. The desirable structures are those that lead to a good combination of hardness and toughness, normally after tempering. So mainly martensite and lower bainite. Ideal quenching has to assure the maximum amount of desired microstructure as possible.
Normally the tool material within the compositional range is selected so that, transformation kinetics to stable but not desirable structures (ferrite, perlite, upper bainite (or alike), alone or in combination) has to be slowed as much as possible. It can be separated between the transformations that take place above Tjnt and the ones that take place between Tjnt and Tiow, since they determine the cooling and quenching rates desirable. At least 600 seconds for 10% ferrite/perlite transformation is normally desired, preferably more than 1200 seconds and even more than 7000 seconds for 10% ferrite/perlite transformation. In fact for the composition can be chosen in the compositional range so as to practically suppress such transformation, but it has some incidences on other relevant properties that might not be desirable for certain applications,
so that such compositions cannot always be chosen. Also more than 100 seconds for 20% transformation into bainite (or alike) is desired, preferably more than 180 seconds, more preferably more than 600 seconds and even more than 6200 seconds for 20% bainite.
Therefore, to be able to conduct a successful quenching under these conditions where thermal gradients are of big importance, often severe mediums have to be used. For most applications of the present invention, oil is typically used or any other fluid with an equivalent attainable cooling rate from Tint to Tiow. New developments of polymeric solutions are also to be used. Depending on bainitic transformation times as well as geometry of the work-piece, other cooling mediums more severe should be used. For some applications requiring higher toughness, water (with or without salt), slurries, molten metals... should be used. If the application requires it, and just for special compositions, the steel can be quenched in partially frozen salt water or even with gas (typically nitrogen, compressed air, argon or helium). In all cases, great agitation is much recommended to promote maximum heat exchange from the material to the cooling media used. In the case the fluid is a gas, normally great pressures and flow rates are required. The quenchant ratio and size of the part have also a great influence on the actual cooling rate. For small and/or thin work pieces, surface and nuclei achieve the desired temperature quickly and with a small delay of time, leading to a homogeneous martensitic micro structure. Unfortunately, cooling rates at the surface and in the core is not the same for bigger sections. The area in contact with the cooling agent cools immediately after contact and evens out with that of the medium. The inner depths of the material however, do not cool so rapidly. This results in a work-piece that does not have the same crystal structure throughout its entire bulk shape. Then, final microstructure is composed of pure martensite on the surface; a transition zone of mixed microstructures; and bainite -either lower or upper bainite depending on the mentioned parameters- in the center of the work-piece. This is not so detrimental for some applications. Even ferrite plus pearlite is allowed to be found in the core in some cases. The other negative effect caused by differences in cooling rates during quenching comes from the fact that while the surface is already cold, nuclei is still hot, and because of the volume change involved during the martensitic transformation, high tractive and compressive stresses are created in the transition zone which at the end can lead to cracks.
This last consequence is highly intensified in pieces of complex geometries. Plastic injection molds as well as aluminum injection molds, to mention some of the most relevant applications, have normally complicated shapes depending on final parts to be produced, for example the gear box or the battery shell of a car. Sometimes, the mold requires having a lot of inner cooling channels. Different thicknesses as well as unbalanced refrigerating zones submit the workpiece to high stresses during quenching because of the intensification of hot spots and cold spots and lead to undesirable and catastrophic cracks in the more stressed and weakest zones.
The present invention is very well suited for such cases because when composition is correctly chosen, the phase diagrams allow to perform the special heat treatment which highly minimizes crack risk.
Examples
Some illustrative examples should reinforce the main text for the comprehension of the skilled person to fully understand the way that the invention can be executed. The reported examples have no pretension to be covering the full range of the invention, which would be from the extension point of view impossible, but just to serve as complement in case it is more understandable for the skilled person to understand the full concept and the way in which the claimed steel compositions and the heat treatment described in the present invention can be specified when seeing a couple practical cases: Example 1:
Steels with compositions specified in Table 1 with %Ni content between 0% and 2% induce smaller hardenability to the material. Samples were austenitised at a temperature between 1000-1150°C for about 30 minutes (once the core of the pieces had reached the temperature). Different implementations of the heat treatment of the present invention where implemented. Tint was chosen to be in the 480-680 °C range. And at least in one of the treatments Tint was chosen in the 500-580 °C range. The cooling to Tint was made with a salt bath and samples were soaked at that temperature for one hour. Afterwards, the material was severely quenched in oil or cold water with maximum agitation (water was used for the compositions with theoretical or measured bainitic nose in the TTT diagram with a transformation time of less than 100 seconds to 20% bainite (or alike). Cooling rate
in a salt bath is quick enough for this %Ni content to avoid a generalized ferritic-perlitic transformation.
Table 1
Final micro structure was composed mainly by martensite. The hardness right after heat treatment was in all cases above 37 HRc. And for all compositions at least with one of the heat treatments the hardness was above 43 HRc. Samples were afterwards tempered, it was seen that in all cases a hardness superior to 48 HRc could be attained in the tempering graph. Samples were tempered beyond the secondary hardness peak and in all cases resilience exceeded 100 J/cm 2 (in many cases more than 450 J/cm 2 were measured) for hardnesses above 48 HRc. All compositions were also further tempered to a hardness of 40-45 HRc for a CVN test where in all cases a value of more than 11 J was encountered (in some cases more than 90J were measured). Finally the samples were further tempered in 20 °C steps until about 35 HRc. For all compositions a diffusivity at room temperature of more than 9.0 mm 2 /s (often more than 10,5 mm 2 /s and even more than 14 mm 2 /s) were measured at some point of tempering.
Example 2:
Steels with compositions specified in Table 2 with %Ni content between 2.00% (preferably 2.15%) and 3% induce moderaqte hardenability to the material. Samples were austenitised at a temperature between 1000-1120°C for about 30 minutes (once the nuclei of the pieces had reached the temperature). Tint was chosen to be in the 480-650°C range. And at least in one of the treatments Tint was chosen in the 500-560°C range. The cooling to Tjnt was made by means of changing the piece to another furnace running at the Tint temperature and samples were soaked at that temperature one hour. Afterwards, the material was severely quenched indistinctly in oil or water with maximum agitation (again, water was used for the compositions with theoretical or measured bainitic nose in the TT diagram with a transformation time of less than 100 seconds to 20% bainite (or alike). The higher %Ni content allows a less severe cooling from austenitisation temperature to stopping temperature.
Table 2
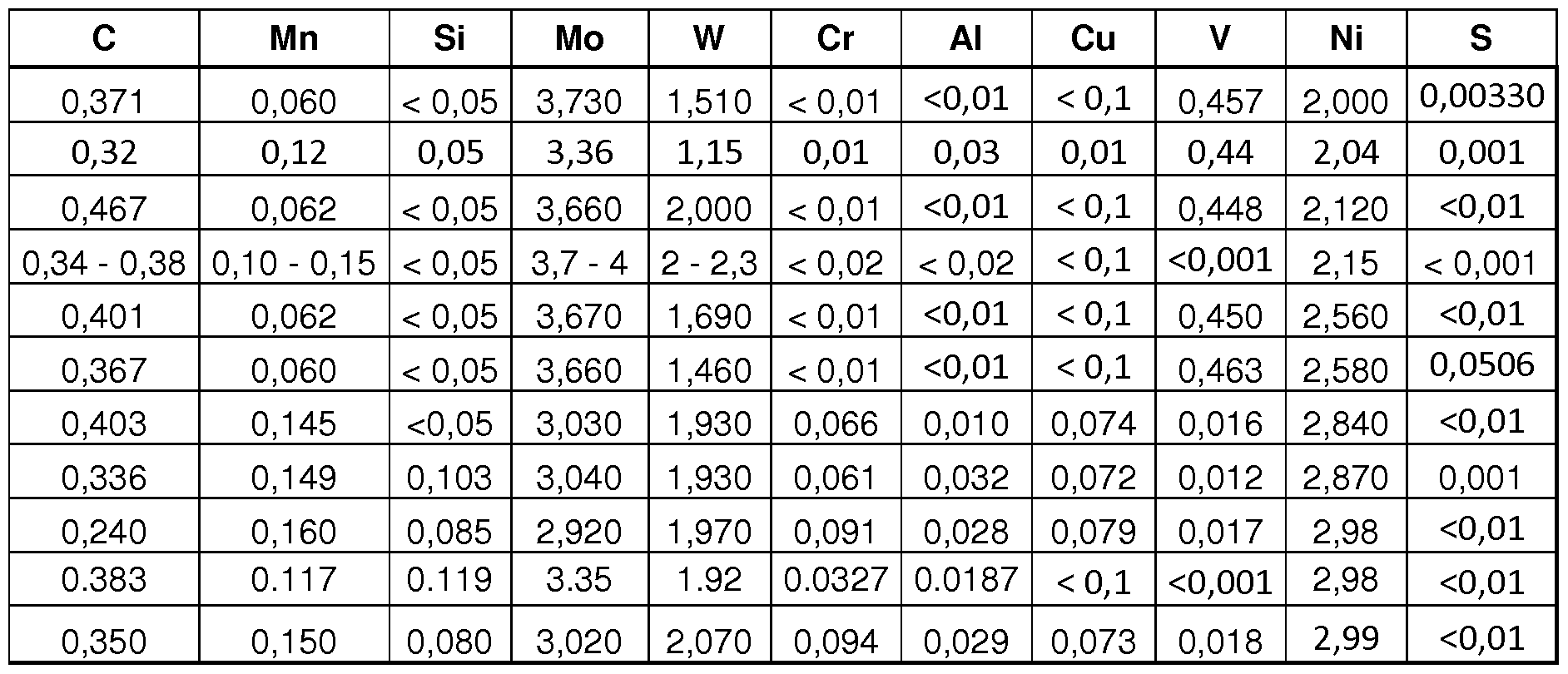
Final micro structure was composed mainly by martensite. The hardness right after heat treatment was in all cases above 45 HRc. And for all compositions at least with one of the heat treatments the hardness was above 50HRc. Samples were afterwards tempered. It was seen that hardness superior to 47 HRc could be attained in the tempering graph. Samples were tempered beyond the secondary hardness peak resulting in hardnesses above 50HRc. In all cases resilience exceeded 150 J/cm 2. In many cases, more than 295 J/cm 2 was measured and in some cases even more than 450 J/cm . All compositions were also further tempered to a hardness of 40-45 HRc for a CVN test where in all cases a value of more
than 11 J was encountered (in some cases even more then 90 J were obtained). Finally samples were further tempered in 20°C steps until about 43.5HRc. For all compositions a diffusivity at room temperature of more than 8.5 mm 2 /s (often more than 10,5 mm 2 /s and even more than 12 mm /s) were measured at some point of tempering. Example 3:
Steels with compositions specified in Table 3 with %Ni content more than 2.99% were austenitised at a temperature between 1000-1100°C for about 30 minutes (once the nuclei of the pieces had reached the temperature). Temperature was decreased at about 500°C/h to around a Tint chosen to be in the range of 470-600°C. At least in one of the treatments Tint was was chosen in the 480-560°C range. The cooling to Tint was made by rapidly decreasing the temperature inside the furnace itself and soaked at that temperature one hour. Afterwards, the material was severily quenched indistinctly in oil or water with maximum agitation (like in all examples, water was used for the compositions with theoretical or measured bainitic nose in the TT diagram with a transformation time of less than 100 seconds to 20% bainite (or alike). The higher %Ni content in these steels provides more time for the cooling from austenitisation temperature in a way that even a rapid cooling in the furnace is possible.
Table 3 c Mn Si Mo W Cr Al Cu V Ni S
0,32 0,210 0,000 2,81 2,10 0,120 0,040 0,100 0,080 3,00 <0,01
0,322 0,144 <0,05 3,01 0 1 ,930 0,071 0,01 1 0,080 0,01 7 3,01 0 0,001
0,32 0,17 0,13 3,13 1 ,9 0,07 0,03 0,08 0,030 3,04 0,003
0,340 0,135 <0,05 3,100 1 ,990 0,120 0,019 0,069 0,01 6 3,07 <0,01
0,371 0,066 < 0,05 3,660 1 ,390 < 0,01 <0,01 < 0,1 0,465 3,070 <0,01
0,402 0,166 <0,05 3,060 2,100 0,085 0,018 0,081 0,020 3,08 <0,01
0,384 0,158 0,088 3,080 2,130 0,074 0,019 0,077 0,01 6 3,08 <0,01
0,330 0,140 0,050 3,58 1 ,27 0,010 0,01 50 0,0200 < 0,005 3,0900 0,00319
0,32 0,16 0,14 2,92 1,75 0,1 0,02 0,08 0,030 3,1 0,003
0,384 0,168 0,104 3,090 2,080 0,079 0,026 0,079 0,01 9 3,1 1 <0,01
0,392 0,070 < 0,05 3,670 1 ,500 < 0,01 <0,01 < 0,1 0,459 3,190 0,0039
0,240 0,240 0,010 3,20 2,39 0,070 0,080 0,190 0,050 3,21 <0,01
0,392 0,213 0,0958 3,63 2,52 0,0832 0,0182 0,0845 0,0216 3,73 <0,005
Final micro structure was composed mainly by martensite. The hardness right after heat treatment was in all cases above 45 HRc. And for all compositions at least with one of the heat treatments the hardness was above 48HRc. Samples were afterwards tempered. It was seen that hardness superior to 45 HRc could be attained in the tempering graph. Samples were tempered beyond the secondary hardness peak resulting in hardnesses above 49HRc.
In all cases resilience exceeded 180 J/cm 2. In many cases, more than 340 J/cm 2 was measured and in some cases even more than 450 J/cm . All compositions were also further tempered to a hardness of 40-45 HRc for a CVN test where in all cases a value of more than 10J was encountered (in some cases more than 16J and even more then 90J were obtained). Finally samples were further tempered in 20°C steps until about 42.5 HRc. For all compositions a diffusivity at room temperature of more than 8.5 mm /s (often more than 9.6 mm 2 /s and sometimes even more than 11 mm 2 /s) were measured at some point of tempering.