TITLE CHAIN-STITCHED CARPET YARNS BACKGROUND OF THE INVENTION
Field of the Invention The present invention relates to carpet yarns composed of multiple component yarns which have been chain-stitched together, and methods for producing such yarns. These yarns are characterized by a unique structure, where each component yarn forms a series of tightly held loops along the entire length of yarn. The invention also encompasses carpets composed of such yarns. Description of the Related Art
The most common way for combining two or more component yarns in order to make a larger composite yarn, suitable for carpets, is by twisting them together. For example, in making yarns for saxony-type cut pile carpets, two or more bulked continuous filament yarns or staple yarns are twisted in one direction individually and then ply-twisted together in the opposite direction. The composite yarn is then heated while at low or no tension to a temperature at which the yarn strands become heat-set in the twisted condition. As a result, the yarns tend to remain twisted when they are inserted into a carpet backing and subsequently cut to form parallel vertical tufts. However, under continuous wear, the tuft tips gradually lose their twist and filaments of one tuft become entangled with those of neighboring tufts to form a matted surface appearance. Thus, a tuft tip structure which retains its integrity during wear would be greatly desired.
In preparing the above-described conventional ply-twisted yarns for cut pile carpets, the plies must be twisted firmly together; otherwise, they will untwist prematurely. To achieve acceptable twisting, a
lubricant solution must be applied to the component yarns in an amount of approximately 1% of the total yarn mass. The lubricant ingredients are then removed from the yarn when the carpets are dyed or scoured before sale, thus interfering with the treatment of effluent streams in waste water treatment systems of carpet mill communities. Yarn preparation systems which do not need such lubricants would be a great advantage.
A proposed alternative method for making carpet yarns is a stitching operation, where the component yarns are enchained together by a series of lock stitches, as described in Parlin, U.S. Patent 2,822,605. This operation involves varying the tension applied to the individual yarn strands, such that each yarn strand forms a series of tightly held loops and loosely held loops along its length. The process is carried out upon an overedge stitcher provided with a chain-forming mandrel. However, this type of yarn is not particularly desirable for making carpets today, due to the presence of loosely held loops in its structure.
Now, in accordance with this invention, novel chain-stitch yarns having a unique structure which makes them particularly suitable for carpet pile and a method for producing such yarns have been found. SUMMARY OF THE INVENTION
The present invention provides chain-stitched carpet yarns, carpets composed of such yarns r and a method for producing such yarns. The yarn comprises a plurality of component yarns, preferably two component yarns, characterized by each component yarn forming a series of loops, wherein a loop of one component yarn is enchained with a loop of the other component yarn to form a series of chain-stitches evenly spaced along the length of the
yarn. Each component yarn forms a series of tightly held loops uniformly along the entire length of yarn. Preferably, there are 3 to 16 chain-stitches per inch of yarn. The component yarns may all be of the same color, or they may be of different colors.
Suitable component yarns for this invention include bulked continuous filament yarns and crimped staple fiber yarns. These yarns include, for example, polyolefin yarns, such as polypropylene yarns, polyamide yarns, such as nylon 6,6 and nylon 6 yarns, polyacrylonitrile yarns, and polyester yarns.
The invention also provides a novel process for producing such yarns. The process involves chain-stitching a plurality of component yarns together, such that a loop of one component yarn is enchained with a loop of the other component yarn to form a series of chain-stitches evenly spaced along the length of the yarn. During the operation, uniform tension is applied along each component yarn such that each component yarn forms a series of tightly held loops uniformly along the entire length of yarn. The yarns may be subsequently heat-set, making them ideal for cut-pile carpets. Furthermore, no yarn lubricant is needed for producing these yarns.
The invention also includes carpets, such as those having cut-pile and loop pile surfaces. For cut-pile carpets", the yarns are preferably heat-set and have two or more chain-stitches per tuft.
BRIEF DESCRIPTION OF THE DRAWINGS Figure 1 is a schematic drawing of the chain-stitched yarn of this invention.
Figure 2A is an enlarged photograph (about 5X) of conventionally ply-twisted nylon bulked continuous filament (BCF) yarn tufts in a cut pile carpet before wear testing.
Figure 3A is a view of the carpet of Figure 2A after wear testing.
Figure 2B is an enlarged photograph (about 5X) of tufts of chain-stitched yarns of this invention in a cut pile carpet before wear testing.
Figure 3B is a view of the carpet of Figure 2B after wear testing.
Figure 2C is an enlarged photograph (about 5X) of tufts of chain-stitched yarns of this invention in a cut pile carpet before wear testing.
Figure 3C is a view of the carpet of Figure 2C after wear testing.
Figure 2D is an enlarged photograph (about 5X) of tufts of chain-stitched yarns of this invention in a cut pile carpet before wear testing.
Figure 3D is the carpet of Figure 2D after wear testing.
Figure 2E is an enlarged photograph (about 5X) of tufts of chain-stitched yarns of this invention in a cut pile carpet before wear testing.
Figure 3E is a view of the carpet of Figure 2E after wear testing.
Figure 4 is a perspective view of a sewing machine capable of making the chain-stitched yarns of this invention.
Figure 5 is an enlarged view of the needle and looper portion of the sewing machine shown in Figure 4.
Figure 6 is a partial view of the opposite side of the sewing machine of Figure 4, showing a puller roll device for removing the stitched yarn from the needle and looper mechanism.
Figure 7 is a cross-sectional view of a yarn of this invention under tension.
DETAILED DESCRIPTION OF THE INVENTION
The present invention provides carpet yarns having an improved "chain-stitch" structure, carpets composed of such yarns, and a method for producing such yarns. By the term, "chain-stitch", it is generally meant a structure where component yarns are combined into a series of equally spaced loops of which each loop of one component yarn is enchained with a loop of the other component yarn or yarns. In a known process for producing chain-stitch yarns, as described in the aforementioned U.S. Patent 2,822,605, a chain-stitch structure may be produced upon an overedge stitcher having a needle, an upper and lower looper, a mandrel about which successive stitches are formed, and a device for drawing-off the completed yarn at a predetermined rate. This conventional process is governed by a solenoid controlled tensioning mechanism, where one of the feeding yarn strands is subjected to a high tension, while relatively low tension is applied to the other strand for a predetermined length along the enchained yarn. At other predetermined lengths along the same yarn, the tensioning effect on the yarn strands reverses, thus providing each yarn strand with a series of tightly held loops (caused by high tension) and a series of loosely held loops (caused by low tension) .
Referring to the drawings, Figure 1 shows a chain-stitched yarn of the present invention formed from component carpet yarns (1) and (2) . The schematic stitch structure is slightly expanded, to show the yarn paths more clearly. It is understood that the actual structures for the yarns of this invention are more compact, as shown in Figures 2B-2E and 3B-3E.
As shown in Figure 1, the chain-stitches are formed by interlacing and interlooping the loops of
component yarn (1) with the loops of component yarn (2) . These stitches are referred to as Stitch-type 401 in United States Federal Standard No. 715A, "Stitches, Seams, and Stitchings". A stitch is composed of one loop of one component yarn enchained with a loop consisting of one or more second component yarns. Generally, there should be 3 to 16, and preferably 6 to 9, chain-stitches per inch of carpet yarn.
The key improvement of the chain-stitched carpet yarns of this invention is a structure, where each component yarn forms a series of tightly held loops along the entire length of yarn. The component yarns are firmly secured together by the successive tightly held loops of both component yarns. Since there is no formation of relatively loosely held loops, the carpet yarn does not have a loose flowing appearance. Rather, the carpet yarn exhibits a tightly looped structure which is highly resilient and less likely to lose its integrity.
When a yarn structure of the present invention, as shown in Figures 2B-2E and 3B-3E, is compressed axially, the yarn loops near the upper end of the tuft compress and contact the loops below, thus gradually increasing the resistance of the tuft to further compression. The resistance of the loops to bending also assists the resilience of the yarn structure. When the same yarn in a loop pile carpet or when lying on its side in a long cut pile carpet is compressed transversely, the stitch structure also supports load and recovers from compression more effectively than conventional ply-twisted yarn.
In contrast, as shown in Figure 2A, when tufts in cut pile carpets composed of conventional ply-twisted yarns are compressed axially by foot traffic, the twisted structure opens. This opening, when repeated many times
and combined with scuffing of the tuft tip, causes the fibers at the tip to spread apart and tangle with fibers of adjacent tufts, giving a matted appearance, as shown in Figure 3A. These conventional ply-twisted tufts exhibit significantly higher tip flaring than the chain-stitched yarns of this invention.
This chain-stitch structure, as shown in Figures 2B-2E, compresses the component yarns laterally so that it may develop less bulk than the conventional yarn structures of Figure 2A. This is particularly true for structures having a high number of chain-stitches per inch. However, the increased bending resilience, as described above, at least partially offsets any loss of bulk. Thus, in the present invention, high bulk component yarns may be used, since they contribute added resilience and load-bearing ability. In contrast, high bulk component yarns are often not used in conventional ply-twisted structures because the tufts are too soft and lose their appearance of newness rapidly. Figures 2E and 3E show cut pile yarn having six chain-stitches per inch tufted into 1/4 inch pile height carpet. It can be seen from Figure 2E (before wear testing) that there is only slightly more than one complete stitch showing, and after wear testing, the stitch structure has largely disappeared (Figure 3E) . Therefore, for best cut pile wear, the yarn denier, stitches per inch, and pile height should be selected so that the majority of tufts in cut pile carpets have two or more stitches. The unique yarn structure of this invention is obtained by applying uniform tension along the entire length of each component yarn during the chain-stitching process. The chain-stitches may be formed by sewing machines, Raschel knitting machines, or similar
interlooping equipment. When more than two yarns are employed,, the additional yarn or yarns is preferably added to the looper of a sewing machine or its equivalent.
In Figure 4, feed yarns (20), (21) and (22) are shown being threaded through conventional tensioners (23) , (24) and (25) , on a Union Special, Model 56100-MZ sewing machine and thence to the needles, shown more clearly in Figure 5. Yarns (26), (27) and (28) go through tensioners (29) , (30) and (31) to the loopers. Referring to Figure 5, yarns (20), (21) and (22) are each threaded through the eye of a needle (32), (33) and (34) , respectively. Yarns (26) , (27) and (28) are each threaded through looper (35) , (36) and (37) , respectively. In operation, needle (32) works with looper (35) to form a chain-stitched yarn (38) (see Figure 6) from feed yarns (20) and (26), needle (33) works with looper (36) to form a chain-stitched yarn (39) from feed yarns (21) and (27) , and needle (34) works with looper (37) to form a chain-stitched yarn (40) from feed yarns (22) and (28) .
Figure 6 shows the opposite side of the sewing machine from Figures 4 and 5. Chain-stitched yarns (38) , (39) and (40) are moved away from the needle and looper mechanisms by puller roll (41) which presses the yarns against the upper surface of the machine table. The puller roll's speed is adjusted by selecting the diameters of sprockets (42) and (43) which cooperate with cogged belt (44) to maintain a desired number of stitches per inch. A slower puller speed gives higher stitches per inch and vice versa. From here, the yarns may each go to a wind-up and be wound on a package.
Although the sewing machine shown in Figures 3-6 has three sets of needles and loopers, suitable machines may be obtained having one to thirty sets or more.
The productivity and speed of the present operation is not limited by centrifugal force as is conventional ply-twisting, and therefore the presently-existing stitch-forming equipment is not only faster than ply-twisting but does not have similar limitations on future speed increases.
The simplest chain-stitch structures of this invention require about twice the length of feed yarn as ply twisting; therefore, a two-feed chain-stitched yarn consumes four times the yarn length and gives a final yarn of about four times the starting yarn denier. To make a two-feed chain-stitched yarn of about 2200 final denier, two ends of about 550 denier each are required. In contrast, in order to produce a 2200 denier ply-twisted yarn two ends of about 1100 denier are required. More complex chain-stitch structures may require still longer lengths of smaller denier yarns. Large yarns may be made inexpensively by feeding multiple yarns to the looper so that a large yarn is produced in the same machine operating time as a smaller one.
When two or more component yarns of different color, dyeability or other property are used in the present process, it is found that the composite yarn appearance can be controlled more precisely and uniformly than when employing entangling processes of the prior art. It is important that the tension applied to each component yarn be uniform along the entire length of yarn. Tension on the feed yarns may be controlled by the tensioners furnished with the stitch-forming machine. However, for better control of tension, other types of known tensioners used in yarn processing operations may be substituted. These tensioners include, e.g., disc tensioners and spring-loaded tensioners, which are available from Steel Heddle of Greenville, SC. These
tensioners are commonly mounted off the stitch-forming machines. The tension in each feed yarn may be more easily measured if tensioners are mounted so that an accurate tensio eter may be inserted between the tensioner and the needle or looper.
It is recognized that the tension applied to one component yarn may be different than the tension applied to the other component yarn. In such a case, there will be a change in the proportion of one component yarn to another in the final yarn, with a corresponding contrast in the general color effect, where two or more component yarns of different color are used. It has been found that this colored appearance can be controlled more precisely and uniformly with this method versus known yarn entangling processes.
The effect of yarn tension on the cross-sectional shape of the yarn can be seen in Figure 7. Figure 7 is a cross-sectional view of a yarn of this invention, where dimensions (5) and (6) are substantially equal, which is typical when two component yarns (3) and (4) of equal properties are chain-stitched together at equal yarn tensions. A specific dimension will be greater when larger or stiffer yarn is employed or when tension is lower. The ratio of the dimensions is preferably no greater than 2:1, more preferably no greater than 1.5:1, because a yarn of elongated cross-section provides less "cover" for hiding the backing of a carpet. However, yarns having a ratio greater than 2:1 may be used to obtain unusual visual or mechanical properties in a cut or loop pile carpet.
Suitable component yarns for this invention include bulked continuous filament yarns and crimped staple fiber yarns. These yarns include, for example, polyolefin yarns, such as polypropylene yarns, polyamide
yarns, such as nylon 6,6 and nylon 6 yarns, polyacrylonitrile yarns, and polyester yarns.
In contrast to conventional ply-twisted yarn where filaments can spread in all directions from a tuft tip and entangle with those from neighboring tufts, the nature of the present yarn's stitch structure holds the cut filament ends closely together. This occurs even if the chain-stitch structure starts to slightly unravel, such as in cases of heavy wear. Another advantage of the chain-stitch structure is that the cut end is only about one-half the denier of a ply-twisted tuft, therefore having many fewer filament ends to spread and entangle.
If the yarns of this invention are to be used in cut pile carpets, the yarn should be heat-set. The heat-setting of the stitched yarn greatly retards unraveling in even the most susceptible directions. The heat-setting operation may involve passing a yarn through a Superba heat-setting machine, which treats the yarn with pressurized saturated steam to heat-set the stitches. Another method involves passing the yarn through a continuous Suessen heat-setting machine, which treats the yarn with dry heat to heat-set the stitches. For nylon yarns, steam at 120° to 140°C or dry air at 180° to 210°C is effective. The heat-setting step may be done after the chain-stitched yarns are wound or as the yarn travels from the stitch-forming operation to winding.
If the yarns of this invention are to be used in loop pile carpets, it is not necessary to heat-set them. Generally, nylon or other synthetic staple yarn is not commonly used in loop pile carpets, because the scuffing which the yarn receives on the tops of the loops from shoes loosens the twisted yarn structure and allows free ends of the staple filaments to protrude from the yarn and be drawn out further to form unsightly fuzz and pills.
However, when a staple yarn is formed in accordance with this invention, particularly at a stitching rate of 6 stitches per inch or greater, the stitch structure constricts the yarn and allows only small lengths of the fibers to be exposed to scuffing. The constructions prevent fiber ends from protruding and being drawn out to form pills and fuzz.
It is recognized that the chain-stitched yarns of this invention can be made from a broad range of synthetic or natural fiber component yarns and may be used for other purposes than as pile in carpets. These yarns may be used as cords or ropes, or they may, for example, be used as craft yarns in hand knitting. They may also be incorporated in warp and circular knits and in woven fabrics, and are especially suited for applications where improved resistance to wear is needed. Testing- Methods Texture Retention
The texture retention of the carpet samples was evaluated after wear tests which were conducted in a
Vetterman drum test apparatus, Type KSG manufactured by Schoenberg & Co. (Bamberg, Germany) . The drum was lined with carpet samples, with the pile facing inwards and contained a steel ball having 14 rubber buffers which rolled randomly inside the rotating drum. - The drum was rotated in alternating directions. A circular brush within the drum was in light contact with the carpet surface and removed loose pile fibers which were continuously removed by suction. After a period of cycles, the samples were removed and inspected to evaluate texture retention.
Texture retention was determined using a scale of 1-5 with a rating of 5 corresponding to an untested
control sample and 1 corresponding to an extremely matted control sample. Measurement of Chain-Stitches
The number of chain-stitches per inch of yarn may be measured by (1) reading the stitch rate from a roller puller sprocket table supplied by the stitch forming machine manufacturer when the top or driven sprocket and bottom or drive sprocket are known, (2) directly from a piece of fabric run through the machine with the help of a puller such that the yarn is stitched into the fabric and a series of chain-stitches is formed, or (3) stretching the yarn under minimal tension and manually counting the number of stitches.
The following examples further describe the invention but should not be construed as limiting the scope of the invention.
EXAMPLES EXAMPLE 1 Carpet A .Control) Commercially available, Du Pont 1100 Type 746 BCF
(bulked continuous filament) nylon 6,6 yarns of 1100 total denier and comprised of 68 filaments (of trilobal cross-section) were produced by a conventional process. Two of these yarns were plied and twisted to provide a yarn with a balanced twist of 4.5 turns per inch (tpi) .
Plied and twisted yarn was then conventionally heat-set in a Superba heat-set apparatus at 270 degrees F with a resulting yarn denier of 2400. A cut pile tufted carpet was constructed from the heat-set yarn to the following specifications: 40 oz./sq.yd. weight, 11/16 inch pile height, 5/32 inch gauge, and 12.5 stitches per inch. The carpet was dyed to a light blue shade on a continuous dye line using the following dye formulation and based on the weight of carpet: 0.0005% "Tectilon" Orange 3G-200
(C.I.Acid Orange 156), 0.0005% "Tectilon" Red 2B-200 (C.I. cid Red 361) and 0.0075% "Tectilon" Blue 4R-200 (C.I. cid Blue 277), (available from Ciba-Geigy Corp.). After dyeing, the carpet was rinsed, extracted and subsequently treated with a commercial fluorochemical soil repellent in a conventional spray application. Finally the carpet was dried in an oven, latexed and sheared. Carpet B
BCF nylon 6,6 yarns of 550 total denier and comprised of 34 filaments (of trilobal cross-section) were produced by a conventional process of splitting commercially available, Du Pont nylon yarn of 1100 Type 746. Two of these yarns were chain-stitched together on an industrial type sewing machine, Model No. 56100-MZ, made by Union Special, to form a chain-stitched composite yarn having 5 stitches per inch. The chain-stitched yarn was then heat-set in a Superba heat-set apparatus at 270 degrees F with a resultant total yarn denier of 2800. A cut pile tufted carpet was constructed from the heat-set yarn to the following specifications: 40 oz./sq.yd. weight, 11/6 inch pile height, 5/32 inch gauge, and 10 stitches per inch. This carpet was dyed and finished in the same manner as Carpet A. Carpet C The carpet was prepared in the same fashion as
Carpet B, except that the yarns were chain-stitched together to form a chain-stitched composite yarn having 8 stitches per inch. The carpet dyeing and finishing were done in the same manner as Carpet B. Carpet D
Commercially available, Du Pont 1100 Type 746 BCF nylon 6,6 yarns of 1100 denier and comprised of 68 filaments (of trilobal cross-section) were produced by a conventional process. Two of these yarns were
chain-stitched together using the same machine as described above for the yarns in Carpet B to form a chain-stitched composite yarn having 5 stitches per inch. The chain-stitched yarn was then passed through the stuffer box with 5 p.s.i. steam pressure prior to heat-setting in a Superba heat-set apparatus at 270 degrees F. The final "textured" yarn had a total yarn denier of 6300. A cut pile tufted carpet was constructed from the heat-set yarn to the following specifications: 40 oz./sq.yd. weight, 5/8 inch pile height, 5/32 inch gauge, and 4 stitches per inch. The carpet was dyed to a light beige shade on a continuous dye line using the following dye formulation and based on the weight of carpet: 0.02% "Tectilon" Orange 3G-200 (C.I.Acid Orange 156), 0.01% "Tectilon" Red 2B -200 (C.I. Acid Red 361) and 0.0125% "Tectilon" Blue 4R-200 (C.I.Acid Blue 277). After dyeing, the carpet was latexed and finished in the same manner as Carpet A. Carpet E BCF nylon 6,6 yarns of 705 total denier and comprised of 42 filaments (of trilobal cross-section) were produced by a conventional process of splitting Du Pont nylon yarn 1410 Type 696AS. Two of these yarns were chain-stitched together using the same commercial sewing machines as used in making yarns for Carpet B to form a chain-stitched composite yarn having 6 stitches per inch and the resultant denier of 2900. The yarn was not heat-set. A cut pile tufted carpet was constructed from these non heat-set yarns to the following specifications: 16 oz./sq.yd. weight, 1/4 inch pile height, 1/8 inch gauge, and 6 stitches per inch. This carpet was dyed and finished in the same manner as Carpet A.
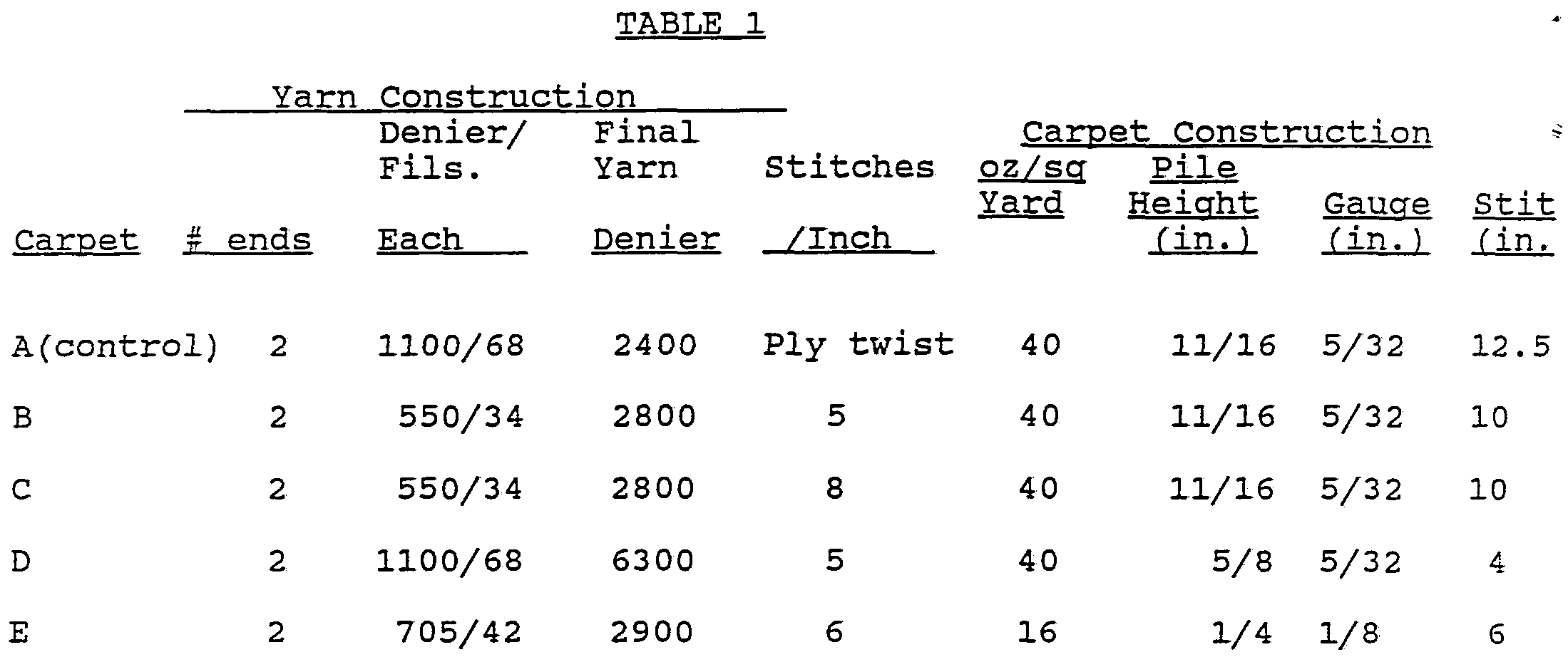
All five (5) carpets (Control Carpet A, and carpets using the new invention technique B, C, D and E) were subjected to the wear test for 5000 cycles, and evaluated for texture retention, as outlined above. The texture of each evaluated carpet was rated by 3 different people, and the average of those ratings is reported in Table 2. Figures 2 and 3A are photographs of Control Carpet A; Figures 2B and 3B are photographs of Carpet B; Figures 2C and 3C are photographs of Carpet C; Figures 2D and 3D are photographs of Carpet D; and Figures 2E and 3E are photographs of Carpet E.
17 TABLE 2
Texture Retention
Sample Rating REMARKS
Carpet A 3.5 Open and fuzzed tuft tips; pile (Control) matted.
Carpet B 4.3 Better tuft definition; less matting than control Carpet A. Carpet C* 3.5 Better tuft retention compared to other textured products in a similar construction made by conventional ply- twisting techniques.
Carpet D 4.7 Extremely well defined tufts; appear almost like not wear tested, Superior texture retention when compared with control Carpet A.
Carpet E< 1.9 Matted, but better appearance (crush resistance) than other carpets in a similar construction made by conventional ply- twisting techniques.
*NOTE: Carpet C is compared with a textured residential carpet in a similar construction and Carpet E is compared with an automotive carpet in a similar construction using a non-heatset yarn.
EXAMPLE 2 Two ends of commercially available, Du Pont 1245 denier BCF solution dyed nylon 6,6 ANTRON LUMENA were chain-stitched at 9, 7.5 and 6 stitches per inch (spi) to yield separate yarns having deniers of 7964, 6821 and 7214, respectively (~3X imput feed yarn deniers) . These yarns were used to make carpets by tufting them as bands on a 1/8 gauge loop pile tufter at 0.188 inch pile height and 6.75 stitches per inch (spi) to approximately 32 oz/sq.yd. The loop pile carpets were topically treated with 0.9% anti-soil fluorochemical followed by latexing/drying. These carpets, along with control carpets composed of conventional air-entangled yarns, were exposed to 110,000, 220,000 and 330,000 cycles in the Vetterman drum and ranked on a 1-5 scale, as described above. The carpet ratings are shown in Table 3.
EXAMPLE 3 Three ends of commercially available, Du Pont 1245 denier BCF solution dyed nylon 6,6 ANTRON LUMENA were chain-stitched at 9, 7.5 and 6 spi to yield separate yarns having deniers of 12122, 11477, and 13563, respectively, (~3X imput feed yarn deniers) . These yarns were used to make carpets by tufting them as bands on a 1/8 gauge loop pile tufter at 0.188 inch pile height and 7.25 spi to 49, 41 and 44 oz/sq. yd. , respectively. The loop pile carpets were treated with the finishing agent described in Example 2. These carpets were exposed to 110,000, 220,000, and 330,000 cycles in the Vetterman drum and ranked on a 1-5 scale, as described above. The carpet ratings were similar to the ratings for the carpets of EXAMPLE 2.
EXAMPLE 4 Two ends of 622 denier (produced by splitting the threadline of Du Pont ANTRON 1245 denier BCF piece-dye
hollow filament yarn on the commercial spinning machine) yarns were chain-stitched at 9, 7.5 and 6 spi to yield separate yarns having deniers of 4017, 3703 and 3553, respectively (~3X input feed yarn deniers) . These yarns were tufted as bands on a 1/8 gauge loop pile tufter at 0.188 inch pile and 13 spi to 31, 32, and 34 oz/sq. yd., respectively. The loop pile carpet samples were beck dyed using 0.0115% "Tectilon" Orange 3G-V, 0.0165% "Tectilon" Red 2B-V, 0.1100% "Tectilon" Blue 4R, and 1% Du Pont "Alkanol" ND. These carpets were exposed to 110,000, 220,000, and 330,000 cycles in the Vetterman drum and ranked on a 1-5 scale, as described above. The carpet ratings were similar to the ratings for the carpets of EXAMPLE 2. EXAMPLE 5
Three ends of 950 denier polypropylene were chain-stitched to yield a yarn having a denier of 10,000. The yarn was tufted on a 1/8 gauge table top tufter at 0.188 inch pile and 5 spi to 33 oz./sq. yd. .The loop pile carpet was latexed and dried. The finished carpet had unique visuals and excellent Vetterman drum performance after 22,000 cycles.
Air-Entangled "Rooster- Tail"
Controls 110M 3 Noticeable crushing " 220M 2.5 Very noticeable crushing
" 330M Slightly severe crushing
"Gilbos" Air- Entangled
Controls 330M 1.5 Severe crushing "Texalor" Air- Entangled Controls 330M Very severe crushing
*M = thousand